磁控溅射玻璃镀膜电源
磁控溅射电源原理

磁控溅射电源原理磁控溅射电源这玩意儿可神奇啦!咱们先来说说啥是磁控溅射。
简单来讲,就像是一场微观世界的“子弹射击战”。
材料原子或者分子被当成“子弹”,从一个地方“射”到另一个地方,然后在目标表面形成一层薄薄的膜。
而磁控溅射电源呢,就是这场“射击战”背后的“能量提供者”。
想象一下,这个电源就像是一个超级大力士,不断地给“射手们”加油打气,提供足够的力量让它们能够快速、准确地发射。
它输出的电能就像是一股强大的洪流,推动着整个溅射过程顺利进行。
那它到底是怎么做到的呢?其实啊,磁控溅射电源内部有一套复杂但又超级厉害的机制。
它能把输入的普通电能,通过一系列的魔法变换,变成适合磁控溅射工艺的特殊电能。
比如说,它得控制电压和电流的大小和变化。
这就好像是控制水龙头的水流大小一样,得恰到好处。
电压太高或者电流太大,可能会把整个过程搞砸;电压太低或者电流太小,又没办法让“子弹”有力地射出去。
所以,电源得时刻保持警惕,精准地调整这两个参数。
而且哦,这个电源还得特别稳定。
不能今天心情好输出的能量多,明天心情不好输出的能量少。
它得像一个靠谱的老朋友,始终保持稳定的输出,让磁控溅射过程能够一直顺利进行,不会出现一会儿好一会儿坏的情况。
另外呢,磁控溅射电源还得应对各种各样的外界干扰。
就像我们在生活中会遇到各种烦心事一样,它也会遇到电压波动、电磁干扰等等麻烦。
但是,它可不能被这些小困难打倒!它得有坚强的“内心”,通过各种巧妙的设计和技术,把这些干扰统统排除掉,保证自己能够稳定可靠地工作。
你看,磁控溅射电源虽然看起来只是一个小小的设备,但它在磁控溅射这个大舞台上可是起着至关重要的作用呢!没有它,就没有那一层又一层完美的薄膜,没有那些高科技产品的诞生。
所以说啊,可别小看了这个家伙,它虽然不大,但是能量满满,为我们的科技进步默默地贡献着自己的力量!怎么样,是不是觉得它很厉害呢?。
磁控溅射镀膜机的使用流程
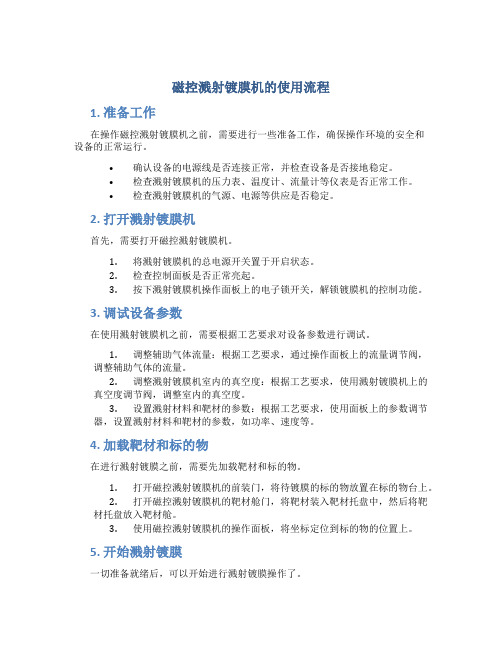
磁控溅射镀膜机的使用流程1. 准备工作在操作磁控溅射镀膜机之前,需要进行一些准备工作,确保操作环境的安全和设备的正常运行。
•确认设备的电源线是否连接正常,并检查设备是否接地稳定。
•检查溅射镀膜机的压力表、温度计、流量计等仪表是否正常工作。
•检查溅射镀膜机的气源、电源等供应是否稳定。
2. 打开溅射镀膜机首先,需要打开磁控溅射镀膜机。
1.将溅射镀膜机的总电源开关置于开启状态。
2.检查控制面板是否正常亮起。
3.按下溅射镀膜机操作面板上的电子锁开关,解锁镀膜机的控制功能。
3. 调试设备参数在使用溅射镀膜机之前,需要根据工艺要求对设备参数进行调试。
1.调整辅助气体流量:根据工艺要求,通过操作面板上的流量调节阀,调整辅助气体的流量。
2.调整溅射镀膜机室内的真空度:根据工艺要求,使用溅射镀膜机上的真空度调节阀,调整室内的真空度。
3.设置溅射材料和靶材的参数:根据工艺要求,使用面板上的参数调节器,设置溅射材料和靶材的参数,如功率、速度等。
4. 加载靶材和标的物在进行溅射镀膜之前,需要先加载靶材和标的物。
1.打开磁控溅射镀膜机的前装门,将待镀膜的标的物放置在标的物台上。
2.打开磁控溅射镀膜机的靶材舱门,将靶材装入靶材托盘中,然后将靶材托盘放入靶材舱。
3.使用磁控溅射镀膜机的操作面板,将坐标定位到标的物的位置上。
5. 开始溅射镀膜一切准备就绪后,可以开始进行溅射镀膜操作了。
1.检查一遍设备的参数和操作流程是否设定正确。
2.按下溅射镀膜机操作面板上的“启动”按钮,启动溅射镀膜过程。
3.监控溅射镀膜过程中的参数变化,并根据需要进行相应的调整。
4.在镀膜时间达到要求后,按下操作面板上的“停止”按钮,停止溅射镀膜过程。
6. 完成操作完成溅射镀膜后,需要进行一些收尾工作。
1.关闭磁控溅射镀膜机的电源开关。
2.清理溅射镀膜机内的靶材残留物和镀膜沉积物。
3.维护设备,保持设备的清洁和正常运行。
4.将操作面板上的电子锁开关设置为锁定状态,以防止设备误操作。
磁控溅射法沉积TCO薄膜的电源技术

磁控溅射法沉积TCO薄膜的电源技术1前言透明导电氧化物薄膜(TCO薄膜)有着广泛的用途,如作为LCD、OLED显示器面板的电极,作为触摸屏的感应电极,作为薄膜太阳能电池的电极以及作为LED芯片前电极等[1]。
目前,主要的TCO薄膜有氧化铟锡(ITO)、氧化锡(SnO2)、氧化锌铝(AZO)三种[2],其中SnO2薄膜是最早应用的TCO薄膜,但由于其光电特性相对较差,目前主要应用在一些较低端的使用领域。
ITO薄膜是目前光电特性最好,使用范围最广的TCO薄膜,但其同时存在使用稀有元素In,生产成本较高、In元素有毒、在氢等离子工艺氛围中性能退化等缺点。
近年来,成本低、性能优良、无毒害的ZnO:Al(AZO)薄膜[3]得到了广泛的关注与研究,有希望替代ITO薄膜。
因此,ITO与AZO材料是当前研究和生产的最主要的TCO材料。
目前,产业界制备ITO、AZO薄膜主要是采用磁控溅射镀膜技术[4][5]。
磁控溅射技术基于等离子技术,通常是在存在高电势差的靶(阴极)与阳极之间注入气体(一般为Ar气),通过等离子辉光放电实现对气体原子的离化,电场与磁场对离子加速和变向,进而轰击靶材表面,导致靶材原子被轰击到空间中,溅射在一块衬底材料上聚集形成薄膜[6]。
对于磁控溅射装置,磁控溅射电源决定了磁控溅射工艺过程等离子体状态,对镀膜工艺和膜层生长质量起着至关重要的作用[7]。
随着生产和科技不断发展,用户对产品质量性能的要求越来越高。
所以要求磁控溅射镀膜设备具有良好的可靠性、稳定性,有较高的镀膜效率和镀膜质量。
本文将主要描述磁控溅射ITO、AZO两大主要TCO薄膜的核心电源技术的发展现状、最新进展以及未来面临的挑战。
2磁控溅射TCO薄膜的电源技术发展概述2.1磁控溅射直流电源磁控溅射电源类型有直流电源、中频电源和射频电源。
其中中频电源与射频电源成本较高,且沉积速率偏慢,尤其是射频电源沉积速率慢且由于驻波效应等,不适宜进行大面积镀膜,因此在制备大面积TCO薄膜技术领域应用较少。
磁控溅射镀膜技术综合介绍
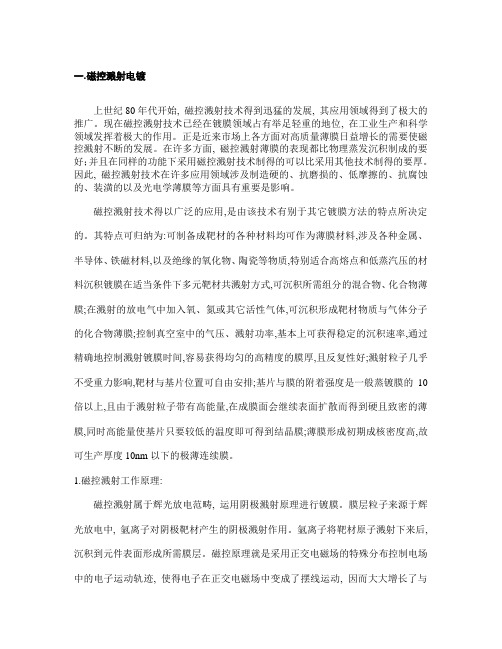
一.磁控溅射电镀上世纪80年代开始, 磁控溅射技术得到迅猛的发展, 其应用领域得到了极大的推广。
现在磁控溅射技术已经在镀膜领域占有举足轻重的地位, 在工业生产和科学领域发挥着极大的作用。
正是近来市场上各方面对高质量薄膜日益增长的需要使磁控溅射不断的发展。
在许多方面, 磁控溅射薄膜的表现都比物理蒸发沉积制成的要好;并且在同样的功能下采用磁控溅射技术制得的可以比采用其他技术制得的要厚。
因此, 磁控溅射技术在许多应用领域涉及制造硬的、抗磨损的、低摩擦的、抗腐蚀的、装潢的以及光电学薄膜等方面具有重要是影响。
磁控溅射技术得以广泛的应用,是由该技术有别于其它镀膜方法的特点所决定的。
其特点可归纳为:可制备成靶材的各种材料均可作为薄膜材料,涉及各种金属、半导体、铁磁材料,以及绝缘的氧化物、陶瓷等物质,特别适合高熔点和低蒸汽压的材料沉积镀膜在适当条件下多元靶材共溅射方式,可沉积所需组分的混合物、化合物薄膜;在溅射的放电气中加入氧、氮或其它活性气体,可沉积形成靶材物质与气体分子的化合物薄膜;控制真空室中的气压、溅射功率,基本上可获得稳定的沉积速率,通过精确地控制溅射镀膜时间,容易获得均匀的高精度的膜厚,且反复性好;溅射粒子几乎不受重力影响,靶材与基片位置可自由安排;基片与膜的附着强度是一般蒸镀膜的10倍以上,且由于溅射粒子带有高能量,在成膜面会继续表面扩散而得到硬且致密的薄膜,同时高能量使基片只要较低的温度即可得到结晶膜;薄膜形成初期成核密度高,故可生产厚度10nm以下的极薄连续膜。
1.磁控溅射工作原理:磁控溅射属于辉光放电范畴, 运用阴极溅射原理进行镀膜。
膜层粒子来源于辉光放电中, 氩离子对阴极靶材产生的阴极溅射作用。
氩离子将靶材原子溅射下来后,沉积到元件表面形成所需膜层。
磁控原理就是采用正交电磁场的特殊分布控制电场中的电子运动轨迹, 使得电子在正交电磁场中变成了摆线运动, 因而大大增长了与气体分子碰撞的几率。
用高能粒子(大多数是由电场加速的气体正离子)撞击固体表面(靶), 使固体原子(分子)从表面射出的现象称为溅射。
磁控溅射镀膜机技术规格

磁控溅射镀膜机技术规格1. 货物名称、数量磁控溅射镀膜机1套2. 工作条件及用途2.1 工作条件2.1.1 能在电源电压380?10%V、50?2%Hz、室温0?~40?的环境下连续正常工作。
2.1.2 连续工作时间能力不应少于168小时,设备服役期限15年。
2.2 用途主要用于镀制多层金属及金属化合物薄膜。
3. 技术规格卖方所提供的磁控溅射镀膜机必须是技术先进,经济合理,成熟可靠的产品。
本条中带*技术指标为关键指标,不允许有超标。
3.1基本要求磁控溅射镀膜机由无油真空系统、溅射系统、气体压强控制装置、气体流量控制装置以及烘烤旋转系统等组成。
可满足样品尺寸为,50mm,多片(4片以上)同时镀制要求,可满足三靶共溅射要求;溅射室采用1Cr18Ni9Ti不锈钢制造;气体管路采用不锈钢硬管;所有设备要求为集装式。
溅射室的观察窗不少于2个;备用接口不少于2个,溅射室内部应有照明装置。
3.1.1样品尺寸:?,50mm,*3.1.2膜厚不均匀性:?,5%;*3.1.3膜厚重复性?,3%;3.2真空系统3.2.1真空室直径?φ500mm。
-53.2.2极限真空度:? 6.0,10Pa-3*3.2.3恢复抽真空时间:从大气~4×10Pa小于15分钟-5*3.2.4真空测量装置范围:大气~1×10Pa3.2.5系统漏率:停泵关机12小时后真空度?5Pa。
3.2.6真空测量:宽量程真空计(用于真空监测)和精度优于1.5%的薄膜规(用- 1 -于工艺真空控制,建议采用美国MKS产品);3.3溅射系统3.3.1溅射材料: Ti,Pt,Au,钛酸锶钡等;还可溅射其它金属、氧化物等; *3.3.2溅射靶:溅射靶的数量不少于4个,可满足三靶共溅射要求;要求共溅射和单靶溅射模式转换调节方便;预留一个靶的空位和接口,作为离子源安装备用接口;3个直流靶为高真空型、1个射频靶,其中一个直流靶为磁场增强靶;靶位置:向上溅射;溅射靶与基片距离可调节,每只溅射靶分别配有挡板;4个永磁靶均为摆头靶,可分别实现多层镀膜和掺杂镀膜。
玻璃磁控溅射镀膜

玻璃磁控溅射镀膜是一种在玻璃表面形成一层或多层金属、金属化合物或其它化合物薄膜的工艺技术。
以下是该工艺的简要介绍:
1. 溅射原理:在磁控溅射镀膜过程中,电子在电场的作用下加速飞向基片,与氩原子发生碰撞,电离出大量的氩离子和电子。
氩离子在电场的作用下加速轰击靶材,溅射出大量的靶材原子,呈中性的靶材原子(或分子)沉积在基片上成膜。
2. 磁控技术:二次电子在加速飞向基片的过程中受到磁场洛仑磁力的影响,被束缚在靠近靶面的等离子体区域内。
该区域内等离子体密度很高,二次电子在磁场的作用下围绕靶面作圆周运动,该电子的运动路径很长,在运动过程中不断地与氩原子发生碰撞电离出大量的氩离子轰击靶材。
经过多次碰撞后电子的能量逐渐降低,摆脱磁力线的束缚,远离靶材,最终沉积在基片上。
3. 镀膜种类:根据不同的应用需求,可以溅射不同的材料,形成各种不同的镀膜。
例如,热反射镀膜可以使玻璃具有遮蔽太阳光的功能;低辐射镀膜可以使玻璃具有保温作用,具有节能效果。
4. 工业应用:玻璃磁控溅射镀膜工艺在建筑、汽车、家居、电子等多个行业都有广泛的应用。
如LOW-E玻璃就是一种典型的磁控溅射镀膜玻璃,它具有保温、隔热、节能等效果。
总的来说,玻璃磁控溅射镀膜工艺通过精确控制薄膜的成分和厚度,赋予了玻璃一系列特殊的性能,极大地拓展了玻璃的应用范围。
如需更多信息,建议查阅磁控溅射镀膜相关论文获取。
磁控溅射玻璃镀膜电源

磁控溅射玻璃镀膜电源Dr. Dirk OchsHÜTTINGER Elektronik GmbH + Co KG, Freiburg, Germany黄新盈深圳市微普真空系统集成有限公司介绍:近年来,建筑玻璃市场对Low‐e镀膜玻璃产生了巨大的需求。
特别是经济快速增长的中国,印度和东欧地区。
目前高档Low‐e主要采用磁控溅射方式镀膜,关于镀膜设备,Low‐E 制造商们关注的是溅射速率,薄膜质量和生产成本。
在Low‐E生产中,连续镀膜系统常用的是30‐200KW的直流和中频磁控溅射电源[1,2,3,4]。
对于建筑玻璃镀膜所使用的电源,则要求高精度的过程控制能力,配备强大的打弧管理系统,并提供可调整的参数。
能使生产过程中的干扰最大程度的减少,获得最优化的膜层。
为了保证溅射速率和产量,生产过程中对电源的打弧管理提出了很高的要求。
比如反应溅射低熔点材料,打弧非常容易在靶面上造成孔洞。
快速先进的打弧管理,能预防靶面产生的缺陷并且获得更高的功率,意味着安全可靠的获得更高的溅射速率。
应用:建筑玻璃的主要应用是阳光控制膜,低辐射膜和减反膜。
图1是典型的阳光控制膜系。
玻璃基板首先沉积了一层厚度在10‐100nm的SnO2。
膜厚从10nm从增加到100nm时,颜色则从银色渐变为青铜色,最后是蓝色。
在SnO2上还需要沉积CrNx和SnO2膜。
一个典型的低辐射膜系图2,开始也是先在玻璃基板上沉积SnO2,起到减反的作用。
然后是反射红外线的银层,再沉积阻挡层NiCrOx,和减反层SnO2。
减反的膜系(图3)由一个高折射系数材料和一个低折射系数的材料交替组合而成。
常用的高折射系数的材料有ZrO2,Ta2O5和TiO2。
低折射系数材料如MgF2,SiO2,或Al2O3。
金属膜通常是用直流电源驱动单个磁控靶溅射。
而氧化物和氮化物膜层则使用中频电源,配合孪生磁控靶进行反应溅射。
磁控溅射原理如图4所示首先是工艺气体通入到已经抽空的腔体中。
磁控溅射中电源的种类
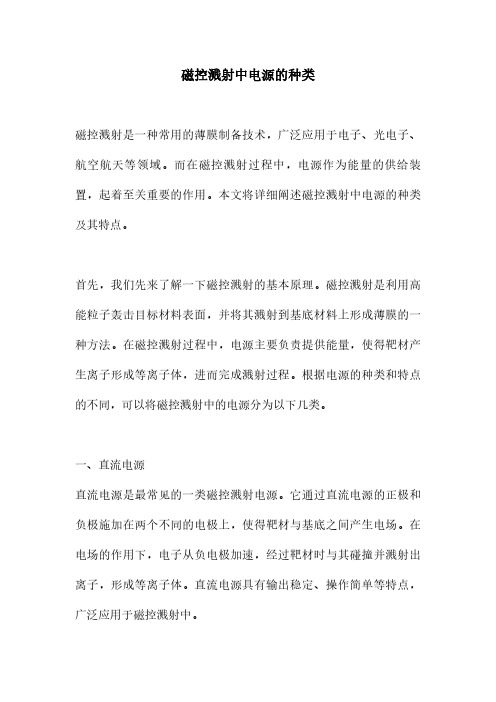
磁控溅射中电源的种类磁控溅射是一种常用的薄膜制备技术,广泛应用于电子、光电子、航空航天等领域。
而在磁控溅射过程中,电源作为能量的供给装置,起着至关重要的作用。
本文将详细阐述磁控溅射中电源的种类及其特点。
首先,我们先来了解一下磁控溅射的基本原理。
磁控溅射是利用高能粒子轰击目标材料表面,并将其溅射到基底材料上形成薄膜的一种方法。
在磁控溅射过程中,电源主要负责提供能量,使得靶材产生离子形成等离子体,进而完成溅射过程。
根据电源的种类和特点的不同,可以将磁控溅射中的电源分为以下几类。
一、直流电源直流电源是最常见的一类磁控溅射电源。
它通过直流电源的正极和负极施加在两个不同的电极上,使得靶材与基底之间产生电场。
在电场的作用下,电子从负电极加速,经过靶材时与其碰撞并溅射出离子,形成等离子体。
直流电源具有输出稳定、操作简单等特点,广泛应用于磁控溅射中。
二、脉冲电源脉冲电源是另一类常用的磁控溅射电源。
与直流电源相比,脉冲电源在输出电流上存在周期性变化。
它通过周期性的电流脉冲,使得靶材与基底之间的电场在正负极性之间切换。
这种脉冲切换的电场可以增强离子的动能,使得溅射速率更高,薄膜质量更好。
脉冲电源的使用可以提高磁控溅射的效率和薄膜的性能。
三、射频电源射频电源是一种高频交流电源,在磁控溅射中应用较为广泛。
它通过射频电场的作用,使得靶材与基底之间形成高频交变电场。
在交变电场的刺激下,靶材表面的原子和离子更容易被激发和溅射,进而形成等离子体。
射频电源具有频率可调、能量高等特点,适用于制备高质量薄膜和复杂结构的磁控溅射过程。
四、磁控溅射电源的选择在选择磁控溅射电源时,需要根据具体的应用需求和制备要求来确定。
直流电源操作简单、成本较低,适用于一般的薄膜制备。
脉冲电源虽然复杂度稍高,但通过调节脉冲参数可以改善溅射速率和膜层性能。
射频电源适用于制备高质量薄膜和复杂结构,但需要更高的成本投入和技术要求。
总结起来,磁控溅射中电源的种类有直流电源、脉冲电源和射频电源。
磁控溅射高频脉冲(a2k)电源的研制1

磁控溅射高频脉冲(A-2K)电源的研制1中南民族大学硕士学位论文磁控溅射高频脉冲(A<'2>K)电源的研制姓名:刘亚东申请学位级别:硕士专业:等离子体物理指导教师:孙奉娄20080501摘要根据调研和文献,对不同的溅射技术进行了比较,针对脉冲磁控溅射(Pulse Megnetron Sputtering(PMS))的特点及受限于电源技术的瓶颈,提出了A2K(Active Arc Killer)电源指标:输出频率最高达300kHz,负向电压在0~-500V可调,负向最大峰值电流达2A,正向电压在0~100V可调,正向最大峰值电流达1A,负向占空比10%~60%范围可调的双向脉冲电源。
为了实现电源指标,分析了拟设计电源的难点:主要是受电力电子器件的限制,电压、电流和频率同时达到所需水平的电力电子器件目前在国内无法找到,即使找到了成本也是相当高。
因此,本文从结构上入手,提出了整体的电源解决方案,它由两个独立的DC/DC变换(分别用于调节正、负向电压)、一个斩波系统(用于形成正向脉冲)和一个逆变倍频系统(用于形成负向脉冲)构成。
逆变倍频系统及其与斩波系统的配合是核心问题,方案在一定程度上突破了电力电子器件的限制,为溅射电源设计提供了新的方案。
根据总体方案,详细论述了主电路的拓扑选择、功率器件的选择、磁性器件的设计、缓冲电路的选择、控制电路和驱动电路的设计。
在比较了各种拓扑优缺点之后,根据电源指标要求,选择了全桥电路作为负向调压系统的DC/DC变换拓扑,正激电路作为正向调压系统的DC/DC变换拓扑,逆变倍频系统也采用全桥逆变,副边采用可控整流。
由于对频率有较高要求,功率开关管全部采用功率MOSFET。
讨论了中高频下Miller效应对功率开关管驱动的影响及其解决方案,还讨论了缓冲电路的作用及参数选择。
本文还从工程经验上详细描述了电源调试中出现的问题和如何解决这些问题的详细过程。
磁控溅射镀膜实验报告..doc

磁控溅射镀膜实验报告..doc
本次实验的目的是磁控溅射镀膜技术在材料科学中的应用,通过对磁控溅射镀膜过程的研究,探究其原理,并对所得到的薄膜进行分析。
一、实验步骤
1.将不同材料的基片放入溅射室中。
2.通过高频电源将气体放入溅射室中。
3.通过磁控电源产生磁场,使气体被激发。
4.激发后的气体离子在磁场作用下,被加速与基片的表面相撞,形成薄膜。
5.取出薄膜进行表面形貌、成分和结构的分析。
二、实验结果
本次实验我们选取了铜、铁和碳三种材料进行磁控溅射镀膜实验,得到了三组薄膜。
通过扫描电镜、X射线衍射仪、场发射扫描电子显微镜等手段对其进行了分析。
1.铜薄膜:表面均匀光滑,没有明显的颗粒,厚度在几十纳米。
2.铁薄膜:表面呈现网状结构,均匀分布的圆形颗粒,颗粒直径约为100纳米,厚度在50纳米左右。
3.碳薄膜:表面比较光滑,无明显纹路和颗粒,但是颜色比较暗,黑色。
通过X射线衍射实验,铜和铁薄膜的晶体结构比较完善,而碳薄膜由于其非晶结构,无法通过X射线衍射仪观察到其晶体形态。
另外,通过场发射扫描电子显微镜对样品进行表面成分分析,我们发现铜薄膜表面主要是铜元素,铁薄膜表面主要是铁元素,碳薄膜表面主要是碳元素。
三、经验总结
1.磁控溅射镀膜技术是一种高端的材料制备方法,具有良好的制备效果和广泛的应用前景。
2.制备薄膜的品质取决于材料本身的质量和处理工艺。
3.通过对薄膜的表面形貌、成分和结构的分析,可以更好的了解样品的特性和有效性。
4.在实验中,操作人员需要熟悉实验设备的操作规程,正确使用实验设备并遵守实验安全规范。
磁控溅射电源的作用

磁控溅射电源的作用
一、磁控溅射原理
磁控溅射是利用磁场约束等离子,使其螺旋运动而获得较高离子化率和离子密度,并利用磁场聚集等离子轰击靶材,使靶材原子溅射到基体上形成薄膜的过程。
二、磁控溅射电源的组成
磁控溅射电源主要由直流电源、匹配电路、电磁线圈等组成。
直流电源为系统提供直流电能,匹配电路实现加载阻抗的匹配,电磁线圈产生磁场。
三、磁控溅射电源的主要功能
1. 提供稳定的直流放电电压,维持等离子体的正常放电。
2. 通过调节放电参数,控制等离子体密度和能量。
3. 电力匹配,提高系统的电能传输效率。
4. 为电磁线圈供电,形成磁场,约束和聚集等离子。
四、磁控溅射电源的重要性
磁控溅射电源的输出电压波形稳定、匹配效果好,直接影响磁场的形成、等离子体的激发与控制,进而影响溅射过程中的离子激发、靶材溅射和薄膜沉积。
因此电源的性能直接关乎磁控溅射过程的稳定性。
五、磁控溅射电源的发展趋势
提高稳定性、灵活可控、高效匹配是电源发展的重点。
开发脉冲电源、中频电源等新型电源,实现过程控制;研发先进匹配电路,提高系统效率。
磁控溅射镀膜多年经验总结
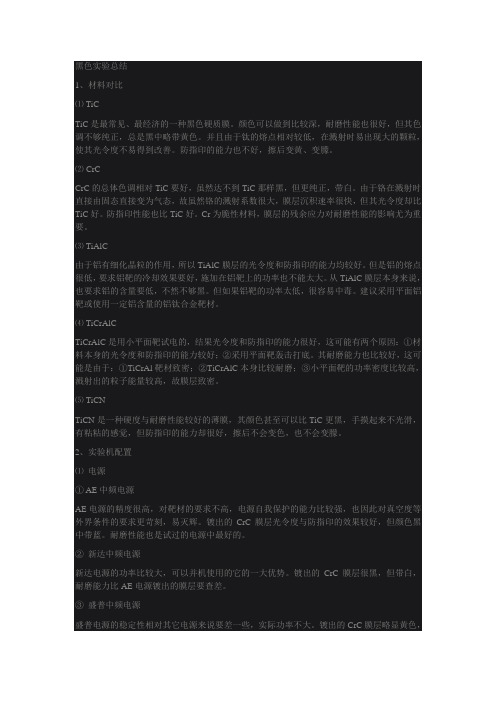
黑色实验总结1、材料对比⑴ TiCTiC是最常见、最经济的一种黑色硬质膜。
颜色可以做到比较深,耐磨性能也很好,但其色调不够纯正,总是黑中略带黄色。
并且由于钛的熔点相对较低,在溅射时易出现大的颗粒,使其光令度不易得到改善。
防指印的能力也不好,擦后变黄、变朦。
⑵ CrCCrC的总体色调相对TiC要好,虽然达不到TiC那样黑,但更纯正,带白。
由于铬在溅射时直接由固态直接变为气态,故虽然铬的溅射系数很大,膜层沉积速率很快,但其光令度却比TiC好。
防指印性能也比TiC好。
Cr为脆性材料,膜层的残余应力对耐磨性能的影响尤为重要。
⑶ TiAlC由于铝有细化晶粒的作用,所以TiAlC膜层的光令度和防指印的能力均较好。
但是铝的熔点很低,要求铝靶的冷却效果要好,施加在铝靶上的功率也不能太大。
从TiAlC膜层本身来说,也要求铝的含量要低,不然不够黑。
但如果铝靶的功率太低,很容易中毒。
建议采用平面铝靶或使用一定铝含量的铝钛合金靶材。
⑷ TiCrAlCTiCrAlC是用小平面靶试电的,结果光令度和防指印的能力很好,这可能有两个原因:①材料本身的光令度和防指印的能力较好;②采用平面靶轰击打底。
其耐磨能力也比较好,这可能是由于:①TiCrAl靶材致密;②TiCrAlC本身比较耐磨;③小平面靶的功率密度比较高,溅射出的粒子能量较高,故膜层致密。
⑸ TiCNTiCN是一种硬度与耐磨性能较好的薄膜,其颜色甚至可以比TiC更黑,手摸起来不光滑,有粘粘的感觉,但防指印的能力却很好,擦后不会变色,也不会变朦。
2、实验机配置⑴电源① AE中频电源AE电源的精度很高,对靶材的要求不高,电源自我保护的能力比较强,也因此对真空度等外界条件的要求更苛刻,易灭辉。
镀出的CrC膜层光令度与防指印的效果较好,但颜色黑中带蓝。
耐磨性能也是试过的电源中最好的。
②新达中频电源新达电源的功率比较大,可以并机使用的它的一大优势。
镀出的CrC膜层很黑,但带白,耐磨能力比AE电源镀出的膜层要查差。
磁控溅射镀膜机使用说明
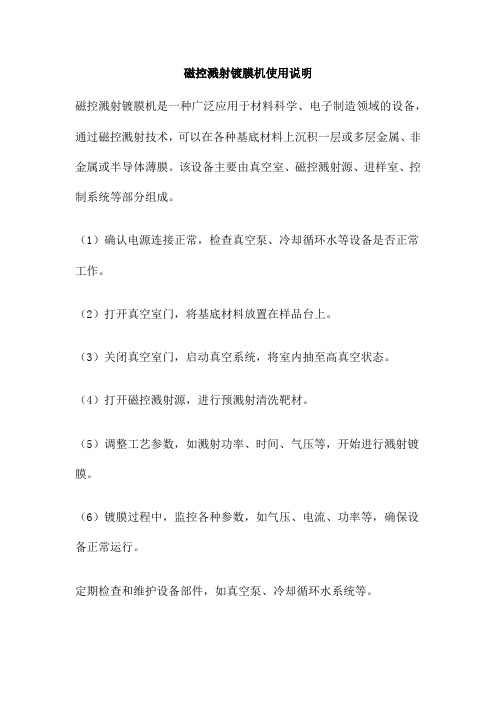
磁控溅射镀膜机使用说明磁控溅射镀膜机是一种广泛应用于材料科学、电子制造领域的设备,通过磁控溅射技术,可以在各种基底材料上沉积一层或多层金属、非金属或半导体薄膜。
该设备主要由真空室、磁控溅射源、进样室、控制系统等部分组成。
(1)确认电源连接正常,检查真空泵、冷却循环水等设备是否正常工作。
(2)打开真空室门,将基底材料放置在样品台上。
(3)关闭真空室门,启动真空系统,将室内抽至高真空状态。
(4)打开磁控溅射源,进行预溅射清洗靶材。
(5)调整工艺参数,如溅射功率、时间、气压等,开始进行溅射镀膜。
(6)镀膜过程中,监控各种参数,如气压、电流、功率等,确保设备正常运行。
定期检查和维护设备部件,如真空泵、冷却循环水系统等。
避免在镀膜过程中触摸设备内部部件,以免造成人身伤害。
如遇设备故障或异常情况,请立即停机检查,并专业人员进行维修。
保持设备清洁和整洁,定期进行清洁和维护。
磁控溅射镀膜技术的研究始于20世纪70年代,最初是为了满足空间电子器件对抗辐射损伤的需求。
随着科技的发展,磁控溅射镀膜技术的应用领域越来越广泛,然而也存在一些问题,如薄膜应力大、耐磨性差等,需要进一步研究和改进。
磁控溅射镀膜技术的基本原理是利用磁场控制下的电场放电,使靶材表面上的原子或分子被激发后沉积到基材表面,形成一层薄膜。
具体工艺过程包括:真空泵抽气、加热靶材、加磁场、加电场、溅射沉积等步骤。
该技术的特点在于沉积速度快、薄膜质量高、适用范围广等。
磁控溅射镀膜技术在光电领域的应用主要是在太阳能电池上制备减反射膜和抗反射膜。
在光学领域,磁控溅射镀膜技术可以用来制备各种光学薄膜,如增透膜、反射膜、滤光片等。
在电子领域,磁控溅射镀膜技术可以用来制备各种电子薄膜,如半导体薄膜、绝缘薄膜、导电薄膜等。
未来,磁控溅射镀膜技术的发展趋势主要体现在以下几个方面:一是进一步完善磁控溅射镀膜技术的工艺参数,提高薄膜的质量和性能;二是研究磁控溅射镀膜技术在新型材料制备中的应用,如纳米材料、石墨烯等;三是探索磁控溅射镀膜技术在生物医学、环境治理等领域的应用可能性。
磁控溅射镀膜

2、磁控溅射镀膜原理动画模拟
二、什么是真空
什么是真空?
相对真空
绝对真空
相对真空与绝对真空
相对真空 :通常把容器内气压低于正常大气压(101325 Pa)的都称之
罗茨泵使用注意事项
罗茨泵的启动程序 1、检查冷却水、油杯,齿轮箱和前端盖内是否有足够的润滑油; 2、启动前级泵,有旁通阀的罗茨泵可同时启动,无旁通阀罗茨泵,可看其联轴 节是否转动,从转动到不转动后即可启动罗茨泵。 3、吸入气体中有灰尘或金属粉末等,应在泵人口前加除尘装置或过滤装置; 4、吸入气体含有较多的水蒸气时,且前级泵的油封泵无气镇装置时,应在泵排 出口加冷凝器,防止前级泵油乳化; 5、运转中经常检查泵各部位的温度,水冷泵的冷却水出口温度是否超过规定; 6、泵在运转中如有局部过热或电流突然增加现象时应立即停泵检查,停泵时先 停罗茨泵,再停前级泵,放出全部冷却水。
磁控溅射镀膜原理及维护注意事项
摘要
一、磁控溅射镀膜原理 二、什么是真空 三、真空镀膜系统主要构成 四、真空获得设备的构成 五、真空泵的工作原理及维护 六、常用靶材 七、关于磁控溅射中遇到的问题 八、各种镀膜技术的比较
一、磁控溅射镀膜原理
1、磁控溅射的工作原理是指电子在电场作用下,在飞向基片过程中与
真空镀膜系统主要构成
1.真空腔体 设备主要有连续涂层生产线及单室涂层机两种形式,不锈钢材料制造、氩弧 焊接、表面进行化学抛光或喷砂处理,真空室组件上焊有各种规格的法兰接 口。 2.真空获得部分 在真空技术中,真空获得部分是重要组成部分。真空的获得不是一种真空设 备和方法所能达到的,必须将几种泵联合使用,如旋片泵、罗茨泵、分子泵 、扩散泵、离子泵系统等。 3.真空测量部分 真空系统的真空测量部分,就是要对真空室内的压强进行测量。像真空泵一 样,没有一种真空计能测量整个真空范围,人们于是按不同的原理和要求制 成了许多种类的真空计。如热偶计,电离计,皮拉尼计等等。
磁控溅射镀膜工艺介绍

➢反应磁控溅射适合于制备大面积均匀薄膜,并能 实现对镀膜的大规模工业化生产。
.
12
反应溅射的应用
➢ 现代工业的发展需要应用到越来越多的化合物薄膜。 ➢ 如光学工业中使用的TiO2、SiO2和TaO5等硬质膜。 ➢ 电子工业中使用的ITO透明导电膜,SiO2、Si2N4和
Al2O3等钝化膜、隔离膜、绝缘膜。 ➢ 建筑玻璃上使用的ZNO、SnO2、TiO2、SiO2等介质膜
.
13
真空系统的基本知识 ➢ 真空的定义:压力低于一个大气压的任何气态空间,采用 真空度来表示真空的高低。 ➢ 真空单位换算:1大气压≈1.0×105帕=760mmHg(汞柱) =760托 ➢ 1托=133.3pa=1mmHg
.
9
反应溅射模拟图
.
10
中频孪生反应溅射
.
11
反应溅射的特点
➢反应磁控溅射所用的靶材料(单位素靶或多元素 靶)和反应气体(氧、氮、碳氢化合物等)通常 很容易获得很高的纯度,因而有利于制备高纯度 的化合物薄膜。
➢反应磁控溅射中调节沉积工艺参数,可以制备化 学配比或非化学配比的化合物薄膜,从而达到通 过调节薄膜的组成来调控薄膜特性的目的。
接地
ArBiblioteka -V(DC)至真空泵
垂直方向分布的磁力线将电子约束在靶材表面附近,延长其在等离
子体中的运动轨迹,提高它参与气体分子碰撞和电离过程的几率的
作用。
.
2
❖磁控溅射镀膜-磁控阴极
.
3
相对蒸发镀,磁控溅射有如下的特点:
➢ 膜厚可控性和重复性好 ➢ 薄膜与基片的附着力强 ➢ 可以制备绝大多数材料的薄膜,包括合金,化合物等 ➢ 膜层纯度高,致密 ➢ 沉积速率低,设备也更复杂
一种直流磁控溅射镀膜电源快速灭弧电路[发明专利]
![一种直流磁控溅射镀膜电源快速灭弧电路[发明专利]](https://img.taocdn.com/s3/m/c28c5251cbaedd3383c4bb4cf7ec4afe04a1b16f.png)
(10)申请公布号 (43)申请公布日 2015.02.18C N 104362593A (21)申请号 201410530034.1(22)申请日 2014.10.10H02H 7/12(2006.01)(71)申请人湖南红太阳光电科技有限公司地址410205 湖南省长沙市高新开发区桐梓坡西路586号(72)发明人杨建生 刘嘉宾 郭艳(74)专利代理机构长沙正奇专利事务所有限责任公司 43113代理人马强(54)发明名称一种直流磁控溅射镀膜电源快速灭弧电路(57)摘要本发明公开了一种直流磁控溅射镀膜电源快速灭弧电路,包括第一功率开关管和第二功率开关管,所述第一功率开关管串联在直流电源输出端上,所述第二功率开关管与所述直流电源的输出端并联,且所述第二功率开关管一端并联接到所述第一功率开关管和所述直流电源的输入端之间;所述第二功率开关管与缓冲储能电路并联;所述第一功率开关管和第二功率开关管的控制极均与控制驱动器连接。
本发明电路结构简单,体积小,实时性强,方便现有电源加装改造。
本发明可以使电源工作于频繁产生打弧的工艺条件下,极大地降低打弧的能量,提高溅射沉积薄膜的质量。
(51)Int.Cl.权利要求书1页 说明书2页 附图2页(19)中华人民共和国国家知识产权局(12)发明专利申请权利要求书1页 说明书2页 附图2页(10)申请公布号CN 104362593 A1.一种直流磁控溅射镀膜电源快速灭弧电路,其特征在于,包括第一功率开关管和第二功率开关管,所述第一功率开关管串联在直流电源输出端上,所述第二功率开关管与所述直流电源的输出端并联,且所述第二功率开关管一端并联接到所述第一功率开关管和所述直流电源的输入端之间;所述第二功率开关管与缓冲储能电路并联;所述第一功率开关管和第二功率开关管的控制极均与控制驱动器连接;当发生打弧现象时,所述控制驱动器控制第一功率开关管关断,所述直流电源电感产生的能量转移到所述缓冲储能电路中然后开通第二功率开关管,待所述缓冲储能电路放电结束后,所述控制驱动器控制所述第二功率开关管关断,并开通所述第一功率开关管。
- 1、下载文档前请自行甄别文档内容的完整性,平台不提供额外的编辑、内容补充、找答案等附加服务。
- 2、"仅部分预览"的文档,不可在线预览部分如存在完整性等问题,可反馈申请退款(可完整预览的文档不适用该条件!)。
- 3、如文档侵犯您的权益,请联系客服反馈,我们会尽快为您处理(人工客服工作时间:9:00-18:30)。
磁控溅射玻璃镀膜电源
Dr. Dirk Ochs
HÜTTINGER Elektronik GmbH + Co KG, Freiburg, Germany
黄新盈
深圳市微普真空系统集成有限公司
介绍:
近年来,建筑玻璃市场对Low‐e镀膜玻璃产生了巨大的需求。
特别是经济快速增长的中国,印度和东欧地区。
目前高档Low‐e主要采用磁控溅射方式镀膜,关于镀膜设备,Low‐E 制造商们关注的是溅射速率,薄膜质量和生产成本。
在Low‐E生产中,连续镀膜系统常用的是30‐200KW的直流和中频磁控溅射电源[1,2,3,4]。
对于建筑玻璃镀膜所使用的电源,则要求高精度的过程控制能力,配备强大的打弧管理系统,并提供可调整的参数。
能使生产过程中的干扰最大程度的减少,获得最优化的膜层。
为了保证溅射速率和产量,生产过程中对电源的打弧管理提出了很高的要求。
比如反应溅射低熔点材料,打弧非常容易在靶面上造成孔洞。
快速先进的打弧管理,能预防靶面产生的缺陷并且获得更高的功率,意味着安全可靠的获得更高的溅射速率。
应用:
建筑玻璃的主要应用是阳光控制膜,低辐射膜和减反膜。
图1是典型的阳光控制膜系。
玻璃基板首先沉积了一层厚度在10‐100nm的SnO2。
膜厚从10nm从增加到100nm时,颜色则从银色渐变为青铜色,最后是蓝色。
在SnO2上还需要沉积CrNx和SnO2膜。
一个典型的低辐射膜系图2,开始也是先在玻璃基板上沉积SnO2,起到减反的作用。
然后是反射红外线的银层,再沉积阻挡层NiCrOx,和减反层SnO2。
减反的膜系(图3)由一个高折射系数材料和一个低折射系数的材料交替组合而成。
常用的高折射系数的材料有ZrO2,Ta2O5和TiO2。
低折射系数材料如MgF2,SiO2,或Al2O3。
金属膜通常是用直流电源驱动单个磁控靶溅射。
而氧化物和氮化物膜层则使用中频电源,配合孪生磁控靶进行反应溅射。
磁控溅射原理如图4所示
首先是工艺气体通入到已经抽空的腔体中。
在靶材上施加几百伏的负高压后,在靶面前方产生辉光放电的(起辉)等离子体,工艺气体的离子(通常是氩气)被靶的负高压吸引而撞向靶材,碰撞后将靶材溅射出来。
溅射出的材料则沉积在与靶相对的基板上。
而对于介质材料的镀膜,如氧化物或氮化物则需要对等离子体额外通入氧气或氮气。
孪生靶的两个阴极各自连接到电源的一极。
这样的话,当其中一个阴极处于负压溅射状态时,另一个处于正压可以看作是阳极。
以一定频率(中频)交替互为阴阳极 。
对于所有的镀膜过程而言,都要对打弧现象进行控制尤其是在高功率密度下,以增加溅
射速率。
除了镀膜系统本身的功能如工艺和气体控制,电源及其打弧管理功能也扮演着重要的角色。
电源的作用是将电网的能量转变成不同的电压和频率水平,对电网和负载进行隔离,还有对镀膜过程中的功率实施动态控制。
在电源设计时必须仔细考虑等离子体的阻抗动态变化的三个阶段,从气体隔离,起辉,然后产生等离子体,打弧再到打弧熄灭。
直流电源
为了提高电源性能同时降低成本,提出了直流电源模块化的概念。
电源系统可按单台20kw 或30kw设计成一个模块(图5)。
该模块设计紧凑,风冷或水冷,可组合堆栈(主/从设计)。
最大功率可组合到120kw。
额定功率为30kw时,输出电压从400‐800V随不同的靶材变化。
为保证等离子体的产生(起辉),集成了一个帮助装置提供>1400V的起辉电压。
智能打弧管理和直流电源的控制是等离子体应用中的重要一环。
参数设置可通过DeviceNet或Profibus接口由外部进行控制。
打弧检测非常迅速(<1ms﹚,打弧关断延长时间可调(<1μs up to 100 ms)。
中频电源
近来某些工艺要求电源具有超快速的打弧管理,研发出了一款新型电源(图6)。
从原理上讲,该电源包括两部分,直流单元和中频单元。
直流单元包括30kw的功率模块,最多可叠加4个。
中频单元将直流单元的直流电压转变成一个中频的交流电压。
频率由其内部振荡电路产生,频率高低则由电容和电感决定。
通过改变电容和电感,电源频率可在20KHz 到70KHz的范围内改变,以满足工艺需要。
接下来重点要介绍的是打弧管理方面的改进,下列条件是用于打弧检测的临界条件,不仅预置参数配方还可进行调整。
电压下降,电流上升的绝对和相对限制值。
两个阴极之间的电流不对称性。
电源会对两个阴极之间的电流进行比较。
频率变化
半波波形的变化
检测到打弧后,电源开始响应。
可立即关断或延时关断。
电源中断通过额外的快速打弧开关实现。
如图7所示,这项技术使打弧检测和电源关断能在5μs实现,打弧残余能量为5mJ/kw.改良的打弧管理对镀膜系统运行的经济性起到了很明显的贡献。
首先,快速而灵活的打弧处理将打弧造成的缺陷最小化,改善了膜层质量。
其次,保证了工艺稳定性,从而或得很高的溅射速率,这就意味着镀膜产量的提高。
额外的益处是打
弧残余能量最小化,每kw单位功率残留的能量只有5mJ。
即使是快用完的靶材,产生打弧的概率非常高,也能从容应对,有效延长靶材的使用寿命和利用率。
从本质上来说,有效打弧管理的显著特征是提供一个稳定的等离子体生产环境。
快速的抑弧能最大程度的减少溅射过程的中断次数,打弧次数几乎可以忽略不计。
不过打弧对清洁靶面上的污染物有益,所以电源必须能精确控制和调节打弧能量。
总结
大功率的直流和中频电源可满足各种要求的建筑玻璃镀膜工艺。
上述电源具有高精度工艺控制能力和最先进的打弧管理,使镀膜过程受到的干扰最小化。
从而得到最优的膜层均匀性,化学计量比和光学性能。
此外,优秀的打弧管理系统还保证了较高的镀膜速率。
参考
[1] Hüttinger Elektronik, SCALO/ SCASAR
Product Literature, 2007
[2] V. Kirchhoff, T. Kopte, T. Winkler, M. Schulze,
P. Wiedemuth: 5th Conference on Plasma
Surface Engineering, PSE, 1996
[3] G. Br鋟er, J. Szczyrbowski, G. Teschner:
Surface and Coatings Technology., 94-95, p.
658-662, 1997
[4] T. Rettich, P. Wiedemuth:, 40th Annual Technical Conference Proceedings, p. 135-138, SVC, 1997。