汽车车身设计方法
汽车车身设计及制造工艺新技术分析

汽车车身设计及制造工艺新技术分析随着汽车行业的不断发展,车身设计及制造工艺技术也在不断地更新和升级。
在这篇文章中,我们将对汽车车身设计及制造工艺新技术进行分析,探讨其对汽车行业的影响以及未来的发展趋势。
一、汽车车身设计新技术分析1. 轻量化设计技术随着环保意识的增强和能源危机的加剧,轻量化设计技术成为汽车行业的热门话题。
轻量化设计通过采用更轻、更坚固的材料来减轻车身重量,达到降低燃油消耗、提高能源利用率的目的。
目前,碳纤维复合材料、铝合金和镁合金等新材料的应用成为轻量化设计的主要趋势。
这些新材料具有密度低、强度高的特点,能够在保证车身安全性的前提下显著减少整车重量,提高汽车的动力性能和燃油经济性。
2. 智能化设计技术随着人工智能和大数据技术的快速发展,智能化设计技术也逐渐在汽车行业中得到应用。
智能化设计技术通过借助计算机仿真和虚拟现实技术,实现对车身结构的优化设计和自动化生产。
这种技术能够提高设计效率,降低成本,同时还能够更精确地预测车身在碰撞、扭曲等情况下的变形和破坏情况,为车身设计和工艺提供更科学的依据。
3. 模块化设计技术随着汽车产品线不断丰富和多样化,模块化设计技术成为一种普遍的设计趋势。
模块化设计技术能够将车身结构分割成不同的模块,并且通过标准化和通用化的设计,使得不同车型之间的共用率提高,降低制造成本。
模块化设计技术还能够提高生产效率,减少生产周期,更好地适应市场需求的快速变化。
二、汽车车身制造工艺新技术分析1. 激光焊接技术传统的汽车车身焊接工艺主要采用点焊和焊锡等方式,而激光焊接技术则是一种新型的高效、精确的焊接工艺。
激光焊接技术能够快速并且精确地完成焊接工作,焊接接头的质量更加可靠,焊接变形、气泡等缺陷减少,大大提高了车身的质量和稳定性。
与传统焊接相比,激光焊接技术还可以减少对环境的污染和对工人的伤害,是一种环保型的制造工艺。
2. 涂装技术涂装工艺是汽车制造过程中的重要环节,也是保证汽车外观质量和耐久性的关键。
汽车车身刚性设计

汽车车身刚性设计在汽车工程领域中,车身刚性设计是一个至关重要的方面。
车身刚性直接关系到汽车的安全性、稳定性和乘坐舒适性。
本文将从汽车车身刚性设计的原理、优化方法以及发展趋势等方面进行探讨。
一、汽车车身刚性设计的原理汽车车身的刚性主要指的是车身的扭转刚性和弯曲刚性。
扭转刚性是指车身在行驶过程中扭转变形的能力,弯曲刚性则是指车身在受力下弯曲变形的能力。
这两个刚性指标越高,说明车身结构越稳定,具有更好的行驶性能和安全性。
车身刚性设计的原理主要包括以下几个方面:1. 结构优化:通过钢材的选择和优化布局来提高车身的刚性。
高强度钢材的使用可以增加车身的刚度,并且减少车身重量。
2. 加强梁的设计:在车身结构关键位置设置加强梁,可以有效地提高车身的刚性。
特别是在车身的前后部分和底部,加强梁的设置可以提升整体刚性。
3. 空间结构设计:合理的空间结构设计可以增加车身的刚性。
例如,设置横梁和纵梁等结构,能够有效地减少车身的形变和振动。
4. 焊接技术:采用先进的焊接技术来提高车身的整体刚性。
优化焊接点的设计,使焊接点具有更好的连接性和刚性。
二、汽车车身刚性设计的优化方法为了实现更好的车身刚性设计,汽车工程师需要采用一些优化方法。
下面介绍几种常见的优化方法:1. 结构拓扑优化:通过数值模拟和仿真分析,找到车身结构中的薄弱环节,并进行结构调整和优化。
通过减少材料的使用和改变结构布局,来提高车身刚性。
2. 材料优化:选择高强度、高刚性和轻量化的材料,如高强度钢、铝合金等,来替代传统的钢材。
同时,还可以采用复合材料和纤维增强材料等,以进一步提高刚性和降低重量。
3. 车身加固:在车身结构中加入加强件,如加强梁、加固板等,以提高车身的整体刚性。
通过有限元分析和试验验证,确定加固部位和加固方式,实现刚性的最优化设计。
三、汽车车身刚性设计的发展趋势随着汽车工业的不断发展和技术的进步,汽车车身刚性设计也在不断演进。
以下是一些当前和未来的发展趋势:1. 轻量化设计:为了减少车身重量,提高燃油经济性和环保性能,汽车制造商将采用更多的轻质材料,如碳纤维复合材料、镁合金等。
车身主断面设计规范及要点

02
03
多目标优化
拓扑优化
综合考虑刚度、强度、NVH性能 等多个目标,采用多目标优化算 法对车身主断面进行优化设计。
运用拓扑优化技术对车身主断面 进行材料分布Байду номын сангаас化,实现轻量化 设计。
实例分享:某车型主断面优化过程剖析
01
初始设计分析
对某车型初始设计的车身主断面 进行仿真分析,评估其性能表现
。
03
优化结果验证
行业的健康、可持续发展做出了贡献。
未来发展趋势预测
智能化设计
随着人工智能和大数据技术的不断发展,未 来车身主断面设计将更加智能化,能够实现 自动化设计、优化和仿真。
轻量化设计
为了满足日益严格的节能环保要求,车身主断面设 计将更加注重轻量化,采用高强度轻质材料和先进 的制造工艺。
个性化定制
随着消费者需求的多样化,车身主断面设计 将更加注重个性化定制,以满足不同消费者 的审美和功能需求。
输入条件收集
收集造型、总布置、动力系统、底盘系统等相关专业的 输入条件,明确主断面的设计约束和依据。
设计方案制定
基于设计目标和输入条件,制定主断面的初步设计方案 ,采用高强度钢材料和高刚度连接方式。
仿真分析与优化
利用CAE分析软件对设计方案进行仿真验证,发现刚度 不足和NVH性能不佳的问题,对设计方案进行优化改 进,采用局部加强结构和阻尼材料等措施。
组织专家对主断面设计方案进行评审,并 根据评审意见进行修改完善,最终发布设 计结果。
关键技术与方法应用
多学科优化技术
综合考虑车身结构、材料、工艺等多方面 的因素,对主断面设计方案进行多学科优
化,提高设计质量和效率。
A 有限元分析技术
汽车车身结构设计技术与方法
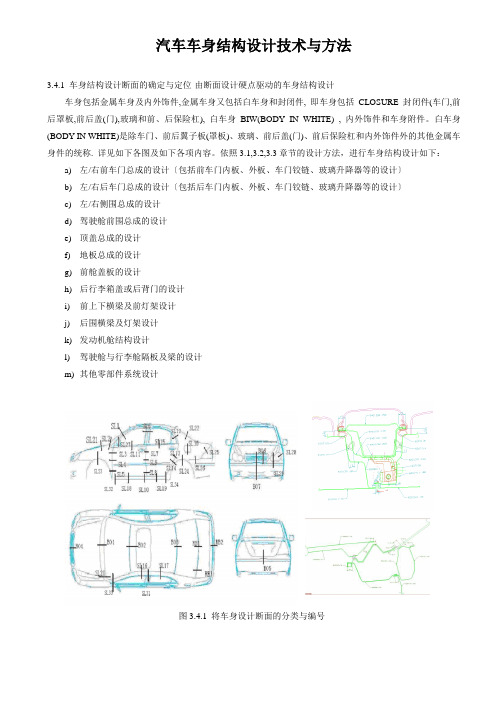
汽车车身结构设计技术与方法3.4.1 车身结构设计断面的确定与定位-由断面设计硬点驱动的车身结构设计车身包括金属车身及内外饰件,金属车身又包括白车身和封闭件, 即车身包括CLOSURE封闭件(车门,前后罩板,前后盖(门),玻璃和前、后保险杠), 白车身BIW(BODY IN WHITE) , 内外饰件和车身附件。
白车身(BODY IN WHITE)是除车门、前后翼子板(罩板)、玻璃、前后盖(门)、前后保险杠和内外饰件外的其他金属车身件的统称. 详见如下各图及如下各项内容。
依照3.1,3.2,3.3章节的设计方法,进行车身结构设计如下:a)左/右前车门总成的设计〔包括前车门内板、外板、车门铰链、玻璃升降器等的设计〕b)左/右后车门总成的设计〔包括后车门内板、外板、车门铰链、玻璃升降器等的设计〕c)左/右侧围总成的设计d)驾驶舱前围总成的设计e)顶盖总成的设计f)地板总成的设计g)前舱盖板的设计h)后行李箱盖或后背门的设计i)前上下横梁及前灯架设计j)后围横梁及灯架设计k)发动机舱结构设计l)驾驶舱与行李舱隔板及梁的设计m)其他零部件系统设计图3.4.1 将车身设计断面的分类与编号图3.4.2 基于参考车型的BENCHMARK断面的断面设计图3.4.3 选定车身密封断面的设计方案车身结构设计的步骤与过程如下所述:图3.4.5 建立benchmark车型白车身数字化原型车设计建模造型面硬点3.4.2 开闭件设计开闭件(CLOSURE)一样包括4门2盖或5门1盖(两厢有后尾门汽车)。
1、车门设计车门外板设计是依照光顺好的整体造型面和车门轮廓线的切割面片基础上加上周边翻边和门锁等特点后的车身零件. 分缝线通过两种方法获得(a)一样先将汽车内外外观面整体造型面光顺到A级曲面(CLASS A), 同时将造型边界线投影到XZ铅垂平面后光顺到A级曲线, 然后采纳该投影的边界线投影到光顺好的A级大造型面上与造型面相交获得的边界线,该交线理论上确信也是A级曲面。
汽车车身研发设计流程

汽车车身研发设计流程一、需求分析在汽车车身研发设计的最初阶段,首先要进行需求分析。
这一步骤主要确定新车型的定位、目标市场、消费者需求和竞争对手情况等。
通过对这些信息的综合分析,为后续的设计工作提供明确的方向和目标。
二、概念设计基于需求分析的结果,进行概念设计。
这一阶段主要关注整体造型、风格和车型定位等方面的设计。
通过初步的三维建模和效果图制作,展现新车型的外观和内饰设计理念。
三、详细设计在概念设计得到认可后,进入详细设计阶段。
这一阶段涉及对新车型各个部件的详细设计,如车身结构、零部件尺寸和装配关系等。
同时,还需进行初步的工艺分析和可行性评估。
四、结构设计在详细设计的基础上,进行结构设计。
这一步骤主要关注车身结构和各个零部件的精确建模与设计。
确保结构设计满足性能要求、工艺性和装配需求。
五、性能模拟在结构设计完成后,通过使用专业的仿真软件进行性能模拟,以评估新车型的性能表现。
这包括碰撞安全、动力学性能、空气动力学等方面的模拟。
六、工艺性审查在性能模拟得到满意结果后,进行工艺性审查。
这一步骤主要评估新车型的可制造性和生产效率。
确保新车型的制造工艺可行,设备需求合理,并满足生产节拍要求。
七、供应商选择根据新车型的零部件需求,选择合适的供应商进行合作。
这一过程需综合考虑供应商的技术能力、产品质量、成本和交货期等因素。
与供应商建立良好的合作关系,确保零部件供应的可靠性和经济性。
八、样品制作与测试在确定了零部件供应商后,开始制作新车型的样品并进行一系列的测试。
这些测试包括但不限于装配测试、性能测试、环境适应性测试和碰撞安全性测试等。
确保新车型在实际生产中表现良好,符合设计要求和安全标准。
九、设计验证在样品测试完成后,进行设计验证阶段。
这一步骤主要是对新车型的设计进行全面评估和审核,确保设计满足所有要求,并进行必要的优化和改进。
通过第三方审核或专家评估来进一步确认设计的可靠性和有效性。
十、投产准备在设计验证得到批准后,开始投产准备阶段。
3.1 汽车车身设计开发流程与方法

第三章汽车车身设计开发技术与方法3.1汽车车身设计开发流程与方法学3.1.1车身设计开发主要工作内容及流程(程序)1)车身总布置设计及安全法规计算校核(或三维数字虚拟样机Archetype)2)造型设计3)三维曲面和造型面设计4)1:5或1:4 模型及1:1外模型制作或数控加工(或三维数字模型)5)1:1内模型(或三维数字模型)6)发动机舱三维数字模型7)地板三维数字模型8)测量与曲面光顺9)白车身结构详细设计(BIW)(9.1)1:1外模型光顺后数据分块(9.2) 车身设计断面的定义与尺寸确定(9.3) 密封结构确定与密封件选择(9.4) 确定分块线(9.5) 与车身有关的设计硬点的确定(9.6) 左右侧围设计(A, B, C, D柱设计, 前后翼子板设计)(9.7) 顶盖设计(外板, 横梁与纵边梁设计) (9.8) 发动机前围板设计(9.9) A柱下段设计(9.10) 发动机舱与前轮包设计(9.11) 前后灯具设计(9.12) 格栅设计(9.13) 前围板设计(9.14) 前保险杠设计(9.15) 地板总成设计(前中后)(9.16) 后门总成设计(9.17) 前门总成设计(9.18) 尾门总成设计(9.19) 前发动机罩设计(9.20)前风当总成设计10)内饰、外饰设计11)先行车, 螺钉车或概念车的(Prototype)试制,第二轮试验样车(定型车)试制12)碰撞与结构分析及结构优化设计13)成型过程仿真14) 模具与工艺工装设计如图3.1.1为车身详细设计阶段面向对象的产品模型(OPM)并行设计流程图OM2 OM2 OM2 OM2 OM2 OM2T21: CAD T22: DF A可装配设计T23: CAE T24: 评审T25: DFM 可制造设计T26: CS 碰撞仿真IM21: 输入产品模型,请求详细设计OM21: 向下游预发布零部件信息OM22: 输出DF A结果OM23: 输出CAE结果OM24: 输出同意或修改概要设计建议OM25: 输出DFM结果输出OM26: CS结果图3.1.1 汽车车身并行详细设计OPM模型31 32 3334 35T 31: CAPP T 32: CAFD 机算机辅助工装卡具设计(CA FIT DE SIGN)T 33: CAM T 34: MPS(制造过程仿真) T 35: 评审 IM 31: 请求加工过程设计 OM 31: 输出CAPP 结果 OM 33: 输出 CAFD 结果OM 33: 输出CAM 结果 OM 34: 输出MPS结果OM 35: 输出同意或修改详细设计建议图3.1.2 汽车产品开发试制与加工过程设计OPM 模型 g 1: 请求详细设计(结构) g 2: 预发布零部件消息,请求试制或加工过程设计 g 3: 请求修改概念设计(造型设计) g 4: 请求修改详细设计(结构设计)图3.1.3 汽车车身并行开发过程OPM 模型图3.1.4 车型数字化设计过程3.1.2 车身结构设计方法学1 1995年后的先进的车身设计技术与方法1995年后车身设计技术发展与市场需求体现在如下几个方面:图3.1.5 虚拟产品开发描述图3.1.6 白车身设计过程描述图3.1.7 并行设计与开发周期降低图3.1.8 全数字化设计方法图3.1.9 确定设计结构方案图3.1.10 产品设计及工艺设计集成计方法图3.1.12 参数化结构断面设计图3.1.13 全相关参数化的车身开发全过程2 数字化车身结构设计方法学(1)设计硬点设计区的设计方法复杂的结构实际上是众多简单的设计的叠加组合(复杂设计简单化)任何复杂的车身结构设计与设计结果都是由如下两个方面决定: (a) 满足诸多设计硬点的特征结构设计(HARDPOINT DESIGN AREA), 例如, 造型面硬点, 与车身有关的零部件装配孔面及结构等设计硬点, 选定的设计断面结构, 造型分界线硬点, 造型形状形成的设计断面引导线硬点, 车身零件间的焊接装配面, 零件的分块线硬点. (b) 自由设计区设计(FREE DESIGN AREA), 即在满足设计硬点基础上, 进行的自由设计区, 一般非设计硬点的设计区域都属于自由设计区, 自由设计区不同的设计人员会得到不同的设计结果, 这也是自由设计区自由的特点, 但这不等于自由设计区可以胡乱设计, 应遵循如下一些设计原则, 以便才能使设计结构更合理, 水平更高.因此车身设计过程与方法应满足如下公式:车身结构设计特征(BSDF)=自由设计区自由设计特征(FDF)+断面设计硬点决定的设计特征(SDHF)+造型设计硬点决定的特征(IDHF)+造型决定的断面引导主轴线(一个零件多个断面几何中心连线)特征(ISSF)+其他附件或COPY件等确定的设计硬点特征(CDHF)+零件分块线与焊接边界线等的设计硬点特征(BDHF)即为:BSDF=FDF+SDHF+IDHF+ISSF+CDHF+BDHF车身零件结构的设计过程或设计建模(BSDP or BSDM)=用三维CAD软件完成车身结构设计特征的过程或结果(BSDFP or BSDFM)即为:BSDP=BSDFPBSDM=BSDFM车身设计建模(BDM)=完成所有车身零件的设计建模与装配设计建模的总称(TOL_BSDM) 即为:BDM=TOL_BSDM全数字化车身设计开发(BDD)=采用三维CAD 软件完成全部车身设计建模, 并采用CAD/CAE/CAM一体化技术完成车身设计,结构优化及制造(或制造模具)的全过程(3D_CAD/CAE/CAM_BDM).即为:BDD=3D_CAD/CAE/CAM_BDM(2) 自由设计区的设计方法与设计原则a 自由设计区的设计方法(a) 先用三维CAD软件将设计硬点确定的结构与特征连接成一体, 成为一个粗的异型大面, 中间可以用一些平面与设计硬点面的相交获得连接线或倒角线.(b) 对设计硬点之间形成的设计区域-自由设计区每一个进行分析, 强度和刚度一般性要求的部位一般小于50*50mm的面积区域, 可以不加特征结构(加强筋, 加强沉孔(如果没有密封要求), 折边, 卷边等特征结构建模), 但要在边界上导角. 大于50*50的区域一般要加特征以便加强结构并导角,较大的区域不留任何空地, 以便使刚度最大, 材料最省.a 自由设计区的设计准则(a) 最大刚度原则- 自由设计区必须尽力获得最大刚度的设计原则, 因此, 要加加强筋和加强沉孔, 以便获得高水平的设计结构.(b) 最轻量化原则- 设计结构要确保满足刚度要求的基础上使材料最省的原则, 尽可能使结构设计可以使料厚簿一些, 没有密封要求的结构可以用沉孔以便轻量化与刚度最大化的双嬴, 等要充分考虑结构形式和结构方案.(c) 最大园角原则-自由设计区, 一般都是内部结构区域, 不在外观缝隙线条区域. 因此, 为了提高冲压工艺性, 减少制造成本, 应尽可能设计较大的设计过渡园角. 但不能影响设计硬点结构. 在在外观区域应尽可能最小园角原则,最小值为料厚(d) 特征结构最大斜度原则- 筋槽设计的立面尽可能采用较大的斜度. 以便获得较好的制造工艺性, 防止冲压裂纹和褶皱.(e) 最符合工艺性原则-从设计结构上和面的光顺程度上尽可能获得好的制造工艺性, 如材料流动均匀性与制造可能性.(f) 创新与多样化设计原则-自由自由就意味着允许多样化, 也就是创新原则.(g) 最复杂化原则, 因为模具加工不会增加制造成本, 只会降低成本(如材料轻, 成本低了).(h) 满足CAE/OPTIMIZATION结构优化分析设计要求.。
CATIA汽车车身设计

CA TIA汽车车身设计方法汽车车身除了要有漂亮的外表和与众不同的个性特征,同时还要能安全可靠地行驶,这就需要整个设计过程融入各种相关知识,包括车身结构、制造工艺要求、空气动力学、人机工程学等。
细化开发流程与同步开发手段,对于设计出消费者认可的新车型至关重要。
汽车车身设计简单理解是根据一款车型的多方面要求来设计汽车的外观及内饰,使其在充分发挥性能的基础上艺术化。
汽车车身除了要有漂亮的外表和与众不同的个性特征,同时还要能安全可靠地行驶,这就需要整个设计过程融入各种相关的知识:车身结构、制造工艺要求、空气动力学、人机工程学、工程材料学、机械制图学、声学和光学知识。
从一个灵感到最后实现,需要一系列的步骤。
得到市场的认可,性能优良的内“芯”,再加上一袭新衣包装,才是新车待嫁时。
下面,让我们看看正向设计如何为一款新车设计“嫁衣”。
项目策划项目策划包括:项目计划、可行性分析、项目决策及组建项目组等几个方面。
图1为项目策划阶段的示意图。
图1 项目策划阶段示意图汽车企业的产品规划部门必须做好企业产品发展的近期和远期规划,具有市场的前瞻性与应变能力。
项目前期需要在市场调研的基础上生成项目建议书,明确汽车形式及市场目标。
可行性分析包括:政策法规分析、竞争对手和竞争车型、自身资源和研发能力的分析等。
项目论证要分析与审查论点的可行性和论据的可靠性与充分性。
经过这一阶段,要开发一个什么样的车型,类似于同行什么等级的车型,其性价比方面有哪些创意与特点即展现在我们面前。
项目策划的最后阶段是组建项目组:组建新品开发项目小组、确立项目小组成员的职责、制定动态的项目实施计划、明确各阶段的项目工作目标、规定各分类项目的工作内容、计划进度和评价要求。
概念设计阶段概念设计在新产品开发中有着重要地位,因此,新产品概念设计流程再造是新产品开发流程再造成败的关键所在。
一个全新的汽车创意造型设计分为以下几部分:1. 总体布置草图设计:绘制产品设计工程的总布置图(如图2),一方面是汽车造型的依据;另一方面它是详细总布置图确认的基础,在此基础上将产品的结构具体化,直至完成所有产品零部件的设计。
现代汽车车身设计技术课件(完整篇)

现代汽车车身设计技术课件第一部分:引言汽车车身设计是汽车工业中至关重要的一环,它不仅关系到汽车的外观美感,还直接影响到汽车的空气动力学性能、安全性能和舒适性。
随着科技的进步和消费者需求的不断变化,现代汽车车身设计技术也在不断发展和创新。
本课件将带您深入了解现代汽车车身设计技术,包括设计理念、设计流程、材料选择、制造工艺等方面的内容。
一、设计理念现代汽车车身设计强调以人为中心,注重用户体验和情感共鸣。
设计师们通过研究消费者的需求和喜好,结合汽车品牌的特点和定位,创造出符合时代潮流和审美趋势的车身造型。
同时,设计师们还注重车身设计的创新性和可持续性,力求在满足功能需求的同时,实现环保和节能的目标。
二、设计流程1. 市场调研:了解消费者的需求和喜好,分析竞争对手的产品特点,为车身设计提供依据。
2. 概念设计:根据市场调研结果,设计师们提出初步的设计方案,包括车身造型、颜色、材质等方面的构思。
3. 详细设计:在概念设计的基础上,设计师们对车身各个部分进行详细设计,包括车身结构、车门、车窗、车灯等。
4. 工程设计:工程师们根据详细设计图纸,进行车身结构的强度和刚度分析,确保车身的安全性能。
5. 制造工艺设计:根据工程设计图纸,设计师们制定车身制造的工艺流程,包括冲压、焊接、涂装等环节。
6. 试制和验证:根据制造工艺设计,制造出实车样品,进行各项性能测试和验证,确保设计目标的实现。
三、材料选择现代汽车车身设计在选择材料时,需要考虑材料的强度、刚度、轻量化、耐腐蚀性、可回收性等多个方面的因素。
常用的车身材料包括钢材、铝合金、镁合金、碳纤维复合材料等。
设计师们根据车身各个部位的功能需求,选择合适的材料,以实现最佳的性能和成本平衡。
四、制造工艺现代汽车车身制造工艺包括冲压、焊接、涂装等环节。
冲压工艺用于制造车身的外覆盖件,如车门、车顶、翼子板等;焊接工艺用于将各个冲压件焊接成完整的车身结构;涂装工艺用于提高车身的耐腐蚀性和美观性。
- 1、下载文档前请自行甄别文档内容的完整性,平台不提供额外的编辑、内容补充、找答案等附加服务。
- 2、"仅部分预览"的文档,不可在线预览部分如存在完整性等问题,可反馈申请退款(可完整预览的文档不适用该条件!)。
- 3、如文档侵犯您的权益,请联系客服反馈,我们会尽快为您处理(人工客服工作时间:9:00-18:30)。
不能用一般的机械制图方法将它完整地表现出来。在产品设计生产准备和投产等阶段中,实 物可以补充图样之不足,保证成套工艺装备(模具和裝焊夹具等)之间乃至零件之间的协调 验证。正因为如此,决定了车身设计的复杂性。
现形式:表示整车(图2-3)的,该图最好按照透视规律绘制并配以色彩,要求
逼真、形象,以收到使未来新车型跃然纸上的效果;表示局部效果的,这时只
要求细致刻划和突出需要琢磨的部位,如:车头、后尾、前脸以及内饰等等。
在车身内饰图上应具体地反映出车身内部装饰(如仪表板、座椅、侧壁的覆饰和有
关附件等)的效果。
• 在绘制效果图的过程中,
动机和传动系的布置等),以轿车为例,绘制1:5车身布置的三视图(图2-2)。在此图中,应初
步确定车身的主要控制尺寸,如:前悬与后悬、前、后风窗位置及其倾角、前围板位置、
发动机高度、地板高度、座椅布置、操纵机构布置以及内部空间的控制尺寸等。
• 2. 绘制l:5的彩色效果图
•
在上述车身布置图的基础上绘制多方案的彩色效果图,此种图有多种表
• 6.制作1:1内部模型
•
此模型一般均采用木制骨架如图2-7所示,其内部覆饰和装备(如仪表板、
座椅和方向盘等)则尽量采用或借用实物。其目的主要在于检验内部布置尺
寸(考虑操纵方便性、乘坐舒适性以及上下车方便性和视野性等)及内部装饰效果。
•
根据1:1油泥模型和内部模型,可以确定车身表面和车身的结构,门
悦目的色彩使人获得美感享受。车身外形还可反映时代的风貌、民族传统和独特的企业形
象。它的外形设计、制图和结构计算方法、制造与装配工艺均不同于其他总成的设计。在
传统的车身设计中,要制作主图板和主模型;而在现代的汽车车身设计中要建立数字化车
身模型,这是其他机械产品很少进行的工作。
3. 车身的结构设计有独特的要求。
第2章 汽车车身设计方法
● 汽车车身设计的特点 ●传统车身设计方法 ●现代车身设计方法
迈腾以技术见长入市,其 高科技一直是其宣传的两点, 其中运用到安全方面的科技所 占比例最大。迈腾采用了高强 度车身结构设计,车身结构 74%采用了高强度和超高强度 钢板,其中关键结构都采用工 艺技术更高的热成型钢板;并 采用空腔灌蜡技术,保证12年 防锈穿;同时还不惜成本运用 了无缝激光焊接技术,焊缝总 长度达42米,焊缝接合达到分 子层面,碰撞时只会变形而不 会断裂,使得车身达到了整体 钢板的强度。
现代车身结构分析方法常采用数值模拟和试验分析方法,现代数值模拟分析方法主要是 指有限元分析方法;现代试验分析方法主要是指电测法,即应用传感器、测量和分析仪器对 车身实物零部件或小比例模型进行支承加载和测试,这是数值分析模型验证的主要手段。
4. 车身设计时除满足车身应有一定的强度、刚度要求外,还应 进行防振降噪、碰撞安全性、金属材料缓蚀性及轻量化方面的 结构设计。
车身的零件繁多、结构复杂,一般轿车白车身由约400~500多个冲压件组成。车身所受 载荷复杂,包括驱动、制动、转弯等;惯性力,还包括路面反力和作用于不同位置的发动机 等总成载荷。车身边界复杂,不同的悬架种类在不同情况下对车身产生不同的约束和支承, 因此在设计计算时一般无法获得汽车车身结构的强度、刚度和模态的解析解。
2.1 汽车车身设计特点
•
车身是一个薄壳曲面封闭体,相当于一个临时住所或活
动的建筑物,但又都受到质量和空间的限制。因此,车身设
计有别于汽车上其他总成的设计,有其自身的设计特点。
• 汽车车身设计的特点是:
• 1. 汽车车身设计涉及面广,远远超出一般机械产品的范围。
•
车身设计要考虑节能、环保、安全三大主题;要考虑空气动力学、人机工程学要求;
• 4. 绘制1:1线型图
•
此图是在初步设计的基础上进行绘制的,因为从线型图可以大致
观察汽车的外形轮廓,所以这一步的目的在于发现和修正前一阶段初
步设计中小模型上所暴露的问题。据此可以从各个角度面对竖置的线
ቤተ መጻሕፍቲ ባይዱ
型图(图2-5)进行观测,这样可检验放大后的效果,以便作适当的修改,
从而避免后续各步走弯路而导致不必要的返工。
2.2 传统车身设计方法
•
传统车身设计方法规定车身图样必须采用刻有坐标网格的铝板,同
时还必须制作三维立体模型作为设计的依据,形成了整套较复杂的设计
方法。该方法分为初步设计和技术设计两个阶段,其过程如图l-l所示。
一、传统车身设计方法的步骤:
• 1. 车身总布置草图设计
•
根据整车的初步控制尺寸(汽车的总长、总宽、总高、轴距、轮距等)和总布置方案(发
的1/5)的平台上,模型上也划分有相应的网格线(见图2-4)。模型的外表各部(如前
脸、屋灯、门把手等)应力求细致,以便于观察其立体效果。
•
在雕塑此模型的过程中,出于审美实感的要求,还可能要对1:5车身布置图
和彩色效果图作某些相应的非原则性的补充和小修改。由此可见,以上三步实
际土是相辅相成,反复交叉进行的。
• 出于审美的要求,往往需
• 要对上述车身布置图的线
• 型作相应的修改。至此即
• 可广泛征求意见,从中初
• 步选定一种满意的方案。
• 3. 雕塑1:5的油泥模型
•
以1:5车身布置图的外形尺寸和彩色效果图的外观为依据,即可进行雕掣
1:5油泥(或石膏)模型。此模型应定位安放在刻有坐标网格线(每格距离为200mm
• 5.雕塑1:1油泥模型
•
此模型实际上是经修改过后的1:5油泥模型的放大模型(如图2-6所
示),它反映了未来新车的立体造型效果,模型上和平台上也都刻划有
相应的坐标网格(每格距离为200mm)。此模型要求表面光整、曲线
连续、能较准确地反映出车身各部分曲面的外形。这样才能从模型上
直接取得样板,以供绘制主图板作依据。
设计时还涉及车身造型艺术、内部装饰、取暖、通风、防振隔声、密封、照明以及人体工
程等。另外,同时还要保证其具有足够的强度和刚度,以保证运行中的可靠性,这涉及结
构力学、计算数学和计算机等方面的知识。
• 2.汽车车身设计方法有别于汽车上其他总成。
•
车身不仅是一个产品,还是一件精致的艺术品,它以其优雅的雕塑形体、内外装饰及