品质改善会议案例 ppt课件
合集下载
品质改善专案完美版PPT

4、设 计对 灌注 口的 保护 装置。 订 立长 期灭 蚊的 方案程 序 。
包 装 厂
包 装 厂 品 检 部 XM/包 装 厂
专案具体的目标及成效
专案具体的目标:
• 杂质事故发生率为“3瓶/一百万瓶”(3瓶/5000T) (此处指小包装油中含有较明显的杂质,即引起
消费者反感/不满的异物) • 小包装油内有蚊子或其它飞虫的事故发生率为0
蚊子
环境
1
0.11
合计
972
100
备注
表二数据说明:1)70%的杂质来源于物料或设备产生, 小黑点多为焊 点、锈点,还有一部分较难发现的小黑点可能来自瓶子本身。2)明显来 自物料 的杂质占了29%,这类杂质有三种:A、透明胶丝:一般残留 瓶口的丝状披锋;B、白胶丝:套瓶口时刮伤白色手挽所致或密封盖里 面残留的锋边。C、胶冰颗粒:附在瓶子里面,直径较大,约0.5至3MM 3)由环境因素引起的杂质比例虽然不到1%,但属严重质量问题,有头发、
蚊子、蚂蚁。
此专案成立背景(续二)
出现较严重的有关产品质量方面的投诉
市场上曾经发现我司极少量的小包装 产品中含有苍蝇、蚊虫等昆虫及头发、纸 屑等杂质;
小包装产品杂质来源分析
编编号 杂质来源
改善方案
负责部门
1 空瓶(空罐)中 1. 含有的杂质来源 2.
3.
加大对空瓶进货检验的抽样量,从 0.1%提高到 0.2%
分之三,相差千倍。 D线由于较多PVC材料胶樽,而PVC由于带静电而吸引较多杂质
于胶樽之内,导致杂质出现机率较多
此专案成立背景(续一)
二、杂质来源分析表(表二)
杂质名称 来 源 数量(支) 百分比%
小黑点 设备或物料 681
包 装 厂
包 装 厂 品 检 部 XM/包 装 厂
专案具体的目标及成效
专案具体的目标:
• 杂质事故发生率为“3瓶/一百万瓶”(3瓶/5000T) (此处指小包装油中含有较明显的杂质,即引起
消费者反感/不满的异物) • 小包装油内有蚊子或其它飞虫的事故发生率为0
蚊子
环境
1
0.11
合计
972
100
备注
表二数据说明:1)70%的杂质来源于物料或设备产生, 小黑点多为焊 点、锈点,还有一部分较难发现的小黑点可能来自瓶子本身。2)明显来 自物料 的杂质占了29%,这类杂质有三种:A、透明胶丝:一般残留 瓶口的丝状披锋;B、白胶丝:套瓶口时刮伤白色手挽所致或密封盖里 面残留的锋边。C、胶冰颗粒:附在瓶子里面,直径较大,约0.5至3MM 3)由环境因素引起的杂质比例虽然不到1%,但属严重质量问题,有头发、
蚊子、蚂蚁。
此专案成立背景(续二)
出现较严重的有关产品质量方面的投诉
市场上曾经发现我司极少量的小包装 产品中含有苍蝇、蚊虫等昆虫及头发、纸 屑等杂质;
小包装产品杂质来源分析
编编号 杂质来源
改善方案
负责部门
1 空瓶(空罐)中 1. 含有的杂质来源 2.
3.
加大对空瓶进货检验的抽样量,从 0.1%提高到 0.2%
分之三,相差千倍。 D线由于较多PVC材料胶樽,而PVC由于带静电而吸引较多杂质
于胶樽之内,导致杂质出现机率较多
此专案成立背景(续一)
二、杂质来源分析表(表二)
杂质名称 来 源 数量(支) 百分比%
小黑点 设备或物料 681
品质改善活动的改善案例ppt课件

QCC改善活动资料
1
选定主题—选择
异常原因分析和对策中必备项:
1.生产不良 制造原因只有在产品生产时发生及对策
2.流出不良 流出原因在制造过程和检查过程都会 产生。并如在出货检查时防止异常流出, 可达成客户要求的标签与实物不符不良 不良件数“0”目标
2
选定主题—定案
减少客户投诉中多数量不良,达成客户 PPM目标。 理由是: *客户每年都有相关联络,要求各供应商 减少标签与实物不符的异常。 *品管检查作业方法中可以对应。
件
10月份纳入不良个数明细
不良数 不良比率
500
112233445050505050500000000000
56.1% 386 43.3%
2 0.2%
1 0.1%
1 0.1%
60.0% 50.0% 40.0% 30.0% 20.0% 1 10.0% 0.1% 0.0%
标签与实物不符 外观不良 露底不良 寸法不良 组装不良 性能不良
作业台
人
培训不足 标准不了解
未按照作业标 准实施
线上配料异常
料
工作时间太 长,疲惫
人员工作时精 神不集中
个人原因
流
出
不
良
原
因
分
析
来料错误
来料错误时,受入检查 和工程中的生产前确认 可发现,需提前预防。
8
喔哦~
原因分析—分析结论说明
NO
不良项目
原因
对策
人
1.培训后向受训人确认培
为 因
训内容是否理解;
6
设定目标
来来来,一 起来改善!
出货检查流程及方法: 1.制造完成品检查
(全数检查)
1
选定主题—选择
异常原因分析和对策中必备项:
1.生产不良 制造原因只有在产品生产时发生及对策
2.流出不良 流出原因在制造过程和检查过程都会 产生。并如在出货检查时防止异常流出, 可达成客户要求的标签与实物不符不良 不良件数“0”目标
2
选定主题—定案
减少客户投诉中多数量不良,达成客户 PPM目标。 理由是: *客户每年都有相关联络,要求各供应商 减少标签与实物不符的异常。 *品管检查作业方法中可以对应。
件
10月份纳入不良个数明细
不良数 不良比率
500
112233445050505050500000000000
56.1% 386 43.3%
2 0.2%
1 0.1%
1 0.1%
60.0% 50.0% 40.0% 30.0% 20.0% 1 10.0% 0.1% 0.0%
标签与实物不符 外观不良 露底不良 寸法不良 组装不良 性能不良
作业台
人
培训不足 标准不了解
未按照作业标 准实施
线上配料异常
料
工作时间太 长,疲惫
人员工作时精 神不集中
个人原因
流
出
不
良
原
因
分
析
来料错误
来料错误时,受入检查 和工程中的生产前确认 可发现,需提前预防。
8
喔哦~
原因分析—分析结论说明
NO
不良项目
原因
对策
人
1.培训后向受训人确认培
为 因
训内容是否理解;
6
设定目标
来来来,一 起来改善!
出货检查流程及方法: 1.制造完成品检查
(全数检查)
品质改善及计划PPT课件
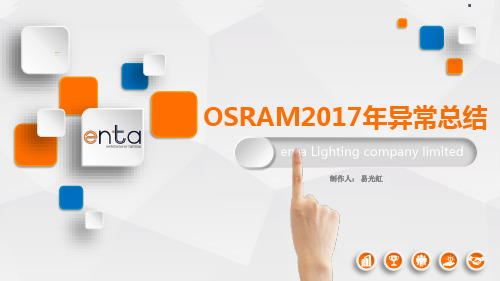
检验数量 合格数 不良率 灯珠偏位 IC偏位 ICL连锡 其他
479699 6607 1.377% 0.259% 0.553% 0.322% 0.243%
SMT炉后不良统计
0.243% 0.259%
0.322%
0.553%
灯珠偏位 IC偏位 ICL连锡 其他
检验数量
2017年成品不良数据统计(主要不良统计)
经理:1 人
文员/文控 1 人
检验组:组长/副主管 1 人
三楼 QC:6 人
三楼 IPQC: 1人
6 楼 QC: 9人
6楼 FQC:2 人
6楼 IPQC:2 人
SQE 1 人 IQC 组长 1 人 IQC:2 人
QE 2 人
6楼 QA:3 人
实验室技术员 1人
品质工作计划
序 任务名称 号
1
品质流程改善
不合格数 不良率 灯不亮
不良分类
丝印不良 脏污
焊盘偏位 其他
479699
8946 1.87% 0.768% 0.378% 0.250%
成品检验不良分类
0.019% 0.45%
0.45% 0.019%
0.250%
0.768%
0.378%
灯不亮 丝印不良 脏污 焊盘偏位 其他
SMT不良改善——灯珠不亮
二、改善对策 1.来料过程: ①由SQE重新制定检验标准“针对性VIP客户专项检验标准,检验报表修改”,避免作业人员操作时按照其内容执行无遗漏操作或检验不彻底登现象。——已完成 (FPC、标签) ②SQE对与IQC平时作业方式进行监督、稽核确认作业方式是否合理,按照规定执行,品质经理每天不定时进行现场稽核 ③对于来料检验样品进行整理,归类,建立电子档案,便于查找 ④供应商对此异常进行流程改善——
479699 6607 1.377% 0.259% 0.553% 0.322% 0.243%
SMT炉后不良统计
0.243% 0.259%
0.322%
0.553%
灯珠偏位 IC偏位 ICL连锡 其他
检验数量
2017年成品不良数据统计(主要不良统计)
经理:1 人
文员/文控 1 人
检验组:组长/副主管 1 人
三楼 QC:6 人
三楼 IPQC: 1人
6 楼 QC: 9人
6楼 FQC:2 人
6楼 IPQC:2 人
SQE 1 人 IQC 组长 1 人 IQC:2 人
QE 2 人
6楼 QA:3 人
实验室技术员 1人
品质工作计划
序 任务名称 号
1
品质流程改善
不合格数 不良率 灯不亮
不良分类
丝印不良 脏污
焊盘偏位 其他
479699
8946 1.87% 0.768% 0.378% 0.250%
成品检验不良分类
0.019% 0.45%
0.45% 0.019%
0.250%
0.768%
0.378%
灯不亮 丝印不良 脏污 焊盘偏位 其他
SMT不良改善——灯珠不亮
二、改善对策 1.来料过程: ①由SQE重新制定检验标准“针对性VIP客户专项检验标准,检验报表修改”,避免作业人员操作时按照其内容执行无遗漏操作或检验不彻底登现象。——已完成 (FPC、标签) ②SQE对与IQC平时作业方式进行监督、稽核确认作业方式是否合理,按照规定执行,品质经理每天不定时进行现场稽核 ③对于来料检验样品进行整理,归类,建立电子档案,便于查找 ④供应商对此异常进行流程改善——
品质提升改善方案(ppt共20张)

品质提升改善方案(PPT20页)
品质提升改善方案(PPT20页)
长期计划
制程
来料
工程
品质
检查 体制
提升 体制
品质提升改善方案(PPT20页)
品质提升改善方案(PPT20页)
实施细则(1)
来料品质--进料接收标准,供方审核
一、供应商现场检讨分析 二、来料不良追踪/回复/改善效果确认 三、供应商定期辅导培训 四、供应商现场审核 五、供应商品质异常处罚 六、供应商份额调配 页)
改善方针
三
不接受不良品
不
不制造不良品
原
则
不传递不良品
制定严禁不良品流入下一工序的管理方案,并持续不断地 构建一个完善的管理体系。
品质提升改善方案(PPT20页)
品质提升改善方案(PPT20页)
改善团队
姓名
XX XX XX XX XX XX XX XX XX XX XX XX XX
品质体系提升
质量体系--全员参与,提高品质意识
一、工作流程化 二、作业标准化 三、文件规范化 四、人员信息化 五、质量精细化
品质提升改善方案(PPT20页)
供应商管理
来料品质--进料接收标准,供方审核
一、完善进料品质检查记录,确保源数据的 真实性、可靠性及可追溯性,对异常频发的 供应商进行辅导,推动供应商进行内部改善。 二、年内对供应商进行审核评分,对供应商 的经营状况、财务状况、生产能力、设备状 况及质量管理体系等方面进行摸查,对未能 达到我司要求的供应商进行淘汰更换。
品质提升改善方案(PPT20页)
品质提升改善方案(PPT20页)
实施细则(5)
提升体制--全员参与,提高品质意识
一、建立品质考核制度,提升操作人员 的责任感。
品质提升改善方案(PPT20页)
长期计划
制程
来料
工程
品质
检查 体制
提升 体制
品质提升改善方案(PPT20页)
品质提升改善方案(PPT20页)
实施细则(1)
来料品质--进料接收标准,供方审核
一、供应商现场检讨分析 二、来料不良追踪/回复/改善效果确认 三、供应商定期辅导培训 四、供应商现场审核 五、供应商品质异常处罚 六、供应商份额调配 页)
改善方针
三
不接受不良品
不
不制造不良品
原
则
不传递不良品
制定严禁不良品流入下一工序的管理方案,并持续不断地 构建一个完善的管理体系。
品质提升改善方案(PPT20页)
品质提升改善方案(PPT20页)
改善团队
姓名
XX XX XX XX XX XX XX XX XX XX XX XX XX
品质体系提升
质量体系--全员参与,提高品质意识
一、工作流程化 二、作业标准化 三、文件规范化 四、人员信息化 五、质量精细化
品质提升改善方案(PPT20页)
供应商管理
来料品质--进料接收标准,供方审核
一、完善进料品质检查记录,确保源数据的 真实性、可靠性及可追溯性,对异常频发的 供应商进行辅导,推动供应商进行内部改善。 二、年内对供应商进行审核评分,对供应商 的经营状况、财务状况、生产能力、设备状 况及质量管理体系等方面进行摸查,对未能 达到我司要求的供应商进行淘汰更换。
品质提升改善方案(PPT20页)
品质提升改善方案(PPT20页)
实施细则(5)
提升体制--全员参与,提高品质意识
一、建立品质考核制度,提升操作人员 的责任感。
《品质的改善与提升》PPT课件

C入库检验管理
类别 月份
1
2
3
4
5
6
7
8
9
10
11
12
入库合计 不合格统计
合格率
#DIV/0! #DIV/0! #DIV/0!
53 0 100%
119 3
97%
66 12 82%
合格率
120%
100%
80%
60%
40%
20%
0%
1
2
3
4
5
6
7
8
9
10
11
12
合格率
存在关键问题: 1、发现较多的一些低级生产过程控制品质问题,如漏附件;2、员工上岗操作技能与质量意识培训、质量业绩考核机制 太弱,员工不规范操作经常发生,造成产品表面刮伤、碰坏等返工;4、质量标准要求不明确、过程质量控制机制缺失,
三、如何建立提升品质的持续改善机制
如何建立提升品质的持续改善机制
管理创新 改善细节 强化执行 品质突破
2021品质管理3个阶段
第一阶段、(1-6月) 质量团队的建设,明确产品全过程的监控,制定检验标准依据,数
据的建立。 第二阶段、(7-10月)
通过培训,制定相应的管理制度(供应商评价准则/生产过程中质 量检验规程),强化全员质量意思,预防质量问题的重复发生 第三阶段 (10月份以后,持续改进)
1、产品实现全过程的品控保证体系还需 强化执行力与持续改进与完善; 2、供应链的质量保证能力要求与管理提 升势在必行;
内部 因素
公司的生产规模与产值急剧 扩大,产品种类较多,质量 管理工作难度增加;
公司领导战略决策,公司产 品向高端进军规划
品质管理问题点和改善建议ppt课件

样机测试报告, 可靠性测试报告
品质部
9
试产评估,总结改善行动及改 生产工程部对试产中各部门提出问题进行汇总,组织试产总结确认改善行动。 试产评估报告及
各相关部门
善效果确认,
品质部跟踪对策实施效果并及时通报相应部门。对于严重质量问题没有改善品 改善对策
质部应有权拒绝批量生产。正式作业指导书、工装夹具的完善
品质主管
品质部文员
IQC
塑
电
胶
子
五
料
金
检
包
验
材
检
验
IPQC
制 程 巡 检 员
QA
组
装
包
成
装
品
抽
抽
检
检
பைடு நூலகம்QA
QA
11
四:品质部人员需求表与岗位职责
序 号
职位
职责
1
主管
全面负责品质部工作计划,组织,实施和检查工作,确保产品质量达到质量目标符 合客户要求
2
文员 部门人事,文件收发,质量记录统计工作
3
QE工 程师
的资料上显示的都不一样。资料变更频繁未回收旧版,变更后生产,品质对变更跟进实施不够导至出错。
12.生产现场,仓库物料的标识不够全面没有按ERP系统编码去区分标识。比如SMT ML-9000B灯板半成品板标识不同订单不同料号的却编为同
一个料号。
3
B、改善建议
序号
1
问题点
部门质量目标未细化并统计达成情况
2
供应商质量控制
3
进料检验检出度
4
生产过程的控制
1、完善供应商选择,评估,考核标准并执行 2、确保物料质量要求得到正确的实别并传达到供应商
《品质改善报告》课件
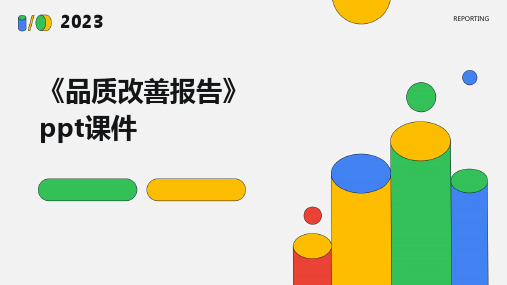
REPORTING
总结
品质改善的背景
介绍当前品质问题的严重性, 以及品质改善的必要性和紧迫
性。
品质改善的历程
概述品质改善的整个过程,包 括问题识别、原因分析、解决 方案制定和实施等。
品质改善的成果
详细介绍品质改善所取得的成 果,包括产品合格率提升、客 户满意度提高、成本降低等。
品质改善的经验教训
总结在品质改善过程中所遇到 的问题和困难,以及应对策略
03
02
详细描述
04
引入先进的生产技术和方法,优化工艺流 程。
制定详细实施计划,确保工艺改进顺利进 行。
05
06
持续监测改进效果,进行必要的调整和优 化。
方案二:设备升级
总结词:通过升级生产设 备,提高产品质量、生产
效率和降低成本。
对现有设备进行全面评估 ,确定需要升级的设备和
部位。
制定设备安装和调试计划 ,确保设备正常运行。
对培训效果进行评估和反 馈,持续改进培训计划。
2023
PART 04
品质改善实施计划
REPORTING
实施步骤一:方案准备
目标设定
明确品质改善的目标,包括提高 产品合格率、降低不良品率等。
现状分析
对当前品质状况进行深入分析, 找出问题所在,为后续方案制定
提供依据。
方案制定
根据现状分析结果,制定相应的 品质改善方案,包括改进工艺、
随着市场竞争的日益激烈,提高产品 品质成为企业赢得市场的关键。
企业生产过程中存在一些品质问题, 如不良品率较高、产品性能不稳定等 ,需要解决。
客户对品质要求提高
客户需求日益多样化,对产品品质的 要求也越来越高,促使企业不断改进 品质。
项目管理:质量改善案例DMAICPPT幻灯片
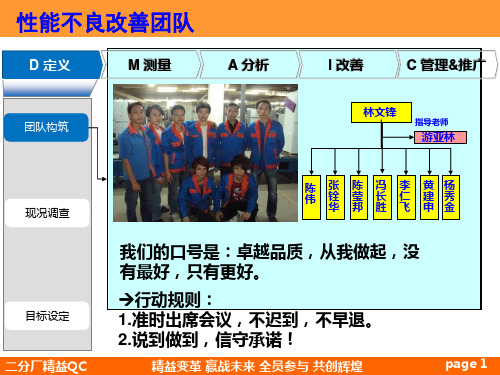
更换长弹簧,接触良好
C 管理&推广
效果确认
改善效果
1)减少由于电源接触不良导致箱体在抽空过程中出现断电现 象,加强抽空效果,减少抽空不良
二分厂精益QC
精益变革 赢战未来 全员参与 共创辉煌
page 14
改善事例 四
D定义
M测量
A 分析
I 改善
C 管理&推广
方案导出 方案实施
工位
管道 吹污
改善者
贺洪明 林文锋
200
不良数
70.0%
累积不良率
60.0%
150
50.0%
40.0% 100
30.0%
50
20.0%
10.0%
0
0.0%
结霜不均
不制冷
管折
制冷不合格 无停机点(cn) 回气管结霜
本月后续事项:对策标准化、水平展开
下期改善点现状调查
下期重点改善:结霜不均、安检不良
改善目标:结霜不均下降30%;安检不良下降
-20.45%
现状调查 目标设定
二分厂精益QC
11月性能不良改善目标
改善周期:
4.4%
10-11~11-30日;
3.5%
2.0%
本期目标:3%以下 质量改善以一个月
为PDCA循环改善,每
10月
11月 最终
月设定改善目标。
不良
目标 目标
精益变革 赢战未来 全员参与 共创辉煌
page 3
二分厂精益QC
二分厂精益QC
精益变革 赢战未来 全员参与 共创辉煌
page 8
工程流程图分析
D定义
M 测量
A 分析
品质改善小组PPT幻灯片

7
流程管理与改善的七大步骤
1. 建立制程管理责任(负责者) 2. 定义制程及确认客户需求(管理阶层) 3. 定义及建立(判断)测量基准 4. 评估基准与客户需求的一致性 5. 评估/研究制程确认改善机会 6. 改善机会分级并设定目标 7. 改善制程品质
8
流程管理与改善的七大步骤
管理制程 ( 程序 1-4)
(a)利用QC 7 Tools去找出原因并针对问题做出原因影响度 的分析。
(b)第二次的分析着重于分析具有执行性的问题来源/原因, 而不是所有的原因。
3
全面品质管理
品质机能展开(QPD)
品质机能管理 (Policy Management)
品质改善小组(QIT)
全面品质管理
品质小组 Quality Teams
TQM
每日工作之品质 Quality in
Daily Work
顾客满意 Customer Satisfaction
事据(实)管理 Management
(d)设定好要做为以后追查进度的标准/基准。 (e)决定到底需要做多少的改善活动。 (f)标示出改善的效果会对所设定的主题产生的影响 (g)叙述对改善问题/区域所要执行的程序。
Good Target
图表
25
步骤一:改善理由
可运用的工具/手法
(a)图表 (b)管制图 (c)程序流程图
21
朗讯(台湾)品质改善小组模式
22
品管报导(QC Story)
題目選定 目标订定
現況分析 汇总,状态
原因分析
收集所有 可能原因
探寻 无 差异
有 无
分析差异 差异原因
真因調查 证实真因
對策構想 创意及评价
流程管理与改善的七大步骤
1. 建立制程管理责任(负责者) 2. 定义制程及确认客户需求(管理阶层) 3. 定义及建立(判断)测量基准 4. 评估基准与客户需求的一致性 5. 评估/研究制程确认改善机会 6. 改善机会分级并设定目标 7. 改善制程品质
8
流程管理与改善的七大步骤
管理制程 ( 程序 1-4)
(a)利用QC 7 Tools去找出原因并针对问题做出原因影响度 的分析。
(b)第二次的分析着重于分析具有执行性的问题来源/原因, 而不是所有的原因。
3
全面品质管理
品质机能展开(QPD)
品质机能管理 (Policy Management)
品质改善小组(QIT)
全面品质管理
品质小组 Quality Teams
TQM
每日工作之品质 Quality in
Daily Work
顾客满意 Customer Satisfaction
事据(实)管理 Management
(d)设定好要做为以后追查进度的标准/基准。 (e)决定到底需要做多少的改善活动。 (f)标示出改善的效果会对所设定的主题产生的影响 (g)叙述对改善问题/区域所要执行的程序。
Good Target
图表
25
步骤一:改善理由
可运用的工具/手法
(a)图表 (b)管制图 (c)程序流程图
21
朗讯(台湾)品质改善小组模式
22
品管报导(QC Story)
題目選定 目标订定
現況分析 汇总,状态
原因分析
收集所有 可能原因
探寻 无 差异
有 无
分析差异 差异原因
真因調查 证实真因
對策構想 创意及评价
品质会议模板(共27张PPT)
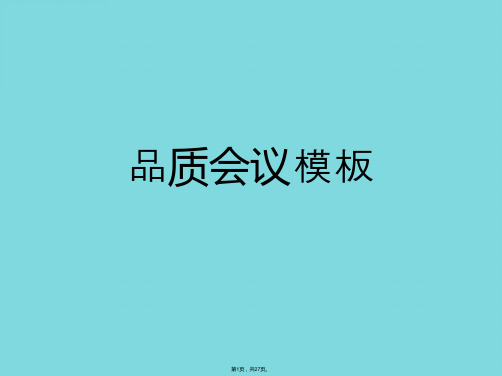
Ⅰ. 品质指标现况(工序不良率分解)
工序不良率
[ Y类 ]
担当:C
[单位:%]
10.00 8.00 6.00 4.00 2.00 0.00
7.93
3.52
0.59
0.94
0.75
0.12
0
0
第7页,共27页。
Ⅰ. 品质指标现况(收率)
收率推移
[ X类 ] 100.0 90.0 80.0 70.0 60.0
第12页,共27页。
担当:B
[单位:%]
19
担当:C
[单位:%]
97
Ⅰ. 品质指标现况(出品检验直通率)
2.X类
担当:B
[单位:%]
19
第13页,共27页。
Ⅰ. 品质指标现况(出品检验直通率)
3.Y类
担当:C
[单位:%]
97
第14页,共27页。
Ⅰ. 品质指标现况(出品检验直通率)
4.X类直通率低下的日别不良率
20.00
15.00
10.00
5.00
0.00
*月:
▶ **:38%
▶ **:20% ▶ **:17%
*月(20日前): ▶ **:39% ▶ **:21%
▶ **:15%
*月: ▶ **:23% ▶ **:21%
▶ **:10%
第22页,共27页。
担当:C
40 [单位:%]
**下线:
1.**:44% 2.**:12%
总经理
第2页,共27页。
前月责任人对策完成情况点检
前月问题点简述
责任部门 责任人 完成日期 点检者
完成情况
前月
本月
- 1、下载文档前请自行甄别文档内容的完整性,平台不提供额外的编辑、内容补充、找答案等附加服务。
- 2、"仅部分预览"的文档,不可在线预览部分如存在完整性等问题,可反馈申请退款(可完整预览的文档不适用该条件!)。
- 3、如文档侵犯您的权益,请联系客服反馈,我们会尽快为您处理(人工客服工作时间:9:00-18:30)。
贴膜 99.59% 99.90%
2518各工序验证良率目标
镭雕
周转
CNC
99.80% 100.00%
97.95%
99.90% 100.00%
99.30%
出货检 99.79% 99.50%
直通率 96.20% 98.56%
良率要求 98.5
工序名 来料检
贴膜 镭雕 周转 CNC 出货检 直通率
目标值 99.95% 99.90% 99.90% 100.00% 99.30% 99.50% 98.56%
内部品质良率达成改善检 讨会
P 计划
1.主题选定 2.活动计划 3.现况把握 4.目标制订
D 实施
5.原因分析 6.对策分析 7.对策实施
C 检查
8.效果确认
A 改进
9.标准化 10.总结
Page 7
P
A
D
C
日期 生产数 不良数 不良率
8/1 2550
55 2.16%
1.主题选定(P)
8/2 2550
Page 5
一般常见会议
1.工作例会
一般每周或每两周召开一次。 例会是部门负责人了解其所管 理工作最直接的途径,通过例 会沟通了解工作进展、讨论存 在问题、检查落实情况。
4、每天碰头会:
对于进度要求紧的项目,每一天都会 有新的进展,因此有必要每天开一个 碰头会,相互沟通一下今天的项目进 展、问题、需要的资源等,并要求小 组负责人将碰头会的会议纪要提交给 高层负责人,以便高层监控项目的状
97.95%
99.79% 96.20%
98.5
工序名
不良数 量
侧面压点
不良分类及位置 碰伤 小A面伤 侧面压印
来料检 5
1
3
1
贴膜
2
镭雕
1
2 裸露处碰
伤 1
周转 CNC
10
正面压伤
裸露处碰 伤
反面倒角
异色
1
7
1
1
出货检 1
1
Page 10
工序 现良率 计划目标
来料检 99.00% 99.95%
4.目标制订/期望的水平(P)
符纯豪/张欢 黄晓杰
制订计划,什么人在什么时间完成什么事!
Page 9
工序 验证数量 不良数量
良率
3.现状把握/数据收集(现在的水平)(P)
来料检 500 5
贴膜 490
2
2518各工序验证良率结果
镭雕
周转
CNC
488
487
487
1
0
10
出货检 477 1
直通率 500 19
良率要求
99.00% 99.59% 99.80% 100.00%
现良率值 99.00% 99.59% 99.80% 100.00% 97.95% 99.79% 96.20%2518目标ຫໍສະໝຸດ 成计划W32W33
99.25%
99.50%
99.65%
99.75%
Page 6
3、阶段总结会:
项目有阶段性进展时,需要组织一次 总结会,总结经验、成绩以及问题。 根据里程碑的意义,可以适当地与表 彰(检讨)结合起来开。预见项目推 动有困难时,需要组织一次大型的动
员会,以鼓舞大家的士气。
6、内部改善检讨会
产品在生产加工过程发生的异常需组 织相关人员进行分析改善,可以采用 4M1E分析解决,多问5个为什么,彻底 找了真正的原因,实施有效的对策.
况
2、工作协调会:
工作推进过程中,必定会遇到 各种困难,需要中高层来协调 资源。如果是紧急的项目可以 要求每周组织一次项目协调会; 一般项目可以每个月组织一次 规模较大的协调会,并提前预 约高层参加。
5、设计评审会
一般在项目研制计划中会将 项目进行阶段划分,设定阶 段的里程碑,到了这个时间, 就要针对计划中提到的一些 进度、节点任务完成情况进 行评审,确定本阶段工作是 否可以顺利转入下一阶段。
Page 8
2.计划制订(P)
2518产品不良分析改善计划
项目
W32
8/8 8/9 8/10 8/11 8/12 8/13 8/14
内容
数据收集
验证500PCS产品,每工序全检实际良率,并统计各项发生不良 项目及不良位置
负责人 符纯豪
目标设定
每工序根据实际产生不良率设定各工序目标达成
王运功
原因分析 对策分析 对策实施
会议组织与策划 主讲品质改善会议案例(虚拟)
北京精雕东莞精雕机械科技有限公司 品质部:王运功 2016.08.06
Page 1
会议会遇到以下情况:
• 会议开完了,大家各奔东西,没有人整理会议纪要,达成的意见没 有记录;
• 会议失去控制,跑题严重,会议的时间太长,在会议过程中废话太 多;
• 会议开完了,发现没有开会的必要,可开可不开; • 会议讨论了很多问题,但是会后大家却不知道究竟要完成哪些工作; • 会议的决策落实到了具体的部门或人员去执行,但是执行的结果如
负责人根据发生不良分析根本原因 各工序负责人根据发生不良原因制订相应的对策 各工序负责人执行制订的对策,需注意有无反效果
张欢/毛泽永/王 运功
张欢/毛泽永/王 运功
张欢/毛泽永/王 运功
效果验验
品质部对实施的对策连续跟踪三天结果,并对改善前后的效果 进行比较。
符纯豪
备注
标准化 总结
制定标准化,防止不良再发生并维持效果 进行全期改善活动管理循环(PDCA)检讨
发言人
组织者
参与人
Page 4
会议与PDCA:
• 每个组织都有丰富的会议经验,甚至天天在开会,但是很多会 议都是“会而不议、议而不决、决而不行、行而不果”,徒然 浪费大家的时间。
• PDCA(Plan Do Check Action)循环是由美国统计学家戴明提 出的,戴明先生是美国著名的质量控制专家之一。PDCA就是 策划、实施、检查和改进,这个循环是现代质量管理体系最核 心的理论,应用到质量体系涉及的各个过程,形成了现代质量 管理体系。PDCA循环除了在质量管理中广泛应用外,目前已 经成为管理学中非常重要的工具。
65 2.55%
8/3 2550 50 1.96%
8/4 2550 48 1.88%
8/5 2550 62 2.43%
8/6 2550
59 2.31%
8/7 2550 56 2.20%
合计 损耗标准
17850 395 2.21%
1.5%
新投入量产的2518产品最近一周每天超出 规定损耗,且未出现有不良降低的现象
何却没有人关注; • 会议开始的时间到了,投影仪无法正确连接;
• 与“会人为员更迟到好,会的议组推迟织;会议做 • 在开会过好程中准人进备人!出,!会”议混乱; “有备无患!!”
Page 2
问题:
1、我们平时主要组织哪些会议? 2、我们组织会议的目的是什么?
Page 3
会议中,谁最重要?
主持人