抗阴极剥离型重防腐环氧涂料
管道用熔结环氧粉末涂层长效防腐的关键

管道用熔结环氧粉末涂层长效防腐的关键师立功【摘要】熔结环氧粉末涂料(FBE)具有优异的附着力和抗阴极剥离性能,已广泛应用于管道防腐的内外涂层.作为内防护涂层,其主要体现防腐与减阻的作用;而作为外防护涂层,则主要有单层FBE(SLFBE)涂层、双层FBE(DPS)涂层、三层FBE(3LFBE)涂层、三层挤塑(3PE)涂层、高性能复合(HPCC)涂层几种涂层形式,与阴极保护相结合可实现管道的长效防腐保护.本文结合防腐及阴极剥离机理,得出管道涂层长效防腐的关键是FBE涂层的交联密度、厚度及与基材的附着力.因此必须合理设计FBE 的配方,并按正确工艺涂装及固化,以保证FBE涂层的长效防腐.本文对未来FBE涂层的发展也进行了简单阐述.【期刊名称】《涂料工业》【年(卷),期】2017(047)002【总页数】8页(P73-80)【关键词】FBE;防腐;内外涂层;阴极保护;涂层寿命【作者】师立功【作者单位】北京汉森邦德科技有限公司,102600【正文语种】中文【中图分类】TQ637.82目前已有大量文献报道管道用熔结环氧粉末涂料的破坏机理或对涂层某一性能(如抗阴极剥离性能)的改进。
本文整理了管道内外防腐FBE的涂层形式,并结合腐蚀机理分析了FBE涂层的各项性能与FBE配方设计的关联性,总结了管道涂层长效防腐的关键因素。
熔结环氧粉末涂料(FBE)一般通过加热熔融固化粘接在金属底材上,所得涂层具有附着力优良、氧渗透率低、抗微生物腐蚀、无阴极屏蔽、坚硬耐磨、涂层表面光滑以及耐腐蚀性优异等特点,广泛用于输油管道、输气管道以及输水管道的内外防护,为处于各种环境中的管线提供了可靠的保障。
FBE涂层是将环氧粉末经180 ℃以上高温熔结固化在钢管上形成的具有一定厚度的防护层。
这种热固性交联涂层可与钢管以化学键方式牢固结合,涂层坚硬、光滑、耐化学腐蚀性优良,是目前世界上应用最广泛的管道防护手段之一。
作为管道的内防护层,FBE涂层既能有效防腐又安全卫生,输送流体流动阻力小,具有极大的优势;而其作为外防护层时,与阴极保护相配合也可为埋地管道提供长期有效地保护。
一、环氧系列防腐涂料

一、环氧系列防腐涂料一、简介随着现代工业的发展,一批新兴工业领域的出现和许多现代工程的兴建,对防腐涂料承受环境的能力和使用寿命提出了更高的要求。
常用的防腐涂料已不能满足这些需要。
人们提出的“重防腐涂料(Heavy Duty Coating)”的概念,一般指在苛刻的腐蚀环境使用,包括底漆和面漆的配套涂料。
简单地说:重防腐涂料就是使用寿命更长,可适应更苛刻的使用环境的涂料称为重防腐涂料。
在化工大气和海洋环境里重防腐涂料一般可使用10年或15年以上,在酸、碱、盐和溶剂介质里,并在一定温度的腐蚀条件下,一般应能使用5年以上。
重防腐涂料的应用涉及现代化各个领域,大型的工矿企业:化工、石油化工、钢铁及大型矿山冶炼的管道、贮槽、设备等;重要的能源工业:天然气、油管、油罐、输变电、核电设备及煤矿矿井等;现代化的交通运输:桥梁、船舶、集装箱、火车和汽车等;新兴的海洋工程:海上设施、海岸及海湾构造物及海上石油钻井平台等。
环氧树脂是由环氧氯丙烷和双酚A在碱催化下缩合而成的聚合物,随分子量的不同,可分为液体和固体环氧树脂。
以环氧树脂为主要成膜物质的涂料称为环氧涂料。
每年世界上约有40%以上的环氧树脂用于制造环氧涂料,其中大部分用于防腐领域。
环氧防腐涂料是目前世界上用得最为广泛、最为重要的重防腐涂料之一。
环氧树脂类防腐蚀涂料种类很多,大致可分为:胺固化环氧涂料、聚酰胺固化环氧涂料、胺加成物固化环氧涂料、环氧粉末涂料、环氧改性涂料。
二、环氧系列防腐涂料性能特点环氧系列涂料产品具有涂膜坚韧、耐磨、附着力好、耐化学腐蚀、耐强碱、耐水、耐溶剂、耐油等性能优异的特性,并有良好的绝缘性。
主要体现在以下几个方面:1、极好的附着力环氧树脂结构中含有不易水解的脂肪基(-C-)和醚键(-C-O-C-),能够产生电磁引力。
另外,在固化过程中活泼的环氧基和介质表面上的游离键起反应而形成牢固的化学键,从而使环氧树脂涂层获得极好的附着力。
2、优异的防腐蚀性能环氧树脂固化涂层,含有稳定的苯环、醚键等,结构致密,耐酸、耐碱、耐有机溶剂、耐水。
防腐工程常用的重防腐涂料有哪几种

对重防腐涂料的应用涉及现代化各个领域,大型的工矿企业:化工、石油化工、钢铁及大型矿山冶炼的管道、贮槽、设备等;重要的能源工业:天然气、油管、油罐、输变电、核电设备及煤矿矿井等;现代化的交通运输:桥梁、船舶、集装箱、火车和汽车等;新兴的海洋工程。
海上设施、海岸及海湾构造物及海上石油钻井平台等。
以环氧树脂为主要成膜物质的涂料称为环氧涂料。
每年世界上约有40%以上的环氧树脂用于制造环氧涂料,其中大部分用于防腐领域。
环氧防腐涂料是目前世界上用得最为广泛、最为重要的重防腐涂料之一。
管道补口技术与FBE及3LPE防腐层的适用性
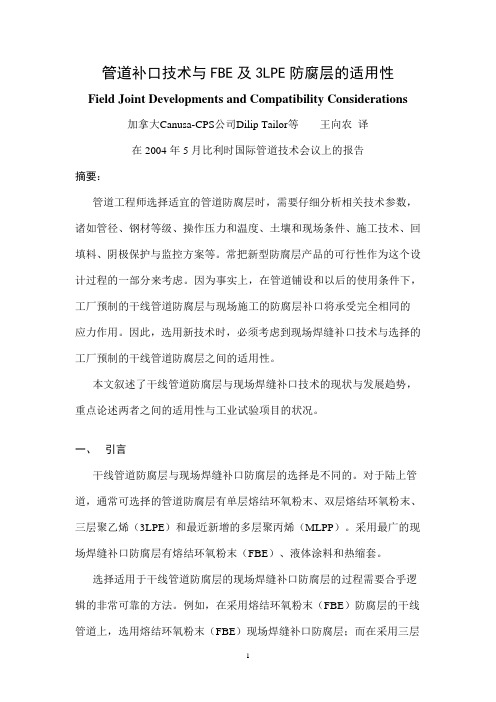
管道补口技术与FBE及3LPE防腐层的适用性Field Joint Developments and Compatibility Considerations 加拿大Canusa-CPS公司Dilip Tailor等王向农译在2004年5月比利时国际管道技术会议上的报告摘要:管道工程师选择适宜的管道防腐层时,需要仔细分析相关技术参数,诸如管径、钢材等级、操作压力和温度、土壤和现场条件、施工技术、回填料、阴极保护与监控方案等。
常把新型防腐层产品的可行性作为这个设计过程的一部分来考虑。
因为事实上,在管道铺设和以后的使用条件下,工厂预制的干线管道防腐层与现场施工的防腐层补口将承受完全相同的应力作用。
因此,选用新技术时,必须考虑到现场焊缝补口技术与选择的工厂预制的干线管道防腐层之间的适用性。
本文叙述了干线管道防腐层与现场焊缝补口技术的现状与发展趋势,重点论述两者之间的适用性与工业试验项目的状况。
一、引言干线管道防腐层与现场焊缝补口防腐层的选择是不同的。
对于陆上管道,通常可选择的管道防腐层有单层熔结环氧粉末、双层熔结环氧粉末、三层聚乙烯(3LPE)和最近新增的多层聚丙烯(MLPP)。
采用最广的现场焊缝补口防腐层有熔结环氧粉末(FBE)、液体涂料和热缩套。
选择适用于干线管道防腐层的现场焊缝补口防腐层的过程需要合乎逻辑的非常可靠的方法。
例如,在采用熔结环氧粉末(FBE)防腐层的干线管道上,选用熔结环氧粉末(FBE)现场焊缝补口防腐层;而在采用三层聚乙烯(3LPE)防腐层的干线管道上,选用三层热缩套作为现场焊缝补口防腐层,这样的选择就是比较合乎逻辑和比较可靠的。
本文讨论了不同区域防腐层的选择倾向,阐述了不同技术的优缺点,着重探讨了不同防腐技术之间的适用性。
人们已经在不同防腐技术之间的适用性方面做了大量研究,如由于环氧与聚乙烯基本极性的不同导致防腐层的附着力很差。
本文还探讨了模拟防腐层施工与使用条件下不同防腐技术之间的适用性研究。
防腐涂料的研究 - 中国涂料在线

防腐涂料的研究由于防腐涂料具有性能优异、制造方便、价格低廉等一些其它材料无法比拟的优点,因此在选择防腐措施时成为优先考虑的对象。
随着防腐技术的成熟,防腐涂料也必将得到进一步发展。
其中高固体分涂料因其可挥发成分少、固化速度快、施工性能好必将成为发展的趋势。
研究和分析了环氧树脂、聚氨酯等金属防腐涂料的特点,介绍了它们的最新发展动向。
金属的腐蚀,是金属受环境介质的化学或电化学作用而被破坏的现象。
金属的腐蚀遍及国民经济各个领域,给国民经济带来了巨大的损失。
在工业发达的国家中,腐蚀造成的直接经济损失占国民经济总产值的1%~4%,每年腐蚀生锈的钢铁约占产量的20%,约有30%的设备因腐蚀而报废。
在中国,由于金属腐蚀造成的经济损失每年高达300亿元以上,占国民生产总值的4%。
长期以来,人们一直采用多种技术对金属加以保护,防止腐蚀的发生。
其中,金属设备防腐蚀最有效、最常用的方法之一是在金属表面涂敷防腐蚀涂层,以隔绝腐蚀介质与金属基体。
防腐涂料和其它涂料一样,其配方组成主要包括基料(树脂)、颜填料和溶剂。
基料树脂是成膜物质,是涂料中的主要成分,它的分子结构决定着涂料的主要性能;颜填料是用来辅助隔离腐蚀因素的,根据作用机理又可分为防锈颜料和片状填料;溶剂分为有机溶剂或水,用来溶解基料树脂,便于成膜。
本文拟对常用金属防腐涂料的最新研究进展作一综述。
环氧树脂涂料环氧树脂是平均每个分子含有两个或两个以上环氧基的热固性树脂。
环氧树脂以其易于加工成型、固化物性能优异等特点而被广泛应用,通过环氧结构改性、环氧合金化、填充无机填料、膨胀单体改性等高性能化后可以制成防腐涂料。
环氧树脂涂料有优良的物理机械性能,最突出的是它对金属的附着力强;它的耐化学药品性和耐油性也很好,特别是耐碱性非常好。
环氧树脂涂料的主要成分是环氧树脂及其固化剂,辅助成分有颜料、填料等。
不锈钢粉末是最近几年发展起来的金属颜料,由于其具有不活泼性,特别是在高温强蚀环境中的防护性极好,所以既可用来作为主要颜料,也可作为复合颜料的一部分,与粘合剂组成防护性涂料。
双层环氧粉末防腐体系-石油工程建设

双层环氧粉末防腐体系
温慧芬 陈守平 霍兴立 (大庆建材公司防腐管道厂) 163712 黑龙江省大庆市
摘 要 报道双层环氧粉末 (FBE)防腐体系的涂层性能 、 涂敷工艺方法和特点 , 探讨了在
就一般涂层而言 , 同时使这些性能达到最佳状 标准的 FBE 涂层作底涂层 , 以改性的 FBE 涂
态是不可能的 , 依靠涂层来完全隔断水 、 氧等 腐蚀性因素也比较困难 。 而且 , 作BE 涂层防腐体系 , 进一步提高了涂层的机械性能 , 增强了涂层的
管道的防腐涂层 , 不仅需要有一般涂层的防腐 抗冲击能力 、 耐高温能力以及高温时的抗渗透
FBE 底涂层和改性的 FBE 面涂层组成 。双层 FBE 的涂敷工艺与标准的熔结 FBE 喷涂工艺
料相比 , F BE 涂层的渗水性略大 。
基本相同 , 只是在喷粉室和喷枪的布置上有所
为了完善这一涂层体系 , 欧洲防腐公司和 变化 , 不需增加复杂的设备 。
美国防腐公司采取了不同的方法 。 欧洲防腐公
我国推广应用的可能性 , 认为这种双层防腐体系在性能上完全达到了聚烯烃与 FBE 结合的三层
防护体系的性能 , 而且其施工应用更为简便 。
主题词 管道钢管 防腐 环氧树脂涂层 性能 应用
1 前言
系 ———三层作法 。由于聚烯烃为非极性材料 ,
在钢质管道的防腐蚀措施中 , 涂料防腐涂 实现聚乙烯或聚丙烯与 FBE 涂层的粘结比较
作用 , 同时又要承受一定高的工作温度 , 以减 性 。同时保持了单层 F BE 涂层与阴极保护的
少原油输送过程中的能源消耗 , 并要求有较好 相容性能 , 同样不会产生阴极保护屏蔽 。 美国
钢管三层PE特加强级防腐
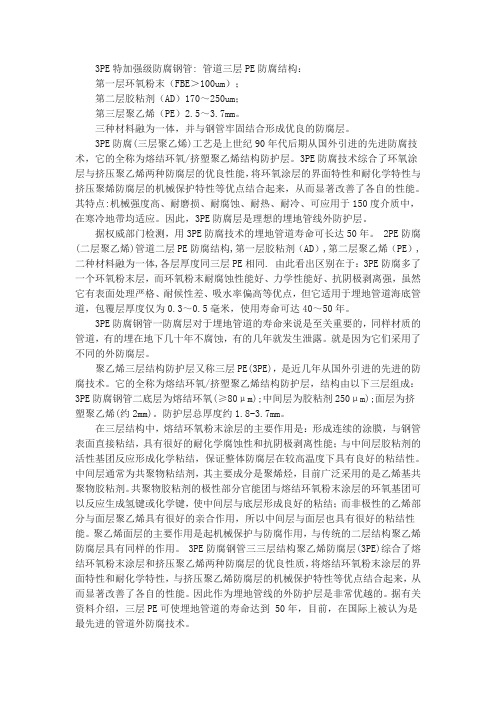
3PE特加强级防腐钢管: 管道三层PE防腐结构:第一层环氧粉末(FBE>100um);第二层胶粘剂(AD)170~250um;第三层聚乙烯(PE)2.5~3.7mm。
三种材料融为一体,并与钢管牢固结合形成优良的防腐层。
3PE防腐(三层聚乙烯)工艺是上世纪90年代后期从国外引进的先进防腐技术,它的全称为熔结环氧/挤塑聚乙烯结构防护层。
3PE防腐技术综合了环氧涂层与挤压聚乙烯两种防腐层的优良性能,将环氧涂层的界面特性和耐化学特性与挤压聚烯防腐层的机械保护特性等优点结合起来,从而显著改善了各自的性能。
其特点:机械强度高、耐磨损、耐腐蚀、耐热、耐冷、可应用于150度介质中,在寒冷地带均适应。
因此,3PE防腐层是理想的埋地管线外防护层。
据权威部门检测,用3PE防腐技术的埋地管道寿命可长达50年。
2PE防腐(二层聚乙烯)管道二层PE防腐结构,第一层胶粘剂(AD),第二层聚乙烯(PE),二种材料融为一体,各层厚度同三层PE相同. 由此看出区别在于:3PE防腐多了一个环氧粉末层,而环氧粉末耐腐蚀性能好、力学性能好、抗阴极剥离强,虽然它有表面处理严格、耐候性差、吸水率偏高等优点,但它适用于埋地管道海底管道,包覆层厚度仅为0.3~0.5毫米,使用寿命可达40~50年。
3PE防腐钢管一防腐层对于埋地管道的寿命来说是至关重要的,同样材质的管道,有的埋在地下几十年不腐蚀,有的几年就发生泄露。
就是因为它们采用了不同的外防腐层。
聚乙烯三层结构防护层又称三层PE(3PE),是近几年从国外引进的先进的防腐技术。
它的全称为熔结环氧/挤塑聚乙烯结构防护层,结构由以下三层组成:3PE防腐钢管二底层为熔结环氧(≥80μm);中间层为胶粘剂250μm);面层为挤塑聚乙烯(约2mm)。
防护层总厚度约1.8-3.7mm。
在三层结构中,熔结环氧粉末涂层的主要作用是:形成连续的涂膜,与钢管表面直接粘结,具有很好的耐化学腐蚀性和抗阴极剥离性能;与中间层胶粘剂的活性基团反应形成化学粘结,保证整体防腐层在较高温度下具有良好的粘结性。
无溶剂环氧防腐徐料性能的影响因素

文章编号 :10 - 6 6 2 1 ) 1 04 - 3 09 19 ( 0 2 0 - 0 10
㈣ i # # ¥| 蝴 ≈ ㈣ #辨 ∞ # 榭 鼎 ∞ # 嬲 | ¥¨ i t p 辨 螋 ∞* ¨ |
j
峥
无 溶 剂 环 氧 涂 料 以 低 黏 度 双 酚 F环 氧 树 脂 为 基 料, 添加 高 耐磨 颜 填 料 及 助 剂 等 ,以改 性 脂 肪 胺 、 硅 氧 烷 等 为 固化 剂 , 有 厚 涂 、固化 速 度 快 、 磨 性 优 具 耐 异、 附着 力 强 、 盐雾 性 优 异 、 阴极 剥 离 性 良好 等 耐 耐
;
料各 组 分对 涂料 性 能的 影响 及 其研 究 现状 。
关键词:无溶剂环氧防腐涂 料 重 防腐涂料 ;影响 因素 中图分类号:T 3 . 。 Q6 0 7 _文献标识码 :A
|# 口 8 一 ㈣ ∞ , ¥ 孵 ∞ ∞ # 渤 黪| # ∞ * e # ㈣ g ∞B
Ta l Th o tn e f r n ewi i e e t s a i n be1 e c a i g p ro ma c t d f r n h f ma sr to
由于加入溶剂或稀释剂 , 而使漆膜出现针孔 、 脆性大
等 弊 病 。但 双 酚 F 氧 树脂 价 格 要 比双 酚 A环 氧 树 脂 环 高 , 合考虑涂料成本与性能 , 过试验确定双酚 F 综 经 环 氧 树脂 含 量 占总量 的 3%~ 0 时 , 价 比最 高 。 5 5% 性
加体 系 的黏 度 ;沉 淀 硫 酸 钡 吸油 度 低 , 充量 大 , 填 可 提高 涂 层 的耐磨 性 , 蔽 紫 外线 , 屏 耐介 质 性 好 ;滑石 粉 吸油 度 大 , 介 质性 好 ;微 硅粉 则 吸油 度低 , 耐 耐介 质 性 好 。 量 的加 入 填 料 不 仅 可 以提 高 涂 层 的机 械 适 强度 、 耐磨 性 以及遮 盖力 , 能 减 少涂 料 固化 时 的体 且 积 收缩 率 ,降低成 本 , 赋 予 其 良好 的贮存 稳 定 性 。 并 郭 超 群 等 人 … 为 增 强 涂 膜 的 耐 化 学 品性 和 提 高 物 理 机 械性 , 用 片 状 绢 云母 粉 料 。片 状 填料 可 以增 采 强 涂 膜 的 阻 隔 性 能 , 长 介 质 的 渗 透 路 径 。同种 填 延 料 , 细 粒 子 与较 粗 粒 子 相混 合 时 , 细 粒 子趋 向于 较 较
关于重防腐熔结环氧粉末涂料施工工艺
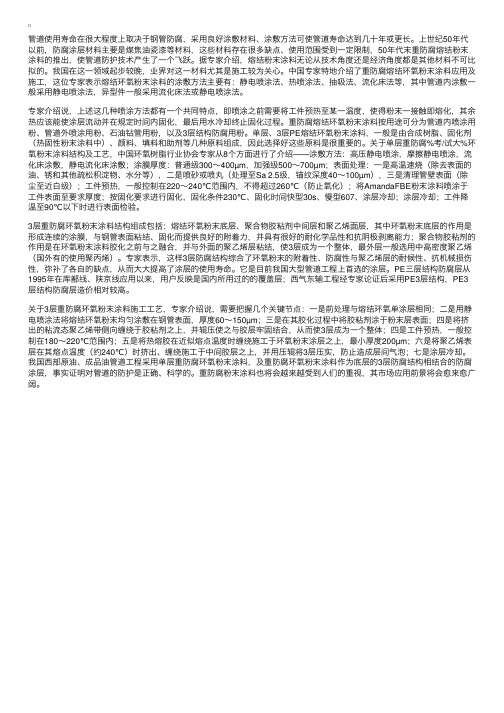
管道使⽤寿命在很⼤程度上取决于钢管防腐,采⽤良好涂敷材料、涂敷⽅法可使管道寿命达到⼏⼗年或更长。
上世纪50年代以前,防腐涂层材料主要是煤焦油瓷漆等材料,这些材料存在很多缺点、使⽤范围受到⼀定限制,50年代末重防腐熔结粉末涂料的推出,使管道防护技术产⽣了⼀个飞跃。
据专家介绍,熔结粉末涂料⽆论从技术⾓度还是经济⾓度都是其他材料不可⽐拟的。
我国在这⼀领域起步较晚,业界对这⼀材料尤其是施⼯较为关⼼。
中国专家特地介绍了重防腐熔结环氧粉末涂料应⽤及施⼯,这位专家表⽰熔结环氧粉末涂料的涂敷⽅法主要有:静电喷涂法、热喷涂法、抽吸法、流化床法等,其中管道内涂敷⼀般采⽤静电喷涂法,异型件⼀般采⽤流化床法或静电喷涂法。
专家介绍说,上述这⼏种喷涂⽅法都有⼀个共同特点,即喷涂之前需要将⼯件预热⾄某⼀温度,使得粉末⼀接触即熔化,其余热应该能使涂层流动并在规定时间内固化,最后⽤⽔冷却终⽌固化过程。
重防腐熔结环氧粉末涂料按⽤途可分为管道内喷涂⽤粉、管道外喷涂⽤粉、⽯油钻管⽤粉,以及3层结构防腐⽤粉。
单层、3层PE熔结环氧粉末涂料,⼀般是由合成树脂、固化剂(热固性粉末涂料中)、颜料、填料和助剂等⼏种原料组成,因此选择好这些原料是很重要的。
关于单层重防腐%考/试⼤%环氧粉末涂料结构及⼯艺,中国环氧树脂⾏业协会专家从8个⽅⾯进⾏了介绍——涂敷⽅法:⾼压静电喷涂,摩擦静电喷涂,流化床涂敷,静电流化床涂敷;涂膜厚度:普通级300~400µm,加强级500~700µm;表⾯处理:⼀是⾼温速烧(除去表⾯的油、锈和其他疏松积淀物、⽔分等),⼆是喷砂或喷丸(处理⾄Sa 2.5级,锚纹深度40~100µm),三是清理管壁表⾯(除尘⾄近⽩级);⼯件预热,⼀般控制在220~240℃范围内,不得超过260℃(防⽌氧化);将AmandaFBE粉末涂料喷涂于⼯件表⾯⾄要求厚度;按固化要求进⾏固化,固化条件230℃、固化时间快型30s、慢型607、涂层冷却;涂层冷却;⼯件降温⾄90℃以下时进⾏表⾯检验。
hzf-101型环氧重防腐涂料标准

hzf-101型环氧重防腐涂料标准一、范围本标准规定了HZF-101型环氧重防腐涂料的产品信息、原材料要求、制备方法、性能要求、测试方法、涂装工艺、质量保证、包装、标识与贮存、安全性等方面的内容。
本标准适用于需要具备优良耐腐蚀性能的各类设备和构筑物等。
二、规范性引用文件下列文件对于本文件的应用是必不可少的。
凡是注日期的引用文件,仅注日期的版本适用于本文件。
凡是不注日期的引用文件,其最新版本(包括所有的修改单)适用于本文件。
三、术语和定义下列术语和定义适用于本标准。
1. 环氧重防腐涂料:以环氧树脂为主要成膜物质,加入颜料、填料、助剂等制成的涂料,具有优异的耐腐蚀性能和附着力。
2. 耐腐蚀性:涂料抵抗化学腐蚀的能力。
3. 附着力:涂料与基材的粘附能力。
4. 硬度:涂料表面的抗划痕能力。
5. 耐磨性:涂料表面的抗磨损能力。
6. 耐温变性:涂料在温度变化下的稳定性。
7. 耐候性:涂料在自然环境下的耐久性。
8. 耐化学品性:涂料抵抗化学品的侵蚀能力。
9. 干燥时间:涂料成膜所需的干燥时间。
10. 柔韧性:涂料对基材的柔顺度。
四、产品信息HZF-101型环氧重防腐涂料的产品信息如下:1. 产品名称:HZF-101型环氧重防腐涂料。
2. 产品型号:HZF-101。
3. 产品颜色:各色。
4. 产品包装:净重为5公斤或10公斤的密封包装。
5. 产品使用期限:自生产之日起,存储期为一年。
6. 产品适用范围:适用于各类设备和构筑物等需要具备优良耐腐蚀性能的场所。
7. 产品性能特点:具有优异的耐腐蚀性能、附着力强、硬度高、耐磨性好、耐温变性优良、耐候性好、耐化学品性强等特点。
8. 产品使用说明:详见产品说明书。
9. 产品注意事项:详见产品说明书。
10. 产品安全警示:详见产品说明书。
五、原材料要求HZF-101型环氧重防腐涂料的主要原材料应符合以下要求:1. 环氧树脂:应选用质量稳定的品牌,并符合相关质量标准。
具体型号和规格应根据产品性能要求进行选择。
无溶剂环氧涂层在酸性溶液中对集输管道内壁的防腐性能

无溶剂环氧涂层在酸性溶液中对集输管道内壁的防腐性能卢仁玲,佘春艳,冉明鑫,苏槐,程正骏,池伸,艾俊哲*(长江大学化学与环境工程学院,湖北荆州434023)[摘要]针对含二氧化碳酸性油气田集输管道内壁的严重腐蚀问题,采用自制的管道内涂层SLE-17进行内壁防护。
通过对涂层的基础性能测试、耐化学性能测试、电化学测试以及腐蚀工况模拟试验,对涂层的适应性进行了评价研究。
结果表明,该防腐涂料附着力为12.73 MPa,耐冲击性为55 kg·cm、经过30 d模拟高温高压腐蚀试验,附着力仍大于8 MPa,涂层外观完好,无气泡、开裂、剥落等涂层失效情况。
对其进行电化学阻抗测试和抗阴极剥离测试,其阻抗值为1.1×109 Ω·cm2,抗阴极剥离半径为2.9 mm,涂层仍能有效阻止腐蚀物质渗透到金属基体,具有良好的适应性。
[关键词]集输管道;防腐;涂层;适应性;酸性介质[中图分类号]TG174.41 [文献标识码]A [文章编号]1007-1865(2021)05-0004-04Anticorrosion Performance of Solvent Free Epoxy Coating on Inner Wall of Gathering and Transportation Pipeline in Acidic SolutionLu Renling, She Chunyan, Ran Mingxin, Su Huai, ChengZhengjun, Chi Shen, Ai Junzhe*(School of Chemistry and Environmental Engineering, Yangtze University, Jingzhou 434023, China) Abstract:The problem of serious corrosion of the inner wall of acid oil and gas field gathering and transportation pipeline containing carbon dioxide is discussed, the self-made inner coating of pipeline SLE-17 was used to protect the inner wall. The adaptability of the coating was evaluated by basic performance test, chemical resistance test, electrochemical test and corrosion condition simulation test. The results show that the adhesion of the anticorrosive coating is 12.73 MPa, the impact resistance is 55 kg·cm, after 30 days of simulated high temperature and high pressure corrosion test, The adhesion is still greater than 8 MPa the coating appearance is intact, no bubbles, cracking, peeling and other coating failure. On the electrochemical impedance test and cathodic disbonding resistance test, the impedance value of1.1×109 Ω·cm2, radius of cathodic disbonding resistance is 2.9 mm, coating can effectively prevent corrosion penetration to the metal substrate, has good adaptability.Keywords: gathering and transportation pipeline;corrosion protection;coating; adaptive;acidic media能源工业是经济发展的动力和血脉,我国对油气资源的开发利用程度逐步增大[1],然而在实际开采和运输过程中,油气集输管线(材质主要为N80碳钢)面临严重腐蚀,特别是酸性油气田,通常介质为含CO2的酸性环境,管道内腐蚀是安全生产的最严峻挑战之一[2]。
阴极剥离相关标准指标汇总
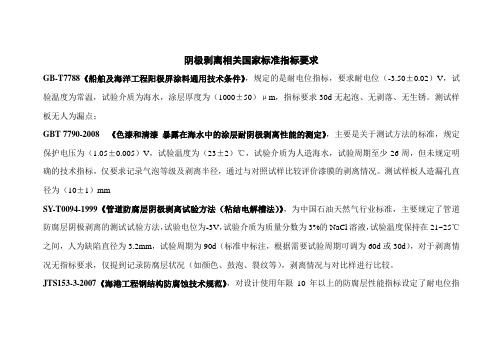
阴极剥离相关国家标准指标要求GB-T7788《船舶及海洋工程阳极屏涂料通用技术条件》,规定的是耐电位指标,要求耐电位(-3.50±0.02)V,试验温度为常温,试验介质为海水,涂层厚度为(1000±50)μm,指标要求30d无起泡、无剥落、无生锈。
测试样板无人为漏点;GBT 7790-2008 《色漆和清漆暴露在海水中的涂层耐阴极剥离性能的测定》,主要是关于测试方法的标准,规定保护电压为(1.05±0.005)V,试验温度为(23±2)℃,试验介质为人造海水,试验周期至少26周,但未规定明确的技术指标,仅要求记录气泡等级及剥离半径,通过与对照试样比较评价漆膜的剥离情况。
测试样板人造漏孔直径为(10±1)mmSY-T0094-1999《管道防腐层阴极剥离试验方法(粘结电解槽法)》,为中国石油天然气行业标准,主要规定了管道防腐层阴极剥离的测试试验方法,试验电位为-3V,试验介质为质量分数为3%的NaCl溶液,试验温度保持在21~25℃之间,人为缺陷直径为3.2mm,试验周期为90d(标准中标注,根据需要试验周期可调为60d或30d),对于剥离情况无指标要求,仅提到记录防腐层状况(如颜色、鼓泡、裂纹等),剥离情况与对比样进行比较。
JTS153-3-2007《海港工程钢结构防腐蚀技术规范》,对设计使用年限10年以上的防腐层性能指标设定了耐电位指标,测试方法执行GB/T 7788,但强调了当采用外加电流阴极保护时配套涂层耐阴极电位为-1.50V,常规情况下耐电位为-1.20V。
GBT 23257-2009《埋地钢质管道聚乙烯防腐层》,规定了环氧粉末涂料的抗阴极剥离指标,试验电位为-1.50V,试验介质为质量分数为3%的NaCl溶液,人为缺陷直径为3.2mm,涂层厚度为(300~400)μm,试验条件为(65℃,48h)时,剥离指标为≤8mm; 试验条件为(65℃,30d)时,剥离指标为≤15mm。
熔结环氧粉末涂料

熔结环氧粉末涂料Fusion Bonding Epoxy Powder Coatings天津瑞远粉末涂料有限公司毕学振摘要:FBE是指热固性重防腐环氧粉末涂料。
文章详细介绍了FBE的防腐机理、类型、施工工艺、涂层结构和应用领域,阐述了熔结环氧粉末在各种管道防腐涂装中的重要作用。
1 前言热固性重防腐环氧粉末涂料又称熔融结合环氧粉末涂料,简称熔结环氧粉末,是一种以空气为载体进行输送和分散的固体涂料,将其施涂于经预热的钢铁制品表面,熔化、流平、固化形成一道均匀的涂层,故得此名,英文名称Fusion Bonding Epoxy Powder Coatings,简称FBE。
熔结环氧粉末的每个颗粒都均匀地包含所有组成成分,使涂敷的操作过程以及形成的涂层都具有连续稳定的均匀性。
熔结环氧粉末涂装过程无三废污染,是一种环保型涂料,国外最早开发于上世纪50年代,在60年代实现了工业化生产。
由于FBE具有优良的机械性能、抗腐蚀性能和耐久性能,所以被广泛应用于陆上、水下、海底等管线的防腐涂装,为处于各种环境中的管线长期低维护运行提供了可靠的保证。
40多年来,经过不断的发展完善,这项技术已经走向成熟。
迄今为止,全球已有20余万公里以上的管道使用了熔结环氧粉末,铺设于世界各地——从陆地到海洋,从城市到乡村,从赤道到极地,从平原到山地、河流、湖泊,从西伯利亚草原到非洲沙漠,从美洲大陆到中东海湾,都有熔结环氧粉末的应用实例。
熔结环氧粉末涂层能够在各种极端的气候条件和苛刻的机械应力作用、化学介质侵蚀的环境中得到广泛应用,足以证明熔结环氧粉末涂层是一种可靠的保护涂层,经得起实践和时间的考验。
我国熔结环氧粉末技术起步较晚,上世纪80年代才开始引进国外先进的环氧粉末及工艺、设备。
天津瑞远粉末涂料有限公司在国内率先推出了重防腐系列环氧粉末涂料,打破国外产品的垄断,在国家许多重点工程上得到应用,取得了明显的经济效益和社会效益,特别是在一些国家重点工程中,瑞远公司占据了重要地位,产品应用现场反应良好,不仅保证了工程顺利进行,而且为国家节约了大量工程投资。
钢质管道3PE涂层阴极剥离性能分析与控制措施

l 前 言
为 了防止埋 地钢质 管道 的腐蚀 , 确保 管道 的使用 寿命 , 通常采 用外 防腐 层和 阴极 保 护 的双重措施 。外
防腐 层对埋 地钢质 管道 的腐 蚀起 到约 9 % 以上 的保 5 护作用 ; 阴极 保 护是 一种 补 救措 施 , 是 当 防腐 层 局 就
钢铁
为 了对 存 在 漏 点 的钢 质 管 道 涂 层 进 行 防腐 弥
补 , 前 的做法是实行外加电流的阴极保护 , 目 它是基
于电化 学 原理 而采 用 的一 种 电化 学保 护 , 要 是 通 主
剥 离性 能提 供 依 据 , 可指 导 生产 实 际。 关键词 环氧 粉 末 阴极 保护 阴极 剥 离
An l ss a d Co t o f Ca h ‘ c Dib n m e t a y i n n r lo t 0 l s o d i n
o f3 LPE a i g n S e lPi ei e Co tn s o t e p l n
部 破损产生 漏 点 时 , 避免 管 道发 生 腐 蚀 的保 护 方 法 。
但是 阴极保 护在对钢 质管道产 生保 护 的 同时 , 却对 涂 层 有剥 离破 坏 作用 。 阴极剥 离 试验 就 是用 来 评 定 涂 层 在阴极保 护作用 下的抗 阴极 剥离性 能 。
2 e O 3:F 2 3・X 2 铁 锈 )+( r ( H) eO H O( 3一X)
这 种腐蚀 反 应不 断 发 生 连 续进 行 , 点 处 的 金 属 就 漏
不 断被腐 蚀 。
2 2 阴极保 护 .
钢质管道 的外防腐层在连续致密没有缺 陷时 , 防腐层有很好的抗 渗透性 , 且与被保 护的金属表 并
无溶剂环氧高强涂料产品说明书
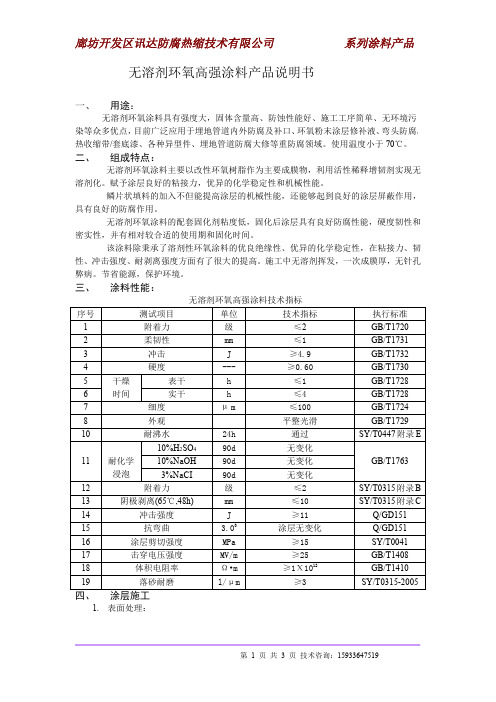
堆放。注意灰尘进入。
五、 质量检验:
1、 对防腐层应进行外观、厚度、漏点和粘接力检验。外观应呈平整、光滑的漆膜 状。厚度采用磁性测厚仪测量,在一周内检测四个点,上、下、左、右。厚度 一般为 350—500µm 之间。漏电检查采用电火花针孔捡漏仪以 2000V 的捡漏电 压进行检查。每根都做全部检查。对于厚度、漏电检查不合格应予以补涂。粘 接力检验按无溶剂环氧煤沥青涂料标准规定进行。
二、 组成特点:
无溶剂环氧涂料主要以改性环氧树脂作为主要成膜物,利用活性稀释增韧剂实现无
溶剂化。赋予涂层良好的粘接力,优异的化学稳定性和机械性能。
鳞片状填料的加入不但能提高涂层的机械性能,还能够起到良好的涂层屏蔽作用,
具有良好的防腐作用。
无溶剂环氧涂料的配套固化剂粘度低,固化后涂层具有良好防腐性能,硬度韧性和
搅拌均匀后即可涂刷;配比量多少,以 A:B=100:20—25(重量比)进行混配搅 匀后(搅拌 3-4 分钟,熟化 3-4 分钟),开始刮涂,在 30 分钟内涂刷完,。 D、 补口时:首先对焊缝处进行预处理,清除毛刺、焊瘤等,预涂死角处。如果管 体是环氧粉末涂层,请把粉末涂层打毛 100mm 左右,清扫干净杂质,然后涂刷无 溶剂涂料。涂刷时,450μm 厚度的涂层,一般需要涂刷两次为好,第一次的涂刷 200μm 左右,表干后(表干是手指轻轻触摸漆不沾手,夏季一般为 40 分左右,冬 季时间要长一些,根据气候而定,一般 50 分钟左右。最低温度不要超过-5℃,温 度越低活性越差,对固化影响越大。)涂刷第二次。每次配料根据使用现场而定, 补口使用时,一般每次配三道口的第一层用量。(无溶剂涂料的密度为 1.38-1.45。 固体含量在 99%以上。) E、 补伤时:首先把受伤的部位进行打磨,严重部位漏出钢铁,打出锚纹,周围粉末 处进行拉毛,拉毛粉末距离破损处为 50mm 为好。拉毛后吹扫干净杂质,调整好涂料 可以进行涂刷。为了保证附着力及涂层厚度,一般情况下需要涂刷两次。第一次涂 刷厚度不易超过 200μm 左右。冬季施工,请对 A 组份和 B 组份分别进行预热,预热 温度 A 组不易超过 50℃,B 组不要超过 30℃,流动即可。温度越高混合使用时间越 短。 F、 弯头和管体防腐时,首先是进行管体表面的喷砂除锈,除锈等级达到技术要求, 除锈之后请注意焊缝的处理,首先是焊渣、毛刺、凹凸的处理,然后是灰尘的清理 干净。刷涂时,先对角、边、焊缝等不易涂到或难以涂刷的地方进行预涂,然后再 进行管体的涂刷。涂刷 450μm 左右厚度,一般需要涂刷两次为好,第一次的涂刷 200μm 左右,表干后在涂刷第二遍。(涂料的配量,原则上不超过 1.5 公斤,30 分 钟内用完。一般厚度为 450μm 左右厚度的涂层,理论每平方米用量为 0.75-0.85 公斤)。一般弯头涂层厚度为大于 650μm 为好。(1.15 公斤-1.30 公斤/m2)
环氧类防腐涂料的防腐原理

环氧类防腐涂料的防腐原理1.隔绝空气和水分的接触:环氧类防腐涂料在施工后会形成一层坚固的涂层,能够有效地隔绝外界空气和水分对金属表面的直接接触。
空气中的氧气和水分是金属腐蚀的主要原因之一,通过阻止它们的接触,可以减少金属发生腐蚀的可能性。
2.降低电极电位差:环氧类防腐涂料是一种具有较高电绝缘性能的材料,可以降低金属表面的电极电位差,减少了金属腐蚀的发生。
金属腐蚀是一种电化学反应,电极电位差越大,腐蚀反应速度越快。
而环氧类防腐涂料的应用能够有效地降低金属的电位差,从而减缓腐蚀反应的进行。
3.形成抗酸堵蚀的氧化膜:环氧类防腐涂料在固化过程中能够形成一种坚硬、耐酸碱的氧化膜,能够在一定程度上抵御酸性物质对金属表面的侵蚀。
这种氧化膜具有很好的物理和化学稳定性,能够有效地阻止酸性物质与金属表面的接触,保护金属免受腐蚀。
4.提供物理屏障防护:环氧类防腐涂料的涂层是一种均匀、致密、耐磨的物理屏障,能够有效地抵挡外界的侵蚀因子,如水分、氧气、酸碱等。
它的刚性和硬度能够有效地抵挡外界的机械冲击和摩擦。
此外,涂层的表面光滑度和平整度也能够减少微生物和腐蚀介质的附着,阻止其对金属表面的侵蚀。
5.具有自愈合能力:环氧类防腐涂料具有一定的自愈合能力,可以自行修复涂层表面的微小划痕和裂纹。
当涂层表面发生损伤时,涂料中的环氧基团会启动自愈合反应,填补和修复涂层表面的缺陷,形成一个完整的保护层,延长涂层的使用寿命。
总的来说,环氧类防腐涂料的防腐原理是通过形成坚固的涂层,隔绝外界的空气和水分;降低金属的电极电位差,减缓电化学腐蚀反应的进行;形成抗酸堵蚀的氧化膜,抵御酸蚀;提供物理屏障防护,减少外界侵蚀因子的接触;具有一定的自愈合能力,修复涂层表面的损伤。
这些机制相互作用,使得环氧类防腐涂料具有较好的防腐性能,能够延长金属材料的使用寿命。
- 1、下载文档前请自行甄别文档内容的完整性,平台不提供额外的编辑、内容补充、找答案等附加服务。
- 2、"仅部分预览"的文档,不可在线预览部分如存在完整性等问题,可反馈申请退款(可完整预览的文档不适用该条件!)。
- 3、如文档侵犯您的权益,请联系客服反馈,我们会尽快为您处理(人工客服工作时间:9:00-18:30)。
抗阴极剥离型重防腐环氧涂料重防腐环氧粉末涂料是一种能在严酷的腐蚀环境下长期有效使用的熔结型环氧粉末涂料,由于其具有优良的机械性能、抗腐蚀、耐老化性能,所以被广泛应用于陆上、水下、海底等管线的防腐涂装,给处于各种苛刻环境中的管线的长期低维护运行提供了可靠的保证。
据中国环氧树脂行业协会()专家介绍,在对重防腐粉末涂料出现阴极剥离的相关因素进行分析的基础上,从改变环氧树脂主链结构,提高固化物交联密度与对金属附着力入手,通过相应的对比试验,合成了具有较高抗阴极剥离能力的环氧树脂与固化剂,成功研制出新型环氧粉末涂料,解决了在较高温度条件下长期使用过程中抗阴极剥离难题,拓展了重防腐环氧粉末涂料在苛刻环境下的应用范围。
1、前言重防腐环氧粉末涂料是一种能在严酷的腐蚀环境下长期有效使用的熔结型环氧粉末涂料,由于其具有优良的机械性能、抗腐蚀、耐老化性能,所以被广泛应用于陆上、水下、海底等管线的防腐涂装,给处于各种苛刻环境中的管线的长期低维护运行提供了可靠的保证。
据中国环氧树脂行业协会()专家介绍,重防腐粉末涂料与普通粉末涂料在功能上各有所侧重,普通粉末涂料虽然也注重对基材的保护作用,但其装饰作用往往处于较重要的位置。
重防腐粉末涂料则主要是侧重于对底材的保护功能。
此外,该种粉末涂料主要是用于工业涂料,批量大,生产作业要求成膜速度快,其涂装方式往往采取加热快速熔化与固化方式,因而在国外这类粉末涂料被称之为热融结环氧(fusion bonded epoxy),简称fbe。
在管道防腐方式中,常常是防腐涂料层和阴极保护联合应用,这样可以使管道金属结构物获得最经济和有效的保护。
良好的涂覆层可以保护构筑物99%以上的外表面不受腐蚀,因此,地下或水下的金属结构物通常在使用前涂覆防护涂层用以将金属与电介质环境绝缘隔离。
但由于施工过程中的运输、安装及补口,热应力及土壤应力、涂层的老化及涂层微小针孔的存在,金属结构物的外涂层总会存在一些缺陷,而这些缺陷最终将导致金属的局部腐蚀产生。
对于裸露或防腐涂层很差的地下或水下金属构筑物,阴极保护甚至是腐蚀防护的唯一可选择的手段,而阴极保护技术和涂层联合应用则可以更有效防止金属的腐蚀。
一方面阴极保护可有效地防止涂层破损处产生的腐蚀,延长涂层使用寿命,另一方面涂层又可大大减少保护电流的需要量,改善保护电流分布,增大保护半径,使阴极保护变得更为经济有效,上述优点使重防腐粉末涂料涂层加阴极保护措施成为目前埋地管道的主要防腐措施。
虽然防腐涂料层和阴极保护联合应用有利于管道防腐,但阴极保护中的电化学反应却易引起防腐涂层的腐蚀,特别是引起防腐涂层与金属之间结合力的下降从而导致阴极剥离的发生,出现涂层起泡并导致开裂,最终破坏了涂层的防腐效果。
所以在防腐涂料层和阴极保护联合应用时对防腐涂料的抗阴极剥离性能要求较高,以保证涂层与阴极保护能长期共存,共同防护管道。
据中国环氧树脂行业协会()专家介绍,由于环氧树脂分子中含有大量的羟基、醚键等极性基团,对金属有极强的粘合力,故具有较强的抗阴极剥离性能。
但由于常用的固体环氧树脂多为双酚a型长链树脂,该树脂分子只在分子两端存在环氧基团,故与固化剂反应后的固化物交联密度不是很高,所以在苛刻环境下的长时间抗阴极剥离的能力还不是太好,而致密度高的酚醛环氧树脂的固化物则往往又因交联密度过高,固化过秤产生的内应力大、抗弯曲与冲击性不够好而易导致涂层开裂,不适宜做管道粉末涂料使用。
近年来随着国家经济建设的飞速发展,对石油天然气埋地管道重防腐粉末涂料环氧树脂与助剂的需求量越来越大,质量要求也越来越高。
对涂层在苛刻条件下的抗阴极剥离能力也提出了更高的要求,如以前只要求“65℃下,在1.5v电压下通电2天的阴极剥离距离不大于8mm”,而现在则要求“60℃,在1.5v电压下通电30天的阴极剥离距离不大于10mm”。
这种苛刻的试验要求对环氧粉末涂料提出了更高的挑战,市场亟待一种能满足此要求的国产重防腐粉末涂料的出现。
为满足客户的需要,我们曾对市面上的多种环氧树脂与固化剂进行了实验比较,结果均不太理想。
为了提高抗阴极剥离能力,据中国环氧树脂行业协会()专家介绍,业界在以前研制普通重防腐粉末涂料专用环氧树脂与固化剂的基础上,根据阴极剥离发生机理与材料性能之间的关系有针对性地进行了大量的改进试验,终于研制出了有较高抗阴极剥离能力的重防腐粉末涂料用环氧树脂和固化剂,进而研制出满足新标准要求的粉末涂料配方,并成功地将此型重防腐粉末涂料投向了市场。
2、涂料阴极剥离的影响因素分析(1)重防腐环氧粉末涂料阴极剥离的影响因素要提高重防腐环氧粉末涂料的抗阴极剥离能力,首先就必须先弄清粉末涂料阴极剥离的影响因素。
重防腐环氧粉末涂料的抗阴极剥离能力与环氧树脂、固化剂、填料的选用密切相关,在实际使用中,又与管道金属的表面处理以及固化工艺密切关联。
研究发现,管道金属在阴极保护的情况下,在金属表面发生的阴极剥离过程以析氢反应为主,其结果就导致了金属表面局部oh-离子浓度的增大,这种局部碱环境会侵蚀聚合物涂层并使界面处金属氧化物溶解,腐蚀性液体进而沿着金属与涂层的界面不断扩散,渗透,引起新的腐蚀、剥离,最终引起涂层起泡并导致开裂,破坏聚合物涂层的防腐效果。
在这种情况下,要抑制阴极剥离的进行就必须在增强环氧涂层与基体金属间的结合力的同时增强环氧涂层的防腐性(尤其是耐碱性),以抑制腐蚀物质沿金属与环氧涂层界面的扩散过程。
环氧涂层与基体金属之间的结合力,既受环氧树脂和固化剂上的极性基团数目影响,也受涂层与基体金属之间的结合键的类型的影响,还与环氧涂层内应力有关。
内应力过大时,也会削弱环氧涂层与基体金属之间的结合程度。
若环氧涂层极性基团数目越多、涂层与基体金属之间的结合键越强、环氧涂层内聚力、内应力越小时,涂层与基体金属之间的结合程度越高。
据中国环氧树脂行业协会()专家介绍,但这种理想情况不易实现,例如涂层的极性基团(特别是亲水型极性基团)数目太多,虽能提高附着力,但却导致涂层耐水性(特别是耐盐水性)的下降,进而难以抑制腐蚀性介质沿涂层与基体金属界面的扩散渗透进程,若耐水性下降的负面影响超过了附着力提高带来的正面影响,就会导致涂层阴极剥离的加剧进行。
环氧涂层的耐腐蚀性受涂层的致密性和涂层固化物中的化学键耐腐蚀性强弱的影响。
当涂层致密性越高,不耐腐蚀的化学键越少时,环氧涂层的耐腐蚀性越强。
而涂层致密性越高时,涂层的内聚力、内应力就会越大,当超过涂层与基体金属之间的结合力时,就会引起涂层与基体金属之间剥离。
在涂层中不耐腐蚀的化学键要越少越好,例如酯键耐碱性较差,就不太适用于重防腐涂料采用。
据中国环氧树脂行业协会()专家介绍,对酚醛树脂,由于芳香密度与交联密度较大,用它来改性环氧树脂或固化剂,用量合适能提高防腐性,但由于酚羟基具有一定酸性,耐碱性较差,用量过多时易引起涂层抗阴极剥离能力的下降。
另外由于酚醛树脂具有一定脆性,固化产物内应力较大,用量过多时也不利于涂层的抗阴极剥离。
(2)抗阴极剥离型重防腐环氧粉末涂料的配方设计由上述分析可推知,在选用环氧树脂与固化剂体系时要求环氧树脂有较高的环氧值以保证较高的致密度,同时要有一定的韧性(这一点也可通过提高固化剂的韧性来弥补),以消除固化产物过多的内应力,另外要有一定数量的耐碱性与耐水性较好的极性基团,以提高涂层与基体金属之间的结合力,以形成兼顾结合力、耐蚀性、柔韧性的环氧固化体系,从而达到提高抗阴极剥离的效果。
根据上述分析,中国环氧树脂行业协会()专家,有针对性地合成了分子结构中具有多个环氧基团的与一定韧性jenp-02a改性环氧树脂,较好地协调了附着力、耐蚀性、柔韧性的相应要求,取得了很好的抗阴极剥离效果。
在选择相应固化剂时,同样存在兼顾致密度与韧性的协调,通过固化剂分子中刚性基团与韧性基团的比例的合理调节,合成出软硬适中的固化剂来消除内应力。
据中国环氧树脂行业协会()专家介绍,在实验研究中采用的是端羟基聚合物型复配固化剂,该类型固化剂聚合度越高,分子量大,韧性好,同时软化点也较高,有利于保存。
在复配型固化剂中,包含有主固化剂与促进剂(常用阴离子型催化剂)的配比。
主固化剂与阴离子型促进剂的固化反应机理有所不同,主固化剂主要是通过端羟基与环氧基进行加成聚合反应,具有一定的韧性,固化产物内应力较小。
而阴离子型促进剂则是通过阴离子作用使环氧基开环,形成新的阴离子,这种新的阴离子再与新的环氧基反应,形成链式增长。
链式反应一经引发就快速进行,反应速度快、放热剧烈,容易形成内应力使涂膜发脆,导致涂膜与基体金属结合力下降,加剧阴极剥离的进程。
中国环氧树脂行业协会()专家介绍说,另外阴离子型促进剂加入量太多,会导致端羟基型固化剂不能充分反应,未反应的端羟基耐碱性较差,也会加剧阴极剥离的进程。
通过控制主固化剂的聚合度与促进剂的加入量,开发的jecp-01b固化剂,较好地满足了应用要求。
在环氧树脂与固化剂确定的前提下,选用合适的颜填料对提高涂料的抗阴极剥离效果也有举足轻重的作用。
中国环氧树脂行业协会()专家说,应尽量避免用刺激性颜填料,而应多采用硫酸钡、硅微粉等惰性颜填料。
研究发现,填料在涂层中分布越均匀、填料与树脂接触面积越大、填料与树脂结合越紧密、涂层耐蚀性越好,涂层抗阴极剥离效果越好。
另外片状鳞片类填料(如泡状云母),由于能延长腐蚀介质渗透的路径,也对提高抗阴极剥离能力有很好的效果。
3.抗阴极剥离型重防腐环氧涂料的制备(1)实验原料①环氧树脂,jenp-02,外观浅黄色透明颗粒,环氧值0.13~0.15 mol/100g,软化点85~90℃;②固化剂,jecp-01b,外观浅黄色透明颗粒,羟基当量200~220g/mol,软化点90~100℃,粘度(40%乙二醇丁醚溶液)240~400mpa.s 25℃;③流平剂,hs-802;④脱气剂,ht-382,黄山盛龙化工厂;⑤钛白粉,r-940,江苏镇江钛白粉厂;⑥气相白碳黑,jl-958,上海金锦乐公司;⑦沉淀硫酸钡, 600目,青岛东风化工厂;⑧活性硅微粉,600目,湖州硅微粉厂;⑨云母粉,1250目,滁州市万桥绢云母粉厂,颜料群青。
(2)粉末涂料实验与检测设备①螺杆挤出机gst-30e型,烟台三立工业有限公司;②粉末喷涂设备,gq-ⅱ型,上海新星静电喷涂设备厂;③粉末涂料热性能检测,示差扫描量热仪,dsc-131,法国setaram公司;④涂层冷弯试验机,自制;⑤涂层附着力测试,0~100℃恒温水浴,上海实验仪器厂;⑥涂层阴极剥离,用恒温烘箱,电阻箱、铂电极、甘汞电极、调压器、电压表组装。
(3)实验方法①粉末涂料配方抗阴极剥离型重防腐环氧粉末涂料按以下配方进行试验(重量组成)环氧树脂jenp-02a,100 固化剂jecp-01b,20~24沉淀硫酸钡,40 活性硅微粉,15云母粉,10 钛白粉,5流平剂,1 脱气剂,0.2气相白碳黑,0.1 群青,适量②粉末涂料的制备将树脂、固化剂、助剂、颜填料等原料经准确称量后在高速混料机中混合5-8分钟,再在挤出机混炼挤出(挤出机ⅰ区温度设定为100±2℃,ⅱ区温度设定为90±2℃),然后经压片、破碎、磨粉、过120目筛等工艺,即制得成品粉末涂料。