机械加工过程中的振动讲解
强迫振动现象分析资料讲解
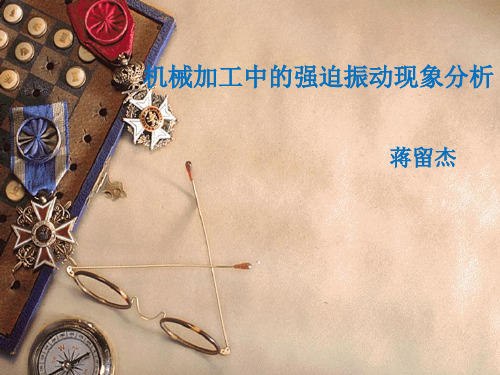
蒋留杰
机械加工过程中 ,在工件和刀具之间常产 生振动 。 产生振动时 ,工艺系 统的正常 切削 过程便受到干扰和破坏 ,从而零件 加工表面出现振纹 ,降低了 零件的加工 精度和表面质量 。机械加工过程中 产生 的振动 ,按其产生的原因来分 ,可分为自 由 振动 、强迫振动 和 自 激振动 三大 类 。 自由振动往往是由于切削力的突然 变化或其他外力的冲击等原因所引 起的 。 这种振动一般可以迅速衰减 ,因此对机械 加工过程中 的影响较小 。 而强迫振动 和自激振动都是不能自 然衰减而且危害 较大的振动 。
(2) 隔振 :即在振动的路线中安放具有弹性性 能的隔振装置 ,使振源所产生的大部分振动由 隔振装置来吸收 ,以减小振源对加工过程中 的干扰 。 如将机床安置在防振地基上及在振 源与刀具和工件之间设置弹簧或橡皮垫片等 。
(3) 提高工艺系统的刚度及增大阻尼 ,其目 的是使强迫振动的频率远离系统的固有频率 。 如使其避开共振区 ,使在λ≤0 (干扰力的频 率与系统固有频率的比值) 或λ ≥0 的情况 下加工 ,采用刮研接触面来提高部件的刚度 。
Байду номын сангаас
1 . 4 外部振源
由邻近设备 (如冲压设备 、龙门 刨等) 工作时的强烈振动通过地基传来 ,使工艺 系统产生相同 (或整倍数) 频率的强迫振 动。
3
减小强迫振动的措施和途径
(1) 减少或消除振源的激振力 :例如精确平衡 各回转零件、部件 ,对电动机的转子和砂轮不 但要进行静平衡 ,而且要进行动平衡。 轴承 的制造精度以及装配和调试质量常常对减小强 迫振动有较大的影响 。
1 .2 机床传动系统中的误差
机床传动系统中的齿轮 ,由于制造和装配误 差而产生周期性的激振力 。此外 ,皮带接 缝 ,轴承滚动体尺寸差和液压传动中油液脉 动等各种因素均可能引起工艺系统强迫振 动。
机械加工过程中机械振动的原因及对策分析
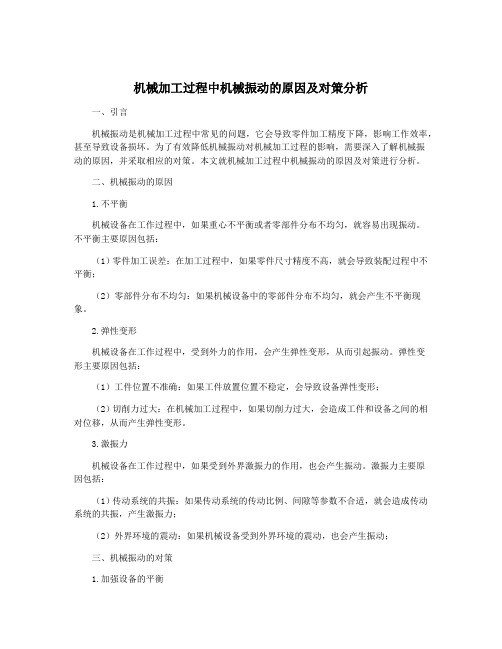
机械加工过程中机械振动的原因及对策分析一、引言机械振动是机械加工过程中常见的问题,它会导致零件加工精度下降,影响工作效率,甚至导致设备损坏。
为了有效降低机械振动对机械加工过程的影响,需要深入了解机械振动的原因,并采取相应的对策。
本文就机械加工过程中机械振动的原因及对策进行分析。
二、机械振动的原因1.不平衡机械设备在工作过程中,如果重心不平衡或者零部件分布不均匀,就容易出现振动。
不平衡主要原因包括:(1)零件加工误差:在加工过程中,如果零件尺寸精度不高,就会导致装配过程中不平衡;(2)零部件分布不均匀:如果机械设备中的零部件分布不均匀,就会产生不平衡现象。
2.弹性变形机械设备在工作过程中,受到外力的作用,会产生弹性变形,从而引起振动。
弹性变形主要原因包括:(1)工件位置不准确:如果工件放置位置不稳定,会导致设备弹性变形;(2)切削力过大:在机械加工过程中,如果切削力过大,会造成工件和设备之间的相对位移,从而产生弹性变形。
3.激振力机械设备在工作过程中,如果受到外界激振力的作用,也会产生振动。
激振力主要原因包括:(1)传动系统的共振:如果传动系统的传动比例、间隙等参数不合适,就会造成传动系统的共振,产生激振力;(2)外界环境的震动:如果机械设备受到外界环境的震动,也会产生振动;三、机械振动的对策1.加强设备的平衡对于不平衡造成的振动,可以采取以下对策:(1)提高零件加工精度:在零件加工过程中,应严格控制尺寸精度,避免误差导致的不平衡;(2)调整零部件分布:改变零部件的位置,使得机械设备的重心分布更加均匀。
2.增加刚度对于弹性变形引起的振动,可以采取以下对策:(1)稳定工件位置:通过改进夹具结构,提高工件的抓紧力,稳定工件的位置,减少弹性变形;(2)优化切削参数:通过调整切削速度、切削深度等参数,降低切削力,减少工件和设备之间的相对位移,减小弹性变形。
3.减少激振力对于激振力引起的振动,可以采取以下对策:(1)改善传动系统的设计:优化传动系统的传动比例、间隙等参数,避免传动系统的共振;(2)加强设备的隔振措施:通过在机械设备底部安装隔振装置,降低设备受外界环境震动的影响。
机械加工中振动的产生机理以及防治措施

机械加工中振动的产生机理以及防治措施一、机械加工过程中振动的危害振动会在工件加工表面出现振纹,降低了工件的加工精度和表面质量,低频振动时会产生波度;振动会引起刀具崩刃打刀现象并加速刀具或砂轮的磨损;振动使机床夹具连接部分松动,影响运动副的工作性能,并导致机床丧失精度;产生噪声污染,危害操作者健康;影响生产效率;二、机械加工过程中振动的类型机械加工过程中振动的类型:自由振动、强迫振动、自激振动。
1.自由振动工艺系统受到初始干扰力而破坏了其平衡状态后,系统仅靠弹性恢复力来维持的振动称为自由振动。
由于系统中存在阻尼,自由振动将逐渐衰弱,对加工影响不大。
2.强迫振动由稳定的外界周期性的干扰力(激振力)作用引起;除了力之外,凡是随时间变化的位移、速度和加速度,也可以激起系统的振动;强迫振动振源:机外+机内。
机外:其他机床、锻锤、火车、卡车等通过地基把振动传给机床机内:1)回转零部件质量的不平衡(旋转零件的质量偏心)2)机床传动件的制造误差和缺陷(如齿轮啮合时的冲击、皮带轮圆度误差及皮带厚度不均引起的张力变化,滚动轴承的套圈和滚子尺寸及形状误差)3)切削过程中的冲击(如往复部件的冲击;液压传动系统的压力脉动;断续切削时的冲击振动)强迫振动的特征:频率特征:与干扰力的频率相同,或是干扰力频率整倍数幅值特征:与干扰力幅值、工艺系统动态特性有关。
当干扰力频率接近或等于工艺系统某一固有频率时,产生共振相角特征:强迫振动位移的变化在相位上滞后干扰力一个φ角,其值与系统的动态特性及干扰力频率有关强迫振动的运动方程:图示:内圆磨削振动系统a) 模型示意图b)动力学模型c)受力图3.自激振动在没有周期性外力(相对于切削过程)作用下,由系统内部激发反馈产生的周期性振动;自激振动过程可用传递函数概念说明;切削过程本身能引起某种交变切削力,而振动系统能通过这种力的变化,从不具备交变特性的能源中周期性的获得补充能量,从而维持住这个振动。
机械加工中机械振动的原因解析与应对

机械加工中机械振动的原因解析与应对随着工业技术的不断发展,机械加工已成为现代生产中不可或缺的重要环节。
然而在机械加工过程中,经常会遇到机械振动的问题,这不仅会影响加工质量,还有可能引发安全事故。
了解机械振动的原因和有效应对是非常重要的。
一、机械振动的原因解析1.不稳定的加工条件在机械加工过程中,如果加工条件不稳定,比如切削速度、切削深度、进给速度等参数没有得到合理控制,就会引起机床工作状态的不稳定,从而产生振动。
2.机床结构设计不合理机床是机械加工的主要设备,如果机床的结构设计不合理,会导致刚性不足、固定件松动等问题,使得在加工过程中产生振动。
3.切削刀具磨损切削刀具是机械加工中常用的工具,如果刀具磨损严重或者安装不良,就会引起加工过程中的振动。
4.工件材料变形在加工过程中,由于工件材料自身性能的变化,也有可能引起机械振动。
5.进给系统问题进给系统的性能不稳定、传动链条出现松动等问题,会导致机床在工作时的振动。
刀具在加工时,间歇切削会引起刀具的振动,影响加工质量。
二、机械振动的应对措施1.合理选择切削工艺参数在机床的结构设计上,要注重刚性的设计和加强工装的固定,确保机床在加工过程中稳定性。
加强机床的维护保养工作,及时发现并解决机床结构问题。
3.切削刀具的选择和维护合理选择切削刀具,并确保刀具的安装正确、刃磨合适,定期进行刀具的维护和更换工作。
选择质量稳定的工件材料,对材料性能进行精密测试和处理,以减少因材料变形引起的机械振动。
对进给系统进行定期的检查和维护工作,确保传动链条、导轨等部件的稳定性和耐磨性。
6.刀具间歇切削的解决方法对于刀具间歇切削引起的问题,可以采用提高刀具速度、增加刀具的刚度等方法来减少刀具的振动。
三、结语在机械加工中,机械振动是一个常见问题,如果不能得到及时合理的处理,会对加工质量和安全性造成很大影响。
加强对机械振动原因的分析和应对措施的研究非常重要。
通过合理选择加工条件、加强机床结构设计和维护、切削刀具的选择和维护、工件材料处理、进给系统的维护以及解决刀具间歇切削等措施,可以有效减少机械振动的发生,提高机械加工的质量和效率。
机械加工中的振动类型分类

了解振动要先从振动的类型开始,振动从不同的角度来划分,可以分为很多类型,有强迫型、自激型、自由型等,每种类型都有各自的特点,都对机械生产过程会产生不同的影响,下面我们就具体来看看吧。
1自激振动的概念及类型分析
自激振动是振动的另一种类型,自激振动从某种意义上说是一种自发振动。
因为这种振动是不受外力干扰,而自动引起的自发性振动,在振动的过程中,受交变力的影响会引起持续的运动,持续且有规律性,机械设备在工作时,齿轮和部件相互交织在一起,而产生一定的磨擦导致这种自激振动产生。
2自由振动的概念及类型分析
振动中还有最后一种类型,是自由振动类型。
这种振动类型对机械加工的影响相对不是很大。
由于机械运转过程中,激振力对系统不断作用,从而机械设备的平衡就被破坏,我们把能对激振力,进行约束的方式称为自由振动。
3强迫振动的概念及类型分析
强迫振动类型,是在外力有规律的作用下产生的振动。
例如,在我们经常见到的,削、切、磨的过程中,由于机械设备的带动,像电动机械,砂轮、皮带等的带动下,都会产生振动。
这其中因为皮带或长或短,或厚或薄,油泵不稳定等因素的影响,从不同程度上都会促使振动的发生,这种振动现象就是强迫振动,这种振动会对加工产品的精密准确度产生影响,
从而影响加工产品的圆度、加工产品的粗糙度等。
一些回转动的机械设备,振动对回转精度也会产生影响。
机械加工中机械振动的原因解析与应对

机械加工中机械振动的原因解析与应对
机械加工中的机械振动指的是机器在运行过程中的震动和共振现象。
机械振动不仅会影响产品的加工精度和质量,还会对机器本身造成损伤,因此必须引起足够的重视。
以下是机械振动的原因解析与应对措施。
一、机械振动的原因
1.不平衡:机械零件中存在不平衡现象时,发动机转动时会由于离心力产生横向或纵向的振动。
2.共振:当机器设备的固有频率与强制振动频率接近或相等时,就会出现共振现象,引起机器的强烈振动。
3.摩擦和磨损:机械零件的摩擦和磨损会导致运动不平稳,引起机器的振动。
4.不稳定结构:机器结构不够稳定,机械零件的振动会自我放大。
5.加工精度:由于零件加工误差、装配不良等原因,会导致机械零件在运行时振动加剧。
二、机械振动的应对措施
1.动平衡处理:对于不平衡现象严重的零件,应采取动平衡处理,通过在转子上安装调节重量来消除不平衡,降低振动的影响。
2.增加阻尼:在机械设备中增加阻尼器,可以有效地减小机械振动的幅度和频率。
3.改变固有频率:对于因共振引起的振动,可以通过改变机器的结构和材料,改变固有频率,避免共振的出现。
4.加强润滑:保持机器设备的良好润滑状态,减少磨损和摩擦,可以降低机械振动的程度。
5.改善加工质量:严格控制零件加工误差,加强装配质量,提高机器的运行精度,从而减轻机械振动的影响。
综上所述,机械振动是机械加工中必须面对的一个问题。
只有全方位的应对措施,才能保证机器的正常运行,同时也能保证产品加工的质量和精度。
补充:机械加工过程中的振动
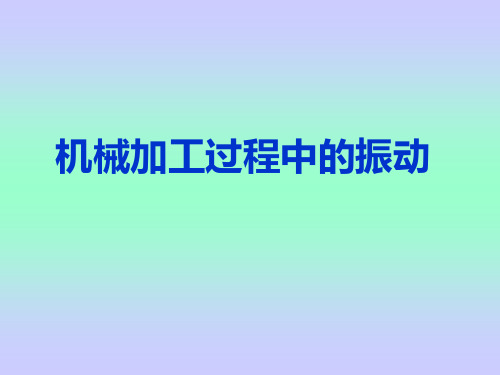
机械加工过程中产生的振动,是一种十 分有害的现象,这是因为:
1)刀具相对于工件振动会使加工表面 产生波纹,这将严重影响零件的使用性能。
2)刀具相对于工件振动,切削截面、 切削角度等将随之发生周期性变化,工艺系 统将承受动态载荷的作用,刀具易于磨损 (有时甚至崩刃),机床的连接特性会受到 破坏,严重时甚至使切削加工无法进行。
再生型切削颤振:这种由于切削厚度变化效 应(简称再生效应)而引起的自激振动称为再 生型切削颤振。
图4-49 再生型颤振的产生过程
切削过程一般都是部分地或完全地在有 振纹(波纹)的表面上进行的,车削、铣削、 刨削、钻削、磨削等均不例外,由振纹再生 效应引发的再生型切削颤振是机床切削的主 要形态。
产生再生型颤振的条件:
3)为了避免发生振动或减小振动,有 时不得不降低切削用量,致使机床、刀具的 工作性能得不到充分发挥,限制了生产效率 的提高。
综上分析可知,机械加工中的振动对于 加工质量和生产效率都有很大影响,须采取 措施控制振动。
一、机械加工过程中的强迫振动 强迫振动:机械加工过程中的强迫振动
是指在外界周期性于扰力的持续作用下,振 动系统受迫产生的振动。
机械加工过程中的强迫振动与一般机械 振动中的强迫振动没有本质上的区别。机械 加工过程中的强迫振动的频率与干扰力的频 率相同或是其整数倍;当干扰力的频率接近 或等于工艺系统某一薄弱环节固有频率时, 系统将产生共振。
强迫振动的振源有来自于机床内部的机 内振源和来自机床外部的机外振源。
机外振源甚多,但它们都是通过地基传给 机床的,可以通过加设隔振地基来隔离外部 振源,消除其影响。
2.增大工艺系统的阻尼 增大工艺系统中的阻尼,可通过多种方 法实现。例如,使用高内阻材料制造零件, 增加运动件的相对摩擦,在床身、立柱的封 闭内腔中充填型砂,在主振方向安装阻振器 等。 (三)采用减振装置 常用的减振装置有动力式减振器、摩擦 式减振器和冲击式减振器等三种类型。
机械加工过程中振动产生的原因

机械加工过程中振动产生的原因2.1自然振动由于机械的构造非常复杂,在通电之后,机械会受到电力驱使进行运作。
由于机械内部的机械零部件非常多,在使用过程中机械零件急速运转,不同零件受空气阻力,进而产生振动。
可以说,自然振动是机械运转中不可避免的.振动问题,也是最常见、原理最为简单的振动类型。
同时,自然振动还包括外部因素影响,生产地不平、风力因素等影响。
通常情况下,机械各个运作零件都有一个磨合期,在刚刚接通电流时会产生明显振动,随着不同零件正常运转,起振动力机会逐渐削弱。
总之,自然振动是受技术、环境的影响,是不可避免的振动问题,对机械整体运作不会产生明显影响。
2.2自激振动有关调查研究显示,自然振动虽然是一种不可控问题,但如果不加以限制即会产生自激振动。
自激振动相比自然振动来说,就会对机械主体产生一定的伤害,轻则运作零部件松动、重则造成机械短路烧毁电线以及零件破损。
自激振动即是机械主体颤振,机械在正常加工中出现高频率振动,严重影响工业生产。
机械加工产生颤动的原因主要表现在以下几点:(1)机械在加工过程中,由于加工主体硬度突然变化,刀具运作频率突然改变,进而发生刀崩问题后,即会因为内部零件运作不协调而产生自激振动。
(2)机械中的各个零部件在生产中,由于刀具与零件之间契合度不足或生产规格不规范,而产生运作冲突,进而产生自激振动。
(3)机械刀具质量不过关,刚性较差,在生产过程中刀杆振动,进而带动机械整体振动。
(4)在机械生产过程中,由于生产刀具与产品生产规格相冲突,导致切削量无法满足标准,进而出现自激振动。
总体来说自激振动主要是由机械内部因素所引起的问题,主要是机械刀具或零部件之间的问题而产生的自激振动。
但是在自激振动中,振动周期会出现一定变化。
2.3强迫振动强迫振动与自激振动不同,强迫振动通常受外界因素与内部因素所产生的振动问题。
其内部因素主要是指:机械加工生产中,会由于机械各个部门零件所产生的离心振动,继而导致机械整体振动。
机械加工过程中机械振动的成因及解决方法

机械加工过程中机械振动的成因及解决方法摘要:机械加工过程中机械振动会影响加工的质量,因此在开展机械加工的过程中,需要采取有效控制措施来使机械振动得到降低。
本文对机械加工过程中发生振动的原因和特点进行了介绍,希望能够通过更加有效地方式解决机械振动的问题,从而更好地促进机械加工行业的发展。
关键词:机械加工;机械振动;成因;解决措施引言在以往的机械加工过程中,经常会出现振动现象,使加工的精准度和精细度受到严重影响。
机械加工中的振动会使加工刀具在加工的过程中出现位置偏移,从而使加工产品出现瑕疵,影响了加工产品的质量。
同时,机械振动还会使刀具出现磨损现象,影响了刀具的使用寿命,同时对机床整体系统产生影响,使加工系统在振动反作用力的影响下难以正常运行。
在开展机械加工工作的过程中,机械振动的现象通常情况下来源于对机械设备的不合理使用,从而导致机械技工的设备操作不能够符合相应的规范性特点,使机械振动现象对机械加工产生严重影响。
在开展机械加工的过程中,需要提高操作规范性,使机械振动现象能够得到有效改善。
1在机械加工时发生振动的原因和对应特点1.1 自由振动在开展机械加工工作的过程中,经常会出现零部件自由振动的现象,这种振动现象产生的原因也最为简单。
在机械加工零部件的时候,机械切削加工通常会导致操作波动,进而引发整个机械系统的自由振动。
同时,自由振动现象的出现还与外界各种力的因素有关,外力通过对振动力的影响,使振动力能够通过自由振动的方式逐渐衰弱,从而能够在机械振动的过程中确保机械的正常运转,使机械加工自由振动工作能够更好地得以发展。
在出现自由振动之后,由于缺乏外力的补充,使自由振动在发生一段时间后自动减弱。
因此,从整体上来看,自由振动对整个机械加工过程的影响不大。
但是,相关施工人员也要注意在开展机械加工的过程中对自由振动加以控制,避免自激振动的发生。
1.2 强迫振动在开展机械加工的过程中,通常会受到干扰力的影响而出现强迫振动,因此在开展强迫振动消除的过程中,首先要借助一定的技术和方式来消除干扰力。
浅谈机械加工过程中的振动

浅谈机械加工过程中的振动摘要:一般说来,机械加工过程中的振动是一种十分有害的现象,它对于加工质量和生产效率都有很大影响,必须认真对待。
在切削过程中,当振动发生时,加工表面将恶化,产生较明显的表面振痕。
本文主要论述了机械加工过程中振动的产生原因,并提出了一些自己的观点看法,希望能为解决振动产生的不良影响提供一些思考。
关键词:机械加工振动影响机械加工过程中,工艺系统(工件—夹具—刀具—机床)经常会发生振动,给加工过程带来很多不利的影响。
发生振动时,工艺系统的正常切削过程受到干扰和破坏,使零件加工表面产生振纹,降低了零件的加工精度和表面质量,低频振动增大波度,高频振动增加表面粗糙度;振动可能使刀刃崩碎,特别是对硬质合金、陶瓷、金刚石和立方氮化硼等韧性差的刀具,影响刀具的寿命;振动会导致机床、夹具的零件连接松动,增大间隙,降低刚度和精度,并缩短使用寿命;强烈的振动和伴随而来的噪声污染环境,危害操作者的身心健康。
由于振动限制了切削用量的进一步提高,影响了生产效率,严重时甚至不能正常切削,因此,研究机械加工过程中的振动,探索抑制、消除振动的措施是十分必要的。
1 机械加工过程中振动分类1.1 自由振动当振动系统受到初始干扰力(又称激振力)的作用而破坏了平衡状态后,去掉激振力或约束后所发生的振动,称为自由振动。
由于系统总是存在阻尼,故自由振动总是衰减的,因此,一般来说,自由振动对加工过程的影响不大。
自由振动的特性取决于系统本身,即其固有频率,振型取决于振动系统的质量和刚度。
1.2 强迫振动在外界周期性干扰力的作用下,系统受迫产生的振动称为强迫振动。
由于有外界周期性干扰力作能量补充,所以振动能够持续进行。
只要外界周期性干扰力存在,振动就不会因阻尼而停止。
强迫振动的频率等于外界周期性干扰力的频率或者是它的整数倍。
1.3 自激振动由振动系统自身产生的交变力激发和维持的一种周期性振动称为自激振动。
切削过程中产生的自激振动也称为颤振。
机械装配中的振动特性分析与优化方法
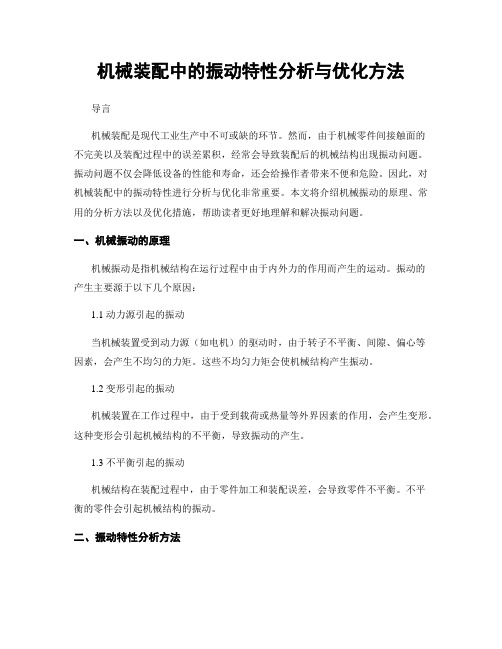
机械装配中的振动特性分析与优化方法导言机械装配是现代工业生产中不可或缺的环节。
然而,由于机械零件间接触面的不完美以及装配过程中的误差累积,经常会导致装配后的机械结构出现振动问题。
振动问题不仅会降低设备的性能和寿命,还会给操作者带来不便和危险。
因此,对机械装配中的振动特性进行分析与优化非常重要。
本文将介绍机械振动的原理、常用的分析方法以及优化措施,帮助读者更好地理解和解决振动问题。
一、机械振动的原理机械振动是指机械结构在运行过程中由于内外力的作用而产生的运动。
振动的产生主要源于以下几个原因:1.1 动力源引起的振动当机械装置受到动力源(如电机)的驱动时,由于转子不平衡、间隙、偏心等因素,会产生不均匀的力矩。
这些不均匀力矩会使机械结构产生振动。
1.2 变形引起的振动机械装置在工作过程中,由于受到载荷或热量等外界因素的作用,会产生变形。
这种变形会引起机械结构的不平衡,导致振动的产生。
1.3 不平衡引起的振动机械结构在装配过程中,由于零件加工和装配误差,会导致零件不平衡。
不平衡的零件会引起机械结构的振动。
二、振动特性分析方法为了更好地了解机械装配中的振动特性,需要进行振动测试和分析。
下面介绍几种常用的振动特性分析方法:2.1 频谱分析频谱分析是一种将时间域信号(振动信号)转换到频率域的方法。
通过频谱分析,可以得到机械结构在不同频率上的振动情况。
常用的频谱分析方法包括傅里叶变换和小波变换。
2.2 模态分析模态分析是一种通过测量机械结构在不同模态下的振动特性,来研究结构的振动行为的方法。
模态分析可以得到机械结构的固有频率、振型和振动模态等信息,有助于判断结构的强度和稳定性。
2.3 有限元分析有限元分析是一种通过将实际结构离散为有限数量的元素,将结构的振动行为转化为运动微分方程组求解的方法。
通过有限元分析,可以计算机械结构在不同工况下的振动响应和应力分布,从而指导结构的优化设计。
三、振动优化方法在进行振动优化时,可以采取以下几种方法:3.1 优化零件加工精度提高零件加工精度可以减小零件间的装配误差,从而减少振动的发生。
机械加工过程中机械振动的原因及对策分析

机械加工过程中机械振动的原因及对策分析机械加工过程中出现机械振动的原因较多,主要包括以下几个方面:1.切削力的不平衡:机械加工过程中,切削力的大小和方向会不断变化,如果切削力不平衡,就会引发机械振动。
这主要是由于工件材料的异质性、表面瑕疵等原因导致的切削力不均匀分布。
2.进给速度过大:如果在机械加工过程中进给速度过大,刀具与工件之间会发生剧烈的冲击,从而产生振动。
进给速度过大还会引起切屑的断裂不良、刀具严重磨损等问题。
3.机床刚度不足:机床的刚度不足也是引起机械振动的重要原因。
刚度不足会导致机械系统的固有频率过低,与工件切削频率接近,从而引起共振现象。
4.切削液不当:切削液在机械加工过程中起到冷却润滑的作用,如果切削液的流量、温度、质量不合适,则会导致切削液无法有效冷却刀具和工件,增加切削力并引起振动。
针对上述问题,可以采取以下对策来降低机械振动:1.切削力平衡:选择合适的刀具和进给方式,确保切削力均匀分布。
在加工过程中可以采用动态平衡的方法动态调整刀具和工件的重心位置,提高切削力的平衡性。
2.控制进给速度:根据加工材料的性质和切削条件,合理控制进给速度,避免过大的进给速度引起振动。
如果需要加工高硬度材料,可以采用高速切削技术来提高加工效率,减少机械振动。
3.提高机床刚度:加强机床的刚度和稳定性可以有效抑制机械振动。
可以采用增加机床结构重量、增大导轨尺寸、优化机械系统刚度等措施来提高机床刚度。
4.优化切削液:选择合适的切削液,并设置合理的流量、温度和质量控制,确保切削液能够有效冷却刀具和工件,降低切削力。
还可以通过合理的刀具设计、提高工件材料的均匀性、改善切削过程中的冷却条件等方法来减少机械振动的发生,提高加工质量和效率。
对于特殊要求的加工任务,可以采用振动缓冲系统、动态平衡系统等技术手段来抑制机械振动,实现稳定加工。
机械加工过程中的振动和防止方法
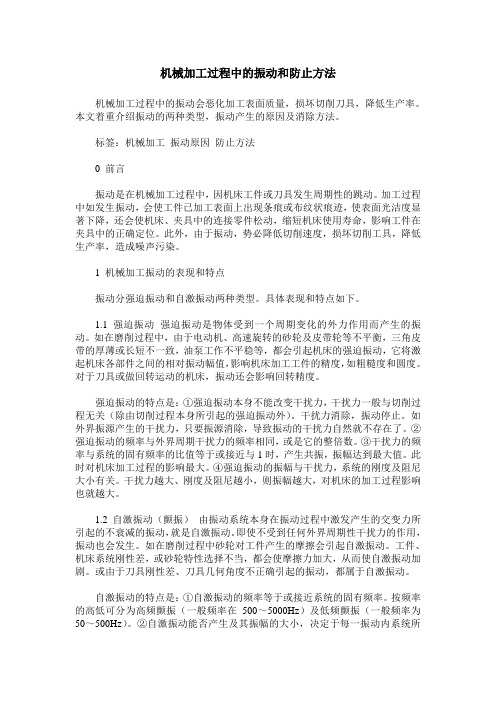
机械加工过程中的振动和防止方法机械加工过程中的振动会恶化加工表面质量,损坏切削刀具,降低生产率。
本文着重介绍振动的两种类型,振动产生的原因及消除方法。
标签:机械加工振动原因防止方法0 前言振动是在机械加工过程中,因机床工件或刀具发生周期性的跳动。
加工过程中如发生振动,会使工件已加工表面上出现条痕或布纹状痕迹,使表面光洁度显著下降,还会使机床、夹具中的连接零件松动,缩短机床使用寿命,影响工件在夹具中的正确定位。
此外,由于振动,势必降低切削速度,损坏切削工具,降低生产率,造成噪声污染。
1 机械加工振动的表现和特点振动分强迫振动和自激振动两种类型。
具体表现和特点如下。
1.1 强迫振动强迫振动是物体受到一个周期变化的外力作用而产生的振动。
如在磨削过程中,由于电动机、高速旋转的砂轮及皮带轮等不平衡,三角皮带的厚薄或长短不一致,油泵工作不平稳等,都会引起机床的强迫振动,它将激起机床各部件之间的相对振动幅值,影响机床加工工件的精度,如粗糙度和圆度。
对于刀具或做回转运动的机床,振动还会影响回转精度。
强迫振动的特点是:①强迫振动本身不能改变干扰力,干扰力一般与切削过程无关(除由切削过程本身所引起的强迫振动外)。
干扰力消除,振动停止。
如外界振源产生的干扰力,只要振源消除,导致振动的干扰力自然就不存在了。
②强迫振动的频率与外界周期干扰力的频率相同,或是它的整倍数。
③干扰力的频率与系统的固有频率的比值等于或接近与1时,产生共振,振幅达到最大值。
此时对机床加工过程的影响最大。
④强迫振动的振幅与干扰力,系统的刚度及阻尼大小有关。
干扰力越大、刚度及阻尼越小,则振幅越大,对机床的加工过程影响也就越大。
1.2 自激振动(颤振)由振动系统本身在振动过程中激发产生的交变力所引起的不衰减的振动,就是自激振动。
即使不受到任何外界周期性干扰力的作用,振动也会发生。
如在磨削过程中砂轮对工件产生的摩擦会引起自激振动。
工件、机床系统刚性差,或砂轮特性选择不当,都会使摩擦力加大,从而使自激振动加剧。
机械加工中机械振动的原因解析与应对

机械加工中机械振动的原因解析与应对
机械加工中的机械振动是指在机械加工过程中产生的机械系统的非均匀运动现象。
机械振动的产生原因很多,主要包括以下几个方面:
1.切削力引起的振动:切削力在机床和工件之间传递,当切削力不平衡时,就会引起机床和工件的振动。
2.零件不平衡引起的振动:在机械加工过程中,如果工件本身不平衡,或者夹具装夹不平衡,都会导致机床的振动。
3.切削过程中的共振现象:机械系统有自然振动频率,当切削过程中的振动频率与机械系统的自然频率相近时,就会发生共振现象,从而引起振动。
4.机床刚度不足引起的振动:机床的刚度直接影响着机床的稳定性和阻尼效果,如果机床刚度不足,就会导致振动加剧。
为了应对机械振动,可以采取以下几种措施:
1.提高机械系统的刚度:通过加强机床的结构设计和制造工艺,增加机床的刚度,从而减少机械振动的发生。
2.使用平衡装置:对工件和夹具进行平衡处理,减小零件的不平衡量,从而减少振动。
3.优化切削参数:合理选择切削速度、进给速度和切削深度等切削参数,避免过大或过小的切削力。
4.选用合适的切削工具:选择合适的切削工具,如刀具的刚度、刀具的几何形状等,从而减小切削力和振动。
5.加强润滑和冷却:合理使用润滑剂和冷却剂,保持切削过程中工件和切削工具的表面温度,减少摩擦和热变形,从而减小振动。
机械振动在机械加工中是一个普遍存在的问题,但通过合理的措施可以减少和控制振动,提高机械加工的质量和效率。
机械加工过程中机械振动的成因分析

机械加工过程中机械振动的成因分析摘要:随着科学技术的飞速发展,机械加工水平也不断提高。
在加工过程中经常出现机械振动就会对机械加工造成不利的影响,因此有必要对机械加工过程中机械振动的成因进行深入研究,以便更好的保证工件的表面质量,并结合具体原因制定解决方案,减少振动的发生,提高加工质量。
关键词:机械加工;机械振动;成因分析1 机械加工中机械振动的分类1.1 强迫振动强迫振动是机械加工过程中较为常见的振动类型之一,产生这一振动的主要原因是由于在机械加工过程中受到外界周期性干扰的影响,进而导致设备系统出现强迫振动现象。
同时由于外界力量所产生的干扰具有周期性的特点,因此可以提供持续的动力机械振动。
也就是说,只要有外力干扰,振动将不会停止。
其中强迫振动的特点主要有:一是干扰力不会受到强迫振动的影响而改变;二是强迫振动的频率与外界周期干扰力的频率具有一定关系,频率相同或者存在整倍数关系;三是当外界干扰力的频率与系统固有频率的比值等于或接近时,机械系统则会产生共振,并且在这种情况下,所产生的振幅将达到最大值。
1.2 自激振动自激振动是在机械加工过程中所出现的交替周期振动,是在一定相互作用下产生的。
其中自激振动表现的特点主要有:一是自激振动的频率与系统固有频率具有一定关第,通常会表现为处于等于或接近的状态;二是自激振动的产生及其振幅受到多种因素影响,通常会取决于系统所获得的能量与阻尼消耗能量的对比情况;三是因为持续自激振动的干扰力是由振动过程本身激发的,所以当外界振动中止,其干扰力及能量补充过程也就会立即消失。
2 产生机械加工振动的原因分析2.1 产生强迫振动的原因在加工过程中容易出现的强迫振动,产生强迫振动有内部因素和外部因素,但主要受到内部因素的影响,主要表现在以下几个方面:一是机床上回转件不平衡影响了机械整体离心力发生周期性变化。
这一状况通常会由电机或卡盘、皮带轮回转不平衡引起。
二是因为机床传动零件的缺陷情况导致周传动力的期性变化。
机械加工中的振动概述PPT(18张)
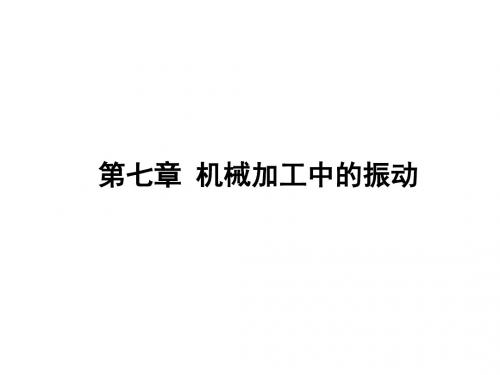
7.1.2 工艺系统的动刚度和动柔度 303
7.2 切削过程中的颤振
304
7.2.1 再生颤振原理
305
7.2.2 振型耦合颤振原理
307
7.2.3 刀具的高频颤振
309
7.3 减小振动、提高稳定性的工艺途径 309
7.3.1 机械加工中的强迫振动及其减小途径 309
7.3.2 减小或消除切削颤振的工艺途径 310
主偏角对振幅的影响
前角对振幅的影响
倒棱消振车刀
波形刃铣刀抑制振动的机理 波形刃立铣刀铣削时切削层分布
三、提高工艺系统的抗振性和采用减振装置消 除振动
( 1)阻尼减振器 (2)摩擦阻尼器 (3)冲击减振器 (4)动力减振器
•
1、有时候,我们活得累,并非生活过于刻薄,而是我们太容易被外界的氛围所感染,被他人的情绪所左右。
7.3.3 提高工艺系统的抗振性和采用减振装置消除振动
第七章 机械加工中的振动
§7-1 机械加工中振动的基本概念
一、机械加工中振动的基本类型
自由振动、强迫振动、自激振动
二、工艺系统的动刚度和动柔度
动刚度: 动柔度:
KD
P X
机床工作中Wd场出K1D现的XP三种振动:
整机摇晃、接合面处部件间的相对振动、机床零部
三、刀具的高频颤振
1、刀具后刀面与工件间的摩擦摩擦力小;车刀向下振动时,相对速度小, 摩擦力大,产生动态力
2、刀具切削时实际前后角的变化 3、切削力的下降特性
刀具振动前后角的变化
切削力与切削速度关系
§7-3 减小振动、提高稳定性的工艺途径
5、世上最美好的事是:我已经长大,父母还未老;我有能力报答,父母仍然健康。
论述机械加工的振动消除与利用的方法

论述机械加工的振动消除与利用的方法振动能够给机械加工带来不良的影响。
如果出现振动,工件相对于刀具会产生位移,生产的产品会在表面产生振痕,如果振动严重会导致产品质量下降。
振动能够使加工系统不断受到工件的反作用力,会使刀具磨损或者崩刃,破坏机床加工系统,使工作无法正常进行。
同时振动也有一定作用,例如通过振动消磨和超声波加工等方式,会对机械加工产生促进的作用。
因此需要对机械加工中产生振动的原因进行分析,对振动进行控制,充分地将振动有效地利用起来。
1 振动的类型和产生原因导致振动产生的原因有许多方面,主要有3种类型:自由振动、强迫振动、自激振动。
1.1 对自由振动进行分析如果系统工作中外力消失,机床系统自身会产生衰减运动,称为自由振动。
产生的原因是工艺系统受到部分作用力,例如外界对系统的冲击力、机床传动系统非周期性引起的冲击力和加工工件时产生的冲击力等,会使系统的本身不平衡,需要靠系统本身的弹性恢复力进行恢复,由此产生的振动主要是自由振动。
自由振动的频率同系统自身的频率相同,但是系统会产生阻尼作用力,因此自由振动会慢慢消退。
1.2 对强迫振动进行分析强迫振动主要是受到外界周期性的干扰力引起的振动。
其产生的主要原因是:在切削加工中,因为构造机床的零件有些精度不高,当机床在工作时会出现不均匀的现象,从而导致振动的产生。
同时在刀具反面也会引起振动,各种刀具都具有自己独特的刃口高度,因此在机械加工就会产生振动。
如果被切削的工件出现表面不连续以及软硬度不相同等等方面的原因,也能够导致在加工中产生振动。
同时在加工系统的外部,也存在着导致车床在工作时产生振动的原因。
强迫振动具有自己独特的特点,主要为:因为导致振动产生的稳态是谐振动,所以在干扰力没有消除时,振动不会减退,如果干扰力消除,振动就会立刻停止;根据振动产生的原因,振动的频率等同于干扰力的频率;当系统的阻尼力变小,强迫振动的振幅就会变大,谐波的影响轨迹范围也越大,因此加大阻尼,可以有效地减少强迫振动的振幅;在共振的区域,很小的频率就会导致振幅变化大,同时相位角也会发生变化。
- 1、下载文档前请自行甄别文档内容的完整性,平台不提供额外的编辑、内容补充、找答案等附加服务。
- 2、"仅部分预览"的文档,不可在线预览部分如存在完整性等问题,可反馈申请退款(可完整预览的文档不适用该条件!)。
- 3、如文档侵犯您的权益,请联系客服反馈,我们会尽快为您处理(人工客服工作时间:9:00-18:30)。
再生型切削颤振:这种由于切削厚度变化效 应(简称再生效应)而引起的自激振动称为再 生型切削颤振。
图4-49 再生型颤振的产生过程
切削过程一般都是部分地或完全地在有 振纹(波纹)的表面上进行的,车削、铣削、 刨削、钻削、磨削等均不例外,由振纹再生 效应引发的再生型切削颤振是机床切削的主 要形态。
2.消除或减弱产生自激振动的条件 (1)减小重叠系数 再生型颤振是由于 在有波纹的表面上进行切削引起的,如果本 转(次)切削不与前转(次)切削振纹相重 叠,就不会有再生型颤振发生。重叠系数越 小,就越不容易产生再生型颤振。重叠系数 值大小取决于加工方式、刀具的几何形状及 切削用量等。适当增大刀具的主偏角和进给 量,均可使重叠系数减小。
综上分析可知,机械加工中的振动对于 加工质量和生产效率都有很大影响,须采取 措施控制振动。
一、机械加工过程中的强迫振动 强迫振动:机械加工过程中的强迫振动
是指在外界周期性于扰力的持续作用下,振 动系统受迫产生的振动。
机械加工过程中的强迫振动与一般机械 振动中的强迫振动没有本质上的区别。机械 加工过程中的强迫振动的频率与干扰力的频 率相同或是其整数倍;当干扰力的频率接近 或等于工艺系统某一薄弱环节固有频率时, 系统将产生共振。
2)刀具相对于工件振动,切削截面、 切削角度等将随之发生周期性变化,工艺系 统将承受动态载荷的作用,刀具易于磨损 (有时甚至崩刃),机床的连接特性会受到 破坏,严重时甚至使切削加工无法进行。
3)为了避免发生振动或减小振动,有 时不得不降低切削用量,致使机床、刀具的 工作性能得不到充分发挥,限制了生产效率 的提高。
绩80% ❖ 授课教师:赵斌(机电工程学院) ❖ 联系方式(手机):18203671508 ❖ 电子邮箱:zhaobin978@ ❖ QQ:49588976
第五节 机械加工过程中的振动
机械加工过程中产生的振动,是一种十 分有害的现象,这是因为:
1)刀具相对于工件振动会使加工表面 产生波纹,这将严重影响零件的使用性能。
❖ 选用教材:机械制造技术基础.于骏一,邹青主编.机械工业出 版社
❖ 参考书: 1. 谢家赢.机械制造技术.机械工业出版社 2. 冯之敬主编.《机械制造工程原理》. 清华大学出版社 3. 张福润 徐鸿本 刘延林.《机械制造技术基础》.华中科技
大学出版社 4. 卢秉恒主编.《机械制造技术基础》.机械工业出版社 5. 杨叔子主编.《机械制造技术基础》.机械工业出版社 ❖ 考核方式:平时成绩(平时、作业、论文)的比例20%,期末成
强迫振动的振源有来自于机床内部的机 内振源和来自机床外部的机外振源。机外振 源甚多,但它们都是通过地基传给机床的, 可以通过加设隔振地基来隔离外部振源,消 除其影响。机内振源主要有:机床上的带轮、 卡盘或砂轮等高速回转零件因旋转不平衡引 起的振动;机床传动机构的缺陷引起的振动; 液压传动系统压力脉动引起的振动;由于断 续切削引起的振动等。
效地提高机床加工系统的稳定性。提高各结 合面的接触刚度,对主轴支承施加预载荷, 对刚性较差的工件增加辅助支承等都可以提 高工艺系统的刚度。
2.增大工艺系统的阻尼 增大工艺系统中的阻尼,可通过多种方 法实现。例如,使用高内阻材料制造零件, 增加运动件的相对摩擦,在床身、立柱的封 闭内腔中充填型砂,在主振方向安装阻振器 等。 (三)采用减振装置 常用的减振装置有动力式减振器、摩擦 式减振器和冲击式减振器等三种类型。
如果确认机械加工过程中发生的是强迫 振动,就要设法查找振源,以便消除振源或 减小振源对加工过程的影响。
二、机械加工过程中的自激振动(颤振) 1.机械加工过程中的自激振动 与强迫振动相比,自激振动具有以下特
征: l)机械加工中的自激振动是指在没有
周期性外力(相对于切削过程而言)干扰下 产生的振动运动。
重叠系数:
(2)减小切削刚度 减小切削刚度可以 减小切削力,可以降低切削厚度变化效应 (再生效应)和振型耦合效应的作用。改善 工件材料的可加工性、增大前角、增大主偏 角和适当提高进给量等,均可使切削刚度下 降。
(3)合理布置振动系统小刚度主轴的位 置。
(二)改善工艺系统的动态特性 1.提高工艺系统刚度 提高工艺系统薄弱环节的刚度,可以有
2.振型耦合原理 实际振动系统一般都是多自由度系统。
四、控制机械加工振动的途径 (一)消除或减弱产生振动的条件 1.消除或减弱产生强迫振动的条件 (1)消除或减小内部振源 机床上的高
速回转零件必须满足动平衡要求;提高传动 元件及传动装置的制造精度和装配精度,保 证传动平稳;使动力源与机床本体分离。
(2)调整振源的频率 通过改变传动比, 使可能引起强迫振动的振源频率远离机机床加 工系统薄弱环节的固有频率,避免产生共振。
(3)采取隔振措施 使振源产生的部分振 动被隔振装置所隔离或吸收。隔振方法有两种, 一种是主动隔振,阻止机内振源通过地基外传; 另一种是被动隔振,阻止机外干扰力通过地基 传给机床。常用的隔振材料有橡皮、金属弹簧、 空气弹簧、矿渣棉、木屑等。
2)自激振动的频率接近于系统某一薄 弱振型的固有频率。
三、自激振动的激振机理 1.振纹再生原理 在刀具进行切削的过程中,若受到一个瞬
时的偶然扰动力的作用,刀具与工件便会产生 相对振动(属自由振动),振动的幅值将因系 统阻尼的存在而逐渐衰减。但该振动会在已加 工表面上留下一段振纹。当工件转过一转后, 刀具便会在留有振纹的表面上进行切削,切削 厚度时大时小,这就有动态切削力产生。如果 机床加工系统满足产生自激振动的条件,振动 便会进一步发展到持续的振动状态。
产生再生型颤振的条件,一般说,本转 (次)切削的振纹与前转(次)切削的振纹 总不会完全同步,它们在相位上有一个差值。 设本转(次)切削的振动运动为:
yt An cost
则上转(次)切削的振动运动为
yt T An1 cost
式中 T-工件转一转的时间;
-振动源频率;
An -本转(次)切削的振动振幅; An1 -上转(次)切削的振动幅值。