等温变换技术应用于各类煤气化变换装置简介
煤制合成氨不同等温变换技术探讨

煤制合成氨不同等温变换技术探讨曹志斌【摘要】2 kinds of isothermal conversion technologies used in HT-L for pulverized coal pressure gasification were introduced.Respectively from the process scheme,shift converter configuration,key equipment,catalyst and utility consumption as well as economic and technical indicators,the 2 technologies were compared and analyzed.The results showed that both processes had their respective advantages.But because the actual application time was short,the company should take overall consideration according to its situation and choose the isothermal conversion technology suitable for it.%介绍了应用于航天炉粉煤加压气化制合成氨过程的两种等温变换工艺技术,分别从工艺方案、变换炉配置、关键设备情况、催化剂、公用工程消耗以及经济技术指标等方面,对两种等温变换技术进行了比较和分析,企业在进行选择时,应根据自身情况,综合考虑,选择适用于自身的等温变换技术.【期刊名称】《煤化工》【年(卷),期】2017(045)004【总页数】3页(P34-36)【关键词】航天炉;等温变换工艺;合成氨;变换炉;催化剂;公用工程【作者】曹志斌【作者单位】航天长征化学工程股份有限公司兰州分公司,甘肃兰州730010【正文语种】中文【中图分类】TQ54航天粉煤加压气化(简称航天炉)于2009年进入长周期稳定运行以来,广泛应用于煤制烯烃、煤制乙二醇、煤制油、煤制己内酰胺等传统煤化工和新型煤化工领域。
“水移热等温变换技术”成功用于低水气比变换装置
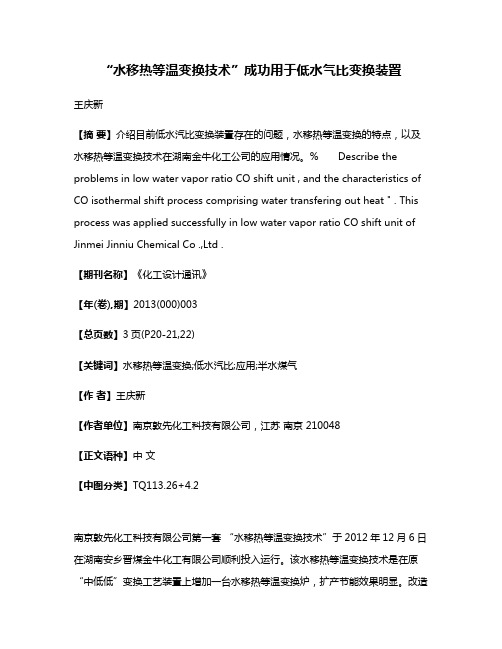
“水移热等温变换技术”成功用于低水气比变换装置王庆新【摘要】介绍目前低水汽比变换装置存在的问题,水移热等温变换的特点,以及水移热等温变换技术在湖南金牛化工公司的应用情况。
% Describe the problems in low water vapor ratio CO shift unit , and the characteristics of CO isothermal shift process comprising water transfering out heat " . This process was applied successfully in low water vapor ratio CO shift unit of Jinmei Jinniu Chemical Co .,Ltd .【期刊名称】《化工设计通讯》【年(卷),期】2013(000)003【总页数】3页(P20-21,22)【关键词】水移热等温变换;低水汽比;应用;半水煤气【作者】王庆新【作者单位】南京敦先化工科技有限公司,江苏南京 210048【正文语种】中文【中图分类】TQ113.26+4.2南京敦先化工科技有限公司第一套“水移热等温变换技术”于2012年12月6日在湖南安乡晋煤金牛化工有限公司顺利投入运行。
该水移热等温变换技术是在原“中低低”变换工艺装置上增加一台水移热等温变换炉,扩产节能效果明显。
改造后变换系统出口CO 含量由原来的1.2%降至0.6%,系统阻力由原来的0.12MPa 降至0.07MPa,吨氨蒸汽消耗下降了135kg,变换冷却水消耗下降了20m3,同时副产0.7MPa饱和蒸汽236kg,供造气及铜洗使用,热水循环量由原来的9860kg降至5 670kg,热水塔出口温度由原来的104℃降至84℃。
水移热等温变换炉投运后,湖南安乡晋煤金牛化工有限公司停运一台4t/h沸腾锅炉。
水移热等温变换炉为全径向结构,催化剂床层阻力几乎测不出来,同平面温差不超过5℃。
等温变换在水煤浆加压气化变换装置中的应用
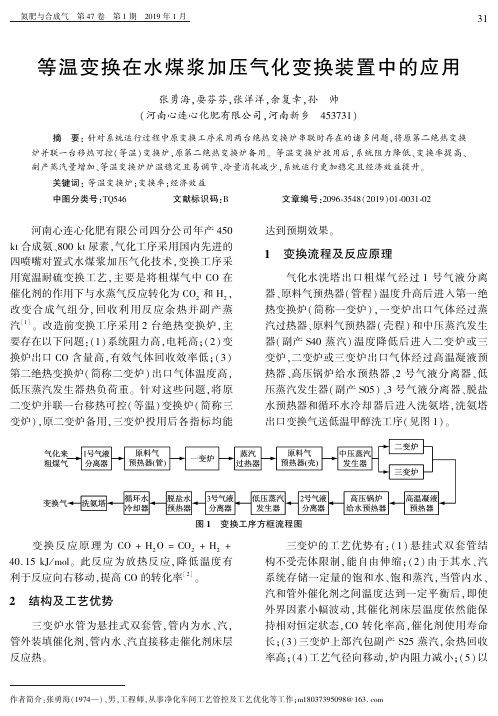
作者简介:张勇海(1974 )ꎬ男ꎬ工程师ꎬ从事净化车间工艺管控及工艺优化等工作ꎻm18037395098@163.com等温变换在水煤浆加压气化变换装置中的应用张勇海ꎬ耍芬芬ꎬ张洋洋ꎬ余复幸ꎬ孙㊀帅(河南心连心化肥有限公司ꎬ河南新乡㊀453731)㊀㊀摘㊀要:针对系统运行过程中原变换工序采用两台绝热变换炉串联时存在的诸多问题ꎬ将原第二绝热变换炉并联一台移热可控(等温)变换炉ꎬ原第二绝热变换炉备用ꎮ等温变换炉投用后ꎬ系统阻力降低㊁变换率提高㊁副产蒸汽量增加㊁等温变换炉炉温稳定且易调节㊁冷量消耗减少ꎬ系统运行更加稳定且经济效益提升ꎮ㊀㊀关键词:等温变换炉ꎻ变换率ꎻ经济效益㊀㊀中图分类号:TQ546㊀㊀㊀㊀㊀文献标识码:B㊀㊀㊀㊀㊀文章编号:2096 ̄3548(2019)01 ̄0031 ̄02㊀㊀河南心连心化肥有限公司四分公司年产450kt合成氨㊁800kt尿素ꎬ气化工序采用国内先进的四喷嘴对置式水煤浆加压气化技术ꎬ变换工序采用宽温耐硫变换工艺ꎬ主要是将粗煤气中CO在催化剂的作用下与水蒸气反应转化为CO2和H2ꎬ改变合成气组分ꎬ回收利用反应余热并副产蒸汽[1]ꎮ改造前变换工序采用2台绝热变换炉ꎬ主要存在以下问题:(1)系统阻力高ꎬ电耗高ꎻ(2)变换炉出口CO含量高ꎬ有效气体回收效率低ꎻ(3)第二绝热变换炉(简称二变炉)出口气体温度高ꎬ低压蒸汽发生器热负荷重ꎮ针对这些问题ꎬ将原二变炉并联一台移热可控(等温)变换炉(简称三变炉)ꎬ原二变炉备用ꎬ三变炉投用后各指标均能达到预期效果ꎮ1㊀变换流程及反应原理㊀㊀气化水洗塔出口粗煤气经过1号气液分离器㊁原料气预热器(管程)温度升高后进入第一绝热变换炉(简称一变炉)ꎬ一变炉出口气体经过蒸汽过热器㊁原料气预热器(壳程)和中压蒸汽发生器(副产S40蒸汽)温度降低后进入二变炉或三变炉ꎬ二变炉或三变炉出口气体经过高温凝液预热器㊁高压锅炉给水预热器㊁2号气液分离器㊁低压蒸汽发生器(副产S05)㊁3号气液分离器㊁脱盐水预热器和循环水冷却器后进入洗氨塔ꎬ洗氨塔出口变换气送低温甲醇洗工序(见图1)ꎮ图1㊀变换工序方框流程图㊀㊀变换反应原理为CO+H2O=CO2+H2+40.15kJ/molꎮ此反应为放热反应ꎬ降低温度有利于反应向右移动ꎬ提高CO的转化率[2]ꎮ2㊀结构及工艺优势㊀㊀三变炉水管为悬挂式双套管ꎬ管内为水㊁汽ꎬ管外装填催化剂ꎬ管内水㊁汽直接移走催化剂床层反应热ꎮ三变炉的工艺优势有:(1)悬挂式双套管结构不受壳体限制ꎬ能自由伸缩ꎻ(2)由于其水㊁汽系统存储一定量的饱和水㊁饱和蒸汽ꎬ当管内水㊁汽和管外催化剂之间温度达到一定平衡后ꎬ即使外界因素小幅波动ꎬ其催化剂床层温度依然能保持相对恒定状态ꎬCO转化率高ꎬ催化剂使用寿命长ꎻ(3)三变炉上部汽包副产S25蒸汽ꎬ余热回收率高ꎻ(4)工艺气径向移动ꎬ炉内阻力减小ꎻ(5)以微调汽包蒸汽压力控制床层温度ꎬ床层处于恒温状态ꎬ控制容易ꎬ操作简单[3]ꎮ3㊀投运前后对比3.1㊀阻力对比三变炉投用前后系统压力㊁压差对比见表1ꎮ表1㊀三变炉投用前后系统压力、压差对比阶段系统压力/MPa变换进口温度/ħ系统压差/MPa一变炉压差/MPa二变炉㊁三变炉压差/MPa二变炉运行6.0002360.6270.0770.066三变炉运行5.8852320.5530.0640.027㊀㊀由表1可得:三变炉投运后ꎬ工艺气径向移动ꎬ压差较二变炉压差下降39kPaꎬ系统压差下降74kPaꎬ系统压差的降低致使系统压力随之下降ꎮ3.2㊀变换出口CO对比三变炉投用前后变换出口CO体积分数及变换率对比见表2ꎮ由表2可得:变换反应为放热反应ꎬ三变炉内设有水管将反应热带出ꎬ导致其热点温度较二变炉降低ꎬ有利于CO向H2的转化ꎮ进气量相当的前提下ꎬ系统出口CO体积分数由原来的0.9%下降至目前的0.5%ꎬ整体的变换率维持在98.5%以上ꎮ变换气体积流量按照25万m3/hꎬCO体积分数降低0.4%ꎬ每小时多产生1000m3的H2ꎬ按0.8元/m3计算ꎬ每小时多产生800元的经济效益ꎮ表2㊀三变炉投用前后变换出口CO体积分数及变换率对比阶段二变炉㊁三变炉热点温度/ħ系统进口CO体积分数/%一变炉出口CO体积分数/%一变炉变换率/%系统出口CO体积分数/%二变炉㊁三变炉变换率/%系统变换率/%二变炉运行280~29047.06.880.10.985.697.9三变炉运行230~24046.54.187.60.587.898.53.3㊀副产蒸汽量对比三变炉投用前后副产蒸汽质量流量见表3ꎮ表3㊀三变炉投用前后副产蒸汽质量流量t/h阶段S40S25S05二变炉运行36.85077.00三变炉运行36.4021.0059.20㊀㊀由表3可见:负荷相当的情况下ꎬ副产S40蒸汽质量流量基本不变ꎻ二变炉出气温度在280ħꎬ低压蒸汽发生器副产S05蒸汽质量流量为77t/hꎻ三变炉出气温度降低至235ħꎬ低压蒸汽发生器副产S05蒸汽质量流量减小为59.2t/hꎬ低压蒸汽发生器热负荷降低ꎻ三变炉汽包副产S25蒸汽质量流量为21t/hꎻ二变炉运行时ꎬ蒸汽总质量流量为113.8t/hꎬ三变炉投用后蒸汽总质量流量约增加2t/hꎮ3.4㊀液氮洗氮洗塔负荷对比液氮洗涤近似于多组分精馏ꎬ它是利用H2与CO㊁Ar㊁CH4的沸点相差较大ꎬ将气相的CO㊁CH4㊁Ar溶解到液氮中ꎬ从而达到脱除CO㊁CH4㊁Ar等杂质的目的ꎮ由于N2和CO的气化潜热非常接近ꎬ1mol的CO溶解到液氮中ꎬ相应1mol液氮气化ꎮ液氮吸收CO至一定程度后会影响氮洗塔塔顶净化气微量ꎬ所以氮洗塔内液氮需要不断置换ꎮ氮洗塔内液氮通过塔底减压阀减压后送入氢气分离器㊁气液分离器回收H2㊁CO㊁CH4和N2ꎮ因此ꎬ净化气中CO含量降低势必会造成液氮洗系统冷量消耗减少[4]ꎮ4㊀结语㊀㊀经过改造后ꎬ三变炉温度更易控制ꎬ有利于系统的稳定运行ꎻ变换系统阻力降低ꎬ电耗降低ꎻCO转化率提高ꎻ副产蒸汽量增加ꎻ液氮洗系统冷量消耗减少ꎬ单位产品综合能耗降低ꎮ参考文献[1]㊀许世方ꎬ蒋永刚ꎬ杨国洞ꎬ等.原料结构调整项目中压耐硫变换装置运行总结[J].氮肥与合成气ꎬ2017ꎬ45(10):20 ̄23.[2]㊀汪家铭.CO等温变换技术在合成氨生产中的应用[J].泸天化科技ꎬ2013(3):169 ̄172.[3]㊀王庆新. 水移热等温变换技术 在高水气比㊁高CO变换装置的应用[J].中氮肥ꎬ2013(4):21 ̄22.[4]㊀张寒修ꎬ王延吉.液氮洗生产问题探讨[J].辽宁化工ꎬ2018ꎬ47(3):235 ̄237.(收稿日期㊀2017 ̄12 ̄17)。
等温变换技术等温变换技术等温变换技术等温变换技术

“““等温变换技术等温变换技术等温变换技术等温变换技术””””解决措施解决措施解决措施解决措施公司根据各类变换工艺流程分别系统阻力、降低循环冷却水耗。
我们对湖南安乡晋煤金牛化工有限公司5万吨/年合成氨的中低低装0.8MPa”工艺3t/h2012年12月6日投入运行后:1CO含量由原来的1.2%降至0.6%;20.12MPa降至0.07MPa;3135kg/tNH420m3/tNH50.6 1.3MPa饱和蒸汽236kg/tNH3供造气及铜洗使用;69860kg/tNH3降至5670kg/tNH3710282℃;84t/h沸腾锅炉。
945.6元/tNH3517万吨/年合成氨项目设计一套带有饱和热水塔0.8MPaCO0.7 1.3MPa饱和蒸汽变换系统出口CO≤1.2%供蒸汽消耗≤100kg/tNH31CO≤1.2%;271.2℃;30.05MPa;3100kg/tNH3;48m3/tNH3;55m3/tNH3;适用于无饱和热水塔低水汽比适用于无饱和热水塔低水汽比适用于无饱和热水塔低水汽比适用于无饱和热水塔低水汽比、、、、低低低低COCOCOCO 2.5MPa2.5MPa2.5MPa2.5MPa为例为的““““等温变换技术等温变换技术等温变换技术等温变换技术””””以固定床间歇式气化炉所产低水汽比、低CO单套合成氨装置生产能力达到18万吨/ 2.0 2.7MPa之间。
由于压力CO2、H2S PH低CI-1及其它酸根离子对不锈钢焊缝有腐蚀。
近十年来所建系统压力大于2.0MPa的变换装置均取消了饱和+喷水冷激”的全低变工艺设计理念。
此类11.0MPa左右;2CO反应被移到后续催化剂床层;3统出口CO含量在1.2 1.5%汽消耗一般在350450kg/tNH3;45氧水水加热器、脱盐水加热器以及喷水增湿器等设备均需要选择不锈CI-1用高。
南京敦先化工科技有限公司针对无饱和热水塔低水汽比、低CO半水煤气变换工艺采用我公司“等温变换”专利技术很好得解决了以上问题。
粗煤气co恒等温变换技术及应用

粗煤气co恒等温变换技术及应用粗煤气是煤气化过程中所得到的一种含有大量CO和H2的气体混合物,常被用作能源和原料。
在粗煤气的使用中,高浓度的CO也是一个不可避免的问题。
CO具有极强的毒性和爆炸性,对人类和环境造成极大的危害。
因此,粗煤气中的CO含量必须控制在安全范围内。
而恒等温变换技术是一种用于降低粗煤气中CO含量的有效方法。
该技术基于热力学原理,通过控制反应条件使CO与H2O反应生成CO2和H2,从而使CO含量减少,而H2含量增加。
恒等温变换反应的化学式为:CO + H2O ⇌ CO2 + H2该反应的平衡常数K为:K=[H2][CO2]/[CO][H2O]可以看出,当反应达到平衡时,CO含量与K值成反比,因此可以通过控制反应条件,使K值变小,从而CO含量减少。
恒等温变换反应的控制条件主要有温度、压力和催化剂等。
温度是影响反应速率和平衡常数的重要因素。
反应温度越高,CO含量越少,但同时反应速率也增加,需要消耗更多的能量。
因此,需要在保证反应速率的同时,尽可能降低反应温度。
一般来说,反应温度为350-450℃。
压力也是影响反应速率和平衡常数的因素之一。
压力升高会使反应平衡向生成物方向移动,从而减少CO含量。
但是,压力越高,设备的成本和能量消耗也越大。
因此,需要在不影响设备和能源成本的情况下,选择适当的压力。
一般来说,反应压力为20-40 bar。
催化剂对反应速率和平衡常数也有重要影响。
常见的催化剂包括Fe-Cu、Ni、Co等。
催化剂的特定组成和物理形态会影响反应的速率和选择性。
催化剂的选择应根据具体的反应条件进行优化。
恒等温变换技术在工业上有广泛应用。
一般来说,该技术需要与其他技术结合使用,来实现有效的粗煤气处理。
例如,在工业上,粗煤气先通过两级变换反应器,将CO含量降低到1%以下,然后进入酸性氧化器,将残余的CO完全氧化为CO2。
再加入干燥和洗涤等工艺,最终得到纯净的氢气。
总之,恒等温变换技术是一种有效降低粗煤气中CO含量的方法。
可控移热变换(俗称:等温变换)技术简介-王庆新

“可控移热变换”技术应用于各种煤化工变换装置简介(南京敦先化工科技有限公司王庆新邮编210048)0、前言随着煤制油、煤制天然气、煤制氢、煤制烯烃、煤制乙二醇等现代煤化工向大型化、规模化、集约化发展,传统绝热变换技术已成为现代煤化工发展的瓶颈。
传统煤化工企业(如煤制合成氨、煤制甲醇、炼油及制药企业制氢原料路线改造等)在进行原料路线改造及节能降耗时也在不断寻求先进、节能、抵投资的变换新技术。
南京敦先化工科技有限公司自2010年以来一直只致力于节能环保、低投资、易于大型化的新型变换技术研发工作。
通过多年来不断努力,已将开发的“新型节能深度转化可控移热变换工艺”(以下简称:可控移热变换)和“非均布可控移热变换炉(以下简称:可控移热变换炉)”等专利技术成功应用到粉煤加压气化、水煤浆加压气化、间歇式固定床常压气化的水煤气或半水煤气的变换装置上。
目前在建的有5套、已经投入运行的6套,近期有数家煤制油、煤制天然气、煤制氢、煤制乙二醇、煤制甲醇、煤制合成氨等业主正在于我们洽谈。
首套可控移热变换装置于2012年年底在安乡晋煤金牛化工有限公司投入运行,至今近两年时间,各项指标超过设计值。
用于4.0MPa粉煤加压气化水煤气的可控移热变换装置于2014年4月在安徽昊源化工集团有限公司成功投入运行,与传统绝热变换工艺相比,设备减少减少了近1/3、流程缩短了1/2、工程总投资减少了1/4、系统阻力仅为0.09MPa。
2014年6月,该套可控移热变换装置顺利通过中国石油和化学工业联合会的科学技术成果鉴定(中石化联鉴字[2014]第30号文),鉴定结论为:(1)开发了非均布高效可控变换反应器,采用径向内置管式水移热,催化剂可以自卸,合理、先进,符合催化剂的使用特性,易实现大型化;(2)改变了传统变换工艺的设计思路,大幅度缩短流程,减少了设备台数,提高了变换系统反应热的热能利用率和品位,降低系统阻力,简化了工艺操作;(3)该成果实现了传统变换工艺的技术提升,减少了工程投资和装置的运行成本,特别适用于高一氧化碳、高汽/气比水煤气的苛刻工况,可应用于不同领域变换工段的节能改造及新建项目,促进节能减排、利于装置大型化,具有较好的经济和社会效益;(4)该技术路线合理可行,技术指标先进,达到了国际先进水平。
CO等温变换技术挺进煤制气领域

CO等温变换技术挺进煤制气领域
佚名
【期刊名称】《石油化工应用》
【年(卷),期】2013(32)8
【摘要】由湖南安淳高新技术有限公司自主开发的CO等温变换技术近日在山西阳煤丰喜肥业临猗分公司甲醇改合成氨装置中一次开车成功,目前装置已稳定运行十多天,经检测效果达到设计要求。
该技术在煤制合成气高浓度CO变换领域成功实现工业化应用。
据了解,传统CO变换技术为多段绝热反应技术,很难应用于高浓度CO气体变换。
如果CO浓度在65%以上,变换反应将十分剧烈,反应温度也难以控制。
另外,传统技术通常需采用4。
5台变换炉,中间配装繁杂的控温换热设备,不仅反应流程长,系统阻力还高达0.4~0.6MPa,操作难度也较大。
【总页数】2页(P127-128)
【关键词】变换技术;CO变换;煤制气;等温;合成氨装置;工业化应用;CO浓度;开车成功
【正文语种】中文
【中图分类】TQ113.264
【相关文献】
1.清能院煤制气甲烷化催化剂和等温反应器技术获得突破 [J], ;
2.煤制合成氨不同等温变换技术探讨 [J], 曹志斌
3.煤制氢绝热变换和等温变换技术方案研究 [J], 赵代胜
4.煤制合成氨不同等温变换技术探讨 [J], 王智军
5.浅议煤制甲醇装置等温变换技术及优化 [J], 刘景隆
因版权原因,仅展示原文概要,查看原文内容请购买。
等温变换-王庆新
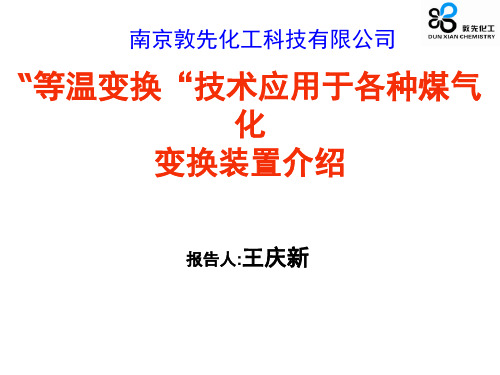
二、资质及专利证书
三、南京敦先“等温变换” 服务模式及设计理念
1、“一站式”服务模式: 提供软件包、专有技术设备、催化剂用量、催 化剂装填量、现场指导开车直至转入正常生产。这种服务模式利于系统 优化设计、投资抵、能耗低; 2、具体情况具体对待,工艺流程不可能千篇一律:加压气化水煤气采用 “两级等温变换”、“一级等温变换”或“等温变换+非变换”;固定 床半水煤气采用“预变+等温变换”;固定床半水煤气改造技术,找出 最佳点增加一台等“温变换炉”,达到节能目的; 3、安全长周期运行:大型装置可以做到~10年一个运行周期,外围催化 剂床层同样积灰厚度,全径向等温变换炉使用寿命为轴向床层的12.5倍 时间(18.75年);使用5年后一级等变炉催化剂床层积灰厚度仅是绝 热变换炉使用1.5年时积灰厚度的26.99%;中小型装置做到5~8年一个 运行周期。另外,反应器泄漏检测我们已经解决,确保“等变炉”有微 漏也不会影响系统正常使用。
7、低品位热能少、实 现变换“无”冷却水消耗、将低品位热能 转 化为高品位蒸汽:加压气化的等温变换:我们采用CO反应前移、 低品位热能前移、变换无冷却水消耗为“零”;固定床半水煤 气 变换则是把低品位热能转化为高品位蒸汽(饱和热水塔出口变 换气温度95/80、全低变装置大热交出口变换气温度120/82) 8、我们不仅仅是将低压甲醇塔搬到变换系统 :变换反应空速低、 催化剂易水合、水蒸气易出现露点、大型装置“二级等温变换炉” 承受负压差大、加压气化气质脏等问题,在软件包设计时均需要 考虑,这也是等温变换技术必须要 “一站式”服务模式的根本, “三分天下”服务模式很难把问题考虑全面(低投资抵、节能等)。 9、等温变换炉必须做到:内件与外筒分开设计、全径向、承受很 负压差大、易于装置大型化、易于反应器直径放大、催化剂便于 自卸(变换催化剂冷热态强度大于低压甲醇催化剂)、要有最佳操 作曲线、易操作等。不是所有低压甲醇塔结构形式均可作为“等
水移热等温变换技术_用于高水气比高一氧化碳煤化工装置简述_王庆新
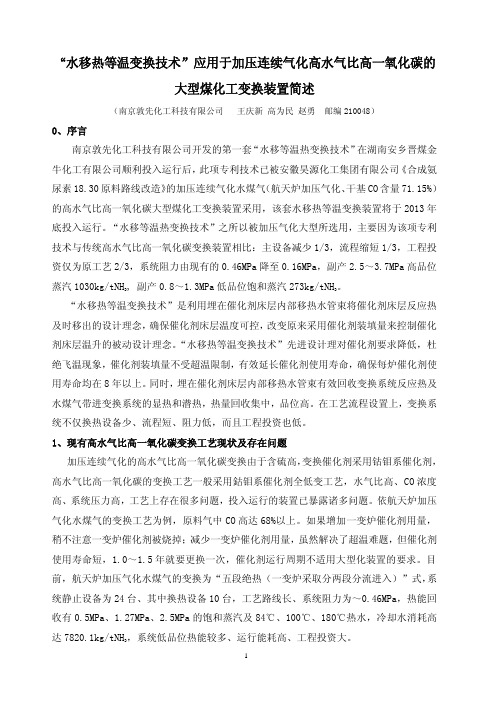
O I s o t h e r m a l S h i f t P r o c e s s C o m r i s i n W a t e r T r a n s f e r i n O u t H e a t D e v i c e C " p g g A l i e d i n C o a l C h e m i c a l U n i t w i t h H i h W a t e r V a o r R a t i o a n d H i h C O C o n t e n t p p g p g
单位:南京敦先化工科技有限公司 地址:南京市沿江工业开发区葛关路 625 号 邮编:210048 联系方式:王庆新(13852281028) 、高为民(13705175345) 、赵勇(15062293231)
3
第3 9 卷第 4 期 0 1 3 年 8 月 2
化工设计通讯 C h e m i c a l E n i n e e r i n D e s i n C o mm u n i c a t i o n s g g g
1
壳牌(Shell)气化的变换工艺在引进时,变换存在航天炉气化的变换同样问题。近几 年,部分煤化工企业将壳牌气化炉的出口气体温度降低,降低水气比,然后又添加蒸汽。 改造后的工艺解决了催化剂超温烧结难题,但系统工艺流程更长,人为增加工程投资、 增 加系统阻力、提高系统能耗。 水煤浆气化的变换工艺, 虽然 CO 摩尔分率偏低一些, 采用的变换技术仍为三段或四段 绝热反应的工艺流程, 水煤气或变换气每一阶段显热和潜热的回收均需要单独一台换间接 换热设备,工艺路线存在与航天炉、壳牌等水煤气变换工艺路线长、工程投资大、系统阻 力大、低品位热能多等缺陷。 2、水移热等温变换技术研发与进展 南京敦先化工科技有限公司自成立至今始终把降低变换能耗作为主攻方向之一,并将 径向气体分布专利技术、水移热低压甲醇合成专利技术、低阻力高效换热器专利技术、 阶 梯式回收余热理念与变换本征动力学、 宏观动力学、 热力学以及变换系统本身固有显热和 潜热的特性有机结合起来,成功开发出“有饱和热水塔低水气比水移热等温变换技术”、 “ 无饱和热水塔低水气比水移热等温变换技术”、 “ 高水气比高一氧化碳水移热等温变 换技术”。以上“水移热等温变换技术”不仅适用新上装置,同时也可用来改造已投入运 行高能耗变换装置。 南京敦先化工科技有限公司开发的 “水移等温热变换技术” 已被湖南安乡晋煤金牛化 工有限公司有饱和热水塔的低水气比变换装置及安徽昊源化工集团有限公司高水气比高 一氧化碳(航天炉加压气化、干基 CO 含量 71.15%)的大型煤化工变换装置所采用充分说 明“水移等温热变换技术”已经非常成熟。 3、南京敦先公司“水移等温热变换技术”与航天炉气化原有变换工艺运行指标对比 我们将为安徽昊源化工集团有限公司《合成氨尿素 18.30 原料路线改造》的加压连续 气化水煤气(航天炉加压气化、干基 CO 含量 71.15%)的高水气比高一氧化碳大型煤化工 变换装置设计的 “水移热等温变换” 装置与航天炉加压气化水煤气变换装置技术经济指标 分别列于下表: 主要技术经济指标名称 主 要 技 术 经 副产蒸汽量(2.5 MPa) 副产蒸汽量(1.27 MPa) 副产蒸汽量(0.5 MPa) 加热除氧水量(满足变换及氨合成需求)
“水移热等温变换技术”用于高水气比高一氧化碳煤化工装置简述

理 念 。“ 水 移 热 等 温变 换 技 术 ”对 催 化 剂要 求 降
低 ,杜绝 飞 温 现 象 ,催 化 剂 装 填 量 不 受 超 温 限
原料 路 线改 造” 的 加 压 连续 气 化 ( 航 天 炉 加 压 气
化 、干 基 C O含量 7 1 . 1 5 ) 的 高 水 气 比高 一 氧
第 3 9卷 第 4期
2 0 1 3年 8 月
化 工 设 计 通 讯
Che mi c a l En gi n e e r i n g De s i gn Co mm u ni c a t i o ns ‘1 9 。
“ 水移热等温变换技术’ ’ 用 于 高水 气 比高 一 氧化 碳 煤仅 为原 工艺 的 2 / 3 ,系 统 阻力 由现 有 的 0 . 4 6 MP a降 至 0 . 1 6 MP a ,吨 氨 副 产 2 . 5~
南 京 敦 先 化 工 科 技 有 限公 司 开 发 的第 一 套 “ 水 移热 等 温变 换 技 术 ” 在湖 南 安 乡晋 煤 金 牛 化
工有 限公 司顺利 投入 运行 后 ,此项 专 利技术 又 被 安徽 吴 源化 工集 团有 限公 司 “ 合成 氨 尿 素 1 8 ・ 3 O
移 出 ,确保 催化 剂床 层温度 可 控 ,改 变原 来通 过 催 化剂装 填 量来 控制催 化剂 床 层温 升的被 动设 计
制 ,有效 延 长催 化剂使 用 寿命 ,确保 每 炉催化 剂 使 用寿命 均 在 8年 以上 。同时 ,埋在 催化 剂床 层 内部 的移热 水管束 有 效 回收变换 系统 反应 热及 水 煤 气带 进 变 换 系 统 的显 热 和潜 热 ,热 量 回 收 集 中 ,品位高 。在 工艺 流程设 置 上 ,变 换 系统不 仅 换 热设备 少 、流程 短 、阻力 低 ,而且 工程 投资 也
一氧化碳等温变换技术助力节能减排
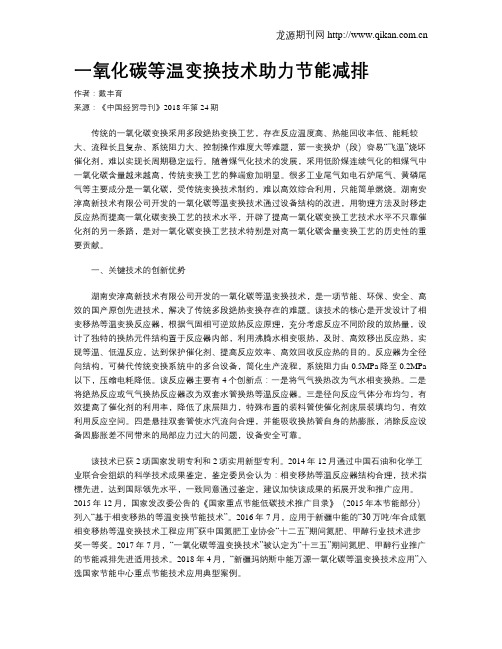
一氧化碳等温变换技术助力节能减排作者:戴丰育来源:《中国经贸导刊》2018年第24期传统的一氧化碳变换采用多段绝热变换工艺,存在反应温度高、热能回收率低、能耗较大、流程长且复杂、系统阻力大、控制操作难度大等难题,第一变换炉(段)容易“飞温”烧坏催化剂,难以实现长周期稳定运行。
随着煤气化技术的发展,采用低阶煤连续气化的粗煤气中一氧化碳含量越来越高,传统变换工艺的弊端愈加明显。
很多工业尾气如电石炉尾气、黄磷尾气等主要成分是一氧化碳,受传统变换技术制约,难以高效综合利用,只能简单燃烧。
湖南安淳高新技术有限公司开发的一氧化碳等温变换技术通过设备结构的改进,用物理方法及时移走反应热而提高一氧化碳变换工艺的技术水平,开辟了提高一氧化碳变换工艺技术水平不只靠催化剂的另一条路,是对一氧化碳变换工艺技术特别是对高一氧化碳含量变换工艺的历史性的重要贡献。
一、关键技术的创新优势湖南安淳高新技术有限公司开发的一氧化碳等温变换技术,是一项节能、环保、安全、高效的国产原创先进技术,解决了传统多段绝热变换存在的难题。
该技术的核心是开发设计了相变移热等温变换反应器,根据气固相可逆放热反应原理,充分考虑反应不同阶段的放热量,设计了独特的换热元件结构置于反应器内部,利用沸腾水相变吸热,及时、高效移出反应热,实现等温、低温反应,达到保护催化剂、提高反应效率、高效回收反应热的目的。
反应器为全径向结构,可替代传统变换系统中的多台设备,简化生产流程,系统阻力由0.5MPa降至0.2MPa 以下,压缩电耗降低。
该反应器主要有4个创新点:一是将气气换热改为气水相变换热。
二是将绝热反应或气气换热反应器改为双套水管换热等温反应器。
三是径向反应气体分布均匀,有效提高了催化剂的利用率,降低了床层阻力,特殊布置的装料管使催化剂床层装填均匀,有效利用反应空间。
四是悬挂双套管使水汽流向合理,并能吸收换热管自身的热膨胀,消除反应设备因膨胀差不同带来的局部应力过大的问题,设备安全可靠。
等温变换装置的运行情况

新增设备一览表
规格 / mm 2 400 × 18 945 × 42 1 600 × 6 231 × 26 1 200 × 7 382 × 40 ( 封头壁厚 42 ) 1 100 × 4 744 × 28 1 800 × 5 550 × 30
2
汽包的设计压力。 ( 2 ) 热交换器的换热面积偏小 热交换器利用原有设备, 换热面积仅 95. 8 m ,只能将经过热交换器之 后 的 水 煤 气 从 206 ℃ 提高到 221 ℃ ,导致进预变炉的水煤气偏离露 点温度仅 15 ℃ ,达不到设计要求的 20 ℃ ,不利 于预变炉的长期稳定运行。 6 结 语
2 2. 1
工艺流程及特点 主工艺气体流程 从气化工段来的 3. 75 MPa、210 ℃ 的饱和水
煤气 ( 含 CO 45% , 干基 ) , 经煤气水分离器、 热交 换 器 ( 240 ℃ ) 、 预 变 炉 反 应 后 ( 含 CO 36% ,温度 256 ℃ ) ,进入等温变换炉继续反应 ( 265 ℃ ) ,反应后气体 ( 含 CO 0. 9% ) 再进入热 交换器、废热锅炉、水解脱硫槽、汽包给水预热 器、高压脱盐水预热器、变换气一水分离器、低 压脱盐水预热器、变换气冷却器 ( 40 ℃ ) 、变换 气二水分离器,最后变换气去脱硫工段 ( 系统应 在预变炉前预留下次新增气体除尘装置位置) 。 2. 2 等温变换炉内流程 预变炉出口气体从等温变换炉底部两侧管口 进入内外筒环隙,经环隙均匀分布径向进入催化 剂床层,从圆周方向向圆中心方向不断地横向流 过催化剂床、扫过垂直沸腾水管,反应后的气体 进入床层中心的集气管, 在集气管中自上而下, 然后由集气管圆中心进入四周径向催化剂床层 ( 绝热段 ) , 反应后气体汇集于内件径向筐和内 径向筐环隙空腔中,向下经径向筐底部中心尾管 出设备。 等温变换炉内悬挂式双套管、汽室、水室与 炉外高置的汽包构成 1 个饱和水、饱和蒸汽的循 环闭路。从汽包下来的水进入水室,被均匀分配 进入各内管, 由上而下在管的底端折转到外管, 在外管由下而上流动,吸收管外催化剂床层反应 热,此过程中一部分饱和水被汽化,汽水混合物 上升到汽室, 由汽室中心汽水升气管上升到汽 包。由于高置的汽包有一定的位差, 再加上内、 外管的水、汽水混合物密度上的差别,故在悬挂 式双套管、 汽室、 水室、 汽包这个循环闭路内, 饱和水、饱和蒸汽能如此得以无动力循环。汽包
等温变换与绝热变换在高水气比粗煤气变换中的应用对比

等温变换与绝热变换在高水气比粗煤气变换中的应用对比李雅静【摘要】The pressurized pulverized coal gasification technology was used in quite a few new ammonia plants. It is of high water gas ratio,high CO content in the raw gas. Isothermal shift and adiabatic shift which match with the gasification were introduced in the paper,making comparison between the two processes respectively from the process flow,plot area,key equipment,utility consumption,catalyst dosage,economic investment,etc. The results showed that the isothermal shift had some advantages in the application of raw gas with high water gas ratio,but it had such drawbacks as few reference application plants and short operating period.%不少新建合成氨装置采用粉煤加压气化工艺,其粗煤气中水气比高、CO含量高,介绍了与其配套的等温变换和绝热变换2种变换工艺,分别从工艺流程、占地面积、关键设备、公用工程消耗、催化剂用量和经济投资等方面对二者进行了对比.结果表明,等温变换在高水气比粗煤气变换中应用具有一定的优势,但也存在应用业绩不多、运行年限较短的问题.【期刊名称】《煤化工》【年(卷),期】2017(045)005【总页数】5页(P13-17)【关键词】粗煤气;等温变换;绝热变换;粉煤加压气化;合成氨;高水气比【作者】李雅静【作者单位】中海油石化工程有限公司,山东济南 250101【正文语种】中文【中图分类】TQ546.4变换是将煤气中的CO转化为H2的过程,其配置方案与进界区煤气组成和出界区变换气中CO含量要求有关。
煤制氢绝热变换和等温变换技术方案研究

煤制氢绝热变换和等温变换技术方案研究赵代胜【摘要】介绍了绝热变换、等温变换各自的工艺流程和技术特点.以50万m3/h 煤制氢项目为例,分别从工艺流程、系列数、变换炉配置、关键设备情况、催化剂和公用工程消耗以及经济指标等方面,对两种变换技术方案进行了比较和分析.结果表明,等温变换技术在煤制氢项目中具有一定的优势,但也存在低品位蒸汽利用问题及大规模工业化应用业绩偏少等实际情况,企业可根据自身情况,综合考虑,确定最佳煤制氢变换技术方案.【期刊名称】《煤化工》【年(卷),期】2016(044)002【总页数】5页(P6-9,14)【关键词】煤制氢;绝热变换;等温变换;系列数;变换炉;催化剂;公用工程消耗【作者】赵代胜【作者单位】中国神华煤制油化工有限公司北京工程分公司,北京 100011【正文语种】中文【中图分类】TQ54在当前全球发展低碳经济、应对气候变化的背景下,立足我国的能源现状,大力发展煤炭清洁产业具有重大现实意义,煤制氢等煤炭清洁转化技术受到了行业内的广泛关注[1-4]。
煤制氢是将煤气化产生的以C O、H2为主要成分的粗煤气,经过变换、酸性气体脱除、氢提纯等处理而获得一定纯度的产品氢。
其中变换技术是煤制氢过程中的关键技术之一[5-6],主要通过变换反应,即一氧化碳与水蒸气在催化剂的作用下,于一定温度、压力下,产生二氧化碳和氢气,进而将粗煤气中一氧化碳转化成氢气的过程。
在传统的工业生产中,变换炉均采用绝热反应器,由于变换反应是强放热反应,且是一个热力学控制的过程,因此绝热变换采用多段反应、多段换热的方式,这样会造成绝热变换工艺流程较复杂。
为了优化变换流程及换热方式,近期国内又提出了等温变换理念[7-8]。
本文中,以4.0 M P a(G)水煤浆气化产生合成气,经过变换、酸性气体脱除、氢提纯等工艺路线,制取50万m3/h氢气的煤制氢路线为例,就绝热变换、等温变换两种变换技术方案进行比较和分析,以期给相关研究提供参考。
15某企业煤炭气化变换装置反应原理及工艺流程描述

某企业煤炭气化变换装置反应原理及工艺流程描述气化洗涤塔出来的煤气中,CO和硫含量都较高(其中:CO干气含量为45.08%mol、H2S含量为1.765g/Nm³、COS含量为0.35g/Nm³),为将其中的CO部分或全部转化为CO2和H2,变换采用三段耐硫变换技术,即一段宽温耐硫变换串两段低温耐硫变换工艺,在一定的温度下,煤气中的一氧化碳与水蒸气借助催化剂发生变换反应生成氢气和二氧化碳,与此同时约90%的COS亦转化为H2S,其化学反应如下:CO+H2O=CO2+H2+QCOS+H2=CO+H2S +QCOS+H2O=CO2+H2S+Q该工艺具有如下特点:(1)钴-钼耐硫催化剂适用于原料气中硫含量较高的变换气,对原料气中硫只有最低要求,无上限要求。
(2)由于变换原料气中CO含量较高,变换反应温升较大,须采用分段变换工艺移走热量。
(3)CO变换反应余热采用分等级回收方式,高温工艺余热采用过热中压蒸汽和副产中压蒸汽的方式回收;低温工艺余热用于副产低压蒸汽、预热锅炉给水和脱盐水等。
(4)工艺冷凝液根据压力等级,分别进行处理后回收利用。
高温变换冷凝液气体闪蒸后,作为粗煤气的洗涤水回用;低温变换冷凝液,即变换气和水煤气的洗涤水经过汽提后送气化灰水处理的脱气槽处理回用;汽提塔顶气经冷却分离后的冷凝液,连同甲醇精馏排出的部分含醇水及低温甲醇洗废水一起送入煤气化备煤系统用作制浆,分离后的气体送硫回收焚烧炉焚烧,焚烧气再送煤锅炉氨法脱硫,制得副产品硫胺。
由气化装置来的煤气,温度为242℃,压力为6.3MPaA,先经过入口分离器(01S0301)分离掉机械杂质及冷凝液,出分离器的气体分成两股,其中部分粗煤气(工况一下为81.6%,工况二下为71.5%)进入原料气预热器(01E0304)预热到285℃,然后进入蒸汽加热器(01E0303)升温后进入第一变换炉(01R0301),开车时蒸汽加热器用于为变换触媒升温还原提供热量,正常生产时蒸汽加热器用于满足触媒末期的温度要求。
- 1、下载文档前请自行甄别文档内容的完整性,平台不提供额外的编辑、内容补充、找答案等附加服务。
- 2、"仅部分预览"的文档,不可在线预览部分如存在完整性等问题,可反馈申请退款(可完整预览的文档不适用该条件!)。
- 3、如文档侵犯您的权益,请联系客服反馈,我们会尽快为您处理(人工客服工作时间:9:00-18:30)。
等温变换技术应用于各类煤气化变换装置简介发表时间:2014-1-1 文字〖大中小〗阅读次数:580 [关闭窗口]0、前言南京敦先化工科技有限公司开发的“等温变换技术”是利用埋在催化剂床层内部移热水管束将催化剂床层反应热及系统多余的低品位热能转化为高品位蒸汽,同时降低催化剂床层温度,提高反应推动力,延长催化剂使用寿命,降低系统阻力,降低工程投资、减少设备腐蚀。
该技术已经被安徽昊源化工集团“18.30”合成氨项目(航天炉加压气化水煤气、3.78MPa)、内蒙古某能源单位40亿立方米/年煤制天然气项目(单套通过干基水煤气量6.67×105Nm3/h)、山东某石油化工有限公司160万吨/年深度裂解装置合成气变换装置、山东联盟化工股份有限公司15万吨/年合成氨项目(固定床间歇气化半水煤气、2.2MPa)、河南新乡永昌化工股份有限公司17万吨/年合成氨项目(固定床间歇气化半水煤气、0.8MPa)、湖北华强化工集团10万吨/年合成氨项目(固定床间歇气化半水煤气、0.8MPa)、河北天成化工股份有限公司卢龙分公司6万吨/年合成氨项目(固定床间歇气化半水煤气、0.8MPa)、安乡晋煤金牛化工有限公司5万吨/年合成氨项目(固定床间歇气化半水煤气、0.8MPa)等单位不同煤气化的变换装置所采用。
与粉煤加压气化、水煤浆加压气化以及天然气转化等高水气比、高CO水煤气相配套的变换装置不仅要完成CO转化任务,同时兼顾完成前工序带进变换系统热量回收任务。
变换装置热量回收率及回收热能品位高低直接关系到整个装置综合能耗。
目前,与之相配套的传统变换工艺多为“多段绝热反应+间接热能回收”方式,工艺流程长、设备多、工程投资大、系统阻力大、露点腐蚀多、设备维修费用高、回收热能品位低、热量回收率低。
与固定床间歇式气化以及尾气回收等低水气比、低CO半水煤气或水煤气相配套的变换工艺流程类型繁多,从热能回收来分可以分为“有饱和热水塔”和“无饱和热水塔”两种类型;从催化剂选型上来分可以分为“中串低”、“中低低”、“全低变”三大类型。
此类变换装置均需要向系统添加蒸汽,流程设置上也是“多段绝热反应+间接热能回收”方式,就现有运行的变换装置而言,普遍存在蒸汽消耗高、系统阻力大、设备腐蚀严重、低品位热能多等缺陷。
现有变换装置工艺流程及热能回收是按照催化剂使用温区、CO转化率、各段平衡温距作为主要设计依据的绝热催化剂床层设计理念。
随着CO摩尔分率高、CO转化率提高、催化剂使用温区窄,在确保每段具有较大反应推动力时,势必造成催化剂床层多、间接移热设备多、工艺流程长、系统阻力大、热能回收率低、低品位热能多等缺陷。
随着煤价不断攀升,变换装置已经成为各类煤化工企业降低综合能耗、降低产品成本的重要工序。
目前,变换装置存在能耗偏高、低品位热能多、工程投资大等诸多缺陷主要因为催化剂厂家仅提供催化剂用量、分段数量及进出催化剂床层简单物料热量衡算;设计院或使用单位根据催化剂厂的条件完成软件包及工程设计,设计院或使用单位在完成软件包设计时不能违背催化剂使用条件,只有采用不同温度的介质将变换系统热量移走以满足每一床层进口温度需求和变换系统热能回收,势必造成流程设置越来越长、工程投资加大、运行费用增加;反应器设计单位按照设计院或使用单位的条件设计变换炉,反应器设计单位不仅要满足催化剂厂要求,还要符合设计院或使用单位的条件。
这种“三分天下”的组合技术是很难提供出一个投资低、运行费用低、露点腐蚀少的变换装置。
南京敦先公司利用自己建立的等温变换反应器数据模型,独立完成反应器动力学、热力学以及系统工艺流程模拟计算。
独立完成催化剂用量、系统各节点温度设置、系统物料热量平衡、系统工艺流程设计、设备工艺计算以及系统软件包开发等工作。
南京敦先可以对软件包、催化剂选型和用量、催化剂硫化升温、系统转入轻负荷以及转入正常生产进行全面设计、售后服务和技术指导,确保装置一次开车成功。
南京敦先公司这种“一站式服务”的等温变换技术及服务模式完全能够杜绝“三分天下”组合技术存在的问题及缺陷。
南京敦先化工科技有限公司针对现有变换装置存在问题以及不同气化路线所产的水煤气或半水煤气分别开发出适合煤制合成氨、煤制天然气、煤制氢、煤制油、煤制乙二醇、煤制甲醇、煤制烯烃等“等温变换技术”。
本文就本公司各种“等温变换技术”阐述如下:1、适用于粉煤加压气化(以航天炉为例)所产水煤气的“等温变换技术”粉煤加压连续气化所产水煤气具有水气比高、CO摩尔分率高、系统压力高等优点,依航天炉水煤气为例,水煤气中CO 高达68%以上,目前在运行的变换装置为“五段绝热+冷激+间接换热”式,系统静止设备为24台、其中换热设备10台,工艺路线长、系统运行阻力在0.46~0.75MPa,热能回收有0.5MPa、1.27MPa、2.5MPa的饱和蒸汽及180℃、100℃、84℃热水,冷却水消耗高达7820.1kg/tNH3,系统低品位热能较多、运行能耗高、工程投资大。
一变炉催化剂易超温,催化剂使用寿命短,1.0~1.5年就要更换一次催化剂。
南京敦先化工科技有限公司针对高水气比、高CO的粉煤加压连续气化所产水煤气变换装置采我公司开发“等温变换”专利技术设计理念,等温变换系统静止设备仅为13台、其中换热设备为6台,工艺路线缩短1/2,工程投资仅为原工艺2/3,系统阻力由现有的0.46~0.75MPa降至0.13~0.18MPa,副产2.5~3.7MPa高品位蒸汽1030kg/tNH3, 副产0.8~1.3MPa低品位饱和蒸汽273kg/tNH3,变换冷却水为“零”消耗。
该“等温变换技术”与传统变换工艺相比具有以下优点:(1)杜绝一变炉发生催化剂飞温事故:“等温变换技术”是利用埋在催化剂床层内部移热水管束将催化剂床层反应热及时移出的设计理念,确保催化剂床层温度可控,在任何工况下,第一变换炉催化剂床层温度均可以控制在180~350℃范围,彻底杜绝飞温等安全事故发生;(2)催化剂装填量不受温度限制、运行周期长:“等温变换技术” 是利用埋在催化剂床层内部移热水管束将催化剂床层反应热及时移出,催化剂装填量不受超温限制,有效延长催化剂使用寿命,确保每炉催化剂使用寿命均在8年以上;(3)热能回收率高、运行费用低:“等温变换技术”热能回收达96.5%以上,副产蒸汽品位高,脱盐水加热到104℃直接去热力除氧,无需外加蒸汽,变换系统冷却水“零”消耗。
与传统变换变换工艺相比,吨氨节省运行费用92.9441元/NH3,对于一套30万吨合成氨装置而言,全年可以节省2788.323万元;(4)开车时间短、开车平稳、有效降低生产费用:“等温变换炉”配置开工蒸汽喷抢,每次开车前通过蒸汽喷射抢将蒸汽添加在等温变换炉内部水管中,并利用本身的热水循环系统将催化剂床层温度提高到200℃以上。
负荷较轻时,通过蒸汽喷射枪过来的蒸汽维持催化剂床层热平衡;负荷较大时,循环水吸收催化剂床层热量转化为蒸汽向外界输送,完全可以实现变换装置开车时间为“零”,每次开车至少可以缩短10小时以上。
有效杜绝绝热催化剂床层用电炉把催化剂床层温度升起来,但随着进入气量大后,催化剂床层又降下来,又要加大电炉功率再提升催化剂床层炉温等不断来回折腾现象;(5)等温变换炉操作温度易于控制、杜绝催化剂反硫化现象:此类水煤气的变换装置必须选用宽温区耐硫钴钼系催化剂,该类型催化剂在高水气比、高温、低硫等状态下均会出现反硫化现象,造成催化剂中硫丢失,催化剂活性下降。
如果采用绝热催化剂床层变换技术,一变催化剂床层温度大部分在450℃以上,此类工况催化剂在开车时(2.0MPa左右)会出现反硫化,影响催化剂活性,缩短催化剂使用寿命。
而“等温变换技术”是利用埋在催化剂床层内部移热水管束将催化剂床层反应热及时移出的设计理念,确保催化剂床层温度可控,催化剂床层温度完全可以控制在180~350℃范围内,完全杜绝催化剂反硫化;(6)等温变换炉操作温度低、有效减少甲烷化反应:目前运行的传统变换工艺,气化岛过来的水煤气温度一般在~208℃,水气比在0.9716左右。
一变转化率较高,一变催化剂床层大部分在450℃以上,一变炉中下部水气比降低,很容易发生甲烷化反应,而“等温变换技术”一变炉催化剂床层温度在180~350℃范围内,完全杜绝甲烷化副反应现象;(7)工艺路线短、露点腐蚀少、维修费用低:传统变换工艺,绝热变换炉4台、换热器10台、主设备不少于24台,工艺路线长,出现露点多,设备腐蚀点多。
而“等温变换技术”变换炉仅2台、换热设备6台,主设备13台,回收变换系统潜热和显热大部分在等温变换炉内完成,有效减少露点腐蚀,降低运行维修费用;(8)操作简单方便:“等温变换技术”变换炉床层温度时通过副产蒸汽压力控制的,操作简单平稳,易于控制。
(9)南京敦先的“等温变换技术”在运行过程中总水汽比、变换气体余热回收均为一个定值,有效解决了“五段绝热+间接换热”变换工艺随着一至三变催化剂衰退,水汽比上升及回收变换气余热低品位热能增加、冷却水耗增大、设备腐蚀加剧等缺陷;(10)等温变换炉操作温度低、催化剂用量少、生产成本低:变换催化转化主要受热力学和动力学控制,如果将催化剂床层反应热及时移出,变换反应主要受热力学控制,则催化剂用量就减少。
现有绝热变换技术是随着气体流经催化剂床层深度增加,气体温度越来越高,平衡温距变小,绝热催化剂床层的变换反应主要受动力学控制,不得不采用加大催化剂用量及降低空速手段来完催化任务。
催化剂用量大,床层阻力进一步增加,带来运行能耗高。
而“等温变换技术”二变炉催化剂床层温度完全可以控制在180~300℃范围内,催化反应主要受热力学控制,催化剂装填量少,势必带来系统阻力低、工程总投资降低、生产费用低等优点。
我们将南京敦先化工有限公司开发的“等温变换技术”与传统变换装置经济指标分别列于表(1):2、适用于水煤浆加压气化(以6.5MPa为例)所产水煤气的“等温变换技术”近二十年来,我国水煤浆气化技术发展速度较快,设计压力由4.0及6.5MPa两个压力等级已经发展到1.6~8.7MPa诸多个压力等级。
无论什么压力下的水煤浆气化炉,在完成水煤浆气化时,气化炉内部也进行部分CO变换,与粉煤加压连续气化相比,水煤浆气化所产水煤气H2含量高、CO含量略低,但总的有效气体成分变化不大。
因此,与之配套变换装置回收气化岛带过来的显热和潜热任务更艰巨。
传统变换装置低品位热能非常多(以产合成氨为例),副产蒸汽压力等级大致为2.5(或4.0)MPa、1.27MPa、0.5MPa等中低压蒸汽,预热脱盐水仅为99.19℃,低品位热能量非常多,如副产0.5MPa低品位蒸汽1180.56kg/tNH3,预热99.19℃脱盐水6009.71kg/tNH3,给整个工序水汽平衡带来很大难度,部分单企业放弃对80℃以下变换气热能的回收,采用循环冷却水直接降温,造成从气化岛带出的热能回收率低,冷却水消耗大、系统综合能耗高。