汽车车身内外饰的尺寸工程开发概述
车身部DTS培训课件
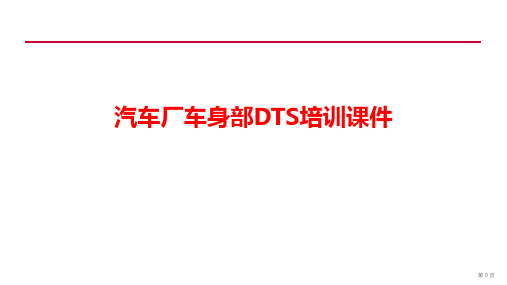
• 前大灯到引擎盖的DTS标准。包 括了上下及左右方向的间隙、间 隙的平行度;前后方向的平整度、 平整度的平行度。如果设计上平 整度非零的话还要定义出哪个零 件低。
第5页
1.1 尺寸十步法
2、尺寸技术规范(DTS) • 仪表板上本体到前门内饰板的 DTS标准。包括左右方向的间隙、 前后方向的平整度、左右间隙的 一致性、上下方向的直线度。
一、尺寸工程的工作流程概述
GD&T
测点图
第 12 页
1.1 尺寸十步法
6、测量系统 定义:在生产过程中具体使用什么设备,如何对零件、总 成、整车进行测量。包括在线和离线两种用方式。 不同的测量设备能提供不同的测量输出,但需要的成本和 时间都不同。在制造规划中,这是用非常重要的环节。 常用用的测量设备:三坐标测量机+测量用支架、检具、 白光扫描、激光扫描、游标卡尺、塞尺等等。
第9页
1.1 尺寸十步法
3、尺寸偏差分析
输入 • 造型 • 基准定位策略 • 制造工艺 • 制造能力
一、尺寸工程的工作流程概述
尺寸 偏差分析
输出 • ±3σ(99.73%) • 设计目标的理 论超差概率 (< 5%) • 影响因素的权 重
第 10 页
1.1 尺寸十步法
一、尺寸工程的工作流程概述
4、工程图纸/基准定位策略 尺寸工程前期开发阶段的最后一步工作,以输出为主。 包括了基准定位策略和工程图纸。
9、尺寸验证 定义:在小批量的匹配验证以及大批量的尺寸数据管理的基础上,大批量地验证零件及DTS的实现状态。
第 16 页
1.1 尺寸十步法
一、尺寸工程的工作流程概述
10、稳定性控制/经验总结 定义:在投产阶段完成所有尺寸验证以后,项目开始进入稳定生产阶段。持续提升制造稳定性,并继 续优化尺寸波动,使其更趋向于设计名义值。同时为新项目的开发做好经验总结。
汽车内外饰结构设计及成型工艺分析

汽车内外饰结构设计及成型工艺分析摘要:汽车内外饰件的设计已成为人们购买汽车时考虑的一个重要因素,对整个汽车行业的发展起着十分重要的作用。
基于此,本文重点论述了汽车内外饰结构设计及成型工艺。
关键词:汽车;内外饰;结构设计;成型工艺汽车生产属于高科技生产工艺,其程序复杂,不仅对内外饰结构设计有所要求,还需精妙的成型工艺。
因此,科学的工程设计能促进更好的人工制造,并与汽车生产的品质和质量密切相关。
所以,为了保证汽车产品的美感和品质,有必要掌握汽车内外饰结构设计的原则和基本内容,从而改善和提高成型技术与水平。
一、汽车内饰概述汽车内饰(AutomotiveInterior)是指汽车内部改装所用到的汽车产品,这部分零部件不光只有装饰作用,其所涉及到的功能性、安全性及工程属性较丰富。
汽车内饰系统是汽车车身的重要组成部分,内饰系统的设计工作量占到车造型设计工作量的60%以上。
车身设计分为造型设计和工程设计两部分,其次就是内饰系统的设计,车身外观覆盖件的设计排在最后。
二、汽车内外饰件的发展现状近年来,汽车几乎成为每家每户的标配,人们在选择汽车时对其内外饰部件提出了更高的要求。
因此,不仅汽车的外观越来越受到用户的关注,而且其内饰也是用户关注的重点。
舒适优美的车内环境无疑能给用户带来更好的使用体验,而汽车内饰也不仅仅是为了赢得用户的视觉青睐。
除了装饰车内空间给用户带来良好的视觉、触觉体验外,更重要的是具备安全性能。
虽然汽车内外饰部件只是汽车组装中的一小部分,但汽车内外饰件的质量和外观将直接影响到汽车给用户带来的整体体验。
因此,汽车零部件的设计水平及专业化生产无疑是提高汽车满意度的科学途径。
内外饰是车身系统的重要部件,它属于车身系统的一大主要零部件组件,与车身壳体、车身附件、座椅等部件共同构成一个完整的车身系统。
内外饰关系到汽车产品的安全、舒适、视觉性。
内外饰分为内饰件和外饰件,内饰件是具有功能性、装饰性的部件,更强调舒适性和视觉性,通常为非金属件。
车身汽车车身设计与开发(完整版)
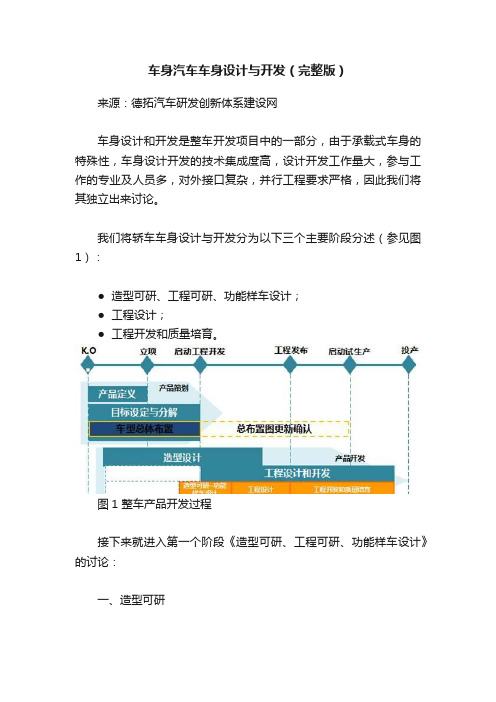
车身汽车车身设计与开发(完整版)来源:德拓汽车研发创新体系建设网车身设计和开发是整车开发项目中的一部分,由于承载式车身的特殊性,车身设计开发的技术集成度高,设计开发工作量大,参与工作的专业及人员多,对外接口复杂,并行工程要求严格,因此我们将其独立出来讨论。
我们将轿车车身设计与开发分为以下三个主要阶段分述(参见图1):●造型可研、工程可研、功能样车设计;● 工程设计;● 工程开发和质量培育。
图1 整车产品开发过程接下来就进入第一个阶段《造型可研、工程可研、功能样车设计》的讨论:一、造型可研当总布置给出了初步控制硬点图、造型给出了内外CAS面(3D数字化表面),车身即要进行造型的可行性研究(简称造型可研)。
业界将造型师称为Designer——设计师,他们是真正的概念和创意的提出者,因而在开发中享有至高的权威。
但是造型师的创意是需要工程实现的,因此作为它的技术支撑——车身部门首先要分析其创意的整体和各个局部实现的方式和代价,即可行性,这一工作就是造型可研。
该阶段车身主要从事几何绘制和分析:—选择相关部件的结构形式(也是车身部件的创意和构想);—绘制部件的断面、确定连接关系、对空间布置进一步细化,即做layout;—将白车身的主要断面放进内外CAS面之间,确定主要断面是否得到了保证;—进行法规满足性分析。
对于几何空间不够,造型元素实现的代价太大,法规不满足等都需要和造型部门协商、调整。
我们以结构选型举例:图2是前格栅的安装方案比较示意。
有安装在发动机罩上,也有安装在保险杠或车身上。
其中安装在机罩上还有嵌入式和与金属板连接式。
这些方案的美学效果、结构重量、制造成本都不一样。
因此类似的结构方案都要和造型敲定,以便造型能实现美学期望并锁定分缝线,车身确定大体结构及安装关系,项目认可成本,商品认可竞争力。
图2 前格栅安装方式对于一个成熟、积累较多经验的车身设计团队,结构选型的过程十分简单。
造型在效果图中表达清楚了,车身及相关部门明确一下是曾经某车的结构沿用就算定了。
内外饰产品设计开发
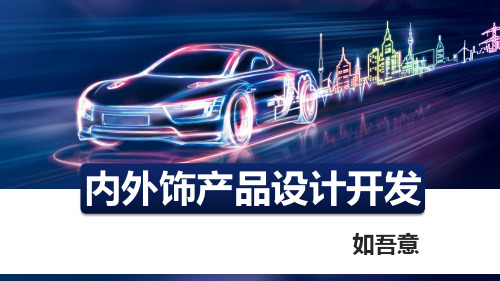
五、内外饰产品开发
1、内外饰产品造型设计开发过程
效果图:造型二 维效果图创意
绘制
效果图第一轮 评审
效果图第二轮 评审
效果图N轮评 审冻结
五、内外饰产品开发
2、内外饰产品造型设计开发过程
三维CAS-B面 数据制作
三维CAS-B面 数据评审-硬质 模型、油泥模
型制作
CAS-B面数据 制作二次评审
三维CAS-B面 数微调制作
பைடு நூலகம்
四、内外饰产品设计
11、内外饰设计流程
注:红色 标注部分 是与内外 饰相关的
五、内外饰产品开发
1、内外饰产品开发流程
上汽研发整车流程
五、内外饰产品开发
2、内外饰产品开发流程
吉利研发整车流程
五、内外饰产品开发
3、内外饰产品开发流程
NPDS与GVDP研发体系流程差异化: 1、NPDS更加强调项目启动之前的分析与研究,在充分调研和分析产品平台化、模块化策略前提下,规划产品群以应对市场竞争。 2、把整车研发体系流程分三大块,项目战略、概念设计、产业化。
内外饰产品设计开发
如吾意
目录
content
01 前言 02 内外饰系统简介 03 内外饰常用材料及工艺 04 内外饰产品设计 05 内外饰产品开发
一、前言
一、 本讲义主要介绍了内外饰产品设计开发中的一些基础知识,为刚入职同事需要了解内 外饰产品设计开发基础知识的同事提供一个借鉴和参考,让新同事更快更好的投入到工作中 来!
12.30 造型冻结
8 15 22 29 7 14 21 28 4 11 18 25 2 9 16 23 30
4.30 工程设计冻结
造型阶段
质量 阀
汽车内外饰件设计开发概述
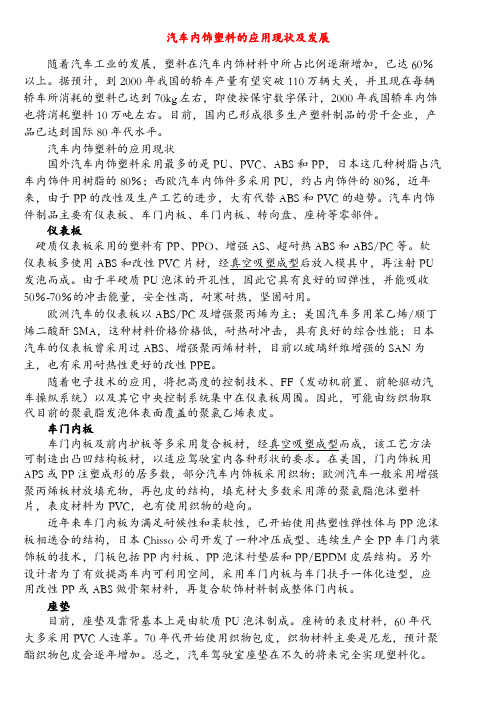
汽车内饰塑料的应用现状及发展随着汽车工业的发展,塑料在汽车内饰材料中所占比例逐渐增加,已达60%以上。
据预计,到2000年我国的轿车产量有望突破110万辆大关,并且现在每辆轿车所消耗的塑料已达到70kg左右,即使按保守数字保计,2000年我国轿车内饰也将消耗塑料10万吨左右。
目前,国内已形成很多生产塑料制品的骨干企业,产品已达到国际80年代水平。
汽车内饰塑料的应用现状国外汽车内饰塑料采用最多的是PU、PVC、ABS和PP,日本这几种树脂占汽车内饰件用树脂的80%;西欧汽车内饰件多采用PU,约占内饰件的80%,近年来,由于 PP的改性及生产工艺的进步,大有代替ABS和PVC的趋势。
汽车内饰件制品主要有仪表板、车门内板、车门内板、转向盘、座椅等零部件。
仪表板硬质仪表板采用的塑料有PP、PPO、增强AS、超耐热ABS和ABS/PC等。
软仪表板多使用ABS和改性PVC片材,经真空吸塑成型后放入模具中,再注射PU 发泡而成。
由于半硬质PU泡沫的开孔性,因此它具有良好的回弹性,并能吸收50%-70%的冲击能量,安全性高,耐寒耐热,坚固耐用。
欧洲汽车的仪表板以ABS/PC及增强聚丙烯为主;美国汽车多用苯乙烯/顺丁烯二酸酐SMA,这种材料价格价格低,耐热耐冲击,具有良好的综合性能;日本汽车的仪表板曾采用过ABS、增强聚丙烯材料,目前以玻璃纤维增强的SAN为主,也有采用耐热性更好的改性PPE。
随着电子技术的应用,将把高度的控制技术、FF(发动机前置、前轮驱动汽车操纵系统)以及其它中央控制系统集中在仪表板周围。
因此,可能由纺织物取代目前的聚氨脂发泡体表面覆盖的聚氯乙烯表皮。
车门内板车门内板及前内护板等多采用复合板材,经真空吸塑成型而成,该工艺方法可制造出凸凹结构板材,以适应驾驶室内各种形状的要求。
在美国,门内饰板用APS 或PP注塑成形的居多数,部分汽车内饰板采用织物;欧洲汽车一般采用增强聚丙烯板材放填充物,再包皮的结构,填充材大多数采用薄的聚氨脂泡沫塑料片,表皮材料为PVC,也有使用织物的趋向。
整车(内外饰)开发流程

产品开发流程
思路+理念 这一阶段主要实为了把设计师的
用更细腻的手法表现出来,加入细节描绘和色彩
通过精致的绘画表达这款车的直观感受和立体效果。这是汽车设计的重要环节之一。
21/50
二、P2节点介绍
产品开发流程
观感评估:1/5油泥模型制作
虽然现代科技技术发达,但是制作油泥模型依然是汽车设计生产中必 要环节,这是一种类似橡皮泥的黏土,但是更加坚硬,成型后的细节需要 用刀刮削才能完成。一般先要制作比例小的油泥模型作为提案,通常由设 计师亲自操刀,大约两三个月才能最后完工。
一、总体介绍
产品开发流程
整车项目新产品开发分类
l 平台开发:开发全新的平台,全新整车造型、系统结构、 配置、布置的整车项目。例如:B、S、T平台
l车型开发:在已有平台的基础上,全新整车造型和布置, 通常选用已开发成熟的零部件,对整车系统结构进行改动的 整车项目。例如:B14、S12
l变型开发:保留平台,通过局部改变造型和布置,选用 已开发成熟的零部件对车型进行小范围改动的整车项目。例 如:B11+2.0MT、S12 +1.1MT、 S12 +1.3MT+RHD
P0、P1、P2、P3、P4、P5、P6、P7、P8、P9
① 节点定义 ② 标志物定义 ③ 示意图 ④ 供应商介入要点
19/50
二、P2节点介绍
产品开发流程
节点编号 P2 节点名称 项目工程启动
项目组织机构成立、项目网计划制定、项目目标框架
①
建立,项目策划完成;内外油泥模型已经冻结,标志前期
整车开发结束和项目工程开始正式启动;产品技术方案的
节点定义 可行性分析结束;结构定义明确且经过总体工艺可行性分
02尺寸工程概述
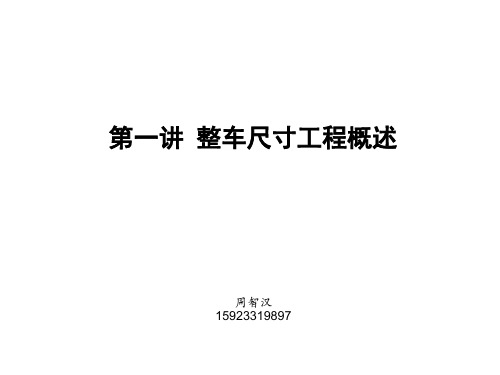
尺寸工程是支撑精致工艺的基础工程领域,是一项系统的工程,国外的汽车公司通过漫长的造车历程已经 系统掌握。国外汽车企业现阶段没有庞大的尺寸工程部门,因为尺寸工程已经体系化,体现在流程、标准、 规范、数据库及工程师的技术素养等各个环节中。
国外汽车企业(通用、福特等)研发板块现阶段专 职尺寸工程师较少,系统及零部件级的尺寸公差设 计均由产品工程师完成,尺寸工程师的主要职责是 整车级外观尺寸、性能尺寸及装配尺寸的集成和风 险控制。
二、国内汽车尺寸工程领域的现状和发展趋势
2.1 国内现状
目前,国内汽车企业尺寸业务可分为两种模式:
1、合资企业模式: 数据库支持:工程师经验丰富,整车尺寸开发(设计)一次设计对程度较高,产品图质量高; 平台化支持:产品设计及工艺开发形成模块化,尺寸设计环节风险较低; 本土化尺寸控制团队强大:结合中国汽车制造综合环境及供应商质量管理能力,所有合资主机厂在试生 产及投产启动阶段尺寸管控手段齐全(含机构、人员配置等)。 2、自主品牌模式: 数据库支持:未形成有效的尺寸开发(设计)数据库,产品图质量差,尺寸设计风险非常多; 平台化支持:平台化、模块化未形成,典型的产品结构、工艺策略、尺寸控制策略未有效形成; 投产启动阶段:缺乏系统的尺寸管理体系。
福特、通用、大众、丰田等
整体情况:正在起步
整体情况:体系成熟
尺寸精细化设计
1、造型家族化正在起步 2、平台化、模块化、经典结构(工艺)应用处 在早期 3、整车尺寸公差集成设计体系(含公差验证) 正在搭建 4、零部件2D图(GD&T)精细化设计正在推动
侧面外观尺寸
前端外观尺寸
尾端外观尺寸
门板区域外观尺寸
IP区域外观尺寸
一、汽车尺寸工程研究的内容
浅谈尺寸工程在汽车开发中的应用
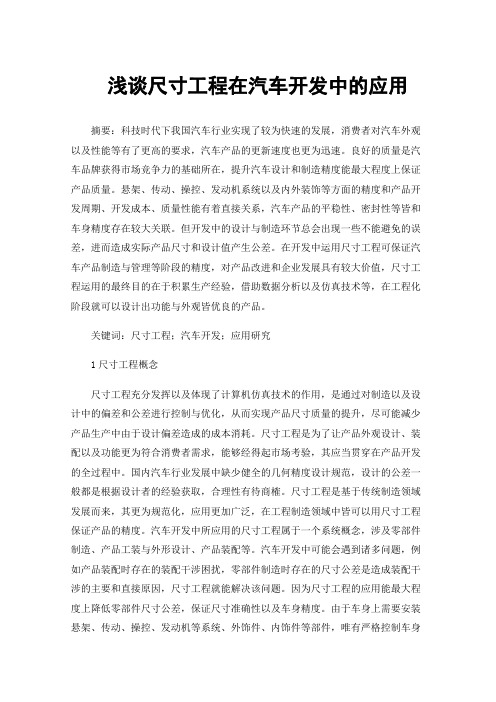
浅谈尺寸工程在汽车开发中的应用摘要:科技时代下我国汽车行业实现了较为快速的发展,消费者对汽车外观以及性能等有了更高的要求,汽车产品的更新速度也更为迅速。
良好的质量是汽车品牌获得市场竞争力的基础所在,提升汽车设计和制造精度能最大程度上保证产品质量。
悬架、传动、操控、发动机系统以及内外装饰等方面的精度和产品开发周期、开发成本、质量性能有着直接关系,汽车产品的平稳性、密封性等皆和车身精度存在较大关联。
但开发中的设计与制造环节总会出现一些不能避免的误差,进而造成实际产品尺寸和设计值产生公差。
在开发中运用尺寸工程可保证汽车产品制造与管理等阶段的精度,对产品改进和企业发展具有较大价值,尺寸工程运用的最终目的在于积累生产经验,借助数据分析以及仿真技术等,在工程化阶段就可以设计出功能与外观皆优良的产品。
关键词:尺寸工程;汽车开发;应用研究1尺寸工程概念尺寸工程充分发挥以及体现了计算机仿真技术的作用,是通过对制造以及设计中的偏差和公差进行控制与优化,从而实现产品尺寸质量的提升,尽可能减少产品生产中由于设计偏差造成的成本消耗。
尺寸工程是为了让产品外观设计、装配以及功能更为符合消费者需求,能够经得起市场考验,其应当贯穿在产品开发的全过程中。
国内汽车行业发展中缺少健全的几何精度设计规范,设计的公差一般都是根据设计者的经验获取,合理性有待商榷。
尺寸工程是基于传统制造领域发展而来,其更为规范化,应用更加广泛,在工程制造领域中皆可以用尺寸工程保证产品的精度。
汽车开发中所应用的尺寸工程属于一个系统概念,涉及零部件制造、产品工装与外形设计、产品装配等。
汽车开发中可能会遇到诸多问题,例如产品装配时存在的装配干涉困扰,零部件制造时存在的尺寸公差是造成装配干涉的主要和直接原因,尺寸工程就能解决该问题。
因为尺寸工程的应用能最大程度上降低零部件尺寸公差,保证尺寸准确性以及车身精度。
由于车身上需要安装悬架、传动、操控、发动机等系统、外饰件、内饰件等部件,唯有严格控制车身精度,才能提升汽车产品质量以及性能,可以较大程度上提高整车的行驶平稳性、密封性等,以较高的质量在市场竞争中赢得一席之地。
- 1、下载文档前请自行甄别文档内容的完整性,平台不提供额外的编辑、内容补充、找答案等附加服务。
- 2、"仅部分预览"的文档,不可在线预览部分如存在完整性等问题,可反馈申请退款(可完整预览的文档不适用该条件!)。
- 3、如文档侵犯您的权益,请联系客服反馈,我们会尽快为您处理(人工客服工作时间:9:00-18:30)。
三维尺寸偏差分析(3-DCS)
通过专业软件在计算机三维空间中模拟零件之间的装配,建立数学模型, 用以分析最终的DTS配合公差。 优点:能在三维空间中模拟零件的平移、转动,考虑因素比较全面,分析 结果更接近实际情况。分析过程是完全模拟实际装车顺序,零件状态根据 输入的公差范围随机选取。
缺点:将所有零件默认为刚体,无法考虑装配变形、焊接变形、热胀冷缩 等因素对最终配合的影响。建模时间较长,工作量较大。
汽车车身内外饰的尺寸工程开发概述
内容
• 为什么关注尺寸设计 • 尺寸设计的过程 • 应用实例
汽车车身开发研究的一些主题
整车 安全性
轻轻整量量车化化
整车 刚度
人机 工程
造型 设计
油耗 / 重量
可制 造性
整车 耐久性
车辆动 力学
热与气 动力学
轻精尺致寸量工设艺化计性
振动 噪声
典型研究
新近研究
客户满意度模型(Kano Model )
Head Lamp to Turn Lamp Upper C/C Gap
DTS/CVS/BTS_# 60.4:01.02.05
Samples
989
No Builds (Incl)
11
Nominal
6.00
Mean
5.99
Median
6.00
Std Dev
1.02
Cp
0.65
Cpk
0.65
Est Min
•DTS图示文件,以图片表达DTS的位置以及具体的要求。 •DTS汇总表,以列表的形式来表达DTS,便于统计以及状态跟踪。 •典型断面 •统一基准定位策略
前大灯到引擎盖的DTS标准。包括 了上下及左右方向的间隙、间隙的 平行度;前后方向的平整度、平整 度的平行度。如果设计上平整度非 零的话还要定义出哪个零件低。
• 性能
• 油耗
• 外观造型
• 精致工艺性
• 价格
• 安全
• 空间
• 质量/可靠性
低
• 舒适
• 驾驶乐趣
• 售后服务
• 高科技
• 环保
• ……
客户满意
欣喜
愉悦质量
性能质量
高
程度
怒气
基本质量
追求最佳的车身 内外饰外观配合
整车尺寸评估
尺寸设计
尺寸技术规范 (DTS)
基准定义、偏差 分析、风险评估
技术要求 ----------------
装车策略 工程图纸要求 均衡后的DTS
测量系统
工程设计初始
尺寸设计
工程设计完成
白车身图纸要求 大总成图纸要求 小总成图纸要求 单个零件图纸要求
尺寸工程的基本工作流程
1. 尺寸管理计划 2. 尺寸技术规范(DTS) 3. 偏差分析 4. 图纸(GD&T)要求 5. 测量点 6. 测量系统 7. 匹配 8. 测量数据的收集及分析 9. 整车尺寸状态评判 10. 持续改进
制造工程师
“输出”
一维尺寸偏差分析 (1-DCS)
三维尺寸偏差分析 (3-DCS)
柔性零件偏差分析 (EVAS)
尺寸技术规范 (DTS)风险报告
改进措施
偏差分析的实质
通过计算机建立偏差分析模型的过程实质上就是模拟装车的过程, 模拟装车过程中的波动因素。
分析间隙或平整度,一般考虑的有:
• 零件的面轮廓度; • 零件定位基准的尺寸公差; • 零件的安装误差,包括平移和转动; • 零件的安装变形,例如重力因素、焊接等。
造型 DTS模版 制造能力 初步的零件定位、
公差及偏差分析
团队工作
设计工程师 尺寸工程师
尺寸项目经理
造型工程师 制造工程师
*CBOB:Competitive Best of Best
“输出”
DTS图示文件及汇 总表(整车技术 标准的一部分)
在典型断面中表示 出来
发布初步的整车测 量表格
尺寸技术规范(DTS)
优化/平衡区域
= Initial = Optimized
11
2
4
75 6
3
5 7
11 4
6 52
37
3
4
2
6
3 2 4 6
一维尺寸偏差分析(1-DCS)
通过模拟零件在单一主线方向下的平移及尺寸偏差来建立数学模型,用以 分析最终的DTS配合公差 •优点:建模方法简单,分析迅速,能快速地得到想要的分析结果。 •缺点:仅考虑了零件在单一主线方向的平移,考虑因素不完全。当零件 尺寸较长,尺寸链较长的时候与实际情况偏离较大。
2.92
Est Max
9.07
Est Range(99.7%) 6.15
Est %Below
2.59
Est % Above
2.51
Est % Out
5.09 Y
SAMPLES
100 90 80 70 60 50 40 30 20 10 0
3.0
LSL
NORMAL
4.0
4.0 5.0 6.0 7.0
USL 8.0
8.0 9.0
TurnLamp
Upr_Gap
HeadLamp
Sensitivity Analysis
Total Variance 1.0496
Part
Point
Tolerance
1 Brackefile Tolerance at Upper Outer Surface
2 Bracket
turn_fa
Bracket_x
Profile Tolerance at Upper Inner Surface
3 Head_Lamp
lmp_upr
hlmp_y
Profile Tolerance at Upper Gap
Program Name
3D Analysis
NACG Dimensional Engineering Analysis
Compartment Name Model Date
Name
Upr_Gap
Type
Distance Between turn_upr and lmp_upr
Description
仪表板木纹条到门内饰板木纹条的 DTS标准。包括左右方向的间隙、 前后方向的平整度、左右间隙的一 致性、上下方向的直线度。
偏差分析
“输入”
尺寸管理计划 尺寸技术规范
(DTS) • 统一基准定 位策略 • 估算公差 • 工艺及生产 能力 • 造型
团队工作
偏差分析工程师
尺寸工程师 设计工程师
集成供应商
尺寸管理计划
是一种项目管理工具,用以在车辆开发过程中跟踪关键的尺寸工作及其交 付物。
“输入”
团队工作
“输出”
尺寸管理计划模版 项目时间计划 项目内容 经验教训
项目团队
尺寸项目经理
基于项目时间 节点的尺寸 工作计划, 尺寸交付物
工作跟踪表
尺寸工程经理
尺寸技术规范(DTS)
“输入”
顾客呼声 • 标杆车 • 市场调查 • CBOB*