机械加工过程中的振动
机械加工过程中机械振动的原因及对策分析
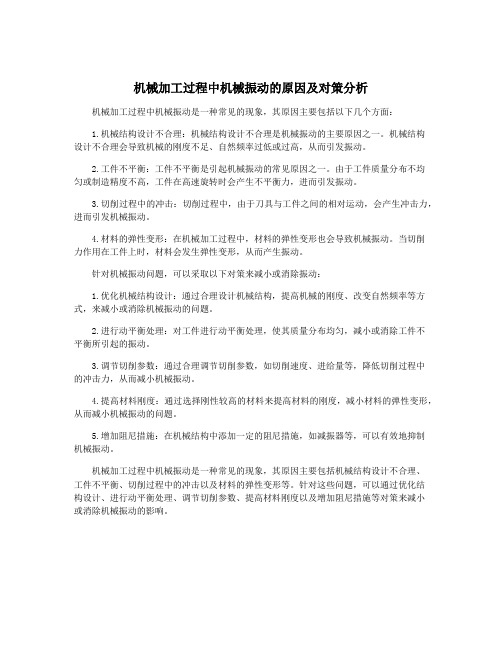
机械加工过程中机械振动的原因及对策分析机械加工过程中机械振动是一种常见的现象,其原因主要包括以下几个方面:1.机械结构设计不合理:机械结构设计不合理是机械振动的主要原因之一。
机械结构设计不合理会导致机械的刚度不足、自然频率过低或过高,从而引发振动。
2.工件不平衡:工件不平衡是引起机械振动的常见原因之一。
由于工件质量分布不均匀或制造精度不高,工件在高速旋转时会产生不平衡力,进而引发振动。
3.切削过程中的冲击:切削过程中,由于刀具与工件之间的相对运动,会产生冲击力,进而引发机械振动。
4.材料的弹性变形:在机械加工过程中,材料的弹性变形也会导致机械振动。
当切削力作用在工件上时,材料会发生弹性变形,从而产生振动。
针对机械振动问题,可以采取以下对策来减小或消除振动:1.优化机械结构设计:通过合理设计机械结构,提高机械的刚度、改变自然频率等方式,来减小或消除机械振动的问题。
2.进行动平衡处理:对工件进行动平衡处理,使其质量分布均匀,减小或消除工件不平衡所引起的振动。
3.调节切削参数:通过合理调节切削参数,如切削速度、进给量等,降低切削过程中的冲击力,从而减小机械振动。
4.提高材料刚度:通过选择刚性较高的材料来提高材料的刚度,减小材料的弹性变形,从而减小机械振动的问题。
5.增加阻尼措施:在机械结构中添加一定的阻尼措施,如减振器等,可以有效地抑制机械振动。
机械加工过程中机械振动是一种常见的现象,其原因主要包括机械结构设计不合理、工件不平衡、切削过程中的冲击以及材料的弹性变形等。
针对这些问题,可以通过优化结构设计、进行动平衡处理、调节切削参数、提高材料刚度以及增加阻尼措施等对策来减小或消除机械振动的影响。
机械加工中机械振动的原因解析与应对

机械加工中机械振动的原因解析与应对机械加工中的振动是指机械加工过程中,工件或工具发生的机械运动形成的振动现象。
机械振动的原因主要包括以下几个方面:1. 不平衡:机械旋转部件如转子、电机、风扇等因不平衡而引起的振动。
这种振动主要是由于旋转部件质量分布不均匀引起的,解决这类问题通常需要进行动平衡。
2. 间隙:机械加工中,由于零件配合尺寸、装配、磨合、磨削等原因引起的间隙,会导致零件在工作时发生相对位移,从而产生振动。
3. 弹性变形:机械零件在受力作用下会发生弹性变形,当受力作用消失时会恢复原状,这种变形会引起机械振动。
4. 不稳定运动:机械加工中,当工件转速超过某一临界值时,会出现不稳定的转子振动现象,即临界速度振动。
5. 过程中的剧烈变形:例如切削过程中的刀具振动、工件材料在切削过程中的振动等。
针对机械振动问题,可以采取以下几种应对方法:1. 优化设计和加工工艺:通过合理设计机械结构,考虑到零件的刚度和强度,尽量减小不平衡、间隙等因素引起的振动。
对于关键零部件尺寸和配合的要求要严格控制,以减小间隙引起的振动。
2. 动平衡和静平衡:对于旋转部件的不平衡问题,可以采取动平衡或静平衡的方法来解决。
动平衡是指在机器运行时,通过在旋转体上加配质量,使得旋转体在高速运动时达到平衡状态;静平衡是指通过加配质量使得旋转体在不转动时达到平衡状态。
3. 提高零部件制造精度:加强零部件的制造工艺控制,例如提高零件的加工精度、配合尺寸的精度等,可减小振动。
4. 采用减振措施:对于已经发生振动的机械设备,可以采取减振措施来降低振动的幅度和频率。
在机械设备周围安装减振器、减振垫等。
5. 检修和维护:定期对机械设备进行检修和维护,及时处理机械设备的故障和不良状态,防止机械振动的产生和发展。
机械振动是机械加工中常见的问题,对机械设备的正常运行和加工品质会产生不良影响,因此需要通过优化设计和加工工艺、动平衡和静平衡、提高零部件制造精度、采用减振措施、检修和维护等多种方法来解决和应对机械振动问题。
机械加工过程中机械振动的原因及对策分析
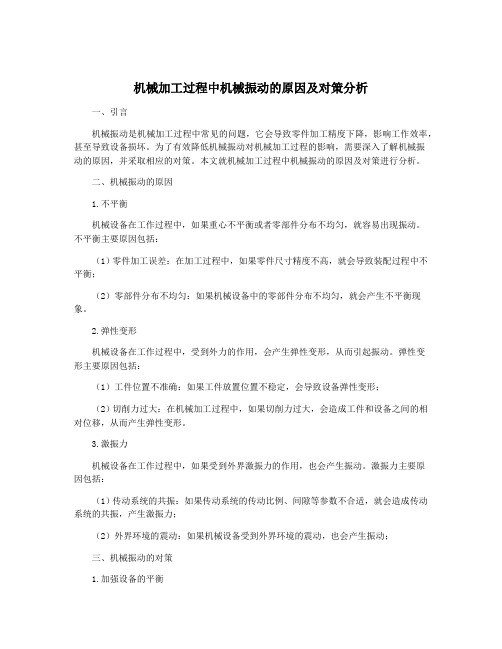
机械加工过程中机械振动的原因及对策分析一、引言机械振动是机械加工过程中常见的问题,它会导致零件加工精度下降,影响工作效率,甚至导致设备损坏。
为了有效降低机械振动对机械加工过程的影响,需要深入了解机械振动的原因,并采取相应的对策。
本文就机械加工过程中机械振动的原因及对策进行分析。
二、机械振动的原因1.不平衡机械设备在工作过程中,如果重心不平衡或者零部件分布不均匀,就容易出现振动。
不平衡主要原因包括:(1)零件加工误差:在加工过程中,如果零件尺寸精度不高,就会导致装配过程中不平衡;(2)零部件分布不均匀:如果机械设备中的零部件分布不均匀,就会产生不平衡现象。
2.弹性变形机械设备在工作过程中,受到外力的作用,会产生弹性变形,从而引起振动。
弹性变形主要原因包括:(1)工件位置不准确:如果工件放置位置不稳定,会导致设备弹性变形;(2)切削力过大:在机械加工过程中,如果切削力过大,会造成工件和设备之间的相对位移,从而产生弹性变形。
3.激振力机械设备在工作过程中,如果受到外界激振力的作用,也会产生振动。
激振力主要原因包括:(1)传动系统的共振:如果传动系统的传动比例、间隙等参数不合适,就会造成传动系统的共振,产生激振力;(2)外界环境的震动:如果机械设备受到外界环境的震动,也会产生振动;三、机械振动的对策1.加强设备的平衡对于不平衡造成的振动,可以采取以下对策:(1)提高零件加工精度:在零件加工过程中,应严格控制尺寸精度,避免误差导致的不平衡;(2)调整零部件分布:改变零部件的位置,使得机械设备的重心分布更加均匀。
2.增加刚度对于弹性变形引起的振动,可以采取以下对策:(1)稳定工件位置:通过改进夹具结构,提高工件的抓紧力,稳定工件的位置,减少弹性变形;(2)优化切削参数:通过调整切削速度、切削深度等参数,降低切削力,减少工件和设备之间的相对位移,减小弹性变形。
3.减少激振力对于激振力引起的振动,可以采取以下对策:(1)改善传动系统的设计:优化传动系统的传动比例、间隙等参数,避免传动系统的共振;(2)加强设备的隔振措施:通过在机械设备底部安装隔振装置,降低设备受外界环境震动的影响。
机械加工中振动的产生机理以及防治措施

机械加工中振动的产生机理以及防治措施一、机械加工过程中振动的危害振动会在工件加工表面出现振纹,降低了工件的加工精度和表面质量,低频振动时会产生波度;振动会引起刀具崩刃打刀现象并加速刀具或砂轮的磨损;振动使机床夹具连接部分松动,影响运动副的工作性能,并导致机床丧失精度;产生噪声污染,危害操作者健康;影响生产效率;二、机械加工过程中振动的类型机械加工过程中振动的类型:自由振动、强迫振动、自激振动。
1.自由振动工艺系统受到初始干扰力而破坏了其平衡状态后,系统仅靠弹性恢复力来维持的振动称为自由振动。
由于系统中存在阻尼,自由振动将逐渐衰弱,对加工影响不大。
2.强迫振动由稳定的外界周期性的干扰力(激振力)作用引起;除了力之外,凡是随时间变化的位移、速度和加速度,也可以激起系统的振动;强迫振动振源:机外+机内。
机外:其他机床、锻锤、火车、卡车等通过地基把振动传给机床机内:1)回转零部件质量的不平衡(旋转零件的质量偏心)2)机床传动件的制造误差和缺陷(如齿轮啮合时的冲击、皮带轮圆度误差及皮带厚度不均引起的张力变化,滚动轴承的套圈和滚子尺寸及形状误差)3)切削过程中的冲击(如往复部件的冲击;液压传动系统的压力脉动;断续切削时的冲击振动)强迫振动的特征:频率特征:与干扰力的频率相同,或是干扰力频率整倍数幅值特征:与干扰力幅值、工艺系统动态特性有关。
当干扰力频率接近或等于工艺系统某一固有频率时,产生共振相角特征:强迫振动位移的变化在相位上滞后干扰力一个φ角,其值与系统的动态特性及干扰力频率有关强迫振动的运动方程:图示:内圆磨削振动系统a) 模型示意图b)动力学模型c)受力图3.自激振动在没有周期性外力(相对于切削过程)作用下,由系统内部激发反馈产生的周期性振动;自激振动过程可用传递函数概念说明;切削过程本身能引起某种交变切削力,而振动系统能通过这种力的变化,从不具备交变特性的能源中周期性的获得补充能量,从而维持住这个振动。
机械加工中机械振动的原因解析与应对

机械加工中机械振动的原因解析与应对随着工业技术的不断发展,机械加工已成为现代生产中不可或缺的重要环节。
然而在机械加工过程中,经常会遇到机械振动的问题,这不仅会影响加工质量,还有可能引发安全事故。
了解机械振动的原因和有效应对是非常重要的。
一、机械振动的原因解析1.不稳定的加工条件在机械加工过程中,如果加工条件不稳定,比如切削速度、切削深度、进给速度等参数没有得到合理控制,就会引起机床工作状态的不稳定,从而产生振动。
2.机床结构设计不合理机床是机械加工的主要设备,如果机床的结构设计不合理,会导致刚性不足、固定件松动等问题,使得在加工过程中产生振动。
3.切削刀具磨损切削刀具是机械加工中常用的工具,如果刀具磨损严重或者安装不良,就会引起加工过程中的振动。
4.工件材料变形在加工过程中,由于工件材料自身性能的变化,也有可能引起机械振动。
5.进给系统问题进给系统的性能不稳定、传动链条出现松动等问题,会导致机床在工作时的振动。
刀具在加工时,间歇切削会引起刀具的振动,影响加工质量。
二、机械振动的应对措施1.合理选择切削工艺参数在机床的结构设计上,要注重刚性的设计和加强工装的固定,确保机床在加工过程中稳定性。
加强机床的维护保养工作,及时发现并解决机床结构问题。
3.切削刀具的选择和维护合理选择切削刀具,并确保刀具的安装正确、刃磨合适,定期进行刀具的维护和更换工作。
选择质量稳定的工件材料,对材料性能进行精密测试和处理,以减少因材料变形引起的机械振动。
对进给系统进行定期的检查和维护工作,确保传动链条、导轨等部件的稳定性和耐磨性。
6.刀具间歇切削的解决方法对于刀具间歇切削引起的问题,可以采用提高刀具速度、增加刀具的刚度等方法来减少刀具的振动。
三、结语在机械加工中,机械振动是一个常见问题,如果不能得到及时合理的处理,会对加工质量和安全性造成很大影响。
加强对机械振动原因的分析和应对措施的研究非常重要。
通过合理选择加工条件、加强机床结构设计和维护、切削刀具的选择和维护、工件材料处理、进给系统的维护以及解决刀具间歇切削等措施,可以有效减少机械振动的发生,提高机械加工的质量和效率。
3-4 机械加工过程中的振动
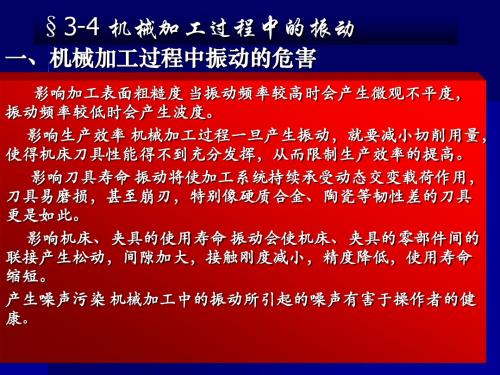
图4-71 机床自激振动闭环系统
2、自激振动的特点
1)自激振动是一种不衰减振动,振动过程本身能引起 某种力的周期性变化,振动系统能通过这种力的变化, 从不具备交变特性的能源中周期性地获得能量补充,从 而维持这个振动。加工系统本身运动一停止,自激振动 也就停止。 2)自激振动的频率等于或接近于系统的固有频率,这 与强迫振动有根本区别。 3)自激振动能否产生及振幅的大小取决于振动系统在每
三、自激振动及其产生机理
1、基本概念 在机械加工过程中,由该加工系统本身引起的交变 切削力反过来加强和维持系统自身振动的现象称自 激振动,又称颤振。 用传递函数概念来分析,机械加工系统是由一个振 动系统和调节系统组成的闭环系统(图4-71)。 在加工过程中,由于受到偶然性的外界干扰,会引 起切削力变化,而变化的切削力作用在机械加工系 统上,将使机械加工系统产生振动。这种振动又将 引起工件与刀具间相对位置的周期性变化,从而导 致切削过程产生维持振动的交变切削力。
2)y0与y相位差φ=π ,与a)类似,系统也无能 量获得。 3)y超前于y0,即 0°< φ<π ,此时切出半 周期中的平均切削厚度比切入半周期的小, 系统所做正功的值小于所做负功的值,系统 消耗能量。 4)y滞后于y0,即 0°>φ>-π ,此时切出比切 入半周期中的平均切削厚度大,正功大于负 功,系统有了能量获得,便产生了自激振动。 不难看出,y滞后于y0是产生再生自激振动的 必要条件。
一个周期内获得和消耗的能量对比情况,如图4-72所示 。图中 表示获得能量, 表示消耗能量。只系
3、自激振动的激振机理
关于自激振动产生的机理,有多种不同的学说,下面仅介绍 其中两种比较公认的理论。 (1)再生自激振动机理 在切削过程中,由于偶然的干扰,使加工系统产生了振 动并在加工表面上留下振纹。当第二次走刀时,刀具就将 在有振纹的表面上切削,使得切削厚度发生变化,导致切 削力作周期性地变化。 这种由切削厚度的变化而使切削力变化的效应称再生效 应,由此产生的自激振动称再生自激振动,如图4-73所示。 1)前一次走刀振纹 与后一次走刀振纹y0无相位差,切入和切 出的半个周期内平均切削厚度相等,切出时切削力所作的正功 (获得能量)等于切入时所作负功(消耗能量),系统无能量 获得.
3.机械加工过程中的振动
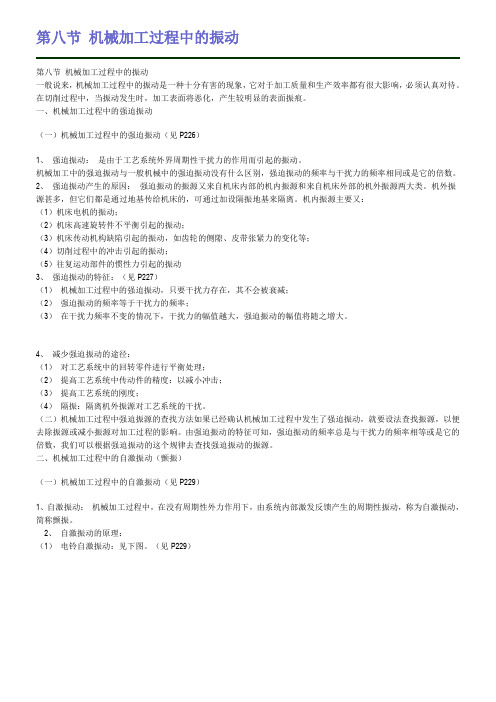
第八节机械加工过程中的振动第八节机械加工过程中的振动一般说来,机械加工过程中的振动是一种十分有害的现象,它对于加工质量和生产效率都有很大影响,必须认真对待。
在切削过程中,当振动发生时,加工表面将恶化,产生较明显的表面振痕。
一、机械加工过程中的强迫振动(一)机械加工过程中的强迫振动(见P226)1、强迫振动:是由于工艺系统外界周期性干扰力的作用而引起的振动。
机械加工中的强迫振动与一般机械中的强迫振动没有什么区别,强迫振动的频率与干扰力的频率相同或是它的倍数。
2、强迫振动产生的原因:强迫振动的振源又来自机床内部的机内振源和来自机床外部的机外振源两大类。
机外振源甚多,但它们都是通过地基传给机床的,可通过加设隔振地基来隔离。
机内振源主要又:(1)机床电机的振动;(2)机床高速旋转件不平衡引起的振动;(3)机床传动机构缺陷引起的振动,如齿轮的侧隙、皮带张紧力的变化等;(4)切削过程中的冲击引起的振动;(5)往复运动部件的惯性力引起的振动3、强迫振动的特征:(见P227)(1)机械加工过程中的强迫振动,只要干扰力存在,其不会被衰减;(2)强迫振动的频率等于干扰力的频率;(3)在干扰力频率不变的情况下,干扰力的幅值越大,强迫振动的幅值将随之增大。
4、减少强迫振动的途径:(1)对工艺系统中的回转零件进行平衡处理;(2)提高工艺系统中传动件的精度:以减小冲击;(3)提高工艺系统的刚度;(4)隔振:隔离机外振源对工艺系统的干扰。
(二)机械加工过程中强迫振源的查找方法如果已经确认机械加工过程中发生了强迫振动,就要设法查找振源,以便去除振源或减小振源对加工过程的影响。
由强迫振动的特征可知,强迫振动的频率总是与干扰力的频率相等或是它的倍数,我们可以根据强迫振动的这个规律去查找强迫振动的振源。
二、机械加工过程中的自激振动(颤振)(一)机械加工过程中的自激振动(见P229)1、自激振动:机械加工过程中,在没有周期性外力作用下,由系统内部激发反馈产生的周期性振动,称为自激振动,简称颤振。
机械加工中的振动

一、机械加工中的振动现象 1、振动对机械加工的影响 、
振动会在工件加工表面出现振纹, 振动会在工件加工表面出现振纹,降低了工件的加工精度和表面 质量; 质量; 振动会引起刀具崩刃打刀现象并加速刀具或砂轮的磨损; 振动会引起刀具崩刃打刀现象并加速刀具或砂轮的磨损; 振动使机床连接部分松动,影响运动副的工作性能, 振动使机床连接部分松动,影响运动副的工作性能,并导致机床 丧失精度; 丧失精度; 强烈的振动及伴随而来的噪声,还会污染环境, 强烈的振动及伴随而来的噪声,还会污染环境,危害操作者的身 心健康。为减小加工过程中的振动,有时不得不降低切削用量, 心健康。为减小加工过程中的振动,有时不得不降低切削用量,使 机械加工生择刀具参数
抑制自激振动途径
提高工艺系统抗振性
采用减振装置 采用减振装置 合理调整主振模态 刚度比及其组合 采用变速切削
减振装置
1) 阻尼器的原理及应用 ) 利用固体或液体的阻 尼来消耗振动的能量, 尼来消耗振动的能量, 实现减振。 实现减振。图7
2) 吸振器的原理及应用 ) ①动力吸振器(图8) 动力吸振器( ) ②冲击吸振器(图9) 冲击吸振器( )
机械加工中振动的种类及其主要特点
自由振动 当系统受到初始干扰力激励破 坏了其平衡状态后,系统仅靠 弹性恢复力来维持的振动称为 自由振动。由于总存在阻尼, 自由振动将逐渐衰减,如图 a所示。(占5%) 系统在周期性激振力(干扰力)持 续作用下产生的振动,称为强迫 振动。强迫振动的稳态过程是谐 振动,只要有激振力存在振动系 统就不会被阻尼衰减掉。 如图 b所示。(占35%) 在没有周期性干扰力作用的情 况下,由振动系统本身产生的 交变力所激发和维持的振动, 称为自激振动。切削过程中产 生的自激振动也称为颤振。 (占65%)
机械加工过程中的振动

(二) 改善工艺系统的动态特性
(1) 提高工艺系统刚度
(2) 增大工艺系统的阻尼
(三) 采用减振装置
(1) 动力式减振器
(2) 摩擦式减振器
(3) 冲击式减振器
1—飞轮 2—毂盘3—扭转轴4—螺 母5—弹簧6—摩擦盘
冲击式减振镗杆和镗刀
冷作硬化
切削过程中产生的塑性变形,会使表层金 属的晶格发生扭曲、畸变,晶粒间产生剪 切滑移,晶粒被拉长,甚至破碎,这些都 会使表层金属的硬度和强度提高,这种现 象称作冷作硬化,亦称强化。
作正功(获得能量)大于切入时所作负功,系统有
能量获得,产生自激振动。
(2) 振型耦合原理
◆ 振型耦合原理:将车床
x1
刀架简化为两自由度振动
x2
k2
系统,等效质量m用相互 垂直的等效刚度分别为k1 、k2两组弹簧支撑(设x1
α2
X
α1
bc
ad
m
为低刚度主轴)
β
◆ 自激振动的产生:
x1 k1
x2
F
① k1=k2,x1与x2无相位差,
❖ 由外界周期性的干扰力(激振力)作用引起 ❖ 强迫振动振源:机外+机内。
➢强迫振动的特征
❖ 频率特征 ❖ 幅值特征 ❖ 相角特征
二、 机械加工过程中自激振动
➢自激振动的概念 ❖ 在没有周期性外力作用 电动机 下,由系统内部激发反馈 (能源)
振动位移 机床振动系统 X(t) (弹性环节)
产生的周期性振动。
第五节 机械加工过程中的振动
➢机械加工过程中振动的危害
❖ 影响加工表面粗糙度,振动频率较低时会产生波度 ❖ 影响生产效率 ❖ 加速刀具磨损,易引起崩刃 ❖ 影响机床、夹具的使用寿命 ❖ 产生噪声污染,危害操作者健康
机械加工过程中机械振动的原因及对策分析
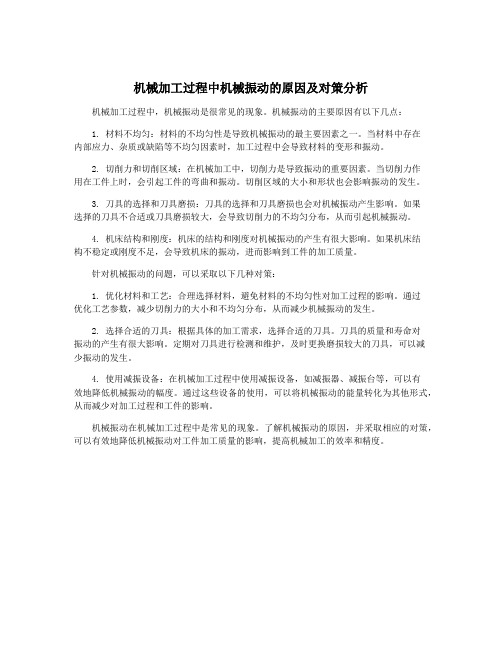
机械加工过程中机械振动的原因及对策分析机械加工过程中,机械振动是很常见的现象。
机械振动的主要原因有以下几点:1. 材料不均匀:材料的不均匀性是导致机械振动的最主要因素之一。
当材料中存在内部应力、杂质或缺陷等不均匀因素时,加工过程中会导致材料的变形和振动。
2. 切削力和切削区域:在机械加工中,切削力是导致振动的重要因素。
当切削力作用在工件上时,会引起工件的弯曲和振动。
切削区域的大小和形状也会影响振动的发生。
3. 刀具的选择和刀具磨损:刀具的选择和刀具磨损也会对机械振动产生影响。
如果选择的刀具不合适或刀具磨损较大,会导致切削力的不均匀分布,从而引起机械振动。
4. 机床结构和刚度:机床的结构和刚度对机械振动的产生有很大影响。
如果机床结构不稳定或刚度不足,会导致机床的振动,进而影响到工件的加工质量。
针对机械振动的问题,可以采取以下几种对策:1. 优化材料和工艺:合理选择材料,避免材料的不均匀性对加工过程的影响。
通过优化工艺参数,减少切削力的大小和不均匀分布,从而减少机械振动的发生。
2. 选择合适的刀具:根据具体的加工需求,选择合适的刀具。
刀具的质量和寿命对振动的产生有很大影响。
定期对刀具进行检测和维护,及时更换磨损较大的刀具,可以减少振动的发生。
4. 使用减振设备:在机械加工过程中使用减振设备,如减振器、减振台等,可以有效地降低机械振动的幅度。
通过这些设备的使用,可以将机械振动的能量转化为其他形式,从而减少对加工过程和工件的影响。
机械振动在机械加工过程中是常见的现象。
了解机械振动的原因,并采取相应的对策,可以有效地降低机械振动对工件加工质量的影响,提高机械加工的效率和精度。
机械加工过程中机械振动的原因及对策分析
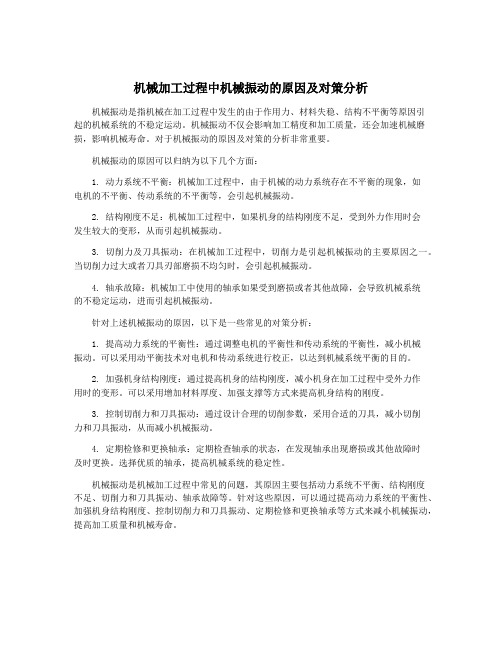
机械加工过程中机械振动的原因及对策分析机械振动是指机械在加工过程中发生的由于作用力、材料失稳、结构不平衡等原因引起的机械系统的不稳定运动。
机械振动不仅会影响加工精度和加工质量,还会加速机械磨损,影响机械寿命。
对于机械振动的原因及对策的分析非常重要。
机械振动的原因可以归纳为以下几个方面:1. 动力系统不平衡:机械加工过程中,由于机械的动力系统存在不平衡的现象,如电机的不平衡、传动系统的不平衡等,会引起机械振动。
2. 结构刚度不足:机械加工过程中,如果机身的结构刚度不足,受到外力作用时会发生较大的变形,从而引起机械振动。
3. 切削力及刀具振动:在机械加工过程中,切削力是引起机械振动的主要原因之一。
当切削力过大或者刀具刃部磨损不均匀时,会引起机械振动。
4. 轴承故障:机械加工中使用的轴承如果受到磨损或者其他故障,会导致机械系统的不稳定运动,进而引起机械振动。
针对上述机械振动的原因,以下是一些常见的对策分析:1. 提高动力系统的平衡性:通过调整电机的平衡性和传动系统的平衡性,减小机械振动。
可以采用动平衡技术对电机和传动系统进行校正,以达到机械系统平衡的目的。
2. 加强机身结构刚度:通过提高机身的结构刚度,减小机身在加工过程中受外力作用时的变形。
可以采用增加材料厚度、加强支撑等方式来提高机身结构的刚度。
3. 控制切削力和刀具振动:通过设计合理的切削参数,采用合适的刀具,减小切削力和刀具振动,从而减小机械振动。
4. 定期检修和更换轴承:定期检查轴承的状态,在发现轴承出现磨损或其他故障时及时更换。
选择优质的轴承,提高机械系统的稳定性。
机械振动是机械加工过程中常见的问题,其原因主要包括动力系统不平衡、结构刚度不足、切削力和刀具振动、轴承故障等。
针对这些原因,可以通过提高动力系统的平衡性、加强机身结构刚度、控制切削力和刀具振动、定期检修和更换轴承等方式来减小机械振动,提高加工质量和机械寿命。
机械加工中机械振动的原因解析与应对
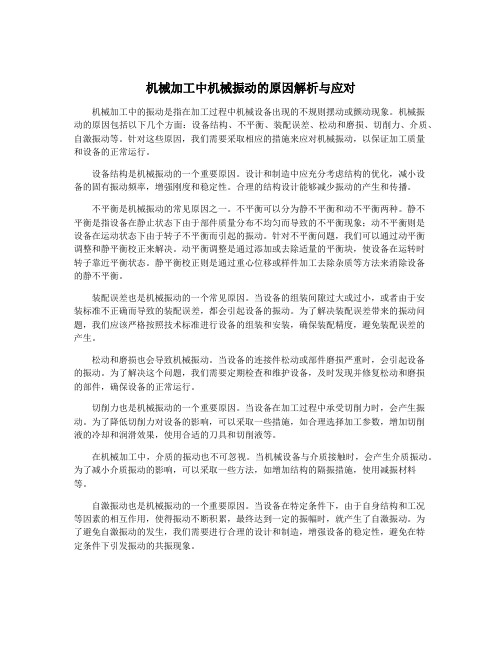
机械加工中机械振动的原因解析与应对机械加工中的振动是指在加工过程中机械设备出现的不规则摆动或颤动现象。
机械振动的原因包括以下几个方面:设备结构、不平衡、装配误差、松动和磨损、切削力、介质、自激振动等。
针对这些原因,我们需要采取相应的措施来应对机械振动,以保证加工质量和设备的正常运行。
设备结构是机械振动的一个重要原因。
设计和制造中应充分考虑结构的优化,减小设备的固有振动频率,增强刚度和稳定性。
合理的结构设计能够减少振动的产生和传播。
不平衡是机械振动的常见原因之一。
不平衡可以分为静不平衡和动不平衡两种。
静不平衡是指设备在静止状态下由于部件质量分布不均匀而导致的不平衡现象;动不平衡则是设备在运动状态下由于转子不平衡而引起的振动。
针对不平衡问题,我们可以通过动平衡调整和静平衡校正来解决。
动平衡调整是通过添加或去除适量的平衡块,使设备在运转时转子靠近平衡状态。
静平衡校正则是通过重心位移或样件加工去除杂质等方法来消除设备的静不平衡。
装配误差也是机械振动的一个常见原因。
当设备的组装间隙过大或过小,或者由于安装标准不正确而导致的装配误差,都会引起设备的振动。
为了解决装配误差带来的振动问题,我们应该严格按照技术标准进行设备的组装和安装,确保装配精度,避免装配误差的产生。
松动和磨损也会导致机械振动。
当设备的连接件松动或部件磨损严重时,会引起设备的振动。
为了解决这个问题,我们需要定期检查和维护设备,及时发现并修复松动和磨损的部件,确保设备的正常运行。
切削力也是机械振动的一个重要原因。
当设备在加工过程中承受切削力时,会产生振动。
为了降低切削力对设备的影响,可以采取一些措施,如合理选择加工参数,增加切削液的冷却和润滑效果,使用合适的刀具和切削液等。
在机械加工中,介质的振动也不可忽视。
当机械设备与介质接触时,会产生介质振动。
为了减小介质振动的影响,可以采取一些方法,如增加结构的隔振措施,使用减振材料等。
自激振动也是机械振动的一个重要原因。
第四节机械加工过程中的振动

假定切削过程受到一个瞬时的偶然性 扰动,刀具与工件便发生相对振动(自由 振动),振动的幅值将因有阻尼存在而逐 渐衰减。但此时会在加工表面上留下一段 振纹,如图4-31b所示。当工件转过一转后, 刀具要在留有振纹的表面上进行切削(图 4-31c),切削厚度将发生波动,这就有交 变的动态切削力产生。如果切削过程中各 种条件的匹配是促进振动的,那么将会进 一步发展到图4-31d那样的颤振状态。通常, 将这种由于切削厚度变化效应引起的自激 振动,称为再生型颤振。
二、产生自激振动的条件
1.自激振动实例
2.产生自激振动的条件
在振出过程中,切削力凡对振动系统 作功,振动系统则从切削过程中吸收一部 分能量(W振出=W12345),贮存在振动系统 中。
刀架的振入运动则是在弹性恢复力F弹 作用下产生的,振入运动与切削力方向相 反,振动系统对切削过程作功,即振动系 统要消耗能量(W振入=W54621)。
5)若干扰力频率与工艺系统某一固有 频率相同,系统将产生共振。如工艺系统 阻尼较小,则共振振幅将十分大。
二、机械加工中的自激振动 (颤振)
(一)概述
机械加工过程中,在没有周期性外力 (相对于切削过程而言)作用下,由系统 内部激发反馈产生的周期性振动,称为自 激振动,简称为颤振。
自激振动产生的原理
若W振出=W振入,则ΔW<0,即振动系统 每振动一次,系统便会损失一部分能量。 因此,系统也不会有自激振动产生,加工 系统仍是稳定的。
当W振出>W振入时,加工系统将有持续 的自激振动产生,加工系统处于不稳定状 态。根据W振出与W振入的差值大小又可 分为以下三种情况:
机械加工过程中机械振动的原因及对策分析
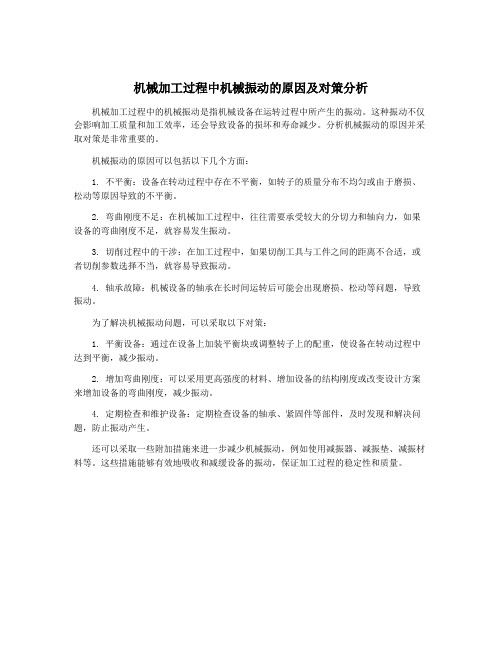
机械加工过程中机械振动的原因及对策分析
机械加工过程中的机械振动是指机械设备在运转过程中所产生的振动。
这种振动不仅会影响加工质量和加工效率,还会导致设备的损坏和寿命减少。
分析机械振动的原因并采取对策是非常重要的。
机械振动的原因可以包括以下几个方面:
1. 不平衡:设备在转动过程中存在不平衡,如转子的质量分布不均匀或由于磨损、松动等原因导致的不平衡。
2. 弯曲刚度不足:在机械加工过程中,往往需要承受较大的分切力和轴向力,如果设备的弯曲刚度不足,就容易发生振动。
3. 切削过程中的干涉:在加工过程中,如果切削工具与工件之间的距离不合适,或者切削参数选择不当,就容易导致振动。
4. 轴承故障:机械设备的轴承在长时间运转后可能会出现磨损、松动等问题,导致振动。
为了解决机械振动问题,可以采取以下对策:
1. 平衡设备:通过在设备上加装平衡块或调整转子上的配重,使设备在转动过程中达到平衡,减少振动。
2. 增加弯曲刚度:可以采用更高强度的材料、增加设备的结构刚度或改变设计方案来增加设备的弯曲刚度,减少振动。
4. 定期检查和维护设备:定期检查设备的轴承、紧固件等部件,及时发现和解决问题,防止振动产生。
还可以采取一些附加措施来进一步减少机械振动,例如使用减振器、减振垫、减振材料等。
这些措施能够有效地吸收和减缓设备的振动,保证加工过程的稳定性和质量。
机械加工过程中机械振动的原因及对策分析

机械加工过程中机械振动的原因及对策分析机械加工过程中出现机械振动的原因较多,主要包括以下几个方面:1.切削力的不平衡:机械加工过程中,切削力的大小和方向会不断变化,如果切削力不平衡,就会引发机械振动。
这主要是由于工件材料的异质性、表面瑕疵等原因导致的切削力不均匀分布。
2.进给速度过大:如果在机械加工过程中进给速度过大,刀具与工件之间会发生剧烈的冲击,从而产生振动。
进给速度过大还会引起切屑的断裂不良、刀具严重磨损等问题。
3.机床刚度不足:机床的刚度不足也是引起机械振动的重要原因。
刚度不足会导致机械系统的固有频率过低,与工件切削频率接近,从而引起共振现象。
4.切削液不当:切削液在机械加工过程中起到冷却润滑的作用,如果切削液的流量、温度、质量不合适,则会导致切削液无法有效冷却刀具和工件,增加切削力并引起振动。
针对上述问题,可以采取以下对策来降低机械振动:1.切削力平衡:选择合适的刀具和进给方式,确保切削力均匀分布。
在加工过程中可以采用动态平衡的方法动态调整刀具和工件的重心位置,提高切削力的平衡性。
2.控制进给速度:根据加工材料的性质和切削条件,合理控制进给速度,避免过大的进给速度引起振动。
如果需要加工高硬度材料,可以采用高速切削技术来提高加工效率,减少机械振动。
3.提高机床刚度:加强机床的刚度和稳定性可以有效抑制机械振动。
可以采用增加机床结构重量、增大导轨尺寸、优化机械系统刚度等措施来提高机床刚度。
4.优化切削液:选择合适的切削液,并设置合理的流量、温度和质量控制,确保切削液能够有效冷却刀具和工件,降低切削力。
还可以通过合理的刀具设计、提高工件材料的均匀性、改善切削过程中的冷却条件等方法来减少机械振动的发生,提高加工质量和效率。
对于特殊要求的加工任务,可以采用振动缓冲系统、动态平衡系统等技术手段来抑制机械振动,实现稳定加工。
机械加工过程中的振动和防止方法
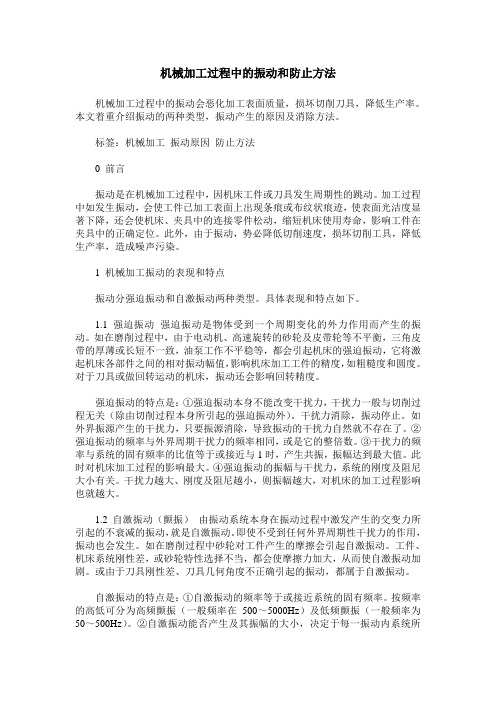
机械加工过程中的振动和防止方法机械加工过程中的振动会恶化加工表面质量,损坏切削刀具,降低生产率。
本文着重介绍振动的两种类型,振动产生的原因及消除方法。
标签:机械加工振动原因防止方法0 前言振动是在机械加工过程中,因机床工件或刀具发生周期性的跳动。
加工过程中如发生振动,会使工件已加工表面上出现条痕或布纹状痕迹,使表面光洁度显著下降,还会使机床、夹具中的连接零件松动,缩短机床使用寿命,影响工件在夹具中的正确定位。
此外,由于振动,势必降低切削速度,损坏切削工具,降低生产率,造成噪声污染。
1 机械加工振动的表现和特点振动分强迫振动和自激振动两种类型。
具体表现和特点如下。
1.1 强迫振动强迫振动是物体受到一个周期变化的外力作用而产生的振动。
如在磨削过程中,由于电动机、高速旋转的砂轮及皮带轮等不平衡,三角皮带的厚薄或长短不一致,油泵工作不平稳等,都会引起机床的强迫振动,它将激起机床各部件之间的相对振动幅值,影响机床加工工件的精度,如粗糙度和圆度。
对于刀具或做回转运动的机床,振动还会影响回转精度。
强迫振动的特点是:①强迫振动本身不能改变干扰力,干扰力一般与切削过程无关(除由切削过程本身所引起的强迫振动外)。
干扰力消除,振动停止。
如外界振源产生的干扰力,只要振源消除,导致振动的干扰力自然就不存在了。
②强迫振动的频率与外界周期干扰力的频率相同,或是它的整倍数。
③干扰力的频率与系统的固有频率的比值等于或接近与1时,产生共振,振幅达到最大值。
此时对机床加工过程的影响最大。
④强迫振动的振幅与干扰力,系统的刚度及阻尼大小有关。
干扰力越大、刚度及阻尼越小,则振幅越大,对机床的加工过程影响也就越大。
1.2 自激振动(颤振)由振动系统本身在振动过程中激发产生的交变力所引起的不衰减的振动,就是自激振动。
即使不受到任何外界周期性干扰力的作用,振动也会发生。
如在磨削过程中砂轮对工件产生的摩擦会引起自激振动。
工件、机床系统刚性差,或砂轮特性选择不当,都会使摩擦力加大,从而使自激振动加剧。
机械加工过程中机械振动的原因及对策分析

机械加工过程中机械振动的原因及对策分析
机械加工过程中的机械振动是指在机床或工件上产生的机械振动现象。
机械振动的原
因可以分为以下几个方面:
1. 刀具与工件的不平衡:刀具与工件的不平衡是引起机械振动的主要原因之一。
刀
具在高速旋转时不平衡会导致振动产生。
3. 刀具与刀架的松动:刀具安装不牢固、刀具松动也会引起机械振动。
刀具松动会
导致刀具与工件之间的相对运动不稳定,从而引起振动。
4. 机床刚度不足:机床刚度不足是引起机械振动的另一常见原因。
机床刚度不足会
导致加工过程中机床产生弯曲变形,使刀具与工件之间的相对位置发生变化,引起振动。
对于机械振动问题,以下是一些常见的对策分析:
1. 动平衡:对刀具、刀架等旋转部件进行动平衡处理,将不平衡量降至最低,减小
机械振动。
2. 调整刀具参数:根据实际情况调整刀具的切削参数,使刀具与工件之间的力平衡,减小机械振动。
3. 固定刀具、刀架:确保刀具、刀架等部件的安装牢固,防止松动引起的振动。
4. 提高机床刚度:通过增加机床的刚度来减小机械振动。
可以通过选用更加稳定的
机床、加强机床的结构设计等方式来提高机床刚度。
5. 使用减振装置:在机床或工件上安装减振装置,减小机械振动。
在机械加工过程中,机械振动是一个常见的问题,会影响加工质量和工作效率。
针对
机械振动问题,可以采取不同的对策,从而减小振动幅度,提高加工精度和稳定性。
机械加工中机械振动的原因解析与应对

机械加工中机械振动的原因解析与应对
机械加工中的机械振动是指在机械加工过程中产生的机械系统的非均匀运动现象。
机械振动的产生原因很多,主要包括以下几个方面:
1.切削力引起的振动:切削力在机床和工件之间传递,当切削力不平衡时,就会引起机床和工件的振动。
2.零件不平衡引起的振动:在机械加工过程中,如果工件本身不平衡,或者夹具装夹不平衡,都会导致机床的振动。
3.切削过程中的共振现象:机械系统有自然振动频率,当切削过程中的振动频率与机械系统的自然频率相近时,就会发生共振现象,从而引起振动。
4.机床刚度不足引起的振动:机床的刚度直接影响着机床的稳定性和阻尼效果,如果机床刚度不足,就会导致振动加剧。
为了应对机械振动,可以采取以下几种措施:
1.提高机械系统的刚度:通过加强机床的结构设计和制造工艺,增加机床的刚度,从而减少机械振动的发生。
2.使用平衡装置:对工件和夹具进行平衡处理,减小零件的不平衡量,从而减少振动。
3.优化切削参数:合理选择切削速度、进给速度和切削深度等切削参数,避免过大或过小的切削力。
4.选用合适的切削工具:选择合适的切削工具,如刀具的刚度、刀具的几何形状等,从而减小切削力和振动。
5.加强润滑和冷却:合理使用润滑剂和冷却剂,保持切削过程中工件和切削工具的表面温度,减少摩擦和热变形,从而减小振动。
机械振动在机械加工中是一个普遍存在的问题,但通过合理的措施可以减少和控制振动,提高机械加工的质量和效率。
- 1、下载文档前请自行甄别文档内容的完整性,平台不提供额外的编辑、内容补充、找答案等附加服务。
- 2、"仅部分预览"的文档,不可在线预览部分如存在完整性等问题,可反馈申请退款(可完整预览的文档不适用该条件!)。
- 3、如文档侵犯您的权益,请联系客服反馈,我们会尽快为您处理(人工客服工作时间:9:00-18:30)。
a)减振镗刀
δ
b)减振镗杆
图4-73 冲击式减振镗刀与减振镗杆
1—冲击块 2—紧定螺钉 郭德伟
11
自激振动的特征
自激振动是一种不衰减振动 自激振动的频率等于或接近于系 统的固有频率
自激振动能否产生及振幅的大小 取决于振动系统在每一个周期内获 得和消耗的能量对比情况。
0
A B C 振幅 郭德伟
4
自激振动系统能量关系
4.6.3 机械加工过程中自激振动
自激振动机理
◆ 再生机理: 切削过程, 由于偶然干扰,使加工系统 产生振动并在加工表面上留 下振纹。第二次走刀时,刀 具将在有振纹的表面上切削 ,使切削厚度发生变化,导 致切削力周期性地变化,产 生自激振动。
振动方向XD f ap B
κr
κ r,
a)切削
fa
b)磨削 郭德伟
8
图4-67 重叠系数
4.6.4 机械加工中振动的防治
减小重叠系数方法 增加主偏角 增大进给量 ◆ 增加切削阻尼(例采用倒棱车刀,图4-78)
-5°~ -20°
0.1~0.3
2°~ 3° 图4-69 车刀消振棱
郭德伟
9
4.6.4 机械加工中振动的防治
1)回转零部件质量的不平衡 2)机床传动件的制造误差和缺陷 3)切削过程中的冲击
强迫振动的特征
频率特征:与干扰力的频率相同,或是干扰力频率整倍数 幅值特征:与干扰力幅值、工艺系统动态特性有关。当干扰力频率接 近或等于工艺系统某一固有频率时,产生共振
相角特征:强迫振动位移的变化在相位上滞后干扰力一个φ角,其值 与系统的动态特性及干扰力频率有关。
郭德伟
6
4.6.4 机械加工中振动的防治
消除或减弱产生强迫振动的条件
减小机内干扰力的幅值 调整振源的频率,一般要求:
fn f 0.25 f
(4-33) x2 1 x1 2 x1 2 β x2 1
式中 f 和 fn 分别为振源频率和 系统固有频率 隔振
图4-76 两种尾座结构
消除或减弱产生自激振动的条件
◆ 调整振动系统小刚度主轴的位置 (图4-76)
郭德伟
7
4.6.4 机械加工中振动的防治
◆ 减小切削或磨削时的重叠系数(图4-67)
bd (切削) b
B fa (磨削) B
(4-34)
式中 bd —— 等效切削宽度,即本次切削实际切到上次切削残留振纹 在垂直于振动方向投影宽度; b —— 本次切削在垂直于振动方向上的切削宽度; B , fa —— 砂轮宽度与轴向进给量。
改善工艺系统动态特性
◆ 提高工艺系统刚度 ◆ 增大工艺系统阻尼
阻尼材料 铸铁环 铸铁套筒
图4-71 零件上加阻尼材料
郭德伟
10
4.6.4 机械加工中振动的防治
采用减振装置
动力减振器 摩擦式减振器(图4-72) 冲击式减振器(图4-73)
δ
图4-72 摩擦式减振器
1—飞轮 2—摩擦盘 3—摩擦 垫 4—螺母 5—弹簧
自由振动
工艺系统受到初始干扰力而破坏了其平衡状态后,系 统仅靠弹性恢复力来维持的振动称为自由振动。 由于系统中总存在由阻尼,自由振动将逐渐衰弱,对 加工影响不大。
郭德伟
2
4.6.2 机械加工过程中强迫振动
强迫振动产生原因
由外界周期性的干扰力(激振力)作用引起
强迫振动振源:机外+机内。机外振源均通过地基把振动传给机床 。机内:
郭德伟
5
4.6.3 机械加工过程中自激振动
◆ 振型耦合机理:将车床 刀架简化为两自由度振动 系统,等效质量 m 用相互 垂直的等效刚度分别为 k1 、 k2 两组弹簧支撑(设 x1 为低刚度主轴,图4-66)
◆ 自激振动的产生: ① k1=k2 ,x1 与 x2 无相位差, 轨迹为直线,无能量输入
图4-66 车床刀架振型耦合模型
② k1>k2,x1超前x2 ,轨迹d→c→b→a为一椭圆,切入半周 期内的平均切削厚度比切出半周期内的大,系统无能量输入
③ k1 < k2 , x1 滞后于 x2 ,轨迹为一顺时针方向椭圆,即: a→b→c→d。此时,切入半周期内的平均切削厚度比切出半 周期内的小,有能量获得,振动能够维持 。
y0 y 切入 切出 φ a) φ y0 y 切入 切出 c) f 切入 切出 d) f y0 y f 切入 切出 b) φ y0 y f
再生自激振动原理图
◆ 产生条件: a)b)c)系统无能量获得;
d)y 滞后于y0,即 0>φ>-π ,此时切出比切入半周期中的平均切削厚 度大,切出时切削力所作正功(获得能量)大于切入时所作负功,系统 有能量获得,产生自激振动
机械制造技术基础
第4章 机械加工质量
Machining Quality
chining Process
郭德伟
1
4.6.1 概述
机械加工过程中振动的危害
影响加工表面粗糙度,振动频率较低时会产生波度 影响生产效率 加速刀具寿命,易引起崩刃 影响机床、夹具的使用寿命 产生噪声污染,危害操作者健康 自由振动 机械加工过程中振动的类型 强迫振动 自激振动
郭德伟
3
4.6.3 机械加工过程中自激振动
自激振动的概念
在没有周期性外力作用下, 由系统内部激发反馈产生的周 期性振动 自激振动过程可用传递函数 概念说明
电动机 (能源) 振动位移 X(t) 机床振动系统 (弹性环节)
调节系统 交变切削力F(t) (切削过程)
自激振动闭环系统
能量E E- Q E+