机械制造工艺学课程设计例题1(DOC31页)
机械制造工艺学及机床夹具设计习题
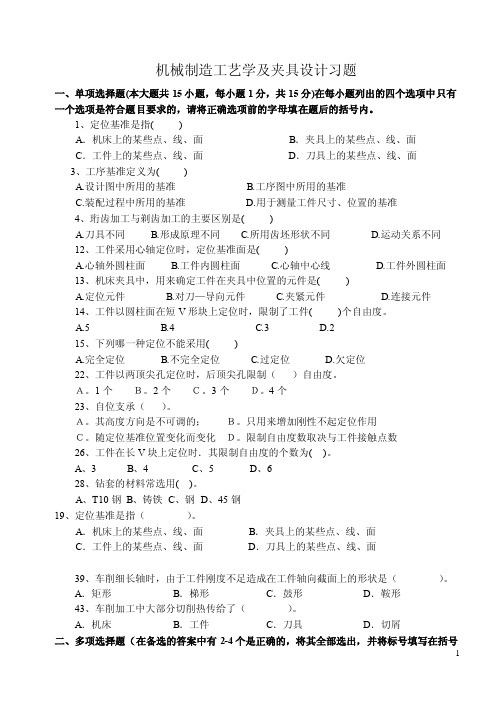
机械制造工艺学及夹具设计习题一、单项选择题(本大题共15小题,每小题1分,共15分)在每小题列出的四个选项中只有一个选项是符合题目要求的,请将正确选项前的字母填在题后的括号内。
1、定位基准是指( )A.机床上的某些点、线、面B.夹具上的某些点、线、面C.工件上的某些点、线、面D.刀具上的某些点、线、面3、工序基准定义为( )A.设计图中所用的基准B.工序图中所用的基准C.装配过程中所用的基准D.用于测量工件尺寸、位置的基准4、珩齿加工与剃齿加工的主要区别是( )A.刀具不同B.形成原理不同C.所用齿坯形状不同D.运动关系不同12、工件采用心轴定位时,定位基准面是( )A.心轴外圆柱面B.工件内圆柱面C.心轴中心线D.工件外圆柱面13、机床夹具中,用来确定工件在夹具中位置的元件是( )A.定位元件B.对刀—导向元件C.夹紧元件D.连接元件14、工件以圆柱面在短V形块上定位时,限制了工件( )个自由度。
A.5B.4C.3D.215、下列哪一种定位不能采用( )A.完全定位B.不完全定位C.过定位D.欠定位22、工件以两顶尖孔定位时,后顶尖孔限制()自由度。
A。
1个B。
2个C。
3个D。
4个23、自位支承()。
A。
其高度方向是不可调的;B。
只用来增加刚性不起定位作用C。
随定位基准位置变化而变化D。
限制自由度数取决与工件接触点数26、工件在长V块上定位时.其限制自由度的个数为( )。
A、3B、4C、5D、628、钻套的材料常选用( )。
A、T10钢B、铸铁C、钢D、45钢19、定位基准是指()。
A.机床上的某些点、线、面B.夹具上的某些点、线、面C.工件上的某些点、线、面D.刀具上的某些点、线、面39、车削细长轴时,由于工件刚度不足造成在工件轴向截面上的形状是()。
A.矩形B.梯形C.鼓形D.鞍形43、车削加工中大部分切削热传给了()。
A.机床B.工件C.刀具D.切屑二、多项选择题(在备选的答案中有2-4个是正确的,将其全部选出,并将标号填写在括号内,多填或少填均不得分,每题2分,共18分)8、螺旋夹紧机构具有以下特点( )。
机械制造工艺学课程设计

机械制造工艺学课程设计一、教学目标本课程旨在让学生掌握机械制造工艺学的基本概念、原理和方法,培养学生分析和解决机械制造过程中实际问题的能力。
1.了解机械制造工艺学的起源、发展及其在现代制造业中的应用。
2.掌握常用的机械加工方法、工艺过程和工艺参数。
3.熟悉机械制造工艺规程的编制方法和原则。
4.掌握机械制造质量控制的基本理论和方法。
5.能够运用所学知识分析和解决机械制造过程中的实际问题。
6.具备编制简单机械制造工艺规程的能力。
7.能够运用质量控制方法对机械制造过程进行监控和改进。
情感态度价值观目标:1.培养学生的创新意识和团队合作精神。
2.增强学生对机械制造行业的认同感和责任感。
3.培养学生严谨治学、勤奋钻研的学习态度。
二、教学内容本课程的教学内容主要包括机械制造工艺学的起源与发展、机械加工方法、工艺过程与参数、工艺规程编制、机械制造质量控制等。
1.机械制造工艺学的起源与发展:介绍机械制造工艺学的起源、发展及其在现代制造业中的应用。
2.机械加工方法:介绍常用的机械加工方法,如铸造、焊接、切削、磨削等。
3.工艺过程与参数:讲述工艺过程的组成、特点和顺序,以及工艺参数的确定方法。
4.工艺规程编制:介绍工艺规程的编制方法、原则和注意事项。
5.机械制造质量控制:讲述机械制造质量控制的基本理论、方法和实践。
三、教学方法本课程采用多种教学方法,如讲授法、案例分析法、实验法等,以激发学生的学习兴趣和主动性。
1.讲授法:通过讲解机械制造工艺学的理论知识,使学生掌握基本概念和原理。
2.案例分析法:通过分析机械制造过程中的实际案例,培养学生分析和解决实际问题的能力。
3.实验法:学生进行实验,使学生更好地理解机械加工方法及其工艺参数。
四、教学资源本课程的教学资源包括教材、参考书、多媒体资料、实验设备等。
1.教材:选用国内知名出版社出版的《机械制造工艺学》教材。
2.参考书:推荐学生阅读相关领域的经典著作和最新研究成果。
3.多媒体资料:制作课件、视频等多媒体资料,以丰富教学手段。
机械制造工艺学课程设计例题1(DOC31页)

机械制造专业(本科)《机械制造工艺学》课程设计目录目录11 绪论22 零件分析23 工艺规程设计33.1 确定毛坯的制造形成33.2 基面的选择33.3制定工艺路线33.4 机械加工余量、工序尺寸及毛坯的确定73.5确定切削用量及基本工时104 夹具设计254.1 问题的提出254.2夹具设计255 总结30参考文献错误!未定义书签。
致谢错误!未定义书签。
1 绪论2 零件分析题目所给的零件是机床尾座体,尾座安装在机床的右端导轨上,尾座上的套筒可以安装顶尖,以支承较长的工件的右端(即顶持工件的中心孔)、安装钻头、绞刀,进行孔加工,也可以安装丝锥攻螺纹工具、圆析牙套螺纹工具加工内、外螺纹。
尾座可以沿尾座导轨作纵向调整移动,然后压下尾座紧固手轮将尾座夹紧在所需位置,摇动尾座手轮可以实现对工件的顶紧、松开或对工件进行切削的纵向进给。
2.1 零件的特点由图可知,该零件为不太规则的部件,其主要技术特点如下:1.铸件需要消除毛刺和砂粒、并作退火处理2.φ17H6要求圆度为0.0033.φ17H6要求圆柱度0.0044.φ17H6与导轨面的平行度为0.0055.φ17H6与燕尾面的平行度为0.0056.φ17H6的孔轴心线与导轨面的位置度误差为0~0.17.φ17H6的孔与燕尾面的位置度误差不超过0.158.各面的粗糙度达到需要的要求9.φ17H6的孔需精加工、研配10.导轨面配刮10~13点/25⨯252.2 零件工艺分析根据零件图可知、主要进行导轨面的加工、孔加工和表面加工、钻孔、攻丝,孔的精度要求高。
该零件年生产5000件属大批量生产,在加工是为了提高劳动效率、降低成本,设计加工零件需要设计专用夹具。
3 工艺规程设计3.1 确定毛坯的制造形成由于该零件的形状较复杂,因此不能用锻造,只能用铸件,而且年生产批量为5000件已达成批生产的水平,采用批量造型生产。
根据零件主要的加工表面的粗糙度确定各表面加工余量,查参考文献查参考文献[2] 《机械加工工艺手册》,以后有计算在此就不重复了。
机械制造工艺学课程设计—齿轮设计
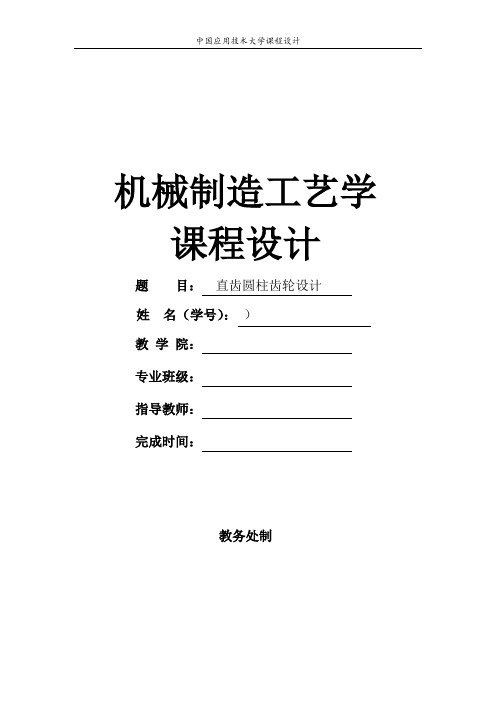
机械制造工艺学课程设计题目:直齿圆柱齿轮设计姓名(学号):)教学院:专业班级:指导教师:完成时间:教务处制目录引言 (1)1.齿轮零件结构分析 (1)1.1 齿轮零件图分析 (1)1.2 齿轮零件结构分析 (2)1.2.1零件表面组成 (2)1.2.2确定主要表面与次要表面 (2)1.2.3零件结构工艺性分析 (2)2.毛坯的确定 (2)2.1毛坯的确定原则 (2)2.2毛胚的选择原则 (2)3.选择定位基准 (3)3.1以内孔和端面定位 (3)3.2以外圆和端面定位 (3)4.拟定齿轮的工艺路线 (3)4.1确定加工方案 (3)4.1.1齿坯加工方案的选择 (3)4.1.2齿形加工 (4)4.2划分加工阶段 (4)4.3选择定位基准 (4)4.4加工工序安排 (4)5.确定加工尺寸和切削用量 (4)5.1背吃刀量的选择 (4)5.2进给量的选择 (5)5.3切削速度的选择 (5)6.设计工序内容 (5)6.1确定工序尺寸 (5)6.2选择设备工装 (6)7.夹具设计 (6)7.1机床夹具的定位误差 (6)7.1.1心轴 (6)7.1.2定位套 (7)7.2机床夹具的对刀装置 (7)7.2.1确定插床夹具对刀块位置尺寸的步骤 (8)7.2.2精度校验 (8)7.3机床夹具的选择原则 (8)9.附件 (9)参考文献 (10)致谢词 (10)引言机械制造工艺学课程设计是我们学完了大学的全部基础课、技术基础课以及大部分专业课之后进行的。
这是我们在进行毕业设计之前对所学各课程的一次深入的综合性的总复习,也是一次理论联系实际的训练,因此,它在我们四年的大学生活中占有重要的地位。
就我个人而言,我希望能通过这次课程设计,了解并认识一般机器的生产工艺过程,巩固和加深已学过的技术基础课和专业课的知识,理论联系实际,对自己未来将从事的工作惊醒一次适应性训练,从中锻炼自己分析问题、解决问题的能力。
为今后的工作打下一个良好的基础。
机械制造工艺学习题计算.doc

0.13510Li图120L21035二、计算题1.图所示某齿轮机构,已知 A]=3O°o.o6mm, A2=5°o.O6mm, A3=38 +0.16 +0.10mm, A4=30.o.o5nim,试计算齿轮右端面与档圈左端血的向端在血的轴向间隙A。
的变动范围。
根据公式 A0=A3-A 1 -A2-A4=38-30-5-3=0ES0=ES3- (EI1+EI2+EI4)=(0」6+0.06+0.04+0.05) mm=+0.31 mmEI0=EI3・(ES1+ES2+ES4) = (0.10-0-0-0) mm=+0.10mm 故轴向间隙AO的变化范围为0.10〜0.31 mimA3\//////——\//////一■吃 Al A0「A4M -----------------2.如图所示,A、B、C、D、E各面及设计尺寸20土0.1 mm,工序尺寸L】、L?都在前工序加工出。
本工序中,以E面为测量基准加工D面,得尺寸10±0.1,并要求保证设计尺寸10±0.4、35±0.2,现在要求计算前工序加工所得到的两个工序尺寸L】、L2的尺寸及偏差,以 满足两个设计尺寸的要求。
L1的尺寸链如图所示。
35为封闭环,L1为增环,10为减环。
可求得:Ll=45±0.1L2的尺寸链如图所示。
10为封闭环,20、L2为减环,35为增环。
可求得:L2=5 ±35±0・2LiESN=ES1-EI2-EI3= 0.016-2 X -0.06 mm=+0.136mm EIN=EII-ES2-ES3=0-2 X -0.02mm=+0.04mm3. 如图所示零件,按图样注出的尺寸A|和A3加工时不易测量,现改为按尺寸A 】和A3加 工,为了保证原设计要求,试计算A?的基本尺寸和偏差。
据题意,按尺寸Al 、A2加工,则A3必须为封闭环,A2则为工序尺寸。
机械制造工艺学课程设计-CA6140车床拨叉

#目录序言…………………………………………………第 5 页零件分析…………………………………………………第 5 页(一)零件的工艺分析…………………………………………第 5 页&(二)零件的作用......................................................... ..............第 5 页工艺规程设计………………………………………………第5 页(一)确定毛坯的制造形式……………………………………第 5 页(二)基准面的选择……………………………………………第 5 页(三)制定工艺路线……………………………………………第 6 页(四)机械加工余量、工序尺寸及毛坯尺寸的确定…………………第 6 页(五)确定切削用量及基本工时…………………………………第 6 页参考文献………………………………………………第16 序言(机械制造技术基础课程设计是我们在学完了大学的全部基础课,专业基础课以及专业课后进行的。
这是我们在进行毕业设计之前对所学的各科课程一次深入的综合性总复习,也是一次理论联系实际的训练。
因此,他在我们的大学四年生活中占有重要的地位。
就我个人而言,我希望通过这次课程设计对自己未来将从事的工作进一步适应性的训练,希望自己在设计中能锻炼自己的分析问题、解决问题、查资料的能力 ,为以后的工作打下良好的基础。
由于能力有限,设计尚有很多不足之处,希望各位老师给予指导。
零件的分析(一).零件的作用题目所给的零件是CA6140机床上的拨叉,他位于机床变速箱内。
主要作用是用于机床的变速。
(二)零件的工艺分析:~CA6140车床共有四处加工表面,其间有一定位置要求。
分述如下:1. 以φ25为中心的加工表面这一组加工表面包括:φ25023.00 的孔。
2 以φ25孔为基准来加工φ60的圆弧和圆弧的两个端面来达到图纸要求。
3 以φ25孔来定位来加工16的槽来满足垂直度要求。
机械制造工艺学习题
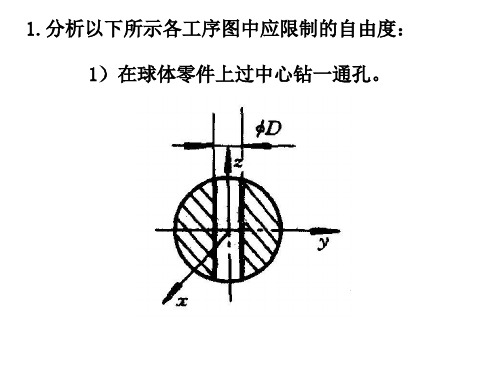
7)试分析下图所示的在卧式拉床上,使用圆拉刀拉削传 动轴突缘内孔时,定位元件(拉刀导向部分可视为长定位销) 所限制的自由度。
8)加工汽车钢板弹簧吊耳时,采用下图所示定位方案, 试分析定位元件所限制的自由度。
9)试分析采用下图所示定位方案精镗活塞销孔时,定位元 件所限制的自由度。
10)分析下图所示变速器壳体的两种定位方案,指出两种方 案中各定位元件所限制的自由度,并说明哪个定位方案较好。
3)在下图所示的汽车传动轴突缘叉上磨削平面K及Q, 需要保证:(1)两平面K及Q间的尺寸为118mm;(2)两平面对 2—¢39孔的垂直度公差为0.1mm;(3)两平面对¢95mm外圆 的对称度公差为0.15mm。
4)在下图所示的拖拉机差速锁操纵杠杆上铣槽和钻孔,应 保证:(1)铣槽宽度尺寸为4.5mm,槽对¢18mm和¢12.5mm 两孔中心平面的对称度公差为0.3mm;(2)钻阶梯孔¢6.7mm及 ¢9mm,位置尺寸如图所示。
11)试分析下图所示的十字轴在四个短V形块上定位时, 定位元件是如何限制自由度的?指出哪几个自由度是过定位自 由度,如何改进定位方案才不出现过定位?
图(e) :钻铰连杆零件小头孔,保证小头孔与大 头孔之间的距离及两孔平行度。
3.指出以下各图所示各定位、夹式钻床上扩活塞销孔时,采用下图所示定 位方案,定位元件所能限制的自由度。
6)试分析在连续拉床上,拉削下图所示连杆接合平面、 半圆孔及两侧面时,定位元件所能限制的自由度。
2.分析以下各图所示定位方案,分析: (1)指出各定位元件所限制的自由度; (2)判断有无欠定位或过定位; (3)对不合理的定位方案提出改进意见。
图(a):过三通管中心。打一孔,使孔轴线与管轴 线OX、OZ垂直相交。
图(b): 车外圆,保证外圆与内孔同轴。
机械制造工艺学课程设计例题1

机械制造工艺学课程设计例题1引言机械制造工艺学是机械制造专业的一门重要课程,通过学习该课程,学生可以掌握机械零件的设计和加工工艺,提高工作效率和生产质量。
本文将介绍一个机械制造工艺学的课程设计例题,帮助学生更好地理解和应用所学的知识。
题目描述设计一种机械零件的加工工艺,要求能够满足以下要求:1.零件材料:冷轧钢板;2.零件尺寸:直径为50mm,厚度为10mm;3.工艺流程:粗加工、精加工、表面处理;4.工艺要求:保持尺寸精度在0.05mm以内,表面粗糙度在Ra0.8以内;5.设备要求:铣床、钻床、平面磨床、抛光机;6.工艺参数:切削速度、进给速度、切削深度等。
解决方案零件材料选择根据题目要求,我们选择冷轧钢板作为零件的材料。
冷轧钢板具有较高的强度和硬度,并且加工性能较好,适合用于制造机械零件。
零件尺寸确定零件直径为50mm,厚度为10mm。
根据零件的尺寸确定加工工艺和设备选择。
工艺流程设计根据题目要求,我们将工艺流程划分为三个阶段:粗加工、精加工和表面处理。
粗加工1.首先,使用钻床进行钻孔处理。
选择钻头直径为5mm,并根据该直径计算所需的切削速度和进给速度。
2.接下来,使用铣床进行整形处理。
根据零件的形状和尺寸,选择合适的加工刀具和切削参数。
精加工1.使用平面磨床进行表面精加工。
根据要求的尺寸精度和表面粗糙度,选择合适的磨削工艺和磨削参数。
表面处理1.最后,使用抛光机进行表面处理。
选择适当的抛光工艺和抛光参数,使零件的表面粗糙度达到要求。
设备选择根据以上工艺流程的设计,我们需要选择以下设备进行加工:1.钻床:用于钻孔处理;2.铣床:用于整形处理;3.平面磨床:用于表面精加工;4.抛光机:用于表面处理。
工艺参数确定根据以上工艺流程和设备选择,我们需要确定合适的工艺参数,包括切削速度、进给速度、切削深度等。
1.钻床工艺参数:根据钻头直径和钻孔深度,确定切削速度和进给速度;2.铣床工艺参数:根据切削刀具类型和零件的形状和尺寸,确定切削速度、进给速度和切削深度;3.平面磨床工艺参数:根据所需的尺寸精度和表面粗糙度,确定磨削速度和进给速度;4.抛光机工艺参数:根据所需的表面粗糙度,确定抛光速度和进给速度。
机械制造工艺学典型习题解答(DOC)
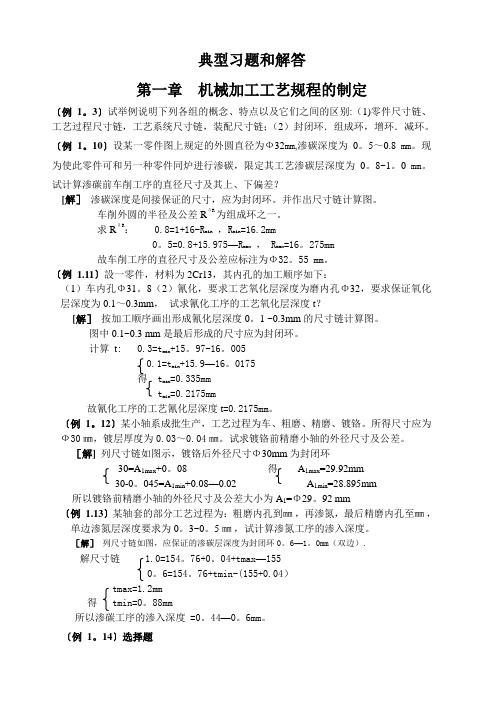
典型习题和解答第一章机械加工工艺规程的制定〔例1。
3〕试举例说明下列各组的概念、特点以及它们之间的区别:(1)零件尺寸链、工艺过程尺寸链,工艺系统尺寸链,装配尺寸链;(2)封闭环.组成环,增环.减环。
〔例1。
10〕设某一零件图上规定的外圆直径为Ф32mm,渗碳深度为0。
5~0.8 mm。
现为使此零件可和另一种零件同炉进行渗碳,限定其工艺渗碳层深度为0。
8~1。
0 mm。
试计算渗碳前车削工序的直径尺寸及其上、下偏差?[解]渗碳深度是间接保证的尺寸,应为封闭环。
并作出尺寸链计算图。
车削外圆的半径及公差RδR为组成环之一。
求RδR: 0.8=1+16-R min,R min=16.2mm0。
5=0.8+15.975—R max, R max=16。
275mm故车削工序的直径尺寸及公差应标注为Φ32。
55 mm。
〔例 1.11〕設一零件,材料为2Cr13,其内孔的加工顺序如下:(1)车内孔Φ31。
8(2)氰化,要求工艺氧化层深度为磨内孔Φ32,要求保证氧化层深度为0.1~0.3mm,试求氰化工序的工艺氧化层深度t?[解]按加工顺序画出形成氰化层深度0。
1 ~0.3mm的尺寸链计算图。
图中0.1~0.3 mm是最后形成的尺寸应为封闭环。
计算t: 0.3=t max+15。
97-16。
0050.1=t min+15.9—16。
0175得 t max=0.335mmt min=0.2175mm故氰化工序的工艺氰化层深度t=0.2175mm。
〔例1。
12〕某小轴系成批生产,工艺过程为车、粗磨、精磨、镀铬。
所得尺寸应为Ф30㎜,镀层厚度为0.03~0.04㎜。
试求镀铬前精磨小轴的外径尺寸及公差。
[解] 列尺寸链如图示,镀铬后外径尺寸Φ30mm为封闭环30=A1max+0。
08 得A1max=29.92mm30-0。
045=A1min+0.08—0.02 A1min=28.895mm 所以镀铬前精磨小轴的外径尺寸及公差大小为A1=Φ29。
机械制造工艺学课程设计
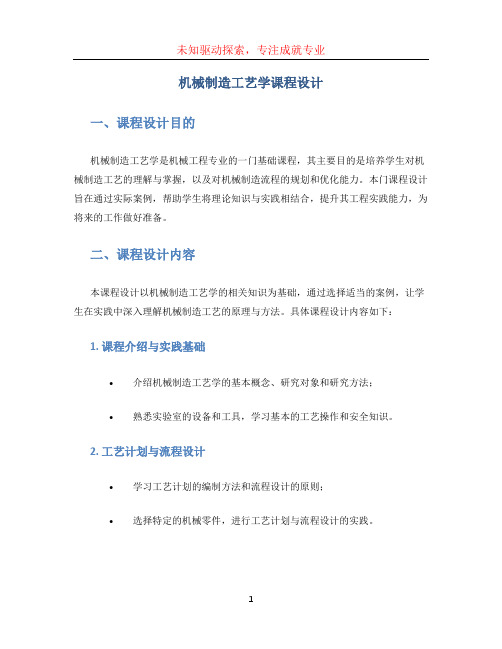
机械制造工艺学课程设计一、课程设计目的机械制造工艺学是机械工程专业的一门基础课程,其主要目的是培养学生对机械制造工艺的理解与掌握,以及对机械制造流程的规划和优化能力。
本门课程设计旨在通过实际案例,帮助学生将理论知识与实践相结合,提升其工程实践能力,为将来的工作做好准备。
二、课程设计内容本课程设计以机械制造工艺学的相关知识为基础,通过选择适当的案例,让学生在实践中深入理解机械制造工艺的原理与方法。
具体课程设计内容如下:1. 课程介绍与实践基础•介绍机械制造工艺学的基本概念、研究对象和研究方法;•熟悉实验室的设备和工具,学习基本的工艺操作和安全知识。
2. 工艺计划与流程设计•学习工艺计划的编制方法和流程设计的原则;•选择特定的机械零件,进行工艺计划与流程设计的实践。
3. 加工工艺与设备选择•学习不同加工工艺的特点和应用场景;•了解不同工艺设备的原理和技术参数;•设计合适的加工工艺与选择相应的设备进行加工实验。
4. 数控加工与自动化生产•学习数控加工的基本原理和编程方法;•了解自动化生产线的构成和工作原理;•设计数控加工程序并进行实际加工操作。
5. 工艺控制与质量管理•学习工艺过程的控制方法和质量管理的原则;•了解各种测量与检测工具的原理和应用;•进行实际的工艺控制和质量管理实验。
三、课程设计要求本课程设计旨在培养学生的实践操作能力和工程实践能力,要求学生能够:1.深入理解机械制造工艺学的基本概念、原理和方法;2.掌握工艺计划与流程设计的基本步骤和原则;3.熟悉常见的加工工艺与设备,并了解其应用场景和操作要点;4.理解数控加工的原理和编程方法,并进行实际加工操作;5.能够进行工艺控制和质量管理,并运用测量与检测工具进行实践。
四、课程设计评估方式本课程设计将采用以下评估方式:1.实验报告:学生需要根据实验过程和结果撰写实验报告,内容包括实验目的、方法、结果和分析;2.设计方案:学生需要根据课程要求,设计机械零件的工艺计划和流程,并进行实际操作;3.课堂展示:学生需要通过课堂展示方式,向其他同学展示自己的实践成果;4.课程考试:学生需要通过闭卷考试来检验对机械制造工艺学的理解和掌握程度。
机械制造工艺学课程设计许文强
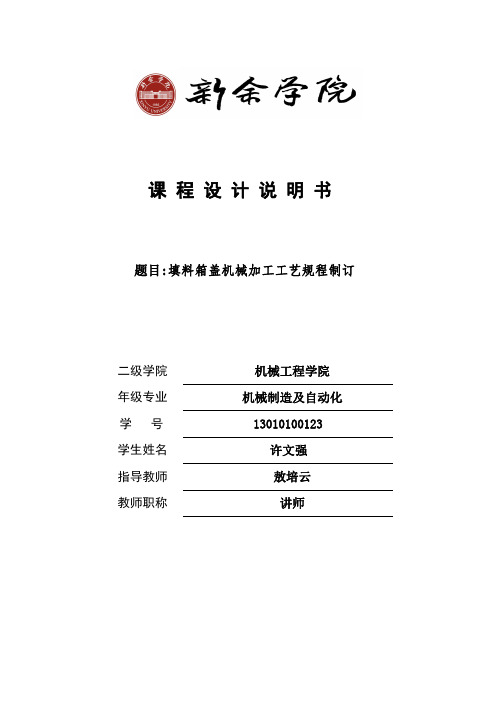
2.4 制订工艺路线................................................................................................... 7 2.5 1 毛坯尺寸余量表.......................................................................................... 10 2.5 2 机械加工余量、工序尺寸的确定.............................................................. 11 2.6 确定切削用量和基本工时............................................................................. 13
0.046 0.046 (2)以 60h5( 0 )孔中心线为基准的加工面:尺寸为 78 与 60H8( 0 )中
心线垂直度为 0.012,表面粗糙度为 0.4 凸台面。
0.046 (3) 以 60H8( 0 )孔中心均匀分布的 12 孔,6-ф13.5,4-M10-6H 深 20 孔深
24 及 4-M10-6H。
0.036 0.20 (4)以 100f8( 表面粗糙度 0.090 )的外圆面和左端面为定位基准加工 7.50
为 3.2 的密封环槽。
4
第2章
2.1 确定毛坯类型与铸造方法
图2 根据零件材料 HT200 确定毛坯为铸件, 据零件结构特征和保证零件加工质量 及便于加工原则, 采用整体半实体铸造毛坯, 分型面通过 60 孔中心线并垂直与 端面, 铸造后对铸件进行人工时效处理, 以免工件加工后因内应力产生较大变形。 零件年产产纲领为为 6000 件/年, 达到大批生产的水平, 且零件的轮廓尺寸不大, 故选用砂型机器铸造。从提高生产率、保证加工精度及经济性等角度考虑,铸造 方案也可行。
机械制造工艺学课程设计题目(新)

1、连杆螺钉,毛坯为锻件技术要求1.调质处理28~32HRC。
3.Φ340-0.016mm圆度、圆柱公差为0.008mm。
2.材料40C r4、磁粉探伤,无裂纹,夹渣等缺陷。
2、活塞杆,毛坯为锻件3、输出轴,毛坯为Φ90棒料技术要求1.调质处理28~32HRC。
3.未注圆角R1。
2.材料45。
4、保留中心孔。
4、偏向套,锻造毛坯5、密封圈定位套,铸造毛坯6、十字头滑套,铸造毛坯7、活塞,铸造毛坯技术要求1.铸件时效处理。
3.活塞环槽80+0.02mm入口倒角为0.3Χ450。
2.材料HT200。
4、未注明倒角1X450。
8、十字头,铸造毛坯技术要求1.铸件时效处理。
3.铸造圆角R5。
2.材料HT200。
4、未注明倒角1X450。
9、圆柱齿轮,锻造毛坯技术要求齿轮基本参数1.热处理:190~217HBS。
m=52. 未注明倒角1X450。
Z=633. 材料HT200。
a=200精度等级8-7-7GK10、镶铜套齿轮,锻造毛坯11.齿轮轴,锻造毛坯12、倒档齿轮,锻造毛坯13、齿条,毛坯为Φ70棒料14、矩形齿花键轴,Φ40棒料技术要求1.调质处理28~32HRC。
3. 未注明倒角0.5X450。
2.材料45。
15、矩形齿花键套,Φ80棒料16、车床拨叉,铸造毛坯,两件合铸,加工到一定工序后切开,切口2mm。
17、轴承座,铸造毛坯18、惰轮轴,铸造毛坯19三轴连杆,锻造毛坯20、推动架,铸造毛坯21、双联齿轮22、外齿轮(模数m n=10,齿数z=97)23、内齿轮24、定位支座零件图25、摇杆零件图26、轴,材料为棒料27、内齿轮28、缸套30、齿轮轴31、皮带轮33、拨叉35、拨叉37、法兰盘38、双联齿轮39、行星减速器输入轴42、行星齿轮减速器行星架44、行星齿轮减速器花键轴45、法兰,材料4546、行星齿轮减速器输入盖板,材料Q23547、行星齿轮减速器太阳轮48、行星齿轮减速器鼓形齿套,材料40Cr50、输入轴。
机械制造工艺学例题

课堂作业
3.试提出成批生产如下图所示零件的机械加工工艺过程的组成(从工序到工步),并 指出各工序的定位基准。
课堂作业
3. 解答 连接件零件加工工艺过程(成批生产)
工序号
工
步
定位基准(面)
1
车端面,钻、扩、铰Φ20孔 (安装1)
外圆
2
车另一端面及外圆Φ75 (安装1)
拉键槽
端面及内孔
3
内孔及端面
4
四、尺寸链的计算
例题1解答:
根据增环及减环的定义,可得出尺寸链中的A1、A2、A3、A4为增环,A5、A6、 A7为减环,所以 (1)封闭环的基本尺寸
A 0 A1 A 2 A 3 A 4 ( A 5 A 6 A 7 ) 30 30 30 10 ( 40 15 40 ) 5mm
课堂练习
在车床的三爪自定心卡盘上精镗一批薄壁铜套的内孔(如下 图所示),工件以φ50h6定位,用调整法加工,试分析影响镗 孔的尺寸、几何形状及孔对已加工外圆φ46h6的同轴度误差的 主要因素有哪些?并分别指出由这些因素引起的加工误差属于 哪一类性质的误差?
答案
影响孔径尺寸精度的因素: (1)镗刀的尺寸调整误差——常值系统误差; (2)镗刀的磨损--—变值规律性误差: (3)铜套的均匀热变形(加工后孔缩小)——常值系统误差。 影响孔几何形状精度的因素: 圆度误差: (1)薄壁铜套的夹紧变形----随机误差; (2)车床主轴的径向跳动----常值系统误差。 圆柱度误差: (1)机床导轨的几何误差(纵导轨在水平面不直(车床);前后导轨扭曲; 纵导轨与机床主轴不平行)----常值系统误差; (2)机床主轴的摆动--—常值系统误差。 (3)工艺系统受力变形(壁厚不均匀)——常值系统误差。 影响孔φ40H7对外圆φ46h6的同轴度误差的因素: (1)基准不符误差(φ46h6与φ50h6的同轴度误差)----随机误差; (2)工件外圆φ50h6的形状误差引起工件安装误差--—随机误差
机械制造工艺学习题参考解答(部分)
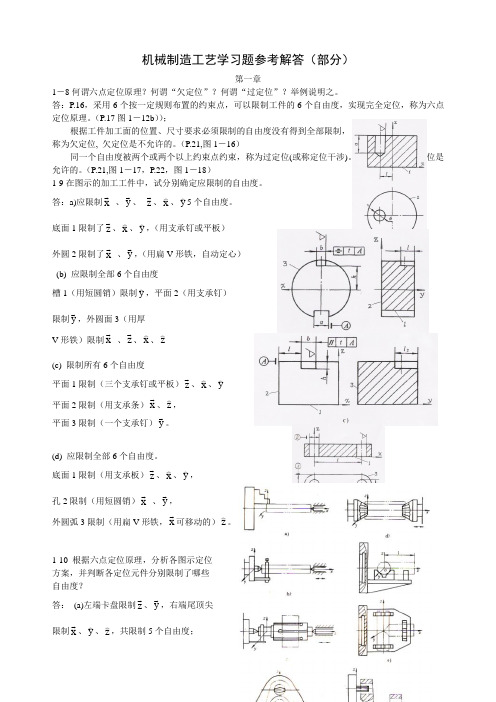
不符合
符合,至少走三刀。
3-10横磨工件时(图3—83),设横向磨削力Fy=100N,
主轴箱刚度Ktj=5000N/mm,尾座刚度Kwz=4000N/mm,
加工工件尺寸如图示,求加工后工件的锥度。
答:设主轴箱支反力为 ,尾座支反力为
= =
= =
零件锥度为:
3-16车削一批轴的外圆,其尺寸为ф25±0.05mm,已知此工序的加工误差分布曲线是正态分布,其标准差σ=0.025mm,曲线的顶峰位置偏于公差带中值的左侧。试求零件的合格率,废品率。工艺系统经过怎样的调整可使废品率降低?
答:画尺寸链图,L0为封闭环, t、L2为增环,L1为减环。
列表解:
公称尺寸
ES
EI
t(待求)
1.0
+0.28
+0.01
L1
-10.3
+0.02
0
L2
10
0
-0.01
L0
0.7
+0.3
0
铣槽尺寸t=
第二章
2-1分析图2—94所列定位方案:①指出各定位元件所限制的自由度;②判断有无欠定位或过定位;③对不合理的定位方案提出改进意见。
1-9在图示的加工工件中,试分别确定应限制的自由度。
答:a)应限制 、 、 、 、 5个自由度。
底面1限制了 、 、 ,(用支承钉或平板)
外圆2限制了 、 ,(用扁V形铁,自动定心)
(b)应限制全部6个自由度
槽1(用短圆销)限制 ,平面2(用支承钉)
限制 ,外圆面3(用厚
V形铁)限制 、 、 、
(c)限制所有6个自由度
4个自由度,右侧一个短V形块限制 、 2个自由度,共限制6个自由度,完全定位;
(完整word版)机械制造工艺学试题及答案(四套全)
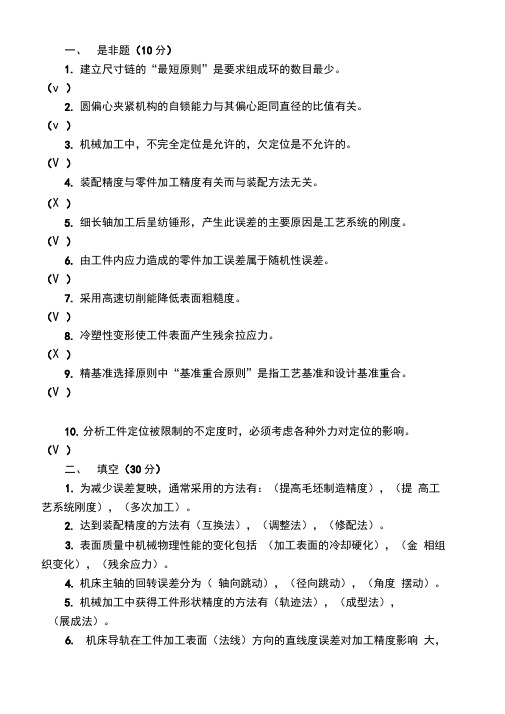
一、是非题(10分)1.建立尺寸链的“最短原则”是要求组成环的数目最少。
(v )2.圆偏心夹紧机构的自锁能力与其偏心距同直径的比值有关。
(v )3.机械加工中,不完全定位是允许的,欠定位是不允许的。
(V )4.装配精度与零件加工精度有关而与装配方法无关。
(X )5.细长轴加工后呈纺锤形,产生此误差的主要原因是工艺系统的刚度。
(V )6.由工件内应力造成的零件加工误差属于随机性误差。
(V )7.采用高速切削能降低表面粗糙度。
(V )8.冷塑性变形使工件表面产生残余拉应力。
(X )9.精基准选择原则中“基准重合原则”是指工艺基准和设计基准重合。
(V )10.分析工件定位被限制的不定度时,必须考虑各种外力对定位的影响。
(V )二、填空(30分)1.为减少误差复映,通常采用的方法有:(提高毛坯制造精度),(提高工艺系统刚度),(多次加工)。
2.达到装配精度的方法有(互换法),(调整法),(修配法)。
3.表面质量中机械物理性能的变化包括(加工表面的冷却硬化),(金相组织变化),(残余应力)。
4.机床主轴的回转误差分为(轴向跳动),(径向跳动),(角度摆动)。
5.机械加工中获得工件形状精度的方法有(轨迹法),(成型法),(展成法)。
6.机床导轨在工件加工表面(法线)方向的直线度误差对加工精度影响大,而在(切线)方向的直线度误差影响小。
8.夹具对刀元件的作用是确定(刀具)对(工件)的正确加工位置。
9.应用点图进行误差分析时X和R的波动反映的是(变值性误差的变化)和(随机性误差)的分散程度。
11.划分工序的主要依据是工作地点是否改变和(工件是否连续完成)。
六、(10分)车削一批轴的外圆,其尺寸要求为①20士 0.06。
若此工序尺寸 呈正态分布,公差带中心大于分布中心,其偏值3 =0.03m m,均方根差X X 19.94 19.97|解:(1)0.02查 F 1 0.4332废品率为F10.0668(2) CX X19.97 200.03S66 0.02 0.12则F i0.5 F i 0.5 0.43320.0668? ?0.02=0.02m m ,求:(3)采用将刀具朝着尺寸变化的方向调整0.015(即直径上增加0.03),使X 与公差带中心重合以消除废品一、是非题(10分)1•在相同的工艺条件下,加工后的工件精度与毛坯的制造精度无关。
(完整版)机械制造工艺学试题及参考答案
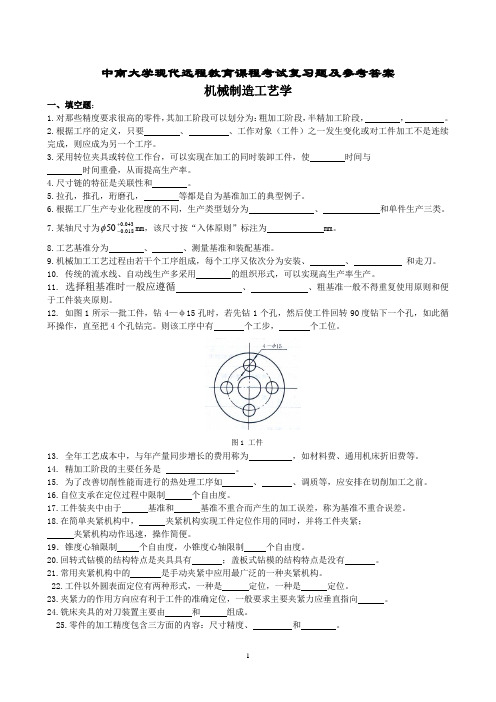
中南大学现代远程教育课程考试复习题及参考答案机械制造工艺学一、填空题:1.对那些精度要求很高的零件,其加工阶段可以划分为:粗加工阶段,半精加工阶段, , 。
2.根据工序的定义,只要 、 、工作对象(工件)之一发生变化或对工件加工不是连续完成,则应成为另一个工序。
3.采用转位夹具或转位工作台,可以实现在加工的同时装卸工件,使 时间与时间重叠,从而提高生产率。
4.尺寸链的特征是关联性和 。
5.拉孔,推孔,珩磨孔, 等都是自为基准加工的典型例子。
6.根据工厂生产专业化程度的不同,生产类型划分为 、 和单件生产三类。
7.某轴尺寸为043.0018.050+-φmm ,该尺寸按“入体原则”标注为 mm 。
8.工艺基准分为 、 、测量基准和装配基准。
9.机械加工工艺过程由若干个工序组成,每个工序又依次分为安装、 、 和走刀。
10. 传统的流水线、自动线生产多采用 的组织形式,可以实现高生产率生产。
11. 选择粗基准时一般应遵循 、 、粗基准一般不得重复使用原则和便于工件装夹原则。
12. 如图1所示一批工件,钻4—φ15孔时,若先钻1个孔,然后使工件回转90 度钻下一个孔,如此循环操作,直至把4个孔钻完。
则该工序中有 个工步, 个工位。
图1 工件13. 全年工艺成本中,与年产量同步增长的费用称为 ,如材料费、通用机床折旧费等。
14. 精加工阶段的主要任务是 。
15. 为了改善切削性能而进行的热处理工序如 、 、调质等,应安排在切削加工之前。
16.自位支承在定位过程中限制 个自由度。
17.工件装夹中由于 基准和 基准不重合而产生的加工误差,称为基准不重合误差。
18.在简单夹紧机构中, 夹紧机构实现工件定位作用的同时,并将工件夹紧;夹紧机构动作迅速,操作简便。
19.锥度心轴限制 个自由度,小锥度心轴限制 个自由度。
20.回转式钻模的结构特点是夹具具有 ;盖板式钻模的结构特点是没有 。
21.常用夹紧机构中的 是手动夹紧中应用最广泛的一种夹紧机构。
机械制造工艺学课程设计

机械制造工艺学课程设计滑动轴承座的机械加工工艺规程级:班学号:姓名:指导老师:机电及自动化学院20 年月日目录1.设计任务 (4)2.零件的分析 (4)2.1零件的作用 (4)2.2零件的工艺分析 (4)3.零件的生产类型 (5)3.1生产类型及工艺特征 (5)4.毛坯的确定 (5)4.1确定毛坯类型及其制造方法及技术要求 (5)4.2估算毛坯的机械加工余量 (5)5.定位基准选择 (6)5.1选择粗基准 (6)5.2选择精基准 (6)6.拟定机械加工工艺路线 (8)6.1选择加工方法 (8)6.2拟定机械加工工艺路线 (8)7.加工余量、机床、刀具及工序尺寸的确定 (10)7.1轴承座下底面的加工 (10)7.2轴承座上表面的加工 (11)7.3轴承座台阶面的加工 (11)7.3轴承座底面孔的 (12)7.4轴承座2×Φ13孔的加工 (12)7.5轴承座的轴承孔的加工 (13)7.6轴承座前后端面的加工 (14)7.7轴承座止口的加工 (15)8. 切削量的计算 (15)8.1轴承座下底面的加工 (15)8.2轴承座2×Φ13孔的加工切削量 (16)8.3镗孔的切削量 (17)8.4轴承座前后端面的加工 (17)8.5轴承座止口的加工 (18)9.时间的计算 (19)9.1磨削下底面 (19)9.2钻2×Φ13孔 (20)9.3镗孔时间 (22)9.4铣削的基本工时 (23)致谢 (24)参考资料 (25)前言机械制造工艺学课程设计是在学完了机械制造工艺学(含机床夹具设计)和大部分专业课,并进行了实习的基础上进行的一个教学环节。
这次设计使我们能综合运用机械制造工艺学中的基本理论,并结合生产实习中学到的实践知识,独立的分析和解决工艺问题,初步具备了设计一个中等复杂程度零件(主轴承盖)的工艺过程的能力和运用夹具设计的基本原理和方法,拟定加工工艺方案,完成零件机械加工工艺过程设计的能力,也是熟悉和运用有关手册、图表等技术及编写技术文件等技能的一次实践机会,形成规范解决问题的理念,为今后的毕业设计及未来从事的工作打下良好的基础。
机械制造工艺学计算题

六、计算题实例例1 各平面已加工,欲加工孔O,保证B和D,设W⊥N 试计算该定位误差。
解:尺寸B的设计基准为顶面M,而定位基准为底面N,基准不重合,△jb=TA △jw=0∴△DwB=△jw+△jb=0+TA=TA尺寸D的设计基准为右面,而定位基准为W面,基准不重合,△jb=T C△jw=0∴△DwD=TC例2一批轴件以平面定位铣键槽,试计算m和n尺寸的定位误差。
解:m尺寸因是平板定位且基准重合,△jb=0,△jw=0∴△Dwm=0 但是键槽会出现对称度误差(Td/2)。
n尺寸是平板定位但基准不重合,△jb= △jw=0∴△Dwn=Td/2,可见这是外圆母线位置的变化量。
例3一批直径为d±Td/2轴铣键槽,定位方式如图所示,V形块夹角为α,试计算m和n尺寸的定位误差。
解:工件以V形块定位,平板从下面夹紧。
m尺寸的工序基准是轴心线,基准重合,△jb=0 ,只有△jw。
n尺寸的工序基准是外圆下母线,除△jw外,还存在△jb。
计算题例3附图例4 一批工件以Φ20H7(+0.021~0)孔用Φ20g6(-0.007~-0.020)心轴定位,在立式铣床上铣键槽,其中Φ40h6(0~-0.016)外圆对内孔之径跳0.02,欲保证1)槽宽尺寸12h9;2)槽距端面尺寸20h12;3)槽底尺寸34.8h11(0~-0.21);4)槽两侧面对外圆轴线的对称度0.1;试分析定位误差。
计算题例4附图解:1)槽宽选相应的铣刀予以保证,无定位误差。
2)槽距尺寸因基准重合,平面定位,△Dw=0。
3)槽底尺寸因基准不重合△jb=Td0/2;又因为是间隙配合△jw=T D/2+Td/2 △Dw= Td0/2+ T D/2+Td/2∴△Dw= (0.016+0.021+0.013)=0.025<0.21×1/3 满足要求4)由于工件安装时可保证间隙只出现在单边,对称度误差主要受外圆对内孔的径跳影响。
∴△Dw对称=0.02<0.1×1/3 满足要求。
- 1、下载文档前请自行甄别文档内容的完整性,平台不提供额外的编辑、内容补充、找答案等附加服务。
- 2、"仅部分预览"的文档,不可在线预览部分如存在完整性等问题,可反馈申请退款(可完整预览的文档不适用该条件!)。
- 3、如文档侵犯您的权益,请联系客服反馈,我们会尽快为您处理(人工客服工作时间:9:00-18:30)。
机械制造专业(本科)《机械制造工艺学》课程设计目录目录11 绪论22 零件分析23 工艺规程设计33.1 确定毛坯的制造形成33.2 基面的选择33.3制定工艺路线33.4 机械加工余量、工序尺寸及毛坯的确定73.5确定切削用量及基本工时104 夹具设计254.1 问题的提出254.2夹具设计255 总结30参考文献错误!未定义书签。
致谢错误!未定义书签。
1 绪论2 零件分析题目所给的零件是机床尾座体,尾座安装在机床的右端导轨上,尾座上的套筒可以安装顶尖,以支承较长的工件的右端(即顶持工件的中心孔)、安装钻头、绞刀,进行孔加工,也可以安装丝锥攻螺纹工具、圆析牙套螺纹工具加工内、外螺纹。
尾座可以沿尾座导轨作纵向调整移动,然后压下尾座紧固手轮将尾座夹紧在所需位置,摇动尾座手轮可以实现对工件的顶紧、松开或对工件进行切削的纵向进给。
2.1 零件的特点由图可知,该零件为不太规则的部件,其主要技术特点如下:1.铸件需要消除毛刺和砂粒、并作退火处理2.φ17H6要求圆度为0.0033.φ17H6要求圆柱度0.0044.φ17H6与导轨面的平行度为0.0055.φ17H6与燕尾面的平行度为0.0056.φ17H6的孔轴心线与导轨面的位置度误差为0~0.17.φ17H6的孔与燕尾面的位置度误差不超过0.158.各面的粗糙度达到需要的要求9.φ17H6的孔需精加工、研配10.导轨面配刮10~13点/25⨯252.2 零件工艺分析根据零件图可知、主要进行导轨面的加工、孔加工和表面加工、钻孔、攻丝,孔的精度要求高。
该零件年生产5000件属大批量生产,在加工是为了提高劳动效率、降低成本,设计加工零件需要设计专用夹具。
3 工艺规程设计3.1 确定毛坯的制造形成由于该零件的形状较复杂,因此不能用锻造,只能用铸件,而且年生产批量为5000件已达成批生产的水平,采用批量造型生产。
根据零件主要的加工表面的粗糙度确定各表面加工余量,查参考文献查参考文献[2] 《机械加工工艺手册》,以后有计算在此就不重复了。
3.2 基面的选择基面的选择是工艺规程中的重要工作之一,基面的选择的正确与合理可以使加工的质量得到保证、生产效率得到提高;否则不但使加工工艺过程中的问题百出,更有甚者,还会造成零件大批报废,使生产无法正常进行。
粗基准的选择:对于象机床尾座这样的零件来说,选择好粗基准是至关重要的,能够保证零件的各种加工余量的选择。
对于一般零件而言,以加工面互为基准完全合理;但对于本零件来说,如果以17的孔为粗基准可能造成位置精度不达标,按照有关粗基准的选择原则(即当零件有不加工表面时,应以这些不加工面作为粗基准)现在选择不加工35的外圆表面和外表不加工面作为粗基准,利用一组两个锥套夹持两端作为主要定位面以消除五个不定度,再用一个支承板、支承在前面用以消除一个不定度,达到完全定位。
用来加工工件的底面。
对于精基准而言,主要应考虑基准的重合问题。
这里主要以已加工的底面为加工的精基准。
当设计基准与工序基准不重合时应该进行尺寸换算,后面对此有专门的计算这里就不重复了。
3.3制定工艺路线制定工艺路线的出发点应当是使零件的几何形状、尺寸精度及位置精度等技术要求能得到合理的保证。
在生产纲领已确定为批量生产的条件下,可以考虑采用万能机床配以专用夹具,并尽量使工序集中来提高生产率。
除此果之外,还应当考虑经济效,以便使用生产成本下降。
3.3.1 工艺路线方案一工序Ⅰ.铣削φ17H 的孔的两端面(粗铣、半精铣)工序Ⅱ.扩φ17H 的孔。
工序Ⅲ.倒角o451⨯工序Ⅳ.铣削孔φ14的端面、铣削M6的端面、粗铣最底面、粗铣导轨面、铣工艺面、铣削2⨯2的退刀槽、精铣导轨面、精铣燕尾面工序Ⅴ.铣削φ28的端面工序Ⅵ.钻φ14的孔、扩孔工序Ⅶ.镗削φ28的沉降孔工序Ⅷ.钻M6的孔、攻丝工序Ⅸ.精加工φ17的孔、研配工序Ⅹ.精加工导轨面配刮12—13点/25⨯25。
3.3.2 艺路线方案二工序Ⅰ.铣削φ17H 的孔的两端面(粗铣、半精铣)工序Ⅱ.粗刨导轨面工序Ⅲ.粗刨燕尾面工序Ⅳ.刨削导轨面的工艺台阶面工序Ⅴ.铣削2⨯2的退刀槽工序Ⅵ.精刨导轨面工序Ⅶ.精刨燕尾面工序Ⅷ.扩φ17的孔工序Ⅸ.铣削φ14的孔的端面工序Ⅹ.镗φ28的孔工序Ⅺ.研配φ17的孔工序Ⅻ.导轨配刮3.3.3.工艺方案的比较分析上述两方案的特点在于:方案一是先加工孔,然后以此孔为基准加工其它各处,而方案二是以导轨面为基准加工其它面,可以看出以先加工孔,以孔作为定位基准加工时位置精度较易保证,并且定位装夹等都比较方便,但是方案一中的一次装夹多道工序除了可以选用专用夹具设计的组合机床(但在成批生产是在普通机床上能保证精度的情况下,应尽量不选用专用机床)以外,只能选用多工位万能铣床加工。
而目前万能铣床的加工精度还不能加工导轨面的精度要求,因此决定将方案二中的工序ⅡⅢⅣⅤⅥⅦⅧⅨⅩⅪⅫ移入方案一,由于铣削时不能很好地加工燕尾处的75的斜面,因此在导轨面和燕尾的加工都采用刨削。
具体工艺过程如下:工序1.粗铣削φ17H6的孔的两端面工序2.精铣削φ17H6的孔的两端面工序3.钻φ17H6的孔工序4.扩φ17H6的孔工序5.惚o451⨯的倒角工序6.粗铣φ14的孔的端面工序7.半精铣φ14的孔的端面工序8.铣削M6的端面工序9. 粗刨燕尾底面工序10.粗刨轨面工序11.铣刨导轨面的工艺面工序12.铣削2⨯2的退刀槽工序13.精刨燕尾面工序14.精刨导轨面工序15.磨燕尾面工序16.磨导轨面工序17.钻φ14的孔工序18.扩φ14的孔工序19.钻M6的螺纹孔工序20.攻丝工序21.镗削φ28的沉降孔工序22.镗削17φ的孔工序23.镗削14φ的孔工序24.导轨面配刮工序25.精加工φ17H6的孔研配工序26.人工时效工序27.终检但考虑工序集中和铸件不适合热处理取消工序26,而且考虑工序集中,集中同一中加工的粗精加工。
具体的工序如下:工序1. 导轨面加工(粗、半精铣削导轨面及刨削导轨面的工艺面、精刨导轨面)工序2.燕尾面加工(粗刨、精刨燕尾面)工序3. 铣削φ17H6的孔的两端面(粗、精铣)工序4.孔加工(钻、扩、绞φ17H6的孔)工序5. 铣削φ14的孔的端面工序6.14的孔加工(φ14的孔钻、扩)工序7.铣削M6的端面工序8.钻孔(钻M6的螺纹孔)工序9. 惚451⨯ 的倒角工序10. 磨削(导轨面、燕尾面)工序11. 镗削(镗削φ28的沉降孔)工序12. 攻丝工序13. 导轨面配刮工序14. 珩磨:mm H 617φ工序15. 精加工φ17H6的孔研配工序16. 终检以上过程详见后面的工艺卡。
3.4 机械加工余量、工序尺寸及毛坯的确定“尾座体”零件的材料为HT200,生产类型为成批生产。
采用自由的砂型,3级精度(成批生产)。
根据上述原始质料及加工工艺,分别确定各加工表面的机械加工余量,工序尺寸及毛坯尺寸如下。
3.4.1 孔17φ的端面的不平度:m R Z μ240=、缺陷度:m 250μ=缺T 查参考资料[4] 《机械制造工艺与夹具设计指导》。
空间偏差:m 1700ρρ=毛 根据参考资料[4] 《机械制造工艺与夹具设计指导》铸造公差:m T μ2200= 查参考资料[4]《机械制造工艺与夹具设计指导》,按铸件宽度mm b 12=查得的宽度公差(1)粗铣余量加工精度:IT12,公差m mm T μ35035.0==查参考资料[4] 《机械制造工艺与夹具设计指导》加工表面粗糙度:3.6αR 查参考资料[4]《机械制造工艺与夹具设计指导》 铸件的加工余量为mm Y 6.21=,(2)精铣余量加工精度及表面粗糙度:要求达到m R μα3.6,公差mm T 005.0=,见图纸要求。
精加工的余量为mm Y 12=。
所以总的加工为 )(221Y Y MA +⨯= 式(3.1)mm 3.7)16.2(2=+⨯=3.4.2 内孔mm H 717φ毛坯为实心,不冲出孔。
内孔精度要求为6IT ,参考资料[4]《机械制造工艺与夹具设计指导》确定工序尺寸及加工余量为:钻孔:mm 15φ扩孔:mm 16φmm Z 121= 查参考资料[4]《机械制造工艺与夹具设计指导》 精镗:mm 9.16φmm Z 81.022= 查参考资料[4]《机械制造工艺与夹具设计指导》 细镗:mm 09.16φmm Z 08.023= 查参考资料[4]《机械制造工艺与夹具设计指导》 珩磨:mm H 617φmm Z 09.024= 查参考资料[4]《机械制造工艺与夹具设计指导》 表2.3-51总的加工余量为:mm Z Z Z Z Z 24321=++=+ 。
式(3-2)3.4.3 燕尾面加工考虑其加工长度为mm 90,与其联结的为导轨面,其精度相对较高,要进行粗加工、半精加工和精加工。
①粗加工:加工精度12IT 、铸件粗加工的余量mm Z 0.61=根据参考资料[4]《机械制造工艺与夹具设计指导》。
②半精加工:加工长度mm B 90=、加工宽度mm 100<,因此半精加工的余量选择mmZ 0.1=参考资料[4]《机械制造工艺与夹具设计指导》 表2.3-59。
③精加工: 加工长度mm B 90=、加工宽度mm 25<,因此精加工的余量选择mm Z 012.03=参考资料[4]《机械制造工艺与夹具设计指导》 表2.3-60总的加工余量mm Z Z Z Z 012.7321=++=。
式(3.3)3.4.4 导轨面刨削加工考虑其加工长度为mm 138,同样也是和导轨配合,其加工精度要求非常高,因此需要进行粗加工,半精加工和精加工。
①粗加工:加工精度选择12IT 选择加工余量mm Z 5.5=②半精加工:加工长度mm B 138=、加工宽度mm k 100=,因此加工余量选择mm Z 0.1= 。
由参考资料[4]《机械制造工艺与夹具设计指导》 表2.3-59③精加工:加工长度mm B 138=、加工宽度mm k 90=,因此精加工的余量选择mm Z 022.03=由参考资料[4]《机械制造工艺与夹具设计指导》表2.3-60总的加工余量由式3-3得:mmZ 522.6=总。
3.4.5 孔14φ的内径表面毛坯为实心,不冲出孔。
内孔精度要求不太高,参考参考资料[2]《机械加工工艺手册》确定工序加工尺寸及余量为:钻孔:mm 8.12φ扩孔:mm 14φmm Z 2.12= (查参考资料[2] 《机械加工工艺手册》表2.3-48) 7.M6的孔加工公称直径mm 6,加工前的钻孔直径mm 5 (查参考资料[2] 《机械加工工艺手册》表2.3-71) 因此钻孔的加工余量为:mm Z 1=。
3.5确定切削用量及基本工时3.5.1铣削φ17H6的孔的两端面。