电木成型要求
电木注塑成型新技术--资料

电木注塑成型新技术热固性塑料注塑利用一螺杆或一柱塞把聚合物经一加热过的料筒(120~260°F)以降低粘度,随后注入一加热过的模具中(300—450°F)。
一旦物料充满模具,即对其保压。
此时产生化学交联,使聚合物变硬。
硬的(即固化的)制品趁热即可自模具中顶出,它不能再成型或再熔融。
注塑成型设备有带一用以闭合模具的液压驱动合模装置和一能输送物料的注射装置。
多数热固性塑料都是在颗粒态或片状下使用的,可由重力料斗送入螺杆注射装置。
当加工聚酯整体模塑料(BMC)时,它有如“面包团”,采用一供料活塞将物料压入螺纹槽中。
采用这种工艺方法的加工聚合物是(依其用量大小排列);酚醛塑料、聚酯整体模塑料、三聚氰胺、环氧树脂、脲醛塑料、乙烯基酯聚合物和邻苯二甲酸二烯丙酯(DAP)。
多数热固性塑料都含有大量的填充剂(达 70%重量份),以降低成本或提高其低收缩性能,增加强度或特殊性能。
常用填充剂包括玻璃纤维、矿物纤维、陶土、木纤维和炭黑。
这些填充物可能十分有磨损性,并产生高粘度,它们必须为加工设备所克服。
工艺过程热塑性塑料和热固性塑料在加热时都将降低粘度。
然而,热固性塑料的粘度却随时间和温度而增加,这是因为发生了化学交联反应。
这些作用的综合结果是粘度随时间和温度而呈U型曲线。
在最低粘度区域完成充填模具的操作这是热固性注射模塑的目的,因为此时物料成型为模具形状所需压力是最低的。
这也有助于对聚合物中的纤维损害最低。
注射模塑工艺过程利用一螺杆使物料流经加热过的料筒,料筒则以水或油循环于料筒四周的夹套中。
螺杆可按每种材料的不同类型加以设计,稍加压缩以脱除空气并加热物料获得低粘度。
大多数热固性物料在此处的流动都是相当好的。
使物料进入模具的操作是中止螺杆转动和用液压把螺杆高速推向前,使被塑化的低粘度物料压入模具中。
这种快速流动要求在0.5秒的时间里填满模腔,压力需达到193MPa。
一旦填满膜腔时物料的高速流动产生更大的摩察热以加速化学反应。
电木粉注塑成型工艺流程
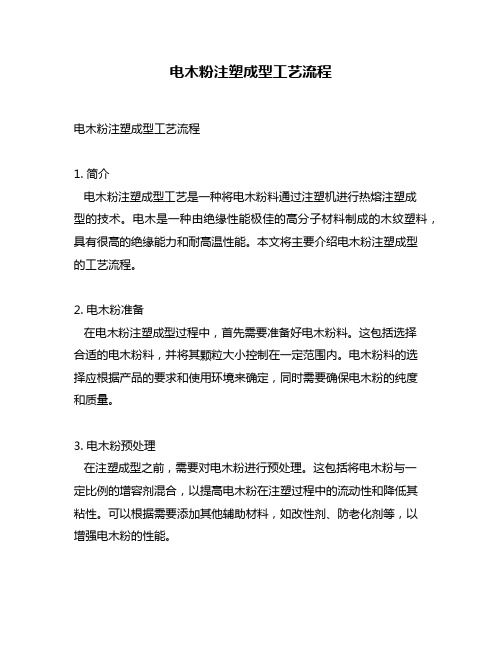
电木粉注塑成型工艺流程电木粉注塑成型工艺流程1. 简介电木粉注塑成型工艺是一种将电木粉料通过注塑机进行热熔注塑成型的技术。
电木是一种由绝缘性能极佳的高分子材料制成的木纹塑料,具有很高的绝缘能力和耐高温性能。
本文将主要介绍电木粉注塑成型的工艺流程。
2. 电木粉准备在电木粉注塑成型过程中,首先需要准备好电木粉料。
这包括选择合适的电木粉料,并将其颗粒大小控制在一定范围内。
电木粉料的选择应根据产品的要求和使用环境来确定,同时需要确保电木粉的纯度和质量。
3. 电木粉预处理在注塑成型之前,需要对电木粉进行预处理。
这包括将电木粉与一定比例的增容剂混合,以提高电木粉在注塑过程中的流动性和降低其粘性。
可以根据需要添加其他辅助材料,如改性剂、防老化剂等,以增强电木粉的性能。
4. 注塑机调试在进行电木粉注塑成型前,需要对注塑机进行调试。
首先是调整注塑机的温度控制系统,确保熔融状态下的电木粉温度适宜。
还需要设置合适的注塑机压力和注射时间,以保证注塑成型的质量和效率。
5. 模具设计和制造根据产品的形状和尺寸要求,需要设计和制造相应的电木粉注塑模具。
这包括确定模具的结构和尺寸,选用合适的模具材料,并进行加工和组装。
模具的设计和制造对于电木粉注塑成型的成品质量和生产效率具有重要影响。
6. 电木粉注塑成型在进行电木粉注塑成型时,首先将预处理好的电木粉加入注塑机的料斗中。
通过注塑机的加热系统,将电木粉加热至熔融状态。
接下来,通过注射系统将熔融的电木粉注入到模具腔中。
待电木粉冷却固化后,打开模具,取出成品。
7. 后处理和检验在注塑成型完成后,需要进行一些后处理和检验工作。
首先是对成品进行修整和打磨,以使其达到预期的表面光滑度和尺寸精度。
会对成品进行一系列的物理性能测试和电性能测试,以验证其绝缘能力和耐高温性能。
8. 结语电木粉注塑成型是一种应用广泛的塑料加工技术,它可以制造出具有良好绝缘性能和高温耐受性的电木制品。
通过精心选择和处理电木粉料,合理调试注塑机参数,设计和制造适用的模具,并进行后处理和检验,可以获得高质量的电木粉注塑成型产品。
电木粉注塑成型工艺
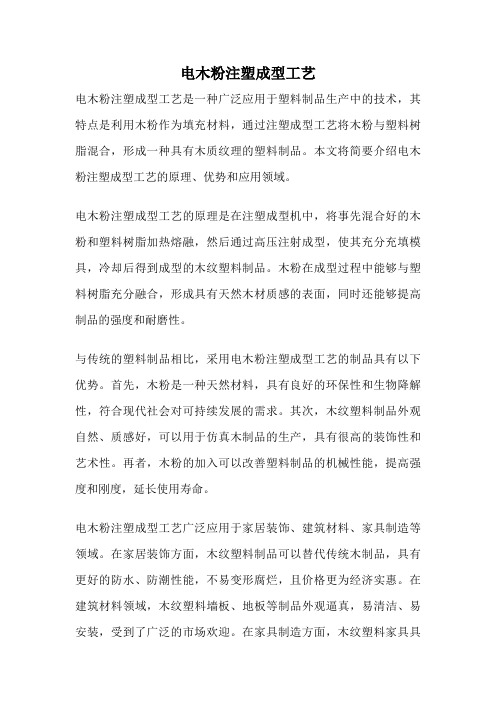
电木粉注塑成型工艺电木粉注塑成型工艺是一种广泛应用于塑料制品生产中的技术,其特点是利用木粉作为填充材料,通过注塑成型工艺将木粉与塑料树脂混合,形成一种具有木质纹理的塑料制品。
本文将简要介绍电木粉注塑成型工艺的原理、优势和应用领域。
电木粉注塑成型工艺的原理是在注塑成型机中,将事先混合好的木粉和塑料树脂加热熔融,然后通过高压注射成型,使其充分充填模具,冷却后得到成型的木纹塑料制品。
木粉在成型过程中能够与塑料树脂充分融合,形成具有天然木材质感的表面,同时还能够提高制品的强度和耐磨性。
与传统的塑料制品相比,采用电木粉注塑成型工艺的制品具有以下优势。
首先,木粉是一种天然材料,具有良好的环保性和生物降解性,符合现代社会对可持续发展的需求。
其次,木纹塑料制品外观自然、质感好,可以用于仿真木制品的生产,具有很高的装饰性和艺术性。
再者,木粉的加入可以改善塑料制品的机械性能,提高强度和刚度,延长使用寿命。
电木粉注塑成型工艺广泛应用于家居装饰、建筑材料、家具制造等领域。
在家居装饰方面,木纹塑料制品可以替代传统木制品,具有更好的防水、防潮性能,不易变形腐烂,且价格更为经济实惠。
在建筑材料领域,木纹塑料墙板、地板等制品外观逼真,易清洁、易安装,受到了广泛的市场欢迎。
在家具制造方面,木纹塑料家具具有防水、耐磨、易清洁的特点,适用于各种户外环境和工程场所。
总的来说,电木粉注塑成型工艺是一种具有广泛应用前景的技术,其独特的优势和特点使其在塑料制品生产领域有着独特的地位。
随着人们对环保、美观、实用性的需求不断增加,相信电木粉注塑成型工艺将在未来得到更广泛的应用和推广。
希望本文的介绍能够让更多的人了解和认识这一技术,为其在各个领域的发展提供有益的参考。
电木材料的国家标准
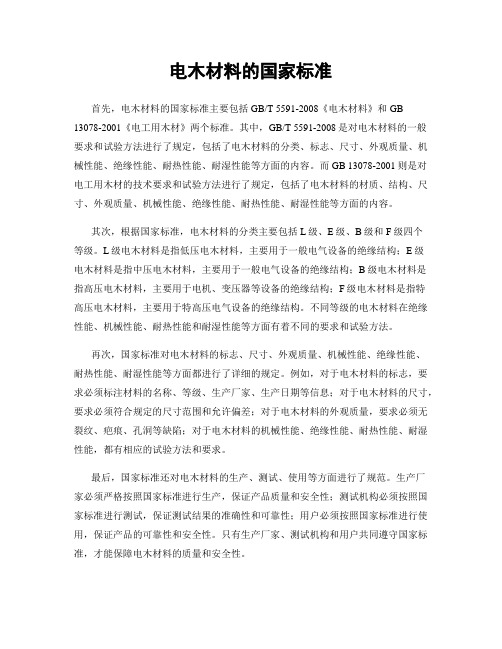
电木材料的国家标准首先,电木材料的国家标准主要包括GB/T 5591-2008《电木材料》和GB 13078-2001《电工用木材》两个标准。
其中,GB/T 5591-2008是对电木材料的一般要求和试验方法进行了规定,包括了电木材料的分类、标志、尺寸、外观质量、机械性能、绝缘性能、耐热性能、耐湿性能等方面的内容。
而GB 13078-2001则是对电工用木材的技术要求和试验方法进行了规定,包括了电木材料的材质、结构、尺寸、外观质量、机械性能、绝缘性能、耐热性能、耐湿性能等方面的内容。
其次,根据国家标准,电木材料的分类主要包括L级、E级、B级和F级四个等级。
L级电木材料是指低压电木材料,主要用于一般电气设备的绝缘结构;E级电木材料是指中压电木材料,主要用于一般电气设备的绝缘结构;B级电木材料是指高压电木材料,主要用于电机、变压器等设备的绝缘结构;F级电木材料是指特高压电木材料,主要用于特高压电气设备的绝缘结构。
不同等级的电木材料在绝缘性能、机械性能、耐热性能和耐湿性能等方面有着不同的要求和试验方法。
再次,国家标准对电木材料的标志、尺寸、外观质量、机械性能、绝缘性能、耐热性能、耐湿性能等方面都进行了详细的规定。
例如,对于电木材料的标志,要求必须标注材料的名称、等级、生产厂家、生产日期等信息;对于电木材料的尺寸,要求必须符合规定的尺寸范围和允许偏差;对于电木材料的外观质量,要求必须无裂纹、疤痕、孔洞等缺陷;对于电木材料的机械性能、绝缘性能、耐热性能、耐湿性能,都有相应的试验方法和要求。
最后,国家标准还对电木材料的生产、测试、使用等方面进行了规范。
生产厂家必须严格按照国家标准进行生产,保证产品质量和安全性;测试机构必须按照国家标准进行测试,保证测试结果的准确性和可靠性;用户必须按照国家标准进行使用,保证产品的可靠性和安全性。
只有生产厂家、测试机构和用户共同遵守国家标准,才能保障电木材料的质量和安全性。
综上所述,电木材料的国家标准对电木材料的生产、测试、使用等方面进行了详细的规范,是保障电木材料质量和安全性的重要依据。
电木注塑生产工艺
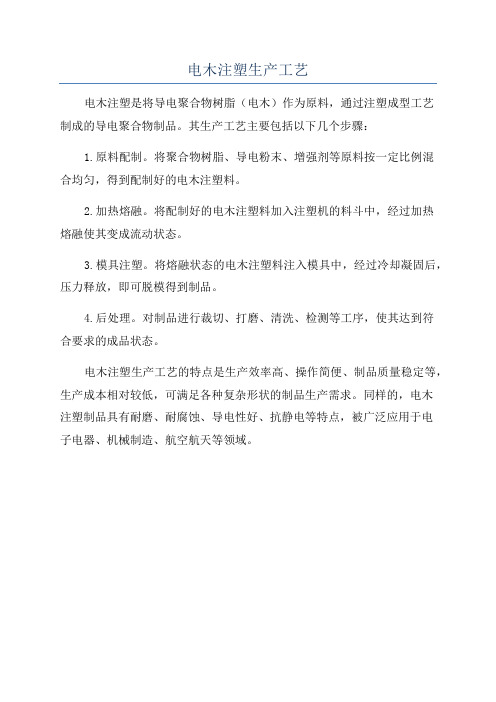
电木注塑生产工艺
电木注塑是将导电聚合物树脂(电木)作为原料,通过注塑成型工艺
制成的导电聚合物制品。
其生产工艺主要包括以下几个步骤:
1.原料配制。
将聚合物树脂、导电粉末、增强剂等原料按一定比例混
合均匀,得到配制好的电木注塑料。
2.加热熔融。
将配制好的电木注塑料加入注塑机的料斗中,经过加热
熔融使其变成流动状态。
3.模具注塑。
将熔融状态的电木注塑料注入模具中,经过冷却凝固后,压力释放,即可脱模得到制品。
4.后处理。
对制品进行裁切、打磨、清洗、检测等工序,使其达到符
合要求的成品状态。
电木注塑生产工艺的特点是生产效率高、操作简便、制品质量稳定等,生产成本相对较低,可满足各种复杂形状的制品生产需求。
同样的,电木
注塑制品具有耐磨、耐腐蚀、导电性好、抗静电等特点,被广泛应用于电
子电器、机械制造、航空航天等领域。
电木的工艺

电木的工艺
电木是一种特殊的木材工艺,是通过将木材浸泡在浸渍剂中进行处理而产生的改性木材。
其工艺步骤如下:
1. 选择合适的木材:通常选择具有较好的耐久性和稳定性的木材,如松木、橡木等。
2. 防腐处理:将木材进行预处理,去除表面皮层和松散部分,然后进行防腐处理,以提高木材的抗虫、防腐性能。
3. 浸渍剂处理:将木材浸泡在浸渍剂中,使其充分吸收和吸附浸渍剂,进而改变木材的结构和性能。
浸渍剂通常采用水性树脂、防腐剂等。
4. 乾燥处理:将浸渍过的木材进行乾燥处理,以使其含水率降低到合适的水平。
乾燥过程可以通过天然晾晒或者人工加热乾燥等方式进行。
5. 表面涂装:对乾燥后的木材进行表面涂装,以提高木材的耐久性、防水性和美观性。
电木经过这些工艺处理后,具有如下特点和优势:
1. 防腐性能好:电木经过防腐处理,能够有效抵抗真菌、昆虫等的侵蚀,延长
木材的使用寿命。
2. 抗水性好:通过浸渍剂处理,电木具有较好的防水性能,可用于湿度较高或水接触较多的场所。
3. 稳定性高:电木经过浸渍处理和乾燥处理,具有较低的含水率,从而减少了木材的体积变化和收缩,提高了木材的稳定性。
4. 保持木材天然美观:电木在保留木材自然纹理和色泽的同时,经过表面涂装,增加了木材的光泽和美观性。
5. 可塑性强:电木经过改性处理,其结构和性能发生改变,具有较好的可塑性,可以进行各种形状和尺寸的加工。
总之,电木工艺可以改善木材的性能和使用寿命,提高其防腐性、抗水性和稳定性,同时保持木材的天然美观。
这使得电木广泛应用于建筑、家具、园林等领域。
电木注塑
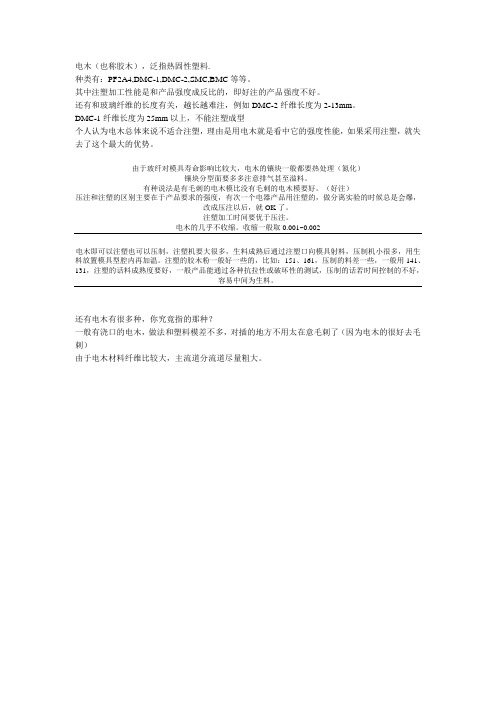
电木(也称胶木),泛指热固性塑料.
种类有:PF2A4,DMC-1,DMC-2,SMC,BMC等等。
其中注塑加工性能是和产品强度成反比的,即好注的产品强度不好。
还有和玻璃纤维的长度有关,越长越难注,例如DMC-2纤维长度为2-13mm。
DMC-1纤维长度为25mm以上,不能注塑成型
个人认为电木总体来说不适合注塑,理由是用电木就是看中它的强度性能,如果采用注塑,就失去了这个最大的优势。
由于玻纤对模具寿命影响比较大,电木的镶块一般都要热处理(氮化)
镶块分型面要多多注意排气甚至溢料。
有种说法是有毛刺的电木模比没有毛刺的电木模要好。
(好注)
压注和注塑的区别主要在于产品要求的强度,有次一个电器产品用注塑的,做分离实验的时候总是会爆,改成压注以后,就OK了。
注塑加工时间要优于压注。
电木的几乎不收缩。
收缩一般取0.001~0.002
电木即可以注塑也可以压制,注塑机要大很多,生料成熟后通过注塑口向模具射料,压制机小很多,用生料放置模具型腔内再加温。
注塑的胶木粉一般好一些的,比如:151、161,压制的料差一些,一般用141、131,注塑的话料成熟度要好,一般产品能通过各种抗拉性或破坏性的测试,压制的话若时间控制的不好,容易中间为生料。
还有电木有很多种,你究竟指的那种?
一般有浇口的电木,做法和塑料模差不多,对插的地方不用太在意毛刺了(因为电木的很好去毛刺)
由于电木材料纤维比较大,主流道分流道尽量粗大。
电木生产工艺
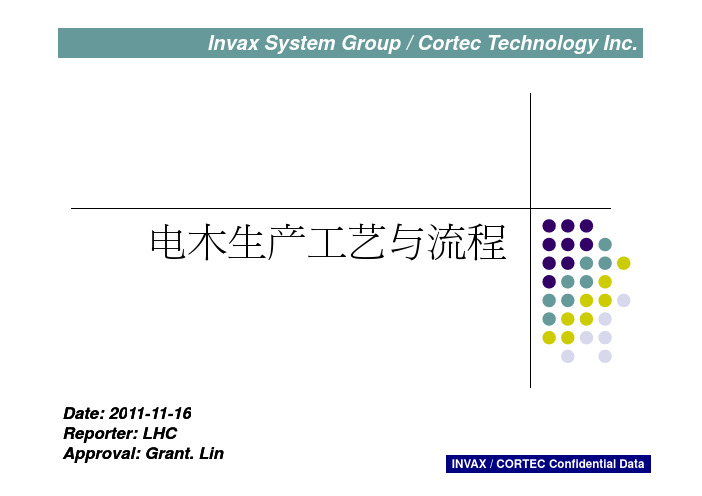
Invax System Group / Cortec Technology Inc.电木生产工艺与流程Date: 20Date: 2011111116Date:201111--11--20Reporter: LHCApproval: Grant. Lin11——1.1材料电木电木的化学名称叫酚醛塑料,是塑料中第一个投入工业生产的品种。
它具有较高的机械强度、良好的绝缘性,耐热、耐腐蚀,因此常用于制造电器材料,如开关、灯头、耳机、电话机壳、仪表壳等,“电木”由此而得名。
它的问世,对工业发展具有重要的意义。
12酚类和醛类化合物在酸性或碱性催化剂作用下,经缩聚反应可制得酚醛1.2电木制法树脂。
将酚醛树脂和锯木粉、滑石粉(填料)、乌洛托品(固化剂),硬脂酸(润滑剂)、颜料等充分混合,并在混炼机中加热混炼,即得电木粉。
将电木粉在模具中加热压制成型后得到热固性酚醛塑料制品。
如下苯酚与甲醛的缩聚反应如下:苯酚与甲醛的缩聚反应电木粉酚醛塑料由于原料来源丰富,合成工艺简单,价格便宜,产品又具有优良的性能,目前仍然是世界上产量最大的热固性塑料。
1.3 电木的特性电木的特性是不吸水、不导电、耐高温、强度高,因为多用在电器上,所以叫做「电木」。
电木是用粉状的酚醛树脂,加进锯木屑、石棉或陶土等混合後,在高温下用模子压出成品,其中酚醛树脂是世界第一个人工合成的树脂。
酚醛塑料(电木):表面坚硬,质脆易碎,敲击有木板声,多为不透明深色(棕色或黑色),在热水中不变软。
是绝缘体,它的主要成分是酚醛树酯。
1.4 电木的优点A.热固性塑料价格低廉,仅为热塑性塑料的1/2~1/5,因其成份中含有40%以上价格低廉的各种填料。
新的成型加艺不断出现和完善,热固性注塑艺在化B.新的成型加工工艺不断出现和完善,热固性注塑工艺在工业化国家已成为热固性塑件“主流生产工艺”,可与热塑性成型工艺处于并驾齐驱的地位。
C.热固性塑料制品的外观有热塑性制品不能相比的光泽。
电木模要求

电木模要求1,其实电木模应该称为胶木模,你们中有部分人认为电木模是用电木粉压出来的,但是现在绝大多数的胶木模是用专用注塑机做产品的。
胶木模与塑料模的主要区别在于胶木模必须做硬模,进胶的浇口比较大,浇口套也比较大,进胶的浇口一般要做镶件,胶木模与塑料模的还有不同在于,胶木模的成型温度很高,所以需要加热,所以模具中应有加热管,而塑料模一般情况下是冷却。
在成型时,胶木模的分型面是有一定的缝隙,很小,要根据产品的大小,质量要求有关,做出的产品在击穿部位都有飞边。
注射用的电木模与塑胶模没什么多大区别,就一点点差异。
1,电木模用料要8407,635,SKD61类的这些材料,要求在高温下有好的品质和硬度。
2,电木模很容易磨损,故要热处理到HRC60左右,也就是说要类似刀具的硬度。
当然了,如果量不大,也可用NAK80类的预硬钢,HRC40左右,也是可行的。
3,特别容易磨损的地方是进胶点,所以进胶点处最好做成镶件,镶白钢或乌钢。
当然乌钢最好了,但乌钢易碎,只能采用线割或磨削加工。
做成可换镶件是为了磨损后好换。
4,因模具要加热,故必须加发热管或发热片。
5。
为了加热时热量不要被注塑机带走,故还需在上下面板上各加一块隔热板,可以是石棉,也可用电木板。
6,因加热模具会热膨胀,故为防止模具卡死,模具的导柱与导套之间比塑胶模配松一点。
7.电木模容易粘模,故都要做成光面,且型腔表面镀硬铬。
铡面是绝对不能有纹的,顶面如是大至平顺面还可以有一些纹类装饰8,电木模用的钢材与塑胶模不一样,模具上下面板上要各覆一层绝热板9.电木属于热固性材料.电木粉在料筒里温度为100度,在浇口处为160度,在模内为180度.电木注塑模具注塑前需加热到160度,所以需加发热管.10.电木模的鋼材與塑膠模差不多一樣﹐要么是8407﹑S136熱處理﹑SKD61熱處理﹐不過最主要的是模具必須拋光到2000#砂紙然后鍍硬鉻﹐防止粘模﹐模具內部必須加加熱棒加熱才能生產產品。
电木工艺技术

电木工艺技术电木工艺技术是一种将木材与电气技术相结合的工艺技术。
通过对木材进行特殊处理,使其具备导电性和阻燃性能,从而可以应用于电气设备和电子产品的制造过程中。
电木工艺技术的出现,不仅提高了产品的绝缘性能,还增加了产品的稳定性和安全性。
电木工艺技术主要包括两个方面的内容:电导木材的制备和电木产品的制造。
电导木材的制备是将天然的木材经过特殊处理,使其具备导电性能。
传统的木材是绝缘材料,它无法传导电流。
而电导木材则通过将导电材料,如金属纳米粉末,注入到木材的细胞壁中,从而使得木材具备导电性。
这样处理后的木材不仅保留了木材的天然美感,而且具备了良好的导电性能,可以用于电气设备的制造。
电木产品的制造是利用电导木材制作出的产品。
通过将电导木材制成板材、管材等形状,并结合传统的电子元器件,制造出各种类型的电气设备和电子产品。
比如,利用电导木材制作的电子设备外壳具备了天然的绝缘和阻燃性,提高了产品的安全性。
同时,电导木材还可以用于制作智能家居产品,如智能灯具和智能插座等,提高了产品的稳定性和使用寿命。
电木工艺技术的应用领域非常广泛。
首先,在电子产品制造方面,电导木材可以替代传统的塑料材料,提高产品的品质和用户体验。
其次,在建筑装饰领域,电导木材可以用于制作防火墙和防火门等防火装置,保障人们的生命财产安全。
此外,电导木材还可以应用于新能源领域,如太阳能电池板的边框和壳体制造等。
尽管电木工艺技术在一定程度上解决了传统木材在电子产品制造中的难题,但是仍然面临一些挑战。
首先,电导木材的生产成本较高,限制了其大规模应用。
其次,电导木材的性能稳定性和耐久性有待进一步提高。
因此,研究人员需要持续努力,不断改进电木工艺技术,推动其在各个领域的应用。
总之,电木工艺技术是一种将木材与电气技术相结合的新兴技术。
它的出现,不仅提高了产品的绝缘性能,还增加了产品的稳定性和安全性。
随着技术的不断改进和完善,相信电木工艺技术将在未来得到更广泛的应用。
电木机及其电木料的注塑工艺
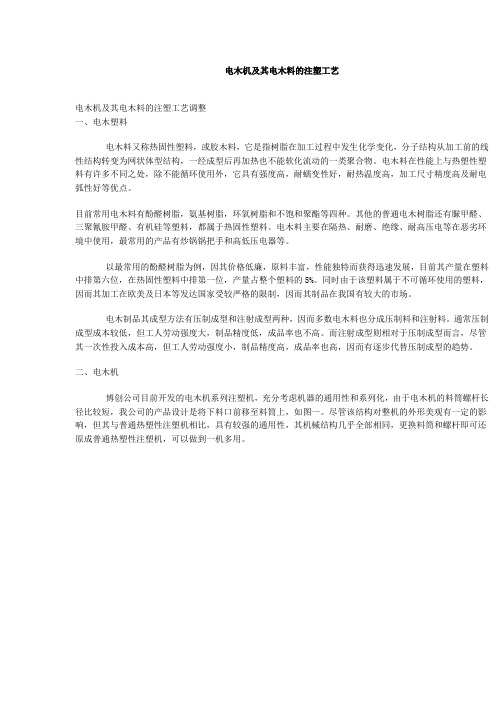
电木机及其电木料的注塑工艺电木机及其电木料的注塑工艺调整一、电木塑料电木料又称热固性塑料,或胶木料,它是指树脂在加工过程中发生化学变化,分子结构从加工前的线性结构转变为网状体型结构,一经成型后再加热也不能软化流动的一类聚合物。
电木料在性能上与热塑性塑料有许多不同之处,除不能循环使用外,它具有强度高,耐蠕变性好,耐热温度高,加工尺寸精度高及耐电弧性好等优点。
目前常用电木料有酚醛树脂,氨基树脂,环氧树脂和不饱和聚酯等四种。
其他的普通电木树脂还有脲甲醛、三聚氰胺甲醛、有机硅等塑料,都属于热固性塑料。
电木料主要在隔热、耐磨、绝缘、耐高压电等在恶劣环境中使用,最常用的产品有炒锅锅把手和高低压电器等。
以最常用的酚醛树脂为例,因其价格低廉,原料丰富,性能独特而获得迅速发展,目前其产量在塑料中排第六位,在热固性塑料中排第一位,产量占整个塑料的5%。
同时由于该塑料属于不可循环使用的塑料,因而其加工在欧美及日本等发达国家受较严格的限制,因而其制品在我国有较大的市场。
电木制品其成型方法有压制成型和注射成型两种,因而多数电木料也分成压制料和注射料。
通常压制成型成本较低,但工人劳动强度大,制品精度低,成品率也不高。
而注射成型则相对于压制成型而言,尽管其一次性投入成本高,但工人劳动强度小,制品精度高,成品率也高,因而有逐步代替压制成型的趋势。
二、电木机博创公司目前开发的电木机系列注塑机,充分考虑机器的通用性和系列化,由于电木机的料筒螺杆长径比较短,我公司的产品设计是将下料口前移至料筒上,如图一。
尽管该结构对整机的外形美观有一定的影响,但其与普通热塑性注塑机相比,具有较强的通用性,其机械结构几乎全部相同,更换料筒和螺杆即可还原成普通热塑性注塑机,可以做到一机多用。
由于酚醛树脂对料筒螺杆有较大的腐蚀性,一般材料制作的螺杆及喷嘴使用寿命较短,所以我公司设计均采用合金螺杆及合金喷嘴,这进一部提高了塑化组件的使用寿命。
此外,由于酚醛树脂对温度控制需较为准确,通常误差不超过±5℃,国内目前普遍采用料筒恒温系统和普通模温机加热两种方式,通常前一种方式成本较低,后一种温度控制较为稳定,但成本相对较高,因为该模温机需要两段温度控制,相当于两台模温机。
电木粉的成型条件介绍
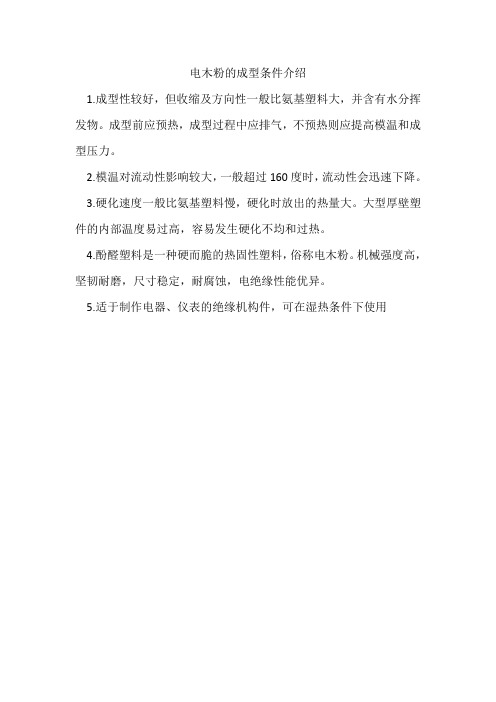
电木粉的成型条件介绍
1.成型性较好,但收缩及方向性一般比氨基塑料大,并含有水分挥发物。
成型前应预热,成型过程中应排气,不预热则应提高模温和成型压力。
2.模温对流动性影响较大,一般超过160度时,流动性会迅速下降。
3.硬化速度一般比氨基塑料慢,硬化时放出的热量大。
大型厚壁塑件的内部温度易过高,容易发生硬化不均和过热。
4.酚醛塑料是一种硬而脆的热固性塑料,俗称电木粉。
机械强度高,坚韧耐磨,尺寸稳定,耐腐蚀,电绝缘性能优异。
5.适于制作电器、仪表的绝缘机构件,可在湿热条件下使用。
电木粉打饼预热成型工艺
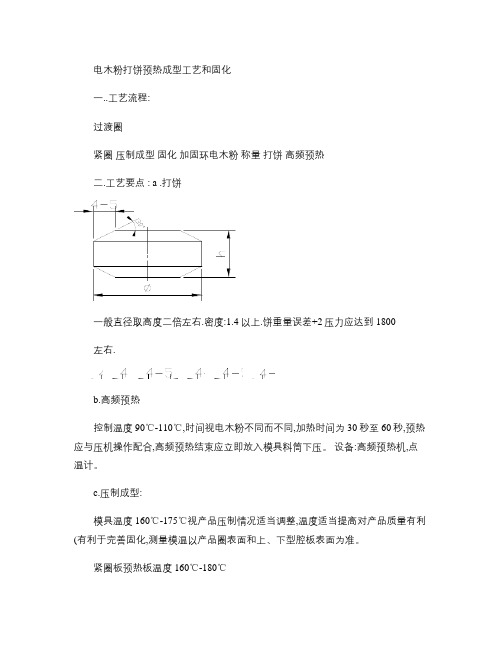
以上“四不”不是指在同一产品采用,在一个产品采用“一个不”“两个不”或“三个不”。“四不”的应用必须要解决所需要的前期加工工艺。采用“四不”成本不一定降下来,良品率可能下降,只是客户需要时组织安排,而且华瑞在组织实施试验工作有的项目进行了一、二年。
下顶缸顶出,开模是顶出产品。
②.三组加热,压头、料筒、产品圈分别控制加热。
③.上模开模时,压头与料筒由拉杆自动分离。
关于华瑞换向器加工中的“四不”说明
所谓“四不”是在换向器加工中的不镗内孔、不铣钩脚、不铣下刻和不车外圆。
不镗内孔:对有衬套换向器讲采用弹簧衬套、粉末冶金衬套或其他材料内孔已加工至成品进行压制后不再对内孔进行加工或进行补充回孔。弹簧衬套采用普通铁丝,进行轧扁、冲台阶绕制后压制,衬套内孔比成品内孔大0.1左右,芯轴尺寸取孔中下偏差直径,公差为0.002,压制后进行金刚石研磨棒回孔。不镗内孔工艺的应用,先决条件是压制模同轴度要求,压制后产品内孔与外圆同轴度应保证小于0.10,否则会影响换向器动平衡和回转精度。对于无衬套的采用固化时塞轴,成本大未采用。
设备:压机、压模、点温计
d.固化曲线(电动工具
50
℃以下
60℃以下开箱
<20℃/
h温度时间
(℃
0 e .压模
(1有下顶缸压机,如无下顶缸,则增加拉钩把产品圈(紧圈开模时拉上来。
开、合模示意图
(2.华瑞所谓的“摩根模”式采用上海一个“摩根厂”设计的模具。其主要特点:
①.产品圈(紧圈不取出,固定在机床上,下型腔部分与顶杆套制成一起,由
c.压制成型:
模具温度160℃-175℃视产品压制情况适当调整,温度适当提高对产品质量有利(有利于完善固化,测量模温以产品圈表面和上、下型腔板表面为准。
电木成型知识
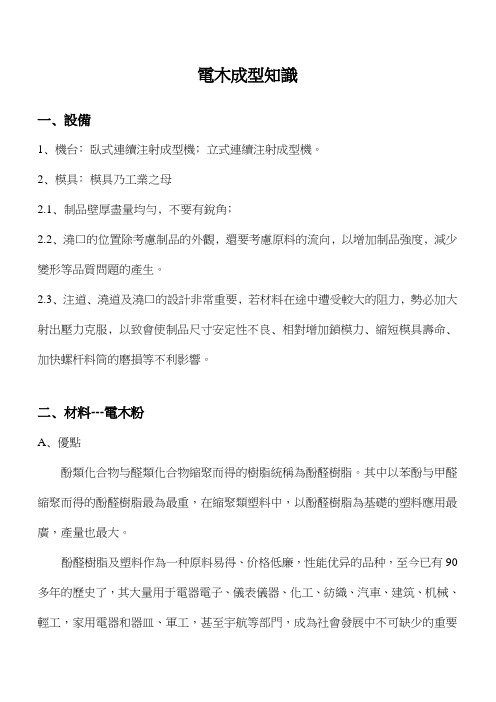
電木成型知識一﹑設備1﹑機台﹕臥式連續注射成型機﹔立式連續注射成型機。
2﹑模具﹕模具乃工業之母2.1﹑制品壁厚盡量均勻﹐不要有銳角﹔2.2﹑澆口的位置除考慮制品的外觀﹐還要考慮原料的流向﹐以增加制品強度﹐減少變形等品質問題的產生。
2.3﹑注道﹑澆道及澆口的設計非常重要﹐若材料在途中遭受較大的阻力﹐勢必加大射出壓力克服﹐以致會使制品尺寸安定性不良﹑相對增加鎖模力﹑縮短模具壽命﹑加快螺杆料筒的磨損等不利影響。
二﹑材料---電木粉A﹑優點酚類化合物与醛類化合物縮聚而得的樹脂統稱為酚醛樹脂。
其中以苯酚与甲醛縮聚而得的酚醛樹脂最為最重,在縮聚類塑料中,以酚醛樹脂為基礎的塑料應用最廣,產量也最大。
酚醛樹脂及塑料作為一种原料易得、价格低廉,性能优异的品种,至今已有90多年的歷史了,其大量用于電器電子、儀表儀器、化工、紡織、汽車、建筑、机械、輕工,家用電器和器皿、軍工,甚至宇航等部門,成為社會發展中不可缺少的重要原料,主要具有以下优點;1、熱固性塑料价格低廉,僅為熱塑性塑料的1/2~1/5,因其成份中含有40%以上价格低廉的各种填料。
2、新的成型加工工藝不斷出現和完善,熱固性注塑工藝在工業化國家已成為熱固性塑件“主流生產工藝”,可与熱塑性成型工藝處于并駕齊驅的地位。
3、熱固性塑料制品的外觀有熱塑性制品不能相比的光澤。
4、在采用酸性樹脂和填料后,机械強度可以達到以塑代木,以塑代鋼的性能,可以滿足各种場合的使用。
5、酚醛塑料制品的鋼性大,具不熔性,可在150℃~200℃的范圍內使用,而且即使在非常的溫度下,它也不軟化變形,制件表面會有燒焦現象。
6、在水潤滑條件下具有較低的摩擦系數(0.01~0.03),很高的PV极限值,可作軸承、齒輪、凸輪等。
特別是在不能使用油潤滑的條件下,顯示它的优越性。
7、熱固性塑料制品具有耐高壓、抗老化、耐燃燒等特點,是熱塑性塑料制品無法比較的,所以熱固性塑料可用來填補熱塑性塑料和金屬制品之間的不足。
电木模具要求
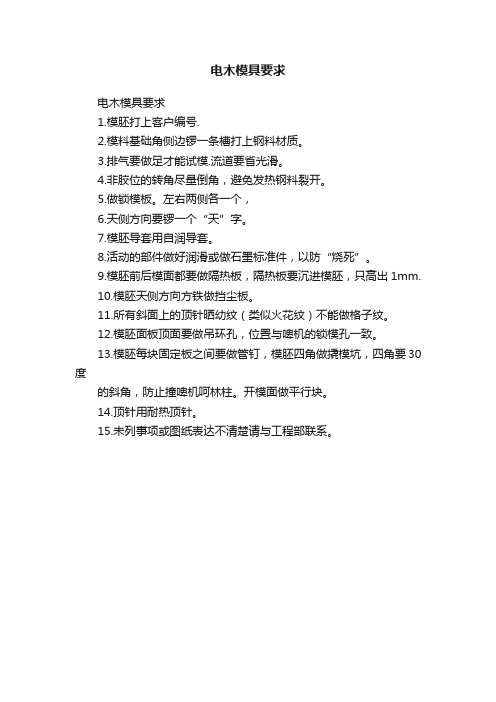
电木模具要求
电木模具要求
1.模胚打上客户编号.
2.模料基础角侧边锣一条槽打上钢料材质。
3.排气要做足才能试模.流道要省光滑。
4.非胶位的转角尽量倒角,避免发热钢料裂开。
5.做锁模板。
左右两侧各一个,
6.天侧方向要锣一个“天”字。
7.模胚导套用自润导套。
8.活动的部件做好润滑或做石墨标准件,以防“烧死”。
9.模胚前后模面都要做隔热板,隔热板要沉进模胚,只高出1mm.
10.模胚天侧方向方铁做挡尘板。
11.所有斜面上的顶针晒幼纹(类似火花纹)不能做格子纹。
12.模胚面板顶面要做吊环孔,位置与啤机的锁模孔一致。
13.模胚每块固定板之间要做管钉,模胚四角做撬模坑,四角要30度
的斜角,防止撞啤机呵林柱。
开模面做平行块。
14.顶针用耐热顶针。
15.未列事项或图纸表达不清楚请与工程部联系。
电木知识汇总资料
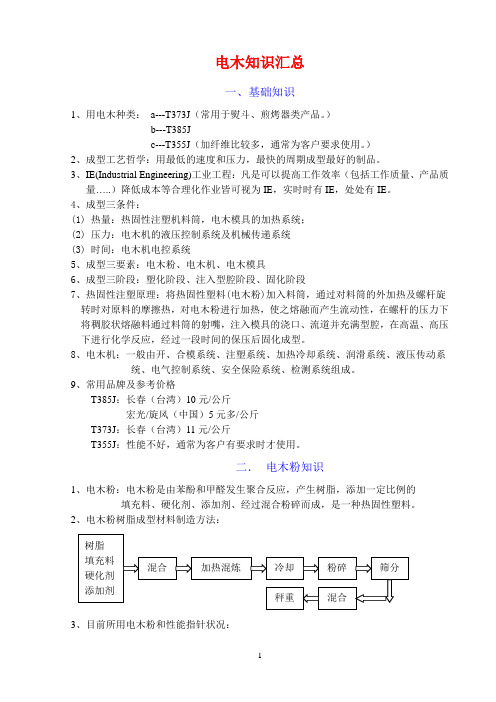
电木知识汇总一、基础知识1、用电木种类:a---T373J(常用于熨斗、煎烤器类产品。
)b---T385Jc---T355J(加纤维比较多,通常为客户要求使用。
)2、成型工艺哲学:用最低的速度和压力,最快的周期成型最好的制品。
3、IE(Industrial Engineering)工业工程:凡是可以提高工作效率(包括工作质量、产品质量…..)降低成本等合理化作业皆可视为IE,实时时有IE,处处有IE。
4、成型三条件:(1) 热量:热固性注塑机料筒,电木模具的加热系统;(2) 压力:电木机的液压控制系统及机械传递系统(3) 时间:电木机电控系统5、成型三要素:电木粉、电木机、电木模具6、成型三阶段:塑化阶段、注入型腔阶段、固化阶段7、热固性注塑原理:将热固性塑料(电木粉)加入料筒,通过对料筒的外加热及螺杆旋转时对原料的摩擦热,对电木粉进行加热,使之熔融而产生流动性,在螺杆的压力下将稠胶状熔融料通过料筒的射嘴,注入模具的浇口、流道并充满型腔,在高温、高压下进行化学反应,经过一段时间的保压后固化成型。
8、电木机:一般由开、合模系统、注塑系统、加热冷却系统、润滑系统、液压传动系统、电气控制系统、安全保险系统、检测系统组成。
9、常用品牌及参考价格T385J:长春(台湾)10元/公斤宏光/旋风(中国)5元多/公斤T373J:长春(台湾)11元/公斤T355J:性能不好,通常为客户有要求时才使用。
二.电木粉知识1、电木粉:电木粉是由苯酚和甲醛发生聚合反应,产生树脂,添加一定比例的填充料、硬化剂、添加剂、经过混合粉碎而成,是一种热固性塑料。
2、电木粉树脂成型材料制造方法:3、目前所用电木粉和性能指针状况:4、电木粉主要组成成份及特性:a、组成成份:酚醛树脂、木粉、硬化剂及添加剂组成,其中添加剂包括固化剂、增塑剂、着色剂、润滑剂、固化促进剂。
b、酚醛树脂:酚类化合物与醛类化合物缩聚而得的树脂(主要为苯酚与乙醛的缩合物)称为酚醛树脂。
电木粉做成的模有哪些要求?
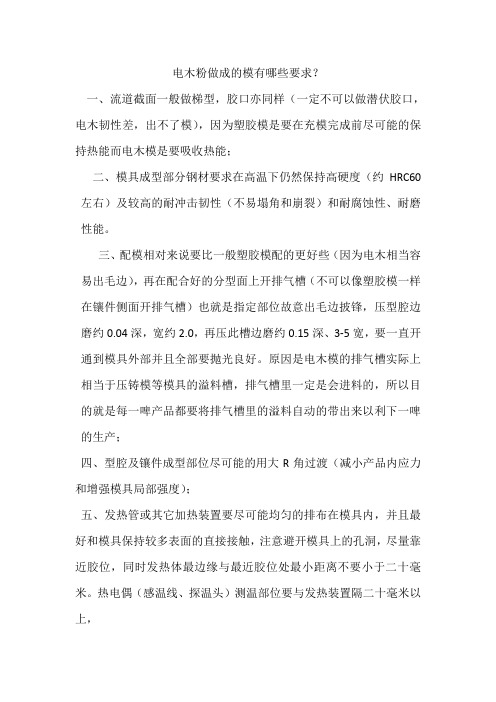
电木粉做成的模有哪些要求?
一、流道截面一般做梯型,胶口亦同样(一定不可以做潜伏胶口,电木韧性差,出不了模),因为塑胶模是要在充模完成前尽可能的保持热能而电木模是要吸收热能;
二、模具成型部分钢材要求在高温下仍然保持高硬度(约HRC60左右)及较高的耐冲击韧性(不易塌角和崩裂)和耐腐蚀性、耐磨性能。
三、配模相对来说要比一般塑胶模配的更好些(因为电木相当容易出毛边),再在配合好的分型面上开排气槽(不可以像塑胶模一样在镶件侧面开排气槽)也就是指定部位故意出毛边披锋,压型腔边磨约0.04深,宽约2.0,再压此槽边磨约0.15深、3-5宽,要一直开通到模具外部并且全部要抛光良好。
原因是电木模的排气槽实际上相当于压铸模等模具的溢料槽,排气槽里一定是会进料的,所以目的就是每一啤产品都要将排气槽里的溢料自动的带出来以利下一啤的生产;
四、型腔及镶件成型部位尽可能的用大R角过渡(减小产品内应力和增强模具局部强度);
五、发热管或其它加热装置要尽可能均匀的排布在模具内,并且最好和模具保持较多表面的直接接触,注意避开模具上的孔洞,尽量靠近胶位,同时发热体最边缘与最近胶位处最小距离不要小于二十毫米。
热电偶(感温线、探温头)测温部位要与发热装置隔二十毫米以上,。
电木加工技巧

电木加工技巧
电木加工是一种现代化的木材加工方式,通过利用电动工具对木材进行切割、雕刻等加工工艺,可实现更加细致精准的木材加工效果。
以下是一些电木加工的技巧和注意事项:
1.选择合适的电动工具:电动锯、电动刨刀、电动雕刻刀等工具是电木加工的关键,因此要根据不同的加工需求选择合适的工具。
2.掌握正确的使用方法:使用电动工具时要注意安全,掌握正确的使用方法,避免危险操作。
3.选用合适的木材:不同的木材适合不同的加工方式,因此要根据需要选择合适的木材,以保证加工效果。
4.加工前进行设计和测量:在开始加工前,要进行设计和测量,确定好加工的形状和尺寸,以避免浪费材料和时间。
5.注意木材的方向性和纹理:木材有方向性和纹理,要根据这些特点进行切割和雕刻,以保持木材的美观和强度。
6.注意细节处理:电木加工时要注意细节处理,如去除毛刺、平整表面、修边等,以保持加工完成品的美观和质量。
7.保持工具的锋利度:电动工具的效果和安全性与工具的锋利度密切相关,因此要保持工具的锋利度,定期进行刃口修整和更换。
总之,电木加工技巧虽然需要一定的技术和经验,但只要掌握了正确的方法和注意事项,就能够实现更加精准和美观的木材加工效果。
- 1 -。
- 1、下载文档前请自行甄别文档内容的完整性,平台不提供额外的编辑、内容补充、找答案等附加服务。
- 2、"仅部分预览"的文档,不可在线预览部分如存在完整性等问题,可反馈申请退款(可完整预览的文档不适用该条件!)。
- 3、如文档侵犯您的权益,请联系客服反馈,我们会尽快为您处理(人工客服工作时间:9:00-18:30)。
电木注塑
注射电木粉的应用工艺,如能按其性能特点控制,对提高制成品率;减轻注射机的工作负荷;减少对螺杆料筒的磨损;缩短成型周期;改善制件外观会有很大的帮助。
合理使用注射电木粉可使一般氮化钢螺杆的使用寿命延长至8—12个月,并改善对模具的损伤。
一、概念:材料必须在适当的温度条件下经螺杆在料筒内充分熔融塑化,使它呈现良好的熔融状态和流动性,使之具备最佳的注射成型工艺。
注射型电木粉具有良好的料筒热稳定性,120℃条件下料筒内可保持10分钟以上,在85—100℃时呈现最佳熔融流动状态,料筒保持时间可达20分钟。
二、建议料筒温度的设置条件:
1.两段控温的料筒:前90—95℃,后
75—85℃;
2.三段控温的料筒:前90—100℃,中80—90℃,后70—80℃;
3.根据配合工艺需要的材料流动性可以用适当提高或降低前料筒温度的办法来
调节。
三、背压的关系:注射电木粉为基本颗粒状,除需温度的配合使之熔融外必须调整背压来完成和完善材料的预塑化,使注射过程中流动性良好,加量均匀稳定。
背压的调节一般可控制在加料松退时喷
嘴有适当的料流出,和注射过程中调节加料稳定,视不同机器大约在3—5㎏/㎝2
四、压力和注射(射料)速度:由于材料充分熔融流动性良好,不需很高的注射压力就能注满型腔,能大幅度降低并减轻机床的负荷,一般在60㎏左右就能满足注
射成型的要求。
射料和喷嘴、流道、浇口,模具快速摩擦会产生过高的温度和加剧
对螺杆料筒的磨损。
特别是单比例阀控制的注射机,高压高速对螺杆模具等的损伤更为严重,所以射料速度不宜太快。
过慢会影响效率,也不可取。
一般视制件大小和浇口形式,控制在每秒10—25克。
以不产生制件硬泡和气体顶住而注不到头
为好。
五、模具温度和保型时间:注射电木粉有较快的成型速度,在170℃条件下就能满足它的成型要求。
保型时间以每毫米14秒并随厚度的增加,时间的增加量递减。
一般制件的每模周期在60—80秒。