新低压浇注工艺L-21
铝合金低压铸造技术

铝合金低压铸造技术随着我国经济的快速发展,铝合金在房屋建铸中的应用越来越广泛,在生产铝合金上,当前应用最广泛的依旧是低压铸造技术,这种技术不仅成本较低,而且操作起来也比较简单。
本文先介绍了低压铸造路合金的基本原理与特点,然后详细分析了路合金低压铸造的过程以及发展前景。
标签:铝合金;低压铸造;生产流程铝合金是非常常用的铸件材料,被应用建铸、机械设备、艺术创作各个方面。
在铝合金的生产上,最常见的生产工业是低压铸造工艺,主要是指铝液在压力的作用下,完成充型与凝固的过程,利用该铸造工艺不仅能使铝合金获得较高的强度,还能塑造出各种复杂的铸件,使金属材料的利用率提高。
1铝合金低压铸造原理及特点铝合金中由于各组元的不同,合金会表现出不同的物理性能及化学性能,并且合金结晶的过程也不尽相同。
因此,在进行铝合金铸造时,必须针对铝合金的特性,选择合理的铸造方法,以便优化铸件。
1.1 低压铸造原理铝合金低压铸造的原理是将干燥的空气压缩到一个密封的容器中,容器中事先装有铝液,铝液在气体压力的作用下就会沿着深液管铸件上升,通过铸型浇口平稳的进入到铸件的腔内,在铸液过程中,铝液的气体压力一直保持同一水平,一直到铝液完全凝固后终止。
在铝液完全凝固后,就可以接触铝液表面的气体压力,使多余的铝液返回到容器中,铸型内凝固的铝液形状就是最终所需要的铸件。
因为该工艺所需要的容器压力较低,故被称为低压铸造工艺。
1.2 低压铸造特点低压铸造的特点是成分简单,铸造性能好,能够很方便的进行铸造,在铸造过程中也可以自由的控制压力与铝液的流速,这中铸造工艺可以应用于其他的浇铸作业中。
低压铸造所使用的容器是底注式充型容器,铝液的金属液面能够保持平稳的状态,在铸造过程中不存在溅射的情况,因此在铸造时也就能够避免卷入气体或者颗粒粉尘的情况,提高逐渐的密实度与合格率。
因为铸件是在空气压力的作用下完成凝固的,所以铸件的轮廓往往会比较清晰,表面呈光滑状,铸件的力学性能较高,这有利于大薄壁的铸型。
低压注塑工艺
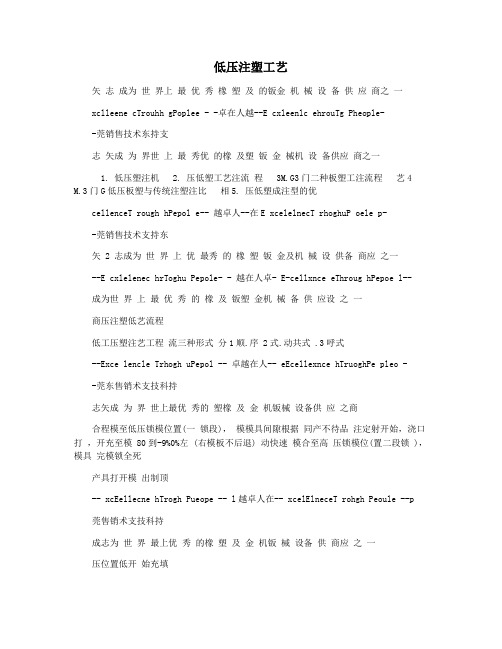
低压注塑工艺矢志成为世界上最优秀橡塑及的钣金机械设备供应商之一xclleene cTrouhh gPoplee - -卓在人越--E cxleenlc ehrouTg Pheople--莞销售技术东持支志矢成为界世上最秀优的橡及塑钣金械机设备供应商之一1. 低压塑注机2. 压低塑工艺注流程 3M.G3门二种板塑工注流程 艺4 M.3门G低压板塑与传统注塑注比 相5. 压低塑成注型的优cellenceT rough hPepol e-- 越卓人--在E xcelelnecT rhoghuP oele p--莞销售技术支持东矢 2 志成为世界上优最秀的橡塑钣金及机械设供备商应之一--E cxlelenec hrToghu Pepole- - 越在人卓- E-cellxnce eThroug hPepoe l--成为世界上最优秀的橡及钣塑金机械备供应设之一商压注塑低艺流程低工压塑注艺工程流三种形式分1顺.序 2式.动共式 .3呼式--Exce lencle Trhogh uPepol -- 卓越在人-- eEcellexnce hTruoghPe pleo --莞东售销术支技科持志矢成为界世上最优秀的塑橡及金机钣械设备供应之商合程模至低压锁模位置(一锁段),模模具间隙根据同产不待品注定射开始,浇口打,开充至模 80到-9%0%左 (右模板不后退) 动快速模合至高压锁模位(置二段锁 ),模具完模锁全死产具打开模出制顶-- xcEellecne hTrogh Pueope -- l越卓人在-- xcelElneceT rohgh Peoule --p莞售销术支技科持成志为世界最上优秀的橡塑及金机钣械设备供商应之一压位置低开始充填死--E celxelne Throucg Phepol -e 卓-越人在- -xcEellecn Theruoh Pgoplee --销莞技售术持支矢成志为世界上最优秀的橡塑及钣金机设械备供应商之一共动式工艺流程合模至压低锁模位(一段置锁模)模,具间根隙据不产品同待定注射开始口浇开打慢速锁注塑保压结速模,时同高压模锁完成具模打开顶出品型- E-cexllnee Tchorugh Peopel- 卓越-人-在-E xelcelnce Thrugh Peoolp e-莞售销技术持支科矢志成为世界上最优秀橡的塑及钣机金械设供应备商之慢充速锁模作动与充同填时行具锁死充模填完成xEelcelnec Throgu Phepleo- 卓越在-人- -Ecxleelnec Thorgh ueopPle -东莞销-售术支持科志成为世界最上优的秀橡塑及钣金械机设供应备之商一模高至锁模位压置 (二锁模段注)开始射浇,口开,充打至模 0%-89%左右动模板慢速0后退至低压模锁置位 (一锁段模) 速锁快模至高压锁模位 (一段锁模)置具打开出制顶品-- 保xcEellenc ehTough Perope -- 卓l越在-人 Ex-elclene chroTuhg eopPle --售技术销持支科志矢为成世界最优上秀的橡及塑钣金机械设备供应之商高一压位置开始填充模慢板速后退至压低锁位置模- E-xcellenc ehroughT Poelp e- 卓-在人越--E xcellecn ehTorgu hePpleo --莞销售技术持支矢志成为世界最优上秀的橡及塑钣金机械设备应供商之MG3一板门二种注塑艺工流程- -Ecellxnce ehTrogh uPeolpe --卓越在-人- EcexllnceeT horuhg People-东莞-销技售支术持1矢志成为世上最界秀优的橡及钣金塑机械设供备应商之模定顶出板模后到退位合至低压锁模模位(一置段模锁),具模间隙.12m~1.mm5m注射始,开序顺浇口依阀次打,充模到至9 5左%右动 (模不后退板)模具开打顶制品射注压保,顺阀浇口依序次闭合速至模压高模位锁 (二段锁模)置模具完,锁全死东莞销技售支术持-科-Ex ellcnee cThorugh Pepleo --卓越在 -人- xceEllece nTrohgu Pehple o-矢- 成为志世界最上优秀的橡塑及钣金机械备设供商应之一工手挂表皮定顶出模模板后退位合到至高模压模锁位置 (二段锁模,) 模具全完死锁注开始射顺序阀浇口依,次打,至充开模7到080~左% (右动模不后板)退模至低压锁开位模置一(段锁模),模间具隙 .50mm1~0.m充至模95~%79%左右此(过程动模板后退不)模打开顶出制品注保压,射序顺阀口浇依次关闭模高至锁模压位置( 二锁模),模具段完锁全死东莞销售术支技科持13-E xcllenec Terhuoh Pegpleo-- 卓越在 --人E cexllnee Thcorguh Peopel- -成为世界上最秀的优橡塑钣及金械机设备供应商之一MG门板低压注3塑与统传塑注比相G3门M板锁模力塑注力压统注传塑成型低压注塑成 120型T 800% 300T 4%5 - -Ecexllece nhrTugo hePolpe-- 越在人卓-- Execllnec eTrhugh Peoope --l 销售莞技支术持成世为上最界优秀的塑橡及钣金机设备械供商之一应压注塑低成型的优势需锁模力注低压塑力低模具排气果好效压注塑成型制品变品小形制品外观效佳果料材子分取向小东莞售技术销支持--E cxellncee Throgh Peoplue --卓越在人- -xEelclncee ThoughrPeo pe l--矢志成为世界上最优秀橡塑的及钣金机械设备供应商之一--Exce llnec Therouh Pgeplo -- e越在人-卓- xEcellnce eThrouhgP eope -东l莞售技术销支科持。
低压灌浆技术修补裂缝
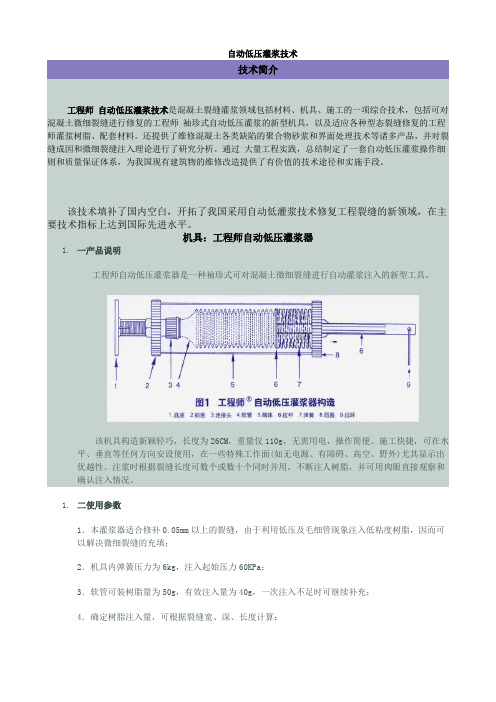
自动低压灌浆技术技术简介工程师自动低压灌浆技术是混凝土裂缝灌浆领域包括材料、机具、施工的一项综合技术,包括可对混凝土微细裂缝进行修复的工程师袖珍式自动低压灌浆的新型机具,以及适应各种型态裂缝修复的工程师灌浆树脂、配套材料。
还提供了维修混凝土各类缺陷的聚合物砂浆和界面处理技术等诸多产品,并对裂缝成因和微细裂缝注入理论进行了研究分析。
通过大量工程实践,总结制定了一套自动低压灌浆操作细则和质量保证体系,为我国现有建筑物的维修改造提供了有价值的技术途径和实施手段。
该技术填补了国内空白,开拓了我国采用自动低灌浆技术修复工程裂缝的新领域,在主要技术指标上达到国际先进水平。
机具:工程师自动低压灌浆器1.一产品说明工程师自动低压灌浆器是一种袖珍式可对混凝土微细裂缝进行自动灌浆注入的新型工具。
该机具构造新颖轻巧,长度为26CM,重量仅110g,无需用电,操作简便、施工快捷,可在水平、垂直等任何方向安设使用,在一些特殊工作面(如无电源、有障碍、高空、野外)尤其显示出优越性。
注浆时根据裂缝长度可数个或数十个同时并用,不断注人树脂,并可用肉眼直接观察和确认注入情况。
1.二使用参数1.本灌浆器适合修补0.05mm以上的裂缝,由于利用低压及毛细管现象注入低粘度树脂,因而可以解决微细裂缝的充填;2.机具内弹簧压力为6kg,注入起始压力60KPa;3.软管可装树脂量为50g,有效注入量为40g,一次注入不足时可继续补充;4.确定树脂注入量,可根据裂缝宽、深、长度计算:1.根据经验,实际需用树脂约为理论量的1.3倍以上,某些振捣不密实的混凝土或砖墙注入量可达理论量的数倍。
2.三裂缝灌浆过程示意1.四裂缝灌浆施工步骤2.1、观测裂缝:正确观测裂缝宽度并统计出裂缝总长度,为施工做准备;2、基层处理:清除裂缝表面的灰尘、油污,可用气泵清理裂缝,若混凝土已抹灰则要剔掉抹灰层,露出混凝土表面,施工时一定要保证裂缝干燥,切忌用水冲刷裂缝;3、确定注入口:一般按15~20cm距离设置一个注入口,贴上胶带,预留。
l-21使用说明

v1.0 可编辑可修改XL-21动力柜电柜使用说明书版编制:谢小军校核:周清平审定:批准:华自科技股份有限公司目录1产品概述 (1)2环境条件 (1)3型号含义 (1)4技术参数 (2)5结构功能 (2)6使用与维护 (3)8订货须知 (5)1产品概述XL-21型动力配电柜适用于发电厂、变电站、民用建筑及工矿企业等额定频率50Hz,额定电压380V,额定电流600A以下三相交流系统,作为电能的转换、分配,或现场负荷就地操作控制之用。
2环境条件2.1户内使用,海拔高度不超过1000米;2.2周围空气温度为-5℃~+40℃,24小时内平均温度不得高于+35℃,超过时,需要根据实际情况降容运行;2.3相对湿度在最高温度+40℃时不超过50%,在较低温度时允许有较大的相对湿度,如+20℃为90%,应考虑到由于温度的变化可能会偶然产生凝露的影响,日平均值不大于95%,月平均值不大于90%;2.4水蒸汽日平均值不大于*10-3Mpa,月平均值不大于*10-3Mpa;2.5设备安装时与垂直面的倾斜度不超过5度;2.6地震烈度不超过8度;2.7无经常性的剧烈振动;2.8周围空气应不受腐蚀性或可燃气体、水蒸气等的污染;2.9当使用环境特殊或有其它要求时需与制造厂协商。
3型号含义XL-21设计序号动力用配电柜(箱)4技术参数5结构功能本配电柜柜体结构用钢板弯制焊接而成,其正面为单扇左开门,门上装有电压表、电流表等测量仪表和操作元件、信号元件。
一般情况下,刀开关操作手柄安装在箱前右侧上部,配电柜靠墙安装,进出线电缆由底部引入。
用户有特殊要求,亦可在箱顶盖板上开进线敲落孔或加装母线室。
本配电柜可单独成柜,或组合成柜。
5.1主要功能分类:进线、馈电、电动机控制。
5.2主要组成部分:柜体、柜门(可装仪表)、后封板、眉头、上进出线孔封板、母排、电器元件、母线夹板、绝缘支撑件、绝缘子、辅材等。
5.3操作方式:正面操作。
5.4安装方式:户内式、固定垂直安装。
浇注工艺规程
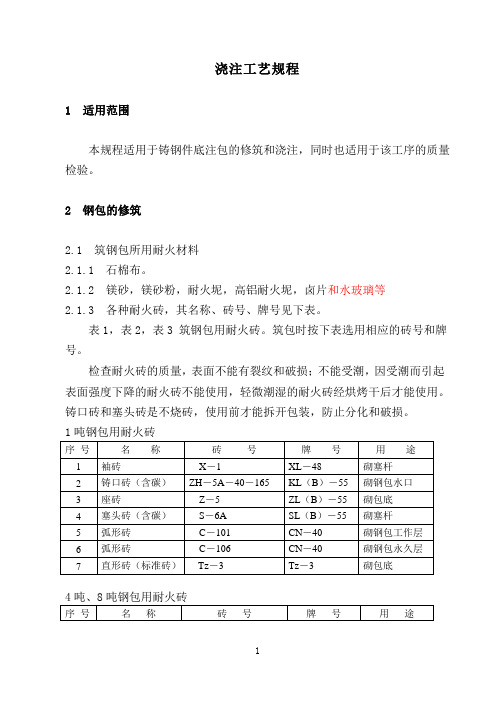
浇注工艺规程1 适用范围本规程适用于铸钢件底注包的修筑和浇注,同时也适用于该工序的质量检验。
2 钢包的修筑2.1 筑钢包所用耐火材料2.1.1 石棉布。
2.1.2 镁砂,镁砂粉,耐火坭,高铝耐火坭,卤片和水玻璃等2.1.3 各种耐火砖,其名称、砖号、牌号见下表。
表1,表2,表3 筑钢包用耐火砖。
筑包时按下表选用相应的砖号和牌号。
检查耐火砖的质量,表面不能有裂纹和破损;不能受潮,因受潮而引起表面强度下降的耐火砖不能使用,轻微潮湿的耐火砖经烘烤干后才能使用。
铸口砖和塞头砖是不烧砖,使用前才能拆开包装,防止分化和破损。
1吨钢包用耐火砖序号名称砖号牌号用途1 袖砖X-1 XL-48 砌塞杆2 铸口砖(含碳)ZH-5A-40-165 KL(B)-55 砌钢包水口3 座砖Z-5 ZL(B)-55 砌包底4 塞头砖(含碳)S-6A SL(B)-55 砌塞杆5 弧形砖C-101 CN-40 砌钢包工作层6 弧形砖C-106 CN-40 砌钢包永久层7 直形砖(标准砖)Tz-3 Tz-3 砌包底4吨、8吨钢包用耐火砖序号名称砖号牌号用途1 袖砖X-2 XL-48 砌塞杆2 铸口砖(含碳)ZH-6A-50-206 KL(B)-55 砌钢包水口3 座砖Z-6 ZL(B)-55 砌包底4 塞头砖(含碳)S-7 SL(B)-55 砌塞杆5 弧形砖 C -100 CN-40 砌钢包6 弧形砖C-106 CN-40 砌钢包永久层7 直形砖(标准砖)Tz-3 LZ-70 砌包底8 直形砖(标准砖)Tz-3 N-2a 砌包底永久层12吨钢包用耐火砖序号名称砖号牌号用途1 袖砖X-4 XL-48 砌塞杆2 铸口砖(含碳)ZH-13-60-315 KL(B)-55 砌钢包水口3 座砖Z-11 ZL(B)-55 砌包底4 塞头砖(含碳)S-8 SL(B)-55 砌塞杆5 弧形砖 C -100 CN-40 砌钢包工作层6 弧形砖C-106 CN-40 砌钢包永久层7 直形砖(标准砖)Tz-3 LZ-70 砌包底8 直形砖(标准砖)Tz-3 N-2a 砌包底永久层增加20吨包用砖规格2.2筑包前的检查工作。
低压铸造

由图2可以看出铝合金液上升的液面并不平稳,在0.17s出现泉状。整个铸件的充型时间是0.567s,说明型腔在设定的充型时间0.5s内没有充满,充型过程延长到了增压阶段,而增压阶段的升压速率明 显高于充型阶段,液体会在0.5s时发生剧烈波动,使空气卷入金属液,影响排气。
图3铸件各部分的凝固时间分布
由图3可以看出整个铸件所需的时间为112.93s,超出了设定的保压时间60s,重新设定保压时间为150s,从上图看铸件是由上到下的顺序凝固,浇口位置最后凝固,能起到很好的补缩作用,说明模具设计合理。
模具预热温度高有利于金属液的充型,但是会影响金属液的凝固速度,不利于获得细化的晶粒,还容易引起偏析,氧化,缩松等铸件缺陷。为了解决这一矛盾,应根据具体的铸件类型来选择其适当的模具温度,对与叶轮这样的薄壁复杂铸件,成型问题是首要矛盾,应在保证充型完整的前提下降低模具的预热温度。容易出现充型不足的地方在叶片,所以石膏模预热温度应稍高。上模具铸铁主要起冷却作用,因而其预热温度应稍低,有利于铸件快速凝固。综上所述石膏模的预热温度设置在175℃ ~ 250℃之间,铸铁模预热温度设置在125℃ ~ 200℃之间。
根据上述分析浇注温度、模具预热温度的设置如表1所示。
表1浇注温度、模具预热温度
浇注温度/℃
石膏温度/℃
铸铁温度/℃
660
175
125
670
200
150
680
225
175
690
250
200
参数优化
铝合金液在型腔内的充型状态主要与压力—时间曲线有关,特别是充型阶段的充型压力和升压速率对其影响最大,浇注温度和模具的预热温度对充型过程影响较小。先设定浇注温度为680℃,石膏模具的预热温度为225℃,冷铁预热温度为175℃的情况下。模拟得到的铸件各部分充型时间分布如图2所示,凝固时间分布如图3所示。
低压铸造原理及特点

低压铸造原理及特点使铸件远离浇口的部位先凝固,让浇口最后凝固,使铸件在凝固过程中通过浇口得到补缩,实现顺序凝固。
常采用下述措施:1.浇口设在铸件的厚壁部位,而使薄壁部位远离浇口;2.用加工裕量调整铸件壁厚,以调节铸件的方向性凝固;3.改变铸件的冷却条件。
对于壁厚差大的铸件,用上述一般措施又难于得到顾序凝固的条件时,可采用一些特殊的办法,如在铸件厚壁处进行局部冷却,以实现顺序凝固。
第四节低压铸造工艺低压铸造的工艺规范包括升液、充型、增压、保压结晶、卸压、冷却延时,以及铸型预热温度、浇注温度、铸型的涂料等。
(1)升液压力和升液速率升液压力是指当金属液面上升到浇口,所需要的压力。
金属液在升液管内的上升速度即为升液速度,升液应平稳,以有利于型腔内气体的排出,同时也可使金属液在进入浇口时不致产生喷溅。
(2)充型压力和充型速度充型压力是指使金属液充型上升到铸型顶部所需的压力。
在充型阶段,金属液面上的升压速度就是充型速度。
(3)增压和增压速度金属液充满型腔后,再继续增压,使铸件的结晶凝固在一定大小的压力作用下进行,这时的压力叫结晶压力或保压压力。
结晶压力越大,补缩效果越好,最后获得的铸件组织也愈致密。
但通过结晶增大压力来提高铸件质量,不是任何情况下都能采用的。
(4)保压时间型腔压力增至结晶压力后,并在结晶压力下保持一段时间,直到铸件完全凝固所需要的时间叫保压时间。
如果保压时间不够,铸件未完全凝固就卸压,型腔中的金属液将会全部或部分流回批捐,造成铸件“放空”报废:如果保压时间过久,则浇口残留过长,这不仅降低工艺收得率,而且还会造成浇口“冻结”,使铸件出型困难,故生产中必须选择一适宜的保压时间。
(5)卸压阶段铸件凝固完毕(或浇口处已经凝固),即可卸除坩埚内液面上的压力(有称排气),使升液管和浇口中尚未凝固的金属液依靠重力落回坩埚中。
(6)延时冷却阶段:卸压后,为使铸件得到一定的凝固强度,防止开型、脱模取件时发生变形和损坏,须延时冷却。
铝合金薄壁筒体铸件的低压铸造工艺优化
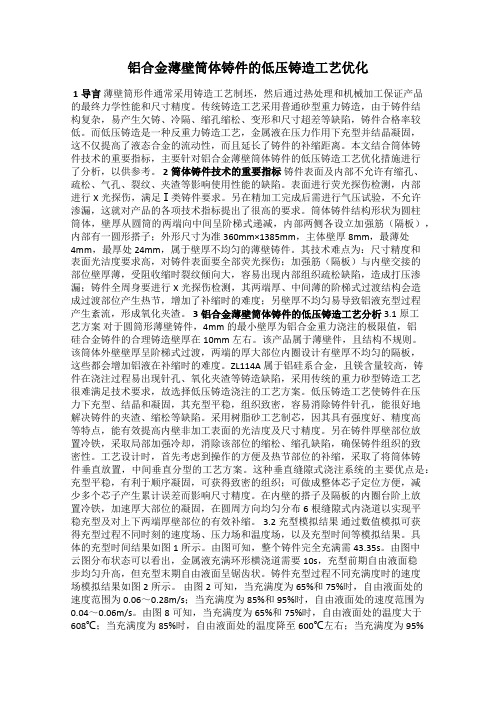
铝合金薄壁筒体铸件的低压铸造工艺优化1导言薄壁筒形件通常采用铸造工艺制坯,然后通过热处理和机械加工保证产品的最终力学性能和尺寸精度。
传统铸造工艺采用普通砂型重力铸造,由于铸件结构复杂,易产生欠铸、冷隔、缩孔缩松、变形和尺寸超差等缺陷,铸件合格率较低。
而低压铸造是一种反重力铸造工艺,金属液在压力作用下充型并结晶凝固,这不仅提高了液态合金的流动性,而且延长了铸件的补缩距离。
本文结合筒体铸件技术的重要指标,主要针对铝合金薄壁筒体铸件的低压铸造工艺优化措施进行了分析,以供参考。
2筒体铸件技术的重要指标铸件表面及内部不允许有缩孔、疏松、气孔、裂纹、夹渣等影响使用性能的缺陷。
表面进行荧光探伤检测,内部进行X光探伤,满足Ⅰ类铸件要求。
另在精加工完成后需进行气压试验,不允许渗漏,这就对产品的各项技术指标提出了很高的要求。
筒体铸件结构形状为圆柱筒体,壁厚从圆筒的两端向中间呈阶梯式递减,内部两侧各设立加强筋(隔板),内部有一圆形搭子;外形尺寸为准360mm×1385mm,主体壁厚8mm,最薄处4mm,最厚处24mm,属于壁厚不均匀的薄壁铸件。
其技术难点为:尺寸精度和表面光洁度要求高,对铸件表面要全部荧光探伤;加强筋(隔板)与内壁交接的部位壁厚薄,受阻收缩时裂纹倾向大,容易出现内部组织疏松缺陷,造成打压渗漏;铸件全周身要进行X光探伤检测,其两端厚、中间薄的阶梯式过渡结构会造成过渡部位产生热节,增加了补缩时的难度;另壁厚不均匀易导致铝液充型过程产生紊流,形成氧化夹渣。
3铝合金薄壁筒体铸件的低压铸造工艺分析 3.1原工艺方案对于圆筒形薄壁铸件,4mm的最小壁厚为铝合金重力浇注的极限值,铝硅合金铸件的合理铸造壁厚在10mm左右。
该产品属于薄壁件,且结构不规则。
该筒体外壁壁厚呈阶梯式过渡,两端的厚大部位内圈设计有壁厚不均匀的隔板,这些都会增加铝液在补缩时的难度。
ZL114A属于铝硅系合金,且镁含量较高,铸件在浇注过程易出现针孔、氧化夹渣等铸造缺陷,采用传统的重力砂型铸造工艺很难满足技术要求,故选择低压铸造浇注的工艺方案。
21世纪低压铸造技术
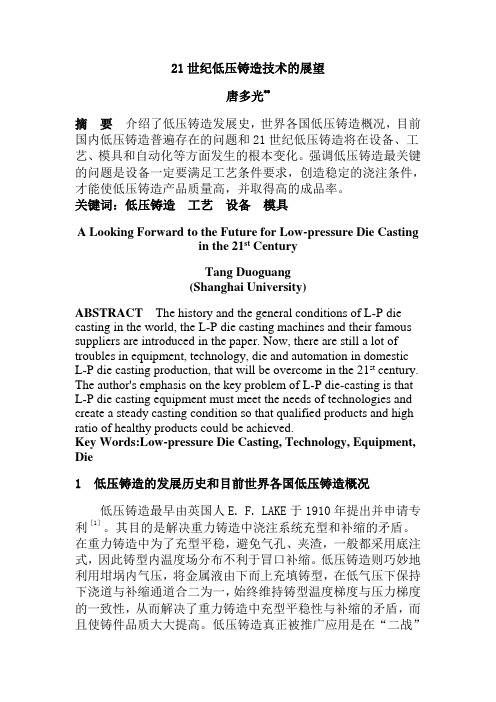
21世纪低压铸造技术的展望唐多光**摘要介绍了低压铸造发展史,世界各国低压铸造概况,目前国内低压铸造普遍存在的问题和21世纪低压铸造将在设备、工艺、模具和自动化等方面发生的根本变化。
强调低压铸造最关键的问题是设备一定要满足工艺条件要求,创造稳定的浇注条件,才能使低压铸造产品质量高,并取得高的成品率。
关键词:低压铸造工艺设备模具A Looking Forward to the Future for Low-pressure Die Castingin the 21st CenturyTang Duoguang(Shanghai University)ABSTRACT The history and the general conditions of L-P die casting in the world, the L-P die casting machines and their famous suppliers are introduced in the paper. Now, there are still a lot of troubles in equipment, technology, die and automation in domestic L-P die casting production, that will be overcome in the 21st century. The author's emphasis on the key problem of L-P die-casting is that L-P die casting equipment must meet the needs of technologies and create a steady casting condition so that qualified products and high ratio of healthy products could be achieved.Key Words:Low-pressure Die Casting, Technology, Equipment, Die1 低压铸造的发展历史和目前世界各国低压铸造概况低压铸造最早由英国人E. F. LAKE于1910年提出并申请专利[1]。
低压注塑成型工艺

26
二、低压注塑工艺应用案例
电子行业线圈
Copyright © 2012 SINBON Electronics Co., Ltd. All rights reserved.
27
三、低压注塑工艺总结
低压注塑工艺正在被越来越多的工业领域所采用,如 航空、汽车、手机、医疗器械等等。低压注塑压力低 可以很好的保证产品的质量,周期短提高了工作的效 率,以及胶水的可回收重复利用性可以最大限度的使 用原材料从而达到节省成本.
21
二、低压注塑工艺应用案例
3、PCB的封装
Copyright © 2012 SINBON Electronics Co., Ltd. All rights reserved.
22
二、低压注塑工艺应用案例
3、PCB的封装
此图面是信邦即将量产的机 种,中间SR选用的是汉高的 6208S这款热熔胶,中间 PCBA功能是将12V DC转化 为2.8V DC
2019/12/30 Copyright © 2012 SINBON Electronics Co., Ltd. All rights reserved.
9
一、低压注塑工艺
应用案例:汽车传感器封装 双组份灌封 VS Macromelt 低压注塑工艺
Copyright © 2012 SINBON Electronics Co., Ltd. All rights reserved.
10
一、低压注塑工艺
8、低压注塑工艺的流程 低压注塑工艺流程与传统灌封工艺流程对比
d.高低温稳定性:耐热循环、耐低温、耐高温(-40°C
~150°C);不含任何有毒物质,符合殴监RoHS指令;可回
收利用。
低压注塑工艺及其应用培训
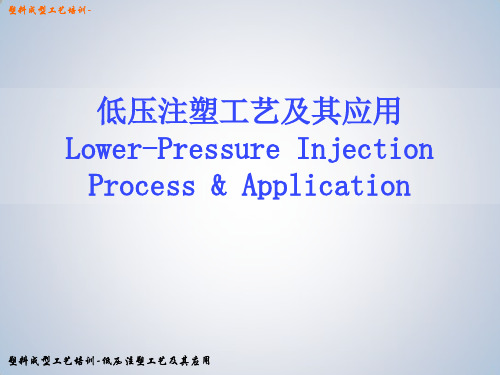
22
塑料成型工艺培训-低压注塑工艺及其应用
塑六料成、型工低艺培压训-注塑的核心技术
5、预变形技术: 在低压注塑时,由于注射速度,压力,料温,面料
厚度产品结构等因素的影响,产品易发申翘曲变形且不易 更改;可进行前期分析,在模具加工前进行确认变形量, 避免后续复杂工作。
塑料成型工艺培训-
一、低压注塑工艺介绍
3、分类 低压注塑被称做In-mould decoformation,常用的分为以下两
种: ①冲切好的织物覆盖到模具内,然后合模直接注射成型; ②冲切好的织物覆盖到模具内,将树脂注射到织物背面然后
合模压缩成型;
5
塑料成型工艺培训-低压注塑工艺及其应用
塑料成型工艺培训-
动作和设备的匹配以及注射的工艺参数等。同时,整个生 产流程较长产品的外观质量要求高,任何一个环节出现轻 微的差错都会导致产品的质量达不到要求,因此需要前期 的全面工艺过程策划和过程的严格控制以及相对较长的调 试过程。
21
塑料成型工艺培训-低压注塑工艺及其应用
塑六料成、型工低艺培压训-注塑的核心技术
11
塑料成型工艺培训-低压注塑工艺及其应用
塑料成型工艺培训-
三、产品设计要点
7、产品背面分型线往里设计10-15mm面料固定区域,不设计其 余结构;
面料翻遍长 度10-15mm
12
塑料成型工艺培训-低压注塑工艺及其应用
塑料成型工艺培训-
三、产品设计要点
8、产品转角不易太多,尽量将大零件拆分成小零件到达低压注塑 的目的;
塑料成型工艺培训-
低压注塑工艺及其应用 Lower-Pressure Injection
Process & Application
低压铸造
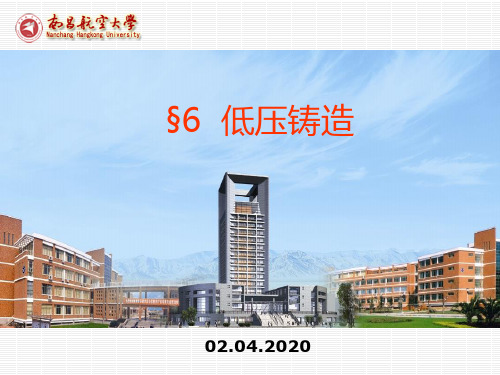
02.04.2020
6)涂料 金属型低压铸造时,为了提高其寿命及
铸件质量,必须刷涂料;涂料应均匀,涂料厚 度要根据铸件表面光洁度及铸件结构来决定。
02.04.2020
6.3 低压铸造的特点及应用
1、低压铸造独特的优点: 1)浇注压力和速度可调,适应各种铸型、合 金和铸件大小; 2)液态金属充型平稳,夹杂缺陷减少;--底 注式平稳充型,无飞溅、气体卷入和型壁冲刷 等弊病,铸件合格率提高; 3)型腔内液流与气流方向一致,减少了产生 气孔的可能性;
02.04.2020
特殊低压铸造工艺
(1)压差法低压铸造
有些铸件的内部质量要求高,希望在较高的压力下结晶,但一般低 压铸造时的结晶压力不能太大。因而发展出压差法低压铸造。其工艺过 程是将电阻保温炉和铸型全部进行密封,在密封罩内通人压力较大如 500kPa的压缩空气,这时由于铸型与坩埚内部的压力相等,金属液不 会上升,然后金属液向上补充50kPa压力,金属液就会上升充填型腔。 同时铸型内的金属液也在高压下结晶凝固。这种方法使铸件得到较致密 的结晶组织,提高了铸件的机械性能。据资料介绍这种工艺与一般铸造 方法相比,使铸件强度提高约25%,延伸率提高约50%。但设备较庞 大,操作麻烦,只有特殊要求时才应用。
13
—
70~80
21~24 —
98
合金为 ZAl Mg10
—
440~450 —
17~22 —
120~125
02.04.2020
02.04.2020
02.04.2020
02.04.2020
6.4 低压铸造的工艺设计
6.4.1低压铸造所用的铸型
1、金属型 金属型多用于大批、大量生产的有色金属铸件。
新低压浇注工艺L 21
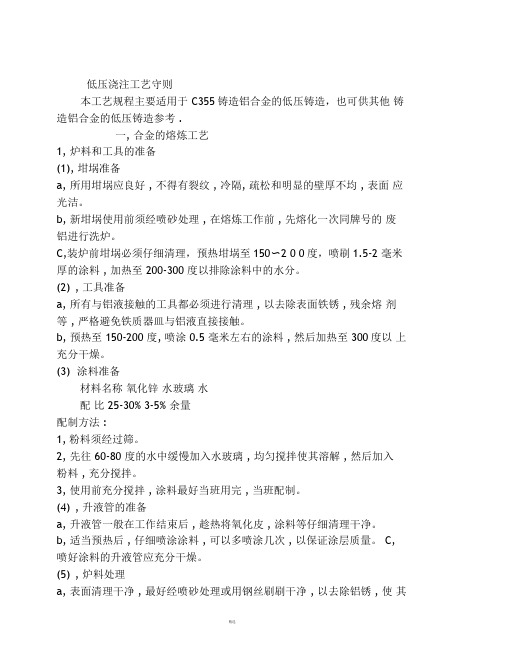
低压浇注工艺守则本工艺规程主要适用于 C355铸造铝合金的低压铸造,也可供其他铸造铝合金的低压铸造参考 .一, 合金的熔炼工艺1,炉料和工具的准备(1), 坩埚准备a,所用坩埚应良好 , 不得有裂纹 , 冷隔, 疏松和明显的壁厚不均 , 表面应光洁。
b,新坩埚使用前须经喷砂处理 , 在熔炼工作前 , 先熔化一次同牌号的废铝进行洗炉。
C,装炉前坩埚必须仔细清理,预热坩埚至150〜2 0 0度,喷刷1.5-2 毫米厚的涂料 , 加热至 200-300 度以排除涂料中的水分。
(2), 工具准备a,所有与铝液接触的工具都必须进行清理 , 以去除表面铁锈 , 残余熔剂等 , 严格避免铁质器皿与铝液直接接触。
b,预热至 150-200 度, 喷涂 0.5 毫米左右的涂料 , 然后加热至 300度以上充分干燥。
(3)涂料准备材料名称氧化锌水玻璃水配比 25-30% 3-5% 余量配制方法 :1,粉料须经过筛。
2,先往 60-80 度的水中缓慢加入水玻璃 , 均匀搅拌使其溶解 , 然后加入粉料 , 充分搅拌。
3,使用前充分搅拌 , 涂料最好当班用完 , 当班配制。
(4), 升液管的准备a,升液管一般在工作结束后 , 趁热将氧化皮 , 涂料等仔细清理干净。
b,适当预热后 , 仔细喷涂涂料 , 可以多喷涂几次 , 以保证涂层质量。
C, 喷好涂料的升液管应充分干燥。
(5), 炉料处理a,表面清理干净 , 最好经喷砂处理或用钢丝刷刷干净 , 以去除铝锈 , 使其露出金属光泽 , 表面清理后的炉料应尽快用于生产。
(6), 检查设备主要检查加热机构 , 控温装置等是否正常 , 严禁带病工作。
(7), 熔剂准备2, 合金熔炼(1), 炉料融化a,当炉料由回炉料和铝锭组成 ,应首先熔化铝锭 ,然后熔化回炉料 ,回炉料用量不得超过炉料的30%.当Fe>0.2%时不得使用。
b,容易烧损的炉料 , 如镁应在最后加入 , 最好在 680-700 度时压入预热至 200 度左右的镁锭。
浇注工艺

干式变压器甲基四氢苯酐环氧树脂的浇注2006-6-12 22:44:22半个多世纪以来,世界上许多城市都以极高的速度向现代化发展,随着城市的发展,供电负荷逐年增长。
为了确保安全,人们迫切需要一种既可深入负荷中心又无燃烧危险的变压器,而油浸式变压器在这方面却有它不可避免的缺陷。
干式变压器由于具有结构简单、维护方便、防火、阻燃、防尘等特点,正好能够满足人们迫切需要。
因此,近年来在国内得到了迅猛发展。
1 干式变压器的种类和特点1.1 浸渍绝缘干式变压器该种变压器生产历史最长,制造工艺也比较简单,导线采用玻璃丝包,垫块用相应的绝缘等级材料热压成型,随浸渍漆不同,变压器绝缘分B、F、H、C级,主纵绝缘的空道全部以空气为绝缘介质。
这类变压器绕组制造工装设备简单、成本低,但相对其它形式干式变压器,它承受短路能力较差。
另外,绕组的防潮和防尘性能差,变压器停用再投入使用时,可能因为周围的环境因素产生的吸潮甚至凝露,使其绝缘水平大大降低,使用前必须进行清理和干燥处理。
该种变压器技术经济性能好,产品价格与树脂绝缘的大体相当。
1.2 环氧树脂绝缘干式变压器环氧树脂是一种早就广泛应用的化工原料,它不仅仅是一种难燃、阻燃的材料,且具有优越的电气性能,以后逐渐为电工制造业所采用。
这种变压器根据绕组包封方式可分为树脂浇注和绕包绝缘两大类。
树脂浇注式的工艺特点就是必须靠模具并采用专用浇注设备,在真空状态下使线圈浇注成型,它又有下列两种类型。
无填料树脂浇注。
这种纯树脂浇注的干式变压器内外绝缘厚度一般为1.5~2 mm,属于薄绝缘。
目前我国使用的产品以这种结构最多,其结构特点为变压器高、低压绕组内外层用玻璃纤维增强,在真空状态下采用环氧树脂用模具进行浇注,线圈导体外部形成富有弹性的既韧又薄的树脂包封层,它可随线圈一起膨胀和收缩,因而不再担心会发生开裂。
另外,由于包封绝缘层的厚度很薄,既达到了包封的效果,又减少了包封绝缘层的温差,因而对改善浇注线圈的热传导是非常有益的。
低压铸造工艺规程

1、目的和范围1.1规范锶变质汽车车轮低压铸造的操作工艺。
1.2本规程适用于铝合金轮毂低压铸造工序。
2、流程3、生产前准备3.1设备准备3.1.1保温炉在使用前,要逐步分阶段升温至700~720℃。
3.1.2将预热好的升液管小心装入保温炉,并密封紧固。
3.1.3检查铸造机油路、油缸及冷却有无漏油,温控、液压系统工作是否正常。
3.1.4低压机供气压力不低于0.4Mpa ,供水压力不低于0.35Mpa 。
3.1.5低压机供气的压缩空气的露点≤-45℃。
3.2工具量具准备3.2.1涂料按比例配比好,使用前要充分搅拌,配比后超过八小时禁止使用。
3.2.2检查烤模器通风要均匀,否则应修理或更换。
3.2.3涂料喷枪须先检查有无泄漏,有泄漏的喷枪严禁使用。
3.2.4专用检验器具是否齐备,有无损坏。
3.2.5扁铲、铁棒、铝锤、钢丝刷、烤枪、取件夹、过滤片、钢印等工具须准备齐全。
3.3文件准备3.3.1工艺规程须准备好。
3.3.2低压模具使用跟踪卡,压铸监控记录表、低压铸造工艺卡片、作业准备验证表是否准备齐全。
3.4模具准备3.4.1调整模具及限位,要求无错模,限位到位。
3.4.2开合模具检验运行是否自如,顶杆顶出.复位是否正常.3.4.3试压过滤片合适:合模后与分流锥有1~2mm的间隙3.4.4将模具烘烤至380~450℃。
3.5铝液准备3.5.1铝液化学成分符合表一要求。
表一:保温炉内的化学成份3.5.2测氢密度≥2.45g/CM3。
3.5.3铝液温度在685℃-710℃范围内。
3.5.4保温炉加铝水前、后必须扒渣,加完铝水前,清理保温炉内铝液的浮渣、炉壁挂渣、升液管和热电偶保护套侧面的渣要清干净;加铝后用漏铲将铝液表面的浮渣轻扒至炉门口,再将渣扒到铝渣槽内,严禁在炉内上下翻动铝液扒渣。
3.5.5合格铝液在保温炉内储存时间≤4小时,超过4小时要求重新检测保温炉内铝液化学成份和含氢量,达到要求,才可使用;否则禁止使用。
- 1、下载文档前请自行甄别文档内容的完整性,平台不提供额外的编辑、内容补充、找答案等附加服务。
- 2、"仅部分预览"的文档,不可在线预览部分如存在完整性等问题,可反馈申请退款(可完整预览的文档不适用该条件!)。
- 3、如文档侵犯您的权益,请联系客服反馈,我们会尽快为您处理(人工客服工作时间:9:00-18:30)。
低压浇注工艺守则
本工艺规程主要适用于C355铸造铝合金的低压铸造,也可供其他铸造铝合金的低压铸造参考.
一,合金的熔炼工艺
1,炉料和工具的准备
(1),坩埚准备
a,所用坩埚应良好,不得有裂纹,冷隔,疏松和明显的壁厚不均,表面应光洁。
b,新坩埚使用前须经喷砂处理,在熔炼工作前,先熔化一次同牌号的废铝进行洗炉。
c,装炉前坩埚必须仔细清理,预热坩埚至150~200度,喷刷1.5-2毫米厚的涂料,加热至200-300度以排除涂料中的水分。
(2),工具准备
a,所有与铝液接触的工具都必须进行清理,以去除表面铁锈,残余熔剂等,严格避免铁质器皿与铝液直接接触。
b,预热至150-200度,喷涂0.5毫米左右的涂料,然后加热至300度以上充分干燥。
(3)涂料准备
材料名称氧化锌水玻璃水
配比 25-30% 3-5% 余量
配制方法:
1,粉料须经过筛。
2,先往60-80度的水中缓慢加入水玻璃,均匀搅拌使其溶解,然后加入粉料,充分搅拌。
3,使用前充分搅拌,涂料最好当班用完,当班配制。
(4),升液管的准备
a,升液管一般在工作结束后,趁热将氧化皮,涂料等仔细清理干净。
b,适当预热后,仔细喷涂涂料,可以多喷涂几次,以保证涂层质量。
c,喷好涂料的升液管应充分干燥。
(5),炉料处理
a,表面清理干净,最好经喷砂处理或用钢丝刷刷干净,以去除铝锈,使其露出金属光泽,表面清理后的炉料应尽快用于生产。
(6),检查设备
主要检查加热机构,控温装置等是否正常,严禁带病工作。
(7),熔剂准备
2,合金熔炼
(1),炉料融化
a,当炉料由回炉料和铝锭组成,应首先熔化铝锭,然后熔化回炉料,回炉料用量不得超过炉料的30%.当Fe>0.2%时不得使用。
b,容易烧损的炉料,如镁应在最后加入,最好在680-700度时压入预热至200度左右的镁锭。
c,在连续熔化时,坩埚内可剩余一部分铝液,以加速下一炉的熔化。
d,采用覆盖剂时,应在炉料开始熔化时就加入熔剂。
(2)除气精练
a,精炼剂的加入量为铝液重量的1.5-2.5%。
b,处理温度为700-720度。
c,在铝液达到处理温度时,用钟罩将精练剂压入铝液中,距坩埚底100毫米处作水平缓慢移动,待反应基本完成后取出钟罩,静置10分钟。
d,均匀撒入集渣剂,促使混在溶渣中的铝液汇入熔池中以减少损耗,同时使铝液和熔渣分离,提高铝液质量,然后扒渣,集渣剂的加入量为铝液的0.1-0.2%。
(3),变质、细化处理
a,细化剂用量为铝液的0.2-0.3%,变质剂用量为铝液的0.2-0.3%。
b,处理温度为710-720度,处理时间4-5分钟。
c,在处理温度下,用钟罩将变质剂和细化剂压入铝液,距坩埚底
100-150毫米处作水平移动,待变质细化良好后撇掉残余细化剂及熔渣。
3,检验铝液质量
(1),含气量检验
a,浇注试样,试样规格为D50×20。
b,将试样的铸型预热到300-400度,浇入试样铝快,在凝固前用干净的铁片扒去表面氧化皮,检验铝液中的含气量,以铝液金属表面不冒气泡或极少的小气泡为合格。
c,试样凝固后打开试样断面,根据断面上的白点检验铝液的含气量。
(2),化学成分的测定
每炉批均应作炉后分析,以检验已经浇注的合金的化学成分是否合格和指导下一炉的配料,试样规格与含气量试样相同。
(3),细化效果检验
a,浇注试样,试样显扁平状,在金属型中铸成,其断面一般选择与铸件
最大壁厚一致。
b,观察试样断口状态,当断口为银白色,断口平整,组织细致,有时可
见细小,分布均匀的硅亮点,此时即为细化良好状态。
c,当细化不足时(断口显暗灰色,断口较平整,组织粗大,硅亮点较大).应重新加入细化剂。
铝液质量检验合格后清理坩埚边,组装密封盖,准备浇注,合盖浇注前先浇注理化试样,并写上炉批号。
二,低压浇注工艺
1,浇注准备
(1),设备调试。
(2),接通升液管,调整温度。
按以下工艺参数进行调整:
P
(MPa)
P1
注:该数据视具体的轮子型号来定
型号 P2 △t1 △t2
J81-K28 0.024-0.028MPa 3-5s 100-140s
J92 0.026-0.03MPa 2.5-3s 100-140s
110J,J114 0.024-0.024Mpa 4s 100-140s
HT3B
12GJ,J140 0.018MPA 2s 240s
2,浇注
a,接通控制柜与坩埚的连接管道。
b,升液管口平面上放置石棉垫板和过滤网片。
c,石膏型清除型内杂质(石膏型出炉温度为180度左右)置于低压浇注机上压紧(注意不能将石膏型压坏.)避免石膏型开裂。
d,按动浇注控制按钮,浇注铸件,铝液浇注温度为690-720℃在保证铸件成型的情况下浇注温度越低越好。
e,浇注完毕,石膏铸件空冷。
注:
1,浇注现场应有良好的通风周围不得有积水。
2,操作者应穿戴好防护用品。
3,低压浇注应使用干燥清洁的压缩空气,连续工作一个月,应拆开过滤器处理干燥剂。
三,铸件清理,修正
1,石膏型的自然冷却,不得低于1小时。
2,铸件的脱型清理不能采用铁锤等敲击,振动等手段,一般情况下采用手工操作,轻轻敲击石膏型,震落边缘石膏,取出铸件。
3,修正去毛刺,去除表面可修复性缺陷。
4,铸件初步检验。
四铸件的热处理工艺
按制订的热处理工艺进行热处理。
五铸件表面处理
1,水喷砂处理。
<<水喷砂操作规程>>
2,将喷砂好的铸件浸入80度的水中1-2分钟,吹干,经表面处理
后的铸件表面显银白色或银灰色。
六铸件的最终检验
1,铸件的几何尺寸按图纸要求.
2,铸件外观要求符合规范标准。
3,机械性能符合规范标准。
4,铸件荧光检验(100%)符合荧光检验标准。
5,检验合格的铸件即可入库。
石膏型烘干工艺参数守则
本工艺参数规程仅适用于本公司石膏型低压浇注中的石膏型的烘干过程参数的控制。
烘干工艺参数:
室温加热2H ℃
保温10H后加热2H 100℃保温15H后加热2H 150℃
保温10H后加热2H 200℃
、J95保温至浇注结束
注:加“”者为冬天采用,而夏天则不宜采用。