【塑料橡胶制品】配方设计与橡胶硬度的关系
橡胶制品配方设计与胶料工艺性能的关系
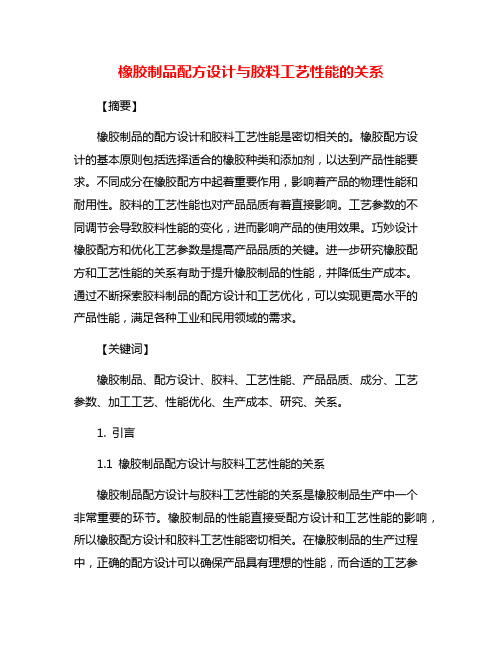
橡胶制品配方设计与胶料工艺性能的关系【摘要】橡胶制品的配方设计和胶料工艺性能是密切相关的。
橡胶配方设计的基本原则包括选择适合的橡胶种类和添加剂,以达到产品性能要求。
不同成分在橡胶配方中起着重要作用,影响着产品的物理性能和耐用性。
胶料的工艺性能也对产品品质有着直接影响。
工艺参数的不同调节会导致胶料性能的变化,进而影响产品的使用效果。
巧妙设计橡胶配方和优化工艺参数是提高产品品质的关键。
进一步研究橡胶配方和工艺性能的关系有助于提升橡胶制品的性能,并降低生产成本。
通过不断探索胶料制品的配方设计和工艺优化,可以实现更高水平的产品性能,满足各种工业和民用领域的需求。
【关键词】橡胶制品、配方设计、胶料、工艺性能、产品品质、成分、工艺参数、加工工艺、性能优化、生产成本、研究、关系。
1. 引言1.1 橡胶制品配方设计与胶料工艺性能的关系橡胶制品配方设计与胶料工艺性能的关系是橡胶制品生产中一个非常重要的环节。
橡胶制品的性能直接受配方设计和工艺性能的影响,所以橡胶配方设计和胶料工艺性能密切相关。
在橡胶制品的生产过程中,正确的配方设计可以确保产品具有理想的性能,而合适的工艺参数可以保证产品质量的稳定和提高生产效率。
了解橡胶配方设计和工艺性能之间的关系对于生产优质橡胶制品至关重要。
2. 正文2.1 橡胶配方设计的基本原则橡胶配方设计的基本原则是橡胶制品生产中至关重要的一环。
一个合理设计的橡胶配方能够确保产品的性能稳定和优良,同时也能够提高生产效率和降低成本。
在进行橡胶配方设计时,需要考虑以下几个基本原则:1. 成分选择:橡胶制品的性能很大程度上取决于配方中所选的橡胶种类、填料、增塑剂、硫化剂等成分。
需要根据产品的用途和要求来选择合适的成分,确保产品具有所需的力学性能、耐热性、耐老化性等特性。
2. 比例控制:各种成分在橡胶配方中的配比是影响产品性能的关键因素之一。
合理的比例能够保证产品的物理和化学性能达到最佳状态,过高或过低的比例都会导致产品性能下降甚至失效。
橡胶制品配方设计与胶料工艺性能的关系

橡胶制品配方设计与胶料工艺性能的关系橡胶制品是一种重要的工业原材料,广泛应用于汽车制造、电子设备、建筑材料等领域。
而橡胶制品的性能,很大程度上取决于配方设计和胶料的工艺性能。
本文将从橡胶制品配方设计与胶料工艺性能的关系进行分析,探讨影响橡胶制品性能的因素以及如何优化配方设计和胶料工艺性能。
1. 橡胶制品配方设计橡胶制品的性能由配方设计决定,配方设计包括橡胶原料的选择、添加剂的使用和配比的确定。
橡胶原料是橡胶制品的主要组成部分,其种类和质量直接影响到橡胶制品的性能。
常用的橡胶原料包括天然橡胶、合成橡胶和再生橡胶等,它们之间的性能差异较大,需根据具体的应用场景选择合适的橡胶原料。
添加剂是为了改善橡胶制品的特定性能而添加的物质,包括增塑剂、防老剂、硫化剂、填料等,其种类和用量也会影响橡胶制品的性能。
配比的确定是指各种原料和添加剂的比例,不同的配比会导致橡胶制品性能的差异,需要在实际生产过程中进行精细调整。
2. 胶料工艺性能胶料工艺性能是指橡胶原料在橡胶制品生产过程中的加工性能,包括塑炼性能、硫化性能和成型性能等。
塑炼性能是橡胶原料在混炼机中的分散性能和流动性能,它直接关系到橡胶混炼的均匀性和硫化后的性能稳定性。
硫化性能是指橡胶原料在硫化过程中的交联程度和硫化速度,它会影响橡胶制品的硬度、强度和耐磨性等。
成型性能是指橡胶原料在成型过程中的流动性和填充性能,它直接关系到橡胶制品的成型质量和外观。
配方设计和胶料工艺性能之间存在着密切的关系,配方设计的好坏会直接影响胶料工艺性能,而胶料工艺性能的优劣也会反过来影响橡胶制品的性能。
一方面,合理的配方设计可以提高橡胶原料的塑炼性能和硫化性能,使得橡胶原料更容易加工成优质的橡胶制品。
良好的胶料工艺性能可以保证橡胶原料在生产过程中有较好的流动性和填充性能,从而保证橡胶制品的成型质量。
4. 优化配方设计和胶料工艺性能的方法为了获得优质的橡胶制品,需要不断优化配方设计和胶料工艺性能。
橡胶成型技术-配方设计

五、配方设计的内容、原则与程 序
基础配方(标准配方)仅包括最基本的组分,采用传统的配合量,以生胶和配合剂鉴定为 目的,反映胶料基本工艺性能及硫化胶基本物理机械性能的配方。
基础配方的获得:
(1)ASTM美国材料实验协会((American Society of Testing Materials )标准
一、橡胶配方设计的概念
所谓橡胶配方设计,就是根据橡胶产品的性能要求和工 艺条件合理选用原材料,确定各种原材料的用量配比关系, 使得胶料的物性、工艺性和成本三者取得最佳平衡。
橡胶配方:生胶和多种配合剂按照一定比例的一种组合。
配方设计的意义
(1)决定产品成本及质量 (2)保证加工过程的顺利进行
例:设计胶管的内层胶
五、配方设计的内容、原则与程 序
(一)配方设计的内容
1、确定硫化胶的主要性能及性能指标范围
(1)已有成品:解剖成品,测试性能 (2)无成品:借鉴同类或相似产品或计算机模拟分析提出
2、确定合适的工艺条件及指标值的范围(实验确定) 3、确定主体材料和配合剂的品种与用量 4、确定原材料的指标范围
实验研究确定,参考原材料出厂检测指标,以满足制品 性能要求为准。
ZnO
St S 促M 防DPPD 重钙
合计
单价pi /(元/kg)
18 8 6.5 14 6 1.8 16 32 0.35
——
密度ρi /(g/cm3)
0.94 1.8 1 5.57 0.85 2 1.52 1.28 2.8
——
体积 /cm3
106.38 27.78 5.00 0.90 1.18 0.75 0.66 0.78 17.86
原材料 名称
NR S 促M
橡胶硬度配方估算及调整

橡胶硬度配方估算及调整
橡胶硬度是衡量橡胶材料刚度的一个重要指标,它反映了橡胶材料在受力后抵抗形变的能力。
在橡胶制品的研发和生产过程中,硬度是一个需要严格控制的物理性能指标。
为了估算和调整橡胶硬度,可以采用以下配方:
1. 生胶体系:选择适当的胶种和配方比例,可以调节橡胶的硬度。
例如,增加高苯乙烯、PVC/NBR合金的用量可以提高硬度。
2. 硫化促进体系:通过增加硫化剂的用量,可以提高交链密度,从而提高硬度。
例如,在生产再生橡胶制品时,加入相应硫磺用量可在一定程度上提高橡胶制品硬度。
3. 补强填充体系:添加炭黑作为填充剂,可以显著影响橡胶制品的硬度。
通过更换炭黑品种或添加胶粉,可以在保持含胶率不变的前提下,大幅增加硬度。
4. 增塑软化体系:调整橡胶油用量,可以改变橡胶制品的软化效果,从而提高硬度。
请注意,以上配方估算及调整方法仅供参考,实际应用中还需要考虑其他因素,如温度、压力、时间等。
同时,建议在专业人士指导下进行配方调整,以确保产品质量和安全性。
橡胶配方与各性能的关系
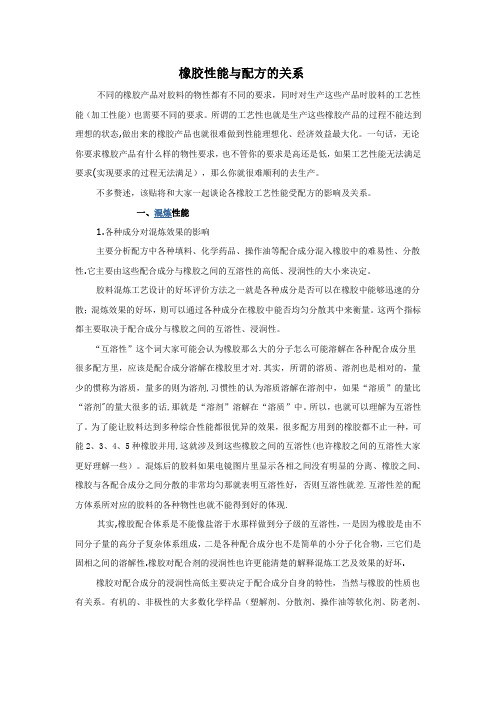
橡胶性能与配方的关系不同的橡胶产品对胶料的物性都有不同的要求,同时对生产这些产品时胶料的工艺性能(加工性能)也需要不同的要求。
所谓的工艺性也就是生产这些橡胶产品的过程不能达到理想的状态,做出来的橡胶产品也就很难做到性能理想化、经济效益最大化。
一句话,无论你要求橡胶产品有什么样的物性要求,也不管你的要求是高还是低,如果工艺性能无法满足要求(实现要求的过程无法满足),那么你就很难顺利的去生产。
不多赘述,该贴将和大家一起谈论各橡胶工艺性能受配方的影响及关系。
一、混炼性能1.各种成分对混炼效果的影响主要分析配方中各种填料、化学药品、操作油等配合成分混入橡胶中的难易性、分散性.它主要由这些配合成分与橡胶之间的互溶性的高低、浸润性的大小来决定。
胶料混炼工艺设计的好坏评价方法之一就是各种成分是否可以在橡胶中能够迅速的分散;混炼效果的好坏,则可以通过各种成分在橡胶中能否均匀分散其中来衡量。
这两个指标都主要取决于配合成分与橡胶之间的互溶性、浸润性。
“互溶性”这个词大家可能会认为橡胶那么大的分子怎么可能溶解在各种配合成分里很多配方里,应该是配合成分溶解在橡胶里才对.其实,所谓的溶质、溶剂也是相对的,量少的惯称为溶质,量多的则为溶剂,习惯性的认为溶质溶解在溶剂中,如果“溶质”的量比“溶剂"的量大很多的话,那就是“溶剂”溶解在“溶质”中。
所以,也就可以理解为互溶性了。
为了能让胶料达到多种综合性能都很优异的效果,很多配方用到的橡胶都不止一种,可能2、3、4、5种橡胶并用,这就涉及到这些橡胶之间的互溶性(也许橡胶之间的互溶性大家更好理解一些)。
混炼后的胶料如果电镜图片里显示各相之间没有明显的分离、橡胶之间、橡胶与各配合成分之间分散的非常均匀那就表明互溶性好,否则互溶性就差.互溶性差的配方体系所对应的胶料的各种物性也就不能得到好的体现.其实,橡胶配合体系是不能像盐溶于水那样做到分子级的互溶性,一是因为橡胶是由不同分子量的高分子复杂体系组成,二是各种配合成分也不是简单的小分子化合物,三它们是固相之间的溶解性.橡胶对配合剂的浸润性也许更能清楚的解释混炼工艺及效果的好坏.橡胶对配合成分的浸润性高低主要决定于配合成分自身的特性,当然与橡胶的性质也有关系。
橡胶制品配方设计与胶料工艺性能的关系
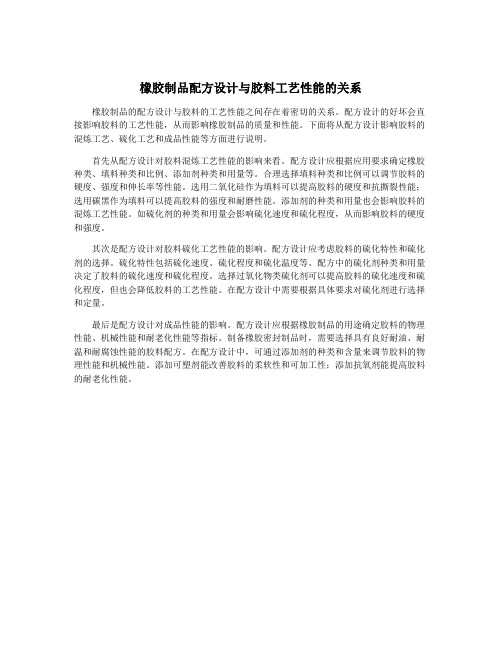
橡胶制品配方设计与胶料工艺性能的关系
橡胶制品的配方设计与胶料的工艺性能之间存在着密切的关系。
配方设计的好坏会直接影响胶料的工艺性能,从而影响橡胶制品的质量和性能。
下面将从配方设计影响胶料的混炼工艺、硫化工艺和成品性能等方面进行说明。
首先从配方设计对胶料混炼工艺性能的影响来看。
配方设计应根据应用要求确定橡胶种类、填料种类和比例、添加剂种类和用量等。
合理选择填料种类和比例可以调节胶料的硬度、强度和伸长率等性能。
选用二氧化硅作为填料可以提高胶料的硬度和抗撕裂性能;选用碳黑作为填料可以提高胶料的强度和耐磨性能。
添加剂的种类和用量也会影响胶料的混炼工艺性能。
如硫化剂的种类和用量会影响硫化速度和硫化程度,从而影响胶料的硬度和强度。
其次是配方设计对胶料硫化工艺性能的影响。
配方设计应考虑胶料的硫化特性和硫化剂的选择。
硫化特性包括硫化速度、硫化程度和硫化温度等。
配方中的硫化剂种类和用量决定了胶料的硫化速度和硫化程度。
选择过氧化物类硫化剂可以提高胶料的硫化速度和硫化程度,但也会降低胶料的工艺性能。
在配方设计中需要根据具体要求对硫化剂进行选择和定量。
最后是配方设计对成品性能的影响。
配方设计应根据橡胶制品的用途确定胶料的物理性能、机械性能和耐老化性能等指标。
制备橡胶密封制品时,需要选择具有良好耐油、耐温和耐腐蚀性能的胶料配方。
在配方设计中,可通过添加剂的种类和含量来调节胶料的物理性能和机械性能。
添加可塑剂能改善胶料的柔软性和可加工性;添加抗氧剂能提高胶料的耐老化性能。
橡胶工艺配方与制品性能的关系
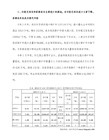
1.硫化胶受到交变应力作用时,材料的结构和性能发生变化的现象叫疲劳。随着疲劳过徎的进行,导至材料破坏的现象叫做疲劳破坏。
橡胶结构的影响,玻璃化温度低的橡胶耐疲劳性能好。有极性基团的橡胶耐疲劳性能差。分子内有庞大基团或侧基的橡胶,耐疲劳性能差、结构序列规整的橡胶,容易聚向结晶,耐疲劳性差。
弹性与填充体系有关,提高含胶率是提高弹性的最直接、最有效的办法,补强性越好的填充对弹性越不利。
弹性与软化剂的关系。软化剂与橡胶的相溶性有关,相溶性越小,弹性越差。如天然、顺丁、丁基加石腊油,优于加环烷油。丁睛加DOP优于使用环烷油、芳烃油。一般来说增塑剂会降低橡胶的弹性,应尽量少用增塑剂。
一、拉伸强度
橡胶技术咨询网为广大从事橡胶行业的朋友提供橡胶技术、橡胶价格信息、橡胶培训学习、橡胶资料交流学习交易的平台。我们努力打造一个橡胶人最喜爱的橡胶技术信息交流平台。
拉伸强度是制品能够抵抗拉伸破坏的根限能力。它是橡胶制品一个重要指标之一。许多橡胶制品的寿命都直接与拉伸强度有关。如输送带的盖胶、橡胶减震器的持久性都是随着拉伸强度的增加而提高的。
2.疲劳磨耗,与摩擦面相接触的硫化胶表面,在反复的过程中受周期性的压缩、剪切、拉伸等变形作用,使橡胶表面产生疲劳,并逐渐在其中产生微裂纹。这些裂纹的发展造成材料表面的微观剥落。疲劳磨耗随着橡胶的弹性模量、压力提高而增加,随着拉伸强度的降低而和疲劳性能变差而加大。
3.巻曲磨耗,橡胶下光滑的表面接触时,由于磨擦力的作用,使硫化胶表面不平的地方发生变形,并被撕裂破坏,成巻的脱落表面。
七、扯断伸长率(延伸率)
扯断伸长率与拉伸强度有关,只有具有较高的拉伸强度,保证其在变形过程中不受破坏,才会有较高的伸长率。一般随着定伸应力和硬度增大则扯断伸长率下降,回弹性大、永久变形小,则扯断伸长率大。不同的橡胶,它的扯断伸长率不同,天然胶它的含胶率在80%以上时它的扯断伸长率可达1000%。在形变时易产生塑性流动的橡胶也会有较高的伸长率。如丁基橡胶。
2020年(塑料橡胶材料)配方设计与橡胶硬度的关系

(塑料橡胶材料)配方设计与橡胶硬度的关系配方设计和橡胶硬度的关系配方设计和橡胶硬度的关系生胶品种硫化体系补强填充剂软化增塑剂邵尔A型硬度测定中的影响因素1.试样厚度的影响邵尔A型硬度值是由压针压入试样的深度来测定的,因此试样配方设计和橡胶硬度的关系·生胶品种·硫化体系·补强填充剂·软化增塑剂邵尔A型硬度测定中的影响因素1.试样厚度的影响邵尔A型硬度值是由压针压入试样的深度来测定的,因此试样厚度直接影响试验结果。
试样受到压力厚产生变形,受到压力的部位变薄,硬度值增大。
所以,试样厚度小硬度值达,试样厚度大硬度值小。
2.压针长度对试验结果的影响标准中规定邵尔A硬度计的压针露出加压面的高度为2.5mm,在自由状态时指针应指零点。
当压针在平滑的金属板或玻璃上时,仪器指针应指100度,如果指示大于或小于100度时,说明压针露出高度大于或小于2.5mm或小于2.5mm,这种情况下应停止使用,进行校正。
当压针露出高度大于2.5mm时测得的硬度值偏高。
3.压针端部形状对试验结果的影响邵尔A型硬度计的压针端部在长期作用下,造成磨损,使其几何尺寸改变,影响试验结果,磨损后的端部直径变大所测得结果也大,这是因为其单位面积的压强不同所致。
直径大则压强小所测得硬度值偏大,反之偏小。
4.温度对试验结果的影响橡胶为高分子材料,其硬度值随环境的变化而变化,温度高则硬度值降低。
胶料不同其影响程度不同,如结晶速度慢的天然橡胶,温度对其影响小些,而氯丁橡胶、丁苯橡胶等则影响显著。
5.读数时间的影响邵尔A型硬度计在测量时读数时间对试验结果影响很大。
压针和试样受压后立即读数和指针稳定后再读数,所得的结果相差很大,前者高,后者偏低,二者之差可达5至7度左右,尤其再合成橡胶测试中较为显著,这主要使胶料在受压后产生蠕变所致。
所以当试样受压后应立即读取数据。
目录壹.硬度的定义二.硬度的测试方法三.分别介绍几种硬度测试方法和相关单位四.各种硬度的区别壹.硬度的定义硬度——材料局部抵抗硬物压入其表面的能力称为硬度。
橡胶制品配方设计与胶料工艺性能的关系

橡胶制品配方设计与胶料工艺性能的关系
橡胶制品的配方设计是指根据用途要求,选用合适的橡胶粘合剂、增塑剂、助剂等原
材料,按照一定的比例配制成胶料的过程。
而从胶料工艺性能的角度来看,配方设计与胶
料工艺性能存在着密切的关系。
首先,配方设计的精度直接影响着胶料工艺性能。
如橡胶粘合剂的选择决定了胶料的
黏附性能,不同粘合剂的不同用量会导致不同的黏附力;增塑剂的使用量和种类也是影响
胶料硬度、柔韧性和耐久性等多种性能的关键因素。
如果配方设计不合理,过量或不足的
原料用量都可能导致胶料的性能出现异常,从而影响工艺性能。
其次,胶料工艺性能的优化需要依赖配方设计的优化。
在胶料加工过程中,如在挤出、压延或成型等工序中,容易出现黏性不足、熔体流动性不良、热稳定性低等工艺问题。
这时,需要根据工艺问题的具体情况,调整配方中的原材料种类和用量,以优化工艺性能。
最后,配方设计的改进还能够提高胶料产品的市场竞争力。
通过改变原材料的种类和
比例,可以提升胶料产品的性能特点,例如提高强度、耐磨性、耐寒性等。
这些性能的提
升可以增进产品的品质和成本效益,帮助企业在市场中取得更大的生存空间。
综上所述,橡胶制品配方设计与胶料工艺性能之间存在着紧密的联系。
一个科学合理
的配方设计能够保证胶料的优良性能和优秀的工艺性能,进而提高产品的市场竞争力。
橡胶配方设计与性能的关系-参考模板
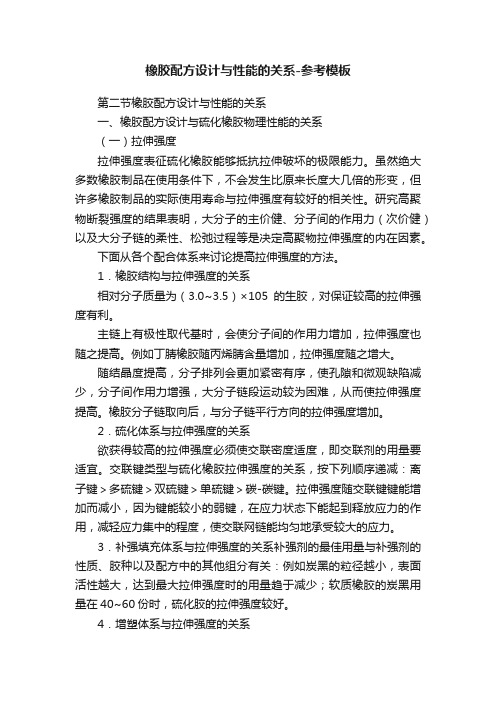
橡胶配方设计与性能的关系-参考模板第二节橡胶配方设计与性能的关系一、橡胶配方设计与硫化橡胶物理性能的关系(一)拉伸强度拉伸强度表征硫化橡胶能够抵抗拉伸破坏的极限能力。
虽然绝大多数橡胶制品在使用条件下,不会发生比原来长度大几倍的形变,但许多橡胶制品的实际使用寿命与拉伸强度有较好的相关性。
研究高聚物断裂强度的结果表明,大分子的主价健、分子间的作用力(次价健)以及大分子链的柔性、松弛过程等是决定高聚物拉伸强度的内在因素。
下面从各个配合体系来讨论提高拉伸强度的方法。
1.橡胶结构与拉伸强度的关系相对分子质量为(3.0~3.5)×105的生胶,对保证较高的拉伸强度有利。
主链上有极性取代基时,会使分子间的作用力增加,拉伸强度也随之提高。
例如丁腈橡胶随丙烯腈含量增加,拉伸强度随之增大。
随结晶度提高,分子排列会更加紧密有序,使孔隙和微观缺陷减少,分子间作用力增强,大分子链段运动较为困难,从而使拉伸强度提高。
橡胶分子链取向后,与分子链平行方向的拉伸强度增加。
2.硫化体系与拉伸强度的关系欲获得较高的拉伸强度必须使交联密度适度,即交联剂的用量要适宜。
交联键类型与硫化橡胶拉伸强度的关系,按下列顺序递减:离子键>多硫键>双硫键>单硫键>碳-碳键。
拉伸强度随交联键键能增加而减小,因为键能较小的弱键,在应力状态下能起到释放应力的作用,减轻应力集中的程度,使交联网链能均匀地承受较大的应力。
3.补强填充体系与拉伸强度的关系补强剂的最佳用量与补强剂的性质、胶种以及配方中的其他组分有关:例如炭黑的粒径越小,表面活性越大,达到最大拉伸强度时的用量趋于减少;软质橡胶的炭黑用量在40~60份时,硫化胶的拉伸强度较好。
4.增塑体系与拉伸强度的关系总地来说,软化剂用量超过5份时,就会使硫化胶的拉伸强度降低。
对非极性的不饱和橡胶(如NR、IR、SBR、BR),芳烃油对其硫化胶的拉伸强度影响较小;石蜡油对它则有不良的影响;环烷油的影响介于两者之间。
橡胶配方设计与胶料工艺性能的关系
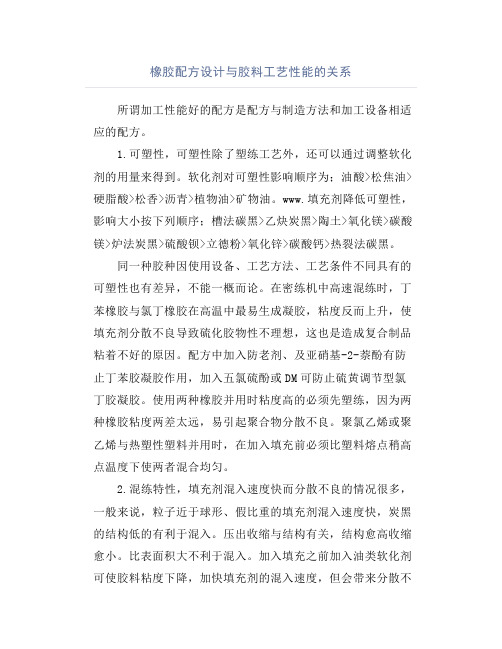
橡胶配方设计与胶料工艺性能的关系所谓加工性能好的配方是配方与制造方法和加工设备相适应的配方。
1.可塑性,可塑性除了塑练工艺外,还可以通过调整软化剂的用量来得到。
软化剂对可塑性影响顺序为;油酸>松焦油>硬脂酸>松香>沥青>植物油>矿物油。
www.填充剂降低可塑性,影响大小按下列顺序;槽法碳黑>乙炔炭黑>陶土>氧化镁>碳酸镁>炉法炭黑>硫酸钡>立德粉>氧化锌>碳酸钙>热裂法碳黑。
同一种胶种因使用设备、工艺方法、工艺条件不同具有的可塑性也有差异,不能一概而论。
在密练机中高速混练时,丁苯橡胶与氯丁橡胶在高温中最易生成凝胶,粘度反而上升,使填充剂分散不良导致硫化胶物性不理想,这也是造成复合制品粘着不好的原因。
配方中加入防老剂、及亚硝基-2-萘酚有防止丁苯胶凝胶作用,加入五氯硫酚或DM可防止硫黄调节型氯丁胶凝胶。
使用两种橡胶并用时粘度高的必须先塑练,因为两种橡胶粘度两差太远,易引起聚合物分散不良。
聚氯乙烯或聚乙烯与热塑性塑料并用时,在加入填充前必须比塑料熔点稍高点温度下使两者混合均匀。
2.混练特性,填充剂混入速度快而分散不良的情况很多,一般来说,粒子近于球形、假比重的填充剂混入速度快,炭黑的结构低的有利于混入。
压出收缩与结构有关,结构愈高收缩愈小。
比表面积大不利于混入。
加入填充之前加入油类软化剂可使胶料粘度下降,加快填充剂的混入速度,但会带来分散不良。
因此原则上是后加油。
高填充配方在混练时,可分批加入填充及油料。
从配方设计角度方面考滤,可选用分散良好的填充剂。
分散良好的填充剂应具备以下条件,A,补强性较小B相同配方中粒经较大C,含水份较少D,假比重较大E,具有异向性能F,碳黑结构度较高等。
操作油中芳烃含量高亦能促进分散。
促进剂一般易分散,但必须注意硫黄的分散。
3.包辊性。
强度高、粘性好、具有收缩性的生胶包辊性好,天然胶的粘性,强度高所以包辊性好,合成橡胶中除了氯丁橡胶外一般强度都很低,所以在配合上要多想办法,选择增加混练胶强度的填充剂,补强性高的炭黑、白炭黑、硬质陶土、碳酸镁、白艳华等。
橡胶刚度和硬度的关系
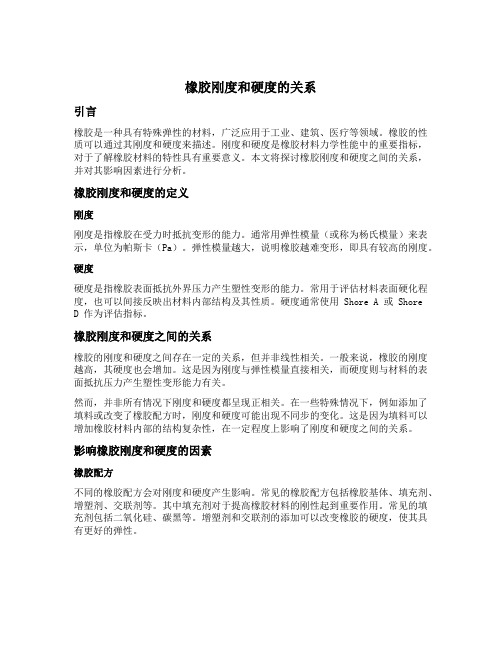
橡胶刚度和硬度的关系引言橡胶是一种具有特殊弹性的材料,广泛应用于工业、建筑、医疗等领域。
橡胶的性质可以通过其刚度和硬度来描述。
刚度和硬度是橡胶材料力学性能中的重要指标,对于了解橡胶材料的特性具有重要意义。
本文将探讨橡胶刚度和硬度之间的关系,并对其影响因素进行分析。
橡胶刚度和硬度的定义刚度刚度是指橡胶在受力时抵抗变形的能力。
通常用弹性模量(或称为杨氏模量)来表示,单位为帕斯卡(Pa)。
弹性模量越大,说明橡胶越难变形,即具有较高的刚度。
硬度硬度是指橡胶表面抵抗外界压力产生塑性变形的能力。
常用于评估材料表面硬化程度,也可以间接反映出材料内部结构及其性质。
硬度通常使用 Shore A 或 Shore D 作为评估指标。
橡胶刚度和硬度之间的关系橡胶的刚度和硬度之间存在一定的关系,但并非线性相关。
一般来说,橡胶的刚度越高,其硬度也会增加。
这是因为刚度与弹性模量直接相关,而硬度则与材料的表面抵抗压力产生塑性变形能力有关。
然而,并非所有情况下刚度和硬度都呈现正相关。
在一些特殊情况下,例如添加了填料或改变了橡胶配方时,刚度和硬度可能出现不同步的变化。
这是因为填料可以增加橡胶材料内部的结构复杂性,在一定程度上影响了刚度和硬度之间的关系。
影响橡胶刚度和硬度的因素橡胶配方不同的橡胶配方会对刚度和硬度产生影响。
常见的橡胶配方包括橡胶基体、填充剂、增塑剂、交联剂等。
其中填充剂对于提高橡胶材料的刚性起到重要作用。
常见的填充剂包括二氧化硅、碳黑等。
增塑剂和交联剂的添加可以改变橡胶的硬度,使其具有更好的弹性。
加工工艺橡胶的加工工艺也会对刚度和硬度产生影响。
例如,在橡胶成型过程中,温度、压力和时间等参数的不同调节会导致橡胶材料内部结构的变化,从而影响其刚度和硬度。
环境条件环境条件也会对橡胶材料的刚度和硬度产生一定影响。
例如,温度和湿度等因素都可以改变橡胶材料的物理性质,从而影响其刚度和硬度。
测试方法为了准确评估橡胶材料的刚度和硬度,常用以下测试方法:弹性模量测试弹性模量可以通过应力-应变关系来计算。
橡胶制品配方设计与胶料工艺性能的关系

橡胶制品配方设计与胶料工艺性能的关系
橡胶制品配方设计是指根据特定的应用要求和物料特性,合理选择不同的胶料和其他
助剂,并确定它们的比例,从而达到理想的性能要求的过程。
胶料工艺性能则是指橡胶制
品在加工过程中的可塑性、流动性、黏合性、热稳定性以及最终制品的耐磨性、耐老化性
等性能。
橡胶制品配方设计与胶料工艺性能之间存在着密切关系。
橡胶制品配方设计直接影响着胶料的工艺性能。
配方中的各种胶料之间存在相互作用,它们的相对比例以及添加顺序的不同都会对橡胶的可塑性和流动性产生影响。
合理的配方
设计可以提高橡胶的可加工性,使其更易于塑料化和润湿,有利于加工过程中胶料的填充
和流动,从而降低生产成本,提高生产效率。
橡胶制品的工艺性能还与工艺参数的选择息息相关。
温度、压力和时间等工艺参数对
胶料的流动性和黏合性有着重要的影响。
选择合适的工艺参数可以提高橡胶制品的成型效果,同时也会影响最终制品的物理性能。
橡胶制品的材质选择也会对胶料的工艺性能产生影响。
不同类型的橡胶具有不同的物
理和化学性质,如硬度、弹性、耐磨性、耐老化性等。
对于不同的应用领域,需要选择具
有相应性能的橡胶材料。
在橡胶制品配方设计中,选择合适的胶料材质对于提高胶料的工
艺性能至关重要。
橡胶配方设计和性能的关系

橡胶配方设计和性能的关系橡胶配方设计是指利用橡胶材料及其各类辅料,按一定比例、方法的程序组成一种可满足特定要求和使用条件下所需要的性能的胶料配方。
橡胶材料具有一定的可塑性、韧性、耐腐蚀性等特点,广泛应用于工业、医疗、交通等领域,其性能的好坏直接关系到产品的质量和使用效果。
因此,橡胶配方设计和性能之间的关系显得尤为重要。
首先,橡胶配方设计与性能之间的关系是密切相关的。
正确的配方能够使橡胶材料在不同的使用条件下,具备特定的性能,如高弹性、高耐磨、高耐温等。
而如果配方设计不合理,就会导致橡胶材料的性能不足。
例如,过多的填料会影响弹性和可塑性,过多的硫化剂会降低弹性,而过多的油会降低化学稳定性,从而导致产品的质量下降。
其次,橡胶配方设计中的各种辅料也会对性能产生影响。
例如,硫化剂是橡胶材料的重要辅料,能够决定硫化效果和耐老化性能。
同时,填料的粒度、形状和类型都会影响橡胶材料的性能。
根据不同类型和形状的填料,可以调整橡胶材料的力学性能、电气性能、导热性能等。
添加剂也是配方设计的重要因素,如促进剂、防老剂、消光剂等都能调整橡胶材料的性能。
最后,橡胶配方设计也需要考虑产品的使用条件。
橡胶制品在不同的使用环境和条件下,需要不同的性能。
例如,在高温下使用的产品需要具备高耐热性和防老化性能;在低温下使用的产品需要具备低温柔性和耐寒性。
不同的使用条件对橡胶材料和其配方设计都有很高的要求。
在应用时,需要针对不同的使用条件设计不同的配方,以满足产品的性能要求。
综上所述,橡胶配方设计与性能之间的关系是密不可分的。
正确的配方设计能够使橡胶材料具备所需的性能,并满足特定的使用条件。
因此,在橡胶制品的生产过程中,配方设计的重要性得到了越来越多的重视。
唯有具备正确的配方,才能生产出优质、高性能的橡胶制品。
配方设计和橡胶硬度的关系
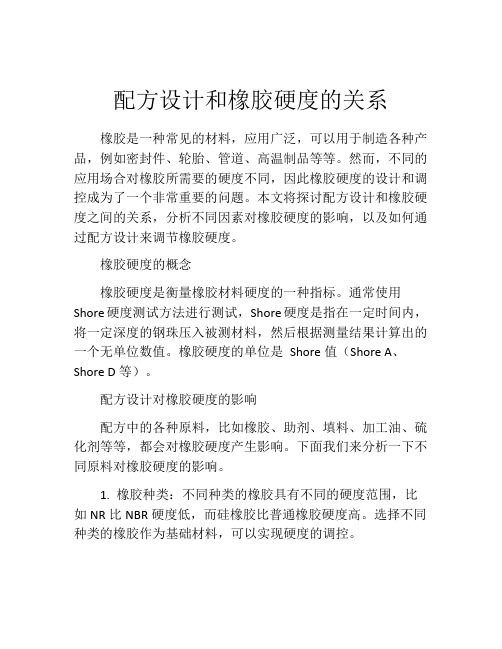
配方设计和橡胶硬度的关系橡胶是一种常见的材料,应用广泛,可以用于制造各种产品,例如密封件、轮胎、管道、高温制品等等。
然而,不同的应用场合对橡胶所需要的硬度不同,因此橡胶硬度的设计和调控成为了一个非常重要的问题。
本文将探讨配方设计和橡胶硬度之间的关系,分析不同因素对橡胶硬度的影响,以及如何通过配方设计来调节橡胶硬度。
橡胶硬度的概念橡胶硬度是衡量橡胶材料硬度的一种指标。
通常使用Shore硬度测试方法进行测试,Shore硬度是指在一定时间内,将一定深度的钢珠压入被测材料,然后根据测量结果计算出的一个无单位数值。
橡胶硬度的单位是Shore值(Shore A、Shore D等)。
配方设计对橡胶硬度的影响配方中的各种原料,比如橡胶、助剂、填料、加工油、硫化剂等等,都会对橡胶硬度产生影响。
下面我们来分析一下不同原料对橡胶硬度的影响。
1. 橡胶种类:不同种类的橡胶具有不同的硬度范围,比如NR比NBR硬度低,而硅橡胶比普通橡胶硬度高。
选择不同种类的橡胶作为基础材料,可以实现硬度的调控。
2. 助剂:比如加压剂、加硫促进剂、质量调节剂等等。
助剂的种类、用量和质量等都会影响到橡胶硬度。
例如,加压剂的用量越大,橡胶硬度越高;而加硫促进剂的种类和量,对橡胶硬度的变化也有影响。
3. 填料:常见的填料有碳黑、硅灰石、滑石粉、钛白粉等等。
填料的粒度、种类和用量都会影响到橡胶硬度。
例如,添加大颗粒的填料,可以增加橡胶硬度,而小颗粒的填料则相反。
4. 加工油:加工油的种类和用量也会对橡胶硬度产生影响。
例如某些加工油会增加橡胶软度,从而降低硬度。
5. 硫化剂:硫化剂是橡胶硬度的重要因素之一。
硫化剂的种类、用量和硫化时间都会影响橡胶硬度。
硫化剂用量越大、硫化时间越长,橡胶硬度越高。
通过配方设计调节橡胶硬度对于不同的应用场合,需要不同硬度的橡胶,因此需要通过配方设计来调节橡胶硬度。
一般来说,橡胶硬度的增加需要增加填料和硫化剂的用量,而减少助剂和加工油的用量。
浅析塑料与橡胶的关系

再生资源网/本文摘自再生资源回收-变宝网()浅析塑料与橡胶的关系塑料与橡胶同属于高分子材料,主要由碳和氢两种原子组成,另有一些含有少量氧,氮,氯,硅,氟,硫等原子,其性能特殊,用途也特别。
在常温下,塑料是固态,很硬,不能拉伸变形。
而橡胶硬度不高,有弹性,可拉伸变长,停止拉伸又可回复原状。
这是由于它们的分子结构不同造成的。
另一不同点是塑料可以多次回收重复使用,而橡胶则不能直接回收使用,只能经过加工制成再生胶,然后才可用,所以看到这里就明白它们的紧密关系。
①导热性橡胶是热的不良导体,其导热系数在厚度为25毫米时约为2.2~6.28瓦/米2·0K。
是优异的隔热材料,如果将橡胶做成微孔或海绵状态,其隔热效果会进一步提高,使导热系数下降至0.4~2.0瓦。
任何橡胶制件在使用中,都可能会因滞后损失产生热量,因此应注意散热。
②热膨胀由于橡胶分子链间有较大的自由体积,当温度升高时其链段的内旋转变易,会使其体积变大。
橡胶的线膨胀系数约是钢的20倍。
这在橡胶制品的硫化模型设计中必须加以考虑,因为橡胶成品的线性尺寸会比模型小1.2~3.5%。
对于同一种橡胶,胶料的硬度和生胶含量对胶料的收缩率也有较大的影响,收缩率与硬度成反比,与含胶率成正比。
各种橡胶在理论上的收缩率的大小顺序为:氟橡胶>硅橡胶>丁基橡胶>丁腈橡胶>氯丁橡胶>丁苯橡胶>天然橡胶,这也是为何在管道配件行业中选择橡胶作为主要原料的原因。
在当今橡胶工业发展日新月异的时候,世界橡胶工业的销售额已超过2500亿美元,橡胶制品早已成为国际贸易重要的大宗商品。
在世界市场上,橡胶产品已形成了轮胎为中心,以工业、建筑用品为重点,涉及胶鞋、胶布等日用制品以及医疗卫生、文化体育等各大类的产品群体。
本文摘自变宝网-废金属_废塑料_废纸_废品回收_再生资源B2B交易平台网站;变宝网官网:/?qxb买卖废品废料,再生料就上变宝网,什么废料都有!。
橡胶制品配方设计与胶料工艺性能的关系
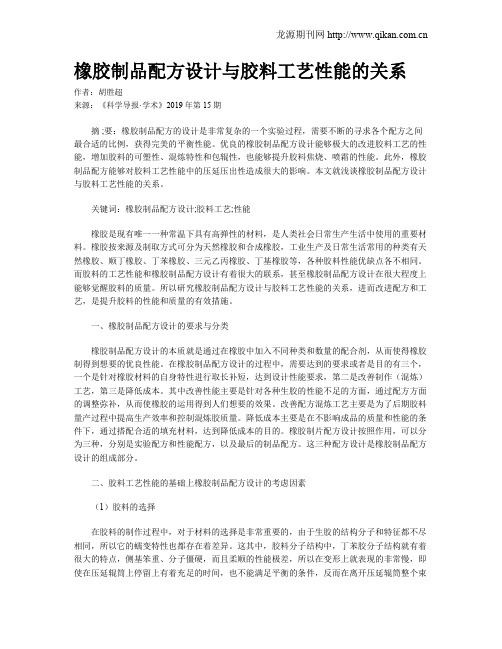
橡胶制品配方设计与胶料工艺性能的关系作者:胡胜超来源:《科学导报·学术》2019年第15期摘 ;要:橡胶制品配方的设计是非常复杂的一个实验过程,需要不断的寻求各个配方之间最合适的比例,获得完美的平衡性能。
优良的橡胶制品配方设计能够极大的改进胶料工艺的性能,增加胶料的可塑性、混炼特性和包辊性,也能够提升胶料焦烧、喷霜的性能。
此外,橡胶制品配方能够对胶料工艺性能中的压延压出性造成很大的影响。
本文就浅谈橡胶制品配方设计与胶料工艺性能的关系。
关键词:橡胶制品配方设计;胶料工艺;性能橡胶是现有唯一一种常温下具有高弹性的材料,是人类社会日常生产生活中使用的重要材料。
橡胶按来源及制取方式可分为天然橡胶和合成橡胶,工业生产及日常生活常用的种类有天然橡胶、顺丁橡胶、丁苯橡胶、三元乙丙橡胶、丁基橡胶等,各种胶料性能优缺点各不相同。
而胶料的工艺性能和橡胶制品配方设计有着很大的联系,甚至橡胶制品配方设计在很大程度上能够觉醒胶料的质量。
所以研究橡胶制品配方设计与胶料工艺性能的关系,进而改进配方和工艺,是提升胶料的性能和质量的有效措施。
一、橡胶制品配方设计的要求与分类橡胶制品配方设计的本质就是通过在橡胶中加入不同种类和数量的配合剂,从而使得橡胶制得到想要的优良性能。
在橡胶制品配方设计的过程中,需要达到的要求或者是目的有三个,一个是针对橡胶材料的自身特性进行取长补短,达到设计性能要求,第二是改善制作(混炼)工艺,第三是降低成本。
其中改善性能主要是针对各种生胶的性能不足的方面,通过配方方面的调整弥补,从而使橡胶的运用得到人们想要的效果。
改善配方混炼工艺主要是为了后期胶料量产过程中提高生产效率和控制混炼胶质量。
降低成本主要是在不影响成品的质量和性能的条件下,通过搭配合适的填充材料,达到降低成本的目的。
橡胶制片配方设计按照作用,可以分为三种,分别是实验配方和性能配方,以及最后的制品配方。
这三种配方设计是橡胶制品配方设计的组成部分。
橡胶配方设计与性能的关系

橡胶配方设计与性能的关系橡胶配方设计是橡胶制品生产中的一项重要任务,它是指将橡胶材料与各种添加剂按一定比例混合,在特定条件下加工成所需的橡胶制品。
橡胶配方设计的好坏直接影响着橡胶制品的性能,包括力学性能、物理性能、耐热性、耐寒性、耐油性、耐腐蚀性等指标,因此橡胶配方设计与性能的关系是非常密切的。
一、橡胶配方设计对力学性能影响橡胶制品的力学性能主要包括抗张强度、伸长率、硬度、耐磨性等指标。
橡胶配方中的填料和活性剂的种类和用量会直接影响橡胶制品的力学性能。
例如,碳黑是一种高性能填料,可以提高橡胶制品的硬度和耐磨性,但其加入量过多会导致制品拉力强度下降;而硅酸盐填料具有良好的增强作用,但是其与橡胶材料的界面相互作用弱,易剥离,导致其加入量也要控制在一定范围之内。
二、橡胶配方设计对物理性能影响橡胶制品的物理性能主要包括硬度、韧性、耐裂、耐寒性等,这些性能也和橡胶配方设计有着密切的关系。
其中,增塑剂和软化剂的种类和用量会直接影响橡胶制品的膨胀率、可变形率、疲劳性能等,不同的配方会导致橡胶制品在压缩、拉伸等状态下具有不同的变形量和变形后恢复速度。
此外,橡胶配方中加入的抗氧剂、防老剂、抗紫外线剂等助剂也会对橡胶制品的物理性能产生直接影响。
三、橡胶配方设计对耐热性、耐寒性等特殊性能影响橡胶配方设计也会对橡胶制品的耐热性、耐寒性等特殊性能产生影响。
对于具有耐热性要求的橡胶制品,要采用具有耐高温性的材料和助剂,例如草酸钙、氧化锆等高温助剂。
对于具有耐寒性要求的橡胶制品,要采取附加的配方设计,增加含量和分子量、活性剂的种类和数量,以提高它的软化点和耐低温能力。
四、橡胶配方设计对钢丝绳等强度材料影响钢丝绳等强度材料所要用到的橡胶胶既要满足橡胶自身的力学性能,也要满足钢丝绳的强度要求。
此时在橡胶配方中还要添加一些增强剂而不影响橡胶的可加工性,这些增强剂通常是聚酰胺纤维、芳纶纤维等高强度纤维制品,在和橡胶混合后具有良好的增强作用。
橡胶刚度和硬度的关系
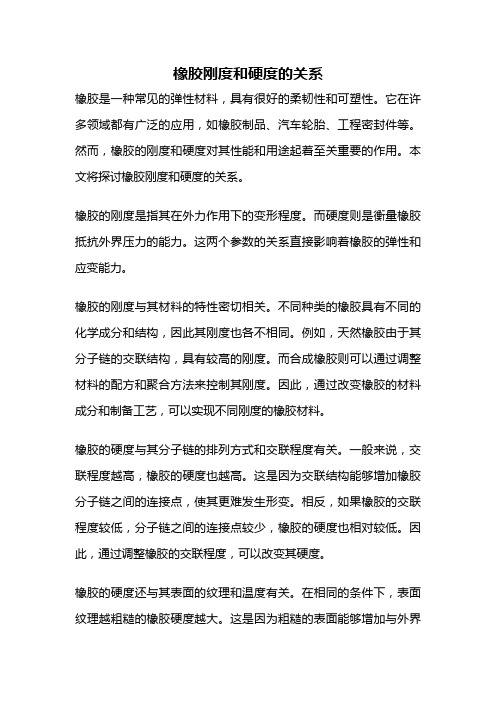
橡胶刚度和硬度的关系橡胶是一种常见的弹性材料,具有很好的柔韧性和可塑性。
它在许多领域都有广泛的应用,如橡胶制品、汽车轮胎、工程密封件等。
然而,橡胶的刚度和硬度对其性能和用途起着至关重要的作用。
本文将探讨橡胶刚度和硬度的关系。
橡胶的刚度是指其在外力作用下的变形程度。
而硬度则是衡量橡胶抵抗外界压力的能力。
这两个参数的关系直接影响着橡胶的弹性和应变能力。
橡胶的刚度与其材料的特性密切相关。
不同种类的橡胶具有不同的化学成分和结构,因此其刚度也各不相同。
例如,天然橡胶由于其分子链的交联结构,具有较高的刚度。
而合成橡胶则可以通过调整材料的配方和聚合方法来控制其刚度。
因此,通过改变橡胶的材料成分和制备工艺,可以实现不同刚度的橡胶材料。
橡胶的硬度与其分子链的排列方式和交联程度有关。
一般来说,交联程度越高,橡胶的硬度也越高。
这是因为交联结构能够增加橡胶分子链之间的连接点,使其更难发生形变。
相反,如果橡胶的交联程度较低,分子链之间的连接点较少,橡胶的硬度也相对较低。
因此,通过调整橡胶的交联程度,可以改变其硬度。
橡胶的硬度还与其表面的纹理和温度有关。
在相同的条件下,表面纹理越粗糙的橡胶硬度越大。
这是因为粗糙的表面能够增加与外界的接触面积,从而增加了受力面积,使橡胶更难发生形变。
另外,温度对橡胶硬度的影响也很大。
一般来说,橡胶在低温下会变得更硬,而在高温下则会变得更软。
这是因为低温下橡胶分子链之间的相互作用增强,使其更难发生形变;而高温下分子链之间的相互作用减弱,使其更容易发生形变。
橡胶的刚度和硬度对其性能和用途起着重要作用。
橡胶刚度的调节可以通过改变材料成分和制备工艺来实现,而硬度则受到分子链的排列方式、交联程度、表面纹理和温度等因素的影响。
理解橡胶刚度和硬度的关系,对于选择合适的橡胶材料以及优化橡胶制品的设计和应用具有重要意义。
- 1、下载文档前请自行甄别文档内容的完整性,平台不提供额外的编辑、内容补充、找答案等附加服务。
- 2、"仅部分预览"的文档,不可在线预览部分如存在完整性等问题,可反馈申请退款(可完整预览的文档不适用该条件!)。
- 3、如文档侵犯您的权益,请联系客服反馈,我们会尽快为您处理(人工客服工作时间:9:00-18:30)。
(塑料橡胶材料)配方设计与橡胶硬度的关系配方设计与橡胶硬度的关系配方设计与橡胶硬度的关系生胶品种硫化体系补强填充剂软化增塑剂邵尔A型硬度测定中的影响因素1.试样厚度的影响邵尔A型硬度值是由压针压入试样的深度来测定的,因此试样配方设计与橡胶硬度的关系·生胶品种·硫化体系·补强填充剂·软化增塑剂邵尔A型硬度测定中的影响因素1.试样厚度的影响邵尔A型硬度值是由压针压入试样的深度来测定的,因此试样厚度直接影响试验结果。
试样受到压力厚产生变形,受到压力的部位变薄,硬度值增大。
所以,试样厚度小硬度值达,试样厚度大硬度值小。
2.压针长度对试验结果的影响标准中规定邵尔A硬度计的压针露出加压面的高度为2.5mm,在自由状态时指针应指零点。
当压针在平滑的金属板或玻璃上时,仪器指针应指100度,如果指示大于或小于100度时,说明压针露出高度大于或小于2.5mm或小于2.5mm,这种情况下应停止使用,进行校正。
当压针露出高度大于2.5mm时测得的硬度值偏高。
3.压针端部形状对试验结果的影响邵尔A型硬度计的压针端部在长期作用下,造成磨损,使其几何尺寸改变,影响试验结果,磨损后的端部直径变大所测得结果也大,这是因为其单位面积的压强不同所致。
直径大则压强小所测得硬度值偏大,反之偏小。
4.温度对试验结果的影响橡胶为高分子材料,其硬度值随环境的变化而变化,温度高则硬度值降低。
胶料不同其影响程度不同,如结晶速度慢的天然橡胶,温度对其影响小些,而氯丁橡胶、丁苯橡胶等则影响显著。
5.读数时间的影响邵尔A型硬度计在测量时读数时间对试验结果影响很大。
压针与试样受压后立即读数与指针稳定后再读数,所得的结果相差很大,前者高,后者偏低,二者之差可达5至7度左右,尤其再合成橡胶测试中较为显著,这主要使胶料在受压后产生蠕变所致。
所以当试样受压后应立即读取数据。
目录一.硬度的定义二.硬度的测试方法三.分别介绍几种硬度测试方法和相关单位四.各种硬度的区别一.硬度的定义硬度——材料局部抵抗硬物压入其表面的能力称为硬度。
它是衡量材料软硬程度的一个性能指标。
它既可理解为是材料抵抗弹性变形、塑性变形或破坏的能力,也可表述为材料抵抗残余变形和反破坏的能力。
硬度不是一个简单的物理概念,而是材料弹性、塑性、强度和韧性等力学性能的综合指标。
二.硬度的测试方法硬度试验的方法较多,原理也不相同,测得的硬度值和含义也不完全一样。
最普通方法是用锉刀在工件边缘上锉擦,由其表面所呈现的擦痕深浅以判定其硬度的高低。
这种方法称为锉试法这种方法不太科学。
用硬度试验机来试验比较准确,是现代试验硬度常用的方法。
最常用的是静负荷压入法硬度试验,即洛氏硬度HRA|HRB|HRC、布氏硬度HB、维氏硬度HV,其值表示材料表面抵抗坚硬物体压入的能力。
而里氏硬度(HL)、肖氏硬度HS则属于回跳法硬度试验,其值代表金属弹性变形功的大小。
因此,硬度不是一个单纯的物理量,而是反映材料的弹性、塑性、强度和韧性等的一种综合性能指标。
硬度试验是机械性能试验中最简单易行的一种试验方法。
为了能用硬度试验代替某些机械性能试验,生产上需要一个比较准确的硬度和强度的换算关系。
实践证明,金属材料的各种硬度值之间,硬度值与强度值之间具有近似的相应关系。
因为硬度值是由起始塑性变形抗力和继续塑性变形抗力决定的,材料的强度越高,塑性变形抗力越高,硬度值也就越高。
三.分别介绍几种硬度测试方法和相关单位1.布式硬度(Brinellhardness)|HB:布氏硬度以HB[N(kgf/mm2)]表示(HBS\HBW)(参照GB/T231-1984),布式硬度HB 是以一定大小的试验载荷,将一定直径的淬硬钢球或硬质合金球压入被测金属表面,保持规定时间,然后卸荷,测量被测表面压痕直径。
布式硬度值是载荷除以压痕球形表面积所得的商。
一般为:以一定的载荷一般3000kg把一定大小直径一般为10mm的淬硬钢球压入材料表面,保持一段时间,去载后,负荷与其压痕面积之比值,即为布氏硬度值HB,单位为公斤力/mm2N/mm2。
所以生产中常用布氏硬度法测定经退货、正火和调质得刚健,以及铸铁、有色金属、低合金结构钢等毛胚或半成品的硬度。
2.维氏硬度(Vickershardness)|HV:维氏硬度HV以120kg以内的载荷和顶角为136°的金刚石方形锥压入器压入材料表面,用材料压痕凹坑的表面积除以载荷值,即为维氏硬度值HV。
它适用于较大工件和较深表面层的硬度测定。
维氏硬度尚有小负荷维氏硬度,试验负荷1.961~49.03N,它适用于较薄工件、工具表面或镀层的硬度测定;显微维氏硬度,试验负荷小于1.961N,适用于金属箔、极薄表面层的硬度测定。
3.邵氏硬度(Shorehardness)|HA/HD:具有一定形状的钢制压针﹐在试验力作用下垂直压入试样表面﹐当压足表面与试样表面完全贴合时﹐压针尖端面相对压足平面有一定的伸出长度L,以L值的大小来表征邵氏硬度的大小,L值越大﹐表示邵尔硬度越低﹐反之越高。
4.肖氏硬度(Shorehardness)|HS:肖氏硬度试验是一种动载试验法,其原理是将具有一定质量的带有金刚石或合金钢球的重锤从一定高度落向试样表面,根据重锤回跳的高度来表征测量硬度值大小。
符号为HS。
重锤回跳得越高,表面测量越硬。
A90属金刚钻的硬度、D45属淬火钢的硬度。
5.洛式硬度(Rockwellhardness)|HR:洛式硬度是以压痕塑性变形深度来确定硬度值指标。
以0.002毫米作为一个硬度单位。
当HB>450或者试样过小时,不能采用布氏硬度试验而改用洛氏硬度计量。
它是用一个顶角120°的金刚石圆锥体或直径为1.59、3.18mm的钢球,在一定载荷下压入被测材料表面,由压痕的深度求出材料的硬度。
根据试验材料硬度的不同,分三种不同的标度来表示:HRA:是采用60kg载荷和钻石锥压入器求得的硬度,用于硬度极高的材料|如硬质合金等HRB:是采用100kg载荷和直径1.58mm淬硬的钢球求得的硬度,用于硬度较低的材料|如铸铁HRC:是采用150kg载荷和钻石锥压入器求得的硬度,用于硬度很高的材料|如淬火钢等6.莫氏硬度(Mohs’scaleofhardness)|HM表示矿物硬度的一种标准。
1824年由德国矿物学家莫斯(FrederichMohs)首先提出。
应用划痕法将棱锥形金刚钻针刻划所试矿物的表面而发生划痕,习惯上矿物学或宝石学上都是用莫氏硬度。
用测得的划痕的深度分十级来表示硬度:7.努氏(Knoophardness)HK8.里氏(Leebhardness)|HL9.韦氏(Websterhardness)|HW韦氏硬度的基本原理是采用一定形状的淬火压针,在标准弹簧的作用力下压入式样表面,定义0.01MM的压入深度为一个韦氏硬度单位.材料的硬度与压入深度成反比.压入越浅硬度越高,反之则低.HW=20-L/0.01,HW--表示韦氏硬度符号L---表示压针伸出长度,即压入式样深度/MM0.01---定义值/MM四.各种硬度的区别1.洛氏硬度可分为HRA、HRB、HRC、HRD四种,它们的测量范围和应用范围也不同。
一般生产中HRC用得最多。
压痕较小,可测较薄得材料和硬得材料和成品件得硬度。
维氏硬度以HV表示(参照GB/T4340-1999),测量极薄试样。
2.钢材的硬度:金属硬度(Hardness)的代号为H。
按硬度试验方法的不同,常规表示有布氏(HB)、洛氏(HRC)、维氏(HV)、里氏(HL)硬度等,其中以HB及HRC 较为常用。
HB应用范围较广,HRC适用于表面高硬度材料,如热处理硬度等。
两者区别在于硬度计之测头不同,布氏硬度计之测头为钢球,而洛氏硬度计之测头为金刚石。
HV-适用于显微镜分析。
维氏硬度(HV)以120kg以内的载荷和顶角为136°的金刚石方形锥压入器压入材料表面,用材料压痕凹坑的表面积除以载荷值,即为维氏硬度值(HV)。
HL手提式硬度计,测量方便,利用冲击球头冲击硬度表面后,产生弹跳;利用冲头在距试样表面1mm处的回弹速度与冲击速度的比值计算硬度,公式:里氏硬度HL=1000×VB(回弹速度)/VA(冲击速度)。
便携式里氏硬度计用里氏(HL)测量后可以转化为:布氏(HB)、洛氏(HRC)、维氏(HV)、肖氏(HS)硬度。
或用里氏原理直接用布氏(HB)、洛氏(HRC)、维氏(HV)、里氏(HL)、肖氏(HS)测量硬度值。
3.HB-布氏硬度;布氏硬度(HB)一般用于材料较软的时候,如有色金属、热处理之前或退火后的钢铁。
洛氏硬度(HRC)一般用于硬度较高的材料,如热处理后的硬度等等。
布式硬度(HB)是以一定大小的试验载荷,将一定直径的淬硬钢球或硬质合金球压入被测金属表面,保持规定时间,然后卸荷,测量被测表面压痕直径。
布式硬度值是载荷除以压痕球形表面积所得的商。
一般为:以一定的载荷(一般3000kg)把一定大小(直径一般为10mm)的淬硬钢球压入材料表面,保持一段时间,去载后,负荷与其压痕面积之比值,即为布氏硬度值(HB),单位为公斤力/mm2(N/mm2)。
4.洛式硬度是以压痕塑性变形深度来确定硬度值指标。
以0.002毫米作为一个硬度单位。
当HB>450或者试样过小时,不能采用布氏硬度试验而改用洛氏硬度计量。
它是用一个顶角120°的金刚石圆锥体或直径为1.59、3.18mm的钢球,在一定载荷下压入被测材料表面,由压痕的深度求出材料的硬度。
根据试验材料硬度的不同,分三种不同的标度来表示:HRA:是采用60kg载荷和钻石锥压入器求得的硬度,用于硬度极高的材料(如硬质合金等)。
HRB:是采用100kg载荷和直径1.58mm淬硬的钢球,求得的硬度,用于硬度较低的材料(如退火钢、铸铁等)。
HRC:是采用150kg载荷和钻石锥压入器求得的硬度,用于硬度很高的材料(如淬火钢等)。
另外:1.HRC含意是洛式硬度C标尺,2.HRC和HB在生产中的应用都很广泛3.HRC适用范围HRC20--67,相当于HB225--650若硬度高于此范围则用洛式硬度A标尺HRA。
若硬度低于此范围则用洛式硬度B标尺HRB。
布式硬度上限值HB650,不能高于此值。
5.洛氏硬度计C标尺之压头为顶角120度的金刚石圆锥,试验载荷为一确定值,中国标准是150公斤力。
布氏硬度计之压头为淬硬钢球(HBS)或硬质合金球(HBW),试验载荷随球直径不同而不同,从3000到31.25公斤力。
6.洛式硬度压痕很小,测量值有局部性,须测数点求平均值,适用成品和薄片,归于无损检测一类。
布式硬度压痕较大,测量值准,不适用成品和薄片,一般不归于无损检测一类。