铝合金压铸技术要求汇总
压铸铝合金技术要求

压铸铝合金技术要求嘿,咱今儿就来聊聊压铸铝合金技术要求这档子事儿!你说这压铸铝合金啊,就像是一位需要精心呵护的宝贝。
首先呢,材料得选对咯!可不是啥铝合金都能拿来压铸的呀。
这就好比做饭,得挑好食材才能做出美味佳肴不是?对铝合金的成分那可得讲究,各种元素的比例得恰到好处。
要是比例不对,那压铸出来的东西可能就不结实,容易出问题。
就好像盖房子,根基不牢,那房子能稳当吗?压铸的过程呢,也得万分小心。
温度得控制好,高了不行,低了也不行。
这温度就像是炒菜时的火候,火候大了糊了,火候小了又不熟。
压力也得适中,不然压出来的东西不是这儿缺一块就是那儿多一块,那可就难看啦!模具也是关键啊!模具就像是一个模子,得做得精细,才能压铸出形状规整、漂亮的铝合金制品。
要是模具有瑕疵,那压铸出来的东西不就跟着有问题啦?这就跟刻印章似的,印章不好,印出来的字能好看吗?还有啊,压铸之后的处理也不能马虎。
表面得打磨光滑,不能有毛刺啥的。
这就跟人出门一样,得收拾得干干净净、利利索索的,不然多难看呀。
咱再说说这压铸铝合金的性能要求。
强度得够吧,不然怎么经得起使用呢?就像人的身体,得强壮才能干重活呀。
韧性也不能差,不然稍微碰一下就断了,那可不行。
而且啊,这压铸铝合金还得耐腐蚀。
你想想,要是容易被腐蚀了,那用不了多久不就坏了吗?这就好比一件好衣服,得耐穿才行,要是洗两次就破了,那多可惜呀。
在实际操作中,可得严格按照这些技术要求来。
不能偷工减料,不能马马虎虎。
每一个环节都得认真对待,就像呵护自己最心爱的东西一样。
总之呢,压铸铝合金技术要求可真是不少,但只要咱都做到位了,就能压铸出高质量的铝合金制品。
这不仅能让咱自己满意,也能让使用这些制品的人放心呀!这可不是开玩笑的事儿,大家可得重视起来哟!不然出了问题,那可就麻烦大啦!。
铝合金压铸技术要求(DOC)

页号:1/81、范围本标准规定了铝合金压铸件的技术要求、试验方法、检验规则、交货条件等。
本标准适用于汽车发电机铝合金端盖压铸件。
2、引用标准GB6414铸件尺寸公差GB6987.1-GB6987.16铝及铝合金化学分析方法GB288-87金属拉力试验法GB/T13822-92 压铸有色合金试样GB6060.5 表面粗造度比较样块抛(喷)丸、喷吵加工表面3、技术要求3.1 压铸铝合金的牌号压铸铝合金采用UNS-A03800(美国A380.0,日本ADC10)可选用材料UNS-A03830 (美国383.0,日本ADC12)化学成份见表1表1页号:2/8供应商可选择上述四种牌号的任何一种,如在生产过程中更换其它牌号,需重新进行样件鉴定。
3.1.1回炉料使用规定3.1.1.1回炉料分类一级回炉料:浇道、化学成份合格的废铸件,后加工次品等不含水分和油污。
二级回炉料:集渣包、坩埚底部剩料、退货废品、存放时间长(超过10天)的一级回炉料。
三级回炉料:飞边、溅屑、细小的碎料、带有油污的渣料、因化学成份报废的铸件、从铝渣中捡出的铝粒。
3.1.1.2回炉料使用比例使用单一某级回炉料:一级回炉料最大使用量50%,二级回炉料最大使用量40%。
一级、二级回炉料混合使用:回炉料总量不超过40%,其中二级回炉料最大使用量20%。
三级回炉料:不能直接使用,必须经过重熔、精炼且化学成份分析合格后才能使用,其最大使用量10%,仅与铝锭混合使用。
页号:3/83.1.1.3加料循序小颗粒回炉料大块回炉料铝锭,如此循环。
3.2 力学性能采用单铸拉力试样检验,其力学性能应满足抗拉强度≥240Mpa,伸长率≥1%,HB85(5/250/30)。
试样尺寸及形状应符合GB/T 13822-92《压铸有色合金试样》的规定。
3.3 压铸件尺寸压铸件的几何形状和尺寸应符合铸件图的规定。
3.4 待加工表面用符号“”标明,尖头指向被加工面。
例:0.5 表示该表面留有加工余量0.5mm3.5 表面质量3.5.1 铸件清理后的表面质量铸件的浇口、飞边、溢流口、隔皮等应清理干净,但允许留有清理痕迹。
铝合金压铸技术要求
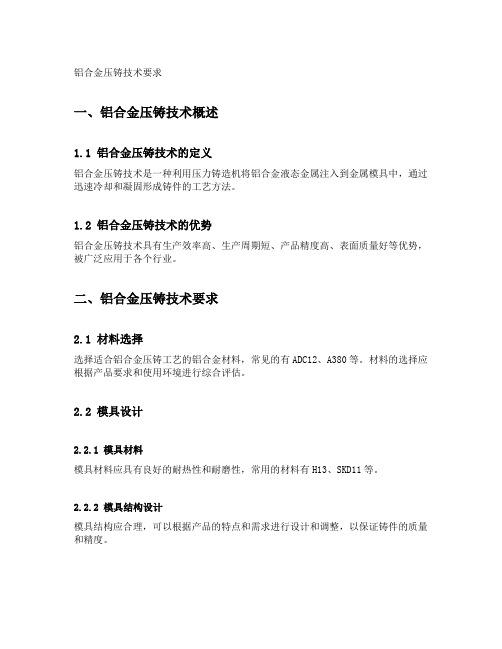
铝合金压铸技术要求一、铝合金压铸技术概述1.1 铝合金压铸技术的定义铝合金压铸技术是一种利用压力铸造机将铝合金液态金属注入到金属模具中,通过迅速冷却和凝固形成铸件的工艺方法。
1.2 铝合金压铸技术的优势铝合金压铸技术具有生产效率高、生产周期短、产品精度高、表面质量好等优势,被广泛应用于各个行业。
二、铝合金压铸技术要求2.1 材料选择选择适合铝合金压铸工艺的铝合金材料,常见的有ADC12、A380等。
材料的选择应根据产品要求和使用环境进行综合评估。
2.2 模具设计2.2.1 模具材料模具材料应具有良好的耐热性和耐磨性,常用的材料有H13、SKD11等。
2.2.2 模具结构设计模具结构应合理,可以根据产品的特点和需求进行设计和调整,以保证铸件的质量和精度。
2.3 注射设备2.3.1 压铸机选择根据产品的要求确定压铸机的型号和规格,包括锁力、注射压力等参数的选择。
2.3.2 注射系统注射系统包括注射缸、注射头、喷嘴等组成,其设计应合理,确保铝合金液态金属的注入和充填。
2.3.3 润滑系统润滑系统的设置对于铝合金压铸技术的稳定运行起着重要作用,应注意润滑剂的选择和使用。
2.4 工艺参数控制压铸工艺参数对于产品的质量和尺寸稳定性有很大的影响,应进行合理的控制和调整。
2.4.1 注射速度注射速度过快会导致铸件内部气孔、缺陷等问题,注射速度过慢会导致铝合金液态金属凝固不完全。
2.4.2 注射温度注射温度过高会导致铝合金液态金属粘度降低,流动性增强,但也会加快模具磨损。
注射温度过低则会导致液态金属凝固时间过长。
2.4.3 注射压力注射压力的控制对于铸件的密实性和表面质量有着重要影响,应根据产品要求进行精确控制。
2.4.4 注射时间注射时间应根据实际需要进行合理设置,以保证铝合金液态金属充填充实模腔。
2.5 热处理工艺铝合金压铸件在铸造成型后,经过热处理工艺可以改善其机械性能和物理性能,如固溶处理、时效处理等。
2.6 铸件表面处理铝合金压铸件的表面处理包括喷砂、喷涂、电镀等方法,以提高产品的外观质量和耐腐蚀性能。
铝合金压铸技术

铝合金熔解
1.冷室机:熔解温度630~650℃ 2.压铸铝合金的熔解温度(For ADC-12熔点为
516~582℃),另加高50~70℃以防热损.
射出速度
射出依柱塞的运动速度可分为两个阶段:
>第一个阶段,柱塞是以低速前进将熔汤充满 料管到浇口的空间.
>第二个阶段,柱塞是以高速前进,以便将熔汤 高速射入模穴.
熔汤在料管中的流动
1.柱塞速度小于临界速度料管的空气排不出 2.柱塞速度大于临界速度料管的空气包卷 3.柱塞速度等于临界速度料管的空气能排出
慢射阶段的临界速度( in/sec )
料 管 直 径 ( in )
1.00 1.25 1.50 1.75 2.00 2.25 2.50
50 11.3 12.6 13.8 15.0 16.0 17.0 17.9
1.3max 1.3max
0.5max 0.5max
ቤተ መጻሕፍቲ ባይዱ
0.5max 0.5max
0.3max 其余 0.3max 其余
1.3max 0.3max 0.3max 0.3max 其余
压铸概论
压铸机分冷室压铸机和热室压铸机二种: 1.冷室压铸机适合:铝合金和铜合金. 2.热室压铸机适合:锌合金,镁合金和锡铅合金.
铝合金压铸制程
铝合金压铸的过程首先将铝合金锭熔解, 然后将熔汤送至压铸机内,再将熔汤射入模穴 内,待铸件成形冷却后,开模,顶出铸件并取出, 然后对模具喷离型剂,合模后等待射出即完成 一个循环.
压铸制程特性
>高速充填 >充填时间很短 >高压 >熔汤和冷却速度快
铝合金压铸制程流程
1.合金熔解 2.将熔汤送至压铸机→射出→成形→开模→顶
铝压铸技术要求
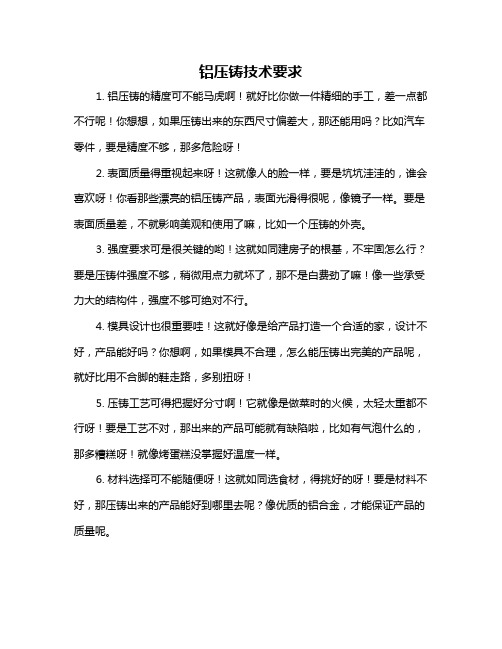
铝压铸技术要求
1. 铝压铸的精度可不能马虎啊!就好比你做一件精细的手工,差一点都不行呢!你想想,如果压铸出来的东西尺寸偏差大,那还能用吗?比如汽车零件,要是精度不够,那多危险呀!
2. 表面质量得重视起来呀!这就像人的脸一样,要是坑坑洼洼的,谁会喜欢呀!你看那些漂亮的铝压铸产品,表面光滑得很呢,像镜子一样。
要是表面质量差,不就影响美观和使用了嘛,比如一个压铸的外壳。
3. 强度要求可是很关键的哟!这就如同建房子的根基,不牢固怎么行?要是压铸件强度不够,稍微用点力就坏了,那不是白费劲了嘛!像一些承受力大的结构件,强度不够可绝对不行。
4. 模具设计也很重要哇!这就好像是给产品打造一个合适的家,设计不好,产品能好吗?你想啊,如果模具不合理,怎么能压铸出完美的产品呢,就好比用不合脚的鞋走路,多别扭呀!
5. 压铸工艺可得把握好分寸啊!它就像是做菜时的火候,太轻太重都不行呀!要是工艺不对,那出来的产品可能就有缺陷啦,比如有气泡什么的,那多糟糕呀!就像烤蛋糕没掌握好温度一样。
6. 材料选择可不能随便呀!这就如同选食材,得挑好的呀!要是材料不好,那压铸出来的产品能好到哪里去呢?像优质的铝合金,才能保证产品的质量呢。
7. 生产效率也很重要呢,你说是不是?这就好像比赛跑步,谁快谁就有优势呀!如果生产效率低,怎么跟别人竞争呀,尤其在量大的时候,不快怎么行呢!就好像打仗,速度可不能慢。
8. 质量检测绝对不能少哇!这就像是给产品做体检,有毛病就得赶紧治呀!不检测怎么知道产品合不合格呢,不管是小瑕疵还是大问题,都得检测出来呀!就像给病人看病一样仔细。
我的观点结论就是:铝压铸技术要求真的很多,每一项都非常重要,都需要我们认真对待,这样才能生产出高质量的铝压铸产品啊!。
铝合金压铸技术要求汇总-共8页
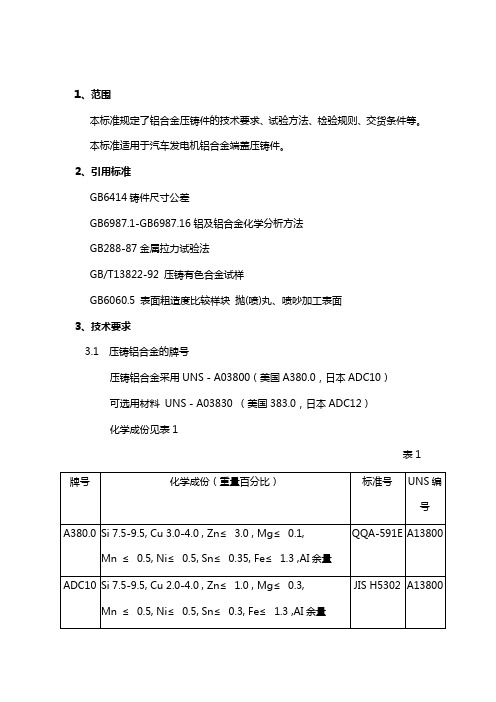
1、范围本标准规定了铝合金压铸件的技术要求、试验方法、检验规则、交货条件等。
本标准适用于汽车发电机铝合金端盖压铸件。
2、引用标准GB6414铸件尺寸公差GB6987.1-GB6987.16铝及铝合金化学分析方法GB288-87金属拉力试验法GB/T13822-92 压铸有色合金试样GB6060.5 表面粗造度比较样块抛(喷)丸、喷吵加工表面3、技术要求3.1 压铸铝合金的牌号压铸铝合金采用UNS-A03800(美国A380.0,日本ADC10)可选用材料UNS-A03830 (美国383.0,日本ADC12)化学成份见表1表1供应商可选择上述四种牌号的任何一种,如在生产过程中更换其它牌号,需重新进行样件鉴定。
3.1.1回炉料使用规定3.1.1.1回炉料分类一级回炉料:浇道、化学成份合格的废铸件,后加工次品等不含水分和油污。
二级回炉料:集渣包、坩埚底部剩料、退货废品、存放时间长(超过10天)的一级回炉料。
三级回炉料:飞边、溅屑、细小的碎料、带有油污的渣料、因化学成份报废的铸件、从铝渣中捡出的铝粒。
3.1.1.2回炉料使用比例使用单一某级回炉料:一级回炉料最大使用量50%,二级回炉料最大使用量40%。
一级、二级回炉料混合使用:回炉料总量不超过40%,其中二级回炉料最大使用量20%。
三级回炉料:不能直接使用,必须经过重熔、精炼且化学成份分析合格后才能使用,其最大使用量10%,仅与铝锭混合使用。
3.1.1.3加料循序小颗粒回炉料大块回炉料铝锭,如此循环。
3.2 力学性能采用单铸拉力试样检验,其力学性能应满足抗拉强度≥240Mpa,伸长率≥1%,HB85(5/250/30)。
试样尺寸及形状应符合GB/T 13822-92《压铸有色合金试样》的规定。
3.3 压铸件尺寸压铸件的几何形状和尺寸应符合铸件图的规定。
3.4 待加工表面用符号“”标明,尖头指向被加工面。
例:0.5 表示该表面留有加工余量0.5mm3.5 表面质量3.5.1 铸件清理后的表面质量铸件的浇口、飞边、溢流口、隔皮等应清理干净,但允许留有清理痕迹。
铝合金压铸件一般技术要求
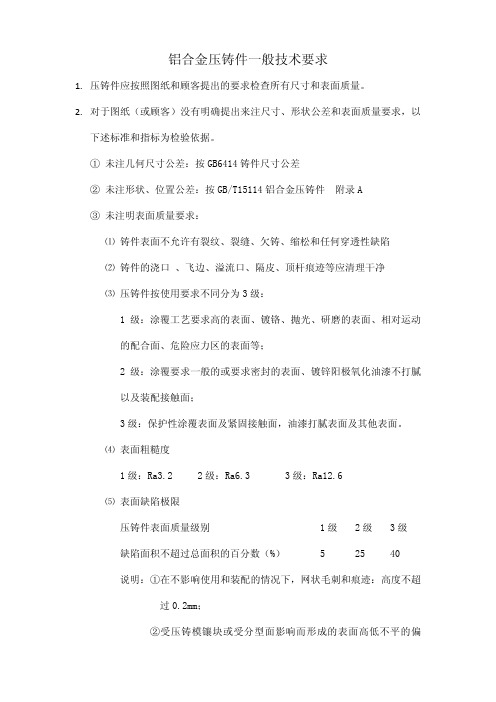
铝合金压铸件一般技术要求1.压铸件应按照图纸和顾客提出的要求检查所有尺寸和表面质量。
2.对于图纸(或顾客)没有明确提出来注尺寸、形状公差和表面质量要求,以下述标准和指标为检验依据。
①未注几何尺寸公差:按GB6414铸件尺寸公差②未注形状、位置公差:按GB/T15114铝合金压铸件 附录A③未注明表面质量要求:⑴铸件表面不允许有裂纹、裂缝、欠铸、缩松和任何穿透性缺陷⑵铸件的浇口 、飞边、溢流口、隔皮、顶杆痕迹等应清理干净⑶压铸件按使用要求不同分为3级:1级:涂覆工艺要求高的表面、镀铬、抛光、研磨的表面、相对运动的配合面、危险应力区的表面等;2级:涂覆要求一般的或要求密封的表面、镀锌阳极氧化油漆不打腻以及装配接触面;3级:保护性涂覆表面及紧固接触面,油漆打腻表面及其他表面。
⑷表面粗糙度1级:Ra3.2 2级:Ra6.3 3级:Ra12.6⑸表面缺陷极限压铸件表面质量级别 1级 2级 3级缺陷面积不超过总面积的百分数(%) 5 25 40说明:①在不影响使用和装配的情况下,网状毛刺和痕迹:高度不超过0.2mm;②受压铸模镶块或受分型面影响而形成的表面高低不平的偏差,不超过相关的公差尺寸;③推杆痕迹表面凸出或凹入铸件表面的深度,一般为±0.2mm;⑹表面质量要求(见附表)⑺挫痕:目视挫痕应均匀、一致,不允许有明显的凹凸。
经锉加工的表面和未经锉加工的表面允许有角度,但角度应在10°以内;⑻变形:压铸件成型后,如有变形应进行调整,经调整后的压铸件表面不允许有明显的打击痕迹。
调整部分的平面度:0.2mm;⑼对于顾客的特殊要求,要形成相应的工艺文件,规定其相关的工艺过程和检验方法。
总工办2003年4月附表: 缺陷名称 缺陷范围表面质量级别 备注 1级2级 3级 流痕深度(mm )≤ 0.05 0.07 0.15 面积不超过总面积的百分数515 30冷隔深度(mm )≤ 不允许1/5壁厚 1/4壁厚 1. 在同一部分对应出不允许同时存在 2. 长度是指缺陷流向的展开长度长度不大于铸件的最大轮廓尺寸的(mm ) 1/101/5所在面上的不允许超过的数量 2处 2处 离铸件边缘距离(mm )≥ 4 4 两冷隔间距(mm )≥10 10 拉伤深度(mm )≤ 0.05 0.1 0.25 除一级表面外,浇道部位允许增加一倍 面积不超过总面积的百分数35 10 凹陷 凹入深度(mm ) 0.10.3 0.5 粘附物痕迹整个铸件缺陷不允许超过 不允许1处 2处 占带缺陷的表面面积的百分比5 10气泡平均直径≤3mm1.每100cm 2缺陷个数不超过 不允许 1 2 允许两种气泡同时存在,但大气泡不超过3个,总数不超过10个。
压铸件技术要求
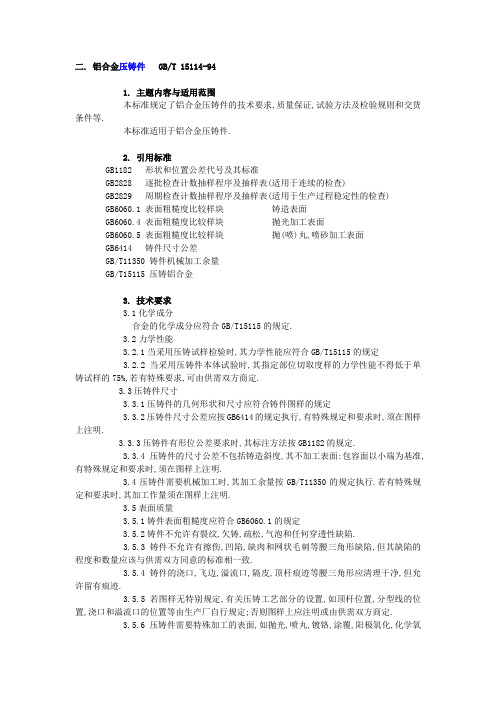
二. 铝合金压铸件 GB/T 15114-941. 主题内容与适用范围本标准规定了铝合金压铸件的技术要求,质量保证,试验方法及检验规则和交货条件等.本标准适用于铝合金压铸件.2. 引用标准GB1182 形状和位置公差代号及其标准GB2828 逐批检查计数抽样程序及抽样表(适用于连续的检查)GB2829 周期检查计数抽样程序及抽样表(适用于生产过程稳定性的检查)GB6060.1 表面粗糙度比较样块铸造表面GB6060.4 表面粗糙度比较样块抛光加工表面GB6060.5 表面粗糙度比较样块抛(喷)丸,喷砂加工表面GB6414 铸件尺寸公差GB/T11350 铸件机械加工余量GB/T15115 压铸铝合金3. 技术要求3.1化学成分合金的化学成分应符合GB/T15115的规定.3.2力学性能3.2.1当采用压铸试样检验时,其力学性能应符合GB/T15115的规定3.2.2当采用压铸件本体试验时,其指定部位切取度样的力学性能不得低于单铸试样的75%,若有特殊要求,可由供需双方商定.3.3压铸件尺寸3.3.1压铸件的几何形状和尺寸应符合铸件图样的规定3.3.2压铸件尺寸公差应按GB6414的规定执行,有特殊规定和要求时,须在图样上注明.3.3.3压铸件有形位公差要求时,其标注方法按GB1182的规定.3.3.4压铸件的尺寸公差不包括铸造斜度,其不加工表面:包容面以小端为基准,有特殊规定和要求时,须在图样上注明.3.4压铸件需要机械加工时,其加工余量按GB/T11350的规定执行.若有特殊规定和要求时,其加工作量须在图样上注明.3.5表面质量3.5.1铸件表面粗糙度应符合GB6060.1的规定3.5.2铸件不允许有裂纹,欠铸,疏松,气泡和任何穿透性缺陷.3.5.3铸件不允许有擦伤,凹陷,缺肉和网状毛刺等腰三角形缺陷,但其缺陷的程度和数量应该与供需双方同意的标准相一致.3.5.4铸件的浇口,飞边,溢流口,隔皮,顶杆痕迹等腰三角形应清理干净,但允许留有痕迹.3.5.5若图样无特别规定,有关压铸工艺部分的设置,如顶杆位置,分型线的位置,浇口和溢流口的位置等由生产厂自行规定;否则图样上应注明或由供需双方商定.3.5.6压铸件需要特殊加工的表面,如抛光,喷丸,镀铬,涂覆,阳极氧化,化学氧化等须在图样上注明或由供需双方商定.3.6内部质量3.6.1压铸件若能满足其使用要求,则压铸件本质缺陷不作为报废的依据.3.6.2对压铸件的气压密封性,液压密封性,热处理,高温涂覆,内部缺陷(气孔,疏孔,冷隔,夹杂)及本标准未列项目有要求时,可由供需双方商定.3.6.3在不影响压铸件使用的条件下,当征得需方同意,供方可以对压铸件进行浸渗和修补(如焊补,变形校整等)处理.4. 质量保证4.1当供需双方合同或协议中有规定时,供方对合同中规定的所有试验或检验负责.合同或协议中无规定时,经需方同意,供方可以用自已适宜的手段执行本标准所规定的试验和要求,需方有权对标准中的任何试验和检验项目进行检验,其质量保证标准应根据供需双方之间的协议而定.4.2根据压铸生产特点,规定一个检验批量是指每台压铸设备在正常操作情况下一个班次的生产量,设备,化学成分,铸型和操作连续性的任何重大变化都应被认为是新是一个批量开始.供方对每批压铸件都要随机或统计地抽样检验,确定是否符合全部技术要求和合同或铸件图样的规定要求,检验结果应予以记录.5. 试验方法及检验规则5.1化学成分5.1.1合金化学成分的检验方法,检验规则和复检应符合GB/T15115的规定.5.1.2化学成分的试样也可取自压铸件,但必须符合GB/T15115的规定5.2力学性能5.2.1力学性能的检验方法,检验频率和检验规则就符合GB/T15115的规定.5.2.2采用压铸件本体为试样时,切取部位尺寸,测试形式由供需双方商定.5.3压铸件几何尺寸的检验可按检验批量抽验或按GB2828,GB2829的规定进行,抽检结果必须符合标准3.3的规定.5.4压铸件表面质量就逐检查,检查结果应符合本标准3.5的规定.5.5压铸件表面粗糙度按GB6060.1的规定执行.5.6压铸件需抛光加工的表面按GB6060.4的规定执行,5.7压铸件需喷丸,喷砂加工的表面按GB6060.5的规定执行.5.8压铸件内部质量的试验方法检验规则由供需双方商定,可以包括:X射线照片,无损探伤,耐压试验,金相图片和压铸件剖面等,其检难结果应符合3.6的规定.5.9经浸渗和修补处理后的压铸件应做相应的质量检验.技术要求1.1化学成分:合金的化学成分应符合GB/T15115的规定.1.2力学性能:1.2.1当采用压铸试样检验时,其力学性能应符合GB/T15115的规定.1.2.2当采用压铸件本体试验时,其指定部位切取度样的力学性能不得低于单铸试样的75%,若有特殊要求,可由供需双方商定.1.3压铸件尺寸:1.3.1压铸件的几何形状和尺寸应符合铸件图样的规定.1.3.2压铸件尺寸公差应按GB6414的规定执行,特殊规定和要求按图样上注明.1.3.3压铸件有形位公差要求时,其标注按GB1182的规定.1.3.4压铸件的尺寸公差不包括铸造斜度,其不加工表面:包容面以小端为基准,特殊规定和要求按图样上注明.1.4压铸件需要机械加工时,其加工余量按GB/T11350的规定执行.若有特殊规定和要求时,其加工作量根据图样上注明.1.5表面质量:1.5.1铸件表面粗糙度应符合GB6060.1的规定1.5.2铸件不允许有裂纹,欠铸,疏松,气泡和任何穿透性缺陷.1.5.3铸件不允许有擦伤,凹陷,缺肉和网状毛刺等腰三角形缺陷,但其缺陷的程度和数量应该与供需双方同意的标准相一致.1.5.4铸件的浇口,飞边,溢流口,隔皮,顶杆痕迹等腰三角形应清理干净,但允许留有痕迹.1.5.5若图样无特别规定,有关压铸工艺部分的设置,如顶杆位置,分型线的位置,浇口和溢流口的位置等由生产厂自行规定;否则按图样所注明或由供需双方商定.1.5.6压铸件需要特殊加工的表面,如抛光,喷丸,镀铬,涂覆,阳极氧化,化学氧化等由供需双方商定.1.6内部质量:1.6.1压铸件若能满足其使用要求,则压铸件本质缺陷不作为报废的依据.1.6.2对压铸件的气压密封性,液压密封性,热处理,高温涂覆,内部缺陷(气孔,疏孔,冷隔,夹杂)及本标准未列项目有要求时,可由供需双方商定.1.6.3在不影响压铸件使用的条件下,当征得需方同意,供方可以对压铸件进行浸渗和修补(如焊补,变形校整等)处理.。
标准铝压铸工艺参数表

标准铝压铸工艺参数表1. 压铸温度。
铝合金的压铸温度是影响产品质量的重要参数之一。
通常情况下,铝合金的压铸温度在650°C至750°C之间。
过高的温度会导致产品熔融不均匀,而过低的温度则会造成产品表面粗糙。
因此,在实际生产中,需要根据具体的铝合金材料选择合适的压铸温度。
2. 压射速度。
压射速度是指铝合金液态金属进入模腔的速度。
适当的压射速度可以确保产品充填充分,避免气孔和夹杂物的产生。
一般来说,压射速度应根据产品的形状和尺寸进行调整,以保证产品的成型质量。
3. 模具温度。
模具温度对铝合金压铸产品的表面质量和尺寸精度有着重要影响。
过高或过低的模具温度都会导致产品的缺陷,因此需要根据具体的铝合金材料和产品要求来确定合适的模具温度。
4. 注射压力。
注射压力是指压铸机对铝合金液态金属施加的压力。
适当的注射压力可以确保产品充填充分,避免产品内部产生气孔和夹杂物。
在实际生产中,需要根据产品的形状和尺寸来确定合适的注射压力。
5. 冷却时间。
冷却时间是指产品在模具中冷却的时间。
适当的冷却时间可以确保产品的尺寸精度和表面质量。
通常情况下,冷却时间需要根据产品的厚度和材料来确定,以确保产品达到理想的硬度和强度。
6. 顶杆力。
顶杆力是指顶出铝合金产品的力量。
适当的顶杆力可以确保产品顺利脱模,避免产品变形和损坏。
在实际生产中,需要根据产品的形状和尺寸来确定合适的顶杆力。
7. 模具开合力。
模具开合力是指模具在开合过程中所受的力量。
适当的模具开合力可以确保模具的正常运行,避免模具损坏和产品缺陷。
在实际生产中,需要根据模具的结构和尺寸来确定合适的模具开合力。
总结:以上是标准铝压铸工艺参数表的相关内容,希望能对大家在铝合金压铸加工过程中有所帮助。
在实际生产中,需要根据具体的产品要求和铝合金材料来确定合适的工艺参数,以确保产品质量和生产效率。
同时,也需要不断优化和调整工艺参数,以适应市场和客户需求的变化。
希望大家能够加强学习和实践,不断提升铝合金压铸加工的技术水平和质量管理水平。
压铸铝技术参数
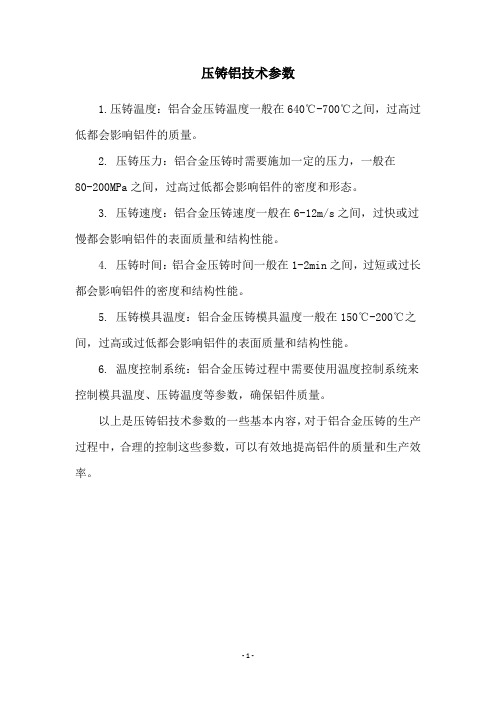
压铸铝技术参数
1.压铸温度:铝合金压铸温度一般在640℃-700℃之间,过高过低都会影响铝件的质量。
2. 压铸压力:铝合金压铸时需要施加一定的压力,一般在
80-200MPa之间,过高过低都会影响铝件的密度和形态。
3. 压铸速度:铝合金压铸速度一般在6-12m/s之间,过快或过慢都会影响铝件的表面质量和结构性能。
4. 压铸时间:铝合金压铸时间一般在1-2min之间,过短或过长都会影响铝件的密度和结构性能。
5. 压铸模具温度:铝合金压铸模具温度一般在150℃-200℃之间,过高或过低都会影响铝件的表面质量和结构性能。
6. 温度控制系统:铝合金压铸过程中需要使用温度控制系统来控制模具温度、压铸温度等参数,确保铝件质量。
以上是压铸铝技术参数的一些基本内容,对于铝合金压铸的生产过程中,合理的控制这些参数,可以有效地提高铝件的质量和生产效率。
- 1 -。
锌合金、铜合金、铝合金压铸件技术条件

中华人民共和国第一机械工业部部标准锌合金、铝合金、铜合金压铸件技术条件JB 2702—80北京1981中华人民共和国第一机械工业部部标准JB 2702—80 锌合金、铝合金、铜合金压铸件技术条件本标准适用于机电、仪表、汽车、拖拉机等机械工业产品的锌合金、铝合金、铜合金压铸件(以下简称铸件)。
对有特殊要求的铸件,经商议后应在图样中注明。
一、铸件分类及级别1.铸件按使用要求分为两类,见表1。
2.铸件表面质量按使用范围分为三级,见表2。
3.铸件的类别和表面质量的级别应在图样中注明,表示方法如下:Ⅱ-∽铸件表面质量级别铸件分类类别铸件标准代号如有更高要求的部位应在图样中有关面处分别注明。
4.未注明铸件类别、级别和尺寸精度者,均按本标准相关的最低级别处理。
二、尺寸精度5.铸件线性尺寸公差才选用中华人民共和国第一机械工业部发布 1 9 8 1 年 1 月 1 日实施一机部沈阳铸造研究所提出上海电器压铸三、上海电表厂等起草共11页第2页 JB 2702—80⑴铸件的基本尺寸公差按表3选用。
铸件受分型面或模具活动部位影响的尺寸应按表4、表5规定,在基本尺寸公差上再加附加公差。
铸件基本尺寸公差表3线性尺寸受分型面影响时的附加公差表4线性尺寸受模具活动部位影响时的附加公差表5注:一模多铸时,铸件分型面上的投影面积为各铸件投影面积之和附加公差应用示例:JB 2702—80 共11页第3页1 铝合金压铸件的尺寸A为3+0.12mm(基本公差按7级精度),模具活动部位由成形滑块构成,其投影面积为34cm2,由表5查得其附加公差为0.20mm,则A的尺寸公差应为0.12+0.20=0.32(mm) 。
2 在同一铸件上尺寸B为2.5+0.12mm(基本公差按7级精度),模具活动部位由滑块型芯构成,型芯直径为20mm,则其投影面积为3.14cm2,由表5查得其附加公差为0.15mm,则B处的尺寸公并为+0.12/-0.15。
⑵尺寸公差带的位置a.不加工的配合尺寸,孔取正(+),轴取负(-)。
铝合金压铸件综合技术条件(总11页)
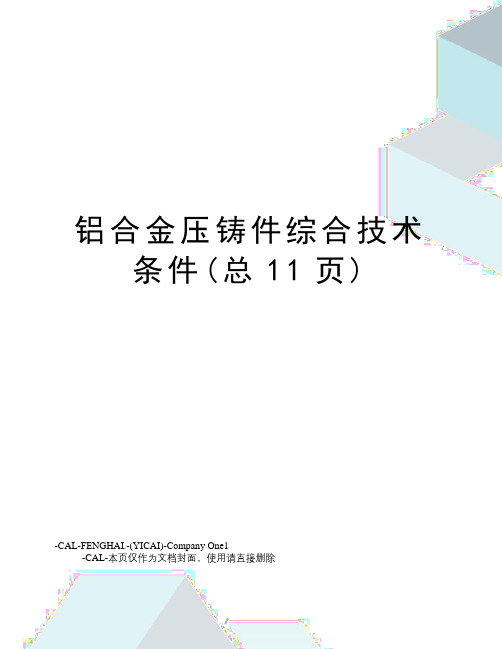
铝合金压铸件综合技术条件(总11页)-CAL-FENGHAI.-(YICAI)-Company One1-CAL-本页仅作为文档封面,使用请直接删除1 主题内容与适用范围本标准根据GB 1173及GB 9438的相关内容,规定了铝合金铸件的分类和铸件的外观质量、内在质量以及铸件修补等内容的技术要求与检验规则等。
本标准适用于铝硅系合金铸件的砂型铸造、特种铸造(不含压力铸造)。
2 一般规定2.1 合金牌号2.1.1 铸造铝合金牌号由铝及主要合金元素的化学成分符号组成。
主要合金元素后面跟有表示其名义百分含量的数字(名义百分含量为该元素的平均百分含量的修约化整值)。
如果合金化元素的名义百分含量不小于1,该数字用整数表示;如果合金化元素的名义百分含量小于1,一般不标数字,必要时可用一位小数表示。
在合金牌号前面冠以字母“Z”(“铸”字汉语拼音第一个字母)表示属于铸造合金。
2.1.2 若合金化元素多于两个,除对表示合金的本质特性是必不可少的外,不必把所有的合金化元素都列在牌号中。
2.1.3 杂质含量较一般合金低、性能高的优质合金,在其牌号后面附加字母“A”。
2.1.4 在牌号中主要合金化元素按名义百分含量的递减次序排列,当名义百分含量相等时,按其化学符号字母顺序排列。
2.2 合金代号本标准中合金代号由字母“Z”、“L”(它们分别是“铸”、“铝”的汉语拼音第一个字母)及其后面的三个阿拉伯数字组成。
“ZL”后面第一个数字表示合金系列,其中“1”表示铝硅系列合金,第二、三两个数字表示顺序号。
优质合金,在其代号后面附加字母“A”。
引用顾客提供的材料标准时,其代号按原用代号不变。
2.3 合金铸造方法、变质处理代号S——砂型铸造J——金属型铸造R——熔模铸造K——壳型铸造B——变质处理2.4 合金状态代号F——铸态T1——人工时效T2——退火T4——固溶处理+自然时效T5——固溶处理+不完全人工时效T6——固溶处理+完全人工时效T7——固溶处理+稳定化处理T8——固溶处理+软化处理2.5 数字修约规则合金牌号中合金化元素的名义百分含量、合金化学成分、合金性能等数字修约按GB 1.1中附录C规定。
铝合金压铸件一般技术要求

铝合金压铸件一般技术要求铝合金压铸件是利用铝合金熔体通过高压注射进入金属模具中,通过自身的凝固过程形成的零件。
它具有良好的综合性能,广泛应用于各个领域,如汽车、航空航天、电子等。
为了保证铝合金压铸件的质量和可靠性,有一系列一般技术要求需要遵守。
首先,铝合金压铸件的设计要合理。
合理的设计能保证零件的结构和尺寸满足使用要求,避免因结构设计不当而导致的铝合金压铸件质量问题。
设计时应考虑铝合金材料的特性和成型工艺,合理布置加强筋和放大壁厚等措施,确保压铸件有足够的强度和刚度。
其次,材料的选择要合适。
铝合金压铸件一般采用高强度、高导热性的铝合金材料,如ADC12、A380等。
材料的选择要符合使用环境的要求,具有良好的耐热、耐腐蚀、耐磨损和耐腐蚀性能。
材料的选择还需要考虑成本因素,以保证生产的经济性。
第三,模具的制造要精确。
模具的精度和质量对铝合金压铸件的成型质量起着重要的影响。
模具制造应严格按照设计要求进行,尺寸精度应达到零件的使用要求。
模具材料一般选用精密,耐磨耐热的材料,如合金钢、硬质合金等,以保证模具的耐用性和寿命。
第四,操作工艺要规范。
铝合金压铸件的压铸过程需要控制压铸机的参数,如注射速度、注射压力和注入时间等。
同时,还需要注意合金的热处理和退火工艺,以提高原材料的性能和细化晶粒。
此外,还需要对压铸件进行后处理,如除霜、抽调、清洗和表面处理等,以保证铝合金压铸件的表面质量和使用寿命。
最后,质量检查要全面。
对铝合金压铸件进行全面的质量检查是确保产品质量的重要手段之一、常用的检查方法有外观检查、尺寸检查、物理性能测试、金相组织分析等。
通过严格的质量检查,可以及时发现和纠正问题,保证产品的合格率和一致性。
综上所述,铝合金压铸件的一般技术要求涉及设计、材料、模具、操作工艺和质量检查等方面,通过科学的设计和精确的制造工艺,可以生产出质量可靠的铝合金压铸件,满足不同领域的使用需求。
铝合金压铸技术要求
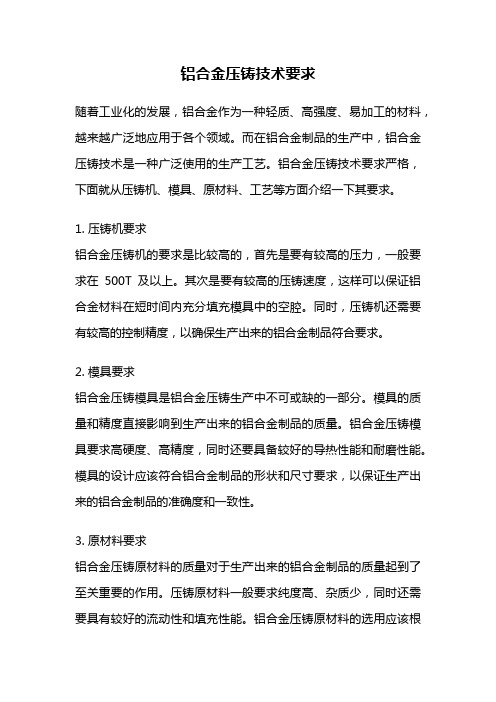
铝合金压铸技术要求随着工业化的发展,铝合金作为一种轻质、高强度、易加工的材料,越来越广泛地应用于各个领域。
而在铝合金制品的生产中,铝合金压铸技术是一种广泛使用的生产工艺。
铝合金压铸技术要求严格,下面就从压铸机、模具、原材料、工艺等方面介绍一下其要求。
1. 压铸机要求铝合金压铸机的要求是比较高的,首先是要有较高的压力,一般要求在500T及以上。
其次是要有较高的压铸速度,这样可以保证铝合金材料在短时间内充分填充模具中的空腔。
同时,压铸机还需要有较高的控制精度,以确保生产出来的铝合金制品符合要求。
2. 模具要求铝合金压铸模具是铝合金压铸生产中不可或缺的一部分。
模具的质量和精度直接影响到生产出来的铝合金制品的质量。
铝合金压铸模具要求高硬度、高精度,同时还要具备较好的导热性能和耐磨性能。
模具的设计应该符合铝合金制品的形状和尺寸要求,以保证生产出来的铝合金制品的准确度和一致性。
3. 原材料要求铝合金压铸原材料的质量对于生产出来的铝合金制品的质量起到了至关重要的作用。
压铸原材料一般要求纯度高、杂质少,同时还需要具有较好的流动性和填充性能。
铝合金压铸原材料的选用应该根据铝合金制品的要求和生产工艺来进行选择。
4. 工艺要求铝合金压铸技术的工艺要求主要包括模具温度、压铸温度、压铸速度等。
模具温度一般要求在200℃以上,以保证铝合金材料充分流动。
压铸温度要求控制在合适的范围内,过高会导致铝合金材料产生气孔,过低则会导致铝合金材料填充不充分。
压铸速度也要根据铝合金制品的要求和生产工艺来进行调整。
铝合金压铸技术要求严格,需要从多个方面考虑,才能生产出符合要求和标准的铝合金制品。
同时,压铸技术的不断创新和完善,也为铝合金制品的生产提供了更好的技术支持。
铝合金压铸件一般技术要求

铝合金压铸件一般技术要求铝合金压铸件这玩意儿,在咱们的日常生活和工业生产里那可真是太常见啦!小到一个精致的手机外壳,大到汽车发动机的零部件,都可能有它的身影。
咱先来说说铝合金压铸件的材质要求吧。
这铝合金啊,可不能是随随便便的材料。
它得有足够的强度和韧性,就像一个强壮又灵活的运动员,既能承受住压力,又不会轻易折断。
比如说,有一次我在一个工厂里看到师傅们在检测铝合金的成分,那叫一个仔细!拿着各种仪器,一点点分析,就怕有一点点杂质影响了最终的质量。
再说说尺寸精度吧。
这可太重要啦!要是尺寸不对,那整个零件可能就没法用了。
就好比你盖房子,砖头的大小不合适,那这房子能结实吗?我曾经看到过一个因为压铸件尺寸偏差导致组装不顺利的情况,工人们在那着急得直挠头,真是让人印象深刻。
表面质量也是不容忽视的。
这表面得光滑平整,不能有气孔、砂眼之类的缺陷。
想象一下,你买了个漂亮的铝合金制品,结果表面坑坑洼洼的,多闹心啊!有一回我看到一个精美的铝合金工艺品,那表面简直就像镜子一样光滑,让人爱不释手。
还有啊,铝合金压铸件的内部组织也得均匀致密。
不然的话,在使用过程中就容易出现裂缝或者疲劳损坏。
这就好像是一块蛋糕,如果里面有的地方松软,有的地方硬邦邦,一掰就断啦。
另外,对于铝合金压铸件的力学性能也有一定的要求。
它得有足够的硬度和抗拉强度,这样才能在各种环境下正常工作。
我记得有一次看到一个测试铝合金压铸件硬度的实验,那个测试仪器压下去的瞬间,真让人紧张,就盼着能达到标准。
总之,铝合金压铸件的一般技术要求那是相当严格的。
每一个环节都不能马虎,只有这样,才能生产出高质量的铝合金压铸件,为我们的生活和工作提供可靠的保障。
所以啊,不管是生产厂家还是使用者,都得对这些技术要求心里有数,才能让铝合金压铸件发挥出它们最大的作用!。
铝合金铸造技术要求

铝合金铸造技术要求铝合金铸造技术是一种常用的金属加工技术,广泛应用于航空航天、汽车、机械等领域。
在铝合金铸造过程中,需要满足一定的技术要求,以确保产品的质量和性能。
本文将介绍铝合金铸造技术的要求,包括合金选择、模具设计、熔炼与浇注、热处理和表面处理等方面。
一、合金选择选择合适的铝合金对于铝合金铸造至关重要。
铝合金的选择应根据产品的用途、性能要求和成本考虑。
常用的铝合金有铝硅合金、铝铜合金、铝镁合金等。
不同的合金具有不同的性能特点,如强度、耐蚀性、导热性等。
在选择合金时,需综合考虑产品的使用环境和要求,以及合金的可加工性。
二、模具设计模具设计是铝合金铸造中的关键环节。
合理的模具设计能够提高产品的质量和生产效率。
在模具设计中,需要考虑产品的结构形式、壁厚、收缩率等因素。
模具的结构应具有足够的强度和刚性,以承受铝液的冲击和热应力。
同时,模具的排气和冷却系统也需要合理设计,以避免缺陷的产生。
三、熔炼与浇注铝合金铸造的熔炼与浇注过程需要严格控制。
首先,需选择合适的熔炼设备和工艺。
熔炼设备应具备良好的加热和保温性能,以确保铝液达到适宜的浇注温度。
其次,需控制铝液的成分和温度,以确保合金的成分和性能符合要求。
在浇注过程中,应注意避免气体和杂质的混入,以减少缺陷的产生。
四、热处理热处理是提高铝合金铸造品质的重要手段。
常用的热处理方法有时效处理、固溶处理和淬火等。
热处理能够改善铝合金的强度、硬度和耐腐蚀性。
在热处理过程中,需控制加热温度、保温时间和冷却速率,以确保合金的组织和性能达到预期目标。
五、表面处理表面处理是铝合金铸造的最后一道工序,能够提高产品的外观和耐腐蚀性。
常用的表面处理方法有阳极氧化、电泳涂装和喷涂等。
表面处理能够形成保护膜,防止铝合金与外界环境的接触,延长产品的使用寿命。
铝合金铸造技术要求包括合金选择、模具设计、熔炼与浇注、热处理和表面处理等方面。
合理选择合金、设计模具、控制熔炼与浇注过程、进行合适的热处理和表面处理,能够确保铝合金铸造产品的质量和性能,满足用户的需求。
铝合金压铸件综合技术条件(拉力).

1 主题内容与适用范围本标准根据GB 1173及GB 9438的相关内容,规定了铝合金铸件的分类和铸件的外观质量、内在质量以及铸件修补等内容的技术要求与检验规则等。
本标准适用于铝硅系合金铸件的砂型铸造、特种铸造(不含压力铸造)。
2 一般规定2.1 合金牌号2.1.1 铸造铝合金牌号由铝及主要合金元素的化学成分符号组成。
主要合金元素后面跟有表示其名义百分含量的数字(名义百分含量为该元素的平均百分含量的修约化整值)。
如果合金化元素的名义百分含量不小于1,该数字用整数表示;如果合金化元素的名义百分含量小于1,一般不标数字,必要时可用一位小数表示。
在合金牌号前面冠以字母“Z”(“铸”字汉语拼音第一个字母)表示属于铸造合金。
2.1.2 若合金化元素多于两个,除对表示合金的本质特性是必不可少的外,不必把所有的合金化元素都列在牌号中。
2.1.3 杂质含量较一般合金低、性能高的优质合金,在其牌号后面附加字母“A”。
2.1.4 在牌号中主要合金化元素按名义百分含量的递减次序排列,当名义百分含量相等时,按其化学符号字母顺序排列。
2.2 合金代号本标准中合金代号由字母“Z”、“L”(它们分别是“铸”、“铝”的汉语拼音第一个字母)及其后面的三个阿拉伯数字组成。
“ZL”后面第一个数字表示合金系列,其中“1”表示铝硅系列合金,第二、三两个数字表示顺序号。
优质合金,在其代号后面附加字母“A”。
引用顾客提供的材料标准时,其代号按原用代号不变。
2.3 合金铸造方法、变质处理代号S——砂型铸造J——金属型铸造R——熔模铸造K——壳型铸造B——变质处理2.4 合金状态代号F——铸态T1——人工时效T2——退火T4——固溶处理+自然时效T5——固溶处理+不完全人工时效T6——固溶处理+完全人工时效T7——固溶处理+稳定化处理T8——固溶处理+软化处理2.5 数字修约规则合金牌号中合金化元素的名义百分含量、合金化学成分、合金性能等数字修约按GB 1.1中附录C规定。
压铸件技术要求
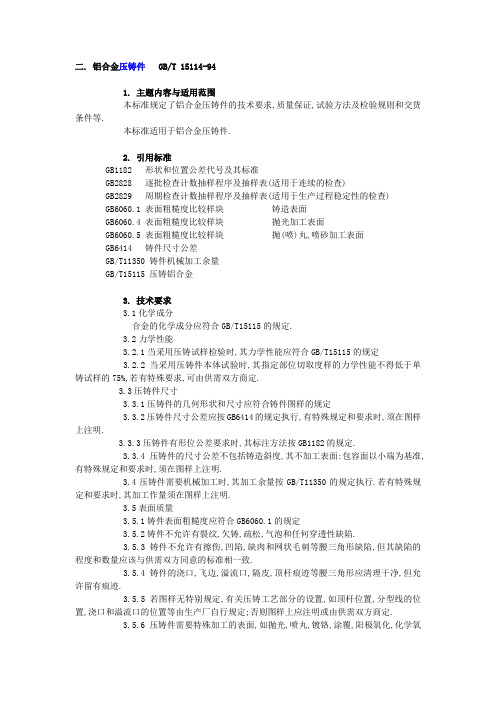
二. 铝合金压铸件 GB/T 15114-941. 主题内容与适用范围本标准规定了铝合金压铸件的技术要求,质量保证,试验方法及检验规则和交货条件等.本标准适用于铝合金压铸件.2. 引用标准GB1182 形状和位置公差代号及其标准GB2828 逐批检查计数抽样程序及抽样表(适用于连续的检查)GB2829 周期检查计数抽样程序及抽样表(适用于生产过程稳定性的检查)GB6060.1 表面粗糙度比较样块铸造表面GB6060.4 表面粗糙度比较样块抛光加工表面GB6060.5 表面粗糙度比较样块抛(喷)丸,喷砂加工表面GB6414 铸件尺寸公差GB/T11350 铸件机械加工余量GB/T15115 压铸铝合金3. 技术要求3.1化学成分合金的化学成分应符合GB/T15115的规定.3.2力学性能3.2.1当采用压铸试样检验时,其力学性能应符合GB/T15115的规定3.2.2当采用压铸件本体试验时,其指定部位切取度样的力学性能不得低于单铸试样的75%,若有特殊要求,可由供需双方商定.3.3压铸件尺寸3.3.1压铸件的几何形状和尺寸应符合铸件图样的规定3.3.2压铸件尺寸公差应按GB6414的规定执行,有特殊规定和要求时,须在图样上注明.3.3.3压铸件有形位公差要求时,其标注方法按GB1182的规定.3.3.4压铸件的尺寸公差不包括铸造斜度,其不加工表面:包容面以小端为基准,有特殊规定和要求时,须在图样上注明.3.4压铸件需要机械加工时,其加工余量按GB/T11350的规定执行.若有特殊规定和要求时,其加工作量须在图样上注明.3.5表面质量3.5.1铸件表面粗糙度应符合GB6060.1的规定3.5.2铸件不允许有裂纹,欠铸,疏松,气泡和任何穿透性缺陷.3.5.3铸件不允许有擦伤,凹陷,缺肉和网状毛刺等腰三角形缺陷,但其缺陷的程度和数量应该与供需双方同意的标准相一致.3.5.4铸件的浇口,飞边,溢流口,隔皮,顶杆痕迹等腰三角形应清理干净,但允许留有痕迹.3.5.5若图样无特别规定,有关压铸工艺部分的设置,如顶杆位置,分型线的位置,浇口和溢流口的位置等由生产厂自行规定;否则图样上应注明或由供需双方商定.3.5.6压铸件需要特殊加工的表面,如抛光,喷丸,镀铬,涂覆,阳极氧化,化学氧化等须在图样上注明或由供需双方商定.3.6内部质量3.6.1压铸件若能满足其使用要求,则压铸件本质缺陷不作为报废的依据.3.6.2对压铸件的气压密封性,液压密封性,热处理,高温涂覆,内部缺陷(气孔,疏孔,冷隔,夹杂)及本标准未列项目有要求时,可由供需双方商定.3.6.3在不影响压铸件使用的条件下,当征得需方同意,供方可以对压铸件进行浸渗和修补(如焊补,变形校整等)处理.4. 质量保证4.1当供需双方合同或协议中有规定时,供方对合同中规定的所有试验或检验负责.合同或协议中无规定时,经需方同意,供方可以用自已适宜的手段执行本标准所规定的试验和要求,需方有权对标准中的任何试验和检验项目进行检验,其质量保证标准应根据供需双方之间的协议而定.4.2根据压铸生产特点,规定一个检验批量是指每台压铸设备在正常操作情况下一个班次的生产量,设备,化学成分,铸型和操作连续性的任何重大变化都应被认为是新是一个批量开始.供方对每批压铸件都要随机或统计地抽样检验,确定是否符合全部技术要求和合同或铸件图样的规定要求,检验结果应予以记录.5. 试验方法及检验规则5.1化学成分5.1.1合金化学成分的检验方法,检验规则和复检应符合GB/T15115的规定.5.1.2化学成分的试样也可取自压铸件,但必须符合GB/T15115的规定5.2力学性能5.2.1力学性能的检验方法,检验频率和检验规则就符合GB/T15115的规定.5.2.2采用压铸件本体为试样时,切取部位尺寸,测试形式由供需双方商定.5.3压铸件几何尺寸的检验可按检验批量抽验或按GB2828,GB2829的规定进行,抽检结果必须符合标准3.3的规定.5.4压铸件表面质量就逐检查,检查结果应符合本标准3.5的规定.5.5压铸件表面粗糙度按GB6060.1的规定执行.5.6压铸件需抛光加工的表面按GB6060.4的规定执行,5.7压铸件需喷丸,喷砂加工的表面按GB6060.5的规定执行.5.8压铸件内部质量的试验方法检验规则由供需双方商定,可以包括:X射线照片,无损探伤,耐压试验,金相图片和压铸件剖面等,其检难结果应符合3.6的规定.5.9经浸渗和修补处理后的压铸件应做相应的质量检验.技术要求1.1化学成分:合金的化学成分应符合GB/T15115的规定.1.2力学性能:1.2.1当采用压铸试样检验时,其力学性能应符合GB/T15115的规定.1.2.2当采用压铸件本体试验时,其指定部位切取度样的力学性能不得低于单铸试样的75%,若有特殊要求,可由供需双方商定.1.3压铸件尺寸:1.3.1压铸件的几何形状和尺寸应符合铸件图样的规定.1.3.2压铸件尺寸公差应按GB6414的规定执行,特殊规定和要求按图样上注明.1.3.3压铸件有形位公差要求时,其标注按GB1182的规定.1.3.4压铸件的尺寸公差不包括铸造斜度,其不加工表面:包容面以小端为基准,特殊规定和要求按图样上注明.1.4压铸件需要机械加工时,其加工余量按GB/T11350的规定执行.若有特殊规定和要求时,其加工作量根据图样上注明.1.5表面质量:1.5.1铸件表面粗糙度应符合GB6060.1的规定1.5.2铸件不允许有裂纹,欠铸,疏松,气泡和任何穿透性缺陷.1.5.3铸件不允许有擦伤,凹陷,缺肉和网状毛刺等腰三角形缺陷,但其缺陷的程度和数量应该与供需双方同意的标准相一致.1.5.4铸件的浇口,飞边,溢流口,隔皮,顶杆痕迹等腰三角形应清理干净,但允许留有痕迹.1.5.5若图样无特别规定,有关压铸工艺部分的设置,如顶杆位置,分型线的位置,浇口和溢流口的位置等由生产厂自行规定;否则按图样所注明或由供需双方商定.1.5.6压铸件需要特殊加工的表面,如抛光,喷丸,镀铬,涂覆,阳极氧化,化学氧化等由供需双方商定.1.6内部质量:1.6.1压铸件若能满足其使用要求,则压铸件本质缺陷不作为报废的依据.1.6.2对压铸件的气压密封性,液压密封性,热处理,高温涂覆,内部缺陷(气孔,疏孔,冷隔,夹杂)及本标准未列项目有要求时,可由供需双方商定.1.6.3在不影响压铸件使用的条件下,当征得需方同意,供方可以对压铸件进行浸渗和修补(如焊补,变形校整等)处理.。
铝合金压铸件标准
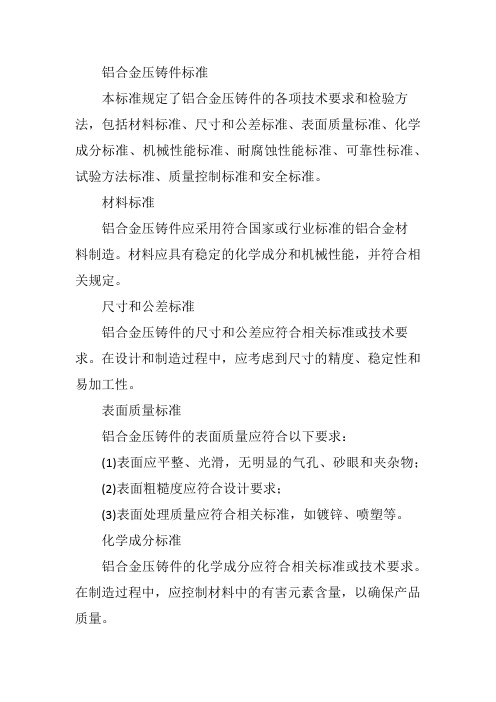
铝合金压铸件标准本标准规定了铝合金压铸件的各项技术要求和检验方法,包括材料标准、尺寸和公差标准、表面质量标准、化学成分标准、机械性能标准、耐腐蚀性能标准、可靠性标准、试验方法标准、质量控制标准和安全标准。
材料标准铝合金压铸件应采用符合国家或行业标准的铝合金材料制造。
材料应具有稳定的化学成分和机械性能,并符合相关规定。
尺寸和公差标准铝合金压铸件的尺寸和公差应符合相关标准或技术要求。
在设计和制造过程中,应考虑到尺寸的精度、稳定性和易加工性。
表面质量标准铝合金压铸件的表面质量应符合以下要求:(1)表面应平整、光滑,无明显的气孔、砂眼和夹杂物;(2)表面粗糙度应符合设计要求;(3)表面处理质量应符合相关标准,如镀锌、喷塑等。
化学成分标准铝合金压铸件的化学成分应符合相关标准或技术要求。
在制造过程中,应控制材料中的有害元素含量,以确保产品质量。
机械性能标准铝合金压铸件的机械性能应符合相关标准或技术要求,包括抗拉强度、屈服强度、延伸率和硬度等指标。
在制造过程中,应采用合理的工艺参数和热处理制度,以确保产品具有良好的机械性能。
耐腐蚀性能标准铝合金压铸件应具有良好的耐腐蚀性能,以适应不同的使用环境。
在制造过程中,应采用适当的表面处理方法,以提高产品的耐腐蚀性能。
可靠性标准铝合金压铸件应具有较高的可靠性,以确保在使用过程中不会出现故障或损坏。
在制造过程中,应采用合理的工艺参数和材料,并进行严格的检验和控制,以确保产品的可靠性和稳定性。
试验方法标准铝合金压铸件的各项技术要求和检验方法应符合相关标准或技术要求。
在制造过程中,应按照规定的试验方法进行检验和测试,以确保产品质量符合要求。
质量控制标准铝合金压铸件的质量控制应贯穿整个制造过程,包括材料采购、加工、热处理、表面处理等环节。
在制造过程中,应建立完善的质量控制体系,并进行严格的检验和控制,以确保产品质量符合要求。
安全标准铝合金压铸件的安全标准应符合相关国家或行业标准的要求。
- 1、下载文档前请自行甄别文档内容的完整性,平台不提供额外的编辑、内容补充、找答案等附加服务。
- 2、"仅部分预览"的文档,不可在线预览部分如存在完整性等问题,可反馈申请退款(可完整预览的文档不适用该条件!)。
- 3、如文档侵犯您的权益,请联系客服反馈,我们会尽快为您处理(人工客服工作时间:9:00-18:30)。
湖北德科雷米公司编号:ES-301条件术铝合金压铸件技版本:07产品规范页号:1/8、范围1术要求、试验方法、检验规则、交货条件等。
件的技铝合金压铸本标准规定了压铸件。
合金端盖车发电机铝本标准适用于汽准2、引用标件尺寸公差铸GB6414合金化学分析方法及铝GB6987.1-GB6987.16铝法金属拉力试验GB288-87试样压铸有色合金GB/T13822-92吵加工表面)丸、喷较样块抛(喷GB6060.5表面粗造度比要求3、技术合金的牌号3.1压铸铝)ADC10(美国A380.0,日本压铸铝合金采用UNS-A03800)ADC12383.0,日本可选用材料UNS-A03830(美国1化学成份见表供应商可选择上述四种牌号的任何一种,如在生产过程中更换其它牌号,需重新进行样件鉴定。
湖北德科雷米公司编号:ES-301条件合金压铸件技术铝版本:范07产品规页号:2/8定回炉料使用规3.1.1类回炉料分3.1.1.1件,后加工次品等不含水分和油浇道、化学成份合格的废铸一级回炉料:污。
天)过10二级回炉料:集渣包、坩埚底部剩料、退货废品、存放时间长(超级回炉料。
的一污的渣料、因化学成份报回炉料:飞边、溅屑、细小的碎料、带有油三级铝粒。
渣中捡出的废的铸件、从铝回炉料使用比例3.1.1.2回炉料:一某级使用单。
40%50%,二级回炉料最大使用量一级回炉料最大使用量回炉料混合使用:级、二级一。
20%40%,其中二级回炉料最大使用量回炉料总量不超过回炉料:三级且化学成份分析合格后才能使用,其最不能直接使用,必须经过重熔、精炼铝锭混合使用。
10%,仅与大使用量加料循序3.1.1.3小颗粒回炉料大块回炉料铝锭,如此循环。
力学性能3.2率度强≥240Mpa,伸长单铸采用拉力试样检验,其力学性能应满足抗拉。
(5/250/30)HB85≥1%,试样》的规定。
《压铸有色合金应试样尺寸及形状符合GB/T13822-92件尺寸压铸3.3规定。
件的几何形状和尺寸压铸应符合铸件图的头指向被加工面。
标明,尖3.4待加工表面用符号“”0.5mm表示该表面留有加工余量例:0.5量表面质3.5量3.5.1铸件清理后的表面质留有清理痕,但允许浇口、飞边、溢流口、隔皮等应铸件的清理干净所形成的缺肉或高出均不得迹。
在不影响使用的情况下,因去除浇口、溢流口时超过壁厚的四分之一,并且不得超过1.5mm。
量质件不加工表面的铸 3.5.2.湖北德科雷米公司编号:ES-301条件铝合金压铸件技术版本:07品规范产页号:3/8铸和任何穿透性缺陷。
欠纹,3.5.2.1不允许有裂件表面高低不平的铸镶拼或受分型面影响而形成由于模具组合3.5.2.2过有关尺寸公差。
不得超偏差,壁厚过该处,深度不得超许凹入铸件表面3.5.2.3推杆痕迹不得凸起,允。
mm并不超过0.4的十分之一,许存在任何凸起的痕迹。
,配合面上不允3.5.2.4工艺基准面存在气泡或有缺孔壁不允许,孔口毛剌0.25max,3.5.2.5孔必须为穿孔现象。
肉缩孔。
许存在冷隔和3.5.2.6铸件外表面不允处理不能去除的流痕、擦伤、有色喷丸件外表面不允许存在3.5.2.7铸斑点及粘附物痕迹。
积面积不超过总0.1许存在深度不大于mm,面3.5.2.8铸件内表面允伤。
的流痕和擦15%mm,度不大于101/5壁厚,长3.5.2.9铸件内表面允许存在深度不大于4边缘距离大于10距铸件冷隔数量不超过2个,两冷隔间距不小于mm的冷隔,。
mm的凹陷。
mm存在深度不大于0.3铸3.5.2.10件内表面允许凸起高度不mm,存在直径<3件允3.5.2.11在不影响装配的情况下,铸许个。
过3,0.2mm的气泡数量不超大于。
5%度的0.5mm,长度不超过边长3.5.2.12铸件边角残缺深度不大于量质铸件待加工表面的3.5.3围的表面缺陷和痕迹。
过加工余量范3.5.3.1不允许有超基准面艺以上的推杆痕迹,在工过有凸起高度超1mm不允3.5.3.2许许有凸起的推杆痕迹。
上不允量件机械加工后的表面质铸3.5.4铸态表皮存在。
有影响使用的局部不允3.5.4.1许规定的孔穴存在。
有超过表2许 3.5.4.2不允量质的表面纹机械加工螺 3.5.4.3.湖北德科雷米公司编号:ES-301条件件技术铝合金压铸版本:07规范产品页号:4/8定所规3其余螺纹不允许超有过表头两扣不允许有任何缺陷,的缺陷。
3.5.5铸件需采用不锈钢钢丸进行喷丸或喷砂处理,表面粗造度≤Ra12.5。
3.6内部质量压铸件不得有影响其使用要求的内部气孔,疏松、缩孔、夹杂等。
3.7若图样无特别规定,有关压铸工艺部分的设置,如顶杆位置,分型线的位置,浇口和溢流口的位置等由生产厂自行规定,否则图样上应注明或由供需双方商定。
3.8在不影响铸件使用的条件下,应征得需方同意,供方可以对铸件进行浸渗和修补(如焊补)处理。
而后铸件必须作相应的复验满足以上各项要求。
3.9试验方法及检验规则3.9.1化学成份3.9.1.1化学成份的检验按GB6987.1-6987.16的规定执行,在保证分析精度湖北德科雷米公司编号:ES-301条件铝合金压铸件技术版本:07品规范产页号:5/8许使用其它方法。
允的条件下,检验单。
厂要提供化学成份生产每批压铸件,3.9.1.2力学性能3.9.2规定。
的符合方法应GB2283.9.2.1拉伸试验检验频率由供方自定。
3.9.2.2力学性能验钉底孔的质量部规定。
铸件中自攻螺3.9.3压铸件几何尺寸的检验按公司准倍的标3下容易装配且其平均破标准:在实际装配状态环力矩减去收,按以下。
本数量≥20紧固力矩的最大要求值。
样偏差应大于其规定。
的 3.5结果应符合本标准检查3.9.4压铸件表面质量应逐件,抽检规的3.6果其结应符合 3.9.5压铸件内部质量可通过机加工做剖面来检验,定。
色均匀一颜洁,规定执行。
外观清理表面按压铸件喷丸处GB6060.5的3.9.6致。
标记及包装。
压铸件的3.10产年月日。
编码及生压铸件的指定区域内应有制造厂的模具3.10.1。
,R2按要求,厂家名称首字母加数字序号,如R1模具编码。
0.4-0.6mm5mm,凸出高度厂家代码按公司采购部要求,使用黑体,字高年月按以下方式:产铸件生等份,均分区12φ10。
内、外圆之间区域均分两个同心圆,内圆为φ5,外圆为均分位置打示,每月在相应中间用数字标时钟域序号参照分布,年号在φ5内圆观清晰。
形美均匀,图。
线凸出高度0.4-0.6条粗细0.3-0.5,形一点。
图线粗1-产年份后两位数字表示,年份位置使用实际生案不要求有图实际标示对应12表示月份位置,位置用打点表示对应产具体数字,生月份在日按以下方式:产件生铸.湖北德科雷米公司编号:ES-301条件铝合金压铸件技术版本:07品规范产页号:6/8等份,均分区10。
内、外圆之间区域均分圆,内圆为φ5,外圆为φ10两个同心应均分位置打一点。
具等份,每月在相3间均分为域序号按图示分布,φ5内圆中。
线0.4-0.6粗0.3-0.5,凸出高度对应1-10序号内打一点表示,图形线体生产日在观清晰。
图形美条粗细均匀,段,表示本月上中下旬三个时间、2中间部分0、1两个1和日位置,31日在101-10表示对应生产案不要求有具体图打点表示,实际标示区域同时位置用打点表示对应数字,生产日在损伤。
内防止潮湿和机械输过程中和存放时间件的包装应保证在运3.10.2铸时间。
和交付合格印记志应有:名称、数量、制造厂名、检验3.10.3包装的标释解词名附录物等缺陷所形成的孔洞:孔和1、孔穴、气孔、缩夹杂湖北德科雷米公司编号:ES-301条件件技术铝合金压铸版本:07规范产品页号:7/8光滑的较为规则、表面较为)气孔:卷入压铸件内部的气体所形成的形状(1孔洞。
规则、表面不足所造成的形状不过程中,由于内部补偿)缩孔:压铸件在冷凝(2较粗糙的孔洞。
杂质。
件内的金属或非金属物:混入压铸(3)夹杂、气泡:压铸件表皮下气孔鼓起所形成的泡状缺陷。
2态。
的部分,其表面呈自然冷却状凹瘪3、凹陷:平滑表面上出现#0,用:肉眼可见的、但用手感觉不出来的、颜色不同于基体的金属纹络4、花纹砂布稍擦下即可去除。
展的可能,用抛光得出的局部下陷的纹络。
此缺陷无发5、流痕:表面上用手感觉法能去除。
形,有的线接但未熔合而出现缝隙,呈不规则6、冷隔:温度较低的金属流互相对趋势。
穿透的、未穿透的两种,在外力作用下有发展的隙,有穿透的和不穿透的两种,缝状的、裂纹:合金基体被破坏或断开形成细丝7趋势。
展的有发过程中填充不完整的部位。
:成型8、欠铸、印痕:铸件表面由于模具型腔磕碰而形成凸出或凹下的痕迹。
9铸件表面上的网状凸起印痕。
裂而形成生龟10、网状毛剌:由于模具腔表面产积物等脱落而形成的痕迹。
件表面由于金属物或涂料堆11、粘附物痕迹:铸、有色斑点:表面上不同于基体金属颜色的斑点。
一般由涂料碳化物形成。
12件表着出模方向,由于金属粘附或模具制造斜度太小而造成在铸伤:顺13、擦伤痕迹。
面的拉小麻细压条件下表面形成的低,在欠、麻面:充型过程中由于模温或料温过14点状分布存的区域。
隙而造大的缝:由于铸模的精度、配合或装配等等欠佳,在合模时产生过15、飞边边缘的片状金属皮。
件成的铸层。
、隔皮:该穿透而未穿透的金属16轮廓不清。
角边的局部缘件周铸角残缺:、边17.湖北德科雷米公司编号:ES-301条件术铝合金压铸件技版本:07范产品规页号:8/8组织。
、疏松:不紧实的18批准:核:审制:编。