产品生产过程审核标准
生产通过或失败的判定标准
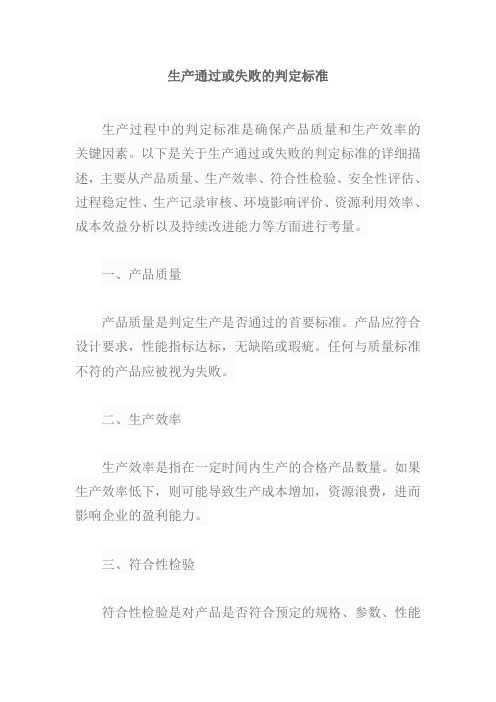
生产通过或失败的判定标准生产过程中的判定标准是确保产品质量和生产效率的关键因素。
以下是关于生产通过或失败的判定标准的详细描述,主要从产品质量、生产效率、符合性检验、安全性评估、过程稳定性、生产记录审核、环境影响评价、资源利用效率、成本效益分析以及持续改进能力等方面进行考量。
一、产品质量产品质量是判定生产是否通过的首要标准。
产品应符合设计要求,性能指标达标,无缺陷或瑕疵。
任何与质量标准不符的产品应被视为失败。
二、生产效率生产效率是指在一定时间内生产的合格产品数量。
如果生产效率低下,则可能导致生产成本增加,资源浪费,进而影响企业的盈利能力。
三、符合性检验符合性检验是对产品是否符合预定的规格、参数、性能标准等进行检验的过程。
任何不符合要求的产品都应被视为失败。
四、安全性评估安全性评估主要是评估产品在使用过程中可能对用户或环境产生的风险。
任何可能带来安全隐患的产品都应被视为失败。
五、过程稳定性过程稳定性是指生产过程中工艺参数的稳定性和一致性。
如果生产过程中出现频繁的波动或异常,可能会导致产品质量下降或生产效率降低。
六、生产记录审核生产记录审核是对生产过程中各项数据和记录的审核,以确认生产过程的可追溯性和可靠性。
任何不符合记录要求的生产批次都应被视为失败。
七、环境影响评价环境影响评价主要是评估生产过程对环境的影响,如废气、废水、固体废弃物的排放等。
任何对环境造成不良影响的生产过程都应被视为失败。
八、资源利用效率资源利用效率是指生产过程中对原材料、能源和水等资源的利用效率。
高效的资源利用可以降低生产成本,减少资源浪费。
低效的资源利用可能会导致成本增加,对环境造成负面影响。
九、成本效益分析成本效益分析主要是评估产品的制造成本与销售收益之间的关系。
如果产品的制造成本过高,可能会导致企业盈利能力下降。
因此,成本效益分析也是判定生产是否通过的重要标准之一。
十、持续改进能力持续改进能力是指企业是否有能力在生产过程中发现问题并及时采取措施进行改进。
IATF16949制造过程审核细则

制造过程审核细则(IATF16949-2016)在产品制造过程的每道工序中,必须使所策划的和已落实的过程的技术和人员素质达到要求,加以监控并从经济的角度进行持续改进。
员工素质、过程设备和检测器具的适用与改进、与所生产零件的特性相适应的运输和储存是制造过程审核的重点。
1人员/素质选择具备相应岗位素质的人员,使其保持应有的素质以及进一步培养成具有更高岗位素质的人员,这是管理者的任务。
必须对员工是否具备承担过程任务的素质进行验证。
1.1员工监控产品质量和过程质量情况1.1.1为提高产品质量和过程质量,不断改进,员工应具备质量改进的意识。
1.1.2自检情况。
1.1.3坚持设备点检情况。
1.1.4首件检查和末件检查情况。
1.1.5掌握过程的工艺要求以及理解控制图,达到应知应会要求。
1.1.6零件不能满足要求时的处理是否按有关规定执行。
1.2员工对生产设备和生产环境的职责和权限1.2.1生产设备和环境应保持整齐和清洁。
1.2.2员工应对生产设备进行日常的维修与保养,出现故障时应及时报修。
1.2.3零件、工装按规定贮存。
1.2.4按时报请对检测、试验设备的检定和校准。
1.3为了完成所交付的任务员工应具备的素质1.3.1操作者应经过培训并持有有效操作证书上岗。
1.3.2员工应熟悉产品技术要求。
1.3.3具有安全生产和生产环境要求的意识。
1.3.4具有特殊工序工艺验证方面的知识。
1.4顶岗人员的配置计划在人员配置计划中要考虑缺勤因素(如病假、休假、培训)。
对顶岗人员也要确保所需的素质。
1.5有效地使用了提高员工工作积极性的方法通过针对性的信息宣传,促进员工工作的主动性,并以此来提高质量意识。
1.5.1经常发布质量信息,使员工了解质量现状。
(有目标值和实际值)1.5.2产品质量改进的合理化建议和“六小”活动的开展情况。
1.5.3员工参加培训和质量小组的积极性。
1.5.4病假率低。
1.5.5员工对质量改进的效果。
1.5.6员工具有自我评定的意识。
过程审核评分等级标准

过程审核评分定级标准一、评分根据对提问的要求以及在产品批量生产过程中满足该要求的情况,对提问进行评定。
每个提问的得分可以是0、4、6、8或10分,满足要求的程度是打分的根据。
评定不满6分(包括6分)必须制订改进措施,确定责任人并落实期限。
过程要素符合率P n [%]的计算公式如下:各相关问题实际得分的总和×100P n[%]=各相关问题满分的总和每个生产线总符合率P的计算公式如下:P1+P2+P3+…+P nP[%]=被评定工序的数量二、定级注*:1.若任何一项提问得分为零,而不符合要求可能会给产品质量和过程质量造成严重的影响,则可把被审核部门从A级降到B级或从B级降到C级。
2.若被审核的部门的总符合率超过90%,但其在任何两个或以上提问的符合率只达到6分(60%)或以下,则必须从A级降到B级。
3.必须在审核报告中说明降级的原因。
文案编辑词条B 添加义项 ?文案,原指放书的桌子,后来指在桌子上写字的人。
现在指的是公司或企业中从事文字工作的职位,就是以文字来表现已经制定的创意策略。
文案它不同于设计师用画面或其他手段的表现手法,它是一个与广告创意先后相继的表现的过程、发展的过程、深化的过程,多存在于广告公司,企业宣传,新闻策划等。
基本信息中文名称文案外文名称Copy目录1发展历程2主要工作3分类构成4基本要求5工作范围6文案写法7实际应用折叠编辑本段发展历程汉字"文案"(wén àn)是指古代官衙中掌管档案、负责起草文书的幕友,亦指官署中的公文、书信等;在现代,文案的称呼主要用在商业领域,其意义与中国古代所说的文案是有区别的。
在中国古代,文案亦作" 文按 "。
公文案卷。
《北堂书钞》卷六八引《汉杂事》:"先是公府掾多不视事,但以文案为务。
"《晋书·桓温传》:"机务不可停废,常行文按宜为限日。
" 唐戴叔伦《答崔载华》诗:"文案日成堆,愁眉拽不开。
化妆品生产一致性审核管理制度

化妆品生产一致性审核管理制度一、总则为了保障化妆品生产的一致性,提高产品质量,确保产品的安全性和有效性,特制定本管理制度。
本管理制度适用于本公司在化妆品生产过程中的一致性审核管理。
二、审核范围本管理制度涉及的审核范围包括但不限于以下内容:1.生产过程的一致性审核;2.质量控制和管理的一致性审核;3.安全性和有效性的一致性审核;4.相关法律法规和标准的一致性审核。
三、一致性审核程序1.确定审核对象:确定需要进行一致性审核的生产过程或管理流程;2.制定审核计划:编制一致性审核计划,明确审核的目的、范围、方法和时间表;3.组织审核团队:确定审核团队成员,确保审核团队具有相关的专业知识和经验;5.整理审核结果:整理审核结果,对审核情况进行总结和评价;6.提出改进建议:根据审核结果,提出改进建议,对存在的问题和不足进行整改。
四、一致性审核要求1.生产过程的一致性审核要求:生产过程应符合相关的标准和规范要求,所有操作应按规定进行,确保产品的质量和安全性;2.质量控制和管理的一致性审核要求:质量控制和管理要有完善的体系和程序,确保产品符合质量标准;3.安全性和有效性的一致性审核要求:产品的安全性和有效性应经过严格审核和检测,确保对消费者的安全和有效性;4.法律法规和标准的一致性审核要求:生产过程和产品要符合相关的法律法规和标准要求,确保合法合规。
五、监督和改进1.监督审核结果:建立监督机制,对审核结果进行监督和跟踪,确保改进措施的有效实施;2.定期评估一致性审核制度:定期评估一致性审核制度的实施情况和效果,及时调整和改进;3.持续改进:根据持续改进理念,不断优化一致性审核管理制度,提高审核效率和质量。
总之,本化妆品生产一致性审核管理制度旨在保障产品质量,确保产品的安全性和有效性,提高公司的竞争力和可持续发展能力。
公司相关部门和人员应严格遵守本制度的规定,认真执行一致性审核,做好产品的管理和监督工作,不断提高产品质量和客户满意度。
IATF16949制造过程审核细则

制造过程审核细则(IATF16949-2016)在产品制造过程的每道工序中,必须使所策划的和已落实的过程的技术和人员素质达到要求,加以监控并从经济的角度进行持续改进。
员工素质、过程设备和检测器具的适用与改进、与所生产零件的特性相适应的运输和储存是制造过程审核的重点。
1人员/素质选择具备相应岗位素质的人员,使其保持应有的素质以及进一步培养成具有更高岗位素质的人员,这是管理者的任务。
必须对员工是否具备承担过程任务的素质进行验证。
1.1员工监控产品质量和过程质量情况1.1.1为提高产品质量和过程质量,不断改进,员工应具备质量改进的意识。
1.1.2自检情况。
1.1.3坚持设备点检情况。
1.1.4首件检查和末件检查情况。
1.1.5掌握过程的工艺要求以及理解控制图,达到应知应会要求。
1.1.6零件不能满足要求时的处理是否按有关规定执行。
1.2员工对生产设备和生产环境的职责和权限1.2.1生产设备和环境应保持整齐和清洁。
1.2.2员工应对生产设备进行日常的维修与保养,出现故障时应及时报修。
1.2.3零件、工装按规定贮存。
1.2.4按时报请对检测、试验设备的检定和校准。
1.3为了完成所交付的任务员工应具备的素质1.3.1操作者应经过培训并持有有效操作证书上岗。
1.3.2员工应熟悉产品技术要求。
1.3.3具有安全生产和生产环境要求的意识。
1.3.4具有特殊工序工艺验证方面的知识。
1.4顶岗人员的配置计划在人员配置计划中要考虑缺勤因素(如病假、休假、培训)。
对顶岗人员也要确保所需的素质。
1.5有效地使用了提高员工工作积极性的方法通过针对性的信息宣传,促进员工工作的主动性,并以此来提高质量意识。
1.5.1经常发布质量信息,使员工了解质量现状。
(有目标值和实际值)1.5.2产品质量改进的合理化建议和“六小”活动的开展情况。
1.5.3员工参加培训和质量小组的积极性。
1.5.4病假率低。
1.5.5员工对质量改进的效果。
1.5.6员工具有自我评定的意识。
产品审核和过程审核讲解

产品审核和过程审核讲解产品审核和过程审核是企业质量管理体系中非常重要的两个环节,通过对产品和过程的审核,可以确保产品质量的稳定和过程的规范,提高企业的竞争力和市场认可度。
本文将从定义、流程、方法和意义等方面对产品审核和过程审核进行详细讲解。
一、产品审核产品审核是对生产过程中生产的产品进行评估,以确定其符合质量标准和客户要求的程度。
产品审核的目的是确保产品质量的稳定和持续改进,并为客户提供满意的产品。
产品审核的流程通常包括以下几个步骤:1.确定审核范围:根据产品的特性和客户需求,确定需要审核的内容和要求。
2.收集产品信息:收集产品的相关信息,包括制造过程、原材料使用情况、质量控制措施等。
3.评估产品符合性:根据产品标准和客户要求,对产品进行评估,确定是否符合质量要求。
4.记录审核结果:记录审核的过程和结果,包括发现的问题、改进措施等。
5.制定改进计划:根据产品审核结果,制定改进计划,对问题进行分析和解决,以提高产品质量。
产品审核的方法有很多种,常用的包括:检查法、抽样法、测量方法等。
其中,检查法是最常用的方法,通过对产品进行外观检查、功能测试等方式,对产品的质量进行评估。
产品审核的意义在于保证产品质量的稳定和改进,提高客户满意度,增加市场竞争力。
通过对产品进行审核,及时发现和解决问题,避免产品质量不达标而给企业带来的经济损失和声誉损害。
二、过程审核过程审核是对企业生产过程中各个环节的评估,以确定其是否符合质量管理体系的要求和规范。
过程审核的目的是确保生产过程的规范化和稳定性,提高产品质量的可靠性和一致性。
过程审核的流程通常包括以下几个步骤:1.确定审核范围:根据企业的生产过程和质量管理体系的要求,确定需要审核的过程和环节。
2.收集过程信息:收集过程的相关信息,包括操作规程、工艺参数、机器设备等。
3.评估过程符合性:对过程进行评估,确定是否符合质量管理体系的要求和规范。
4.记录审核结果:记录审核的过程和结果,包括发现的问题、改进措施等。
产品审核的实施流程和步骤
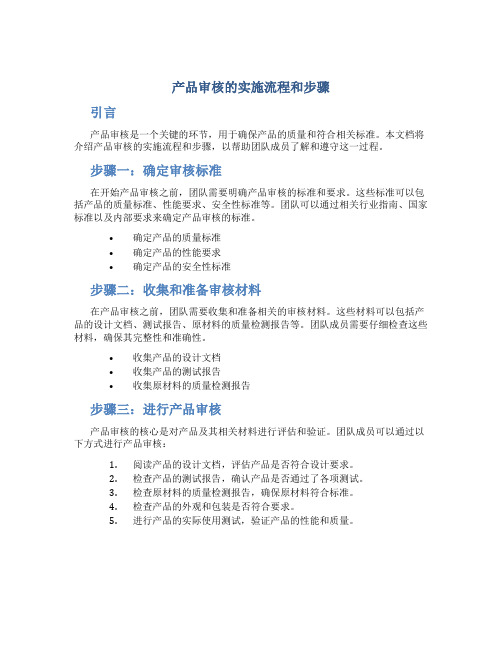
产品审核的实施流程和步骤引言产品审核是一个关键的环节,用于确保产品的质量和符合相关标准。
本文档将介绍产品审核的实施流程和步骤,以帮助团队成员了解和遵守这一过程。
步骤一:确定审核标准在开始产品审核之前,团队需要明确产品审核的标准和要求。
这些标准可以包括产品的质量标准、性能要求、安全性标准等。
团队可以通过相关行业指南、国家标准以及内部要求来确定产品审核的标准。
•确定产品的质量标准•确定产品的性能要求•确定产品的安全性标准步骤二:收集和准备审核材料在产品审核之前,团队需要收集和准备相关的审核材料。
这些材料可以包括产品的设计文档、测试报告、原材料的质量检测报告等。
团队成员需要仔细检查这些材料,确保其完整性和准确性。
•收集产品的设计文档•收集产品的测试报告•收集原材料的质量检测报告步骤三:进行产品审核产品审核的核心是对产品及其相关材料进行评估和验证。
团队成员可以通过以下方式进行产品审核:1.阅读产品的设计文档,评估产品是否符合设计要求。
2.检查产品的测试报告,确认产品是否通过了各项测试。
3.检查原材料的质量检测报告,确保原材料符合标准。
4.检查产品的外观和包装是否符合要求。
5.进行产品的实际使用测试,验证产品的性能和质量。
步骤四:记录审核结果在完成产品审核后,团队需要记录审核结果。
这些记录可以包括通过的产品、未通过的产品以及审核过程中发现的问题和改进意见。
这些记录将有助于团队跟踪产品审核的过程,以及改进产品的质量和性能。
•记录通过的产品•记录未通过的产品•记录审核过程中发现的问题和改进意见步骤五:处理审核结果根据产品审核的结果,团队需要采取相应的行动。
对于通过审核的产品,团队可以继续推进产品的生产和销售;对于未通过审核的产品,团队需要分析问题的原因,并制定改进措施。
团队还可以根据审核结果,更新产品的设计文档、测试方法和质量标准。
•推进通过审核的产品的生产和销售•分析未通过审核的产品的问题原因•制定改进措施•更新产品的设计文档、测试方法和质量标准结论产品审核是一个关键的环节,可以确保产品的质量和符合相关标准。
过程审核的规定及流程

目录
❖ 1. 体系审核、过程审核和产品审核的关系 ❖ 2. 过程审核的规定 ❖ 3. 审核流程 ❖ 4. 审核准备 ❖ 5. 实施审核 ❖ 6. 评分与定级 ❖ 7. 末次会议 ❖ 8. 纠正措施及其有效性验证 ❖ 9. 审核报告及存档 ❖ 10.过程审核提问表
ISO/TS16949:2002
ISO/TS16949:2002
常州明飞企业管理咨询有限公司 张爱明
❖ 由于不同的企业其评定范围和目标要求可能不 同,有时需要对总符合率(百分率)定级的界 限以及级别名称进行调整。可以使用定性的评 定方法,也可以只对个别的过程要素进行评定 。但上述这些不同的评定方法(例如:定性评 定方法)必须由供方和顾客协商确定并在审核 报告中注明。
这有助于限制缺陷起因并采取纠正措施。
❖
计划外过程审核的起因可能是,例如:
❖
—产品质量下降
❖
—顾客索赔及抱怨
❖
—过程不稳定
❖
—强制降低成本
ISO/T❖S16949:2002 —内部部常门州明的飞企愿业望管理。咨询有限公司 张爱明
❖ 2.3 应用范围
❖
在内部和外部可以在整个质量控制环的下列部门运用过程审
❖ 这些前期的工作是制订审核提问表的重要基础。
ISO/TS16949:2002
常州明飞企业管理咨询有限公司 张爱明
❖ 另外,审核员和被审核企业还要了解确定过程审核框 架条件的一些相关文件。框架条件例如:
❖ —组织规定 ❖ —责任分工。 ❖ 确定框架条件的相关文件,例如:
❖ —质量手册 ❖ —程序文件 ❖ —TS丛书 ❖ —标准 ❖ —顾客要求。
❖ 针对项目的审核
❖
在项目开发和策划过程中及早地在确定的项目分界
产品审核、过程审核标准

产品审核不合格权数缺陷级别A B C D 等效缺陷数(加权值)10050101产品审核用产品质量不合格严重性分级表缺陷级别/加权分值对性能功能影响对外观质量影响对包装质量影响对后序和顾客影响社会和经济影响A类致命缺陷/100肯定致命影响产品性能、功能和安全,造成事故和索赔外观缺陷严重而明显,顾客会发现和投诉错、漏装零件,包装丧失功能导致产品损坏,顾客会投诉肯定会引起严重混乱产品安全责任B类严重缺陷/50可能严重影响产品性能、功能和安全,可能造成事故,顾客不满外观缺陷较明显,顾客可能会发现和投诉包装会导致产品质量损失,如表面损坏、锈蚀,可能会引起顾客投诉可能会引起严重混乱,但肯定会引起一般混乱顾客投诉和经济赔偿C类一般缺陷/10可能一般影响产品性能、功能和安全,不会造成事故和索赔缺陷可能会被发现,但不会被投诉包装缺陷可能影响应有的产品功能,但顾客不会投诉可能引起一般或次要混乱信誉和经济损失D类轻微或次要缺陷/1几乎不影响产品性能、功能和安全几乎不会被顾客发现或不被介意几乎不会被发现和介意不会引起任何混乱轻微经济损失抽样。
生产线随机抽样批数量N 样本量nN<100 3目标质量指数:80﹪(依据以往产品检验结果分析和顾客反馈信息确定)。
产品审核用产品质量处理准则缺陷发现处理措施轻微缺陷/ 由相关部门或责任人对缺陷品进行纠正,如返工或返修,对产品做让步放行处理一般缺陷由相关部门或责任人对缺陷品进行纠正,如返工或返修,适当时可对产品做让步放行处理或100﹪检验严重缺陷/ 应对产品做100﹪全检,接收合格者,并由相关部门或责任人对缺陷品进行纠正,如返工或返修,产品在彻底整改前不允许放行或做让步放行致命缺陷发现关键缺陷或质量指数低于80﹪,应对产品做100﹪全检,接收合格者,并由相关部门或责任人对缺陷品进行纠正,如返工或返修,并分析原因采取进一步纠正措施,产品在彻底整改前不允许放行或做让步放行≥1.33过程能力指数:Cpk过程定级表总符合率,% 对过程的评定 级别名称 86~100 符合,具有质量能力 A71~85 绝大部分符合,有条件的质量能力 B0~70 不符合,不具有质量能力 C说明:出现单个或多个要素符合率低于75%或有的问题得分为零且后果严重时,A级应降为B级或C级。
制造过程审核的核查内容

制造过程审核的核查内容
制造过程审核是指对整个制造过程进行检查、核实和评估,以确保产品的质量、安全和符合规定的要求。
下面是制造过程审核中需要核查的内容:
1.工艺流程:审查并确认工艺流程是否正确,是否满足产品质量要求,是否符合法规和标准的要求。
2.设备和工具:检查生产设备和工具是否符合规定,是否能够满足产品生产的要求,并保证设备和工具的使用安全。
3.物料和零部件:核查使用的物料和零部件是否符合规定的质量标准,是否具有合格证明,是否符合产品的技术要求。
4.操作程序:检查操作程序是否规范,是否符合产品要求和工艺流程要求,是否有好的记录和文档。
5.人员培训:确认员工是否接受了必要的培训,是否具备生产所需的技能和知识,是否能够正确操作设备。
6.质量控制:核查质量控制措施是否有效,是否能够保证产品符合质量标准,是否有好的记录和文档。
7.环境和安全:检查生产环境和工作安全是否符合相关法规和标准,是否能够保障员工的生命安全和身体健康。
综合以上内容,制造过程审核旨在确保产品生产的全过程符合相关法规和标准的要求,保证产品的质量和安全,提高企业运营效率和产品竞争力。
- 1 -。
001 过程审核规定要求与解释

一.过程审核流程与内容
A产品诞生过程B批量生产
(a) 产品开发(设计)
■1产品开发的策划
■2产品开发的落实 (b)过程开发
■3过程开发的策划
■4程开发的落实■5供方/原材料
■6生产(对每一工序的评定)
■人员/素质
■生产设备 / 工装
■运输/搬运/贮存/包装
■缺陷分析/纠正措施/持续改进■7服务/顾客满意程度
二.提问和过程要素的单项评分和总体等级
根据对提问的要求以及在产品诞生过程(服务诞生过程)和批量生产(实施服务)中满足该要求的情况对提问进行评定。
每个提问的得分可以是0、4、6、8或10分,满足要求的程度是打
过程要素符合率E
E
的计算公式如下:
E
E
[%]= 各相关问题实际得分的总和/各相关问题满分的总和×100%
说明
1.若总符合率超过90%或80%,但其中在一个或多个要素上符合率只达到75%以下,则必须从A级降到AB级或从AB级降到B级。
2.若有的提问得分为0分,而不符合要求可能会给产品和过程质量造成严重的影响,则可以从A级降到AB级或从AB级降到B级。
在特别情况下,也可降到C级。
3.必须在结果说明中说明降级的原因。
三.流程详细要求与解释:
内容见下页。
VDA6.3过程审核标准P6要素

VDA(德国汽车工业联合会)的 构成
13家整车厂(如大众、奔驰、宝马等) 75家服务商; 490家零件供应商(如博世、采埃孚、 大陆、麦格纳等)
VDA 质量手册的编制成员
8家整车(大众有4家、宝马、戴姆勒等) 8家供应商(如博世、大陆等代表服务商和供应商) 2家组织(VDA与VDA-QMC)
Page 2
2)考虑客户对产品放行的特殊要求。
3)确保放行的材料/零部件被提供给下道工序(避免误用不良件、待确认件等)。 4)须在合理的框架范围内,确保所生产的产品的可追溯性(如:批次使用记录),据产品风险,须在从供应 商到客户之间整条过程链上确保可追溯性。
5)须考虑可追溯性标记方面的客户要求;售后市场零件的标识;考虑法律法规及产品责任法的要求。
3)仓储位置/加工工位/容器须达到产品整洁/干净/防撞击等的要求。
4)须明确特殊材料/零部件的仓储时间及使用有效期(如:最长、最短仓储时间;据不同的供货周期,定义不 同的库存量;案例:整车一般2周、零部件为1个月、钢材/注塑材料为半年甚至更长)。
5)机器/设备所需的关键生产资料和辅料,若对产品或产品质量有直接影响,须加以监控。
须不断提高自己的专业能力;并与所处专业领域内最新的发展始终保 持同步。(可参加论坛、专家培训/指导、供应商经验交流等方式)
一、VDA6.3标准简介
5、VDA6.3架构
A部分:开发
B部分:批量生产
P2:项目管理(7) P3:产品和过程开发的策划(5) P4:产品和开发过程的实现(9)
P5:供应商管理(7) P6:过程分析/生产(26) P7:客户关怀/客户满意度/服务(6)
6)质量检验方案与客户要求/同客户的约定相一致。
Page 22
VDA过程审核要求条例

值 ❖ 环保观点 ❖ 各有关部门的介入 ❖ 试验结果 ❖ 由过程P-FMEA导出的产品特定措施
1.2.2设计FMEA是否在项目过程中补充更新, 符合现状?并且,已确定的措施是否已落实?
对产品和过程的更改必须由项目负责人 进行评定,在与FMEA小组商讨后,必要时 须进行新的分析。在措施落实后也要求补充 更新,使其符合现状(设计审查)。
1.1.2是否具有产品开发计划,并坚持 目标值?
要点: ➢ 顾客要求 ➢ 成本 ➢ 时间表:策划认可/采购认可,更改停止,样
车样件/试生产,批量生产开始 ➢ 定期向企业领导汇报 ➢ 同步工程小组(SET)
1.1.3是否规划了用于落实产品开发的 开发能力规模?
所要求的开发能力规模必须在报价阶段 已调查并考虑到了。在正式委托后,这些数 据须精确化。在要求更改时,如有必要,须 做开发能力模拟调查的相应变更。必备的资 源规划并备齐:
1.1.4是否了解/考虑到了对产品的要求?
通过各科间的相互合作/行业水准比较以 了解产品的要求,例如:有QFD(质量功能展 开),DOE(实验设计)等方法。至今的经验 与未来的期待必须予以考虑。对产品的要求 必须相应于市场要求与顾客期望,产品必须 有竞争力。
1.1.4是否了解/考虑到了对产品的要求?
1.2.1是否已进行了设计D-FMEA,并确 定了改进措施?
通过各科间的合作及与顾客、配套厂的 合作,了解清楚产品风险,并用合适的措施 不断低产品风险,对于复杂零部件或整套功 能系统,使用系统S-FMEA(参见VDA第4册, 第1,第2部分)很有意义,其它类似的分析 技术的应用,可与顾客商定。
1.2.1是否已进行了设计D-FMEA,并确 定了改进措施?
产品审核、过程审核推荐标准
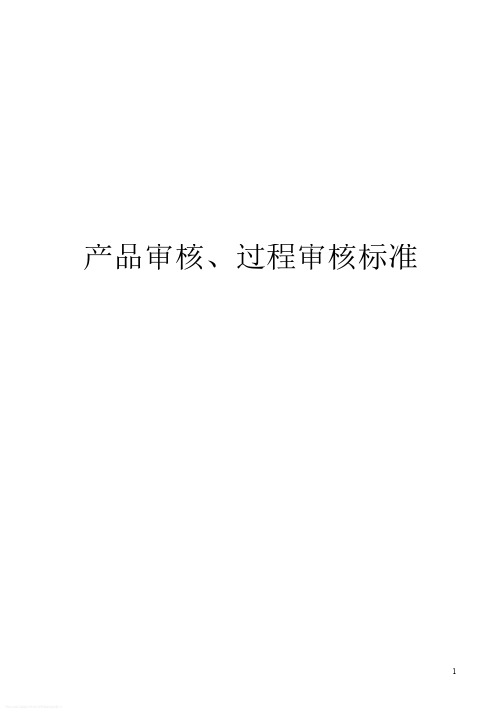
产品审核、过程审核标准一、供应商质量能力审核1 2 范围本标准规定了供应商质量能力审核评价方法及评级原则、审核要素、审核报告等内容。
本标准适用于中国一汽红旗品牌汽车零部件供应商质量能力审核,其它自主品牌整车公司汽车零部件供应商质量能力审核可参照执行。
审核要素对供应商质量能力审核分为以下三个要素:供应商管理;生产过程控制;顾客关怀、顾客满意度、服务。
3 评价方法及评级原则3.1 评价方法依据现场审核、资料查阅、双方沟通等确认的结果,按审核要素评价打分。
3.2 评级原则3.2.1 审核要素评分原则3.2.1.1 单项要素评分原则单项要素评分原则见表1。
表1 单项审核要素评分原则序号分数单项审核要素的符合程度1 2 3 4 5 108完全符合要求绝大部分*符合要求;小的偏差部分符合要求;大的偏差符合程度不足;严重偏差不符合要求64对“绝大部分”应理解是,有效的符合大于3/4的要求,没有特别的风险。
3.2.2.2 单项要素(E)审核符合率计算方法E审核要素的实得分E [%]=E×100% 该审核要素的满分3.2.2.3 审核要素的符合率供应商管理(E ),生产过程控制(E ),顾客关怀、顾客满意、服务(E )。
由于各个产品组具 Z PGK 有不同的工序,对于“生产过程控制”这个要素的评价必须将不同工序的评价结果汇总起来从而得到 E 。
要素供应商管理(E )和顾客关怀、顾客满意、服务(E )将各自得到评分。
PGZ K 3.2.2.4 生产过程控制审核要素的计算方法对每一道工序进行审核,根据产品组将各道工序的审核结果汇总起来,确保各个要素的同等重要 性。
因此,在“生产过程控制”这个大组中,对具体的产品组来说,由于工序是每一次审核时选定的, 故得到的符合率可能相同。
每个产品组的平均值E 的计算方法:PG E1+ E2+…+EnE [%]= PG ×100%已评价的工序数其中,E1和En 分别为各产品组生产的第一道工序和最后一道工序的单项要素(E )审核符合率。
电子产品生产厂商质量验收标准

电子产品生产厂商质量验收标准电子产品的生产过程中,厂商需要经过一系列的质量验收程序来确保产品的质量达到标准要求。
本文将介绍电子产品生产厂商常用的质量验收标准,以及验收的相关内容。
一、产品外观检验产品外观是消费者直接接触到的第一印象,因此良好的外观质量对于产品的销售非常重要。
厂商在质量验收中通常会对产品的外观进行检验,包括外壳的外观缺陷、表面光洁度、尺寸精度、标识和标志等。
1. 外观缺陷:对产品外观是否存在划痕、裂纹、变形等缺陷进行检查,并记录缺陷情况及数量。
2. 表面光洁度:通过观察产品表面是否光滑、无杂质、无气泡、无刮痕等,评估产品的表面光洁度。
3. 尺寸精度:根据产品设计要求,测量产品的各项尺寸,确保其在允许范围内。
4. 标识和标志:检查产品上的标识和标志是否齐全、清晰可见,并与产品技术规格进行比对。
二、功能性测试产品的功能性是其最基本的要求,因此在质量验收中进行功能性测试非常重要。
常见的功能性测试包括性能测试、耐久性测试、可靠性测试等。
1. 性能测试:测试产品在正常工作环境下的各项性能指标,如功耗、速度、分辨率、存储容量等。
2. 耐久性测试:通过模拟产品的正常使用情况,测试其在长时间使用后是否能够保持正常工作。
3. 可靠性测试:通过对产品进行环境适应性测试、振动测试、温度测试等,评估产品在各种环境条件下的可靠性和稳定性。
三、安全性检验对于电子产品而言,安全性是一个重要的考量指标。
在质量验收中,厂商通常会对产品的安全性进行检验,以确保产品在正常使用过程中不会对用户造成伤害。
1. 电气安全性:测试产品的电气性能是否符合相关安全标准,如电流、电压、绝缘电阻等。
2. 辐射安全性:测试产品在正常使用情况下是否会产生辐射,并确保辐射水平在允许范围内。
3. 材料安全性:对产品使用的材料进行测试,确保不含有有害物质,符合环保要求。
四、质量管理体系审核除了对产品本身进行验收外,厂商还需要通过质量管理体系审核来验证其质量管理体系是否符合相关标准要求。
VDA6.3过程审核标准简介
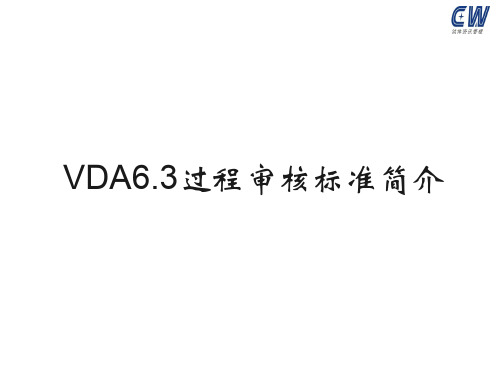
VDA 6.3—2016 过程审核条款
条例P1 – 潜力分析
使用评价表,进行评分(红灯、黄灯、绿灯); 最多只能有3个问题可以不进行评审 (nb), 需说明原因
说明结果,并且出具报告 封页 (说明结果) 评价表; 偏差以及潜力列表(改进计划); 描述生产场所(布局、过程步骤、设备、经验、参考„) 供方自评结果,等。
超过14个提问
1个提问
有条件批准
最多14个提问
无
批准的供方
最多7个提问
无
文件链接:潜力分析报告样张
过程审核评价--打分原则(单个提问)
评分
产品风险
过程风险
与质量管理体系 的相关性
10
•满产足品技没术有要任求何缺陷,•程规满的范足技涵术盖要产求品/技和术过
•记录显示在生产实践中落实了质 量管理体系
•达到了目标要求
审核结果的综合评分计算方法
过程各要素(P2,P3,.. P7)符合率Ee计算公式如下:
各相关问题实际得分的总和 Ee(%)= ------------------------------------- × 100%
各相关问题满分的总和
举例:P2共有7个审核提问,得分为:4,6,4,8,6,4,6 P2综合得分:
过程要素 P2 项目管理 P3 产品和过程研发的策划 P4 产品和过程研发的实现 P5 供应商管理 P6 批量生产 (P6.1- P6.6) P7 客户支持,客户满意度,服务
审核提问 (2010) 7 5 9 7 26 6
总共 :
60
审核提问 (2016) 7 5 8 7 26 5
58
VDA6.3 过程要素及审核
级别名称
A
B
VDA6.3-2016过程审核条款要求

在资源规划中,要特别留意关键路径。
针对人员和设备(例如测试和实验室设备等)方面必要的项目预算,进行了规划并审批通过。
项目组织机构(与顾客接口)的变更必须进行通报。
2.3
X
是否编制项目计划,并且与顾客协调一致?
项目计划满足顾客的具体要求。 所有内部里程碑以及顾客里程碑都被完整地纳入项目计划。 在项目计划中所定义的里程碑时刻开展评审,以确认所有计划的事项都得到实施,相对应的成熟度等级得到落实。 产品如有特殊的法规方面的认证/批准要求,那么该认证/批准程序要包括在项目策划中。 要确保内部对于项目计划变更的联络沟通。对于影响到顾客的项目计划变更,要同顾客协商沟通并达成一致。 关键路径体现于项目计划,顾及到关键的零件范围。
P4 产品和过程开发的实现 产品和过程开发计划中确定的事项是否得到落 实?
在开发策划中确定的产品和过程开发的方法得到了应用,从而基于经验的积累,量产的产品能够满足使用要求(功能、可 靠性、安全性)。
在开发阶段,必须利用风险分析(例如FMEA)来确保产品和过程在功能、可靠性等方面符合顾客的要求。在做风险分析 (例如产品FMEA)时,涉及的生产工厂必须参与其中。
3.3 3.4 3.5 4.1 * X
是否具有产品和过程开发事项的详细计划?
产品和过程开发策划的详细程度取决于零部件、软件以及过程的复杂程度。 在开发阶段,必须采用合适的方法,为产品和过程开发提供保证,使得产品在量产时能够满足使用条件(功能,可靠性, 安全性)。这点必须在策划时予以考虑。 风险分析(产品FMEA和过程FMEA,或其他类似方法)是策划的内容之一。 在策划阶段,新产品和新过程的开发要考虑产品的使用条件。 时间计划包含产品和过程开发的所有信息(总体项目计划里的时间节点/持续时间、里程碑,效能测试,PPA日期,软件标 准)。 开发的批准方法要满足顾客要求,如有不同,要与顾客澄清。 对采购有关的事项进行计划,并与总体时间进度保持一致。 外包的过程和服务也是项目策划的内容。
生产过程检验实施细则

生产过程检验实施细则引言概述:生产过程检验是确保产品质量的重要环节,通过对生产过程中各个环节的检验,可以及时发现问题并采取相应措施,以保证产品的合格率和稳定性。
本文将从四个方面详细阐述生产过程检验的实施细则。
一、原材料检验1.1 原材料的选择:根据产品的要求,选择符合标准的原材料,并确保供应商的信誉和质量保证体系。
1.2 原材料的抽样检验:对每批原材料进行抽样检验,包括外观、尺寸、化学成分等方面的检测,确保原材料的质量符合要求。
1.3 原材料的追溯:建立原材料追溯体系,对每批原材料进行记录和标识,以便在后续生产过程中进行追溯和溯源。
二、生产设备检验2.1 设备的校验和调试:在生产前,对生产设备进行校验和调试,确保设备的运行正常,各项参数符合要求。
2.2 设备的定期维护:制定设备的定期维护计划,包括清洁、润滑、更换易损件等,确保设备的稳定性和可靠性。
2.3 设备的故障处理:建立设备故障处理流程,及时处理设备故障,减少生产中的停机时间,保证生产进度和产品质量。
三、生产过程监控3.1 生产参数的监测:对生产过程中的关键参数进行实时监测,如温度、压力、速度等,确保生产过程的稳定性。
3.2 生产现场的巡检:定期对生产现场进行巡检,检查设备、工艺流程和操作人员的工作情况,及时发现问题并进行纠正。
3.3 生产记录的管理:建立完善的生产记录管理系统,对生产过程进行记录和归档,以备后续的追溯和分析。
四、成品检验4.1 成品的外观检验:对成品进行外观检验,包括尺寸、颜色、表面质量等方面的检测,确保成品的外观符合要求。
4.2 成品的功能检验:对成品进行功能性能测试,验证成品的性能指标是否符合要求。
4.3 成品的包装检验:对成品的包装进行检验,确保包装的完整性和防护性,以防止在运输和储存过程中的损坏。
总结:生产过程检验的实施细则涵盖了原材料检验、生产设备检验、生产过程监控和成品检验四个方面。
通过严格按照这些细则的要求进行检验,可以确保产品的质量稳定性和合格率,提高生产过程的可控性和可靠性。
- 1、下载文档前请自行甄别文档内容的完整性,平台不提供额外的编辑、内容补充、找答案等附加服务。
- 2、"仅部分预览"的文档,不可在线预览部分如存在完整性等问题,可反馈申请退款(可完整预览的文档不适用该条件!)。
- 3、如文档侵犯您的权益,请联系客服反馈,我们会尽快为您处理(人工客服工作时间:9:00-18:30)。
1、有分供方明确材料、配套件特性,并在量 0~2 产之前开展验证活动。2、有验证报告或记录。
1.6 确定分供方质量目标,根据质量实绩, 实施了工序检查重点整改。未达到质量目标 有8D报告/或纠正预防措施。
・材料、配套件入厂材质 证明;验收尺寸、性能试 验报告; ・入厂报检单或检验后的 入库单能有批次管理并与 帐簿相统一 ; ・不合格品管理控制程序 1、有确定分供方质量目标,并基于质量实绩
量产产品生产过程审核标准
供应商名称:
1、材料/配套件入厂质量控制 (过程审核)评价项目 应确认的文件、记录(报 告)、帐目、图表 过程审核评估指标 标准 确认结果 Result/指出问题 分值 得分
审核产品及件号:
过程审核人员:
1.1 供应商拥有程序文件管理入厂产品质量 要求事项(重点变更管理、不合格品管理等 写入程序文件)
1.7 材料、配套件入厂批次管理追溯和标识
1.8 每件材料/零件存放位置明确
1.9 供应商不能检查的项目有委外检查措施
1.10 对于分供方的质量不良,拥有预防不合 格的发生、出厂、再发生的程序。 1.11 对于分供方的变更管理零件,让其提交 变更信息,并根据需要确认实施状况。
1、对于分供方,有防止发生、防止流出、防 止再发生的程序(例:8D报告) 。 0~2 2、有产品质量不合格纠正措施实施结果。 1、对于分供方变更管理,有要求其提交变更 信息的许可书 0~1 2、确认变更管理零件实施情况 注:建议评分间隔:0.5分。 24 合计
2、制造过程质量控制 (过程审核)评价项目 2.1.1 随时对控制计划、作业指导书、检验 文件、检查基准书、控制图表及点检表进行 修改,且处于最新版本状态(所有文件尺寸 、控制统一) 应确认的文件、记录(报 告)、帐目、图表 过程审核评估指标 标准 确认结果 Result/指出问题 分值 得分
1、口头进行修订。 2、虽然进行了重新修订,但是手写的,未经过 评审和审批。 0~3 3、进行了重新修订、原件进行了修订。 4、根据质量问题的发生等,随时重新修订技术 文件(控制计划、作业指导书、PFMEA)。
2.1.2 产品材料和技术标准符合长安设计部 门规定。 2.1.3 经过特殊工序制造的零件,根据制造 条件得到管理,能够实际证明零件必要的产 品特性得到监视—(特殊工序…例如:铸造 、锻造、热处理、焊接、电镀、涂装、粘接 、压接、压焊等)。
1、产品材料和技术标准不符合长安设计部门要 求。 2、产品材料符合长安设计部门要求,但技术标 0~4 准不符合。 3、产品材料和技术标准符合长安设计部门要求 。 1、遗漏了特殊工序的制造条件、应监视检查 的特性。 0~2 2、应监视检查的产品特性记录证明在标准范 围内。 1、检测量具齐全,但测量仪器和设备不齐全。 2、量具、测量仪器、仪表和设备齐全能满足要 求。 3、量具、测量仪器、仪表和设备在周期内使 用,并对过期量具建立了产品追踪评价制度和 0~3 保留记录。 4、量具、测量仪器、仪表和设备有检测合格证 (查看检测报告)。 5、有试验设备的维护保养计划、保养记录和日 常点检记录 1、以作业指导书为基础,虽然有设定了自检 方法和自检周期的质量记录,但操作人员无法 判断自检项目。 0~2 2、有设定周期内的质量记录,即使是第3者看 到也可以理解、操作人员可以进行判断。 1、未遵守,重大不符合(重要特性)2个项目 以上。 2、未遵守,重大缺陷(重要特性)为1个或轻微 0~2 缺陷为3个以上。 3、未遵守,轻微缺陷2个以内。
2.1.4 作业指导书中必须的产品验证试验和 生产过程中的日常检(试)验设备如:量具 、测量仪器、仪表和设备齐全,建立了试验 设备的维护保养计划、保பைடு நூலகம்记录和日常点检 记录。
2.1.5 操作者掌握作业指导书内规定了操作 方法、操作点,自检方法和自检周期,质量 记录得到保留。
1、供应商拥有质量管理要求的程序文件,开展 此活动。 2、变更管理的评审、不合格品的评审加入到 0~2 ・质量协议书 了质量管理文件中。 ・作业指导书 3、供应商根据过去实施的事实重新对分供方的 ・材料、配套件入厂控制 质量要求文件修改并进行实施。
计划(是产品开发的一部 分) 1.2 分供方被指定二次配套零件符合长安公 ・入厂验收质量问题分供 司(如有)的要求 方不良对策书; ・每个供应商的质量记 录; 1.3 材料、配套件入厂检验是否按要求充分 ・原材料/配套件入厂验 验证其外观、尺寸、性能(包括型式试验) 收流程; ・规定了接收检查项目及 抽样数文件; 1.4 对分供方要确认PPAP/PSW等,量产开始 的质量保证状況,才能同意量产产品的交货 ・分供方的PPAP批准/PSW 签署; 1.5 对分供方明确材料、配套件(如有)的 ・材料、配套件入厂材质 特性,在量产之前,开展特性确认。 (Pass- 证明;验收尺寸、性能试 Through特性・・・即使用工场接收时从分供 验报告; 方处接受的产品特性,且在使用工场之后的 ・入厂报检单或检验后的 工序内无法管理的特性。例如:铸造,锻造 入库单能有批次管理并与 的硬度,化学成分,物理性能等) 帐簿相统一 ; ・不合格品管理控制程序
等进行包含工序检查在内的重点改善。 0~3 2、分供方未达到质量目标有纠正措施并得到 验证。 1、批次管理不能追溯。 2、批次管理能够追溯。 0~2 3、批次管理和帐簿统一、能追溯,有醒目的标 识分区。 1、库房合格品、不合格品无标识。 2、有标识无区域划分和区域定置。 0~2 3、库房内设置了隔离区域防止不合格品出厂。 4、有明确的原材料流程图。 原材料/配套件不能检查的项目— 1、没有委外检(试)验。 2、有委外检(试)验,按规定提供了报告。 0~2
1、没有按长安指定的二次配套厂购买零部件。 0~3 2、是向长安指定二次配套厂购买零部件。
1、未进行入厂验收,又提不出检(试)验证据 。2、有进行外观、尺寸验收。3、有进行外观 0~3 、尺寸检验和性能(包括型式)试验报告。 1、有向分供方要求新产品开发活动程序。 2、有实施工序及产品质量验证确认后,PPAP 0~2 批准交货。