自工序完结丰田PPT课件
合集下载
丰田自工序完结推进

(3)自工序完结的事例
400~500台
冲压
焊接
涂装
总装 检验
自工序
自车间
发现
异常 可以马上判断作业状态
冲压切割
检验 发现 不良
原来的作业是啥状态来着??
良品制造的成就感
・需要很长时间才能判断状态是否良好 ⇒可能造成持续制作不良品 ・找不到原因或需要很长时间解决
自工序保证的优势(后工序控制的劣势) ◇作业或设备的问题一目了然 ⇒发生不良时,可以即时判断发生原因。 ◇能立即采取对策 ⇒ 可以迅速进行效果确认。 ◇可以保证完成品状态无法发现的问题。 ⇒可以用直接特性保证,无需代用特性。
・在组装总成件内全部零部件的同时,组装完毕后进行确认,以保证质量。如发动机 分装、安装车窗玻璃、仪表盘、顶棚灯等。
(3)机能完结
・在组装同一机能系统内全部构成件的同时,组装完毕后确认整个机能系统的组装状 态,以保证质量。如安装空调、刹车等。
10/52
4、自工序完结的定义(2)
作为制造质量维持管理活动的一部分,自工序完结有多重含义。
管理
6/52
2、自工序完结的定位(4)
自工序完结是生产现场作业活动的目的,标准作业(即作业的标准化)
则是实现自工序完结的前提。设计部门、工艺部门和制造部门应为生产现场
创造能够实现标准作业的条件。
设计(开发阶段)
这里的部门是按照质量机能划分, 间接的职能部门没有列出。
◆保证质量的产品结构
◆质量标准的明确化
在这里介绍的是生产现场的自工序完结。除有说明外,表单都是 丰田的,在开展自工序完结活动时,需要转化。
3/52
2、自工序完结的定位(1)
实现生产现场的自工序完结 是制造质量管理的首要目标
自工序完结丰田

①良品条件完善率 × ②标准作业
设计・生技・
设计 要件
生技 制造 要件 要件
制造(方法) 全部「○」 判定「○」
物 等
设备・夹具 等
方法
〔判定〕
良品条件 = 遵守率 人
自工序 完结度
①A的要素作业 1 ○ × ○ ×
1.人的工位
② 〃 2○○ ○ ○
③ 〃 3○○ ○ ○
④B的要素作业 4 ○ ○ ×
检查 防止发生防误措施
防止流出防误措施 检查 确认作业
只能生产 良品的工 艺构造
检查
各车间内检查
检查
最终检查
出厂
不将不良品 流到后工序
(2)自工序完结的构造
概略图
自工序完结的推进 ⇒“完善良品条件”和“遵守标准作业”
“良品条件”
(制造良品的条件)
设计要件・生技要件・制造要件
4M 物 设备 方法 人
3 チューブエルボ組付け作業 1)チューブエルボ(φ9)を差し込む 1個 2)チューブエルボ(φ10)を差し込む 1個 3)チューブエルボ(φ8)を差し込む 2個
* ゲージに入らないものは、検討品置場に置く
名称「 501F チューブエルボー組付作業」
上述2点是从哪方面进行改善的? ①:方法(制造要件) ②:物(设计要件) ③:上部板表皮外漏治具上面追加塑料薄片:生技要件
与结果指标的关系
1)自工序完结度(过程指标)
100%
●
90%
80%
70%
60%
50%
2)后工序发现不良(结果指标)
0.02
0.01
0
●
“自工序完结度”(过程指标)与 “后工序发现不良”(结果指标)
丰田精益生产PPT

分销渠道
✓现场决不是狭义意义上的“车间”! ✓现场管理的内涵:制造型企业全部门、全过程管理 ✓现场管理常常被忽略,而过度注重研发、营销、财务 ✓分清企业中的2种人:赚钱的人、花钱的人
客户
管理哲学: “执行”→→“实现”的学问
生产运作管理的误区:功利主义
✓ 体系论:ISO体系、精益生产JIT体系、、、 ✓ 工具论:TQM、TPM、6sigma、SPC、、、、
生命进化的法则——适者生存
龙
世
❖庞大的身躯—能量负担
界
❖低下的神经系统—信息反馈迟钝
的 悲
❖不适应多变的自然环境
哀
:
灭亡
当代海洋霸主、陆地霸主的 生存之道?
企 企业的生命同样遵循这个法则———
业
适应市场环境者生存
的
生
要求:完善的管理体制、快速的市场反 应机制、供应链的协同作战
命
三种经营策略
企业使命及其实践
与
X O 机修工
全员预防保全
理解持续改进对理解日本人和西方人在管 理方法上的差异是非常重要的。
日本的持续改进是过程导向思维方式,而 西方人是创新和结果导向思维方式,创新和持 续改进都是一个企业生存和发展所必需的。
✓不一味追求“突破性”创新(科技突破、管理突破、 最新生产技术)
✓注重“渐变式”“细节性”改进,达到从量变到质 变的飞跃
ムラ:不平衡、不均匀
2023/5/10
等待浪费
搬运浪费
工 8 不良浪费
厂 大 动作浪费
浪 常
见
加工浪费
的 费 库存浪费
地下工厂
企业每生产一件产品就在制 造一份浪费。伴随企业运营中各 业务环节不被察觉或不被重视的 浪费,日本企业管理界将之形象 地比喻为“地下工厂”。
丰田生产方式精品PPT课件

消 利润创造
及 超
除浪
管理的安定 物质的安定
平衡化市生化时产生 生产
费
划
规
S练
P T
教育与训
T
缺
易
自主研流究线会化生产 足
安 质量的安定 产
定
设备的安定
化生 产
人员的样安板定线建设及推广
PS基外础部交流学习 认 知
难全员改外善部活顾动问指导
1、丰田生产方式的基本思想
基本思想:彻底消除浪费
目标
(降低成本、提高利润)
①制作过多的浪费 ③加工的浪费
⑤库存的浪费
⑦等待的浪费
②不良·手修的浪 费
④搬运的浪费
⑥动作的浪费
万恶之源!
如果生产过剩 制作过剩的浪费 将会发生下面这样的浪费
・需要放置场地 ・需要利润 ・产生搬运的浪费 ・材料、零部件先被用掉 ・电、油等能源的浪费 ・发生质量不良时发生不必要的手修作业 ・其他
TPS生产追求的七个“零”目标
地。
成本降了一 些,还可以 赚一些。
我只出100 元,不然
不买!
售价 100元 利润10元
成本 90元
OK!卖了!虽 然只卖100元,
但还是要赚20 元,所以成本
要降到80元。
售价100 元,我买
了!
售价 100元 利润 20元
成本 80元
成本主义
售价=成本+利润 需求>供给
售价主义
利润=售价-成本 需求≤供给
零 7个“
”目标 ☆ 零切换浪费
☆ 零库存
☆ 零浪费
☆ 零不良
☆ 零故障
☆ 零停滞
☆ 零事故
动与働
《丰田精益生产》PPT课件
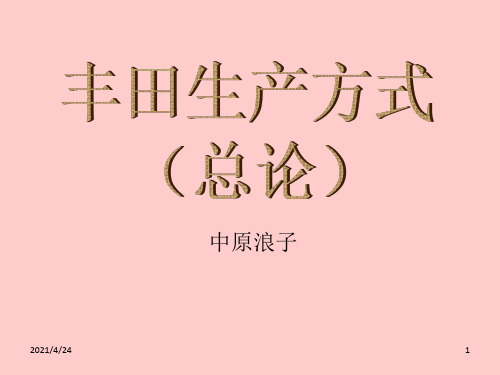
③在这里重要的是,即使生产了超过销售量的产品、提高了效率,这也是
表面上提高了效率,并不能真正的提高效率,因而不能实现实质性的降低成
本202。1/4/24
8
(2)表面的效率和真正效率
需要量(销售量)100个/日
表面的效率
真正的效率
100个/10人→120个/10人
100个/10人→100个/9人
(图1)表面的效率和真正的效率
业。 一般来说,创造附加价值的动作的比率,在总作业量中所占
比率越高,生产效率就越好。
2021/4/24
5
(2)MUDA的种类
MUDA存在和发生在各个环节。将这些MUDA可以分类为(下图)所示的七 种。
No
MUDA的种类
主要内容
1
生产过剩
过早地、过多地生产。→最坏的MUDA
2
空手等待
等待零部件到来、设备运转中的等待。
①表面上提高效率,是指和产品销路毫无关系,在现有人员的情况下增加产 量、提高效率的做法,它仅仅是计算上的效率提高。
②真正的提高效率,指以需要的是少人员和设备生产可销售数量,从而提高 效率的做法,它可以实现实质性的降低成本。
③用(图1)具体说明一下表面的效率和真正的效率。 假设:需要数量(可销售数量)为100个/1日。
所谓"Just-In-Time",是指为了应付需求变化、提高经营效 率,只在需要的时候、生产和搬运所需数量的、需要的产品这 个体系以及这种思想。
Just-In-Time以“平准化”为前提,并有三个基本原则。
(1)Just-In-Time的基本原则
通过贯彻基本原则①“工
序的流畅化”和②“以需要 数量决定T.T”可以缩短生产 的交货周期,在全工序确保生 产的同期化。
PDCA与丰田的工作方法PPT课件

Step 2. 撰写资料纲要
Step 3. 确定版面设计
Step 4. 撰写资料内容
Step 5. 检查校对资料
(1)考虑是“面向谁”的资料 (2)考虑要“如何使用”资料 (3)考虑资料用于“何种用途” (4)考虑要传达“什么内容”
(1)确定纲要的主体 (2)对纲要的主体进行补充的内容 (3)检查纲要整体
1962年导入机能别管理和方针管理
1961
1962
1963
1964
1965
公司管理出现了问题:
• 顾客满意度低
• 跨部门横向联协 恶化
• 企业目标难于实 现
• 职能的管理机制 不明确
丰田制定了第一版 “Global Master Plan”
丰田转换为职能别 组织管理
PROCESSES
Corporate Planning
(1)根据纲要,确定版面设计 (2)确定各文本框的标题
(1)分别将各部分内容填入模板 (2)修饰资料,使内容能够一目了然
(1)最后检查整体的效果
贯穿PDCA工作全过程的沟通
•1.承认 (切不可先否定对方)
•2.倾听(仔细、认真,及时反映)
•3.同感 •4.配合 •5.发问
反复-归纳-督促
发问
限定式发问
当素养有缺陷时
整个三角形就会 向左倾倒
专业能力
基础理论 专业知识 工作经历 工作成果
好的工作
“有一定难度”的工作 “有干劲”的工作 “有成就感”的工作
素养
守则意识 使命意识 人品修养
基本能力
资料制作能力 沟通能力 问题解决能力 团队合作能力
当基本能力有不 足时,整个三角 形就会向右倾倒
什么是好的工作
Step 3. 确定版面设计
Step 4. 撰写资料内容
Step 5. 检查校对资料
(1)考虑是“面向谁”的资料 (2)考虑要“如何使用”资料 (3)考虑资料用于“何种用途” (4)考虑要传达“什么内容”
(1)确定纲要的主体 (2)对纲要的主体进行补充的内容 (3)检查纲要整体
1962年导入机能别管理和方针管理
1961
1962
1963
1964
1965
公司管理出现了问题:
• 顾客满意度低
• 跨部门横向联协 恶化
• 企业目标难于实 现
• 职能的管理机制 不明确
丰田制定了第一版 “Global Master Plan”
丰田转换为职能别 组织管理
PROCESSES
Corporate Planning
(1)根据纲要,确定版面设计 (2)确定各文本框的标题
(1)分别将各部分内容填入模板 (2)修饰资料,使内容能够一目了然
(1)最后检查整体的效果
贯穿PDCA工作全过程的沟通
•1.承认 (切不可先否定对方)
•2.倾听(仔细、认真,及时反映)
•3.同感 •4.配合 •5.发问
反复-归纳-督促
发问
限定式发问
当素养有缺陷时
整个三角形就会 向左倾倒
专业能力
基础理论 专业知识 工作经历 工作成果
好的工作
“有一定难度”的工作 “有干劲”的工作 “有成就感”的工作
素养
守则意识 使命意识 人品修养
基本能力
资料制作能力 沟通能力 问题解决能力 团队合作能力
当基本能力有不 足时,整个三角 形就会向右倾倒
什么是好的工作
IETPS丰田生产方式自働化PPT课件

• 现场主义解决问题的关键就在于如何抓住现场,迅速采取行动。有时候虽然专家赶来了,但是犯人已经跑了 (不合格产品的产生原因不见了),再去查找原因是很困难的。
• 如果能够经常同与不合格产品接触的作业人员养成用5个为什么来思考的习惯,就能够把问题逐个解决,不 合格产品就会无限接近为零。
第9页/共39页
在现场解决问题的思考办法
• 像丰田这样立刻停止生产线并加以改善,可以向顾客保证质量。很多没有停止生产线的企业,就是因为没有 培育起一种停止了生产线后能迅速进行改善的体质,从而在改善和继续运转机器的时候,产生了大量的浪费。
第4页/共39页
可以实现自働化的改善体质
• 通常,5W1H是指(什么时候,什么地方、谁、干什么、为什么、怎么 样)。不过,在丰田就是通过反复问“为什么”来查找问题发生的真正原 因。
规格
不合格产品
不合格产品产生 是因为产品质量 不一致。
第10页/共39页
在现场解决问题的思考办法(续)
第 为什么产品的 一 质量会不一致 阶 段
观察现场的着眼点
观察不合格产品 • 以平淡的心情观察(舍掉先入为主
找
出
观察现场
的观点) • 拥有强烈的解决问题的意识
原
•把握作业异常
因
观察步骤
(正常和异常)(倾向和周期性)
那是因为 4M+1E不一致
• 观察各道工序,找出问题点。 •通过排除法缩小为题点范围。 •在缩小了的问题点发生的场所,进一步细致观察。
第 二 通过观察现场不 阶 能找出原因时 段
有可能降低精确度 因为有误差
• 问有经验的人(前辈、作业人员等) • 分析不一致的产品(数据等) • 缩小问题点范围(利用帕拉图)
• 如果能够经常同与不合格产品接触的作业人员养成用5个为什么来思考的习惯,就能够把问题逐个解决,不 合格产品就会无限接近为零。
第9页/共39页
在现场解决问题的思考办法
• 像丰田这样立刻停止生产线并加以改善,可以向顾客保证质量。很多没有停止生产线的企业,就是因为没有 培育起一种停止了生产线后能迅速进行改善的体质,从而在改善和继续运转机器的时候,产生了大量的浪费。
第4页/共39页
可以实现自働化的改善体质
• 通常,5W1H是指(什么时候,什么地方、谁、干什么、为什么、怎么 样)。不过,在丰田就是通过反复问“为什么”来查找问题发生的真正原 因。
规格
不合格产品
不合格产品产生 是因为产品质量 不一致。
第10页/共39页
在现场解决问题的思考办法(续)
第 为什么产品的 一 质量会不一致 阶 段
观察现场的着眼点
观察不合格产品 • 以平淡的心情观察(舍掉先入为主
找
出
观察现场
的观点) • 拥有强烈的解决问题的意识
原
•把握作业异常
因
观察步骤
(正常和异常)(倾向和周期性)
那是因为 4M+1E不一致
• 观察各道工序,找出问题点。 •通过排除法缩小为题点范围。 •在缩小了的问题点发生的场所,进一步细致观察。
第 二 通过观察现场不 阶 能找出原因时 段
有可能降低精确度 因为有误差
• 问有经验的人(前辈、作业人员等) • 分析不一致的产品(数据等) • 缩小问题点范围(利用帕拉图)
精益生产(TPS丰田生产方式)ppt课件

1950年 3月日本全厂罢工, 1950年 4 .11- 6.10 TOYOTA自动车劳动争议
- 因日銀나고야支店的经济条件充足得到的资金
① 把销售公司从TOYOTA自动车工业里分离独立起来.- 销售部门分离
② TOYOTA自动车只生产销售公司能销售出的台数.- 在月1,500台里4吨BM型卡车扩散减少到940 台.
精选课件
23
1. TOYOTA的成本MIND
Ⅱ. 得出利益的生产方式
销售额 = 成本 + 利益 : 只有成本主义的话是不能生存下去的.
利益 = 销售值 – 成本 : 这思考方式是基本. 一定,客户决定
为了挣钱(为了扩大利益) 只有节减成本的方法.
为了这个有必要彻底排除浪费
以下3种方法中哪方法最有现实性?
Ⅰ. TPS的概要
文书化的技能 • 确保跟继承一样的方针的连续性 • 仅TOYOTA所有的经营思想的连续性,强调给营业员的构造 • 公式规则体制的,得意的保存方法
精选课件
11
Ⅰ. TPS的概要
TOYOTA Soichiro的遗传子
减少
TOYOTA Eiji的遗传子
减少
TOYOTA 退三的遗传子
改定•制定 统治
1938年在擧母工厂的准公式上TOYOTA喜一郞强调 “JUST IN TIME”
生产方式是 “每日需要的 在需要时 只制作需要的那么量”
投入TOYOTA式的流水作业
精选课件
6
Ⅰ. TPS的概要
什么是TPS (Toyota Production System)
- TOYOTA的生产SYSTEM是,把生产能力效率性的活动的生产SYSTEM. - TOYOTA生产SYSTEM是将人力和设备等的生产能力,按需要的量维持也把效率极大化的把
3.自工序完结ppt课件

· 即使很有经验也要
经常练习基本功:
先用不同的力度打出 小点凹陷,然后按要 求摸出点的深浅不同
27
【案例】
28
五、生产过程中的异常管理
5.1 什么是异常?
●平时不出现的不良发生时; ●平时的不良成倍出现时; ●发现与平常的状态不一样时; ●哪怕有1件不良流入后序时。295.2 出现来自常怎么办?怎么办 呢?
根据统计数据编制 作业手顺、要领等
技术文件
作业 人员 遵守
作业遵守标准
作业手顺 作业要领 质量特性
品质确认遵守标准
上工序的不良 本工序的不良 过住不良
25
No.3---改善标准作业
日常良品条件的 维持与遵守
良品条件 的整备
良品条件充实 及标准化
反馈
后工序 问题发生
让每个人都能 判断工序的好坏
不忘初心,回归工程
18
四、自工序完结的推进方法
品质基准——我们工作的输出结果 怎样达成品质基准呢?
19
4.1 自工序完结—良品条件整备
良品条件 整备
良品条件 遵守
自工序完结
良品条件应如何整备?
20
良品条件 为制造良品在制造过程中所必需的条件
21
【案例】
通过品质专念 良品条件钻研 活动,积累良 品条件数据库
?????
11
如果这个螺栓恰恰是
1 、车轮螺栓
12
如果这个螺栓恰恰是
2 、油道螺栓
整台发动
机报废!
13
如果这个螺栓恰恰是
3 、后刹车泵密封螺栓
制动能力降低,刹车失灵!
14
三、生产过程中如何保证品质
理想的品质保证方法
丰田自工序完结推进

第二部分 自工序完结
11. 选定实施工序 12. 制定实施方案 13. 梳理工序质量特性 14. 工序·质量管理 15. 作业检查的管理 16. 目视化事例 17. 提炼并实施改善课题 18. 做好维持管理 19. 效果跟踪·持续改善
第四部分 建议
20. 对自工序完结活动的建议
1/52
1、自工序完结的宗旨(1)
制造质量与自工序完结
制造质量培训材料
目录
第一部分 制造质量
1. 自工序完结的宗旨 2. 自工序完结的定位 3. 长沙厂自工序完结的现状 4. 自工序完结的定义 5. 自工序完结的意义
第二部分 推进
6. 自工序完结的要素 7. 自工序完结的推进步骤 8. 自工序完结的重点实施事项 9. 自工序完结的职责 10. 自工序完结的推进方法
(11年8月)
质量宣言
生产线
班组
员工
存在质量问题
产生原因分析 改进措施 质量宣言
1 2 3 1 2 3 类似决心、保证之类的话语 例:“今天我的缺陷为零”等
“我的质量宣言”
——不良对策到个人
(11年9月)
“班线长指导日志” ——培养班线长的管理习惯
(12年8月)
“班组制造质量评分” ——明确管理重点 (12年5月)
8/52
3、南车工序完结活动的现状(2)
《自工序完结的现状》 ・管理规定・作业标准・点检表不完善,缺乏技术和管理基础 ・因工序和人的不同,管理方式也是多种多样,缺乏一致性 ・依赖班组长个人的技术知识和经验,开展程度的不一 ・能保持零缺陷人数上升缓慢,实物质量的提升不显著
车间
零缺陷记录 保持人数 最长天数 最短天数
制造质量是生产现场作业 活动过程的直接结果。技术活 动和管理活动的成果,要依赖 生产现场每一道工序、每一步 的作业活动才能得以体现到制 造质量中。
- 1、下载文档前请自行甄别文档内容的完整性,平台不提供额外的编辑、内容补充、找答案等附加服务。
- 2、"仅部分预览"的文档,不可在线预览部分如存在完整性等问题,可反馈申请退款(可完整预览的文档不适用该条件!)。
- 3、如文档侵犯您的权益,请联系客服反馈,我们会尽快为您处理(人工客服工作时间:9:00-18:30)。
60%
50%
2)后工序发现不良(结果指标)
0.02
0.01
0
●
“自工序完结度”(过程指标)与 “后工序发现不良”(结果指标)
在推进过程中需要相互确认。
遵守标准作业 标准作业遵守状况点检 作业观察实施场面
遵守标准作业
标准作业遵守率点检表
遵守率%=实际遵守的作业要素数X100% 全作业要素数
標準作業の遵守チェックシート
品质状况的推移
工序内不良状况
0.8 凯美瑞
单
台 0.6
不 良 率
0.4
0.2
不良率降低到一定程度后停止不前
需要开展0不良活动
推进“自工序完结”活 动
雅力士
凯美瑞 0.049/台 雅力士 0.094件/台 (目标0.07件/台)
0
06/5
8 11 07/2
5
8 11 08/2
5 8 11 09/2
5
制造月份
3 通过自工序完结实现100%的良品保证活动
(1)何谓自工序完结
能够判断自己工作成果的好坏, 不将不良品流到下一工序。
你做到自工序完结了么?
蔬菜店的老板为何如此干劲十足?
新鲜安全的蔬菜 便宜卖
顾客开心
物不美 价不廉
顾客生气 下次不再购买!
所以有干劲!
马上知道自己工作结果的好坏 只要动脑筋想出好点子,就会有成就感
3/3
8/9=88%
4/4 4/5 遵守
6/6 良品条件
4/4
0.66x0.93
6/7
=62%
5/5
29/31=93%
2/2
遵守 标准作业
2/3
4/4
良品条件 4/5
6/6
遵守 良品条件
0.55x0.88 =48%
的保持 4/5
22/25=88%
【自工序完结度事例:扶手】
后门扶手自工序完结度计算实例.xls
C
设备 D
①设备A
设备 F
②设备B ③设备C ④设备D
○○ ○ ○ ○× ○ × ×○ ○ × ○○ ○ ○
设备 A
设备 E
⑤设备E ⑥设备F
统计
○○ ○ ○ ○○ ○ ○ 5/6 5/6 6/6 4/6=66%
3.人和设备的混合工位
①A的要素作业 1 ②〃
设备 A
设备 B
设备 C
③B的要素作业 1
* ゲージに入らないものは、検討品置場に置く
⇒只能生产良品 良品与否能够进行判断
(在自工序做到防止发生和流出)
“标准作业的遵守”(良品条件的保持)S NhomakorabeaCCESS
THANK YOU
2019/7/31
构成要素
良
设计要件
物等 【理想状态】
・按照图纸要求做 就能制造出良品
・作业完成后能够 判断合格与否
品条
生技要件
设备/夹具工具等
件
制造要件
方法
标准作业的遵守
人
・制造良品
・配备了能够判断合 格与否的设备和夹 具工具
应作出规定的内容 都有相关的明确规定
(谁、什么时候、 做什么、怎样做)
・规定能够持续遵守 ・实践持续改善
【实施事项】
提高设备和模具完成 提高图纸完成精度 精度 (明确制造相关要件 (明确生技要件并 并反映到图纸中去) 向制造现场展开)
标准类的完善和 完成精度的提高
自工序完结的目标
工作的好坏可以当场判断,立即采取对应措施
⇒①没有返修/返工 :对自己的工作充满信心 ②工作开心:积极性提高
确信自己制造的是良品 (不依赖于确认/检查/返修)
只生产良品 (不良品不送到后工序去)
自工序完结的思考方法
(理想状态)
工 厂 完
自工序 各车间 完结
完结
结
标准作业 制造良品的条件
作業手順 簡潔に!
No.
内容( 何をどうする )
1 検査完了品を勘合ゲージ台に乗せる
2 アクチュエーター組付け作業 1)部品箱からアクチュエーターを取る 2)アクチュエーター取り付け部にセットする
3 チューブエルボ組付け作業 1)チューブエルボ(φ9)を差し込む 1個 2)チューブエルボ(φ10)を差し込む 1個 3)チューブエルボ(φ8)を差し込む 2個
社内已实施自工序完结改善实例: ①装饰条间隙:天气温度下降时,开启加热灯; ②上部板表皮外漏:上部板反包边
上述2点是从哪方面进行改善的? ①:方法(制造要件) ②:物(设计要件) ③:上部板表皮外漏治具上面追加塑料薄片:生技要件
与结果指标的关系
1)自工序完结度(过程指标)
100%
●
90%
80%
70%
【自工序完结度事例】
举例说明
评价单位
(1)要素作业 (2)设备 (3)不良 等
①良品条件完善率 × ②标准作业
设计・生技・
设计 要件
生技 制造 要件 要件
制造(方法) 全部「○」 判定「○」
物 等
设备・夹具 等 方法
〔判定〕
良品条件 = 遵守率 人
自工序 完结度
①A的要素作业 1 ○ × ○ ×
1.人的工位
② 〃 2○○ ○ ○
③ 〃 3○○ ○ ○
④B的要素作业 4 ○ ○ ×
×
车身
车身
车身
⑤ 〃 5○○ ○ ○
⑥ 〃 6○○ × ×
⑦C的要素作业 7 ○ ○ ○ ○
⑧ 〃 8○○ ○ ○
作业员A 作业员B 作业员C ⑨ 〃 9 ○ ○ ○ ○
统计
- - - 6/9=66%
2.设备的工位
设备 设备
B
自工序完结
——挑战100%的良品保证
2009年6月26日 广汽丰田汽车有限公司 质量管理部
丰田生产方式
理念
Just・in・Time 必要的时候 提供必要数量的 必要物品 不浪费
自働化 不制造不良品 发生异常时要停止
自工序完结
(本日主题)
丰田的出发点 (它就是我们本身正在开展的工作、非“特别活动”)
标准作业遵守率 的提高
人的培养:使其遵守 岗位条件配备:使其易于遵守
从设计、生技、制造的观点,列出 所有能想到的“制造良品的条件”
遵守“制造良品的条件” /通过改善使其易于遵守
(3)自工序完结度的定义
为了表示“自工序完结”的进展状况,导入 “自工序完结度”的定义。
自工序完结度 =良品条件的完善率×标准作业的遵守率
检查 防止发生防误措施
防止流出防误措施 检查 确认作业
只能生产 良品的工 艺构造
检查
各车间内检查
检查
最终检查
出厂
不将不良品 流到后工序
(2)自工序完结的构造
概略图
自工序完结的推进 ⇒“完善良品条件”和“遵守标准作业”
“良品条件”
(制造良品的条件)
设计要件・生技要件・制造要件
4M 物 设备 方法 人
设备 ④ 〃 2 D⑤ 〃 3
⑥设备A
作业员A
作业员B
⑦设备B ⑧设备C
⑨设备D
统计
○× ○ × 2○ ○ ○ ○ ○○ × × ○○ ○ ○ ○○ ○ ○
制造良品 ○ ○ ○ ○
○× ○ × ×○ ○ ×
的条件 ○ ○ ○ ○
9/9 7/9 8/9 5/9=55%
3/3
遵守
2/3 标准作业 0.66x0.88 =58%