压载水处理装置(BWMS)产品检验大纲
JFE_BWMS说明资料20110420(PDF)[1]
![JFE_BWMS说明资料20110420(PDF)[1]](https://img.taocdn.com/s3/m/024dde26aaea998fcc220e90.png)
实际使用有效氯浓度:5 mg/L 试验时的有效氯浓度: 20 and 50 mg/L
160
140
Untested
50 days
120
210 days
100
340 days
80
60
40
20
0
Untested
Artificial Seawater
Artificial
Artificial
Seawater + Seawater +
・不需要供给药剂
・有氢气产生,要防爆 ・杀菌效果易受海水成分影响 ・需要电极更换 ・耗电量大(1000m3/hr >> 50kw)
・有臭氧产生,对身体有危害 ・设备多,故障率高,成本大 ・耗电量大(1000m3/hr >> 87kw )
可通过2种溶液的混合在现场制 ・原液错误混合时有爆炸的危险性 造,原液浓度高,储存容器小 ・分解物(游离氯)对身体有危害
Ballast water Volume(m3)
5,000 10,000 15,000 25,000 50,000 100,000
Biocide (m3)
0.25 0.5 0.75 1.25 2.5 5.0
Reducing agent
Powder (kg) Solution (m3)
15
0.14
30
IMO公约实施日程(假设)
2012年1月
2014年1月
2017年1月
2019年1月
新造船DWT15000以下
Байду номын сангаас
新造船DWT15000以上
旧船DWT15000以下
旧船DWT15000以上
压力容器产品安全质量监督检验大纲

压力容器产品安全质量监督检验大纲1. 引言压力容器是一种用于储存或运输气体或液体的设备,由于容器内部存在高压力,其使用和制造必须符合相关的安全质量标准和监督检验要求。
本大纲将介绍压力容器产品的安全性和质量标准,以及监督检验的流程和要点。
2. 压力容器产品安全要求压力容器产品的安全性是制造和使用过程中必须考虑的重要因素。
安全要求包括但不限于以下几个方面:2.1 强度和稳定性压力容器必须具有足够的强度和稳定性,能够承受内部介质的压力和外界环境力的影响。
在设计和制造过程中,需要考虑容器材料的强度参数和力学性能,采用合适的结构形式和加固措施,以保证容器的安全使用。
2.2 密封性能压力容器在使用中需要保持压力介质的安全封闭,避免泄漏和泄爆现象的发生。
其密封性能包括容器与容器之间的连接密封、容器与附件之间的连接密封以及容器本身的封闭性。
2.3 防爆性能压力容器在承受外界力的作用下,应能有效地抵抗爆炸压力,并减轻并且控制事故发生时的爆炸冲击和危害。
为此,需要采取相应的防爆措施,如爆炸阀、减压装置等。
2.4 安全附件压力容器的安全附件是保证容器正常运行和安全使用的重要组成部分。
常见的安全附件包括压力表、温度计、安全阀等,这些附件一般需要经过严格的检验和校准。
3. 压力容器产品质量标准3.1 国家标准《压力容器设计制造安全技术规范》是中国国家标准委员会颁布的压力容器设计和制造的基本标准,其中涵盖了以下内容:•压力容器的分类和定义•压力容器的设计和制造要求•压力容器的检验和测试方法•压力容器的安装和使用要求3.2 行业标准除了国家标准外,还存在一些行业标准和规范,针对不同类型的压力容器产品制定了具体的安全质量要求。
例如,石化行业的压力容器产品可能需要符合《石油化工装备安全技术规程》等相关标准。
4. 压力容器产品监督检验流程4.1 设计和制造阶段检验压力容器在设计和制造阶段需要经历一系列的检验环节,主要包括设计审查、材料检验、焊接检验、气密性试验等。
01 - BWM Convention 压载公约

MEPC.252(67) BWM.2/Circ.42/Rev.1
PSC Guidelines for BWM was adopted at MEPC 67, to be used in association with BWM.2/Circ.42/Rev.1 – Sampling and Analysis Guidance for Trial Use
Seriously affecting human health, cause damage to local aquatic life and local economies 严重地影响人类建康,破坏当地水中生物,环境生态,与地区经济
The effects costs millions of dollars to deal with each year 从而带来每年千万美元以上的损失
Implementation dates in BWM 2004 are different, and part of contents are not relevant, hence A.1088(28) need to be amended, so as BWM 2004 in due course
Management System (AMS) – as of 19 May 2016 到 2016年 5月 19日,USCG接受了57 套压载水处理系统为“替代处理系统” (AMSor IMO type approved BWTS: using UV technology – 27, using electrolysis – 16 得到 IMO 型式认可的BWTS : 使用紫外线 – 27,使用电解 – 16
Xian Dong ZHANG
张晓东
压载水处理装置(BWMS)技术条件

船舶压载水处理装置(BWMS)技术条件(企业标准)(第一版)20XX年X月XX日发布20XX年X月XX日实施拟制:批准:日期:日期:1.内容及适用范围本标准规定了船舶压载水处理系统的设计,制造,检验,性能测试方法及包装,运输,贮存等要求。
本标准适用于船舶压载水处理系统的设计、制造和检验。
压载水管理系统,是基于国际海事组织(IMO)关于《国际船舶压载水及其沉积物控制和管理公约》D-2规定,设计并建造的船舶压载水处理系统,目的在于有效控制压载水中的海洋生物,病毒和其它微生物的转移,防止外来物种的迁徙。
本系统适用于远洋船舶的压载水处理。
本系统也适用于中水回用,工业冷却水系统等的末端处理。
本产品特点是采用纯物理处理工艺,不添加或产生任何化学物质,对船舶无任何腐蚀影响。
设备布置紧凑,占地小,系统全自动控制,操作简单,维护方便等。
2. 引用标准下列标准所包含的条文,通过在本标准中引用而构成本标准的条文。
如其中某个标准被修订,使用本标准应参照相应的最新版执行。
IMO,《2004年国际船舶压载水及其沉积物控制和管理公约》IMO,《船舶压载水管理系统认可导则》(G8)IMO,《船舶压载水管理系统取样导则》(G2)Resolution MEPC, 173(58)中国船级社,《船舶压载水管理计划编制指南》(2006)中国船级社,《电气电子产品型式认可试验指南》(2006)3. 产品组成及型号3.1 产品组成船舶压载水处理系统由全自动自清洗过滤器、紫外杀菌装置和控制系统三个主要部分组成。
3.2 产品命名及型号编制方法防爆型代码额定处理能力(m3/hr)压载水处理装置代码公司代码3.3 产品规格3.3.1 BWMS 设备规格系列3.3.2 自清洗过滤器规格系列3.3.3 UV(紫外)消毒装置规格系列4. 产品技术要求及参数4.2 技术要求:采用机械过滤加中压紫外消毒的工艺对压载水进行有效处理;对于处理后的压载水,按照公约进行压载水管理的排放,达到公约D-2条规定,其中的生物浓度:1).最小尺寸大于或等于50 μm的存活生物少于10个/m3;2).最小尺寸小于50 μm但大于等于10 μm的存活生物少于10个/mL。
BSKY^TM压载水处理装置在实船中的应用
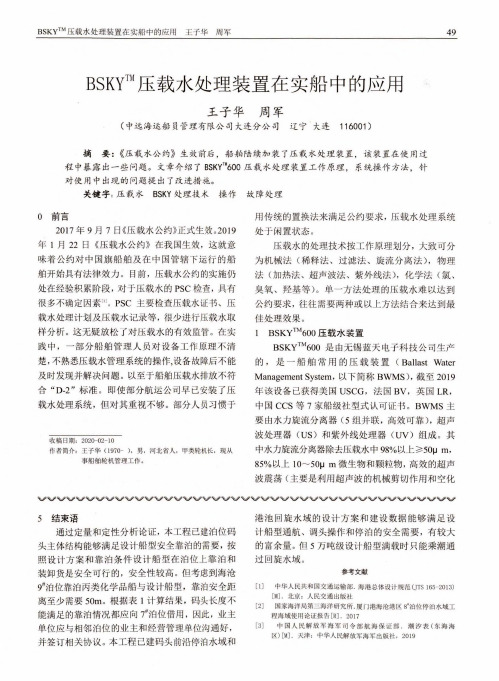
BSKYTM压载水处理装置在实船中的应用王子华周军49BSKY"4压载水处理装置在实船中的应用王子华周军(中远海运船员管理有限公司大连分公司辽宁犬连116001)摘要:《压载水公约》生效前后,船舶陆续加装了压载水处理装置,该装置在使用过程中暴露出一些问题。
文章介绍了BSKY"600压载水处理装置工作原理,系统操作方法,针对使用中出现的问题提出了改进措施。
关键字:压载水BSKY处理技术操作故障处理0前言2017年9月7日《压载水公约》正式生效。
2019年1月22日《压载水公约》在我国生效,这就意味着公约对中国旗船舶及在中国管辖下运行的船舶开始具有法律效力。
目前,压载水公约的实施仍处在经验积累阶段,对于压载水的PSC检查,具有很多不确定因素叭PSC主要检查压载水证书、压载水处理计划及压载水记录等,很少进行压载水取样分析。
这无疑放松了对压载水的有效监管。
在实践中,一部分船舶管理人员对设备工作原理不清楚,不熟悉压载水管理系统的操作,设备故障后不能及时发现并解决问题。
以至于船舶压载水排放不符合“D-2”标准。
即使部分航运公司早已安装了压载水处理系统,但对其重视不够。
部分人员习惯于收稿日期:2020-02-10作者简介:王子华(1970-),男,河北省人,甲类轮机长,现从事船舶轮机管理工作°用传统的置换法来满足公约要求,压载水处理系统处于闲置状态。
压载水的处理技术按工作原理划分,大致可分为机械法(稀释法、过滤法、旋流分离法),物理法(加热法、超声波法、紫外线法),化学法(氯、臭氧、疑基等)。
单一方法处理的压载水难以达到公约要求,往往需要两种或以上方法结合来达到最佳处理效果。
1BSKY™600压载水装置BSKY™600是由无锡蓝天电子科技公司生产的,是一船舶常用的压载装置(Ballast Water Management System,以下简称BWMS),截至2019年该设备已获得美国USCG,法国BV,英国LR,中国CCS等7家船级社型式认可证书。
压力容器产品安全质量监督检验大纲

压力容器产品安全质量监督检验大纲压力容器是一种能够储存和输送液体或气体的装置,其主要特点是能够承受内部压力的作用。
由于压力容器包含高压液体或气体,在使用过程中存在一定的安全风险。
因此,为了确保压力容器的安全质量,需要进行监督检验。
压力容器产品安全质量监督检验大纲主要包括以下内容:一、背景介绍压力容器是现代工业生产中常用的设备之一,广泛应用于石油化工、医药、航空航天等领域。
由于其具有一定的危险性,为了确保压力容器的安全使用,各国都制定了相应的法律法规和标准。
二、监督检验的目的和意义压力容器监督检验的主要目的是为了降低压力容器使用过程中的风险,保障人身安全和财产安全。
通过监督检验,可以及时发现和处理存在的安全问题,确保压力容器的安全可靠性,减少事故发生的可能性。
三、监督检验的内容和要求1. 压力容器的设计与制造监督检验应对压力容器的设计和制造过程进行全面的审核,包括设计图纸、制造工艺、材料采购等。
检验应确保压力容器的设计合理性、制造工艺符合要求,并对材料的质量进行抽样检验。
2. 压力容器的安装与调试监督检验应对压力容器的安装和调试过程进行检查,确保安装过程中的安全措施到位,并且调试过程中的参数设置合理。
对压力容器的连接、密封、防爆措施等进行检验,确保安装质量符合标准要求。
3. 压力容器的运行与维护监督检验应对压力容器的运行和维护过程进行检查,包括压力容器的定期检验、压力控制和溢压保护装置的运行情况、介质的处理和排放等。
检验应确保压力容器的运行和维护符合相关标准要求。
4. 压力容器的退役与报废监督检验应对压力容器的退役和报废过程进行检查,包括对压力容器的检验和清洗、封存和报废处理。
检验应确保压力容器的退役和报废过程安全可靠,避免对环境造成污染和对人员造成伤害。
四、监督检验的方法和要求1. 抽样检验监督检验可以通过抽样的方式进行,对具有代表性的样品进行检测或试验。
抽样应根据相关标准和要求,保证样品具有代表性和可靠性。
2023年压力容器产品安全质量监督检验大纲

2023年压力容器产品安全质量监督检验大纲一、前言近年来,压力容器产品在工业生产和民生领域的应用越来越广泛,因此对其安全质量的监督检验工作显得尤为重要。
为确保压力容器产品的安全性和可靠性,制定本大纲旨在规范2023年的压力容器产品的安全质量监督检验工作。
二、监督检验的对象本大纲中所指的压力容器产品主要包括:锅炉、炉窑、压力容器、埋地及水下管道、汽车气瓶、工业管道、压缩空气容器等。
三、监督检验的内容监督检验主要包括以下几个方面的内容:1. 设计审查和评定对压力容器产品的设计手册和图纸进行审查,评估其设计和制造的可行性、合理性以及符合相应的行业标准和技术规范。
特别要注意设计中的安全防护措施及应急措施。
2. 材料检验对使用于压力容器产品的各种材料进行检验,确保其质量合格。
着重检查材料的力学性能、抗腐蚀性能和可靠性。
3. 制造过程监督对压力容器产品的制造过程进行监督,包括材料的加工、组装和焊接等工序。
特别要关注焊接工艺的质量控制、焊接接头的可靠性以及焊缝的质量。
4. 强度试验对压力容器产品进行强度试验,以验证其在正常工作条件下的承载能力和安全性。
试验内容包括静态试验、冲击试验和疲劳试验等。
5. 安全装置检验检查压力容器产品的安全装置的性能和可靠性,确保其能够在超压、超温等异常情况下及时启动并起到保护作用。
6. 检测与检验对压力容器产品进行非破坏性检测和破坏性检验,包括射线检测、超声波检测、磁力检测等,以验证其质量是否合格。
7. 出厂检验对已制造完成的压力容器产品进行全面检验,确保其满足标准和技术规范的要求,并颁发合格证书。
四、监督检验的要求1. 检验机构应具备相应的资质,拥有合格的检验员和检测设备,确保检验结果的准确性和可靠性。
2. 检查和检验过程应符合国家标准和技术规范的要求,确保检验工作的科学性和严谨性。
3. 检验机构应当建立健全完善的质量管理体系,确保检验过程的可控性和可追溯性。
4. 检验机构应及时报告检验结果,并对不合格产品采取相应的措施,确保不合格产品不流入市场。
压力容器产品安全质量监督检验大纲

压力容器产品安全质量监督检验大纲一、大纲背景压力容器是一种高风险的装置,使用时需要进行安全质量监督检验,以确保其在使用过程中不会显现安全事故。
本大纲旨在对压力容器产品安全质量监督检验进行规范,供给检验标准和要求,确保压力容器产品的安全性和稳定性。
二、适用范围本大纲适用于各种类型、各种规格的压力容器产品的安全质量监督检验,包括但不限于固定式压力容器、半固定式压力容器和流动式压力容器等。
三、检验标准和要求1、压力容器安全质量性能检验(1)压力容器应充足设计、制造、使用和维护规范要求,确保其工作性能稳定牢靠。
(2)在设计压力范围内,压力容器应充足静态区、动态区和疲乏寿命等性能要求。
(3)压力容器应充足液体、气体、气液混合物等介质的工作温度、工作压力、流量和防腐蚀等要求。
(4)压力容器应充足使用环境的安全、卫生、环保等要求。
2、制造和检验工艺掌控(1)压力容器的制造和检验应符合相关国家和行业标准。
(2)压力容器的制造和检验应有订立的工艺程序和质量掌控程序,并进行全过程监控。
(3)压力容器的材料、构造及相关部件的制造、加工、组装过程应有合格证明,并建档保存。
3、压力容器安全附件及设备检验(1)压力容器的压力表、温度传感器、阀门及其他安全附件和设备应符合设计要求,并进行认证检验。
(2)压力容器的安全附件和设备应对温度、压力、流量、液位等参数进行实时监测,并适时报警处理。
4、压力容器运输和安装检验(1)压力容器的运输应符合相关法律法规和行业标准要求。
(2)压力容器的安装应依照设计要求进行,确保稳妥和牢靠。
(3)在压力容器安装过程中,应进行加固、固定、掌控及降噪等处理。
5、压力容器定期检验与维护(1)压力容器应依照相关标准规定进行定期检验和维护,包括外观、安全附件及设备、材料强度、泄漏失效等方面。
(2)压力容器的检验和维护应由专业团队进行,并建档保存。
四、检验程序和内容1、常规检验(1)压力容器的外观、尺寸、物理性质、密度、厚度测量等常规检验。
第三方检测船舶压载水检测标准

第三方检测船舶压载水检测标准第三方检测船舶压载水检测标准是确保船舶压载水的质量和安全性的重要措施。
在船舶运输中,为了保持稳定性和提高载货能力,常常需要借助压载水的使用。
然而,由于船舶的使用环境复杂多变,且压载水的来源和处理方式各不相同,因此需要制定一套科学严谨的检测标准来确保压载水的质量。
船舶压载水的检测标准应包含以下几个方面:1.物理性质检测:包括压载水的温度、密度、酸碱度、溶解氧和浊度等物理参数的测定。
这些物理参数的检测结果可以评估压载水的稳定性和适用性,以及对船舶结构和设备的腐蚀性。
2.化学成分检测:通过检测压载水中的含盐量、溶解氧、硅酸盐、腐蚀性物质等化学成分,可以评估压载水的锈蚀、污染和腐蚀程度。
同时,还需要检测压载水中的有机污染物和微生物含量,以评估压载水的卫生和环境影响。
3.微生物检测:压载水中存在大量的微生物,包括细菌、病毒和藻类等。
这些微生物有可能对人体健康和环境产生负面影响。
因此,需要对压载水中的微生物进行定量和定性检测,以评估其对船舶和环境的危害程度。
4.处理工艺检测:船舶压载水一般需要经过处理才能使用。
因此,需要对压载水处理工艺进行检测,包括沉积物处理、滤波、消毒和除盐等工艺的效果检测。
这些处理工艺的效果直接关系到压载水的质量和安全性。
5.船舶压载水的监测和记录:为了确保船舶压载水的质量和安全性,需要进行定期的监测和记录。
监测过程中,应确保监测数据的准确性和可追溯性。
同时,还需要建立完善的记录系统,将监测数据和处理结果进行记录和归档。
以上仅是对第三方检测船舶压载水检测标准的一个概要描述。
具体的检测标准需要由相关的标准制定机构或业界专家进行细化和具体化。
然而,无论具体的标准如何制定,都应尽可能地科学、严谨和可操作,以确保船舶压载水的质量和安全性,保护船员和环境的健康和安全。
压载水处理装置(BWMS)功能检验大纲

船舶压载水处理系统(BWMS)功能检验大纲(第一版)20XX年X月XX日发布20XX年X月XX日实施拟制:批准:日期:日期:为了确保船舶压载水管理系统的有效运行,对船舶压载水管理系统的各种功能进行系统有效的检测验证,特编制本大纲。
本大纲适用于船舶压载水管理系统产品出厂或现场交付前对相关功能进行检验和检测。
2. 术语和定义数据采集:数据处理:数据储存:数据显示:显示告警:通讯:3. 基本功能描述见工艺描述相关内容。
4. 基本功能检验4.1 基本功能检验前应具备的基本条件系统检验前应提供下列技术文件:●P&ID;●设备配置表;●接线测试记录(包括查线记录、绝缘电阻和接地电阻测试记录);●调试记录和调试报告;●系统检验报告(包括产品检验报告、合格证书及相关材料)●系统已经完成全部的内部和外部连线,确认正确;4.2 基本功能检验项目4.2.1资料文件电气原理图用户手册接线检查表产品检验单产品合格证4.2.2 电源输入:工作电压供电电源频率其它参数4.2.3 柜内功能项柜内开关:-主电源开关-24VDC电源开关-PLC/触摸屏电源-其它开关柜内照明:15W柜内通风:排风扇温度控制:温控器过载保护:柜内电源插座:3孔、2孔多功能模数化插座4.2.4 柜面板和触摸屏功能确认指示灯:-电源指示:主电源合闸,电源指示灯亮-运行指示:UV预热指示:指示灯红色指示UV运行指示:指示灯绿色指示UV冷却指示:指示灯红绿闪烁-故障指示:故障指示灯闪烁,且蜂鸣报警转换开关-就地/远程转换开关-压载/旁通/排放转换开关按钮开关-急停开关触摸屏显示:10寸彩色屏4.2.5 触摸屏画面显示开机页面次页面-过滤器页面-UV页面运行模式参数设定系统状态报警状态阀门检查工程师模式-工程师模式1:参数设定数据查询-工程师模式2:过滤器参数设定UV参数设定5. 控制系统功能5.1 数据采集功能过滤器单元:差压控制信号自清洗行程正向位置信号自清洗行程反向位置信号UV消毒单元:UV强度信号UV腔体温度检测信号UV自清洗行程正向位置信号UV自清洗行程反向位置信号管路系统:系统电磁流量计流量信号On/Off阀门位置信号流量控制调节阀开度信号系统状态:包括UV灯管的运行状态,故障状态和工作状态电子镇流器的运行状态,故障状态和工作状态动力柜温度信号其它:船舶运行GPS地理位置信号日期及时间数据采集功能可通过所配备的监测设备和触摸屏页面各原始数据记录表进行验证。
压力容器产品安全质量监督检验大纲范本
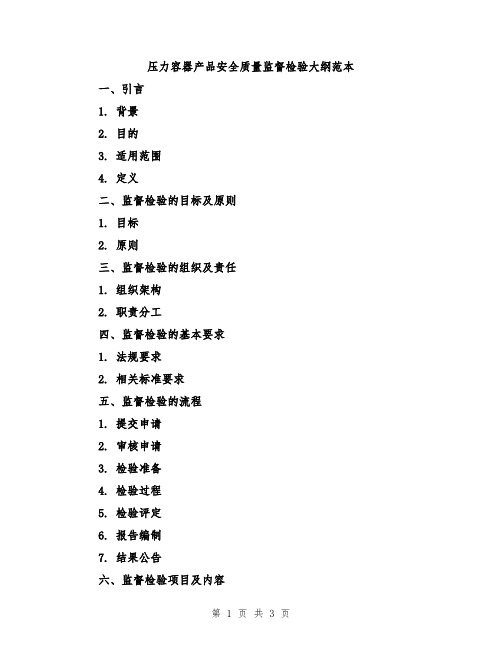
压力容器产品安全质量监督检验大纲范本一、引言1. 背景2. 目的3. 适用范围4. 定义二、监督检验的目标及原则1. 目标2. 原则三、监督检验的组织及责任1. 组织架构2. 职责分工四、监督检验的基本要求1. 法规要求2. 相关标准要求五、监督检验的流程1. 提交申请2. 审核申请3. 检验准备4. 检验过程5. 检验评定6. 报告编制7. 结果公告六、监督检验项目及内容1. 外观检验2. 尺寸检验3. 技术要求检验4. 材料检验5. 强度试验6. 压力试验7. 安全装置检验七、监督检验的方法与要求1. 检验方法2. 检验设备与工具3. 检验记录八、监督检验结果的评定与判定1. 评定标准2. 判定方式九、监督检验的监督与管理1. 抽检计划2. 抽检方法3. 报告审核十、监督检验的监督与处罚1. 监督方式2. 处罚措施十一、监督检验的质量管理1. 质量控制2. 安全控制十二、监督检验的信息化建设1. 数据管理系统2. 信息化手段十三、监督检验的研究及改进1. 检验方法研究2. 技术改进十四、监督检验的例外处理1. 特殊情况处理2. 突发事件应对十五、监督检验的统计与分析1. 统计指标2. 分析方法结论以上是一份压力容器产品安全质量监督检验大纲的范本,仅供参考使用。
在实际应用中,具体内容需要根据实际情况进行调整和完善。
压载水 检验报告

压载水检验报告1. 引言压载水是一种在海洋工程中广泛使用的灌注材料,用于增加船舶或海洋平台的稳定性。
本文将介绍对压载水进行检验的步骤和方法。
2. 实验设备为了进行压载水的检验,我们需要以下设备:•压载水样品•称重器•pH计•盐度计3. 检验步骤3.1 样品收集从船舶或海洋平台的压载水系统中取得样品。
确保取得的样品是充分混合并代表整个系统的水。
3.2 重量测量使用称重器准确地测量样品的重量。
记录下样品的质量以备后续分析使用。
3.3 pH值测量使用pH计测量样品的pH值。
将pH电极插入样品中,等待一段时间直至读数稳定,记录下pH值。
3.4 盐度测量使用盐度计测量样品的盐度。
将盐度计浸入样品中,等待一段时间直至读数稳定,记录下盐度值。
4. 结果分析根据测量结果,我们可以对压载水的质量进行评估和分析。
4.1 重量分析通过对样品重量的测量,我们可以计算压载水的密度。
密度是衡量压载水稳定性的重要指标之一。
较高的密度意味着压载水具有更好的稳定性。
4.2 pH值分析pH值可以反映压载水的酸碱性。
一般来说,压载水的pH值应保持在中性范围内,即7左右。
如果pH值过高或过低,可能会影响压载水的性能和稳定性。
4.3 盐度分析盐度是压载水中溶解的盐类的含量。
过高或过低的盐度都可能导致压载水的稳定性下降。
因此,合适的盐度范围对于压载水的性能至关重要。
5. 结论通过对压载水样品的重量、pH值和盐度的测量和分析,我们可以得出如下结论:•压载水的密度符合要求,具备良好的稳定性。
•压载水的pH值在合理范围内,不会对其性能产生负面影响。
•压载水的盐度适中,有利于保持其稳定性和性能。
通过本次检验,我们对压载水的质量进行了评估和分析,并得出了正面的结论。
这有助于确保在海洋工程中使用压载水时的安全和可靠性。
参考文献[1] 某某某. 海洋工程概论. XXX出版社, 20XX.[2] 另外一个作者. 压载水的应用及其质量控制. XX杂志, 20XX.。
压载水检验报告
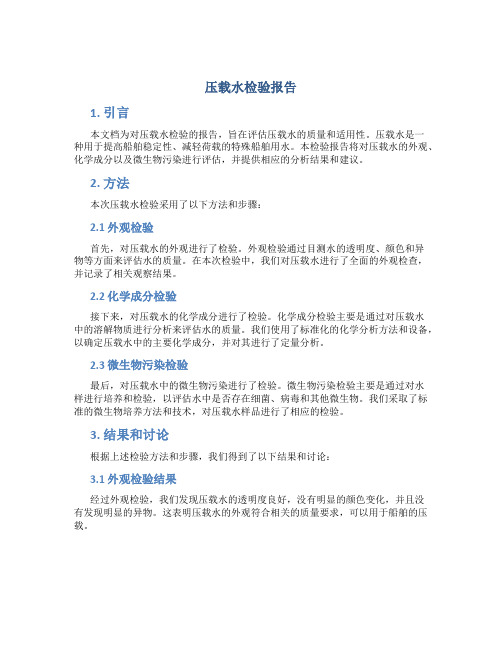
压载水检验报告1. 引言本文档为对压载水检验的报告,旨在评估压载水的质量和适用性。
压载水是一种用于提高船舶稳定性、减轻荷载的特殊船舶用水。
本检验报告将对压载水的外观、化学成分以及微生物污染进行评估,并提供相应的分析结果和建议。
2. 方法本次压载水检验采用了以下方法和步骤:2.1 外观检验首先,对压载水的外观进行了检验。
外观检验通过目测水的透明度、颜色和异物等方面来评估水的质量。
在本次检验中,我们对压载水进行了全面的外观检查,并记录了相关观察结果。
2.2 化学成分检验接下来,对压载水的化学成分进行了检验。
化学成分检验主要是通过对压载水中的溶解物质进行分析来评估水的质量。
我们使用了标准化的化学分析方法和设备,以确定压载水中的主要化学成分,并对其进行了定量分析。
2.3 微生物污染检验最后,对压载水中的微生物污染进行了检验。
微生物污染检验主要是通过对水样进行培养和检验,以评估水中是否存在细菌、病毒和其他微生物。
我们采取了标准的微生物培养方法和技术,对压载水样品进行了相应的检验。
3. 结果和讨论根据上述检验方法和步骤,我们得到了以下结果和讨论:3.1 外观检验结果经过外观检验,我们发现压载水的透明度良好,没有明显的颜色变化,并且没有发现明显的异物。
这表明压载水的外观符合相关的质量要求,可以用于船舶的压载。
3.2 化学成分检验结果化学成分检验结果显示,压载水中主要包含水分和少量的无机盐。
我们还发现压载水中铁、铜、锌等金属含量低于相关标准的限制值。
从化学成分角度来看,压载水符合质量要求,并可安全使用。
3.3 微生物污染检验结果微生物污染检验结果显示,压载水中没有检测到细菌、病毒等有害微生物的存在。
这表明压载水在微生物污染方面符合相关质量标准,并可以安全使用。
4. 结论根据对压载水的外观、化学成分和微生物污染的检验结果,我们得出以下结论:•压载水的外观良好,符合质量要求。
•压载水的化学成分符合相关标准,可以安全使用。
型式认可试验大纲_201209
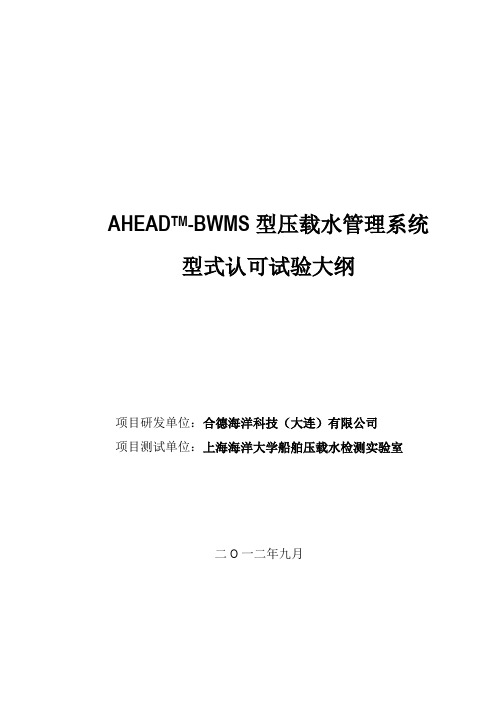
AHEAD TM-BWMS型压载水管理系统型式认可试验大纲项目研发单位:合德海洋科技(大连)有限公司项目测试单位:上海海洋大学船舶压载水检测实验室二О一二年九月目录1总则 12试验目的 (1)3试验依据的规范、标准 (1)4型式认可试验项目及合格判定的标准 (2)4.1型式认可的范围 (2)4.1.1AHEAD TM– BWMS系列产品 (2)4.1.2主要零部件: (2)4.1.3紫外监控: (3)4.2岸基试验 (4)4.2.1有效衡准 (5)4.2.2合格衡准 (5)4.3船上实验 (6)4.3.1有效衡准 (6)4.3.2合格衡准 (6)4.4环境条件试验 (6)5岸基试验 (7)5.1试验准备和试验条件 (7)5.2样品的选择和符合性验证 (9)5.3试验中添加的生物门类 (10)5.4试验方法和试验程序 (10)5.4.1 出厂检验程序 (10)5.4.2性能试验程序 (12)5.4.3水样检测方法 (16)5.5取样示意图及取样说明 (18)5.5.1取样时间段设计 (18)5.5.2取样点的设置 (18)5.5.3采样记录 (20)5.6试验机构、试验地点和检测设备 (20)5.7拟定的样品分析实验室资质 (21)6船上试验 (21)6.1试验准备和试验条件 (21)6.1.1试验用文件和资料: (21)6.1.2试验用设备 (21)6.1.3试验设施 (21)6.1.4保障条件 (22)6.2样品的选择和符合性验证 (22)6.3试验中添加的生物门类 (23)6.4试验方法和试验程序 (23)6.4.1试验程序 (23)6.4.2水样检测方法 (27)6.5取样示意图及取样说明 (28)6.5.1取样点的设置 (28)6.5.2取样时间段设计 (31)6.6试验机构、试验地点和检测设备 (31)6.7拟定的样品分析实验室资质 (31)7电控系统环境条件试验 (31)7.1试验依据 (31)7.2试验条件 (32)7.3试验方法和试验程序 (32)7.4机构、试验地点和检测设备 (48)7.5拟定的样品分析实验室资质 (48)附录附录E1.岸基试验水质条件的调控附录E2.水质参数测定方法附录E3.生物检测方法附录E4.紫外线剂量计算书附录E5.参考文献1总则本试验大纲规定了AHEAD TM-BWMS型压载水管理系统型式试验的目的、内容和要求。
压力容器产品安全质量监督检验大纲

压力容器产品安全质量监督检验大纲概述随着工业生产和科学技术的不断发展,压力容器逐渐成为各行各业的必备设备,但其中存在着一定的安全隐患。
为了保障人民生命财产安全,必须对压力容器产品进行安全质量监督检验。
本文就压力容器产品安全质量监督检验相关内容进行阐述。
适用范围本标准适用于压力容器产品制造、使用、监督检验等环节中所涉及的各项安全质量监督检验工作,包括压力容器产品的设计、制造、安装、维修、保养和使用等各个阶段。
检验内容1. 产品设计•产品设计是否满足国家和地方规定的相关标准要求;•地震工况要求是否满足或超过规定标准。
2. 材料揭示检验•压力容器产品主要材料的合格证、质量证明材料等文件内容是否与委托加工单要求一致;•主要材料是否符合国家或行业标准的要求;•废材料和不合格材料的控制是否符合相关标准。
3. 焊接材料检验•焊条和焊丝是否符合相关标准;•焊接材料质量证明文件的审核情况是否合格。
4. 设备检验•压力容器产品相关部件、附件、仪表、管道、阀门等是否正确齐全,是否符合设计要求;•检验过程中应强调安全措施,采取相应的安全措施,避免因操作不当而造成的安全事故。
5. 焊接控制•焊接人员是否持有相关的资格证书;•焊接过程是否符合设备制造厂商、设计单位和国家标准要求;•控制焊接变形、内部缺陷和尺寸偏差等技术要求。
6. 焊接质量检验•焊缝外观质量和尺寸偏差是否符合设计要求;•焊缝的焊道性质是否符合设计要求;•至少进行超声波探伤或射线探伤。
7. 热处理•控制热处理参数是否正确和符合要求;•热处理后的产品硬度值是否符合要求。
8. 水压试验•检验设备要满足要求;•水压是否达到规定要求;•水压试验应采取安全措施。
9. 渗漏试验•渗漏试验的方法、时间、压力是否符合要求;•试验结果是否合格。
10. 结构考核•产品结构是否符合要求;•断口形态和位置是否符合标准要求;•高、低温冲击试验是否合格。
结论根据以上检验内容进行检验后,应得出符合要求或不符合要求的结论。
压载水处理系统水样化验法定要求
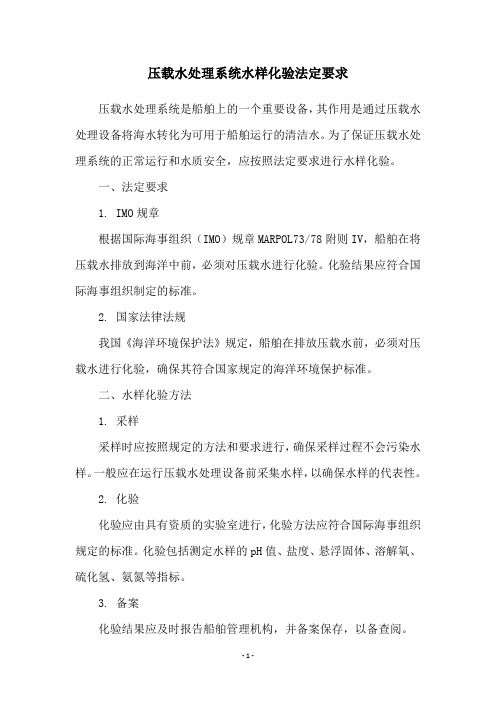
压载水处理系统水样化验法定要求
压载水处理系统是船舶上的一个重要设备,其作用是通过压载水处理设备将海水转化为可用于船舶运行的清洁水。
为了保证压载水处理系统的正常运行和水质安全,应按照法定要求进行水样化验。
一、法定要求
1. IMO规章
根据国际海事组织(IMO)规章MARPOL73/78附则IV,船舶在将压载水排放到海洋中前,必须对压载水进行化验。
化验结果应符合国际海事组织制定的标准。
2. 国家法律法规
我国《海洋环境保护法》规定,船舶在排放压载水前,必须对压载水进行化验,确保其符合国家规定的海洋环境保护标准。
二、水样化验方法
1. 采样
采样时应按照规定的方法和要求进行,确保采样过程不会污染水样。
一般应在运行压载水处理设备前采集水样,以确保水样的代表性。
2. 化验
化验应由具有资质的实验室进行,化验方法应符合国际海事组织规定的标准。
化验包括测定水样的pH值、盐度、悬浮固体、溶解氧、硫化氢、氨氮等指标。
3. 备案
化验结果应及时报告船舶管理机构,并备案保存,以备查阅。
三、结论
为了保证船舶运行的安全和环境保护,船舶管理机构和船员应严格按照法定要求进行压载水处理系统水样化验。
同时,还应加强压载水处理设备的维护和管理,确保设备的正常运行和水质安全。
压力容器产品安全质量监督检验大纲模版
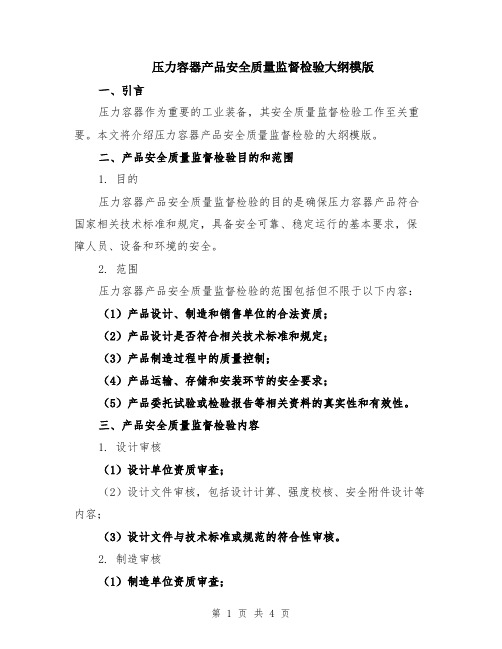
压力容器产品安全质量监督检验大纲模版一、引言压力容器作为重要的工业装备,其安全质量监督检验工作至关重要。
本文将介绍压力容器产品安全质量监督检验的大纲模版。
二、产品安全质量监督检验目的和范围1. 目的压力容器产品安全质量监督检验的目的是确保压力容器产品符合国家相关技术标准和规定,具备安全可靠、稳定运行的基本要求,保障人员、设备和环境的安全。
2. 范围压力容器产品安全质量监督检验的范围包括但不限于以下内容:(1)产品设计、制造和销售单位的合法资质;(2)产品设计是否符合相关技术标准和规定;(3)产品制造过程中的质量控制;(4)产品运输、存储和安装环节的安全要求;(5)产品委托试验或检验报告等相关资料的真实性和有效性。
三、产品安全质量监督检验内容1. 设计审核(1)设计单位资质审查;(2)设计文件审核,包括设计计算、强度校核、安全附件设计等内容;(3)设计文件与技术标准或规范的符合性审核。
2. 制造审核(1)制造单位资质审查;(2)制造过程质量控制文件的审查,包括工艺控制计划、质量控制计划等;(3)制造过程的检查,包括材料采购、装配、焊接等环节的质量控制。
3. 压力试验(1)按照相关技术标准或规定进行压力试验;(2)试验过程的监督和记录。
4. 安全附件检测(1)安全附件资质文件的审核;(2)安全附件的现场检测,包括安全阀、压力表等的检查。
5. 安装环境检查(1)安装现场环境的检查,包括场地平整度、基础设施等;(2)安装单位的施工质量控制文件和过程的审核。
6. 委托试验和检验报告审核(1)委托试验资质文件的审核;(2)委托试验的监督和记录;(3)检验报告的真实性和有效性审核。
四、监督检验方法和要求1. 监督检验方法(1)抽样检验方法:按照抽样检验方案和比例进行抽样;(2)现场检查方法:对压力容器产品的生产制造、销售和使用现场进行检查;(3)验收性试验方法:对压力容器产品进行性能试验和功能验证。
2. 监督检验要求(1)监督检验应依据相关的技术标准、规范和监督检验程序进行;(2)监督检验应督促和指导设计、制造、销售单位全面执行相关要求和规定;(3)监督检验应及时发现和纠正存在的问题,防止不合格产品流向市场;(4)监督检验应及时处理压力容器产品安全事故和投诉,维护消费者合法权益。
水处理通用试验大纲

47.71
1133
65
2000
附注
软水器在进水硬度≤10mmol/L、悬浮物<2mg/L、游离氯<0.1 mg/L、含铁量<0.3mg/L、水温在5~45℃时,出水硬度≤0.03mmol/L。增压泵扬程≮8m。
标记
处数
更改文件号
签名
日期
标记
处数
更改文件号
签名
日期
标记
处数
更改文件号
签名
日期
水处理装置
试验大纲
水处理装置
签字
日期
编制
校对
共4页
共1页
审核
审定
水处理装置
试验大纲
共4页
第2页
为确保水处理装置正常安全可靠地运行,根据QB/HKT3007《水处理装置技术条件》的有关规定,每台水处理装置组装完后,出厂前均要对其制造质量和技术性能通过调试试验进行考核,为此特制定本试验大纲。
一、引用标准:
GB/T 1576-2008工业锅炉水质
JT/T 424-2000船用锅炉水质技术条件
二、水处理装置性能参数:
水处理装置规格参数表。
型号
软水器
增压泵
流量
加药箱
盐液罐
交换能力
工作流量
树脂量
格令
g
gal/min
m3/h
L
≮m3/h
L
L
EFC-60-1
60000
3888
16
3.63
57
4.5
100
180
EFC-90-1
90000
5832
21
4.77
1、软水器均按设定参数运行;
压载水处理装置(BWMS)技术条件

船舶压载水处理装置(BWMS)技术条件(企业标准)(第一版)20XX年X月XX日发布20XX年X月XX日实施拟制:批准:日期:日期:1.内容及适用范围本标准规定了船舶压载水处理系统的设计,制造,检验,性能测试方法及包装,运输,贮存等要求。
本标准适用于船舶压载水处理系统的设计、制造和检验。
压载水管理系统,是基于国际海事组织(IMO)关于《国际船舶压载水及其沉积物控制和管理公约》D-2规定,设计并建造的船舶压载水处理系统,目的在于有效控制压载水中的海洋生物,病毒和其它微生物的转移,防止外来物种的迁徙。
本系统适用于远洋船舶的压载水处理。
本系统也适用于中水回用,工业冷却水系统等的末端处理。
本产品特点是采用纯物理处理工艺,不添加或产生任何化学物质,对船舶无任何腐蚀影响。
设备布置紧凑,占地小,系统全自动控制,操作简单,维护方便等。
2. 引用标准下列标准所包含的条文,通过在本标准中引用而构成本标准的条文。
如其中某个标准被修订,使用本标准应参照相应的最新版执行。
IMO,《2004年国际船舶压载水及其沉积物控制和管理公约》IMO,《船舶压载水管理系统认可导则》(G8)IMO,《船舶压载水管理系统取样导则》(G2)Resolution MEPC, 173(58)中国船级社,《船舶压载水管理计划编制指南》(2006)中国船级社,《电气电子产品型式认可试验指南》(2006)3. 产品组成及型号3.1 产品组成船舶压载水处理系统由全自动自清洗过滤器、紫外杀菌装置和控制系统三个主要部分组成。
3.2 产品命名及型号编制方法防爆型代码额定处理能力(m3/hr)压载水处理装置代码公司代码3.3 产品规格3.3.1 BWMS 设备规格系列3.3.2 自清洗过滤器规格系列3.3.3 UV(紫外)消毒装置规格系列4. 产品技术要求及参数4.2 技术要求:采用机械过滤加中压紫外消毒的工艺对压载水进行有效处理;对于处理后的压载水,按照公约进行压载水管理的排放,达到公约D-2条规定,其中的生物浓度:1).最小尺寸大于或等于50 μm的存活生物少于10个/m3;2).最小尺寸小于50 μm但大于等于10 μm的存活生物少于10个/mL。
压力容器产品安全质量监督检验大纲模版(2篇)
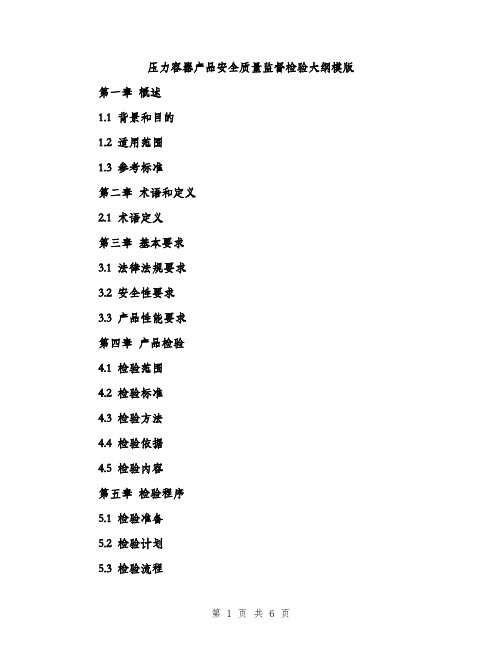
压力容器产品安全质量监督检验大纲模版第一章概述1.1 背景和目的1.2 适用范围1.3 参考标准第二章术语和定义2.1 术语定义第三章基本要求3.1 法律法规要求3.2 安全性要求3.3 产品性能要求第四章产品检验4.1 检验范围4.2 检验标准4.3 检验方法4.4 检验依据4.5 检验内容第五章检验程序5.1 检验准备5.2 检验计划5.3 检验流程5.4 检验记录5.5 检验报告第六章产品追踪与管理6.1 产品追踪要求6.2 产品管理要求6.3 产品维护和保养要求第七章监督检查与整改措施7.1 监督检查要求7.2 整改措施要求7.3 监管机构的职责和权利第八章异常处理和风险评估8.1 异常处理措施8.2 风险评估要求8.3 安全预防措施第九章培训与证书9.1 员工培训要求9.2 证书颁发要求第十章文件和记录10.1 文件编制要求10.2 记录保留要求第十一章实施与审查11.1 实施要求11.2 审查和改进要求附录附录A 相关标准以上是一个压力容器产品安全质量监督检验大纲模板的简单示例,具体内容需要根据实际情况进行补充和修改。
在编写实际的大纲时,需要根据相关法律法规、标准要求和实际情况,确定具体的检验范围、检验标准、检验方法等内容,并结合检验程序、产品追踪与管理、监督检查与整改措施等要求进行完善。
同时,还需要考虑到异常处理和风险评估、培训与证书、文件和记录、实施与审查等方面的要求,以确保压力容器产品的安全性和质量。
压力容器产品安全质量监督检验大纲模版(二)第一部分:导论1.1 检验目的本次压力容器产品安全质量监督检验的目的是为了确保压力容器产品的安全运行和质量稳定,保护人身、财产安全,维护公共利益。
1.2 检验范围本次检验涵盖了压力容器产品的外观检验、机械性能检验、材料及焊接工艺评定等方面。
第二部分:压力容器产品外观检验2.1 检验方法2.1.1 目视检查:对压力容器产品的表面进行目视检查,发现是否存在裂纹、变形、腐蚀等缺陷。
- 1、下载文档前请自行甄别文档内容的完整性,平台不提供额外的编辑、内容补充、找答案等附加服务。
- 2、"仅部分预览"的文档,不可在线预览部分如存在完整性等问题,可反馈申请退款(可完整预览的文档不适用该条件!)。
- 3、如文档侵犯您的权益,请联系客服反馈,我们会尽快为您处理(人工客服工作时间:9:00-18:30)。
船舶压载水处理装置(BWMS)
产品检验大纲
(第一版)
20XX年X月XX日发布20XX年X月XX日实施
拟制:批准:
日期:日期:
1.适用范围
本大纲适用于船舶压载水处理装置的产品检验,确保达到有关技术标准和用户的要求。
2.参考标准和文件
IMO 《船舶压载水管理系统认可导则》(G8)
《压载水处理装置(BWMS)技术条件》
产品图纸
产品调试报告
3. 一般技术要求
3.1 系统设备应符合《船舶压载水处理系统技术条件》要求,设计的图纸和技术文件经公司相关部门审核批准后,方能有效,才能制造。
3.2 原材料包括制作用的钢板、法兰、钢管,应有质量合格证明文件,经供应商进货检验合格后,方能投入生产。
3.3 罐体的强度符合设计及工艺要求,应为吊装制作合适的吊耳。
4. 制作方面的要求
4.1 排板要求:
相邻筒节的纵向焊接接头之间的距离不得小于200mm;盖、底的拼接接头端点与相邻筒节的纵向焊接接头之间的距离不得小于200mm;接管、补强圈、支座、支座垫板、吊耳、吊耳垫板等与筒体焊接接头的边缘距离不得小于50mm。
4.2 坡口要求:坡口加工表面应平滑,不得有裂纹、分层、夹渣等缺陷。
施焊前
须将坡口及其母材两侧表面20毫米范围内的氧化物、油污、熔渣等清除干净。
4.3 筒身组装后,必须保持内壁平齐,壳体上纵、环形焊接接头的最大允许对口
错边量,应符合下表1规定;复合钢板的对口错边量,应不大于钢板的50%,且不大于2mm。
表1
4.4 各接管的中心线应与设计中心线吻合,其最大偏差不得超过接管长度的0.5%,
且不大于3 mm。
各接管的安装位置允许偏差为2 mm,伸出长度允许偏差为
3 mm。
4.5 接管法兰面、人孔法兰面应垂直于接管或圆筒的主轴中心线,安装时应保证
法兰面的水平或垂直,其偏差Δe不得超过法兰外径Do的1%(法兰外径小于100毫米时,按100毫米计),且不大于3mm;法兰螺栓孔应对称分布在筒体主轴中心线的两侧。
4.6 护栏、爬梯和平台的制作所选用的标准,以与客户签订的技术协议为准,如
无特殊要求,按中国标准执行;
5 焊接要求
5.1 冷作工、电焊工必须具有有效的资质证书。
5.2 焊条及焊剂使用前按产品说明书规定的烘焙时间和温度进行烘焙,低氢型焊
条经烘焙后,放入保温桶内,随取随用。
5.3 施焊前,焊工应检查焊件的接头质量和焊区的处理情况;如发现有不符合的
质量要求时,应修正合格后方可施焊。
5.4 为使筒体内表面减少变形,在保证质量的前提下,宜选用小工艺规范、短电
弧和多层多道焊工艺;层间温度不宜过高, 每一层焊道焊完后,应即时检查,清除缺陷后再焊。
5.5 双面焊时,对内表面焊接接头的坡口两侧各100 mm范围内应涂上白垩粉或
其他防溅剂,以防止飞溅物沾污焊件表面。
焊接完毕,焊工应清理焊缝表面的熔渣及两侧的飞溅物。
5.6 焊件的焊缝应平整、光滑、不应有裂纹、气孔、夹渣、未焊透、未熔合等缺
陷。
5.7 焊缝咬边深度不大于0.5mm,咬边连续长度不大于100mm,焊缝两侧咬边
总长不得超过该焊缝长度的10%。
5.8 罐壁的纵向对接接头不得有低于母材表面的缺陷;罐壁的环向对接接头低于
母材表面的凹陷深度,不得大于0.5mm,凹陷的连续长度不得大于100mm,凹陷的总长度,不得大于该焊接接头长度的10%。
5.9 焊接接头的宽度应按坡口宽度两侧各增加1~2mm。
5.10 表面余高e≤1+0.2倍焊接接头宽度,且不大于4mm。
6 防腐、涂装质量要求
6.1 材料预处理:对所采购的板材、型材,先进行表面预处理,表面喷砂或喷丸
处理,喷砂达到Sa2.5级,一般处理后的金属表面应在4小时内进行第一次涂装作业, 所喷涂环氧富锌底漆,漆膜厚度在20~30um。
6.2 工件在制作完毕,检验合格后,进行表面二次处理:碳钢制品防腐油漆前彻
底清除焊渣、飞溅、铁锈、毛刺、锐边打磨倒钝。
6.3 所选用油漆的品牌、颜色、漆膜厚度,以与客户签订的技术协议为准;如无
特殊要求,执行本公司标准,依次喷涂环氧富锌底漆、环氧云铁中间漆、环氧类面漆,干漆膜厚度室外一般为150μm,室内应为125μm,其允许偏差为-25μm。
6.4 除法兰密封面等特殊表面,碳钢材料制作的产品的表面均应油漆。
6.5 涂装表面质量应均匀细致、无明显色差、无流挂、失光、起皱、针孔、气孔、
返锈、裂纹、脱落、赃物粘附、漏涂等、附着力好。
7 清洗机构的制作要求
7.1 清洗机构应符合本公司的相关技术规定,并与过滤器或UV本体相配套,按
规定程序,设计的图纸和技术文件经公司审核合批准,方能有效,才能进行制造。
7.2 用于制作清洗机构的原材料、外购件、外包加工件必须有合格证明文件,经
进货验证合格后方能投入生产。
7.3 焊件的表面应平整光洁,两侧应平整过渡,焊缝不得有裂纹、烧穿、焊瘤及
影响产品的焊接缺陷,焊缝咬边的深度不应超过下表3规定:
表3
7.4 装配要求
7.4.1 清洗机构的驱动轴平面应垂直于UV或过滤器的主轴中心线,安装时应保
证平面的水平或垂直,其偏差Δe不得超过法兰盘外径Do的1%(法兰外径小于100毫米时,按100毫米计),且不大于3mm;法兰螺栓孔应对称分布在主轴中心线的两侧。
7.4.2 相邻的机壳法兰面连接应平整密合,其间隙不应超过0.5毫米,机壳内表
面接头处错位偏差不应超过1.4毫米。
7.4.3 清洗支架部件最大尺寸边缘与机壳间的名义间隙不得超过下表8的规定,
最小间隙不得小于名义间隙的50%。
7.4.4 安装后的清洗轴直线度不应超过下表9规定
8 清洗机构试运转试验要求
8.1 机器运转平稳可靠,紧固件无松动现象。
8.2 工厂试运行时,连续运行时间不应少于2h;电机、减速机工作温度正常,轴
承温升应不大于75º,清洗及机构与机壳之间无异常声响。
8.3 减速器无漏油现象,无异常声响,电器设备、联轴节安全可靠。
8.4 清洗机构运转时,电机所产生噪声≤65dB。
8.5 试运行时,处理能力应达到设计要求。
8.6 电动机电流应平稳,不得大于额定电流。
9 设备的检验方法与规则
9.1 每台UV反应器和自清洗过滤器设备经过最终检验,质量合格后方能出厂,
并附有合格证。
设备装配完毕,装配检验符合要求后,可进行相关试验检验,试验应符合以下要求:
9.2 先进行空负荷运行,后进行负荷运行。
9.3 电机转向正确,电流应平稳,不得大于额定电流,控制箱无异常跳闸现象。
9.4 清洗机构运转时应平稳,不得有冲击、振动和不正常响声。
9.5 负载试验在规定的试验台上进行。
9.6 负载试验时,电动机、减速机、清洗机构三者应匹配,电动机运行平稳;轴承箱工作温度正常,且最高温度不超过75℃,润滑密封无泄漏,无异常声音;清洗机构运转时应平稳,无周期性振动、跳动和不正常响声。
9.7 负载试验的同时,完成相应的功能检测。
9.8 空负荷运行持续时间不少于10分钟;
9.10 负载试验运行持续时间不少于40分钟;
9.11 电机噪声≤85dB。
9.12 试验及检验规则应符合下表2的规定。
表2:现场试验及检验表
9 记录
适用的检验记录表见附件。
检验记录表。