不锈钢镜面抛光工艺及方法和要求
不锈钢镜面抛光工艺设计及方法和要求
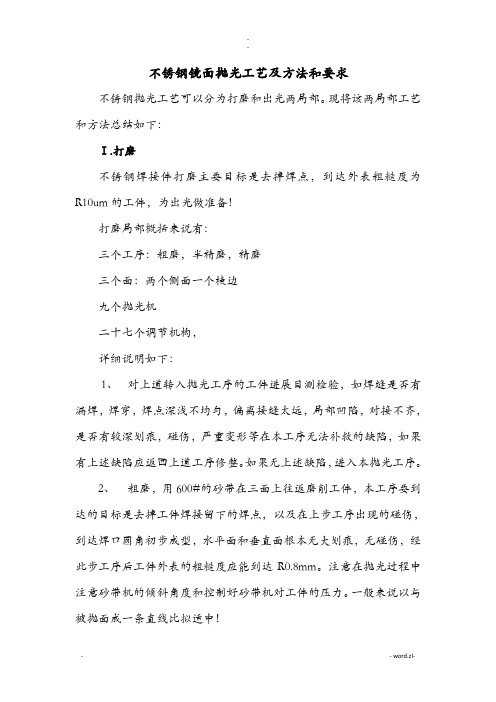
不锈钢镜面抛光工艺及方法和要求不锈钢抛光工艺可以分为打磨和出光两局部。
现将该两局部工艺和方法总结如下:Ⅰ.打磨不锈钢焊接件打磨主要目标是去掉焊点,到达外表粗糙度为R10um的工件,为出光做准备!打磨局部概括来说有:三个工序:粗磨,半精磨,精磨三个面:两个侧面一个棱边九个抛光机二十七个调节机构,详细说明如下:1、对上道转入抛光工序的工件进展目测检验,如焊缝是否有漏焊,焊穿,焊点深浅不均匀,偏离接缝太远,局部凹陷,对接不齐,是否有较深划痕,碰伤,严重变形等在本工序无法补救的缺陷,如果有上述缺陷应返回上道工序修整。
如果无上述缺陷,进入本抛光工序。
2、粗磨,用600#的砂带在三面上往返磨削工件,本工序要到达的目标是去掉工件焊接留下的焊点,以及在上步工序出现的碰伤,到达焊口圆角初步成型,水平面和垂直面根本无大划痕,无碰伤,经此步工序后工件外表的粗糙度应能到达R0.8mm。
注意在抛光过程中注意砂带机的倾斜角度和控制好砂带机对工件的压力。
一般来说以与被抛面成一条直线比拟适中!3、半精磨,用800#的砂带按照前面往返磨削工件的方法中磨工件的三面,主要是对前面工序出现的接缝进展修正以及对粗磨后产生的印痕进展进一步的细磨,对前面工序留下的印痕要反复磨削,到达工件外表无划痕,根本变亮。
本工序外表粗糙度应能到达R0.4mm。
〔注意本工序不要产生新的划痕及碰伤,因为在后面的工序无法修补此类缺陷。
〕4、精磨,用1000#的砂带主要是对前步工序出现的细小纹线的修正磨削,磨削方法与上同。
本工序要到达的目标是磨削局部与工件未磨削局部的接缝根本消失,工件外表进一步光亮,通过本工序磨削后的工件要根本接近镜面效果,工件外表粗糙度应能到达R0.1mm5、关于更换砂带的说明:一般来说,600#的砂带可以抛磨1500mm长的工件6-8根,800#的砂带可以抛磨工件4-6根,1000#的砂带可以抛磨工件1-2根,具体情况还需以工件焊接焊点情况,抛光使用的压力,以及打磨的方式方法有很大的关系。
不锈钢镜面抛光标准
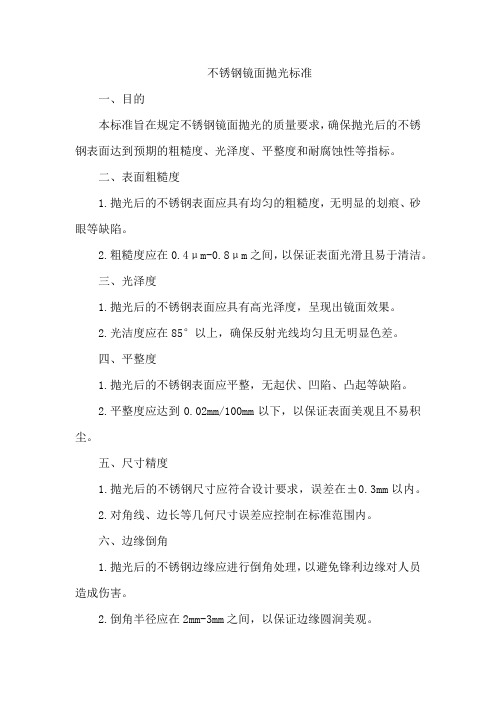
不锈钢镜面抛光标准一、目的本标准旨在规定不锈钢镜面抛光的质量要求,确保抛光后的不锈钢表面达到预期的粗糙度、光泽度、平整度和耐腐蚀性等指标。
二、表面粗糙度1.抛光后的不锈钢表面应具有均匀的粗糙度,无明显的划痕、砂眼等缺陷。
2.粗糙度应在0.4μm-0.8μm之间,以保证表面光滑且易于清洁。
三、光泽度1.抛光后的不锈钢表面应具有高光泽度,呈现出镜面效果。
2.光洁度应在85°以上,确保反射光线均匀且无明显色差。
四、平整度1.抛光后的不锈钢表面应平整,无起伏、凹陷、凸起等缺陷。
2.平整度应达到0.02mm/100mm以下,以保证表面美观且不易积尘。
五、尺寸精度1.抛光后的不锈钢尺寸应符合设计要求,误差在±0.3mm以内。
2.对角线、边长等几何尺寸误差应控制在标准范围内。
六、边缘倒角1.抛光后的不锈钢边缘应进行倒角处理,以避免锋利边缘对人员造成伤害。
2.倒角半径应在2mm-3mm之间,以保证边缘圆润美观。
七、耐腐蚀性1.抛光后的不锈钢表面应具有良好的耐腐蚀性,能够抵抗常见的酸、碱、盐等化学物质的侵蚀。
2.在正常环境下,耐腐蚀时间应达到50年以上。
八、工艺流程1.预处理:对不锈钢表面进行除油、除锈等预处理,以确保表面清洁且无杂质。
2.粗磨:使用粗磨轮对表面进行初步磨削,去除多余的杂质和氧化层。
3.精磨:使用精磨轮对表面进行精细磨削,达到预期的粗糙度和光泽度。
4.抛光:使用抛光轮对表面进行抛光处理,去除细微划痕和不平整区域,提高镜面效果。
5.清洗:使用清洗剂对表面进行清洗,去除残留的磨削杂质和油脂。
6.检验:对抛光后的不锈钢表面进行质量检验,确保各项指标符合要求。
7.包装:对合格的产品进行包装,防止运输过程中受损。
九、设备选择1.磨削设备:选择性能稳定、精度高的磨削设备,如数控磨床或专业磨床。
2.抛光设备:选择高效、稳定的抛光设备,如自动抛光机或手动抛光机。
3.清洗设备:选择能够彻底清洗表面的清洗设备,如超声波清洗机或高压水枪。
不锈钢镜面抛光工艺及方法总结
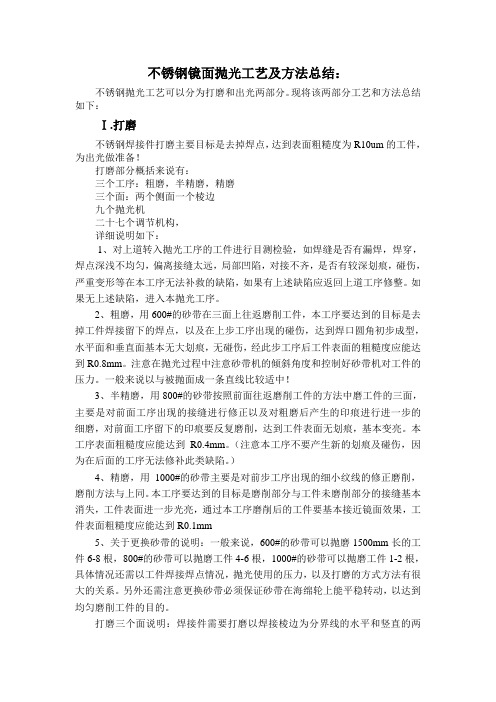
不锈钢镜面抛光工艺及方法总结:不锈钢抛光工艺可以分为打磨和出光两部分。
现将该两部分工艺和方法总结如下:Ⅰ.打磨不锈钢焊接件打磨主要目标是去掉焊点,达到表面粗糙度为R10um的工件,为出光做准备!打磨部分概括来说有:三个工序:粗磨,半精磨,精磨三个面:两个侧面一个棱边九个抛光机二十七个调节机构,详细说明如下:1、对上道转入抛光工序的工件进行目测检验,如焊缝是否有漏焊,焊穿,焊点深浅不均匀,偏离接缝太远,局部凹陷,对接不齐,是否有较深划痕,碰伤,严重变形等在本工序无法补救的缺陷,如果有上述缺陷应返回上道工序修整。
如果无上述缺陷,进入本抛光工序。
2、粗磨,用600#的砂带在三面上往返磨削工件,本工序要达到的目标是去掉工件焊接留下的焊点,以及在上步工序出现的碰伤,达到焊口圆角初步成型,水平面和垂直面基本无大划痕,无碰伤,经此步工序后工件表面的粗糙度应能达到R0.8mm。
注意在抛光过程中注意砂带机的倾斜角度和控制好砂带机对工件的压力。
一般来说以与被抛面成一条直线比较适中!3、半精磨,用800#的砂带按照前面往返磨削工件的方法中磨工件的三面,主要是对前面工序出现的接缝进行修正以及对粗磨后产生的印痕进行进一步的细磨,对前面工序留下的印痕要反复磨削,达到工件表面无划痕,基本变亮。
本工序表面粗糙度应能达到R0.4mm。
(注意本工序不要产生新的划痕及碰伤,因为在后面的工序无法修补此类缺陷。
)4、精磨,用1000#的砂带主要是对前步工序出现的细小纹线的修正磨削,磨削方法与上同。
本工序要达到的目标是磨削部分与工件未磨削部分的接缝基本消失,工件表面进一步光亮,通过本工序磨削后的工件要基本接近镜面效果,工件表面粗糙度应能达到R0.1mm5、关于更换砂带的说明:一般来说,600#的砂带可以抛磨1500mm长的工件6-8根,800#的砂带可以抛磨工件4-6根,1000#的砂带可以抛磨工件1-2根,具体情况还需以工件焊接焊点情况,抛光使用的压力,以及打磨的方式方法有很大的关系。
不锈钢镜面抛光工艺及方法总结
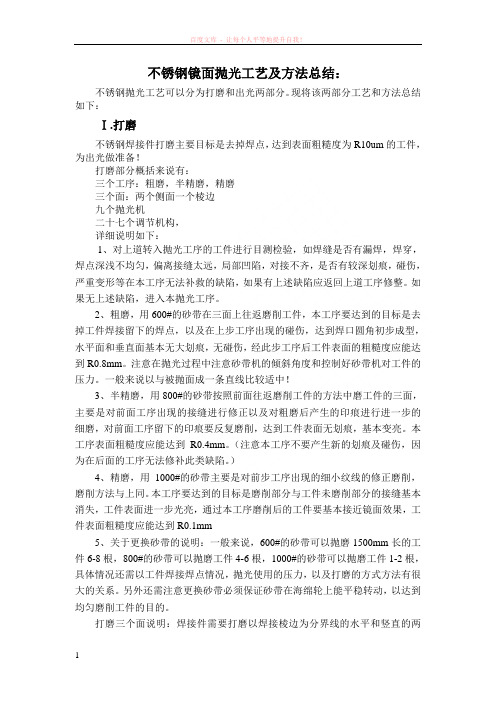
不锈钢镜面抛光工艺及方法总结:不锈钢抛光工艺可以分为打磨和出光两部分。
现将该两部分工艺和方法总结如下:Ⅰ.打磨不锈钢焊接件打磨主要目标是去掉焊点,达到表面粗糙度为R10um的工件,为出光做准备!打磨部分概括来说有:三个工序:粗磨,半精磨,精磨三个面:两个侧面一个棱边九个抛光机二十七个调节机构,详细说明如下:1、对上道转入抛光工序的工件进行目测检验,如焊缝是否有漏焊,焊穿,焊点深浅不均匀,偏离接缝太远,局部凹陷,对接不齐,是否有较深划痕,碰伤,严重变形等在本工序无法补救的缺陷,如果有上述缺陷应返回上道工序修整。
如果无上述缺陷,进入本抛光工序。
2、粗磨,用600#的砂带在三面上往返磨削工件,本工序要达到的目标是去掉工件焊接留下的焊点,以及在上步工序出现的碰伤,达到焊口圆角初步成型,水平面和垂直面基本无大划痕,无碰伤,经此步工序后工件表面的粗糙度应能达到R0.8mm。
注意在抛光过程中注意砂带机的倾斜角度和控制好砂带机对工件的压力。
一般来说以与被抛面成一条直线比较适中!3、半精磨,用800#的砂带按照前面往返磨削工件的方法中磨工件的三面,主要是对前面工序出现的接缝进行修正以及对粗磨后产生的印痕进行进一步的细磨,对前面工序留下的印痕要反复磨削,达到工件表面无划痕,基本变亮。
本工序表面粗糙度应能达到R0.4mm。
(注意本工序不要产生新的划痕及碰伤,因为在后面的工序无法修补此类缺陷。
)4、精磨,用1000#的砂带主要是对前步工序出现的细小纹线的修正磨削,磨削方法与上同。
本工序要达到的目标是磨削部分与工件未磨削部分的接缝基本消失,工件表面进一步光亮,通过本工序磨削后的工件要基本接近镜面效果,工件表面粗糙度应能达到R0.1mm5、关于更换砂带的说明:一般来说,600#的砂带可以抛磨1500mm长的工件6-8根,800#的砂带可以抛磨工件4-6根,1000#的砂带可以抛磨工件1-2根,具体情况还需以工件焊接焊点情况,抛光使用的压力,以及打磨的方式方法有很大的关系。
304不锈钢镜面抛光工艺

304不锈钢镜面抛光工艺304不锈钢是一种常见的不锈钢材料,具有良好的耐腐蚀性和机械性能。
而镜面抛光工艺则是一种常用的表面处理技术,可以使304不锈钢表面光滑如镜,增加其美观性和耐腐蚀性。
本文将介绍304不锈钢镜面抛光工艺的原理、步骤和应用。
一、原理304不锈钢镜面抛光工艺的原理是通过机械研磨和化学抛光相结合,去除不锈钢表面的氧化皮和金属颗粒,使其表面变得光滑。
具体原理如下:1. 机械研磨:通过使用研磨材料(如砂轮、砂带等)对不锈钢表面进行研磨,去除表面的氧化皮和金属颗粒,使其表面平整。
2. 化学抛光:在机械研磨的基础上,使用化学溶液进行抛光。
常用的化学抛光溶液包括硝酸、硫酸和氢氟酸等,可以溶解表面的氧化物和金属颗粒,使不锈钢表面更加光滑。
二、步骤304不锈钢镜面抛光工艺的步骤包括以下几个方面:1. 清洗:首先需要将不锈钢材料进行清洗,去除表面的灰尘和污垢,保证后续处理的效果。
2. 机械研磨:使用砂轮、砂带等研磨材料对不锈钢表面进行研磨。
研磨过程中应注意控制研磨的力度和速度,避免对不锈钢材料造成损伤。
3. 清洗:研磨完毕后,需要再次对不锈钢表面进行清洗,去除研磨过程中产生的金属颗粒和碎屑。
4. 化学抛光:将清洗干净的不锈钢材料浸入化学抛光溶液中,进行抛光处理。
抛光时间和温度需根据具体情况进行控制,以保证抛光效果。
5. 清洗:抛光完毕后,需要再次对不锈钢表面进行清洗,去除抛光溶液残留物,以免对不锈钢材料产生腐蚀。
6. 干燥:最后将抛光干净的不锈钢材料进行干燥,确保表面无水迹和水渍,以保持其光滑如镜的效果。
三、应用304不锈钢镜面抛光工艺广泛应用于家居、建筑、厨具、电子设备等领域。
具体应用如下:1. 家居:304不锈钢镜面抛光工艺可用于制作家具、楼梯扶手、门把手等装饰品,增添高档感和美观性。
2. 建筑:304不锈钢镜面抛光工艺可用于制作建筑立面、栏杆、门窗框等,提升建筑物的整体形象。
3. 厨具:304不锈钢具有良好的耐腐蚀性和耐高温性,镜面抛光工艺可以增加其光滑度和易清洁性,使厨具更加耐用和美观。
不锈钢镜面抛光工艺及方法总结

不锈钢镜面抛光工艺及方法总结:不锈钢抛光工艺可以分为打磨和出光两部分。
现将该两部分工艺和方法总结如下:Ⅰ.打磨不锈钢焊接件打磨主要目标是去掉焊点,达到表面粗糙度为R10um的工件,为出光做准备!打磨部分概括来说有:三个工序:粗磨,半精磨,精磨三个面:两个侧面一个棱边九个抛光机二十七个调节机构,详细说明如下:1、对上道转入抛光工序的工件进行目测检验,如焊缝是否有漏焊,焊穿,焊点深浅不均匀,偏离接缝太远,局部凹陷,对接不齐,是否有较深划痕,碰伤,严重变形等在本工序无法补救的缺陷,如果有上述缺陷应返回上道工序修整。
如果无上述缺陷,进入本抛光工序。
2、粗磨,用600#的砂带在三面上往返磨削工件,本工序要达到的目标是去掉工件焊接留下的焊点,以及在上步工序出现的碰伤,达到焊口圆角初步成型,水平面和垂直面基本无大划痕,无碰伤,经此步工序后工件表面的粗糙度应能达到R0.8mm。
注意在抛光过程中注意砂带机的倾斜角度和控制好砂带机对工件的压力。
一般来说以与被抛面成一条直线比较适中!3、半精磨,用800#的砂带按照前面往返磨削工件的方法中磨工件的三面,主要是对前面工序出现的接缝进行修正以及对粗磨后产生的印痕进行进一步的细磨,对前面工序留下的印痕要反复磨削,达到工件表面无划痕,基本变亮。
本工序表面粗糙度应能达到R0.4mm。
(注意本工序不要产生新的划痕及碰伤,因为在后面的工序无法修补此类缺陷。
)4、精磨,用1000#的砂带主要是对前步工序出现的细小纹线的修正磨削,磨削方法与上同。
本工序要达到的目标是磨削部分与工件未磨削部分的接缝基本消失,工件表面进一步光亮,通过本工序磨削后的工件要基本接近镜面效果,工件表面粗糙度应能达到R0.1mm5、关于更换砂带的说明:一般来说,600#的砂带可以抛磨1500mm长的工件6-8根,800#的砂带可以抛磨工件4-6根,1000#的砂带可以抛磨工件1-2根,具体情况还需以工件焊接焊点情况,抛光使用的压力,以及打磨的方式方法有很大的关系。
不锈钢镜面抛光工艺及制作工艺总结
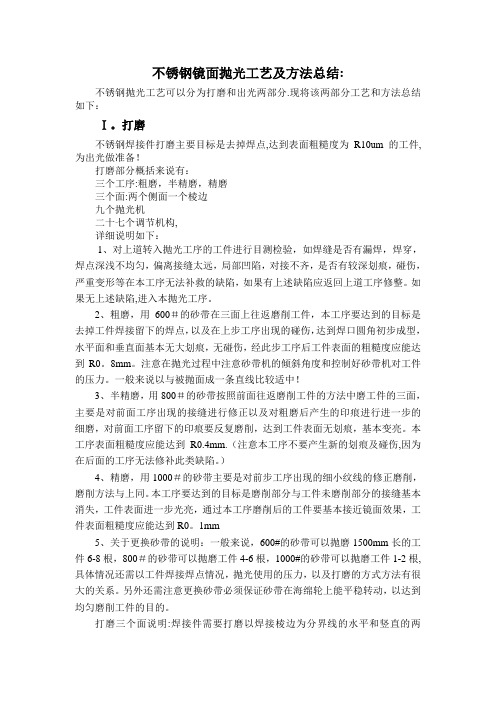
不锈钢镜面抛光工艺及方法总结:不锈钢抛光工艺可以分为打磨和出光两部分.现将该两部分工艺和方法总结如下:Ⅰ。
打磨不锈钢焊接件打磨主要目标是去掉焊点,达到表面粗糙度为R10um的工件,为出光做准备!打磨部分概括来说有:三个工序:粗磨,半精磨,精磨三个面:两个侧面一个棱边九个抛光机二十七个调节机构,详细说明如下:1、对上道转入抛光工序的工件进行目测检验,如焊缝是否有漏焊,焊穿,焊点深浅不均匀,偏离接缝太远,局部凹陷,对接不齐,是否有较深划痕,碰伤,严重变形等在本工序无法补救的缺陷,如果有上述缺陷应返回上道工序修整。
如果无上述缺陷,进入本抛光工序。
2、粗磨,用600#的砂带在三面上往返磨削工件,本工序要达到的目标是去掉工件焊接留下的焊点,以及在上步工序出现的碰伤,达到焊口圆角初步成型,水平面和垂直面基本无大划痕,无碰伤,经此步工序后工件表面的粗糙度应能达到R0。
8mm。
注意在抛光过程中注意砂带机的倾斜角度和控制好砂带机对工件的压力。
一般来说以与被抛面成一条直线比较适中!3、半精磨,用800#的砂带按照前面往返磨削工件的方法中磨工件的三面,主要是对前面工序出现的接缝进行修正以及对粗磨后产生的印痕进行进一步的细磨,对前面工序留下的印痕要反复磨削,达到工件表面无划痕,基本变亮。
本工序表面粗糙度应能达到R0.4mm.(注意本工序不要产生新的划痕及碰伤,因为在后面的工序无法修补此类缺陷。
)4、精磨,用1000#的砂带主要是对前步工序出现的细小纹线的修正磨削,磨削方法与上同。
本工序要达到的目标是磨削部分与工件未磨削部分的接缝基本消失,工件表面进一步光亮,通过本工序磨削后的工件要基本接近镜面效果,工件表面粗糙度应能达到R0。
1mm5、关于更换砂带的说明:一般来说,600#的砂带可以抛磨1500mm长的工件6-8根,800#的砂带可以抛磨工件4-6根,1000#的砂带可以抛磨工件1-2根,具体情况还需以工件焊接焊点情况,抛光使用的压力,以及打磨的方式方法有很大的关系。
不锈钢镜面抛光工艺及制作工艺总结
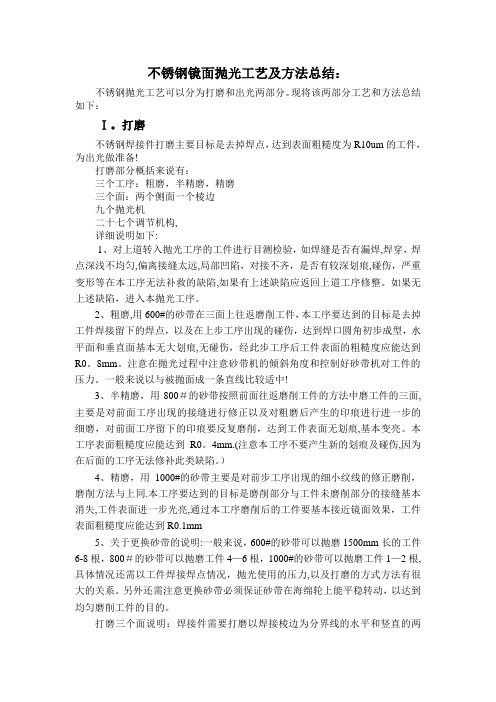
不锈钢镜面抛光工艺及方法总结:不锈钢抛光工艺可以分为打磨和出光两部分。
现将该两部分工艺和方法总结如下:Ⅰ。
打磨不锈钢焊接件打磨主要目标是去掉焊点,达到表面粗糙度为R10um的工件,为出光做准备!打磨部分概括来说有:三个工序:粗磨,半精磨,精磨三个面:两个侧面一个棱边九个抛光机二十七个调节机构,详细说明如下:1、对上道转入抛光工序的工件进行目测检验,如焊缝是否有漏焊,焊穿,焊点深浅不均匀,偏离接缝太远,局部凹陷,对接不齐,是否有较深划痕,碰伤,严重变形等在本工序无法补救的缺陷,如果有上述缺陷应返回上道工序修整。
如果无上述缺陷,进入本抛光工序。
2、粗磨,用600#的砂带在三面上往返磨削工件,本工序要达到的目标是去掉工件焊接留下的焊点,以及在上步工序出现的碰伤,达到焊口圆角初步成型,水平面和垂直面基本无大划痕,无碰伤,经此步工序后工件表面的粗糙度应能达到R0。
8mm。
注意在抛光过程中注意砂带机的倾斜角度和控制好砂带机对工件的压力。
一般来说以与被抛面成一条直线比较适中!3、半精磨,用800#的砂带按照前面往返磨削工件的方法中磨工件的三面,主要是对前面工序出现的接缝进行修正以及对粗磨后产生的印痕进行进一步的细磨,对前面工序留下的印痕要反复磨削,达到工件表面无划痕,基本变亮。
本工序表面粗糙度应能达到R0。
4mm.(注意本工序不要产生新的划痕及碰伤,因为在后面的工序无法修补此类缺陷。
)4、精磨,用1000#的砂带主要是对前步工序出现的细小纹线的修正磨削,磨削方法与上同.本工序要达到的目标是磨削部分与工件未磨削部分的接缝基本消失,工件表面进一步光亮,通过本工序磨削后的工件要基本接近镜面效果,工件表面粗糙度应能达到R0.1mm5、关于更换砂带的说明:一般来说,600#的砂带可以抛磨1500mm长的工件6-8根,800#的砂带可以抛磨工件4—6根,1000#的砂带可以抛磨工件1—2根,具体情况还需以工件焊接焊点情况,抛光使用的压力,以及打磨的方式方法有很大的关系。
不锈钢镜面抛光工艺及方法和要求
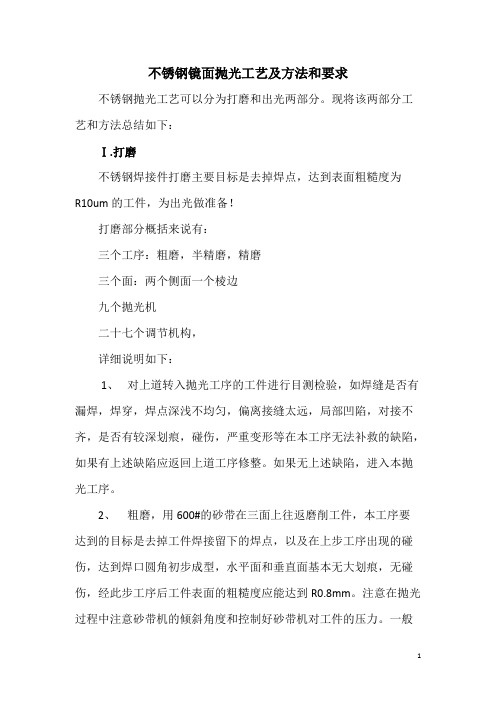
不锈钢镜面抛光工艺及方法和要求不锈钢抛光工艺可以分为打磨和出光两部分。
现将该两部分工艺和方法总结如下:Ⅰ.打磨不锈钢焊接件打磨主要目标是去掉焊点,达到表面粗糙度为R10um的工件,为出光做准备!打磨部分概括来说有:三个工序:粗磨,半精磨,精磨三个面:两个侧面一个棱边九个抛光机二十七个调节机构,详细说明如下:1、对上道转入抛光工序的工件进行目测检验,如焊缝是否有漏焊,焊穿,焊点深浅不均匀,偏离接缝太远,局部凹陷,对接不齐,是否有较深划痕,碰伤,严重变形等在本工序无法补救的缺陷,如果有上述缺陷应返回上道工序修整。
如果无上述缺陷,进入本抛光工序。
2、粗磨,用600#的砂带在三面上往返磨削工件,本工序要达到的目标是去掉工件焊接留下的焊点,以及在上步工序出现的碰伤,达到焊口圆角初步成型,水平面和垂直面基本无大划痕,无碰伤,经此步工序后工件表面的粗糙度应能达到R0.8mm。
注意在抛光过程中注意砂带机的倾斜角度和控制好砂带机对工件的压力。
一般来说以与被抛面成一条直线比较适中!3、半精磨,用800#的砂带按照前面往返磨削工件的方法中磨工件的三面,主要是对前面工序出现的接缝进行修正以及对粗磨后产生的印痕进行进一步的细磨,对前面工序留下的印痕要反复磨削,达到工件表面无划痕,基本变亮。
本工序表面粗糙度应能达到R0.4mm。
(注意本工序不要产生新的划痕及碰伤,因为在后面的工序无法修补此类缺陷。
)4、精磨,用1000#的砂带主要是对前步工序出现的细小纹线的修正磨削,磨削方法与上同。
本工序要达到的目标是磨削部分与工件未磨削部分的接缝基本消失,工件表面进一步光亮,通过本工序磨削后的工件要基本接近镜面效果,工件表面粗糙度应能达到R0.1mm5、关于更换砂带的说明:一般来说,600#的砂带可以抛磨1500mm长的工件6-8根,800#的砂带可以抛磨工件4-6根,1000#的砂带可以抛磨工件1-2根,具体情况还需以工件焊接焊点情况,抛光使用的压力,以及打磨的方式方法有很大的关系。
不锈钢镜面抛光工艺及制作工艺总结

不锈钢镜面抛光工艺及方法总结:不锈钢抛光工艺可以分为打磨和出光两部分。
现将该两部分工艺和方法总结如下:Ⅰ.打磨不锈钢焊接件打磨主要目标是去掉焊点,达到表面粗糙度为R10um的工件,为出光做准备!打磨部分概括来说有:三个工序:粗磨,半精磨,精磨三个面:两个侧面一个棱边九个抛光机二十七个调节机构,详细说明如下:1、对上道转入抛光工序的工件进行目测检验,如焊缝是否有漏焊,焊穿,焊点深浅不均匀,偏离接缝太远,局部凹陷,对接不齐,是否有较深划痕,碰伤,严重变形等在本工序无法补救的缺陷,如果有上述缺陷应返回上道工序修整。
如果无上述缺陷,进入本抛光工序。
2、粗磨,用600#的砂带在三面上往返磨削工件,本工序要达到的目标是去掉工件焊接留下的焊点,以及在上步工序出现的碰伤,达到焊口圆角初步成型,水平面和垂直面基本无大划痕,无碰伤,经此步工序后工件表面的粗糙度应能达到R0.8mm。
注意在抛光过程中注意砂带机的倾斜角度和控制好砂带机对工件的压力。
一般来说以与被抛面成一条直线比较适中!3、半精磨,用800#的砂带按照前面往返磨削工件的方法中磨工件的三面,主要是对前面工序出现的接缝进行修正以及对粗磨后产生的印痕进行进一步的细磨,对前面工序留下的印痕要反复磨削,达到工件表面无划痕,基本变亮。
本工序表面粗糙度应能达到R0.4mm。
(注意本工序不要产生新的划痕及碰伤,因为在后面的工序无法修补此类缺陷。
)4、精磨,用1000#的砂带主要是对前步工序出现的细小纹线的修正磨削,磨削方法与上同。
本工序要达到的目标是磨削部分与工件未磨削部分的接缝基本消失,工件表面进一步光亮,通过本工序磨削后的工件要基本接近镜面效果,工件表面粗糙度应能达到R0.1mm5、关于更换砂带的说明:一般来说,600#的砂带可以抛磨1500mm长的工件6-8根,800#的砂带可以抛磨工件4-6根,1000#的砂带可以抛磨工件1-2根,具体情况还需以工件焊接焊点情况,抛光使用的压力,以及打磨的方式方法有很大的关系。
不锈钢镜面抛光工艺及制作工艺总结

不锈钢镜面抛光工艺及方法总结:不锈钢抛光工艺可以分为打磨和出光两部分。
现将该两部分工艺和方法总结如下:Ⅰ。
打磨不锈钢焊接件打磨主要目标是去掉焊点,达到表面粗糙度为R10um的工件,为出光做准备!打磨部分概括来说有:三个工序:粗磨,半精磨,精磨三个面:两个侧面一个棱边九个抛光机二十七个调节机构,详细说明如下:1、对上道转入抛光工序的工件进行目测检验,如焊缝是否有漏焊,焊穿,焊点深浅不均匀,偏离接缝太远,局部凹陷,对接不齐,是否有较深划痕,碰伤,严重变形等在本工序无法补救的缺陷,如果有上述缺陷应返回上道工序修整.如果无上述缺陷,进入本抛光工序。
2、粗磨,用600#的砂带在三面上往返磨削工件,本工序要达到的目标是去掉工件焊接留下的焊点,以及在上步工序出现的碰伤,达到焊口圆角初步成型,水平面和垂直面基本无大划痕,无碰伤,经此步工序后工件表面的粗糙度应能达到R0.8mm。
注意在抛光过程中注意砂带机的倾斜角度和控制好砂带机对工件的压力.一般来说以与被抛面成一条直线比较适中!3、半精磨,用800#的砂带按照前面往返磨削工件的方法中磨工件的三面,主要是对前面工序出现的接缝进行修正以及对粗磨后产生的印痕进行进一步的细磨,对前面工序留下的印痕要反复磨削,达到工件表面无划痕,基本变亮。
本工序表面粗糙度应能达到R0。
4mm。
(注意本工序不要产生新的划痕及碰伤,因为在后面的工序无法修补此类缺陷.)4、精磨,用1000#的砂带主要是对前步工序出现的细小纹线的修正磨削,磨削方法与上同。
本工序要达到的目标是磨削部分与工件未磨削部分的接缝基本消失,工件表面进一步光亮,通过本工序磨削后的工件要基本接近镜面效果,工件表面粗糙度应能达到R0.1mm5、关于更换砂带的说明:一般来说,600#的砂带可以抛磨1500mm长的工件6-8根,800#的砂带可以抛磨工件4—6根,1000#的砂带可以抛磨工件1—2根,具体情况还需以工件焊接焊点情况,抛光使用的压力,以及打磨的方式方法有很大的关系。
不锈钢镜面抛光工艺标准及其方法和要求

不锈钢镜面抛光工艺及方法和要求不锈钢抛光工艺可以分为打磨和出光两部分。
现将该两部分工艺和方法总结如下:Ⅰ.打磨不锈钢焊接件打磨主要目标是去掉焊点,达到表面粗糙度为R10um的工件,为出光做准备!打磨部分概括来说有:三个工序:粗磨,半精磨,精磨三个面:两个侧面一个棱边九个抛光机二十七个调节机构,详细说明如下:1、对上道转入抛光工序的工件进行目测检验,如焊缝是否有漏焊,焊穿,焊点深浅不均匀,偏离接缝太远,局部凹陷,对接不齐,是否有较深划痕,碰伤,严重变形等在本工序无法补救的缺陷,如果有上述缺陷应返回上道工序修整。
如果无上述缺陷,进入本抛光工序。
2、粗磨,用600#的砂带在三面上往返磨削工件,本工序要达到的目标是去掉工件焊接留下的焊点,以及在上步工序出现的碰伤,达到焊口圆角初步成型,水平面和垂直面基本无大划痕,无碰伤,经此步工序后工件表面的粗糙度应能达到R0.8mm。
注意在抛光过程中注意砂带机的倾斜角度和控制好砂带机对工件的压力。
一般来说以与被抛面成一条直线比较适中!3、半精磨,用800#的砂带按照前面往返磨削工件的方法中磨工件的三面,主要是对前面工序出现的接缝进行修正以及对粗磨后产生的印痕进行进一步的细磨,对前面工序留下的印痕要反复磨削,达到工件表面无划痕,基本变亮。
本工序表面粗糙度应能达到R0.4mm。
(注意本工序不要产生新的划痕及碰伤,因为在后面的工序无法修补此类缺陷。
)4、精磨,用1000#的砂带主要是对前步工序出现的细小纹线的修正磨削,磨削方法与上同。
本工序要达到的目标是磨削部分与工件未磨削部分的接缝基本消失,工件表面进一步光亮,通过本工序磨削后的工件要基本接近镜面效果,工件表面粗糙度应能达到R0.1mm5、关于更换砂带的说明:一般来说,600#的砂带可以抛磨1500mm长的工件6-8根,800#的砂带可以抛磨工件4-6根,1000#的砂带可以抛磨工件1-2根,具体情况还需以工件焊接焊点情况,抛光使用的压力,以及打磨的方式方法有很大的关系。
不锈钢镜面抛光工艺及方法总结

不锈钢镜面抛光工艺及方法总结不锈钢抛光工艺可以分为打磨和出光两部分。
现将该两部分工艺和方法总结如下:Ⅰ.打磨不锈钢焊接件打磨主要目标是去掉焊点,达到表面粗糙度为R10um的工件,为出光做准备!打磨部分概括来说有:三个工序:粗磨,半精磨,精磨三个面:两个侧面一个棱边九个抛光机二十七个调节机构,详细说明如下:1、对上道转入抛光工序的工件进行目测检验,如焊缝是否有漏焊,焊穿,焊点深浅不均匀,偏离接缝太远,局部凹陷,对接不齐,是否有较深划痕,碰伤,严重变形等在本工序无法补救的缺陷,如果有上述缺陷应返回上道工序修整。
如果无上述缺陷,进入本抛光工序。
2、粗磨,用600#的砂带在三面上往返磨削工件,本工序要达到的目标是去掉工件焊接留下的焊点,以及在上步工序出现的碰伤,达到焊口圆角初步成型,水平面和垂直面基本无大划痕,无碰伤,经此步工序后工件表面的粗糙度应能达到R0.8mm。
注意在抛光过程中注意砂带机的倾斜角度和控制好砂带机对工件的压力。
一般来说以与被抛面成一条直线比较适中!3、半精磨,用800#的砂带按照前面往返磨削工件的方法中磨工件的三面,主要是对前面工序出现的接缝进行修正以及对粗磨后产生的印痕进行进一步的细磨,对前面工序留下的印痕要反复磨削,达到工件表面无划痕,基本变亮。
本工序表面粗糙度应能达到R0.4mm。
(注意本工序不要产生新的划痕及碰伤,因为在后面的工序无法修补此类缺陷。
)4、精磨,用1000#的砂带主要是对前步工序出现的细小纹线的修正磨削,磨削方法与上同。
本工序要达到的目标是磨削部分与工件未磨削部分的接缝基本消失,工件表面进一步光亮,通过本工序磨削后的工件要基本接近镜面效果,工件表面粗糙度应能达到R0.1mm5、关于更换砂带的说明:一般来说,600#的砂带可以抛磨1500mm长的工件6-8根,800#的砂带可以抛磨工件4-6根,1000#的砂带可以抛磨工件1-2根,具体情况还需以工件焊接焊点情况,抛光使用的压力,以及打磨的方式方法有很大的关系。
不锈钢镜面抛光工艺及方法和要求
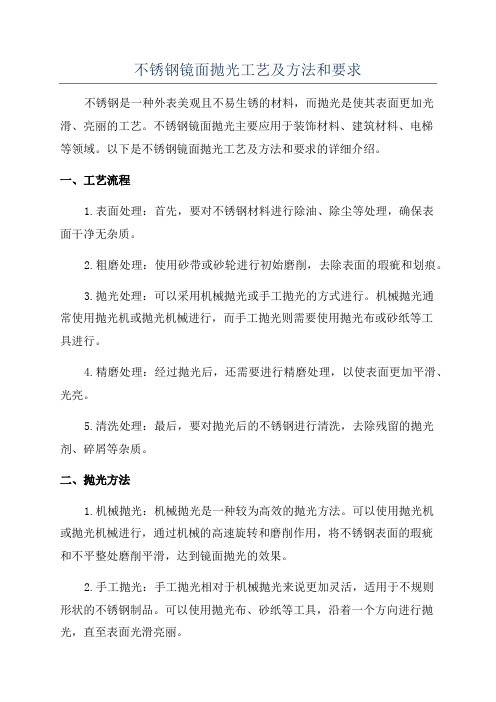
不锈钢镜面抛光工艺及方法和要求不锈钢是一种外表美观且不易生锈的材料,而抛光是使其表面更加光滑、亮丽的工艺。
不锈钢镜面抛光主要应用于装饰材料、建筑材料、电梯等领域。
以下是不锈钢镜面抛光工艺及方法和要求的详细介绍。
一、工艺流程1.表面处理:首先,要对不锈钢材料进行除油、除尘等处理,确保表面干净无杂质。
2.粗磨处理:使用砂带或砂轮进行初始磨削,去除表面的瑕疵和划痕。
3.抛光处理:可以采用机械抛光或手工抛光的方式进行。
机械抛光通常使用抛光机或抛光机械进行,而手工抛光则需要使用抛光布或砂纸等工具进行。
4.精磨处理:经过抛光后,还需要进行精磨处理,以使表面更加平滑、光亮。
5.清洗处理:最后,要对抛光后的不锈钢进行清洗,去除残留的抛光剂、碎屑等杂质。
二、抛光方法1.机械抛光:机械抛光是一种较为高效的抛光方法。
可以使用抛光机或抛光机械进行,通过机械的高速旋转和磨削作用,将不锈钢表面的瑕疵和不平整处磨削平滑,达到镜面抛光的效果。
2.手工抛光:手工抛光相对于机械抛光来说更加灵活,适用于不规则形状的不锈钢制品。
可以使用抛光布、砂纸等工具,沿着一个方向进行抛光,直至表面光滑亮丽。
三、抛光要求1.平整度要求:不锈钢镜面抛光后的表面应该平整、无凹凸、无疤痕。
2.光泽度要求:不锈钢镜面抛光后的表面应具有良好的光泽度和反射性,能够产生清晰的反射图像。
3.清洁度要求:抛光后的不锈钢表面应干净、无污渍,并且不易粘贴灰尘等杂质。
4.耐腐蚀性要求:不锈钢抛光后的表面应具有良好的耐腐蚀性,不易生锈。
综上所述,不锈钢镜面抛光是一种重要的表面处理工艺,对于提高不锈钢制品的美观度和使用寿命具有重要的作用。
在进行抛光时,需要根据不同的情况选择适合的抛光方法,同时要严格按照抛光要求进行操作,以确保抛光效果达到预期目标。
不锈钢镜面抛光工艺及方法和要求

不锈钢镜面抛光工艺及方法和要求不锈钢抛光工艺可以分为打磨和出光两部分。
现将该两部分工艺和方法总结如下:Ⅰ.打磨不锈钢焊接件打磨主要目标是去掉焊点,达到表面粗糙度为R10um的工件,为出光做准备!打磨部分概括来说有:三个工序:粗磨,半精磨,精磨三个面:两个侧面一个棱边九个抛光机二十七个调节机构,详细说明如下:1、对上道转入抛光工序的工件进行目测检验,如焊缝是否有漏焊,焊穿,焊点深浅不均匀,偏离接缝太远,局部凹陷,对接不齐,是否有较深划痕,碰伤,严重变形等在本工序无法补救的缺陷,如果有上述缺陷应返回上道工序修整。
如果无上述缺陷,进入本抛光工序。
2、粗磨,用600#的砂带在三面上往返磨削工件,本工序要达到的目标是去掉工件焊接留下的焊点,以及在上步工序出现的碰伤,达到焊口圆角初步成型,水平面和垂直面基本无大划痕,无碰伤,经此步工序后工件表面的粗糙度应能达到R0.8mm。
注意在抛光过程中注意砂带机的倾斜角度和控制好砂带机对工件的压力。
一般来说以与被抛面成一条直线比较适中!3、半精磨,用800#的砂带按照前面往返磨削工件的方法中磨工件的三面,主要是对前面工序出现的接缝进行修正以及对粗磨后产生的印痕进行进一步的细磨,对前面工序留下的印痕要反复磨削,达到工件表面无划痕,基本变亮。
本工序表面粗糙度应能达到R0.4mm。
(注意本工序不要产生新的划痕及碰伤,因为在后面的工序无法修补此类缺陷。
)4、精磨,用1000#的砂带主要是对前步工序出现的细小纹线的修正磨削,磨削方法与上同。
本工序要达到的目标是磨削部分与工件未磨削部分的接缝基本消失,工件表面进一步光亮,通过本工序磨削后的工件要基本接近镜面效果,工件表面粗糙度应能达到R0.1mm5、关于更换砂带的说明:一般来说,600#的砂带可以抛磨1500mm长的工件6-8根,800#的砂带可以抛磨工件4-6根,1000#的砂带可以抛磨工件1-2根,具体情况还需以工件焊接焊点情况,抛光使用的压力,以及打磨的方式方法有很大的关系。
镜面不锈钢抛光方法

镜面不锈钢抛光方法
镜面不锈钢抛光方法如下:
1. 准备工作:在开始抛光之前,先将不锈钢表面清洁干净,去除灰尘和污垢。
2. 粗磨处理:使用粗砂纸或研磨轮将不锈钢表面的凹凸处进行磨砂,直到表面平整。
3. 中磨处理:使用中号砂纸或中号研磨轮对整个不锈钢表面进行磨砂,注意要保持均匀的力度和方向。
4. 细磨处理:使用细砂纸或细研磨轮进行细磨,直到不锈钢表面光滑均匀。
5. 抛光处理:使用抛光膏或抛光机对不锈钢表面进行抛光处理,注意要均匀覆盖整个表面,并使用适当的力度和速度。
6. 清洗和保养:抛光完毕后,用清水冲洗不锈钢单面,确保没有抛光膏残留。
之后,用软布轻轻擦干不锈钢单面,最后可以涂上一层不锈钢保养剂,以保护不锈钢单面的亮度和光滑度。
需要注意的是,进行不锈钢抛光时要保持一致的方向,并用适当的砂纸和抛光膏,以避免划伤和不均匀的抛光效果。
另外,抛光的力度和速度也要根据具体情况进
行调整,以免对不锈钢表面造成过度磨损。
不锈钢镜面抛光工艺及制作工艺总结

不锈钢镜面抛光工艺及方法总结:不锈钢抛光工艺可以分为打磨和出光两部分。
现将该两部分工艺和方法总结如下:Ⅰ.打磨不锈钢焊接件打磨主要目标是去掉焊点,达到表面粗糙度为R10um的工件,为出光做准备!打磨部分概括来说有:三个工序:粗磨,半精磨,精磨三个面:两个侧面一个棱边九个抛光机二十七个调节机构,详细说明如下:1、对上道转入抛光工序的工件进行目测检验,如焊缝是否有漏焊,焊穿,焊点深浅不均匀,偏离接缝太远,局部凹陷,对接不齐,是否有较深划痕,碰伤,严重变形等在本工序无法补救的缺陷,如果有上述缺陷应返回上道工序修整。
如果无上述缺陷,进入本抛光工序。
2、粗磨,用600#的砂带在三面上往返磨削工件,本工序要达到的目标是去掉工件焊接留下的焊点,以及在上步工序出现的碰伤,达到焊口圆角初步成型,水平面和垂直面基本无大划痕,无碰伤,经此步工序后工件表面的粗糙度应能达到R0.8mm。
注意在抛光过程中注意砂带机的倾斜角度和控制好砂带机对工件的压力。
一般来说以与被抛面成一条直线比较适中!3、半精磨,用800#的砂带按照前面往返磨削工件的方法中磨工件的三面,主要是对前面工序出现的接缝进行修正以及对粗磨后产生的印痕进行进一步的细磨,对前面工序留下的印痕要反复磨削,达到工件表面无划痕,基本变亮。
本工序表面粗糙度应能达到R0.4mm。
(注意本工序不要产生新的划痕及碰伤,因为在后面的工序无法修补此类缺陷。
)4、精磨,用1000#的砂带主要是对前步工序出现的细小纹线的修正磨削,磨削方法与上同。
本工序要达到的目标是磨削部分与工件未磨削部分的接缝基本消失,工件表面进一步光亮,通过本工序磨削后的工件要基本接近镜面效果,工件表面粗糙度应能达到R0.1mm5、关于更换砂带的说明:一般来说,600#的砂带可以抛磨1500mm长的工件6-8根,800#的砂带可以抛磨工件4-6根,1000#的砂带可以抛磨工件1-2根,具体情况还需以工件焊接焊点情况,抛光使用的压力,以及打磨的方式方法有很大的关系。
- 1、下载文档前请自行甄别文档内容的完整性,平台不提供额外的编辑、内容补充、找答案等附加服务。
- 2、"仅部分预览"的文档,不可在线预览部分如存在完整性等问题,可反馈申请退款(可完整预览的文档不适用该条件!)。
- 3、如文档侵犯您的权益,请联系客服反馈,我们会尽快为您处理(人工客服工作时间:9:00-18:30)。
不锈钢镜面抛光工艺及方法和要求
不锈钢抛光工艺可以分为打磨和出光两部分。
现将该两部分工艺和方法总结如下:
Ⅰ.打磨
不锈钢焊接件打磨主要目标是去掉焊点,达到表面粗糙度为R10um的工件,为出光做准备!
打磨部分概括来说有:
三个工序:粗磨,半精磨,精磨
三个面:两个侧面一个棱边
九个抛光机
二十七个调节机构,
详细说明如下:
1、对上道转入抛光工序的工件进行目测检验,如焊缝是否有漏焊,焊穿,焊点深浅不均匀,偏离接缝太远,局部凹陷,对接不齐,是否有较深划痕,碰伤,严重变形等在本工序无法补救的缺陷,如果有上述缺陷应返回上道工序修整。
如果无上述缺陷,进入本抛光工序。
2、粗磨,用600#的砂带在三面上往返磨削工件,本工序要达到的目标是去掉工件焊接留下的焊点,以及在上步工序出现的碰伤,达到焊口圆角初步成型,水平面和垂直面基本无大划痕,无碰伤,经此步工序后工件表面的粗糙度应能达到R0.8mm。
注意在抛光过程中注意砂带机的倾斜角度和控制好砂带机对工件的压力。
一般来说以与被抛面成一条直线比较适中!
3、半精磨,用800#的砂带按照前面往返磨削工件的方法中磨工件的三面,主要是对前面工序出现的接缝进行修正以及对粗磨后产生的印痕进行进一步的细磨,对前面工序留下的印痕要反复磨削,达到工件表面无划痕,基本变亮。
本工序表面粗糙度应能达到R0.4mm。
(注意本工序不要产生新的划痕及碰伤,因为在后面的工序无法修补此类缺陷。
)
4、精磨,用1000#的砂带主要是对前步工序出现的细小纹线的修正磨削,磨削方法与上同。
本工序要达到的目标是磨削部分与工件未磨削部分的接缝基本消失,工件表面进一步光亮,通过本工序磨削后的工件要基本接近镜面效果,工件表面粗糙度应能达到R0.1mm
5、关于更换砂带的说明:一般来说,600#的砂带可以抛磨1500mm长的工件6-8根,800#的砂带可以抛磨工件4-6根,1000#的砂带可以抛磨工件1-2根,具体情况还需以工件焊接焊点情况,抛光使用的压力,以及打磨的方式方法有很大的关系。
另外还需注意更换砂带必须保证砂带在海绵轮上能平稳转动,以达到均匀磨削工件的目的。
打磨三个面说明:焊接件需要打磨以焊接棱边为分界线的水平和竖直的两面,具体来说一共需打磨三面,其打磨示意图如下图所示:
焊接工件焊缝示意图
九个抛光机示意图:三个砂带机作为一个工序(一组)打磨三个面,实际工作中,后一组砂带机的打磨位置需比前一组砂带机的打磨位置前进1-1.5mm ,此设计是为了后面一组抛光机能更好的打磨掉前一组留下的抛光的印痕。
二十七个调节机构:每个砂带机上分别有前后调节机构,上下调节机构,砂
负责抛左
边的焊缝
负责抛中
间的焊缝
负责抛右
边的焊缝
左右调
节机构
上下调
节机构
角度调
节机构
带机角度调节机构。
视工件焊接的具体情况,最终完成的设备由三至四个机组组成,每个机组安装不同目的砂带进行抛光。
每个砂带机的抛光位置和角度及抛光压力由抛光机调节机构控制,并在设备开始工作之前进行调节,使每台砂带机处于恰当的位置和恰当的角度并和具有恰当的工作压力,在上述所示的三个调节机构中,需有一个机构能通过光电开关检测的信号来控制其相应调节,防止出现打磨两端磨削量过大的情况。
比如设置砂带机角度调节机构,通过光电开关检测工件进入到砂带机的下方,这时调节机构启动控制砂带机抬起,等待工件进入到某一位置时调节机构将砂带机落下,砂带机通电或者通气开始进行抛光工作,抛光快结束时检测机构同样检测到工件即将抛光完成,调节机构气动控制砂带机抬起,待工件通过后落下,这样可以避免不锈钢方管两端抛磨过量的情况出现。
打磨的方式方法:
通过砂带机的大海绵轮压住工件进行打磨,打磨的同时可以水平移动砂带机或者工件,把焊接的焊点逐一打磨掉。
3.实际使用抛光机抛光方式截图如右图:
砂带机
工件
工件夹具将工件45°倾斜夹持,应用砂带机的大砂带轮进行抛光Ⅱ、出光部分
出光部分主要目的是将前面打磨出的不锈钢进行镜面出光,达到镜面的目的。
本工艺概括来说有:
两个工艺:打蜡,擦亮
两个电机,两个羊毛轮,大青腊,布
具体内容如下所述:
1、目测上一步工序进入本工序的焊接件,检查确认是否有漏打磨至1000#、所有焊点未完全打磨、存在粗打磨痕迹、破坏保护膜严重、以及磨削过量、圆角过大、两端磨削严重、打磨不均匀有的地方深浅不一等各种抛光打磨阶段出现的在出光阶段无法修复的问题,若存在这样的问题需返回重新打磨或者修补。
(在本工序中无法修复打磨中出现的碰伤,磕伤,以及大的划痕,但可以修复很细小的细纹,
比如1000#打磨出的比较小的细纹。
但是很费事)
2、 镜面
利用高速电机驱动用羊毛轮(市面有售),配合大青腊仿照前面的抛光的方法进行镜面磨光,本工序主要目的是把经过前面几道工序抛光完成后的工件进行镜面磨光,而不是进一步磨削。
注意在此步工序操作时不要将抛光蜡蹭到工件表面的覆盖膜上面,注意不要损伤覆盖膜。
3、 擦亮
本工序是镜面抛光的最后一道工序,用干净的棉布轮在经过镜面后的工件表面摩擦,将前面所有工序完成后的工件擦干净,擦亮。
本工序的目标是工件表面分辨不出焊接痕迹,以及将打蜡抛磨过的工件擦亮,亮度达到镜面反射高8k ,而且工件抛过的部分与没抛过的部分几乎看不出区别。
达到完全镜面效果。
4、 关于打蜡的说明:
a.打蜡的方式方法:一般情况是在进行抛磨工件之前先给羊毛轮
进行打蜡,待羊毛轮上粘满青腊
后才开始进行抛磨。
打蜡的方式如下图所示: 羊毛轮
夹具
工件 旋转
方向
b.为什么高速电机直接驱动羊毛轮打蜡抛磨不锈钢工件能致使其变亮:因为大青腊是一种油性物质,
在常温下时呈固态,在高温下呈液态,高速电机直接驱动羊毛轮高速旋转当羊毛轮表面粘上大青腊后在工件表面研磨由于油性物质的油性使得工件表面变亮,因此驱动羊毛轮进行抛光的电机的选择就很重要,通过实际经验总
抛光使用的电机其转速应不低于13000r/min ,其功率不应低于500w ,速度低于这个速度时其抛磨出的工件的无论从亮度或者镜面效果都不是很理想,因此一般的普通电机很难满足其要求,一般选择高速电机。
c.市面上的羊毛轮有粗轮和细轮之分。
羊毛轮的选择很重要,使电机
工件 出光电机 工件移动方向
用羊毛很粗糙的羊毛轮抛磨后容易出现打磨过的痕迹,在实际生产中一般使用细羊毛轮,这样抛出来的效果才好!
d.在抛磨过程中还需控制好对工件的压力,过大的压力羊毛轮打磨掉保护膜的区域面积过大,甚至会出现打黑工件,破坏工件原本的镜面效果等情况
e.在打磨的过程中需不断供给大青腊,否则会出现由于温度过高羊毛轮出现冒烟的现象,这对羊毛轮的磨损非常严重,对不锈钢的损害也很大。
f.对于需要在出光阶段修复的细小纹路需单独人工修复,修复工作非常费事,如果可以尽量不要在此阶段进行任何修复工作。
g.打蜡电机一般安装两个电机,每个电机负责抛光工件的其中的一面,视情况可以考虑增加一个抛磨棱边的电机,以增加棱边的亮度。
h.视情况对羊毛轮进行更换。
关于擦亮的几点补充:
a.擦亮方法方式:
工件布轮夹具电机
旋转方向
擦亮电机
工件
工件移动方向
擦亮方法基本和打蜡方式方法一致,只是打蜡中的羊毛轮换为擦亮中的布轮。
擦亮是整个抛光中的最后一道工艺,一定要确保工件抛光出光后不会有任何破坏镜面的情况,否则前功尽弃。
a.擦亮的方法是将布轮直接安装在高速电机上,实现高速转动,在工件表面上擦拭,擦掉工件上的污物和附着的大青腊,达到擦亮的目的!在实际的擦亮中往往配以研磨粉一并进行,研磨粉能去除油性物质大青腊,其在擦亮中的的主要作用是为了很容易的去掉粘附在工件上的青腊,如果不配合研磨粉,工件表面的大青腊将很难去除,而且还容易粘到其他地方,影响其他地方的美观。
b.为了得到的工件的亮度符合镜面要求,布轮的干净状况尤为重要,在实际生产中需视具体情况及时更换布轮。