三基SCH系列卧式挤压铸造机性能参数表
压铸机工艺参数分析

∙压铸工艺参数分析(一)∙∙为了便于分析压铸工艺参数,下面示出如图5-1和图5-2所示的卧式冷室压铸机压射过程图以及压射曲线图。
压射过程按三个阶段进行分析。
第一阶段(图5-1b):由0 -Ⅰ和Ⅰ-Ⅱ两段组成。
0 -Ⅰ段是压射冲头以低速运动,封住浇料口,推动金属液在压射室内平稳上升,使压射室内空气慢慢排出,并防止金属液从浇口溅出;Ⅰ-Ⅱ段是压射冲头以较快的速度运动,使金属液充满压射室前端并堆聚在内浇口前沿。
第二阶段(图5-1c):Ⅱ-Ⅲ段,压射冲头快速运动阶段,使金属液充满整个型腔与浇注系统。
第三阶段(图5-1d):Ⅲ-Ⅳ段,压射冲头终压阶段,压射冲头运动基本停止,速度逐渐降为0。
a)图5-1 卧式冷室压铸机压射过程图图5-2 卧式冷室压铸机压射曲线图s--冲头位移曲线P0--压力曲线v--速度曲线1、压力参数(1)压射力压射冲头在0-Ⅰ段,压射力是为了克服压射室与压射冲头和液压缸与活塞之间的摩擦阻力;Ⅰ-Ⅱ段,压射力上升,产生第一个压力峰,足以能达到突破内浇口阻力为止;Ⅱ-Ⅲ段,压射力继续上升,产生第二个压力峰;Ⅲ-Ⅳ段,压射力作用于正在凝固的金属液上,使之压实,此阶段有增压机构才能实现,此阶段压射力也叫增压压射力。
(2)比压比压可分为压射比压和增压比压。
在压射运动过程中0-Ⅲ段,压射室内金属液单位面积上所受的压射力称为压射比压;在Ⅲ-Ⅳ段,压射室内金属液单位面积上所受的增压压射力称为增压比压。
比压是确保铸件质量的重要参数之一,推荐选用的增压比压如表5-1所示。
表5-1 增压比压选用值(单位:MPa)(3)胀型力压铸过程中,充填型腔的金属液将压射活塞的比压传递至型(模)具型腔壁面上的力称为胀型力。
主胀型力的大小等于铸件在分型面上的投影面积(多腔模则为各腔投影面积之和),浇注系统、溢流、排气系统的面积(一般取总面积的30%)乘以比压,其计算公式如下F主=APb/10式中F主-主胀型力(KN);A-铸件在分型面上的投影面积(cm2);Pb-压射比压(MPa)。
压铸工艺参数分析

压铸工艺参数分析1.注射压力:注射压力是指在铸造过程中,金属熔液被压入型腔的压力大小。
注射压力的大小对于铸件的排气、充盈、凝固过程以及零部件的尺寸稳定性有着重要的影响。
过高的注射压力会导致铸件内部气泡的形成、表面粗糙度增大等问题,而过低的注射压力则会导致型腔内充盈不充分。
2.注射速度:注射速度是指熔融金属进入模具腔体的速度。
适当的注射速度可以使熔融金属在型腔内充盈均匀,防止铸件出现疏松、夹杂等缺陷。
过高的注射速度会导致金属熔液的剪切力增加,容易产生气泡和金属破碎现象,而过低的注射速度则会导致金属熔液在充盈过程中受到阻力,形成冷障。
3.注射温度:注射温度是指金属熔液注入型腔时的温度。
注射温度的高低会直接影响到铸件的凝固形态和组织结构。
过高的注射温度会导致铸件的表面质量较差,因为金属熔液的冷却速度过快,易产生冷障和贝氏体组织。
而过低的注射温度则会导致金属熔液黏度增大,充盈性变差。
4.金属液温度:金属液温度是指金属熔体在注射之前的温度。
金属液温度的高低会直接影响到铸件的凝固过程和性能。
过高的金属液温度会导致铸件的组织粗大,出现热裂纹等问题。
而过低的金属液温度则会导致铸件的毛细孔增多,降低铸件的密实性。
5.压射机的闭模力:压射机的闭模力是指用于关闭型腔的力大小。
闭模力的大小会直接影响到铸件的尺寸稳定性和机械性能。
过高的闭模力会导致铸件的尺寸过大,形成表面凸起和冷障等问题。
而过低的闭模力则会导致铸件尺寸的不稳定性和机械性能的下降。
6.模具温度:模具温度是指模具在铸造过程中的温度。
模具温度的高低会直接影响到铸件的组织结构和表面质量。
适当的模具温度可以提高铸件的表面光洁度,减少气孔和缩松等问题。
过高的模具温度会导致铸件的热组织粗大,而过低的模具温度则会导致铸件充盈性差。
总结起来,压铸工艺参数对于铸件质量和性能有着直接的影响。
合理的控制和选择工艺参数可以有效地改善铸件的表面质量、减少缺陷率,提高铸件的力学性能和尺寸稳定性。
压铸机调试工艺参数

压铸机调试工艺参数1.机器在调节时应注意的事项1)只能调节机器使用说明书上指出的可调参数。
调压时应按使用说明书的要求进行,不准大于规定的压力值,尽量防止调压过高,而致使油温增高或损坏元件。
2)不准在执行元件(液压缸、液压马达)运动状态下调节系统工作压力。
3)调压前应先检查压力表是否损坏,若有异常,待压力表更换后再调节压力。
4)调压前,先把所要调节的调压阀上的调节螺母放松,调压后,应将调节螺钉的紧固螺母拧紧,以免松动。
2.主要工艺参数的调节技能(1)开、合型(模)慢速段的调节开型(模)和合型(模)慢速段的速度统一由慢速油阀左侧的调节螺钉控制。
顺时针旋紧螺钉,则开、合型(模)慢速段速度减慢,逆时针旋松螺钉,则开、合型(模)慢速速度加快。
调节合适后,将固定螺母拧紧,如图1所示图1开、合型(模)慢速段的调节(2)开、合型(模)常速(即快速)段的调节1)开型(模)常速段速度由开、合型(模)换向阀右侧的调节螺钉控制。
顺时针旋紧螺钉,则速度减慢,逆时针旋松螺钉,则速度加快。
调节合适后,将固定螺母拧紧,如图2所示。
图2开型(模)常速(即快速)段的调节2)合型(模)常速段速度由开、合型(模)换向阀左侧的调节螺钉控制。
顺时针旋紧调节螺钉,则合型常速段速度减慢,逆时针旋松调节螺钉,则合型常速段速度加快。
调节合适后,将固定螺母拧紧,如图3所示。
图3合型(模)常速(即快速)段的调节(3)低压大流量泵压力的调节起动机器作自动循环运动,用手旋转双泵流量控制阀上的调节螺钉,可调节低压压力到一定值(一般5×106Pa(50bar)左右),低压压力值从低压压力指示表上读出。
调节合适后,将固定螺母拧紧,如图4所示。
图4低压大流量泵压力的调节(4)射料二速工作压力的调节射料二速工作压力由控制二速压力的调节螺钉调节,用手旋转减压阀上的调节螺钉可调节压力大小,其压力示值从射料二速压力表中读出,此压力即为二速射料运动中的射料压力。
上海三基冷室压铸机主要技术参数表
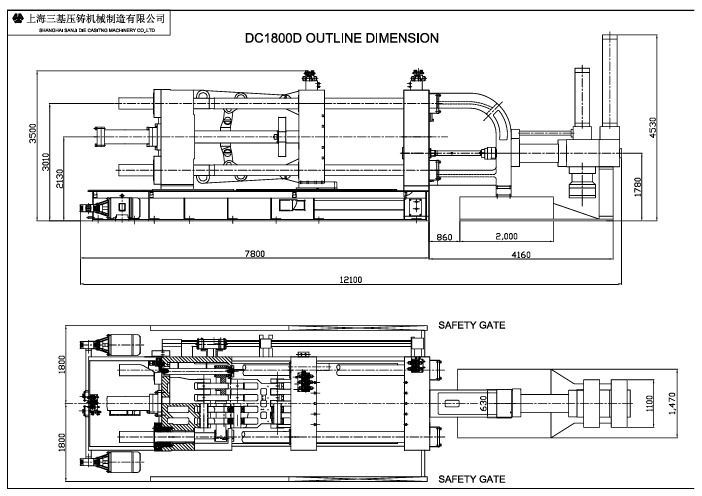
上海三基冷室压铸机主要技术参数表SANJI COLD CHAMBERDIE-CASTING MACHINE SPECIFICATIONS项目 ITEMS单位 UNIT DC-1800C锁模部分 CLAMPING UNIT锁模力CLAMPING FORCE KN18000模板尺寸Platen Size mm2060x2260哥林柱间隔Space between Tie Bar mm1300X1500(WxH)哥林柱直径Tie Bar Diameter mm250锁模行程Die Stoke mm1000模板厚薄距离Die Height mm700-1600射料部分 INJECTION UNIT射料力Injection Force KN530-1250跟踪距离Plunger Tip Penetration mm450射料位置Shot Position mm-350压射头直径Standard Tip Diametre mm110,130,150射料重量(铝)Casting Weight Kg29铸造压力Injection Pressure Mpa56-126最大铸造面积Injection Area(400MPa)cm24,500顶出部分 EJECTION UNIT顶出压力Ejection Force KN500顶出行程Ejection Stroke mm200油泵与电机 Pump and Motor液压泵Hydraulic Pump 2-Vame Pump (045-028) (60bar,140bar)电机Electric Motor:1.液压泵电机For Hydraulic Pump 2-37kw 380V2.调模电机For Die Height Adjust USE Hydralic Motor 用液压马达3.润滑电机For Lub.Pump2-30w 220V其它 OTHERS油箱容积Tank Capacity litre2000机身尺寸Overall dimensions(L x W x H)m12 X 3 .7X 4.6出机重量Height of Machine TON99PDF 文件使用 "pdfFactory Pro" 试用版本创建。
三基-挤压铸造技术介绍

三基-挤压铸造技术介绍
嘿,朋友们!今天咱来聊聊三基-挤压铸造技术。
这玩意儿可厉害啦!
你想想看,就好像我们做蛋糕一样,要把各种材料完美地融合在一起,挤压铸造技术也是这么个道理。
它能把金属材料像变魔术一样变成我们想要的形状和性能。
这技术啊,就像是一个超级厉害的工匠,能把金属材料雕琢得特别精细。
它可以让铸件的组织更加致密,强度那是蹭蹭往上涨啊!而且啊,它还能减少气孔、缩松这些让人头疼的缺陷呢。
说起来,以前没有这技术的时候,我们制造一些复杂形状的金属零件可麻烦了,不是这儿有问题就是那儿不行。
但有了三基-挤压铸造技术后,哇塞,一切都变得不一样啦!它能让那些形状复杂的零件轻松地被制造出来,而且质量还特别好,这不是太棒了吗?
你再想想,如果把金属材料比作是一堆积木,那挤压铸造技术就是那个能把积木搭出各种奇妙造型的人。
它能让这些积木紧密地结合在一起,变得无比坚固。
这技术在很多领域都大显身手呢!比如汽车制造,那些高质量的零部件可少不了它的功劳。
还有航空航天领域,对零件的要求那么高,三基-挤压铸造技术就能很好地满足需求呀。
而且哦,它还特别节能环保呢!比起其他一些制造方法,它能节省不少材料和能源,这对我们的地球妈妈来说可是个大好事呀!
你说,这么好的技术,我们能不重视它吗?我们得好好研究它,让它发挥更大的作用呀!我们的生活中有那么多需要高质量金属零件的地方,三基-挤压铸造技术就是那个能帮我们实现的魔法呀!
所以啊,大家可别小瞧了这三基-挤压铸造技术,它可是我们现代工业的宝贝呢!让我们一起为它点赞,一起期待它能给我们带来更多的惊喜吧!。
标准铝压铸工艺参数表

标准铝压铸工艺参数表1. 压铸温度。
铝合金的压铸温度是影响产品质量的重要参数之一。
通常情况下,铝合金的压铸温度在650°C至750°C之间。
过高的温度会导致产品熔融不均匀,而过低的温度则会造成产品表面粗糙。
因此,在实际生产中,需要根据具体的铝合金材料选择合适的压铸温度。
2. 压射速度。
压射速度是指铝合金液态金属进入模腔的速度。
适当的压射速度可以确保产品充填充分,避免气孔和夹杂物的产生。
一般来说,压射速度应根据产品的形状和尺寸进行调整,以保证产品的成型质量。
3. 模具温度。
模具温度对铝合金压铸产品的表面质量和尺寸精度有着重要影响。
过高或过低的模具温度都会导致产品的缺陷,因此需要根据具体的铝合金材料和产品要求来确定合适的模具温度。
4. 注射压力。
注射压力是指压铸机对铝合金液态金属施加的压力。
适当的注射压力可以确保产品充填充分,避免产品内部产生气孔和夹杂物。
在实际生产中,需要根据产品的形状和尺寸来确定合适的注射压力。
5. 冷却时间。
冷却时间是指产品在模具中冷却的时间。
适当的冷却时间可以确保产品的尺寸精度和表面质量。
通常情况下,冷却时间需要根据产品的厚度和材料来确定,以确保产品达到理想的硬度和强度。
6. 顶杆力。
顶杆力是指顶出铝合金产品的力量。
适当的顶杆力可以确保产品顺利脱模,避免产品变形和损坏。
在实际生产中,需要根据产品的形状和尺寸来确定合适的顶杆力。
7. 模具开合力。
模具开合力是指模具在开合过程中所受的力量。
适当的模具开合力可以确保模具的正常运行,避免模具损坏和产品缺陷。
在实际生产中,需要根据模具的结构和尺寸来确定合适的模具开合力。
总结:以上是标准铝压铸工艺参数表的相关内容,希望能对大家在铝合金压铸加工过程中有所帮助。
在实际生产中,需要根据具体的产品要求和铝合金材料来确定合适的工艺参数,以确保产品质量和生产效率。
同时,也需要不断优化和调整工艺参数,以适应市场和客户需求的变化。
希望大家能够加强学习和实践,不断提升铝合金压铸加工的技术水平和质量管理水平。
压铸工艺参数(二)
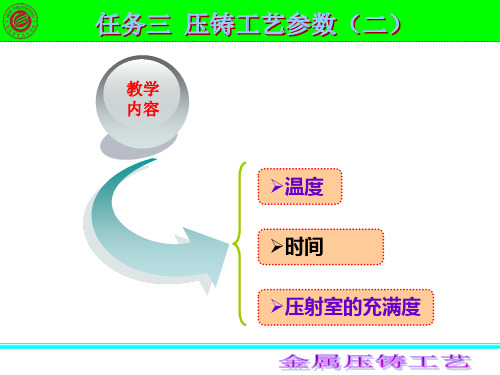
三、压射室的充满度
浇入压射室的金属液量占压射室总容量的程度称为压射室的充满度,通常 以百分数表示。
充满度对于卧式冷压室压铸机有着特殊 的意义。因为卧式压铸机的压射室在浇入金 属液后,并不是完全充满,而是在金属液面 上方留有一定的空间。 这个空间所占的体积越大,存有空气越 多,对于填充型腔时的气体量的影响越大。 其次,充满度小,合金液在压射室内的激冷 度过多,对填充也不利。因此,压射室充满 度不应过小,以免上部空间过大,一般充满 度应在40%~80%范围内,而以75%左右最 为适宜。
1 2 mv n mcT s 2 2 vn Ts 2c
式中 m——运动中的合金质量,kg; vn——内浇口速度,m/s; c ——合金的比热容,J/kg· ℃; Ts——因摩擦加热后升高的温度,℃。
上述公式计算得出内浇口速度与温升的关系见图3-17。
图3-17 内浇口速度与合金温升的关系
当内浇口速度为80m/s时,镁合金液进入型腔时的温度将增加25℃。 而内浇口速度越大,则温度增加得越多,这对准确地控制浇注温度有一 定的意义。
④避免模具因激热而胀裂;
⑤缩小模具工作时冷热交变的温度差,延长模具寿命。
(1) 影响模具温度的主要因素 1) 合金浇注温度、浇注量、热容量和导热性。 2) 浇注系统和溢流槽的设计,用以调整平衡状态。 3) 压铸比压和压射速度。 4) 模具设计。模具体积大,则热容量大,模具温度波动较小。模具 材料导热性越好,则温度分布就越均匀,有利于改善热平衡。 5) 模具合理预热提高初温,有利于改善热平衡,可提高模具寿命。 6) 生产频率快,模具温度升高,这在一定范围内对铸件和模具寿命 都是有利的。 7) 模具润滑起到隔热和散热的作用。
如果压力升高时间过短,金属尚未完全凝固,增压压力早已建成并作 用于其上,则将增大胀型力,从而引起胀型力超过允许值,发生机器锁模 力不足的现象。 因此,机器压射系统的增压装置上,压力升高时间的可调性十分重要。 其调整范围在0.015~0.3s内比较适宜。
压铸取件机特点与技术参数
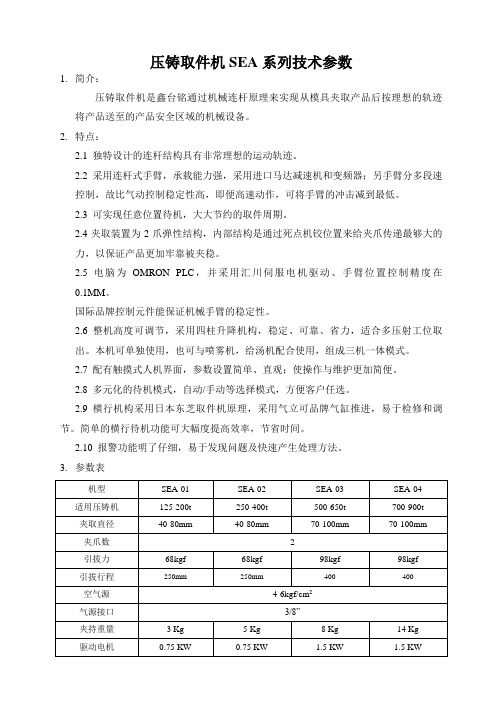
压铸取件机SEA系列技术参数
1.简介:
压铸取件机是鑫台铭通过机械连杆原理来实现从模具夹取产品后按理想的轨迹将产品送至的产品安全区域的机械设备。
2.特点:
2.1 独特设计的连杆结构具有非常理想的运动轨迹。
2.2采用连杆式手臂,承载能力强,采用进口马达减速机和变频器;另手臂分多段速
控制,故比气动控制稳定性高,即便高速动作,可将手臂的冲击减到最低。
2.3 可实现任意位置待机,大大节约的取件周期。
2.4夹取装置为2爪弹性结构,内部结构是通过死点机铰位置来给夹爪传递最够大的
力,以保证产品更加牢靠被夹稳。
2.5 电脑为OMRON PLC,并采用汇川伺服电机驱动、手臂位置控制精度在
0.1MM。
国际品牌控制元件能保证机械手臂的稳定性。
2.6 整机高度可调节,采用四柱升降机构,稳定、可靠、省力,适合多压射工位取
出。
本机可单独使用,也可与喷雾机,给汤机配合使用,组成三机一体模式。
2.7 配有触摸式人机界面,参数设置简单、直观;使操作与维护更加简便。
2.8 多元化的待机模式,自动/手动等选择模式,方便客户任选。
2.9 横行机构采用日本东芝取件机原理,采用气立可品牌气缸推进,易于检修和调节。
简单的横行待机功能可大幅度提高效率,节省时间。
2.10 报警功能明了仔细,易于发现问题及快速产生处理方法。
3.参数表
4:取件机图片夹手图片。
压铸机基本参数教案(精)
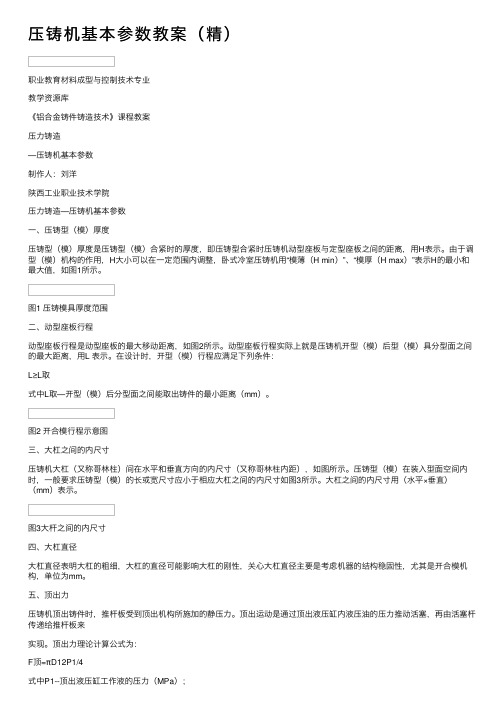
压铸机基本参数教案(精)职业教育材料成型与控制技术专业教学资源库《铝合⾦铸件铸造技术》课程教案压⼒铸造—压铸机基本参数制作⼈:刘洋陕西⼯业职业技术学院压⼒铸造—压铸机基本参数⼀、压铸型(模)厚度压铸型(模)厚度是压铸型(模)合紧时的厚度,即压铸型合紧时压铸机动型座板与定型座板之间的距离,⽤H表⽰。
由于调型(模)机构的作⽤,H⼤⼩可以在⼀定范围内调整,卧式冷室压铸机⽤“模薄(H min)”、“模厚(H max)”表⽰H的最⼩和最⼤值,如图1所⽰。
图1 压铸模具厚度范围⼆、动型座板⾏程动型座板⾏程是动型座板的最⼤移动距离,如图2所⽰。
动型座板⾏程实际上就是压铸机开型(模)后型(模)具分型⾯之间的最⼤距离,⽤L 表⽰。
在设计时,开型(模)⾏程应满⾜下列条件:L≥L取式中L取—开型(模)后分型⾯之间能取出铸件的最⼩距离(mm)。
图2 开合模⾏程⽰意图三、⼤杠之间的内尺⼨压铸机⼤杠(⼜称哥林柱)间在⽔平和垂直⽅向的内尺⼨(⼜称哥林柱内距),如图所⽰。
压铸型(模)在装⼊型⾯空间内时,⼀般要求压铸型(模)的长或宽尺⼨应⼩于相应⼤杠之间的内尺⼨如图3所⽰。
⼤杠之间的内尺⼨⽤(⽔平×垂直)(mm)表⽰。
图3⼤杆之间的内尺⼨四、⼤杠直径⼤杠直径表明⼤杠的粗细,⼤杠的直径可能影响⼤杠的刚性,关⼼⼤杠直径主要是考虑机器的结构稳固性,尤其是开合模机构,单位为mm。
五、顶出⼒压铸机顶出铸件时,推杆板受到顶出机构所施加的静压⼒。
顶出运动是通过顶出液压缸内液压油的压⼒推动活塞,再由活塞杆传递给推杆板来实现。
顶出⼒理论计算公式为:F顶=πD12P1/4式中P1--顶出液压缸⼯作液的压⼒(MPa);D1--顶出液压缸内径(mm);F顶--顶出⼒(N)。
六、顶出⾏程顶出⾏程是顶出机构可以将压铸件顶出的最⼤距离。
液压顶出时与顶出液压缸本⾝⾏程有关,机械式顶出与后推杆长度有关。
顶出机构应该保证将压铸件从型腔中顶出⼀定距离,使其与压铸模具脱离,⽅便取出,⽤S 表⽰,单位为mm。
36MN“短行程”单动卧式铝挤压机
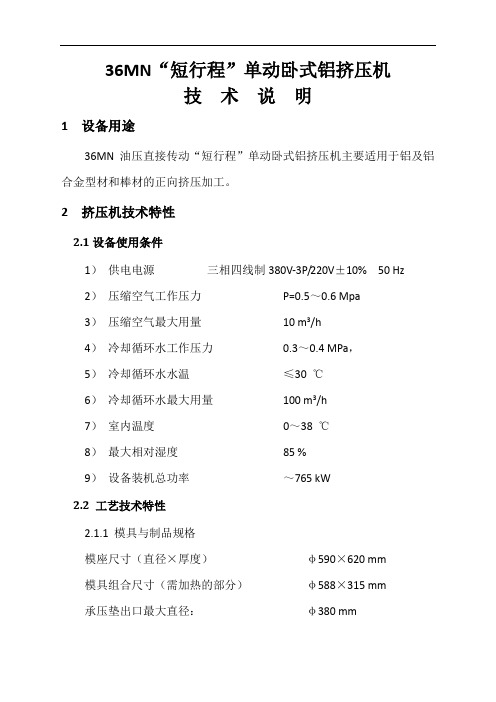
36MN“短行程”单动卧式铝挤压机技术说明1 设备用途36MN油压直接传动“短行程”单动卧式铝挤压机主要适用于铝及铝合金型材和棒材的正向挤压加工。
2 挤压机技术特性2.1设备使用条件1)供电电源三相四线制380V-3P/220V±10% 50 Hz2)压缩空气工作压力P=0.5~0.6 Mpa3)压缩空气最大用量10 m3/h4)冷却循环水工作压力0.3~0.4 MPa,5)冷却循环水水温≤30 ℃6)冷却循环水最大用量100 m3/h7)室内温度0~38 ℃8)最大相对湿度85 %9)设备装机总功率~765 kW2.2 工艺技术特性2.1.1 模具与制品规格模座尺寸(直径×厚度)φ590×620 mm模具组合尺寸(需加热的部分)φ588×315 mm承压垫出口最大直径:φ380 mm承压垫出口允许型材制品最大截面尺寸:150×400;80×470 mm 2.1.2 坯锭规格园坯锭直径/长度(最大)φ310/1250 mm扁坯锭尺寸/长度(最大)170X390/1250 m2.3 主要技术参数总挤压力36 MN主工作缸力31.5 MN侧缸力 4.5 MN回程力 2.3 MN挤压筒锁紧力(可调整) 3 MN挤压筒松开力 2.3 MN主剪剪力 1.7 MN模内剪力0.8 MN主柱塞(挤压杆)行程1900 mm挤压筒行程(最大1650mm)1900 mm主剪行程1120 mm模内剪行程400 mm移动模架行程1850 mm快换模行程750 mm挤压工作速度(闭环控制可调) 0.2-18 mm/s主柱塞空程前进速度300 mm/s主柱塞回程速度300 mm/s挤压筒闭合速度300 mm/s挤压筒松开速度300 mm/s主剪空程/剪切速度270/200 mm/s模架移动速度200 mm/s挤压筒加热温度≤450 ℃(可调)挤压筒规格挤压筒内径/长度园φ320/1350 mm 挤压筒内径/长度扁180X400/1350 mm 挤压筒加热功率65 kW主系统工作介质压力28 MPa控制系统工作介质压力16 MPa辅助系统工作介质压力12 Mpa3 挤压机技术说明36MN单动卧式(短行程)铝挤压机由挤压机本体、液压传动与控制系统、机械化设备、挤压机自动检测与控制装置和电气控制系统等组成。
铸造工艺设计参数

如何判断铸件的变形方向? 铸件冷却缓慢的一侧必定受拉应力而产生内凹变形 冷却较快的一侧必定受压应力而发生外凸变型
例如 各种床身导轨处都较厚大,因此轨面总是产生下凹变形
再如下图所示箱体,壁厚虽均匀,但内部冷却慢,外部冷却 快,因此壁发生向外凸出变形,模样反变形量应向内侧凸起
>1~4
- 3 4 5 6 8 10 12 14 16 18 20 24 - - -
>4~10
- 2 3 4 5 6 8 10 12 14 16 18 20 24 - -
>10~40
- - 2 3 4 5 6 8 10 12 14 16 18 20 24 -
>40~100
- - - 2 3 4 5 6 8 10 12 14 16 18 20 24
加工余量和尺寸公差的关系 最小加工量等于加工余量减去铸件尺寸的下偏差
影响加工余量的主要因素有:
铸造合金种类 铸造工艺方法 生产批量 设备及工装的水平
加工表面所处的浇注位置(顶、 底、侧面)
铸件基本尺寸的大小 和结构
选取加工余量图例
四、铸造收缩率
铸造收缩率K的定义是
K = L M - L J ×100 %
严格工艺过程的管理 提高操作水平
铸件基本尺寸即铸件图上给定的尺寸,应包括机械加工余量。
公差带应对称分布,有特殊要求时,也可非对称分布, 并应在图样上注明或技术文件中规定。
壁厚尺寸公差一般可降低一级
例如:图样上一般尺寸公差为CT10级,则壁厚尺寸公差为CT11级。在图样 上采用公差等级代号标注,如GB6414-86CT10
2、铸件的基本尺寸小于或等于16mm时,CT13至CT16的公差值需单独标注,可提高2~3级
压铸机主要技术参数.ppt
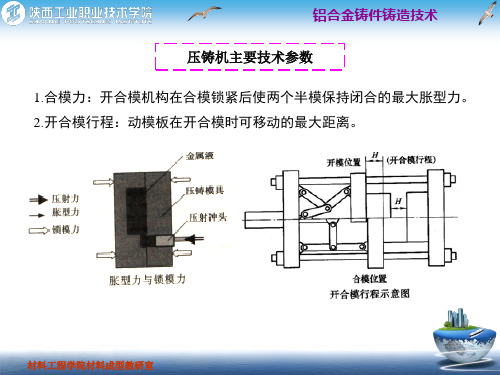
铝合金铸件铸造技术 7.大杠间距:压铸机的四根大杠在水平和垂直方向的距离。一般压铸机 水平和垂直方向的距离相等。 8.大杠直径:大杠的粗细,影响大杠的刚性。 9.压射位置:压室在定模板上所处的高度位置,一般由定模板中心位置 及向下可调造技术
10.压射行程:压射冲头从起始到终点位置经过的距离。 11.压射冲头推出距离:压射冲头跟踪推出的距离,其值等于推出终止时, 压射冲头端面至定模板工作面之间的距离。 12.压室/压射冲头直径:压室的内径或压射冲头的外径。 13.动态压射力:压射系统在压射充型阶段中能够形成的压射力。 14.增压压射力:冷室压铸机都设有增压液压缸,以便在金属液凝固期间 实现增压压实。 15.系统压力:液压系统中常态压力,一般是由液压泵输出压力确定。 16.蓄能器压力:蓄能器中氮气压力一般为系统压力的80%,保证系统中 的液压油压入其中。
材料工程学院材料成型教研室
铝合金铸件铸造技术
材料工程学院材料成型教研室
铝合金铸件铸造技术
材料工程学院材料成型教研室
铝合金铸件铸造技术
材料工程学院材料成型教研室
材料工程学院材料成型教研室
铝合金铸件铸造技术
17.最大压射速度:压射系统的极限速度,也称空压射速度。 18.建压时间:充型结束至增压压力形成所需的时间。 19.压室容积:压射冲头处于原始位置时压室内的空间体积,或可容纳金 属液的体积。 20.最大投影面积:压铸件在开合模方向上的投影所形成的面积上限。 21.压力峰值系数:表示压力峰值大小的参数,其值等于峰值压力与有效 压力之比。
铝合金铸件铸造技术 压铸机主要技术参数 1.合模力:开合模机构在合模锁紧后使两个半模保持闭合的最大胀型力。 2.开合模行程:动模板在开合模时可移动的最大距离。
压铸工艺参数的设定和调节
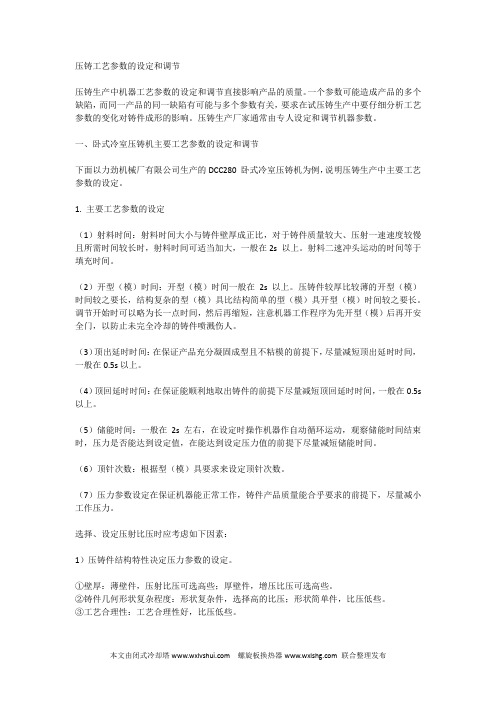
压铸工艺参数的设定和调节压铸生产中机器工艺参数的设定和调节直接影响产品的质量。
一个参数可能造成产品的多个缺陷,而同一产品的同一缺陷有可能与多个参数有关,要求在试压铸生产中要仔细分析工艺参数的变化对铸件成形的影响。
压铸生产厂家通常由专人设定和调节机器参数。
一、卧式冷室压铸机主要工艺参数的设定和调节下面以力劲机械厂有限公司生产的DCC280 卧式冷室压铸机为例,说明压铸生产中主要工艺参数的设定。
1. 主要工艺参数的设定(1)射料时间:射料时间大小与铸件壁厚成正比,对于铸件质量较大、压射一速速度较慢且所需时间较长时,射料时间可适当加大,一般在2s 以上。
射料二速冲头运动的时间等于填充时间。
(2)开型(模)时间:开型(模)时间一般在2s 以上。
压铸件较厚比较薄的开型(模)时间较之要长,结构复杂的型(模)具比结构简单的型(模)具开型(模)时间较之要长。
调节开始时可以略为长一点时间,然后再缩短,注意机器工作程序为先开型(模)后再开安全门,以防止未完全冷却的铸件喷溅伤人。
(3)顶出延时时间:在保证产品充分凝固成型且不粘模的前提下,尽量减短顶出延时时间,一般在0.5s以上。
(4)顶回延时时间:在保证能顺利地取出铸件的前提下尽量减短顶回延时时间,一般在0.5s 以上。
(5)储能时间:一般在2s 左右,在设定时操作机器作自动循环运动,观察储能时间结束时,压力是否能达到设定值,在能达到设定压力值的前提下尽量减短储能时间。
(6)顶针次数:根据型(模)具要求来设定顶针次数。
(7)压力参数设定在保证机器能正常工作,铸件产品质量能合乎要求的前提下,尽量减小工作压力。
选择、设定压射比压时应考虑如下因素:1)压铸件结构特性决定压力参数的设定。
①壁厚:薄壁件,压射比压可选高些;厚壁件,增压比压可选高些。
②铸件几何形状复杂程度:形状复杂件,选择高的比压;形状简单件,比压低些。
③工艺合理性:工艺合理性好,比压低些。
2)压铸合金的特性决定压力参数的设定①结晶温度范围:结晶温度范围大,选择高比压;结晶温度范围小,比压低些。
挤压机主要技术参数确定
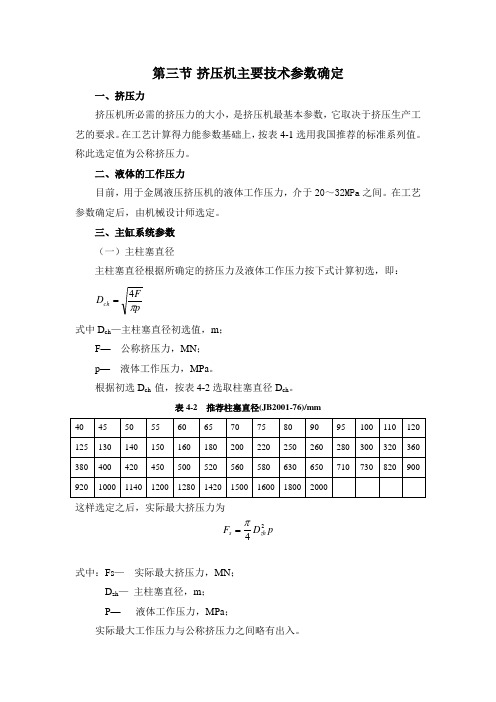
第三节 挤压机主要技术参数确定一、挤压力挤压机所必需的挤压力的大小,是挤压机最基本参数,它取决于挤压生产工艺的要求。
在工艺计算得力能参数基础上,按表4-1选用我国推荐的标准系列值。
称此选定值为公称挤压力。
二、液体的工作压力目前,用于金属液压挤压机的液体工作压力,介于20~32MPa 之间。
在工艺参数确定后,由机械设计师选定。
三、主缸系统参数 (一)主柱塞直径主柱塞直径根据所确定的挤压力及液体工作压力按下式计算初选,即:pFD ch π4=式中D ch —主柱塞直径初选值,m ;F — 公称挤压力,MN ; p — 液体工作压力,MPa 。
根据初选D ch 值,按表4-2选取柱塞直径D ch 。
表4-2 推荐柱塞直径(JB2001-76)/mm这样选定之后,实际最大挤压力为p D F zh s 24π=式中:Fs — 实际最大挤压力,MN ; D zh — 主柱塞直径,m ;P —液体工作压力,MPa ;实际最大工作压力与公称挤压力之间略有出入。
(二)主柱塞行程主柱塞行程取决于挤压机装入锭坯的方式,主柱塞行程有长行程和短行程之分。
行程长短与装锭方式的关系如图4-2所示。
当锭坯在挤压筒和挤压轴之间装入时,主柱塞行程至少要大于挤压筒长度、锭坯长度、锭片厚度三者之和。
称为长行程,其值按下式选取,即:t zh L S )3.22.2(-=式中:S zh —主柱塞行程,mm Lt — 挤压筒长度,mm短行程挤压机分两种情况,锭坯在挤压筒(可移动)和模座间装入;挤压筒可移出挤压中心线外装入锭坯。
此时主柱塞行程为短行程,一般取为t zh L S )3.12.1(-=(三)主柱塞回程力主柱塞回程力F h ,一般按经验公式确定,即 F h =(0.05~0.08)F 式中 F h —主柱塞回程力,MN ;F — 公称挤压力,MN 。
对于小型挤压机,系数取上限值,否则反之。
(四)快速前进力对于泵-蓄势器传动的挤压机,主柱塞空程前进是靠低压罐中的液体(0.8~1.2MPa )推动,不存在快速前进力。