工序质量控制
工序质量控制
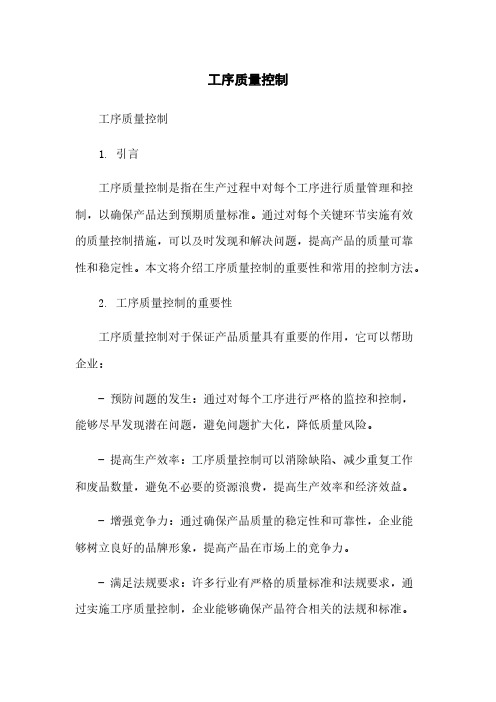
工序质量控制工序质量控制1. 引言工序质量控制是指在生产过程中对每个工序进行质量管理和控制,以确保产品达到预期质量标准。
通过对每个关键环节实施有效的质量控制措施,可以及时发现和解决问题,提高产品的质量可靠性和稳定性。
本文将介绍工序质量控制的重要性和常用的控制方法。
2. 工序质量控制的重要性工序质量控制对于保证产品质量具有重要的作用,它可以帮助企业:- 预防问题的发生:通过对每个工序进行严格的监控和控制,能够尽早发现潜在问题,避免问题扩大化,降低质量风险。
- 提高生产效率:工序质量控制可以消除缺陷、减少重复工作和废品数量,避免不必要的资源浪费,提高生产效率和经济效益。
- 增强竞争力:通过确保产品质量的稳定性和可靠性,企业能够树立良好的品牌形象,提高产品在市场上的竞争力。
- 满足法规要求:许多行业有严格的质量标准和法规要求,通过实施工序质量控制,企业能够确保产品符合相关的法规和标准。
3. 工序质量控制的方法3.1 工艺流程控制工艺流程控制是指通过监控和调整工艺参数,保持工序的稳定性和一致性。
常用的方法包括:- 设定合理的工艺参数范围:确定每个工序的关键参数范围,超出范围的数据需要进行调整或纠正。
- 定期检查和校准设备:确保关键设备的准确性和稳定性,避免设备问题对质量的影响。
- 实施标准化操作程序:为每个工序制定操作指导书或标准作业程序,确保操作人员按照规定的程序进行操作,减少人为操作错误的可能性。
3.2 检验和测试控制检验和测试控制是通过对产品进行检验和测试,对工序质量进行验证和控制。
常用的方法包括:- 抽样检验:根据抽样标准制定合理的抽样方案,对产品进行检验和测试,确保产品的质量符合要求。
- 无损检测:利用无损检测技术对产品进行检测和评估,发现潜在缺陷和问题,并采取相应的措施进行修复。
- 建立完善的测试和分析体系:制定测试和分析计划,对产品进行全面的测试和分析,找出潜在问题的根本原因。
3.3 预防控制预防控制是指通过采取措施预防问题的发生,减少质量风险。
简述工序质量控制的主要内容

简述工序质量控制的主要内容摘要:一、工序质量控制的概念二、工序质量控制的主要内容1.工艺过程控制2.质量检测与评价3.不良品预防与控制4.质量改进与持续优化三、工序质量控制的方法与策略四、工序质量控制的应用与实践五、总结与展望正文:工序质量控制是制造业中至关重要的一环,它主要关注的是在生产过程中如何保证产品质量满足预定标准。
工序质量控制的主要内容可以从以下几个方面进行阐述:一、工序质量控制的概念工序质量控制是指在生产过程中,对各个工序的质量进行监测、评价和调整,以确保最终产品的质量满足要求。
工序质量控制是质量控制体系的重要组成部分,它强调预防性原则,通过对生产过程的实时监控,及时发现并解决问题。
二、工序质量控制的主要内容1.工艺过程控制:工艺过程控制是工序质量控制的基础,它关注的是生产过程中各个工序的执行情况。
通过对工艺参数、操作方法等进行严格控制,确保产品质量的稳定性。
2.质量检测与评价:质量检测是工序质量控制的关键环节,通过对产品进行定期的检测,评价产品质量是否满足标准要求。
检测结果可用于评价生产过程的质量状况,为不良品预防提供依据。
3.不良品预防与控制:不良品预防与控制是工序质量控制的核心内容。
通过对生产过程中可能出现的不良品进行预测和分析,制定相应的预防措施,降低不良品产生的风险。
4.质量改进与持续优化:质量改进是工序质量控制的目标。
通过对生产过程的不断优化,提高产品质量,降低生产成本,实现企业的可持续发展。
三、工序质量控制的方法与策略工序质量控制的方法与策略包括:统计过程控制(SPC)、全面生产维护(TPM)、六西格玛管理等。
这些方法与策略旨在提高生产过程的稳定性,降低不良品率,提高客户满意度。
四、工序质量控制的应用与实践在实际生产中,工序质量控制的应用与实践主要包括:制造业的质量管理、工程项目的质量管理、服务业的质量管理等。
通过实施工序质量控制,企业可以有效提高产品质量,降低生产成本,提升竞争力。
工序质量控制的步骤

工序质量控制的步骤
工序质量控制是确保产品或服务在生产过程中满足预定质量要求的方法。
以下是工序质量控制的步骤:
1. 制定质量计划:在项目开始时,明确项目的质量目标、标准和相关的质量要求。
质量计划应包括质量目标、质量标准、质量保证措施和质量验收标准等。
2. 过程分析:分析生产过程中的各个环节,识别潜在的质量问题,找出影响质量的关键因素。
3. 制定质量控制措施:针对识别出的质量问题和关键因素,制定相应的质量控制措施,确保在生产过程中质量得到有效控制。
4. 质量检测:对生产过程中的产品或服务进行定期检测,确保产品或服务符合质量标准。
质量检测方法包括首件检验、过程检验和成品检验等。
5. 数据分析:收集和分析质量检测数据,评估工序质量状态,发现异常情况及时采取措施进行调整。
6. 过程改进:根据质量控制数据和检测结果,不断优化生产过程,提高工序质量。
7. 质量审核:对质量管理体系进行定期审核,确保质量管理体系的有效性和适用性。
8. 持续改进:根据质量审核结果和过程改进需求,持续改进质量管理体系,形成良性循环。
9. 培训与沟通:加强员工的质量意识培训,提高员工的质量控制能力,确保质量控制措施得到有效执行。
同时,建立有效的沟通机制,确保各部门之间质量信息的传递和协作。
10. 客户满意度评价:收集客户对产品或服务的满意度评价,对质量控制效果进行评估,持续改进产品质量。
通过以上步骤,企业可以有效地控制工序质量,提高产品或服务的质量水平,满足客户需求。
第八章工序质量控制

TL
(TM
T )x
2
T 2
T (1
2
k)
3C p (1
k)
TU
(TM
T
)
x
2
T 2
T (1 k)
2
3C p (1 k )
所以有 P [3C p (1 k )] [3C p (1 k )]
当工序左偏,即 x TM 时,
TL
(TM
T) 2
x
T 2
T
(1 2
k)
3C p
(1
k)
所以仍有
也是μ的无偏估计量,但计算更方便。
• 总体标准差σ可用样本标准差s来估计,也可用样本极差R或R序
列的平均值
R
来估计。两者都是σ的无偏估计 ,但极差的计算要
容易得多。实际应用中,σ的估计值
^
R
样本容量n有关的参数,可查表8-1。
d2
,其中 d2是和
表8-1 3σ控制限参数表
n
d2
d3
A2
D3
D4
m3 E
两个已知,则可查得第三个的值。
三、工序能力的判断及处置
工序能力判断的目的是对工序进行预防性处置,以确保生产过 程的质量水平。理想的工序能力既要能满足质量保证的要求,又要 符合经济性的要求。表8-3给出了利用工序能力指数对工序能力作 出判断的一般标准。
表8-3 工序能力指数判断标准
工序能力等级 特级 一级 二级 三级 四级
10 3.077 5 0.797 0.308 0.223 1.777 1.176 0.975
第二节 工序能力指数
一、工序能力分析
(一)工序能力的概念 (二)工序能力的调查 (三)工序能力的测定
工序质量控制的方法

工序质量控制的方法什么是工序质量控制工序质量控制是指为把工序质量的波动限制在规定的界限内所进行的活动。
工序质量控制是利用各种方法和统计工具判断和消除系统因素所造成的质量波动,以保证工序质量的波动限制在要求的界限内.工序质量控制的方法由于工序种类繁多,工序因素复杂,工序质量控制所需要的工具和方法也多种多样,现场工作人员应根据各工序特点,选定既经济又有效的控制方法,避免生搬硬套.企业在生产中常采用以下三种方法:一是自控;二是工序质量控制点;三是工序诊断调节法.自控是操作者通过自检得到数据后,将数据与产品图纸和技术要求相对比,根据数据来判定合格程度,作出是否调整的判断.操作者的自控是调动工人搞好产品质量的积极性,进行工序质量控制是确保产品质量的一种有效方法.工序质量控制点的日常控制应是监视工序能力的波动,检测主导因素的变化,调整主导工序因素的水平.通过监视工序能力波动可得到主导工序因素变化的信息,然后检测各主导工序因素,对异常变化的主导因素及时进行调整,使工序处于持续稳定的加工状态.按一定的间隔取样,通过样本观测值的分析和判断,尽快发现异常, 找出原因,采取措施,使工序恢复正常的质量控制方法,称为工序诊断调节法.尽快地发现工序状态异常,就是所谓的工序诊断;寻找原因,采取对策,使工序恢复正常,就是所谓的工序调节.工序诊断调节法,适用于机械化和自动化水平高的生产过程.主要工序因素的质量控制主要工序因素的质量控制,即关键工序、重要工序的质量控制。
就航空产品而言,对这类工序的控制要求十分严格。
航空企业都必须按照国家颁布的标准及军工产品质量管理条例要求,在生产中要加强工序的关键件、重要件制造中的严审工作,以确保产品质量。
企业在生产制造过程中要进行严格的生产管理和周密的工序质量控制,尤其是关键工序、重要工序的质量控制。
这类控制很适合于研制和批量生产的军民品的工序控制。
其方法是:1、工艺规程的编制。
根据企业工艺管理特点,采用细化工艺堆积编制方法,把关键或重要图纸尺寸、技术要求写入工序名称栏内,工序图纸中的关键尺寸、重要尺寸或其它技术要求(如形状、位置公差标量),在该尺寸旁加盖“关键”或“重要”印记。
一般工序质量控制的方法

一般工序质量控制的方法
一般工序质量控制的方法有以下几种:
1. 过程监控:对生产过程进行实时监控,确保每个工序都按照标准操作程序进行。
可以使用监控设备、传感器等技术手段,实时收集数据并进行分析,及时发现问题并进行纠正。
2. 统计过程控制(SPC):采用统计方法对生产过程进行监控和分析,通过控制图、过程能力指数等工具,识别过程中的异常情况,并采取相应的纠正措施。
3. 检查和测试:在工序完成后,进行检查和测试,以确保产品质量符合要求。
可以采用手动检查、自动化检测设备等方式进行。
4. 建立质量标准:明确每个工序的质量要求和验收标准,使操作人员清楚知道应该达到的质量水平。
5. 培训和教育:对操作人员进行培训,使其了解工序的操作要求、质量标准以及如何识别和解决质量问题。
6. 质量反馈:收集客户反馈、内部质量报告等信息,及时了解产品在市场上的质量表现,以便对工序进行改进和优化。
7. 持续改进:通过不断地分析质量数据、实施改进措施,逐步提高工序的稳定性和产品的质量水平。
8. 预防性维护:对设备进行定期维护和保养,确保设备的正常运行,减少因设备故障导致的质量问题。
这些方法可以帮助企业有效地控制一般工序的质量,提高产品的合格率和客户满意度。
工序质量控制
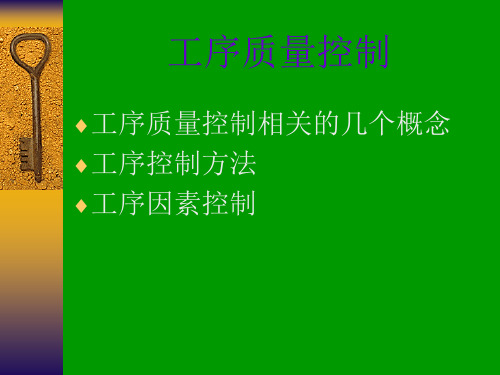
工序质量控制的对象
工序质量控制的实质对象是工序因素 5M1E(人、机、料、法、环、测)。
工序控制的对象从直观上来说是控制工 序形成的质量特性值,而质量特性值的 波动受工序因素的影响,所以说工序质 量控制的实质对象是工序因素5M1E,尤 其是其中的主导因素。
工序质量控制点
工序质量控制点是指产品生产过程中必 须重点控制的质量特性、关键部位、薄 弱环节和主导因素。
工序质量控制
工序质量控制相关的几个概念 工序控制方法 工序因素控制
工序质量控制
工序质量控制相关的几个概念
工序质量控制相关的几个概念
工序 工序的过程 工序质量 工序质量控制 工序质量控制的对象 工序质量控制点
工序
工序是产品制造过程的基本环节。 工序一般包括加工、检验、搬运、 停留4个环节。
工序的过程
验和成品检验 合理选择供应商 搞好协作厂间的协作关系,督促、帮助
供应商做好质量控制和质量保证工作。
工艺方法的因素
工艺方法包括工艺流程的安排,工艺之间的衔 接,工序加工手段的选择(加工环境条件的选 择,工艺装备配置的选择,工艺参数的选择) 和工序加工的指导文件的编制(如作业指导书, 操作规程,工艺质量分析表等)。
可以以质量特性值、工序因素(5M1E) 等为对象来设置工序质量控制点。
工序质量控制
工序控制方法
工序控制方法
专职三检制 工检结合三检制 应用统计图表法
专职三检制
由专职检验员工在每班次正式加工开始 前首检,加工过程中进行中间检或巡回 检、加工结束时进行完工检或末件检。
工检结合三检制
在专职三检制基础上,增加操作者自检,班组 长、班组质量员对本组各工序的互检和下道工 序对上道工序的互检。这种制度提供更多、更 及时地质量信息,是适用于各种工序质量控制 形式的控制方法。
工序质量控制的内容

工序质量控制的内容工序质量控制。
工序质量控制是指在生产过程中,通过对每个工序的质量进行监控和管理,以确保最终产品的质量符合要求。
它是生产过程中的重要环节,对于提高产品质量、降低生产成本、增强市场竞争力具有重要意义。
本文将就工序质量控制的相关内容进行详细介绍。
首先,工序质量控制的核心是质量管理。
在生产过程中,通过建立完善的质量管理体系,包括质量目标的设定、质量标准的制定、质量责任的明确等,来确保每个工序的质量得到有效控制。
同时,还要加强对生产设备、生产环境等方面的管理,保证生产过程的稳定性和可控性。
其次,工序质量控制需要依靠科学的方法和手段。
在生产过程中,可以采用各种质量管理工具和方法,如质量检测、质量抽样、质量统计分析等,对每个工序的质量进行监控和分析,及时发现问题并加以解决。
同时,还可以借助信息化技术,建立质量信息管理系统,实现对质量数据的实时监控和分析,提高质量管理的科学化和精细化水平。
再次,工序质量控制需要全员参与。
质量是全员责任,每个员工都应该对自己的工作质量负责。
因此,在生产过程中,需要加强对员工的培训和教育,提高他们的质量意识和责任感。
同时,还要建立健全的奖惩机制,激励员工参与质量管理,推动质量管理工作的落实和持续改进。
最后,工序质量控制需要不断改进。
质量管理工作是一个持续改进的过程,需要不断总结经验、发现问题、改进方法,以适应市场需求和技术变革的发展。
因此,企业应该建立健全的质量管理评估机制,定期对质量管理工作进行评估和审查,找出存在的问题和不足,并采取相应的改进措施,推动质量管理工作不断向前发展。
综上所述,工序质量控制是确保产品质量的重要手段,需要依靠完善的质量管理体系、科学的方法和手段、全员参与和持续改进来实现。
只有这样,企业才能在激烈的市场竞争中立于不败之地,赢得消费者的信赖和认可。
希望本文对工序质量控制有所帮助,谢谢阅读。
工序活动的质量控制方案及措施
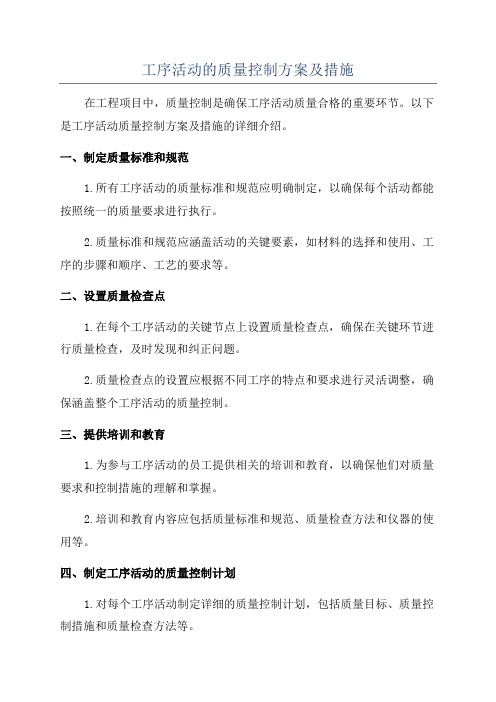
工序活动的质量控制方案及措施在工程项目中,质量控制是确保工序活动质量合格的重要环节。
以下是工序活动质量控制方案及措施的详细介绍。
一、制定质量标准和规范1.所有工序活动的质量标准和规范应明确制定,以确保每个活动都能按照统一的质量要求进行执行。
2.质量标准和规范应涵盖活动的关键要素,如材料的选择和使用、工序的步骤和顺序、工艺的要求等。
二、设置质量检查点1.在每个工序活动的关键节点上设置质量检查点,确保在关键环节进行质量检查,及时发现和纠正问题。
2.质量检查点的设置应根据不同工序的特点和要求进行灵活调整,确保涵盖整个工序活动的质量控制。
三、提供培训和教育1.为参与工序活动的员工提供相关的培训和教育,以确保他们对质量要求和控制措施的理解和掌握。
2.培训和教育内容应包括质量标准和规范、质量检查方法和仪器的使用等。
四、制定工序活动的质量控制计划1.对每个工序活动制定详细的质量控制计划,包括质量目标、质量控制措施和质量检查方法等。
2.根据工序的复杂程度和风险评估的结果,调整质量控制计划的内容和频率。
五、实施质量检查和测试1.进行定期的质量检查和测试,以验证工序活动的质量是否符合标准和规范要求。
2.质量检查和测试应包括外观检查、尺寸测量、材料成分分析等,确保每个活动的质量问题被及时发现和解决。
六、记录和分析质量数据1.记录每个工序活动的质量数据,包括质量检查结果、质量问题和解决方案、工序活动的执行情况等。
2.对质量数据进行分析,找出常见的质量问题和改进措施,以提升整体质量水平。
七、持续改进质量控制1.定期评估质量控制方案的有效性,并进行必要的调整和改进。
2.建立反馈机制,收集和分析员工和客户的意见和建议,以改进质量控制方案和提升客户满意度。
以上是工序活动质量控制方案及措施的详细介绍。
通过制定质量标准和规范、设置质量检查点、提供培训和教育、制定质量控制计划、实施质量检查和测试、记录和分析质量数据以及持续改进质量控制,能够有效地确保工序活动的质量合格,提升工程项目的整体质量水平。
工序质量控制
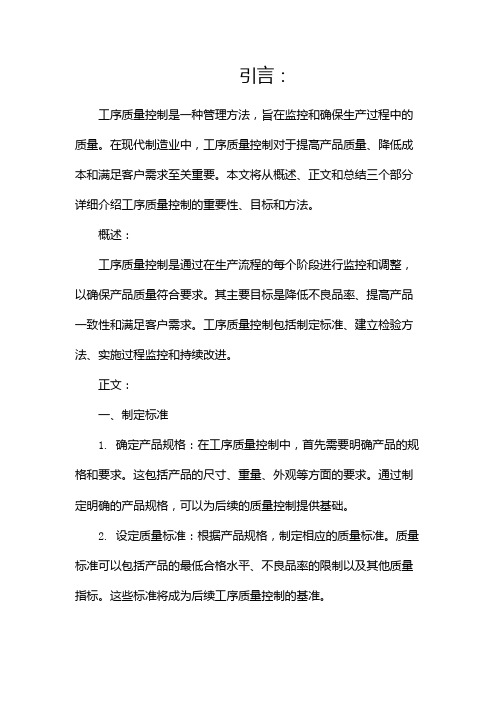
引言:工序质量控制是一种管理方法,旨在监控和确保生产过程中的质量。
在现代制造业中,工序质量控制对于提高产品质量、降低成本和满足客户需求至关重要。
本文将从概述、正文和总结三个部分详细介绍工序质量控制的重要性、目标和方法。
概述:工序质量控制是通过在生产流程的每个阶段进行监控和调整,以确保产品质量符合要求。
其主要目标是降低不良品率、提高产品一致性和满足客户需求。
工序质量控制包括制定标准、建立检验方法、实施过程监控和持续改进。
正文:一、制定标准1. 确定产品规格:在工序质量控制中,首先需要明确产品的规格和要求。
这包括产品的尺寸、重量、外观等方面的要求。
通过制定明确的产品规格,可以为后续的质量控制提供基础。
2. 设定质量标准:根据产品规格,制定相应的质量标准。
质量标准可以包括产品的最低合格水平、不良品率的限制以及其他质量指标。
这些标准将成为后续工序质量控制的基准。
3. 建立检验方法:为了验证产品是否符合规格和质量标准,需要建立相应的检验方法。
检验方法可以包括尺寸测量、外观检查、化学分析等。
通过确定适当的检验方法,可以进行有效的质量检验。
二、过程监控1. 设立过程控制点:在生产过程中,确定关键的过程控制点是工序质量控制的关键。
通过在关键的步骤设置控制点,可以实时监控工艺参数和产品质量指标。
2. 实施统计过程控制:统计过程控制是一种通过收集和分析工序中的样本数据来监控过程稳定性并及时调整的方法。
通过控制图、过程能力指数等工具,可以准确评估工序的稳定性和功效。
3. 采用自动化技术:现代制造业中,自动化技术可以提高工序质量控制的效率和准确性。
自动采样、自动检测和自动调整等技术可以减少人为因素的干扰,并提高生产过程的稳定性。
三、持续改进1. 进行根本原因分析:当发生质量问题时,需要进行根本原因分析,找出导致质量问题的根本原因。
通过这种分析,可以采取适当的纠正和预防措施,避免类似问题的再次发生。
2. 实施持续改进计划:持续改进是工序质量控制的核心。
《工序质量控制 》课件
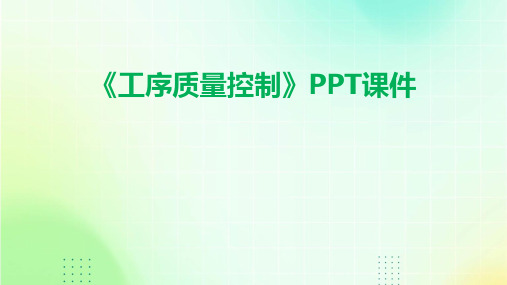
包括目标管理、流程优化、六西格玛管理等,旨在不断优化生产和 服务过程,提高产品质量和客户满意度。
持续改进的工具
如鱼骨图、直方图、控制图等,用于分析问题、识别改进机会和监 控改进效果。
持续改进的实施步骤
包括确定改进目标、分析现状、制定改进计划、实施改进措施和评 估改进效果等,确保持续改进的有效性和系统性。
防错技术是一种通过设计工艺、设备和管理方法等手段来预防缺陷和错误产生的质量控制 方法。它强调在产品设计、制造和检测等环节采取预防措施,以最大限度地减少人为因素 造成的质量波动和损失。
1. 设计阶段
采用简化设计、标准化设计等方法,降低操作难度和出错概率;
2. 制造阶段
采用自动化、机器人等技术,减少人工参与和操作环节;
02
工序质量控制方法
统计过程控制(SPC)
定义
统计过程控制是一种应用统计分 析技术对生产过程进行监控和管 理的质量控制方法。
目的
通过监控关键工序的特性,发现 异常波动,及时采取措施调整, 使生产过程处于受控状态。
方法
使用控制图对关键工序的特性进 行监控,通过分析控制图上的数 据,判断生产过程的稳定性。
06
未来工序质量控制展望
新兴的质量控制技术
01
实时监控技术
通过传感器和数据分析技术,实 时监测生产过程中的质量数据, 及时发现异常并进行调整。
02
机器学习与人工智 能
利用机器学习算法对大量质量数 据进行学习,自动识别异常模式 ,提高质量控制精度。
03
虚拟现实与增强现 实
通过虚拟现实和增强现实技术, 模拟生产环境,预测和优化生产 过程中的质量问题。
3
方法
选择合适的控制图类型,确定控制图的参数和界 限,收集数据并绘制控制图,根据控制图上的数 据进行质量分析和改进。
简述工序质量控制的内容
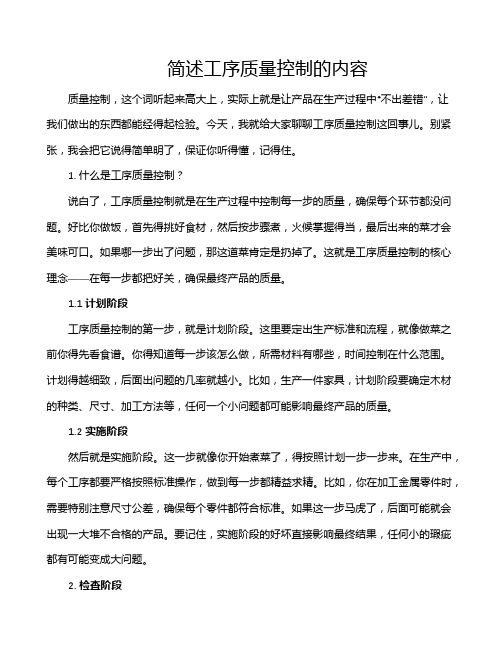
简述工序质量控制的内容质量控制,这个词听起来高大上,实际上就是让产品在生产过程中“不出差错”,让我们做出的东西都能经得起检验。
今天,我就给大家聊聊工序质量控制这回事儿。
别紧张,我会把它说得简单明了,保证你听得懂,记得住。
1. 什么是工序质量控制?说白了,工序质量控制就是在生产过程中控制每一步的质量,确保每个环节都没问题。
好比你做饭,首先得挑好食材,然后按步骤煮,火候掌握得当,最后出来的菜才会美味可口。
如果哪一步出了问题,那这道菜肯定是扔掉了。
这就是工序质量控制的核心理念——在每一步都把好关,确保最终产品的质量。
1.1 计划阶段工序质量控制的第一步,就是计划阶段。
这里要定出生产标准和流程,就像做菜之前你得先看食谱。
你得知道每一步该怎么做,所需材料有哪些,时间控制在什么范围。
计划得越细致,后面出问题的几率就越小。
比如,生产一件家具,计划阶段要确定木材的种类、尺寸、加工方法等,任何一个小问题都可能影响最终产品的质量。
1.2 实施阶段然后就是实施阶段。
这一步就像你开始煮菜了,得按照计划一步一步来。
在生产中,每个工序都要严格按照标准操作,做到每一步都精益求精。
比如,你在加工金属零件时,需要特别注意尺寸公差,确保每个零件都符合标准。
如果这一步马虎了,后面可能就会出现一大堆不合格的产品。
要记住,实施阶段的好坏直接影响最终结果,任何小的瑕疵都有可能变成大问题。
2. 检查阶段实施完之后,检查阶段就登场了。
这一步就像是你煮菜时尝味道,看看是否需要加盐、加糖。
检查阶段要对每一个工序进行严格的质量检查,确保没有疏漏。
这个过程中,有时你需要用一些专业的工具,比如测量仪器,来确认各项指标是否符合标准。
就像你要用温度计来测量汤的温度,确保它煮到刚刚好的状态。
检查阶段要细致入微,哪怕是一个微小的偏差,都可能影响到产品的最终质量。
2.1 记录和分析在检查阶段,你还得记录每一步的检查结果。
这就像做饭时,你可能会记下每道菜的调料比例,以后做饭时可以参考。
工序质量控制
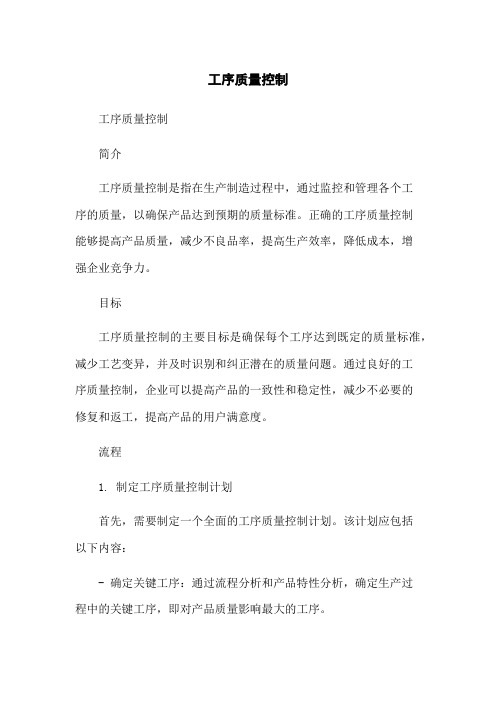
工序质量控制工序质量控制简介工序质量控制是指在生产制造过程中,通过监控和管理各个工序的质量,以确保产品达到预期的质量标准。
正确的工序质量控制能够提高产品质量,减少不良品率,提高生产效率,降低成本,增强企业竞争力。
目标工序质量控制的主要目标是确保每个工序达到既定的质量标准,减少工艺变异,并及时识别和纠正潜在的质量问题。
通过良好的工序质量控制,企业可以提高产品的一致性和稳定性,减少不必要的修复和返工,提高产品的用户满意度。
流程1. 制定工序质量控制计划首先,需要制定一个全面的工序质量控制计划。
该计划应包括以下内容:- 确定关键工序:通过流程分析和产品特性分析,确定生产过程中的关键工序,即对产品质量影响最大的工序。
- 设定质量标准:为每个关键工序确定明确的质量标准,包括产品的尺寸、外观、性能等方面的要求。
- 制定检测方法:选择适当的检测方法,如目视检查、计量检测、抽样检测等,确保能够准确地检测出工序中的质量问题。
- 制定检测频率:确定每个关键工序的检测频率,以保证质量问题能够及时被发现并纠正。
2. 实施工序质量控制在生产过程中,需要根据制定的工序质量控制计划,实施相应的控制措施。
- 培训操作员:对操作员进行培训,使其了解每个关键工序的质量标准和检测方法,掌握正确的操作技能。
- 监控关键参数:对每个关键工序的关键参数进行实时监控,确保生产过程在可控范围内,并及时调整参数,以确保产品质量的稳定性。
- 进行质量抽检:按照计划的频率进行抽检,对关键工序进行质量检测,确保产品符合质量标准。
- 记录和分析检测结果:对每次质量检测的结果进行记录和分析,及时识别和纠正潜在的质量问题,并采取相应的改进措施。
3. 持续改进工序质量控制是一个持续改进的过程,需要不断地进行监控和分析,以寻找改进的机会。
- 分析检测结果:定期分析检测结果,统计质量指标,识别异常情况和趋势,找出质量问题的根本原因。
- 制定改进计划:基于分析结果,制定相应的改进计划,包括调整工艺参数、改进工艺流程、提供培训等。
工序质量控制点

工序质量控制点标题:工序质量控制点引言概述:工序质量控制是生产过程中非常重要的一环,它能够确保产品质量和生产效率。
在生产过程中,确定合适的质量控制点是至关重要的,惟独在关键的环节进行质量控制,才干有效地避免质量问题的发生。
本文将从五个方面介绍工序质量控制点的重要性和具体内容。
一、原材料质量控制点1.1 原材料的选择:选择优质原材料是保证产品质量的基础,必须对原材料的质量进行严格把控。
1.2 原材料的检验:在进入生产流程之前,需要对原材料进行全面的检验,确保符合产品要求。
1.3 原材料存储条件:正确的原材料存储条件也是原材料质量控制的重要环节,避免因存储不当导致质量问题。
二、生产工艺质量控制点2.1 设定工艺参数:在生产过程中,设定正确的工艺参数是确保产品质量的关键,需要根据产品特性进行调整。
2.2 监控生产过程:对生产过程进行实时监控,及时发现问题并进行调整,确保产品符合标准。
2.3 完善工艺流程:不断优化生产工艺流程,提高生产效率和产品质量。
三、设备维护质量控制点3.1 定期保养设备:设备的正常运转对产品质量至关重要,定期保养设备可以减少故障率。
3.2 设备检修记录:建立设备检修记录,及时发现设备问题并进行维修,确保设备正常运转。
3.3 设备运行参数:设备运行参数的设定也是设备维护质量控制的重要环节,需要根据产品要求进行调整。
四、人员技术质量控制点4.1 培训与考核:对生产人员进行定期培训和考核,提高其技术水平和质量意识。
4.2 责任分工:明确每一个人员的责任分工,确保每一个环节都有专人负责,避免责任含糊。
4.3 激励机制:建立激励机制,激励人员积极参预工序质量控制,提高产品质量。
五、成品质量控制点5.1 抽检成品:对成品进行抽检,确保产品符合标准。
5.2 产品追溯:建立产品追溯体系,及时发现问题产品并进行处理。
5.3 售后服务:做好售后服务工作,及时处理客户反馈的质量问题,提高客户满意度。
结论:工序质量控制点的设定和实施对于产品质量的提升和生产效率的提高至关重要。
工序质量控制点
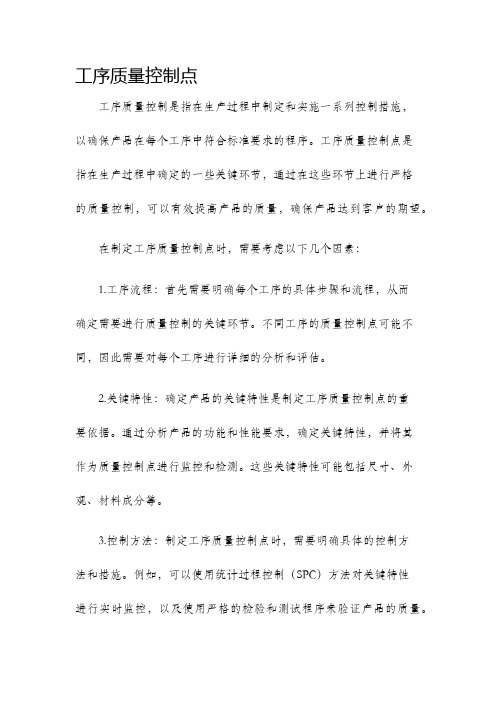
工序质量控制点工序质量控制是指在生产过程中制定和实施一系列控制措施,以确保产品在每个工序中符合标准要求的程序。
工序质量控制点是指在生产过程中确定的一些关键环节,通过在这些环节上进行严格的质量控制,可以有效提高产品的质量,确保产品达到客户的期望。
在制定工序质量控制点时,需要考虑以下几个因素:1.工序流程:首先需要明确每个工序的具体步骤和流程,从而确定需要进行质量控制的关键环节。
不同工序的质量控制点可能不同,因此需要对每个工序进行详细的分析和评估。
2.关键特性:确定产品的关键特性是制定工序质量控制点的重要依据。
通过分析产品的功能和性能要求,确定关键特性,并将其作为质量控制点进行监控和检测。
这些关键特性可能包括尺寸、外观、材料成分等。
3.控制方法:制定工序质量控制点时,需要明确具体的控制方法和措施。
例如,可以使用统计过程控制(SPC)方法对关键特性进行实时监控,以及使用严格的检验和测试程序来验证产品的质量。
4.质量记录:在每个工序的质量控制点上,应该建立相应的质量记录系统。
通过记录和追踪相关数据,可以及时发现问题并采取纠正措施。
这些记录可以用于分析和改进生产流程,提高产品的质量和可靠性。
在实施工序质量控制点时,需要注意以下几个关键点:1.培训和教育:确保所有操作人员都明确了解工序质量控制点的重要性和具体要求。
提供必要的培训和教育,以确保操作人员能够正确执行质量控制措施。
2.强调团队合作:工序质量控制是一个团队工作,需要各个部门之间的紧密合作。
各个部门之间应该加强沟通和协调,共同推动质量控制工作的顺利进行。
3.持续改进:工序质量控制点是一个动态的过程,需要不断进行改进和优化。
通过分析质量数据和反馈,及时调整和改进控制措施,以确保质量控制工作的持续有效性。
综上所述,工序质量控制点对于确保产品质量的稳定性和可靠性至关重要。
通过制定和实施严格的质量控制措施,建立质量记录。
工序质量控制的方法

引言:正文内容:1.强化员工培训在工序质量控制中,员工的专业技能是至关重要的。
因此,企业应该加强员工培训,提高其专业技能水平。
培训内容可以包括工艺流程、操作规范、质量标准等方面的知识。
培训方式可以采用内部培训和外部培训相结合的方式。
内部培训可以由公司内部的专业人员进行,外部培训可以通过邀请行业专家或外聘培训机构来进行。
2.设立工序检查点在生产过程中,可以设置一些关键的检查点来监控工序的质量。
这些检查点可以是工序中的某个环节,也可以是工序之间的转换点。
在每个检查点上,应该制定详细的检查标准,根据标准进行检查,并及时记录检查结果。
如果有不合格项,应该立即采取相应的纠正措施。
3.引入先进的质量控制技术随着科技的进步,许多先进的质量控制技术已经应用于工业生产中。
企业可以考虑引入这些技术来提高工序的质量控制水平。
例如,使用自动化设备和传感器可以实时监测工序中的各项指标,并通过数据分析来判断工序是否符合要求。
还可以使用一些先进的测量仪器和分析软件来帮助进行质量检测和数据分析。
4.建立完善的质量管理体系建立一个完善的质量管理体系是工序质量控制的基础。
这个体系应该包括质量方针、质量目标、质量手册等基本文件,还应该有相应的质量流程和工作指导文件。
还应该建立质量管理的组织结构,明确各个岗位的职责和权限。
通过这些措施,可以确保工序质量控制的各项工作有序进行。
5.加强供应链管理供应链管理在工序质量控制中起着重要的作用。
企业应该与供应商建立良好的合作关系,并对供应商进行认证和评估。
在供应链中,可以采取一些措施来控制质量风险。
例如,建立供应商的质量审查机制,定期对供应商的产品进行检验,并及时反馈结果。
总结:本文详细阐述了工序质量控制的各个方面,包括员工培训、设立检查点、引入先进技术、建立管理体系和加强供应链管理等。
这些方法可以帮助企业提高工序的质量控制水平,保证产品的质量符合要求。
在实践中,企业应根据自身的实际情况,结合上述方法,并不断改进和创新,以适应市场的需求和发展。
质量主要工序控制措施
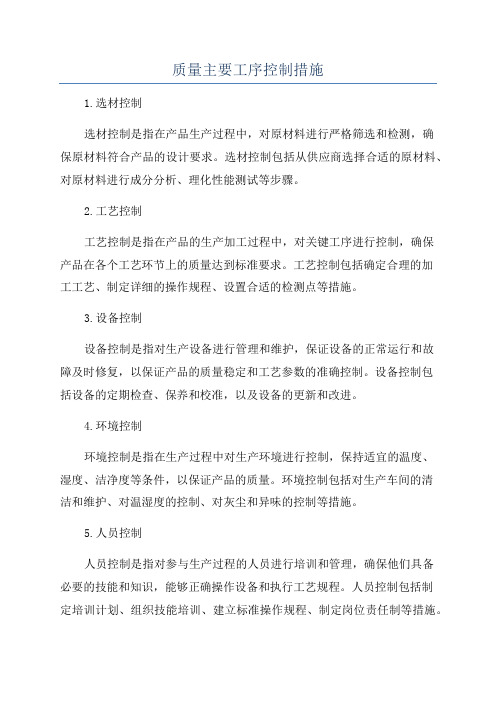
质量主要工序控制措施
1.选材控制
选材控制是指在产品生产过程中,对原材料进行严格筛选和检测,确
保原材料符合产品的设计要求。
选材控制包括从供应商选择合适的原材料、对原材料进行成分分析、理化性能测试等步骤。
2.工艺控制
工艺控制是指在产品的生产加工过程中,对关键工序进行控制,确保
产品在各个工艺环节上的质量达到标准要求。
工艺控制包括确定合理的加
工工艺、制定详细的操作规程、设置合适的检测点等措施。
3.设备控制
设备控制是指对生产设备进行管理和维护,保证设备的正常运行和故
障及时修复,以保证产品的质量稳定和工艺参数的准确控制。
设备控制包
括设备的定期检查、保养和校准,以及设备的更新和改进。
4.环境控制
环境控制是指在生产过程中对生产环境进行控制,保持适宜的温度、
湿度、洁净度等条件,以保证产品的质量。
环境控制包括对生产车间的清
洁和维护、对温湿度的控制、对灰尘和异味的控制等措施。
5.人员控制
人员控制是指对参与生产过程的人员进行培训和管理,确保他们具备
必要的技能和知识,能够正确操作设备和执行工艺规程。
人员控制包括制
定培训计划、组织技能培训、建立标准操作规程、制定岗位责任制等措施。
以上是对质量主要工序控制措施的介绍。
在实际生产中,这些措施需要根据具体的产品和生产环境进行有针对性的调整和实施。
通过采取这些控制措施,可以最大限度地提高产品的质量稳定性和一致性,减少质量问题的发生,满足客户的需求和期望。
只有通过严格的质量控制,企业才能提高产品的竞争力和市场份额。
工序质量控制情况范本

工序质量控制情况范本一、工序质量控制情况简介工序质量控制是指在生产制造过程中对每个环节进行监控和管理,以确保产品的质量符合标准要求。
有效的工序质量控制能够提高产品的质量稳定性,减少不良率,降低生产成本,增强企业竞争力。
本文将围绕工序质量控制情况展开详细介绍。
二、工序质量控制内容1. 设立检测点在生产制造过程中,需要在关键环节设立检测点,对产品质量进行实时监测。
检测点的设置应根据工序流程和产品特性进行详细规划,确保能够有效把控产品质量。
2. 制定标准作业流程针对不同工序,应制定相应的标准作业流程,规范员工操作行为。
在执行过程中,要求员工按照标准作业流程进行操作,确保产品质量的稳定性和一致性。
3. 强化员工培训为提高员工操作技能和工艺水平,需要加强员工培训和考核。
通过培训,提升员工的质量意识和责任心,使其能够熟练掌握操作技能,保证产品质量符合标准要求。
4. 实施巡回检查定期对工序进行巡回检查,发现问题及时处理。
巡回检查是发现和解决问题的有效手段,能够帮助企业及时调整生产过程,确保产品质量得到有效控制。
5. 引入先进技术手段积极引入先进的技术手段,如智能设备、质量管理软件等,提升工序质量控制水平。
通过技术手段的应用,能够实现实时数据监测和分析,为质量控制提供更精准的支持。
6. 建立质量档案建立完善的质量档案,记录和管理每个工序的质量数据和相关信息。
质量档案可以为产品质量问题的溯源提供重要依据,同时为未来工序质量改进提供参考。
三、工序质量控制情况改进1. 建立持续改进机制建立持续改进机制,通过定期评估和总结工序质量控制情况,及时发现问题并采取改进措施。
持续改进是保证工序质量控制效果的关键,能够不断提升产品质量水平。
2. 加强内部沟通协作加强内部部门之间的沟通协作,构建质量管理的闭环体系。
通过协同合作,实现信息互通、问题共同解决,提升工序质量控制效率和效果。
3. 培育质量文化倡导企业质量文化,强调每个员工都是质量控制的参与者。
工序质量控制点
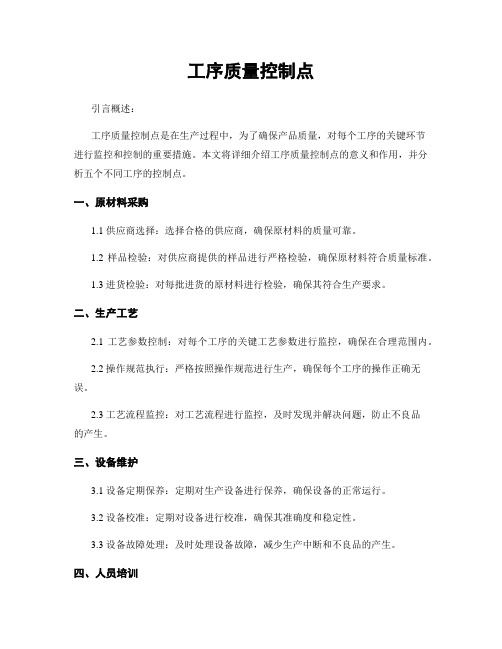
工序质量控制点引言概述:工序质量控制点是在生产过程中,为了确保产品质量,对每个工序的关键环节进行监控和控制的重要措施。
本文将详细介绍工序质量控制点的意义和作用,并分析五个不同工序的控制点。
一、原材料采购1.1 供应商选择:选择合格的供应商,确保原材料的质量可靠。
1.2 样品检验:对供应商提供的样品进行严格检验,确保原材料符合质量标准。
1.3 进货检验:对每批进货的原材料进行检验,确保其符合生产要求。
二、生产工艺2.1 工艺参数控制:对每个工序的关键工艺参数进行监控,确保在合理范围内。
2.2 操作规范执行:严格按照操作规范进行生产,确保每个工序的操作正确无误。
2.3 工艺流程监控:对工艺流程进行监控,及时发现并解决问题,防止不良品的产生。
三、设备维护3.1 设备定期保养:定期对生产设备进行保养,确保设备的正常运行。
3.2 设备校准:定期对设备进行校准,确保其准确度和稳定性。
3.3 设备故障处理:及时处理设备故障,减少生产中断和不良品的产生。
四、人员培训4.1 岗位培训:对每个工序的操作人员进行专业培训,确保其熟练掌握操作技能。
4.2 质量意识培养:加强员工的质量意识培养,使其认识到自己的工作对产品质量的重要性。
4.3 持续学习:鼓励员工进行持续学习,了解最新的工艺和质量管理知识,提升自身素质。
五、过程监控5.1 抽样检验:对每个工序的生产批次进行抽样检验,确保产品质量符合标准。
5.2 数据分析:对生产过程中产生的数据进行分析,及时发现问题和异常,采取相应措施。
5.3 不良品处理:对不良品进行分类和处理,分析原因并采取措施,防止类似问题再次发生。
结论:工序质量控制点是确保产品质量的重要环节,在原材料采购、生产工艺、设备维护、人员培训和过程监控等方面都有明确的控制点。
通过对这些控制点的有效管理,可以提高产品质量,满足客户需求,提升企业竞争力。
因此,企业应高度重视工序质量控制点的建立和执行,不断优化和改进质量管理体系,实现持续的质量提升。
工序质量控制名词解释

工序质量控制名词解释1. 啥叫工序质量控制呀?就好比你做蛋糕,从准备材料到搅拌、烘烤,每一步都得精心对待,不能马虎,这就是对做蛋糕这个工序的质量控制呀!比如你烤蛋糕时温度没控制好,那蛋糕不就烤砸啦!2. 工序质量控制呢,简单来说,就是确保生产过程像火车在轨道上稳稳运行一样。
就像组装一个玩具,每个零件的安装都要到位,不然这玩具可就不完美了呀!你想想,要是少装个零件,那玩具还能好玩吗?3. 嘿,工序质量控制不就是让每个工序都像花朵绽放一样完美嘛!比如制造汽车,从车架到发动机安装,都要精益求精。
要是某个螺丝没拧紧,那在路上开着开着不就危险啦!4. 哎呀,工序质量控制就像是给生产过程上了一道保险呀!比如制作衣服,裁剪、缝制都得精细,不然穿起来不合身多难看呀!要是线缝歪了,这衣服质量不就大打折扣了嘛!5. 工序质量控制其实就是守护生产的小天使呀!好比盖房子,地基、砌墙每个环节都要牢固。
要是墙砌歪了,这房子还能安全吗?6. 哇塞,工序质量控制不就是让一切都顺顺利利的魔法嘛!像做一顿美味的饭菜,洗菜、切菜、炒菜都要恰到好处。
要是盐放多了,那可就咸得没法吃啦!7. 工序质量控制呀,就好像是给生产过程指引方向的明灯呀!比如印刷一本书,排版、印刷都不能出错。
要是印错字了,那读者看了多别扭呀!8. 嘿呀,工序质量控制不就是让生产严丝合缝的秘诀嘛!就像生产手机,每个零部件的安装都不能有差错。
要是屏幕有瑕疵,那这手机可就不完美了呀!9. 工序质量控制就是让生产变得超级棒的法宝呀!好比种植蔬菜,播种、施肥、浇水都要得当。
要是水浇多了,蔬菜不就烂根啦!10. 工序质量控制简单讲就是让生产过程美美的呀!像制作陶瓷,塑形、烧制都要把握好。
要是烧制温度不对,陶瓷不就变形啦!我的观点结论就是:工序质量控制真的太重要啦,它关系到产品的好坏,可不能小瞧它呀!。
- 1、下载文档前请自行甄别文档内容的完整性,平台不提供额外的编辑、内容补充、找答案等附加服务。
- 2、"仅部分预览"的文档,不可在线预览部分如存在完整性等问题,可反馈申请退款(可完整预览的文档不适用该条件!)。
- 3、如文档侵犯您的权益,请联系客服反馈,我们会尽快为您处理(人工客服工作时间:9:00-18:30)。
二、工序控制的方法如前所述,影响工序过程质量的因素有人、机、料、法、环、测,即通常所说的5M1E。
经验与理论表明,这六个因素对不同的工序及其质量的影响程度有着显著的差别。
这里有必要引进有关工序“主导因素”的概念。
“主导因素”是指在众多影响最终质量的因素中,起决定全局或占支配地位的因素。
任何加工制造过程都存在这样的因素,而且一种或几种占支配地位的情况到处可见。
根据专业技术知识和经验,人们一般可以从各种影响因素中识别出主导因素来。
例如铸造上模具、熔炼、型砂起主导作用,加工上除了模具因素外,还有工装、工艺参数(刀具、切削速度等)、员工的操作规范等也起主导作用。
我们可以根据实际分析结果建立控制系统。
在制造过程中,我们可以运用主导因素这一概念,分别对不同的工序采取切实有效的防误和控制措施,从而达到控制制造质量的目的。
下面,我们对6大因素的特点及防误、控制措施分别做一下介绍。
需要强调指出的是,不同产品特点的条件下,工序的主导因素各不相同,因而主要控制措施也不相同,应因地、因产品而已。
1、操作人员的因素往往操作人员的技能和谨慎作风是关键因素,它是产品或零件产生不良的主要原因。
凡是在操作人员起主导作用的工序所产生的不良,一般可以由操作人员控制。
造成操作误差的主要原因有:质量意识差;操作时粗心大意;不遵守操作规程;操作技能低、技术不熟练,以及由于工作简单重复而产生的厌烦情绪等。
防误和控制措施:加强“质量第一、用户第一、下道工序是客户”的质量意识教育,建立健全质量责任制;编写明确详细的操作规程,加强工序专业培训;加强检验工作,适当增加检验的频次;充分利用愚巧法防错;通过工种间的人员调整、工作经验丰富化等方法,消除操作人员的厌烦情绪;广发开展QC小组活动,促进自我提高和自我改进能力。
2、机器设备的因素机器设备是保证工序生产符合技术要求的产品的重要条件之一,尤其是自动化程度较高、有定位装置的设备,它们对于确保工序质量起着决定性的作用。
对于一般通用机器设备来说,机器设备的精度保持性、稳定性和性能可靠性;配合件、传动件的间隙;定位装置的准确性和可靠性等,都直接影响到工序质量特性的波动幅度。
属于机器设备起主导作用的典型工序有:加工中心、自动切削、造型线等。
在这些情况下,工序虽然复制性程度较高,但是,随着时间的推移,由于设备的磨损、升温等情况的发生和变化,质量特性数据会发生较大的变化,甚至在一批产品,都不可避免地会出现不合格品。
因此必须定期检查和校正。
消除此类异常因素的主要控制措施:1)、加强设备维护和保养,定期检测机器设备的关键精度和性能项目,并建立设备关键部位日点检制度,对工序质量控制点的设备进行重点控制。
2)、采用首件检验,核实定位等的调整量。
3)、尽可能根据情况采用愚巧发,以减少对工人调整工作可靠性的依赖。
3、原材料的因素由于产品不同,因而所使用的原材料的类别也会各不相同。
原材料对产品的质量起着主导作用。
主要的控制措施有:1)、在原材料的采购合同中明确规定质量要求;2)、加强原材料的进厂检验和厂内自制产品的工序和成品检验;3)、合理选择供应商,搞好协作厂间的关系,督促供方搞好质量控制。
4、工艺方法的因素工艺方法包括工艺流程的安排、工艺之间的衔接、工序加工手段的选择(加工环境条件、工艺装备配置、工艺参数)和工序加工的指导文件的编制(如操作规程、作业指导书、工序质量分析表)。
工艺方法对工序质量的影响主要来自两个方面:一是制定的加工方法,选择的工艺参数和工艺装备等的正确性和合理性;二是贯彻执行方法的严肃性。
对于成型加工、定程加工的工序来说,例如定长度切削、造型等,工装模具的设计和制作,成型刀具、刃具的制造和刃磨,都直接对工序质量起决定作用。
此外加工的切削速度、切削深度和走刀量等工艺参数的选择;工艺的编排和衔接;工装模具的制造、鉴定和保管;计量器具的选用、鉴定和保管等,也严重地影响着工序质量。
由于不严格贯彻执行工艺方法,违法操作规程,致使大大降低了工序能力,甚至发生重大质量事故和人身安全事故,这不但影响了产品质量和进度,也影响着经济效益。
工艺方法的防误和控制措施:保证定位装置的准确性,严格首件检验,并保证定位中心准确,防止加工特性值数据分布中心偏离公差中心;加强技术业务培训,使操作人员熟悉定位装置和调整方法,尽可能配置显示定位数据装置;加强定形刀具或刀具的刃磨和管理,实行强制更换制度;积极推行控制图管理,以便及时采取措施调整;严肃工艺纪律,对贯彻执行操作规程进行检查和监督;加强工具工装和计量器具管理,切实做好工装模具和计量器具的周期检定工作。
5、测量的因素为了得到准确、可靠的质量数据和质量信息,准确判断原材料、外购外协件、在制品、半成品和成品是否满足规定要求,有必要对测量和实验设备进行严格的控制,确保测量和实验设备的准确可靠。
主要控制措施有:确定测量任务及所要求的准确度,选择适用的、具有所需准确度和精密度能力的测试设备;定期对所有测量和实验设备进行确认、校准和调整;规定校准规程,其内容包括设备类型、编号、地点、校验周期、校验方法、验收标准,以及发生问题时应采取的措施;保存校验记录;发现测量和实验设备未处于校准状态时,立即评定以前的测量和实验结果的有效性,并记入有关文件。
6、环境因素由于生产产品的工序不同,环境条件的内容也不同。
所谓环境,一般指生产现场的温度、湿度、噪音干扰、振动、照明、室内净化和现场污染程度等。
三、过程控制要设置质量控制点设置质量控制点是过程质量控制活动中的一项重要措施和方法。
它具有动态特性,也就是说,随着过程的进行,质量控制点的设置不是永久不变的。
如某环节的质量不稳定因素得到了有效控制,处于稳定状态,这时该控制点就可以撤销;而当别的环节、因素上升成为主要矛盾时,还需要增设新的质量控制点。
1、设置质量控制点应考虑的因素在甚么地方设置质量控制点,需要对产品的质量特性求和制造过程中的各个工序进行全面分析来确定。
一般应考虑以下因素:(1)、对产品的适用性(性能、精度、寿命、可靠性、安全性等)有严重影响的关键质量特性、关键部位或重要影响因素,应设置质量控制点。
(2)、对工艺上有严格要求,对下工序的工作有严重影响的关键质量特性、部位,应设置质量控制点。
(3)、对质量不稳定、出现不合格品多的项目,应建立质量控制点。
(4)、对用户反馈的重要不良项目,应建立质量控制点。
(5)、对紧缺物资或可能对生产安排有严重影响的关键项目,应建立质量控制点。
质量控制点一般可分为长期型和短期型两种,对于设计、工艺要求方面的关键,重要项目是必须长期重点控制的,而对工序质量不稳定、不合格品多或用户反馈的项目、或因为材料供应,生产安排等在某一时期的特殊需要则要设置短期质量控制点。
当技术改进项目的实施、控制措施的标准化等经过一段时间有效性验证有效后,可以相应撤销转入一般的质量控制。
质量控制点还可以搜集大量有用的数据、信息,为质量改进提供依据。
所以,设置质量控制点,加强工序管理是企业生产现场质量管理工作的基础环节。
2、质量控制点的主要职责(1)、设计部门对影响产品适用性的关键质量特性作出判断,并列入质量控制。
(2)、工艺部门根据产品设计和工艺要求确定产品加工过程中应建立的质量控制点。
(3)、将顾客要求(包括法规等)确定的“质量要求”转换为规定的产品“特性”、过程“特性”,工艺技术部门要组织有关人员进行工序分析,在编制作业指导书时就要把质量控制点纳入进去。
(4)、设备、工具和检验部门负责配备有关设备和工装及仪器,并编制设备点检卡。
四、预防系统控制和过程控制的主要职责1、控制实施过程中设计人员的职责设计人员一定要作好前期策划,策划过程要改变以往那种各自为战的作风,每个项目都要跟踪协调到位。
改变以往逐级转序的排队工程,要实行同步工程,每个项目要实现与外部客户同步,与内部客户质保、销售、机修分厂及生产等部门同步。
确定顾客的要求和期望,以提供比竞争对手更好的产品和服务。
促进对所需更改的早期识别,以预防为主为核心,避免后期更改,避免质量问题的重复发生,也可缩短开发周期。
这就要求我们要做好实验设计,保证开发出一个有效的制造系统,以满足顾客的要求、需要和期望。
通过预防产生质量,要求资源的配置能保证工作正确完成,而不是把资源浪费在生产过程中问题的查找和补救上面。
验证的过程要做好跟踪、落实、总结分析实验设计与加工时产生的变差结果。
试验通过后,那就要制定一个理论与实践的综合效果的标准化的作业文件,交付生产单位。
以最低的成本及时提供优质产品,为公司创造更大价值。
2、质量控制点实施过程中过程品管的职责对过程品管员来说,严格按指导书进行检验,检验后将结果尽快告诉操作者,使操作者及时掌握产品质量的状况,并防止操作者继续出现同样的质量问题,要充分认识到检验的作用不仅要把住产品质量关,更重要的是对操作者提供适当的信息,帮助他们及时发现问题,及时解决问题。
(1)、明确质量控制点影响质量特性的主导因素及有关参数,并加以跟踪检测。
(2)、明确质量控制点中工序的检测重点,配合操作工人做好监测和记录,和操作工密切配合,帮助操作工严格执行质量控制点的有关技术文件,帮助他们及时发现异常原因,指导他们尽快采取有效措施。
(3)、熟悉掌握质量控制点的质量要求及检测和试验方法,并按控制规范规定的进行检验严格把关。
研究分析工序能力,预防和消除异常因素,使工序处于稳定状态,对关键部位或关键质量特性值的影响因素,进行重点控制。
(4)、从管结果转变为管因素,实行预防为主,把不合格品消灭在它的形成过程中,做到防患于未然。
(5)、及时掌握必要的信息,并不断和有关人员交流沟通信息,这对较好处理质量问题是必不可少的环节。
(6)、要做好不合格品的管理。
对已经产生的不符合标准的产品要严格管理,对于不合格品要做好记录、标示,按规定给予报废、降级让步、筛选,或按规定程序经核准后,予以返修或回用。
要严格防止以次充好,将不合格品作为合格品处理。
同时对不合格品进行统计分析,查清原因,制定改进措施,争取减少不合格品,预防不合格品重复发生。
(7)、检验员要当好“三员”,并坚持做到“三满意”。
三员,即产品质量的检验员,质量第一的宣传员和生产技术的辅导员。
三满意,即生产服务的态度让操作者满意,检验过的产品让下道工序满意,出厂的产品质量让用户满意。
3、操作工人必须明确自己应履行的职责:每一个操作者都担负着一定的工序加工任务,而操作者的技能和工作质量是影响产品质量的直接因素。
生产工人应认真执行本岗位的质量职责,坚持“质量第一”,以预防为主,自我控制,不断改进的思想和方法,把保证工序加工的符合性质量作为自己必须完成的任务;争取最大限度地提高工序加工的合格率和一次合格率,以优异的工作质量保证产品质量,是下道工序和用户满意。