手板件检验规范
一般手板件的未注公差标准
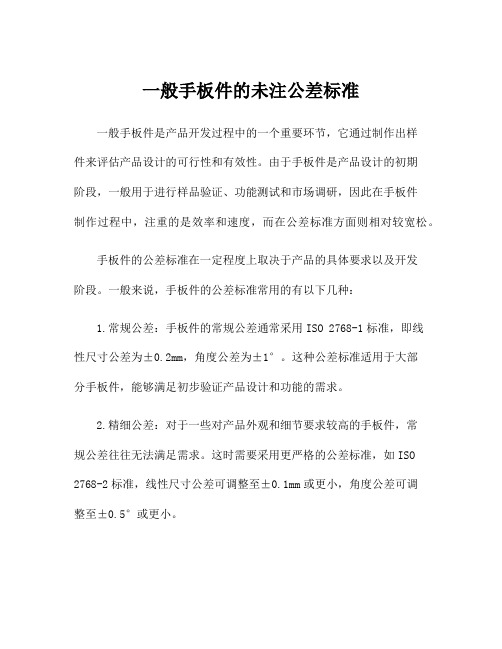
一般手板件的未注公差标准一般手板件是产品开发过程中的一个重要环节,它通过制作出样件来评估产品设计的可行性和有效性。
由于手板件是产品设计的初期阶段,一般用于进行样品验证、功能测试和市场调研,因此在手板件制作过程中,注重的是效率和速度,而在公差标准方面则相对较宽松。
手板件的公差标准在一定程度上取决于产品的具体要求以及开发阶段。
一般来说,手板件的公差标准常用的有以下几种:1.常规公差:手板件的常规公差通常采用ISO 2768-1标准,即线性尺寸公差为±0.2mm,角度公差为±1°。
这种公差标准适用于大部分手板件,能够满足初步验证产品设计和功能的需求。
2.精细公差:对于一些对产品外观和细节要求较高的手板件,常规公差往往无法满足需求。
这时需要采用更严格的公差标准,如ISO 2768-2标准,线性尺寸公差可调整至±0.1mm或更小,角度公差可调整至±0.5°或更小。
3.最大公差:在一些特殊情况下,由于产品设计要求或生产工艺的限制,手板件的公差会较大。
在这种情况下,公差标准通常会根据实际情况进行灵活调整,以保证手板件能够达到预期的功能和效果。
除了上述常规的公差标准外,手板件的公差还需要考虑以下因素:1.材料特性:不同材料具有不同的物理性质和加工特性,因此在确定公差标准时,需要考虑材料的收缩率、热变形等因素,以确保手板件制作的准确性和稳定性。
2.加工工艺:手板件通常采用快速成型技术,如3D打印、数控加工等。
这些制造工艺的精度和精细程度对于公差的控制起着重要作用,因此需要综合考虑加工工艺的特点来确定公差范围。
3.产品用途:手板件的公差标准还要根据产品的具体用途和要求来确定。
例如,对于精密仪器或电子产品,公差要求通常较高,而对于日常生活用品或临时验证模型,公差要求可能较为宽松。
总之,手板件制作的公差标准通常较为宽松,以确保能够在短时间内快速制作出样件,进行初步验证和评估。
板材来料检验规范

4.平面度要求≤4mm
3.0+0/-0.16
冷
扎
板
1.0+0/-0.08
1.2+0/-0.09
1.其厚度尺寸要求用千分尺测量.
1.5+0/-0.10
2.对于板厚有特殊要求的,见技术要求.
2.0+0/-0.11
3.平面度要求≤4mm
2.5+0/-0.12
3.0+0/-0.13
≤28
≤35
单位:mm
8.板材宽度/长度公差要求(摘选GB/T708-2006)
公称厚度
宽度允许偏差
公称宽度
≤125
>125-250
>250-400
>400-600
>600
≤0.40
+0.3/-0
+0.6/-0
+0.3/-0
+1.5/-0
+2.0/-0
>0.40-1.0
+0.5/-0
+0.8/-0
+0.3/-0
板材来料检验指导书
文件名称:
板材检验指导书
文件编号:
页码:
1/5
版本/修改状态:
A/0
发布日期:
2019-1-12
1.目的
为检验员提供来料检验规则和检验方法,保证来料质量状况,从而稳定产品质量。
2.适用范围
本标准适用于本公司所有采购板材物料的检验。
3.检验工具
游标卡尺;千分尺;卷尺
4.用语定义
4.1表面缺陷:指表面裂纹、腐蚀斑点、折痕、压痕、摩擦痕、气泡、生锈、金属压入物、非金属压入物、脏污、色差等缺陷。
2.5 -0.05/-0.11
3.0 -0.05/-0.12
铝
板
活扳手检验规程

活扳手检验规程拟制:日期:审核:日期:批准:日期:山东九鑫机械工具有限公司二〇〇六年八月十八日1范围本规程规定了活扳手的检验方法和检验规则。
本规程适用于活扳手的半成品检验和成品检验。
2引用文件GB/T4440-2008《活扳手》活扳手工艺文件GB/T2828-87《逐批检查计数抽样程序及抽样表(适用于连续批的检查)》3检验原则和基本要求3.1 检验分全检和抽检,磨光﹑初装﹑电镀﹑装配为全检工序,其它为抽检工序。
3.2 抽样与组批半成品检验的检验批应由同一规格型号的产品组成(镀层厚度检验除外),成品检验的检验批可由不同规格型号的产品组成。
样本应从提交检验批中随机抽取。
抽样方案按表1和表2的规定,其中一次抽样方案适用于下料﹑磨毛刺﹑冲尾孔﹑调直﹑精锻﹑抛丸工序的半成品检验,二次抽样方案适用于热处理工序的半成品检验﹑装配工序的扭矩检验和电镀工序的镀层厚度检验。
3.3判定规则a. 抽样检验中检验批合格与否的判定按产品质量标准和抽样方案的规定进行。
b. 不合格检验批可由操作者自行挑选出不合格品后重新提交检验。
3.4 检验报告检验完成后应做检验报告,包括返工﹑返修后重新检验的报告。
表1 一次抽样方案表2 二次抽样方案4 锻造工序产品检验4.1 下料4.1.1 质量标准a. 料棒不得有裂纹﹑空心﹑折叠﹑弯曲﹑椭圆等现象。
b. 料棒斜头量不大于1。
c. 料棒尺寸偏差按表3的规定。
表3 料棒尺寸偏差4.1.2 检验方法a. 料棒表面质量用目测检验。
b. 料棒长度尺寸及斜头量用游标卡尺检验。
4.1.3检验规则a. 根据表1规定的一次抽样方案进行抽样检验。
b.不合格检验批的处理:因斜头量超差造成的不合格进行返工,用砂轮磨削处理;因长度尺寸超差造成的不合格经评审后让步放行或改作它用。
4.2 锻造(扳体)4.2.1 质量标准a.毛坯无裂纹﹑夹层及形状不完整现象;b.毛坯错模量12″(包括12″)以下规格不大于0.5, 12″以上规格不大于0.8;c. 毛坯头部两边缘厚度相差12″(包括12″)以下规格不大于0.4,12″以上规格不大于0.5;d. 毛坯残留毛刺不大于0.8;e. 毛坯表面无严重氧化现象;f. 毛坯柄部平直,字迹清晰;g. 毛坯无切边造成的切筋﹑挤压及明显的切痕;h. 毛坯头部和柄部厚度符合工艺文件要求。
扳手检验标准

扳手检验标准发布时间:10-08-06 来源:点击量:1526 字段选择:大中小(1)呆扳手、梅花扳手和两用扳手:主要用于扳螺栓或螺母。
呆扳手由于两头开口的宽度不同,所以一把扳手可以扳二种尺寸的螺栓或螺母。
当螺母或螺栓头的周围空间狭小,不能容纳普通扳手时,须采用梅花扳手。
以上三种扳手为装配和修理工作中常用的工具。
它的种类可分为公制扳手和英制扳手二种。
呆扳手的规格有5件套、6件套、7件套、8件套、10件套。
梅花扳手的规格有5件套、6件套、8件套、12件套。
两用扳手的规格有5件套、6件套、7件套、8件套、9件套、11件套、14件套。
检验项目:呆扳手、梅花扳手和两用扳手的检验标准为:GB4388~4393。
①外观质量检验:扳手不应有裂缝、毛刺及明显的夹缝、切痕、氧化皮等缺陷,柄部应平直。
扳手的表面应进行电镀、煮黑或其他表面处理。
经电镀的扳手,其表面应色泽均匀,不应有气孔、漏镀、烧焦、起层等缺陷,镀层不低于8μm。
经煮黑处理的扳手,其表面应有均匀的黑色氧化层,不应有黄、绿、红色斑点及露底现象。
②尺寸检验:扳手的外形尺寸应符合GB4388和GB4389两标准的有关规定。
扳手的开口和扳手孔的公差应符合GB4 390标准的规定。
③硬度试验:扳手的硬度应符合表6—10—95规定。
④扭矩试验:扳手的扭矩应符合GB4393标准中的有关规定。
⑤开口与头宽的对称度检验:扳手的开口与头宽的对称度其偏差应符合GB4393标准中的有关规定。
⑥表面粗糙度检验:扳手开口两侧面的表面粗糙度Ra值应不大于12.5μm,扳手孔的表面粗糙度Ra值不大于25μm。
(2)套筒扳手:当螺母或螺栓由于位置限制,普通扳手不能工作时,就须采用这种扳手,常为车辆及农业机械等的装配、拆换和修理工作中采用。
套筒扳手为套装工具主要由:手柄、接头、各种不同尺寸的套筒头组成。
规格有9件套、10件套、13件套、15件套、17件套、28件套、32件套等。
检验项目:套筒扳手的检验标准为:GB3390.1-3390.5。
工序操作检验规范

工序操作检验规范一、数冲操作检验规范1.严格执行首检制度2.所有圆孔毛刺不得超过板厚的10%3.所有尺寸应符合图纸要求,更不许存在多孔少孔现象4.冲密孔工件时,应注意材质的选用,以免变形过大5.材质、板厚应符合图纸要求6.工件表面不得有压伤等外观缺陷,拉丝氧化的铝件表面不许有黑点等缺陷7.表面处理为拉丝氧化的工件,其表面划伤深度不得超过0.2mm8.表面处理为电镀的工件,其表面不得有锈斑、划伤等外观缺陷二、折弯操作检验规范1.严格执行首检制度2.折弯角度误差不得超过0.5°3.未注公差要求:公称尺寸为0~300mm ,允许公差值±0.20公称尺寸为300~1200mm ,允许公差值±0.30公称尺寸为1200~3000mm ,允许公差值±0.40 4.材料板厚有误差时,应调整各道折弯尺寸,误差分摊,以免将误差集中在某一个尺寸上,造成工件报废或代用。
5.折弯拉丝件或表面有特殊要求的工件时,应垫上保护膜后再折弯6.加强筋等对称工件,折弯时应将毛刺朝内7.使用拼模并且无避位要求时,应使拼膜贴紧密,以免有刀痕三、拉丝操作检验规范1.注意拉丝方向是否正确2.注意砂带粒度是否符合图纸要求3.进给量不可过大,以免工件单边明显下陷4.拉丝后应去除工件孔内及周边砂带所挤出来的毛刺5.堆放时工件间应用纸垫或气珠胶等隔离,以免表面划伤6.拉丝后工件表面不应有可见异痕四、钳工操作检验规范(一) 冲床1.严格执行首检制度2.冲孔时应保证孔大小、位置公差等符合图纸要求3.冲孔毛刺不得超过板厚的6%4.种钉、种母时注意规格、方向、位置要正确,螺牙要合格5.种钉、种母时应保证牢固可靠,且工件表面无伤痕6.拉丝、电镀及喷涂后工件种钉、种母时注意表面不得划伤或有油污7.冲床冲孔、成形、种钉、种母等加工后工件不得变形8.冲波位、压“Z”形时工件不得有裂痕、冲破等现象9.冲圆角时,应使圆角与棱边相切过茺,不得有台阶(二) 钻床1.严格执行首检制度2.钻孔位置、尺寸公差应符合图纸要求,严禁多边形边或三角形孔出现3.钻孔后应去除孔边毛刺4.沉头孔应注意沉孔方向,深度与相应沉头螺钉试配应水平或略深约0.1mm 5.钻长孔时应保证孔中心与基准面的垂直度(三) 攻丝机1.用螺纹规检验螺牙,绝对不允许有滑牙或无牙现象2.铝氧化件上重要螺牙应先打底孔,氧化后再攻牙3.拉丝氧化件攻牙时注意保护表面,不得划伤、压伤,并尽量减少油污4.攻丝后应将牙孔内废屑去除干净5.攻牙深度应符合图纸要求6.攻牙时应保证螺孔中心与基准面垂直(四) 型材下料1.严格执行首检制度2.下料尺寸应达到图纸公差要求3.下料时应保证断面与型材表面的垂直度4.型材装夹时注意不得划伤、压伤型材表面5.下料后工件应将两端面毛刺去除干净6.工件摆放时应轻拿轻放,工件间最好用纸板隔开(五) 铆接1.工件沉孔角度应与铆钉头角度一致2.工件沉孔深度应使铆钉头与工件表面平或略高0.2mm3.铆接大工件时应将两个工件校平之后再进行铆接4.铆钉长度一般为两个工件板厚之和再加2~3mm为宜5.铆接后应将工件校平,有强度要求时应配后再加铆几个铆钉6.铆接后应使铆接头与工件表面基本平整,工件表面不许有较大凹坑或凸包7.铆接要牢靠,铆钉不应有松动现象五、焊接操作检验规范1.严格执行首检制度2.所有门角接缝满焊,不得虚焊、漏焊3.铁件焊缝高度要求0.5~1.0mm,铝件焊缝高度要求0.5~1.5mm,门板等组件碰焊时要求外表面焊点深度不得超过0.3mm4.整机架组焊外表面的焊缝一般均要求满焊,且焊缝要饱满。
来料检验规范
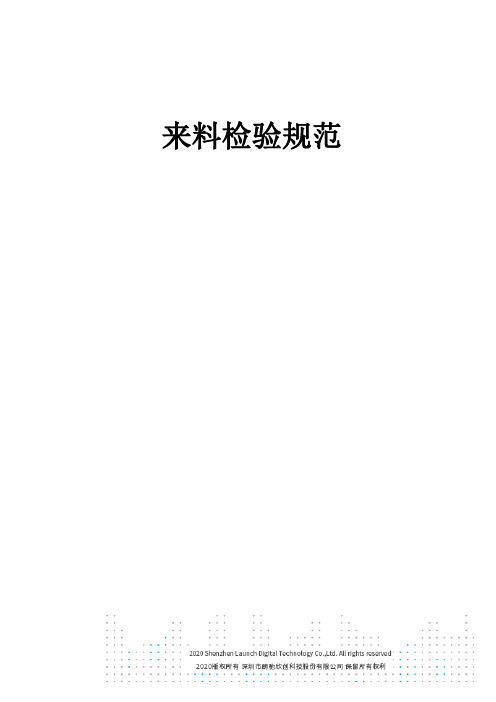
来料检验规范文件状态 XXXX发布日期 XXXX-XX-XX生效日期 XXXX-XX-XX目录一、目的: (3)二、适用范围 (3)三、职责 (3)四、定义 (3)五、工作程序 (3)5.1 来料检验操作程序 (3)5.2 来料检验比例和允收准则 (4)5.3 来料不合格品特采程序 (5)六、流程简图 (6)七、相关文件记录 (6)一、目的:规范原材料来料检验流程,明确各部门职责,做好原材料质量控制,防止不合格品流入产线,特制定本文件。
二、适用范围试用于公司所有原材料、委外加工成品/半成品、辅料。
三、职责3.1 质量部3.1.1 IQC负责来料的品质检验、不良判定与隔离、报告整理。
3.1.2 SQE负责问题反馈供应商、组织不合格品评审、处理、供应商问题整改推进。
3.2 采购部不合格品的退货确认、不合格品处理进度跟踪。
3.3 中试部负责参与来料不良的评审及给出处理意见。
3.4 仓储部3.4.1 负责对来料规格的初步核实、数量的清点及开单送检。
3.4.2 负责检验合格物料的入库。
3.5 研发中心负责参与来料不良的评审及给出处理意见。
3.6 产品中心负责参与来料不良的评审及给出处理意见。
四、定义4.1 IQC:来料质量检验与控制。
4.2 AQL:接收质量限,检验抽检使用,可在ERP上查询对应物料AQL值。
五、工作程序5.1 常规来料检验操作程序5.1.1 到料时,仓储部根据供应商“送货单”(如无送货单根据实际数量)对来料实物的数量、包装、型号进行初步验收,并打印“到货单”。
5.1.2 仓储部验收无误,打印“内部物料标签”贴于待检物料上,连同“到货单”和待检实物送于IQC。
5.1.3 IQC应根据计划部的订单信息、急料信息等及时布置好对原材料的检验工作。
5.1.4 检验员对待检的物料以对应的来料检验标准、物料样板、图纸、生产规格书或客户的特殊要求作为来料检验依据,并根据GB/T2828.1-2012抽样计划进行抽样。
手板制作要求方案

手板制作要求方案手板制作是研发部们为了提升研发实力,对新品的外观、结构可行性是一重要环接。
提高手板制作就是研发成熟度而实行的一项重要工作。
由于速度快,成本低,大大降低了产品的开发费用,时间与风险。
可以满足产品开发过程中的性能测试。
极大地提高了新品竞争力。
图纸有结构、项目负责、XX总签字后,才能下达到手板组加工。
结构人员需提供二维图纸、三维文件、手板清单、加工协议单。
一、职责分配:1.手板模型进度和质量有结构人员负责。
2.手板零件外观和精度尺寸有手板人员负责。
3.喷涂有手板组安排专业人员负责。
4.手板模型加工后有结构人员按照设计意图负责装配。
5.手板零件验收由结构人员判定(参照手板零件检验表)。
二、手板制作注意事项:1.按图纸要求达到粗糙度标准。
2.签定加工协议单排定计划日期。
3.模型制作中根据设计所需配颜色一起制作。
4.透明件对应图纸要求材料制作,内壁光滑不能有机床加工的刀纹路。
5.塑件结构灵活,并可以当完整产品使用。
5. 手板的制作前期设计人员要与手板制作人员沟通。
6. 设计的产品要肯定好成形工艺和工序,不会因零件难以加工而修改定型设计。
7. 手板制作方可提前做加工准备,防止匆忙中考虑不周,影响工期。
8.手板在喷涂前要考虑油漆厚度是否与图纸要求尺寸有差别。
9.手板件加工前要考虑粗加工和精加工余量,防止出现开裂和内外不同心、产品外观有加工纹理。
10.零件加工前对材料的正确选用,结构件在受高温和低温变化后,手板人员协助结构人员动手修改。
11.每个手板零件加工后有结构人员测量并组装,设计出现问题将有结构人员修改,需要再通过评审后才能到手板组重新加工。
总之,制作高质量手板,只有双方紧密配合,才能最终降低新品开发成本,缩短周期。
一般手板件的未注公差标准
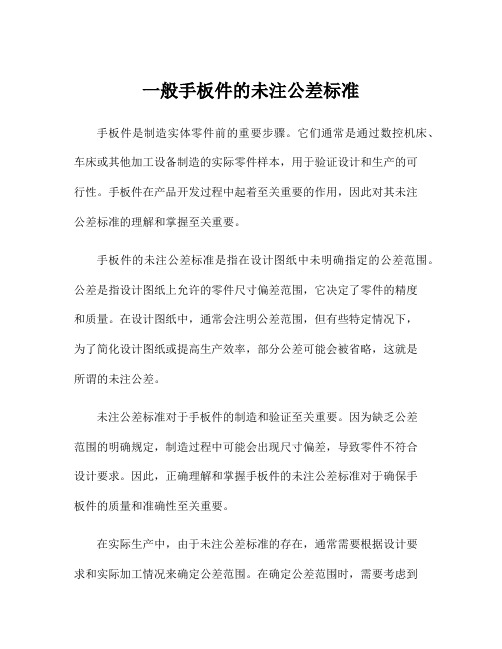
一般手板件的未注公差标准手板件是制造实体零件前的重要步骤。
它们通常是通过数控机床、车床或其他加工设备制造的实际零件样本,用于验证设计和生产的可行性。
手板件在产品开发过程中起着至关重要的作用,因此对其未注公差标准的理解和掌握至关重要。
手板件的未注公差标准是指在设计图纸中未明确指定的公差范围。
公差是指设计图纸上允许的零件尺寸偏差范围,它决定了零件的精度和质量。
在设计图纸中,通常会注明公差范围,但有些特定情况下,为了简化设计图纸或提高生产效率,部分公差可能会被省略,这就是所谓的未注公差。
未注公差标准对于手板件的制造和验证至关重要。
因为缺乏公差范围的明确规定,制造过程中可能会出现尺寸偏差,导致零件不符合设计要求。
因此,正确理解和掌握手板件的未注公差标准对于确保手板件的质量和准确性至关重要。
在实际生产中,由于未注公差标准的存在,通常需要根据设计要求和实际加工情况来确定公差范围。
在确定公差范围时,需要考虑到材料的性质、加工工艺、设备精度、生产环境等诸多因素。
只有合理确定未注公差范围,才能确保手板件的精度和质量。
在实际加工过程中,可以采用以下几种方法来确定手板件的未注公差标准:1.参考相关标准:根据产品的类型和用途,可以参考相关的国家标准或行业标准,来确定手板件的公差范围。
这种方法相对简单快捷,但可能无法完全满足特定产品的需求。
2.借鉴类似产品:可以参考类似产品的设计和加工经验,来确定手板件的公差范围。
这种方法可以根据实际产品的特点来确定公差范围,但需要充分了解和分析类似产品的设计特点和加工过程。
3.实际加工验证:可以通过试制手板件,并进行实际加工验证来确定公差范围。
这种方法相对较为准确,但需要投入一定的成本和时间。
除了确定未注公差标准之外,还需要在加工过程中严格控制加工工艺、设备精度、原材料质量等因素,以确保手板件的精度和质量。
同时,在设计阶段也应该尽量明确公差范围,以减少未注公差的影响。
总之,手板件的未注公差标准对于产品的设计和加工过程至关重要。
塑料件半成品检验规范

塑料件半成品检验规范1.0目的:1.为有效保证最终到达客户(消费者)手上的产品不发生重大品质问题;特别是结构及功能问题,能在厂内有效管控并检出;针对可靠性项目,能有效识别出产品究竟在什么时候会暴露出缺陷,从而找出该参数之平均无故障时间。
2.为确保从最初理念产品开发至最终交付客户使用整个过程,在工艺、物料、产品结构、量产可制造性;在标准,方法及可靠性等等在质量方面能给予有效评估,评审;从而通过检出度保证,防呆,信赖性标准及方法,工艺开发设计,检测手段设计,以确保平均无故障时间能达到客户需求,以期保证公司从发展期迈入飞速发展期此一关键时期的品质。
3.公司拟成立一个流程功能团队,来负责从理念产品到客户手上整条线的串接,使现阶段公司品质方面的主要问题尽快解决,而不是成为阻力,不只是把问题卡在厂内,还要去负责疏通,解决。
4.希望透过对各阶段设计输出资料、研发输出、模具承认、产品试产的审查、评估,确保这些资料的全面性、可控性、适宜性,有效、可操作性。
2.0适用范围:1.本程序适用于公司新产品(OBM、ODM、OEM)的设计/开发、生产量产、交付、使用等全过程之管理,现行产品的改进和改型,以及为了满足客户特殊要求而对产品进行的修正、改良。
2.本程序由公司市场部、设计、研发、产品、工程、模具、品保、品管、采购、生产、工艺、试产等相关人员执行3.针对上述范围内的产品,依产品部提供的项目时间表追踪,评估与评审设定的结点3.0职责1.设计评审结果的评估及追踪(包括:模具、样品、结构、手板、ID、电子等)2.产品工艺评审,是否可执行、有效(包括:试模、测试治具、包装、流程设计及方法、检验点及方法、防呆方法设计评审、工艺参数评估等)3.试产阶段生产要素如何管控、试产评审4.可靠性检测手段计划提出,检测度保证方法设计及评审5.检测点设置、检测项目制订6.量产突发重大品质异常检测方法、标准、手段,检出度设计及验证7.材料设计评审及送检承认评审8.试验设计4.0述语定义:MTTF:(meantimetofailure)失效前平均时间,定义为随机变量、出错时间等的“期望值”。
手持设备按键板实验、检验标准0.0

IQC检验
13、内应力浸泡测试
PC
ABS+PC
ABS
IQC检验
甲苯+正丙醇(乙醇)1:3
乙酸乙酯+甲醇2:3
冰醋酸
3分钟
3分钟
3分钟
将胶件取出,自然风干,无外力施加于产品上进行检查产品外观;
各胶件应无有块状崩落、裂纹、严重变形等现象。
1目的
规范按键板的检验标准,以此作为本公司品质部按键板检验的依据。
2范围
本标准适用于移动事业部IQC对按键板的检验工作。
3检验规则
在交货方提供的合格产品中按GB/T 2828.1-2003《计数抽样检验程序 第1部分:按接收质量限(AQL)检索的逐批检验抽样计划》中一次正常抽样方案进行抽样,合格质量水平(AQL)及检查水平(IL)规定如下:
-
-
-
-
-
-
√
-
√
-
√
-
-
-
-
2)外观、尺寸
缺陷内容描述
缺陷判定
备注
检验内容
Z
A
B
C
1、外观
1、笔划的粗细差别超过标准W允许的文字线粗的1/5----------------
2、飞边长度a>1/3h(字高)、 边长度b>1/3h(字高)-------------
3、中心编移值Δ>0.30mm----------------------------------------
8、温度循环
把样品放入温度+66℃,20%RH的箱中保持1小时,然后降低到32℃,90%RH保持1小时,接着调整箱中的温度到-40℃保持1小时后升温到25℃50%RH保持1小时,以这样为一个周期循环,共进行,共进行27个周期物质循环。然后在25℃,50%RH状态下取出试验样品,再在常温下恢复两小时后进行外观检验,并进行百格试验。
一般手板件的未注公差标准
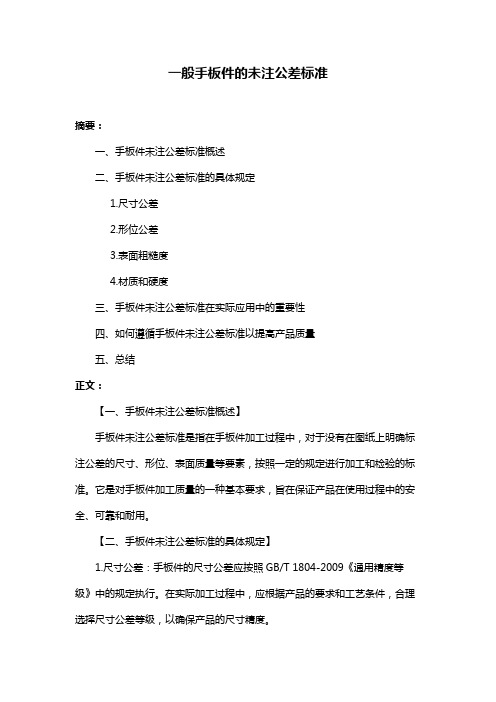
一般手板件的未注公差标准摘要:一、手板件未注公差标准概述二、手板件未注公差标准的具体规定1.尺寸公差2.形位公差3.表面粗糙度4.材质和硬度三、手板件未注公差标准在实际应用中的重要性四、如何遵循手板件未注公差标准以提高产品质量五、总结正文:【一、手板件未注公差标准概述】手板件未注公差标准是指在手板件加工过程中,对于没有在图纸上明确标注公差的尺寸、形位、表面质量等要素,按照一定的规定进行加工和检验的标准。
它是对手板件加工质量的一种基本要求,旨在保证产品在使用过程中的安全、可靠和耐用。
【二、手板件未注公差标准的具体规定】1.尺寸公差:手板件的尺寸公差应按照GB/T 1804-2009《通用精度等级》中的规定执行。
在实际加工过程中,应根据产品的要求和工艺条件,合理选择尺寸公差等级,以确保产品的尺寸精度。
2.形位公差:手板件的形位公差应按照GB/T 1182-2008《形状和位置公差》中的规定执行。
加工过程中,要保证形位公差的要求,以保证产品具有良好的形位精度。
3.表面粗糙度:手板件的表面粗糙度应按照GB/T 3514-2008《金属表面粗糙度》中的规定执行。
在加工过程中,应根据产品使用环境和要求,选择合适的表面粗糙度参数,以提高产品的耐磨性、抗腐蚀性等性能。
4.材质和硬度:手板件的材质和硬度应根据产品使用要求和技术条件进行选择和控制。
在加工过程中,要保证材质的纯净度、硬度的均匀性等指标,以保证产品的使用寿命和性能。
【三、手板件未注公差标准在实际应用中的重要性】手板件未注公差标准在实际应用中具有重要意义。
遵循这一标准,可以确保手板件加工质量的稳定性和一致性,降低产品在使用过程中出现故障的风险。
同时,它可以提高我国制造业的整体水平和竞争力,满足国内外市场的需求。
【四、如何遵循手板件未注公差标准以提高产品质量】要遵循手板件未注公差标准,首先要提高企业和员工对标准的认识和理解。
企业应组织培训,加强员工的技能和知识储备。
手板件检验规范

版本修订记录1.适用范围本标准适用于公司现有产品所使用的手板件来料检验。
2.工作职责IQC:负责来料检验及按标准判断物料是否合格;仓管员:负责物料报检及不良品的退料工作;采购员:负责物料采购及退单打印;品质部:负责来料不良品评审组织;其它部门:负责不良品评定。
3.抽检方案一致性:全检外观:按正常检查一次抽样方案, 检查水平Ⅱ:AQL=0.65;尺寸:首次量产来料全尺寸检验1pcs,重要尺寸全检;正常每批抽检3pcs重要尺寸。
适配性:首次量产来料适配3pcs,正常每批抽检1pcs特殊性能:阻燃测试首次来料测试1pcs,正常每6批(最小数量100pcs)抽测1pcs。
附着力测试首次量产来料测试1pcs,正常每3批(最少数量30pcs)抽测1pcs耐酒精测试首次量产来料测试1pcs,每批来料抽测1pcs环保要求:根据样品资料,首次导入的供应商样品阶段测试1pcs,正常每6批(最小数量100pcs)抽测1pcs。
4.仪器及工具游标卡尺、直尺、针规、酒精灯、软布、500g砝码、3M胶纸、橡皮擦、美工刀、放大镜、塞规、毛刷5.检验条件5.1 所有检验均应在正常光线条件下或在40W至60W日光灯下,并模拟最终使用条件下进行。
检测过程中不使用放大镜,所检验表面和人眼呈45°角(如图1)。
A级面在检验时应转动,以获得最大反光效果。
B级面和C级面在检验时不必转动。
光源=40W日光灯毫米图16.定义6.1一致性:指同一批来料应具有良好的一致性,其体现在:外形、颜色、光泽、丝印、包装、标识等,并且与样件无明显差别、与前批来料可保持良好的一致。
6.2外观标准定义:外观标准为A、B、C面:图纸最少需表面A、B、C面,参考图纸确定如因特殊原因未标明按照以下定义来确定A、B、C面。
A面:零件组装成产品后无需借助辅助工具在允许的可视角度(+/-45度)范围内可见区域。
B面:零件组装成产品后无需借助辅助工具非A面范围内可见区域的其它区域;零件组装成产品后需借助辅助查看工具的区域。
手扳葫芦检测标准
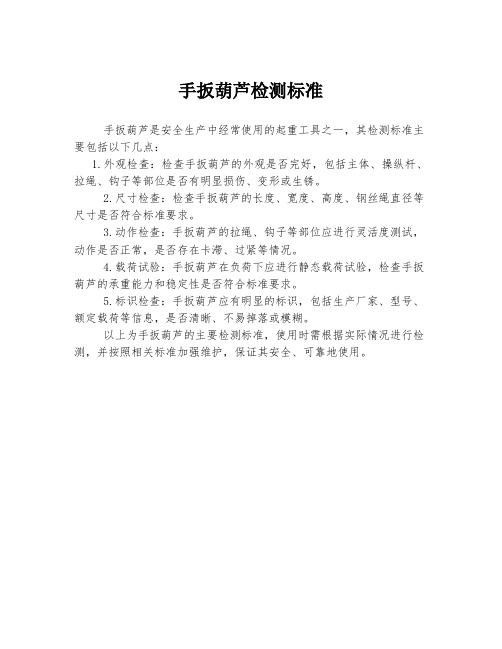
手扳葫芦检测标准
手扳葫芦是安全生产中经常使用的起重工具之一,其检测标准主要包括以下几点:
1.外观检查:检查手扳葫芦的外观是否完好,包括主体、操纵杆、拉绳、钩子等部位是否有明显损伤、变形或生锈。
2.尺寸检查:检查手扳葫芦的长度、宽度、高度、钢丝绳直径等尺寸是否符合标准要求。
3.动作检查:手扳葫芦的拉绳、钩子等部位应进行灵活度测试,动作是否正常,是否存在卡滞、过紧等情况。
4.载荷试验:手扳葫芦在负荷下应进行静态载荷试验,检查手扳葫芦的承重能力和稳定性是否符合标准要求。
5.标识检查:手扳葫芦应有明显的标识,包括生产厂家、型号、额定载荷等信息,是否清晰、不易掉落或模糊。
以上为手扳葫芦的主要检测标准,使用时需根据实际情况进行检测,并按照相关标准加强维护,保证其安全、可靠地使用。
机械手模具验收规范

冲压机械手模具验收技术要求1.模具外观:a)模具(规格型号)内容完整,字符清晰,排列整齐。
b)模具零部件不允许有裂纹、工作面划伤、机械损伤及锈蚀等缺陷;c)热处理部件硬度不小于 HRC58;d)退料板导柱等部件配合,需流畅顺滑;e)模具外轮廓尺寸大于500mm时,模具上、下模板都要有起吊螺栓孔;f)模具结构为反冲,凸凹模在下方装配,模架为4根精密滚珠导柱(套)+ 4精密内导向为主。
如有异议请与我方技术人员联系;g)模具上、下模板厚度尺寸不应小于50mm。
2.模具材质:a)上、下模板首选为A3,如需换特殊材料必须与我方技术人员沟通同意后,方可更换材料;b)垫板、退料板、压料板如需热处理,硬度不小于HRC40(建议材料;40Gr 45#等);c)凸模、凹模主要材料为国标D2.Cr12MoFn SKD11,热处理硬度HRC58—62。
3.模具加工要求:a)凸模凹模等重要部件要求采用精密加工手段,如慢丝切割,CNC 等加工b) 模具零部件加工,一定要求有基准面,统一基准加工4.模具安装要求:a)该模具装在200吨冲床上,设计模具合模高度应在350--500mm;b)如需增加垫铁,厚度≧60mm,数量不少于4件;c)模具内框要增加限位块,防止刃口切入过深;d)退料橡皮或弹簧要沉入到下模板内,沉入≧15mm ;防止飞溅伤人。
5.模具使用要求:a)寿命持续达到≧500万次,模具首次上线生产不低于10万次;(100万/次二级保养,400万/ 次更换主要零部件即凸模凹模等)b)冲制产品无任何变形,尺寸符合图纸要求;c)如有相关问题请及时与我方技术人员沟通,我方同意后方可继续进行。
d)模具制作好后,应在相关危险部位涂色标注危险警示。
6.模具配件要求:a)五金配件选用,国内标准规格方便快速采购;不允许使用非标部件,增加后续问题。
b)模具制作好后,应配备相应数量的易损件(如:定位块,冲头和各种镶嵌部件)c)如模具使用特种部件,请配备齐相关工具,方便拆卸模具7机械手模具每分钟生产20件。
手雕质检流程检验标准

手工雕刻质检流程检验标准采用纯手工雕刻的家具,承载着我国明清时期精湛的家具制作工艺,向来体现着红木家具文化价值之所在。
手雕家具所展现出来的,是一幅栩栩如生、张力十足的画面,无论是人物还是花鸟,都充满着动感和生命力。
检验要求检验雕刻工艺是否符合要求,可按以下标准执行。
雕刻的重要原则就是讲究整体协调,画面主题、层次分明,以雕刻云龙为例,层次可依次分为龙头、龙身、龙爪、云朵、底云;此外,图案结构还要做到均匀,龙头要突出,龙须粗细均匀、线条流畅、龙身清晰,龙爪肌肉强劲有力。
操作步骤1)设计、贴图。
图纸设计是雕刻工作的蓝图,好比建造一座大厦需要施工图一样,雕刻也不例外。
首先由专门的设计人员精心设计,再绘制成图,将设计好的图纸贴于被雕刻的木材表面。
2)锣地。
根据图纸的设计需要,抠空空地,初步体现雕刻层次,精确控制图案层次的深度,并依据图案小样用机器抠空打薄,如遇穿孔需用线锯机把中间部分凿穿。
注意要调好机器,木材板厚度至少应为0.8cm。
3)打坯。
此步骤基本能做出雕刻图案的初步轮廓,家具为名贵木材则一般先用白木打样,把基本图形扫描进雕刻机,然后机器会根据样板雕刻成形。
4)修光。
机雕出来的半成品已有大概的图案样子,此时需要专门的雕刻工人进行修光,主要工作内容为按照图案的层次、高低、深浅逐步施工,塑造整体层次和立体感。
5)精雕。
这是雕刻的最后一道工序,这要求操作者非常细心与耐心,如龙须、龙鳞之类的细小部位需由专门的工人来做。
其中龙须的雕刻,如果稍微分心就容易造成须沟破碎或雕刻刀越界。
因此,判断工艺的高低,取决于龙须是否粗细均匀、线条是否流畅。
操作要点1.不同的题材尽可能由专门设计人员完成,比如某人精于山水但不擅长云龙,那么尽可能让其扬长避短,把可能出现的问题解决在设计源头。
2.雕刻机器的操作需要专业操作人员,上岗前必须经过专业培训,某些企业对于新手的培训尤为严格,时间长达半年。
3.避免有疤结的材料用于雕刻面,如果选料不当极易造成雕刻图案受损,进而影响图案的完整性和家具的美观。
手工、试整检验标准
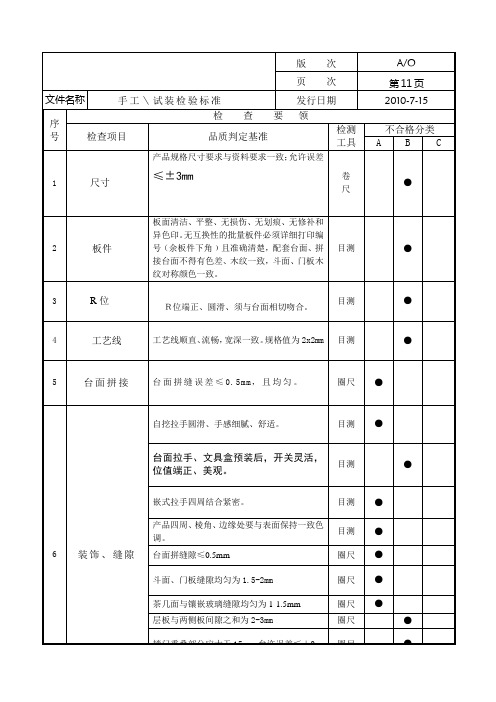
●
3
R位
R位端正、圆滑、须与台面相切吻合。
目测
●
4
工艺线
工艺线顺直、流畅,宽深一致。规格值为2x2mm
目测
●
5
台面拼接
台面拼缝误差≤0.5mm,且均匀。
圈尺
●
6
装饰、缝隙
自挖拉手圆滑、手感细腻、舒适。
目测
●
台面拉手、文具盒预装后,开关灵活,位值端正、美观。
目测
●
嵌式拉手四周结合紧密。
目测
●
产品四周、棱角、边缘处要与表面保持一致色调。
版次
1
A/O
页次
第11页
文件名称
手工\试装检验标准
发行日期
2010-7-15
序
号
检查要领
检查项目
品质判定基准
检测工具
不合格分类
A
B
C
1
尺寸
产品规格尺寸要求与资料要求一致;允许误差
≤±3mm
卷尺
●
2
板件
板面清洁、件下角﹚且准确清楚,配套台面、拼接台面不得有色差、木纹一致,斗面、门板木纹对称颜色一致。
目测
●
台面拼缝隙≤0.5mm
圈尺
●
斗面、门板缝隙均匀为1.5-2mm
圈尺
●
茶几面与镶嵌玻璃缝隙均匀为1-1.5mm
圈尺
●
层板与两侧板间隙之和为2-3mm
圈尺
●
趟门重叠部分应大于15mm,允许误差≤±2mm
圈尺
●
产品有缺色的用毛笔蘸取同色漆补色,注意效果自然协调。
目测
●
塑料手板检验报告
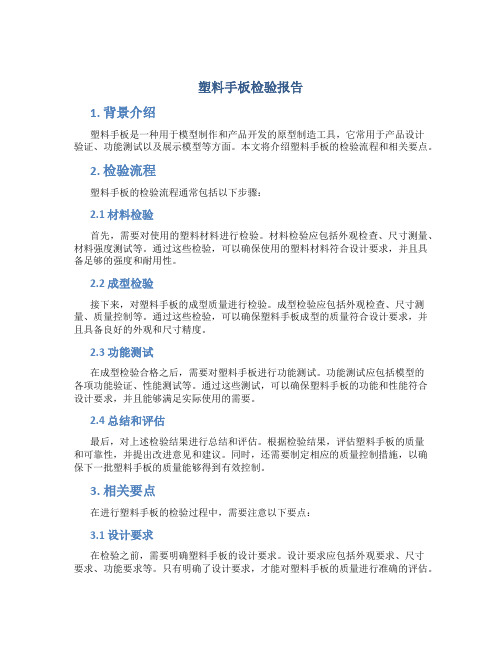
塑料手板检验报告1. 背景介绍塑料手板是一种用于模型制作和产品开发的原型制造工具,它常用于产品设计验证、功能测试以及展示模型等方面。
本文将介绍塑料手板的检验流程和相关要点。
2. 检验流程塑料手板的检验流程通常包括以下步骤:2.1 材料检验首先,需要对使用的塑料材料进行检验。
材料检验应包括外观检查、尺寸测量、材料强度测试等。
通过这些检验,可以确保使用的塑料材料符合设计要求,并且具备足够的强度和耐用性。
2.2 成型检验接下来,对塑料手板的成型质量进行检验。
成型检验应包括外观检查、尺寸测量、质量控制等。
通过这些检验,可以确保塑料手板成型的质量符合设计要求,并且具备良好的外观和尺寸精度。
2.3 功能测试在成型检验合格之后,需要对塑料手板进行功能测试。
功能测试应包括模型的各项功能验证、性能测试等。
通过这些测试,可以确保塑料手板的功能和性能符合设计要求,并且能够满足实际使用的需要。
2.4 总结和评估最后,对上述检验结果进行总结和评估。
根据检验结果,评估塑料手板的质量和可靠性,并提出改进意见和建议。
同时,还需要制定相应的质量控制措施,以确保下一批塑料手板的质量能够得到有效控制。
3. 相关要点在进行塑料手板的检验过程中,需要注意以下要点:3.1 设计要求在检验之前,需要明确塑料手板的设计要求。
设计要求应包括外观要求、尺寸要求、功能要求等。
只有明确了设计要求,才能对塑料手板的质量进行准确的评估。
3.2 检验方法在进行检验时,需要选择合适的检验方法。
检验方法的选择应根据具体的检验要求和检验对象来确定。
常用的检验方法包括目视检查、测量检验、性能测试等。
3.3 质量控制在进行塑料手板的检验过程中,需要建立相应的质量控制措施。
质量控制应从材料采购、成型过程、功能测试等方面入手,确保每一道工序都符合要求,并且能够有效控制塑料手板的质量。
3.4 检验记录在进行检验时,需要做好相应的检验记录。
检验记录应包括检验日期、检验人员、检验方法、检验结果等信息。
液压扳手出厂检验作业指导书

北京xxxx机电技术有限公司文件编号:CBE/WI-QA-001版本:V1.0页数:7发布日期:2016-8-18液压力矩扳手出厂检验作业指导书编制:审核:批准:文件更改记录1目的规范液压力矩扳手出厂检验流程和检验项目,明确检验要求,确保产品出厂质量合格。
2适用范围适用液压力矩扳手出厂检验活动。
3检验依据3.1CBE-RC-82 产品出厂验收规范-20140321-V4.0;3.2CBE-QA(2011)-05检验规范-20110911-C。
4职责4.1库房管理员根据《发货信息》提供液压力矩扳手,通知检验员检验。
4.2检验员负责根据《发货信息》和本作业指导书对产品质量的符合性进行检验和试验,合格品放行。
5工作内容5.1外观检验5.2 数量检验5.3 压力试验液压力矩扳手在空载、负载及保压状态下,各部位无泄漏,无损坏,操作流程如下: 5.3.1 试验准备5.3.1.1 HPE520电动液压泵1台,如下图。
5.3.1.2 油管2根,如下图。
压力 调节阀压力表母接头公接头低压 启动键高压 启动键5.3.1.3 扭矩标定台及转换接头,如下图。
5.3.1.4 液压力矩扳手1套,如下图。
(以TMCS-3型为例)5.3.1.5 防护眼镜。
(检验员在试验过程中需佩戴防护眼镜) 5.3.2 组装油管两端接头均为母接头 油管两端接头均为公接头转换接头公接头R扳手体驱动棒母接头 A反支撑扭矩标定台大角方向5.3.2.1油管两端分别与电动液压泵和液压力矩扳手进行组装,采取公、母接头对接形式连接并紧固,如下图所示。
5.3.2.2电动液压泵接通电源。
5.3.3试验5.3.3.1单击低压启动键,启动电动泵,运行1-2分钟无异常后继续试验。
5.3.3.2单击高压启动键,根据压力表显示值调整压力调节阀,将压力调整至10000psi为止。
(液压扭矩扳手最大承载压力为10000psi,禁止超压)5.3.3.3按住高压启动键,在10000psi压力下保压10秒钟后松开高压启动键,液压力矩扳手各部件无损坏、无泄漏为合格。
活动扳手出货检验标准
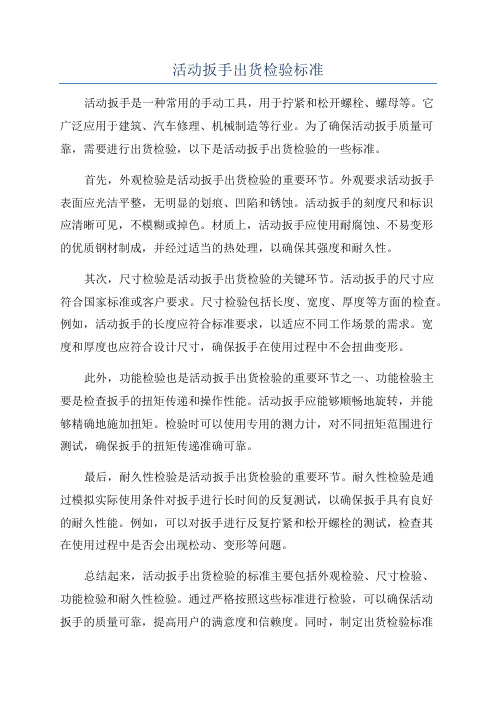
活动扳手出货检验标准活动扳手是一种常用的手动工具,用于拧紧和松开螺栓、螺母等。
它广泛应用于建筑、汽车修理、机械制造等行业。
为了确保活动扳手质量可靠,需要进行出货检验,以下是活动扳手出货检验的一些标准。
首先,外观检验是活动扳手出货检验的重要环节。
外观要求活动扳手表面应光洁平整,无明显的划痕、凹陷和锈蚀。
活动扳手的刻度尺和标识应清晰可见,不模糊或掉色。
材质上,活动扳手应使用耐腐蚀、不易变形的优质钢材制成,并经过适当的热处理,以确保其强度和耐久性。
其次,尺寸检验是活动扳手出货检验的关键环节。
活动扳手的尺寸应符合国家标准或客户要求。
尺寸检验包括长度、宽度、厚度等方面的检查。
例如,活动扳手的长度应符合标准要求,以适应不同工作场景的需求。
宽度和厚度也应符合设计尺寸,确保扳手在使用过程中不会扭曲变形。
此外,功能检验也是活动扳手出货检验的重要环节之一、功能检验主要是检查扳手的扭矩传递和操作性能。
活动扳手应能够顺畅地旋转,并能够精确地施加扭矩。
检验时可以使用专用的测力计,对不同扭矩范围进行测试,确保扳手的扭矩传递准确可靠。
最后,耐久性检验是活动扳手出货检验的重要环节。
耐久性检验是通过模拟实际使用条件对扳手进行长时间的反复测试,以确保扳手具有良好的耐久性能。
例如,可以对扳手进行反复拧紧和松开螺栓的测试,检查其在使用过程中是否会出现松动、变形等问题。
总结起来,活动扳手出货检验的标准主要包括外观检验、尺寸检验、功能检验和耐久性检验。
通过严格按照这些标准进行检验,可以确保活动扳手的质量可靠,提高用户的满意度和信赖度。
同时,制定出货检验标准也可以帮助生产厂家提高生产工艺和产品质量控制,促进企业的可持续发展。
- 1、下载文档前请自行甄别文档内容的完整性,平台不提供额外的编辑、内容补充、找答案等附加服务。
- 2、"仅部分预览"的文档,不可在线预览部分如存在完整性等问题,可反馈申请退款(可完整预览的文档不适用该条件!)。
- 3、如文档侵犯您的权益,请联系客服反馈,我们会尽快为您处理(人工客服工作时间:9:00-18:30)。
版本修订记录1.适用范围本标准适用于公司现有产品所使用的手板件来料检验。
2.工作职责IQC:负责来料检验及按标准判断物料是否合格;仓管员:负责物料报检及不良品的退料工作;采购员:负责物料采购及退单打印;品质部:负责来料不良品评审组织;其它部门:负责不良品评定。
3.抽检方案一致性:全检外观:按正常检查一次抽样方案, 检查水平Ⅱ:AQL=0.65;尺寸:首次量产来料全尺寸检验1pcs,重要尺寸全检;正常每批抽检3pcs重要尺寸。
适配性:首次量产来料适配3pcs,正常每批抽检1pcs特殊性能:阻燃测试首次来料测试1pcs,正常每6批(最小数量100pcs)抽测1pcs。
附着力测试首次量产来料测试1pcs,正常每3批(最少数量30pcs)抽测1pcs耐酒精测试首次量产来料测试1pcs,每批来料抽测1pcs环保要求:根据样品资料,首次导入的供应商样品阶段测试1pcs,正常每6批(最小数量100pcs)抽测1pcs。
4.仪器及工具游标卡尺、直尺、针规、酒精灯、软布、500g砝码、3M胶纸、橡皮擦、美工刀、放大镜、塞规、毛刷5.检验条件5.1 所有检验均应在正常光线条件下或在40W至60W日光灯下,并模拟最终使用条件下进行。
检测过程中不使用放大镜,所检验表面和人眼呈45°角(如图1)。
A级面在检验时应转动,以获得最大反光效果。
B级面和C级面在检验时不必转动。
光源=40W日光灯毫米图16.定义6.1一致性:指同一批来料应具有良好的一致性,其体现在:外形、颜色、光泽、丝印、包装、标识等,并且与样件无明显差别、与前批来料可保持良好的一致。
6.2外观标准定义:外观标准为A、B、C面:图纸最少需表面A、B、C面,参考图纸确定如因特殊原因未标明按照以下定义来确定A、B、C面。
A面:零件组装成产品后无需借助辅助工具在允许的可视角度(+/-45度)范围内可见区域。
B面:零件组装成产品后无需借助辅助工具非A面范围内可见区域的其它区域;零件组装成产品后需借助辅助查看工具的区域。
C面:零件组装成产品后被其它部件遮盖的区域,或借助辅助拆卸工具(如电批)方可看见的区域。
7.0检验标准7.1 尺寸检验标准:对已在图纸中标明的关键尺寸,选择合适的测量仪器对照有效版本图纸进行检验并记录指定的尺寸数据,其它尺寸(仅作符合性验证)可只记录不合格数据,如果没有标注关键尺寸,以带小数点的尺寸为关键尺寸。
7.2手板件外观检验标准颜色、丝印、表面处理、外形、嵌件、包装等符合图纸要求,缺陷原则上以图纸为准,如图纸未注明参照以下要求。
7.3尺寸符合图纸要求7.4适配性无装配困难、无法装配现象,符合图纸设计要求。
7.5特殊性能7.5.1阻燃要求根据图纸要求符合阻燃特性,图纸无要求无需符合此项标准。
7.5.2附着力标准:符合图纸要求。
图纸无要求无需符合此项标准,图纸有要求需符合以下标准,图纸特殊要求除外。
7.5.2.1烤漆工艺需测试符合百格测试要求(切口脱落面积小于10%);7.5.2.2喷漆喷油工艺工艺橡皮擦测试橡皮擦擦拭或软布测试无脱落;7.5.2.3直接成型无表面处理工艺(如喷漆、丝印、烤漆)工艺无需测试。
7.5.3 耐酒精标准:符合图纸要求,原则上图纸必须注明表面处理是否需耐酒精,如图纸没有此要求一律按耐酒精处理,图纸特殊要求除外,其它需符合以下要求:通过耐酒精测试8.0检验方法8.1 ROHS检验查看来料出厂检验报告、供方ROSH声明、来料绿色ROHS标签、或ROHS检测报告,确认是否为ROHS来料。
8.2外观检验8.2.1参照图纸,确认包装及颜色符合要求,然后确认外观是否有缺陷,无缺陷判定合格,有缺陷使用塞规、针规或卡尺确定缺陷状况,同时参照7.2标准判定是否符合要求。
8.2.2缺陷说明8.2.2.1凸物:产品表面突出的部份。
8.2.2.2雾状:金属零件表面呈云雾状模糊、不清晰、不光亮现象。
8.2.2.3水印:电镀与氧化后不洁凈或氧化不力造成附着产品表面上的膜状或块状之杂物。
8.2.2.4发黄:氧化作业时,其表面药水未清洗干凈或无色铬酸盐作业时,其作业时间与作业方式不规范,产品表面呈现黄色印迹。
8.2.2.5异色:同一产品,其颜色与亮度在不同的部份,呈现出明显的差异,如孔边亮块。
8.2.2.6色差:产品表面颜色及亮度与标准颜色及亮度样本呈现明显差异或同批产品其表面颜色与亮度存在着明显差异。
8.2.2.7凹坑:因基体材料表面本身缺陷或由于加工过程中造成材料表面出现凹陷弹丸状的缺陷,如压伤等。
8.2.2.8刮伤:硬质或尖锐物体划过产品而形成的有手感的线状浅沟。
8.2.2.9刮、擦花:表面之间或产品与其它异物相互接触,引起磨损或磨擦而造成的无手感表面缺陷。
8.2.2.10基材花料:电镀或氧化前因基体材料腐蚀;或者材料中的杂质;或材料微孔等原因所造成的,与周围材质表面不同光泽或粗糙度的花纹外观。
8.2.2.11砂眼、斑点:因基体材料本身存在着汽泡、杂质等原因,氧化后,产品表面出现针孔状小孔,因氧化、喷砂不良造成产品表面呈现斑状小点。
8.2.2.12缺角:同基材本身缺陷或加工过程中相互碰撞造成棱角边碰坏的不良现象。
8.2.2.13裂纹:产品基材断裂或其表面氧化皮膜龟裂,所呈现的线状纹路。
8.2.2.14露白:因氧化挂具装卸产品不当或产品相互碰撞、摩擦,造成表面氧化膜脱落,现露基材本色之状况。
8.2.2.15烧伤:拉丝处理时,操作不当造成零件表面过热而留下之烧蚀痕迹。
8.2.2.16手印:因人员操作时用手直接触摸产品而在产品表面留下的印迹。
8.2.2.17腐蚀:因产品在碱腐蚀中,表面产生大量黑点及白点状斑点。
8.2.2.18晶粒:产品在氧化过程中产生的雪花状斑点。
8.2.2.19聚油:产品在喷漆过程中,孔或框边缘,漆聚集。
8.2.2.20披锋:加工过程中边角及孔位边所残留的铝屑。
8.2.2.21变形:目视散热器齿的弯曲。
8.2.2.22水口不平:进胶口位没有修整,高出正常平面,系人为因素造成。
8.2.2.23缺料:由于注塑机压力过低,打出的制品出现不完整或缺胶的现象,很薄的壁出现。
8.2.2.24工艺角清理不净:由于加工过程导致一些不能加工的角无法清理干净。
8.2.2.25手工打磨:机加无法加工,然后通过手工打磨达到的形状。
8.2.2.26预埋件松动:手板中的预埋件(螺母、螺柱等)等嵌入零件主体中容易松动,甚至脱落等情况。
8.3尺寸检验参照图纸要求,使用卡尺、直尺及针规量测重要尺寸及全尺寸8.4特殊性能检验8.4.1阻燃性能检验(适用于硅胶、橡胶、塑料等手板件)取一小片手板样品(直径6cm左右),放入酒精灯上,样品点燃后移开酒精灯如6秒内火焰熄灭符合阻燃测试要求。
8.4.2附着力检验(根据图纸要求是否进行此项试验)8.4.2.1百格测试取产品烤漆表面(最好为B级面或C级面)或色板样品上,用用美工刀纵横各划出11条划线,划线长度约为20MM,深度以划破漆层为宜。
用毛刷将划线边缘的漆层粉末或丝状物清除干净。
准备好长度约为75MM的3M 胶带,将3M胶带的一端从百格的最边缘,慢慢平贴在百格上面,然后用手指轻轻触压,确保胶带与色板(或产品)之间无残留气泡,压平后,等待90±30秒,然后左手压住色板(或产品),右手捏住胶带的自由端,反方向约180度迅速撕除3M胶带。
使用放大镜,仔细检查百格上涂层的脱落情况。
8.4.2.2橡皮擦测试/软布测试取产品喷漆或喷油表面(最好为B级面或C级面)或色板样品上,使用橡皮擦或软布均匀用力(约0.5kgn 力)反复擦拭20次,用干净软布清洁表面后检查喷漆或喷油是否有严重脱落。
8.4.3耐酒精测试(根据图纸要求是否进行此项试验)用2层棉纱布裹住500g的砝码上,将酒精滴在棉纱布上,使沙布充分吸收酒精,以不流出酒精为宜,以2秒/来回一次的速度在60mm长度范围内来回擦拭50次;(棱角弧面为20次),测试面无油漆脱落,无印油褪色。
注:如无500g砝码可用同等重量的无棱角面物体代替。
8.5 记录检验完成后将检验状况做好相关记录(P08-03YA 物料入厂检验报告)。
9.0 注意事项9.1 取出放回时请注意保护手板件表面,遵从轻拿轻放原则,如需其它工具(如刀片)打开包装时请注意防止工具刮伤。
9.2 外观检查前需先确认包装是否符合要求,如包装不符合要求可判定不合格。
9.3 外观检查时先用软布将表面擦拭干净后方可开始检查,如批量表面未做清洁可判定不合格。
9.4 附着力测试时优先按照色板样品、产品C级面、B级面、A级面取样,取样只取一次,如取产品测试,测试完后的产品需按照不合格品评审流程来评审测试样品。
9.5 耐酒精测试优先按照产品B级面、A级面、C级面取样、色板样品,取样只取一次,如非A级面测试时发现不符合要求需加测A级面测试。
9.6 外观检验时发现不合格,需抽检1pcs尺寸规格,判定尺寸是否符合规格要求。
9.7 返工产品再次检验时需完成所有检验。
(特殊性能检验按照正常抽检)10.0判定原则任何不符合7.0条例(检验标准)要求的均判定为不合格,按照不合格品程序处理,符合检验标准IQC办理允收动作。
特殊性能测试如发现不合格需追踪抽测未测试批次的特殊性能。