典型橡胶制品配方实例
氟橡胶的配方设计(附30例配方)

氟橡胶的配方设计(附30例配方)一、氟橡胶的主要性能物理性能 :氟橡胶具有较好的力学性能, 有较好的拉伸强度和硬度 , 但常态下的弹性较差。
耐热性: 氟橡胶有很好的耐热性 , 26型氟橡胶可在 250 下长期工作 ,在 300 可短期工作。
氟橡胶性能随温度的变化大于硅橡胶 , 其拉伸强度和硬度均随温度升高而明显下降 , 至250~ 260 时, 下降趋势减缓。
耐腐蚀性能 :氟橡胶有很高的化学稳定性, 是所有弹性体中最耐介质的一种 ; 它对有机液体各种烃类有良好的抗耐性 , 仅仅不耐低分子的酯、醚、酮及部分胺类化合物。
耐过热水、蒸汽的性能 : 过氧化物硫化的氟胶优于胺类、酚类化合物硫化的氟橡胶。
抗压缩变形性能 : 据统计 , 50% 以上的氟橡胶用于密封制品 , 压缩变形是一个主要性能。
美国杜邦公司一直致力于改进压缩变形性能。
耐寒性能 : 26 型氟橡胶的耐寒性能较差, 其保持弹性的极限温度为 - 15~ - 20℃。
美国杜邦公司开发的 Viton GLT, 其低温性能得到很好的改进 , 可适用于 - 54 ℃下的密封 ,是阿拉斯加油田用的低温密封材料。
特定的超低温下的密封 , 有时也用氟橡胶。
气透性与真空性能 : 氟橡胶有很低的透气性 , 在高温、高真空条件下 , 具有极小的气体挥发量 (失重 ) , 因此 , 它的耐高真空性能特别好。
耐侯、耐臭氧性能 : 氟橡胶对日光、臭氧和天候老化十分稳定。
硫化胶经过 10 年的自然老化 , 还保持很好的性能。
耐燃性能 :氟橡胶与火接触能燃烧 , 但离开火后即熄灭 , 它属于自熄橡胶。
氟橡胶的氧指数为 61~ 64。
二、氟橡胶配方, 一般是由生胶、吸酸剂、硫化剂、促进剂、补强填充剂、加工助剂等组成。
1、生胶国产氟橡胶和国外的氟橡胶的性能基本相同, 只是加工性能有些差异 , 国产胶的加工性能较差 , 主要是门尼粘度较高 , 相应影响胶料的加工流动性。
国产氟橡胶 26 相当于美国杜邦公司的VitonA , 氟橡胶 246 相当于VitonB , 国外的氟橡胶生胶中有不少已添加了硫化剂 , 美国 3M公司和日本大金公司供应的氟橡胶已经含有硫化剂。
橡胶配方大全范文

橡胶配方大全范文1.天然橡胶配方:-天然橡胶:100份-硫磺:2份-罗塞林:5份-碳黑:50份-橡胶软化剂:5份-稳定剂:1份2.丁苯橡胶配方:-丁苯橡胶:100份-碳黑:40份-硫磺:2份-弹性体:5份-稳定剂:1份-硬质填料:10份3.丁羟橡胶配方:-丁羟橡胶:100份-碳黑:40份-硫磺:2份-粘度调节剂:5份-稳定剂:1份4.乙酸乙烯橡胶配方:-乙酸乙烯橡胶:100份-碳黑:50份-硫磺:2份-塑化剂:5份-硬质填料:10份-稳定剂:1份5.氯丁橡胶配方:-氯丁橡胶:100份-碳黑:40份-硫磺:2份-塑化剂:5份-稳定剂:1份-硬质填料:10份6.氟橡胶配方:-氟橡胶:100份-硫磺:2份-塑化剂:5份-硬质填料:10份-稳定剂:1份以上是几种常见的橡胶配方,其中的各种原料按比例混合,然后进行橡胶化反应。
这些配方可以根据具体的应用要求进行调整和改善,以满足不同领域对橡胶材料性能的需求。
在混合橡胶配方时需要注意以下几点:1.原料的质量:保证配方中的各种原料质量良好,以确保橡胶制品的性能。
2.混合均匀:混合原料时需要确保均匀混合,以避免出现局部性能差异。
3.适当调整配方:根据具体应用要求,可以适当调整配方中各种原料的比例,以获得更优异的性能。
4.工艺条件控制:橡胶化反应需要在一定的工艺条件下进行,如温度、时间等,需要严格控制这些条件,以保证反应的成功。
通过合理的配方设计和优化,可以制备出满足不同应用领域需求的橡胶制品,提供更好的性能和可靠性。
以上仅是几种常见的橡胶配方,实际应用中还需根据具体的要求进行细化和改进。
希望以上内容能对您有所帮助。
橡胶配方资料大全(doc 25页)

合计161 100.00 100.00 80.5 天然橡胶(NR)基础配方原材料名称NBC标准试样编号质量份原材料名称NBC标准试样编号质量份NR 氧化锌硬脂酸—37037210052防老剂PBN促进剂DM硫磺377373371112.5注:硫化时间为140℃×10min,20min,40min,80min。
NBS为美国国家标准局编写丁苯橡胶(SBR)基础配方原材料名称NBC标准试样编号非充油SBR配方充油SBR配方充油量25phr充油量37.5phr充油量50phr充油量62.5phr充油量75phr非充油SBR 充油SBR氧化锌硬脂酸硫磺炉法炭黑促进剂NS ——370372371378384100—311.75501—1253.751.252.1962.501.25—137.54.121.382.4268.751.38—1504.51.52.63751.5—162.54.881.632.8581.251.63—1755.251.753.0687.51.75Phr指每百质量份橡胶的分量数注:硫化时间为145℃×25min,35min,50min 氯丁橡胶(CR)基础配方原材料名称NBC标准试样编号纯胶配方半补强炉黑(SRF)配方CR(W型) 氧化镁硬脂酸SRF氧化锌—37637238237010040.5—510041295促进剂NA-22 防老剂D —3770.3520.52注:硫化时间为150℃×15min,30min,60min 丁基橡胶(IIR)基础配方原材料名称NBC标准试样编号纯胶配方槽黑配方高耐磨炭黑(HAF)配方IIR氧化锌硫磺硬脂酸促进剂DM 促进剂TMTD 槽发炭黑HAF —37037137237337437537810052——1——1005230.5150—10031.751—1—50注:硫化时间为150℃×20min,40min,80min;150℃×25min,50min,100min丁腈橡胶(NBR)基础配方原材料名称NBC标准试样编号瓦斯炭黑配方NBR氧化锌硬脂酸硫磺促进剂DM 瓦斯炭黑—370372371373382100511.5140注:硫化时间为150℃×10min,20min,80min顺丁橡胶(BR)基础配方原材料名称NBC标准试样编号HAF配方BR氧化锌硫磺硬脂酸促进剂NS —37037137238410031.520.9HAF ASTM型103油378—6015注:硫化时间为145℃×25min,35min,50min异戊橡胶(IR)基础配方原材料名称NBC标准试样编号HAF配方IR氧化锌硫磺硬脂酸促进剂NSHAF —37037137238437810052.2520.735注:硫化时间为15℃×20min,30min,40min,60min。
常用橡胶制品参考配方_美国橡胶协会

4.12 Manufacture of Rubber Products4.12.1 General Process Description1Many of the rubber manufacturing facilities in the United States produce pneumatic tires for automobile, trucks, airplanes and farm machinery. However, many rubber manufacturing facilities produce other engineered rubber products. The processes involved in these industries are very similar. Differences basically consist of the raw rubber material (natural or synthetic) used, the chemical additives, and the type of curing employed. The following is a description of a generic rubber manufacturing facility applicable to both tire and other manufactured rubber products, except where noted.The manufacturing of rubber products involves six principal processing steps (mixing, milling, extrusion, calendering, curing, and grinding), with ancillary steps in between. Initially, the raw rubber (natural or synthetic) is mixed with several additives which are chosen based upon the desired properties of the final product. The mixed rubber is often milled and transferred to an extruder where it can be combined with other rubbers. Many rubber products contain synthetic fabric or fibers for strengthening purposes. These fibers are typically coated with mixed rubber using a calender. The extruded rubber and rubber coated materials are then assembled into a final shape and cured. Among the steps in the tire assembly process, described in more detail below, are bead building; cementing and marking; cutting and cooling; tire building; and green tire spraying. It is during the curing process that the rubber vulcanizes (crosslinks), producing the characteristic properties of finished rubber. Once the final product is cured, it is often ground to remove rough surfaces and/or to achieve symmetry.Mixing consists of taking the raw rubber and mixing it with several chemical additives. These additives consist of accelerators (to initiate the vulcanization process), zinc oxides (to assist in accelerating vulcanization), retarders (to prevent premature vulcanization), antioxidants (to prevents aging), softeners (to facilitate processing of the rubber), carbon black or other fillers (to serve as reinforcing / strengthening agents), and inorganic or organic sulfur compounds (to serve as vulcanizing agents).Mixing typically is performed in an internal batch mixer. The internal mixer contains two rotors which shear the rubber mix against the wall of the vessel. Internal mixing is performed at elevated temperatures up to approximately 330o F.Once mixed, the rubber is discharged from the mixer and processed into slab rubber or pellets. Rubber mixing typically occurs in two or more stages wherein the rubber is returned to the mixer and re-mixed with additional chemicals. The initial stage results in non-productive compounds, and the final stage results in productive compounds. It should also be noted that various rubber compounds produced at a particular facility can be exported to other facilities for use there.Non-productive compounds consist of the raw rubber, process oils, reinforcing materials such as carbon black and / or silica and the antioxidant / antiozonant protection system. These materials are mixed at temperatures around 330o F. The final, “productive,” stage involves mixing the rubber from the last non-productive stage with the activators, accelerators and sulfur curing agents. This stage is mixed at a lower temperature (around 230o F) because the rubber compound will now scorch and cure at elevated temperatures.The majority of rubber products produced in the United States are composed of one or more of 23 generic rubber compounds shown in Table 4.12-14. Emissions factors were derived from the specific compound recipes shown in Table 4.12-2. Emissions from manufacturing aids such as solvents and adhesives ARE NOT included in these emission factors.4.12-1TableIndex of Rubber CompoundsCompound #1: Tire Inner Liner (BrIIR/NR)Compound #2: Tire Ply Coat (Natural Rubber / Synthetic Rubber)Compound #3: Tire Belt Coat (Natural Rubber)Compound #4: Tire Base/Sidewall (Natural Rubber / Polybutadiene Rubber)Compound #5: Tire Apex (Natural Rubber)Compound #6: Tire Tread (Styrene Butadiene Rubber / Polybutadiene Rubber)Compound #7: Tire Bladder (Butyl Rubber)Compound #8: EPDM 1 (EPDM Sulfur Cure)Compound #9: EPDM 2 (Peroxide Cure)Compound #10: EPDM 3 (Non-Black EPDM Sulfur Cure)Compound #11: CRW (Polychloroprene W Type)Compound #12: CRG (Polychloroprene G Type)Compound #13: Paracryl OZO (NBR/PVC)Compound #14: Paracryl BLT (NBR)Compound #15: Hypalon (CSM)Compound #16: Fluoroelastomer (FKM)Compound #17: AEM (Vamac)Compound #18: Hydrogenated Nitrile (HNBR)Compound #19: Silicone (VMQ)Compound #20: Acrylate Rubber (ACM)Compound #21: Chlorinated Polyethylene (CPE)Compound #22: Emulsion SBR (SBR 1502)Compound #23: Epichlorohydrin (ECO)Table4.12-2Rubber Compound Recipes aCompound #1: Tire Inner Liner (BrIIR/NR)Recipe:Brominated IIR X-2 85.00SMR 20 Natural Rubber 15.00Black 60.00 GPFStearic Acid 1.00Paraffinic Medium Process Oil 15.00Unreactive Phenol Formaldehyde Type Resin (Arofene 8318, SP1068) 5.00Oxide 3.00 ZincSulfur .50MBTS 1.50186.00Number of Passes/Temperature:1 (NP Temperature: 320°F; Chlorobutyl or 290°F Bromobutyl)2 (P) Temperature: 220°FCompound #2: Tire Ply Coat (Natural Rubber / Synthetic Rubber)Recipe:50472 Natural RubberSMR-GP Natural Rubber 70.00707 30.00 DuradeneN330 36.50Sundex790 20.00H 1.50 FlectolIP 2.30 SantoflexSunproof Super Wax 1.20Oxide 5.00 ZincAcid 1.00 StearicSulfur 2.30CBS .80170.60Number of Passes / Temperature:1 (NP) Temperature: 330°F2 (P) Temperature: 220°FTable 4.12-2 (cont.)Rubber Compound RecipesCompound #3: Tire Belt Coat (Natural Rubber)Recipe:#1RSS Natural Rubber 100.00HAF Black (N330) 55.00Oil 5.00 AromaticN-(1,3 dimethylbutyl)-N-phenyl-P-phenylene diamine (Santoflex 13) 1.00ZincOxide 10.00Acid 2.00 Stearicn-tertiary-butyl-2-benzothiazole disulfide (Vanax NS) .80Sulfur 4.00Cobalt Neodecanate (20.5% cobalt) 2.50180.30Number of Passes / Temperatures:1 (NP) Temperature: 330°F; add 1/2 black, add 1/2 oil2 (NP) Temperature: 330°F, add remainder of black and oil3 (remill) Temperature: 300°F4 (P) Temperature: 220°FCompound #4: Tire Base / Sidewall (Natural Rubber / Polybutadiene Rubber)Non-Productive Recipe:CV 50.00 NR-SMR-51220 50.00 TakteneN330 Carbon Black 50.00Oxide 1.50 ZincAcid 2.00 StearicAgerite Resin D 2.00Vulkanox4020 3.00Vanwax H Special 3.00Flexon 580 Oil 10.00171.50Productive Recipe:Productive 171.50 NonOxide 1.50 ZincRubber Maker Sulfur 1.75DPG 0.10CBS 0.60175.45Number of Passes / Temperatures:1 (NP) Temperature: 330°F2 (P) Temperature: 220°FTable 4.12-2 (cont.)Rubber Compound RecipesCompound #5: Tire Apex (Natural Rubber)Recipe:TSR 20 Natural Rubber 100.00HAF Black (N330) 80.00AromaticOil 8.00Acid 1.00 StearicResorcinol 3.00Hexamethylenetetramine 3.00Oxide 3.00 ZincN-tertiary-butyl-2-benzothiazole disulfide (Vanax NS) 1.50 n-cyclohexythiophthalimide (Santogard PVI) .30Sulfur 3.00202.801 (NP) Temperature: 330°F; add 60 parts black, add 6 parts oil2 (NP) Temperature: 330°F; add Resorcinol, add 20 parts black, add 2 parts oil3 (P) Temperature: 200°F; add HexamCompound #6: Tire Tread (Styrene Butadiene Rubber / Polybutadiene Rubber)Non-Productive Recipe #1:1712C 110.00 SBRN299 Carbon Black 60.00 1220 20.00 TakteneOxide 1.50 ZincAcid 3.00 Stearic4020 2.00 Vulkanox100 2.00 WingstayVanox H Special 2.50Sundex 8125 Oil 20.00221.00Non-Productive Recipe #2:#1: 221.00 Non-ProductiveN299 Carbon Black 20.00Sundex 8125 Oil 5.00246.00Productive Recipe:#2 246.00 Non-ProductiveOxide 1.50 ZincRubber Makers Sulfur 1.60TMTD 0.20CBS 3.00252.30Rubber Compound RecipesNumber of Passes / Temperatures:1(NP) Temperature: 330°F; add 60 parts black, add 20 parts oil2(NP) Temperature: 330°F; add 20 parts black, add 5 parts oil3 (P) Temperature: 220°FCompound #7: Tire BladderRecipe:BUTYL268 100.00N330 55.00Oil 5.00 CastorSP 1045 Resin 10.00Oxide 5.00 ZincW 5.00Neoprene180.00Number of Passes / Temperatures:NP 1 All Butyl, Castor Oil, Zinc Oxide, 45 phr N330, discharge approx 330°F / 340°F+Resin, 10 phr N330, discharge approx 270 / 280°F DO NOT EXCEED 290°FPROD NP2 = neoprene, discharge approx 250F / 260°FCompound #8: EPDM 1 (EPDM Sulfur Cure)Non-Productive Recipe:Vistalon7000 50.003777 87.50 VistalonN650 GPF-HS Black 115.00N762 SRF-LM Black 115.00Process Oil Type 104B (Sunpar 2280) 100.00Oxide 5.00 ZincAcid 1.00Stearic473.50Productive Recipe:Non-Productive 473.50 Sulfur 0.50 TMTDS 3.00 ZDBDC 3.00 ZDMDC 3.00 DTDM 2.00485.00Number of Passes / Temperatures1 (NP) Temperature: 340°F; upside down mix, rubber then black and oil2 (P) Temperature: 220°FRubber Compound RecipesCompound #9: EPDM 2 (Peroxide Cure)Non-Productive Recipe:502 100.00 RoyaleneN 762 Carbon Black 200.00SunparOil 85.00 2280Oxide 5.00 ZincAcid 1.00Stearic391.00 Productive:Non-Productive 391.00 40C 6.00 DICUPSARET 500 (on carrier / 2 parts active) 2.56399.56 NP Temperature: 330°FP Temperature: 240°FCompound #10: EPDM 3 (Non-black EPDM Sulfur Cure)Recipe:Vistalon5600 50.003777 87.50 VistalonHard Clay (Suprex) 180.00Mistron Vapor Talc 100.00 Whiting 40.00 AtomiteProcess Oil Type 104B (Sunpar 2280) 60.00Silane(A-1100) 1.50Wax 5.00 ParaffinZincOxide 5.00Acid 1.00 StearicSulfur 1.50 Cupsac 0.50 TMTD 3.00535.00 Number of Passes / Temperatures:1 (NP) Temperature: 330°F2 (P) Temperature: 220°F, add Sulfur, Cupsac, and TMTDSRubber Compound RecipesCompound #11: CRW (Polychloroprene W Type)Recipe:NonProductive:WRT 100.00 NeopreneN550 13.20762 15.70 NAgerite Staylite S 2.00Sunproof Super Wax 2.00IP 1.00 SantoflexOxide 4.00 MagnesiumAcid 0.50 StearicDoz 15.00PlastHall153.40 Productive Recipe:Non-Productive 153.40 Oxide 5.00 ZincTMTD 0.50 Dispersed Ethylene Thiourea 1.00159.90 Number of Passes / Temperatures:1 pass at 240°F; add accelerator package at 200°FCompound #12: CRG (Polychloroprene G Type)Non-Productive Recipe:GN 100.00 NeopreneSRF 50.00 Sundex790 10.00 Octamine 2.00 Acid 1.00 StearicMaglite D 4.00167.00 Productive Recipe:Non-Productive 167.00 TMTM 0.50 Sulfur 1.00 DOTG 0.50 Oxide 5.00Zinc174.00 Number of Passes / Temperatures:1 (NP) Temperatures: 240°F; add zinc oxide and curatives late at 200°F2 (P) Temperature: 200°FRubber Compound RecipesCompound #13: Paracryl OZO (NBR / PVC)Recipe:PARACRILOZO 100.00Oxide 5.00 ZincOCTAMINE 2.00Clay 80.00 HardBlack 20.00 (N-550)FEFAcid 1.00 StearicMBTS 2.50 TUEX 1.50 ETHYLTUEX 1.50 DOP 15.00 KP-140 15.00 Sulfur 0.20Spider243.70Number of Passes:(NP) Temperature: 330°F(P) Temperature: 220°F; add MBTS, TUEX, ETHYLTUEX, Spider SulfurCompound #14: Paracryl BLT (NBR)Recipe:BLT 100.00 PARACRILOxide 5.00 ZincBlack 100.00 SRF(N-774)TP-95 15.00G-25 5.00 ParaplexAMINOX 1.50Acid 1.00 StearicESEN 0.50MONEX 1.50Sulfur 0.75230.25Number of Passes / Temperatures:(NP) Temperature: 280°F(P) Temperature: 220°F; add sulfur, MONEX, and possibly ESENTable 4.12-2 (cont.)Rubber Compound RecipesCompound #15: Hypalon (CSM)Recipe:40 100.00 HypalonCLS 4 PBD 3.00Carbo wax 4000 3.00PE617A 3.00Mag Lite D 5.00200 3.00 PE(Atomite) 100.00 WhitingN650 100.00 Oil 70.00 TOTMMBTS 1.00A 1.50 TetroneNBC 0.50HVA-2 0.50390.50Uses of Formulas / Temperatures:Number of Passes:1 (P) Temperature: 280°FCompound #16: Fluoroelastomer (FKM)Recipe:VitonE60C 100.00Black 20.00 N990CalciumHydroxide 6.00D 3.00Maglite129.00Compound #17: AEM (Vamac)Recipe:Masterbatch 124.00 VAMAC*B-12418D .50 ARMEENAcid .20 StearicSRF Carbon Black (N-774) 10.00 #1 4.00 DIAKDPG 4.00142.70Table 4.12-2 (cont.)Rubber Compound RecipesCompound #18: Hydrogenated Nitrile (HNBR)Non-Productive Recipe:HNBR Zetpol 2020 100.00 Black 45.00 N6507P 1.00 FlexoneAgerite Resin D 1.00ZMTI 1.00 Kadox 911 C 5.00 Acid 1.00 StearicTrioctyl trimellitate (TOTM) 7.00161.00 Productive Recipe:Sulfur 0.50 MBTS 1.50 TMTD 1.50 MTDMonex .50165.00 Number of Passes / Temperatures:1 (NP) Temperature: 275°F2 (P) Temperature: 210°FCompound #19: Silicone (VMQ)Recipe:Rubber 70.00 SiliconeSilastic NPC-80 silicone rubber 30.005 Micron Min - U - Sil 68.00Silastic HT - 1 modifier 0.80Vulcanizing agent: Varox DBPH 50 1.00169.80Compound #20: Acrylate Rubber (ACM)Non-Productive Recipe:AR71 100.00 HytempAcid 1.00 Stearic550 65.00N166.00 Productive Recipe:Non-Productive 166.00 SodiumStearate 2.25Stearate 0.75 PotassiumSulfur 0.30169.30 Number of Passes / Temperatures:1 (NP) Temperature: 260°F2 (P) Temperature: 220°FTable 4.12-2 (cont.)Rubber Compound RecipesCompound #21: Chlorinated Polyethylene (CPE)Recipe:0136 100.00 CMMagliteD 10.00N 774 Black 30.00 VH 35.00 SterlingDER 331 DLC 7.00Agerite Resin D 0.20Oil 35.00 TOTMTriallyl Isocyanurate Cure 5223 (provided by Gates) 2.9017/40 10.00Trigonox230.10Number of Passes / Temperatures:Single pass mixed to 240°F; add Triallylisocyanurate,Triganox 17/40 at 200°FCompound #22: Emulsion SBR (SBR 1502)Non-Productive Recipe:1502 100.00 SBRN330 Carbon Black 58.50Oxide 10.00 ZincStearicAcid 2.00Agerite Resin D (Naugard Q) 2.007P 1.00 FlexoneSunproof Super Wax 1.50Sundex 790 Oil 7.00182.00Productive Recipe:Non-Productive 182.00Rubber Makers Sulfur 2.00TBBS 1.80185.80 Number of Passes / Temperatures:Non-productive pass mixed to 330°F,Second pass mixed to 220°F.Table 4.12-2 (cont.)Rubber Compound RecipesCompound #23: Epichlorohydrin (ECO)Recipe:2000 100.00 HydrinN330 Carbon Black 50.00 Acid 1.00 StearicVulkanox MB-2 / MG / C 1.00Carbonate 5.00 CalciumZisnetF-PT 1.00Diphenylguanadine 0.50 PVI 0.50Santogard159.00Number of Passes / Temperatures:1 Pass at 240°Fa Reference 4Emissions of volatile organic compounds (VOCs) due to use of cements, solvent tackifiers, and release agents in rubber manufacturing are generally determined by either material balance, assuming a 100% loss to the atmosphere or, in some cases, by direct measurement. In cases where solvent emissions are determined by a mass balance calculation which assumes 100% loss at the time of application to the rubber substrate, there is a potential for double-counting a small percentage of the solvent emissions when using the emission factors to determine process volatile organic emissions. This situation is due to the partial absorbption of some solvents into the rubber surface during manufacturing, and subsequent volatilization during downstream processing or curing.It is not possible to determine to what extent typical hydrocarbon solvent constituents reported in the emission factors may have resulted from use of solvents or adhesives upstream in the manufacturing process. Anecdotal evidence suggests that as much as 5% of the solvent applied to the surface of the rubber may migrate into the rubber and appear later in the process as a volatile emission. Caution should therefore be exercised when compiling a facility-wide VOC emission inventory which combines the use of process emission factors and mass balance calculations of solvent usage. Otherwise, this methodology will generally result in an overstatement of the actual facility-wide VOC emissions.Milling operations are conducted to form the rubber compounds into sheets or strips for introduction into calenders or extruders, for warming up rubber for ease of handling and processing and to homogenize recycled rubber compounds for reuse in the process.In the mixing area rubber compound is discharged from the Banbury mixer into a drop mill, extruder or pelletizer which forms it into a long sheet of rubber compound. Additional mills may be located directly downstream from the Banbury drop mill to provide additional mixing or handling capability. From the mill(s) the hot, tacky rubber sheet is then passed through a water-based "anti-tack" solution which prevents the rubber sheets from sticking together as they cool to ambient temperature. The rubber sheets are placed directly onto a long conveyor belt (festoon) which, through the application of cool air or water, lowers their temperature. After cooling the rubber sheets are piled onto a storage pallet for transfer to the component preparation area.Mills are also used to prepare rubber for introduction to calendering and extruding processes. In these cases the mills are used to heat the rubber compound in order to make the rubber stock more flexible for further handling and processing.Mills are also used to homogenize recycled rubber compounds for reintroduction into the process.Extrusion is often performed to combine several types of previously mixed rubber compounds. The extruder consists of a power-driven screw within a stationary cylinder. A die is attached to the head of the screw to produce the desired shape or cross section of the extruded rubber.Extruders may have multiple heads providing laminations of extruded shapes. Extruding heats the rubber and the rubber remains hot until it is cooled via air cooling or use of a water bath or spray conveyor where cooling takes place.Extrusion can be performed with both warm or cold rubber feed. The extruder is jacketed to maintain the desired operating temperature.Extruders may be utilized in the mixing area, along with mills to shape mixed rubber compound for further processing.Calendering is often used in the rubber manufacturing industry to apply a rubber coat onto a continuous textile or metal mesh web. The calender is a heavy-duty machine equipped with multiple rolls revolving in opposite directions. Calenders receive hot strips of rubber from mills and squeeze the rubber into reinforcing fibers of cloth or steel or cloth-like fiber matrices, thus forming thin sheets of rubber coated materials. Calenders are also used to produce non-reinforced, thickness controlled sheets of rubber called innerliner or gum strip. After calendering, the calendered stock is wound into a liner to prevent sticking on itself. The calendered material is next cut to desired width and / or length for use in tire building.The function of the bead is to provide a proper seal between the tire and the wheel rim when a tire is mounted on the rim. Bead compounds produced in mixing are used to coat bead wires. Brass-plated bead wire is received on large spools. Bundles of wires are passed through an extrusion die and given a coating of rubber. The rubber coated wire is then wound into a hoop of specific diameter and thickness and sent to the tire-building machine. In some cases, cement may be applied to the finished bead.Cementing operations are used at various stages in the tire building process. For example, cements (adhesives) may be used to improve the adhesion of different components to each other during the tire building process. Traditionally cements have been used in the bead building process, applied to extruded tread stock (end cementing for cut treads and undertread cementing for retreads and certain other tread stocks) and at tire building machines. It is important to note that cement usage can vary significantly from facility to facility depending on the type of tire being manufactured and the process being utilized.Marking inks are used at various stages of the process to aid in the identification of the components being managed. Typically marking inks are applied to extruded tread stocks to aid in the identification and handling of cured tires. Again, it is important to note that marking practices can vary significantly from facility to facility.The various components manufactured in component preparation must be cut and cooled prior to introduction into tire building. Typically, the processing of the rubber compounds generates heat which causes an increase in rubber temperature. If this temperature is not controlled properly the compound may begin to cure prematurely, thus rendering it unusable.Tire components from bead making, extrusion, and calendering are moved to the component assembly area. The assembly of various tire components is referred to as tire building. The main mechanical component of the tire-building operation is the drum, which is a collapsible cylinder that can be turned and controlled by the tire builder.The typical tire building process begins with the application of a thin layer of special calendered rubber compound, called the inner liner, to the drum. Next, plies are placed on the drum, one at a time. The cords (calendered stock - rayon, nylon, polyester and related fabrics coated with rubber) are laid in alternate direction in each successive ply. This step is followed by a process of setting the beads in place. The plies are turned up around the beads and incorporate the beads into the tire. Chafer (extruder) stock from extruding or calendering is added if needed. Belts (metal or fabric calendered stock), if any are then applied. Finally, the tread and sidewalls are added to complete the tire. The tire may be “stitched” under pressure to remove air from between the components and bind them together. Radial tire production involves limited use of cements and solvents. Cement usage during tire building will vary significantly from facility to facility.The drum is then collapsed and the uncured (green) tire is transferred to the green tire spraying operation. In preparation for curing, the uncured green tire may be coated with a lubricant (green tirespray). The lubricating spray is either a solvent-based or a water-based silicone. The function of the green tire spray is to ensure the cured tire does not stick to the curing mold when being removed.The final step in manufacturing of rubber products is vulcanizing (curing). There are three predominant vulcanizing processes: press mold curing, autoclave curing, and hot air curing. Press mold curing uses high temperature and pressure to cure the final product. The high pressure (600-10,000 psi) forces the rubber to conform to the shape of the mold. Press mold curing is used in tire and engineered products manufacturing.Autoclave curing utilizes saturated steam at an elevated pressure to cure the rubber mix. Unlike press mold curing, the product is formed into its final shape prior to the curing process. Autoclave curing is the common method in non-tire rubber manufacturing facilities.Hot air curing entails passing uncured, engineered products through a chamber with a heated atmosphere. Temperature and residence times may vary, depending on the product type and formulation. As with the autoclave curing, these products have already been formed into their final shape prior to undergoing the curing process.Grinding is often performed to remove rough edges and other blemishes from the final product or in some cases to actually form and shape the product. The ground rubber is occasionally recycled and utilized as filler in some rubber manufacturing processes. In the tire manufacturing industry, grinding is performed to balance the tire and also to expose the white sidewall or lettering. Relative to the engineered products industry, grinding may actually be used to obtain the correct shape of the final product such as the final shaping of drive belts.4.12.2 Equipment Scale ConsiderationsEmissions testing was performed on several sizes of similar process equipment. These size differences are the most profound on the sizes of internal mixers tested. Emissions tests were performed on internal mixers ranging from a two-pound laboratory mixer, to a 200-pound pilot scale system up to a 500-pound production mixer. On a pound of pollutant emitted per pound of rubber mixed basis, test data indicated that emissions were not dependent on mixer size. This is especially true for the volatiles and semivolatile emissions. There was some variability of metals emissions which is most likely the result of greater particulate losses into the ventilation system on the larger mixers during charging than on smaller scale equipment.Since there was no direct correlation to process equipment size and emissions, no scaling factors were developed for equipment size.4.12.3 Emissions And ControlsThe mechanically-created or externally-added heat present during the six principal processes (mixing, milling, extrusion, calendering, curing, and grinding) cause volatile organic compounds (VOC) and hazardous air pollutants (HAP) to be emitted. Particulate matter is primarily emitted from the dry chemicals utilized in mixing and as a result of grinding.Dust collectors (baghouses, fabric filters) are commonly used to control particulate matter emissions from mixing. Cyclone separators in combination with dust collectors or electrostatic precipitators are typically used in grinding applications.4.12.4 Emission Factors3The following is common to each of the emission factors tables:(1) Total VOCs were analyzed by EPA Reference Method 25A / FID.(2) Total speciated organics were analyzed by EPA Reference Methods TO-14 / GC-MS(speciated volatiles), TO-14 / GC-FID (volatile ozone precursors) and M8270 (semi-volatiles).Note: Results from Method 25A and results from the total speciated organics reference methods are not directly comparable due to the inherent differences in the method ofanalysis.(3) Total Organic HAP are hazardous air pollutants as defined by the Clean Air Act Amendmentsof 1990, Section 301 and were analyzed by EPA Reference Method TO-14 / GC-MS andM8240 (volatiles), M8270 (semi-volatiles), and TO-14 / GC / FPD (sulfur compounds).(4) Total Metal HAP are hazardous air pollutants as defined by the Clean Air Act Amendmentsof 1990, Section 301 and were analyzed by EPA Reference Methods M6010 and M7000(metals).(5) Total HAP are the sum of total organic HAP and total metal HAP.(6) Total Particulate Matter (PM) was analyzed by EPA Reference Method 5.(7) Target analytes which were not detected in any runs for a particular process and compoundwere not included in the tables. The assumption is that if a target analyte went undetected inany runs, there is a high probability that even if it was present, the low detection limitsindicate that its overall contribution is insignificant.(8) Target analytes detected in one or more runs were averaged together. Target analytes thatwere not detected in a test run were assumed to have been present at a concentration of one-half the test detection limit for averaging purposes.(9) Metals were expected to be detected in the particulate matter emitted during rubber mixingbut were not expected to be a significant emission in any other process. To confirm thisassumption, the extruder emissions were analyzed for metals. Metals emitted proved to be soinsignificant that they could be within the margin of error of the analytical procedure. Metalemissions were therefore considered to be insignificant in other processes.Nine separate tables of emission factors comprise the remainder of this section. The tables are available in spreadsheets on the CHIEF web site at /ttn/chief/ap42/ch04/. The tables are too large to include in the section and are more useful as spreadsheets. The contents of the MS Excel spreadsheet are shown in Table 4.12-3.4.12.5 Updates since the Fifth EditionThis section was released as a draft in 1997 for review and comment. It was not finalized.。
几种橡胶的配方范文

几种橡胶的配方范文橡胶是一种重要的材料,广泛应用于工业和日常生活中。
根据不同的用途和要求,可以使用不同的橡胶配方来生产橡胶制品。
以下是几种常见的橡胶配方。
1.天然橡胶配方:天然橡胶是从橡胶树脂中提取的,具有极高的弹性和耐磨性。
它常用于制造轮胎、橡胶鞋等产品。
天然橡胶配方一般包括以下成分:乙烯丙烯二烯橡胶、纯天然橡胶、防老化剂、硫化剂、填充剂(如炭黑)、软化剂等。
其中,乙烯丙烯二烯橡胶增加了橡胶的强度和耐用性,纯天然橡胶提高了橡胶的弹性和耐磨性。
防老化剂可以延长橡胶制品的使用寿命,硫化剂用于促进橡胶的硫化反应,填充剂用于增加橡胶的硬度和强度,而软化剂则用于提高橡胶的柔软性。
2.丁苯橡胶配方:丁苯橡胶是一种合成橡胶,具有很高的耐热性和化学稳定性。
它常用于制造密封件、橡胶管等产品。
丁苯橡胶配方一般包括以下成分:丁苯橡胶、防老化剂、硫化剂、填充剂(如炭黑)、软化剂等。
丁苯橡胶的优点是具有良好的抗老化性和耐热性,但相对于天然橡胶来说,缺乏弹性和耐磨性。
因此,一般会在配方中加入合适的填充剂来增加橡胶的硬度和强度。
3.氟橡胶配方:氟橡胶是一种特殊的橡胶,具有极高的耐腐蚀性和耐高温性能。
它常用于制造密封件、汽车零部件等产品。
氟橡胶配方一般包括以下成分:氟橡胶、防老化剂、硫化剂、填充剂等。
氟橡胶的优点是具有优异的抗腐蚀性和耐高温性,但相对较高的成本也限制了其应用范围。
在氟橡胶配方中,填充剂的选择十分重要,通常采用石墨、滑石等耐腐蚀材料。
除了上述几种橡胶配方外,根据不同的需求,还可以使用其他合成橡胶(如丁腈橡胶、丙烯橡胶等)进行配方。
此外,还可以根据不同的用途对橡胶配方进行调整,以满足不同的性能需求。
橡胶配方的工艺和操作也非常重要,需要根据具体的情况进行调整。
总之,橡胶配方的选择和调整将直接影响到最终产品的性能和质量。
典型橡胶制品配方实例
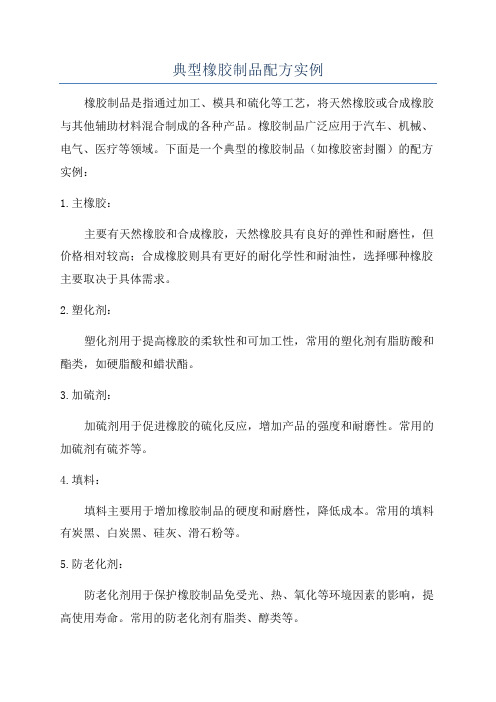
典型橡胶制品配方实例
橡胶制品是指通过加工、模具和硫化等工艺,将天然橡胶或合成橡胶与其他辅助材料混合制成的各种产品。
橡胶制品广泛应用于汽车、机械、电气、医疗等领域。
下面是一个典型的橡胶制品(如橡胶密封圈)的配方实例:
1.主橡胶:
主要有天然橡胶和合成橡胶,天然橡胶具有良好的弹性和耐磨性,但价格相对较高;合成橡胶则具有更好的耐化学性和耐油性,选择哪种橡胶主要取决于具体需求。
2.塑化剂:
塑化剂用于提高橡胶的柔软性和可加工性,常用的塑化剂有脂肪酸和酯类,如硬脂酸和蜡状酯。
3.加硫剂:
加硫剂用于促进橡胶的硫化反应,增加产品的强度和耐磨性。
常用的加硫剂有硫芥等。
4.填料:
填料主要用于增加橡胶制品的硬度和耐磨性,降低成本。
常用的填料有炭黑、白炭黑、硅灰、滑石粉等。
5.防老化剂:
防老化剂用于保护橡胶制品免受光、热、氧化等环境因素的影响,提高使用寿命。
常用的防老化剂有脂类、醇类等。
6.加工助剂:
加工助剂用于提高橡胶的加工性能,如增塑剂、润滑剂等。
7.制剂:
制剂可根据具体需求进行选择,例如,如果需要改善橡胶的耐油性,
可以加入耐油制剂。
以上是一个典型的橡胶密封圈的配方实例,根据具体产品的要求和性
能需求,配方可能有所不同。
通过合理的配方选择,可以制备出性能优异、符合要求的橡胶制品。
橡胶制品实用配方大全
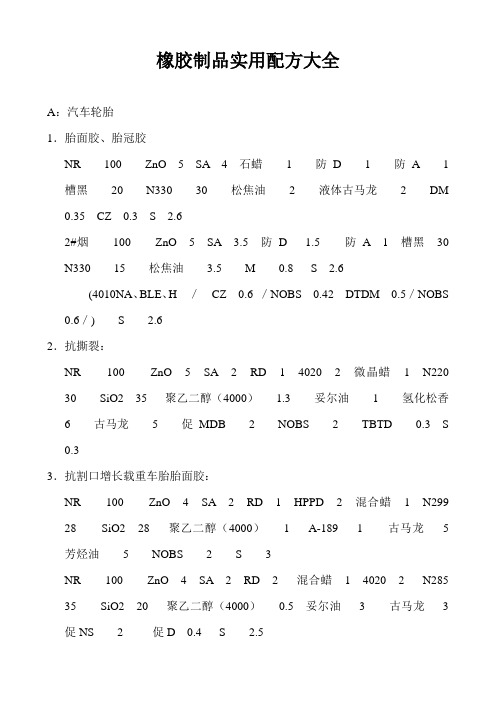
橡胶制品实用配方大全A:汽车轮胎1.胎面胶、胎冠胶NR 100 ZnO 5 SA 4 石蜡 1 防D 1 防A 1槽黑20 N330 30 松焦油 2 液体古马龙 2 DM0.35 CZ 0.3 S 2.62#烟100 ZnO 5 SA 3.5 防D 1.5 防A 1 槽黑30 N330 15 松焦油 3.5 M 0.8 S 2.6(4010NA、BLE、H /CZ 0.6 /NOBS 0.42 DTDM 0.5/NOBS0.6/) S 2.62.抗撕裂:NR 100 ZnO 5 SA 2 RD 1 4020 2 微晶蜡 1 N22030 SiO2 35 聚乙二醇(4000) 1.3 妥尔油 1 氢化松香6 古马龙 5 促MDB 2 NOBS 2 TBTD 0.3 S0.33.抗割口增长载重车胎胎面胶:NR 100 ZnO 4 SA 2 RD 1 HPPD 2 混合蜡 1 N29928 SiO2 28 聚乙二醇(4000) 1 A-189 1 古马龙 5芳烃油 5 NOBS 2 S 3NR 100 ZnO 4 SA 2 RD 2 混合蜡 1 4020 2 N28535 SiO2 20 聚乙二醇(4000)0.5 妥尔油 3 古马龙 3促NS 2 促D 0.4 S 2.5并用SBR:NR 70 SBR 30 ZnO 4 SA 3 石蜡 1.5 防D 0.7 40101.5 H 0.5 槽黑27 N330 20 古马龙 4.5 DM 1.2M 0.8 S 2.2NR烟70 SBR 30 ZnO 5 SA 3 防D 1.5 防A 1槽黑30 混气炭黑15 松焦油 4.5 DM 1 CZ 0.4 S 2.3NR烟70 SBR 30 ZnO 5 SA 2.5 防 D 1.5 防 A1 石蜡 1 槽黑28 N330 18 松焦油 4.5 DM0.63 CZ 0.33 S 2.15胎冠上层胶:2#烟70 SBR 30 ZnO 4 SA 3 4010 1 防D 1防H0.4 石蜡 2 槽黑25 N330 20 三线油 4.5 DM0.35 NOBS 0.6 S 2.21#烟60 SBR 40 ZnO 4 SA 3 4010 0.5 防 A 1 石蜡 1.5 中超耐磨炭黑52 芳烃油10 NOBS 0.8 S1.8白胎面:NR 70 SBR 30 ZnO 3 SA 2 防ODA 1 混合蜡 2 Si 50 A-189 0.8 聚乙二醇(4000)1.5 古马龙10 TiO2 5 NOBS 2 S 2.8NR 50 SBR(溶聚) 50 ZnO 4 SA 3 防4010NA 1.5 石蜡 1 RD 1.5 中超耐磨53 操作油8NOBS 0.8 S 1.5NR 35 SBR 65 ZnO 5 SA 5 防HPPD 2 混合蜡 2 RD 1.5 Si 25 N285 45 聚乙二醇(4000) 1 古马龙20 油 5 NOBS 1.3 D 0.3 S 1.7NR 30 SBR 70 ZnO 4 SA 3 防D 1.5 防4010NA 1.5 石蜡 1 防H 0.3 RP-3 防护蜡1.5 中超50 机油10 NOBS 0.8 S 1.8与BR并用:NR 75 BR 25 ZnO 4 SA 3 防D 1.5 防4010NA 1.5 石蜡 1 槽黑10 中超37 机油10 CTP 0.1 CZ 0.9 S 1.2(1.5)NR 70 BR 30 ZnO 4 SA 3 防D 1.2 防4010NA 0.5 石蜡 1 防AW 1.3 石蜡 1 中超20 N330 30 锭子油 5 NOBS 0.6 S 1.5(屈挠龟裂OK)耐磨抗撕裂载重越野胎面:。
彩色橡胶制品高弹性和低压变研制(附带案例配方-天然、丁腈、乙丙橡胶三个)

彩色橡胶制品高弹性和低压变研制(附带案例配方-天然、丁腈、乙丙橡胶三个)彩色橡胶常出现的问题1、混炼胶料中的颜料分散不均出现色差;吃料慢,难分散;混炼密炼升温快易焦烧(死胶);2、硫化硫化速度慢制品高温色变;制品容易黏磨;出磨热撕性差;飞胶边厚,难修边;3、成品橡胶成品弹性差、压缩变形大;橡胶成品时间长出现色差、黄变现象;橡胶成品停放厚容易出现喷霜。
影响高弹和压变:1.橡胶的种类弹性取决于橡胶分子链的内旋转难易,分子问作用力的大小。
如天然胶、顺丁胶、丁基胶、硅橡胶等被认为足弹性好的橡胶。
2.分子量的大小影响分子链的卷曲程度、无用未端的数量。
分子量大,弹性较好。
3.共聚橡胶的化学组成及结构本文来自橡胶信息网丁苯胶、丁腈胶中随苯乙烯和丙烯腈含量的增加弹性变差。
乙丙橡胶中,丙烯的含量为4O~5O%时弹性最好,这时形成的共聚物是无规共聚物,如果乙烯含量超过7O%,形成较长的乙烯嵌段,长乙烯嵌段易形成结品而使乙丙胶失去弹性。
二、补强填充剂对硫化胶弹性的影响非炭黑补强填充剂会损害橡胶的弹性,增大压缩永久变形。
这与在应力作用下,橡胶分子在非活性填充剂表面滑动,除去应力以后,又阻碍分子键的恢复有关。
偶联荆的应用可以大大地改善非补强填充剂对硫化胶弹性的影响(改善填充荆的分敝性和表面活性)大多文献资料中都说,随着炭黑粒径的增大,硫化胶的弹性增强,但往往忽略了填充量对硫化橡胶弹性的影响。
实际上各种橡胶产品都有一定的硬度和强度要求,如单一地使用低补强性炭黑时,用量需要增大,这样同样会损害橡胶的弹性和恢复。
在一定变形量的硫化橡胶中,填充的橡胶分子链的变形量要比实际变形量大,扩大的数值与填充量成比例。
变形量的增大同样会影响橡胶分子链的位移位置和恢复,增大永久变形。
采用适当地补强剂并用和适当地混合工艺,使混炼胶获得理想的结构形态,可以得到高弹性的硫化橡胶。
本文来自橡胶信息网三、软化荆和增塑荆软化荆通常指与橡胶桕容性火是很好的汕类或树脂,增塑荆指与橡胶桕容性好的油或树脂。
几种橡胶的配方范文
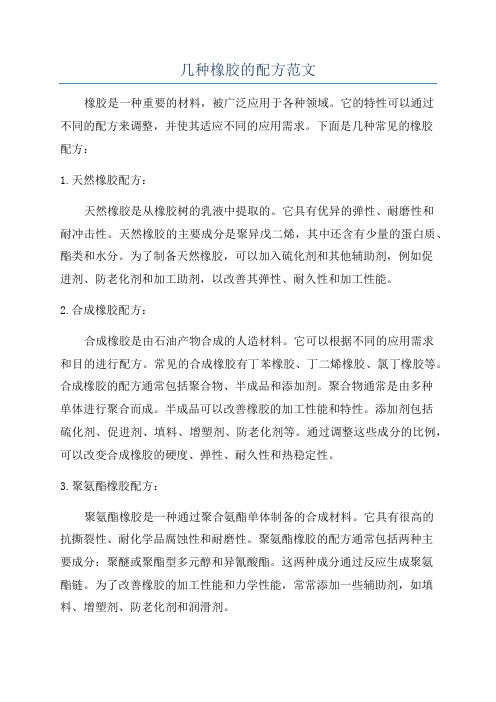
几种橡胶的配方范文橡胶是一种重要的材料,被广泛应用于各种领域。
它的特性可以通过不同的配方来调整,并使其适应不同的应用需求。
下面是几种常见的橡胶配方:1.天然橡胶配方:天然橡胶是从橡胶树的乳液中提取的。
它具有优异的弹性、耐磨性和耐冲击性。
天然橡胶的主要成分是聚异戊二烯,其中还含有少量的蛋白质、酯类和水分。
为了制备天然橡胶,可以加入硫化剂和其他辅助剂,例如促进剂、防老化剂和加工助剂,以改善其弹性、耐久性和加工性能。
2.合成橡胶配方:合成橡胶是由石油产物合成的人造材料。
它可以根据不同的应用需求和目的进行配方。
常见的合成橡胶有丁苯橡胶、丁二烯橡胶、氯丁橡胶等。
合成橡胶的配方通常包括聚合物、半成品和添加剂。
聚合物通常是由多种单体进行聚合而成。
半成品可以改善橡胶的加工性能和特性。
添加剂包括硫化剂、促进剂、填料、增塑剂、防老化剂等。
通过调整这些成分的比例,可以改变合成橡胶的硬度、弹性、耐久性和热稳定性。
3.聚氨酯橡胶配方:聚氨酯橡胶是一种通过聚合氨酯单体制备的合成材料。
它具有很高的抗撕裂性、耐化学品腐蚀性和耐磨性。
聚氨酯橡胶的配方通常包括两种主要成分:聚醚或聚酯型多元醇和异氰酸酯。
这两种成分通过反应生成聚氨酯链。
为了改善橡胶的加工性能和力学性能,常常添加一些辅助剂,如填料、增塑剂、防老化剂和润滑剂。
4.丁腈橡胶配方:丁腈橡胶是一种合成橡胶,具有出色的耐油性、耐溶剂性和耐热性。
它的主要成分是丁二烯和丙烯腈。
丁腈橡胶的配方通常还包括填料、填充剂、增塑剂、稳定剂等。
填料可以改变橡胶的硬度、强度和抗撕裂性。
填充剂用于调节橡胶的流动性和流变性能。
通过控制这些配方成分的比例,可以获得不同硬度和性能的丁腈橡胶。
总之,橡胶的配方对于其性能和应用非常重要。
通过调整聚合物、添加剂和填料的比例,可以满足不同的需求和应用要求。
无论是天然橡胶、合成橡胶、聚氨酯橡胶还是丁腈橡胶,都需要仔细选择和控制配方,以获得所需的特性和性能。
橡胶制品实用配方大全

橡胶制品实用配方大全橡胶制品是一种常见的材料,在日常生活和工业生产中都有着广泛的应用。
橡胶制品的性能和质量很大程度上取决于配方的选择和制备工艺。
因此,掌握一些实用的橡胶制品配方对于橡胶制品生产和改进具有重要意义。
本文将介绍一些常见的橡胶制品配方,希望能够对橡胶制品生产者和研究人员有所帮助。
1. 橡胶制品硫化剂配方。
硫化剂是橡胶制品中的重要添加剂,它能够促进橡胶分子间的交联反应,从而提高橡胶制品的强度和耐磨性。
常用的硫化剂有硫醚类、过氧化物类和有机过硫酸盐类等。
一般来说,硫化剂的选择要根据具体的橡胶种类和要求来确定,同时还要考虑硫化的温度和时间等因素。
2. 橡胶制品增塑剂配方。
增塑剂是一类能够提高橡胶柔软度和延展性的添加剂,常用的增塑剂有酯类、酚醛树脂类和聚氯乙烯类等。
在橡胶制品的配方设计中,增塑剂的选择要考虑到橡胶的种类、硬度和使用环境等因素,以及增塑剂与其他添加剂的相容性。
3. 橡胶制品填充剂配方。
填充剂是橡胶制品中的一种重要添加剂,它能够提高橡胶制品的硬度和耐磨性,降低生产成本。
常用的填充剂有碳黑、二氧化硅和滑石粉等。
在配方设计中,填充剂的种类和用量要根据橡胶制品的具体要求和使用环境来确定,同时还要考虑填充剂与橡胶的分散性和增强效果。
4. 橡胶制品防老化剂配方。
防老化剂是一类能够延缓橡胶老化过程的添加剂,常用的防老化剂有芳香胺类、酚类和酮类等。
在橡胶制品的配方设计中,防老化剂的选择要考虑到橡胶的种类、使用环境和预期使用寿命等因素,以及防老化剂与其他添加剂的相容性和协同效应。
5. 橡胶制品硫化体系配方。
硫化体系是橡胶制品中的一个重要组成部分,它由硫化剂、活性剂和助剂等组成。
在橡胶制品的配方设计中,硫化体系的选择要考虑到橡胶的种类、硬度和使用环境等因素,以及硫化体系与其他添加剂的相容性和协同效应。
总结。
橡胶制品的配方设计是一个复杂而又关键的工作,它直接影响着橡胶制品的性能和质量。
在实际生产中,需要根据具体的橡胶种类和要求,合理选择和搭配各种添加剂,进行科学的配方设计和工艺控制,以确保橡胶制品具有良好的性能和稳定的质量。
标准橡胶配方
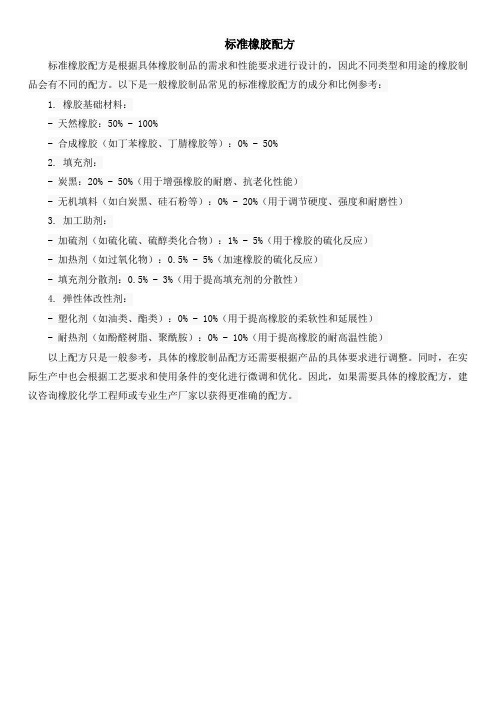
标准橡胶配方
标准橡胶配方是根据具体橡胶制品的需求和性能要求进行设计的,因此不同类型和用途的橡胶制品会有不同的配方。
以下是一般橡胶制品常见的标准橡胶配方的成分和比例参考:
1. 橡胶基础材料:
- 天然橡胶:50% - 100%
- 合成橡胶(如丁苯橡胶、丁腈橡胶等):0% - 50%
2. 填充剂:
- 炭黑:20% - 50%(用于增强橡胶的耐磨、抗老化性能)
- 无机填料(如白炭黑、硅石粉等):0% - 20%(用于调节硬度、强度和耐磨性)
3. 加工助剂:
- 加硫剂(如硫化硫、硫醇类化合物):1% - 5%(用于橡胶的硫化反应)
- 加热剂(如过氧化物):0.5% - 5%(加速橡胶的硫化反应)
- 填充剂分散剂:0.5% - 3%(用于提高填充剂的分散性)
4. 弹性体改性剂:
- 塑化剂(如油类、酯类):0% - 10%(用于提高橡胶的柔软性和延展性)
- 耐热剂(如酚醛树脂、聚酰胺):0% - 10%(用于提高橡胶的耐高温性能)
以上配方只是一般参考,具体的橡胶制品配方还需要根据产品的具体要求进行调整。
同时,在实际生产中也会根据工艺要求和使用条件的变化进行微调和优化。
因此,如果需要具体的橡胶配方,建议咨询橡胶化学工程师或专业生产厂家以获得更准确的配方。
三元乙丙橡胶实用配方

三元乙丙橡胶实用配方配方一:原材料:-三元乙丙橡胶:100份-碳酸钙:30份-增塑剂:15份-促进剂:5份-抗老化剂:3份-防火剂:2份-空气分散剂:2份-硫化剂:1份步骤:1.将三元乙丙橡胶加入橡胶混炼机中进行预混。
预混时间约为5分钟,温度控制在120-140℃。
2.将碳酸钙、增塑剂、促进剂、抗老化剂、防火剂和空气分散剂逐一加入预混橡胶中,并进行均匀混合。
混合时间约为15分钟,温度控制在120-140℃。
3.将硫化剂加入混合橡胶中,并继续混合20分钟,温度保持在120-140℃。
4.将混合橡胶取出,放入橡胶成型机中进行成型。
成型时可采用挤出、压延或注塑等方法。
5.成型后的橡胶制品放置在恒温恒湿条件下进行硫化。
硫化温度为150℃,时间根据制品大小而定,一般为20-30分钟。
6.经硫化后的橡胶制品经冷却后即可包装出库。
配方二:原材料:-三元乙丙橡胶:100份-丙烯酸甲酯:30份-丁二酸二丁酯:15份-酸性活化剂:5份-抗氧剂:3份-防火剂:2份-空气分散剂:2份-硫化剂:1份步骤:1.将三元乙丙橡胶和丙烯酸甲酯加入橡胶混炼机中进行预混。
预混时间约为5分钟,温度控制在110-130℃。
2.将丁二酸二丁酯、酸性活化剂、抗氧剂、防火剂和空气分散剂逐一加入预混橡胶中,并进行均匀混合。
混合时间约为15分钟,温度控制在110-130℃。
3.将硫化剂加入混合橡胶中,并继续混合20分钟,温度保持在110-130℃。
4.将混合橡胶取出,放入橡胶成型机中进行成型。
成型时可采用挤出、压延或注塑等方法。
5.成型后的橡胶制品放置在恒温恒湿条件下进行硫化。
硫化温度为140℃,时间根据制品大小而定,一般为20-30分钟。
6.经硫化后的橡胶制品经冷却后即可包装出库。
这两种配方可以根据具体的应用需求和工艺要求进行调整,比例也可以根据实际需要进行微调。
配方中的增塑剂、促进剂、抗老化剂、防火剂、空气分散剂和硫化剂的种类和用量可以根据橡胶制品的性能要求来选择。
橡胶配方——精选推荐
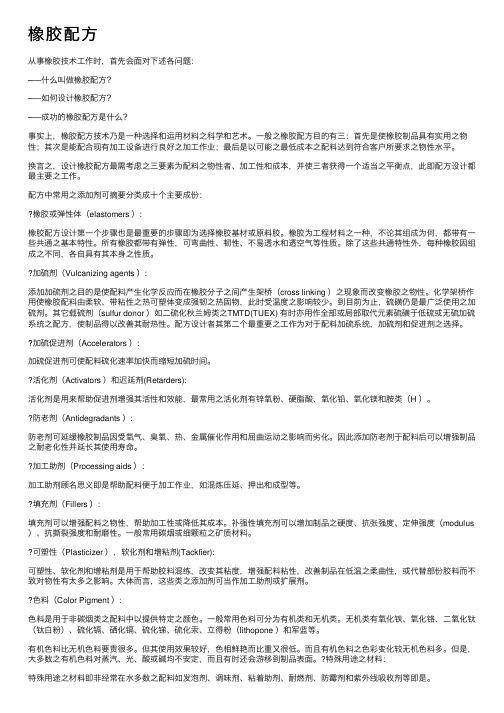
橡胶配⽅从事橡胶技术⼯作时,⾸先会⾯对下述各问题:─—什么叫做橡胶配⽅?─—如何设计橡胶配⽅?─—成功的橡胶配⽅是什么?事实上,橡胶配⽅技术乃是⼀种选择和运⽤材料之科学和艺术。
⼀般之橡胶配⽅⽬的有三:⾸先是使橡胶制品具有实⽤之物性;其次是能配合现有加⼯设备进⾏良好之加⼯作业;最后是以可能之最低成本之配料达到符合客户所要求之物性⽔平。
换⾔之,设计橡胶配⽅最需考虑之三要素为配料之物性者、加⼯性和成本,并使三者获得⼀个适当之平衡点,此即配⽅设计都最主要之⼯作。
配⽅中常⽤之添加剂可摘要分类成⼗个主要成份:橡胶或弹性体(elastomers ):橡胶配⽅设计第⼀个步骤也是最重要的步骤即为选择橡胶基材或原料胶。
橡胶为⼯程材料之⼀种,不论其组成为何,都带有⼀些共通之基本特性。
所有橡胶都带有弹性,可弯曲性、韧性、不易透⽔和透空⽓等性质。
除了这些共通特性外,每种橡胶因组成之不同,各⾃具有其本⾝之性质。
加硫剂(Vulcanizing agents ):添加加硫剂之⽬的是使配料产⽣化学反应⽽在橡胶分⼦之间产⽣架桥(cross linking )之现象⽽改变橡胶之物性。
化学架桥作⽤使橡胶配料由柔软、带粘性之热可塑体变成强韧之热固物,此时受温度之影响较少。
到⽬前为⽌,硫磺仍是最⼴泛使⽤之加硫剂。
其它载硫剂(sulfur donor )如⼆硫化秋兰姆类之TMTD(TUEX) 有时亦⽤作全部或局部取代元素硫磺于低硫或⽆硫加硫系统之配⽅,使制品得以改善其耐热性。
配⽅设计者其第⼆个最重要之⼯作为对于配料加硫系统,加硫剂和促进剂之选择。
加硫促进剂(Accelerators ):加硫促进剂可使配料硫化速率加快⽽缩短加硫时间。
活化剂(Activators )和迟延剂(Retarders):活化剂是⽤来帮助促进剂增强其活性和效能,最常⽤之活化剂有锌氧粉、硬脂酸、氧化铅、氧化镁和胺类(H )。
防⽼剂(Antidegradants ):防⽼剂可延缓橡胶制品因受氧⽓、臭氧、热、⾦属催化作⽤和屈曲运动之影响⽽劣化。
通用橡胶配方集锦_一_王作龄
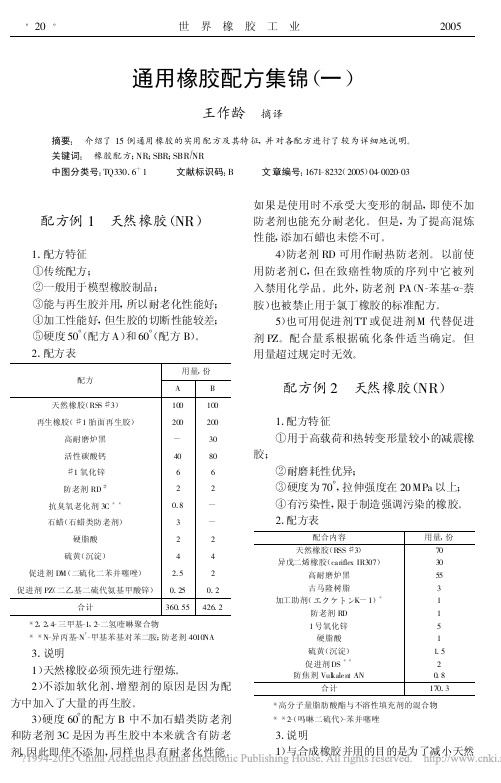
配方例 1 天然橡胶(NR)
1 .配方特征 ①传统配方 ; ②一般用于模型橡胶制品 ;
③能与再生胶并用 , 所以耐老化性能好 ; ④加工性能好 , 但生胶的切断性能较差 ; ⑤硬度 50°(配方 A)和 60°(配方 B)。 2 .配方表
配方
用量 , 份
A
B
天然橡胶(RSS #3)
100
100
再生橡胶(#1 胎面再生胶)
3)在将 EPDM 用于实用橡胶配方以前 , 除 了 CR 以外 , 设计污染性小的耐臭氧橡胶配方 比较困难 。 通过将防老剂 NBC 和石蜡类防老 剂并用 , 经臭氧浓度为 50 PPhm , 老化时间 48 h 的臭氧试验后符合使用要求 。有轻微污染性 。 防老剂 NBC 的用量超过 1 .5 份时产生污染 。
No 12. 3 Заявка на пат.2293419 Beликобритании, МКИ F 16C
33 20.Oпубл.27.03.1996 . 4 Пат.2108496 Pоссии, МКИ 16C 17 02 .Oпубл.10.04 .
1998 .бюл.N o 10. 5 Baukasten fbrErwachsene , [ J] .Produktion .— .1999.—
4)防老剂 RD 可用作耐热防老剂 。 以前使 用防老剂 C , 但在致癌性物质的序列中它被列 入禁用化学品 。此外 , 防老剂 PA(N-苯基-α-萘 胺)也被禁止用于氯丁橡胶的标准配方 。
5)也可用促进剂 TT 或促进剂 M 代替促进 剂 PZ 。配合量系根据硫 化条件适当确定 。 但 用量超过规定时无效 。
4)为了使胶料充分硫化 , 在添加了大量陶 土 、白 炭 黑 等 的 胶 料 中 使 用 有 机 胺 活 性 剂 (Acting B)。此外 , 二甘醇也可用作活性剂 。
三元乙丙橡胶配方集锦
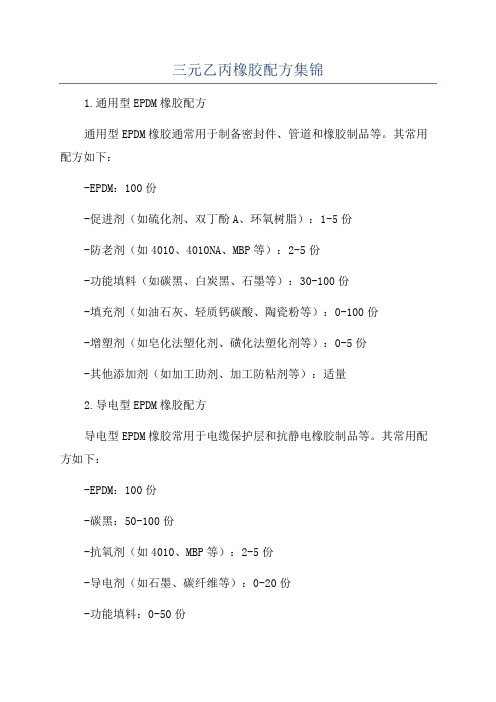
三元乙丙橡胶配方集锦1.通用型EPDM橡胶配方通用型EPDM橡胶通常用于制备密封件、管道和橡胶制品等。
其常用配方如下:-EPDM:100份-促进剂(如硫化剂、双丁酚A、环氧树脂):1-5份-防老剂(如4010、4010NA、MBP等):2-5份-功能填料(如碳黑、白炭黑、石墨等):30-100份-填充剂(如油石灰、轻质钙碳酸、陶瓷粉等):0-100份-增塑剂(如皂化法塑化剂、磺化法塑化剂等):0-5份-其他添加剂(如加工助剂、加工防粘剂等):适量2.导电型EPDM橡胶配方导电型EPDM橡胶常用于电缆保护层和抗静电橡胶制品等。
其常用配方如下:-EPDM:100份-碳黑:50-100份-抗氧剂(如4010、MBP等):2-5份-导电剂(如石墨、碳纤维等):0-20份-功能填料:0-50份-增塑剂:0-5份-其他添加剂:适量3.耐油型EPDM橡胶配方耐油型EPDM橡胶常用于汽车零部件、密封件和油管等。
其常用配方如下:-EPDM:100份-碳黑:50-100份-抗老剂(如4010、4010NA等):2-5份-功能填料:0-50份-耐油剂(如PAO、磺化法可塑化剂等):10-20份-防撕裂剂:0-5份-填充剂:0-100份-其他添加剂:适量4.抗臭气型EPDM橡胶配方抗臭气型EPDM橡胶通常应用于污水处理设备、汽车内饰件等需要抗臭气侵蚀的场合。
其常用配方如下:-EPDM:100份-碳黑:50-100份-功能填料:0-50份-抗臭气剂(如ZnO、二氧化锆等):10-20份-填充剂:0-100份-增塑剂:0-5份-其他添加剂:适量这几种EPDM橡胶的配方只是基础参考配方,具体的配方设计需要根据产品的具体要求和应用环境来确定。
此外,还应根据实际生产情况进行试验和调整,以确保最终产品的性能和质量。
常用橡胶制品的配方与工艺
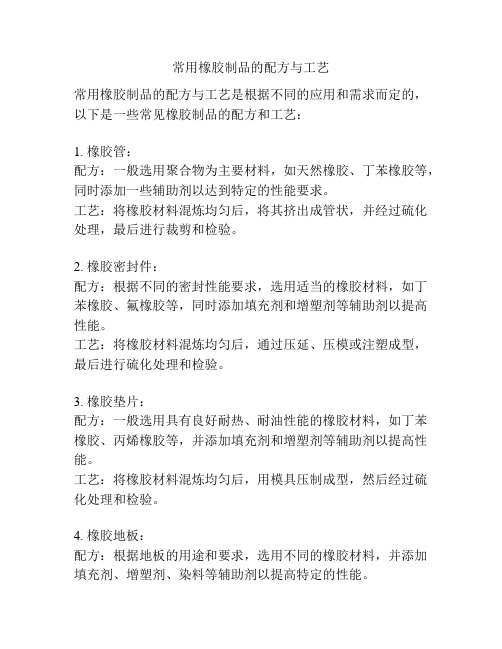
常用橡胶制品的配方与工艺
常用橡胶制品的配方与工艺是根据不同的应用和需求而定的,以下是一些常见橡胶制品的配方和工艺:
1. 橡胶管:
配方:一般选用聚合物为主要材料,如天然橡胶、丁苯橡胶等,同时添加一些辅助剂以达到特定的性能要求。
工艺:将橡胶材料混炼均匀后,将其挤出成管状,并经过硫化处理,最后进行裁剪和检验。
2. 橡胶密封件:
配方:根据不同的密封性能要求,选用适当的橡胶材料,如丁苯橡胶、氟橡胶等,同时添加填充剂和增塑剂等辅助剂以提高性能。
工艺:将橡胶材料混炼均匀后,通过压延、压模或注塑成型,最后进行硫化处理和检验。
3. 橡胶垫片:
配方:一般选用具有良好耐热、耐油性能的橡胶材料,如丁苯橡胶、丙烯橡胶等,并添加填充剂和增塑剂等辅助剂以提高性能。
工艺:将橡胶材料混炼均匀后,用模具压制成型,然后经过硫化处理和检验。
4. 橡胶地板:
配方:根据地板的用途和要求,选用不同的橡胶材料,并添加填充剂、增塑剂、染料等辅助剂以提高特定的性能。
工艺:将橡胶材料混炼均匀后,通过模压、挤出或涂布等工艺进行成型,经过硫化处理和检验后,进行平整和切割。
以上仅是一些常见橡胶制品的配方和工艺,实际上还有许多其他类型的橡胶制品,其配方和工艺也会有所不同。
需要根据具体的产品要求和生产工艺进行调整和优化。
各种橡胶的基础配方
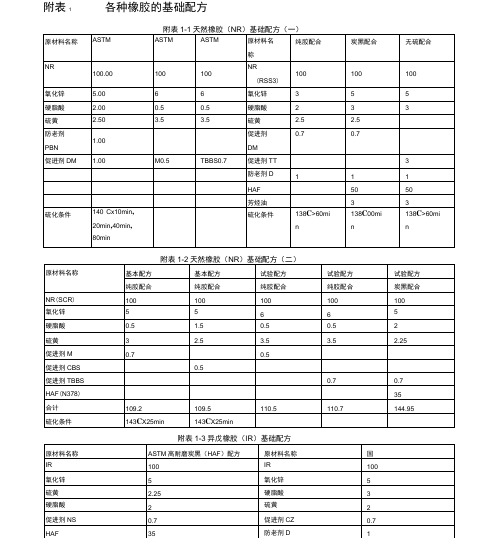
附表1各种橡胶的基础配方
附表1-1天然橡胶(NR)基础配方(一)
附表1-2天然橡胶(NR)基础配方(二)
附表1-3异戊橡胶(IR)基础配方
附表1-4丁苯橡胶(SBR )基础配方(ASTM )(一
①N-叔丁基-2-苯并噻唑次磺酰胺。
②phr 指每百质量份橡胶的质量份数。
附表1-5丁苯橡胶(SBR )基础配方(二)
附表1-6氯丁橡胶(CR )基础配方
附表1-7丁基橡胶(IIR)基础配方
附表1-8丁腈橡胶(NBR)基础配方
附表1-9顺丁橡胶(BR)基础配方
注:硫化条件在第三单体为DCDP时为160CX30min,40min;第三单体为ENB时为160C X10min,20min。
附表1-11氯磺化聚乙烯(CSM)基础配方
附表1-12氯化丁塞橡胶(CIIR)基础配方
附表1-13聚硫橡胶(
②该胶主要单体为二氯乙烷、二氯乙基缩甲醛,系美国固态聚硫橡胶牌号,必须通过添加促进剂,在混炼前用开炼机薄通,进行化学塑解剂而塑炼。
附表1-14丙烯酸酯橡胶(ACM)基础配方
附表1-15混炼型聚氨酯橡胶(PUR)基础配方
①选择AdipreneCM(美国Dupont公司产品牌号)②促进剂DM与氧化锌的复合物。
表附表1-16氯醇橡胶(CO)基础配方
附表1-17氟橡胶(FKM)基础配方。
橡胶配方(摘录)【范本模板】

橡胶配方(摘录)一、橡胶的并用.无论是什么橡胶不可能具有十全十美的性能,使用部门往往对产品提出多方面的性能要求,为了满足此目的,而采用橡胶并用的方法。
如,为提高二烯烃类橡胶耐热、耐光老化性能,可加入氯磺化聚乙烯.丁睛橡胶的耐粙性很好,但耐寒性不好,若并用10%的天然胶,便可改善它的耐寒性。
在橡胶中并用高苯乙烯、改性酚醛树脂、三聚氰胺树脂等都可改善橡胶的补强性能.合成橡胶的工艺性能一般都不够好,特别是饱和较高的合成橡胶,无论是炼胶、压延、贴合、硫化等性能都比较差,所以常加入天然橡胶或树脂。
以改善其未硫化胶的加工性能。
如,丁苯橡胶加入5—20份低压聚乙烯,可减少丁苯橡胶的收缩率。
乙丙橡胶中加入酚醛树脂可提高粘性。
加入天然胶对一般合成橡胶的工艺性能都会有所改善。
为了改进工艺加工性能,并用天然胶或树脂的比例一般都在20%以下。
有些合成橡胶性能优良,但价格昂贵,在不损害原物性的前提下,并用其它橡胶或树脂是完全可行的,如,丁睛胶中并用聚氯乙烯或丁苯胶中掺入天然橡胶,都能起到这一作用.1. 橡胶并用必须具有一定的相溶性,对橡胶来说天然、顺丁、异戊橡胶等能以任何比例均一地混合,最终达到相溶状态。
而天然胶与丁基橡胶就不能均一地混合.若硬性机械地混合,所得硫化胶的实际使用性能会显着地下降,这是因为它们的相溶性很差。
并用体系最重要的因素是相溶性,从应用的观点来看,如果混合不均,非但达不到并用的目的,反而影响工艺加工,特别是硫化。
因此,并用问题的焦点是两种橡胶能否相互混合,以及混合后达到什么样的相容程度。
固体橡胶并用时,因橡胶本身粘度很大,高分子的布朗运动不像液体那么容易,扩散速度较慢,对大分子的位移造成很大的阻力,严重影响橡胶间的互容作用。
为此在工业生产中都采用机械力强化分子运动,用提高温度和加入软化剂的方法来降低粘度,以促进两种橡胶的混合,所以产物从宏观上来看虽没有相分离,但真正达到溶解状态也不是很多的,其原因包括下来有以下几点,橡胶的极性、内聚能密度、橡胶的结晶、橡胶的分子量等。
三元乙丙橡胶配方

三元乙丙橡胶配方1. 胶辊三元乙丙橡胶(301) 100氧化锌60硬脂酸1白炭黑20环烷油5松香7. 5促进剂CZ 2促进剂TETD 2促进剂TMTD 2硫黄0. 5合计200(以上均为质量份)硬度(邵尔A) 58 ;拉伸强度13. 5 MPa ;拉断伸长率860 %;压缩永久变形(70 ℃×22 h) 51. 1 %。
2. 低硬度胶料充油三元乙丙橡胶(6537) 200氧化锌5硬脂酸1炭黑N550 40石腊油5煅烧陶土60聚乙二醇5EG23 4硫黄1. 5合计321(以上均为质量份)硫化条件200 ℃×3 min ;硬度(邵尔A) 23 ;拉伸强度8. 5 MPa ;300 %定伸应力2 MPa ;撕裂强度12KNPm;压缩永久变形(70 ℃×22 h) 11 %。
3. 高硬度胶料三元乙丙橡胶(512) 100氧化锌5硬脂酸锌1. 5炭黑N762 270石腊油15低分子聚乙烯15石腊5促进剂BZ 1. 5促进剂DM 3促进剂TMTD 0. 8硫黄0. 7合计468. 3(以上均为质量份)硬度(邵尔A) 88 ;拉伸强度10. 2 MPa ;拉断伸长率18 %;125 ℃×70 h 后变化:硬度增加3 度,拉伸强度增加18 %;拉断伸长率减少33 %。
4.阻燃低压绝缘制品三元乙丙橡胶(501A) 100氧化锌5硬脂酸1煅烧陶土80石腊油10三氧化二锑10十溴二苯醚20DCP(40 %) 7对醌二肟1合计234(以上均为质量份)硫化条件160 ℃×15 min ;硬度(邵尔A) 56 ;拉伸强度7. 35 MPa ;300 %定伸应力3 MPa ;拉断伸长率800 %;体积电阻9 ×10- 14Ωcm;介电常数3. 67 ;介电损耗角正切0. 65 ×10 - 2 ;介电强度15 kVPmm。
5. 导电制品三元乙丙橡胶(301) 100氧化锌5硬脂酸1乙炔炭黑150环烷油60促进剂M 0. 5促进剂TMTM 1. 5硫黄1合计319(以上均为质量份)硫化条件160 ℃×30 min ;硬度(邵尔A) 85 ;拉伸强度10. 88 MPa ;300 %定伸应力10. 19 MPa ;拉断伸长率350 %;体积电阻3. 8 ×10 Ωcm。
典型橡胶制品配方实例

重量份
NBR
100
氧化锌
5
硬脂酸
炭黑N770
110
增塑剂DOP
10
防老剂OD
促进剂CZ
促进剂TT
硫黄
硫化胶物理性能
拉伸强度Mpa
扯断伸长率%
280
硬度〔邵A〕
79
压缩永久变形%
18
工业用密封胶配方
2005-6-30
组份
重量份
NBR
100
氧化锌
5
硬脂酸
1
炭黑N550
50
轻度碳酸钙
25
外表处理碳酸钙
tanδ(60℃)
tanδ(0℃)
轿车子午胎胎侧胶配方
2005-7-1
组份
重量份phr
NR(SMR20)
50
BR(Budene1207)
50
炭黑N660
50
环烷油641
12
酚醛增粘树脂
5
聚乙烯蜡
1
防老剂4020
防老剂RD
1
硬脂酸
1
氧化锌
3
促进剂NS
1
硫黄
2
硫化胶物理性能
拉伸强度MPa
300%定伸应力Mpa
2005-7-1
组份
重量份〔phr〕
NBR 35V
100
炭黑N550
50
硬质陶土Βιβλιοθήκη 100增塑剂35混合蜡
3
防老剂RD
氧化锌
3
硬脂酸
促进剂DM
1
促进剂DOTC
促进剂TMTD
硫黄
硫化胶物理性能
拉伸强度Mpa
200%定伸应力Mpa
- 1、下载文档前请自行甄别文档内容的完整性,平台不提供额外的编辑、内容补充、找答案等附加服务。
- 2、"仅部分预览"的文档,不可在线预览部分如存在完整性等问题,可反馈申请退款(可完整预览的文档不适用该条件!)。
- 3、如文档侵犯您的权益,请联系客服反馈,我们会尽快为您处理(人工客服工作时间:9:00-18:30)。
组份
重量份phr
SSBR1216
75
BR1207
25
白炭黑
16.5
炭黑
58.5
偶联剂
6.5
芳烃油
25
硬脂酸
2
氧化锌
2.5
防老剂4020
2.0
防老剂RD
1.5
促进剂NS
1.7
促进剂D
2.0
硫黄
1.7
硫化胶物理性能
拉伸强度MPa
19.3
扯断伸长率%
444
300%定伸应力Mpa
11.4
tanδ(60℃)
拉伸强度Mpa
23.1
20
300%定伸应力Mpa
11.9
8.33
扯断伸长率%
616
442
回弹性%
58.4
64.2
撕裂强度KN/m
86
70
阿克隆磨耗指数
206
59
斜交载重胎胎体胶配方
2005-7-1
组份
重量份
NR
100
炭黑N770
50
氧化锌
5
硬脂酸
2
防老剂4020
3
环烷油
8
促进剂NS
0.5
硫黄
2.5
硫化胶物理性能
1
---
促进剂CZ
---
1.8
防焦剂CTP
---
0.1
硫黄给予体DTDM
1
---
硫黄
3
1.4
硫化胶性能
拉伸强度Mpa
15.4
21.5
300%定伸应力Mpa
11.1
9.3
硬度(邵A)
55
58
扯断伸长率%
370
550
钢丝帘布层胶配方
2005-7-1
组份
重量份
NR(SMR)
100
炭黑N330
50
活性白炭黑
5.4
扯断伸长率%
620
硬度(BPA)
54
撕裂强度KN/M
31.5
轿车胎胎体胶料配方
2005-7-1
组份
重量份
CIIR1060
55
NR(SMR20)
45
炭黑660
55
环烷油641
5
酚醛树脂
8
均匀剂40MS
7
硬脂酸
1
氧化锌
3
石蜡
0.4
促进剂NS
1
硫化剂Vultac5
0.8
促进剂D
1
硫黄
0.75
胶料性能
扯断伸长率%
194
撕裂强度KN/m
44
静态粘合力(141℃×60min)N
473
斜交轮胎载重胎胎面胶配方
2005-7-1
组份
重量份
NR
60
40
BR
40
60
炭黑N220
55
55
操作油
15
15
氧化锌
5
5
硬脂酸
2
2
防老剂RD
2
2
防老剂4020
1
1
硫黄
2
2
促进剂NS
0.8
0.8
防焦剂CTP
0.1
0.1
硫化胶性能
0.05
tanδ(0℃)
0.11
轿车子午胎胎侧胶配方
2005-7-1
组份
重量份phr
NR(SMR20)
50
BR(Budene1207)
50
炭黑N660
50
环烷油641
12
酚醛增粘树脂
5
聚乙烯蜡
1
防老剂4020
2.5
防老剂RD
1
硬脂酸
1
氧化锌
3
促进剂NS
1
硫黄
2
硫化胶物理性能
拉伸强度MPa
13.8
300%定伸应力Mpa
10
活性氧化锌
6
防老剂4010NA
2.5
间苯二酚RS
1
甲醛给予体AS/F
1
钴-硼络合物Manobonclc-16
0.1
促进剂DZ
2
促进剂TMTD
0.1
硫黄
4.5
防焦剂CTP
0.3
硫化胶性能
拉伸强度Mpa
18.6
300%定伸应力Mpa
16.7
硬度(邵A)
78
回弹性%
38
撕裂强度N/4mm
248
钴盐增进钢丝帘线粘合胶料配方
典型橡胶制品配方实例
轿车子午胎不同补强体系胎面配方
2005-7-1
组份
I
II
III
高乙烯基溶聚丁苯胶
103
103
103
高顺式顺丁胶
25
25
25
炭黑N347
85
高分散白炭黑
70
标准白炭黑
70
硅烷偶联剂
---
11.2
11.2
氧化锌
1.5
1.5
1.5
硬脂酸
1
1
1
防老剂4020
2
2
2
硫黄
1.5
1.5
1.5
促进剂CZ
20.4
拉伸强度Mpa
28.86
24.93
300%定伸应力Mpa
12.56
11.2
扯断伸长率%
574
536
硬度(邵A)
61
59
流变仪返原(降低2个转矩单位)
3.9
9.5
裤形撕裂N
8.9
17
地硫胶撕裂N
7
12
老化后撕裂(100℃×48h)
5
8.7
载重胎胎侧抗臭氧胶料配方
2005-7-1
组份
重量份(phr)
拉伸强度Mpa
23.81
300%定伸应力Mpa
8.13
1.25
1.25
1.25
促进剂D
1.25
1.25
1.25
硫化胶物理性能
硬度邵尔A
72
73
71
滚动阻力tanδ(70℃)
0.262
0.129
0.12
湿牵引性tanδ(0℃)
0.72
0.732
0.651
DIN磨耗损失%
137
124
135
全天候轿车胎胎面胶配方
2005-7-1
组份
重量份(phr)
SBR1712
2005-7-1
组份
重量份
NR
100
活性剂PCTP
0.15
炭黑N326
55
芳烃油
12
白炭黑
10.5
氧化锌
8
硬脂酸
0.75
防老剂4020
2
防老剂BLE
1
树脂PF
2.5
HMMM
3.5
不溶性硫黄
6
促进进剂DZ
0.8
防焦剂CTP
0.1
树脂
2
钴盐monobond680C
0.25
硫化胶性能
拉伸强度Mpa
15.6
拉伸强度Mpa
13
300%定伸强度Mpa
6.1
扯断伸率%
570
硬度(邵A)
57
粘合液
胶料撕裂
轿车子午胎气密层胶料配方
2005-7-1
组份
重量份(phr)
BIIR
100
炭黑N762
60
操作油
15
氧化锌
4
硬脂酸
1
增粘树脂
4
促进剂DM
2
硫黄
0.5
胶料物理性能
拉伸强度Mpa
10.2
100%定伸应力Mpa
1
扯断伸长率%
25%拉伸
72极轻微龟裂
载重子午胎胎面基部胶配方
2005-7-1
组份
重量份
NR
60
100
BR
40
Renacil7 0.15
炭黑N660
45
---
炭黑N220
---
20
白炭黑VN3
---
25
硅烷偶联剂Si-69
---
4
氧化锌
5
5
硬脂酸
1.5
3
防老剂4020
1.5
1.5
环烷油
6
---
蜡
0.5
---
促进剂NS
82.5
NR(SMR20)
20
BR
20
炭黑N234
65
高芳烃油
22.5
氧化锌
4
硬脂酸
2
防老剂4010NA
1.5
微晶蜡
1
硫黄
2
促进剂NS
1.2
促进剂TMTD80
0.15
硫化胶物理性能
硬度(国际硬度)
61
拉伸强度MPa
20
300%定伸应力Mpa
6.8
扯断伸长率%
615
回弹性(登录普)℃23%
46.2
轿车胎低滚动阻力胎面配方
NR
55
BR
45
炭黑N660
50
氧化锌
3
硬脂酸
1.5
环烷油
7
防老剂4020
3
石蜡
2
促进剂NS
1
不溶性硫黄(80%)
2