尺寸精度与表面粗糙度
各种加工方法的经济精度和表面粗糙度

各种加工方法能够达到的尺寸的经济精度表1 孔加工的经济精度表2 圆锥形孔加工的经济精度表3 圆柱形深孔加工的经济精度表4 花键孔加工的经济精度表5 外圆柱表面加工的经济精度表6 端面加工的经济精度(mm)表7 用成形铣刀加工的经济精度(mm)注:指加工表面至基准的尺寸精度。
表8 同时加工平行表面的经刘精度(mm)注:指两平行表面距离的尺寸精度。
表9 平面加工的经济精度注:1 表内资料适用于尺寸<1m,结构刚性好的零件加工,用光洁的加工表面作为定位和测量基准。
2 端铣刀铣削的加工精度在相同的条件下大体上比圆柱铣刀铣削高一级。
3 细铣仅用于端铣刀铣削。
表10 公制螺纹加工的经济精度表11 花键加工的经济精度表12 齿形加工的经济精度各种加工方法能够达到的形状的经济精度表13 平面度和直线度的经济精度表14 圆柱形表面形状精度的经济精度注:形状精度等级的公差值见附表2、3。
表15 曲面加工的经济精度表16 在各种机床上加工时形状的平均经济精度各种加工方法所能够达到的相互位置的经济精度表17 平行度的经济精度表18 端面跳动和垂直度的经济精度表19 同轴度的经济精度表20 轴心线相互平行的孔的位置经济精度注:对于钻、卧镗及组合机床的镗孔偏差同样适用于铰孔。
表21 轴心线相互垂直的孔的位置经济精度注:在镗空间的垂直孔时,中心距误差可按上式相应的找正方法选用。
各种加工方法能够达到的零件表面粗糙度表22 各种加工方法能够达到的零件表面粗糙度各类型面的加工方案及经济精度表23 外圆表面加工方案表24 孔加工方案表25 平面加工方案——机械篇标准公差及形位公差附表1 标准公差值注:基本尺寸小于1mm时,无IT14至IT18。
13 22-4-25 10:32附表2 平面度、直线度公差值附表3 圆度、圆柱度公差值附表4 平行度、垂直度、倾斜度公差值附表5 同轴度、对称度、圆跳动、全跳动公差值参考文献1 《金属机械加工工艺人员手册》修订本上海科学技术出版社1981年2 《机械制造工艺学》顾崇衔等编著陕西科学技术出版社1982年3 《航空机械设计手册》第三机械工业部612所编1979年4 《机械制造工艺学课程设计简明手册》华中工学院机械制造工艺教研室编1981年5 《机械工程手册》第46篇机械工业出版社1981年6 《圆柱齿轮加工》上海科学技术出版社1979年切削用量切削用量的选择原则正确地选择切削用量,对提高切削效率,保证必要的刀具耐用度和经济性,保证加工质量,具有重要的作用。
零件精度等级与公差等级的区别

零件精度等级与公差等级的区别一、引言零件的精度和公差是制造过程中非常重要的概念,对于产品的质量和性能有着直接的影响。
在实际的制造过程中,精度等级和公差等级是两个不可或缺的概念,它们共同决定了零件的加工精度和使用要求。
本文将从深度和广度的角度对零件精度等级与公差等级进行全面评估,并探讨它们之间的区别与联系。
二、零件精度等级的概念1.精度等级是指零件在加工过程中所能达到的精度水平,通常包括了形位精度、尺寸精度和表面粗糙度等方面。
精度等级越高,零件的加工精度就越高,相应的成本和加工难度也会增加。
2.在实际生产中,零件的精度等级通常会通过标准规范或技术要求来确定,不同的零件类型和用途会有不同的精度等级要求。
对于高精度要求的零件,通常需要进行精密加工和检测,以确保其精度符合要求。
3. 总结与回顾:零件精度等级是决定零件加工精度水平的重要依据,不同的零件类型和用途会有不同的精度等级要求,对于高精度要求的零件,通常需要进行精密加工和检测。
三、公差等级的概念1.公差是指零件在设计和加工过程中允许的尺寸偏差范围,用来表示零件的尺寸变化范围。
公差等级包括了最大材料条件和最小材料条件,其目的是为了确保零件在装配和使用过程中能够满足相关要求。
2.在实际的设计和制造中,公差等级通常会根据零件的功能和使用要求来确定,不同的零件类型和应用场景会有不同的公差等级标准。
对于高精度要求的零件,通常会有更严格的公差要求,以确保零件在装配和使用过程中能够保持稳定性和精度。
3. 总结与回顾:公差等级是零件在设计和加工过程中允许的尺寸偏差范围,不同的零件类型和应用场景会有不同的公差等级标准,对于高精度要求的零件,通常会有更严格的公差要求。
四、零件精度等级与公差等级的区别与联系1. 区别:精度等级和公差等级在概念上有着明显的不同,精度等级主要关注零件加工过程中实际达到的精度水平,而公差等级则主要关注零件尺寸偏差范围的许可。
精度等级是对零件精度要求的一种表述,而公差等级则是对零件尺寸偏差的一种规定。
表面粗糙度和尺寸公差等级IT

表面粗糙度表面粗糙度R a值的应用范围注:1. 粗糙度代号I为第一种过渡方式。
它是取新国标中相应最靠近的下一档的第1系列值,如原光洁度(旧国标)为▽5,R a的最大允许值取6.3。
因此,在不影响原表面粗糙要求的情况下,取该值有利于加工。
2. 粗糙度代号Ⅱ为第2种过渡方式。
它是取新国标中相应最靠近的上一档的第1系列值,如原光洁度为▽5,R a的最大允许值取3.2。
因此,取该值提高了原表面粗糙度的要求和加工的成本。
尺寸公差等级(IT)公差(1)公差基本术语的含义1)基本尺寸;设计时给定的尺寸,称为基本尺寸。
的基本尺寸2)实际尺寸:零件加工后经测量所得到的尺寸,称为实际尺寸。
3)极限尺寸:实际尺寸允许变化的两个界限值称为极限尺寸。
它以基本尺寸确定。
两个极限值中较大的一个称为最大极限尺寸Dmax(或dmax);较小的一个称为极限尺寸Dmin(或dmin)。
)尺寸偏差;某一尺寸减其基本尺寸所得的代数差,称为尺寸偏差,简称偏差。
实际偏差=实际尺寸一基本尺寸最大极限尺寸减其基本尺寸所得的代数差,称为上偏差;最小极限尺寸减其基本尺寸所得的代数差,称为下偏差;上偏差和下偏差统称为极限偏差。
国家标准规定,孔的上偏差代号为ES,轴的上偏差代号为es;孔的下偏差代号为EI,轴的下偏差代号为ei,则:ES=孔的最大极限尺-孔的基本尺寸cs=轴的最大极限尺寸-轴的基本尺寸EI=孔的最小极限尺寸-孔的基本尺寸ei=轴的最小极限尺寸-轴的奥基本尺寸偏差值可以为正、负或零值。
5)尺寸公差,允许尺寸的变动量称为尺寸公差,简称公差。
公差等于最大极限尺寸与最小极限尺寸的代数差的绝对值;或等于上偏差与下偏差代数差的绝对值。
6)零线:图1a中示意表明了基本尺寸相向、相互配合的孔与轴之间极限尺寸、尺寸偏差与尺寸公差之间的相互关系,为方便起见,在实际讨论的过程中,通常只画出放大了的孔和轴的公差带,称为公差与配合图解,简称公差带图,如阁l-b所示。
谈表面粗糙度与尺寸公差及形位公差间的协调关系
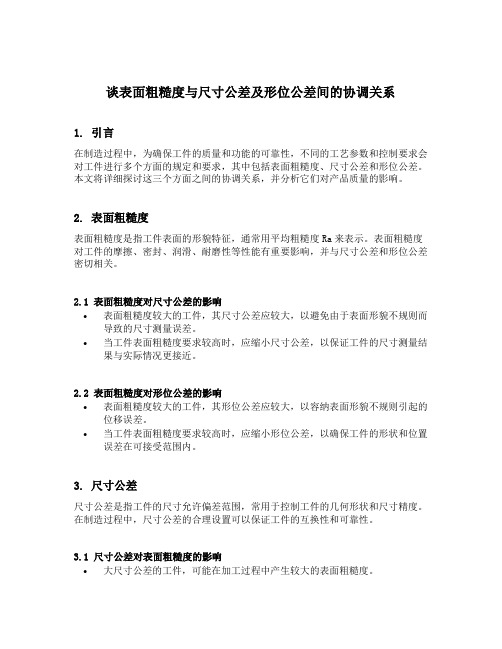
谈表面粗糙度与尺寸公差及形位公差间的协调关系1. 引言在制造过程中,为确保工件的质量和功能的可靠性,不同的工艺参数和控制要求会对工件进行多个方面的规定和要求,其中包括表面粗糙度、尺寸公差和形位公差。
本文将详细探讨这三个方面之间的协调关系,并分析它们对产品质量的影响。
2. 表面粗糙度表面粗糙度是指工件表面的形貌特征,通常用平均粗糙度Ra来表示。
表面粗糙度对工件的摩擦、密封、润滑、耐磨性等性能有重要影响,并与尺寸公差和形位公差密切相关。
2.1 表面粗糙度对尺寸公差的影响•表面粗糙度较大的工件,其尺寸公差应较大,以避免由于表面形貌不规则而导致的尺寸测量误差。
•当工件表面粗糙度要求较高时,应缩小尺寸公差,以保证工件的尺寸测量结果与实际情况更接近。
2.2 表面粗糙度对形位公差的影响•表面粗糙度较大的工件,其形位公差应较大,以容纳表面形貌不规则引起的位移误差。
•当工件表面粗糙度要求较高时,应缩小形位公差,以确保工件的形状和位置误差在可接受范围内。
3. 尺寸公差尺寸公差是指工件的尺寸允许偏差范围,常用于控制工件的几何形状和尺寸精度。
在制造过程中,尺寸公差的合理设置可以保证工件的互换性和可靠性。
3.1 尺寸公差对表面粗糙度的影响•大尺寸公差的工件,可能在加工过程中产生较大的表面粗糙度。
•当工件表面粗糙度要求较高时,应缩小尺寸公差,以减少加工过程中对表面质量的影响。
3.2 尺寸公差对形位公差的影响•大尺寸公差的工件,其形位公差应较大,以容纳加工误差和装配误差。
•当工件形位精度要求较高时,应缩小尺寸公差,以确保工件的形状和位置误差在可接受范围内。
4. 形位公差形位公差是指工件的形状和位置要求,用于描述工件的几何关系。
形位公差的合理设置可以确保工件在装配过程中满足设计要求,并保证产品的性能和可靠性。
4.1 形位公差对表面粗糙度的影响•较大的形位公差要求可能导致工件表面粗糙度的增加。
•当工件表面粗糙度要求较高时,应缩小形位公差,以减少对表面质量的影响。
尺寸公差、形位公差、表面粗糙度三者的关系
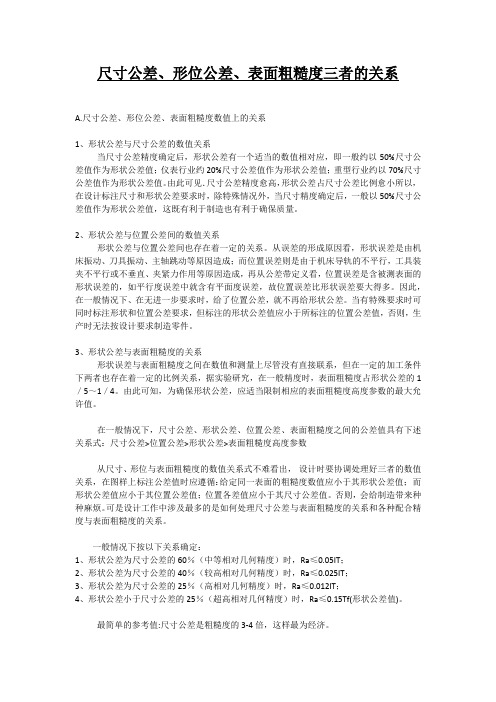
尺寸公差、形位公差、表面粗糙度三者的关系A.尺寸公差、形位公差、表面粗糙度数值上的关系1、形状公差与尺寸公差的数值关系当尺寸公差精度确定后,形状公差有一个适当的数值相对应,即一般约以50%尺寸公差值作为形状公差值;仪表行业约20%尺寸公差值作为形状公差值;重型行业约以70%尺寸公差值作为形状公差值。
由此可见.尺寸公差精度愈高,形状公差占尺寸公差比例愈小所以,在设计标注尺寸和形状公差要求时,除特殊情况外,当尺寸精度确定后,一般以50%尺寸公差值作为形状公差值,这既有利于制造也有利于确保质量。
2、形状公差与位置公差间的数值关系形状公差与位置公差间也存在着一定的关系。
从误差的形成原因看,形状误差是由机床振动、刀具振动、主轴跳动等原因造成;而位置误差则是由于机床导轨的不平行,工具装夹不平行或不垂直、夹紧力作用等原因造成,再从公差带定义看,位置误差是含被测表面的形状误差的,如平行度误差中就含有平面度误差,故位置误差比形状误差要大得多。
因此,在一般情况下、在无进一步要求时,给了位置公差,就不再给形状公差。
当有特殊要求时可同时标注形状和位置公差要求,但标注的形状公差值应小于所标注的位置公差值,否则,生产时无法按设计要求制造零件。
3、形状公差与表面粗糙度的关系形状误差与表面粗糙度之间在数值和测量上尽管没有直接联系,但在一定的加工条件下两者也存在着一定的比例关系,据实验研究,在一般精度时,表面粗糙度占形状公差的1/5~1/4。
由此可知,为确保形状公差,应适当限制相应的表面粗糙度高度参数的最大允许值。
在一般情况下,尺寸公差、形状公差、位置公差、表面粗糙度之间的公差值具有下述关系式:尺寸公差>位置公差>形状公差>表面粗糙度高度参数从尺寸、形位与表面粗糙度的数值关系式不难看出,设计时要协调处理好三者的数值关系,在图样上标注公差值时应遵循:给定同一表面的粗糙度数值应小于其形状公差值;而形状公差值应小于其位置公差值;位置各差值应小于其尺寸公差值。
尺寸公差形位公差、表面粗糙度数值上的关系
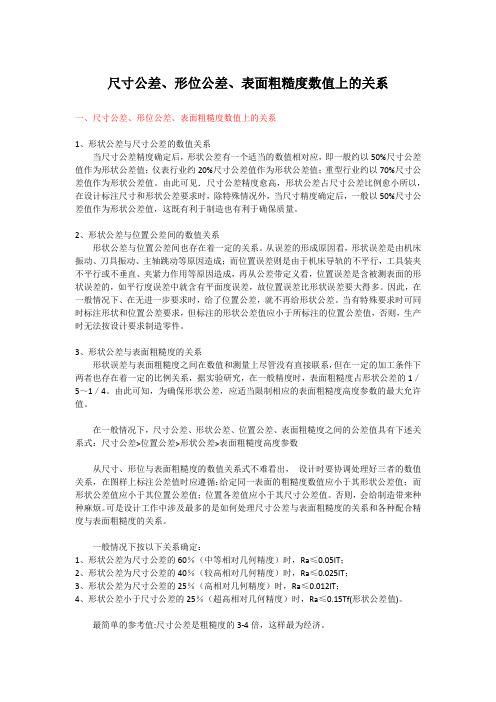
尺寸公差、形位公差、表面粗糙度数值上的关系一、尺寸公差、形位公差、表面粗糙度数值上的关系1、形状公差与尺寸公差的数值关系当尺寸公差精度确定后,形状公差有一个适当的数值相对应,即一般约以50%尺寸公差值作为形状公差值;仪表行业约20%尺寸公差值作为形状公差值;重型行业约以70%尺寸公差值作为形状公差值。
由此可见.尺寸公差精度愈高,形状公差占尺寸公差比例愈小所以,在设计标注尺寸和形状公差要求时,除特殊情况外,当尺寸精度确定后,一般以50%尺寸公差值作为形状公差值,这既有利于制造也有利于确保质量。
2、形状公差与位置公差间的数值关系形状公差与位置公差间也存在着一定的关系。
从误差的形成原因看,形状误差是由机床振动、刀具振动、主轴跳动等原因造成;而位置误差则是由于机床导轨的不平行,工具装夹不平行或不垂直、夹紧力作用等原因造成,再从公差带定义看,位置误差是含被测表面的形状误差的,如平行度误差中就含有平面度误差,故位置误差比形状误差要大得多。
因此,在一般情况下、在无进一步要求时,给了位置公差,就不再给形状公差。
当有特殊要求时可同时标注形状和位置公差要求,但标注的形状公差值应小于所标注的位置公差值,否则,生产时无法按设计要求制造零件。
3、形状公差与表面粗糙度的关系形状误差与表面粗糙度之间在数值和测量上尽管没有直接联系,但在一定的加工条件下两者也存在着一定的比例关系,据实验研究,在一般精度时,表面粗糙度占形状公差的1/5~1/4。
由此可知,为确保形状公差,应适当限制相应的表面粗糙度高度参数的最大允许值。
在一般情况下,尺寸公差、形状公差、位置公差、表面粗糙度之间的公差值具有下述关系式:尺寸公差>位置公差>形状公差>表面粗糙度高度参数从尺寸、形位与表面粗糙度的数值关系式不难看出,设计时要协调处理好三者的数值关系,在图样上标注公差值时应遵循:给定同一表面的粗糙度数值应小于其形状公差值;而形状公差值应小于其位置公差值;位置各差值应小于其尺寸公差值。
车削工艺的大致精度

车削工艺的大致精度车削工艺是一种通过旋转刀具和工件相对运动来削除工件上的材料的加工方法。
它是金属加工中最常用的一种工艺,可以用于加工各种金属材料,包括铸件、锻件和焊接件等。
车削工艺的主要目的是在工件上获得所需的几何形状和尺寸,以及精确的表面质量。
车削工艺的大致精度是指加工后工件与设计尺寸之间的偏差。
车削精度通常可以通过以下几个方面来衡量:1. 尺寸精度:指工件加工后的尺寸与设计尺寸之间的偏差。
尺寸精度主要取决于机床的精度、刀具的刚性和刀具的磨损情况等因素。
一般来说,车削加工可以达到较高的尺寸精度,通常在0.01mm到0.05mm之间。
2. 圆度精度:指加工后圆形工件的圆形度偏差。
圆度精度主要取决于刀具和工件的运动精度、机床的刚性和刀具磨损等因素。
通常情况下,车削工艺可以达到较高的圆度精度,一般在0.01mm到0.02mm之间。
3. 其他形状精度:除了尺寸和圆度之外,车削工艺还可以获得其他形状的精度,如平面度、垂直度和倾斜度等。
这些形状精度主要取决于机床和刀具的精度。
4. 表面粗糙度:指加工后工件表面的粗糙程度。
表面粗糙度主要取决于切削刃的几何形状、切削速度和进给速度等因素。
通常情况下,车削工艺可以获得较小的表面粗糙度,一般在Ra 0.8um到Ra 3.2um之间。
车削工艺的精度可以通过以下几个方面来提高:1. 选择适当的工艺参数:选择合适的切削速度、进给速度和切削深度等工艺参数可以有效地提高车削工艺的精度。
合理的工艺参数可以保证切削过程的稳定性和刀具寿命的长久性,从而提高工件的加工精度。
2. 使用高精密机床和工具:高精密机床和工具可以提供更高的加工精度和刚性。
选择高精密机床和工具可以有效地改善车削工艺的精度。
3. 使用先进的切削刃材料:选择合适的切削刃材料可以降低刀具磨损和断裂的风险,提高车削工艺的精度。
4. 加强工艺控制和检测:加强车削工艺的控制和检测可以及时发现和纠正加工中的问题,提高工件的加工精度。
表面粗糙度和尺寸公差等级IT
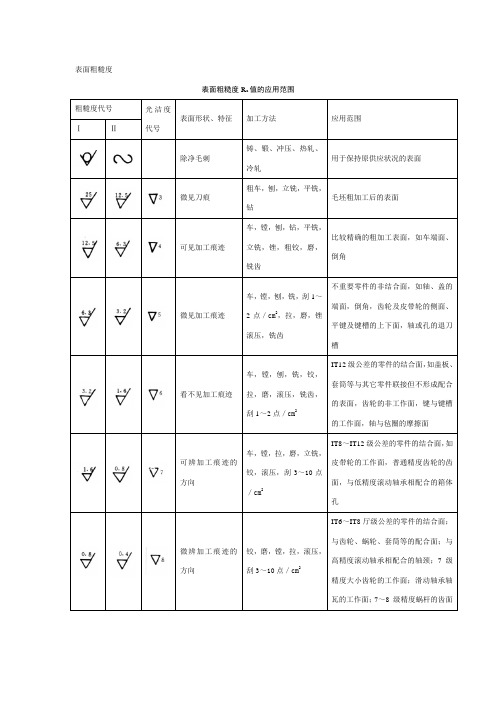
表面粗糙度表面粗糙度R a值的应用范围注:1. 粗糙度代号I为第一种过渡方式。
它是取新国标中相应最靠近的下一档的第1系列值,如原光洁度(旧国标)为▽5,R a的最大允许值取6.3。
因此,在不影响原表面粗糙要求的情况下,取该值有利于加工。
2. 粗糙度代号Ⅱ为第2种过渡方式。
它是取新国标中相应最靠近的上一档的第1系列值,如原光洁度为▽5,R a的最大允许值取3.2。
因此,取该值提高了原表面粗糙度的要求和加工的成本。
尺寸公差等级(IT)公差(1)公差基本术语的含义1)基本尺寸;设计时给定的尺寸,称为基本尺寸。
的基本尺寸2)实际尺寸:零件加工后经测量所得到的尺寸,称为实际尺寸。
3)极限尺寸:实际尺寸允许变化的两个界限值称为极限尺寸。
它以基本尺寸确定。
两个极限值中较大的一个称为最大极限尺寸Dmax(或dmax);较小的一个称为极限尺寸Dmin(或dmin)。
)尺寸偏差;某一尺寸减其基本尺寸所得的代数差,称为尺寸偏差,简称偏差。
实际偏差=实际尺寸一基本尺寸最大极限尺寸减其基本尺寸所得的代数差,称为上偏差;最小极限尺寸减其基本尺寸所得的代数差,称为下偏差;上偏差和下偏差统称为极限偏差。
国家标准规定,孔的上偏差代号为ES,轴的上偏差代号为es;孔的下偏差代号为EI,轴的下偏差代号为ei,则:ES=孔的最大极限尺-孔的基本尺寸cs=轴的最大极限尺寸-轴的基本尺寸EI=孔的最小极限尺寸-孔的基本尺寸ei=轴的最小极限尺寸-轴的奥基本尺寸偏差值可以为正、负或零值。
5)尺寸公差,允许尺寸的变动量称为尺寸公差,简称公差。
公差等于最大极限尺寸与最小极限尺寸的代数差的绝对值;或等于上偏差与下偏差代数差的绝对值。
6)零线:图1a中示意表明了基本尺寸相向、相互配合的孔与轴之间极限尺寸、尺寸偏差与尺寸公差之间的相互关系,为方便起见,在实际讨论的过程中,通常只画出放大了的孔和轴的公差带,称为公差与配合图解,简称公差带图,如阁l-b所示。
尺寸公差配合与表面粗糙度分析

F7 G 7 H 7 JS 7 K 7 M 7 N 7 P 7 R 7 S 7 6 h 6 h 6 h 6 h 6 h 7 h 7 h 6
E8 F 8
H8 JS 8 K 8 M 8 N 8
h7
h7 h 7
h7 h 7 h 7 h 7 h 7
E8 F8
例1
查表写出φ18
H f
78的极限偏差数值。
解:
从配合表可知,Hf
8 7
是基孔制的优先配合,其中H8是基
准孔的公差代号;f7是配合轴的公差代号。
(1)φ18H8基准孔的极限偏差,可由附录附表中查出。在
表中由基本尺寸从大于14至18的行和公差带H8的列相交处
查得 +0.027 0
这就是基准孔的上、下偏差,所以 φ18H8
H 6 H 7 H 7 H7 H7 H7 H7 H7 H7 H7 H7 H7 H7 H7 H7 H7
f 6 g 6 h 6 Js6 k6 m6 n6 p6 r6 s6 t6 u6 v6 x6 y6 z6 H 8 H 8 H 8 H 8 H8 H8 H8 H8 H8 H8 H8 H8 H8
e 7 f 7 g 7 h 8 Js7 k7 m7 n7 p7 r7 s7 t7 u7
• 实际偏差:实际尺寸减基本尺寸的代数差。 • 极限偏差:极限尺寸减去基本尺寸。极限偏差又分上偏差
(ES、es)和下偏差(EI、ei)。 ES=Dmax-D es=dmax-d EI=Dmin-D ei=dmin-d • 公差:允许尺寸的变动量。等于最大极限尺寸与最小极限 尺寸之代数差的绝对值。孔、轴的公差分别用Th和Ts表示。 Th=︱ Dmax- Dmin ︱= ︱ ES-EI︱ Ts=︱ dmax- dmin ︱= ︱ es-ei︱
尺寸公差与表面粗糙度

05 总结与展望
总结
尺寸公差与表面粗糙度是机械加工中的重要参数,它 们对产品的性能和可靠性有着显著的影响。
随着科技的不断发展,对尺寸公差与表面粗糙度的要 求也越来越高,这需要我们不断探索新的加工方法和
测量技术,以提高产品的质量和性能。
在实际应用中,应综合考虑尺寸公差与表面粗糙度的 关系,以及它们对产品性能的影响,以制定合理的加
工和测量方案。
展望
随着数字化和智能化技术的不断发展,未来的机械加工将更加依赖于先进的测量技术和数据分析方法。
新的加工方法和材料将对尺寸公差与表面粗糙度提出更高的要求,需要我们不断探索和创新,以适应新 的市场需求。
在未来,尺寸公差与表面粗糙度的研究将更加注重跨学科的合作和交流,以推动相关领域的发展和进步。
测量精度
测量精度对结果的影响很大,因此需要选择精度 合适的测量工具和正确的测量方法,以获得准确 的测量结果。
03 尺寸公差与表面粗糙度的 控制方法
加工工艺控制
加工方法选择
根据零件材料、结构、精度要求等选择合适的加工方 法,如车削、铣削、磨削等。
加工余量分配
合理分配各工序的加工余量,确保最终加工尺寸的精 度。
02
表面粗糙度越高,摩擦系数越大,磨损速度越快,从而影响零
件的耐磨性。
表面粗糙度对零件疲劳强度的影响
03
表面粗糙度越高,应力集中越严重,疲劳裂纹容易形成和扩展,
降低零件的疲劳强度。
尺寸公差对表面粗糙度的影响
尺寸公差越小,表面粗糙度越低
在加工过程中,尺寸公差越小,切削深度、进给量等工艺参数越小,从而减小 表面粗糙度。
热处理工艺
控制零件的热处理工艺,以减小变形和组织不均匀性 对尺寸精度的影响。
尺寸公差,形状公差与表面粗糙度的关系
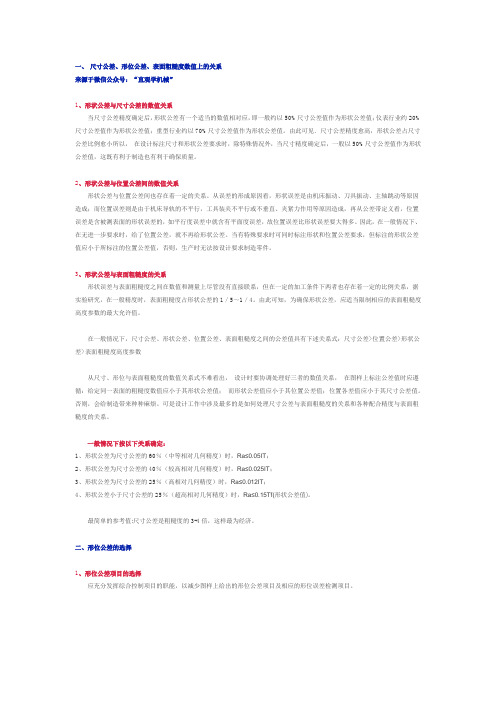
一、尺寸公差、形位公差、表面粗糙度数值上的关系来源于微信公众号:“直观学机械”1、形状公差与尺寸公差的数值关系当尺寸公差精度确定后,形状公差有一个适当的数值相对应,即一般约以50%尺寸公差值作为形状公差值;仪表行业约20%尺寸公差值作为形状公差值;重型行业约以70%尺寸公差值作为形状公差值。
由此可见.尺寸公差精度愈高,形状公差占尺寸公差比例愈小所以,在设计标注尺寸和形状公差要求时,除特殊情况外,当尺寸精度确定后,一般以50%尺寸公差值作为形状公差值,这既有利于制造也有利于确保质量。
2、形状公差与位置公差间的数值关系形状公差与位置公差间也存在着一定的关系。
从误差的形成原因看,形状误差是由机床振动、刀具振动、主轴跳动等原因造成;而位置误差则是由于机床导轨的不平行,工具装夹不平行或不垂直、夹紧力作用等原因造成,再从公差带定义看,位置误差是含被测表面的形状误差的,如平行度误差中就含有平面度误差,故位置误差比形状误差要大得多。
因此,在一般情况下、在无进一步要求时,给了位置公差,就不再给形状公差。
当有特殊要求时可同时标注形状和位置公差要求,但标注的形状公差值应小于所标注的位置公差值,否则,生产时无法按设计要求制造零件。
3、形状公差与表面粗糙度的关系形状误差与表面粗糙度之间在数值和测量上尽管没有直接联系,但在一定的加工条件下两者也存在着一定的比例关系,据实验研究,在一般精度时,表面粗糙度占形状公差的1/5~1/4。
由此可知,为确保形状公差,应适当限制相应的表面粗糙度高度参数的最大允许值。
在一般情况下,尺寸公差、形状公差、位置公差、表面粗糙度之间的公差值具有下述关系式:尺寸公差>位置公差>形状公差>表面粗糙度高度参数从尺寸、形位与表面粗糙度的数值关系式不难看出,设计时要协调处理好三者的数值关系,在图样上标注公差值时应遵循:给定同一表面的粗糙度数值应小于其形状公差值;而形状公差值应小于其位置公差值;位置各差值应小于其尺寸公差值。
不同的加工方法可能达到的尺寸精度及表面粗糙度
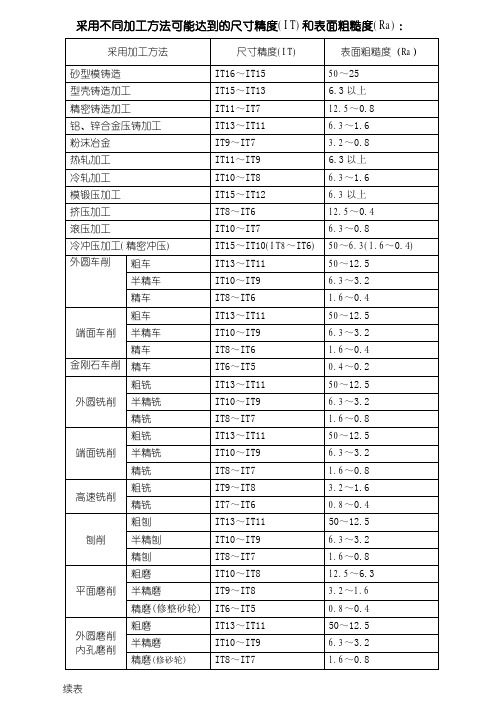
2.基本尺寸小于或等于 1mm 时无 IT14 至 IT18。
0.4~0.2
6.3~0.4
0.05~0.01 0.8~0.2 3.2~0.4 6.3~0.05 0.4~0.2 0.8~0.4 0.8~0.05 0.8~0.4 0.4~0.2 0.4~0.2 0.2~0.1
机械切削加工尺寸未注公差(單位:mm)
公称尺寸
f-精密级
0.5~3
±0.05
>3 ~6
±0.05
50~12.5 25~6.3 50~12.5 6.3~3.2 3.2~1.6 0.8~0.4 25~12.5 6.3~3.2 1.6~0.8 0.8~0.2 12.5~25 6.3~1.6 1.6~0.8 0.8~0.4 0.8~0.1 50~0.8 50~12.5
IT8~IT7 IT10~IT8 IT9~IT8
切削加工:粗加工:IT13~IT11 Ra:50~12.5 ; 半精加工:IT10~IT8 Ra:6.3~1.6 ; 精加工:IT7~IT5 Ra:0.8~0.2 ; 精密加工:IT5 以下 Ra:0.1~0.025 ; 超精加工:IT3 以下 Ra:0.025 以下的最光面.
1.粗糙面(如 Ra:50、25、12.5)的粗加工公差等级:T13~IT11,如粗车、粗铣、粗刨、 粗镗、毛锉、锯断、钻孔、倒角等,适用于没有配合要求的自由面; 2.半光面(如 Ra:6.3、3.2、1.6)的半精加工公差等级:IT10~IT8,如半精车、半精铣、半精镗、 粗磨、扩孔等,适用于接触面、不甚精确定心的配合面; 3.光面(如 Ra:0.8、0.4、0.2)的精加工公差等级:IT7~IT5,如精车、精拉、精铰、精铣、 精磨、座标磨、研磨、抛光等,适用于要求精确定心的重要配合面; 4.最光面(如 Ra:0.1、0.05、0.02)的超精加工公差等级:IT5 以下,如研磨、珩磨、超精磨、抛光、 镜面磨等,适用于高精度、高速运动的零部件的配合表、较重要的装饰面,如镜面模仁等;
各种加工方法的经济精度和表面粗糙度
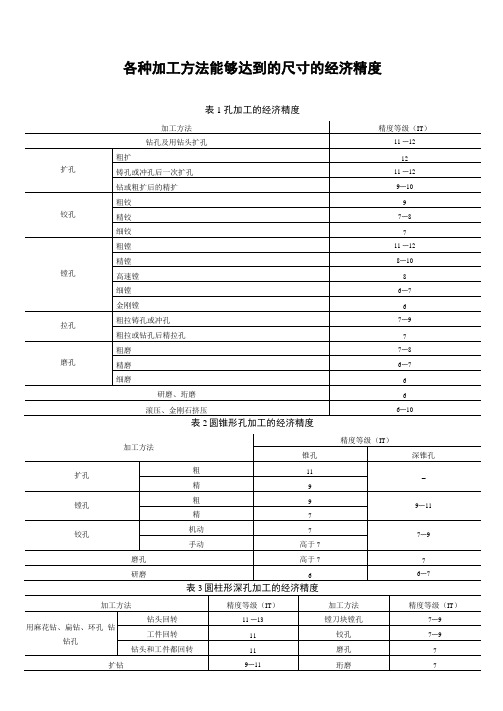
各种加工方法能够达到的尺寸的经济精度表1 孔加工的经济精度表2圆锥形孔加工的经济精度表3圆柱形深孔加工的经济精度6mm7mm91<1m2端铣刀铣削的加工精度在相同的条件下大体上比圆柱铣刀铣削高一级。
3细铣仅用于端铣刀铣削。
11各种加工方法能够达到的形状的经济精度2315各种加工方法所能够达到的相互位置的经济精度表19同轴度的经济精度表20 轴心线相互平行的孔的位置经济精度注:对于钻、卧镗及组合机床的镗孔偏差同样适用于铰孔。
表21轴心线相互垂直的孔的位置经济精度各种加工方法能够达到的零件表面粗糙度表22 各种加工方法能够达到的零件表面粗糙度各类型面的加工方案及经济精度表23外圆表面加工方案标准公差及形位公差附表1标准公差值1mm IT14IT1813 22-2-21 16:331 《金属机械加工工艺人员手册》修订本上海科学技术出版社1981年2 《机械制造工艺学》顾崇衔等编著陕西科学技术出版社1982年3 《航空机械设计手册》第三机械工业部612所编1979年4 《机械制造工艺学课程设计简明手册》华中工学院机械制造工艺教研室编1981年5 《机械工程手册》第46篇机械工业出版社1981年6 《圆柱齿轮加工》上海科学技术出版社1979年切削用量切削用量的选择原则正确地选择切削用量,对提高切削效率,保证必要的刀具耐用度和经济性,保证加工质量,具有重要的作用。
1粗加工切削用量的选择原则:粗加工时加工精度与表面求不高,毛坯余量较大。
因此,选择粗加工的切削用量时,要尽可能保证较高的单位时间金属切除量(金属切除率)和必要的刀具耐用度,以提高生产效率和降低加工成本。
金属切除率可以用下式计算:Z k vfa X1000式中Zw——单位时间内的金属切除量(mm3/s);v --- 切削速度(m/s);f --- 进给量(mm/r);a p -------- 切削深度(mm)。
提高切削速度、增大进给量和切削深度,都能提高金属切除率。
GBT1804未注尺寸公差、未注形位公差及表面粗糙度

未注尺寸公差、未注形位公差及表面粗糙度一、未注尺寸公差按GB/T1804(1)线性尺寸的极限偏差数值(GB/T1804-2000)(mm)公差等级尺寸分段0.5~3>3~6>6~30>30~120>120~400>400~1000>1000~2000>2000~4000f(精密级)±0.05±0.05±0.1±0.15±0.2±0.3±0.5-m(中等级)±0.1±0.1±0.2±0.3±0.5±0.8±1.2±2 c(粗糙级)±0.2±0.3±0.5±0.8±1.2±2±3±4 v(最粗级)-±0.5±1.5±1.5±2.5±4±6±8(2)倒圆半径和倒角高度尺寸的极限偏差(GB/T1804-2000)mm公差等级尺寸分段0.5~3>3~6>6~30>30f(精密级)±0.2±0.5±1±2m(中等级)c(粗糙级)±0.4±1±2±4v(最粗级)注:倒圆半径与倒角高度的含义见GB6403.4(零件倒圆与倒角)(3)角度尺寸的极限偏差数值(GB/T1804-2000)公差等级长度mm≤10>10~50>60~120>120~400>400m(中等级)±1°±30'±20'±20'±5' c(粗糙级)±1°30'±1°±30'±30'±10' v(最粗级)±3°±2°±1°±1°±20'二、未注形位公差按GB/T1184(4)直线度和平面度未注公差值(GB/T1184-1996)(mm)公差等级直线度和平面度基本长度的范围~10>10~30>30~100>100~300>300~1000>1000~3000H0.020.050.10.20.30.4 K0.050.10.20.40.60.8 L0.10.20.40.8 1.2 1.6(5)垂直度未注公差值(GB/T1184-1996)(mm)公差等级垂直度公差短边基本长度的范围~100>100~300>300~1000>1000~3000H0.20.30.40.5 K0.40.60.81 L0.511,52(6)对称度未注公差值(GB/T1184-1996)(mm)公差等级对称度公差基本长度的范围~100>100~300>300~1000>1000~3000H0.5K0.60.81 L0.61 1.52(7)圆跳动的未注公差值(GB/T1184-1996)(mm)公差等级圆跳动一般公差值H0.1K0.2L0.5三、选用原则(1)机械加工未注尺寸公差一般选用“m”级,未注形位公差一般选用“K”级。
精度和表面粗糙度的关系

精度和表面粗糙度的关系
精度和表面粗糙度是两个不同的概念,但它们之间有一定的关系。
精度是指测量结果与真实值之间的差异度量。
在制造过程中,精度通常指的是零件的尺寸精度,即零件的实际尺寸与设计尺寸之间的差异。
表面粗糙度是指表面上的微小不规则度和凸起或凹陷的程度。
通常用Ra或Rz等参数来描述表面粗糙度。
表面粗糙度对于某些应用来说是非常重要的,例如摩擦、密封、润滑等。
在制造过程中,精度和表面粗糙度通常是相互影响的。
例如,为了达到更高的尺寸精度,可能需要更加精细的加工,这可能会增加表面粗糙度。
另一方面,为了得到更好的表面质量,可能需要更加细致的研磨和抛光,这可能会降低尺寸精度。
因此,在制造过程中需要权衡这两个因素,并选择合适的加工方法来满足设计要求。
抛光等级、表面粗糙度对应表

抛光尺寸与粗糙度精度等级对照表
Ra 是在取样长度内轮廓偏距绝对值的算术平均值
Rmax 是在取样长度内最大峰高与最大谷深的高度差
Rmax 和Ra没有直接关系,统计上两者间的关系大概是Rmax = 4Ra
μin是半导体方面的单位与1μm=39。
37μin
倒三角是日本的粗糙度,一个三角是是1。
6μm,两个三角就是3.2μm 国标新旧标准对照:
表面光洁度14级=Ra 0.012
表面光洁度13级=Ra 0.025
表面光洁度12级=Ra 0。
050
表面光洁度11级=Ra 0.1
表面光洁度10级=Ra 0.2
表面光洁度9级=Ra 0。
4
表面光洁度8级=Ra 0。
8
表面光洁度7级=Ra 1。
6
表面光洁度6级=Ra 3。
2
表面光洁度5级=Ra 6。
3
表面光洁度4级=Ra 12。
5
表面光洁度3级=Ra 25
表面光洁度2级=Ra 50
表面光洁度1级=Ra 100
以上表面粗糙度单位均为μm,即微米。
尺寸精度与粗糙度

综合举例
1)尺寸的看法
<Q-1>
观察加工图(图-1)、记有尺寸寸法(φ 20 0)
的尺寸、这些都表示什么? 加工直径在『20mm~ 20.3mm』的范围内 1mm φ 25H7 15 36
+0.1 0
<A-1>
+0.3
宽1mm×45°倒角 1mm 45°
+0.3 0
φ 25H7
φ 20
φ 30
+0.3 0
• 同一零件上,工作表面上的粗糙度值应小非工作表 面上的粗糙度值; • 对于速度越高,单位面积压力越大摩擦面则粗糙度 值应越小; • 承受交变载荷的表面及圆角、沟槽处配合性质要求 稳定可靠时的配合表面公差等级和形位精度要求高 的表面, • 一般是:尺寸公差>形位公差>表面粗糙度Rz
表面粗糙度的测量方法
尺寸公差、形位公差与表面粗 糙度
• 互换性:指相同规格的零、部件具有互相 替换使用的性能 • 公差:允许零件几何参数的变动量(误差) 称为公差。 • 公差是实现互换性的保证 • 标准化是对研究的对象,进行简化、优选 和同一的科学管理过程
机械加工质量
位 置 精 度 机械加工精度:是指零件加工后的实际几何参数与理想几 加 工 精 度 形 状 精 度 何参数相符合的程度。二者间的偏差即为加工误差 . 加工 误差愈大 ;反之则愈高.加工精度包括尺寸 ,加工精度则愈低 表 面 粗 糙 度 精度、形状精度和位置精度。 加工质量 表 面 微 观 几 何 形 状 零件的表面质量是指工件经过切削加工后,表面的粗糙度、 表 面 波 度 变形强化的程度,表层残余应力的性质和大小及金相组织 表 面 质 量 表 面 层 冷 作 硬 化 等。 表 面 层 物 理 机 械 性 能 表面层残余应力 表 面 层 相 变 尺 寸 精 度 机械加工质量包括加工精度和加工表面质量两部分 .
- 1、下载文档前请自行甄别文档内容的完整性,平台不提供额外的编辑、内容补充、找答案等附加服务。
- 2、"仅部分预览"的文档,不可在线预览部分如存在完整性等问题,可反馈申请退款(可完整预览的文档不适用该条件!)。
- 3、如文档侵犯您的权益,请联系客服反馈,我们会尽快为您处理(人工客服工作时间:9:00-18:30)。
3.5.1 影响尺寸精度的因素
塑料制品尺寸误差的产生是诸多因素综合影响的结果,在一般情况下,塑料制品要达到金属制品那样的精度是非常困难的。
从模具设计和制造的角度看,影响塑料制品尺寸精度的N素丰要有以厂五个方面:
(1)模具成型部件的制造误差久o
(2)模县成型部件的表面磨损武。
(3)内塑料收缩率波动所引起的塑料制品的尺寸误差久。
(4)模具活动成型部件的配合间隙变化引起的误差承。
(5)模具成型部件的AVX钽电容安装误差乱。
模具原因使塑料制品产生的误差为以上误差值的总和,即
内于累积误差大,在选择塑料制品的精度等级时府十分慎重,以免给模具制造和工艺操
作带来不必要的困难,因为模具成型部件的制造精度总要高于制品的精度。
制品规定的误差
值A,应大于或等于以亡各项因素带来的累积误差,即
一些资料指出,模具制造误差、出收缩率波动引起的误差以及由磨损等造成的误差各占
塑料制品尺寸误差的l/3。
实际上对十小尺寸的制品,模具制造误差对制品尺寸的影响要大
些,而对于大尺寸的制品,收缩率被动引起的误差则是影响制品尺寸精度的主要阅素。
日
前,我国一些上J‘的经验是,当制品的名义尺寸小十120mm时.模具成型部件的尺小公差
取制nDn尺寸公差的1/4—1/3;当制品的尺小芥120一500mm时,模具成型部件的尺寸公差
取制品J4寸公差的1/9—1/8。
30 5.2 尺寸精度和公差的确定
塑料制品的尺寸精度一般是根据使用要求确定的,但还必须充分考虑超料的性能及成型
工艺的特点,过高的精度要求是不恰当的。
我国十2008年8月颁布了叫T14486—2008 《翅料模塑件尺寸公差》。
该标准将塑什J4寸公差分成7个精度等级,根据塑料收缩特性不
同、对每种塑料建议选取其中的=个等级,即标注尺寸公差的高精度等级、一般精度等级和
术注公差尺寸的低精度等级,按表3—4选取。
其巾高精度和一般精度只差一个精度等级,
而——般精度和低精度相差两个精度等级。
表3—4中高桔度要求较高,一般不予选用。
先按
常用材料模塑件公差等级选用表和塑件使用要求决定理件公差等级(见表3—i)。
当公差等
级决定后即可按公差表(见表3—4)查公差值,表3—4仅列有各种精度不同尺寸的公差数
值,而尤配合关系,其上下偏差应根据使用要求进行分配,例如基孔制的7L可取表中数值冠
以(十)号,基轴制的轴可取表小数值冠以(一)号,小心距尺寸取公差数值之半冠以
(i)号,其余情况的卜下偏差N根据材料特性和配合性质对公差值进行分配。
(ii)3.5.3表面粗粮度的确定
(iii)塑料制品的表面粗糙度,除了在成型时从工艺上尽可能避免冷疤、波纹等疵点外,主要
(iv)内模具的表面粗糙度决定。
塑件表面粗糙度参照〔iB/T14234一1993《塑料件表面粗糙度》
(v)选取,决定于模具成型零件的表面粗糙度,塑件的表面粗糙度一般为1.5一o.2Mm,而模具
(vi)的表凹粗糙度数值要比塑件低1—2级。
为了提高模具成型表团的粗糙度,需要模具工人精
(vii)心地打磨和抛光,致使加工成本昂贵。
冈此,对表面粗糙度的级别要求,应以刚好能满足需
(viii)要为佳。
对透明的塑料制品要求型腔和型芯的表9J粗糙度相同;对于个透明的塑料制品,模
(ix)具型芯的成型表回并不影响制品的外观,其作用仅在于提高制品的脱模性能,钽电容因此在木影响
(x)使用要求的前提下,型芯的表面粗糙度的级别可比型腔的表面粗糙度高l一2级。
(xi)
(xii)
(xiii)
wxq$#。