车身尺寸工程(管理)
汽车开发中尺寸工程的实际应用及未来展望
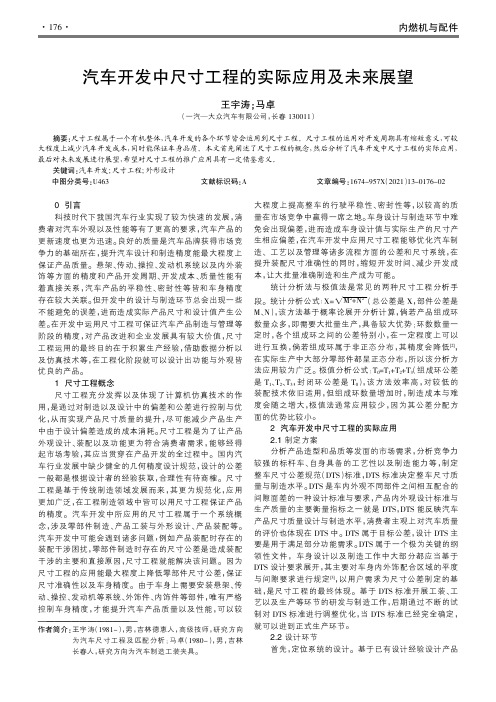
· 176 ·
内燃机与配件
汽车开发中尺寸工程的实际应用及未来展望
王宇涛曰马卓
(一汽—大众汽车有限公司,长春 130011)
摘要院尺寸工程属于一个有机整体,汽车开发的各个环节皆会运用到尺寸工程。尺寸工程的运用对开发周期具有缩短意义,可较
大程度上减少汽车开发成本,同时能保证车身品质。本文首先阐述了尺寸工程的概念,然后分析了汽车开发中尺寸工程的实际应用,
最后对未来发展进行展望,希望对尺寸工程的推广应用具有一定借鉴意义。
关键词院汽车开发;尺寸工程;外形设计
中图分类号院U463
文献标识码院A
ቤተ መጻሕፍቲ ባይዱ
简析汽车白车身尺寸精度控制方法
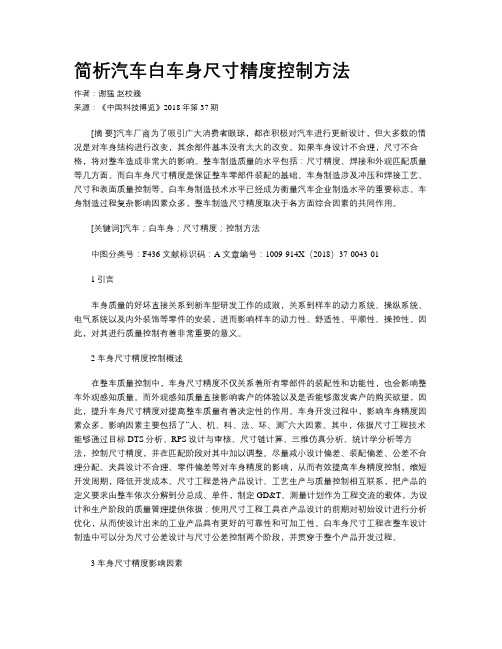
简析汽车白车身尺寸精度控制方法作者:谢猛赵校巍来源:《中国科技博览》2018年第37期[摘要]汽车厂商为了吸引广大消费者眼球,都在积极对汽车进行更新设计,但大多数的情况是对车身结构进行改变,其余部件基本没有太大的改变。
如果车身设计不合理,尺寸不合格,将对整车造成非常大的影响。
整车制造质量的水平包括:尺寸精度、焊接和外观匹配质量等几方面。
而白车身尺寸精度是保证整车零部件装配的基础。
车身制造涉及冲压和焊接工艺、尺寸和表面质量控制等。
白车身制造技术水平已经成为衡量汽车企业制造水平的重要标志。
车身制造过程复杂影响因素众多,整车制造尺寸精度取决于各方面综合因素的共同作用。
[关键词]汽车;白车身;尺寸精度;控制方法中图分类号:F436 文献标识码:A 文章编号:1009-914X(2018)37-0043-011引言车身质量的好坏直接关系到新车型研发工作的成败,关系到样车的动力系统、操纵系统、电气系统以及内外装饰等零件的安装,进而影响样车的动力性、舒适性、平顺性、操控性。
因此,对其进行质量控制有着非常重要的意义。
2车身尺寸精度控制概述在整车质量控制中,车身尺寸精度不仅关系着所有零部件的装配性和功能性,也会影响整车外观感知质量。
而外观感知质量直接影响客户的体验以及是否能够激发客户的购买欲望,因此,提升车身尺寸精度对提高整车质量有着决定性的作用。
车身开发过程中,影响车身精度因素众多。
影响因素主要包括了“人、机、料、法、环、测”六大因素。
其中,依据尺寸工程技术能够通过目标DTS分析、RPS设计与审核、尺寸链计算、三维仿真分析、统计学分析等方法,控制尺寸精度,并在匹配阶段对其中加以调整。
尽量减小设计偏差、装配偏差、公差不合理分配、夹具设计不合理、零件偏差等对车身精度的影响,从而有效提高车身精度控制,缩短开发周期,降低开发成本。
尺寸工程是将产品设计、工艺生产与质量控制相互联系,把产品的定义要求由整车依次分解到分总成、单件,制定GD&T、测量计划作为工程交流的载体,为设计和生产阶段的质量管理提供依据;使用尺寸工程工具在产品设计的前期对初始设计进行分析优化,从而使设计出来的工业产品具有更好的可靠性和可加工性。
汽车尺寸工程学习培训资料
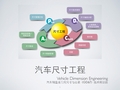
汽⻋车制造业几几何尺寸寸与公差(GD&T)技术培训班
1.1 尺寸寸十十步法
尺寸寸技术规范 尺寸寸管理计划 尺寸寸偏差分析
工工程图纸/ 基准定位策略
稳定性控制/ 经验总结
尺寸寸工工程
测点图
尺寸寸验证 匹配
8
测量系统
尺寸寸数据管理
汽⻋车制造业几几何尺寸寸与公差(GD&T)技术培训班
1.1 尺寸寸十十步法
15
汽⻋车制造业几几何尺寸寸与公差(GD&T)技术培训班
1.1 尺寸寸十十步法
3、尺寸寸偏差分析 输入入
• • • •
输出
• •
尺寸寸 偏差分析
造型 基准定位策略 制造工工艺 制造能力力
±3σ(99.73%) 设计⺫目目标的理 论超差概率
(< 5%)
•
影响因素的权 重
16
汽⻋车制造业几几何尺寸寸与公差(GD&T)技术培训班
1.1 尺寸寸十十步法
2、尺寸寸技术规范(DTS) • 仪表板木木纹条到⻔门内饰板木木纹条的DTS标准。包括左右 方方向的间隙、前后方方向的平整度、左右间隙的一一致性、 上下方方向的直线度。
12
汽⻋车制造业几几何尺寸寸与公差(GD&T)技术培训班
1.1 尺寸寸十十步法
2、尺寸寸技术规范(DTS) • 几几个关键词: • 客户呼声:源自自(a)标杆⻋车的配合状态; (b)市场调查 (c)损益函数 • 间隙(GAP)、平整度(FLUSH)、直线度 (ALIGNMENT) • 平行行度(PARALLEL)、一一致性 (CONSISTENCY)、 • ⻋车身身外饰、空调电子子内饰
1.1 尺寸寸十十步法
• 尺寸寸工工程的定义: - 整⻋车设计的一一部分,致力力于获得最佳的⻋车身身内外饰外 观配合。 - 以尺寸寸技术规范(DTS)为贯穿始终的主线。 - 前期开发阶段(第1到4步)以提出标准为主,包括外 观配合要求以及零件图纸要求,辅以基准定义、偏差 分析、⻛风险评估等工工具。以达到设计合理性为⺫目目的。 - 后期试制阶段(第5到10步)以测量控制为手手段,评 估零件以及整⻋车的尺寸寸表现,以整⻋车匹配达到设计标 准为⺫目目的。
车身尺寸质量的控制方法
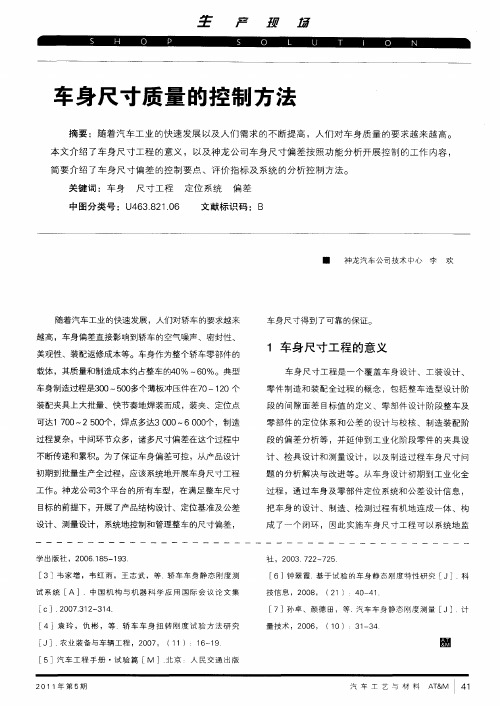
车 身尺 寸 质 量 的控 制 方法
摘要 :随着汽车 工业 的快速 发展 以及人们 需求 的不断提高 ,人们 对车身质量 的要求越来越高 。 本 文介绍 了车 身尺寸工程 的意义 ,以及神 龙公司车 身尺 寸偏差按 照功 能分析开展控 制的工作 内容 , 简 要介绍 了车 身尺寸偏差 的控制要点 、评 价指标及 系统 的分析控 制方法。
(1)车 身焊 接 夹具 是 保证 车 身焊 接精 度 的重 要 因 素
焊 接夹具 的作 用是 保证所 要焊 接零 件 之间 的相 对 位 置和焊 接 件 的尺 寸精 度 ,减 少焊 接过程 中的变形 以 提 高焊 装效 率。 因此 ,车 身焊 接夹具 是 保证车 身焊 接 精度 的最 重 要 的因素 。不 同 的夹具 结构 对零部 件尺 寸 稳定 性 的影 响是不 同 的 ,应 尽早 参 与夹具 方案 设计 , 提 出夹具所 涉及 尺 寸的要 求如 下。
关键 词 :车身 尺寸工程 定 位 系统 偏差 中图分 类号 :U463.821.06 文献标识 码 :B
一 神 龙汽 车公 司技 术中 心 李 欢
随着汽车 工业 的快速发展 ,人们对轿车 的要 求越来 越 高 ,车身偏差直接影 响到轿车 的空气噪声、密封性 、 美观 性、装配返修成本 等。车身作 为整个轿车零部件 的 载体 ,其质量和 制造成 本约 占整车 的40% ~60%。典型 车 身制造过程是300~500多个薄板冲压件在70~1 20个 装配 夹具 上大批量 、快 节奏地焊装而成 ,装夹、定位点 可达 1 700—2 500个 ,焊点 多达3 000~6 000个 ,制造 过程 复杂 ,中间环节众 多 ,诸多尺寸偏差 在这个过程 中 不断传递和 累积。 为了保证 车身偏差可控 ,从产品设计 初期到批量 生产全过程 ,应 该系统地开展 车身尺寸工程 工作 。神龙 公司3个平 台 的所 有车型 ,在 满足整车 尺寸 目标 的前 提下 ,开展 了产 品结构设计 、定位 基准及公差 设计 、测量 设计 ,系统地控 NSn管理整车 的尺寸偏差 ,
车身尺寸工程岗位职责

车身尺寸工程岗位职责车身尺寸工程岗位职责1工作职责:1、车身dts定义、目标设定及尺寸链分解;2、车身匹配尺寸、公差分配;3、车身图纸尺寸审定;4、负责mule/simule car/ep造车设计验证;5、负责竞品车工艺对标及新技术研究。
任职资格:1、本科以上学历,汽车、机械等专业;2、五年以上从事车身冲压工作经验;3、熟悉车身dts定义,尺寸公差gd&t设定、分配及分解及车身结构;4、熟悉整车开发流程;5、设计思路清晰,6、能用英语进行工作交流。
车身尺寸工程岗位职责2职责描述:1、负责制定对应项目的尺寸管理计划;2、进行产品开发过程中车身精度、外观间隙面差的管理,负责完成整车尺寸公差目标(dts)的制定及维护;3、与造型、产品、工艺等部门开展尺寸方案的研究,制定车身及关键内外饰件、分总成的.定位策略、定位基准;4、组织dts风险评估;5、指导产品工程师gd&t图纸发布。
任职要求:1、学历:本科及以上学历2、性别:不限3、专业:汽车类、机械类4、年龄:30及以上5、工作经验:至少5年以上整车厂尺寸分析经验6、资格要求:熟悉整车开发流程;对尺寸工程有较深的理解;熟悉车身、总装工艺编排,了解尺寸链建立过程;对前期设计过程中可能出现的问题做出预判;针对出现的问题能及时组织各方交流讨论;熟悉并运用gd&t图纸各项规范;编写报告并及时上升问题到专业科室/项目层面汇报7、计算机能力:熟练使用办公软件,熟悉常用测量设备的软件应用8、语言要求:普通话9、其他:职业化、目标导向、抗压力强、学习力强。
车身尺寸工程岗位职责3职责描述:负责制定项目整车、白车身及零部件级尺寸公差目标;组织尺寸工程团队完成该项目整车、白车身及零部件级定位基准及公差图纸设计;任职要求:1、本科或以上学历,7年以上大型整车企业相关业务领域工作经验;2年以上团队管理经验;2、熟悉汽车产品开发流程、工艺,熟知汽车构造、理论、前沿技术知识;3、具有很强的协调、管理及决策能力。
☆汽车尺寸工程
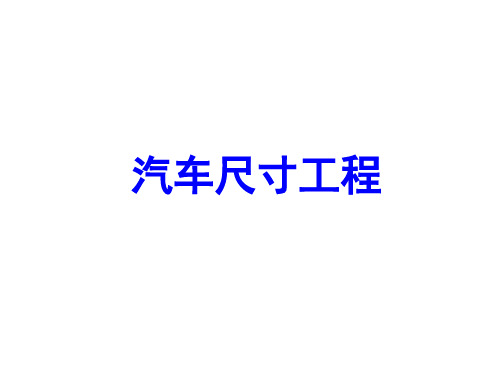
2020/8/9
3
尺寸工程的作用
产品设计
尺寸工程
同步工程
结构分析
工艺/生产
质量控制
◆尺寸工程是连接产品设计和工艺生产、质量控制之间的纽带;
◆尺寸工程将产品的定义要求(如DTS、功能尺寸)分解到分总成、单 件上,制定出统一的工程语言GD&T、测量点计划,为工艺生产、质 量控制提供依据;
◆利用尺寸分析工具(如计算机仿真、统计学知识),在产品设计的前 期进行分析,从而使设计的产品具有更加简便和可靠的加工性能。
在企业内部在流程、体制上还没有明确尺寸工程的作用、地位,没有形成系统管理模式,
缺乏和产品开发周期相对应的流程,没有真正起到设计和工艺沟通的桥梁作用;没有将
供应商纳入主机厂的尺寸管理体系中来,特别缺乏对内外饰、电器、底盘件的尺寸控制;
虽然有先进的计算机辅助软件,但是缺乏熟练运用的人才;在数据统计分析方面没有应
2020/8/9
4
尺寸工程的意义
汽车车身的制造,是一个非常复杂的过程,制造偏差难以 控制,如何在低成本制造的同时,最大程度的保证车身精度和 品质,必须引入尺寸工程。
汽车零部件有几万个,这几万个零部件配合在一起,形成整车,对于整车 而言,任何两个有尺寸关系的零部件之间都有尺寸及公差匹配要求。一般而言, 零部件之间的匹配尺寸无论从设计、生产、检测上都较易保证。例如设计上, 由尺寸链上进行简单的分析就可以确定尺寸,很多绘图软件进行设计时能直接 直观的反映出零部件之间及零部件自身的尺寸关系。而零部件之间的匹配公差 及单件的公差控制,从设计、生产及检测上都较难控制。从设计上讲,由于公 差涉及零件较多,又没有直观的软件进行分析而较难确定。从生产上,如何确 定有效的工艺控制措施,来保证公差要求也是个较难的课题。从检测上看,如 何确定最少的检测点,以实现有效的控制,也需要分析和研究。
汽车尺寸工程师的主要职责

汽车尺寸工程师的主要职责概述汽车尺寸工程师是汽车设计和制造过程中关键的职位之一。
他们负责评估和确定汽车的尺寸、外观和内部空间布局。
他们需要综合考虑诸多因素,如安全性、空间利用、人机工程学等,以确保最终产品满足用户需求和市场竞争力。
分析与设计评估需求汽车尺寸工程师首先要了解市场需求和用户的偏好。
通过市场调研和用户反馈,他们收集数据和信息,以理解目标用户的尺寸偏好和使用场景。
他们还需要考虑竞争对手的产品,并分析市场趋势和未来预测,从而能够为车辆尺寸做出准确的评估和规划。
尺寸规划基于市场需求和产品定位,汽车尺寸工程师制定尺寸规划方案。
他们需要考虑车身长度、宽度、高度、轴距等尺寸参数,并确保其与外观设计、底盘结构和内部空间布局等相互协调。
在制定尺寸规划时,他们还需要考虑安全性、车辆性能和制造成本等因素。
3D建模与仿真汽车尺寸工程师使用计算机辅助设计(CAD)和仿真软件进行三维建模和仿真分析。
他们将尺寸规划转化为数字模型,并对该模型进行各种仿真测试,如碰撞测试、空气动力学分析、雨水排放等。
通过仿真,他们能够评估尺寸设计的合理性、可行性和优化空间。
协调与沟通跨部门合作汽车尺寸工程师需要与其他团队密切合作,如设计团队、工艺工程师和生产部门等。
他们与设计团队协商车辆外观和内饰设计,确保设计美观与尺寸规划一致。
与工艺工程师的合作能确保车辆尺寸在制造过程中的可实施性和一致性。
沟通需求与推动变更汽车尺寸工程师作为技术专家,需要有效沟通自己的设计需求,并推动需要的变更。
他们与产品经理和设计师紧密合作,理解和平衡不同部门的需求,确保最终设计的可行性和市场适应性。
测试与验证集成测试汽车尺寸工程师通过进行集成测试,确保车辆尺寸与其他系统的兼容性。
他们会检测车辆在不同运动状态下的尺寸变化,如悬挂系统工作时的变形、车身刚度和刚性等。
这些测试有助于发现潜在的设计缺陷和解决问题。
室内空间评估汽车尺寸工程师还负责评估和优化车辆的室内空间布局。
关于汽车尺寸工程尺寸链分析方法及流程探究 胡虞刚
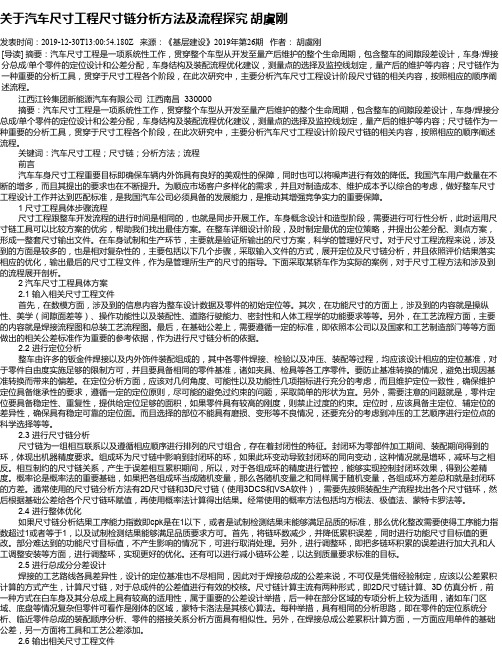
关于汽车尺寸工程尺寸链分析方法及流程探究胡虞刚发表时间:2019-12-30T13:00:54.180Z 来源:《基层建设》2019年第26期作者:胡虞刚[导读] 摘要:汽车尺寸工程是一项系统性工作,贯穿整个车型从开发至量产后维护的整个生命周期,包含整车的间隙段差设计,车身/焊接分总成/单个零件的定位设计和公差分配,车身结构及装配流程优化建议,测量点的选择及监控线划定,量产后的维护等内容;尺寸链作为一种重要的分析工具,贯穿于尺寸工程各个阶段,在此次研究中,主要分析汽车尺寸工程设计阶段尺寸链的相关内容,按照相应的顺序阐述流程。
江西江铃集团新能源汽车有限公司江西南昌 330000 摘要:汽车尺寸工程是一项系统性工作,贯穿整个车型从开发至量产后维护的整个生命周期,包含整车的间隙段差设计,车身/焊接分总成/单个零件的定位设计和公差分配,车身结构及装配流程优化建议,测量点的选择及监控线划定,量产后的维护等内容;尺寸链作为一种重要的分析工具,贯穿于尺寸工程各个阶段,在此次研究中,主要分析汽车尺寸工程设计阶段尺寸链的相关内容,按照相应的顺序阐述流程。
关键词:汽车尺寸工程;尺寸链;分析方法;流程前言汽车车身尺寸工程重要目标即确保车辆内外饰具有良好的美观性的保障,同时也可以将噪声进行有效的降低。
我国汽车用户数量在不断的增多,而且其提出的要求也在不断提升。
为顺应市场客户多样化的需求,并且对制造成本、维护成本予以综合的考虑,做好整车尺寸工程设计工作并达到匹配标准,是我国汽车公司必须具备的发展能力,是推动其增强竞争实力的重要保障。
1 尺寸工程具体步骤流程尺寸工程跟整车开发流程的进行时间是相同的,也就是同步开展工作。
车身概念设计和造型阶段,需要进行可行性分析,此时运用尺寸链工具可以比较方案的优劣,帮助我们找出最佳方案。
在整车详细设计阶段,及时制定最优的定位策略,并提出公差分配、测点方案,形成一整套尺寸输出文件。
在车身试制和生产环节,主要就是验证所输出的尺寸方案,科学的管理好尺寸。
汽车尺寸工程 -尺寸工程公差设计流程

产品部门
尺寸工程 公差设计
工艺部门 生产部门
尺寸工程公差设计是多部门共同协作、参与完成的工作,规范公差设 计流程,有利于协调、梳理好各部门间的工作关系。
GWM-PPT V2012.2
4
范围
GWM-PPT V2012.2
5
范围
范围
该流程阐述了以全新车型开发为模板的新产品开发过程中尺寸工程设 计开展的流程,并为全新车型、局部改型、年度车型的开发提供参考。
CHK011机罩总成
GWM-PPT V2012.2
CHB031机罩总成
14
工作程序
三维偏差仿 真分析
Y
NC阶段GD&T图纸 设计
N
Y
NC阶段GD&T 图纸审核
关键点分析
各分总成、零件公差设计完成后,在NC阶段,进行三维偏差仿真计算, 对单件至总成的公差、RPS进行优化设计,确认最终目标后,由设计公司输 出GD&T图纸,由各专业院、工程院进行审核
尺寸工程公差设计流程
GWM-PPT V2012.2
部 门:上车体平台管理部 讲 师:梁旭昌 课 时:1.5小时 日 期:
GWM-PPT V2012.2
content
目的 范围 术语定义 工作程序
2
目的
GWM-PPT V2012.2
3
目的
目的
本文件依据《尺寸工程设计流程》编写,目的是细化并规范整车尺寸 工程公差设计流程,明确各部门与尺寸工程公差设计相关的职能职责, 明确对应的输入和输出,强化过程控制,统一管理模式,提高工作效率, 降低风险,以确保整车的顺利开发。
GWM-PPT V2012.2
工作程序
GWM-PPT V2012.2
尺寸工程介绍

Sum of Remaining 12 Contributors
15
DM- Dimensional Management
柔性零件偏差分析(EVAS)
• 在三维偏差分析(3-DCS)的基础上融入了有限元的原理来建立数学 模型,充分考虑零件变形,用以分析最终的DTS配合公差。同时还就 焊接工装及检具的夹紧顺序进行分析和改进。 优点:在融入了有限元的原理后,所建立的数学模型与实际零件的状 态最符合,考虑因素最全面。 缺点:建模时间最长,工作量最大。
尺寸项目经理
设计工程师 造型工程师 制造工程师
尺寸工程师
*CBOB:Competitive Best of Best
9
DM- Dimensional Management
尺寸技术规范(DTS)
• • • • DTS图示文件,以图片表达DTS的位置以及具体的要求。 DTS汇总表,以列表的形式来表达DTS,便于统计以及状态跟 踪。 典型断面 统一基准定位策略
质量评估报告
测量设备准备 车身及内外饰零件 在线质量认证 及Launch支持
建立偏差分析模型验算
工艺工程部
生产尺寸数据监控 及数据分析和发布
质量保证部
生成GD&T图纸
不断改进
采购部/供应商
11
DM- Dimensional Management
偏差分析
“输入” • 尺寸管理计划 • 尺寸技术规范 (DTS) –统一基准 定位策略 –估算公差 –工艺及生 产能力 –造型 “输出”
7
DM- Dimensional Management
尺寸管理计划
• 是一种项目管理工具,用以在车辆开发过程中跟踪关键的尺寸工作及 其交付物。 “输入” • 尺寸管理计划 模版
汽车尺寸工程岗位职责

汽车尺寸工程岗位职责汽车尺寸工程师是汽车制造业中一个重要的职位,负责设计和管理汽车的尺寸和外观。
其主要职责如下:1. 尺寸设计:汽车尺寸工程师使用CAD软件进行汽车模型的设计和开发。
他们将根据市场需求、法规要求和制造工艺等因素,确定汽车的整体尺寸和外观。
他们需要考虑到车身长度、宽度和高度,车轴距,轮胎直径等参数,确保汽车在设计和制造过程中符合相关标准。
2. 尺寸优化:汽车尺寸工程师负责对已有车型进行尺寸的优化工作。
他们通过分析市场反馈和竞争车型的尺寸,找出车辆在尺寸方面的优势和不足,并提出改进方案。
他们还会与设计师和工艺工程师密切合作,确保汽车在尺寸上的变化不会对车辆的性能、安全和操控产生负面影响。
3. 材料选择:汽车尺寸工程师需要考虑尺寸和外观对汽车材料的要求。
他们将与材料工程师合作,寻找合适的材料,以满足汽车尺寸方面的要求。
他们需要考虑材料的强度、重量、成本和可加工性等因素,以便在设计过程中做出正确的选择。
4. 法规遵从:汽车尺寸工程师需要了解并遵守相关的法规和标准,包括车身长度、宽度和高度的限制,以及行人保护和碰撞安全等方面的要求。
他们需要确保汽车设计在尺寸方面符合国家和地区的法规,以保证车辆的合法上市和销售。
5. 制造流程管理:汽车尺寸工程师负责管理整个汽车制造工艺中与尺寸相关的流程。
他们需要与制造工程师和生产经理密切合作,确保汽车在设计和制造过程中的尺寸和外观要求得到满足。
他们还需要与供应商和合作伙伴进行沟通和协调,确保零部件的尺寸符合设计要求,并及时解决尺寸方面的问题。
6. 故障分析和解决:在生产和销售阶段,汽车尺寸工程师需要跟踪和分析汽车在尺寸方面的问题,如零部件的尺寸偏差、安装不良等。
他们需要制定相应的解决方案,并与质量工程师和生产团队合作,及时解决尺寸问题,确保车辆的质量和性能。
综上所述,汽车尺寸工程师在汽车制造过程中起着重要的作用。
他们负责汽车尺寸的设计和优化,选择合适的材料,遵守法规和标准,管理制造流程,解决尺寸方面的问题。
第二章.2-车身尺寸工程A
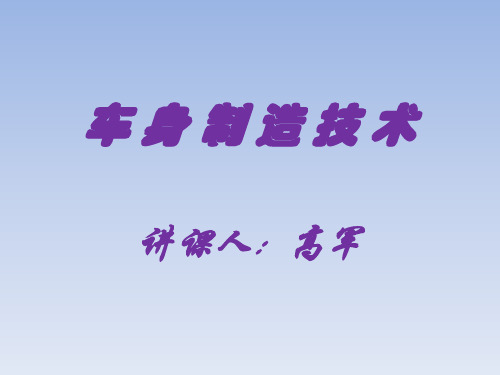
上都要使用RPS点作为支点。 如图所示:
输送装置使用RPS点作为支点
基准点系统
• 合理的定位系统保证了装配的一致性
主定位孔
过孔
副定位孔
31
基准点系统
合理的定位系统保证了装配的一致性
主定位孔 华普车副车架
紧固件用孔
副定位孔
32
翻边孔的应用
承受强度较高的零件 直边长度大于2mm 设置时需要注意料厚方向
特公司。 下面从几个方面对RPS系统作以介绍,以便大家更好地了解
和使用这个系统
二、车身尺寸工程
RPS是德语单词 Referenzpunkt-System (定位点系统)的缩写。
RPS系统就是规定一些从开发到制造、检测直至批量
装车各环节所有涉及到的人员共同遵循的定位点及其公 差与配合的要求。 在确定这些定位点时必须遵循RPS系统的规则,这 一点后面会详细论述。
12
基准点系统
⑹、基准点的特点:
基准点是建立在汽车坐标系中的单位矢量 单位矢量方向尽量与汽车坐标轴重合 每个零件只有一个基准点
所有的基准点以及相关的规定形成了基准点系统
基准点系统是一种标准
RPS点是模具、工装、检具的定位点。为了实现统一的定位技
术规则,必须保证模具、工装、检具都按照RPS点来制造。这一点
1、车身尺寸工程的作用
汽车设计中的基准点系统 定义了产品设计、公差分配、工艺、检测和装配的定位系统 车身公差分配 依据产品外观和功能的要求,并经济地考虑到制造系统的能力, 合理地给零部件制定公差。 统计误差分析 基本统计量、导出量和基本方法 测量系统评估 量具、量仪和检具重复性精度
2、基准点系统
原则的运用。
下图是总成焊接前各零件RPS点的分布情况。
尺寸工程在车身制造过程中的应用
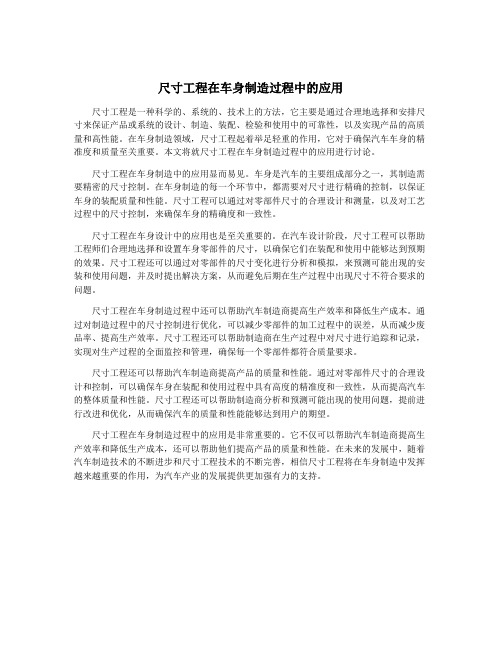
尺寸工程在车身制造过程中的应用尺寸工程是一种科学的、系统的、技术上的方法,它主要是通过合理地选择和安排尺寸来保证产品或系统的设计、制造、装配、检验和使用中的可靠性,以及实现产品的高质量和高性能。
在车身制造领域,尺寸工程起着举足轻重的作用,它对于确保汽车车身的精准度和质量至关重要。
本文将就尺寸工程在车身制造过程中的应用进行讨论。
尺寸工程在车身制造中的应用显而易见。
车身是汽车的主要组成部分之一,其制造需要精密的尺寸控制。
在车身制造的每一个环节中,都需要对尺寸进行精确的控制,以保证车身的装配质量和性能。
尺寸工程可以通过对零部件尺寸的合理设计和测量,以及对工艺过程中的尺寸控制,来确保车身的精确度和一致性。
尺寸工程在车身设计中的应用也是至关重要的。
在汽车设计阶段,尺寸工程可以帮助工程师们合理地选择和设置车身零部件的尺寸,以确保它们在装配和使用中能够达到预期的效果。
尺寸工程还可以通过对零部件的尺寸变化进行分析和模拟,来预测可能出现的安装和使用问题,并及时提出解决方案,从而避免后期在生产过程中出现尺寸不符合要求的问题。
尺寸工程在车身制造过程中还可以帮助汽车制造商提高生产效率和降低生产成本。
通过对制造过程中的尺寸控制进行优化,可以减少零部件的加工过程中的误差,从而减少废品率、提高生产效率。
尺寸工程还可以帮助制造商在生产过程中对尺寸进行追踪和记录,实现对生产过程的全面监控和管理,确保每一个零部件都符合质量要求。
尺寸工程还可以帮助汽车制造商提高产品的质量和性能。
通过对零部件尺寸的合理设计和控制,可以确保车身在装配和使用过程中具有高度的精准度和一致性,从而提高汽车的整体质量和性能。
尺寸工程还可以帮助制造商分析和预测可能出现的使用问题,提前进行改进和优化,从而确保汽车的质量和性能能够达到用户的期望。
尺寸工程在车身制造过程中的应用是非常重要的。
它不仅可以帮助汽车制造商提高生产效率和降低生产成本,还可以帮助他们提高产品的质量和性能。
汽车尺寸工程设计概述
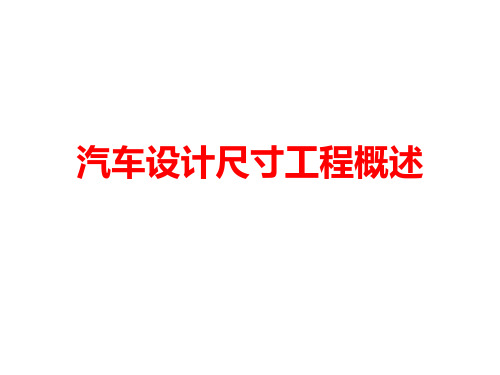
Ø 是一个产品尺寸质量管理的聚焦平台。在这个平台上产品工程师,工 艺工程师,和制造工程师等相互合作共同对产品的尺寸质量和公差进行 分析和优化。
20
五、正向仿真介绍
3DCS分析流程
3DCS
21
五、正向仿真介绍
3DCS软件输出
u 尺寸概率分布
• 采用Monte Carlo 随机数的方法对 定义的输出点估算尺寸变化
Ø 尺寸误差基本是通过装配调整和模具修改来解决,而不是通过尺寸 工程在产品工程化设计,工艺设计前期加以解决的。
26
六、国内外尺寸工程现状介绍
国内尺寸工程当前主要不足
现在尺寸工程还无法支持新车型开发的尺寸工程分析要求, 具体表现在:
Ø 没有明确的尺寸工程分析流程 Ø 不能够为设计提供充分的先期优化筛选方案 Ø 没有准确的几何尺寸与公差工程图标注体系 Ø 不能提供完整的零部件、分总成、总成的几何尺寸与公差工程图 Ø 没有尺寸工程文件指导模具/夹具/检具的设计 Ø 在产品的研发与生产的周期中没有进行必要的尺寸公差分析,对其工程化设计,工艺
24
六、国内外尺寸工程现状介绍
北美尺寸工程基本工作流程
1.主机厂、设计公司、模/夹具供应商共同确定间隙&面差文件
这一步非常重要。主要考虑因素:竞争车型参数、质量目标、模/夹具供应商 的制造精度能力。
2.公差分配计算
GAP&FLUSH文件就是最重要的输入文件。这个工作基本由主机厂来做,也可 以由设计公司来做(需协商夹具公司)。 计算过程:总成公差—子总成公差—零件公差 计算方法:利用统计原理进行公差计算。利用计算机软件、计算方法为Mon Carlo.
尺寸工程将正向设计与逆向设计结合起来,在制造能力一定的情况下, 通过合理的定位基准及公差设计,优化车身结构设计及制造工艺设计,在 满足车身精度的前提下,合理分配公差,最大程度地降低累积公差,降低 制造成本困难。
汽车尺寸工程尺寸链分析方法及流程
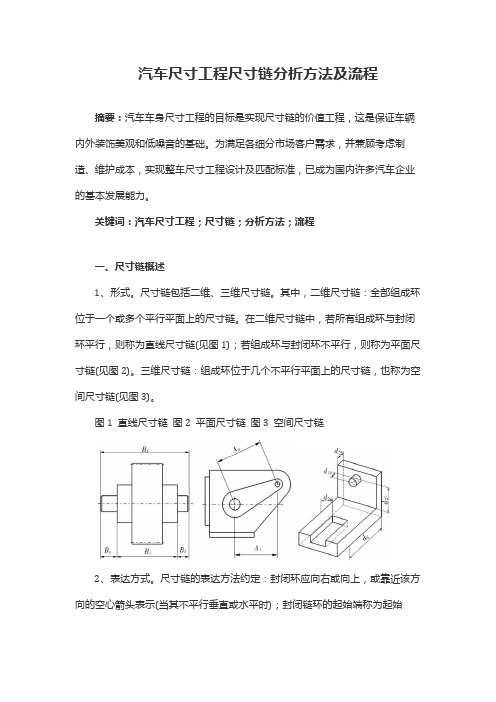
汽车尺寸工程尺寸链分析方法及流程摘要:汽车车身尺寸工程的目标是实现尺寸链的价值工程,这是保证车辆内外装饰美观和低噪音的基础。
为满足各细分市场客户需求,并兼顾考虑制造、维护成本,实现整车尺寸工程设计及匹配标准,已成为国内许多汽车企业的基本发展能力。
关键词:汽车尺寸工程;尺寸链;分析方法;流程一、尺寸链概述1、形式。
尺寸链包括二维、三维尺寸链。
其中,二维尺寸链:全部组成环位于一个或多个平行平面上的尺寸链。
在二维尺寸链中,若所有组成环与封闭环平行,则称为直线尺寸链(见图1);若组成环与封闭环不平行,则称为平面尺寸链(见图2)。
三维尺寸链:组成环位于几个不平行平面上的尺寸链,也称为空间尺寸链(见图3)。
图1 直线尺寸链图2 平面尺寸链图3 空间尺寸链2、表达方式。
尺寸链的表达方法约定:封闭环应向右或向上,或靠近该方向的空心箭头表示(当其不平行垂直或水平时);封闭链环的起始端称为起始面,末端称为到达面;绘制组成环时,从起始面开始,按顺序逐一列出影响因素,并顺序编号,在到达面上形成封闭。
二、尺寸链分析的计算方法1、极值法。
所有组成环公差之和为封闭环的公差。
特点:该方法计算的目标公差考虑了所有组成环的极值状态,简单可靠。
理论上讲,只要每个环的实际偏差在允许范围内,最终封闭环必定超差。
但这种方法也有明显的缺点:即不是所有的组成环都会同时出现极值,计算结果余量太大,也会给后期生产带来麻烦。
2、统计法。
将统计学与组成环的分布形式相结合,计算出封闭环公差。
其优点是根据组成环的实际分布概率进行统计,更接近实际情况。
然而,缺点是概率预测可能不准确,并且在某个封闭环中仍存在超差的可能性。
三、定位分析白车身由许多钣金件焊接、装配而成,每个零件冲压、检验、焊接和装配都需定位基准,以限制其自由度,磨具、检具、夹具各工序零件的基准应尽可能保持一致,以避免基准转换引起的误差。
定位分析应考虑几何角度、功能性和可行性;为保证定位的一致性及继承性,满足3-2-1或N-2-1的定位原则,尽量不要过度约束,所选形状应尽量简单。
整车尺寸工程理论和实战

功能尺寸
整车功能尺寸 车身功能尺寸 零部件功能尺寸
白车身总成 功能尺寸
外覆件功能 尺寸
白车身测点与功能尺寸关系
白车身测点
根据GD&T/Control Drawing的要求, 结合生产工艺,用 于监控、反应产品 和工艺尺寸特性的 测量点
白车身总成功能尺寸
在车身制造过程中 检验和控制车身匹 配质量,以计算测 点之间相对关系的 形式所规定的一系 列尺寸
由于尺寸链中所有零件都处在极限公差的概率非常 小,因此极值法是一种保守的分析方法。在尺寸链 较长的情况下为了保证最终尺寸,会对零件设计过 于严格的公差范围从而导致计算结果失效
均方根法(Root Sum Squares, RSS)
利用方差的可加性,采用方差叠加法对零件 公差进行设计
相比于极值法,均方根法更趋于合理
蒙特卡洛仿真法(Monte-Carlo)
从零件已知的尺寸偏差分布中进行随机采样, 通过已知的零件间的装配关系来求解装配偏差 的统计分布
a ±T1
Part1
3a ±Ttatal a±T2
Part2
a ±T3
Part3
TTatal T1 T2 T3
TTatal T12 T22 T32
VA-正态分布
拟次数
是 输出仿真结果
数模
工装精度 GD&T
Family Tree 测点
VA-三维尺寸模型
结构树
三维模型
模拟视频 单击观看
N-2-1法则
+Z
A1
+Y
A2
+X B1
A3
A1
C A2
B
B2
XY Z X Y Z
A1,A2,A3 Z X Y
汽车尺寸工程技术及应用相关阐述刘洋

汽车尺寸工程技术及应用相关阐述刘洋发布时间:2023-06-22T02:59:54.764Z 来源:《中国科技信息》2023年7期作者:刘洋[导读] 在汽车产品设计制造与生产中,尺寸工程是非常重要的组成部分。
尺寸工程技术的先进与否,运用的得当与否,直接决定了汽车产品的性能与质量。
为此,本文结合实际,对汽车尺寸工程技术及应用相关展开探究阐述,提出有关观点,以供借鉴参考。
身份证号码:34032119830308XXXX摘要:在汽车产品设计制造与生产中,尺寸工程是非常重要的组成部分。
尺寸工程技术的先进与否,运用的得当与否,直接决定了汽车产品的性能与质量。
为此,本文结合实际,对汽车尺寸工程技术及应用相关展开探究阐述,提出有关观点,以供借鉴参考。
关键词:汽车生产制造;尺寸工程;技术应用随着社会经济的发展与收入水平的提高,人们对于汽车的需求越来越大,对汽车的要求也越来越高。
人们越来越注重汽车的质量,而质量是一个综合宽泛的概念,其包含多个方面,也受多种因素影响。
汽车是一个高度集成的产品,内含诸多的零件,每个零件的尺寸都是影响汽车整体质量的要素。
因此在汽车的设计与制造中,要有一定的技术与软件能快速精准地分析尺寸偏差,保证尺寸精度。
下面结合实际,对汽车尺寸工程技术做具体分析。
1汽车尺寸工程技术尺寸工程是从设计到制造的系统化工程,是实现的完善的理论设计到制造阶段的尺寸控制过程,这个过程基于满足预先建立的产品尺寸要求,实现零部件顺利装配,并最终达到预先设定的产品尺寸品质要求【1】。
在汽车产品的设计到制造全过程,尺寸工程贯穿始终。
在汽车设计制造过程中,存在多个会影响整车功能的偏差,如辅助工具偏差、零部件偏差、过程偏差等。
要想保证汽车整车功能的顺利实现,就需要运用相关的标准、技术等对各类偏差进行定义、验证、管理与控制,这个定义、验证、管理与控制的过程就是尺寸工程【2】。
相较于美国、日本等发达国家,我国的汽车尺寸工程起步的较晚,但发展速度较快。
间隙面差在汽车车身尺寸工程中如何控制

间隙面差在汽车车身尺寸工程中如何控制
钱光辉
【期刊名称】《汽车工艺师》
【年(卷),期】2024()4
【摘要】目前,对车身外观间隙面差的测量方法主要是传统的人工检测方法,如利用塞尺。
以悦达起亚间隙面差的管理为例,重点阐述了从开发到量产整个过程间隙面差的控制方法,希望给汽车行业的同行在该方面的应用提供参考。
【总页数】4页(P14-17)
【作者】钱光辉
【作者单位】江苏悦达起亚汽车有限公司
【正文语种】中文
【中图分类】U46
【相关文献】
1.东风天龙车身间隙面差控制
2.DOE在控制汽车AB尾灯的间隙面差问题中的应用
3.车身间隙面差设计及其控制技术
4.浅析设计间隙在车身尺寸控制中的应用
5.基于尺寸工程优化解决车门装配间隙不均与面差问题
因版权原因,仅展示原文概要,查看原文内容请购买。
- 1、下载文档前请自行甄别文档内容的完整性,平台不提供额外的编辑、内容补充、找答案等附加服务。
- 2、"仅部分预览"的文档,不可在线预览部分如存在完整性等问题,可反馈申请退款(可完整预览的文档不适用该条件!)。
- 3、如文档侵犯您的权益,请联系客服反馈,我们会尽快为您处理(人工客服工作时间:9:00-18:30)。
17
基准点系统
基准点:建立在汽车坐标系中零件的定 位点X1、Y1、Z1
Y2
X1-Y1-Z1
Z3
Z2
18
基准点系统
基准点的特点:
基准点是建立在汽车坐标系中的单位矢量
单位矢量方向尽量与汽车坐标轴重合 每个零件只有一个基准点 所有的基准点以及相关的规定形成了基准
点系统 基准点系统是一种标准
点焊翻边的宽度为16 图纸上的翻边(18)- 实际翻 边(16)=2 按照左边的图纸,对翻边宽度 (20)的公差 为 20-2.0
调查是否出现干涉 :若有干涉 将到干涉地点的1/2距离定为 公差
55
二、 对板金翻边指定公差-3
56
二、 对板金翻边指定公差-4
57
二、 对板金翻边指定公差-5
58
直径
序号 1 2 3 4 5 6 7 8 9 95 25+/-0.01 直径分段 24.990-24.992 24.992-24.994 24.996-24.998 24.998-25.000 25.000-25.002 25.002-25.004 25.004-25.006 25.006-25.008 25.008-25.010 频数 2 6 10 16 23 18 12 7 1
34
车身公差分配 1、原则:
依据产品外观和功能的要求,考虑到
制造系统的经济性的制造能力,合理 地给零部件分配公差。
35
车身公差分配
公差分配不合理或不指定公差的后果
如果一份减速机的零件图不指定公差: 零件能装到一起吗?
• 滚动轴承孔和轴配合不符合要求; • 齿轮孔和轴的配合不符合要求; • 箱体两个轴孔的中心距不符合要求; • 。。。。。。 结论是:不负责任的设计!
64
六、 设定孔的公差
若需要设定圆径公差,就采用如下圆径 公差 深度的公差 若在图纸上标定,或者对相应零件已 设定深度的话,不用再设定深度。 按照分析公差的结果来决定
65
六、 设定孔的公差
66
六、 设定孔的公差
67
七、 设定公差综合例子 引擎舱盖 与 翼子钣
68
七、 设定公差综合例子
6 5 4 3 2
+/- 3 +/- 4 +/- 5 +/- 6
1
1
2 3 4 5 6
缺陷(PPM) 2700 63 .57 .002 Cpk 1 1.33 1.67 2
74
Sigma % is “O.K.” 99.73 99.9937 99.999943 99.9999998
B零件的公 差
B零件的 公差
± 0.35 ± 0.7 ± 0.23 ± 0.5 ± 1.0 ± 0.33
± 0.75
± 1.5
± 0.75 ± 0.5 ± 0.5
± 1.06 ± 0.86 ± 0.86
± 1.06 ± 0.86
47
± 0.5
车身公差分配
7、常见的典型应用场合 公差推荐
( 公差手册)
36
车身公差分配
不给车身冲压件或者仪表板指定合理的 公差,结果会如何?
大量地修改冲压模具,
调整夹具;
修改配套件模具 一年以上的质量整改时间 结论是:太昂贵!
37
车身公差分配 2、适用范围
适用于焊接,装配之前的所有零件。
38
车身公差分配 3、具体依据:
以内外观公差为依据; 以功能要求为依据; 以总体技术要求为依据;
76
正态分布 Normal Distribution
数学期望
x
i 1
n
i
n
( xi: 样本参数,n : 样本数量)
方差
2
(x
i 1
n
i
)2 ( xi: 样本参数,n : 样本数量)
n
标准差
cp 设计偏差 UDL LDL 过程偏差 6
过程能力指数
Cp
分析的结果
69
公差分配小结
车身公差分配与一般机械设计公差分配 有相似的部分,也有不同之处 学习公差分配要从特殊到一般 要注意向成熟车型学习 要注意经验的积累 要注意在车身品质培育阶段出现的尺寸 或公差调整行为
70
SPC统计过程控制
统计过程控制(Statistical proess control ) QS9000五大工具之一 APQP, FMEA, MSA, SPC & PPAP
≤1.5
孔 间距
≤ 1.0
≤ 1.0
≤ 0.7
≤ 0.5
* 一般 孔
* 重要 孔
50
一、接合面的公差-1
51
一、接合面的公差-2
52
一、接合面的公差-3
53
二、 对板金翻边指定公差-1
决定翻边宽度:以打焊时起码要
重叠的长度为根据 公差通过从图纸上的尺寸扣除翻 边的尺寸来决定
54
二、 对板金翻边指定公差-2
2
基准点系统
为保证一致性!
3
基准点系统
哪些零件需要定位?
4
基准点系统
所有的零件!
5
基准点系统
紧固不就是定位吗?
6
基准点系统
紧固不等于定位!
7
基准点系统
什么是定位?
8
基准点系统
定位: 限定刚体的六个自由度
Σ F = 0
9
基准点系统
刚体的空间六个自由度
Σ F = 0
10
基准点系统
定位规则:3、2、1 规则
正态分布:Normal Distribution
何以证明或理解过程符合正态分布? 1、过程符合正态分布是经过实际统计数 据证明的
2、我们自己验证:无心磨床磨削零件的 直径符合正态分布
用一台无心磨床磨削100只活塞销,取其 直径为统计量,实测数据见下表:
75
正态分布:Normal Distribution
45
车身公差分配
(2)极限法:
•以概率法难以满足要求时 •多用于要求极为严格的场合
公差=
(A.part)+(B.part)+(C.part)
46
计算公差实例
极限法 外观 公差 A 零件的公差 A 零件的公 差 B零件的公差 C零件的 公差 ± 0.5 ± 0.23 ± 0.23 ± 0.5 ± 0.33 ± 0.33 A 零件的公差 A 零件的公 差 ± 0.5 ± 0.4 ± 0.7 ± 0.58 ± 0.58 ± 0.4 概率法 B零件的公差 C零件的公 差 ± 0.35 ± 0.4 ± 0.7 ± 0.58
Y1,Y2 X1
Z1,Z2,Z3
11
基准点系统
符合定位规则的一面两销方式
Y2
X1-Y1-Z1 Z3
Z2
12
基准点系统
一面两销方式
x,y,z
13
基准点系统
一面两销方式优点:
可靠 容易实现 容易维护
一面两销方式缺点:
精度低
14
基准点系统
符合定位规则的边界方式 边界定位方式优点
71
SPC
用统计法来描述以及评价生产过程 用统计变量来预测过程的发展 用统计法来发现过程中内部参数之间的 关系。 这里仅介绍基本概念和基本统计量的计 算方法
在后面的测量系统里介绍应用实例 过程控制内容不介绍
72
SPC
基本假设是: 被研究的对象服从正态分布。
73
正态分布:Normal Distribution39车身公差分配接合面类:- 打点焊来接合
- 冲压的方式来接合 - 二氧化碳焊接合 - 涂胶面
40
车身公差分配
孔类:
孔的圆径公差 孔的中心位置公差 深度公差 卡扣孔公差 其他: 冲压件裁边公差
41
车身公差分配 4、确定哪些公差?
确定零部件公差 确定模、检、夹具公差
42
车身公差分配
25
基准点系统
大众的RPS系统 VW 010 55
26
基准点系统
定位应用举例:紧固不等于定位!
零件1
零件2
27
基准点系统
由于制造误差造成的安装困难和一致性差
28
基准点系统
合理的定位系统保证了装配的一致性
主定位孔
过孔
副定位孔
29
基准点系统
合理的定位系统保证了装配的一致性
主定位孔
过孔
副定位孔
精度高 可靠性差
边界定位方式缺点:
15
基准点系统
什么是过定位? 采用多于六个定位元素
过定位的原则:只能起到局部控制零部件
形状的作用,不能与主定位元素形成干涉 由于冲压件刚度差,需要过定位 多于六个定位元素的那部分定位称为辅助 定位
16
基准点系统
车身坐标系(国标规定:车辆姿态为满载)
二、 对板金翻边指定公差-6
59
三、一般形状部位的公差-1
60
三、一般形状部位的公差-2
61
四、外部公差
对可能导致回弹,变形的零件,另定处
于自由状态的检查 公差。 用来在检具上测定压件
62
四、外部公差
63
五、裁边公差
①
若裁边公差和翻边的内容相同,就 采用翻遍幅度的公差 ② 若有移动,就采用移动公差表 ③ 一般冲压单件的裁边公差为±1.0 ④ 若无有面临干涉等的可能性,裁边 公差就决定为±1.5, ±2.0