实验一电偶腐蚀
电偶腐蚀速度的测定

实验三:电偶腐蚀速度的测定一、试验目的:1.掌握电偶腐蚀测试原理;2.掌握电极电位、耦合电流的测量方法;3.掌握实验分析方法。
二、实验原理:当两种金属或合金相接触在溶液中可以发现在该液中电,位较负的金属腐蚀速度加大,而电位较正的金属受到保护,这种现象就是电偶腐蚀。
金属或合金制成电极,应用电偶腐蚀计测量,便可测定其各个电极开路电位,耦合电位,回路电流等值。
三、仪器药品电偶腐蚀计,金属电极(Fe,紫铜,黄铜),饱和甘汞电极,烧杯,量筒,天平砂纸,滤纸,酒精棉,pH试纸,NaCl,四、实验内容及步骤1.将各电极用水砂纸打磨光亮,用酒精棉擦干待用;2.配制100毫升3%NaCl溶液,连接电偶腐蚀计线路;3.测定各电极在3%NaCl溶液中相对于石墨电极的自腐蚀电位,填入表格;4.测Fe-紫铜和黄铜-紫铜电偶电流随时间的变化待电极自腐蚀电位稳定后接通电路,测定电偶电流随时间的变化情况,直到电流比较稳定时为止,测量耦合电极相对于参比电极的电位。
电偶电流最初随时间变化较快,可适当缩小记录时间间隔,15秒或半分钟计一次数。
五、实验数据及结果处理1.所有测量数据记录于表格中自腐蚀电位:Fe:-0.595V 黄铜:-0.208V 紫铜:-0.192V耦合电位:Fe-紫铜:-0.552V 黄铜-紫铜:-0.218VFe-紫铜电偶电流随时间变化黄铜-紫铜电偶电流随时间变化2.将Fe-紫铜和黄铜-紫铜电偶电流随时间的变化绘制在同一张图中;Ig/mAt (s)3.结果及讨论1.测量个电极开路电位时,其电位一直浮动不定,这是由于金属表面的极化和由于阴、阳极反应生成表面膜或腐蚀产物的影响。
2.两金属电极电位差越大,其测量电流Ig越大,试验中Fe-紫铜电偶为-0.552V,大于紫铜-黄铜电偶的耦合电位,所以其测量的Ig也大于后者。
3.随着反应的进行,Ig均随时间而减小,反应初始时Ig下降迅速,之后,随着极化的进行,由于电极外侧生成钝化膜等原因,电流都逐渐减小,之后趋于平稳,中间也有波动起伏的过程。
电偶腐蚀
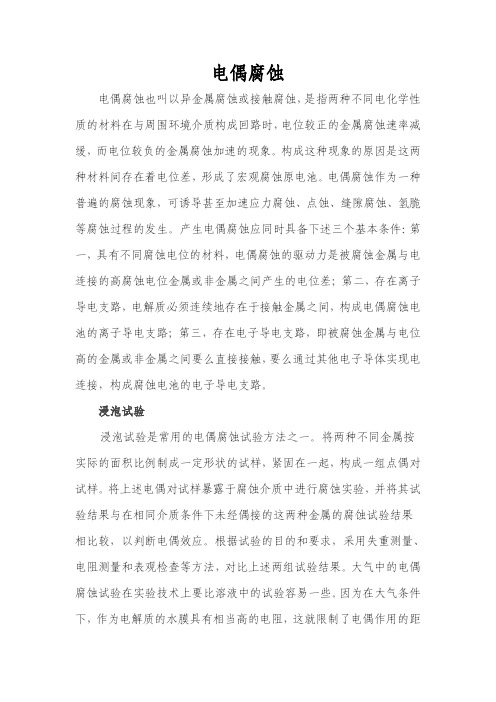
电偶腐蚀电偶腐蚀也叫以异金属腐蚀或接触腐蚀,是指两种不同电化学性质的材料在与周围环境介质构成回路时,电位较正的金属腐蚀速率减缓,而电位较负的金属腐蚀加速的现象。
构成这种现象的原因是这两种材料间存在着电位差,形成了宏观腐蚀原电池。
电偶腐蚀作为一种普遍的腐蚀现象,可诱导甚至加速应力腐蚀、点蚀、缝隙腐蚀、氢脆等腐蚀过程的发生。
产生电偶腐蚀应同时具备下述三个基本条件:第一,具有不同腐蚀电位的材料,电偶腐蚀的驱动力是被腐蚀金属与电连接的高腐蚀电位金属或非金属之间产生的电位差;第二,存在离子导电支路,电解质必须连续地存在于接触金属之间,构成电偶腐蚀电池的离子导电支路;第三,存在电子导电支路,即被腐蚀金属与电位高的金属或非金属之间要么直接接触,要么通过其他电子导体实现电连接,构成腐蚀电池的电子导电支路。
浸泡试验浸泡试验是常用的电偶腐蚀试验方法之一。
将两种不同金属按实际的面积比例制成一定形状的试样,紧固在一起,构成一组点偶对试样。
将上述电偶对试样暴露于腐蚀介质中进行腐蚀实验,并将其试验结果与在相同介质条件下未经偶接的这两种金属的腐蚀试验结果相比较,以判断电偶效应。
根据试验的目的和要求,采用失重测量、电阻测量和表观检查等方法,对比上述两组试验结果。
大气中的电偶腐蚀试验在实验技术上要比溶液中的试验容易一些。
因为在大气条件下,作为电解质的水膜具有相当高的电阻,这就限制了电偶作用的距离,从而限制了相对面积作用,即使是最不相容的金属,电偶作用也仅限于对接触线附近的5~6mm处。
电位测量电位测量包括电偶对中各个金属本身的自然腐蚀电位测量、偶对金属的电位差测量和金属偶接后的电偶电对测量。
电位测量是研究电偶腐蚀的重要手段,测试简单易行。
不同金属在接近实际使用介质条件下所测得的稳定开路电位的高低,标志着它们在该特定环境下相对的热力学稳定性。
因此,可根据开路电位的测量结果,预测不同金属偶接后的电偶效应。
在某些情况下,按金属在特定介质中稳定电极电位排列的电偶序中两种金属之间间隔远近来大致表征电偶效应的相对大小。
金属材料的电偶腐蚀及其防护技术研究进展

金属材料的电偶腐蚀及其防护技术研究进展摘要:金属材料腐蚀现象随处可见,电偶腐蚀是金属材料的一种特殊腐蚀形式,不仅会导致金属材料使用寿命下降,加快金属构件失效,还会引发其他一系列局部腐蚀行为,具有严重的破坏性。
本文主要对金属材料电偶腐蚀问题及其防护技术进行了总结,为电偶腐蚀防护技术研究提供了新方向。
关键词:金属材料;电偶腐蚀问题;防护技术;研究新方向引言在日常生活中金属材料的腐蚀随处可见,腐蚀不仅影响能源科技、医疗器械、国防安全以及一系列新兴产业的发展等,也造成严重的经济损失和带来不可忽视的安全危害。
据统计,我国每年因腐蚀问题造成的经济损失约占全国GDP的3%。
因此,研究金属材料的腐蚀问题,探索金属材料的防腐新技术具有重要现实意义。
一、异种材料电偶腐蚀研究钢结构桥梁、船舶、风电行业中结构轻量化设计广受欢迎,特别是航空航天领域对轻质铝合金、钛合金以及碳纤维增强复合材料等应用广泛,电偶腐蚀是导致连接结构件或复合材料损伤的主要原因之一。
近年来,一些新型研究方法如丝束电极技术(WBE)、扫描振动参比电极(SVET)、扫描开尔文探针技术(SKP)等微区电化学测量技术被运用到电偶腐蚀实验研究中。
利用扫描开尔文探针技术测量AZ91D镁合金与不同偶对材料表面电位变化来研究镁合金电偶对在盐雾实验中电偶腐蚀规律,结果发现电偶腐蚀区域主要集中AZ91D镁合金的一侧,电偶腐蚀效应与偶对材料电位差成正比关系,材料表面腐蚀产物的积累覆盖对基体材料腐蚀起到一定保护作用。
相比于传统电化学测试方法,微区电化学测量技术可以得到准确、详细的局部区域电偶腐蚀情况,有利于从微观层次了解电偶腐蚀机理。
采用有限元或边界元分析等数值模拟仿真技术,建立电偶腐蚀预测模型,分析金属或合金材料间接触区域的电偶腐蚀行为。
采用电化学方法研究在1mol/L盐酸溶液中碳钢端板材料(20MnCr5、42CrMo4和32CrMoV13)与3种低合金钢螺栓(M12、M16和M20)的电偶腐蚀行为,并对端板与螺栓构件接触区的腐蚀参数进行数值模拟分析,可预测设备零部件使用寿命。
电偶腐蚀测试方法介绍
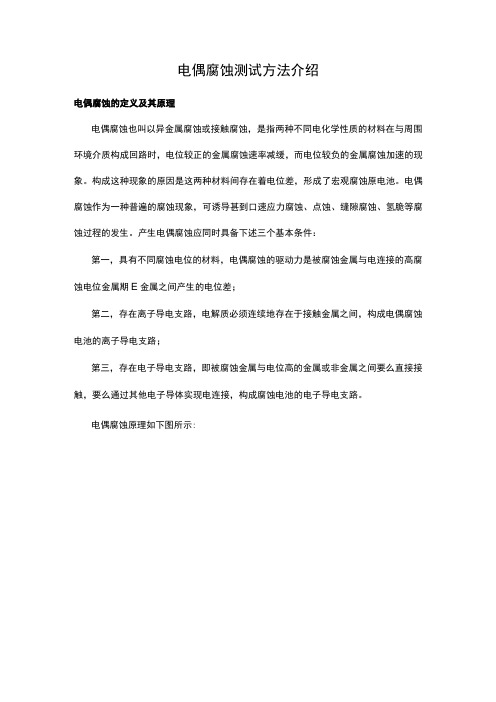
电偶腐蚀测试方法介绍电偶腐蚀的定义及其原理电偶腐蚀也叫以异金属腐蚀或接触腐蚀,是指两种不同电化学性质的材料在与周围环境介质构成回路时,电位较正的金属腐蚀速率减缓,而电位较负的金属腐蚀加速的现象。
构成这种现象的原因是这两种材料间存在着电位差,形成了宏观腐蚀原电池。
电偶腐蚀作为一种普遍的腐蚀现象,可诱导甚到口速应力腐蚀、点蚀、缝隙腐蚀、氢脆等腐蚀过程的发生。
产生电偶腐蚀应同时具备下述三个基本条件:第一,具有不同腐蚀电位的材料,电偶腐蚀的驱动力是被腐蚀金属与电连接的高腐蚀电位金属期E金属之间产生的电位差;第二,存在离子导电支路,电解质必须连续地存在于接触金属之间,构成电偶腐蚀电池的离子导电支路;第三,存在电子导电支路,即被腐蚀金属与电位高的金属或非金属之间要么直接接触,要么通过其他电子导体实现电连接,构成腐蚀电池的电子导电支路。
电偶腐蚀原理如下图所示:图1电偶腐蚀原理示意图电偶腐蚀测试的意义及应用领域电偶腐蚀存在于众多的工业装置和工程结构中,它是一种最普遍的局部腐蚀类型。
轮船、飞机、汽车等许多交通工具都存在着异种金属的相互接触,都会引起程度不同的电偶腐蚀。
电偶腐蚀甚至存在于电子和微电子装备中,它们在临界湿度以上及腐蚀性大气环境下工作时,许多铜导线、镀金、镀银件与焊锡相接触而产生严重的电偶腐蚀。
纽约著名的自由女神铜像内部的钢铁支架发生的严重腐蚀就是因为发生了电偶腐蚀,许多钢铁支架锈蚀得只剩下原来的一半,抑钉也已脱落;同时在潮湿空气、酸雨等作用下,铜皮外衣也被腐蚀得比原先薄了许多。
据报道,各军兵种的军事装备由于电偶腐蚀,破坏了它们的可靠性,导致电子装备的早期失效,直接影响乃至丧失它们的作战能力。
在某些情况下,两种不同的金属虽然没有直接接触,在意识不到的情况下也有引起电偶腐蚀的可能。
例如循环冷却系统中的铜零件,由于腐蚀下来的铜离子可通过扩散在碳钢设备表面上沉积,沉积下的疏松的铜粒子与碳钢之间便形成了微电偶腐蚀电池,结果引起了碳钢设备严重的局部腐蚀。
外科植入物 电解液中电偶腐蚀试验方法

外科植入物电解液中电偶腐蚀试验方法1 范围本标准给出了外科植入物电偶腐蚀测试和评价方法,涵盖了试样选取、试样准备、测试环境、暴露方式和表征电偶对在电解液中腐蚀行为的测试结果评价方法。
本标准适用于表征作为外科植入物或其部件应用于人体的两种或两种以上不同金属在电接触状态下的腐蚀行为。
本标准不适用于评价器械所发生的其它形式腐蚀和降解影响。
本标准也不适用于评价表面状态的改变。
这是由于上述作用机制超出了本标准的范围。
注1:可能需要评估的器械型式包括不同合金的重叠支架、支架和支架标记物的组合、骨板和螺钉中一个或多个螺钉与该器械的其余部分属于不同合金的组合、两种或两种以上合金制成的多部件结构。
对于那些部分植入但长期接触人体的器械(如外固定器械)也可以使用本标准进行评价。
注2:器械所发生的其它形式腐蚀和降解影响包括但不限于以下情况:如微动腐蚀、缝隙腐蚀、任何电偶腐蚀对应力腐蚀和腐蚀疲劳的影响等。
注3:表面状态改变包括但不限于以下情况:如(植入过程可能导致的)划痕或(在制造过程中的)焊接影响等。
2 规范性引用文件下列文件对于本文件的应用是必不可少的。
凡是注日期的引用文件,仅注日期的版本适用于本文件。
凡是不注日期的引用文件,其最新版本(包括所有的修改单)适用于本文件。
GB/T 6682 分析实验室用水规格和试验方法YY/T 0695-2008 小型植入器械腐蚀敏感性的循环动电位极化标准测试方法YY/T 1552 外科植入物评价金属植入材料和医疗器械长期腐蚀行为的开路电位测量方法3 意义和应用可植入的医疗器械可以由不同的金属制成,也可以与不同的金属发生电接触,从而引起电偶腐蚀。
这可能导致腐蚀产物的释放,从而引发有害的生物反应,或牺牲器械的结构完整性。
因此测量这些可植入器械的电偶腐蚀敏感性是很重要的。
使用本测试方法是为了提供两种不同金属相互接触时腐蚀的电偶部件信息。
相互接触的不同金属可以是在同一件植入器械上,也可以是独立的植入器械部件。
电偶腐蚀

在薄电解质层下的锌/钢电偶腐蚀的表面电位分布摘要:在这项研究中,在相对湿度为60和90%的人工海水中锌/钢电偶腐蚀的表面电位和表面pH值的变化进行了研究。
这个结果是从测量表面电位和表面的pH值试验中和之后腐蚀实验得出的。
锌和钢表面的电位在相对湿度为90%时是很低的(小于200 mV)表明全钢的表面在阴极保护下的。
另一方面,在相对湿度为60%的情况下,经过几天的腐蚀后,锌涂层和钢表面的电位差异很大(超过500mV)和因此阴极保护仅限于接触面区域。
在相对湿度为60%时x射线分析腐蚀样品,得出锌腐蚀产物被堆积在钢表面接近接口处,相对于其他钢表面的区域这一区域pH值更低。
随着腐蚀的进行得出这样的结论,钢板的镀锌涂层表面与海水反应水解反应溶解出锌离子,然后铁表面通过氧还原反应显示出碱性。
此外,部分钢表面覆盖着锌腐蚀产物显示出更低的电位,这表明锌腐蚀产物扮演着保护钢不被腐蚀的角色。
假定这种行是关于锌腐蚀产物的吸水能力和在钢表面锌离子的吸附能力这是由于低的)dxpH值。
∅ x=I x dR x=(I(x)ρlt1.引言:镀锌涂层钢一直是在不同的环境中最常见的来保护钢防止被腐蚀的方法。
镀锌涂层是通过屏蔽效应和电效应来保护钢材的。
屏蔽效应是由于在形成腐蚀发过程中锌涂层和腐蚀产物的形成。
然而,当涂层区域被损坏时,比如削减和伸展, 当周围的锌涂层被电腐蚀时钢基是被阴极保护。
在大气腐蚀环境下,在湿干燥周期中腐蚀发生在一层薄的电解质上,限制了应用电化学方法,现在已经有能研究在钢基上的锌涂层的电效应的方法了。
张和Valeriote对钢材薄层的电解质的阴极保护效应进行了研究。
该作者已经使用探针测量了覆盖着一个150um至超过1000um厚的电解质膜的锌/钢偶上的电位和电流。
这项研究作为一个模型,提供了对电化学腐蚀全面的理解。
但是,它没有考虑其他因素的影响,比如腐蚀产物的形成和分布与导电涂层上的pH值。
此外,使用探针会使薄电解质层产生一个大幅度欧姆电压的降低。
AE44-MS电偶腐蚀数值模拟

• 因此,腐蚀产物沉积层的传质现象可由下述方程描 述: • 同理,腐蚀产物沉积层的物质迁移率为:
• 电解质溶液中的溶解氧在阴极表而发生电化学 还原,生成OH-,OH-的通量由法拉第定律计算:
• 阳极表面发生镁合金的阳极溶解,Mg2+的通量 表示如下: • 假设腐蚀产物为Mg(OH)2,它的沉积只发生在电 极表界,则Mg2+和OH-的消耗速率分别为:
•
由此可见,腐蚀产物沉积层的生长界面是金属界面和Mg(OH)2沉积共同作用的结果式中
•
表示由于阳极溶解导致的金属界面移动,引入 动。
控制模拟过程中阴极表面不发生移
•
是由Mg(OH)2沉枳引起的沉积层界面移动。
5.电偶腐蚀模型的验证
• 5.1 模型的验证 • 模型的有效性通过比较计算结果与浸泡实验和SVET的实 验结果验证图2.10给出了 AE44-MS电偶对电极表面电流 分布的SVET实验值和数值模拟值。由图可以看出,模型预 测的最大阳极电流密度约为84.1 A/m2而该值的实验结果 为81.6A/m2,模拟预测值比SVET实验佔计值大3%左右。 同时,SVET实验结果和数值模拟结来均显示,阳极峰值电流 位于电偶对偶接处,并且由于电偶电极表面存在IR降的作 用,远离偶接处的阳极电流密度逐渐减小。很明显,模拟预 测值与SVET实验测量结果吻合得很好。
• 计算结果还表明,腐蚀产物沉积层在偶接处的厚度极 大,而最小厚度位于远离偶接处。因此可以推断:电阻 沿着金属表面是不断变化的。考虎这种非均一电阻分 布的沉枳模型所预测的电极表面电流密度分布与不考 虑腐蚀产物沉积的非沉积模型预测的电流分布完全不 同。图2.13所示为沉积模型和非沉枳模型预测的电极 表面近偶接处的电流演变曲线。如图2.13所示,两个 模型的预测结来均显示,近偶接处的电流密度随着时 间的延长在缓慢地减小,但当有腐蚀产物沉积时,近偶 接处的电流密度减小得更多:同时,相对偏差随着时间 的延长呈增加的趋势。由此可以推断:逐渐增厚的腐 蚀产物沉积展减缓镁合金AE44电偶腐蚀的能力越来 越强。但是,虽然在远离偶接处腐蚀产物沉积层的厚 度也在不断增加,但沉枳模型预测电流密度随着时间 的延长而增大,而非沉积模型预测电流密度随着时间 不断减少。
电偶腐蚀测试

电偶腐蚀测试是一种评估金属材料在不同环境下的耐腐蚀性的方法。
在电偶腐蚀测试中,两种或多种不同的金属在电解质溶液中组成电偶对,其中一种金属为阴极,另一种金属为阳极。
阴极金属被保护,而阳极金属被腐蚀。
测试中需要测量和记录腐蚀速率、腐蚀电流、电位等参数。
电偶腐蚀测试的步骤如下:
1.选取不同的金属材料组合成电偶对。
2.将金属材料加工成适合测试的形状和尺寸。
3.将金属材料放入电解质溶液中,并确保稳定的电偶连接。
4.记录测试过程中的电位、电流等参数,并计算腐蚀速率。
5.分析测试结果,评估不同金属材料的耐腐蚀性。
电偶腐蚀测试的优点包括:能够模拟实际使用环境中的腐蚀情况,可以评估不同金属材料的耐腐蚀性,可以研究不同因素对金属腐蚀的影响。
缺点包括:测试周期较长,需要专业的测试设备和技能,测试结果会受到多种因素的影响。
电偶腐蚀

目录:
1.电偶腐蚀的产生 2.电偶腐蚀的实验 3.电偶腐蚀的防护与控制
定义:金属自身在电解质溶液中发生 腐蚀溶解后,再接触或与自腐蚀电位 更高的金属电连接而使得腐蚀速率加 快的现象。(宏观,易于判别)
产生条件:
1.具有不同腐蚀电位的材料 2.存在离子导体支路 3.存在电子导体支路
形成机理:
根据混合电位理论,偶合的结果使得自腐蚀电位低的金
属腐蚀电流增大,产生阳极极化使之加速腐蚀,而自腐蚀电 位高的金属电流降低,作为阴极而被保护了起来。
Ec Ea Ig Pc Pa R Sc Sa
2015-4-20
影响因素:
1.材料自身特性(驱动力)
2.结构因素:阴阳极面积比值(影响氢过电位) 电偶对间距
谢 谢!
ห้องสมุดไป่ตู้
实验要求:
1.试样要求: a.长110mm,宽25mm,厚2~3mm的平板试样,Ra0.8 b.用汽油和酒精清洗后干燥器中放置七天 c.配对试样表面积需基本相等 d.试样间距5mm
2.腐蚀环境:电解液为化学氯化钠和蒸馏水,溶液体积400ml 电解液温度控制在30℃ 3.实验程序:试样在电解液中稳定30min测量各电极电位 连续测量和记录电偶电流20h,改过程中禁止搅动溶液 平行试验不少于三组
3.环境因素:介质组成,温度,pH值,应力 状态(可能引起电偶极性逆转)
实验方法:
1.浸泡试验:同时将电偶对试样和未经偶接的试样暴 露于同种腐蚀介质中进行腐蚀实验,采用失重测量、 表观检查等方法判断电偶效应。 2.电化学实验法:测量材料的自腐蚀电位和偶合后电 位,以及腐蚀过程中电流变化,极化过程来表征电偶 效应。
电偶序:金属或合金在某一确定电解质溶液中实测 而得的稳定电位相对大小排列而成的次序表。
实验三:电偶腐蚀

实验三:电偶腐蚀速度的测定
一、实验目的
1.掌握电偶腐蚀测试原理;
2.掌握电极电位、耦合电流的测量方法;
3.掌握实验分析方法。
二、实验仪器及用品
电偶腐蚀计,金属电极(Fe,紫铜,黄铜),饱和甘汞电极,烧杯,量筒,天平砂纸,滤纸,酒精棉,pH试纸
NaCl,
三、实验内容及步骤
1.将各电极用水砂纸打磨光亮,用酒精棉擦干待用;
2.配制100毫升3%NaCl溶液,连接电偶腐蚀计线路;
3.测定各电极在3%NaCl溶液中相对于石墨电极的自腐蚀电位,填入表格;4.测Fe-紫铜和黄铜-紫铜电偶电流随时间的变化
待电极自腐蚀电位稳定后接通电路,测定电偶电流随时间的变化情况,直到电流比较稳定时为止,测量耦合电极相对于参比电极的电位。
电偶电流最初随时间变化较快,可适当缩小记录时间间隔,15秒或半分钟计一次数。
四、实验数据及结果处理
1.所有测量数据记录于表格中
自腐蚀电位:Fe:黄铜:紫铜:
耦合电位:Fe-紫铜:黄铜-紫铜:
2.将Fe-紫铜和黄铜-紫铜电偶电流随时间的变化绘制在同一张图中;3.结果及讨论。
汽车中钢铝连接的电偶腐蚀行为研究

Al Bal.
/ 0. 029 0. 05
Ti 0.011 0. 07 0. 032
/
Fe 0. 243 Bal. Bal. Bal.
Cu 3. 823
/ / /
Mg 0. 334
/ / /
Cr 0. 005
/ 0. 18
/
Zn 0. 049
/ / /
Mo
B
0. 004 0. 002 4
蚀问题为背景,对无锯锌铝和电镀锌镰合金涂层处理后 的ST12钢板与热轧钢材间的电偶腐蚀行为进行了实验研 究,结果表明相比于锌铝涂层、锌层,电镀锌镰涂层的 耐电偶腐蚀性能更佳,为汽车工业中紧固件表面处理的 优选工艺。
11 环境技术 / Environmental Technology
Et:—31/环境试验
表1实验用材料的化学组分
Material Cast-Al DX54D+Z D1300HF+AS QP1180
C / 0. 005 0. 24 0. 17
Si 7. 493 0. 008 0. 27
1.7
Mn 0. 235 0. 09 1.22
:环境试验/E囂带
汽车中钢铝连接的电偶腐蚀行为研究
赵雪茹I,付益平食杨冰食衡俐琼食向利1,陈心欣I,张晓东I,王俊1 (1.中国电器科学研究院股份有限公司工业产品环境适应性国家重点实验室,广州510663;
2.东风汽车集团有限公司技术中心,武汉430056)
摘要:本文针对汽车轻量化钢铝车身中潜在的电偶腐蚀问题,对原始及基体状态下的铸铝与DX54D+Z、D1300HF+AS 及QP1180间的偶对,分别开展单种材料动电位极化与偶对电偶电流跟踪研究。结果表明:(1)三种钢材中, D1300HF+AS的耐蚀性优于DX54D+Z及QP1180; (2) QP1180-铸铝偶对的耐蚀性最优、电偶腐蚀敏感性为B级,需在
电偶腐蚀电池电化学法
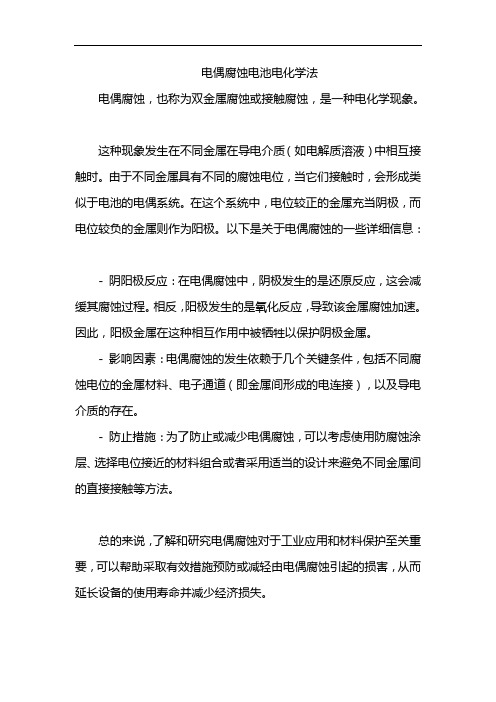
电偶腐蚀电池电化学法
电偶腐蚀,也称为双金属腐蚀或接触腐蚀,是一种电化学现象。
这种现象发生在不同金属在导电介质(如电解质溶液)中相互接触时。
由于不同金属具有不同的腐蚀电位,当它们接触时,会形成类似于电池的电偶系统。
在这个系统中,电位较正的金属充当阴极,而电位较负的金属则作为阳极。
以下是关于电偶腐蚀的一些详细信息:
- 阴阳极反应:在电偶腐蚀中,阴极发生的是还原反应,这会减缓其腐蚀过程。
相反,阳极发生的是氧化反应,导致该金属腐蚀加速。
因此,阳极金属在这种相互作用中被牺牲以保护阴极金属。
- 影响因素:电偶腐蚀的发生依赖于几个关键条件,包括不同腐蚀电位的金属材料、电子通道(即金属间形成的电连接),以及导电介质的存在。
- 防止措施:为了防止或减少电偶腐蚀,可以考虑使用防腐蚀涂层、选择电位接近的材料组合或者采用适当的设计来避免不同金属间的直接接触等方法。
总的来说,了解和研究电偶腐蚀对于工业应用和材料保护至关重要,可以帮助采取有效措施预防或减轻由电偶腐蚀引起的损害,从而延长设备的使用寿命并减少经济损失。
(完整word版)电偶腐蚀

电偶腐蚀简述电偶腐蚀简述摘要。
电偶腐蚀(亦称接触腐蚀),是指当两种或者两种以上不同金属在导电介质中接触后,由于各自电极电位不同而构成腐蚀原电池。
电偶腐蚀是一种普遍存在的且危害极大的腐蚀形成,它广泛地存在石油、天然气、船舶、航空和建筑工业等行业中,一旦发生则极有可能造成严重的损失。
本文主要介绍了关于电偶腐蚀的基本相关知识,包括电偶腐蚀的概念、形成原因、影响因素以及如何判断是否形成了电偶腐蚀及其预防措施。
关键字:电偶腐蚀;金属接触;电位差;预防措施1.电偶腐蚀的基本简介由于腐蚀电位不同,造成同一介质中异种金属接触处的局部腐蚀,就是电偶腐蚀(galvanic corrosion),亦称接触腐蚀或双金属腐蚀。
当两种或两种以上不同金属在导电介质中接触后,由于各自电极电位不同而构成腐蚀原电池,电位较正的金属为阴极,发生阴极反应,导致其腐蚀过程受到抑制;而电位较负的金属为阳极,发生阳极反应,导致其腐蚀过程加速。
它是一种危害极为广泛和可能产生严重损失的腐蚀形式,广泛地存在于船舶、油气、航空、建筑工业和医疗器械中。
它会造成热交换器、船体推进器、阀门、冷凝器与医学植入件的腐蚀失效,是一种普遍存在的腐蚀类型。
电偶腐蚀往往会诱发和加速应力腐蚀、点蚀、缝隙腐蚀、氢脆等其他各种类型的局部腐蚀,从而加速设备的破坏。
两种或两种以上不同电极电位的金属处于腐蚀介质内相互接触而引起的电化学腐蚀,又称接触腐蚀或双金属腐蚀。
电偶腐蚀原理见图1。
发生电偶腐蚀时,电极电位较负的金属通常会加速腐蚀,而电极电位较正的金属的腐蚀则会减慢。
图2为现实中几个电偶腐蚀的例子。
图2 电偶腐蚀的实例合金中呈现不同电极电位的金属相、化合物、组分元素的贫化或富集区,以及氧化膜等也都可能与金属间发生电偶现象,钝化与浓差效应也会形成电偶型的腐蚀现象,这些微区中的电偶现象通常称为腐蚀微电池,不称作电偶腐蚀。
在工程技术中,不同金属的组合是不可避免的,几乎所有的机器、设备和金属结构件都是由不同的金属材料部件组合而成,电偶腐蚀非常普遍。
AE44-MS电偶腐蚀数值模拟.

• 在提出数学模型前,作如下假设: • (1)稀溶液理论适用; • (2)电化学反应只发生在未被腐蚀产物覆盖的电极表面; • (3)阴极不发生腐蚀; • (4)腐蚀沉积层框架坚固、绝缘; • (5)沉积层是多孔的,且孔隙度恒定; • (6) 一旦沉积层沉淀在金属表面,沉积层不溶解。
• 4.1 物理模型
• 腐蚀产物沉积与很多的物理化学过程有关,例如,化学反 应、电化学反应、传质过程和热耗散过程,等等。因此, 模拟腐蚀产物沉积时,必须考虑这些物理化学过程间复 杂的相互作用。由于腐蚀产物沉积层的生长行为不仅 与金属本身的腐蚀行为相关,而且腐蚀沉积层的形成反 过来也可以影响(或加速,或抑制)腐蚀过程,因此,数值模 拟腐蚀产物沉积层的形成过程对理解整个腐蚀过程及 其随时间变化很有实际意义通过有限元软件COMSOL Multiphysics求解模型,分析腐蚀产物沉积对AE44-MS 电偶对腐蚀过程的影响。该模型将不仅能准确地反映 电偶对中每种金属材料的极化行为,而且能形象地反映 多孔的腐蚀沉积层对近电极界面传质过程和电流分布 的影响。此外,本模型还能用于定量地研究腐蚀产物沉 积层的物理性质与电偶腐蚀行为之间的关系。
3.AE44-MS电偶对腐蚀数值模拟
• 在腐蚀性介质中,金属离子首先从阳极表面 释放出来,随后溶液中游离的金属离子与电 解液中的水分子或其它阴离子反应,最终形 成腐蚀产物并在金属表面沉积。沉积的腐 蚀产物严重地影响金属电极的表面状态,改 变了金属/溶液介面的传质行为和电学行为, 并进一步影响金属的腐蚀过程。
• 图2.2为AE44-MS电偶对在1.6 wt.% NaCl介质中 电偶腐蚀实验的物理模型示意图。图中浅色部分 为AE44,深色部分为MS,白色部分为绝缘体。实验 描述如下:在一个25 cmx25 cmx10 cm矩形绝缘容 器中,分别放置尺寸为10 cmx20 cm的AE44和MS 试样片,两个试样片相互接触,通过电连接构成电偶 对,试样片边缘与容器边缘间存在厚为2.5 cm的绝 缘层,最后将AE44-MS电偶对浸没在深为10 cm的 1.6 wt.% NaCl水溶液中进行浸泡实验。为了简化 模拟,本章采用二维的理想模型代替三维的实际模 型,选作计算域的截而为图2.2所示的黑框部分。 图2.3所示为物理模型及计算域网格剖分示意图。 由于阳极部分腐蚀发生电化学溶解,物理化学现象 较阴极部分复杂,因此采用了较细的网格剖分,计算 域总共含有989个计算网格。
01实验一电偶腐蚀
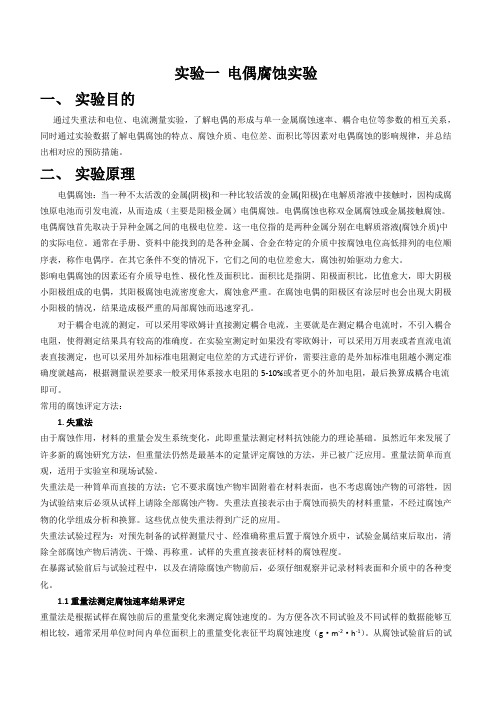
实验一电偶腐蚀实验一、实验目的通过失重法和电位、电流测量实验,了解电偶的形成与单一金属腐蚀速率、耦合电位等参数的相互关系,同时通过实验数据了解电偶腐蚀的特点、腐蚀介质、电位差、面积比等因素对电偶腐蚀的影响规律,并总结出相对应的预防措施。
二、实验原理电偶腐蚀:当一种不太活泼的金属(阴极)和一种比较活泼的金属(阳极)在电解质溶液中接触时,因构成腐蚀原电池而引发电流,从而造成(主要是阳极金属)电偶腐蚀。
电偶腐蚀也称双金属腐蚀或金属接触腐蚀。
电偶腐蚀首先取决于异种金属之间的电极电位差。
这一电位指的是两种金属分别在电解质溶液(腐蚀介质)中的实际电位。
通常在手册、资料中能找到的是各种金属、合金在特定的介质中按腐蚀电位高低排列的电位顺序表,称作电偶序。
在其它条件不变的情况下,它们之间的电位差愈大,腐蚀初始驱动力愈大。
影响电偶腐蚀的因素还有介质导电性、极化性及面积比。
面积比是指阴、阳极面积比,比值愈大,即大阴极小阳极组成的电偶,其阳极腐蚀电流密度愈大,腐蚀愈严重。
在腐蚀电偶的阳极区有涂层时也会出现大阴极小阳极的情况,结果造成极严重的局部腐蚀而迅速穿孔。
对于耦合电流的测定,可以采用零欧姆计直接测定耦合电流,主要就是在测定耦合电流时,不引入耦合电阻,使得测定结果具有较高的准确度。
在实验室测定时如果没有零欧姆计,可以采用万用表或者直流电流表直接测定,也可以采用外加标准电阻测定电位差的方式进行评价,需要注意的是外加标准电阻越小测定准确度就越高,根据测量误差要求一般采用体系接水电阻的5-10%或者更小的外加电阻,最后换算成耦合电流即可。
常用的腐蚀评定方法:1. 失重法由于腐蚀作用,材料的重量会发生系统变化,此即重量法测定材料抗蚀能力的理论基础。
虽然近年来发展了许多新的腐蚀研究方法,但重量法仍然是最基本的定量评定腐蚀的方法,并已被广泛应用。
重量法简单而直观,适用于实验室和现场试验。
失重法是一种筒单而直接的方法;它不要求腐蚀产物牢固附着在材料表面,也不考虑腐蚀产物的可溶牲,因为试验结束后必须从试样上请除全部腐蚀产物。
模拟海洋大气环境下钛铝连接件的电偶腐蚀研究
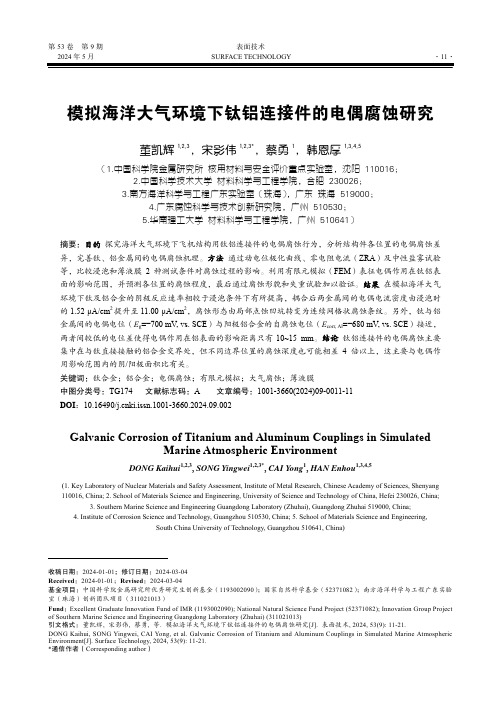
第53卷第9期表面技术2024年5月SURFACE TECHNOLOGY·11·模拟海洋大气环境下钛铝连接件的电偶腐蚀研究董凯辉1,2,3,宋影伟1,2,3*,蔡勇1,韩恩厚1,3,4,5(1.中国科学院金属研究所 核用材料与安全评价重点实验室,沈阳 110016;2.中国科学技术大学 材料科学与工程学院,合肥 230026;3.南方海洋科学与工程广东实验室(珠海),广东 珠海 519000;4.广东腐蚀科学与技术创新研究院,广州 510530;5.华南理工大学 材料科学与工程学院,广州 510641)摘要:目的探究海洋大气环境下飞机结构用钛铝连接件的电偶腐蚀行为,分析结构件各位置的电偶腐蚀差异,完善钛、铝金属间的电偶腐蚀机理。
方法通过动电位极化曲线、零电阻电流(ZRA)及中性盐雾试验等,比较浸泡和薄液膜2种测试条件对腐蚀过程的影响。
利用有限元模拟(FEM)表征电偶作用在钛铝表面的影响范围,并预测各位置的腐蚀程度,最后通过腐蚀形貌和失重试验加以验证。
结果在模拟海洋大气环境下钛及铝合金的阴极反应速率相较于浸泡条件下有所提高,耦合后两金属间的电偶电流密度由浸泡时的1.52 μA/cm2提升至11.00 μA/cm2,腐蚀形态由局部点蚀凹坑转变为连续网格状腐蚀条纹。
另外,钛与铝金属间的电偶电位(E g=−700 mV, vs. SCE)与阳极铝合金的自腐蚀电位(E corr, Al=−680 mV, vs. SCE)接近,两者间较低的电位差使得电偶作用在铝表面的影响距离只有10~15 mm。
结论钛铝连接件的电偶腐蚀主要集中在与钛直接接触的铝合金交界处,但不同边界位置的腐蚀深度也可能相差4倍以上,这主要与电偶作用影响范围内的阴/阳极面积比有关。
关键词:钛合金;铝合金;电偶腐蚀;有限元模拟;大气腐蚀;薄液膜中图分类号:TG174 文献标志码:A 文章编号:1001-3660(2024)09-0011-11DOI:10.16490/ki.issn.1001-3660.2024.09.002Galvanic Corrosion of Titanium and Aluminum Couplings in SimulatedMarine Atmospheric EnvironmentDONG Kaihui1,2,3, SONG Yingwei1,2,3*, CAI Yong1, HAN Enhou1,3,4,5(1. Key Laboratory of Nuclear Materials and Safety Assessment, Institute of Metal Research, Chinese Academy of Sciences, Shenyang110016, China; 2. School of Materials Science and Engineering, University of Science and Technology of China, Hefei 230026, China;3. Southern Marine Science and Engineering Guangdong Laboratory (Zhuhai), Guangdong Zhuhai 519000, China;4. Institute of Corrosion Science and Technology, Guangzhou 510530, China;5. School of Materials Science and Engineering,South China University of Technology, Guangzhou 510641, China)收稿日期:2024-01-01;修订日期:2024-03-04Received:2024-01-01;Revised:2024-03-04基金项目:中国科学院金属研究所优秀研究生创新基金(1193002090);国家自然科学基金(52371082);南方海洋科学与工程广东实验室(珠海)创新团队项目(311021013)Fund:Excellent Graduate Innovation Fund of IMR (1193002090); National Natural Science Fund Project (52371082); Innovation Group Project of Southern Marine Science and Engineering Guangdong Laboratory (Zhuhai) (311021013)引文格式:董凯辉, 宋影伟, 蔡勇, 等. 模拟海洋大气环境下钛铝连接件的电偶腐蚀研究[J]. 表面技术, 2024, 53(9): 11-21.DONG Kaihui, SONG Yingwei, CAI Yong, et al. Galvanic Corrosion of Titanium and Aluminum Couplings in Simulated Marine Atmospheric Environment[J]. Surface Technology, 2024, 53(9): 11-21.*通信作者(Corresponding author)·12·表面技术 2024年5月ABSTRACT: Titanium alloys and aluminum alloys are two of the most widely used lightweight metallic structural materials in the aviation industry. The sum of the two can reach 60%-80% of the overall material of the aircraft. In view of the complex internal structure of the aircraft and the large number of parts, the contact between dissimilar metals is very common, among which titanium-aluminum couplings are the most prevalent. The purpose of this paper is to investigate the galvanic corrosion behavior of titanium and aluminum couplings for aircraft structures in the marine atmospheric environment, and to theoretically analyze the difference of galvanic corrosion at different positions of structural parts, so as to further enrich the galvanic corrosion mechanism between titanium and aluminum. In order to compare the effects of immersion and thin liquid film test conditions on the corrosion process, potentiodynamic polarization curves, zero resistance current test (ZRA) and neutral salt spray test were used. Finite element modeling (FEM) was used to characterize the influence range of galvanic action on the surface of titanium and aluminum, and also predict the local corrosion. Finally, the corrosion morphology and weight loss test were conducted to verify it. In the simulated marine atmospheric environment, the cathodic reduction reaction rate on the surface of titanium and aluminum alloy was higher than that in the immersion condition, and the galvanic current density between the two metals was increased from 1.52 μA/cm2 to 11.00 μA/cm2. In addition, when the area ratio of titanium to aluminum was 1∶1 under the ideal condition, the galvanic potential between titanium and aluminum (E g=−0.70 V, vs. SCE) was close to the self-corrosion potential of aluminum alloy (E corr, Al=−0.68 V, vs. SCE), and away from the sel-corrosion potential of titanium alloy (E corr, Ti=−0.30 V, vs. SCE). However, combined with the effect of solution resistance under actual condition, the influence range of galvanic action on these two metals were different. As for the cathodic titanium alloy, the high cathodic polarization potential of about −400 mV resulted in galvanic effects throughout the whole titanium parts of the couplings. As for the anodic aluminum alloy, the low anodic polarization potential of 20 mV lead to a short influence distance of galvanic effect on the aluminum surface, only 10-15 mm. But the anodic reaction of aluminum alloy in chloride-containing corrosive media was in an active dissolved state, such a small polarization potential could also cause a large change in corrosion rate of aluminum.Therefore, the corrosion at the aluminum alloy boundary in direct contact with titanium is the most serious. It is worth noting that the corrosion depth of anodic aluminum alloy at different boundary positions may also differ by more than 4 times, which is mainly related to the cathode/anode area ratio within the influence range of galvanic action. And the aluminum part of the titanium-aluminum couplings that are not affected by galvanic action is still subject to relatively serious self-corrosion.KEY WORDS: titanium alloy; aluminum alloy; galvanic corrosion; FEM; atmospheric corrosion; thin liquid film钛合金和铝合金是航空领域 2 种重要的轻质金属结构材料,已广泛应用于各型号飞机中[1-4]。
电偶腐蚀事件
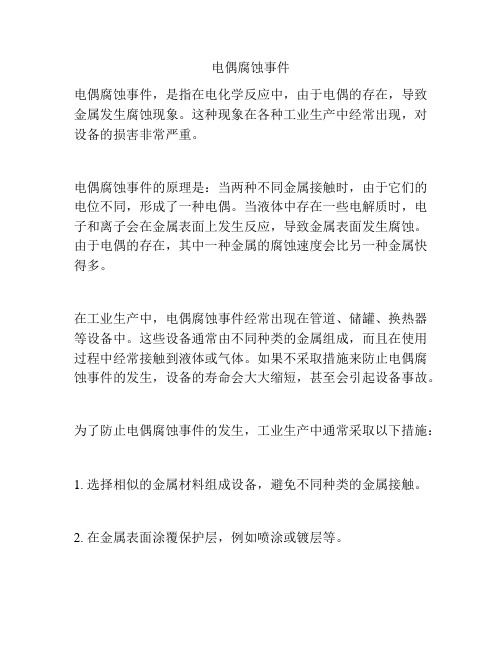
电偶腐蚀事件
电偶腐蚀事件,是指在电化学反应中,由于电偶的存在,导致金属发生腐蚀现象。
这种现象在各种工业生产中经常出现,对设备的损害非常严重。
电偶腐蚀事件的原理是:当两种不同金属接触时,由于它们的电位不同,形成了一种电偶。
当液体中存在一些电解质时,电子和离子会在金属表面上发生反应,导致金属表面发生腐蚀。
由于电偶的存在,其中一种金属的腐蚀速度会比另一种金属快得多。
在工业生产中,电偶腐蚀事件经常出现在管道、储罐、换热器等设备中。
这些设备通常由不同种类的金属组成,而且在使用过程中经常接触到液体或气体。
如果不采取措施来防止电偶腐蚀事件的发生,设备的寿命会大大缩短,甚至会引起设备事故。
为了防止电偶腐蚀事件的发生,工业生产中通常采取以下措施:
1. 选择相似的金属材料组成设备,避免不同种类的金属接触。
2. 在金属表面涂覆保护层,例如喷涂或镀层等。
3. 在液体中加入缓蚀剂,减缓金属表面的腐蚀速度。
4. 定期对设备进行检查和维护,及时发现并处理可能存在的电偶腐蚀问题。
总之,电偶腐蚀事件是工业生产中常见的问题。
只有采取有效的措施来防止其发生,才能保证设备的正常运行和安全生产。
电偶腐蚀磨损腐蚀

34
' S
“性能”之二:低(常)温~高
温
• σs —— 体心立方材料的屈服强度;
• σS` —— 面心立方结构材料的屈服强度;
• σc —— 断裂强度;
• tk —— 韧脆转变温度Tc 。
35
“性能”之二:低温~高温
36
“性能”之二:常温~高温
• Te —— 等强温度 ✓ 常温:晶界↑∴ 细化晶粒——比表面积↑ ✓ 高温:晶内↑∴ 粗晶粒——比表面积↓
26
实例4:搅拌釜合并进出口引发爆炸
27
实例4:搅拌釜合并“进、出料口” 引发爆炸
• 一间歇操作搅拌釜,为减少容器开孔、 布管紧凑,将液态物料“进、出料口” 合并,位于下封头中心。
• 接管端部与下封头采用“平齐结构”, 以满足排液需要,但引发气蚀、闪蒸, 使管口附近封头壁厚减薄。
• 物料中含固体颗粒,桨叶的下返料搅 拌作用加速下封头磨损。
• 裂纹状况:进料口补强圈上沿30mm处 起裂,1020mm长,纵向裂纹(图)。
22
实例3:酒精厂立式蒸煮罐破裂
• 工艺流程:5个蒸煮罐串联,第3个发 生事故。压缩机出口压力:0.5~ 0.6MPa,到第5个达: 0.1~0.2MPa 是降压过程。
• 结构特征:罐内介质下进上出,接管 端部与罐壁平齐。δn:10mm,裂纹 处仅剩0.4~0.9mm厚,进料口上部区 域严重减薄。壳体材料:Q235-C。
316L~304L两个电偶的共同作用, 304L产生严重的腐蚀。
17
实例2:氯化氢塔中段塔节电偶腐蚀
• 穿孔距焊缝6~7mm,属HAZ,加速 腐蚀
• 图中沿焊缝从上到下流线状腐蚀,该 区正处于进口管对面,流体冲刷加速 钝化膜破坏,冲刷与腐蚀相互促进。
- 1、下载文档前请自行甄别文档内容的完整性,平台不提供额外的编辑、内容补充、找答案等附加服务。
- 2、"仅部分预览"的文档,不可在线预览部分如存在完整性等问题,可反馈申请退款(可完整预览的文档不适用该条件!)。
- 3、如文档侵犯您的权益,请联系客服反馈,我们会尽快为您处理(人工客服工作时间:9:00-18:30)。
实验一、电偶腐蚀试验目的:通过失重法和电位、电流测量实验,了解电偶的形成与单一金属腐蚀速率、耦合电位等参数的相互关系,同时通过实验数据了解电偶腐蚀的特点、腐蚀介质、电位差、面积比等因素对电偶腐蚀的影响规律,并总结出相对应的预防措施。
穿插进行伊文斯盐水滴试验,观察氧浓差腐蚀原电池的阴、阳极反应以及阴、阳极区的划分。
试验原理:电偶腐蚀:当一种不太活泼的金属(阴极)和一种比较活泼的金属(阳极)在电解质溶液中接触时,因构成腐蚀原电池而引发电流,从而造成(主要是阳极金属)电偶腐蚀。
电偶腐蚀也称双金属腐蚀或金属接触腐蚀。
电偶腐蚀首先取决于异种金属之间的电极电位差。
这一电位指的是两种金属分别在电解质溶液(腐蚀介质)中的实际电位。
通常在手册、资料中能找到的是各种金属、合金在特定的介质中按腐蚀电位高低排列的电位顺序表,称作电偶序。
在其它条件不变的情况下,它们之间的电位差愈大,腐蚀初始驱动力愈大。
影响电偶腐蚀的因素还有介质导电性、极化性及面积比。
面积比是指阴、阳极面积比,比值愈大,即大阴极小阳极组成的电偶,其阳极腐蚀电流密度愈大,腐蚀愈严重。
在腐蚀电偶的阳极区有涂层时也会出现大阴极小阳极的情况,结果造成极严重的局部腐蚀而迅速穿孔。
对于耦合电流的测定,可以采用零欧姆计直接测定耦合电流,主要就是在测定耦合电流时,不引入耦合电阻,使得测定结果具有较高的准确度。
在实验室测定时如果没有零欧姆计,可以采用万用表或者直流电流表直接测定,也可以采用外加标准电阻测定电位差的方式进行评价,需要注意的是外加标准电阻越小测定准确度就越高,一般采用0.05欧姆或者更小的外加电阻,最后换算成耦合电流即可。
常用的腐蚀评定方法:1. 失重法由于腐蚀作用,材料的重量会发生系统变化,此即重量法测定材料抗蚀能力的理论基础。
虽然近年来发展了许多新的腐蚀研究方法,但重量法仍然是最基本的定量评定腐蚀的方法,并已被广泛应用。
重量法简单而直观,适用于实验室和现场试验。
失重法是一种筒单而直接的方法;它不要求腐蚀产物牢固附着在材料表面,也不考虑腐蚀产物的可溶牲,因为试验结束后必须从试样上请除全部腐蚀产物。
失重法直接表示由于腐蚀而损失的材料重量,不经过腐蚀产物的化学组成分析和换算。
这些优点使失重法得到广泛的应用。
失重法试验过程为:对预先制备的试样测量尺寸、经准确称重后置于腐蚀介质中,试验金属结束后取出,清除全部腐蚀产物后清洗、干燥、再称重。
试样的失重直接表征材料的腐蚀程度。
在暴露试验前后与试验过程中,以及在清除腐蚀产物前后,必须仔细观察并记录材料表面和介质中的各种变化。
1.1 重量法测定腐蚀速率结果评定重量法是根据试样在腐蚀前后的重量变化来测定腐蚀速度的。
为方便各次不同试验及不同试样的数据能够互相比较,通常采用单位时间内单位面积上的重量变化表征平均腐蚀速度(g ·m -2·h -1)。
从腐蚀试验前后的试样重量差计算腐蚀速度v(g ·m -2·h -1)。
公式如下:失重速度AtW W W v w 320--=-式中: A — 试样面积,m 2;t — 试验周期,h ;W 0— 试样原始重量,g ; W 2—试验后含与不含腐蚀产物的试样重量,g ;W 3 —清除腐蚀产物时同样尺寸同种材料空白试样的校正失重,g ;1.2 重量法测定腐蚀速率时腐蚀产物清除方法为了取得准确得失重法实验结果,必须清除试样表面的腐蚀产物,但又不损伤金属基材本身。
实际上完全不损伤基材是不可能的,只要求损伤对腐蚀结果无明显影响即可。
对于不同金属材料和不同腐蚀产物应采用不同的清除腐蚀产物的方法。
一般有机械法、化学法和电解法三种。
1). 机械法 一般先用自来水冲洗,并用橡皮或硬毛刷擦洗,或用木制刮刀、塑料刮刀刮擦。
对绝大部分疏松腐蚀产物用此法已可清除干净。
但要完全清除掉腐蚀产物以精确测试或检查局部腐蚀状况时,尚需进一步采用化学法或电化学法。
2). 化学法 选择适宜的化学溶液及操作条件通过溶解除去试样表面的腐蚀产物的方法。
为了保护金属基体,在化学清除的溶液中往往需要加入缓蚀剂。
表10-11列出一些常用的清除腐蚀产物的化学方法。
这些方法并不复杂,但在使用时有可能损伤基材,造成试验误差。
为此,应在清除工作的同时,将未经腐蚀的相同尺寸的同种材料作空白试样在相同条件下清洗处理,求其失量,然后在实际试样的失重中减去此数,以取得比较真实的试样失重量。
表1-1 针对不同材质清除腐蚀产物的化学方法材料 溶液时间,min 温度 备注 铝合金70%HNO 32~3 室温 随后轻轻擦洗 20%CrO 3,5%H 3PO 41079~85 o C用于氧化膜不溶解于硝酸的情况铜及其合金15~20%HCl2~3室温随后轻轻擦洗5~10%H2SO42~3 室温随后轻轻擦洗铝及其合金10%醋酸10 沸腾随后轻轻擦洗,除PbO 5%醋酸铵热随后轻轻擦洗,除PbO80g/LNaOH,50g/L甘露糖醇,0.62g/L硫酸肼30或至清除为止沸腾随后轻轻擦洗铁和钢20% NaOH,20g/L锌粉 5 沸腾浓盐酸,50g/LSnCl2+20g/LSbCl325或至清除为止冷搅拌溶液10%或20%HNO320 60o C 用于不锈钢,需避免氯化物的污染含有0.15%有机缓蚀剂的15%的浓H3PO4清除为止室温可去除氧化条件下钢表面上形成的氧化皮镁及其合金15%CrO3,1%AgCrO415 沸腾镍及其合金15~20%HCl 清除为止室温10%H2SO4清除为止室温锡及其合金15%的Na3PO410 沸腾随后轻轻擦洗锌先用10%NH4Cl,然后用15%CrO3,1%AgCrO4520s室温沸腾随后轻轻擦洗饱和醋酸铵清除为止室温随后轻轻擦洗100g/L NaCN 15 室温3). 电化学法选择适当的阳极和电解质,以试样为阴极,外加直流电的电解方法。
电解时阴极产生氢气,在氢气泡的机械作用下,使腐蚀产物剥离,残留的疏松物质可用机械法冲刷除净。
此法效果较好,空白试样失重小。
适用于碳钢和许多金属材料的两种电解操作条件示例如下:电解液为5%H2SO4,阳极为碳棒,阴极为试样,阴极电流密度为20A/dm2,加入有机缓蚀剂(如若丁),2ml/L,温度75o C,暴露时间为3min。
实验用品:导线,开关,0.05欧姆标准电阻,烧杯,万用表,232型饱和甘汞参比电极,盐桥,自制参比电极。
锌-碳钢(面积比1:1),锌-碳钢(面积比1:5);铜-锌,以及游标卡尺。
KQ-100型超声波清洗器(昆山市超声仪器有限公司)HWL-1型恒电位/恒电流仪(山东电讯七厂有限责任公司)自制实验用反应容器实验用腐蚀介质:普通海水、酸化海水pH=3~4实验方法:1.失重法——不同面积比耦合以及单独存在条件下的腐蚀失重2.电位、电流测定——耦合电位和耦合电流,开路电位实验步骤:1.根据实验要求的表面积,以纯锌片为基准面积将纯锌、普通碳钢试片按照1:5(1片)和1:1(各2片)的面积比切割,并除去表面的油污和锈迹;2.以纯锌片为基准面积将纯锌、铜试片按照1:1的面积比切割各自2片,3.选取面积比为1:1:1的锌、碳钢、铜各1片将表面氧化物用砂纸分别打磨除锈、碱液除油、自来水清洗、乙醇清洗晾干,干燥称重后,分别安置在装有天然海水容器中;以自制Ag/AgX电极为参比电极,开始间隔3分钟测定并记录一次各自的开路电位;测定4次后,间隔10分钟测定一次开路电位,实验一小时,将试片取出用自来水冲洗干净,滤纸擦干、吹风机风干后分别称重。
记录表格见表1-34.将洁净并预先分别称重的面积比为1:1和1:5的纯锌和普通碳钢试片以及面积比为1:1的铜-锌试片,按照图1-1所示方法连接好,电阻阻值选取0.05欧姆,间隔10分钟测定一次各自试片附近的电位,以及电阻两端的电位差(注意,电位测定表头的量程以及参比电极的测定位置选取),测定天然海水中的变化,测定1小时。
5.一小时后拆开连接并将试片用自来水冲洗干净,滤纸擦干、吹风机风干后分别称量重量。
6.将使用过的试片、仪表、测试表头等按照要求放置在固定位置。
~50mΩ标准电阻图1-1 实验连接示意图Cu Zn海水数据记录与结果处理分别记录上述各实验现象,并根据实验原理分析产生现象的原因。
表1-2 面积比为1:1:1的纯锌、碳钢、铜分别放置于海水中1个小时前后的重量W0W1纯锌碳钢铜表1-3 面积比为1:1:1的纯锌、碳钢、铜分别放置于海水中1个小时开路电位变化1 min 4 min 7 min 10min 20min 30min 40min 50min 60min锌碳钢铜表1-4不同面积比电偶形成在海水中浸泡1小时质量和电阻两端的电位变化电位试样10min 20min 30min 40min 50min 60min 实验前质量实验结束后质量锌1:碳钢5锌1:碳钢1锌1:铜1表1-3 不同面积比纯锌、碳钢、铜分别放置于海水中1个小时耦合电位变化电位试样时间样品1 min 4 min 7min 10min 20min 30min 40min 50min 60min锌1: 碳钢5 Zn Fe锌1: 碳钢1 Zn Fe锌1: 铜1 Zn Cu分析与讨论1、重量法的优点、缺点和适用范围。
2、电偶腐蚀有什么特点?电位差、面积比等因素对电偶腐蚀的影响规律?3、怎样预防电偶腐蚀?4、为什么选用测定电流的标准电阻需要小于50mΩ?这个电阻的大小对最终测定的电流效率有何影响?附录:伊文思盐水滴试验伊文斯盐水滴试验可以用来区分钢铁表面腐蚀的阴、阳极区。
将一滴加有酚酞和铁氰化钾(K3[Fe(CN)6])指示剂的食盐水3.5 wt% 滴在干净的铁表面,从其颜色的变化可以观察到腐蚀的进行及阴、阳极区。
在缺氧的中心区,发生如下阳极反应:2Fe - 4e → Fe2+在盐水滴外缘,由于氧的浓度较大,发生如下阴极过程:O2 + H2O + 4e → 4OH-这个试验一方面说明了阴阳极反应的相对部位,另一方面指出,由于氧浓差所引起的电化学不均匀性,导致了铁的局部腐蚀。
可以根据实验进行的时间间隔穿插进行伊文思盐水滴试验将一滴加有酚酞和铁氰化钾(K3[Fe(CN)6])指示剂的3.5%食盐水,滴在干净的铁试片表面,观察腐蚀的进行及阴、阳极区各自的现象并给予合理的解释。
实验一电偶腐蚀实验的时间分配及其实验结果与讨论表2-1 实验时间分配阶段时间段min 累计min 备注集体讲解~25 25试样剪切预处理~40 65第一阶段实验60 125拆装及后处理15 140第二阶段试验60 200拆装及其后处理15 215实验结束善后20 235实验结果及讨论电阻阻值校正结果为:51.3mΩ表2-2 实验前后质量变化质量/mg 碳钢锌腐蚀前10.7693 0.7174腐蚀后10.7689 0.7169失重0.0004 0.0005失重速率/g/m2h 0.2941 0.3676表2-3 碳钢-锌面积比为1:1时分别放在海水中的开路电位电位(v)碳钢锌时间0min -0.5426 -1.065910min -0.5982 -1.089120min -0.6162 -1.091130min -0.6263 -1.094640min -0.6349 -1.095650min -0.6259 -1.094560min -0.6338 -1.0888表2-4 实验前后质量变化质量/g 碳钢锌腐蚀前10.1637 0.5295腐蚀后10.1637 0.5283失重0 0.0012失重速率/g/m2h 0 0.8824表2-5 碳钢-锌面积比为1:1时电偶腐蚀的电位电位(v)碳钢锌电阻两端电位时间0min -1.0549 -1.0501 0.14mv10min -1.0505 -1.0710 0.13mv20min -1.0515 -1.0712 0.10mv30min -1.0575 -1.0713 1.13mv40min -1.0677 -1.0679 0.07mv50min -1.0621 -1.0601 0.07mv60min -1.0478 -1.0521 0.06mv电流效率η=m/m0×100%=50.76%表2-6 实验前后质量变化质量/mg 铜锌腐蚀前 2.0916 0.3151腐蚀后 2.0915 0.3149失重0.0001 0.0002失重速率/g/m2h 0.2083 0.4167表2-7 铜-锌面积比为1:1时分别放在海水中的开路电位电位(v)铜锌时间0min -0.2108 -1.043110min -0.2327 -1.092520min -0.2229 -1.091930min -0.2189 -1.094340min -0.2223 -1.086050min -0.2863 -1.086860min -0.2470 -1.0871表2-8 实验前后质量变化质量/g 铜锌腐蚀前 2.2538 0.2691腐蚀后 2.2538 0.2684失重0 0.0007失重速率/g/m2h 0 1.4583表2-9 铜-锌面积比为1:1时电偶腐蚀的电位电位(v)铜锌电阻两端电位时间0min -1.0549 -1.0037 0.07mv10min -1.0666 -1.0727 0.06mv20min -0.8666 -0.8989 0.05mv30min -1.0609 -0.5321 0.05mv40min -1.0295 -1.0511 0.05mv50min -0.3665 -1.0350 0.04mv60min -0.7367 -0.7676 0.04mv电流效率η=m/m0×100%=59.22%表2-10 实验前后质量变化质量/g 碳钢锌腐蚀前10.9760 0.1741 腐蚀后10.9756 0.1739 失重0.0004 0.0002 失重速率/g/m2h 0.2941 0.7353表2-11 碳钢-锌面积比为5:1时分别放在海水中的开路电位电位(v)碳钢锌时间0min -0.5391 -1.047610min -0.5800 -1.088120min -0.5998 -1.096030min -0.6019 -1.093740min -0.6047 -1.091250min -0.6062 -1.089660min -0.66120 -1.08446表2-12 实验前后质量变化质量/g 碳钢锌腐蚀前10.1262 0.1529 腐蚀后10.1262 0.1510 失重0 0.0019 失重速率/g/m2h 0 6.9853表2-13 碳钢-锌面积比为5:1时电偶腐蚀的电位电位(v)碳钢锌电阻两端电位时间0min -1.0184 -1.0196 0.18mv10min -1.0450 -1.0407 0.16mv20min -1.0463 -1.0416 0.13mv30min -1.0467 -1.0542 0.18mv40min -1.0481 -1.0559 0.17mv50min -1.0496 -1.0557 0.11mv60min -1.0483 -1.0552 0.17mv电流效率η=m/m0×100%=50.23%实验小结:由表2-2和表2-4得到,在碳钢和锌片的面积比为1:1时,单独在海水中1小时后碳钢失重0.0004g,锌片失重0.0005g,而导线连接同样时间后碳钢无失重,锌片失重0.0012g;由表2-6和表2-8得到,铜片和锌片面积比为1:1时,1小时后铜片失重0.0001g,锌片失重0.0002g,连接发生电偶腐蚀之后,铜片不失重,锌片失重0.0007g;由表2-10和表2-12得到,碳钢和锌面积比为5:1时,1小时后碳钢失重0.0004g,锌片失重0.0002g,导线连接后碳钢无失重,锌片失重0.0019g。