风机叶片前缘开裂维修方案
电站锅炉送风机叶片断裂失效分析及焊接修复
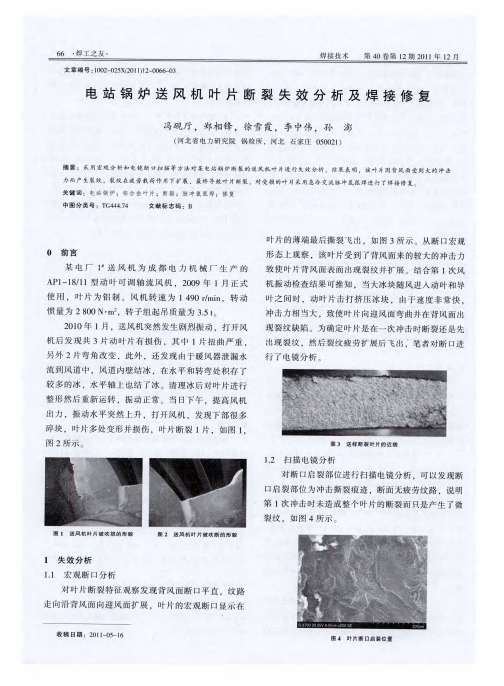
模 ,用 机械 的方 法修 磨成 叶 片的形 状 。将 剩余 的根 部
叶片修 磨 出焊接 坡 口 ,使 铝 板形 成 的 叶 片与 之对 应 ,
表 面清 理 ,另一 方 面采 用交 流氩 弧焊 充分 利用 阴极破
碎 功 能避 免形成 氧 化皮 夹杂 ,第 三是 采用 背 面急 冷处 理 避免 热输 入过 大 引发 焊缝 冲击 性能 下 降 ,第 四是采
用 脉 冲氩 弧焊 以减 小能 量 的输入 。同 时又可保 证 焊合
良好 。
振打 ,表 面形 成 凹坑 ,最后 磨平 。
2 焊 接修 复
根据 不 同的焊 件 可 以采 取水 冷 、风冷 、铜冷 等 多种方 式 ,本次 对损毁 叶片焊 接修 复采用 铜 冷 的方 式 。纯铜 加热 后锻 打成 与 叶片相 近 的形状 ,然 后刮 除贴合 不 良 的位 置 ,直到 贴合 良好 。焊 好背 面 的底 层焊 缝后 ,将 底 层 焊缝 磨平 ,铜 板与 叶 片贴合 。铜板 一方 面起 到高 温下 吸收 多余 热量 的作 用 ,另一 方 面也 起 到低温 下 的 保 温作用 ,既 同时消 除高 温峰值 ,又延长 了低 温 的冷 却时 间 ,既提高 了焊缝 的韧性 ,又降低 了开裂 的风险 。
加 工形成 X形坡 口 .背面坡 口深度 要小 ,其 目的 主要
是背 面形 成较 小 的焊缝后 再 修磨平 滑 ,为背 面 的铜冷 却 做 准备 .同时也 是为 了减 小焊接 变形 。另 外 ,还要
风力发电机组叶片断裂原因分析及防范措施
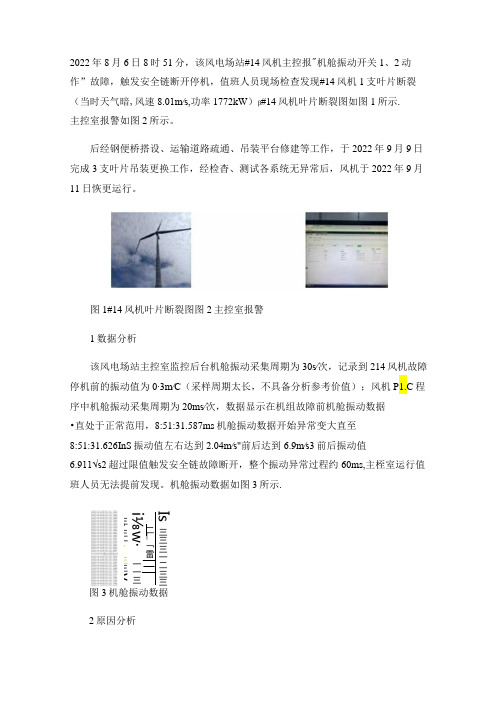
2022年8月6日8时51分,该风电场站#14风机主控报"机舱振动开关1、2动 作”故障,触发安全链断开停机,值班人员现场检查发现#14风机1支叶片断裂(当时天气暗,风速8.01m∕s,功率1772kW )β#14风机叶片断裂图如图1所示. 主控室报警如图2所示。
后经钢便桥搭设、运输道路疏通、吊装平台修建等工作,于2022年9月9日完成3支叶片吊装更换工作,经检杳、测试各系统无异常后,风机于2022年9月11日恢更运行。
图1#14风机叶片断裂图图2主控室报警1数据分析该风电场站主控室监控后台机舱振动采集周期为30s∕次,记录到214风机故障停机前的振动值为0∙3m∕C (采样周期太长,不具备分析参考价值);风机P1.C 程序中机舱振动采集周期为20ms∕次,数据显示在机组故障前机舱振动数据 •直处于正常范用,8:51:31.587ms 机舱振动数据开始异常变大直至8:51:31.626InS 振动值左右达到2.04m∕s"前后达到6.9m∕s3前后振动值6.911√s2超过限值触发安全链故障断开,整个振动异常过程约60ms,主桎室运行值班人员无法提前发现。
机舱振动数据如图3所示.图3机舱振动数据2原因分析Is 三三三一二三三二__「雷三i⅛w∙一一三三-三一.∙三三v对断裂叶片返厂取样分析后,发现该叶片SS面(背风面)主梁断裂处存在褶皱,褶皱的宽度30mm,尚度2E,宽尚比为0.067,超出规定值0.03。
随褶皱缺陷高宽比的增大,叶片材料疲劳寿命逐渐减小,当褶皱缺陷高宽比超过规定值时,材料疲劳寿命下降比较显著,达到90%以上n。
因此判断原本应受力的纤维布未充分受力,使相应拉伸力由该位置树脂一同承受,而树脂的拉伸强度远小于纤维布水平,该位置整体的拉伸强度不及设计要求,使得该位置在机组运行过程中逐步产生院伤⑶.最终在运行过程中,该位置的受力在某时刻超过所能承受的极限值,导致主梁臼褶皱位置发生断裂。
风力发电机组叶片裂纹的分析与预控措施
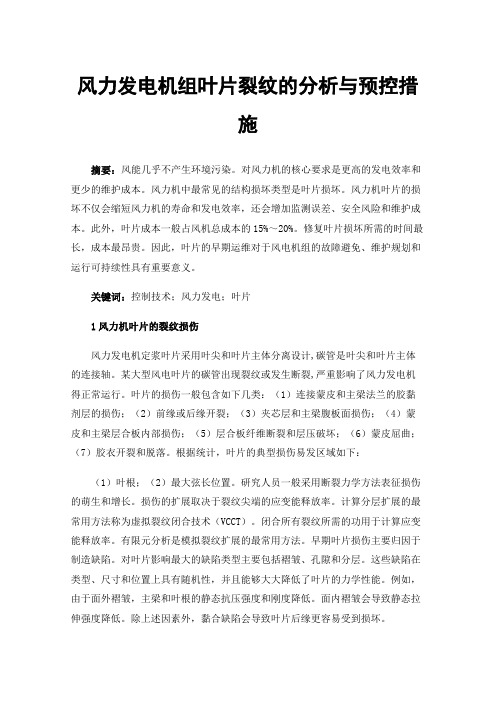
风力发电机组叶片裂纹的分析与预控措施摘要:风能几乎不产生环境污染。
对风力机的核心要求是更高的发电效率和更少的维护成本。
风力机中最常见的结构损坏类型是叶片损坏。
风力机叶片的损坏不仅会缩短风力机的寿命和发电效率,还会增加监测误差、安全风险和维护成本。
此外,叶片成本一般占风机总成本的15%~20%。
修复叶片损坏所需的时间最长,成本最昂贵。
因此,叶片的早期运维对于风电机组的故障避免、维护规划和运行可持续性具有重要意义。
关键词:控制技术;风力发电;叶片1风力机叶片的裂纹损伤风力发电机定浆叶片采用叶尖和叶片主体分离设计,碳管是叶尖和叶片主体的连接轴。
某大型风电叶片的碳管出现裂纹或发生断裂,严重影响了风力发电机得正常运行。
叶片的损伤一般包含如下几类:(1)连接蒙皮和主梁法兰的胶黏剂层的损伤;(2)前缘或后缘开裂;(3)夹芯层和主梁腹板面损伤;(4)蒙皮和主梁层合板内部损伤;(5)层合板纤维断裂和层压破坏;(6)蒙皮屈曲;(7)胶衣开裂和脱落。
根据统计,叶片的典型损伤易发区域如下:(1)叶根;(2)最大弦长位置。
研究人员一般采用断裂力学方法表征损伤的萌生和增长。
损伤的扩展取决于裂纹尖端的应变能释放率。
计算分层扩展的最常用方法称为虚拟裂纹闭合技术(VCCT)。
闭合所有裂纹所需的功用于计算应变能释放率。
有限元分析是模拟裂纹扩展的最常用方法。
早期叶片损伤主要归因于制造缺陷。
对叶片影响最大的缺陷类型主要包括褶皱、孔隙和分层。
这些缺陷在类型、尺寸和位置上具有随机性,并且能够大大降低了叶片的力学性能。
例如,由于面外褶皱,主梁和叶根的静态抗压强度和刚度降低。
面内褶皱会导致静态拉伸强度降低。
除上述因素外,黏合缺陷会导致叶片后缘更容易受到损坏。
除制造缺陷,降水和碎片同样是导致叶片损伤的重要原因。
雨水、冰雹、烟雾和含沙风容易导致前缘侵蚀。
不均匀的积冰会导致旋转不平衡,进而导致发局部损伤甚至失效。
此外,水如果通过预先存在的裂缝、表面缺陷或螺栓接头进入叶片,可能会导致叶片树脂和芯材性能显著下降,并且导致叶片重量增加和力学性能退化。
风机叶片前缘开裂维修方案
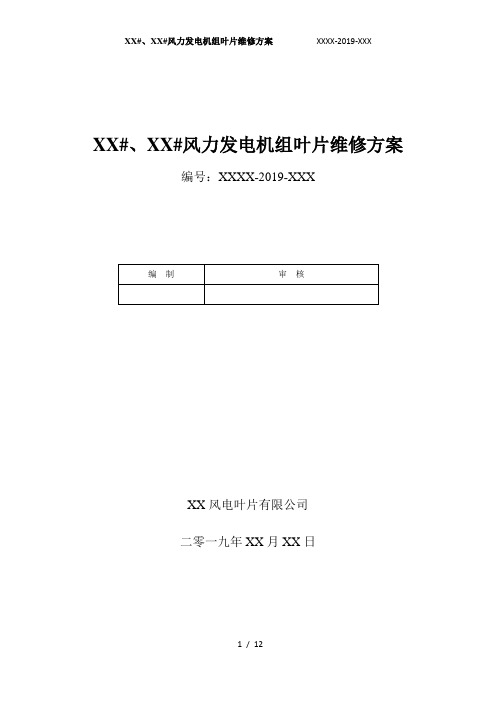
13
密封硅胶
天山
600ml
6支
14
螺纹紧固胶
天山
可塞新1243
4支
紧固胶与紧固胶催化剂比例:2:1
15
螺纹紧固胶催化剂
天山
1764
4支
五、工具辅材清单
序号
工具辅材名称
型号规格
数量
备注
1
角磨机
150#
2台
2
弹性磨片
5个
3
打磨砂纸
P80
10张
4
圆砂纸
80目+200目+400目
各10张
5
托盘(可配角磨机)
催化剂
/
/
稀释剂
/
Mega T764-T
混合重量比
2︰1
5︰1:(0~15%)
催化剂量
/
/
环境温度要求
0~40℃
15~30℃
环境湿度要求
≤85%
20%~85%
湿膜厚度要求
150~200um
约75um×2
25℃操作时间
/
约180min
8)警示漆
面漆表干后,在需要涂警示漆区域辊涂警示漆,色号RAL3020。基料和固化剂的重量比例为9:1,涂层完毕后在20—25℃下自然固化3h。
若内蒙皮无损伤,则先手糊补强一层2AX-1200-0660,面积与打磨区域的尺寸一致,然后开始进行填补芯材。
3)填补芯材
将粘接面全部清理干净后,按照该修补区域芯材距离边缘的距离铺设10mm厚的PVC芯材。将合适大小的芯材用手糊树脂完全浸透后,使用胶黏剂将芯材粘接到芯材缺失区域。
表1.前缘芯材距边距离数据表
R(m)
风电叶片前缘错位质量缺陷的维修方案

风电叶片前缘错位质量缺陷的维修方案1.1 适用范围主要针对叶片脱模后,叶片上下蒙皮发生弦向位移出现错位的维修方案。
1.2 维修流程维修流程:1、C1级:打磨清理→纤维织物纱浸渍手糊树脂→纤维织物纱填充→外侧手糊一层双轴织物→加热固化。
2、B2及B1级:打磨清理→双轴织物手糊补强→加热固化。
3、A2级:(1)前缘粘接角缺胶:打磨外蒙皮→清理粘接角的胶层→手糊织物补强出相关厚度→外蒙皮真空灌注修复→加热固化→错位位置用双轴织物手糊补强→加热固化。
(2)前缘粘接角粘接正常:打磨清理→双轴织物手糊补强→加热固化。
1.3 维修工序1、C1级的维修工序(1)打磨清理将需要手糊补强位置做好打磨清理的工作,须保证待修面表面为粗糙面,且洁净无粉尘、无异物。
(2)纤维织物纱浸渍手糊树脂将纤维织物纱浸渍好手糊树脂,确保树脂的配比正确,纤维织物纱无浸渍不良。
(3)纤维织物纱填充将纤维织物纱填充在缺陷区域。
(4)外侧手糊一层双轴织物在填充好纤维织物纱的外侧手糊补强一层双轴织物。
(5)加热固化使用加热毯或其他加热方式对维修区域进行加热,升温60℃固化3小时,固化完成后,要求玻璃钢Tg≥60℃。
2、B2及B1级的维修工序(1)打磨清理将需要手糊补强位置做好打磨清理的工作,须保证待修面表面为粗糙面,且洁净无粉尘、无异物。
(2)双轴织物手糊补强在缺陷位置铺覆双轴织物(一层双轴织物以0.7mm计算)手糊补强需要填充的层数,详细的手糊工艺维修方案参考1.4。
(3)加热固化使用加热毯或其他加热方式对维修区域进行加热,升温60℃固化3小时,固化完成后,要求玻璃钢Tg≥60℃。
3、A2级的维修工序1.1、前缘粘接角缺胶(1)打磨外蒙皮在前缘粘接角缺胶位置使用角磨机、锋钢刀等工具将外蒙皮打磨开并清理干净。
(2)清理粘接角的胶层将粘接角缺胶位置清理干净。
(3)手糊织物补强出相关厚度使用双轴织物(一层双轴织物以0.7mm计算)手糊补强出相关厚度,详细的手糊工艺维修方案见1.4。
叶片损坏的现象、原因及处理

叶片损坏的现象、原因及处理
叶片损坏是指风力发电机或者风扇等设备中的叶片出现破损、
断裂或者变形的现象。
这种损坏可能会导致设备性能下降甚至完全
失效,因此需要及时处理。
叶片损坏的原因可能有多种,包括以下
几点:
1. 外部碰撞,叶片在运行过程中可能会受到外部物体的撞击,
比如风力发电机叶片可能会被飞离的物体或者鸟类撞击,导致叶片
损坏。
2. 材料疲劳,叶片长时间受到风力或者其他外部力的作用,可
能导致材料疲劳,从而出现裂纹或者断裂。
3. 制造缺陷,叶片在制造过程中可能存在缺陷,比如材料不均匀、结构设计缺陷等,可能导致叶片在运行过程中损坏。
处理叶片损坏的方法可以从多个角度来考虑:
1. 检修维护,定期对叶片进行检查,及时发现潜在的损坏迹象,采取维修措施,可以有效减少因叶片损坏而导致的故障。
2. 强化设计,对叶片的材料和结构进行优化设计,增加其抗风能力和抗外部冲击能力,减少损坏的可能性。
3. 及时更换,一旦发现叶片损坏,应及时更换叶片,以免影响设备的正常运行。
4. 加强保护,可以在叶片周围增加防护措施,比如安装网罩或者其他防护设施,减少外部物体对叶片的损坏。
总之,对叶片损坏问题,需要综合考虑预防和及时处理两个方面,以确保设备的安全运行和性能稳定。
风电叶片的保养与维修技术方案

4,叶根雷击损伤 缺陷描述:1,顺风面叶根轴套雷击损伤,叶片壳体击穿、分层。2,迎风 面叶根尾缘轴套雷击损伤, 叶片壳体击穿、分层
叶片维修从业要求 叶片缺陷产生的原因 叶片维修质量保证
叶片的维修
从事叶片服务的要求
• 门槛低
营业执照,高空作业证
• 专业性强
人员技能,工作经历
• 人为因素大 公司经营理念,人员责任♥
• 安全责任重
安全管理,设备检验
叶片的维修
叶片维修的专业性
叶片的维修
维修
维修案例
1,主梁断裂的维修
a 缺陷描述:叶片SS面距叶根约17m处壳体主梁断裂,并向 尾边横向开裂变形,叶片内部主支架开裂,沿主梁边缘纵向裂纹长7m。
2,尾缘开裂的维修
a,缺陷描述:叶片尾边开裂10m,逆风面玻纤开裂和泡 沫分层7.5m,顺风面泡沫分层9米
3,叶片横向裂纹的维修 a,缺陷描述:叶片横向裂纹。叶片外部距叶跟约9-9.6m,从合模线至前缘 主梁边缘,长度约为1.14m。叶片内部纵向距叶跟9-9.6m,从合模线至主梁边缘 斜向断续开裂,长度为1.0m;
叶片外部+内部检查方法
外部检查方法 平台近距
望远镜/高倍相机远距 高倍相机+平台 无人机近距
质量 较好 一般 一般 较好
叶片质量检查
周期 长 短 短
一般
人工时 台数 16 2台/4人 4 6-8台/4人 6 4-6台/4人 √ 4 3-4台/2人
叶片检查结果输出
• 检查人员不专业
• 检查过程不规范
叶片维修质量保证
专业的人员 专业的设备 专业的材料 专业的工艺 专业的过程控制
叶片的维修
具有专业的技能水平 高效率工作的保证 稳定质量的保证 维修强度的保证 有效的质量监督
风机叶片维修与保养技术

风机叶片维修与保养技术随着工业的发展,风机在许多领域扮演着重要角色,无论是用于冷却、通风还是输送材料,都需要保持其正常运行状态。
而风机的叶片作为其关键部件之一,其维修与保养技术尤为重要。
本文将为读者介绍风机叶片的常见问题、维护保养的注意事项以及一些常用的维修方法,并帮助读者更好地了解并操作风机叶片的维修与保养。
一、风机叶片的常见问题1. 叶片变形叶片由于长期受力或运行时受到外界物体的撞击,可能会出现变形现象。
这种变形会导致风机的不平衡,进而影响其运行效果。
因此,定期检查叶片的形态,发现变形及时进行维修是非常重要的。
2. 叶片磨损由于长时间的摩擦以及颗粒物的侵蚀,风机叶片会逐渐磨损,表面可能产生裂纹或腐蚀现象。
磨损严重会影响风机的工作效率,甚至导致失效,因此及时维修磨损的叶片非常必要。
3. 叶片松动在长期的运行中,叶片螺栓可能会松动,这会导致叶片的不稳定运行,进而影响风机的正常工作。
维修过程中需要检查叶片螺栓的紧固情况,并根据需要进行重新紧固。
二、风机叶片的维护保养1. 定期清洁叶片表面风机叶片常常暴露在外界环境中,容易积累灰尘、油脂等污物。
定期清洁叶片表面,保持其清洁是非常重要的。
清洁时应使用柔软的布料或刷子擦拭,避免使用有腐蚀性的清洁剂。
2. 定期检查叶片的状态定期检查叶片的状态,包括形状、磨损、裂纹等,及时发现问题并进行维修是非常重要的。
若发现叶片严重损坏无法修复,应及时更换叶片以避免安全事故发生。
3. 注意叶片的平衡性定期检查叶片的平衡性非常重要,特别是在长时间高速运转后。
若发现叶片存在失衡现象,应及时进行平衡调整,以保证风机的正常运行。
三、风机叶片的维修方法1. 变形叶片的维修若发现叶片变形,可以采用加热或冷却的方法进行修复。
具体操作时,可将叶片置于适当温度下进行加热或冷却,并手动或用工具进行调整直至恢复原状。
2. 磨损叶片的修复对于磨损比较严重的叶片,可以采用填补方法进行修复。
首先,清洁叶片并打磨表面,然后使用适当的填补材料填补磨损部位,并进行抛光,最后使其恢复平整。
动叶可调轴流风机叶片断裂的原因分析及预防措施
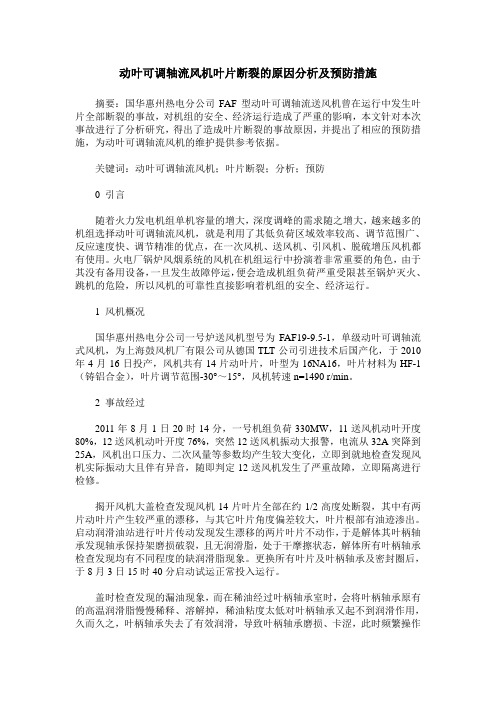
动叶可调轴流风机叶片断裂的原因分析及预防措施摘要:国华惠州热电分公司FAF型动叶可调轴流送风机曾在运行中发生叶片全部断裂的事故,对机组的安全、经济运行造成了严重的影响,本文针对本次事故进行了分析研究,得出了造成叶片断裂的事故原因,并提出了相应的预防措施,为动叶可调轴流风机的维护提供参考依据。
关键词:动叶可调轴流风机;叶片断裂;分析;预防0 引言随着火力发电机组单机容量的增大,深度调峰的需求随之增大,越来越多的机组选择动叶可调轴流风机,就是利用了其低负荷区域效率较高、调节范围广、反应速度快、调节精准的优点,在一次风机、送风机、引风机、脱硫增压风机都有使用。
火电厂锅炉风烟系统的风机在机组运行中扮演着非常重要的角色,由于其没有备用设备,一旦发生故障停运,便会造成机组负荷严重受限甚至锅炉灭火、跳机的危险,所以风机的可靠性直接影响着机组的安全、经济运行。
1 风机概况国华惠州热电分公司一号炉送风机型号为FAF19-9.5-1,单级动叶可调轴流式风机,为上海鼓风机厂有限公司从德国TLT公司引进技术后国产化,于2010年4月16日投产,风机共有14片动叶片,叶型为16NA16,叶片材料为HF-1(铸铝合金),叶片调节范围-30°~15°,风机转速n=1490 r/min。
2 事故经过2011年8月1日20时14分,一号机组负荷330MW,11送风机动叶开度80%,12送风机动叶开度76%,突然12送风机振动大报警,电流从32A突降到25A,风机出口压力、二次风量等参数均产生较大变化,立即到就地检查发现风机实际振动大且伴有异音,随即判定12送风机发生了严重故障,立即隔离进行检修。
揭开风机大盖检查发现风机14片叶片全部在约1/2高度处断裂,其中有两片动叶片产生较严重的漂移,与其它叶片角度偏差较大,叶片根部有油迹渗出。
启动润滑油站进行叶片传动发现发生漂移的两片叶片不动作,于是解体其叶柄轴承发现轴承保持架磨损破裂,且无润滑脂,处于干摩擦状态,解体所有叶柄轴承检查发现均有不同程度的缺润滑脂现象。
叶片褶皱、鼓包、裂纹、前缘腐蚀缺陷维修

叶片褶皱、鼓包、裂纹、前缘腐蚀缺陷维修随着工业发展的进步,各种机械设备的使用日益广泛。
在飞机、汽车、发电机等设备中,叶片作为重要的功能部件,承担着重要的工作任务。
然而,由于长期的使用和环境因素的影响,叶片可能出现褶皱、鼓包、裂纹、前缘腐蚀等缺陷。
本文将分别介绍这些缺陷及其维修方法。
叶片褶皱是指叶片表面出现波浪状或褶皱状的变形。
这种缺陷通常是由于叶片使用过程中受到过大的压力或振动造成的。
对于褶皱问题,一种常见的修复方法是使用专业的热处理设备,将叶片进行加热,然后进行冷却,以恢复其原始形状。
当然,具体的修复方法需要根据叶片的材料和缺陷的程度来决定。
鼓包是指叶片表面出现凸起的区域。
这种缺陷通常是由于叶片在使用过程中受到外部冲击或磨损造成的。
对于鼓包问题,修复的方法通常是将叶片进行拆卸,然后使用专业的工具将鼓包区域进行修复或更换。
在修复过程中,需要注意保持叶片的平整和光滑,以确保其正常工作。
裂纹是叶片常见的一种缺陷,它通常是由于叶片在使用过程中承受过大的应力或疲劳造成的。
裂纹的修复方法通常包括以下几个步骤:首先,对叶片进行彻底的清洁和检查,以确定裂纹的位置和范围;然后,使用专业的焊接设备将裂纹进行修复;最后,进行严格的质量检验,确保叶片的安全和可靠性。
前缘腐蚀是指叶片前缘部分出现腐蚀或损坏的情况。
这种缺陷通常是由于叶片在使用过程中暴露在潮湿的环境中,或者受到化学物质的侵蚀造成的。
对于前缘腐蚀问题,修复的方法通常包括以下几个步骤:首先,将受损的叶片部分进行清洁和除锈;然后,使用专业的修复材料进行修补或更换受损的部分;叶片褶皱、鼓包、裂纹、前缘腐蚀等缺陷对机械设备的正常运行和安全性都会产生一定的影响。
为了确保设备的正常运行,我们需要及时发现和修复这些缺陷。
当然,在修复过程中需要严格按照专业的方法和标准进行操作,以确保修复的效果和质量。
只有这样,才能保证叶片的正常工作和设备的安全可靠。
风力发电叶片维修方案

风力发电叶片维修方案1. 简介风力发电是一种利用风能转换为电能的可再生能源。
在风力发电机中,叶片是最重要的组成部分之一,它们负责捕捉风能并将其转换为机械能以驱动发电机。
然而,由于长时间的运行和自然环境的影响,风力发电叶片可能会出现损坏和磨损。
因此,开发一套维修方案,及时发现和解决叶片问题,是保障风力发电机长期高效运行的关键。
2. 风力发电叶片维修方案2.1 检测和评估在进行风力发电叶片维修之前,首先需要对叶片进行检测和评估,以确定其损坏程度和所需维修的具体方案。
•目视检查:使用无损检测方法,对叶片表面进行目视检查,以寻找明显的损伤,如裂纹、漆面破损等。
•声波检测:使用声波检测装置,对叶片进行声波扫描,检测是否存在内部裂纹和松动。
•照相测量:使用高分辨率相机拍摄叶片表面,并使用计算机软件进行测量和分析,以确定表面平整性、破损程度和变形情况。
•动态测试:当风力发电机处于停机状态时,使用专业仪器对叶片进行动态测试,检测叶片在运行时的振动和变形情况。
2.2 维修方案根据叶片检测和评估的结果,制定相应的维修方案。
以下是常见的风力发电叶片维修方案:•表面修复:对叶片表面进行涂层修复,填补破损和剥落的漆面,提高叶片的防腐性能和表面光滑度。
•裂纹修复:使用专用的充填剂将叶片裂纹处填充,以提高叶片的结构强度和承载能力。
•切割和替换:对严重受损的叶片进行切割和替换,采用新的叶片部件进行更换,确保叶片完整性和性能。
•动态平衡:使用平衡仪对修复的叶片进行动态平衡,以减少振动和噪音,保证风力发电机的稳定运行。
2.3 维修注意事项在执行风力发电叶片维修方案时,需要注意以下事项:•安全:维修过程中,必须遵守相关的安全操作规定和程序,穿戴个人防护装备,确保人员和设备的安全。
•材料和工具:选择符合要求的维修材料和工具,确保维修质量和效果。
•环境保护:在维修过程中,注意环境保护,遵守相关的环境保护法规,正确处置废弃材料和废水。
•记录和报告:维修过程中,及时记录和汇报叶片检测、维修和测试结果,以便跟踪和评估维修效果和维修工作质量。
小型风力机叶片断裂原因及解决方法
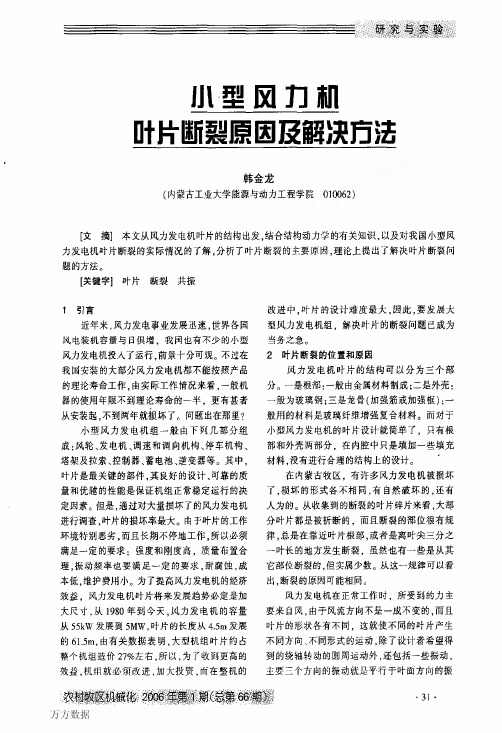
小型风力祁叶片断裂原因及稿决方法韩金龙(内蒙古工业大学能源与动力工程学院010062)[文摘]本文从风力发电机叶片的结构出发,结合结构动力学的有关知识,以及对我国小型风力发电机叶片断裂的实际情况的了解,分析了叶片断裂的主要原因,理论上提出了解决叶片断裂问题的方法。
【关键字】叶片断裂共振1引言近年来,风力发电事业发展迅速,世界各囝风电装机容量与日俱增.我围也有不少的小型风力发电机投入了运行.前景十分可观。
不过在我国安装的大部分风力发电机都不能按照产品的理论寿命工作.由实际工作情况来看,一般机器的使用年限不到理论寿命的一半,更有甚者从安装起,不到两年就损坏了。
问题出在那里?小型风力发电机组一般由下列几部分组成:风轮、发电机、调速和调向机构、停车机构、塔架及拉索、控制器、蓄电池、逆变器等。
其中.叶片是最关键的部件,其良好的设计、可靠的质量和优越的性能是保证机组正常稳定运行的决定因素。
但是.通过对大量损坏了的风力发电机进行调查,叶片的损坏率最大。
由于叶片的工作环境特别恶劣,而且长期不停地工作,所以必须满足一定的要求:强度和刚度高,质量布置合理,振动频率也要满足一定的要求,耐腐蚀,成本低,维护费_l=fj小。
为了提高风力发电机的经济效益.风力发电机叶片将来发展趋势必定是加大尺寸,从1980年到今天.风力发电机的容量从55kw发展到5Mw,叶片的长度从4,5m发展的6l,5m,由有关数据表明,大型机组叶片约占整个机组造价27%左右,所以,为了收到更高的效益.机组就必须改进.加大投资,而在整机的改进中,叶片的设计难度最大,因此,要发展大型风力发电机组,解决叶片的断裂问题已成为当务之急。
2叶片断裂的位置和原因风力发电机叶片的结构可以分为三个部分。
一是根部:一般由金属材料制成;二是外壳:一般为玻璃钢;三是龙骨(加强筋或加强框):一般用的材料是玻璃纤维增强复合材料。
而对于小型风力发电机的叶片设计就简单了,只有根部和外壳两部分,在内腔中只是填加一些填充材料。
汽动引风机叶片断裂故障分析与处理

汽动引风机叶片断裂故障分析与处理
《汽动引风机叶片断裂故障分析与处理》
汽动引风机叶片断裂是一种常见的故障,它会对汽动引风机的正常运行造成严重影响。
因此,对叶片断裂故障的分析和处理显得尤为重要。
首先,需要进行故障分析,主要有以下几点:1、叶片断裂的原因,可能是由于叶片材质、结构设计不合理,或者是叶片受到外力损坏;2、叶片断裂的位置,叶片断裂的位置会影
响汽动引风机的正常运行;3、叶片断裂的程度,叶片断裂的程度越大,汽动引风机的效
率就越低。
其次,需要根据故障分析结果,采取合理的处理措施,主要有以下几点:1、更换新的叶片,以恢复汽动引风机的正常运行;2、对叶片进行润滑,以减少叶片的磨损;3、检查叶片的结构设计,以确保叶片的质量和结构合理;4、限制叶片受到外力损坏的可能性。
综上所述,叶片断裂故障的分析和处理是非常重要的,只有正确分析故障原因,采取合理的处理措施,才能有效地保证汽动引风机的正常运行。
风机叶片损坏分析及修复方法

2018年第7期2018Number7水电与新能源HYDROPOWERANDNEWENERGY第32卷Vol.32DOI:10.13622/j.cnki.cn42-1800/tv.1671-3354.2018.07.016收稿日期:2018-05-04作者简介:吴光军ꎬ男ꎬ高级工程师ꎬ主要从事风电㊁太阳能电站建设管理㊁生产运行及质量安全管理工作ꎮ风机叶片损坏分析及修复方法吴光军1ꎬ吴鸣寰2ꎬ罗浩然1(1.湖北能源集团新能源发展有限公司ꎬ湖北武汉㊀430072ꎻ2.三峡大学电气与新能源学院ꎬ湖北宜昌㊀443002)摘要:针对风机叶片损坏的具体案例ꎬ分析叶片失效的原因ꎬ提出了修复处置方法ꎮ从叶片运行维护㊁控制策略优化环节提出防范措施ꎬ以便有效预防并减少叶片失效的事件ꎮ关键词:风电ꎻ叶片ꎻ失效ꎻ措施中图分类号:TM315㊀㊀㊀文献标志码:B㊀㊀㊀文章编号:1671-3354(2018)07-0072-04AnalysisandTreatmentofBladeDamageofWindTurbineUnitWUGuangjun1ꎬWUMinghuan2ꎬLUOHaoran1(1.HubeiEnergyGroupNewEnergyDevelopmentCo.ꎬLtd.ꎬWuhan430072ꎬChinaꎻ2.CollegeofElectricalEngineering&NewEnergyꎬChinaThreeGorgesUniversityꎬYichang443002ꎬChina)Abstract:Accordingtothepracticalcasesofbladedamageofwindturbineunitꎬpossiblereasonsofthedamagearean ̄alyzedandtreatmentmeasuresareproposed.Preventionmeasuresarealsorecommendedfromtheaspectsofoperationmaintenanceandcontrolstrategyoptimizationꎬwhichcouldeffectivelypreventandreducethebladefailures.Keywords:windpowerꎻbladeꎻfailureꎻmeasures㊀㊀随着风电整机技术迭代进步ꎬ目前ꎬ风机单位kW的售价已下调至3500元左右ꎬ风力发电是应用最广的新能源发电方式ꎬ到2017年底全国累计装机容量达到1.88亿kWꎮ风力发电机组是由叶片㊁传动系统㊁发电机㊁齿轮箱㊁变流器以及电气控制系统㊁塔架等组成的发电装置[1]ꎬ详见图1ꎮ其中ꎬ叶片是保证风力发电机组有效捕获风能转化为机械能㊁并转化为电能的核心部件ꎬ直接影响风机的性能和发电量ꎮ风机叶片尺寸大ꎬ外形复杂ꎬ精度要求高ꎬ表面要求光洁ꎬ同时叶片材质需具备高强度和高刚度ꎬ质量工艺要求较高ꎬ因此叶片技术持续改进及智能化维护成为风力发电可持续发展的关注点ꎮ新形势下ꎬ叶片的减重㊁降载和降噪㊁大型化㊁轻量化和智能化是风电叶片发展的方向ꎮ1㊀风机叶片失效的类型1.1㊀叶片损坏的常见类型风机叶片制造成本约占风机总成本的图1㊀双馈风机结构示意图15%~20%ꎮ叶片整体裸露在野外ꎬ工作条件恶劣ꎬ在高空㊁全天候条件下ꎬ经常受到空气介质㊁大气射线㊁砂尘㊁雷电㊁暴雨㊁冻雨或冰雪的侵袭ꎬ盐腐蚀㊁台风等因27吴光军ꎬ等:风机叶片损坏分析及修复方法2018年7月素影响ꎬ导致叶片失效事件时有发生ꎬ每只叶片损坏后更换(含备件及吊车台班)费用近百万元ꎬ因此对叶片的状态监测预警㊁有效运维分析显得越来越重要ꎮ常见的风电叶片投产运行中损坏有以下几类:普通损坏性㊁前缘腐蚀㊁前缘开裂㊁后缘损坏㊁叶根附近区域折断㊁叶尖开裂㊁表面裂纹㊁雷击损坏㊁覆冰运行断裂等ꎮ同时ꎬ叶片断裂在机组制动之前ꎬ极有可能撞击相邻叶片㊁机舱和塔筒㊁底部的箱变或箱变基础ꎬ处置不当或偏航制动不及时ꎬ将造成事故损失扩大ꎬ发生叶片失效后的二次伤害ꎮ因此ꎬ运维人员及时排查叶片运行异常隐患㊁通过巡检㊁听叶片是否存在哨声ꎬ检查运行参数是否突变等因素ꎬ是及时发现叶片失效隐患的措施ꎬ也是减少叶片失效事件的有效办法ꎮ1.2㊀叶片失效的检查方法(见表1)通过发电企业的维护管理情况来看ꎬ对叶片主动维护的手段少㊁日常维护过程控制不严㊁维护投入相对不足的现象或多或少存在ꎮ所以ꎬ实际运行中的叶片失效事件不断增多ꎬ这直接影响到风电场经营效益ꎬ同时也不利于风电制造业健康发展ꎮ当然ꎬ风电业主通常购买风机机损险及财产一切险ꎬ来转嫁部分直接损失ꎬ而风机停运的发电量损失就无法避免了ꎮ表1㊀叶片失效的检查方法分类人为检测仪器检测检测方式人工目测㊁敲击㊁单反相机远距拍照超声无损检测红外热波无损检测特点可发现缺陷:外部裂纹㊁脱漆㊁雷击损毁㊁外力损伤㊁腐蚀㊁麻面砂眼等ꎮ简单ꎬ直接ꎬ易于操作ꎬ成本较低ꎮ叶片成型前缺陷及人不可及处缺陷无法检测ꎬ人为因素影响检验结果在工厂针对断层和缺胶检查ꎬ目前无法实现风场实时检测检测灵敏度高㊁检测速度快ꎬ检测缺陷范围广ꎬ实时成像ꎬ能够实现风场实时检测2㊀风机叶片失效的原因分析叶片损坏可分为设计缺陷㊁制造工艺缺陷㊁断裂失效㊁开裂失效㊁雷击损伤㊁局部表面磨蚀㊁局部表面裂纹㊁运输吊装损伤和运行维护不当损伤等形式[2]ꎮ下面针对覆冰运行断裂和雷击损坏事件来进行阐述ꎮ2.1㊀叶片覆冰运行中断裂2018-01-24日ꎬ某风机叶片覆冰运行断裂失效ꎬ发生在叶片中部ꎬ呈折断形式ꎬ如图2所示ꎮ图2㊀风机覆冰断裂失效的叶片叶片覆冰断裂的原因往往为运维控制策略缺少优化ꎬ风机覆冰没有及时停机ꎮ超载荷连续运转ꎬ导致叶片损坏(见表2)ꎮ经现场勘查ꎬ叶片断裂位置为前缘L14.32m㊁后缘L12.40m㊁中心区域L11.30mꎮ断裂发生后ꎬ该叶片由SS面向PS面方向倒塌ꎬ并倒向机舱罩方向ꎮ表2㊀故障叶片覆冰前后的重量和质量矩的变化项目覆冰前覆冰后变化量叶片重量/kg8310.510458.8+2148.3叶片质量矩/kgˑm119209.14150024.355+30815.215㊀㊀断裂叶片在故障发生前经历较长时间的覆冰情况ꎮ覆冰状态下ꎬ静载和动载大幅增加ꎬ气动外形变化下带来的升力系数变化ꎬ也给叶片带来额外载荷ꎬ影响叶片的疲劳强度ꎮ风机运行记录显示ꎬ叶片故障发生前ꎬ风机在载荷大幅增加的情况下满功率状态运行ꎮ叶片断裂问题定性为叶片长时间覆冰情况下ꎬ叶片结构负载过大ꎬ直至不能承受上述载荷后发生的叶片弯曲断裂ꎮ该叶片早期已经产生结构上的形变现象ꎬ但未完全失效ꎻ随后叶片形变开裂情况持续ꎬ直至叶片完全折断失效ꎮ鉴于高海拔风电项目冬季低温雨雪频繁ꎬ且存在叶片覆冰情况ꎬ建议项目现场根据天气情况开展相关检查ꎬ防范叶片严重的覆冰风险及时手动或自动停机ꎮ37水电与新能源2018年第7期2.2㊀叶片遭雷击的失效分析2017-09-09日ꎬ某风电场运维人员在进行风电场风机叶片巡检时发现ꎬ33号风机115m叶轮直径的02号叶片的叶尖出现裂纹ꎬ后经返厂解剖勘察ꎬ叶尖部位R52.9m处发现明显的玻璃钢碳化现象ꎬ叶片开裂损坏ꎬ如图3所示ꎮ雷击造成叶片损坏原因一般为防雷系统工作不正常或者损坏会导致叶片遭受雷击ꎮ雷击造成叶片损坏的机理主要有两个方面:一是雷电释放巨大能量ꎬ使叶片结构温度急剧升高ꎬ分解气体高温膨胀ꎬ压力上升造成爆裂破坏ꎻ二是雷击造成的巨大声波ꎬ对叶片结构造成冲击破坏ꎮ1)雷电瞬间电流强度超过导雷线缆通过电流值ꎬ造成叶片雷击损坏ꎻ雷电流通过导雷线缆时ꎬ瞬间高温ꎬ造成接闪器高温熔化ꎬ由于壳体内是有空隙的ꎬ空隙间的空气ꎬ瞬间高温ꎬ体积急剧膨胀ꎬ造成壳体炸裂(雷电计数器显示雷电电流有129kA)ꎮ2)防范措施为在叶尖安装接闪器能有效地拦截直击雷ꎬ在叶片表面安装3对圆盘状接闪器通常能有效将雷电流导入地网ꎮ2.3㊀叶片表面局部损伤叶片表面磨蚀主要发生在叶尖区域迎风面㊁中部迎风面㊁叶片前缘㊁叶片后缘等部位ꎬ如图4所示ꎮ图3㊀荆门某风电场雷击失效的叶片解剖图图4㊀局部表面磨蚀的叶片㊀㊀导致叶片表面局部磨蚀的原因如下ꎮ1)风砂㊁暴雨冲刷及紫外线等磨蚀ꎮ2)叶片巡查时应注意噪声ꎮ风机运行时出现阻力㊁杂音㊁哨声等ꎬ疲劳累计等均属叶片失效诱因ꎮ暴雨㊁大雪㊁冰雹㊁雷电等恶劣天气同样可能造成叶片损坏ꎮ从统计资料来看ꎬ表面局部损伤的分布无明显的规律性ꎬ全叶片均有发生ꎬ迎风面分布相对集中ꎮ综合上述风电叶片故障或失效ꎬ须全面排查是否存在批次性质量问题ꎬ排查风机质量批次隐患ꎬ叶片检查的批次质量问题检查路径及分析报告4可如图5流程执行ꎮ3㊀风机叶片局部损坏的修复方法叶片局部损坏后ꎬ首先应修复成型壳体ꎬ然后铺贴PVC芯材及外层玻纤加强ꎬ最后表面涂刷防紫外线面漆与配重ꎬ叶片质量分析与质量问题报告见图5ꎮ具体修复方法如下ꎮ1)叶片表面打磨ꎮ打磨叶片破损处ꎬ要求打磨破损处玻纤光滑平整ꎬ去掉所有分层的破损玻纤ꎬ分层PVC芯材ꎬ要求打磨时从破损处向完好壳体延伸超过3cmꎬ以便搭接成型衬板ꎮ2)粘结衬板ꎬ成型(成型缺失壳体)ꎮ清洁需要粘结衬板的区域ꎬ用剪刀裁好合适的衬板ꎬ打磨所裁衬47吴光军ꎬ等:风机叶片损坏分析及修复方法2018年7月图5㊀叶片质量分析与质量问题报告板ꎬ清洁后ꎬ可在需要粘结处ꎬ涂布快速粘结胶粘结到破损处ꎮ注意粘结开裂底层玻纤ꎬ要求尺寸尽可能要小ꎬ使底部玻纤加强时ꎬ以使整个玻纤层成为一个整体ꎮ3)叶片破损壳体强固(湿铺玻纤层)ꎮ待粘结胶固化ꎬ打磨多余溢出的粘结胶并予以清洁ꎮ裁好需要湿铺的玻璃纤维ꎬ一层两项玻纤ꎬ一层三项玻纤ꎬ底层破损处ꎬ铺贴三项玻纤ꎬ尺寸超过破损处5cmꎬ上面覆盖一层亮相纤维ꎬ尺寸为超过三项纤维边缘4cm即可ꎮ4)叶片表面固化后ꎬ打磨ꎬ涂布保护胶衣ꎮ玻璃纤维充分固化后ꎬ打磨整个玻璃纤维表面ꎮ打磨时ꎬ为刮涂胶衣ꎬ新旧胶衣要有搭结尺寸ꎬ要求打磨超过涂布区域边缘5cmꎮ使用材料为环氧胶衣(品牌与型号:Guritꎻ7337)ꎮ5)外层胶衣的表面抛光处理ꎮ待外层胶衣自然固化后(禁止强制加热)ꎬ打磨整个涂布表面ꎬ至表面光滑平整ꎮ6)涂布防紫外线面漆ꎮ打磨叶片涂布胶衣处ꎬ要求打磨破损处玻纤光滑平整ꎬ涂布防紫外线聚氨酯面漆ꎬ使用材料为防紫外线面漆(品牌与型号:PPGꎻLT253-5633)ꎮ7)叶片开裂壳体粘结ꎮ对于一面壳体遭撞击ꎬ开裂及壳体玻纤分层的处理要求ꎮ将已经补好壳体的开裂壳体打磨洁净ꎬ然后清洁上下壳体粘结处ꎬ涂布粘结胶ꎬ用快速夹夹紧上下开裂壳体ꎬ加热固化后ꎬ去掉快速夹ꎬ打磨壳体至表面平整光洁ꎬ并进行配重校核㊁贴补前缘保护膜ꎮ4㊀结㊀语风机叶片作为风力发电机组的动力源泉ꎬ叶片状态直接关系整机的运行性能ꎮ定期㊁不定期地对叶片进行检查ꎬ识别叶片状态ꎬ对缺陷隐患及时排查治理ꎬ将叶片失效事件消灭在萌芽状态ꎬ是避免事故㊁减少突发事件风险㊁稳定风电企业收益的有效途径ꎮ检测叶片防雷系统正常可靠ꎬ防雷回路接地电阻应小于4Ωꎮ确保雷电流安全地从雷击点传导到接地轮毂ꎬ避免叶片内部雷电电弧的形成ꎮ探索适应风电机组的安全生产管理模式ꎬ健全风电机组管理制度及相关技术监督标准ꎬ进一步加强对叶片巡检㊁微损伤维护㊁检修流程精益管理ꎻ并根据状态检查和诊断技术提供的叶片状态信息安排维修ꎬ实施一机一控的诊断运行策略ꎬ可减少风机叶片失效导致的停机时间ꎬ有效提高风电机组全生命周期内的可利用率及发电量ꎬ从而促进风电产业可持续高质量发展ꎮ参考文献:[1]宋海辉ꎬ吴光军.风力发电技术与工程[Mə.北京:中国水利水电出版社ꎬ2014[2]李良君.风电机组叶片常见损坏及处理[J].科学中国人ꎬ2016(18):6-757。
风机叶轮故障修复方法

风机叶轮故障修复方法
风机都是经过动平衡试验的,因为其转速高,所以对它的平衡要求也很高,特别是风机的叶轮,对外周的不平衡非常敏感,但对其心部的微小不平衡感要求不是很高。
根据这个特点,对叶轮容易发生的故障,可以采用以下方法进行修复:1.如果叶轮的铆钉头部被磨损,可以通过压紧叶轮体与轮毂用电焊堆焊,让磨损的铆钉头部回到原来的正常状态。
2.对铆钉孔处容易产生疲劳裂纹的情况,可用整根没有用过的新焊条进行焊接修裂纹,但要以叶轮轴心线为中心对称进行,将该裂纹处补焊剩下的焊条留在该处,再用一根新焊条修补相对称的铆钉孔裂纹,焊完后剩下的焊条与对称铆钉修补时剩下的焊条一样长,以保证焊补上去的重量相等。
若是对称的铆钉孔处无裂纹也要将焊条堆焊于此处,用来抵消对称铆钉孔裂纹处新补的焊接重量。
按照这种对称补重的方法焊接就可以修复裂纹。
3.对叶轮进行简单的动平衡试验,方法也很简单。
把叶轮支起后用手拨动使之轻轻旋转,达不到平衡的地方会停到最低点且左右摆动。
若有偏重可在对面的叶轮上点焊,增加重量使其平衡,或者用角磨机磨去偏重叶轮的焊痕,也能达到平衡,这样就可以把风机修复好进行正常工作了。
注意,在对风机的修理过程中不能用电焊随意点焊,将焊痕留到叶轮上,以免影响风机叶轮的平衡,达不到修复的目的,造成更大的损失。
风电叶片修补方法(转载)

风电叶片修补方法(转载)风电叶片制造技术2010-04-2916:53:07阅读122评论0字号:大中小订阅.风力发电机在使用一段时间之后,不可避免地在叶片前缘会形成一个由昆虫和脏物组成的边界。
这个边界会对叶片的效率产生负影响,如果要将其清除,建议按下列说明支做:1.叶片涂上了一层Y achtCleaner蜡,这种蜡是一高浓缩精炼试剂没有添加研磨介质,可用水稀释。
2.将来使用Y achtPolish,它是一种添加研磨介质的蜡。
对于特别难处理的污渍和顽垢,可使用Y achtRubbing。
3.为得到最佳结果,建议不用Y achtWax,它是一种不含研磨介质的蜡,这种蜡保护叶片,为叶片提供防腐。
所有上述产品是由国际FARVGFABRIKALSKNUDBROALL.10DK—3600,STENLOSE制造成的。
如果在叶根法兰上出现刮痕,脏物等,需进行修补。
如果需要补叶片上的破损处,请参阅下面的叶片修补技术4.叶片修补技术由于叶片表面的损伤程度不一样,因此叶片修补的用料和工序也有所不同。
4.1对于严重损伤是指叶片表面有大面积的剥落层,严重折伤或深度裂纹。
对这种损伤采用的修补方法如下:(1)打磨将破损表面进行打磨,同时也要将由损伤引起的有裂纹的表面一块打磨,直到将未损伤的表面(玻璃纤维层)露出,然后再把打磨区打磨光滑。
(2)准备修补材料根据损伤面积的大小和深度,裁出与其面积一般的(通常要稍大一点)的玻璃纤维布2—4块(对主要部位损伤或损伤表面严重的使用3—4块);如果损伤较深,则要剪出一些较碎的玻璃布打底用。
(3)调制聚酯液聚酯液是玻璃纤维布之间粘合的一种特殊材料。
根据损伤表面及所用玻璃纤维布的用量,取适当的聚酯液,然后加以4%--5%的凝固剂,凝固剂的用量可依据实际的气温条件而定,如果工作环境温度较低,则可采用较大的凝固剂比例。
(4)粘贴修补材料先把聚酯液涂于已打磨过的损伤表面,然后粘第一层玻璃纤维布,接着用铁滚子在该玻璃纤维布上来回碾压,直到其完全被聚酯液浸透,且内部无气泡。
兆瓦级风电叶片断裂更换解决方案
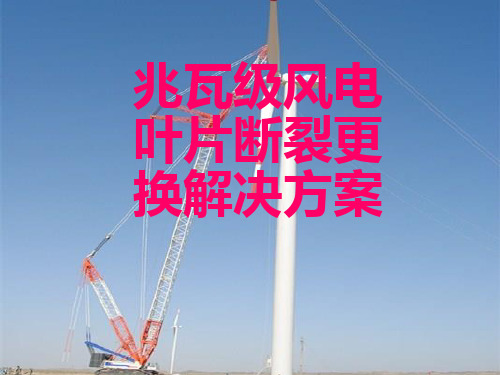
风机叶片断裂原因分析
(一)设计不完善 ①面对降低成本的压力
为了追求更高的利润,管理层要求设计出低廉的部件, 以便使企业有更大的空间。设计部门有时不得不做出妥协, 比如,减小叶片的叶根直径的方式来减少轮毂和叶片的成 本,但是叶根尺寸减小后会导致叶片强度不够,再如,选 择质量不佳但价格便宜的原材料,这往往导致叶片出现致 命的缺陷。 ②擅自更改生产工艺。 ③极限设计
叶片的设计需要考虑到机组其他部件的要求与配合,例 如,塔架与叶片的间距通常是设计叶片强度时需要考虑的 一个原因,主轴和轴承也对叶片的重量提出要求,如果这 些参数考虑不周就会使叶片设计达到极限值。 ④安全质量降低
风机叶片断裂原因分析
(二)生产缺陷
①使用不合理的材料 ②不严格的质量控制 ③生产工工艺过程过于复杂,很难生产质量一致的产品
在风机的日常运行维护时,叶片往往得不到重视。可是 叶片的老化却在阳光,酸雨,狂风,自振,风沙,盐雾等 不利的条件下随着时间的变化而发生着变化。在地面一旦 发现问题,就意味着问题很严重。叶片的日常维护很难检 查和维护到叶片,在许多风场叶片都会因为老化而出现自 然开裂,沙眼,表面磨损,雷击损坏,横向裂纹等。这些 问题如果日常维护做到位,就可以避免日后高额的维修费 用、减少停机中造成的经济损失。
两支叶片折断更换案例
三支叶片折断更换案例
两支、三支叶片折断更换案例
其他风机吊装案例
国内主流风机参数
风电吊装吊车的选型
说明: ●——基本满足要求 ◎——部分满足要求
叶片更换案例 1 单支叶片断裂更换 2 两支叶片断裂更换 3 三支叶片断裂更换
单支叶片断裂更换方法
1.拆除损坏叶片 2.在轮毂与叶片对接的法兰面安装两个吊耳(类似
- 1、下载文档前请自行甄别文档内容的完整性,平台不提供额外的编辑、内容补充、找答案等附加服务。
- 2、"仅部分预览"的文档,不可在线预览部分如存在完整性等问题,可反馈申请退款(可完整预览的文档不适用该条件!)。
- 3、如文档侵犯您的权益,请联系客服反馈,我们会尽快为您处理(人工客服工作时间:9:00-18:30)。
编号:XXXX-2019-XXX
编制
审核
XX风电叶片有限公司
二零一九年XX月XX日
XX#、XX#风力发电机组叶片维修方案
一、损伤情况描述
叶片SS面前缘损伤。其中075#叶片R31.1m—R40.3m,前缘合模缝向上250mm—350mm范围内蒙皮裂纹,局部区域有芯材与蒙皮分层开裂现象。076#叶片有2处损伤区域,R32.17m—R32.87m,R34.3m—R38.8m,前缘合模缝向上约350mm范围内蒙皮不同程度裂纹,076#叶片尖部警示漆区域警示漆涂层损伤,另外076#叶片防雨环部分面漆脱落。两支叶片的全部螺栓均生锈。
表2.铺层顺序
序号
种类
第一层
2AX-1200-0660
第二层
2AX-1200-0660
第三层
2AX-1200-0660
5)固化至可打磨状态
根据现场环境情况,采用自然固化或加热的方式,使手糊铺层固化至可打磨状态。
6)修型
固化后,去除脱模布。将表面凸起及边缘毛刺打磨掉,先用角磨机将铺层与周边壳体平滑过渡,再用粗腻子对前缘外形进行修整,使得前后缘及壳体表面翼型与叶片长度方向的翼型平滑过渡。
R(m)
芯材与前缘合模缝距离(mm)
SS
PS
20
20
57
25
20
49
30
20
42
35
20
34
40
20
27
44
20
20
44.8
20
20
4)手糊外蒙皮
采用手糊方式进行维修。按照原铺层种类,将玻纤布铺设到相应错层位置,每层玻纤布要求压实,将内部气泡完全赶出,保证铺层平整、无褶皱。铺层顺序见下表。要求第一层与周围的正常铺层搭接50mm,第二层与周围正常铺层搭接100mm,第三层与周围正常铺层搭接150mm。
若内蒙皮无损伤,则先手糊补强一层2AX-1200-0660,面积与打磨区域的尺寸一致,然后开始进行填补芯材。
3)填补芯材
将粘接面全部清理干净后,按照该修补区域芯材距离边缘的距离铺设10mm厚的PVC芯材。将合适大小的芯材用手糊树脂完全浸透后,使用胶黏剂将芯材粘接到芯材缺失区域。
表1.前缘芯材距边距离数据表
2)修型
适当用粗腻子对损伤区域外形进行修整,使得涂层损伤区域表面与周围区域表面平滑过渡。
3)涂层
在维修区域表面进行辊涂,一遍底漆,两遍面漆,色号RAL7035。每次涂层完毕后需要表干后才能进行下一次的涂层。技术参数见表3。
4)粘接面要求
粘接面指粘胶剂与复合材料本体、浸润树脂的玻纤布与复合材料本体、腻子与复合材料本体、涂料与复合材料本体、涂料与涂料之间的界面,要求这些粘接面务必是粗糙面(80#~120#砂纸打磨或者脱模布),且粗糙面必须干净(无异物、灰尘等)。
图1.075#蒙皮开裂损伤
图2.0Байду номын сангаас6#蒙皮损伤情况
图3.076#警示漆涂层损伤
图4.076#防雨环掉漆
图5.075#、076#螺栓生锈
二、修补说明
075#、076#叶片的蒙皮均已损伤,所以需将损坏的外蒙皮去除,然后进行维修。075#叶片局部芯材有破损,两支叶片其他损伤区域无法判定内蒙皮是否损伤,需要去除部分芯材后判断,然后决定是否维修内蒙皮。076#警示漆涂层损伤,损伤区域打磨处理后并清理干净,然后修补表面的涂层即可。076#防雨环面漆损伤,将损伤区域打磨处理后并清理干净,然后修补表面的涂层即可。
7)涂层
在维修区域表面进行辊涂,一遍底漆,两遍面漆,色号RAL7035。每次涂层完毕后需要表干后才能进行下一次的涂层。
表3.麦加(MEGA)涂料辊涂体系及技术参数
名称
麦加(MEGA)
胶衣
面漆
基料
Mega WU 210 A(滚涂)
Mega FU 300 A
固化剂
Mega WU 210 B(滚涂)
Mega FU 300 B
催化剂
/
/
稀释剂
/
Mega T764-T
混合重量比
2︰1
5︰1:(0~15%)
催化剂量
/
/
环境温度要求
0~40℃
15~30℃
环境湿度要求
≤85%
20%~85%
湿膜厚度要求
150~200um
约75um×2
25℃操作时间
/
约180min
8)警示漆
面漆表干后,在需要涂警示漆区域辊涂警示漆,色号RAL3020。基料和固化剂的重量比例为9:1,涂层完毕后在20—25℃下自然固化3h。
2)修型
用粗腻子对损伤区域外形进行修整,使得损伤区域表面翼型与周围区域的翼型平滑过渡。
3)涂层
在维修区域表面进行辊涂,一遍底漆,两遍面漆,色号RAL7035。每次涂层完毕后需要表干后才能进行下一次的涂层。技术参数见表3。
4)警示漆
面漆表干后,在需要涂警示漆区域辊涂警示漆,色号RAL3020。基料和固化剂的重量比例为9:1,涂层完毕后在20—25℃下自然固化3h。
两支叶片生锈的全部螺栓需要拆卸掉,更换同样规格的新螺栓。
三、075#、076#维修方案
1.蒙皮损伤修补
1)去除损伤外蒙皮
将损伤的外蒙皮打磨去除,注意不能损伤芯材。
2)内蒙皮损伤判定
外蒙皮去除后,选择损伤最严重的区域,将芯材去除,观察内蒙皮是否有损伤,再根据情况进行修补内蒙皮:
若内蒙皮有损伤,沿叶片长度方向扩大去除芯材的面积,观察周围的内蒙皮是否有损伤,如有损伤,则继续沿长度方向扩大去除芯材的面积,直至观察不到内蒙皮损伤。然后将损伤区域周围100mm拉毛,清理干净后,使用3层2AX-1200-0660双轴布手糊补强。第一层超过损伤区域四周50mm,第二层超过损伤区域四周100mm,第三层超过损伤区域四周150mm。
5)粘接面要求
粘接面指粘胶剂与复合材料本体、浸润树脂的玻纤布与复合材料本体、腻子与复合材料本体、涂料与复合材料本体、涂料与涂料之间的界面,要求这些粘接面务必是粗糙面(80#~120#砂纸打磨或者脱模布),且粗糙面必须干净(无异物、灰尘等)。
3.防雨环面漆脱落修补
1)去除损伤区域的涂层
将损伤的涂层打磨去除,将防雨环接缝处的胶粘剂打磨平滑,注意不能损伤叶片复合材料本体和其他区域的涂层。打磨完毕后用干净的抹布蘸酒精清理干净表面。
9)粘接面要求
粘接面指粘胶剂与复合材料本体、浸润树脂的玻纤布与复合材料本体、腻子与复合材料本体、涂料与复合材料本体、涂料与涂料之间的界面,要求这些粘接面务必是粗糙面(80#~120#砂纸打磨或者脱模布),且粗糙面必须干净(无异物、灰尘等)。
2.警示漆涂层损伤
1)去除损伤区域的涂层
将损伤的涂层打磨去除,注意不能损伤叶片复合材料本体和其他区域的涂层。打磨完毕后用干净的抹布蘸酒精清理干净表面。