中国LNG产业链核心技术发展方向
lng市场发展现状及未来趋势分析

lng市场发展现状及未来趋势分析近年来,液化天然气(LNG)市场经历了快速发展。
LNG作为清洁、环保的能源替代品,被视为未来能源的重要选择。
本文将对LNG市场的现状进行分析,并展望未来的发展趋势。
首先,我们来看LNG市场的现状。
近年来,全球LNG需求持续增长,LNG供应链不断完善。
根据国际能源署(IEA)的数据,2019年全球LNG需求达到了3590亿立方米,较上一年增长12%。
而LNG供应方面,全球LNG出口国和进口国数量都在不断增加。
美国作为新兴LNG出口国,其LNG出口量连续多年位居全球第一。
其次,我们将分析LNG市场的发展驱动力。
首先是环境保护意识的提高。
随着全球气候变化问题的日益突出,各国政府纷纷推动清洁能源的发展,LNG作为一种低碳、低排放的能源,受到了广泛关注。
其次是天然气需求的增长。
随着工业化和城市化进程的加快,全球对清洁能源的需求不断增长,而天然气的供应相对丰富,因此LNG作为天然气的液化形式具有巨大潜力。
在未来的发展中,LNG市场将面临一些挑战。
首先是全球经济增长的不确定性。
经济增长的放缓可能会导致能源需求的下降,从而对LNG市场产生不利影响。
其次是竞争风险。
随着LNG供应国数量的增加,市场竞争压力加大,部分LNG供应商可能会面临价格战等问题。
此外,跨境天然气管道项目的发展也可能会对LNG市场造成一定的冲击。
然而,尽管面临挑战,LNG市场依然具备广阔的发展前景。
首先,LNG的清洁能源属性将继续受到重视。
随着全球环境问题的日益严峻,各国对清洁能源的需求将继续增长,而LNG作为一种低碳能源,将在清洁能源转型中发挥重要作用。
其次,新兴市场的潜力巨大。
尽管发达经济体对LNG需求的增长有限,但新兴市场如印度、中国等地的需求将大幅增加,为LNG市场提供了新的增长点。
此外,技术进步和创新也将推动LNG市场的发展。
例如,LNG的储存和运输技术不断改进,使得LNG能够更加高效地运输到全球各地。
LNG行业现状与前景分析

LNG⾏业现状与前景分析LNG⾏业现状与前景分析第⼀章LNG的基础知识简介 (3)1.1 LNG特性介绍 (3)1.2 LNG优势分析 (3)1.3 LNG主要⽤途 (3)第⼆章LNG⾏业的发展背景与机遇 (5)2.1 LNG⾏业的发展背景 (5)2.2 LNG⾏业的战略作⽤ (5)2.3 政策⽀持LNG⾏业快速发展 (6)第三章LNG⾏业的现状与前景 (7)3.1 LNG⾏业的现状 (7)3.2 LNG⾏业存在的问题 (9)3.3 LNG⾏业的发展前景 (10)第四章LNG⾏业风险分析 (11)4.1 宏观经济波动风险 (11)4.2 政策风险 (11)4.3 价格风险 (12)4.4 需求风险 (12)4.5 替代品风险 (12)第五章LNG⾏业竞争状况分析 (13)5.1 LNG⾏业进⼊壁垒分析 (13)5.2 LNG⾏业竞争结构SWOT分析 (13)第六章LNG产业链分析 (15)6.1 LNG产业链构成 (15)6.2 LNG处理步骤介绍 (16)6.3 LNG产业链的上游 (17)6.4 LNG产业链的中游 (21)6.5 LNG产业链的下游 (23)6.6 LNG设备制造⼚家分析 (25)第七章我公司LNG运营分析 .......................... 错误!未定义书签。
7.1独⾃成⽴运营企业 ..................................... 错误!未定义书签。
7.2 与中⽯油、中⽯化等合资成⽴运营公司错误!未定义书签。
第⼀章LNG的基础知识简介1.1 LNG特性介绍LNG是英⽂Liquefied Natural Gas的简称,即液化天然⽓。
它是天然⽓(甲烷CH4)在经净化及超低温状态下(-162℃、⼀个⼤⽓压)冷却液化的产物。
液化后的天然⽓其体积⼤⼤减少,约为0℃、1个⼤⽓压时天然⽓体积的1/600,也就是说1⽴⽅⽶LNG⽓化后可得600⽴⽅⽶天然⽓,⽆⾊⽆味,主要成份是甲烷,很少有其它杂质,是⼀种⾮常清洁的能源。
2024年LNG加气站市场市场分析现状

LNG加气站市场分析现状一、市场背景随着全球环境保护意识的增强,清洁能源的需求逐渐增加。
液化天然气(LNG)作为一种清洁、高效、环保的替代能源,被广泛关注并应用于交通运输领域。
LNG加气站作为LNG能源的供应基地,发展前景广阔。
本文将深入分析中国LNG加气站市场的现状及发展趋势。
二、市场现状1. 增长势头强劲LNG加气站市场在过去几年取得了快速增长。
中国政府积极推动清洁能源的发展,对LNG加气站的扶持政策不断完善,使得LNG加气站建设进入快速发展阶段。
据统计,截至目前全国已建成的LNG加气站数量超过500座,且增长仍然迅猛。
2. 区域分布不均衡目前中国LNG加气站的分布存在较为明显的区域差异。
主要集中在沿海地区、东北地区以及部分经济发达地区。
而中西部地区的LNG加气站建设相对滞后,仍具有较大的发展空间。
3. 市场竞争加剧随着LNG加气站市场的蓬勃发展,市场竞争日益激烈。
一方面,LNG加气站建设企业数量不断增加,市场竞争进一步加剧;另一方面,LNG加气站服务商为了提高竞争力,纷纷推出创新产品和服务,加速市场渗透。
三、市场前景1. 政策环境助力中国政府对清洁能源的支持将继续加大,在政策环境的推动下,LNG加气站市场仍将保持快速增长。
政府将加大对LNG加气站建设的投资力度,并进一步完善相关政策法规,为市场发展提供有力保障。
2. 加气技术创新随着科技的不断进步,LNG加气站的技术也在不断创新。
目前,LNG加气站建设已经实现了全自动、智能化管理。
未来,随着技术的成熟,加气效率将进一步提高,加气时间将更加快捷,为用户提供更好的服务。
3. 中西部市场潜力巨大当前,中西部地区的LNG加气站建设仍然滞后,市场潜力巨大。
近年来,随着中西部地区经济的发展和交通网络的完善,该地区LNG加气站市场将逐渐释放潜力,成为未来的发展重点。
四、市场挑战1. 成本压力较大LNG加气站的建设和运营成本较高,面临着资金压力。
尤其是在新建LNG加气站时,需投入大量资金进行设备采购和场地开发。
2024年LNG物流市场发展现状

2024年LNG物流市场发展现状引言液化天然气(LNG)是天然气在低温下处理而得到的液态形式。
近年来,LNG的需求不断增加,特别是作为清洁能源的替代品。
随着我国对可再生能源和清洁能源的重视,LNG的物流市场也逐渐发展起来。
本文将通过对LNG物流市场的调研分析,探讨目前LNG物流市场的发展现状。
1. LNG物流市场规模1.1 LNG产量和消费量根据国家能源局的统计数据,我国LNG产量在过去五年内有了显著增长。
截至2020年,中国LNG产量达到XX亿立方米,同比增长XX%。
而LNG的消费量也在不断增加,据预测,到2025年,我国LNG消费量将超过XX亿立方米。
1.2 LNG运输量LNG的运输方式主要包括海上运输和陆上运输。
目前,我国的LNG运输主要依靠LNG船舶和LNG管道等方式进行。
据统计,2019年我国LNG进口量达到XX亿立方米,同比增长XX%。
而国内LNG管道运输量达到XX亿立方米,同比增长XX%。
2. LNG物流市场结构2.1 LNG供应链LNG供应链主要包括LNG生产、运输、储存和销售等环节。
目前,我国的LNG 供应链基本成熟,涵盖了从LNG生产厂商到终端用户的全过程。
在LNG生产环节,国内有多家大型LNG生产企业,如中石油、中石化等。
而在LNG运输环节,除了LNG船舶和管道运输,还出现了一些新兴的运输方式,如LNG陆上集装箱运输等。
2.2 LNG市场参与方LNG物流市场的参与方主要包括生产商、运输商、储存商和销售商等。
这些参与方在LNG物流市场中发挥着不同的角色。
目前,我国的LNG物流市场参与方众多,其中包括本土企业和国际知名企业。
这些企业利用自身优势,通过合作共赢的方式推动LNG物流市场的发展。
3. LNG物流市场发展趋势3.1 政策推动随着我国能源结构调整的需要,政府出台了一系列支持LNG物流市场发展的政策措施。
这些政策从税收减免、资金支持等方面为LNG物流企业提供了良好的发展环境,进一步推动了LNG物流市场的发展。
浅谈国内LNG产业链发展前景
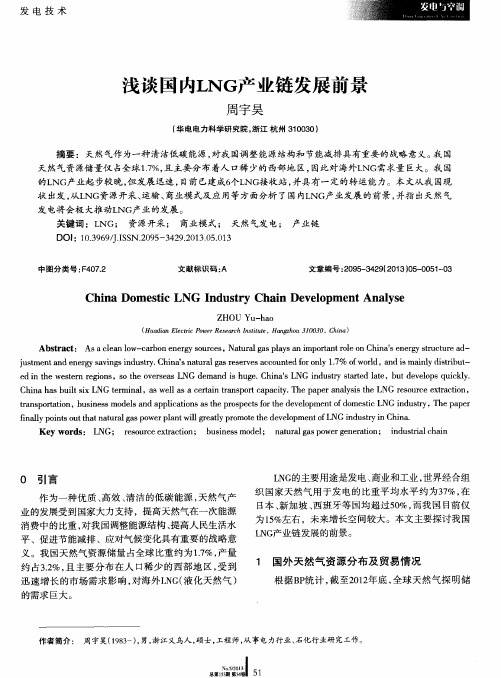
0 引 言
作 为 一 种优 质 、 高效 、 清 洁 的低 碳 能 源 , 天 然 气 产 业 的发展 受 到 国家 大力 支 持 ,提高 天然 气在 一 次 能源 消费 中 的 比重 , 对 我 国调整 能 源结构 、 提 高人 民生活 水 平 、促 进 节 能减排 、应对气 候 变化 具有 重要 的战 略意
Ke y wo r d s : L NG; r e s o u r c e e x t r a c t i o n ; b u s i n e s s mo d e l ; n a t u r a l g a s p o w e r g e n e r a t i o n ; i n d u s t r i a l c h a i n
中 图分 类 号 : F 4 0 7 . 2
文献标识码 : A
文章 编 号 : 2 0 9 5 — 3 4 2 9 ( 2 0 1 3) 0 5 — 0 0 5 1 — 0 3
Ch i n a Do me s t i c LNG I n d u s t r y Ch a i n De v e l o p me n t An a l y s e
发 电将 会 极 大推动 L NG产 业 的发 展 。
关键 词 :L NG; 资 源开采 ; 商业模 式 ; 天然 气发 电 ; 产 业链
D OI : 1 0 . 3 9 6 9 / J . I S S N. 2 0 9 5 — 3 4 2 9 . 2 0 1 3 . 0 5 . 0 1 3
j u s t m e n t a n d e n e r g y s a v i n g s i n d u s t r y . C h i n a ' s n a t u r a l g a s r e s e r v e s a c c o u n t e d f o r o n l y 1 . 7 %o f w o r l d , a n d i s ma i n l y d i s t r i b u t —
国内外lng的的现状和发展趋势

国内外LNG的现状和发展趋势什么是LNG?LNG 全称液化天然气(liquefied natural gas),是天然气在超低温环境下通过液化处理而成,即将气态天然气冷却至零下162度左右,使其凝结成为液态,从而减小体积和增加储存能力。
国内LNG的现状LNG在中国的应用起步较晚,但随着近年来环保政策的推动,其发展迅速。
目前,中国LNG行业主要集中在天然气获取、储存、运输和应用四个方面。
天然气获取中国的天然气供应相对较少,进口天然气是中国目前主要的天然气来源。
数据显示,中国是全球最大的LNG进口国之一。
储存LNG 易于存储和运输,因此被广泛应用于船舶、储罐以及储备能源等领域。
运输LNG的运输主要分为海运和陆运两种方式。
海运时,LNG一般被储存在巨型液化天然气船上,运输到不同的港口或国家。
陆运时,则需要通过输气管道或储罐车进行运输。
应用LNG的应用领域主要包括工业、民用和汽车等方面。
其中,工业领域是LNG 的主要消费领域,主要应用于电力和化工等领域。
国内LNG的发展趋势未来,中国LNG市场的发展趋势将会体现在以下几方面:市场潜力随着国内环保政策的推动,LNG在我国的市场需求将会日益增加。
加之一些相关政策的扶持,未来LNG市场潜力巨大。
进口量增加目前,中国主要依赖一些进口LNG来满足市场需求。
随着市场潜力的不断扩大,未来中国也将加大进口LNG的力度。
技术创新技术创新是LNG行业发展的重要推动力。
目前国内企业在LNG技术创新方面做出了很多努力,如LNG储罐的研发等。
国外LNG的现状和发展趋势LNG在国外的使用时间较长,其产业的发展也更为成熟。
目前,LNG在国际市场中占据着较大的份额。
据数据显示,美国是目前全球最大的LNG生产国之一,在此之后分别是澳大利亚和卡塔尔。
未来,国外LNG市场的发展趋势则表现在以下几方面:慢慢进入饱和期虽然国外LNG市场产值巨大,但LNG行业正在向饱和期发展。
此外,在一些国家政策限制下,LNG产业发展有所受阻。
中小型LNG 在中国的发展前景(谢亮)
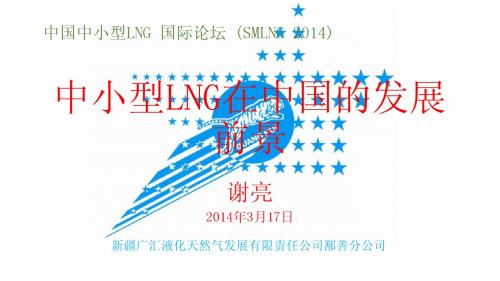
2、 LNG汽车推广配套设施进展情况
国家863《中重型LNG专用车辆开发》情况
2006年10月,新疆广汇液化天然气公 司承担了“国家863《中重型LNG专用 车辆开发》”课题,联合国内主要发动 机公司、整车生产单位、燃气汽车改装 单位、供气系统生产等单位,进行了为 期两年的柴油车改造为LNG单一燃料 的试验,在2009年2月24日,新疆维吾 尔自治区汽车产品质量监督检验站对新 疆广汇开发研制的2辆LNG半挂牵引车 的安装技术、整车安全性、排放性、动 力性、经济性和整车可靠性进行检验, 结果(2009新汽检001号)符合国家机 动车及LNG汽车相关标准,并于2009 年3月31日通过国家科技部863计划现 代交通技术领域办公室的验收,并获得 LNG车辆两项专利(专利号:200920139807.8、
据卓创资讯对全国69家LNG工厂的监测数据显示,截至本周四(3月
13日),开工厂家59家,LNG工厂周均开工率为54%,比上周回落1%。 LNG工厂周均日产2101万立方米,比上周增加9万立方米。 先锋解化设计日产能60万方的LNG项目以及山东西能设计日产能30 万方的LNG项目均稳定对外销售,对外出液工厂增加至69家,总日产
2014 年3月中国LNG工厂检修表 单位:万立方米/日 制作单位:卓创资讯
生产商 禹城华意 吉林天德 吉林天吉 三峡赛普 靖边星源 河北华气 成都永龙 中海油营口 舜天达 吉林天富 吉林天翔 新连海 世益 亨通 新源 寰达 创美 达州汇鑫 昆仑格尔木 中原绿能 位置 山东 吉林 吉林 甘肃 陕西 河北 四川 辽宁 天津 吉林 吉林 甘肃 内蒙 内蒙 内蒙 内蒙 内蒙 四川 青海 河南 起始时间 2013年11月下旬 2013年10月28日 2013年11月20日 2013年12月18日 1月27日 1月底 1月29日 2月 6日 2月25日 2月26日 2月26日 3月 1日 3月 5日 3月 5日 3月 5日 3月 5日 3月 5日 3月 9日 3月10日 3月13日 终止时间 —— —— 3月10日 3月下旬 3月中旬 —— 3月1日 3月15日 3月1日 —— —— —— 3月6日 3月6日 3月6日 3月6日 3月6日 3月12日 3月下旬 3月16日 检修能力 5 7 20 20 150 100 10 18 12 10 5 38 10 30 30 30 20 100 35 30 设计能力 5 7 10 20 150 100 10 18 12 10 5 38 10 30 30 30 20 100 35 30 备注 装置停工 装置停工 装置停工 气源受限 装置停工 装置停工 装置停工 装置停工 装置停工 装置停工 装置停工 装置故障 电力检修 电力检修 电力检修 电力检修 电力检修 装置故障 装置检修 厂区停电
LNG的发展现状与前景

关于如何推动LNG发展的讨论药学院陈洁烽10353069摘要LNG具有多种传统能源没有的优点,而且,LNG的使用在我国得到了一定的认可和推广。
因此,在当今能源紧缺的时代,LNG必将会成为主流能源之一。
所以,我国必须大力发展LNG产业,以解决能源危机。
关键词LNG产业链LNG进口市场化0 前言LNG即液化天然气,是一甲烷为主要组分的天然气在低温下的液态混合物,其体积仅为气态是的1/625,具有运输方便、储存效率高、生产使用安全、环保等特点[1]。
因此LNG具有成为新一代主流能源的潜力。
1 LNG发展的必要性下面就的发展现状来具体分析推动LNG发展的必要性:(1)中海油LNG产业链的形成广东液化天然气项目的正式投产,标志着我国LNG产业进入了一个新里程碑。
在中海油的投资下,国内整个LNG的产业得到了蓬勃发展,而目前中国海洋石油总公司参与的广东、福建、上海等的LNG项目已经进入生产运营期,浙江宁波、珠海、深圳等LNG项目正进入建设和前期研究阶段[2]。
自从1995年中海油确立了“油气并举,向气倾斜”的发展战略,天然气的开发得到的深入研究。
如今已形成一条完整的产业链,若在此的基础上进一步发展的,将会在能源问题上得到很大的解决。
(2)LNG储罐国产化的可能性目前,我国的LNG产业已初具规模,每年进口的LNG已达数百万吨,预计2020年,我国沿海地区进口LNG规模可达6000×104吨[3]。
因LNG的进口量大,LNG储罐的需求也因此加大,所以需要将储罐国产化。
目前有关储罐的技术如9Ni钢焊接等也有一定的技术基础,在大连的LNG项目3号罐也开始安装,总容量达16万立方米[4]。
可见在LNG的储罐上就需要大力的发展,这是当代中国不可忽视的一环。
(3)中小型LNG市场的发展在中小城镇以及大中城市的边远校区因为地理限制,而使管道运输不便和不经济,因此利用LNG的运输灵活得优势,建设LNG卫星站,能够作为燃气供应使用。
中国LNG的发展
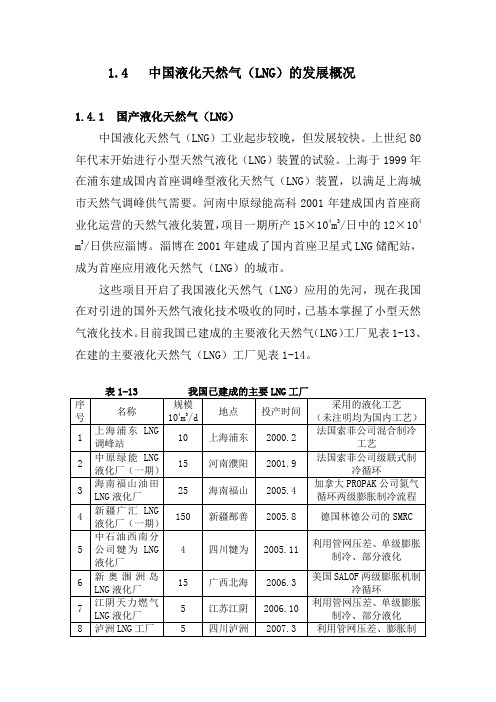
1.4 中国液化天然气(LNG)的发展概况1.4.1 国产液化天然气(LNG)中国液化天然气(LNG)工业起步较晚,但发展较快。
上世纪80年代末开始进行小型天然气液化(LNG)装置的试验。
上海于1999年在浦东建成国内首座调峰型液化天然气(LNG)装置,以满足上海城市天然气调峰供气需要。
河南中原绿能高科2001年建成国内首座商业化运营的天然气液化装置,项目一期所产15×104m3/日中的12×104 m3/日供应淄博。
淄博在2001年建成了国内首座卫星式LNG储配站,成为首座应用液化天然气(LNG)的城市。
这些项目开启了我国液化天然气(LNG)应用的先河,现在我国在对引进的国外天然气液化技术吸收的同时,已基本掌握了小型天然气液化技术。
目前我国已建成的主要液化天然气(LNG)工厂见表1-13、在建的主要液化天然气(LNG)工厂见表1-14。
由上表可以看出,我国的国产液化天然气(LNG)行业发展迅速,呈现出爆炸式增长的态势。
1.4.2 进口液化天然气(LNG)中国进口液化天然气(LNG)项目于1995年启动,当时国家计委委托中国海洋石油总公司进行东南沿海液化天然(LNG)引进规划研究。
1996年12月中海油上报了《东南沿海地区利用LNG和项目规划报告》。
2006年6月在广东大鹏湾秤头角建成了我国第一个液化天然气(LNG)接收站(接收终端)项目,项目包括LNG接收站和输气干线项目,以及配套新建电厂、燃油电厂改造和城市燃气管网项目。
一期进口LNG能力为370×104 t/年,折合输气量约40×108m3/年。
目前,除广东外,福建、上海的液化天然气(LNG)接收站已建成投用,另外十余座接收站项目正在建设中,见表1-15。
除广东LNG接收站外,其他几个主要LNG接收站的情况如下:福建LNG接收站项目:地点在莆田湄洲湾。
一期设计能力为年进口LNG260×104t。
LNG应用技术发展现状及前景

中国L N G应用技术发展现状及前景一、慨述近年来,随着世界天然气产业的迅猛发展,液化天然气LNG已成为国际天然气贸易的重要部分;与十年前相比,世界LNG贸易量增长了一倍,出现强劲的增长势头;据国际能源机构预测,2010 年国际市场上LNG的贸易量将占到天然气总贸易量的30%,到2020年将达到天然气贸易量的40% ,占天然气消费量的15%;至2020年全球天然气消费量将继续以年2%~3%的增长率增长,而LNG在天然气贸易市场中所占份额也将逐步增大,达到8% 的年增长率; LNG在国际天然气贸易中发展势头如此强劲,地位越来越重要,这都得益于世界LNG 应用技术的发展;世界上普遍认为:液化天然气工业是当代天然气工业的一场革命,其发展已经历了六十多年的历史,形成了从液化,储存,运输,汽化到终端利用的一整套完整的工艺技术和装备;LNG是天然气的一种储存和运输形式,其广泛使用有利于边远天然气的回收和储存,有利于天然气远距离运输,有利于天然气使用中的调峰和开拓市场,以及扩展天然气的利用形式;我国早在六十年代,国家科委就制订了 LNG 发展规划, 六十年代中期完成了工业性试验;四川石油管理局威远化工厂拥有国内最早的天然气深冷分离及液化的工业生产装置,除生产 He 外,还生产 LNG ;进入九十年代,我国进一步开始了液化天然气技术的实践, 中科院低温中心联合有关企业,分别在四川和吉林研究建成了两台液化天然气装置,一台容量为每小时生产方LNG ,采用自身压力膨胀制冷循环,一台容量为每小时生产方LNG,采用氮气膨胀闭式制冷循环;与国外情况不同的是,国内天然气液化的研究都是以小型液化工艺为目标;随着我国天然气工业的发展,在液化天然气技术实践的基础上,通过引进国外技术,第一台事故调峰型天然气液化装置于2000 年在上海浦东建成,第一台商业化的天然气液化装置于2001 年在中原油田建成;这标志着,在引进国外天然气液化技术的基础上,国内天然气液化应用技术开始全面推开,随后在新疆,四川等地相继有多个LNG工厂建成投产,促使我国天然气从液化,储存,运输,到终端使用的LNG应用技术的全面发展;二、中国LNG应用技术发展现状从2001年中原油田建成的第一套商业化天然气液化装置开始,到目前近十年的时间,我国LNG应用技术得到了快速发展,建立起了涉及天然气液化,储存,运输,汽化和终端使用,以及配套装备各个方面,具有中国特色的LNG产业,成为了我国天然气工业发展中的一个重要方面;主要体现在:1、天然气的液化、储存和运输目前,我国已建成近20套LNG生产工厂,总规模达到了年产LNG146万吨,在建和待建的还有10套,总规模达到了年产LNG120万吨;前期的工厂大都是在引进国外技术的基础上,通过消化吸收与国内技术相结合完成,中原天然气液化装置由法国索菲燃气公司设计,使用丙烷和乙烯为制冷剂的复叠式制冷循环;新疆广汇天然气液化装置由德国林德公司设计,采用混合制冷剂循环;而国内已建和拟建的中小型 LNG 液化工厂,其液化设备除主要设备外基本以国产设备为主,配套国产化设备已达到60%;近年来,随着多套小型液化装置的建设,我国已完全能自行设计、制造、安装和调试LNG生产装置;2009 年10 月, 由四川空分设备集团有限责任公司自行设计、制造、安装和调试的宁夏30 万方/天天然气液化装置在银川开发区正式开车成功;该套装置采用带制冷机预冷的氮、甲烷混合介质膨胀制冷工艺流程,是目前国内最大的完全国产化的天然气液化装置;在LNG储运方面,我国在低温液体储罐领域,如液氧、液氮、乙烯储罐,国内已有成熟的设计、建造技术;四川空分设备集团有限公司从20 世纪80 年代开始吸收外国设计,建造储罐的先进技术,近年来自主开发了400~6000方的低温液体储罐,目前已建成该类储罐上百台,其中2000方以上储罐20 多台;在国内主要有堆积绝热、高真空缠绕绝热和真空粉末绝热三种类型的LNG储槽,容积从30~700 方组合不等;而结构形式有立式和卧式两种;根据目前国内大型低温LNG 储罐设计、建造技术现状,我国30000 方以下的LNG 储罐实现自主设计、建造的条件已基本成熟;LNG槽车国内也是近年开始研制的;目前有30 方、40 方和、45 方、50 方等规格;因受车规的限制,目前真空粉末绝热一般以30~35 方为限,而多层绝热可能达40~50 方 ,而且从行走、底盘、制动、照明等方面均有新的改善;目前我国LNG槽车运载能力已达到2000万方规模,总车俩数1000多俩,单车有效容积从最初的29方发展到了51方,具有多家专业生产LNG槽车的企业和专业运输公司;同时,罐式集装箱近年来也得到了大力发展;罐式集装箱一次可装运方、40方或方LNG产品,采用高真空多层绝热,绝热性能好,无损储存时间长,自重轻,运输灵活;可公路,水路,铁路运输,或实现联运;51方LNG运输挂车2、LNG卫星站随着LNG生产装置商业化运行,LNG卫星站也得到了快速发展;以2001年建成投产的山东淄博LNG卫星汽化站为标志,在全国已建成100多座日供气规模在1-60万方的LNG卫星站,主要分布在华南和长三角等沿海经济发达地区;目前LNG卫星站已成为城市燃气调峰和弥补管道天然气不足的重要手段;LNG卫星站LNG卫星站主要具有接卸、储存和汽化功能;我国的LNG卫星站以及陆上运输技术也已基本成熟,高真空粉末和超级真空缠绕式绝热技术得到了快速发展,小型LNG瓶方以下的无损存放期在15 天以上,车载罐和卫星站储罐在75 天以上,LNG卫星站的建造和内陆液态运输设备制造都已完全国产化,同类型同性能产品价格比国外成倍的便宜,极具竞争力;已形成的一整套完善、成熟确保安全的小型LNG运输、储存、气化和使用技术,以及一套有关运输、储存和使用的规范和法规,为我国LNG卫星站的健康发展奠定了基础;3、大型LNG接收站中海油1995年受国家发改委委托,在广东沿海开展前期研究建设大型接收站引进国外LNG资源,1999年底国家正式批准在广东深圳试点建设LNG接收站一体化工程项目,从此开始了我国大型LNG接收站的建设;2003年福建LNG一体化工程项目获国家批准,成为我国第二个正式启动的LNG 项目;随后,三大石油公司分别在辽宁、河北,山东,江苏,上海,浙江,海南、广东,广西的沿海地区开展LNG 项目的前期研究工作,积极推动我国大型LNG接收站的建设;广东接收站一体化项目包括LNG接收终端和输气干线项目,以及配套新建电厂、燃油电厂改造和城市管网等用气项目;供气范围覆盖珠江三角洲和香港特区,输气主干线全长为509 km整个工程分两期完成,一期工程包括接收终端和输气干线,每年进口LNG的量为370 ×104 t/ a,年输气量约为40 ×108 m3/ a;二期工程增加1座10 ×104 m3的LNG储罐,每年进口LNG达700 ×104 t/ a,年输气量约82 ×108 m3 / a;项目一期于2006年5月建成投产,标志着我国成功实现了国外天然气的引进,并通过项目的建设,既引进了大型LNG接收站设计和建造技术,又发展了配套产业,同时培养和锻炼了从事LNG应用技术的人才和队伍;对于大型LNG接收站建设,最关键的应用技术是大型储罐的设计和施工;我国最早建造大型液化气体储罐始于90年代中期,分别在深圳和扬子石化建造了2台8OOOO液化石油气LPG低温储罐和10000方低温乙烯储罐;90年代末,上海建造了我国第一台20000低温LNG 储罐;2002-2005年合肥通用机械研究院等单位,承担原国家经贸委“十五”重大技术装备研制项目专题“20000方液化天然气储罐研制”等课题,着重对9Ni 钢焊接、无损检测和低温绝热材料及结构、LNG 储存安全等进行了研究;大型低温LNG 储罐内罐用低温材料选用是其设计与建造的技术关键之一;现在低温LNG 储罐内罐材料最常用的是9Ni 钢和不锈钢,前者因其强度高、低温韧性好广泛应用于大型低温LNG 储罐,后者主要用于50000方以下的中、小型低温LNG 储罐;长期以来,9Ni 钢及其焊接材料一直依赖进口,这是困扰我国大型LNG 工程建设的一个难题;2005-2007年,太原钢铁集团公司承担科技部863项目“液化天然气储罐用超低温9Ni 钢开发及应用技术”研究工作,成功研制出国产9Ni 钢06Ni9 ,随后合肥通用机械研究院等单位对06Ni9钢的综合材料性能与焊接性能进行了广泛深入的技术实验,结果表明:国产9Ni 钢06Ni9的综合性能指标超过了美国标准ASTM A553/A553MⅠ型和欧盟标准EN 10028的要求,与日本、欧洲按上述美欧标准生产的9Ni 钢水平相当或略高;2007年该钢通过了全国锅炉压力容器标准化技术委员会组织的专家评审,同意用于低温储罐和低温压力容器;中石油在建的江苏南通、辽宁大连两个LNG 项目中的16万方LNG 储罐,内罐低温材料已选用国产06Ni9钢;2009 年9月, 中国石油大连液化天然气有限公司位于大孤山半岛的第一个液化天气LNG 储罐罐顶平稳到达预定位置, 标志着我国第一个自主设计、自主采办、自主施工、自主管理的大型LNG 项目储罐升顶作业一次成功, 为我国独立自主建设LNG项目积累了成功经验;这是我国大型低温LNG 储罐国产化的一个重要里程碑;在施工工艺技术方面,国内已建和正建的低温LNG 储罐,不管其工艺及设备技术来自何方,但储罐建造施工无一例外地都由国内施工队伍完成;因此,国内较早承担大型低温LNG 储罐建造施工的企业,已积累了丰富的经验,并在基础及罐壁混凝土施工、内外罐组装焊接施工和绝热结构施工等方面对国外技术进行了改进;目前,我国在LNG相关设计规范与标准、绝热材料、施工工艺技术等方面所取得的积极进展,以及工程设计与施工企业参与大型低温LNG 储罐设计建造的实践,为我国大型低温LNG储罐国产化打下了一定的基础;4、LNG船运LNG 运输船是造船业公认的技术含量、附加值最高、难度最大的货轮,只有美国、日本、韩国和欧洲的少数几个国家的造船厂能建造;在广东LNG 项目中,为实现“国货国运,国船国造”目标,引入了国内造船企业参与竞标,上海沪东中华船厂在招标中最终胜出,从而为中国造船工业争取到一个重要的发展机遇;中国目前是世界第三大造船国,我国造船企业从90年,就开始积极引进和吸收国外先进的LNG船舶建造技术和经验;沪东中华造船厂早在1997年就开始了研发建造LNG船项目,2000年首先成功制造出LNG液货舱模分段,并获得法国GTT公司,以及BV,ABS,LR;DNV等船级社的认证;江南造船厂1996年开始为争取承建LNG船进行相关技术储备,2002年突破了建造LNG船的核心技术,成功建造了NO96薄膜型LNG船货物维护系统,获得法国船级社颁发的LNG船模舱建造证书;同时又与芬兰玛莎造船公司签订了球罐型LNG船设计转让协议,成功引进新型球罐型LNG船设计技术;大连新船重工于2002年获得了法国船级社,以及BV,ABS,LR;DNV等船级社颁发的LNG船模型舱特殊舱室制作证书,掌握了建造LNG船的核心技术;2008年4月,沪东中华造船厂自主建造的我国第一艘LNG船成功交付,标志着我国基本掌握了世界造船尖端技术;沪东中华造船厂在首艘LNG船的制造过程中已经研发了一批LNG船的建造技术,形成了9项专利,并将集中精力进行LNG系列船型的开发,逐步形成自己的品牌;目前,由沪东中华造船厂建造的5艘LNG船已全部交付业主使用,在该批次LNG船上,国产优质船用钢板和低温不锈钢材料、玻璃棉、低密度刚性绝缘和柔性绝缘等都得到了广泛应用,并获得了船东、船检、专利公司的高度认可;目前在抓紧建造在建LNG船的同时,沪东中华造船厂不断跟踪国内外液化天然气运输的需求和LNG船建造技术的发展,着手研发并向市场推出了拥有自主知识产权的16万立方米薄膜型电力推进LNG船,并成立了大型LNG船研发项目组,开展22万立方米薄膜型电力推进LNG船的设计;5、LNG终端利用我国LNG产业的快速发展,促使了LNG的终端利用,并对相关产业起到了非常大的带动作用;特别是LNG应用技术和储运装备,近几年得到了长足的发展;LNG是天然气的一种独特的储存和运输形式,非常利于降低天然气的储存成本和天然气的远距离运输,同时,天然气通过净化处理和液化,比管道输送的天然气更为洁净;因此LNG在终端使用上有比天然气更独特的特性;一是用于天然气市场的开拓;由于天然气管道建设投资大,许多地区不能及时建设管道,所以对管道气不能及时到达的地区,可用LNG培育和发展市场;二是作为管道气的补充和调峰;三是作为汽车和船代用燃料;LNG 在汽车工业中的发展优势非常明显:着火点低,燃烧清洁环保,无黑烟、无灰渣和焦油,几乎可以自由排放;体积小,能量存储密度大,连续行驶距离通常是CNG 的2 倍以上;安全性能好,储存压力低接近常压,而且密度0.45kg/m3比空气密度0.55kg/m3低,泄漏到空气里也会向空中扩散,不会影响人身安全;燃烧性能好,抗爆性强;三、发展中存在的问题我国液化天然气LNG产业经过近十年的快速发展,在应用工程技术和储运装备上取得了积极进展,具备了小型LNG工厂和LNG卫星站系统的设计和建造能力,储运装备生产能力;同时在大型低温LNG 储罐方面相关的设计规范与标准、绝热材料及结构、施工工艺技术等方面所取得的成果,以及工程设计与施工企业在大型低温LNG 储罐设计建造实践过程中取得的经验,为我国大型低温LNG储罐国产化打下了一定的基础;但是,我国在大型低温LNG 储罐标准以及设计与建造专利技术方面与国外相比仍存在较大差距;这也是目前制约30000方以上LNG 储罐实现自主设计、建造的一个重要因素;目前在建的LNG接收终端系统流程的设计基本上均采用国外技术;从目前我国LNG应用技术发展现状来看,主要还存在以下几方面问题:1、LNG相关规范标准体系不足;没有制定LNG的专用设计规范,以及LNG 质量标准,国际先进的标准也转标不足;国内LNG站设计工作一般参考美国NFPA一59A液化天然气LNG生产、储存和装卸标准2001版;应尽快颁布适合我国自身条件的LNG设计规范,制定施工标准,以指导LNG应用领域的设计、施工安装和运行管理;2、国内在建的LNG接收终端系统流程的设计均采用国外技术,国内仅具有卫星LNG站系统的设计能力,尤其是大型LNG储槽的设计与建造技术基本处于起步状态;研究人员应大力提高该方面的技术水平,开发具有自主知识产权的接收终端工艺流程;3、LNG相关设备、阀门、仪表等对材料和结构的保冷性有特殊要求,国内的设计制造水平与国际水平相差较大,应加强防腐蚀、安全性、可靠性的研究,从而大幅度降低产品成本;4、对LNG项目营运与管理缺乏综合性人才;包括液化厂、接收站、LNG 运输船、槽车、小型气化与液化装置设计制造国产化以及安全生产环保管理、经营管理等领域均需要多方面的技术管理人才;四、LNG应用技术发展前景近十年来,随着气田周边小型LNG工厂,以及沿海大型LNG接收站的建造,中国LNG应用技术得到了大力发展,促使了LNG产业的形成,基本建立起了涉及从天然气液化,储存和运输,到接收,汽化和终端利用各环节相配套的LNG 产业;展望未来,我国天然气需求旺盛,在一次能源中增长最快,液化天然气LNG 产业作为天然气工业的一个重要方面,凭借其自身独特的优势, 将促使天然气在发展方式、发展规模、投资成本、生产消费等方面呈现新的特点,同时进一步带动LNG应用技术的发展;从发展前景主要在以下几方面:1、沿海大型LNG接收站进一步的规模建设,将促使我国LNG应用技术进一步发展和完善;自2006年5月深圳LNG接收站一体化项目投产后,我国陆续投产了福建LNG接收站项目和上海接收站项目,三个项目系统流程设计均采用国外技术;通过项目实施,引进了专利技术,保证了LNG工艺的优化与最新技术的使用,同时锻炼了施工技术队伍;主要新工艺技术体现在,最大限度的收集与处理BOG保证了LNG工艺的安全;全容罐的采用最大限度的防止泄漏与事故;再冷器的利用有利于节约冷源;液体加压作为长输管线的动力有利于节能;海水冷却系统有利于节水节能;工程施工都由国内企业完成;因此,在接收站的建造过程中,国内的工程设计和施工企业都得到了很好的锻炼,并掌握了一定的关键技术;随着更多的大型LNG接收站的建设,将为我国的工程设计和施工企业提供自主设计,施工安装和运营管理的机会,从而促进LNG应用技术的发展;2、城市调峰和供气管网缺乏地区是LNG技术应用的重要方面;我国天然气资源主要分布在人口稀少、经济不太发达的中西部地区,而人口稠密、经济发达的东部及东南沿海地区天然气资源相对不足,资源分布和利用之间存在一定的矛盾;近年来,随着西气东输,忠武线,陕京一、二线,川气东送等跨区天然气管线的建设,实现了天然气从产气区向负荷中心的供应,目前我国有280多座城市使用天然气,2009年天然气消费达到了887亿;由于天然气需求旺盛,以及季节性用量差别大,往往造成地区性供气缺口,所以发展小型LNG调峰生产装置和卫星储备站,是保障城市安全平稳供气的重要手段;同时由于地区性经济发展水平的差别,一些地区管网建设有困难,可采取卫星站的方式实现天然气供应;因此,城市调峰和供气管网缺乏地区是小型LNG调峰生产装置和卫星储备站技术应用的重要方面;同时卫星储备站也是大型LNG接收站在合理经济配送半径内,最好的配套设施;3、汽车和内河航运是LNG技术应用的市场未来;从燃气汽车发展来看,经历了天然气到液化石油气,在到压缩天然气CNG 不平凡的过程,这个过程中关键的因素是资源的供应稳定和技术进步问题;近年来,由于天然气资源的快速增长和管道网络的形成,以及燃气发动机的发展,促使了CNG汽车的大力发展;然而,由于CNG须就近管网布点,在经济上才合理,以及其固有的缺点,限制了CNG加气站的大规模发展;而LNG具有CNG 同样的优点,且更具有比CNG更多的优点;因此,未来LNG车用的发展具有很大的潜力;其发展趋势主要体现在以下几方面:LNG撬装加气站1、在非管网覆盖区,以及沿海和江河地区,LNG将成为主流趋势;由于LNG是液态,非常便于经济可靠地远距离运输,在陆上,通常用20~50 m3相当于12000~30000N m3天然气的汽车槽车象运输汽柴油那样将LNG 远送到LNG汽车加气站,或LNG卫星站;也可根据需要用火车槽车,集装箱运输;在海上,通常用大至12~13万m3的 LNG轮船,进行长途运输;内河可用万m3左右的LNG船,或集装箱运输;因此,在非管网覆盖区,以及沿海和江河地区,建设LNG卫星站和汽车加气站不受天然气管网的制约,从而促使这些地区LNG业务的发展;目前,我国已有多个LNG工厂投产,沿海地区已有三座LNG 接收站,未来还将有多个接收站建成,由此可以认为,未来这些地区LNG将成为发展的主流趋势;2、城际长途交通将大力发展LNG汽车;使用LNG的汽车,由于LNG能量密度大,续使里程长;国外大型LNG货车一次加气可连续行驶1000~1300km,非常适合长途运输的需要;国内410升钢瓶加气一次在市区可连续行驶约400km,在高速公路加气一次可连续行驶约700Km以上;因此,特别适合长途大型客车和重型卡车作为燃料使用;目前,我国道路运输平均运距:客运为46.5公里,货运为171.5公里;表明道路货运在跨区间中长途运输、道路客运在短途出行服务中发挥着骨干作用;若在交通枢纽地区和高速公路沿线建设LNG加气站,势必促使城际长途交通大量使用LNG,从而促使使用LNG的汽车得到大力发展;LNG汽车加注3、连网的高速公路将是LNG加气站发展的首选;LNG的优势决定了LNG特别适合大型的长途运输车辆;目前,我国高速公路总里程达到万公里,至2010年,中国新建高速公路将达到万公里以上,总里程将达公里;“十一五”期间,交通部将着手组织实施国家高速公路网规划,五年后,中国东部地区基本形成高速公路网,长江三角洲、珠江三角洲和京津冀地区形成较完善的城际高速公路网,国家高速公路网骨架也基本形成;而据统计,2008年公路客运量和旅客周转量在综合运输体系中所占比重分别为%和%;公路货运量、货物周转量在综合运输体系中所占比重分别为%和%;完善的公路网络和庞大的运量将促使大量的运输车辆的发展,特别是大型车辆;因此,连网的高速公路将是LNG加气站重要的发展区域,并且也是最有潜力的区域;4、内河航运是LNG发展潜力非常大的市场;包括LNG运输和LNG作为船用燃料;内河航运具有运量大、成本低的优势;我国幅员辽阔,大江大河横贯东西、支流沟通南北,江河湖海相连,构成了天然内河航运网;流域面积在100km2以上的河流有5万多条、约43万公里长,大小湖泊900多个,大多水量充沛,常年不冻,为发展内河航运提供了优越的自然条件;2008年水路货运量、货物周转量在综合运输体系中所占比重分别达到了%和%; 内河航运将是我国交通发展的又一新领域相对高速公路和铁路;这势必将促使LNG作为船用燃料LNG和船运LNG的发展;目前由国内韩中深冷公司自行研制的首套船用LNG燃料系统已经通过了挪威船级社认证;该系统具备LNG储存、气化及天然气调压、供气功能,将为1艘在北欧海域运营的大型滚装船配套,为船上的燃气发动机提供燃料;今年5月份,该公司还将交付第二套同类设备;而船运LNG已相当成熟,我国已能自行建造大型的LNG运输船;因此,内河航运是LNG发展潜力非常大的市场;从以上趋势可以看出,在LNG资源充分保证的前提下,未来汽车和内河航运是LNG技术应用的主要市场;总之,LNG利用市场在中国的大力发展,为中国LNG应用技术的发展提供了广阔的空间,势必将进一步促使中国LNG工业的快速发展;。
2024年船用液化天然气(LNG)装备市场发展现状

2024年船用液化天然气(LNG)装备市场发展现状引言船用液化天然气(LNG)装备市场是近年来全球能源行业的热点之一。
随着环境保护意识的提高和全球减排目标的设定,LNG作为一种清洁能源,已经成为减少船舶排放的重要选择。
本文将分析船用LNG装备市场的发展现状,探讨其前景和挑战。
现状分析1. 市场规模船用LNG装备市场规模庞大,不断增长。
根据统计数据显示,2019年全球船用LNG装备市场规模达到XX亿美元,预计到2025年将增长到XX亿美元。
这一庞大市场规模对船用LNG装备企业来说意味着巨大商机。
2. 装备种类船用LNG装备种类多样,包括LNG发动机、LNG储存装置、LNG泵站等。
其中,LNG发动机是船用LNG装备市场的核心产品,也是船舶采用LNG作为燃料的关键。
目前市场上的船用LNG发动机技术不断创新,效率和可靠性得到大幅提升。
3. 主要市场船用LNG装备市场主要分布在欧洲、亚洲和北美地区。
欧洲是全球船用LNG装备市场的领导者,其先进的技术和政府的政策支持推动了市场的发展。
亚洲地区,尤其是中国,也成为船用LNG装备市场的重要参与者,中国政府出台一系列扶持政策,鼓励船舶采用LNG作为燃料,推动了市场的快速发展。
前景展望船用LNG装备市场的前景看好,有以下几个主要原因:1.环保要求推动需求增长:全球减排目标的提出和环保要求的不断升级,使船舶行业迫切需要减少排放。
船用LNG作为清洁能源,具有排放低、环保性强的优势,得到广泛认可。
2.政策支持推动良性发展:各国政府纷纷出台扶持政策,推动船舶行业采用LNG作为燃料。
政策的出台为船用LNG装备市场提供了强有力的支持和保障。
3.技术创新推动市场需求:船用LNG装备技术不断创新,LNG发动机效率提高,储存装置体积减小,泵站的制冷技术更加高效。
这些技术创新提高了船舶采用LNG的经济性和实用性,带动市场需求的增长。
4.发展潜力广阔:目前船用LNG装备的市场份额仍然较小,但随着全球减排目标的加速推进,未来市场潜力巨大。
lng产业链发展趋势
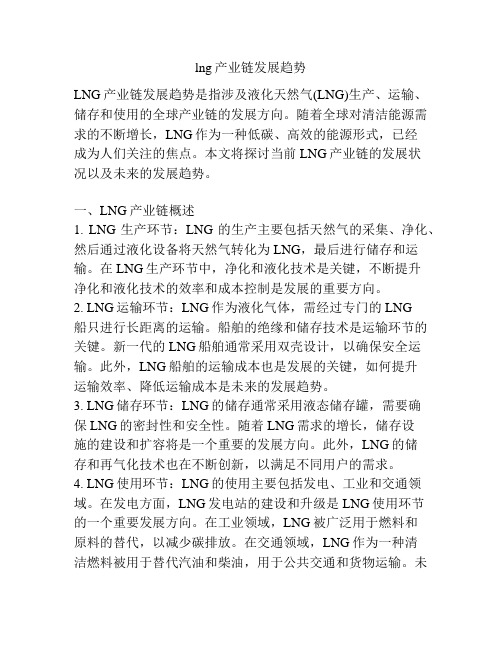
lng产业链发展趋势LNG产业链发展趋势是指涉及液化天然气(LNG)生产、运输、储存和使用的全球产业链的发展方向。
随着全球对清洁能源需求的不断增长,LNG作为一种低碳、高效的能源形式,已经成为人们关注的焦点。
本文将探讨当前LNG产业链的发展状况以及未来的发展趋势。
一、LNG产业链概述1. LNG生产环节:LNG的生产主要包括天然气的采集、净化、然后通过液化设备将天然气转化为LNG,最后进行储存和运输。
在LNG生产环节中,净化和液化技术是关键,不断提升净化和液化技术的效率和成本控制是发展的重要方向。
2. LNG运输环节:LNG作为液化气体,需经过专门的LNG船只进行长距离的运输。
船舶的绝缘和储存技术是运输环节的关键。
新一代的LNG船舶通常采用双壳设计,以确保安全运输。
此外,LNG船舶的运输成本也是发展的关键,如何提升运输效率、降低运输成本是未来的发展趋势。
3. LNG储存环节:LNG的储存通常采用液态储存罐,需要确保LNG的密封性和安全性。
随着LNG需求的增长,储存设施的建设和扩容将是一个重要的发展方向。
此外,LNG的储存和再气化技术也在不断创新,以满足不同用户的需求。
4. LNG使用环节:LNG的使用主要包括发电、工业和交通领域。
在发电方面,LNG发电站的建设和升级是LNG使用环节的一个重要发展方向。
在工业领域,LNG被广泛用于燃料和原料的替代,以减少碳排放。
在交通领域,LNG作为一种清洁燃料被用于替代汽油和柴油,用于公共交通和货物运输。
未来,LNG在交通领域的应用将是一个重要的发展趋势。
二、LNG产业链的发展趋势1. 技术的进步:随着科技的进步,LNG产业链的各个环节都在不断创新和改进。
在LNG生产环节,净化和液化技术的改进将提高生产效率和降低成本。
在LNG运输环节,LNG船舶的设计和技术将进一步提高运输效率和安全性。
在LNG储存环节,液态储存罐的设计和储存技术将变得更加先进和高效。
在LNG使用环节,燃气发电技术的提升和交通领域的LNG应用技术的创新将推动LNG产业链的发展。
LNG接收站核心技术及国产化发展趋势

2012年1月
2012年4月
2012年12月
天然气液化技术
文件解读
天然气输配技术
有限元模型计算 模拟设计
40余项专利授权 LNG接收站关键技术
20几种特殊算法及解决方案 国家LNG储罐设计标准
设计指导文件 关键施工技术和材料研究
•国际LN首G创产3项业链关键设备国产化研发
LNG投资与经济评价
国际领先6项
第 11 页
2.1 LNG接收站关键设备和材料国产化总体概况
从关键材料及装备全部海外引进,到攻克核心技术、打破国外垄断,全面实现自主设计、制造、供货,不 仅降低项目投资成本,也为实现中国制造2025迈出坚实一步。
首座LNG接收 站设备成本
投资减少40%
目前LNG接收 站设备成本 2006
随着国产化率的提升
2018年起,开发并应用LNG储罐罐顶防爆型曲轨式起重机,解决LNG储罐大型化、泵井数量增多、配置装船泵 等设备配置问题,掌握全系列的自主技术产品,实现LNG储罐用起重机的能力、类型全覆盖。
LNG储罐旋臂式起重机
• 打破国外垄断,通过中国石 油和化学工业联合会科技成 果鉴定,达到国内领先水平。
• 在天津LNG、福建LNG、广 西LNG、浙江LNG等项目应 用。
阀门类型 低温球阀 低温蝶阀 低温截止阀 低温止回阀
口径 ½ "-12" 8"-20" ½ "-6" 1“-14"
磅级 1500LB 150LB 300LB 900LB
第 17 页
2.3 主要成果及应用— X7Ni9钢、低温钢筋、保冷材料
X7Ni9钢:分别完成南钢、太钢、鞍钢、宝钢等品牌9镍钢 材的工程化应用,形成充足的国内X7Ni9钢资源;
lng技术 及其发展现状及未来趋势分析

lng技术及其发展现状及未来趋势分析LNG技术:发展现状及未来趋势分析概述:随着能源需求的不断增长,天然气作为一种相对清洁且能源效率较高的燃料,越来越受到关注。
液化天然气(LNG)技术被认为是天然气的最佳补充形式,具有更高的能源密度和更便捷的运输方式,因此在能源行业中发挥着重要作用。
本文将对LNG技术的发展现状及未来趋势进行分析。
一、LNG技术的发展现状1.1 出现背景LNG技术的出现可以追溯到20世纪60年代,当时主要用于天然气长距离海运。
由于LNG具有更低的体积和质量,可以更容易地储存和运输,因此很快受到了工业和民用领域的认可。
1.2 生产技术LNG的生产过程可以简单概括为天然气的液化和储存。
液化天然气需要降低其温度至约-162摄氏度,使用蒸发冷却剂或深冷循环进行处理。
随着生产技术的发展,LNG的生产成本逐渐降低,产能也逐步扩大。
1.3 市场应用LNG作为一种清洁能源,广泛应用于燃料供应领域。
它在发电、加热、工业生产和交通等领域都有广泛的应用,尤其在一些环保意识较高的国家和地区,LNG的应用日益增多。
二、LNG技术的未来趋势2.1 增长预测根据国际能源署(IEA)的数据,未来几十年,全球对天然气的需求将继续增长,并伴随着LNG的出口和进口贸易的增加。
预计到2030年,LNG将占据全球天然气市场的三分之一以上。
2.2 技术创新LNG技术的发展离不开技术创新的推动。
在生产过程中,应用更高效的液化技术和更低成本的储存技术将是未来的发展方向。
同时,应用其他能源技术与LNG技术的结合,如可再生能源和碳捕捉技术,将有助于进一步推动LNG技术的发展。
2.3 区域市场的变化随着LNG技术的成熟和发展,地区市场也将发生变化。
例如,亚洲地区的天然气需求快速增长,对LNG的需求也将随之增加。
预计到2030年,亚洲地区将成为全球LNG需求的主要来源。
此外,新兴市场如印度、东南亚等地区也将成为LNG技术发展的热门区域。
2024年LNG加气站市场市场前景分析

LNG加气站市场前景分析引言随着环境保护和能源转型的推进,液化天然气(LNG)作为一种清洁能源逐渐受到关注。
LNG加气站作为LNG供应的重要环节,也因此在市场上逐渐呈现出增长的趋势。
本文将对LNG加气站市场的前景进行分析,并提出相关建议。
1. LNG加气站市场现状LNG加气站市场目前处于起步阶段,在全球范围内的建设和运营都还相对较少。
不过近年来,随着环境和能源政策的逐渐完善,LNG加气站的建设和使用逐渐增多。
特别是在一些空气质量严重受损的城市,LNG加气站已经成为替代传统燃料加气站的重要选择。
2. LNG加气站市场前景2.1 环保政策推动市场需求增长国内外环保政策的逐渐完善将成为LNG加气站市场增长的重要驱动因素。
LNG作为清洁能源,其燃烧所产生的废气和颗粒物排放较低,能够有效改善空气质量。
因此,未来随着环保政策的力度加大,LNG加气站市场需求将进一步增长。
2.2 市场潜力巨大,发展空间广阔LNG加气站市场潜力巨大,发展空间广阔。
随着LNG的推广和应用,LNG加气站将成为未来能源加气领域的重要基础设施之一。
尤其是在物流、公交、出租车等领域的应用,LNG加气站的需求将大幅增加。
考虑到全球范围内LNG加气站的建设进展较慢,未来的市场空间将更加广阔。
2.3 加气站建设成本逐渐下降随着技术的发展和经验的积累,LNG加气站的建设成本逐渐下降。
从设备设施到供应链建设,整体成本已经较之前有了较大的降低。
这将进一步刺激市场需求的增长,促使更多的经营者投资建设LNG加气站。
3. LNG加气站市场挑战3.1 基础设施建设和改造难度较高LNG加气站的基础设施建设和传统加气站相比更加复杂,需要针对LNG的特性进行改造和调整。
这将增加建设的难度和成本,尤其是在一些老旧城市和交通拥堵较为严重的地区。
3.2 竞争压力加大,市场份额有限随着LNG加气站市场的发展,竞争压力也会逐渐增大。
不仅仅是传统的燃料加气站成为竞争对手,还有新兴的充电桩等清洁能源加气设施竞争同一市场份额。
中国lng发展现状分析

中国lng发展现状分析近年来,中国的液化天然气(LNG)行业取得了快速发展,成为我国能源供应的重要组成部分。
下面将对中国LNG发展的现状进行分析。
首先,中国的LNG消费量持续增长。
由于工业和城市领域对能源需求的增加,中国对LNG的需求量不断增加。
据统计数据显示,中国LNG消费量于2019年超过了6000亿立方米,占全球LNG消费量的25%左右。
中国的LNG消费量预计将在未来几年继续增长。
其次,中国的LNG进口量大幅增加。
由于国内LNG产能有限,中国需要大量进口LNG来满足能源需求。
2019年,中国LNG进口量超过5000万吨,成为全球最大的LNG进口国。
中国与澳大利亚、卡塔尔等国家签署了长期LNG供应合同,确保了稳定的LNG进口量。
另外,中国的LNG综合利用率不断提高。
LNG作为一种清洁的能源替代品,可以在工业、城市燃气、交通等领域广泛应用。
中国不仅将LNG用于发电、取暖和烹饪等传统用途,还积极推动LNG在交通领域的应用。
目前,中国通过建设LNG加气站,鼓励使用LNG的公共交通工具和货运车辆不断增加。
此外,中国LNG产业链的发展逐渐完善。
中国从LNG进口到储存、运输、分销和终端利用的全产业链正在逐步建立。
多个LNG接收站和储罐在中国沿海城市和内陆地区建设,为LNG进口提供了基础设施支持。
同时,中国的LNG运输和分销网络不断扩大,确保了LNG的有效输送和分发。
尽管中国的LNG发展取得了重大进展,但也面临一些挑战。
首先,LNG价格的波动对中国的LNG进口业务产生了一定的影响。
其次,LNG的储存和运输成本较高,需要进行技术改进和成本降低。
此外,与传统能源相比,LNG的综合成本仍然较高,需要进一步提高LNG的竞争力。
综上所述,中国的LNG发展取得了显著进展,但仍需继续努力克服困难和挑战。
中国将继续加大LNG产业的发展力度,推动LNG的广泛应用,提高能源供应的可靠性和可持续性。
中国天然气及LNG产业的发展现状及展望
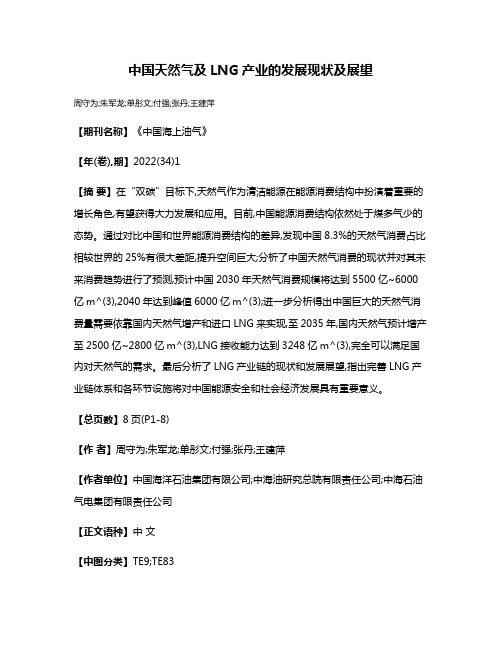
中国天然气及LNG产业的发展现状及展望周守为;朱军龙;单彤文;付强;张丹;王建萍【期刊名称】《中国海上油气》【年(卷),期】2022(34)1【摘要】在“双碳”目标下,天然气作为清洁能源在能源消费结构中扮演着重要的增长角色,有望获得大力发展和应用。
目前,中国能源消费结构依然处于煤多气少的态势。
通过对比中国和世界能源消费结构的差异,发现中国8.3%的天然气消费占比相较世界的25%有很大差距,提升空间巨大;分析了中国天然气消费的现状并对其未来消费趋势进行了预测,预计中国2030年天然气消费规模将达到5500亿~6000亿m^(3),2040年达到峰值6000亿m^(3);进一步分析得出中国巨大的天然气消费量需要依靠国内天然气增产和进口LNG来实现,至2035年,国内天然气预计增产至2500亿~2800亿m^(3),LNG接收能力达到3248亿m^(3),完全可以满足国内对天然气的需求。
最后分析了LNG产业链的现状和发展展望,指出完善LNG产业链体系和各环节设施将对中国能源安全和社会经济发展具有重要意义。
【总页数】8页(P1-8)【作者】周守为;朱军龙;单彤文;付强;张丹;王建萍【作者单位】中国海洋石油集团有限公司;中海油研究总院有限责任公司;中海石油气电集团有限责任公司【正文语种】中文【中图分类】TE9;TE83【相关文献】1.关于大力发展中国液化天然气(LNG)产业战略价值的思考2.中国天然气及LNG 产业人才培养现状与发展前景3.积极有序地发展我国液化天然气产业——"2006年中国LNG国际会议"观点集粹4.液化天然气(LNG)汽车发展现状及优势展望5.中国天然气发电产业发展现状及展望因版权原因,仅展示原文概要,查看原文内容请购买。
- 1、下载文档前请自行甄别文档内容的完整性,平台不提供额外的编辑、内容补充、找答案等附加服务。
- 2、"仅部分预览"的文档,不可在线预览部分如存在完整性等问题,可反馈申请退款(可完整预览的文档不适用该条件!)。
- 3、如文档侵犯您的权益,请联系客服反馈,我们会尽快为您处理(人工客服工作时间:9:00-18:30)。
全球LNG产业发展历史悠久,天然气液化、LNG接收气化技术发展与设施建设为国际LNG贸易和LNG大规模应用奠定了基础。
目前世界上LNG共有20个出口国家,42个进口国家,LNG贸易量同比增长8.3%,达到3.14亿t。
传统的LNG生产国如卡塔尔、澳大利亚等与新兴的俄罗斯、美国等LNG供应量增长潜力巨大,中国、日本、韩国以及欧洲部分国家是目前主要的LNG进口国。
在全球能源结构升级和环保治理等政策驱动影响下,我国天然气消费高速增长,2018年国内天然气表观消费总量达2803亿m3,其中进口LNG5378万t,占天然气供应总量的26%;2019年国内天然气表观消费量达3067亿m3,其中进口LNG6025万t,占天然气供应总量的27%。
进口LNG已经成为我国天然气供应的重要来源之一,为我国快速增长的天然气消费提供了支持和保障。
从远期国内市场供需平衡来看,国际LNG资源供应充裕,贸易灵活性提高,我国LNG进口规模仍将大幅增长。
自2006年中国海洋石油集团有限公司(以下简称“中国海油”)在深圳大鹏的第1个LNG接收站建成投产起,我国LNG产业经过10余年的快速发展,已经形成了完整的产业链。
目前,国内已建成22座LNG沿海接收站(含LNG储备库),年接收能力已超9000万t。
伴随着国内LNG产业的发展,LNG技术得到同步孕育发展和创新突破。
目前,我国已建立了从上游天然气产出、分离液化,中游运输、接收及储存,到下游的天然气利用的完整产业链核心技术体系,部分核心自主技术和核心装备制造能力已达到国际领先水平。
本文聚焦LNG产业链上、中、下游关键环节,对天然气液化技术、LNG接收站技术、LNG储运技术、LNG终端利用技术和LNG关键设备的国产化以及LNG产业标准化等发展现状进行了阐述,对其未来发展趋势进行了展望,并提出了相关技术发展建议。
1中国LNG产业链核心技术发展现状LNG产业链上游主要包括气田产出天然气、天然气的净化分离及液化等;中游包括运输船舶、终端站(储罐和再气化设施)和供气主干管网等;下游,即最终市场用户,如联合循环电站、城市燃气公司、工业和城市居民用户、工业园区和建筑物冷热电多联供的分布式能源站等。
本节以LNG产业链关键环节为例,介绍国内LNG核心技术发展现状。
1.1天然气液化与FLNG技术1.1.1天然气液化技术我国天然气液化技术发展相对较晚,早期的技术研发主要集中在上海交通大学、哈尔滨工业大学、中国科学院等高校或研究院,后续深冷行业单位和石油企业陆续引进液化技术,建造天然气液化装置,并逐渐开始探索大中型天然气液化技术及装备的研发。
2001年11月建成投产的我国首套工业化的天然气液化装置,液化能力为15万m3/d,采用阶式制冷工艺。
近年来,为满足天然气市场的调峰和管网未接入地区发展清洁能源的需要,我国小型LNG装置进入快速发展时期。
截至目前,已经建成230多座天然气液化工厂,广泛分布于内蒙、新疆、陕西、四川等地。
目前我国建设的天然气液化装置全部为中小型,2013年建成的山东泰安260万m3/d和湖北黄冈500万m3/d的天然气液化装置,是国内单列规模最大的2套天然气液化装置。
为推进国外天然气资源的获取和大型液化工厂的自主建设,自2008年起,中国海油和中国石油天然气集团有限公司(以下简称“中石油”)先后组织国内相关单位开展天然气液化技术研究及设备研发。
其中,中国海油旗下的中海石油气电集团有限责任公司(以下简称“中海油气电集团”)牵头开发了2套260万t/a的大型天然气液化工艺包以及配套设备,并进一步开发了多套混合制冷剂液化工艺的液化装置,单线液化能力可覆盖1万t/a的微型液化装置直至500万t/a的超大型液化工厂,达到了国际先进水平(国外大型LNG工程主要采用级联式液化流程及混合制冷剂液化流程,最大规模可达800万t/a以上)。
在天然气预处理方面,针对不同杂质组分的天然气源,开展了三元胺液配比模拟和实验研究,掌握了自主胺液配方的工艺核心技术。
在冷剂方面,建立了混合冷剂配比模型和模拟计算方法,经与实际工程项目现场监测对比,冷剂工艺性能与实际运行情况基本完全吻合。
1.1.2FLNG技术FLNG技术是将天然气处理、液化和产品储存全部集成到船上,要求布置更紧凑,安全性要求更高。
FLNG概念由壳牌公司在1969年首次提出,于1978年第一次被提出用作工程方案。
目前,全球已有4艘FLNG投入使用,其中澳大利亚Prulude项目的360万t/a的FLNG在2019年正式投产。
为配合国家战略发展和我国南海油气资源开发,中国海油积极推进FLNG的技术研发工作,先后完成了FLNG相关的10余项国家科技重大专项、“863”计划和工信部研发课题的研究工作,解决了仓储与上部模块设计建造、液化工艺、核心装备及液舱晃动影响等技术难题,基本掌握了FLNG核心技术,为工程化应用奠定了基础。
中国海油在FLNG核心技术方面的理论和试验研究包括:建设了一套2万m3/d规模的氮膨胀液化工艺中试装置,并依托营口液化实验基地开展现场试验研究;建设了3套摇摆晃动试验台,分别开展微型双混合冷剂液化工艺实验装置的晃动工况模拟与实验研究,晃动工况下LNG绕管式换热器两相流均布及换热性能技术研究和预处理用塔器内部两相流传热传质的模拟和实验研究;提出了晃动工况下的两相流动和化学反应理论模型,并指导了实验工作,解决了晃动工况下两相流设备不均匀流动问题,突破了浮式生产装置两相流设备的流动换热控制关键技术。
1.2LNG接收站技术20世纪90年代,我国开始规划从海上引进LNG。
自2006年广东大鹏LNG接收站投产以来,福建莆田、上海、江苏如东等接收站相继投产,截至目前我国已建成22座LNG接收站。
我国的LNG接收站为满足下游天然气市场日峰、季峰的需要,在设计上需要满足频繁启停外输的稳定性和灵活性的要求,设计及操作是世界同类型接收站中最为复杂的。
中海油气电集团作为中国LNG产业的领军者,目前已经在LNG接收站自主设计、技术创新、整体优化等方面建立了完整的自主技术体系。
在主工艺设计、蒸发气(BOG)计算处理、储罐罐容计算、能耗分析、船舶分析等核心技术方面具有较强先进性和特色,自主研发的接收站四维演化分析技术动态模拟仿真系统包含了接收站三维动态仿真平台、新型试车技术、储罐新型施工技术以及站线联合优化技术,大力激活和提高了接收终端的运营优化空间。
该技术以LNG设施低温特性为切入点,首次对大型LNG接收站进行全厂系统性三维建模,并在此基础上加载物性参数变化因子,在国际上首创了以低温两相流体随物性参数时序变化为特征的四维演化分析技术。
通过该技术,中国海油在LNG低温特性应用领域拥有了低温气液两相流精确仿真、低温动态应力耦合分析、事故动态演化分析、全厂能量动态优化等一系列具有里程碑意义的突破性核心技术成果。
中石油、中国石油化工集团有限公司(以下简称“中石化”)及其他民营企业也同步在LNG领域开展了大量的技术创新研究和工程项目建设工作。
以中石油的深基坑储罐技术、中石化的C2、C3等高碳烃类分离处理技术等为代表,为接收站工程技术提升发展发挥了重要作用。
随着LNG产业的不断发展,除了常规的LNG接收终端外,还涌现出了许多不同形式的LNG接收及再气化基础设施,浮式LNG再气化装置(FSRU)即为其中之一。
FSRU相比传统的同等规模陆上再气化设施,开发时间短,建设成本相对较低,使用起来也更为灵活。
2013年,中海油气电集团成功攻克卸料、系泊、气化等多项关键核心技术,正式建成投产了国内首个FSRU项目———天津FSRU项目,并于2014年实现与陆地设施联合调试外输,成为国际上首例海陆一体化工程项目。
此外,中海油气电集团还在国内首次提出了海上模块化接收终端(CNO-OCGASBLOCK)概念,能够根据需要,实现LNG再气化、LNG海上存储、LNG海上转运、LNG海上加注等功能,具有建设周期短、运营灵活、便于推广、可定制化等显著优点,其理念在世界LNG领域处于领先地位。
1.3LNG储运技术1.3.1LNG储罐技术近年来,国内清洁能源需求快速增长,考虑到应急调峰需求以及国家对天然气储备基础设施的建设要求和国家天然气产供储销体系的建设规划,LNG储罐朝大型化发展(22~27万m3)将是未来国内LNG储存技术的主要发展趋势。
在大型LNG全容储罐技术上,中国海油自主研发了储罐三维全模型、多点接触有限元计算模型、地震谱设计及应用方法、内罐地震响应谱法计算校核方法、外罐M-N曲线配筋设计技术等核心算法;根据LNG储罐桩基础的设计特点,引入欧洲地震设计理论,并结合国内桩基设计规范及工程经验,开发出了一种更精确、更经济、更安全的全新桩基础设计算法;建立了浮顶力学计算方法,引入低温收缩对力学控制方程影响因素,包括载荷确定、力学控制方程、迭代求解等3部分,可以提高储罐浮顶设计的可靠性。
目前我国上海LNG和江苏如东LNG等均开展了20万m3大型LNG储罐的自主化建造,成功打开了超大型LNG储罐技术自主研发的大门。
中国海油在国内首次建立了超大容积(20~27万m3)储罐技术基础理论体系、储罐有限元数值分析体系、储罐模拟设计体系、试验模拟体系和现场监测体系等五大体系,成功掌握了相关核心技术。
目前22万m3储罐技术正在江苏LNG项目上进行工程化应用。
此外,国内在储罐设计建造方面也将逐步拓展超大容积储罐减隔震、软地基下碎石桩处理、高地震带下结构综合处理方案和新型预应力系统设计等技术,必将进一步提高大型液化天然气储罐技术的经济性及安全可靠度。
1.3.2天然气管输技术随着天然气产量和贸易量的增长以及消费市场的扩大,全球输气管道的建设向长运距、大管径和高压力方向发展,形成了具有多气源、多通道、供气灵活可靠等特点的洲际的、多国的、全国性的和许多地区性的大型管网系统。
伴随着天然气管道建设的高速发展,国内外天然气管道在计量技术、泄漏检测、管道减阻剂和运行仿真及基于地理信息系统(GIS)的管道数字化等方面取得了一些新进展。
中海油气电集团结合自身业务需求,在天然气管输工艺方面形成了管网瞬态调峰、混输调质与组分跟踪、管网分时调度、场站动态仿真、第三方开放能力分配、管网能量计量间接赋值等具有差异化特色的自主技术成果。
目前正在攻关解决LNG长距离管道输运面临的难题。
1.3.3LNG罐箱多式联运技术非管输天然气运输因机动灵活、占地少,是管输天然气供应模式的有力补充。
伴随着LNG贸易市场的逐渐壮大,以物联网为基础的一系列创新物流模式迎来发展机遇。
LNG罐箱因具备无损存储时间长、“宜储宜运”的优势,是大型天然气液态储运方式的有力补充,可实现沿海接收站与用户的“门到门”服务,解决管线不能到达地区的供气难题。