机床热补偿
机床热误差产生原因分析及常用补偿办法

机床热误差产生原因分析及常用补偿办法一、引言在数控机床加工中,机床的稳定性和精度是直接影响加工质量的重要因素。
而机床的热误差是影响机床加工精度的主要因素之一。
本文将分析机床热误差产生的原因,并探讨常用的补偿办法,旨在帮助读者理解和解决机床热误差问题。
二、机床热误差产生原因分析(一)热误差的基本原理机床在加工过程中会受到各种外部环境因素的影响,以及自身零部件因摩擦、压力等衍生出的内部热效应。
这些因素都会导致机床的温度发生变化,从而影响机床的几何尺寸和传动精度,从而产生热误差。
(二)原因一:外部环境的影响机床所处的环境温度、湿度等都会对机床产生影响。
冬季室内温度相对较低,会导致机床传动件温度下降,从而引起机床的几何尺寸发生变化;夏季室内温度相对较高,机床零件温度会上升,进而影响机床的加工精度。
(三)原因二:机床自身结构及零部件的影响机床自身的结构、传动件、润滑系统等都会引起机床的温度变化,从而产生热误差。
机床各部件的热膨胀率不同,使得机床温度的变化导致机床的尺寸和传动精度发生变化;机床的润滑系统也会因温度变化而影响机床的加工精度。
(四)原因三:加工过程本身的热效应三、常用的补偿办法(一)采用温度控制系统采用温度控制系统能够控制机床的温度,从而减小温度对机床的影响。
在机床上安装温度传感器,实时监控机床的温度,并通过控制冷却系统或者加热系统,使机床的温度始终保持在一个稳定的范围内,从而减小机床的热误差。
(二)采用热误差补偿技术热误差补偿技术是一种通过软件或者硬件手段来对机床热误差进行补偿的技术。
通过对机床的温度进行监测,并根据温度变化对机床的坐标进行实时补偿,从而减小热误差对机床加工精度的影响。
(三)改进机床结构及材料改进机床的结构和材料也是减小热误差的重要途径。
采用低热膨胀率的材料来制造机床零部件,或者改进机床的结构,减小零部件的膨胀率,从而减小热误差的产生。
(四)优化加工工艺在加工过程中,通过优化工艺参数,减小加工零部件的摩擦和热效应,也可以减小热误差的产生。
机床热误差产生原因分析及常用补偿办法
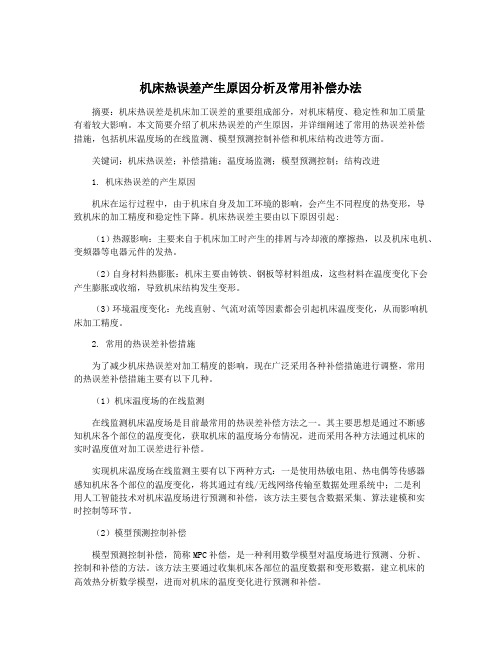
机床热误差产生原因分析及常用补偿办法摘要:机床热误差是机床加工误差的重要组成部分,对机床精度、稳定性和加工质量有着较大影响。
本文简要介绍了机床热误差的产生原因,并详细阐述了常用的热误差补偿措施,包括机床温度场的在线监测、模型预测控制补偿和机床结构改进等方面。
关键词:机床热误差;补偿措施;温度场监测;模型预测控制;结构改进1. 机床热误差的产生原因机床在运行过程中,由于机床自身及加工环境的影响,会产生不同程度的热变形,导致机床的加工精度和稳定性下降。
机床热误差主要由以下原因引起:(1)热源影响:主要来自于机床加工时产生的排屑与冷却液的摩擦热,以及机床电机、变频器等电器元件的发热。
(2)自身材料热膨胀:机床主要由铸铁、钢板等材料组成,这些材料在温度变化下会产生膨胀或收缩,导致机床结构发生变形。
(3)环境温度变化:光线直射、气流对流等因素都会引起机床温度变化,从而影响机床加工精度。
2. 常用的热误差补偿措施为了减少机床热误差对加工精度的影响,现在广泛采用各种补偿措施进行调整,常用的热误差补偿措施主要有以下几种。
(1)机床温度场的在线监测在线监测机床温度场是目前最常用的热误差补偿方法之一。
其主要思想是通过不断感知机床各个部位的温度变化,获取机床的温度场分布情况,进而采用各种方法通过机床的实时温度值对加工误差进行补偿。
实现机床温度场在线监测主要有以下两种方式:一是使用热敏电阻、热电偶等传感器感知机床各个部位的温度变化,将其通过有线/无线网络传输至数据处理系统中;二是利用人工智能技术对机床温度场进行预测和补偿,该方法主要包含数据采集、算法建模和实时控制等环节。
(2)模型预测控制补偿模型预测控制补偿,简称MPC补偿,是一种利用数学模型对温度场进行预测、分析、控制和补偿的方法。
该方法主要通过收集机床各部位的温度数据和变形数据,建立机床的高效热分析数学模型,进而对机床的温度变化进行预测和补偿。
MPC补偿方法能够快速适应机床工作环境的变化,且可以根据用户的需求对模型参数进行调整和优化。
fanuc热位移补偿参数
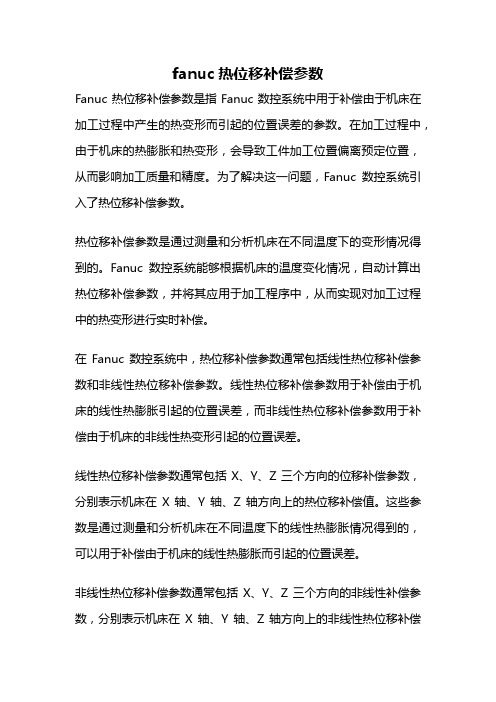
fanuc热位移补偿参数Fanuc热位移补偿参数是指Fanuc数控系统中用于补偿由于机床在加工过程中产生的热变形而引起的位置误差的参数。
在加工过程中,由于机床的热膨胀和热变形,会导致工件加工位置偏离预定位置,从而影响加工质量和精度。
为了解决这一问题,Fanuc数控系统引入了热位移补偿参数。
热位移补偿参数是通过测量和分析机床在不同温度下的变形情况得到的。
Fanuc数控系统能够根据机床的温度变化情况,自动计算出热位移补偿参数,并将其应用于加工程序中,从而实现对加工过程中的热变形进行实时补偿。
在Fanuc数控系统中,热位移补偿参数通常包括线性热位移补偿参数和非线性热位移补偿参数。
线性热位移补偿参数用于补偿由于机床的线性热膨胀引起的位置误差,而非线性热位移补偿参数用于补偿由于机床的非线性热变形引起的位置误差。
线性热位移补偿参数通常包括X、Y、Z三个方向的位移补偿参数,分别表示机床在X轴、Y轴、Z轴方向上的热位移补偿值。
这些参数是通过测量和分析机床在不同温度下的线性热膨胀情况得到的,可以用于补偿由于机床的线性热膨胀而引起的位置误差。
非线性热位移补偿参数通常包括X、Y、Z三个方向的非线性补偿参数,分别表示机床在X轴、Y轴、Z轴方向上的非线性热位移补偿值。
这些参数是通过测量和分析机床在不同温度下的非线性热变形情况得到的,可以用于补偿由于机床的非线性热变形而引起的位置误差。
热位移补偿参数的应用可以有效地提高机床的加工精度和稳定性。
通过对加工过程中的热变形进行实时补偿,可以使机床保持较高的加工精度,并且提高零件的尺寸稳定性。
同时,热位移补偿参数的应用还可以减少因机床热变形引起的零件废品率,提高生产效率和经济效益。
在使用Fanuc数控系统进行加工时,需要合理设置和调整热位移补偿参数,以适应不同的加工条件和要求。
一般来说,可以通过试切试验和实际加工验证来确定最佳的热位移补偿参数,并进行相应的调整和优化。
Fanuc热位移补偿参数是一种用于补偿机床在加工过程中由于热变形引起的位置误差的参数。
机床热误差产生原因分析及常用补偿办法
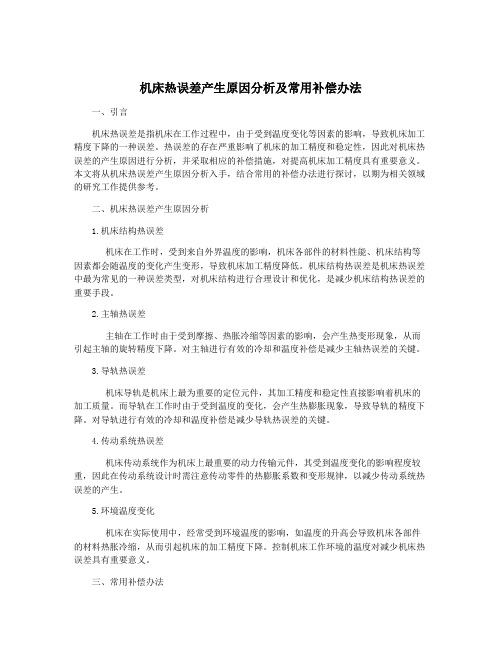
机床热误差产生原因分析及常用补偿办法一、引言机床热误差是指机床在工作过程中,由于受到温度变化等因素的影响,导致机床加工精度下降的一种误差。
热误差的存在严重影响了机床的加工精度和稳定性,因此对机床热误差的产生原因进行分析,并采取相应的补偿措施,对提高机床加工精度具有重要意义。
本文将从机床热误差产生原因分析入手,结合常用的补偿办法进行探讨,以期为相关领域的研究工作提供参考。
二、机床热误差产生原因分析1.机床结构热误差机床在工作时,受到来自外界温度的影响,机床各部件的材料性能、机床结构等因素都会随温度的变化产生变形,导致机床加工精度降低。
机床结构热误差是机床热误差中最为常见的一种误差类型,对机床结构进行合理设计和优化,是减少机床结构热误差的重要手段。
2.主轴热误差主轴在工作时由于受到摩擦、热胀冷缩等因素的影响,会产生热变形现象,从而引起主轴的旋转精度下降。
对主轴进行有效的冷却和温度补偿是减少主轴热误差的关键。
3.导轨热误差机床导轨是机床上最为重要的定位元件,其加工精度和稳定性直接影响着机床的加工质量。
而导轨在工作时由于受到温度的变化,会产生热膨胀现象,导致导轨的精度下降。
对导轨进行有效的冷却和温度补偿是减少导轨热误差的关键。
4.传动系统热误差机床传动系统作为机床上最重要的动力传输元件,其受到温度变化的影响程度较重,因此在传动系统设计时需注意传动零件的热膨胀系数和变形规律,以减少传动系统热误差的产生。
5.环境温度变化机床在实际使用中,经常受到环境温度的影响,如温度的升高会导致机床各部件的材料热胀冷缩,从而引起机床的加工精度下降。
控制机床工作环境的温度对减少机床热误差具有重要意义。
三、常用补偿办法1.热环境调节通过对机床工作环境进行温度调节,以降低环境温度的变化对机床产生的影响,减少热误差的产生。
对机床工作间进行隔热处理,也是一种有效的热环境调节手段。
2.温度补偿技术温度补偿技术是利用传感器实时监测机床各部件的温度变化,并通过控制系统对机床进行温度补偿,以减少热误差的产生。
机床热补偿
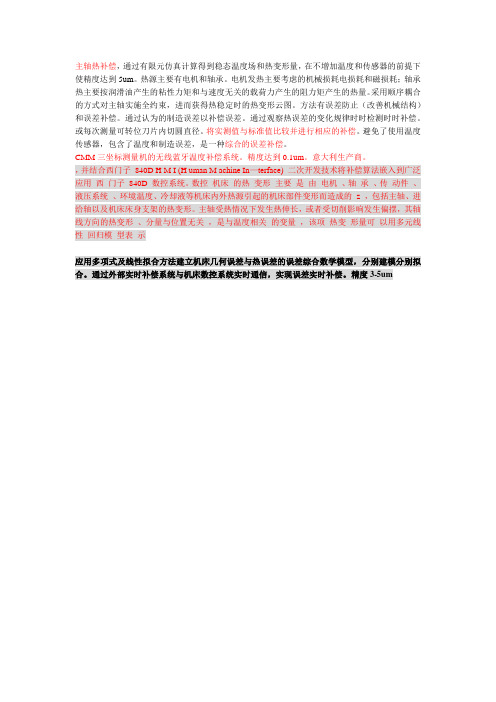
主轴热补偿,通过有限元仿真计算得到稳态温度场和热变形量,在不增加温度和传感器的前提下使精度达到5um。
热源主要有电机和轴承。
电机发热主要考虑的机械损耗电损耗和磁损耗;轴承热主要按润滑油产生的粘性力矩和与速度无关的载荷力产生的阻力矩产生的热量。
采用顺序耦合的方式对主轴实施全约束,进而获得热稳定时的热变形云图。
方法有误差防止(改善机械结构)和误差补偿。
通过认为的制造误差以补偿误差。
通过观察热误差的变化规律时时检测时时补偿。
或每次测量可转位刀片内切圆直径。
将实测值与标准值比较并进行相应的补偿。
避免了使用温度传感器,包含了温度和制造误差,是一种综合的误差补偿。
CMM三坐标测量机的无线蓝牙温度补偿系统。
精度达到0.1um。
意大利生产商。
,并结合西门子840D H M I (H uman M achine In—terface) 二次开发技术将补偿算法嵌入到广泛应用西门子840D 数控系统。
数控机床的热变形主要是由电机、轴承、传动件、液压系统、环境温度、冷却液等机床内外热源引起的机床部件变形而造成的z ,包括主轴、进给轴以及机床床身支架的热变形。
主轴受热情况下发生热伸长,或者受切削影响发生偏摆,其轴线方向的热变形、分量与位置无关,是与温度相关的变量,该项热变形量可以用多元线性回归模型表示
应用多项式及线性拟合方法建立机床几何误差与热误差的误差综合数学模型,分别建模分别拟合。
通过外部实时补偿系统与机床数控系统实时通信,实现误差实时补偿。
精度3-5um。
CNC机床加工中的热变形控制与补偿

CNC机床加工中的热变形控制与补偿引言CNC(Computer Numerical Control)机床是现代制造业中的重要装备,其高精度和高效率使其在各行各业中得到了广泛应用。
然而,由于材料在加工中受到热力影响导致的热变形对加工质量和精度产生了不可忽视的影响。
因此,在CNC机床加工中,热变形的控制与补偿显得尤为重要。
一、热变形的原因CNC机床加工中的热变形主要源于以下几个方面:1. 主轴驱动引起的热变形:主轴的高速旋转产生摩擦热,使主轴温度升高,进而引起机床各部位的热膨胀,导致热变形;2. 切削加工引起的热变形:切削过程中,刀具与工件之间的摩擦产生的热量会使工件局部温度升高,导致热膨胀和变形;3. 内部应力引起的热变形:材料加工后内部应力的释放也会导致热变形。
二、热变形的影响热变形对CNC机床加工的影响主要表现在以下几个方面:1. 加工精度下降:由于机械结构的热膨胀导致零件定位的改变,使加工精度降低;2. 加工质量下降:热变形使得工件表面产生热裂纹、残余应力等缺陷,影响工件的材料性能和使用寿命;3. 加工效率降低:热变形会导致加工过程中频繁调整机床参数,增加生产时间和成本;4. 刀具磨损加剧:由于热变形使刀具与工件接触面积增大,导致刀具磨损加剧,降低切削效率。
三、热变形的控制为了控制CNC机床加工中的热变形,可以采取以下措施:1. 机床结构设计优化:通过对机床结构进行合理的分析和设计,减少热变形的程度;2. 冷却系统改进:加强冷却系统,通过冷却液对主轴和切削区域进行冷却,有效降低温度;3. 热稳定性材料应用:选择具有较低热膨胀系数和较高热导率的材料,减少热变形的可能性;4. 温度监测与控制:通过安装温度传感器,对机床的温度进行监测,及时进行温度调整;5. 热补偿技术应用:通过在机床控制系统中引入热补偿算法,对机床进行实时的热补偿,减小热变形对加工质量的影响。
四、热变形的补偿热变形的补偿是通过对加工过程中发生的热变形进行修正,以保证加工精度和质量。
机床热误差产生原因分析及常用补偿办法

机床热误差产生原因分析及常用补偿办法一、引言现代制造业对产品精度的要求越来越高,但是机床在加工过程中会受到温度影响,导致热误差的产生。
如果不对热误差进行有效的补偿,将会直接影响产品的加工质量,甚至导致生产事故。
研究机床热误差的产生原因以及常用的补偿办法对于保障产品加工精度具有重要意义。
二、机床热误差的产生原因分析1.机床结构热变形机床在工作过程中会受到外部环境温度变化的影响,导致机床结构材料的热膨胀或收缩,从而引起机床的尺寸变化。
特别是大型数控机床,在长时间的加工过程中,由于机床结构的温升会导致机床的各个部分产生不同程度的热变形,从而引起热误差的产生。
2.主轴热变形机床的主轴在高速加工过程中会受到较大的摩擦力和热量的影响,导致主轴温升,从而引起主轴的热变形。
主轴的热变形会直接影响到工件的加工精度,甚至导致产品质量不合格。
3.润滑油温度机床在工作过程中需要进行润滑,而润滑油的温度会直接影响到机床各个零部件的温度。
当润滑油温度升高时,会导致机床各个部件的温度升高,从而引起热误差的产生。
4.外部环境温度5.加工热量6.其他因素除了上述因素之外,机床的热误差还受到机床结构设计、机床材料特性、润滑方式、切削参数等多方面的影响。
以上这些因素的综合作用,导致了机床热误差的产生,因此在实际生产中,需要采取相应的措施对热误差进行有效的补偿。
三、机床热误差的常用补偿办法1.温度补偿温度补偿是对机床热误差进行校正的有效方法之一。
通过在机床的各个部件上设置温度传感器,实时监测机床的温度变化,并且通过控制系统对温度进行实时补偿,从而减小了机床的热误差。
2.结构优化通过对机床的结构进行优化设计,例如采用热稳定性好的材料、合理设置机床的冷却系统、优化机床的传热结构等,可以有效减小机床热误差的产生。
3.控制系统补偿控制系统补偿是通过对机床数控系统的程序进行调整,以达到对热误差的补偿效果。
例如在机床数控系统中设置热误差的补偿参数,通过对加工程序进行调整,从而达到对热误差进行有效补偿的目的。
CNC机床加工中的加工热效应与热误差补偿技术

CNC机床加工中的加工热效应与热误差补偿技术CNC(Computer Numerical Control)机床是一种以计算机控制系统为核心的高精度自动化加工设备。
在CNC机床的加工过程中,由于加工过程中会产生大量的热量,这些热量会对机床和工件产生不可忽视的热效应和热误差。
本文将探讨CNC机床加工中的加工热效应以及热误差的产生原因,并介绍热误差补偿技术在解决这一问题中的应用。
一、加工热效应的原理及影响在CNC机床的加工过程中,由于切削力和摩擦力的作用,机床和工件表面会产生大量的热量。
这些热量会引起机床结构的热膨胀,导致机床刚度的变化,进而影响加工的准确性和精度。
同时,热量也会对工件表面造成变形,从而影响工件的质量。
加工热效应会导致以下问题:1. 机床结构变形:由于机床结构的热膨胀,机床的刚度会发生变化,导致机床的形状和位置发生偏差,进而影响加工的准确性和精度。
2. 工件表面变形:热量会导致工件表面的变形,使得工件的形状和尺寸与设计要求不符。
3. 加工不稳定性:热膨胀还会导致刀具和工件之间的接触状态发生变化,使加工过程中出现振动、共振等问题,影响加工的稳定性和效率。
二、热误差的产生原因热膨胀不均匀是导致热误差产生的主要原因。
在CNC机床的加工过程中,由于不同部位受热不均匀,导致机床结构的热膨胀也不均匀。
这就会引起机床的刚度发生变化,从而导致加工误差的产生。
另外,温度变化也会导致材料性能的变化,例如热导率、热膨胀系数等。
这些变化也会对加工过程产生影响,进一步导致热误差的产生。
三、热误差的补偿技术为了解决CNC机床加工中的热误差问题,热误差补偿技术应运而生。
热误差补偿技术是通过测量加工过程中机床的温度变化,并根据这些温度变化对机床进行实时补偿,从而保证加工的准确性和精度。
热误差补偿技术的主要方法包括以下几种:1. 温度传感器:通过在机床关键部位安装温度传感器,实时监测机床的温度变化。
这些传感器可以将温度信号传输给计算机控制系统,从而实现对机床加工过程中的温度变化进行监测和补偿。
机床热误差产生原因分析及常用补偿办法

机床热误差产生原因分析及常用补偿办法
机床热误差是指由于机床在工作过程中受到温度变化的影响而产生的误差。
热误差的产生原因是多方面的,包括机床本身的结构和材料、环境温度以及工作条件等。
下面将对机床热误差产生的原因进行分析,并介绍常用的补偿办法。
1. 机床本身结构和材料的影响
机床的结构和材料是热误差的主要产生原因之一。
在机床使用过程中,由于机床的各部分受到热胀冷缩的影响,导致机床出现变形,从而产生误差。
此外,机床的各部件材料的热膨胀系数也会对热误差产生影响。
2. 环境温度的影响
3. 工作条件的影响
机床的热误差还与工作条件有关。
例如,在加工高精度零件时,一般要求机床在一定时间内保持稳定温度,以保证加工精度。
此外,加工时机床的负载、转速、冷却方式等也会对热误差产生影响。
1. 温度补偿
温度补偿是最为常见的机床热误差补偿方法。
其原理是在机床上安装感温元件,测量工作环境温度,并通过算法,实现自动补偿。
这种方法适用于需要较高精度的精密加工,如航空航天、国防等行业。
2. 结构优化
通过优化机床的结构和材料,可以尽可能减小机床在工作过程中的变形,从而减小热误差。
例如,采用高强度、低膨胀系数的材料制造机床,并加强机床的刚性等。
3. 温度控制
在工作时控制机床的环境温度,保证机床在稳定的温度环境下工作,可以减小热误差的影响。
例如,控制室内环境温度和湿度,加装空调、加湿器等设备。
总之,尽管机床热误差产生的原因是多方面的,但通过优化机床结构和材料、控制温度和湿度、以及采用温度补偿等方法,可以有效地减小热误差,提高机床加工精度。
机床热误差产生原因分析及常用补偿办法

机床热误差产生原因分析及常用补偿办法机床热误差是指机床在加工过程中由于温度变化引起的尺寸误差。
机床加工过程中会产生大量的热量,而这些热量会导致机床各个部件的温度发生变化,从而引起机床的尺寸变化。
机床热误差主要由以下几个方面的原因引起:1. 机床结构材料的热膨胀:机床主要由铸铁、钢材等金属材料构成,这些材料在加热后会发生热膨胀。
不同材料的热膨胀系数不同,会导致机床各个部件的尺寸发生变化。
2. 加工过程中的摩擦产热:机床在加工过程中,工件与刀具之间会产生摩擦。
摩擦会产生大量的热量,导致机床各个部件的温度升高。
3. 外界环境温度的变化:机床在使用过程中,周围环境的温度会发生变化。
由于机床与环境之间存在热传导,环境温度的变化会影响机床的温度,从而引起尺寸误差。
为了减小机床热误差对加工精度的影响,常用的补偿办法有以下几种:1. 温度补偿:通过测量机床各个部件的温度,对加工程序进行补偿。
可以根据机床的温度曲线,预测机床的热变形,并根据这些变形信息对加工程序进行修正,使加工结果能够达到设计要求。
2. 热稳定化技术:通过采用一定的散热装置,控制机床的温度升高速度,减小机床的热变形。
常用的方法有:增加散热面积、改善散热条件、利用冷却介质对机床进行冷却等。
3. 工艺调整:根据机床加工过程中的热变形规律,调整工艺参数,以减小热误差对加工精度的影响。
通过减小切削刀片与工件之间的摩擦力,降低机床温度升高速度。
4. 采用合适的材料:选择热稳定性好的材料,降低材料的热膨胀系数,减小机床热误差的产生。
机床热误差的产生原因主要是由材料的热膨胀、摩擦产热和外界环境温度的变化等因素引起的。
为了减小机床热误差对加工精度的影响,可以采取温度补偿、热稳定化技术、工艺调整和选择合适的材料等补偿办法。
这些措施可以有效减小机床热误差,提高加工精度。
机床热误差建模及补偿精选全文
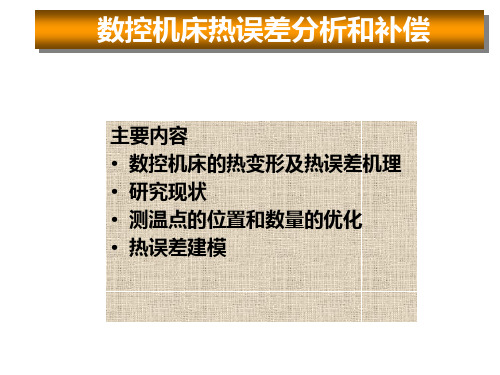
0.9811 4,3,5 0.9915
0.9790 4,6,5 0.9865
0.9789 4,7,5 0.9881
0.9789 4,8,5 0.9900
Rp2
0.9929 0.9937 0.9875 0.9888 0.9912 0.9888
0.9911
0.9858
0.9875
0.9895
• 热误差补偿的数学模型研究 – 多元线性回归模型 – 人工神经网络模型 – 基于多体理论的热误差模型 – 基于主轴转速的热误差模型
3.测温点位置和数量的优化
• 测温点优化的意义 • 关键测温点的确定 • 加工中心关键测温点的确定
3.1 测温点优化的意义
• 前提:机床热误差补偿的温度输入
• 要求:
数控机床热误差分析和补偿
主要内容 • 数控机床的热变形及热误差机理 • 研究现状 • 测温点的位置和数量的优化 • 热误差建模
1.数控机床的热变形及热误差机理
1.1 机床热变形研究的意义 在精密加工过程中由于工艺系统热变形引起的加工 误差占总加工误差的40%-70%,其中机床的热变 形误差占的比重很大,甚至占整个工件加工误差 的50%以上。
4.4 热误差补偿的人工神经网络模型
• 径向基神经网络系统原理
4.4 热误差补偿的人工神经网络模型
• 热误差人工神经网络模型
4.4 热误差补偿的人工神经网络模型
• 隐层(径向基层)
– 确定隐层节点数目
用模糊聚类法把样本分类,从而确定隐层节点数目
– 隐层传递函数参数的确定
• 传递函数(高斯函数)
0.9849 4,7 0.9794
0.9851 4,8 0.9794
Rp2
机床热误差产生原因分析及常用补偿办法

机床热误差产生原因分析及常用补偿办法一、引言随着科学技术的不断发展,机床在工业生产中发挥着越来越重要的作用。
由于各种因素的影响,机床在工作过程中会产生热误差,影响加工精度和稳定性。
研究机床热误差的产生原因,寻求有效的补偿办法,对提高机床加工精度具有重要的意义。
本文将对机床热误差产生原因进行分析,并介绍常用的补偿办法。
二、机床热误差产生原因分析1. 机床结构变形机床在工作过程中,由于受到切削力和惯性力的作用,会导致机床结构的变形。
特别是高速加工时,机床的结构变形更加显著。
这些结构变形会导致机床的位置精度和直线度产生偏差,从而影响加工精度。
2. 主轴热变形在机床工作过程中,主轴由于长时间高速运转,会产生较大的热量。
热量的积聚会引起主轴材料的热膨胀,导致主轴的几何形状发生变化,从而影响主轴的旋转精度。
3. 传动系统的热误差机床的传动系统是由各种机械零部件组成,这些零部件在工作过程中会受到热的影响而发生膨胀或收缩。
尤其是在高速、高精度加工时,由于传动系统的热膨胀影响,会引起工件的位置偏差和形状误差。
4. 环境温度变化周围环境的温度变化也会对机床的热误差产生影响。
特别是在季节转换的时候,温度的变化会导致机床零部件的温度梯度不均匀,进而产生热误差。
5. 冷却液系统的稳定性机床的冷却液系统在工作中起着降温和润滑的作用,稳定性对于机床的热误差具有很大的影响。
如果冷却液系统的供给不均匀或温度波动较大,就会导致机床温度分布不均匀,从而引起热误差。
三、机床热误差补偿办法1. 热补偿热补偿是指通过传感器实时监测机床各部位的温度变化,然后根据监测到的温度数据,通过数学模型计算出热误差的补偿值,再加以修正,以实现对机床热误差的补偿。
通过热补偿的方法可以实现对机床热误差的准确修正,提高了机床的加工精度。
2. 结构改进通过优化设计机床结构,采用高强度、高刚性的材料,改进大梁、床身等部位的结构形式,减少机床在工作过程中的结构变形,以减小热误差的产生。
数控机床加工中材料热变形的补偿方法

数控机床加工中材料热变形的补偿方法在数控机床加工过程中,材料热变形是一个常见的问题,特别是在高温条件下加工难加工材料时。
热变形会对加工精度和产品质量产生负面影响。
为了解决这一问题,工程师和研究人员们开发了多种方法来进行材料热变形的补偿。
一种常用的方法是使用先进的数控机床控制系统。
这种控制系统可以通过对温度变化的监测和分析,以及对相应的补偿算法的应用,来实现对材料热变形的补偿。
该控制系统能够根据工作环境中的温度变化自动调整加工参数,保持加工过程中的稳定性和精度。
通过该方法,可以减少热变形对加工精度的影响,提高产品的质量。
另一种常见的补偿方法是通过加工时对材料进行预热或冷却来控制其温度。
对于易热变形的材料,预热可以提高其热稳定性,减少加工过程中的热变形。
通过将材料加热至一个较高的温度,使其达到临界状态,可以有效降低热变形的程度。
相反,对于难加工材料,采用冷却的方式可以控制其温度,并减少热变形的发生。
这些控温的方法可以在数控机床的加工过程中实现,以确保材料在加工过程中保持适宜的温度,减少热变形的影响。
此外,通过设计合理的刀具和工装夹具,也可以对材料热变形进行补偿。
刀具和工装夹具的设计可以减少加工过程中的热传导,并降低材料的热变形。
例如,通过使用冷却液和降低切削速度,可以减少切削过程中的热传导,从而实现对材料热变形的控制。
此外,采用合理的刀具几何形状和切削参数,也可以降低切削时的热变形。
最后,采用适当的材料也可以对热变形进行补偿。
对于易热变形的材料,可以选择具有较好热稳定性的材料,以减少热变形的程度。
通过对材料的选择和设计,可以使其在高温环境下保持较好的形状稳定性,降低热变形的发生。
这种方法需要在设计和选材阶段进行细致的分析和评估,以确保选择的材料满足加工要求,并具有良好的热稳定性。
综上所述,数控机床加工中材料热变形的补偿方法包括使用先进的数控机床控制系统、通过加热和冷却控制材料的温度、设计合理的刀具和工装夹具以及选择适当的材料等。
机床滚珠丝杠热分析及热补偿讲解
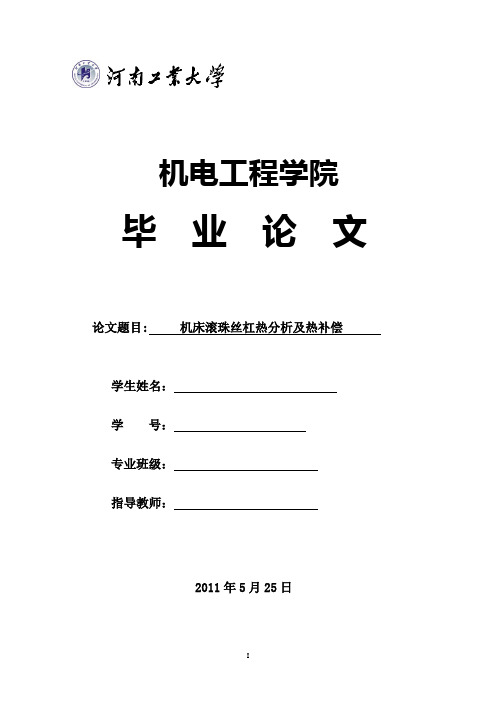
机电工程学院毕业论文论文题目: 机床滚珠丝杠热分析及热补偿学生姓名:学号:专业班级:指导教师:2011年5月25日摘要现代制造技术正日益向高速化、精密化、自动化、智能化方向发展。
数控机床在加工零件运行过程中,由于机床运动部件间的摩擦生热及周围环境热源的影响等诸多因素都将引起机床热变形。
当机床中某些涉及定位、传动的零部件受到热变形影响时,就会造成机床精度下降,甚至无法制造出符合公差要求的产品。
因此,对机床滚珠丝杠进行热特性分析,并根据分析得出的温度场和位移云图总结如何对其进行补偿是很有必要的。
本文以南京工艺装备制造公司生产的DZHQ120型号工作台所配备的滚珠丝杠为热分析研究对象,首先建立实体模型,再用有限元分析方法建立有限元模型,并借助ANSYS热分析模块对滚珠丝杠进行热特性分析,获得仿真结果,为实施热变形补偿提供理论依据。
最后根据热分析结果,提出它的热变形补偿方案。
本文主要工作概括为如下几个方面:1. 通过查阅资料建立滚珠丝杠三维温度场数学模型,以及结合弹性力学、热变形基本方程和有限元理论建立热变形数学模型。
2.根据滚珠丝杠尺寸通过PRO/E建立CAD实体模型,将它导入ANSYS中划分网格,从而建立热特性有限元模型,为CAE分析奠定基础。
3.通过分析计算得出滚珠丝杠上热源以及边界条件相关数据,加载求解后得出温度梯度图和热变形位移图。
4.根据有限元热特性计算结果,通过查看丝杠节点温度和变形情况选取测温点,提出热补偿方案。
关键词:滚珠丝杠热特性有限元 ANSYS 热补偿Title The thermal analysis and thermalcompensation of the screw ballAbstractModern manufacturing techniques are increasingly developing to direction of high-speed, precision, automation and intelligent. CNC machine operation in the processing part, due to the friction heat between moving parts of machine tools and the heat of the surrounding environment and many other factors will cause the machine tool thermal deformation. When the machine parts involved in some of the positioning and the drive are influenced by the thermal deformation, it will result in the decrease of the accuracy of machine,even it can not manufacture the products to meet tolerance requirements.Therefore, to analysis the thermal characteristics of ball screw machine, and it is necessary for concluding how to compensate with the analysis derived from the temperature field and displacement cloud chart. In this paper, the ball screw equipped in DZHQ120 work table which is made by process equipment manufacturing company in Nanjing is as the model for the study of thermal analysis, first is to establish solid model, then establish finite element model by the finite element analysis, and using ANSYS thermal analysis module analysis the thermal characteristic of ball screw, and obtain the simulation results for thermal deformation compensation providing a theoretical basis. Finally, based on thermal analysis results, raising program of thermal deformation compensation. The work of this paper summarized the following aspects:1. Through reading relative information to establish three-dimensional temperature field model of the ball screw, and combine elasticity, the basic equation of thermal deformation and the finite element theory to establish thermal deformation model.2. According to ball screw size to establish CAD solid model by PRO / E, it would mesh when it is imported into ANSYS, so establishing thermal characteristic finite element model, for founding base of the CAE analysis.3. It can be got the relevant data of heat on the ball screw and boundary conditions by analyzing, then it can obtain the heat distortion temperature gradient map and displacement map after loading and solving.4. According to the calculations of thermal characteristic of the finite element, then by viewing temperature and deformation condition of the screw ball nodes to select temperature measurement point, last to raise thermal compensation program.Keywords Ballscrew Thermal characteristics Finite element ANSYS Thermal deformation compensation目录1 绪论 (6)1.1 课题研究目的和意义 (6)1.2 国内外研究现状 (7)1.3 主要研究内容 (8)2 滚珠丝杠热特性有限元建模 (10)2.1 传热基本理论 (10)2.1.1 理论解析 (10)2.1.2 实验方法 (11)2.1.3 比拟(类比)方法 (11)2.1.4 数值计算方法 (11)2.2 温度场计算的有限单元法 (12)2.2.1 傅里叶定律 (12)2.2.2 牛顿冷却公式 (13)2.2.3 导热微分方程及定解条件 (13)2.2.3.1 时间条件 (15)2.2.3.2 边界条件 (15)2.2.4 稳态温度场的有限元法 (17)2.3 热变形的有限元法 (20)2.3.1 热变形有限元法方程的矩阵形式 (20)2.3.2 热变形基本方程 (23)2.3.3 热弹性有限元法 (23)2.4 滚珠丝杠有限元模型的建立 (24)2.4.1 滚珠丝杠三维CAD模型建立 (25)2.4.2 滚珠丝杠向CAE模型的转化 (25)2.4.3 单元类型 (26)2.4.4 材料属性 (27)2.4.5 网格划分 (27)2.5 小结 (28)3 滚珠丝杠温度场分析 (28)3.1 滚珠丝杠边界条件的计算 (29)3.1.1 滚珠丝杠热源及边界条件分析 (29)3.1.1.1 滚动轴承摩擦热的计算 (29)3.1.1.2 滚珠丝杠副摩擦力矩的计算 (32)3.1.2 滚珠丝杠对流边界条件的计算 (32)3.2 滚珠丝杠相关性能参数 (32)3.2.1 滚珠丝杠螺母副介绍 (32)3.2.2 所选滚珠丝杠尺寸参数 (35)3.2.3 材料物理性能参数 (38)3.3 滚珠丝杠热源计算 (38)3.4 温度场的稳态分析 (40)3.5 小结 (42)4 滚珠丝杠热变形分析 (42)4.1 滚珠丝杠热变形分析 (42)4.1.1 滚珠丝杠热变形位移分析过程 (42)4.2 测温点的布置 (44)4.2.1 测温点的布置设计 (44)4.3 小结 (44)5 滚珠丝杠热补偿方案 (45)5.1 热误差补偿原理 (45)5.2 热误差补偿模型建立的理论分析 (46)5.2.1 多元线性回归模型 (47)5.2.2 计算过程 (48)5.3 热误差补偿实现 (49)5.4 小结 (49)结论 (50)致谢 (52)参考文献 (53)1 绪论1.1 课题研究的目的和意义据现有资料显示我们的祖先利用及制造工具最早可追溯到石器时代。
机床热变形及温度补偿
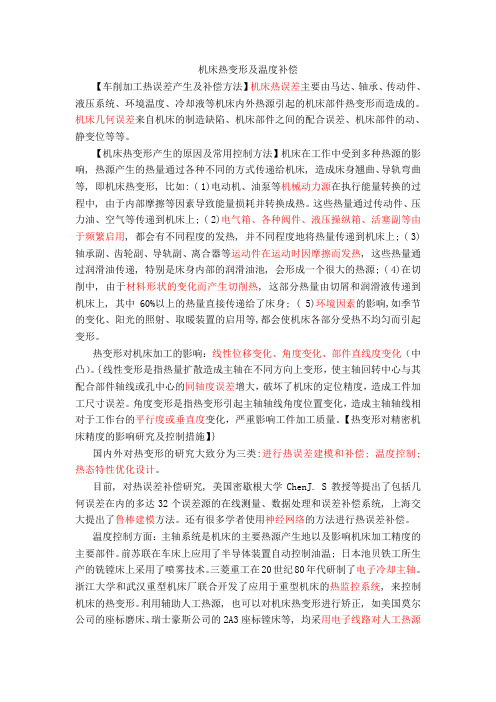
机床热变形及温度补偿【车削加工热误差产生及补偿方法】机床热误差主要由马达、轴承、传动件、液压系统、环境温度、冷却液等机床内外热源引起的机床部件热变形而造成的。
机床几何误差来自机床的制造缺陷、机床部件之间的配合误差、机床部件的动、静变位等等。
【机床热变形产生的原因及常用控制方法】机床在工作中受到多种热源的影响, 热源产生的热量通过各种不同的方式传递给机床, 造成床身翘曲、导轨弯曲等, 即机床热变形, 比如: ( 1)电动机、油泵等机械动力源在执行能量转换的过程中, 由于内部摩擦等因素导致能量损耗并转换成热。
这些热量通过传动件、压力油、空气等传递到机床上; ( 2)电气箱、各种阀件、液压操纵箱、活塞副等由于频繁启用, 都会有不同程度的发热, 并不同程度地将热量传递到机床上; ( 3)轴承副、齿轮副、导轨副、离合器等运动件在运动时因摩擦而发热, 这些热量通过润滑油传递, 特别是床身内部的润滑油池, 会形成一个很大的热源; ( 4)在切削中, 由于材料形状的变化而产生切削热, 这部分热量由切屑和润滑液传递到机床上, 其中60%以上的热量直接传递给了床身; ( 5)环境因素的影响,如季节的变化、阳光的照射、取暖装置的启用等,都会使机床各部分受热不均匀而引起变形。
热变形对机床加工的影响:线性位移变化、角度变化、部件直线度变化(中凸)。
{线性变形是指热量扩散造成主轴在不同方向上变形,使主轴回转中心与其配合部件轴线或孔中心的同轴度误差增大,破坏了机床的定位精度,造成工件加工尺寸误差。
角度变形是指热变形引起主轴轴线角度位置变化,造成主轴轴线相对于工作台的平行度或垂直度变化,严重影响工件加工质量。
【热变形对精密机床精度的影响研究及控制措施】}国内外对热变形的研究大致分为三类:进行热误差建模和补偿; 温度控制; 热态特性优化设计。
目前, 对热误差补偿研究, 美国密歇根大学ChenJ. S教授等提出了包括几何误差在内的多达32个误差源的在线测量、数据处理和误差补偿系统, 上海交大提出了鲁棒建模方法。
数控机床的热稳定性与热误差补偿技术

数控机床的热稳定性与热误差补偿技术随着工业自动化的发展,数控机床在制造业中扮演着重要的角色。
然而,数控机床的热稳定性和热误差一直是制约其精度和稳定性的重要因素。
本文将探讨数控机床的热稳定性问题以及热误差补偿技术的应用。
首先,数控机床的热稳定性是指机床在工作过程中受到热变形和热膨胀等因素的影响,导致工件加工精度下降。
这是因为数控机床在加工过程中会产生大量的热量,而机床的各个部件又具有不同的热膨胀系数。
当机床受热后,不同部件的热膨胀程度不同,从而导致机床的几何形状发生变化,进而影响工件的加工精度。
为了解决数控机床的热稳定性问题,热误差补偿技术应运而生。
热误差补偿技术是通过测量机床在工作过程中的温度分布,然后根据测量结果对机床进行热误差补偿,以提高机床的加工精度和稳定性。
热误差补偿技术主要包括温度传感器的选择和安装、温度测量与分析、热误差模型的建立和热误差补偿算法的设计等方面。
在选择和安装温度传感器时,需要考虑传感器的精度、响应速度、稳定性等因素。
常用的温度传感器有热电偶和热敏电阻等。
热电偶具有响应速度快、测量范围广等优点,但其精度受到环境温度和电磁干扰的影响较大;而热敏电阻则具有精度高、稳定性好等优点,但其响应速度相对较慢。
因此,在选择温度传感器时需要根据具体的应用场景进行综合考虑。
温度测量与分析是热误差补偿技术的重要环节。
通过合理的温度测量与分析,可以获取机床在工作过程中的温度分布情况,为后续的热误差补偿提供准确的数据支持。
在温度测量方面,可以采用红外测温仪、热像仪等非接触式测温设备,以避免对机床结构的影响。
在温度分析方面,可以借助计算机仿真软件对机床的温度分布进行模拟和分析,以揭示机床的热稳定性问题。
热误差模型的建立是热误差补偿技术的核心内容。
热误差模型是通过对机床的温度分布数据进行处理和分析,建立机床的热变形和热膨胀等热误差的数学模型。
热误差模型的建立需要考虑机床的结构特点、材料特性以及温度变化等因素。
机床热补偿
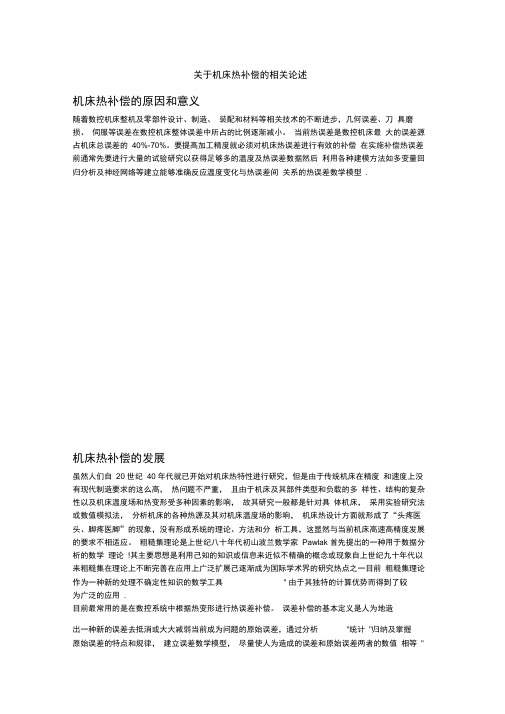
关于机床热补偿的相关论述机床热补偿的原因和意义随着数控机床整机及零部件设计、制造、装配和材料等相关技术的不断进步,几何误差、刀具磨损、伺服等误差在数控机床整体误差中所占的比例逐渐减小。
当前热误差是数控机床最大的误差源占机床总误差的40%-70%。
要提高加工精度就必须对机床热误差进行有效的补偿在实施补偿热误差前通常先要进行大量的试验研究以获得足够多的温度及热误差数据然后利用各种建模方法如多变量回归分析及神经网络等建立能够准确反应温度变化与热误差间关系的热误差数学模型.机床热补偿的发展虽然人们自20 世纪40 年代就已开始对机床热特性进行研究,但是由于传统机床在精度和速度上没有现代制造要求的这么高,热问题不严重,且由于机床及其部件类型和负载的多样性、结构的复杂性以及机床温度场和热变形受多种因素的影响,故其研究一般都是针对具体机床,采用实验研究法或数值模拟法,分析机床的各种热源及其对机床温度场的影响,机床热设计方面就形成了“头疼医头、脚疼医脚”的现象,没有形成系统的理论、方法和分析工具,这显然与当前机床高速高精度发展的要求不相适应。
粗糙集理论是上世纪八十年代初山波兰数学家Pawlak 首先提出的一种用于数据分析的数学理论!其主要思想是利用己知的知识或信息来近似不精确的概念或现象自上世纪九十年代以来粗糙集在理论上不断完善在应用上广泛扩展己逐渐成为国际学术界的研究热点之一目前粗糙集理论作为一种新的处理不确定性知识的数学工具" 由于其独特的计算优势而得到了较为广泛的应用.目前最常用的是在数控系统中根据热变形进行热误差补偿。
误差补偿的基本定义是人为地造出一种新的误差去抵消或大大减弱当前成为问题的原始误差,通过分析"统计"归纳及掌握原始误差的特点和规律,建立误差数学模型,尽量使人为造成的误差和原始误差两者的数值相等"方向相反,从而减少加工误差,提高零件尺寸精度! 最早的误差补偿是通过硬件实现的! 硬件补偿属机械式固定补偿,在机床误差发生变化时要改变补偿量必须重新制作零部件" 校正尺或重新调整补偿机构! 硬件补偿又有不能解决随机性误差" 缺乏柔性的缺点! 软件补偿克服了硬件补偿的许多困难和缺点,把补偿技术推向了一个新的阶段! 热误差补偿法在一定范围内可提高加工精度,有助于降低设计制造成本。
机床热误差产生原因分析及常用补偿办法

机床热误差产生原因分析及常用补偿办法机床热误差是指机床在工作过程中由于热力的影响而产生的误差。
机床在工作过程中会受到加工过程中的大量热源的影响,如主轴传动系统的磨削和加工过程中的摩擦热、电主轴传动系统的电机发热、主轴及导轨系列受到的外部环境温度的影响等。
机床热误差的产生原因主要有以下几个方面:1. 机床结构本身的热膨胀。
机床材料在受热后会发生热膨胀现象,导致机床的尺寸发生变化,进而影响机床的定位精度。
2. 机床工作环境的温度变化。
机床工作环境的温度变化会直接影响机床的工作精度,特别是需要高精度的加工过程中,如果机床工作环境温度变化较大,将会导致机床的加工精度下降。
3. 导轨系列的变形。
导轨系列是机床的重要组成部分,其在机床加工过程中发生的变形会直接影响机床的加工精度。
当导轨系列受到温度的影响时,会发生热变形,导致机床的加工精度下降。
1. 滚动补偿。
机床滚动补偿主要是通过在控制系统中对机床的各个轴进行实时补偿,通过调整机床的位置来补偿热误差的影响。
2. 温度传感器补偿。
在机床的关键位置安装温度传感器,通过测量温度变化来实时监测机床的热变形情况,并通过控制系统对机床进行补偿。
3. 冷却系统。
通过在机床中设置冷却系统,可以有效控制机床工作环境的温度变化,从而减小机床的热误差。
4. 结构改进。
针对机床结构本身的热膨胀问题,可以通过改进结构设计,选用合适的材料,以及采用降低热膨胀系数的方法来减小热误差的影响。
机床热误差的产生对机床的加工精度有着重要的影响,因此需要采取相应的补偿办法来减小热误差的影响。
在使用机床时,需要根据具体情况选择合适的补偿办法,以提高机床的加工精度。
机床热误差产生原因分析及常用补偿办法

机床热误差产生原因分析及常用补偿办法【摘要】本文围绕着机床热误差的产生原因和常用补偿办法展开讨论。
首先介绍了研究背景、研究意义和研究目的,引出了对机床热误差的分析。
在详细分析了机床热误差的产生原因,包括环境温度变化、机床结构刚度和材料特性等方面。
介绍了常用的补偿办法,如温度补偿、结构设计和工艺改进等方法。
最后通过总结和展望,强调了对机床热误差的重视与解决的重要性,为提高加工精度和效率提供了参考。
本文对于了解和应对机床热误差具有一定的指导意义。
【关键词】1. 机床2. 热误差3. 产生原因分析4. 常用补偿办法5. 研究背景6. 研究意义7. 研究目的8. 总结9. 展望1. 引言1.1 研究背景机床热误差是制约数控机床加工精度的重要因素之一,随着机床精度要求的不断提高,对机床热误差的研究也越来越受到重视。
机床在工作过程中,受到外界环境温度的影响以及机械传动元件自身运动和内部热源等因素的影响,都会导致机床温度的变化,进而引起机床热误差的产生。
研究机床热误差的产生原因及补偿办法,有助于提高机床加工精度,保证加工质量,提高生产效率。
在实际生产中,采取有效的补偿措施可以减小机床热误差对加工精度的影响,提高机床的加工稳定性和可靠性。
深入研究机床热误差的产生原因及常用补偿办法具有重要的理论和实践意义,可以为数控加工领域的发展提供技术支撑和参考依据。
1.2 研究意义机床热误差是影响机床加工精度的重要因素之一,研究机床热误差的产生原因及补偿办法具有重要的理论和实际意义。
了解机床热误差产生的原因可以帮助我们更深入地理解机床加工过程中出现的误差,为准确控制机床精度提供理论基础。
通过采取有效的补偿办法来消除或减小机床热误差,可以提高机床加工精度,降低生产成本,提高生产效率,提高产品质量,从而增强企业在市场竞争中的优势。
深入研究机床热误差产生原因和补偿办法具有重要的理论意义和实际应用价值,有助于推动我国机床制造业技术水平的提升,促进制造业的发展和经济的繁荣。
- 1、下载文档前请自行甄别文档内容的完整性,平台不提供额外的编辑、内容补充、找答案等附加服务。
- 2、"仅部分预览"的文档,不可在线预览部分如存在完整性等问题,可反馈申请退款(可完整预览的文档不适用该条件!)。
- 3、如文档侵犯您的权益,请联系客服反馈,我们会尽快为您处理(人工客服工作时间:9:00-18:30)。
关于机床热补偿的相关论述机床热补偿的原因和意义随着数控机床整机及零部件设计、制造、装配和材料等相关技术的不断进步,几何误差、刀具磨损、伺服等误差在数控机床整体误差中所占的比例逐渐减小。
当前热误差是数控机床最大的误差源占机床总误差的40%-70%。
要提高加工精度就必须对机床热误差进行有效的补偿在实施补偿热误差前通常先要进行大量的试验研究以获得足够多的温度及热误差数据然后利用各种建模方法如多变量回归分析及神经网络等建立能够准确反应温度变化与热误差间关系的热误差数学模型.机床热补偿的发展虽然人们自20世纪40年代就已开始对机床热特性进行研究,但是由于传统机床在精度和速度上没有现代制造要求的这么高,热问题不严重,且由于机床及其部件类型和负载的多样性、结构的复杂性以及机床温度场和热变形受多种因素的影响,故其研究一般都是针对具体机床,采用实验研究法或数值模拟法,分析机床的各种热源及其对机床温度场的影响,在机床热设计方面就形成了“头疼医头、脚疼医脚”的现象,没有形成系统的理论、方法和分析工具,这显然与当前机床高速高精度发展的要求不相适应。
粗糙集理论是上世纪八十年代初山波兰数学家Pawlak首先提出的一种用于数据分析的数学理论!其主要思想是利用己知的知识或信息来近似不精确的概念或现象自上世纪九十年代以来粗糙集在理论上不断完善在应用上广泛扩展己逐渐成为国际学术界的研究热点之一目前粗糙集理论作为一种新的处理不确定性知识的数学工具"由于其独特的计算优势而得到了较为广泛的应用.目前最常用的是在数控系统中根据热变形进行热误差补偿。
误差补偿的基本定义是人为地造出一种新的误差去抵消或大大减弱当前成为问题的原始误差,通过分析"统计"归纳及掌握原始误差的特点和规律,建立误差数学模型,尽量使人为造成的误差和原始误差两者的数值相等"方向相反,从而减少加工误差,提高零件尺寸精度!最早的误差补偿是通过硬件实现的!硬件补偿属机械式固定补偿,在机床误差发生变化时要改变补偿量必须重新制作零部件"校正尺或重新调整补偿机构!硬件补偿又有不能解决随机性误差"缺乏柔性的缺点!软件补偿克服了硬件补偿的许多困难和缺点,把补偿技术推向了一个新的阶段!热误差补偿法在一定范围内可提高加工精度,有助于降低设计制造成本。
但是,它是一种被动的和事后补偿的法,其补偿围和有效性具有一定的限制。
当一个机床的热特性比较差的时候,仅靠事后的热补偿是无法满足加工精度要求的。
要提高机床的精度和热性能,必须在设计阶段,从提高机床的热特性、热刚度入手,实现机床的主动热控,从根本上提高机床的热导性。
热量来源机床热误差主要由马达"轴承"传动件"液压系统"环境温度"冷却液等机床内外热源引起的机床部件热变形而造成的!从原理上可以分为如下几方面(1)焦尔热激励线圈和偏置线圈在工作时不可避免地要产生焦尔热:(2)铁损耗交流磁路中存在铁芯损耗,铁芯损耗又分为磁损耗和涡流损耗,这里主要考虑涡流损耗。
(3)摩擦损耗在运动过程中与骨架内壁发生摩擦而产生热量,这部分所占比例较小。
(4)切削热机床热补偿的相关理论、方法及其优缺点在机床热误差补偿技术研究中,如何获得具有良好精确性和鲁棒性的补偿模型是机床热误差补偿研究主要方向。
具体理论方法如下:粗糙理论其优点是具有很强的定性分析能力即不需要预先给定某些特征或属性的描述如统计学中的概率分布模糊集理论中的隶属度或隶属函数而直接从给定问题的描述集合出发通过不可分辨关系和不可分辨类确定给定问题的近似域从而找出问题的内在规律.增量式约简算法和非增量式约简算法[1]用以计算得到机床热补偿误差系统的温度测点优化结果.用非增量式属性约简算法当加入新对象时要重新按照步骤计算一遍而用增量式属性约简算法只需按照步骤做出相应的判断即可得到结果即使计算其计算量也是比较小的相比之下增量式算法的计算量要远远小于非增量式属性约简算法的计算量.但该算法要求新加入的对象与原来的决策表形成的新决策表是协调的.基于热误差神经网络预测模型的机床重点热刚度辨识方法热刚度概念的提出统一了传统力学的刚度概念,对于形成统一设计理念与方法具有重要的指导意义。
依据热刚度理念,机床结构热平衡设计的主要内容是以结构尺寸为设计变量,以弯曲、扭转等热变形的位移量为目标函数,以提高部件和机床整体的热刚度为目标进行优化设计。
热亲和是指与热友好共处的构思。
热亲和”的构思是在尽量减少热量产生的同时接受热,合理利用热。
虽然预测复杂的热变形很困难,但是通过“热变形单纯化”与“温度分布均匀化”的机床构造,进行可预测的规则热位移,并正确地进行热结构平衡补偿控制。
热对称对基础件的热对称设计(结构对称设计和热源分布对称设计)是减小有害热变形的有效措施。
增加局部厚度,改变筋板布置形式可在减轻床身重量的同时改善床身的结构变形。
合理选择立柱结构尺寸参数可提高其热刚度。
热容量平衡设计它是根据机床各部件热容量的不同,对局部热容量大的部件采取一定的措施来控制和减少其温升,使它与热容量较小的部位不致产生较大的温差,尽量达到它们之间的热平衡,从而使机床整体的热变形减少。
合理地设计机床散热板有利于平衡部件之间的温度场。
反变形技术,用反变形来抵消热变形的不良影响是一种简单易行的有效方法。
改善材料变形特性如使用花岗岩、陶瓷、混凝土、玻璃钢等新材料也可以减少热变形。
回归分析方法得到了机床温升与时间的方程,用此方程可近似求出机床部件最大温度、机床温升和热平衡时间等机床热态特性评价指标参数。
将实验方法与有限元分析方法相结合,可有效提高数控机床热特性分析精度。
如有学者应用响应面法构造电主轴系统的对流换热系数与测点温度之间的隐性关系,以实验测得的温度与测点温度计算值的误差作为寻优函数,最终优化各对流换热系数。
经修正后的边界条件能使得到的温度场结果误差大大减小,与实验相结合的机床有限元仿真能使所建立的模型更加精确。
热网络法是一种基于热电比拟原理的集中参数数值分析方法,又称热阻热容法。
相对于有限元法,热网络分析法的优点是物理意义清晰,划分的节点能够反映物理模型。
机床热补偿温度变化与热补偿关系的数学建模方法的本质,并能根据物理模型节点温度的变化率确定其温度变化趋势,其网格划分简单,易被工程技术人员掌握。
采用热网络计算复杂大系统的传热问题,具有简单可行、边界条件易于处理等优点。
尤其是对于包含润滑冷却液、油气混合物、固体结构件等多相传热介质的复杂系统热分析以及薄壁介质问题的处理而言,热网络法要优于有限元法。
运用热网络法可以方便、快捷地实现机床系统的热设计,量化分析改变材料类型、结构尺寸和接触状况对机床温度场的影响。
采用热网络法对机床热关键部件,如轴系统、立柱、轴承等展开热特性研究是机床热特性分析的又一个重要手段。
建模方法如多变量回归分析及神经网络.最小二乘相关1)多元线性回归模型(MRA);2)最小二乘支持向量机(LS.SVM);3)动态自适应加权最小二乘支持矢量机(WLS.SVM);4)在线最小二乘支持向量机(0LS.SVM);5)偏最小二乘回归!神经网络的训练建模(ANN)1)BP 神经网络;2)人体免疫系统 RBF(AIRBF)网络;3)贝叶斯网络;4)最优线性组合神经网络;5)模糊神经网络;6)小脑模型连接控制器(CMAC)神经网络!3.3 系统辨识理论1)灰色系统理论建模;2)灰色系统理论建立了 GM(1,4)及 GM(0,4)模型;3)改进灰色系统的智能预测模型;4)多体系统(MBS)误差建模!3.4 遗传算法(GA)3.5 分段修正系数法3.6 时序分析建模3.7 混合预测模型(综合了时序分析建模和灰色系统理论建模的优点)3.8 平滑自回归模型(AR.MA)3.9 温度变量分组优化建模为了完成机床 - 工件系统的热误差补偿,本研究基于数控编程软件反向补偿原理,设计了数控机床热误差补偿系统,实现刀具的偏移,及刀具与工件之间在运动的逆方向上偏移 1 个大小与误差接近的数值!补偿系统实施方案如图 2 所示!机床热补偿中温度数据采集的对象及其使用的工具和方法机床各种内部热源的发热量及环境温度均随具体的加工情况"时间而变化,同时机床有一定的热容量,其温升必然存在时滞现象,所以根本上说,机床热变形是随时间变化的非恒定现象!研究对象一台HMC800AI立式三轴加工机床.八个测温点左右电机座温度(T1T2)左右轴承座温度(T3T4)环境温度T5左右光栅温度(T6T7)环境温度T5工作台温度T8.使用工具为采用无纸记录仪和激光干涉仪采集.检测时随时更改激光干涉仪的环境参数设置以保证检测准确性从而得到的数据表为了减小机床热变形对加工精度和精度稳定性的影响,需要从设计、制造和使用等方面进行综合分析与优化。
减少机床热误差的主要方法有两种:一是在设计阶段提高机床的热特性二是在运行阶段对机床进行热误差补偿。
实验研究方法一般用红外热像仪、热电偶、激光干涉仪和微位移传感器等精密测量仪器,进行机床空运转综合试验、分离热源试验和磨削试验确定主要热源,并测量各内热源作用下机床各部件的温升、温度场变化、热变形和达到热平衡的时间。
因为机床热误差并不是仅仅和机床某一点的温度变化呈线性对应关系,而是受到各热源的综合作用,并和机床的整体温度变化有关,因此,必须在机床上布置多个测点,并通过数据处理分析找到和热变形相关性好的重要测点,即热关键点如何选择最少的传感器和最佳测量位置,并能最大程度地和机床的热变形误差相对应呢?通常采用两种实验方法来确定机床的热关键点,一是根据实验数据计算热变形量与各测量位置温度变化之间的相关系数,去掉相关系数小的点;二是分析温度变化曲线,剔除提供重复信息和处于不敏感位置的测温点。
机床各发热部件从开始工作到达到热平衡是一个温升过程,热学理论一般将该温升过程用指数函数描述。
对实验数据的处理内容及方法对实验数据处理的主要目的是通过数据的处理找出问题的内在规律进而得到机床热补偿误差系统的温度测点优化结果.1)提取条件属性2)采用了等间隔划分法为了兼顾最终得出的极小决策算法的范化性与预测的准确性在对属性值进行离散化时采用了粗集理论中的局部离散化方法中的一种等间隔划分法3)得到决策表经过预处理之后便得到了粗糙集的模型及决策表4)对上述决策表进行约简得到该决策表的核值从而也可得到极小决策算法通过核值或者极小决策算法得到机床热补偿误差系统的温度测点优化结果热补偿的方法与应用机床热设计的核心目标是最大限度地控制温升,减小热变形,为部件级、组件级和系统级提供良好的热环境,保证它们在一定的热环境下,按预定的要求可靠地工作。
机床热设计一般分为两大类,一类是机床结构的热平衡与优化设计技术,另一类是机床高效冷却技术。