半导体材料和集成电路平面工艺基础
半导体工艺原理-集成电路制造工艺介绍

GND
Vi
T
Vo
R VDD
23
二)、MOS集成电路芯片制 造工艺
(N阱硅栅CMOS工艺)
24
1、CMOS工艺中的元器件结构
电阻
NSD和PSD电阻结构剖面图
25
多晶硅电阻结构剖面图
26
N阱电阻结构剖面图
27
电容
CMOS工艺中PMOS晶体管电容剖面图
28
CMOS工艺中N阱电容剖面图
29
多晶硅-多晶硅电容器剖面图
双极工艺主要分类
3
CMOS
●标准CMOS工艺(数字电路的主流工艺 技术)特点:互补的NMOS、PMOS,工 艺流程简单,集成度高
●模拟CMOS工艺(应用最广泛的模拟IC 工艺)特点:在标准CMOS的基础上集成 高品质的无源器件,此外对阈值电压精度 和耐压的要求更高
●RF CMOS(RF IC) 特点:依靠缩小光刻尺寸提高MOS晶体管 的速度,集成模拟IC所必需的高品质无源 器件
30
二极管
PSD/N阱齐纳二极管剖面图
31
PSD保护环肖特基二极管剖面图
32
MOS晶体管
N阱CMOS工艺中MOS晶体管剖面图
33
P阱CMOS工艺中MOS晶体管剖面图
34
双阱CMOS工艺中MOS晶体管剖面图
35
2、主要工艺流程图
36
衬底准备
P型单晶片
P+/P外延片
37
工艺流程:
氧化、光刻N-阱(nwell)
NBL
NSINK
P阱
PBL
57
●BCD(智能功率集成芯片) 特点:在BiCMOS优势的基础上再集成 DMOS等功率器件,是智能功率芯片的理 想工艺平台
集成电路的制作工艺和质量检测

集成电路的制作工艺和质量检测我们在日常工作中有接触的是以硅平面为工艺基础的半导体集成电路。
其制造过程大体可分为三个阶段。
第一阶段:加工制作集成电路用的基片。
第二阶段:是在基片上按平面工艺流程制作集成电路所需的元器件及其相互连线。
第三阶段:将制成的集成电路基片经过初测,筛选,划片,分成一块一块的集成电路芯片。
然后将合格的芯片烧结在管座上,焊上引线,再封装,老化,总测,分档等工序,成为产品。
我们公司主要做第二阶段。
集成芯片制作的基本工艺按照硅平面工艺,集成电路芯片的各个元器件及其相互间的连线都是在统一的工艺流程中,一步步制成。
而这一流程是右一些基本工艺按制作晶体管的顺序编制而成。
1.外延生长工艺:一般是指在一块衬底上生长一层导体单晶或多晶硅。
它是实现元气件相互隔离的一道重要工序,同时解决了高频晶体管C结击穿电压与集电区体电阻对材料电阻率要求的矛盾。
2.氧化工艺:是要在硅表面生成二氧化硅作为介质。
它可以扩散时对杂质起掩蔽作用。
起绝缘作用,如元器件之间隔绝的绝缘层。
对集成芯片上元器件的表面起保护作用等。
3.光刻工艺:是一种微细的加工工艺。
其利用光敏抗蚀层的光化学反应和蚀刻技术可以在二氧化硅薄膜上精确地刻制出所需要的扩散图形以及元器件相互连接的布线图形。
随着集成电路的不断提高,要求芯片上元器件的尺寸越来越小,这样对光刻工艺提出了更高的要求。
目前发展的超微细加工技术,从光源,曝光方式,感光胶配方,蚀刻方法等诸多方面做了大量改进,从而使最小线宽达到了亚微米的水平。
4.扩散工艺:就是在高温下将杂质原子掺入硅片表层,形成不同电阻率的杂质半导体。
根据集成电路图,在规定的区域并选定适当的杂质进行扩散,就可制成隔离PN结、二极管、三极管、及扩散电阻等。
因此可以说,集成电路的基本结构是通过扩散来实现的。
在扩散中为了达到一定的表面杂质浓度和扩散的深度,可以采用恒定源扩散和限定源扩散这两种。
相比之下限定源扩散既能控制硅表面浓度,又能控制扩散深度。
半导体工艺第一章
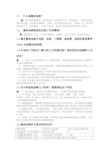
1-1什么是集成电路?解:集成电路是通过一系列特定的平面制造工艺,将晶体管、二极管等有源器件和电阻、电容等无源器件,按照一定的电路互联关系,“集成”在一块半导体单晶片上,冰封装在一个保护外壳内,能执行特定功能的复杂电子系统。
1-2集成电路制造的主要工艺有哪些?解:重复清洗、氧化、化学气相淀积、金属化、光刻、刻蚀、掺杂和平坦化。
1-3画出集成电路中电阻、电容、二极管、晶体管、场效应晶体管和CMOS反相器的结构图。
1-4半导体工艺经历了哪几种工艺发展过程?现在采用的是哪种工艺技术?解:(1)1952年肖克莱发明了生产型晶体管,其特点是在晶体管生长过程中形成NPN型晶体管。
(2)同年萨拜提出了合金结型晶体管,其原理是将铟球放置在锗片的两边,在高温下溶解锗而形成两个PN结。
(3)1954年贝尔实验室提出了采用气相扩散方法形成台面型结型晶体管。
(4)1960年,硅平面结型晶体管的发明;(5)1954年库尔特提出了用PN结来隔离集成电路中的各个晶体管和其他元件。
(6)1959年仙童公司的罗伯特提出了用平面工艺来制作硅集成电路。
现在采用的是硅平面工艺技术;1-5芯片制造包括哪几个阶段?简要描述各个阶段。
解:(1)硅片制备;将硅从沙中提炼并纯化,形成半导体级硅的多晶硅。
(2)芯片制造;硅片到达硅片制造厂,经过清洗、成膜、光刻、刻蚀、和掺杂(扩散、离子注入)等主要工艺之后,加工成的硅片具有永久刻蚀在硅片上的完整的集成电流。
(3)掩膜板制作;掩膜版中包括构成芯片的各层图形结构,现在最常用的掩膜版技术是石英玻璃涂敷,在石英玻璃掩膜版表面的洛层上形成芯片各层结构图形。
(4)装配与封装;芯片制造完成后,封装之前芯片要经过测试/挑选进行单个芯片的电学测试,拣选出合格芯片和不合格芯片,并作出标识,合格芯片包装在保护壳内。
(5)终测;为了确保芯片的功能,要对每个被封装的集成电路进行测试,以保障芯片的电学和环境特性参数满足要求。
集成电路基础

第四节 集成电路的生产过程
一、集成电路制造过程 1、示意图: 设 计 掩模板 单晶 材料
芯片 制造
装 配
检 测
图2-1集成电路制造过程示意图
二、平面工艺技术框图
图象转移
生成 保护 膜
确定 工作 窗口
开设 窗口
渗入 杂质
图2-2
平面工艺基本框图
二、典型双极工艺制造过程 (以PN结隔离技术)
1. 双极NPN晶体管的截面图
二、集成电路的优点及主要性能
优点:体积小、能耗低、价廉、性能好。
集成度:每块集成电路芯片中包含的元器件数目 优值(功耗延迟积):是指电路的延迟时间与功 耗相乘。
特征尺寸:通常是指集成电路中半导体器件的最 小尺度。
第二节 集成电路的分类
一、按结构分:
1、单片集成电路: 双极型: NPN PNP 速度快、驱动能力、 功耗大、 成度低 MOS型:PMOS、NMOS、CMOS能耗低、 输入阻抗、高抗干扰强、集成度高 BiMOS型:兼有二者优点,但工艺复杂
集成电路设计基础
BASIC IC DESIGN
本课程的主要内容及要求
一、本课程的教学目的 1、掌握有关集成电路设计和生产过程中的 基本概念; 2、对集成电路的设计、生产过程的基本知 识有一个比较系统、全面的了解和认识; 3、熟悉集成电路的设计方法及常用电路组 件的功能分析、设计和应用;
4、学习利用CAD工具PSPICE进行器件级 的模拟电路设计; 5、学习基于在系统可编程技术的系统 级的数字集成电路设计。 二、主要内容及要求 1、了解集成电路的生产过程,主要是芯 片加工工艺,结合一种典型的集成加工工艺 过程,对各种工序在整个工艺流程中的作用 和意义有全局性的认识,并掌握一些重要工 艺的概念和作用,安排在第二章集成电路制 造工艺中介绍。
半导体集成电路第4章版图设计与举例课件

计线宽。 前者表示所能达到的工艺水平,后者表示保
证一定成品率前提下所能达到的工艺水平。 最小掩模线宽可根据实际的工艺确定。 对TTL一般4~10um
•半导体集成电路第4章版图设计与举例
•10
二、掩膜图形最小间距
版图设计时,版图上各相邻图形间的 最小间距。 显然,制作到Si平面时,图形的实际位置将与
•
设计中常用BC短•半接导体及集成单电路第独4章B版图C设计结与举两例 种结构。
•25
二、SBD
SBD在集成电路中可作为二极管独立使
用,也可以与晶体管组合构成抗饱和晶体管。
1、SBD版图设计考虑
要求:面积小 ,减小结电容;
串连电阻小,提高钳位效果;
反向击穿电压高。
在设计中,由于rSBD 与结电容的要求相
•
△WMAT-2-0.8xjc+Wdc-B+Gmin
7、DB-I 基区窗口到隔离窗口间距
•
△WMAT+0.8xjc-0.8xjI+Wdc-c+WdI-C+Gmin
•
XjI~125%Wepi-MAX
8、Dc-B n+集电极窗口到基区窗口间距
△WMAT+0.8xjc+0.8xje+Wdc-c+Gmin
9.Wc孔 集电极n+孔宽
目的:实现电路中各个元件的电隔离
规则:
1、集电极等电位的NPN管可共用一个隔离区(基极
等电位的PNP管可共用一个隔离区)
2、二极管按晶体管原则处理。
3、原则上,所有硼扩散电阻可共用同一隔离区。
4、当集电极电位高于硼扩散电阻的电位时,晶体管
平面工艺简介

平⾯⼯艺简介平⾯⼯艺简介关于平⾯⼯艺以及⽤这种⼯艺制造的半导体器件的介绍始于1960年,从此,平⾯⼯艺就成为制造半导体器件合集成电路的主要⽅法,它对半导体器件迅速取代⼀些较⽼的电⼦学元件,并深⼊到电⼦学应⽤的崭新领域做出了重要贡献。
象⼤多数重要的⼯艺进展⼀样,平⾯⼯艺也是从前⼏代⼯艺中脱胎出来的。
因此,叙述平⾯⼯艺的发展过程及其基本原理的最好⽅法是将它和两种最重要的早期半导体器件制造⽅法--⽣长结⽅法和合⾦⽅法作⼀个⽐较。
1.⽣长结⽅法半导体单晶是由掺有某种杂质的半导体熔液⽣长出来的(例如P型)。
在⽣长过程中的某⼀时刻,突然改变熔液的导电类型。
(例如,投⼊⼀颗含有施主杂质的⼩球,结果,单晶的其余部分长成N型的。
)⽣长完成以后,把晶体切成含有P--N结的⼩条。
结型晶体管发明之后的头⼏年,这个⽅法是极其重要的,但从⼤批量⽣产的⾓度来看,⽣长结⽅法还不如早期半导体器件⼯艺中提出的另⼀种⽅法--合⾦结⽅法。
图1 ⽣长结⽅法⽰意图2.合⾦结⽅法将⼀个含有受主型杂质(以此为例)的⼩球放在⼀个n型半导体⽚⼦上。
然后将它们⼀起加热到⾜够⾼的温度,使⼩球以融解或合⾦的形式掺⼊半导体⽚⼦,晶体冷却之后,⼩球下⾯形成⼀个受主型杂质饱和的再分布结晶区,这样就得到了⼀个P--N结。
这种⽅法过去是,⽽且现在仍然是⼆极管和晶体管(主要是锗器件)的⼤批量⽣产中使⽤的⼀种成功的⽅法。
然⽽,随着半导体器件的应⽤范围愈来愈⼴泛,对其性能的要求也⼤⼤提⾼了。
在这些⽇益提⾼的要求⾯前,合⾦⽅法很快就暴露了其固有的局限性。
例如,结的位置总是难以控制的。
图2 合⾦结⽅法⽰意图3.平⾯⼯艺为了探索⼀种能够精确控制P -N 结位置的⽅法,导致了扩散结的发展。
扩散结的形成⽅式与合⾦过程有其相似之处,即⽚⼦的表⾯是暴露于包括在例如⽓体中的相反类型的⾼浓度杂质源之中。
不过,在这种情况下不发⽣相变;杂质靠固态扩散进⼊半导体晶体内部,⽽固态扩散能够⾮常精确地加以控制。
《微电子与集成电路设计导论》第四章 半导体集成电路制造工艺

4.4.2 离子注入
图4.4.6 离子注入系统的原理示意图
图4.4.7 离子注入的高斯分布示意图
4.5 制技术 4.5.1 氧化
1. 二氧化硅的结构、性质和用途
图4.5.1 二氧化硅原子结构示意图
氧化物的主要作用: ➢ 器件介质层 ➢ 电学隔离层 ➢ 器件和栅氧的保护层 ➢ 表面钝化层 ➢ 掺杂阻挡层
F D C x
C为单位体积掺杂浓度,
C x
为x方向上的浓度梯度。
比例常数D为扩散系数,它是描述杂质在半导体中运动快慢的物理量, 它与扩散温度、杂质类型、衬底材料等有关;x为深度。
左下图所示如果硅片表面的杂质浓 度CS在整个扩散过程中始终不变, 这种方式称为恒定表面源扩散。
图4.4.1 扩散的方式
自然界中硅的含量 极为丰富,但不能 直接拿来用。因为 硅在自然界中都是 以化合物的形式存 在的。
图4.1.2 拉晶仪结构示意图
左图为在一个可抽真空的腔室内 置放一个由熔融石英制成的坩埚 ,调节好坩埚的位置,腔室回充 保护性气氛,将坩埚加热至 1500°C左右。化学方法蚀刻的籽 晶置于熔硅上方,然后降下来与 多晶熔料相接触。籽晶必须是严 格定向生长形成硅锭。
涂胶工艺的目的就是在晶圆表面建立薄的、均匀的、并且没有缺陷的光刻胶膜。
图4.2.4 动态旋转喷洒光刻胶示意图
3. 前烘
前烘是将光刻胶中的一部分溶剂蒸发掉。使光刻胶中溶剂缓慢、充分地挥发掉, 保持光刻胶干燥。
4. 对准和曝光
对准和曝光是把掩膜版上的图形转移到光刻胶上的关键步骤。
图4.2.5 光刻技术的示意图
图4.2.7 制版工艺流程
4.3 刻蚀
(1)湿法腐蚀
(2)干法腐蚀 ➢ 等离子体腐蚀 ➢ 溅射刻蚀 ➢ 反应离子刻蚀
半导体集成电路概述

,
这里考虑到 R 1 R 2
,因此,比值 R1 可精确控制。
R2
故集成电路中常设计使它的关键性能依赖两个电阻之
比,而不依赖任何一个特定的电阻值。
(2)一般把阻值较大的集成电阻器设计成 右图的蛇形图形,便可达到减少总面 积目的。拐角处电流流动不均匀,一 般认为拐角处方块电阻为直线上阻值的65%。
(3)若扩散电阻宽度 W 很小,也即 W ~ x j,需考虑到横向 扩散影响,并以实际有效宽度 W’ 代替窗口宽度 W 。
① 衬底结易击穿 ② 衬底结电容增大
[ 说明 ]
(选择好浓度)
①
1 VD 2 WEm
Em
2 VD W
②
寄生结电容
CT
W
3. 集成电路中存在寄生效应 集成电路中存在寄生效应,一般是寄生结电容(包括隔离
结电容等),这是集成电路工艺的特点之五,影响了集成器件 的高频性能。 二、集成晶体管常规工艺流程(以 n pn 晶体管为例)
改善措施
增添 n 埋层
(抑制)
五、集成电路晶体管的图形结构( n pn ) 单基极条形 基区、集电区电阻大,注入及收集效率低。 改善措施 ① 减少基区和集电区电阻 ② 提高集电极收集效率以及发射极注入效率
改进结构
单基极条形
双基极条形
马蹄形
减少基区电阻
集电极提高收集效率
梳形
提高发射极注入效率
发射极马蹄形
O2 直接与Si表面接触,SiO2 生长速率
受到 Si/SiO2 界面处的反 应速率限制。
氧化物厚度 dox与氧化时间 t 满足线性关系:
dox
B (t A
)
式中 为系统装置的初始化参数,A、B为与氧化温度有关的系数
半导体器件工艺基础知识

半导体器件⼯艺基础知识半导体基础知识和半导体器件⼯艺第⼀章半导体基础知识 通常物质根据其导电性能不同可分成三类。
第⼀类为导体,它可以很好的传导电流,如:⾦属类,铜、银、铝、⾦等;电解液类:NaCl⽔溶液,⾎液,普通⽔等以及其它⼀些物体。
第⼆类为绝缘体,电流不能通过,如橡胶、玻璃、陶瓷、⽊板等。
第三类为半导体,其导电能⼒介于导体和绝缘体之间,如四族元素Ge锗、Si硅等,三、五族元素的化合物GaAs砷化镓等,⼆、六族元素的化合物氧化物、硫化物等。
物体的导电能⼒可以⽤电阻率来表⽰。
电阻率定义为长1厘⽶、截⾯积为1平⽅厘⽶的物质的电阻值,单位为欧姆*厘⽶。
电阻率越⼩说明该物质的导电性能越好。
通常导体的电阻率在10-4欧姆*厘⽶以下,绝缘体的电阻率在109欧姆*厘⽶以上。
半导体的性质既不象⼀般的导体,也不同于普通的绝缘体,同时也不仅仅由于它的导电能⼒介于导体和绝缘体之间,⽽是由于半导体具有以下的特殊性质:(1) 温度的变化能显著的改变半导体的导电能⼒。
当温度升⾼时,电阻率会降低。
⽐如Si在200℃时电阻率⽐室温时的电阻率低⼏千倍。
可以利⽤半导体的这个特性制成⾃动控制⽤的热敏组件(如热敏电阻等),但是由于半导体的这⼀特性,容易引起热不稳定性,在制作半导体器件时需要考虑器件⾃⾝产⽣的热量,需要考虑器件使⽤环境的温度等,考虑如何散热,否则将导致器件失效、报废。
(2) 半导体在受到外界光照的作⽤是导电能⼒⼤⼤提⾼。
如硫化镉受到光照后导电能⼒可提⾼⼏⼗到⼏百倍,利⽤这⼀特点,可制成光敏三极管、光敏电阻等。
(3) 在纯净的半导体中加⼊微量(千万分之⼀)的其它元素(这个过程我们称为掺杂),可使他的导电能⼒提⾼百万倍。
这是半导体的最初的特征。
例如在原⼦密度为5*1022/cm3的硅中掺进⼤约5X1015/cm3磷原⼦,⽐例为10-7(即千万分之⼀),硅的导电能⼒提⾼了⼏⼗万倍。
物质是由原⼦构成的,⽽原⼦是由原⼦核和围绕它运动的电⼦组成的。
001 集成电路的基本制造工艺

0
Rp
深度 X
Rp:平均浓度 p:穿透深度的标准差 Nmax=0.4NT/ p NT:单位面积注入的离子数,即离子注入剂量
离子注入的分布有以下两个特点: 1.离子注入的分布曲线形状(Rp,б p),只与 离子的初始能量E0有关。并杂质浓度最大的地方 不是在硅的表面,X=0处,而是在X=Rp处。
AL
离子束
wafer
2、淀积多晶硅
淀积多晶硅一般采用化学汽相淀积(LPCVD)的方法。 利用化学反应在硅片上生长多晶硅薄膜。 适当控制压力、温度并引入反应的蒸汽,经过足够长的 时间,便可在硅表面淀积一层高纯度的多晶硅。
采用 SiH 4 在700°C的高温下,使其分解:
C 700 SiH4 Si 2 H 2 ~
7 第五次光刻-引线接触孔光刻
8 第六次光刻-金属化内连线光刻
主要工序:
衬底选择 基区
隐埋层
外延 隔离
发射区
引线孔 铝
1、衬底选择 1)导电类型:一般选用P型 2)电阻率选择:为提高击穿电压而又不使外延层 在后续工艺中下推太多,衬底电阻率一般选
10 cm
3)晶向:为减少外延层缺陷,选用(111)晶向, 稍偏2到5度。
二是在制作Mask上下功夫,并带有Mask的
修正功能,可通过检测Mask上的缺陷,调整 曝光过程。
第四节 CMOS集成电路加工过程简介
一、硅片制备 二、前部工序
Mask 掩膜版
CHIP
掩膜1: P阱光刻
P-well Si-衬底
具体步骤如下: 1.生长二氧化硅:
SiO2
Si-衬底
2.P阱光刻: 涂胶、掩膜对准、曝光、显影、刻蚀 3.去胶 4.掺杂:掺入B元素
半导体工艺知识

第一章工艺和器件发展概述1947年第一只具有放大作用的点接触晶体管问世,与电子管相比具有很多优点,引起人们广泛注意,在随后的十几年时间相继发明了各式各样晶体管(合金管、合金扩散管、台面管等)。
1960年硅平面工艺和外延技术的出现,使半导器件的制造工艺获得重大突破。
它为集成电路的制造开拓了广阔的途径,促进了半导体器件进一步向微型化、低功耗和高可靠性方向发展。
集成度由SSI、MSI、LSI、VLSI步入了ULSI时代。
1957年第一只SCR问世以来功率器件也取得了长足的进步,相继推出了GTO(可关断晶闸管)TRIAC(双向晶闸管)和GTR(达林顿功率晶体管)这些都是双极型器件,它们共同优点是功率容量大,导通电阻小,缺点是存在少子贮存效应,开关速度低,电流驱动,驱动功率大,不易控制,七十年末由IR和GE公司发明了单极型功率器件功率MOSFET,立即受到制造厂和用户的重视。
三年后西方15家大公司均掌握了功率MOSFET生产技术(VDMOS),1983年诞生了IGBT双极型器件。
半导体器件种类繁多,工艺有别,本次培训主要以外延平面工艺为主,介绍以下内容:单晶硅拉制及衬底制备、外延工艺、氧化工艺、扩散与离子注入工艺、光刻工艺、蒸发工艺、芯片组装工艺。
一、锗合金扩散晶体管制造工艺流程简介合金扩散晶体管是五十年代中期发展起来的一种高频管。
工艺流程:切片→研磨、抛光、腐蚀→扩散(Sb扩)→装发射极(In合金)→真空烧结(500~550℃)→装基极及支架→烧结(H2)→点焊管座→拉丝→涂保护油→台面腐蚀→去油清洗→管芯腐蚀→烘干→涂胶→封管二、硅外延平面晶体管制造工艺流程(NPN型)三、集成电路制造工艺流程原始硅片 P型(衬底) ρ:8-13Ω·cm 晶面(111)比平面晶体管多出工艺隐埋(埋层)扩散,隔离扩散。
四、肖特基二极管芯工艺工艺势垒金属结温 VF IRVR标准工艺 Mo-Si化合物 150℃低适中≤60V830工艺 Pd-Si化合物+Mo 175℃高低≤200VCr Cr-Si化合物+Mo 125℃很低高≤45VV V-Si化合物 100℃极低很高≤45V 管芯工艺流程见附图五、IGBT工艺流程 IGBT、MOSFET芯片结构详见附图第二章单晶拉制与衬底制备半导体单晶是制造半导体器件的基础材料,它的质量好坏直接影响到半导体器件的性能。
半导体集成电路工艺流程

集成电路制造工艺流程晶体的生长晶体切片成wafer晶圆制作功能设计à模块设计à电路设计à版图设计à制作光罩工艺流程1) 表面清洗晶圆表面附着一层大约 2um 的 Al2O3 和甘油混合液保护之 , 在制作前必须进行化学刻蚀和表面清洗。
2) 初次氧化有热氧化法生成 SiO2 缓冲层,用来减小后续中 Si3N4 对晶圆的应力氧化技术干法氧化Si( 固 ) + O2 = SiO2( 固 )湿法氧化Si( 固 ) +2H2O =SiO2( 固 ) + 2H2干法氧化通常用来形成,栅极二氧化硅膜,要求薄,界面能级和固定电荷密度低的薄膜。
干法氧化成膜速度慢于湿法。
湿法氧化通常用来形成作为器件隔离用的比较厚的二氧化硅膜。
当 SiO2 膜较薄时,膜厚与时间成正比。
SiO2 膜变厚时,膜厚与时间的平方根成正比。
因而,要形成较厚的 SiO2 膜,需要较长的氧化时间。
SiO2 膜形成的速度取决于经扩散穿过 SiO2 膜到达硅表面的 O2 及 OH 基等氧化剂的数量的多少。
湿法氧化时,因在于 OH 基在 SiO2 膜中的扩散系数比 O2 的大。
氧化反应, Si 表面向深层移动,距离为 SiO2 膜厚的 0.44 倍。
因此,不同厚度的 SiO2 膜,去除后的 Si 表面的深度也不同。
SiO2 膜为透明,通过光干涉来估计膜的厚度。
这种干涉色的周期约为 200nm ,如果预告知道是几次干涉,就能正确估计。
对其他的透明薄膜,如知道其折射率,也可用公式计算出(d SiO2) / (d ox) = (n ox) / (n SiO2) 。
SiO2 膜很薄时,看不到干涉色,但可利用 Si 的疏水性和 SiO2 的亲水性来判断 SiO2 膜是否存在。
也可用干涉膜计或椭圆仪等测出。
SiO2 和 Si 界面能级密度和固定电荷密度可由 MOS 二极管的电容特性求得。
(100) 面的 Si 的界面能级密度最低,约为 10E+10 -- 10E+11/cm – 2 .e V -1 数量级。
半导体集成电路
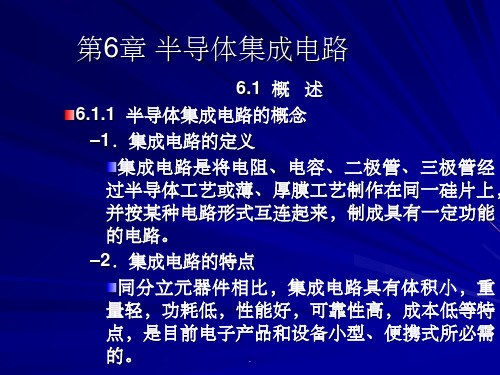
(2) 国产TTL电路分类
T1000:标准系列,相当于国际54/75系列 T2000:高速系列,相当于国际54/74H高速系 列 T3000:肖特基系列,相当于国际54/74S肖特 基系列 T4000 : 低功 耗 肖特 基 系列 , 相当 于 国际 54 / 74LS低功耗肖特基系列 T000可分为T000中速系列和T000高速系列 T000中速系列的性能类同于T1000系列 T000高速系列的性能类同于. T2000系列
6.3 各类集成电路的性能比较
6.3.1 TTL集成电路 TTL集成电路的全名称 是晶体管—晶体管逻 辑集成电路。它由 NPN或PNP型晶体管 组成。
.
1.TTL集成电路的分类
(1) 国际通用标准TTL集成电路的分类
– 54/74系列TTL数字逻辑集成电路一般分为六大 类:
– 54/74XX:标准TTL电路系列 – 54/74SXX:肖特基TLL电路系列 – 54/74HXX:高速TTL电路系列 – 54/74LSXX:低功耗肖特基TTL电路系列 – 54/74ASXX:先进肖特基TTL电路系列 – 54/74ALSXX:先进低功耗肖特基TTL电路系
单列直插式集成电路,识别其引脚时应 使引脚向下,面对型号或定位标记,自 定位标记对应一侧的第一只引脚数起, 依次为①,②,③,④……。此类集成 电路上的定位标记一般为色点、凹坑、 小孔、线条、色带、缺角等。
.
有些厂家生产的集成电路,本是同一种芯片,为了 便于在印制电路板上灵活安装,其引脚排列顺序对 称相反。一种按常规排列,即由左向右,另一种则 由右向左。对此类集成电路若封装上有识别标记, 可按上述规律分清其近脚顺序。但也有少数器件上 没有引脚识别标记,这时应从其型号上加以区别。 若其型号后缀中有一字母R,则表明其引脚顺序为 从右到左反向排列。 还有个别集成电路,设计时尾部引出脚为非等距排 列,作为标记。可按此特点来识别引脚顺序。
半导体工艺笔记

半导体工艺笔记全书主要内容:硅和硅片的制备、外延、热氧化、扩散、离子注入、化学气相沉积、物理气相沉积、光刻、刻蚀、封装。
一、绪论1.芯片制造工艺:由“硅片”到“集成电路结构晶圆”之间的工艺步骤。
2.硅平面工艺:主要有氧化,光刻,扩散掺杂,蒸镀金属四个基本单项工艺构成。
3.晶体管芯片工艺流程:外延、氧化、光刻、掺杂(扩散或离子注入)、金属化(CVD、PVD)5个单项工艺按照一定顺序排列构成的。
4.微电子工艺的特点(超净环境:不同的单项工艺要求的洁净室等级不同,光刻工艺要求的最高;超纯材料:半导体材料(硅、锗)、其他功能性电子材料(Al、Au等金属化材料、掺杂气体、外延用气体高纯度材料)及工艺消耗品(化学试剂是高纯度试剂、石英器皿等杂质低)超纯水等;批量复制(高可靠、高精度、低成本、适合批量化大生产的加工工艺))5.简答:微电子器件主要选用硅,因此硅作为常规半导体材料的优势是什么?(1)硅原料丰富:岩石、砂砾、尘土、水晶、玻璃。
(2)重量轻,密度只有2.33g/cm3。
(3)表面容易氧化。
(4)热学性能好,热膨胀系数小,热导率又高。
(5)工艺性能好。
(6)机械性能良好6.硅单晶的结构是:金刚石结构。
金刚石结构的立方体晶胞含有4*1内部+6*0.5面上+8*1/8角上=8个硅原子,*硅原子密度、*空间利用率。
7.硅器件与电路中常用的[晶向]和(晶面),晶向和晶面互相垂直。
常用的[晶向]:[111]、[110]、[100]常用的(晶面):(111)、(110)、(100)晶体管最常使用(111)晶面的晶片来制造,集成电路和器件常使用(110)晶面的晶片来制造、集成电路常采用(100)晶面的硅片来制造。
硅的双层密排面和解理面都是 (111)晶面。
常用晶面原子分布,用来计算原子面密度=原子数/晶面面积这个可以计算原子线密度=原子数/晶向长度8.缺陷与杂质:点缺陷,线缺陷,面缺陷,体缺陷点缺陷:空位、自填隙、杂质,杂质又有空位杂质和填隙杂质。
半导体器件与工艺基础

PNP
NPN
双极的含义:两种载流子导电。
半导体器件与工艺基础 (李翔宇) 32
BJT的典型应用
基区中的载流 子复合
与WB成反比
半导体器件与工艺基础 (李翔宇)
33
BJT特点
有与MOSFET类似的静态和动态行为 功耗高——有静态电流(基极电流) 尺寸缩小困难——主要性能有基区宽度 决定,但很难控制 输出功率高,驱动能力强 速度快,截止频率高
半导体器件与工艺基础 (李翔宇) 11
常见半导体
单质半导体:IV族元素 (硅、锗) 化合物半导体:GaAs,SiGe
Si Si Si
Si Si Si
Si Si Si
Si Si Si
Si
+
-
Si
产生电子-空穴对
Si Si
Si Si
半导体器件与工艺基础 (李翔宇)
12
载流子
自由电子和空穴在电场的作用下运动,形成电流 载流子(carrier):形成电流的自由电荷(电子、空 穴)
集成电路技术领域
技术领域
• • • • • • • 器件技术 工艺技术 电路技术 系统设计技术 封装技术 测试技术 设计自动化技术
主要指标
• 速度、功耗、可靠性、经济成本
半导体器件与工艺基础 (李翔宇) 9
•导体-半导体-绝缘体 •本征半导体和掺杂半导体
第二节
半导体
半导体器件与工艺基础 (李翔宇)
• • 电子运动方向与电流方向相反 空穴运动方向与电流方向相同
E -- - - - - - - - +++++++++
集成电路设计基础知识
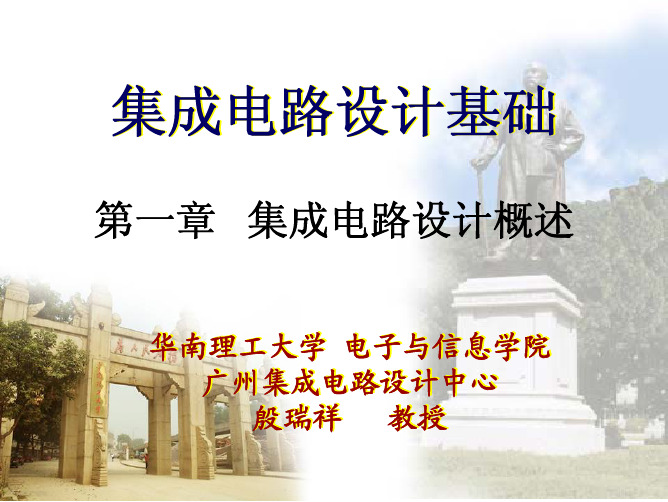
工艺加工
单片半导体材料
1.1 集成电路(IC)的发展
晶体管的发明
• 1946年1月,Bell实验室正式成立半导体研究小组: W. Schokley,J. Bardeen、W. H. Brattain • Bardeen提出了表面态理论, Schokley给出了实现 放大器的基本设想,Brattain设计了实验; • 1947年12月23日,第一次观测到了具有放大作用的 晶体管; • 1947年12月23日第一个点接触式NPN Ge晶体管 发明者: W. Schokley J. Bardeen W. Brattain
1.1 集成电路(IC)的发展
第一章 集成电路设计概述
1.2 当前国际集成电路 技术发展趋势
1.2 当前国际集成电路技术发展趋势 #1
关心工艺线
12 英 寸 (300mm) 0.09 微 米 是 目 前 量产最先进的 CMOS工艺线
1.2 当前国际集成电路技术发展趋势
1.2 当前国际集成电路技术发展趋势 #2
1.1 集成电路(IC)的发展
摩尔定律(Moore’s Law)
• Min. transistor feature size decreases by 0.7X every three years——True for at least 30 years! (Intel公司前董事长Gordon Moore首次于1965提出)
1.3
无生产线集成电路设计技术
Relation of F&F(无生产线与代工的关系)
Design kits
①
Foundry
Fabless
② Internet
Layout
半导体制造主要设备及工艺流程

半导体制造主要设备及⼯艺流程半导体产品的加⼯过程主要包括晶圆制造(前道,Front-End)和封装(后道,Back-End)测试,随着先进封装技术的渗透,出现介于晶圆制造和封装之间的加⼯环节,称为中道(Middle-End)。
由于半导体产品的加⼯⼯序多,所以在制造过程中需要⼤量的半导体设备和材料。
⼀、晶圆制造在这⾥,我们以最为复杂的晶圆制造(前道)和传统封装(后道)⼯艺为例,说明制造过程的所需要的设备和材料。
晶圆⽣产线可以分成7个独⽴的⽣产区域:扩散(Thermal Process)、光刻(Photo- lithography)、刻蚀(Etch)、离⼦注⼊(Ion Implant)、薄膜⽣长(Dielectric Deposition)、抛光(CMP)、⾦属化(Metalization)。
这7个主要的⽣产区和相关步骤以及测量等都是晶圆洁净⼚房进⾏的。
在这⼏个⽣产区都放置有若⼲种半导体设备,满⾜不同的需要。
例如在光刻区,除了光刻机之外,还会有配套的涂胶/显影和测量设备。
传统封装(后道)测试⼯艺可以⼤致分为背⾯减薄、晶圆切割、贴⽚、引线键合、模塑、电镀、切筋/成型和终测等8个主要步骤。
与IC晶圆制造(前道)相⽐,后道封装相对简单,技术难度较低,对⼯艺环境、设备和材料的要求远低于晶圆制造。
三、半导体⼯艺解析半导体制造⼯艺是集成电路实现的⼿段,也是集成电路设计的基础。
⾃从1948年晶体管发明以来,半导体器件⼯艺技术的发展经历了三个主要阶段:1950年采⽤合⾦法⼯艺,第⼀次⽣产出了实⽤化的合⾦结三极管;1955年扩散技术的采⽤是半导体器件制造技术的重⼤发展,为制造⾼频器件开辟了新途径;1960年平⾯⼯艺和外延技术的出现是半导体制造技术的重⼤变⾰,不但⼤幅度地提⾼了器件的频率、功率特性,改善了器件的稳定性和可靠性,⽽且也使半导体集成电路的⼯业化批量⽣产得以成为现实。
⽬前平⾯⼯艺仍然是半导体器件和集成电路⽣产的主流⼯艺。