集中供热锅炉控制系统的PLC控制
微型PLC在集中供热调度自动化系统中的应用

文章编号:1007-967X(2004)01-0049-02微型PLC在集中供热调度自动化系统中的应用¹周旭(鞍钢职工大学,辽宁鞍山114000)摘要:长期以来,供热SCADA系统的RTU都采用单片机为核心来设计,其价格低廉但开放性不好,而近年来出现的微型PLC则是一种性能价格比很高的产品,很多优点是单片机无法比拟的,本文比较了几种常用的RTU类型,并且给出了用PLC来设计RTU的一个实例。
关键词:调度自动化;SCADA系统;RTU;PLC中图分类号:TK3文献标识码:A1前言在城市供热系统中,调度起着指挥中枢的作用,加压站个数越多、管网分布越复杂,调度的作用就越大。
城市供热系统是一个复杂的、动态变化的系统,因此,调度室需要实时掌握整个供热管网的压力、温度分布情况,以及各个加压站的生产情况和其它一些异常事故(如爆管、抢修维修、火灾等),并且根据所掌握的情况来指挥各个加压站的设备开停,保持整个供热系统处于最优化的运行状态。
要保持整个供热系统处于最优化的运行状态,必须建立调度自动化系统,用调度自动化系统来替代传统的人工经验调度。
调度自动化系统包括以下一些内容:建立无线电SCADA系统,主要用于管网和加压站数据的采集;加压站出厂压力自动调节系统;供回水温度,主要用于出厂压力的调节;供热数据处理和传输系统,用于数据的处理和报表,实现无纸化调度;供热优化调度系统,用于对数据进行高层次的分析,实现优化调度,为企业创造良好的经济效益。
其中,无线电SCADA系统是整个调度自动化系统的基础,它一般包括中心主站、传输信道、远程采集端站(RTU)和现场一次仪表这几部分,本文就供热调度系统RTU设计选型和PLC的应用等问题做一些简单的探讨。
2几种类型的RTU的比较目前国内的供热调度系统主要采用以下几种类型的RTU:以单片机为核心的RTU单片机以其集成度高、价格低廉而深受工程技术人员的欢迎,目前国内很多SCADA系统的开发商都采用单片机来生产用于供热调度SCADA系统的RTU,早期的RTU一般采用8031系列的单片机,利用本身的I/O口和计数器来完成数字信号和脉冲信号的采集,利用外围的A/D转换芯片来完成模拟信号的采集,在90年代初期,带有A/D转换功能的8096/8098系列单片机也被大量采用(8098现在已经停产),目前,大量的厂家采用89C51/89C52系列的单片机来生产RTU。
PLC在锅炉控制系统中的作用

PLC在锅炉控制系统中的作用锅炉是工业生产中常用的热力设备,它负责将水或其他流体加热到所需温度,以满足生产过程中的热能需求。
为了保证锅炉能够高效、稳定地运行,控制系统的作用至关重要。
其中,可编程逻辑控制器(PLC)在锅炉控制系统中扮演着重要的角色。
一、PLC简介PLC是一种专门用于工业控制的计算机设备,它能够根据预先编写好的程序,对锅炉的各个部分进行自动控制。
PLC通常由CPU、输入输出模块和通信模块等组成,具备可编程、可扩展、可靠性高等特点。
二、PLC在锅炉控制系统中的应用1. 温度控制在锅炉中,温度控制是至关重要的,它直接影响锅炉的稳定性和效率。
PLC可以通过外部温度传感器获取实时温度数据,并对锅炉的加热器、循环泵等设备进行控制,以确保锅炉水温始终保持在设定范围内。
2. 压力控制锅炉的压力也是需要进行精确控制的参数之一。
过低的压力可能导致供热不足,过高的压力则可能引发爆炸等安全隐患。
PLC可以通过传感器实时监测锅炉的压力,并根据设定值自动调节燃烧器的工作状态,以保证锅炉的压力在安全范围内。
3. 水位控制锅炉的水位是影响锅炉正常运行的重要因素。
若水位过低,锅炉的加热管壁可能过热而损坏;若水位过高,又可能导致锅炉溢水。
PLC可以通过水位传感器监测锅炉的实时水位,并控制进水和排水设备的开关,以保持水位在安全范围内。
4. 烟气排放控制锅炉燃烧过程中会产生大量烟尘和有害气体,对环境造成污染。
PLC可以通过烟气传感器监测烟气的成分和排放浓度,并根据环保要求调整燃烧器的工作状态,以减少污染物的排放。
5. 故障诊断与报警锅炉系统中可能会出现各种故障,如传感器失效、设备故障等。
PLC可以通过自动检测和诊断系统中的故障,并根据设定的规则进行报警。
这样可以帮助运维人员及时发现和解决问题,保证锅炉的正常运行。
三、PLC在锅炉控制系统中的优势1. 稳定性高:PLC具备高性能的计算能力和稳定的特性,可以保证对锅炉各个参数的精确控制,提高系统的稳定性。
PLC在供热站自动控制系统中的应用

PLC在供热站自动控制系统中的应用摘要:在城市集中供热系统中,供热站作为热网系统的一个重要环节,直接决定供热站的控制效果。
加热站的控制效果直接决定了荣热战的能源消耗,同时也决定着采暖效果,自动控制系统的应用减轻了操作人员的劳动强度,甚至可以达到在无人值班的状态下保持运行。
关键词:PLC;供热站;自动控制系统;应用前言随着自动化及信息技术的不断提高和国家节能环保政策的实施,无人值守换热站智能控制系统凭借其高效率、高性能以及危险预报精度高等优点,已成为众多科研人员的研究热点。
为此供热站根据需要,逐步实现自动化控制系统,积极推进两化融合提升企业竞争力与管理能力。
1 PLC的用途目前PLC主要应用在4个方面:一是开关量的开环控制。
PLC的指令系统具有强大的逻辑运算能力,很容易实现定时、计数、顺序(步进)等各种逻辑控制方式。
二是模拟量闭环控制。
模拟量的闭环控制系统主要是对模拟量的输出值进行计算,通过计算来改变输入值,实现对系统的各种连续调节与控制。
三是数字量的智能控制。
控制系统具有旋转编码器和脉冲伺服装置(如步进电动机)时,可利用PLC实现接收和输出高速脉冲的功能,实现对数字量控制。
较为先进的PLC还专门开发了数字控制模块,可实现曲线插补功能,近年来推出的新型运动单元模块,还能提供数字量控制技术的编程语言。
四是数据采集与监控。
因为PLC主要用于现场控制,所以采集现场数据是十分必要的功能。
在此基础上将PLC与上位计算机或触摸屏相连接,既可以观察这些数据的数值,又能及时进行实时计算,有的PLC还具有数据记录单功能,可用一般个人电脑的存储卡插入到该单元中保存采集到的数据。
2 PLC在集中供热系统中的应用PLC在集中供热系统中的应用主要体现在以下几方面:一是通过室外温度实时调节一次网流量。
在室外安装一个温度变送器,将温度信号传入PLC控制系统中,PLC控制系统可根据预先编好的程序将循环泵的转速和室外温度联系起来,多大的温度对应多大的转速,这样就可以不用人工调节转速,而是通过PLC系统来自动、精准地调节转速,更加节约能源。
基于PLC的锅炉供暖监控系统设计

4、监控界面设计技术
4、监控界面设计技术
在上位机监控界面方面,我们采用了组态软件来设计监控界面。组态软件是 一种广泛使用的工业自动化监控软件开发工具,它支持多种图形元素和控件,可 以方便地实现实时数据展示、报警提示、历史数据查询等功能。我们根据锅炉的 实际运行情况,设计了相应的监控界面,并编写了相关的脚本代码,以实现对锅 炉运行数据的实时展示和报警提示等功能。
2、控制技术
2、控制技术
在控制方面,我们采用了PID(比例-积分-微分)控制算法来实现对锅炉的燃 烧和给水控制。PID控制是一种经典的连续控制系统,它通过比较设定值与实际 值之间的误差来计算控制量,实现对被控对象的精确控制。我们根据锅炉的实际 情况,对PID控制算法进行了相应的调整和优化,以实现对锅炉的燃烧和给水系 统的有效控制。
二、关键技术
1、数据采集技术
1、数据采集技术
在数据采集方面,我们采用了高精度传感器和PLC模拟量输入模块,实现了对 锅炉运行参数的实时监测。传感器包括温度传感器、压力传感器和水位传感器等, 它们将采集到的信号通过变送器转换为标准的电信号,再通过PLC模拟量输入模 块输入到PLC中进行数据处理。
一、系统需求与设计
一、系统需求与设计
锅炉供暖系统的主要任务是维持锅炉中水的温度在设定的范围内,同时也要 确保供暖设备的正常运行。因此,系统的需求主要包括:
一、系统需求与设计
1、实时监测锅炉的水温、压力等参数; 2、通过调节锅炉的燃烧器输出,控制水温; 3、保障供暖设备的稳定运行;
一、系统需求与设计
三、应用效果
3、提高了管理效率。通过远程监控锅炉的运行状态,可以在上位机上实现锅 炉的集中管理和监控,从而提高了管理效率。
谢谢观看
基于PLC-PID参数整定的锅炉水温控制系统
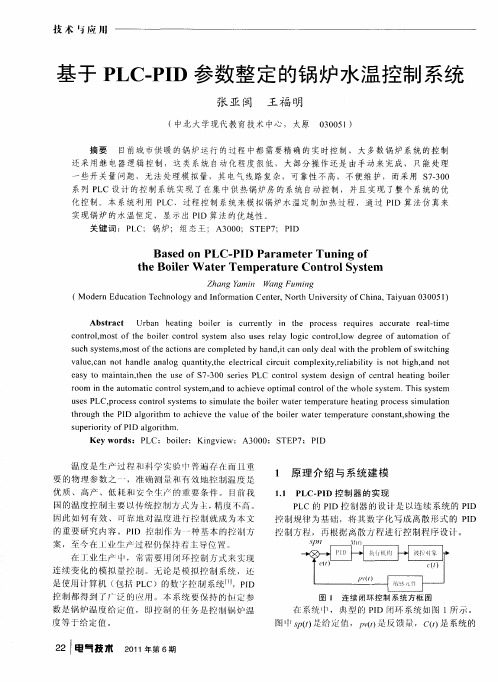
假 设采样 周期为 ,系统开始 的时刻 为 t0 =,
刖 形积 分近 似精确秋 分,用差 分近似 精确微 分 , 将 式 ( ) 离 敞 化 , 第 次 采 样 时 控 制 器 的 输 出 为 1
变 【
M = K I .
e K |Kt + + ∑e d
为
频
器
分 别 为 模 拟 量 在 ( 、 v ) et、 M( 在 第 n次 f (、 ( ) , ) , )
采样 时的数字 量 。
图 3 A3 0 0 0系 统 结 构
图 2 P C 闭 环 控 制 系 统 方 框 图 L
许 多 控 制 系 统 内 ,可 能 只 需 要 P I D 中 的 、 、
工业用板 武换热 器 ,两个 水泵 ,大功 率_】 管 ,滞 J热 J 【
后 时 町以调整 的滞后 系统 ,一个 硬件 联锁保 护系
统 。传 感 器 和 执 行 器 系 统 包 括 5个 温 度 、3个 液 位 、 1 爪 力 、 1 电 磁 流 量 计 、 1个 涡 轮 流 量 计 、 1个 个 个 电动 调 阀 、 两 个 电磁 阀 、2个 液 位 丌 关 。 冈 4为 一 个 闭 环 单 路 的锅 炉 温 度 控 制 系 统 的
度 的给定 值 。过程变 量是经 A D转 换和 计算后 得剑 /
的 被 控 量 的 实 测 值 , 如 加 热 炉 温 度 的 测 量 值 。 给 定
值 与过程 变量 都是与被 控对 象有 关 的值 ,对 于不 删
的 系 统 , 它 们 的 大 小 、 范 围 与 工 单 位 有 很 大 的 区 别 。应 P C 的 PD 指 令 对 这 些 量 进 行 运 算 之 前 , L I 必须将其 转换成 标准化 的浮 点数( 数1 实 。 1 . 锅 炉 水 温 定 值 控 制 系 统 2
热水锅炉的PLC控制器

热水锅炉的PLC控制器热水锅炉是一个非常重要的设备,它的作用在很多工业生产线上都是不可缺少的。
在使用热水锅炉的时候,我们需要关注的一个非常重要的问题就是它的控制系统。
现在,大多数热水锅炉都采用了PLC控制器来控制温度、压力等参数。
今天,我们就来深入了解一下热水锅炉的PLC控制器。
什么是PLC控制器?PLC控制器是一种以可编程方式控制工业机器和过程的电子设备。
它们通常由一个中央处理器、输入输出模块、内存和其他辅助部件组成。
PLC控制器的功能包括监测输入设备,例如传感器和开关,执行控制任务以及驱动输出设备,如电机和阀门。
PLC控制器之所以被广泛采用,是因为它们可以处理和控制复杂的过程和任务。
此外,PLC控制器也可以很容易地编程和修改,使得改变生产线流程和机器控制变得非常方便。
热水锅炉的PLC控制器工作原理PLC控制器控制热水锅炉的过程非常简单。
首先,传感器测量锅炉的温度和压力等参数。
然后,这些数据就被传输到PLC控制器中。
PLC控制器会根据预设的阈值来进行判断,通过控制电磁阀和电机来调整锅炉的温度和压力等参数,以保持在一定的安全和正常工作范围内。
为什么要使用PLC控制器控制热水锅炉?PLC控制器可以自动监控和控制热水锅炉的输出温度和压力等参数。
通过使用PLC控制器,锅炉的温度和压力等参数可以得到更加准确和可靠的控制。
这样可以保证锅炉的安全性和稳定性,并且可以大大降低操作员的工作量。
此外,PLC控制器还可以记录锅炉的生产参数,可以及时检测和排除锅炉故障,提高设备的使用寿命。
同时,PLC控制器的应用还可以节约能源和减少成本,因为它们通常可以根据生产线需要来进行调节。
PLC控制器的优点和缺点使用PLC控制器的优点主要有以下几个:1. 提高了生产线的稳定性和安全性;2. 去除了人为操作的误差和干扰,可以提高生产的精度;3. 可以及时调整参数,避免产生浪费;4. 可以实现过程自动化,减少人力成本和操作困难。
PLC控制器的缺点主要是:1. PLC控制器的价格相对比较高;2. PLC控制器的编程需要专业的人员来完成,如果出现了问题,维修也需要专业人员来解决;3. 需要不断的对PLC控制器进行升级和维护,影响生产成本。
基于plc的锅炉控制系统的设计方案
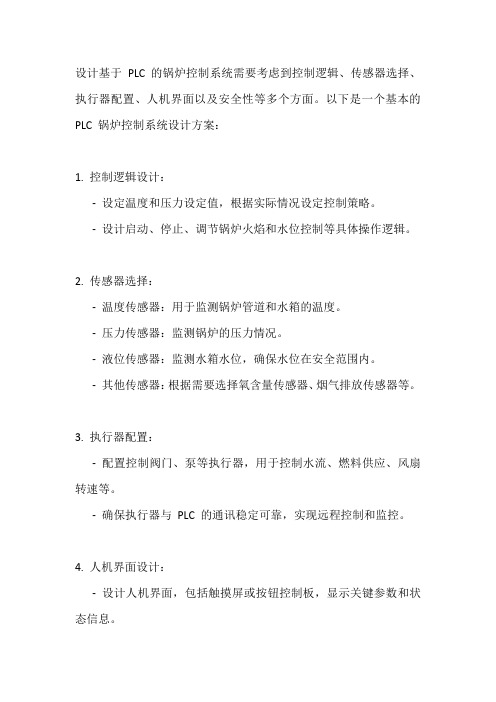
设计基于PLC 的锅炉控制系统需要考虑到控制逻辑、传感器选择、执行器配置、人机界面以及安全性等多个方面。
以下是一个基本的PLC 锅炉控制系统设计方案:1. 控制逻辑设计:-设定温度和压力设定值,根据实际情况设定控制策略。
-设计启动、停止、调节锅炉火焰和水位控制等具体操作逻辑。
2. 传感器选择:-温度传感器:用于监测锅炉管道和水箱的温度。
-压力传感器:监测锅炉的压力情况。
-液位传感器:监测水箱水位,确保水位在安全范围内。
-其他传感器:根据需要选择氧含量传感器、烟气排放传感器等。
3. 执行器配置:-配置控制阀门、泵等执行器,用于控制水流、燃料供应、风扇转速等。
-确保执行器与PLC 的通讯稳定可靠,实现远程控制和监控。
4. 人机界面设计:-设计人机界面,包括触摸屏或按钮控制板,显示关键参数和状态信息。
-提供操作界面,方便操作员设定参数、监控运行状态和进行故障诊断。
5. 安全性设计:-设计安全保护系统,包括过压保护、过温保护、水位保护等,确保锅炉运行安全。
-设置报警系统,当参数超出设定范围时及时警示操作员。
6. 通讯接口:-考虑与其他系统的通讯接口,如SCADA 系统、远程监控系统等,实现数据传输和远程控制。
7. 程序设计:-使用PLC 编程软件编写程序,包括控制逻辑、报警逻辑、自诊断等功能。
-测试程序逻辑,确保系统稳定可靠,符合设计要求。
以上是基于PLC 的锅炉控制系统设计方案的基本步骤,具体设计还需根据实际情况和需求进行调整和优化。
在设计过程中,还需遵循相关标准和规范,确保系统安全可靠、运行稳定。
基于PLC的锅炉供热控制系统的设计

基于PLC的锅炉供热控制系统的设计一、本文概述随着科技的不断发展,可编程逻辑控制器(PLC)在工业自动化领域的应用日益广泛。
作为一种高效、可靠的工业控制设备,PLC以其强大的编程能力和灵活的扩展性,成为现代工业控制系统的重要组成部分。
本文旨在探讨基于PLC的锅炉供热控制系统的设计,通过对锅炉供热系统的分析,结合PLC控制技术,实现对供热系统的智能化、自动化控制,提高供热效率,降低能耗,为工业生产和居民生活提供稳定、可靠的热源。
文章首先介绍了锅炉供热系统的基本构成和工作原理,分析了传统供热系统存在的问题和不足。
然后,详细阐述了PLC控制系统的基本原理和核心功能,包括输入/输出模块、中央处理单元、编程软件等。
在此基础上,文章提出了基于PLC的锅炉供热控制系统的总体设计方案,包括系统硬件选型、软件编程、系统调试等方面。
通过本文的研究,期望能够实现对锅炉供热控制系统的优化设计,提高供热系统的控制精度和稳定性,降低运行成本,促进节能减排,为工业生产和居民生活提供更加安全、高效的供热服务。
也为相关领域的研究人员和技术人员提供有价值的参考和借鉴。
二、锅炉供热系统基础知识锅炉供热系统是一种广泛应用的热能供应系统,其主要任务是将水或其他介质加热到一定的温度,然后通过管道系统输送到各个用户端,满足各种热需求,如工业生产、居民供暖等。
该系统主要由锅炉本体、燃烧器、热交换器、控制系统和辅助设备等几部分构成。
锅炉本体是供热系统的核心设备,负责将水或其他介质加热到预定温度。
其根据燃料类型可分为燃煤锅炉、燃油锅炉、燃气锅炉、电锅炉等。
锅炉的性能参数主要包括蒸发量、蒸汽压力、蒸汽温度等。
燃烧器是锅炉的重要组成部分,负责燃料的燃烧过程。
燃烧器的性能直接影响到锅炉的热效率和污染物排放。
燃烧器需要稳定、高效、低污染,同时要适应不同的燃料类型和负荷变化。
热交换器是锅炉供热系统中的关键设备,负责将锅炉产生的热能传递给水或其他介质。
热交换器的设计应保证高效、稳定、安全,同时要考虑到热能的充分利用和防止结垢、腐蚀等问题。
基于PLC控制的电锅炉控制系统

基于PLC控制的电锅炉控制系统电锅炉控制系统是现代工业制造中常见的一种设备,它通过PLC(可编程逻辑控制器)来实现对电锅炉的精确控制。
PLC控制技术具有灵活、方便、可靠等优点,能够实现复杂的逻辑控制和自动化控制功能。
本文将从PLC控制系统的原理、功能及特点入手,结合电锅炉的工作原理,详细介绍基于PLC控制的电锅炉控制系统的设计与实现。
1. PLC控制系统原理PLC控制系统是一种专门设计用于工业自动化控制的设备,其核心是一个可编程的CPU,通过不同的输入/输出模块和通信模块,与外部传感器、执行器等设备连接,实现对生产过程的控制。
PLC控制系统通过预先编写好的程序,根据不同的输入信号执行相应的逻辑控制,以达到自动化控制的目的。
2. 电锅炉工作原理电锅炉是一种利用电能进行加热的设备,通常由加热元件、控制系统、水泵等部件组成。
在工作过程中,电能被加热元件转换为热能,将水加热至设定的温度,为生产或生活提供热水或蒸汽。
电锅炉的控制系统通常包括温度传感器、压力传感器、水位传感器等,用于监测和控制锅炉的工作状态。
3. 基于PLC控制的电锅炉控制系统设计基于PLC控制的电锅炉控制系统主要由PLC控制器、传感器、执行器、人机界面等部件组成。
在设计过程中,首先需要根据电锅炉的工作原理和需求确定系统的功能要求和控制策略,然后编写PLC程序实现相应的逻辑控制。
通过合理的硬件布局和接线连接,将各部件连接到PLC控制器上,实现信号的采集和输出。
4. 控制系统功能与特点基于PLC控制的电锅炉控制系统具有如下功能与特点:1)灵活性:PLC控制系统可根据需要进行程序修改,实现不同的控制策略;2)可靠性:PLC控制器具有较高的稳定性和可靠性,可以长时间稳定运行;3)精确性:通过PLC控制系统可以实现对电锅炉的精确控制,提高生产效率和产品质量;4)扩展性:PLC控制系统可根据需要扩展输入/输出模块和功能模块,实现系统的功能扩展。
5. 控制系统优化与应用为了进一步优化电锅炉控制系统的性能,可以采用PID控制算法、模糊控制算法等先进的控制技术,提高系统的响应速度和稳定性。
集中供热锅炉控制系统的 PLC 控制

行对 相应外设的驱动。这个阶段完成之后才是 PLC真正输 出的完成 。
3结语
PLC通常是用于工业环境 中的 ,是一种对数字 2 PLC控制器在集 中供热上应具备的功能
集 中供 热锅炉 控制 系统若 是能 够有 效采
运算 的操作 的电子装置 。PLC采用 的是可编程
用 PLC进行 控制 ,能够在 很大程 度上 简化操
运 行 。
【关键词】 集中供 热 锅炉控 制 系统 PLC控制
1.3 输 出刷 新 阶 段
(8)在现 场控制上 ,PLC系统 除了要实 现
上诉 的功能之 外 ,还要 具有远程 的传 输功 能。
在 扫 描工 作完 成 之后 ,PLC控 制就 自动 远控控 制能够让 操作人 员不必进行实地监管变
线路 。在 扫描之 后,系统 自动进行相应的逻辑 务的完成 。
运算 。根据 系统 的运算结果 ,存储的状态要进
(7)要具备 数据的处 理能力 。通 过数据 的
行相 应的刷新 ,以此来决定是否使用梯形图规 处理 ,系统要能够分 析出从数据中存在的异 常
定 的指令 来进行控制
情 况 ,及时发现故 障所在 。
的存储器 ,可以对 其内部存储的资料进行逻辑
PLC控 制器 主要 是 由系统 控制 与液 晶显 作系统 ,提高设备运行 时的稳定性与可靠性 。
运算 工作 。近年 来 ,较大型的用于集 中供热的 示 终端操作组成 的。系统控 制主要包含 I/O模 在 对设备 进行控 制 时,由于 PLC本身 具有数
以便在事故发生之后及时通知现场监 管人员 。
在用 户 的执 行 阶段 ,PLC是按 照 由上 至
(5)在数 据的 发送 上要及 时,并保 障发送
PLC电热锅炉供热控制系统设计

PLC电热锅炉供热控制系统设计一、引言随着社会的不断发展,人们对于供热系统的要求也越来越高。
为了提高供热系统的自动化程度和安全性,PLC(可编程逻辑控制器)技术得到了广泛应用。
本文将针对PLC电热锅炉供热控制系统的设计进行详细讨论,以确保系统运行稳定、安全。
二、PLC电热锅炉供热控制系统设计方案1. 系统架构设计PLC电热锅炉供热控制系统主要由PLC控制器、传感器、执行器等组成。
其中,PLC控制器作为系统的大脑,负责对各个执行器的控制和监测工作。
传感器用于采集环境温度、水箱水位等信息,反馈给PLC控制器,从而实现对系统的自动控制。
2. 系统功能设计(1)温度控制功能:通过传感器实时监测环境温度,当环境温度低于设定值时,PLC控制器将启动电热锅炉,加热水箱中的水,直到温度达到设定值为止。
(2)水位控制功能:传感器监测水箱水位,当水位低于设定值时,PLC将启动给水泵进行给水,保证水箱水位在合适范围内。
(3)故障诊断功能:系统内置故障诊断模块,通过监测系统各部件的运行状态,及时发现故障并进行报警提示,保证系统安全稳定运行。
3. 系统性能设计(1)稳定性:系统采用双PLC热备份设计,确保系统在一台PLC故障时可以自动切换到备用PLC,保证系统的连续运行。
(2)可靠性:系统采用高品质的传感器和执行器,具有较高的抗干扰能力和稳定性,从而确保系统的可靠性。
4. 系统通信设计系统采用以太网通信方式,PLC控制器通过以太网与上位机连接,实现对系统的远程监控和控制。
上位机可以实时监测系统运行状态、温度水位等信息,方便操作人员进行远程管理。
三、系统实施与调试1. 硬件安装:安装PLC控制器、传感器、执行器等硬件设备,确保设备安装位置合理,连接正确。
2. 软件编程:编写PLC控制程序,包括温度控制、水位控制、故障诊断等功能模块。
3. 系统调试:进行系统联调和调试,检验系统各部件是否正常工作,确保系统实现预期功能。
四、系统运行维护1. 定期检查:定期检查系统各部件的运行状态,及时更换老化部件,保持系统的正常运行。
热水锅炉-PLC控制原理图

由 Autodesk 教育版产品制作
兴和集中供热锅炉房自控 图号
+
设计
校对
配电室控制柜(+ K3)原理图 总图号 -
第
页共
页
制图
会签
比例
数量
包头市爱能控制工程
审核
档案
年 月日
有限责任公司
由 Autodesk 教育版产品制作
由 Autodesk 教育版产品制作 PDF 文件使用 "pdfFactory Pro" 试用版本创建
PDF 文件使用 "pdfFactory Pro" 试用版本创建
由 Autodesk 教育版产品制作
由 Autodesk 教育版产品制作 PDF 文件使用 "pdfFactory Pro" 试用版本创建
2AI
由 Autodesk 教育版产品制作
3AI2
由 Autodesk 教育版产品制作
由 Autodesk 教育版产品制作
兴和集中供热锅炉房自控 图号
+
设计
校对
配电室控制柜(+ K3)原理图 总图号 -
第
页共
页
制图
会签
比例
数量
包头市爱能控制工程
审核
档案
年 月日
有限责任公司
由 Autodesk 教育版产品制作
由 Autodesk 教育版产品制作 PDF 文件使用 "pdfFactory Pro" 试用版本创建
由 Autodesk 教育版产品制作
兴和集中供热锅炉房自控 图号
+
设计
校对
配电室控制柜(+ K3)原理图 总图号 -
基于PLC的锅炉加热温度控制系统设计

基于PLC的锅炉加热温度控制系统设计锅炉加热温度控制系统设计是一个非常重要的工程项目,特别是在工业生产中。
PLC(可编程逻辑控制器)是一种高级自动化控制设备,可以实现对锅炉加热温度的精确控制。
本文将介绍一个基于PLC的锅炉加热温度控制系统的设计。
【系统概述】该系统的基本目标是稳定地控制锅炉的加热温度,保证锅炉在正常工作范围内运行,并尽可能地提高热效率。
具体来说,系统需要实现以下功能:1.实时监测锅炉温度。
2.控制锅炉加热功率。
3.响应温度变化,并自动调整加热功率。
4.报警和故障保护功能。
【系统设计】1.硬件设计:硬件部分包括传感器、执行机构和PLC。
传感器用于实时监测锅炉温度,常用的温度传感器有热电偶和敏感电阻。
执行机构用于控制加热功率,可采用电磁阀或电加热器。
PLC负责处理数据和控制信号,可以选择常用的西门子、施耐德等PLC。
2.软件设计:软件部分主要包括PLC编程和人机界面设计。
PLC编程可以使用基于LD(梯形图)或SFC(时序功能图)的编程语言,根据具体控制要求,设计合适的控制算法和逻辑。
人机界面设计可以使用HMI(人机界面)或SCADA(监控与数据采集系统),实时显示锅炉温度、加热功率和系统状态,并提供控制和设定温度的功能。
3.控制策略设计:控制策略需要根据具体情况进行设计,一般分为开环控制和闭环控制两种。
开环控制是根据经验或数学模型预先设定温度和加热功率曲线,直接输出控制信号。
闭环控制则根据实时监测的温度反馈信息,通过控制算法动态调整加热功率,使实际温度尽可能接近设定温度。
4.报警和故障保护设计:系统需要具备报警和故障保护功能,当温度超出设定范围或系统出现故障时,及时发出警报并采取相应的措施,以保护锅炉和工艺安全。
【实施与测试】在实施前,需要进行系统调试,确保PLC编程和硬件连接正常。
在实际运行中,需要对系统进行定期检测和维护,以保证系统的稳定性和可靠性。
总结起来,基于PLC的锅炉加热温度控制系统的设计是一个复杂的工程,需要综合考虑硬件和软件的因素。
供暖锅炉温度和压力的PLC控制
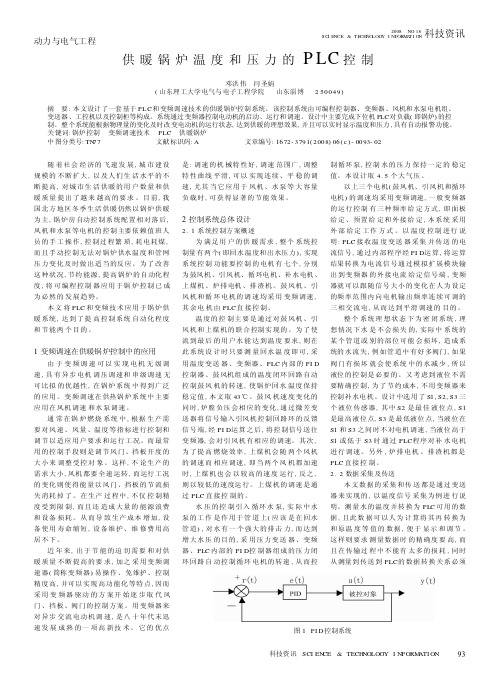
3科技资讯科技资讯S I N &T NOLOGY I NFORM TI ON2008NO .18SC I ENCE &TECH NO LOG Y I NFOR M A TI O N 动力与电气工程随着社会经济的飞速发展,城市建设规模的不断扩大,以及人们生活水平的不断提高,对城市生活供暖的用户数量和供暖质量提出了越来越高的要求。
目前,我国北方地区冬季生活供暖仍然以锅炉供暖为主,锅炉房自动控制系统配置相对落后,风机和水泵等电机的控制主要依赖值班人员的手工操作,控制过程繁琐,耗电耗煤,而且手动控制无法对锅炉供水温度和管网压力变化及时做出适当的反应。
为了改善这种状况,节约能源,提高锅炉的自动化程度,将可编程控制器应用于锅炉控制已成为必然的发展趋势。
本文将PLC 和变频技术应用于锅炉供暖系统,达到了提高控制系统自动化程度和节能两个目的。
1变频调速在供暖锅炉控制中的应用由于变频调速可以实现电机无级调速,具有异步电机调压调速和串级调速无可比拟的优越性,在锅炉系统中得到广泛的应用。
变频调速在供热锅炉系统中主要应用在风机调速和水泵调速。
通常在锅炉燃烧系统中,根据生产需要对风速、风量、温度等指标进行控制和调节以适应用户要求和运行工况。
而最常用的控制手段则是调节风门、挡板开度的大小来调整受控对象。
这样,不论生产的需求大小,风机都要全速运转,而运行工况的变化则使得能量以风门、挡板的节流损失消耗掉了。
在生产过程中,不仅控制精度受到限制,而且还造成大量的能源浪费和设备损耗。
从而导致生产成本增加,设备使用寿命缩短,设备维护、维修费用高居不下。
近年来,出于节能的迫切需要和对供暖质量不断提高的要求,加之采用变频调速器(简称变频器)易操作、免维护、控制精度高,并可以实现高功能化等特点,因而采用变频器驱动的方案开始逐步取代风门、挡板、阀门的控制方案。
用变频器来对异步交流电动机调速,是八十年代末迅速发展成熟的一项高新技术。
基于PLC的锅炉控制系统的设计
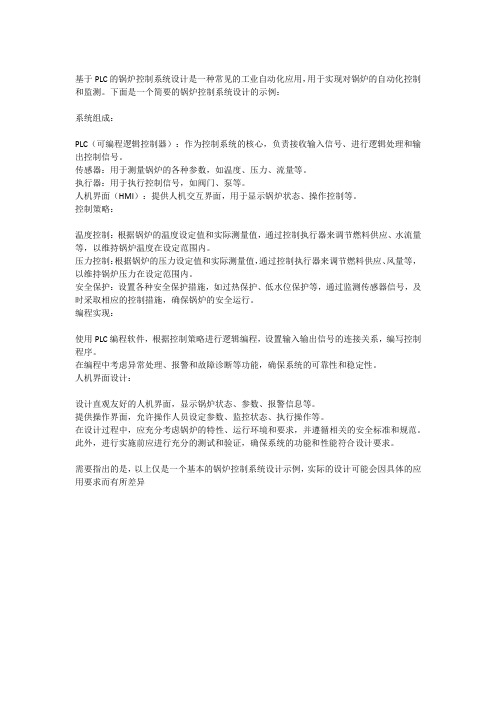
基于PLC的锅炉控制系统设计是一种常见的工业自动化应用,用于实现对锅炉的自动化控制和监测。
下面是一个简要的锅炉控制系统设计的示例:
系统组成:
PLC(可编程逻辑控制器):作为控制系统的核心,负责接收输入信号、进行逻辑处理和输出控制信号。
传感器:用于测量锅炉的各种参数,如温度、压力、流量等。
执行器:用于执行控制信号,如阀门、泵等。
人机界面(HMI):提供人机交互界面,用于显示锅炉状态、操作控制等。
控制策略:
温度控制:根据锅炉的温度设定值和实际测量值,通过控制执行器来调节燃料供应、水流量等,以维持锅炉温度在设定范围内。
压力控制:根据锅炉的压力设定值和实际测量值,通过控制执行器来调节燃料供应、风量等,以维持锅炉压力在设定范围内。
安全保护:设置各种安全保护措施,如过热保护、低水位保护等,通过监测传感器信号,及时采取相应的控制措施,确保锅炉的安全运行。
编程实现:
使用PLC编程软件,根据控制策略进行逻辑编程,设置输入输出信号的连接关系,编写控制程序。
在编程中考虑异常处理、报警和故障诊断等功能,确保系统的可靠性和稳定性。
人机界面设计:
设计直观友好的人机界面,显示锅炉状态、参数、报警信息等。
提供操作界面,允许操作人员设定参数、监控状态、执行操作等。
在设计过程中,应充分考虑锅炉的特性、运行环境和要求,并遵循相关的安全标准和规范。
此外,进行实施前应进行充分的测试和验证,确保系统的功能和性能符合设计要求。
需要指出的是,以上仅是一个基本的锅炉控制系统设计示例,实际的设计可能会因具体的应用要求而有所差异。
浅谈供暖锅炉设备控制系统中PLC的合理选择

浅谈供暖锅炉设备控制系统中PLC的合理选择作者:王江来源:《科技创新导报》2011年第08期摘要:随着PLC在锅炉系统中的应用和推广,PLC种类越来越繁多,其机型、性能、容量、编程方法等方面都各不相同。
在供暖锅炉设备控制系统中的PLC的合理选择方面,从机型、I/O、存储器、编程器及外部设备和安全运行环境等方面分析了锅炉系统的一般选择方法。
关键词:供暖锅炉 PLC 机型 I/O 编程器中图分类号:TK323 文献标识码:A 文章编号:1674-098X(2011)03(b)-0070-01可编程控制器PLC是以微处理器为核心的数字运算操作的电子运算装置,目前在锅炉系统中发挥越来越大的作用,但是市面的PLC种类繁多,性能、指令系统、编程方法等方面存在很大的差异,因此,选择合理的PLC,对于提高PLC在供暖锅炉系统中的应用有着非常重要的意义。
1 锅炉系统PLC的合理选择1.1 机型选择目前市场上流行的机型主要有以下几种:施耐德公司的Quantum、Premium、Momentum等产品,罗克韦尔公司的SLC、Micro、Control、Logix等产品,西门子公司的SIMATIC S7-400、300、200系列产品,GE公司的欧姆龙、三菱、富士、松下等产品。
在选择PLC机型时应满足以下基本原则:首先,应该满足功能需求,供暖锅炉是一种多变量系统,被控制量之间的关系复杂,耦合程度高,因此,在选择PLC机型时,在功能上可以以供水温度、烟气氧量、炉膛负压等作为控制参数,同时具有PID控制,能够加大或解除给煤调节、送风机和引风机调节,从而得到给煤量,送风量和引风量的最佳参数。
其次,由于供暖锅炉虽然工艺固定,但是由于其使用环境复杂,因此,应该选用模块式结构的PLC。
第三,供暖锅炉的控制过程比较复杂,需要实现PID运算、循环控制和通信联网等,因此应该选择中高档机型。
另外,同一个企业应该选用同样的机型,在机型统一的情况下,PLC模块可互相作为备用,即可降低风险,也可以节约技术人员的技术培训方面的经济投入,并可以实现资源共享,便于集中管理。
电热锅炉供热系统的PLC控制程序设计

xxxxxxx机电工程系毕业设计论文电热锅炉供热系统的PLC控制程序设计题目专业名称学生姓名指导教师毕业时间绪论现在生产线控制的主流品种是以继电器、接触器为主的控制装置。
继电器、接触器是一些电磁开关。
由励磁线圈、铁心磁路、触点等部件组成。
通过继电器接触器等其它控制元件的线路连接,可以实现一定的控制逻辑,从而实现设备的各种操作控制。
人们将由导线连接决定器件间的逻辑关系的控制方式称为接线逻辑。
随着工业自动化的程度的不断提高,使用继电器电路构成工业控制系统的缺陷不断暴露出来。
首先是复杂的系统使用成百上千个各种各样的继电器,成千上万根导线连接的密如蛛网。
只要有一个电器,一根导线出现故障,系统就不能工作,这就大大降低了这种接线逻辑的可靠性。
其次是这样的系统维修机改造很不容易,特别是技术改造,当试图改造工作设备的工作过程以改善设备各功能时,人们宁愿重新生产一套控制设备都不愿将继电器控制柜中的线路重接。
而PLC由于采用现代大规模集成电路技术,采用严格的生产工艺制造,内部电路采用了先进的抗干扰技术,具有很高的可靠性。
同时PLC用存储逻辑代替接线逻辑,大大减小了控制设备的外部接线,是控制系统设计及建造的周期大大缩短了。
同时维护也变得容易起来。
更重要的是同一设备经过改变程序改变生产过程成为可能。
本文以PLC技术在锅炉多功能供热系统为例,来阐明PLC在工业控制中发挥的巨大作用关键词:锅炉多功能供热;PLC;目录1 绪论 (2)1.1 PLC的基本概念 (5)1.2 PLC的诞生 (5)1.3 PLC的特点 (6)2 PLC的介绍 (7)2.1 PLC的流派 (7)2.2 PLC的结构和工作原理 (8)3 PLC的应用领域 (11)3.1开关量的逻辑控制 (11)3.2模拟量控制 (11).3.3运动控制 (12)3.4过程控制 (12)3.5数据控制 (12)4 PLC的基本结构 (12)4.1中央处理单元 (13)4.2 存储器 (13)4.3I/O模块 (14)4.4 电源 (15)4.5 底板或机架 (16)4.6 PLC系统的基本设备 (16)5 PLC的基本工作原理 (16)5.1 扫描技术 (16)5.2 PLC与继电器控制与系统微机区别 (18)5.3 基本指令系统特点 (18)5.4编程语言的形式 (19)5.5 PLC控制系统的设计基本原则 (20)5.6 PLC程序的内容和质量评价指标 (21)5.7 PLC程序的调试方法及步骤 (22)5.8 PLC的造型方法 (23)5.9经济性考虑 (27)6 基于PLC的电热锅炉供热控制系统设计 (28)6.1电热锅炉供热控制系统设计要求 (29)6.2电热锅炉供热控制系统设计方案 (30)6.3电热锅炉供热控制系统设计的程序部分的介绍 (34)致谢 (37)参考文献 (38)1.1 PLC的基本概念PLC即可编程控制器(Programmable logic Controller),是指以计算机技术为基础的新型工业控制装置。
基于PLC的锅炉控制系统的设计

基于PLC的锅炉控制系统的设计本文介绍基于PLC的锅炉控制系统的设计的背景和目的。
锅炉控制系统是基于PLC(可编程逻辑控制器)的设计,采用了分布式控制策略。
整体架构包括以下几个组成部分:1.控制器控制器是锅炉控制系统的核心部分,由PLC实现。
PLC具备高速计算能力和强大的输入输出功能,可以对各个设备进行监控和控制。
它接收来自传感器的输入信号,并根据预设的逻辑和算法进行实时处理,向执行器发送输出信号以控制设备运行。
2.传感器传感器负责将锅炉系统的各个参数转化为电信号,并传输给PLC进行处理。
常见的传感器包括温度传感器、压力传感器、流量传感器等。
3.执行器执行器根据PLC的控制信号来执行相应的操作,如调节燃料供给、控制排放阀等。
它们与PLC之间通过信号线或总线进行连接。
4.人机界面人机界面提供给操作员与锅炉控制系统进行交互的界面。
它可以是触摸屏、计算机软件等形式,用于监视系统运行状态、设定参数以及显示报警信息等。
5.通信模块通信模块用于实现锅炉控制系统与外部设备的数据传输和通信。
它可以连接到局域网或远程服务器,实现与其他系统或监控中心的数据交互。
6.电源供应为了保证锅炉控制系统的稳定运行,需要提供可靠的电源供应。
这可以通过备用电源或UPS(不间断电源)来实现。
综上所述,基于PLC的锅炉控制系统采用分布式控制策略,通过控制器、传感器、执行器、人机界面、通信模块和电源供应等组成部分协同工作,实现对锅炉设备的监控和控制。
本文介绍基于PLC的锅炉控制系统所采用的控制策略和算法。
控制策略是指通过采取不同的控制方法和算法,在锅炉运行中实现温度、压力、流量等参数的稳定控制。
基于PLC的锅炉控制系统采用了以下主要的控制策略:PID控制:PID(比例、积分、微分)控制是一种常用的控制方法。
它通过根据控制对象的偏差来调节控制器的输出,使得偏差逐渐趋向于零,从而实现控制目标。
在锅炉控制系统中,PID控制常用于调节温度、压力和流量等参数。
供热电锅炉的PLC控制系统优化设计

O p i a e i n f r PLC o t o y t m fhe tng ee t i ie tm l d sg o c n r l s se o a i l c r c bo l r
G UO a s a H ih n
( rh atDini ies y in 1 2 1 Note s a l Unv ri ,Jl 3 0 2,C ia t i hn )
核 心 。采 用 4组 电 加 热 管 自动 投 切 的控 制 方 式 , 证 了 系 统 的 可 靠 性 与 经 济 性 , 给 出 了 基 本 的 硬 件 配 置 和 编 程 保 并
原理 。
关 键 词 : 加热 锅 炉 ; 编程 序控 制 器 ( L ) 控 制 方 式 ; 靠 性 电 可 PC ; 可 中 图 分 类 号 :T 2 3 P 7 文 献 标 识 码 :A 文 章 编 号 :0 2—16 ( 0 1 0 0 7 0 10 6 3 2 1 ) 3— 18— 2
1 基 于 P C的具 有较 高 自动化 程度 的电热锅 炉 控 套 L 制 系统 。
组数 , 反之 , 少 电加 热 管组 数 , 减 以达 到 节 约用 电量
的 目的 ; 锅炉 中通 过 电加 热 管 加 热 的水 通 过 循 环 泵
直 接 向供 暖 系统供 热 , 环 泵 有 主泵 和 备 用 泵 可 供 循
Absr c : s p p rpu sfr r st e o tma e in fra o tc c n r ls se o lc rc b i rwh c s sS c t a t Thi a e t o wa d h p i ld sg o utma i o to y t m fe e ti ol ih u e i - e me s S —2 0 PL a o e a c r i g t r o .p o o e o a o u o t wic ngwh c u r n e st e r l・ n 7 0 C sc r c o d n owo k f w l r p s st d pta t ma i s thi ih g a a te h e i c a i t n c n my o h y t m n r vd s b sc h r wa e p o l sa d p o r mm ig p i c p e . b l y a d e o o ft e s se a d p o i e a i a d r r f e n r g a i i n rn i ls
基于PLC的热水锅炉自动化控制系统

基于PLC的热水锅炉自动化控制系统【摘要】本文以作者所经历的项目现场的锅炉为背景,分析了基于PLC的供暖锅炉的自动化控制。
结合了工作调试中总结出来的一些工作经验和一些控制思路,分析出几个重要环节的控制思路,以更好的控制给煤量、鼓风量、引风量、供回水温度等参数,以满足生产工艺要求,有效地降低能耗,提高生产管理水平。
【关键词】供暖锅炉PLC负荷控制优化策略【引言】目前,我国很多在运行的锅炉都存在自动化水平不高、效率低和环境污染严重的问题,因此实现锅炉的自动控制具有重要的意义。
PLC自动化系统采用模块化设计,程序也采用模块化设计,且每个模块都可以单独的优化,以便于整个系统的升级、控制管理和日后的维护,保证了系统的可开发性,和有良好的可扩充性,发挥系统的最大性价比。
【正文】热水锅炉的工作原理是通过煤的燃烧,将锅炉中的水加热,并将加热到一定程度的热水通过增加迫使其流出,为外界供暖。
控制系统需要根据工艺需求实时的调整燃烧系统。
按工艺要求,自控程序分锅炉负荷控制(燃烧自动控制)、循环泵自动控制和补水定压控制等几部分。
其中水系统(循环泵、补水泵)控制相对比较简单,负荷控制较为复杂,以下是作者对热水锅炉及机组总结出的负荷控制的控制方案。
1.锅炉负荷控制锅炉负荷控制的目的是:根据供暖需求的热量,通过一系列中间控制环节控制锅炉的供回水温度和流量,使住户处的室内温度达到并维持在合适的温度值,且锅炉运行在节能状态。
当供暖面积一定时,出水流量基本就不变了,所以因为室外温度的变化,所需的热量主要就通过改变供回水温差来实现。
理论上,锅炉负荷控制应该控制总网供回水温差,因为温差可以直接反映出供热质量,温差太大或太小都说明供热质量不很理想。
但实际上,负荷控制是根据总网供水温度控制的,因为总网回水温度测量存在滞后性,一般就直接采用供水温度控制,这也可以更直接反映出锅炉的燃烧情况,使燃烧过程维持在一个动态平衡上,以达到节能的效果。
所以,负荷控制就是总网供水温度控制。
- 1、下载文档前请自行甄别文档内容的完整性,平台不提供额外的编辑、内容补充、找答案等附加服务。
- 2、"仅部分预览"的文档,不可在线预览部分如存在完整性等问题,可反馈申请退款(可完整预览的文档不适用该条件!)。
- 3、如文档侵犯您的权益,请联系客服反馈,我们会尽快为您处理(人工客服工作时间:9:00-18:30)。
集中供热锅炉控制系统的PLC控制彭桂力.刘知贵(西南科技大学信息工程学院,四川绵阳621010)摘要:针对目前对集中供热锅炉控制中没有远距离控制的现状,基于西门子S7—200系列可编程逻辑控制器PLC(Pmgr锄mablehgicContmller)设计了一种集中供热锅炉自动控制系统,介绍其工作原理:控制现场传感器标准信号经过信号调理模块送到现场控制单元PLC。
控制单元通过以太网相连,将需要监控的信号送入上位机,实现人机交互和远程控制。
对系统的控制核心S7—200作了详细的介绍.并给出了软、硬件结构设计方案。
中图分类号:TP273文献标识码:B文章编号:1006—6047(2006)09—0075—030引言近年来.大型集中供热锅炉房的控制系统开始采用可编程逻辑控制器PLC(ProgrammableL0鲥cCon—tmller)控制方式。
在集中供热锅炉房,PLC主要用于输煤、驱动风机及进行比例积分微分PID(PmponionalIntegralDerivative)调节控制系统中[1|。
当前国内许多地方的锅炉控制系统主要是采用分布式控制系统DCS(DistributedControlSvstem)‘2_。
这是由于锅炉系统的仪表信号较多.采用此系统性价比相对较好,但随着PLC技术的不断发展.PLC在仪表控制方面的功能已经不断强化。
用于回路调节和组态画面的功能不断完善.而且PLC的抗干扰能力也很强.对电源的质量要求比较低。
基于PLC在工业控制系统中的良好应用.本文将西门子S7—200PLC用于集中供热系统锅炉控制系统。
整个系统的工作原理为:从控制现场传感器送来的4。
20mA或0。
5v的标准信号经过信号调理模块送到现场控制单元(PLC).经过智能运算后形成控制信号.控制信号再经过信号调理模块返送到现场执行单元(电磁阀)。
各个控制单元通过以太网相连.将需要监控的信号送人上位机,实现人机交互和远程控制。
1系统结构和控制方案系统结构如图1所示。
本系统主要是用西门子图1系统结构图Fig.1Systemstmcture收稿日期:2005—12—13;修回日期:2006—03—04向户PLCS7—200CPU224作为控制器进行控制.主要是对燃煤锅炉进行控制。
包括风机、给煤机的开关,根据液位变化对进出水口阀门的控制.根据锅炉内温度变化进行自动控制.利用PLC中所带有的PID调节器进行调节.以控制锅炉内的温度.再利用远程传输的功能.可以在用户处装上温度传感器.将其温度转成标准信号传到PLC主机上.观测到的温度根据需要进行调节,提高或降低锅炉的温度.直接控制传到用户的温度。
在锅炉内装有压力传感器.这是十分必要的,如果压力过高,可能会降低锅炉的寿命,甚至发生危险,所以一定要控制压力.当压力超过一定的数值,需报警。
并迅速进行处理.降低锅炉内的压力.以免发生危险[3-41。
根据系统的要求.选取西门子PLCS7—200CPU224作为控制核心.同时还扩展了2个EM231模拟量输入模块、1个EM223数字量输入模块和1个CP243—1以太网模块。
CPU224的I/0点数是14/10。
所以要扩展1个EM223的数字量输入/输出模块.它的I/O点数是16/16.作用是提供附加的输入、输出点。
这样完全可以满足系统的要求。
同时.选用了EM231模块.它是AD转换模块,具有4个模拟量输入,12位AD,其采样速度25¨s,温度传感器、压力传感器、流量传感器以及含氧检测传感器的输出信号经过调理和放大处理后.成为0。
5V的标准信号.EM231模块自动完成AD转换。
PLC通过检测温度、水位、压力、流量和气体中的含氧量给出控制信号控制燃烧机、真空泵、给媒机、电磁阀等输出设备[5-刚。
为实现人机对话功能.如系统状态以及变量图形显示、参数修改等。
还扩展了一块TD200触摸显示屏,操作控制简单、方便,可用于设置系统参数。
显示锅炉温度等。
还有一个以太网模块CP243—1.其作用是可以让S7—200直接连入以太网.通过以太网进行远距离交换数据.与其他的S7—200进行数据传输.通信基于TCP/IP,安装方便、简单。
机组控制系统如图2所示j1塞窒至降=S7—200<;习温度传愿器l匝酽CPU224e爿压力传感器I叵辩EM231模块e刊锅炉水位传感匾鲴仁EM223模块C爿气体含氧传感CP243—1模块e爿鎏量箜壁l仄丽酌图2控制系统框图Fig.2Blockdiagramofcontmlsystem为满足集中供热锅炉控制系统、自动控制的工艺要求.规定如下的控制方案。
控制参数:集中供热系统锅炉出水口温度、用户家中温度、炉内温度、锅炉水位、锅炉压力、出水口和进水口的流量、气体中含氧量。
控制内容:燃烧机开关、真空泵开关、电磁阀开关、给煤机开关、报警。
系统根据锅炉内水温高、低控制燃烧机大、小火。
水温控制值可以设定(例如,锅炉出水口温度设为70℃。
大、小火转换温度为10℃,则温度小于60℃时开大火.大于70℃时开小火)。
根据锅炉内空气的含氧量控制真空泵自启动.当含氧量过低时,真空泵启动,向锅炉内吹人空气,控制炉内的温度,当锅炉内温度低于一定值时,同样可以控制真空泵自启动.向锅炉内吹人空气以提高炉内的温度。
根据液位的高低实现锅炉内的自动调节.当液位降低时,进水口的电磁阀开大一些.向锅炉内加入水;锅炉内液位过高。
进水口的电磁阀开小一些。
以保持炉内的液位平衡。
同样.根据出水管内的流量大小也可来控制出水口电磁阀的开关。
当流量过大时,关小电磁阀。
自动调节流量。
根据用户家中的温度高低。
通过以太网模块CP243一l把传感器检测到的数据传人PLC中.根据它的温度同样可以控制燃烧机大、小火和真空泵开启。
故障报警:锅炉内温度高、水位低、水位高、锅炉内压力高、出水管内的流量高、出水管内的流量低、燃烧机故障等。
以上所控制的内容根据现场的实际情况.设定温度值、压力值、液位值、流量值以及炉内空气的含氧量的百分比[8.91。
2控制系统设计2.1CPU224的I/O地址分配集中供热锅炉控制系统的设计主要涉及了7个数字量输入,8个数字量输出,外加5个模拟量输入。
其中扩充了2个EM231的模拟量输入模块.主要是用于测量温度值的.另外扩充的CP243—1以太网通信模块。
可以把远距离的模拟量温度值传到主控中心。
它也可以完成PLC之间的互相通信.这样就可以及时地对用户温度进行检测.然后根据返回的信息对集中供热锅炉进行控制,进行加煤、加热和真空泵的启动【埘。
CPU224的I/O地址分配如表1所示。
表1输入/输出地址rI铀.1AddressesofI/Opoints输入输出序号名称地址序号名称地址1燃烧机故障IO.3l燃烧机Q0.02锅炉内压力值10.62真空泵QO.13水位低I1.O3报警Q0.34水位高I1.14进水口电磁阀Q1.05出水管内的流量大11.25出水口电磁阀Q1.16出水管内的流量小11.36大火Q1.27含氧量检测I1.47小火Q1.38出水管温度8给煤电机Q1.4;进水管温度EM231lO炉内温度ll刳皇的望戤嬲12用户温度2.2PLC的硬件连接S7—200系列PLC采用的是专用的轨道进行连接CPU模块相连组网或同其他扩展模块相连很方便①。
PLC系统用于自动控制具有诸多优点。
方便可靠.另外还加入了人机界面。
系统更加直观。
控制器上设有按键,可以设定系统运行参数,如:温度和压力值。
控制器上设有显示窗口.用于显示时间及系统各部位温度、压力,另外,还有报警指示灯指示系统的故障情况。
控制器上的非易失性存储器,用来存储一些数据可供查询②。
2.3控制系统软件锅炉是一个复杂的控制对象.其控制回路非线性严重。
锅炉的压力(或出水温度)、鼓风控制回路构成锅炉的燃烧控制系统.其控制方案是采用压力或出水温度为主调量.通过调整炉排转速使蒸汽压力或出水温度尽快达到给定值.同时配合风一煤配比控制鼓风量达到经济燃烧.最终达到所需要的温度值。
使输出水温是一个固定值。
热水锅炉的出水温度设定值跟随室外温度的变化自动修正。
使用户室内的温度保持恒定,且实现经济供热。
锅炉水位控制回路使锅炉水位保持恒定,根据锅炉出口流量控制以保持出水的流量恒定。
控制程序采用STEP7一Micr0/Win软件以梯形图方式编写.程序运行方式如图3所示。
图3系统主流程图Fig.3FlowchartofsystemmainpIDg】.am①西门子s7—200PLc用户指南,2004.②siemens.s7—200可编程控制器系统手册,2004由图可知,按下启动键后。
首先检测锅炉水位.如果水位低就停机.否则就正常运行。
接下来是点燃燃烧机和开启真空泵.给锅炉进行大火加热.当达到设定的温度值时.开始向用户输出热水.进水口开启,不断地向锅炉内加入冷水,保持液位平衡.同时检测锅炉内的压力和温度,利用PLC进行控制.使其保持在一个稳定值。
程序还具有报警功能,报警值有炉内温度高、锅炉内压力高、燃烧机故障、水位高、水位底、出水管内的流量高、出水管内的流量低。
其中,燃烧机故障由燃烧机本身自带的故障输出点给出:水位高低由水位传感器给出;锅炉内压力由压力开关给出;温度报警值由温度传感器给出.流量的大小也是由流量传感器给出。
除了低水位报警停止整机工作和炉温高报警停燃烧机外.其他报警不影响机组的运行(见STEP7Micm编程手册)。
3结论集中供热系统采用西门子的PLC控制.不仅简化了系统。
提高了设备的可靠性和稳定性.同时也大幅地提高了燃烧能的热效率。
通过操作面板修改系统参数可以满足不同的工况要求.机组的各种信息,如工作状态、故障情况等可以声光报警及文字形式表示出来.主要控制参数(温度值)的实时变化情况以趋势图的形式记录显示.方便了设备的操作和维护。
该系统通用性好、扩展性强。
直观易操作。
由于本系统只是在计算机上进行了仿真运算.并没有在实际的现场进行应用.可能还存在着很多的不足之处需要改进.例如,以太网的传输速度和准确性问题.锅炉控制时的稳定性都是应该考虑在内的。
通过这次设计.笔者发现可编程控制器领域有很大的发展空间.需要研究人员不断的对其完善,使其能在工业上发挥更大的作用。
参考文献:[1]张世臣.西门子S7—400H在热电厂自动控制系统中的应用[J].自动化仪表,2004,25(6):41—42.ZHANGShi—chen.ApplicationofSiemens’S7—400Hforauto—maticcontrolsystemsincogeneratio“powerplant[J].ProcessAutomationInstmmentation,2004,25(6):41—42.[2]杜建颖.PI£技术及其在锅炉控制系统中的应用[J].机械工程师.2005(4):26—27.DUJian—ying.PLC£echnologyandfheappljcationofboilercon—tr01system[J].MechanicalEn百neer,2005(4):26—27.[3]霍凯.Pc机与S7—200PLc的通讯研究[J].中国仪器仪表,2005(4):74—76.HU0Kai.StudyofthecommunicationbetweenPC粕dS7~200P【£[J].Cl】_inaInBtmmentati叽,2005(4):74—76.[4]赵永生,汪思源,朱吉苓,等.基于软PLC的分布式锅炉微机控制系统[J].微计算机信息,2003,19(7):9一10.ZHA0Yong—sheng,WANGSi—yuaIl,ZHUJi—ling,eta1.Designondistributedboilercontrd8ystembasedonsoffPLC[J].Control&Automation,2003,19(7):9-10.f5]方俊山.可编程序控制器在电加热锅炉控制中的应用[J].工业控制计算机。