振动监测与故障诊断系统介绍
振动监控系统

振动监控系统振动监控系统是一种用于实时监测和分析机械设备振动状况的技术方案。
它利用传感器采集机械设备的振动信号,并通过分析这些信号来实现对机械设备的状态进行监测和预测。
振动监控系统广泛应用于各种工业领域,可有效提高设备的稳定性、可靠性和安全性。
一、振动监控系统的原理和组成振动监控系统主要由传感器、信号放大器、数据采集器、分析软件等组成。
传感器负责采集机械设备振动信号,信号放大器用于放大传感器采集到的微弱信号,数据采集器将信号转换为数字信号并传输给分析软件进行处理。
二、振动监控系统的作用和优势1. 实时监测:振动监控系统能够实时监测机械设备的振动状况,及时发现异常振动,提前预警设备故障,避免机械设备的意外停机,减少生产线的损失。
2. 故障诊断:通过振动信号的分析,振动监控系统可以判断设备是否存在故障,并对故障类型进行诊断。
这有助于准确定位和修复故障,提高维修效率。
3. 预防维护:振动监控系统可以实现对机械设备的预防性维护。
通过持续监测设备振动状况,系统可以根据振动特征和变化趋势提前预警设备故障,制定合理的维护计划,避免设备故障带来的生产中断和维修成本。
4. 数据分析:振动监控系统可以对采集到的振动数据进行分析和处理,提取有用信息,为设备运行状态的评估和改进提供依据。
这有助于优化生产过程,提高设备的使用寿命和稳定性。
三、振动监控系统的应用领域振动监控系统广泛应用于各种工业设备的监测和维护中,如发电机组、风力发电机组、泵站、机床、轴承等。
以下是几个典型的应用场景:1. 发电机组监测:发电机组是电力系统的重要组成部分,振动监控系统可以监测其转子和轴承的振动状况,检测轴承的磨损程度,发现故障隐患,确保发电机组的安全运行。
2. 风力发电机组监测:风力发电机组常受到强风和恶劣环境的影响,振动监控系统可以监测发电机组的桨叶振动、转子振动等,提供及时的故障预警和维护建议。
3. 泵站监测:振动监控系统可以监测泵站的水泵、电机等关键设备的振动状况,预测设备的寿命,并提供有效的维护方案,保证泵站的正常运行。
振动监测与故障诊断系统简介
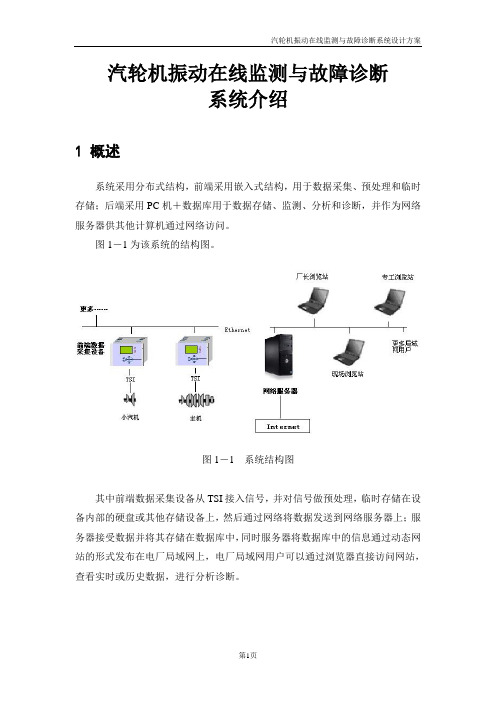
数据采集子系统与气轮机组在线监测故障诊断主系统集成工作的原理如图2-2所示。
图2-2数据采集子系统的工作原理
2.
一体化设计,功能完善,结构合理,商品化的产品。
采用模块化和多CPU主从结构设计,数据采集、处理能力强大,组装、维护方便。
主CPU板和各智能模拟量信号采集板通过内存进行数据交换,数据交换速度高,吞吐量大。
标准VT100终端接口,用户可以方便对装置进行远方检测和在线配置。
工业标准设计,能够工作于各种恶劣环境。
采用电磁兼容(EMC)技术,抗电磁脉冲干扰(EMI)性能强,装置运行稳定可靠。
对敏感信号进行屏蔽。
输入信号采用光电隔离。
内部器件均选用优秀的工业级产品。
不需要特殊的加热器或冷却装置。
充分的可靠性设计,严格的质量检验,为用户提供了可靠的保证。
汽轮机振动在线监测与故障诊断
系统介绍
1
系统采用分布式结构,前端采用嵌入式结构,用于数据采集、预处理和临时存储;后端采用PC机+数据库用于数据存储、监测、分析和诊断,并作为网络服务器供其他计算机通过网络访问。
图1-1为该系统的结构图。
图1-1系统结构图
其中前端数据采集设备从TSI接入信号,并对信号做预处理,临时存储在设备内部的硬盘或其他存储设备上,然后通过网络将数据发送到网络服务器上;服务器接受数据并将其存储在数据库中,同时服务器将数据库中的信息通过动态网站的形式发布在电厂局域网上,电厂局域网用户可以通过浏览器直接访问网站,查看实时或历史数据,进行分析诊断。
键相信号(脉冲信号)接入装置后,需要光电隔离、滤波整形处理。键相信号调理电路由光电隔离器和滤波整形两部分组成。
智能模拟量信号采集板的组成如图2-4所示。
振动检测与故障诊断技术

振动检测是状态检测的手段之一,任何机械在输入能量转化为有用功的过程中,均会产生振动;振动的强弱与变化和故障有关,非正常的震动感增强表明故障趋于严重;不同的故障引起的振动特征各异,相同的振动可能是不同的故障;振动信号是在机器运转过程中产生的,就可以在不用停机的情况下检测和分析故障;因此识别和确定故障的内在原因需要专门的一起设备和专门的技术人才。
1、机械振动检测技术机械运动消耗的能量除了做有用功外,其他的能量消耗在机械传动的各种摩擦损耗之中并产生正常振动,其他的能量消耗在机械传动的各种摩擦损耗之中并产生正常振动,如果出现非正常的振动,说明机械发生故障。
这些振动信号包含了机械内部运动部件各种变化信息。
分辨正常振动和非正常振动,采集振动参数,运用信号处理技术,提取特征信息,判断机械运行的技术状态,这就是振动检测。
所以由此看来,任何机械在输入能量转化为有用功的过程中,均会产生振动;振动的强弱与变化和故障有关,非正常的震动感增强表明故障趋于严重;不同的故障引起的振动特征各异,相同的振动可能是不同的故障;振动信号是在机器运转过程中产生的,就可以在不用停机的情况下检测和分析故障;因此识别和确定故障的内在原因需要专门的一起设备和专门的技术人才。
2、振动监测参数与标准振动测量的方位选择a、测量位置(测点)。
测量的位置选择在振动的敏感点,传感器安装方便,对振动信号干扰小的位置,如轴承的附近部位。
b、测量方向。
由于不同的故障引起的振动方向不同,一般测量互相垂直的三个方向的振动,即轴向(A向)、径向(H 向、水平方向)和垂直方向(v向)。
例如对中不良引起轴向振动;转子不平衡引起径向振动;机座松动引起垂直方向振动。
高频或随机振动测量径向,而低频振动要测量三个方向。
总之测量方向和数量应全面描述设备的振动状态。
测量参数的选择测量振动可用位移、速度和加速度三个参数表述。
这三个参量代表了不同类型振动的特点,对不同类型振动的敏感性也不同。
振动监测及分析系统(VMAS)在发电厂的应用

振动监测及分析系统(VMAS)在发电厂的应用摘要:振动状态监测及分析系统自动连续地采集与设备安全有关地主要状态参数:机组的振动、摆度、键相/转速、轴振、瓦振、轴位移、胀差、偏心、机组轴承负荷及温度、压力和开关量等,并自动形成各种数据库。
它能够自动识别设备的运行状态,预测和诊断设备的故障;能够促进设备维修方式向预知维修(状态维修)的转变,确保设备安全稳定地运行。
关键词:振动状态监测及分析系统(VMAS);信号处理;诊断。
0. 引言随着对发电厂主要设备可靠性、稳定性、以及对电厂设备寿命要求的提高,越来越多的监测和诊断分析系统应用到实际电厂项目中。
汽轮机、发电机、以及主要高压电动机设备作为发电厂的主要运行设备,更是成为监测和诊断的重要对象。
随着先进信号处理技术以及诊断技术的发展,振动监测及分析系统(VMAS)能在故障出现的早期阶段及时地预告故障的存在和发展,避免灾难性事故发生,并可以将现有的周期预防性维修改为预知性的维修, 选择最佳停修时间,提高机组可利用率。
1. 振动状态监测及分析系统(VMAS)的定义振动状态监测及分析系统,英文全称是Vibration monitoring and analyze system ,缩写为VMAS。
振动状态监测及分析系统的主要功能是用于主辅机(通常包括汽轮机、发电机、以及主要的高压设备)状态监测与故障诊断,实现监测、控制、报警、诊断功能。
而在早期,振动状态监测和分析系统主要应用于汽轮发电机组,叫做旋转机械诊断监测管理系统,英文TDM (Turbine diagnosis management) ,在电厂中一般是指汽轮发电机组振动在线状态监测和分析系统。
实际上,这两个叫法是针对一套系统,只是监测的范围不同。
2. 振动状态监测及分析系统基本配置振动状态监测及分析系统是以计算机为平台的旋转机械振动状态在线监测及故障诊断系统,用于对汽轮机、发电机、电动机、风机、泵等设备的振动、转速、压力、流量、温度等信号进行连续监测。
柴油机振动监测及故障诊断系统

Ab t a t T sp p rd s rbe re y t e vb ain mo i rn c a ims o it n ln rwe rn s r c : hi a e e c i s b i f h i r to n t i g me h n s fp so —i e a i g, l o
a n r l av laa c ehutvlel kg n anjun l e igt blg a fut ad ae b oma vl c rn e x a s av a aea d m i o ra b a n r o i l a l e e I e r i oc .H rw r
= . 1 (m O85i) p . ,
= . 5 (m 0 2 5m )
\
= . 2 (m 0 5 5m )
主 撞 击
.
主撞击
1 . 一
\
L
r
1. . - I
0。 丌 T
l
\
L ▲L L 一 ▲I 一
L
罂
振动检测与分析系统方案
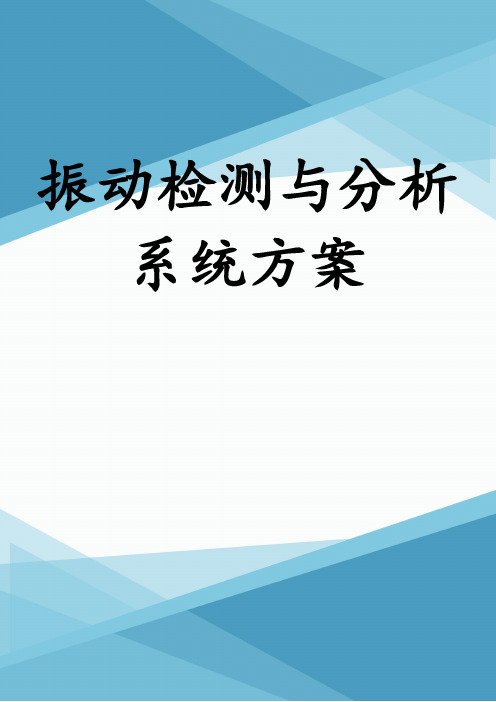
振动检测与分析系统方案振动检测与分析系统方案振动检测与分析系统广泛应用于工程领域,用于监测和分析机械设备、结构物或其他物体的振动情况。
该系统能够提供实时数据,并通过分析判断设备的工作状态,从而实现故障预警和维护计划的制定。
下面是一个振动检测与分析系统的方案,按照步骤逐一介绍。
1. 确定监测目标:首先,需要确定需要监测和分析的目标,例如机械设备、建筑结构等。
根据目标的特点和使用环境,选择适合的振动传感器和数据采集设备。
传感器可以通过接触式或非接触式方式获取振动信号。
2. 安装传感器:将振动传感器安装在目标物体上,并确保传感器与目标之间的接触良好。
对于机械设备,可以选择在关键部位安装传感器,如轴承、齿轮等。
对于结构物,可以选择在梁柱节点或其他关键位置安装传感器。
3. 数据采集:使用数据采集设备将传感器获取的振动信号转化为数字信号,并进行采样和存储。
数据采集设备可以是专用的振动分析仪器,也可以是通用的数据采集器,如传感器与计算机连接的数据采集卡。
4. 数据处理与分析:将采集到的振动数据传输到计算机上,并使用相应的振动分析软件进行处理和分析。
软件可以提供多种振动特征参数的计算和分析方法,如频域分析、时域分析、轴心轨迹分析等,以评估设备或结构的振动情况。
5. 故障诊断与预警:根据振动分析的结果,判断设备或结构是否存在故障或异常情况。
通过设定合适的阈值和告警条件,系统可以实现自动故障诊断和预警功能。
一旦检测到异常振动,系统会发出警报并提供相应的故障诊断结果。
6. 维护计划制定:根据故障诊断结果和预警信息,制定相应的维护计划。
可以根据设备的工作状态和振动特征,确定维护时间和方式,以避免设备故障或减少停机时间。
7. 数据记录和报告:系统可以自动记录和保存振动数据,并生成相应的报告。
报告可以包括设备的振动趋势图、频域谱图、故障诊断结果等信息,为维护人员提供参考和决策依据。
8. 系统优化和改进:根据实际使用情况,对振动检测与分析系统进行优化和改进。
机械振动监测与故障预警
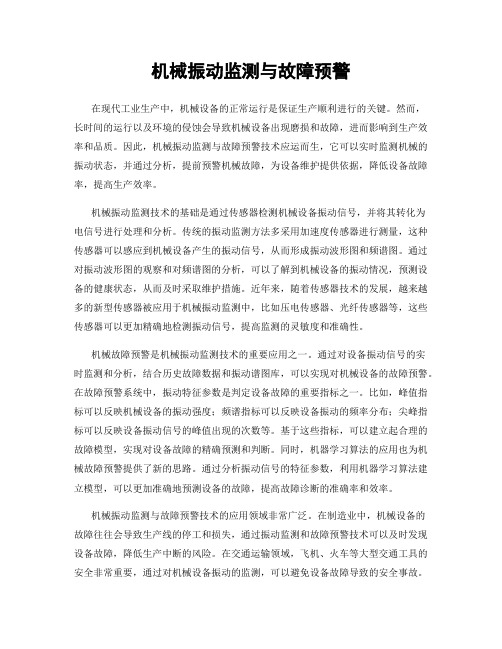
机械振动监测与故障预警在现代工业生产中,机械设备的正常运行是保证生产顺利进行的关键。
然而,长时间的运行以及环境的侵蚀会导致机械设备出现磨损和故障,进而影响到生产效率和品质。
因此,机械振动监测与故障预警技术应运而生,它可以实时监测机械的振动状态,并通过分析,提前预警机械故障,为设备维护提供依据,降低设备故障率,提高生产效率。
机械振动监测技术的基础是通过传感器检测机械设备振动信号,并将其转化为电信号进行处理和分析。
传统的振动监测方法多采用加速度传感器进行测量,这种传感器可以感应到机械设备产生的振动信号,从而形成振动波形图和频谱图。
通过对振动波形图的观察和对频谱图的分析,可以了解到机械设备的振动情况,预测设备的健康状态,从而及时采取维护措施。
近年来,随着传感器技术的发展,越来越多的新型传感器被应用于机械振动监测中,比如压电传感器、光纤传感器等,这些传感器可以更加精确地检测振动信号,提高监测的灵敏度和准确性。
机械故障预警是机械振动监测技术的重要应用之一。
通过对设备振动信号的实时监测和分析,结合历史故障数据和振动谱图库,可以实现对机械设备的故障预警。
在故障预警系统中,振动特征参数是判定设备故障的重要指标之一。
比如,峰值指标可以反映机械设备的振动强度;频谱指标可以反映设备振动的频率分布;尖峰指标可以反映设备振动信号的峰值出现的次数等。
基于这些指标,可以建立起合理的故障模型,实现对设备故障的精确预测和判断。
同时,机器学习算法的应用也为机械故障预警提供了新的思路。
通过分析振动信号的特征参数,利用机器学习算法建立模型,可以更加准确地预测设备的故障,提高故障诊断的准确率和效率。
机械振动监测与故障预警技术的应用领域非常广泛。
在制造业中,机械设备的故障往往会导致生产线的停工和损失,通过振动监测和故障预警技术可以及时发现设备故障,降低生产中断的风险。
在交通运输领域,飞机、火车等大型交通工具的安全非常重要,通过对机械设备振动的监测,可以避免设备故障导致的安全事故。
浅谈风力发电机组振动状态监测与故障诊断

浅谈风力发电机组振动状态监测与故障诊断摘要:随着科技的发展,风电机组单机容量变大,内部的结构越来越复杂,还会受到天气的不可控因素的影响,比如会受到下雨时,打雷闪电等,本文对风力发电机组振动状态监测与故障诊断进行分析,以供参考。
关键词:风力发电;机组振动;状态监测;故障诊断引言风能是自然界中常见的自然现象,特别是在经济不发达,风能资源丰富的山地地区。
考虑到风能对当前社会结构的重要性,它提高了风力发电机运行的可检测性,并允许在整个发电机组运行期间及时发现问题,使整个风力发电机运行更平稳和安全。
1概述近年来国内风电发展迅速,风电机组容量的提升能够有效提高风能利用率和施工效率以及降低后期运维成本。
在机组容量和体型逐渐增大的同时,风电机组的安全成为风电领域内研究的重点。
江苏某风电场安装了多台6.45MW机组,此类型机组是目前国内厂家生产新型大容量机组之一,此机组塔筒高度为110m,叶轮直径达到171m。
国外GE公司生产的12MW风机单支叶片更是长达107m。
机组容量增大的同时叶片也在不断增大。
风电机组叶片成本约占风电机组总成本的15%~20%,风电机组叶片在风电机组运行过程中受风力作用而产生较大的弹性形变,故通常选用质量较轻、强度较大、耐腐蚀、抗疲劳的材料来制作风电机组叶片。
此外,由于结冰或者风力和风向的突变导致叶片振动过大,从而超过设计载荷发生断裂或者扫塔的现象也时有发生,而振动检测是叶片故障识别的常用方法之一,所以研究大型风电机组的叶片振动情况,对于叶片安全检测和监测具有重要的意义,研究结果也可对风电机组的控制策略优化提供重要指导作用。
在风力发电机组中,齿轮箱也存在着异常问题,表面磨损,齿轮轻度裂纹,设备老化等问题,以下对论文展开叙述。
2风力发电机组安全系统2.1分析(1)安全有关停止功能在机组通过安全防护装置(如传感器)检测到风轮转速超过限值、扭缆超过限值、过度振动及控制系统失效等信号时,安全系统起动机组紧急制动进入停止状态。
振动监测及故障诊断系TDM
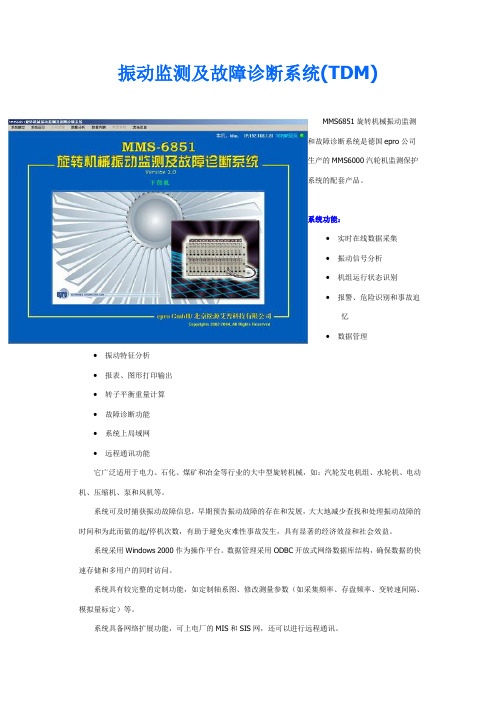
振动监测及故障诊断系统(TDM)MMS6851旋转机械振动监测和故障诊断系统是徳国epro公司生产的MMS6000汽轮机监测保护系统的配套产品。
系统功能:∙实时在线数据采集∙振动信号分析∙机组运行状态识别∙报警、危险识别和事故追忆∙数据管理∙振动特征分析∙报表、图形打印输出∙转子平衡重量计算∙故障诊断功能∙系统上局域网∙远程通讯功能它广泛适用于电力、石化、煤矿和冶金等行业的大中型旋转机械,如:汽轮发电机组、水轮机、电动机、压缩机、泵和风机等。
系统可及时捕获振动故障信息,早期预告振动故障的存在和发展,大大地减少查找和处理振动故障的时间和为此而做的起/停机次数,有助于避免灾难性事故发生,具有显著的经济效益和社会效益。
系统采用Windows 2000作为操作平台。
数据管理采用ODBC开放式网络数据库结构,确保数据的快速存储和多用户的同时访问。
系统具有较完整的定制功能,如定制轴系图、修改测量参数(如采集频率、存盘频率、变转速间隔、模拟量标定)等。
系统具备网络扩展功能,可上电厂的MIS和SIS网,还可以进行远程通讯。
系统组成:通常情况下,MMS6851系统按上、下位机方式配置。
下位机MMS6851/10进行数据采集、存储、网络通讯;上位机MMS6851/20进行数据实时显示、数据分析、故障诊断、远程通讯。
一般情况下MMS6851/10放置在MMS6000 的机柜里,MMS6851/20放置在工程师站。
下位机通过RS-485通讯口与MMS6000汽轮机监测保护系统的RS485总线连接,获取MMS6000系统各测量模块的实时数据。
由于数据直接取自测量模块,无需中间处理,因而具有其它采样方式无可比拟的精度。
通过网卡、多口交换机与MIS和SIS连网。
上位机通过与下位机进行网络通讯而获得实时数据和各种历史数据,通过监视器和打印机实现图形、报表和故障诊断结果的显示和打印输出。
MTS8000振动监测和故障诊断系统简介

MTS8000振动监测和故障诊断系统简介旋转机械是工业应用最广泛的机械,是众多行业的关键设备,这些设备一旦发生故障,将造成巨大的经济损失。
这就要求我们必须对这些设备进行状态监测和故障诊断。
目前国内外对于旋转机械的状态监测系统有以下两种:在线状态监测系统和离线状态监测系统。
仪表监测的主要目的是对机械的运转状态给予准确的判断并做出相应的处理,然而由于仪表与操作员之间的交互能力以及大容量数据分析的能力相对于计算机的差别,使得状态监测系统的应用尤为重要。
大型旋转机械应用在工业现场的许多领域,如:火电厂、水电站、大型泵站、风力发电机组、冶金、石化等。
这些设备一般都是该行业的关键设备,一旦发生故障不仅给企业带来巨大的经济损失,甚至威胁人身安全,生产也将会被迫中断。
因此提升这些设备的信息化管理水平,对企业来说势在必行。
据了解,针对工业企业旋转设备管理所面临的问题,目前主要有北京长城华瑞科技有限公司推出的MTS8000在线状态监测与故障诊断系统。
MTS8000系统是一种高速、全自动、设备无关性的机组运行状态在线监测系统,是长城华瑞最新研发生产的一种集原始信号处理与过程量数据处理于一体的在线状态监测与故障诊断系统。
主要应用于电力、石化、冶金等工业领域中的大型旋转机械设备,适用于水轮发电机组、汽轮发电机组、风力发电机组、大型泵站、电机、水泵、齿轮箱和滚动轴承等机械的在线振动监测分析和故障诊断。
据介绍,MTS8000系统可自动连续地采集与设备安全有关的主要状态参数,并自动形成各种数据库;能够自动识别设备的运行状态,预测和诊断设备的故障;能够实时采集、存储和分析机组运行的状态信息,直观地反映出机组运行的临界状态和平衡状态。
用户通过本系统可以预先诊断机组的运行情况,对机组在运行过程中产生的不正常现象(如:转子不平衡、不对中、轴承损坏、机架松动、轴弯曲以及轴裂等)可以较早的发现,尽早提示用户有针对的检修,从而减少损失。
MTS8000系统具有多种输入输出接口,可以与其他振动监测仪表厂家的设备连接,其接口兼容性较好。
设备故障的振动诊断技术介绍及其应用

设备故障的振动诊断技术介绍及其应用设备故障的振动诊断技术是一种通过分析设备振动特征来判断设备工作状态和健康状况的技术。
它基于振动信号的特性和规律,结合数据采集、信号处理和分析技术,可以及时准确地诊断设备故障,预测设备寿命,指导设备维护和保养工作。
该技术的主要应用包括但不限于以下几个方面:1. 故障诊断:通过监测和分析设备振动信号,可以准确地诊断各种设备故障,如轴承失效、不平衡、松动等,为设备维修提供准确的依据。
2. 故障预测:振动诊断技术不仅可以发现设备已经存在的故障,还可以通过对振动信号的趋势分析和预测,提前预知设备可能出现的故障和故障发展的趋势,从而及时采取措施,避免事故发生。
3. 设备健康监测:通过对设备振动信号进行连续监测和分析,可以实时监测设备的运行状态和健康状况,及时发现和解决设备运行中的问题,保障设备的正常运行。
4. 设备维护管理:振动诊断技术可以为设备的定期维护和保养提供科学的依据和管理手段,有助于合理安排设备维修计划,降低维修成本,延长设备使用寿命。
总之,设备故障的振动诊断技术是一种非常有效的设备健康管理技术,可以帮助企业实现设备的智能化监控和管理,提高设备的可靠性和使用寿命,为企业的生产运营提供有力的支持。
设备振动诊断技术是一门对设备振动进行监测、分析和诊断的技术。
它基于振动信号的特性和规律,通过采集设备振动信号,利用信号处理和分析技术,可以判断设备的运行状态,预测设备健康状况,诊断设备故障,并为设备维护提供科学的依据。
这一技术的广泛应用,可以有效地提高设备的可靠性和使用寿命,减少由于设备故障而导致的生产事故或停工,以及维护管理成本。
下面将详细介绍设备振动诊断技术的原理、方法和应用。
一、原理设备的振动信号是由于设备在运行过程中产生的,其中蕴含了丰富的信息。
通过分析设备振动信号的频率、振幅、相位等特性,可以获得关于设备工作状态、结构状况和健康状况的信息。
设备振动信号包含了来自设备各个部件的振动信号,例如轴承、齿轮、驱动系统等。
EN3600-TRCMS电力变压器状态在线监测和诊断系统V2

EN3600-TRCMS电力变压器振动在线监测故障诊断系统故障发展趋势预测故障预警运行监测检修指导故障部位定位一、技术背景“EN3600电力变压器箱体振动监测诊断系统”是针对大型电力变压器线圈和铁心部件松动故障开发的基于箱体振动的故障监测与诊断系统产品。
线圈和铁心部件松动是变压器的一种常见问题。
变压器在运行过程中,线圈和铁心受到交变电磁力和磁致伸缩力的共同作用,由原始压紧状态逐渐变松,其结果是,轻则造成变压器振动和噪声的增大,重则导致线圈变形,造成绝缘磨损、线圈变形,甚至短路等严重的二次故障。
统计表明,由于线圈变形造成的变压器故障占据较高比例,造成的损失很大。
但是目前国内外尚未有比较成熟的线圈和铁心松动监测技术及产品。
本产品(EN3600)是北京英华达公司与华北电力大学合作,在多年理论研究、试验分析和现场测试基础上开发的一种专用故障监测与诊断系统,具有技术先进、功能强大、易于实现、可靠性高等特点,对准确判断松动状态,提高变压器运行安全可靠性,降低维护维修成本具有很好的实际意义。
本产品可以实现以下类型变压器故障的监测诊断:1)铁心和线圈松动,及其引发的相关故障,包括线圈变形、绝缘劣化等;3)能够通过变压器箱体振动反映的分接开关异常状态。
二、监测原理变压器在运行状态下,铁心磁场的磁致伸缩效应引起铁心振动,线圈负载电流的电场力引起线圈振动,这两种振动源相互作用,形成复杂的振动形态,并经过支座和油介质传递到变压器箱体,使箱体产生振动。
箱体振动特征与变压器铁心线圈的振动形式以及变压器的内部结构关系密切,因此通过监测变压器箱体振动可以有效实现线圈和铁心松动状态的诊断。
基于变压器箱体振动进行线圈和铁心松动状态监测的设想于上个世纪90年代提出,是一项比较新的监测技术。
但是该项技术的实际应用案例和产品尚不多见。
主要原因是对松动状态与箱体振动关系以及松动状态表征方法等方面缺少深入的理论和试验研究。
此外,变压器内部的分接开关在动作过程中,将产生冲击振动激励,经连接结构和油介质传递到箱体,开关正常状态和异常状态产生的冲击振动特征存在差异,因此可以通过箱体振动监测分析,判断分接开关的异常状态。
振动监测保护故障诊断系统的应用
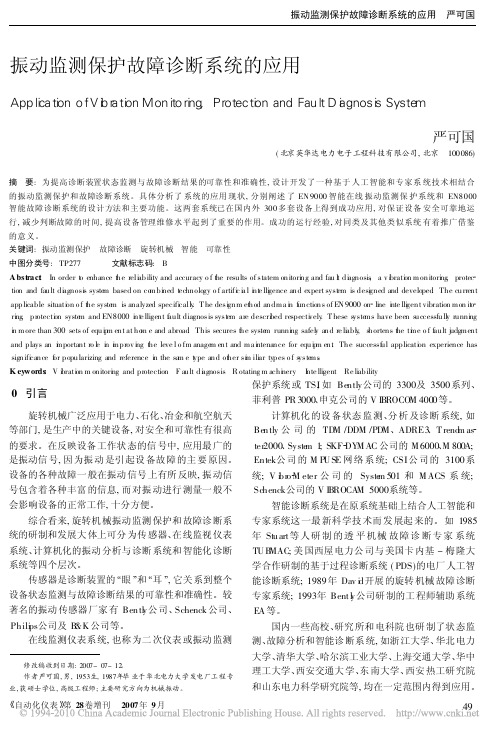
振动监测保护故障诊断系统的应用
App lica tion o f V ib ra tion Mon ito ring, Protec tion and Fau lt D iagnos is System
严可国
(北京英华达电力电子工程科技有限公司, 北京 100086)
大学、清华大学、哈尔滨工业大学、上海交通大学、华中 理工大学、西安交通大 学、东 南大学、西安 热工研 究院 和山东电力科学研究院等, 均在一定范围内得到应用。
自动化仪表 第 28卷增刊 2007年 9月
49
振动监测保护故障诊断系统的应用 严可国
1 智能在线振动监测保护系统的设计
目前 , 在旋转机 械 振动 监 测保 护 系统 方 面, 国内 外的主 要差距 在 于可 靠性 方面 。在中 小 型设 备 振动 监测上 , 有国产单 /双通道振 动监测 保护 表, 在大 型和 特大型 设备 振 动 监 测上 , 国内 主 要 使 用 的 为进 口 产 品, 它 们价格昂贵, 并且存在 显示方 式单 一、系统 调试 复杂、数 据不能共享等问题 。北京 英华达 公司研 制的 EN 9000振动监 测保 护 系统 摒 弃了 上 述缺 点, 根 据机 组保护 的实际 需要, 提 出了 崭新 的设 计 思路, 利 用当 代先进 的机械、微电 子 和自 动化 技术 , 实 现了 信 号采 集、数 据存储、状 态监 测、异常 保 护和 故障 诊 断功 能, 能够为 汽轮机、水 轮机、压缩 机、风机、电机 和 水 泵等 旋转机 械提供转速、轴振、瓦 振、胀 差和轴 位移等 参数 的在线 监测保护, 以最经济合 理的 方式保 证设备 安全 可靠地 运行。
为了提高系统的可靠性, 采取了以下措施: # 采用体积小、功能强、可靠 性高的 嵌入式 操作 系统; ∃ 采 用电源冗 余技术, 在 1路电 源出现故 障时, 保证系统可以正常工作; % 采用热插拔技术, 保证各模块热插拔时不影响 其他模块正常工作; & 采用传感器通道和系统自检技术, 如果传感器 发生短路或断路的情况, 该传感器被旁路, 如果系统出 现问题, 进行自动复位并提示出错; ∋ 采用上电抑制技术, 在系统上电和模块热插拔 时, 在一段时间内保持系统的状态不变, 以便操作人员 观察系统是否工作正常; ( 采用独有的专利技术, 保护报警继电器状态只 在需要时被改变。 此外, 还采取了输入信号自适应数字滤波, 避免现 场干扰信号引起的 误动作; 断 电系 统状态 保存和 单独 的进退保护操作等措施。 EN 9000 系统由主 机 ( TS I) 和上位 机系统 ( TDM + ES ) 组成。主机 ( TS I) 集成了 振动 在线 监测 保护 和初 步的 分析 诊 断 功 能, 可 以 独立 运 行。 主 机 由电 源 模 块、采集保护模 块 ( 键相 模块 、转 速模块 、振 动模 块 )、 过程 量模块、后端 子板及框架 组成, 有 4、8、12个 插槽 可用 于自由配置 测量模块, 带触摸屏的 3 5英吋 彩色 液晶 显示。上位 机系统 ( TDM + ES ) 通 过以 太网 与主 机 组成 局域 网, 对 主机 采集 的数 据进 行存 储、分 析和 诊断 。 主机 ( T SI) 的主要功能如下:
汽轮发电机组的振动监测及故障诊断系统开发
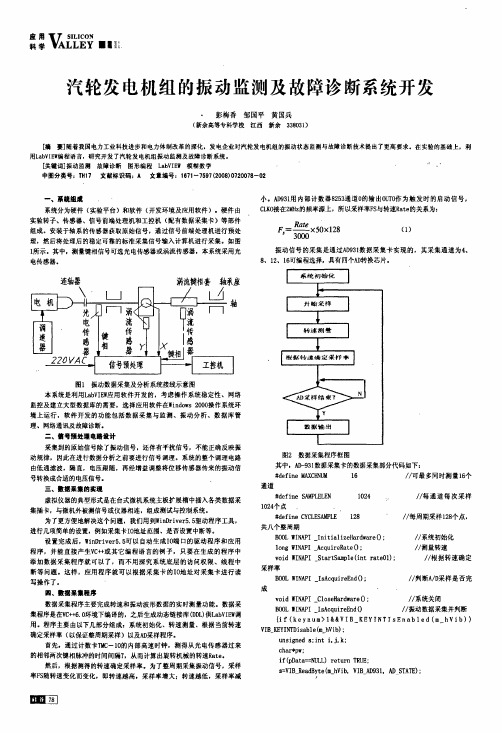
( i f( k e y num>l &&VI B—KEYI NTI s Enab l e d( m— hVi b) )
VIB—I【EYI NTDi s 曲1e(虬hVi b) : uns i g ned 8: i nt i 。j 。k:
cha r 奉pⅣ :
i f ( pDat a:=N【J LL) ret ur n TRUE:
s =VI B- Re adByt e( m- hVi b。 VI B_AD931,AD—S TATx01) &&bAcqui r eBegi n) bEnd=TRUE:
i f ( bEnd)
// 判断 A/ D是 否结 束
{
bAc qui r e Be gi n:FALSE:
图2数据采集程序框图
其中 ,AD- 931 数据采集 卡的数据 采集部分 代码如下 :
#def i ne MA】( c唧UM
16
//可最多同时测量16个
通道
#def i ne sA肝 LEL蹦
1024 ,
//每通道 每次采样
1024个点
.
#def i ne cYCLESA胛 LE
128
/ /每 周期 采样 1 2 8个 点。
//根据转速确定
采样率
B0 0L wI NAPI - I s Acqui r eEnd( ) :
//判断A/D采样是否完
成
voi d wI NAPI - cl oseHar dWar e( ) :
//系 统关闭
Boo L■I NAPI .I sAcqu i r eEnd ( )
//振动数据采集并判断
用LabVI Ew编 程语言,研究开发了 汽轮发电机组振动监 测及故障诊断系统。 [ 关键词] 振动监测故 障诊断图形 编程La bVI EW模糊数 学
发电机组的振动监测与故障诊断

发电机组的振动监测与故障诊断振动监测是发电机组运行过程中非常重要的一项工作,它可以有效地帮助我们了解发电机组的运行状态,及时发现和解决潜在的故障问题。
本文将介绍振动监测的基本原理和方法,并探讨如何通过振动信号来进行故障诊断。
一、振动监测的基本原理发电机组在运行过程中会产生各种振动信号,这些信号可以反映出发电机组的运行状态和各部件的工作情况。
振动监测的基本原理是通过安装振动传感器来采集振动信号,并将信号转化为电信号进行处理和分析。
振动信号可以分为两类:机械振动信号和电子振动信号。
机械振动信号是由发电机组内部运行过程中产生的机械振动引起的,比如转子不平衡、轴承故障等。
电子振动信号是由电器故障或电磁干扰引起的,比如绝缘损坏、接触不良等。
二、振动监测的方法1. 实时监测:通过振动传感器将振动信号实时采集并传输到监测系统,对振动信号进行分析,及时发现异常情况,并及时采取措施进行维修和保养。
2. 定期检测:定期使用振动仪器检测发电机组的振动情况,比如每月进行一次振动检测,可以有效地了解发电机组的运行状态,并及时发现潜在的故障问题。
3. 长期驻点监测:将振动传感器长期安装在发电机组上,通过采集连续不断的振动信号,了解发电机组的长期运行情况,为后续的故障诊断提供重要数据支持。
三、振动信号的故障诊断振动信号的故障诊断是通过对振动信号的分析和处理,来判断发电机组是否存在故障,并确定具体的故障类型和程度。
常用的故障诊断方法包括:1. 时域分析:通过对振动信号在时域上的波形进行分析,判断是否存在周期性故障,比如转子不平衡、轴承故障等。
2. 频域分析:通过对振动信号在频域上的频谱进行分析,得到频域特征参数,来识别故障类型,比如齿轮间隙、电机磁场不均匀等。
3. 振动信号模式识别:通过建立故障模式库,将不同故障类型的振动信号进行分类和归档,根据振动信号的特征进行匹配,从而确定故障类型。
四、振动监测与故障诊断的意义振动监测与故障诊断可以帮助我们及时发现和解决发电机组存在的潜在故障问题,避免故障发生对发电机组造成严重损害。
汽轮发电机组振动监测故障诊断系统的评述

摘 要 : 绍 了几 种 汽 轮 发 电 机组 振 动 监 测 故 障诊 断 系统 ( D 系 统 ) 功 能 、 成 和 实 现 方 式 , 简 单 介 T M 的 组 并
论 述 了各 T M 系 统 的 优 缺 点 。现 场 应用 表 明 : D 系 统 对 机组 的 振 动 监 测 能减 少 机组 停 机 次数 , 高设 备 D T M 提 的可 用 率 , 降低 发 电 成本 。 关 键 词 : 轮发 电机 组 ; 动 监 测 ; 障诊 断 ;可 用 率 汽 振 故
汽 轮 发 电 机组 运 行 的好 坏 直 接 关 系 到 电厂 运行 的安 全性 和经 济 效 益 。汽 轮 发 电机 组 的 异
风电机组振动监测及故障诊断

2
粘结剂
40
3
刚性高的蜡粘合 40
4
绝缘磁座吸合
150
8
频率特性良好,可到达
10kHz
7
频率特性好但不耐温可到
达10kHz
1.5
仅使用于1~2kHz
5
触杆手持测头钉 不限
0.4
仅适用于数百赫兹的频率
CHANG’AN UNIVERSITY
结合本系统测量的实际情况,采用了螺栓固定和胶 水粘合两种方式。如下图分别为为采用螺栓固定和粘结 剂固定的示意图。
changanuniversity各个测点的位置及相应的传感器见下表所示测量对象测试方式传感器位置传感器类型主轴轴承径向轴承座正下方低速加速度传感器主轴轴承轴向轴承座正下方低速加速度传感器第二主轴承径向轴承座正下方低速加速度传感器行星齿轮径向输入齿轮部分轴承座低速加速度传感器行星齿轮径向行星齿轮上方标准加速度传感器二级齿轮径向入口和中间轴之间标准加速度传感器二级齿轮轴向中间轴和高速轴之间标准加速度传感器发电机径向自由端轴承下方标准加速度传感器发电机径向输入端轴承下方标准加速度传感器10主轴径向主轴转速传感器11发电机输入端径向发电机输入端轴转速传感器changanuniversity根据测点测量对象的振动特点系统主要采用了个加速度传感器其中4个低速速度计和个标准传感器
CHANG’AN UNIVERSITY
传感器的选择 择传感器一般从以下几个方面进行考虑: (1)根据测量对象的特点确定传感器类别 (2)传感器的量程要适合 (3)频响范围要合适 (4)灵敏度适度 (5)传感器的稳定性要好 (6)传感器的质量要适合 (7)精度 本系统采用的传感器分为两种: 标准加速度传感器——用以采集高速轴部分的振动信号, 低速加速度传感器——用以采集低频振动信号。
- 1、下载文档前请自行甄别文档内容的完整性,平台不提供额外的编辑、内容补充、找答案等附加服务。
- 2、"仅部分预览"的文档,不可在线预览部分如存在完整性等问题,可反馈申请退款(可完整预览的文档不适用该条件!)。
- 3、如文档侵犯您的权益,请联系客服反馈,我们会尽快为您处理(人工客服工作时间:9:00-18:30)。
产品介绍 | introduction
系统构成
产品介绍 | introduction
实时监测机舱内 外温度 转速信对故障提取起到辅 助作用 传动链上6个加速度传感 器采集机组振动信号,其 中两个位XY方向双通道
采集发电机定子电压电流信 号,与振动信号相结合,提 高故障诊断准确率 系统结构框图
数据采集 | DA
旋转机械的微小故障一旦发展为严重故障,将会对昂贵的风电机组
造成不可恢复的损坏,引起严重的经济损失。 经过大量的实际数据总结,处于恶劣工况下的风电机组的故障多集 中于旋转机械和啮合机械中,发电机的定子转子的故障也越发的增多。 基于振动信号的旋转机械故障诊断技术的广泛有效应用和在行业内 已经取得的相当有效成果,使得风电机组状态监测系统发展极具战略意 义。
项目内容 | contents
1.风电场振动数据的二次接收及存储
2.振动数据的时域分析,时域振动状态参 数分析,正常、异常、故障报警处理 3.设备特征频率提取及频域分析,对轴 承、齿轮、叶片、发电机及塔架故障的诊 断
项目内容 | contents
4.历史分析,检测主要部件故 障的发生、发展趋势,为设备 维护提供依据 5.软件支持设备参数录入、便 于人员操作,联网后支持远程 诊断分析
创新
基于自主开发的嵌入式处理装置来实现高速信息采集、就地处理
分析功能
基于机组振动、转速、发电机电压/电流状态等实时数据进行 分析,实现对机组旋转连接设备的全面有效监测
该系统具备良好的开放性与可扩展性,多路模拟与开关扩展接口 与信号数据处理通道,方便系统的升级改造。
创新
系统具有光纤网络信息传输、断网自动互联功能。提供完善的网络扩展 功能,在多个风电场远程监控系统技术支持下,能够实现多机联合实时 在线监测。 采用Labview软件支撑平台,开发了基于风电机组实测信息、信号
项目过程 | progress
2013.5 与华能酒泉风电有限责任公司签订项目合同
2013.5~2013.7 调查研究、分析论证、方案设计 2013.7~2013.9 搭建硬件环境与软件开发 2013.9~2013.11 软硬件调试,研究,修改
2013.11-2013.12 现场安装调试,整理资 料,验收
风机振动检测及故障诊断系统与研 究软件开发
吕跃刚 教授
二〇一三年十二月
目录 | list
项目背景 项目内容 产品介绍 成果与创新
目录 | list
传动系统是实现风能转换和传递过程的主要承载部件。 风力发电机组主要部件寿命一般20年. 但是由于风电机组多数安装在西部和沿海地区,环境 条件差,机组经常工作在低温、沙尘、雷电、冰雪、风暴
分析与处理技术、时域与频域相结合的状态监测系统,并具有完全
的自主知识产权。
就地装置具有信号输入隔离、浮地、防雷击等功能,保障 设备安全正常运行。
thanks
控制系统
电气系统
0
2
4
6
8
平均故障停机时间(天)
项目背景 | backgrounds
1.减少风电机组故障发生 2.减少机组故障导致的经济损失 3.改善传统设备检修维护手段 4.提高风电机组运行可靠性 5.满足远程在线诊断要求
项目意义 | prospect
随着风力发电技术日趋成熟和装机容量的大规模增加,对风电机组 安全高效的运行有了更高的要求。
等恶劣环境条件,而且由于风速、载荷和风轮转速变化范
围大,上网要求高,导致机组运行工况复杂,极易造成风 电机组叶片和传动系统在寿命期内出现故障甚至损坏,影 响机组的安全可靠性。
项目背景 | backgrounds
风机各部件故障比例
项目背景 | backgrounds
传动系统 支撑架 发电机
齿轮箱
轮毂 机械刹车 叶片故障 偏航系统 液压系统 传感器
故障诊断 | FD
产品功能
权限管理将区分高级管理人员与一般操作人员
进入主监控界面后将显示整个风场各台风机的振动状态界面,风机按停 机、运行、报警故障、严重故障区分 点击对象菜单进入分析界面,按被测对象及部位分别对主轴承、齿轮箱、 发电机、叶片、塔架等进行时域及频域分析。
引入发电机状态监测部分,可即时监视发电机运行过程各参量变化及潜在故障信 息,通过电机信号输出分析与传统振动分析方法相结合,提高故障诊断的准确性和 可靠性。 数据处理是分析的必要步骤,软件中提供了数据截取、放大、滤波、窗函数等工 具,经过一定训练的操作人员可以掌握这些工具。
采用自主研发HDZTJC-4P 智能数据处理器设备。具
有很好稳定性和扩展性。
该装置集ARM-DSP技术为 一体,采用嵌入式设计理 念,高性能CPU,外扩丰 富外设接口,极大满足风 电场运行状态监测与分析 系统的实际应用需求 基于DSP数据处理器硬件结构
软件设计 | software
采用Labview图形化语言编程
可对指定设备单独进行详细故障分析
故障诊断 | FD
对具体设备的信号进行时、频域等全方面多角度分 析,寻找故障特征,应用到了小波降噪、包络谱、倒 频谱、功率谱密度等多个先进信号处理技术
利用XY振动传感器,结合频域积分技术,绘制主轴、 发电机转轴轴心轨迹图,能够直观地观察轴系运动状 态 加入发电机定子电压电流时、频域分析,在诊断发电 机本身故障的同时,与传统振动分析技术相结合,提 高诊断的准确率
界面整洁美观、简单易懂、人机交 互能力强
具有强大的数据分析和处理功能
软件设计 | software
软件整体框图
软件设计 | software
单台风机界面
主界面
分析界面
软件设计 | software
主界面和单台风机监测界面,可显示整体风机和单台风 机即时状态和数据,后者还可显示任意时间历史趋势
配备常见厂家产品配置库,用户可手动设置风机配置