机械加工中的强迫振动现象分析
机械加工过程中机械振动的原因及对策分析
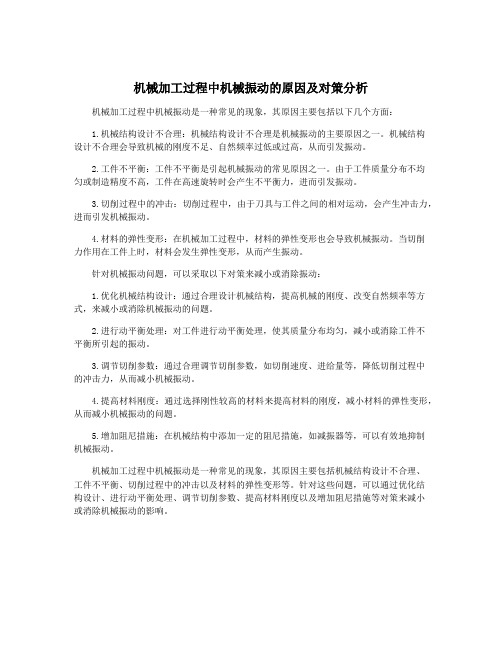
机械加工过程中机械振动的原因及对策分析机械加工过程中机械振动是一种常见的现象,其原因主要包括以下几个方面:1.机械结构设计不合理:机械结构设计不合理是机械振动的主要原因之一。
机械结构设计不合理会导致机械的刚度不足、自然频率过低或过高,从而引发振动。
2.工件不平衡:工件不平衡是引起机械振动的常见原因之一。
由于工件质量分布不均匀或制造精度不高,工件在高速旋转时会产生不平衡力,进而引发振动。
3.切削过程中的冲击:切削过程中,由于刀具与工件之间的相对运动,会产生冲击力,进而引发机械振动。
4.材料的弹性变形:在机械加工过程中,材料的弹性变形也会导致机械振动。
当切削力作用在工件上时,材料会发生弹性变形,从而产生振动。
针对机械振动问题,可以采取以下对策来减小或消除振动:1.优化机械结构设计:通过合理设计机械结构,提高机械的刚度、改变自然频率等方式,来减小或消除机械振动的问题。
2.进行动平衡处理:对工件进行动平衡处理,使其质量分布均匀,减小或消除工件不平衡所引起的振动。
3.调节切削参数:通过合理调节切削参数,如切削速度、进给量等,降低切削过程中的冲击力,从而减小机械振动。
4.提高材料刚度:通过选择刚性较高的材料来提高材料的刚度,减小材料的弹性变形,从而减小机械振动的问题。
5.增加阻尼措施:在机械结构中添加一定的阻尼措施,如减振器等,可以有效地抑制机械振动。
机械加工过程中机械振动是一种常见的现象,其原因主要包括机械结构设计不合理、工件不平衡、切削过程中的冲击以及材料的弹性变形等。
针对这些问题,可以通过优化结构设计、进行动平衡处理、调节切削参数、提高材料刚度以及增加阻尼措施等对策来减小或消除机械振动的影响。
机械加工过程中的振动

机械加工过程中的振动
1) 刀具相对于工件振动会使加工表面产生波纹,这将严峻影响零件的使用性能;
2) 刀具相对于工件振动,切削截面、切削角度等将随之发生周期性变化,工艺系统将承受动态载荷的作用,刀具易于磨损(有时甚至崩刃),机床的连接特性会受到破坏,严峻时甚至使切削加工无法进行;3)为了避开发生振动或减小振动,有时不得不降低切削用量,致使机床、刀具的工作性能得不到充分发挥,限制了生产效率的提高。
一、机械加工过程中的强迫振动
机械加工过程中的强迫振动是指在外界周期性干扰力的持续作用下,振动系统受迫产生的振动。
机械加工过程中强迫振动的振动频率与干扰力的频率相同或是它的整数倍;当干扰力的频率接近或等于工艺系统某一薄弱环节固有频率时,系统将产生共振。
二、机械加工过程中的自激振动(颤振)
1.机械加工过程中的自激振动
机械加工中的自激振动是指在没有周期性外力(相对于切削过程而言)干扰下产生的振动运动。
2.自激振动的激振原理
(1)再生原理
(2)振型耦合原理
三、掌握机械加工振动的途径
1.消退或减弱产生振动的条件(1)消退或减弱产生强迫振动的条件(2)消退或减弱产生自激振动的条件2.改善工艺系统的动态特性
3.采纳减振装置。
机械加工中的振动现象及其影响

κr
κ 磨削
图4-77 重叠系数
减小重叠系数方法
增加主偏角 增大进给量 ◆ 增加切削阻尼(例采用倒棱车刀,图4-78)
-5°~ -20° ° °
0.1~0.3 ~
2°~ 3° ° ° 图4-78 车刀消振棱
改善工艺系统动态特性
◆ 提高工艺系统刚度 ◆ 增大工艺系统阻尼
在没有周期性外力作用 下 , 由系统内部激发反馈 产生的周期性振动 自激振动过程可用传递 函数概念说明( 函数概念说明(图4-72) 72)
电动机 (能源) 振动位移 X(t) 机床振动系统 (弹性环节)
调节系统 交变切削力F(t) (切削过程)
图4-72 自激振动闭环系统
能量E E-
自激振动的特征
强迫振动的特征
频率特征:与干扰力的频率相同,或是干扰力频率整倍数 幅值特征:与干扰力幅值、工艺系统动态特性有关。当干 扰力频率接近或等于工艺系统某一固有频率时,产生共振 相角特征:强迫振动位移的变化在相位上滞后干扰力一个 φ角,其值与系统的动态特性及干扰力频率有关。
(三)机械加工过程中自激振动
自激振动的概念
φ y0 y 切入 切出 a) φ y0 y 切入 切出 c) f 切入 切出 d) f φ y0 y f 切入 切出 b) y0 y f
图4-74 再生自激振动原理图
◆ 产生条件(图4-74) : a)b)c)系统无能量获得; 产生条件( 74) d)y 滞后于y0,即 0>φ>-π ,此时切出比切入半周期中的 平均切削厚度大,切出时切削力所作正功(获得能量)大于 切入时所作负功,系统有能量获得,产生自激振动
机械加工过程中的振动及其影响
一、概 述 机械加工过程中振动的危害
机械加工中机械振动的原因解析与应对

机械加工中机械振动的原因解析与应对
机械加工中的机械振动指的是机器在运行过程中的震动和共振现象。
机械振动不仅会影响产品的加工精度和质量,还会对机器本身造成损伤,因此必须引起足够的重视。
以下是机械振动的原因解析与应对措施。
一、机械振动的原因
1.不平衡:机械零件中存在不平衡现象时,发动机转动时会由于离心力产生横向或纵向的振动。
2.共振:当机器设备的固有频率与强制振动频率接近或相等时,就会出现共振现象,引起机器的强烈振动。
3.摩擦和磨损:机械零件的摩擦和磨损会导致运动不平稳,引起机器的振动。
4.不稳定结构:机器结构不够稳定,机械零件的振动会自我放大。
5.加工精度:由于零件加工误差、装配不良等原因,会导致机械零件在运行时振动加剧。
二、机械振动的应对措施
1.动平衡处理:对于不平衡现象严重的零件,应采取动平衡处理,通过在转子上安装调节重量来消除不平衡,降低振动的影响。
2.增加阻尼:在机械设备中增加阻尼器,可以有效地减小机械振动的幅度和频率。
3.改变固有频率:对于因共振引起的振动,可以通过改变机器的结构和材料,改变固有频率,避免共振的出现。
4.加强润滑:保持机器设备的良好润滑状态,减少磨损和摩擦,可以降低机械振动的程度。
5.改善加工质量:严格控制零件加工误差,加强装配质量,提高机器的运行精度,从而减轻机械振动的影响。
综上所述,机械振动是机械加工中必须面对的一个问题。
只有全方位的应对措施,才能保证机器的正常运行,同时也能保证产品加工的质量和精度。
机械加工过程中机械振动的原因及对策分析
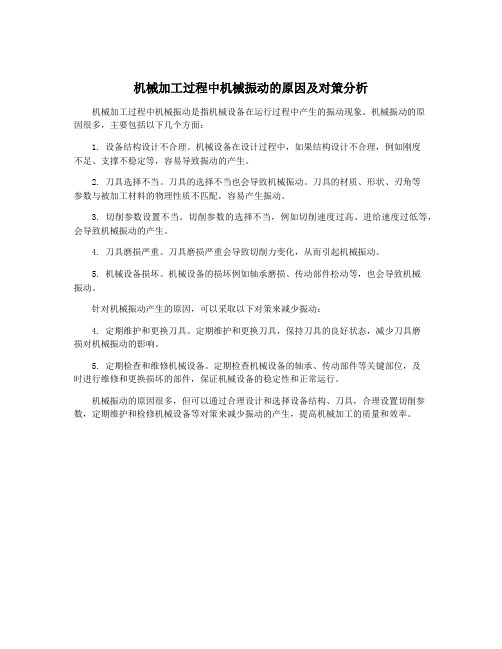
机械加工过程中机械振动的原因及对策分析
机械加工过程中机械振动是指机械设备在运行过程中产生的振动现象。
机械振动的原
因很多,主要包括以下几个方面:
1. 设备结构设计不合理。
机械设备在设计过程中,如果结构设计不合理,例如刚度
不足、支撑不稳定等,容易导致振动的产生。
2. 刀具选择不当。
刀具的选择不当也会导致机械振动。
刀具的材质、形状、刃角等
参数与被加工材料的物理性质不匹配,容易产生振动。
3. 切削参数设置不当。
切削参数的选择不当,例如切削速度过高、进给速度过低等,会导致机械振动的产生。
4. 刀具磨损严重。
刀具磨损严重会导致切削力变化,从而引起机械振动。
5. 机械设备损坏。
机械设备的损坏例如轴承磨损、传动部件松动等,也会导致机械
振动。
针对机械振动产生的原因,可以采取以下对策来减少振动:
4. 定期维护和更换刀具。
定期维护和更换刀具,保持刀具的良好状态,减少刀具磨
损对机械振动的影响。
5. 定期检查和维修机械设备。
定期检查机械设备的轴承、传动部件等关键部位,及
时进行维修和更换损坏的部件,保证机械设备的稳定性和正常运行。
机械振动的原因很多,但可以通过合理设计和选择设备结构、刀具,合理设置切削参数,定期维护和检修机械设备等对策来减少振动的产生,提高机械加工的质量和效率。
机械加工过程中机械振动的原因及对策分析
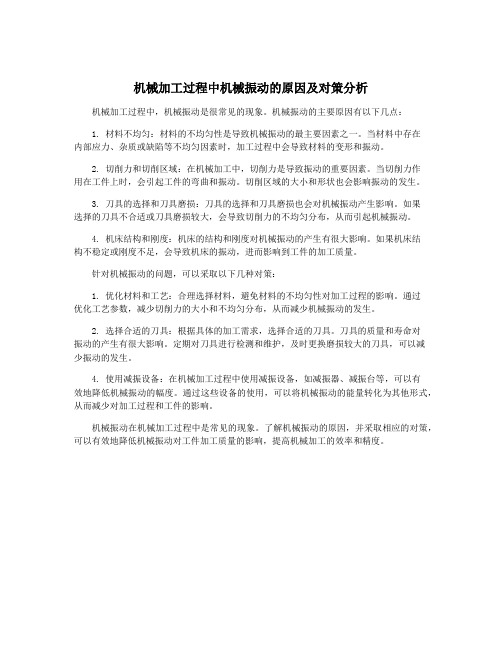
机械加工过程中机械振动的原因及对策分析机械加工过程中,机械振动是很常见的现象。
机械振动的主要原因有以下几点:1. 材料不均匀:材料的不均匀性是导致机械振动的最主要因素之一。
当材料中存在内部应力、杂质或缺陷等不均匀因素时,加工过程中会导致材料的变形和振动。
2. 切削力和切削区域:在机械加工中,切削力是导致振动的重要因素。
当切削力作用在工件上时,会引起工件的弯曲和振动。
切削区域的大小和形状也会影响振动的发生。
3. 刀具的选择和刀具磨损:刀具的选择和刀具磨损也会对机械振动产生影响。
如果选择的刀具不合适或刀具磨损较大,会导致切削力的不均匀分布,从而引起机械振动。
4. 机床结构和刚度:机床的结构和刚度对机械振动的产生有很大影响。
如果机床结构不稳定或刚度不足,会导致机床的振动,进而影响到工件的加工质量。
针对机械振动的问题,可以采取以下几种对策:1. 优化材料和工艺:合理选择材料,避免材料的不均匀性对加工过程的影响。
通过优化工艺参数,减少切削力的大小和不均匀分布,从而减少机械振动的发生。
2. 选择合适的刀具:根据具体的加工需求,选择合适的刀具。
刀具的质量和寿命对振动的产生有很大影响。
定期对刀具进行检测和维护,及时更换磨损较大的刀具,可以减少振动的发生。
4. 使用减振设备:在机械加工过程中使用减振设备,如减振器、减振台等,可以有效地降低机械振动的幅度。
通过这些设备的使用,可以将机械振动的能量转化为其他形式,从而减少对加工过程和工件的影响。
机械振动在机械加工过程中是常见的现象。
了解机械振动的原因,并采取相应的对策,可以有效地降低机械振动对工件加工质量的影响,提高机械加工的效率和精度。
浅析机械加工过程中机械振动的成因及处理方法

浅析机械加工过程中机械振动的成因及处理方法一、机械振动的分类机械加工过程中,工艺系统常常会发生振动,即在工件和刀具的切削刃之间,除了名义上的切削运动外,还会出现一种周期性的相对运动。
产生振动时,工艺系统的正常切削过程便受到干扰和破坏,从而使零件加工表面出现振纹,降低了零件的加工精度和表面质量,频率低时产生波度,频率高时产生微观不平度。
强烈的振动会使切削过程无法进行,甚至造成刀具“崩刃”。
为此,常被迫降低切削用量,致使机床、刀具的工作性能得不到充分的发挥,限制了生产率的提高。
振动还影响刀具的耐用度和机床的寿命,发出噪声,恶化工作环境,影响工人健康。
振动按其产生的原因来分类有三种:自由振动、受迫振动和自激振动。
受迫振动和自激振动都是不能自然衰减而且危害较大的振动。
下面就这两种振动形式进行简单的分析。
二、机械加工中的受迫振动(一)受迫振动产生的原因机械加工中的受迫振功,是一种由工艺系统内部或外部周期交变的激振力(即振源)作用下引起的振动。
机械加工中引起工艺系统受迫振动的激振力,主要来自以下几方面1.机床上高速回转零件的不平衡机床上高速回转的零件较多,如电动机转子、带轮、主轴、卡盘和工件、磨床的砂轮等,由于不平衡而产生激振力F(即离心惯性力)。
2.机床传动系统中的误差机床传动系统中的齿轮,由于制造和装配误差而产生周期性的激振力。
此外,皮带接缝、轴承滚动体尺寸差和液压传动中油液脉动等各种因素均可能引起工艺系统受迫振动。
3.切削过程本身的不均匀性切削过程的间歇特性,如铣削、拉削及车削带有键槽的断续表面等,由于间歇切削而引起切削力的周期性变化,从而激起振动。
4.外部振源由邻近设备(如冲压设备、龙门刨等)工作时的强烈振动通过地基传来,使工艺系统产生相同(或整倍数)频率的受迫振动。
(二)减少受迫振动的途径受迫振动是由于外界周期性干扰力引起的,因此为了消除受迫振动,应先找出振源,然后采取适应的措施加以控制。
1.减小或消除振源的激振力对转速在600r/min以上的零件必须经过平衡,特别是高速旋转的零件,如砂轮,因其本身砂粒的分布不均匀和工作时表面磨损不均匀等原因,容易造成主轴的振动,因此对于新换的砂轮必须进行修整前和修整后的两次平衡。
机械加工过程中机械振动的原因及对策分析
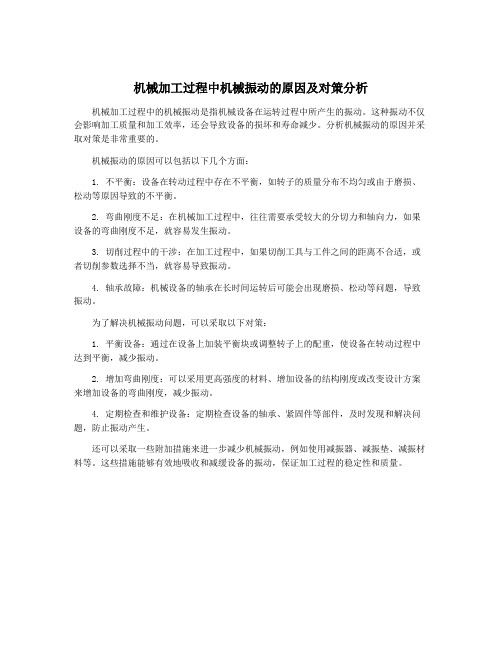
机械加工过程中机械振动的原因及对策分析
机械加工过程中的机械振动是指机械设备在运转过程中所产生的振动。
这种振动不仅会影响加工质量和加工效率,还会导致设备的损坏和寿命减少。
分析机械振动的原因并采取对策是非常重要的。
机械振动的原因可以包括以下几个方面:
1. 不平衡:设备在转动过程中存在不平衡,如转子的质量分布不均匀或由于磨损、松动等原因导致的不平衡。
2. 弯曲刚度不足:在机械加工过程中,往往需要承受较大的分切力和轴向力,如果设备的弯曲刚度不足,就容易发生振动。
3. 切削过程中的干涉:在加工过程中,如果切削工具与工件之间的距离不合适,或者切削参数选择不当,就容易导致振动。
4. 轴承故障:机械设备的轴承在长时间运转后可能会出现磨损、松动等问题,导致振动。
为了解决机械振动问题,可以采取以下对策:
1. 平衡设备:通过在设备上加装平衡块或调整转子上的配重,使设备在转动过程中达到平衡,减少振动。
2. 增加弯曲刚度:可以采用更高强度的材料、增加设备的结构刚度或改变设计方案来增加设备的弯曲刚度,减少振动。
4. 定期检查和维护设备:定期检查设备的轴承、紧固件等部件,及时发现和解决问题,防止振动产生。
还可以采取一些附加措施来进一步减少机械振动,例如使用减振器、减振垫、减振材料等。
这些措施能够有效地吸收和减缓设备的振动,保证加工过程的稳定性和质量。
强迫振动现象分析

谢谢观赏
下面主要对强迫振动进行简单的分析 。
强迫振动产生的原因
Байду номын сангаас
强迫 振动
减小强迫振动的措施和 途径
1 .1 机床上高速回转的零件的不平衡 1 .2 机床传动系统中的误差
1 . 3 切削过程中本身的不均匀性 1 . 4 外部振源
1 .1 机床上高速回转的零件的不平衡
机床上高速回转零件较多 , 如电动机转子、带 轮 、主轴 、卡盘和工件 、磨床的砂轮等 ,由于不平衡 而产生激振力 F(即离心惯性力) 。如图 1 所示是一个 安装在简支梁上的 电动机 ,以 ω 的角速度旋转时 ,假 如由于电动机转子不平衡而产生离心力Fn ,则Fn沿X方向 的分力Fx ( Fx = Fncosωt) 就是该梁的外界周期干扰 力。 在这一干扰力的作用下 ,简支梁将作不衰减的振 动 。
机械加工中的强迫振动现象分析
蒋留杰
机械加工过程中 ,在工件和刀具之间常产 生振动 。 产生振动时 ,工艺系 统的正常 切削 过程便受到干扰和破坏 ,从而零件 加工表面出现振纹 ,降低了 零件的加工 精度和表面质量 。机械加工过程中 产生 的振动 ,按其产生的原因来分 ,可分为自 由 振动 、强迫振动 和 自 激振动 三大 类 。 自由振动往往是由于切削力的突然 变化或其他外力的冲击等原因所引 起的 。 这种振动一般可以迅速衰减 ,因此对机械 加工过程中 的影响较小 。 而强迫振动 和自激振动都是不能自 然衰减而且危害 较大的振动 。
1 .2 机床传动系统中的误差
机床传动系统中的齿轮 ,由于制造和装配误 差而产生周期性的激振力 。此外 ,皮带接 缝 ,轴承滚动体尺寸差和液压传动中油液脉 动等各种因素均可能引起工艺系统强迫振 动 。
强迫振动及其控制措施
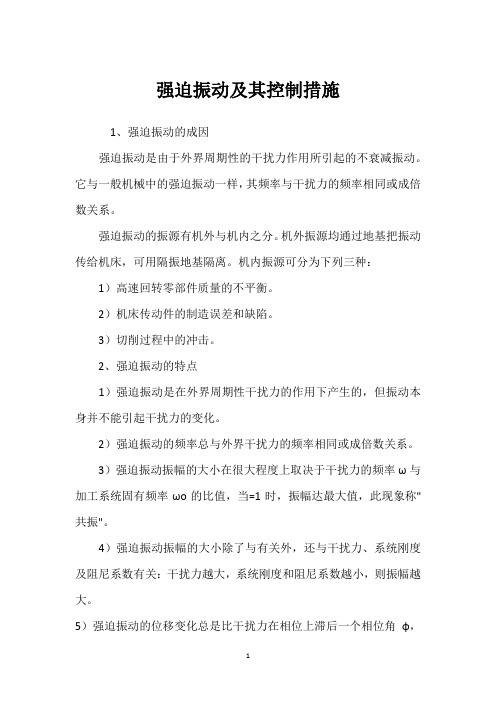
强迫振动及其控制措施
1、强迫振动的成因
强迫振动是由于外界周期性的干扰力作用所引起的不衰减振动。
它与一般机械中的强迫振动一样,其频率与干扰力的频率相同或成倍数关系。
强迫振动的振源有机外与机内之分。
机外振源均通过地基把振动传给机床,可用隔振地基隔离。
机内振源可分为下列三种:1)高速回转零部件质量的不平衡。
2)机床传动件的制造误差和缺陷。
3)切削过程中的冲击。
2、强迫振动的特点
1)强迫振动是在外界周期性干扰力的作用下产生的,但振动本身并不能引起干扰力的变化。
2)强迫振动的频率总与外界干扰力的频率相同或成倍数关系。
3)强迫振动振幅的大小在很大程度上取决于干扰力的频率ω与加工系统固有频率ωo的比值,当=1时,振幅达最大值,此现象称"共振"。
4)强迫振动振幅的大小除了与有关外,还与干扰力、系统刚度及阻尼系数有关:干扰力越大,系统刚度和阻尼系数越小,则振幅越大。
5)强迫振动的位移变化总是比干扰力在相位上滞后一个相位角φ,
其值与系统的动态特性及干扰力频率有关。
3、强迫振动的消退与掌握措施
1)消振、隔振与减振消退强迫振动的最有效方法就是找出振源并消退之,如不能消退,则可用隔离振动的方法。
如:用隔振地基以隔绝邻近机床振动的影响,精密机床和精密仪器常用空气垫来隔振也是个好方法。
还可用动力式减振器。
2)消退回转件质量的不平衡。
3)提高传动零件的制造精度。
4)提高加工系统的刚度,增加系统阻尼。
5)转变机床转速、使用不等齿距刀具。
机械加工过程中机械振动的原因及对策分析

机械加工过程中机械振动的原因及对策分析
机械加工过程中的机械振动是指在机床或工件上产生的机械振动现象。
机械振动的原
因可以分为以下几个方面:
1. 刀具与工件的不平衡:刀具与工件的不平衡是引起机械振动的主要原因之一。
刀
具在高速旋转时不平衡会导致振动产生。
3. 刀具与刀架的松动:刀具安装不牢固、刀具松动也会引起机械振动。
刀具松动会
导致刀具与工件之间的相对运动不稳定,从而引起振动。
4. 机床刚度不足:机床刚度不足是引起机械振动的另一常见原因。
机床刚度不足会
导致加工过程中机床产生弯曲变形,使刀具与工件之间的相对位置发生变化,引起振动。
对于机械振动问题,以下是一些常见的对策分析:
1. 动平衡:对刀具、刀架等旋转部件进行动平衡处理,将不平衡量降至最低,减小
机械振动。
2. 调整刀具参数:根据实际情况调整刀具的切削参数,使刀具与工件之间的力平衡,减小机械振动。
3. 固定刀具、刀架:确保刀具、刀架等部件的安装牢固,防止松动引起的振动。
4. 提高机床刚度:通过增加机床的刚度来减小机械振动。
可以通过选用更加稳定的
机床、加强机床的结构设计等方式来提高机床刚度。
5. 使用减振装置:在机床或工件上安装减振装置,减小机械振动。
在机械加工过程中,机械振动是一个常见的问题,会影响加工质量和工作效率。
针对
机械振动问题,可以采取不同的对策,从而减小振动幅度,提高加工精度和稳定性。
机械加工中的振动分析及控制措施
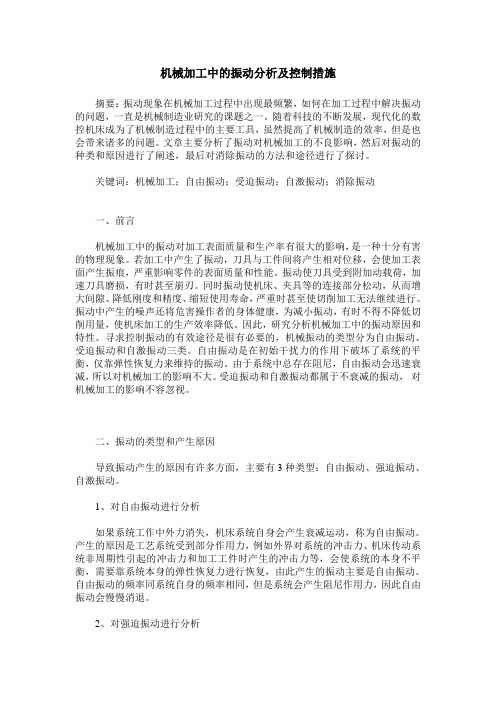
机械加工中的振动分析及控制措施摘要:振动现象在机械加工过程中出现最频繁,如何在加工过程中解决振动的问题,一直是机械制造业研究的课题之一。
随着科技的不断发展,现代化的数控机床成为了机械制造过程中的主要工具,虽然提高了机械制造的效率,但是也会带来诸多的问题。
文章主要分析了振动对机械加工的不良影响,然后对振动的种类和原因进行了阐述,最后对消除振动的方法和途径进行了探讨。
关键词:机械加工;自由振动;受迫振动;自激振动;消除振动一、前言机械加工中的振动对加工表面质量和生产率有很大的影响,是一种十分有害的物理现象。
若加工中产生了振动,刀具与工件间将产生相对位移,会使加工表面产生振痕,严重影响零件的表面质量和性能。
振动使刀具受到附加动载荷,加速刀具磨损,有时甚至崩刃。
同时振动使机床、夹具等的连接部分松动,从而增大间隙、降低刚度和精度、缩短使用寿命,严重时甚至使切削加工无法继续进行。
振动中产生的噪声还将危害操作者的身体健康,为减小振动,有时不得不降低切削用量,使机床加工的生产效率降低。
因此,研究分析机械加工中的振动原因和特性。
寻求控制振动的有效途径是很有必要的,机械振动的类型分为自由振动、受迫振动和自激振动三类。
自由振动是在初始干扰力的作用下破坏了系统的平衡,仅靠弹性恢复力来维持的振动。
由于系统中总存在阻尼,自由振动会迅速衰减,所以对机械加工的影响不大。
受迫振动和自激振动都属于不衰减的振动,对机械加工的影响不容忽视。
二、振动的类型和产生原因导致振动产生的原因有许多方面,主要有3种类型:自由振动、强迫振动、自激振动。
1、对自由振动进行分析如果系统工作中外力消失,机床系统自身会产生衰减运动,称为自由振动。
产生的原因是工艺系统受到部分作用力,例如外界对系统的冲击力、机床传动系统非周期性引起的冲击力和加工工件时产生的冲击力等,会使系统的本身不平衡,需要靠系统本身的弹性恢复力进行恢复,由此产生的振动主要是自由振动。
自由振动的频率同系统自身的频率相同,但是系统会产生阻尼作用力,因此自由振动会慢慢消退。
机械加工中机械振动的原因解析与应对
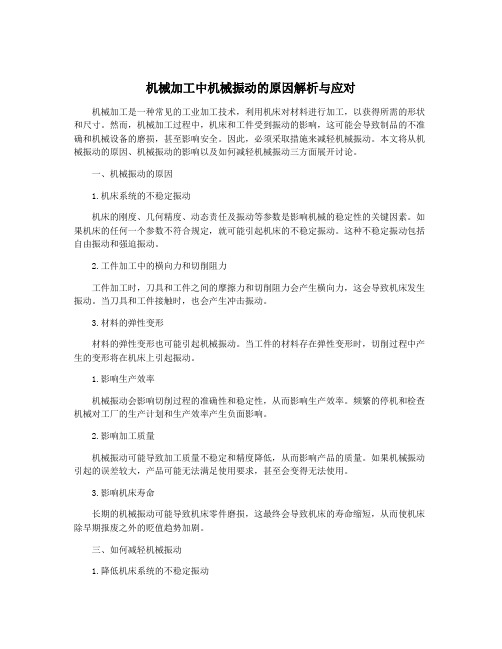
机械加工中机械振动的原因解析与应对机械加工是一种常见的工业加工技术,利用机床对材料进行加工,以获得所需的形状和尺寸。
然而,机械加工过程中,机床和工件受到振动的影响,这可能会导致制品的不准确和机械设备的磨损,甚至影响安全。
因此,必须采取措施来减轻机械振动。
本文将从机械振动的原因、机械振动的影响以及如何减轻机械振动三方面展开讨论。
一、机械振动的原因1.机床系统的不稳定振动机床的刚度、几何精度、动态责任及振动等参数是影响机械的稳定性的关键因素。
如果机床的任何一个参数不符合规定,就可能引起机床的不稳定振动。
这种不稳定振动包括自由振动和强迫振动。
2.工件加工中的横向力和切削阻力工件加工时,刀具和工件之间的摩擦力和切削阻力会产生横向力,这会导致机床发生振动。
当刀具和工件接触时,也会产生冲击振动。
3.材料的弹性变形材料的弹性变形也可能引起机械振动。
当工件的材料存在弹性变形时,切削过程中产生的变形将在机床上引起振动。
1.影响生产效率机械振动会影响切削过程的准确性和稳定性,从而影响生产效率。
频繁的停机和检查机械对工厂的生产计划和生产效率产生负面影响。
2.影响加工质量机械振动可能导致加工质量不稳定和精度降低,从而影响产品的质量。
如果机械振动引起的误差较大,产品可能无法满足使用要求,甚至会变得无法使用。
3.影响机床寿命长期的机械振动可能导致机床零件磨损,这最终会导致机床的寿命缩短,从而使机床除早期报废之外的贬值趋势加剧。
三、如何减轻机械振动1.降低机床系统的不稳定振动为了降低机床的不稳定振动,可以采取以下措施:优化机床的结构和几何精度,加强机床刚度,减少或消除机床的机械间隙,改造机床动态助力系统等。
2.减少横向力和切削阻力可以通过控制工件加工过程中的摩擦力和切削阻力来减少机械振动。
采用合适的刀具和润滑油的选择,对工件进行适当的冷却可以减少摩擦力和切削阻力。
3.提高机床刚度机床刚度是影响机床稳定性的重要因素。
为了提高机床的刚度,可以调整机床的结构设计,选用高质量的材料,以及保障机床及其零部件的充分刚性等。
机械加工中机械振动的原因解析与应对
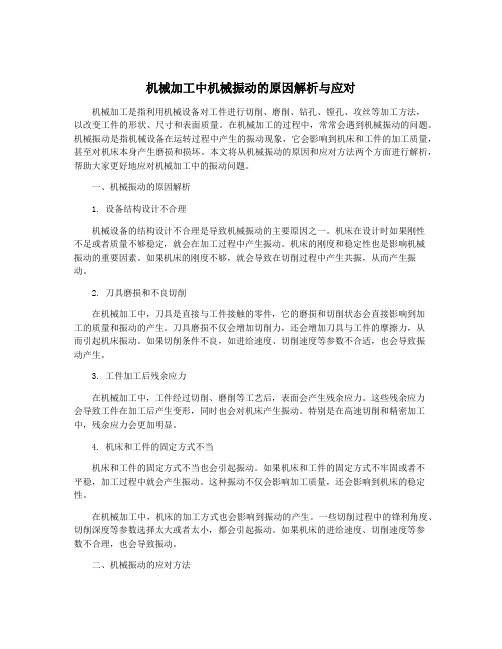
机械加工中机械振动的原因解析与应对机械加工是指利用机械设备对工件进行切削、磨削、钻孔、镗孔、攻丝等加工方法,以改变工件的形状、尺寸和表面质量。
在机械加工的过程中,常常会遇到机械振动的问题。
机械振动是指机械设备在运转过程中产生的振动现象,它会影响到机床和工件的加工质量,甚至对机床本身产生磨损和损坏。
本文将从机械振动的原因和应对方法两个方面进行解析,帮助大家更好地应对机械加工中的振动问题。
一、机械振动的原因解析1. 设备结构设计不合理机械设备的结构设计不合理是导致机械振动的主要原因之一。
机床在设计时如果刚性不足或者质量不够稳定,就会在加工过程中产生振动。
机床的刚度和稳定性也是影响机械振动的重要因素。
如果机床的刚度不够,就会导致在切削过程中产生共振,从而产生振动。
2. 刀具磨损和不良切削在机械加工中,刀具是直接与工件接触的零件,它的磨损和切削状态会直接影响到加工的质量和振动的产生。
刀具磨损不仅会增加切削力,还会增加刀具与工件的摩擦力,从而引起机床振动。
如果切削条件不良,如进给速度、切削速度等参数不合适,也会导致振动产生。
3. 工件加工后残余应力在机械加工中,工件经过切削、磨削等工艺后,表面会产生残余应力。
这些残余应力会导致工件在加工后产生变形,同时也会对机床产生振动。
特别是在高速切削和精密加工中,残余应力会更加明显。
4. 机床和工件的固定方式不当机床和工件的固定方式不当也会引起振动。
如果机床和工件的固定方式不牢固或者不平稳,加工过程中就会产生振动。
这种振动不仅会影响加工质量,还会影响到机床的稳定性。
在机械加工中,机床的加工方式也会影响到振动的产生。
一些切削过程中的锋利角度、切削深度等参数选择太大或者太小,都会引起振动。
如果机床的进给速度、切削速度等参数不合理,也会导致振动。
二、机械振动的应对方法为了降低机械振动,首先要从设备结构设计方面入手,加强机械设备的刚度和稳定性,提高机床的机械传动效率,改进机床结构,减少共振现象,使机床的设计更加合理化。
机械加工过程中机械振动的成因分析

机械加工过程中机械振动的成因分析摘要:随着科学技术的飞速发展,机械加工水平也不断提高。
在加工过程中经常出现机械振动就会对机械加工造成不利的影响,因此有必要对机械加工过程中机械振动的成因进行深入研究,以便更好的保证工件的表面质量,并结合具体原因制定解决方案,减少振动的发生,提高加工质量。
关键词:机械加工;机械振动;成因分析1 机械加工中机械振动的分类1.1 强迫振动强迫振动是机械加工过程中较为常见的振动类型之一,产生这一振动的主要原因是由于在机械加工过程中受到外界周期性干扰的影响,进而导致设备系统出现强迫振动现象。
同时由于外界力量所产生的干扰具有周期性的特点,因此可以提供持续的动力机械振动。
也就是说,只要有外力干扰,振动将不会停止。
其中强迫振动的特点主要有:一是干扰力不会受到强迫振动的影响而改变;二是强迫振动的频率与外界周期干扰力的频率具有一定关系,频率相同或者存在整倍数关系;三是当外界干扰力的频率与系统固有频率的比值等于或接近时,机械系统则会产生共振,并且在这种情况下,所产生的振幅将达到最大值。
1.2 自激振动自激振动是在机械加工过程中所出现的交替周期振动,是在一定相互作用下产生的。
其中自激振动表现的特点主要有:一是自激振动的频率与系统固有频率具有一定关第,通常会表现为处于等于或接近的状态;二是自激振动的产生及其振幅受到多种因素影响,通常会取决于系统所获得的能量与阻尼消耗能量的对比情况;三是因为持续自激振动的干扰力是由振动过程本身激发的,所以当外界振动中止,其干扰力及能量补充过程也就会立即消失。
2 产生机械加工振动的原因分析2.1 产生强迫振动的原因在加工过程中容易出现的强迫振动,产生强迫振动有内部因素和外部因素,但主要受到内部因素的影响,主要表现在以下几个方面:一是机床上回转件不平衡影响了机械整体离心力发生周期性变化。
这一状况通常会由电机或卡盘、皮带轮回转不平衡引起。
二是因为机床传动零件的缺陷情况导致周传动力的期性变化。
机械加工振动分析及控制措施
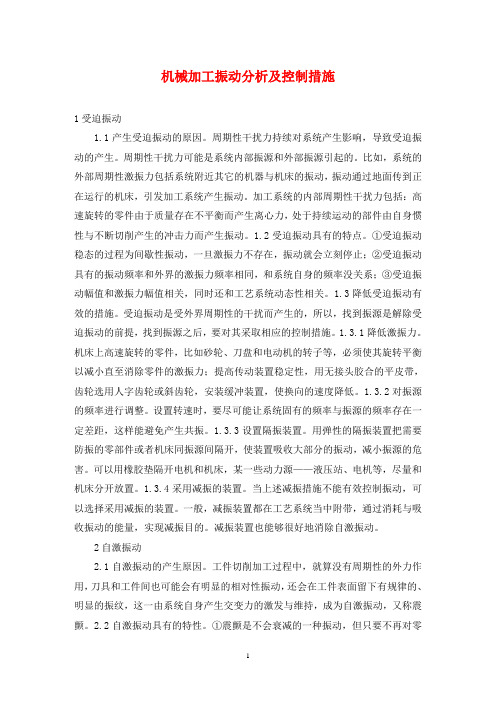
机械加工振动分析及控制措施1受迫振动1.1产生受迫振动的原因。
周期性干扰力持续对系统产生影响,导致受迫振动的产生。
周期性干扰力可能是系统内部振源和外部振源引起的。
比如,系统的外部周期性激振力包括系统附近其它的机器与机床的振动,振动通过地面传到正在运行的机床,引发加工系统产生振动。
加工系统的内部周期性干扰力包括:高速旋转的零件由于质量存在不平衡而产生离心力,处于持续运动的部件由自身惯性与不断切削产生的冲击力而产生振动。
1.2受迫振动具有的特点。
①受迫振动稳态的过程为间歇性振动,一旦激振力不存在,振动就会立刻停止;②受迫振动具有的振动频率和外界的激振力频率相同,和系统自身的频率没关系;③受迫振动幅值和激振力幅值相关,同时还和工艺系统动态性相关。
1.3降低受迫振动有效的措施。
受迫振动是受外界周期性的干扰而产生的,所以,找到振源是解除受迫振动的前提,找到振源之后,要对其采取相应的控制措施。
1.3.1降低激振力。
机床上高速旋转的零件,比如砂轮、刀盘和电动机的转子等,必须使其旋转平衡以减小直至消除零件的激振力;提高传动装置稳定性,用无接头胶合的平皮带,齿轮选用人字齿轮或斜齿轮,安装缓冲装置,使换向的速度降低。
1.3.2对振源的频率进行调整。
设置转速时,要尽可能让系统固有的频率与振源的频率存在一定差距,这样能避免产生共振。
1.3.3设置隔振装置。
用弹性的隔振装置把需要防振的零部件或者机床同振源间隔开,使装置吸收大部分的振动,减小振源的危害。
可以用橡胶垫隔开电机和机床,某一些动力源——液压站、电机等,尽量和机床分开放置。
1.3.4采用减振的装置。
当上述减振措施不能有效控制振动,可以选择采用减振的装置。
一般,减振装置都在工艺系统当中附带,通过消耗与吸收振动的能量,实现减振目的。
减振装置也能够很好地消除自激振动。
2自激振动2.1自激振动的产生原因。
工件切削加工过程中,就算没有周期性的外力作用,刀具和工件间也可能会有明显的相对性振动,还会在工件表面留下有规律的、明显的振纹,这一由系统自身产生交变力的激发与维持,成为自激振动,又称震颤。
第四节机械加工过程中的振动

假定切削过程受到一个瞬时的偶然性 扰动,刀具与工件便发生相对振动(自由 振动),振动的幅值将因有阻尼存在而逐 渐衰减。但此时会在加工表面上留下一段 振纹,如图4-31b所示。当工件转过一转后, 刀具要在留有振纹的表面上进行切削(图 4-31c),切削厚度将发生波动,这就有交 变的动态切削力产生。如果切削过程中各 种条件的匹配是促进振动的,那么将会进 一步发展到图4-31d那样的颤振状态。通常, 将这种由于切削厚度变化效应引起的自激 振动,称为再生型颤振。
二、产生自激振动的条件
1.自激振动实例
2.产生自激振动的条件
在振出过程中,切削力凡对振动系统 作功,振动系统则从切削过程中吸收一部 分能量(W振出=W12345),贮存在振动系统 中。
刀架的振入运动则是在弹性恢复力F弹 作用下产生的,振入运动与切削力方向相 反,振动系统对切削过程作功,即振动系 统要消耗能量(W振入=W54621)。
5)若干扰力频率与工艺系统某一固有 频率相同,系统将产生共振。如工艺系统 阻尼较小,则共振振幅将十分大。
二、机械加工中的自激振动 (颤振)
(一)概述
机械加工过程中,在没有周期性外力 (相对于切削过程而言)作用下,由系统 内部激发反馈产生的周期性振动,称为自 激振动,简称为颤振。
自激振动产生的原理
若W振出=W振入,则ΔW<0,即振动系统 每振动一次,系统便会损失一部分能量。 因此,系统也不会有自激振动产生,加工 系统仍是稳定的。
当W振出>W振入时,加工系统将有持续 的自激振动产生,加工系统处于不稳定状 态。根据W振出与W振入的差值大小又可 分为以下三种情况:
3.机械加工过程中的振动
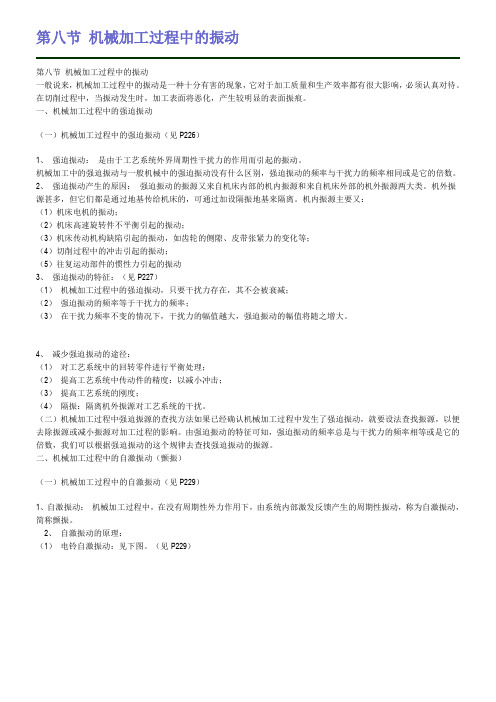
第八节机械加工过程中的振动第八节机械加工过程中的振动一般说来,机械加工过程中的振动是一种十分有害的现象,它对于加工质量和生产效率都有很大影响,必须认真对待。
在切削过程中,当振动发生时,加工表面将恶化,产生较明显的表面振痕。
一、机械加工过程中的强迫振动(一)机械加工过程中的强迫振动(见P226)1、强迫振动:是由于工艺系统外界周期性干扰力的作用而引起的振动。
机械加工中的强迫振动与一般机械中的强迫振动没有什么区别,强迫振动的频率与干扰力的频率相同或是它的倍数。
2、强迫振动产生的原因:强迫振动的振源又来自机床内部的机内振源和来自机床外部的机外振源两大类。
机外振源甚多,但它们都是通过地基传给机床的,可通过加设隔振地基来隔离。
机内振源主要又:(1)机床电机的振动;(2)机床高速旋转件不平衡引起的振动;(3)机床传动机构缺陷引起的振动,如齿轮的侧隙、皮带张紧力的变化等;(4)切削过程中的冲击引起的振动;(5)往复运动部件的惯性力引起的振动3、强迫振动的特征:(见P227)(1)机械加工过程中的强迫振动,只要干扰力存在,其不会被衰减;(2)强迫振动的频率等于干扰力的频率;(3)在干扰力频率不变的情况下,干扰力的幅值越大,强迫振动的幅值将随之增大。
4、减少强迫振动的途径:(1)对工艺系统中的回转零件进行平衡处理;(2)提高工艺系统中传动件的精度:以减小冲击;(3)提高工艺系统的刚度;(4)隔振:隔离机外振源对工艺系统的干扰。
(二)机械加工过程中强迫振源的查找方法如果已经确认机械加工过程中发生了强迫振动,就要设法查找振源,以便去除振源或减小振源对加工过程的影响。
由强迫振动的特征可知,强迫振动的频率总是与干扰力的频率相等或是它的倍数,我们可以根据强迫振动的这个规律去查找强迫振动的振源。
二、机械加工过程中的自激振动(颤振)(一)机械加工过程中的自激振动(见P229)1、自激振动:机械加工过程中,在没有周期性外力作用下,由系统内部激发反馈产生的周期性振动,称为自激振动,简称颤振。
- 1、下载文档前请自行甄别文档内容的完整性,平台不提供额外的编辑、内容补充、找答案等附加服务。
- 2、"仅部分预览"的文档,不可在线预览部分如存在完整性等问题,可反馈申请退款(可完整预览的文档不适用该条件!)。
- 3、如文档侵犯您的权益,请联系客服反馈,我们会尽快为您处理(人工客服工作时间:9:00-18:30)。
机械加工中的强迫振动现象分析
沈庆玲
(七台河煤碳职业技术培训学院)
摘 要:主要介绍了机械加工中强迫振动产生的原因及减少强迫振动的途径。
关键词:机械加工;强迫振动;误差;隔振
中图分类号:U469105 文献标识码:C 文章编号:1008-3383(2004)03-0062-01
机械加工过程中,在工件和刀具之间常产生振
动。
产生振动时,工艺系统的正常切削过程便受到干扰和破坏,从而零件加工表面出现振纹,降低了零件的加工精度和表面质量。
机械加工过程中产生的振动,按其产生的原因来分,可分为自由振动、受迫振动和自激振动三大类。
自由振动往往是由于切削力的突然变化或其他外力的冲击等原因所引起的。
这种振动一般可以迅速衰减,因此对机械加工过程中的影响较小。
而受迫振动和自激振动都是不能自然衰减而且危害较大的振动。
下面主要对强迫振动进行简单的分析。
1 强迫振动产生的原因
机械加工中的强迫振动,是一种由工艺系统内部或外部周期交变的激振力作用下引起的振动。
机械加工中引起工艺系统强迫振动的激振力,主要来自以下几方面。
111 机床上高速回转的零件的不平衡
机床上高速回转零件较多,如电动机转子、带轮、主轴、卡盘和工件、
磨床的砂轮等,由于不平衡而产生激振力F (即离心惯性力)。
如图1所示是一个安装在简支梁上的电动机,以ω的角速度旋转时,假如由于电动机转子不平衡而产生离心力F n ,则F n 沿X 方向的分力F x (F x =F n cos ωt )就是该梁的外界周期干扰力。
在这一干扰力的作用下,简支梁将作不衰减的振动。
图1 强迫振动力学模型
112 机床传动系统中的误差
机床传动系统中的齿轮,由于制造和装配误差
而产生周期性的激振力。
此外,皮带接缝,轴承滚动体尺寸差和液压传动中油液脉动等各种因素均可能引起工艺系统强迫振动。
113 切削过程中本身的不均匀性
切削过程中的间歇特性,如铣削、拉削及车削带有键槽的断续表面等,由于间歇切削而引起切削的周期性变化,从而激起振动。
114 外部振源
由邻近设备(如冲压设备、龙门刨等)工作时的强烈振动通过地基传来,使工艺系统产生相同(或整倍数)频率的强迫振动。
综合上面的讨论,可以看出强迫振动的主要特点有以下几方面。
(1)强迫振动是在外界周期性干扰力的作用下产生的,但振动本身并不能引起干扰力的变化。
当干扰力停止时,则工艺系统的振动也随着停止。
(2)不管振动系统本身的固有频率如何,强迫振动的频率总是与外界干扰力的频率相同。
(3)强迫振动的振幅大小在很大程度上决定于干扰力的频率与系统固有频率的比值λ。
当比值等于或接近1时,振幅将达到量大值,这种现象通常称为“共振”。
(4)强迫振动的振幅大小还与干扰力、系统刚度及其阻尼系数有关。
2 减小强迫振动的措施和途径
(1)减少或消除振源的激振力:例如精确平衡各回转零件、部件,对电动机的转子和砂轮不但要进行静平衡,而且要进行动平衡。
轴承的制造精度以及装配和调试质量常常对减小强迫振动有较大的影响。
(2)隔振:即在振动的路线中安放具有弹性性能的隔振装置,使振源所产生的大部分振动由隔振装置来吸收,以减小振源对加工过程中的干扰。
如将机床安置在防振地基上及在振源与刀具和工件之间设置弹簧或橡皮垫片等。
(3)提高工艺系统的刚度及增大阻尼,其目的是使强迫振动的频率远离系统的固有频率。
如使其避开共振区,使在λ≤0或λ≥0的情况下加工,采用刮研接触面来提高部件的刚度。
(4)采用阻尼器:通过阻尼作用,将振动能量转换成热能散失掉,以达到减振目的。
以上分析了机械加工中强迫振动的原因及特点、减小振动的措施和途径,随着科学技术的发展,也将有更好的措施。
收稿日期:2004-01-08
2004年 第3期(总第121期)
黑龙江交通科技
HEI LONG J I ANG J I AOTONG KE J I
No.3,2004
(Sum No.121)。