我国钒钛磁铁矿直接还原分析
钛磁铁矿直接还原——磁选钛铁分离主要影响因素探析
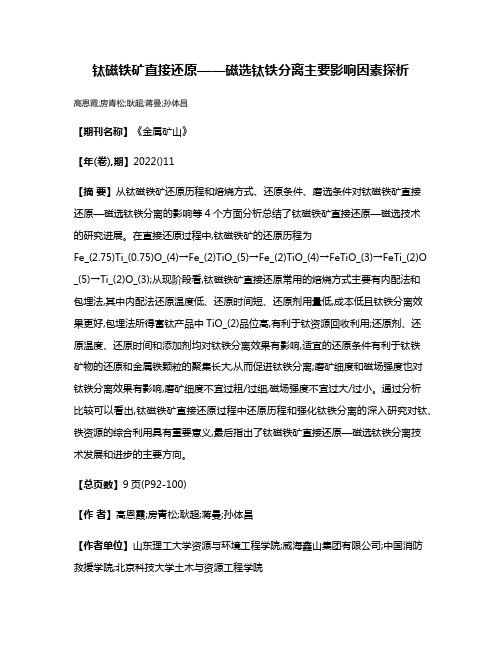
钛磁铁矿直接还原——磁选钛铁分离主要影响因素探析高恩霞;房青松;耿超;蒋曼;孙体昌【期刊名称】《金属矿山》【年(卷),期】2022()11【摘要】从钛磁铁矿还原历程和焙烧方式、还原条件、磨选条件对钛磁铁矿直接还原—磁选钛铁分离的影响等4个方面分析总结了钛磁铁矿直接还原—磁选技术的研究进展。
在直接还原过程中,钛磁铁矿的还原历程为Fe_(2.75)Ti_(0.75)O_(4)→Fe_(2)TiO_(5)→Fe_(2)TiO_(4)→FeTiO_(3)→FeTi_(2)O _(5)→Ti_(2)O_(3);从现阶段看,钛磁铁矿直接还原常用的焙烧方式主要有内配法和包埋法,其中内配法还原温度低、还原时间短、还原剂用量低,成本低且钛铁分离效果更好,包埋法所得富钛产品中TiO_(2)品位高,有利于钛资源回收利用;还原剂、还原温度、还原时间和添加剂均对钛铁分离效果有影响,适宜的还原条件有利于钛铁矿物的还原和金属铁颗粒的聚集长大,从而促进钛铁分离;磨矿细度和磁场强度也对钛铁分离效果有影响,磨矿细度不宜过粗/过细,磁场强度不宜过大/过小。
通过分析比较可以看出,钛磁铁矿直接还原过程中还原历程和强化钛铁分离的深入研究对钛、铁资源的综合利用具有重要意义,最后指出了钛磁铁矿直接还原—磁选钛铁分离技术发展和进步的主要方向。
【总页数】9页(P92-100)【作者】高恩霞;房青松;耿超;蒋曼;孙体昌【作者单位】山东理工大学资源与环境工程学院;威海鑫山集团有限公司;中国消防救援学院;北京科技大学土木与资源工程学院【正文语种】中文【中图分类】TD95;TF55【相关文献】1.添加剂对海滨钛磁铁矿直接还原磁选钛铁分离的影响2.煤泥作还原剂对海滨钛磁铁矿直接还原焙烧磁选的影响3.煤种对钛磁铁矿直接还原-磁选钛铁分离的影响4.还原剂种类对钛磁铁矿直接还原—磁选制备钛酸镁的影响5.CaO对海滨钛磁铁矿精矿直接还原-磁选工艺中还原气氛的影响因版权原因,仅展示原文概要,查看原文内容请购买。
直接还原炼铁工艺现状及攀枝花钒钛磁铁矿处理工艺选择
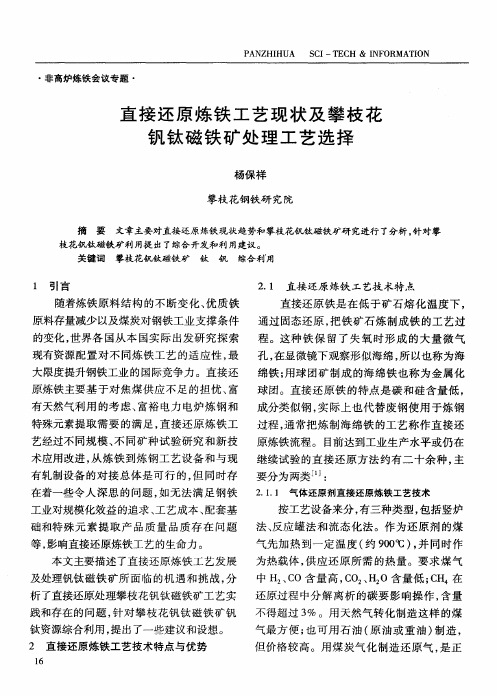
但价格 较高 。用 煤炭气 化制造 还原气 , 是正
第3 5卷
第 4期
攀 枝 花科技 与信 息
( 第 13期 ) 总 0
在 研 究 的课 题 。
排料 , 因此不 怕炉 料粘结 , 操作 温度 较高 , 虽 系 间断作 业 , 产率并 不 低。缺点 是煤 气 利 生
用 差 , 耗 达 ( 34X16千 卡/ )产 品 质 热 达 . 0 吨 , 量 不 均 匀 。 H l海 绵 铁 含 碳 高 ( . % ~ y 12
原炼 铁 主 要 基 于 对 焦 煤 供 应 不 足 的 担 忧 、 富
球团。直接 还原 铁 的特点 是碳 和硅含 量低 ,
有天然气利用 的考虑 、 富裕 电力 电炉炼 钢 和 成分类似钢 , 际上也代替 废钢使 用 于炼 钢 实 特殊元素提取需 要 的满足 , 直接 还原炼 铁工 过程 , 通常把炼 制 海绵铁 的工艺称 作直 接还 艺经过不 同规模 、 同矿 种试验研究 和新 技 原炼铁流程。 目前达到工业生产水平或仍 在 不 术应用改进 , 从炼铁 到炼 钢工艺设备 和 与现 继续试验 的直 接还原 方法 约有二 十余 种 , 主 有轧制设备 的对接 总体是 可行 的, 同时存 要分 为两 类 … : 但
经过预热 、 还原及 冷 却 三个 阶段 。还 原所 得
的 Hy 法 已放弃 四个 反应罐 , l 改用 一个反 应
接近 Mirx法 。 de 的海绵铁 , 却 到 5  ̄ 排 出炉外 , 防再 罐 , 冷 0 C后 以 流态化法 : 流化床 中用煤 气 还原 铁 矿 在 氧化 。还原煤气用 天然气及 竖炉本身 的一部
P ANZ HUA HI
SCI—T ECH & I NF0RMA I rON
直接还原铁工艺技术的对比分析论述

直接还原铁工艺技术的对比分析论述张建国【期刊名称】《资源再生》【年(卷),期】2018(000)002【总页数】5页(P57-61)【作者】张建国【作者单位】北京瀚川鑫冶工程技术有限公司【正文语种】中文在低于矿石融化状态下,通过固态还原,把铁矿石炼制成铁的工艺称作直接还原法,用这种方法生产出的铁也叫作直接还原铁(DRI),由于这种铁保留了失去氧时形成的大量微小气孔,在显微镜下观察形似海绵,所以直接还原铁也称为海绵铁。
直接还原铁是精铁粉在炉内经低温还原形成的低碳多孔状物质,其化学成分稳定,杂质含量少,主要用作电炉炼钢的原料,也可作为转炉炼钢的冷却剂,如果经过二次还原还可供给粉末冶金用。
从上世纪80年代末以来,我国一直宣传推广使用直接还原技术,并对直接还原技术进行了广泛的开发研究,取得了众多成果,为直接还原技术发展奠定了基础。
但是,因铁矿、煤炭、气源等原燃料条件限制,中国直接还原发展的实际成效不大,与钢材、生铁等行业相比还有相当差距。
一、直接还原铁的应用优势直接还原铁生产是指在低于熔化温度之下将铁矿石还原成海绵铁的过程,与传统高炉炼铁方法相比取消了焦炉、烧结等工序,具有流程短、污染小、消耗少,不受炼焦煤短缺影响等优点。
同时海绵铁中硫、磷、硅等有害杂质含量低,有利于电炉冶炼优质纯净钢种。
近年来,由于钢铁产品向小型轻量化、功能高级化、复合化方向发展,因此钢材产品中的非金属材料和有色金属的使用比例在增加,在废钢的破碎分拣过程中,又不能完全有效的剔除非金属和有色金属材料,况且,即使是纯粹完全的黑色废钢料,由于来源不同,化学成分波动也是较大的。
致使加工后的成品入炉废钢的质量很难掌握控制,给电炉炼钢作业带来一定的困难。
如果用一定比例的直接还原铁(30~50%)作为稀释剂与废钢搭配使用,不仅可增加钢的均匀性,还可以改善和提高钢的物理性质,从而达到生产优质钢的目的。
因此,直接还原铁不仅仅是优质废钢的替代品,还是生产优质钢必不可少的高级原料(如天津无缝钢管公司的国外产品设计中就明确要求,必须配置50%的直接还原铁)。
攀枝花钒钛磁铁矿直接还原新工艺流程-攀枝花交流材料

(4)目前,正在开展前期示范生产线放大的可研工作。
转底炉煤基直接还原-电炉熔分冶炼 钒钛磁铁矿新工艺
1、四川龙蟒集团
(1)自2003年起,四川龙蟒集团与攀枝花学院合作研究,进行了大 量钒钛铁精矿生球团制备、转底炉直接还原和电炉熔分工艺试验。
(2)2006-2007年,建成一期7万吨/年示范生产线,进行了3轮工业 性试验。
(3)2008年,进行示范生产线放大,启动了年处理铁精矿20万吨的 二期工程;
攀 枝 花 钒 钛 磁 铁 矿 区 分 布
攀枝花钒钛磁铁矿资源储量
钒钛磁铁矿保有储量
67.3亿吨
钛资源量保有储量
4.28亿吨
钒资源保有储量
1047.86万吨
铬保有储量
696万吨
钴保有储量
152万吨
钪保有储量
23万吨
镓保有储量
21万吨
攀枝花钒钛磁铁矿资源 综合开发利用情况
攀枝花钒钛磁铁矿经过四十多年 的开发,已形成了钒材料、钛材料、 钢铁新材料系列产品。2001年被国 家科技部批准为攀枝花国家新材料 成果转化及产业化基地。2007年新 材料产业实现产值110亿元,成为攀 枝花经济增长的新亮点。
攀枝花---国家新材料成果转化及产业化基地
2001年12月18日,国家科技部批准攀枝花为国家新材 料成果转化及产业化基地,并给予了大力支持。
攀 枝 花 钒 钛 磁 铁 矿 资 源 综 合 开 发 工 艺 流 程 图
钢铁产业
攀枝花钢铁产业作为主导产业,目前已形成年产生铁600多万 吨、钢600多万吨的能力;
1、可全部回收钒钛铁精矿中的钛资源。经转底炉还原后的金 属化球团经过电弧炉熔化分离后,可得到含量为50%以上 的熔分钛渣和含钒生铁,实现铁钒与钛的分离。熔分钛渣 可用于硫酸法钛白生产原料。
电炉熔分工艺处理钒钛磁铁矿

电炉熔分工艺处理钒钛磁铁矿电炉熔分工艺处理钒钛磁铁矿一、引言钒钛磁铁矿是一种重要的钛资源,广泛应用于冶金、化工、建材等领域。
然而,由于其复杂的化学成分和矿物结构,其加工和利用一直面临着挑战。
电炉熔分工艺是一种被广泛采用的处理钒钛磁铁矿的方法。
该方法通过利用电炉的高温和电能,将钒钛磁铁矿矿石在还原气氛下进行熔融和分离,以获得钛铁合金和钒铁合金等有价值的产品。
本文将深入探讨电炉熔分工艺处理钒钛磁铁矿的原理、技术及其在实际应用中的优势和发展前景。
二、电炉熔分工艺的原理及技术(1)原理概述电炉熔分工艺是利用电炉高温和电能的特点,将钒钛磁铁矿在还原条件下进行熔融和分离的过程。
在这个过程中,钒和铁进入钒铁合金,而钛则进入钛铁合金。
这种工艺的基本原理是根据各元素的熔点和还原性能的不同,通过合理的炉内温度和还原气氛控制,实现钒、铁、钛的分离和提取。
(2)技术要点在电炉熔分工艺中,关键的技术要点包括矿石预处理、还原条件控制、温度控制和产物分离等。
矿石预处理是为了提高矿石中有价值元素的回收率和产物质量。
常见的矿石预处理方法包括碎石、磁选和浸出等。
还原条件控制对于熔分工艺的成功与否至关重要。
合理的还原条件能够保证有价值元素的还原率和产物质量。
常用的还原条件包括还原剂种类和用量,还原温度和还原时间等。
温度控制是电炉熔分工艺中一个关键的环节。
适当的温度能够保证矿石充分熔化和元素的分离,同时避免产生不良的副反应。
温度控制的方法包括调整电炉电极的位置和电流强度等。
产物分离是电炉熔分工艺中的一项重要工作。
通过合理的分离装置,将钒铁合金和钛铁合金等产品分离出来,以提高产品质量和价值。
三、电炉熔分工艺的优势和发展前景电炉熔分工艺作为一种兼具深度和广度的处理钒钛磁铁矿的方法,具有以下优势和发展前景。
电炉熔分工艺对于复杂矿石的处理能力强。
由于钒钛磁铁矿的化学成分和矿物结构多样复杂,传统的处理方法存在着诸多限制。
而电炉熔分工艺通过熔融和分离的方式,能够有效地处理各种类型的矿石,实现有价值元素的高效提取。
钒钛磁铁矿精矿钙化焙烧直接提钒研究
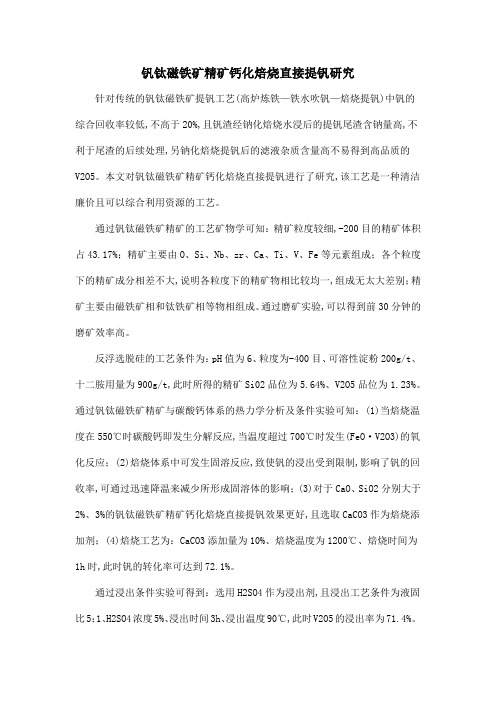
钒钛磁铁矿精矿钙化焙烧直接提钒研究针对传统的钒钛磁铁矿提钒工艺(高炉炼铁—铁水吹钒—焙烧提钒)中钒的综合回收率较低,不高于20%,且钒渣经钠化焙烧水浸后的提钒尾渣含钠量高,不利于尾渣的后续处理,另钠化焙烧提钒后的滤液杂质含量高不易得到高品质的V2O5。
本文对钒钛磁铁矿精矿钙化焙烧直接提钒进行了研究,该工艺是一种清洁廉价且可以综合利用资源的工艺。
通过钒钛磁铁矿精矿的工艺矿物学可知:精矿粒度较细,-200目的精矿体积占43.17%;精矿主要由O、Si、Nb、zr、Ca、Ti、V、Fe等元素组成;各个粒度下的精矿成分相差不大,说明各粒度下的精矿物相比较均一,组成无太大差别;精矿主要由磁铁矿相和钛铁矿相等物相组成。
通过磨矿实验,可以得到前30分钟的磨矿效率高。
反浮选脱硅的工艺条件为:pH值为6、粒度为-400目、可溶性淀粉200g/t、十二胺用量为900g/t,此时所得的精矿Si02品位为5.64%、V2O5品位为1.23%。
通过钒钛磁铁矿精矿与碳酸钙体系的热力学分析及条件实验可知:(1)当焙烧温度在550℃时碳酸钙即发生分解反应,当温度超过700℃时发生(FeO·V2O3)的氧化反应;(2)焙烧体系中可发生固溶反应,致使钒的浸出受到限制,影响了钒的回收率,可通过迅速降温来减少所形成固溶体的影响;(3)对于CaO、SiO2分别大于2%、3%的钒钛磁铁矿精矿钙化焙烧直接提钒效果更好,且选取CaCO3作为焙烧添加剂;(4)焙烧工艺为:CaCO3添加量为10%、焙烧温度为1200℃、焙烧时间为1h时,此时钒的转化率可达到72.1%。
通过浸出条件实验可得到:选用H2SO4作为浸出剂,且浸出工艺条件为液固比5:1、H2SO4浓度5%、浸出时间3h、浸出温度90℃,此时V2O5的浸出率为71.4%。
钒钛铁精矿含碳球团直接还原试验

钒 钛 铁 精 矿 含碳 球 团直 接 还 原 试 验
李俊 翰 , 邱 克 辉 , 杨 绍利
( 1 .成都 理 工 大学, 成都 6 1 0 0 5 9 ;
2 .攀枝 花 学 院 钒 钛 资源 综合 利用 四川 省 重点 实验 室 , 四川攀 枝花 6 1 7 0 0 0 )
摘要 : 采 用 正 交 试 验 和 单 因素 试 验 考 察 还 原 温 度 、 配碳 量 ( n c n o ) 、 还 原 时 间 对 某 钒 钛 磁 铁 矿 精 矿 直 接 还
0 . 4 ,t he me t a l l i z a t i o n r a t e o f r e d uc e d p e l l e t s c a n be i mpr o ve d t o 9 1 . 7 7 ,wi t h p ha s e c o mp os i t i o n of me — t a l l i c i r o n . Ke y wo r ds : v a na d i um a n d t i t a ni u m i r o n c on c e n t r a t e s;r e du c t i on;m e t a l l i z a t i o n r a t e;or t h og o na l e x pe r i me nt s
2 .S i c h u a n Pr ov i nc e Ke y La b o r a t o r y o f Co mp r e he n s i v e Ut i l i z a t i o n f o r Va na d i u m & Ti t a n i u m Re s ou r c e s.
Pa nz h i h ua Uni v e r s i t y,Pa nz h i h ua 6 1 7 0 0 0,Si c h u a n,Ch i n a )
我国煤基直接还原炼铁工艺发展
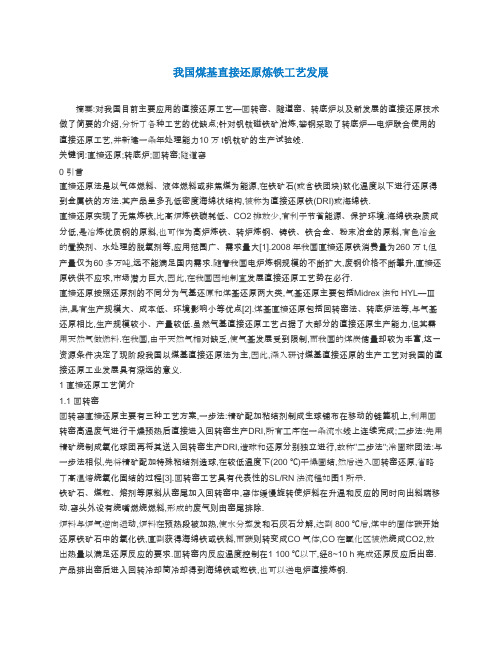
我国煤基直接还原炼铁工艺发展摘要:对我国目前主要应用的直接还原工艺—回转窑、隧道窑、转底炉以及新发展的直接还原技术做了简要的介绍,分析了各种工艺的优缺点;针对钒钛磁铁矿冶炼,攀钢采取了转底炉—电炉联合使用的直接还原工艺,并新建一条年处理能力10万t钒钛矿的生产试验线.关键词:直接还原;转底炉;回转窑;隧道窑0 引言直接还原法是以气体燃料、液体燃料或非焦煤为能源,在铁矿石(或含铁团块)软化温度以下进行还原得到金属铁的方法.其产品呈多孔低密度海绵状结构,被称为直接还原铁(DRI)或海绵铁.直接还原实现了无焦炼铁,比高炉炼铁碳耗低、CO2排放少,有利于节省能源、保护环境.海绵铁杂质成分低,是冶炼优质钢的原料,也可作为高炉炼铁、转炉炼钢、铸铁、铁合金、粉末冶金的原料,有色冶金的置换剂、水处理的脱氧剂等,应用范围广、需求量大[1].2008年我国直接还原铁消费量为260 万t,但产量仅为60多万吨,远不能满足国内需求.随着我国电炉炼钢规模的不断扩大,废钢价格不断攀升,直接还原铁供不应求,市场潜力巨大,因此,在我国因地制宜发展直接还原工艺势在必行.直接还原按照还原剂的不同分为气基还原和煤基还原两大类,气基还原主要包括Midrex法和HYL—Ⅲ法,具有生产规模大、成本低、环境影响小等优点[2].煤基直接还原包括回转窑法、转底炉法等,与气基还原相比,生产规模较小、产量较低.虽然气基直接还原工艺占据了大部分的直接还原生产能力,但其需用天然气做燃料.在我国,由于天然气相对缺乏,使气基发展受到限制,而我国的煤炭储量却较为丰富,这一资源条件决定了现阶段我国以煤基直接还原法为主,因此,深入研讨煤基直接还原的生产工艺对我国的直接还原工业发展具有深远的意义.1 直接还原工艺简介1.1 回转窑回转窑直接还原主要有三种工艺方案,一步法:精矿配加粘结剂制成生球铺布在移动的链篦机上,利用回转窑高温废气进行干燥预热后直接进入回转窑生产DRI,所有工序在一条流水线上连续完成;二步法:先用精矿烧制成氧化球团再将其送入回转窑生产DRI,造球和还原分别独立进行,故称"二步法";冷固球团法:与一步法相似,先将精矿配加特殊粘结剂造球,在较低温度下(200 ℃)干燥固结,然后送入回转窑还原,省略了高温焙烧氧化固结的过程[3].回转窑工艺具有代表性的SL/RN法流程如图1所示.铁矿石、煤粒、熔剂等原料从窑尾加入回转窑中,窑体缓慢旋转使炉料在升温和反应的同时向出料端移动.窑头外设有烧嘴燃烧燃料,形成的废气则由窑尾排除.炉料与炉气逆向运动,炉料在预热段被加热,使水分蒸发和石灰石分解,达到800 ℃后,煤中的固体碳开始还原铁矿石中的氧化铁,直到获得海绵铁或铁料,而碳则转变成CO气体,CO在氧化区被燃烧成CO2,放出热量以满足还原反应的要求.回转窑内反应温度控制在1 100 ℃以下,经8~10 h完成还原反应后出窑.产品排出窑后进入回转冷却筒冷却得到海绵铁或粒铁,也可以送电炉直接炼钢.与高炉工艺相比较,回转窑工艺设备简单,投资少,适用于地方钢铁工业,弥补了高炉—转炉工艺的不足,此外,回转窑还适用于复合矿冶炼,冶金灰尘及各种工业废渣的回收利用,减少环境污染,降低了钢铁生产能耗.同时,回转窑工艺也存在一些缺点,包括窑内结圈、还原温度低(1 100 ℃以下)、流程长、对块矿或球团矿冷强度要求高、要求使用低硫煤等[4].我国山东鲁中矿山公司通过采取提高冷固烧结球团的冷热态强度、加强还原煤的选择和管理、优化回转窑的送风、抛煤、控温温度等措施,预防并降低回转窑结圈,取得了较好的收效.图1 SL/RN法工艺流程1.2 隧道窑隧道窑工艺即将精矿粉、煤粉、石灰石粉,按照一定的比例和装料方法,分别装入还原罐中,然后把罐放在罐车上,推入条形隧道窑中或把罐直接放到环形轮窑中,料罐经预热到1 150 ℃加热焙烧和冷却之后,得到直接还原铁.目前江苏永钢集团拥有两条260 m长煤气隧道窑,为亚洲最长隧道窑.隧道窑生产海绵铁工艺流程如图2所示.图2 隧道窑生产海绵铁工艺流程煤基隧道窑直接还原工艺具有技术成熟、作简单的特点,可因地制宜采用此工艺,利用当地小型分散的铁矿及煤矿资源优势,发展直接还原铁生产,为电炉提供优质原料.但是,总体上讲,我国隧道窑直接还原中存在生产规模较小、能耗高、污染严重、缺乏稳定的原料供应渠道等问题[5],所以,提高机械化程度、改变原料入炉方式、改进燃料及其燃烧、增设余热回收等成为各厂家不断努力改进工艺的方向.我国已建成或正在建设的隧道窑有100多座,约70多个单位规划建设产能5~30 万t/a的隧道窑直接还原铁厂,在不断总结实践经验的基础上,改进现行工艺,开发出诸如大型隧道窑直接还原、AMR—CBI隧道窑直接还原工艺、宽体球状海绵铁隧道窑、L-S快速还原工艺等多种新技术,掀开了隧道窑工艺规模扩大、产能提高、机械及自动化提升的序幕.1.3 转底炉转底炉煤基直接还原是最近几十年间发展起来的炼铁新技术,代表工艺为Fastmet,它由美国Midrex公司与日本神户制钢于20世纪60年发,是采用环形转底炉生产直接还原铁的一种方法.经过多年的半工业性试验和深入的可行性研究,现已完成工艺作参数和装置设计的优化.Fastmelt和ITmk3工艺是在此基础上增加对直接还原铁的处理.图3显示了这三种以转底炉为主体的直接还原工艺流程.图3 转底炉直接还原工艺流程煤粉与铁精粉按比例混匀制成球团,干燥后以1~3层球铺放在转底炉床面,随着炉底的旋转,炉料依次经过预热区、还原区和冷却区.还原区内球团被加热到1 250~1 350 ℃,由于煤粉与铁氧化物紧密接触,铁氧化铁被碳迅速还原成DRI,成品在800~1 000 ℃左右连续从转底炉卸出.球团矿在炉底停留8~30 min,这取决于原料特性、料层厚度及其他因素,成品可作电炉热装炉料或者转炉炉料,也可冷却或生产热压块(HBI).Fastmet工艺技术特点:①在高温敞焰下加热实现快速还原,反应时间只需10~20 min,生产效率高;②原料来源广泛,铁原料方面,除使用高品位粉矿、精矿外,还可用氧化铁皮、代油铁泥、炼钢粉尘、含En、Pb、As等有害杂质的铁矿等;还原剂方面,除煤以外焦末、沥青均可利用,不必担心出现结圈问题;③炉料相对炉底静止,对炉料强度要求不高;④废气中含有大量显热,可用作预热空气、干燥原料等[6]. Fastmelt工艺流程基本与Fastmet一致,只是在后续添加一个熔炉来生产高质量的液态铁水.Itmk3工艺是使金属化球团在转底炉中还原时熔化,生成铁块(Nuggets),同时脉石也熔化,形成渣铁分离.当然转底炉也存在着设备复杂、炉内气氛难控制、传热效率低以及对还原剂硫含量要求严格的缺点.就目前转底炉工艺开发的水平和规模而论,与高炉还有较大差距,但仍存在发展的广阔空间,天津荣程联合钢铁集团已兴建一条100万t级Fastmet生产线,建成目前世界最大的转底炉.另外,用转底炉可处理一些特殊铁矿,如含锌、铅、砷等有害杂质,或含镍、钒、钛等有用元素,均可利用转底炉的工艺优势,或高温挥发,或选择性还原,配合后续工艺,实现资源综合利用.马钢尘泥脱锌转底炉工程项目于2008年5月开工建设,2009年7月6日正式竣工投产,建成了整套转底炉(RHF)脱锌工艺技术装置,不仅解决了含锌尘泥循环利用的后顾之忧,而且将综合利用技术上升到高品质资源化水平.1.4 其他新工艺1.4.1 PF法煤基竖炉直接还原工艺中冶集团北京冶金设备研究设计总院,结合国内情况创新发明了PF法竖炉直接还原工艺.PF法是在吸收K-M法外热式竖炉煤基直接还原工艺的经验基础上,设计的以一种中国特色的罐式还原炉为主反应器的直接还原法.这种工艺技术可靠,技术经济指标在各种煤基直接还原工艺中属先进水平.PF法直接还原工艺流程如图4所示.图4 PF法直接还原工艺流程PF法直接还原工艺主要特点[1]:1)主体设备选用外热式竖炉,预热、还原、冷却三段根据不同的作用和温度选用不同材质和结构,便于传热和化学反应进行,提高热效率和设备寿命.2)原燃料适用性强,对精矿、还原剂和燃料没有特殊要求.3)采用外配碳工艺,还原剂适当过量,扩大了煤的选用范围,造球工艺也因不定量配入煤粉而简化,球团强度较高,DRI质量较好.4)多个反应罐可并列组成任意规模的还原设备,设计和组织生产灵活.1.4.2 低温快速还原新工艺2004年钢铁研究总院提出了低温快速冶金新工艺.新工艺利用纳米晶冶金技术的特点将铁矿的还原温度降低到700 ℃以下.新流程分为气基和煤基两种方法,工艺流程如图5、图6所示.图5 煤基低温快速还原新工艺图6 气基低温快速还原新工艺煤基法使用煤粉为还原剂,在700℃左右快速还原铁精矿粉;气基法使用还原性气体还原铁精矿粉,还原温度可低于600℃.新工艺具有能耗低、环境友好等特点,省去了烧结或造球工艺,缓解了钢铁行业对焦煤的依赖,符合我国国情[7].2 攀钢现状钒钛磁铁矿是攀西地区的特色资源,与普通矿相比,钒钛矿直接还原温度较高、还原时间较长,还原过程产生特有的膨胀粉化现象,因此,存在竖炉结瘤、流化床失流和黏结、回转窑结圈等技术难题.高炉流程冶炼钒钛矿,只回收了铁和钒,钛进入高炉渣没有回收,造成钛资源的大量流失.2005年以来,攀钢科研人员在充分吸收、借鉴新流程及相关研究成果的基础上,通过大量的试验研究,针对钒钛磁铁矿特点,提出并验证了钒钛磁铁矿"转底炉直接还原—电炉深还原—含钒铁水提钒—含钛炉渣提钛"工艺路线,彻底打通了钒钛矿资源综合利用新工艺流程,稳定获得了质量满足要求的低碳生铁、达到GB3283-87要求的片状V2O5和PTA121质量要求的钛白产品.依托该研究成果,攀钢集团攀枝花钢铁研究院于2008年5月4日正式启动了攀钢10 万t/a钒钛矿资源综合利用新工艺中试线工程项目,新建一条转底炉—熔分电炉联合使用,年处理能力10万t钒钛矿的试验生产线,为更深入地研究实践,实现转底炉处理钒钛矿的规模化生产提供了广阔的平台.中试线工艺流程如图7所示.本流程采用硫含量较低的白马铁精矿,还原剂采用无烟煤煤粉,粘结剂为有机粘结剂,原料混合后经高压压球机压球,生球烘干后进入转底炉系统.球团在转底炉内停留10~30 min后出料,金属化球团直接热装进入熔分电炉,在一定温度下还原后,产出含钒铁水及含钛炉渣.继续对铁水进行脱硫、提钒后,得到半钢、脱硫渣及钒渣,半钢进入铸铁机铸铁,生产出铸铁块.钛渣制取钛白,实验室条件下钛回收率达到80%以上;钒渣制取钒氧化物(V2O5),实验室条件下,钒回收率达到65%以上.与高炉流程相比,转底炉流程采用100%钒钛矿冶炼,克服了高炉流程必须配加普通矿的不足,在当前铁资源紧张的形势下,有助于充分发挥攀西地区资源优势,拉动区域经济发展.此外,转底炉流程的铁精矿不需烧结处理,不使用焦炭,从根本上避免了烧结烟气脱硫、焦煤资源采购困难以及环保压力大等问题.3 结语图7 资源综合利用中试线工艺流程煤炭资源总量丰富、焦煤短缺,铁矿资源储量大、富矿少、贫矿和共生矿多是中国钢铁工业面临的现实状况.这种能源、资源结构给煤基直接还原法生产海绵铁的发展提供了机遇.转底炉直接还原技术由于在生产率、规模化、投资费用、单位成本等方面都占有明显的优势,可作为发展直接还原技术的首选工艺.鉴于转底炉处理钒钛磁铁矿技术尚属世界首创,并无较多的经验借鉴,因此要大力开展针对钒钛磁铁矿直接还原的基础研究工作,在实践中借鉴各种直接还原方法已取得的成果,开拓创新,开创钒钛矿直接还原新纪元.参考文献[1] 陈守明,黄超,张金良.煤基竖炉直接还原工艺//2008年非高炉炼铁年会文集.中国金属学会,2008:132-135.[2] 杨婷,孙继青.世界直接还原铁发展现状及分析.世界金属导报,2006.[3] 刘国根,邱冠周,王淀佐.直接还原炼铁中的粘结剂.矿产综合利用,2001(4):27-30.[4] 韩跃新,高鹏,李艳军.白云鄂博氧化矿直接还原综合利用前景.金属矿山,2009 (5):1-6.[5] 魏国,赵庆杰,沈峰满,等.非高炉生产技术进步//2004年全国炼铁生产技术暨炼铁年会文集.2004:878-882.[6] 陶晋. 环形转底炉直接还原工艺现状及发展趋势. 冶金信息工作, 1997.6.[7] 郭培民,赵沛,张殿伟.低温快速还原炼铁新技术特点及理论研究.炼铁,2007,26(1): 57-60.来源:攀枝花钢铁研究院网站。
钒钛磁铁矿中钒钛高效回收与高值利用技术-概述说明以及解释

钒钛磁铁矿中钒钛高效回收与高值利用技术-概述说明以及解释1.引言1.1 概述钒钛磁铁矿是一种重要的矿石资源,广泛存在于世界各地。
它的主要成分是氧化钒和氧化钛,其中包含了丰富的钒、钛等金属元素。
由于其中的钒和钛具有很高的价值,在工业生产中有着广泛的应用前景。
然而,目前钒钛磁铁矿的回收与利用技术仍然面临着一些挑战。
钒钛高效回收与高值利用技术的发展对于提高钒钛磁铁矿的资源利用率、降低生产成本以及促进可持续发展具有重要意义。
本文将从钒钛磁铁矿的特点与应用出发,介绍钒钛磁铁矿的组成和物理性质,以及其在钢铁、镁合金、化工等领域的广泛应用。
在此基础上,将重点探讨钒钛高效回收技术。
通过介绍不同的回收方法和技术,如化学法、物理法和生物法等,以及其优缺点和适用范围,来提高钒钛磁铁矿的回收效率和产出纯度。
同时,还将分析钒钛磁铁矿高值利用技术的前景,包括钒钛合金、催化剂、电池材料等方面的应用潜力,并展望未来的发展方向。
通过本文的研究,我们可以深入了解钒钛磁铁矿的特点和应用,了解不同的高效回收技术,为实现钒钛磁铁矿的资源化和高值利用提供科学依据和技术支持。
对于相关行业的发展和经济发展具有重要意义。
希望本文的研究成果对于推动钒钛磁铁矿资源的可持续利用有所贡献,并为后续研究提供参考。
1.2文章结构文章结构部分的内容可以按照以下方式编写:文章结构:本文主要分为引言、正文和结论三个部分。
1. 引言:引言部分主要概述了本文的研究背景和意义,并介绍了钒钛磁铁矿的重要性和应用前景。
通过对钒钛磁铁矿的特点和存在的问题进行分析,引出了需要进行高效回收与高值利用的技术研究的必要性。
2. 正文:2.1 钒钛磁铁矿的特点与应用:在本节中,将详细介绍钒钛磁铁矿的化学组成、物理性质以及广泛应用的领域。
通过对钒钛磁铁矿的特性分析,可以更好地理解其在工业生产中的重要性和现有困难,从而为后续的高效回收与高值利用技术探索奠定基础。
2.2 钒钛高效回收技术:本节将重点介绍目前已有的钒钛高效回收技术,并对其进行评估和比较。
钒钛磁铁精矿回转窑预还原中试试验研究

钒钛磁铁精矿回转窑预还原中试试验研究栾志华;宋志伟【摘要】回转窑预还原是"磁选―回转窑预还原―电炉熔炼"工艺处理钒钛磁铁矿的关键环节.本文通过中试试验研究了利用该工艺处理莫桑比克Tenge钒钛磁铁矿过程中回转窑预还原指标影响因素,试验给出了钒钛磁铁矿的理化指标及回转窑预还原温度、预还原时间、煤矿比等几个主要工艺技术参数和条件,达到了试验预期目的,确定了"磁选—回转窑预还原—电炉熔炼"未制粒钒钛磁铁精矿的可行性,为工业化生产设计提供了技术依据.【期刊名称】《有色设备》【年(卷),期】2018(000)004【总页数】4页(P10-12,15)【关键词】钒钛磁铁精矿;中试试验;回转窑;预还原;金属化率【作者】栾志华;宋志伟【作者单位】中国有色(沈阳)冶金机械有限公司,辽宁沈阳110141;中国有色(沈阳)冶金机械有限公司,辽宁沈阳110141【正文语种】中文【中图分类】TQ172.6220 前言莫桑比克Baobab公司为了开发其拥有的Tenge矿,进行了Tenge矿的工艺技术开发及可行性研究报告的编制。
该项目决定采用“磁选—回转窑预还原—电炉熔炼”工艺处理钒钛磁铁矿,目的是降低成本、取得良好经济效益。
“磁选—回转窑预还原—电炉熔炼”工艺目前大多数采用首先将钒钛磁铁矿磁选得到精矿,然后将精矿磨细制粒并在低温下预还原为金属化球团,再将金属化球团在电炉内进行冶炼,实现钒钛磁铁精矿的冶炼分离并且获得优质的含钒铁水[1]。
本次中试试验的目的是打破传统工艺,研究钒钛磁铁精矿在未制粒的条件下进行回转窑预还原的可行性,并为工业生产设计提供依据。
因此,本文在研究钒钛磁铁精矿基本特性的基础上,针对回转窑预还原工艺特点,通过中试试验系统地考察预还原温度、预还原时间、煤矿比等几个主要因素对钒钛磁铁精矿未制粒条件下回转窑预还原指标,即有价金属Fe金属化率的影响,最终确定钒钛磁铁精矿未制粒条件下回转窑预还原的可行性及适宜的理想条件。
钛铁矿转底炉固相直接还原工艺制备高钛渣
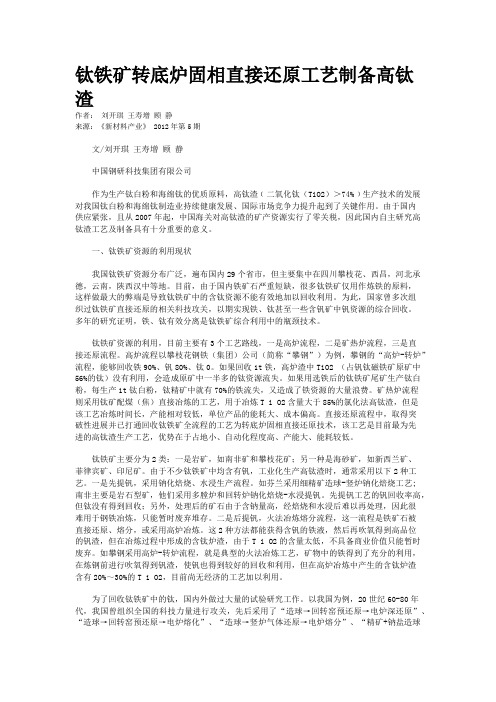
钛铁矿转底炉固相直接还原工艺制备高钛渣作者:刘开琪王寿增顾静来源:《新材料产业》 2012年第5期文/刘开琪王寿增顾静中国钢研科技集团有限公司作为生产钛白粉和海绵钛的优质原料,高钛渣﹝二氧化钛(TiO2)>74%﹞生产技术的发展对我国钛白粉和海绵钛制造业持续健康发展、国际市场竞争力提升起到了关键作用。
由于国内供应紧张,且从2007年起,中国海关对高钛渣的矿产资源实行了零关税,因此国内自主研究高钛渣工艺及制备具有十分重要的意义。
一、钛铁矿资源的利用现状我国钛铁矿资源分布广泛,遍布国内29个省市,但主要集中在四川攀枝花、西昌,河北承德,云南,陕西汉中等地。
目前,由于国内铁矿石严重短缺,很多钛铁矿仅用作炼铁的原料,这样做最大的弊端是导致钛铁矿中的含钛资源不能有效地加以回收利用。
为此,国家曾多次组织过钛铁矿直接还原的相关科技攻关,以期实现铁、钛甚至一些含钒矿中钒资源的综合回收。
多年的研究证明,铁、钛有效分离是钛铁矿综合利用中的瓶颈技术。
钛铁矿资源的利用,目前主要有3个工艺路线,一是高炉流程,二是矿热炉流程,三是直接还原流程。
高炉流程以攀枝花钢铁(集团)公司(简称“攀钢”)为例,攀钢的“高炉-转炉”流程,能够回收铁90%、钒80%、钛0。
如果回收1t铁,高炉渣中TiO2 (占钒钛磁铁矿原矿中56%的钛)没有利用,会造成原矿中一半多的钛资源流失。
如果用选铁后的钛铁矿尾矿生产钛白粉,每生产1t钛白粉,钛精矿中就有70%的铁流失,又造成了铁资源的大量浪费。
矿热炉流程则采用钛矿配煤(焦)直接冶炼的工艺,用于冶炼T i O2含量大于85%的氯化法高钛渣,但是该工艺冶炼时间长,产能相对较低,单位产品的能耗大、成本偏高。
直接还原流程中,取得突破性进展并已打通回收钛铁矿全流程的工艺为转底炉固相直接还原技术,该工艺是目前最为先进的高钛渣生产工艺,优势在于占地小、自动化程度高、产能大、能耗较低。
钛铁矿主要分为2类:一是岩矿,如南非矿和攀枝花矿;另一种是海砂矿,如新西兰矿、菲律宾矿、印尼矿。
钒钛磁铁矿含碳球团转底炉直接还原实验研究

第9卷增刊1 过 程 工 程 学 报 V ol.9 Suppl. No.1 2009 年 6月 The Chinese Journal of Process Engineering June 2009收稿日期:2008−10−22,修回日期:2009−02−17作者简介:刘征建(1982−),男,辽宁省黑山县人,博士研究生,钢铁冶金专业,E-mail: liuzhengjian@.钒钛磁铁矿含碳球团转底炉直接还原实验研究刘征建, 杨广庆, 薛庆国, 张建良, 杨天钧(北京科技大学冶金与生态工程学院,北京 100083)摘 要:对转底炉直接还原钒钛磁铁矿新工艺进行了实验研究,将钒钛磁铁矿精矿粉与煤粉等混合,采用压球机压球,并用石油液化气同空气混合燃烧生成的热烟气干燥生球,通过正交实验考察C/O 、焙烧时间和焙烧温度3个因素对金属化率与抗压强度的影响,得出最优的实验方案是:C/O 为1.3,焙烧温度为1330℃,焙烧时间为25 min. 通过XRD 分析发现在金属化率较高的球团中存在假板钛矿.关键词:资源综合利用;钒钛磁铁矿;转底炉;直接还原中图分类号:TF521 文献标识码:A 文章编号:1009−606X(2009)S1−0051−051 前 言钒钛磁铁矿是一种铁、钒、钛等有价元素共生的复合矿,普通高炉冶炼钒钛磁铁矿的弊端日益凸显,一是钛资源流失严重,占钒钛磁铁原矿中钛总量的一半以上;二是高炉炼铁必须使用焦碳,要消耗大量稀缺而昂贵的焦煤资源,而且炼焦过程污染环境严重[1].进入21世纪以来,随着优质含铁原料供应的日趋紧张和环保要求的日益严格,原料适应性强、能耗低、环境友好的直接还原技术获得了快速发展,出现了诸多新工艺和新技术,转底炉直接还原技术是其中较为典型的代表[2]. 转底炉出现于1978年,最初是应含铁废料和粉尘的处理要求而产生的,1995年以后逐步发展成使用普通铁精矿为原料生产DRI 的直接还原新工艺[3−5]. 转底炉直接还原具有高温、快速的工艺特点和炉料与炉底相对静止的设备特点,能较好的满足钒钛磁铁矿直接还原要求[6]. 共性技术的发展为钒钛磁铁矿直接还原创造了良好的外部条件,在此基础上针对钒钛磁铁矿自身特点,开展铁钒与钛高效分离研究、钒钛提取回收技术研究,实现转底炉直接还原—电炉深还原的产业化生产,达到铁、钒、钛元素分离与综合回收利用的目标. 本工作以钒钛磁铁矿精矿粉、煤粉和粘结剂等为原料,设计正交实验进行钒钛磁铁矿含碳球团转底炉直接还原生产金属化球团的基础研究,为后续的装备设计与工业生产探索规律.2 实验原料实验含铁原料采用某产地的钒钛磁铁矿,化学成分如表1所示.表1 钒钛磁铁矿精矿粉成分Table 1 Composition of vanadic titanomagnetite (%, ω)TFe FeO TiO 2V 2O 5 SiO 2 Al 2O 3 CaOMgO51.46 31.0212.430.53 5.96 5.30 1.983.41此钒钛磁铁矿主要由钛磁铁矿、钛铁矿、硫化矿和脉石矿物等4部分组成. 钛磁铁矿是磁铁矿、钛铁晶石、镁铝尖晶石、钛铁矿片晶复合体. 它占总矿物量的44%左右,含铁57%,是回收铁的主要工业矿物. 由于钛磁铁矿中有4种矿物密切共生,磁铁矿为主晶,其他为客晶. 客晶的粒度极细,不能用机械方法使其单体分离,使所得铁精矿中含有较高的钛、钒、镓、镁、钙、铝、硅等元素,铁品位一般较低;钛铁矿占总矿物量的9.5%,除少量赋存于钛磁铁矿外,大部分单体粒状产出,充填于脉石颗粒之间或铁钛氧化物与脉石之间. 含TiO 2 10.7%,是回收钛的工业矿物. 但其含有较高的钙镁,这些杂质以类质同象赋存在钛铁矿中,因此钛精矿中TiO 2含量一般为46%~48%,钙镁含量达7%~8%;硫化矿占总矿物量的1%,其中磁黄铁矿占硫化矿的95%,是回收硫、钴、镍的工业矿物;脉石矿物以钛普通辉石和斜长石为主,钛普通辉石占总矿物的28%~29%,是回收钪的主要矿物,斜长石占18%~19%.所用固体燃料为宁夏太西无烟煤,工业分析结果如表2所示.表2 煤粉工业分析结果Table 2 Industrial analysis of pulverized coal (%, ω)Fixed carbon V olatile Ash86.47 8.58 4.953 正交实验52 过程工程学报第9卷为了准确控制水分的加入量,混料前所有原料在105℃下干燥2 h,每次实验干料重量约为2.5 kg,人工混料30 min左右. 采用对辊压球机造球,压力可调,所造生球为扁圆形.干燥采用鼓风和抽风两种模式,基本流程是液化石油气同空气混合在燃烧室燃烧,生成的热烟气对含水生球进行干燥. 通过调节液化石油气和空气量来调节干燥入口温度和干燥的风速,本实验中入口温度控制在250℃左右,干燥风速为1.0和1.5 m/s,干燥时间选择10, 15和20 min.焙烧在管式炉中进行,干燥球团用吊篮盛装.采用正交实验考察C/O、焙烧温度和焙烧时间3个因素对含碳球团金属化率和抗压强度的影响,水平设计如表3.表3 实验因素与水平Table 3 Factors and levels of the experimentsLevelFactor A,C/OB,roasting temperature (℃)C,roasting time (min)1 1.31250 152 1.51300 203 1.11330 254 实验结果及分析4.1 造球实验本实验造球压强为15 MPa,转速为10 r/min,膨润土配加比例为3%.4.2 干燥实验用C/O为1.3的1#, 2#, 3#生球进行干燥实验,实验结果如表4所示.表4 干燥实验方案及结果Table 4 Scheme and results of drying experimentNo. DryingmethodGas flowvelocity (m/s)Gas flowrate (m3/h)Drying time(min)Weight of greenballs (g)Weight afterdrying (g)Water content ofgreen balls (%)Dehydration rate(%)1 Blast 1 24 10 1627.8 1479.8 11.93 76.192 Blast 1 24 15 1601.7 1429.4 11.89 90.493 Blast 1 24 20 1594.1 1410.4 11.96 96.32 3 Suction 1 24 15 1608.3 1438.2 11.52 91.84通过实验数据可以看出如下规律[7,8].(1) 鼓风干燥和抽风干燥两种形式的干燥效果没有明显差别,实验中没有发现在抽风干燥过程中下部生球有过湿现象和压坏现象发生;(2) 随着烘干时间的增加脱水率逐渐增加,烘干15 min后脱水率可达到90%以上,完全满足要求,延长时间对于烘干效果没有明显影响.4.3 焙烧实验(1) 实验结果对9组焙烧后金属化球团的化学成分和抗压强度分别进行检测,结果如表5所示.表5 金属化球团的化学分析结果及抗压强度Table 5 Chemical analysis and compressive strength of metallized pelletsNo. TFe(%)MFe(%)Metallization rate(%)V2O5(%)TiO2(%)Compressivestrength (N)1 60.40 32.53 53.86 0.48 9.74 2155.672 60.40 47.08 77.95 0.66 13.33 1036.403 65.25 56.11 85.99 0.65 12.06 2395.004 59.21 44.78 75.63 0.51 13.11 1747.205 62.57 55.60 88.86 0.56 9.58 1337.756 66.33 51.94 78.31 0.60 14.36 2273.007 59.71 35.51 59.47 0.47 11.40 635.008 59.94 40.33 67.28 0.41 12.93 650.509 62.90 48.08 76.44 0.63 12.30 1642.80通过以上结果可以看出:(a) 金属化球团的铁品位较精矿粉的铁品位有较大提高,这是因为煤粉中的碳与铁氧化物中的氧发生反应,去除了精矿粉中的部分氧,而残留的煤粉灰分质量远小于铁氧化物失去氧的质量[9].(b) 金属化球团中只有少量V, Ti被还原. 由Ellingham图可知,V2O5, TiO2只有在1500℃以上高温时才能被碳还原[10].(c) 由于C/O与焙烧条件不同各组的金属化率和抗压强度变化较大.(2) 直观分析[11]判断金属化球团质量的两个重要指标就是金属化率和抗压强度,实际生产中一般要求金属化率和抗压强度越高越好. 由表5可知,不同C/O,不同焙烧条件下增刊1 刘征建等:钒钛磁铁矿含碳球团转底炉直接还原实验研究 53各组的金属化率和抗压强度变化较大. 对正交实验结果采用直观分析法进行分析,以找出最佳的工艺条件,结果如表6所示.表6 直观分析法结果Table 6 The results of intuitive analysisTest index No.1 A2 B3 C Metallization rate (%) Compressive strength (N)1 1 1 1 53.86 635.002 1 2 2 77.95 1747.203 1 3 3 85.99 2155.674 2 1 2 75.63 650.505 2 2 3 88.86 1337.75 6 2 3 1 78.31 1036.407 3 1 3 59.47 1642.808 3 2 1 67.28 2273.009 3 3 2 76.44 2395.00K 1 217.80 188.96 199.45 K 2 242.80 234.09 230.02 K 3 203.19 240.74 234.32 κ1 72.60 62.99 66.48 κ2 80.93 78.03 76.67 κ3 67.73 80.25 78.11 Range 13.20 17.26 11.63 MetallizationrateOptimum scheme A2 B3 C3K 1 4537.87 2928.30 3944.40 K 2 3024.65 5357.95 4792.70 K 3 6310.80 5587.07 5136.22 κ1 1512.62 976.10 1314.80 κ2 1008.22 1785.98 1597.57 κ3 2103.60 1862.36 1712.07 Range 1095.38 886.26 397.27 Compressive strengthOptimum scheme A3 B3 C3从以上分析结果可看出,对于金属化率的3个极差由大到小依次为17.26,13.20,11.63,它们所对应的因素依次为B ,A ,C. 所以,各因素对金属化率的影响按大小次序来说应当是B(焙烧温度)、A(C/O)、C(焙烧时间);最好的方案应当是B3A2C3,即, B3:焙烧温度,第3水平,1330℃;A2:C/O ,第2水平,1.5;C3:焙烧时间,第3水平,25 min.同理可知,各因素对抗压强度的影响按大小次序来说应当是A(C/O),B(焙烧温度),C(焙烧时间);最好的方案应当是A3B3C3,即:A3:C/O ,第3水平,1.1;B3:焙烧温度,第3水平,1330℃;C3:焙烧时间,第3水平,25 min.通过综合平衡法对金属化率和抗压强度两个指标进行计算分析,分别得到2个最优方案:对金属化率为A2B3C3;对抗压强度为A3B3C3. 这2个方案并不完全相同,为便于综合分析,将两个指标随因素水平变化的情况用图形表示出来,如图1所示(为了便于分析,将各点用线段连起来,实际上并不是直线).666870727476788082M e t a l l i z a t i o n r a t e (×102%)C/ORoasting temperature(℃)Roasting time(min)1.11.31.58001000120014001600180020002200C o m p r e s s i v e s t r e n g t h (N )C/O125013001350Roasting temperature(℃)152025Roasting time(min)图1 两个指标随因素水平变化的情况Fig.1 Changes of two indexes with variable factors and levels54 过 程 工 程 学 报 第9卷将图1和表6结合起来,综合分析每一个因素对两个指标的影响.(a) C/O 对两个指标的影响. 从表6看出,对抗压强度来讲,C/O 的极差是最大的,也就是说C/O 是影响最大的因素,从图1看,取1.1最好;对金属化率来讲,C/O 的极差不是最大,即不是影响最大的因素,是较次要的因素,取 1.5最好. 从实际的焙烧过程来看,C/O 越高,煤粉配加量越大,煤粉反应后留下的空隙越多,金属化球团的孔隙度越大,抗压强度越低,这与表6的分析结果很吻合. 针对为实现铁、钛、钒资源综合利用而设计的“钒钛磁铁矿转底炉直接还原−电炉深还原−含钒铁水提钒−含钛炉渣提钛”工业流程,其转底炉生产的金属化球团直接热装电炉,所以对金属化球团的抗压强度要求不是很高,加之电炉深还原要求金属化球团有一定的残碳含量,所以C/O 取中间水平1.3为好[12,13].(b) 焙烧温度B 对两个指标的影响. 从表6看出,对金属化率来讲,焙烧温度的极差是最大的,即焙烧温度是影响最大的因素,从图1看出,取1330℃最好;对抗压强度来讲,焙烧温度的极差不是最大,即不是影响最大的因素,是较次要的因素,但也是取1330℃最好,所以对两个指标来讲,焙烧温度均取1330℃最好.(c) 焙烧时间C 对两个指标的影响. 从表6看出,对金属化率和抗压强度来讲,焙烧时间的极差都是最小的,即是影响最小的因素,从图1看出,都是取25 min 最好,所以对两个指标来讲,焙烧时间均取25 min 最好. 从实际的焙烧过程来看,焙烧时间越长,反应越完全,抗压强度越高. 但这并不意味着焙烧时间越长,金属化率就越高,因为随着焙烧时间的延长,球团内部碳逐渐被消耗完,金属化球团会发生再氧化,从而降低金属化率.综合考虑C/O 、焙烧温度、焙烧时间3个因素对金属化率和抗压强度的影响以及工艺流程的实际要求,得出较好的实验方案为:A1:C/O ,第2水平,1.3;B3:焙烧温度,第3水平,1330℃;C3:焙烧时间,第3水平,25 min.从表6可以看出,这里综合分析出来的较好方案A1B3C3,正好是9组实验中的3#实验,其球团的金属化率(85.99%)和抗压强度(2155.67 N)在9组实验结果中的综合效果最好,与通过计算分析得到的结论一致.(3) XRD 分析对9组实验制得的金属化球团进行XRD 分析,可以看出金属铁均已经明显出现,尤其在金属化率较高的3#实验(85.99%)和5#实验(88.86%)制得的金属化球团中可明显看到假板钛矿(Fe 2TiO 5)的出现,如图2和3所示. 1020304050607080900500100015002000I n t e n s i t y (a .u .)2θ (o)102030405060708090050010001500200025002θ (o)I n t e n s i t y (a .u .)图2 C/O=1.3, T =1330℃, t =25 min (3#实验) 图3 C/O=1.5, T =1300℃, t =25 min (5#实验)Fig.2 C/O=1.3, T =1330℃, t =25 min (Exp.3#) Fig.3 C/O=1.5, T =1300℃, t =25 min (Exp.5#)对于钛铁矿在600℃至成渣温度范围内的还原机理、还原途径及其相变化,前人已有相当充分的研究,对1100 K 以上的Fe −Ti −O 系的相平衡关系也已经基本明确,在与钛铁矿还原有关的相图区域内存在3个主要固溶体也得到公认:在Fe −Fe 2O 3−TiO 2组成的三角形中,在1200℃时介于磁铁矿(Fe 3O 4)和钛铁晶石(Fe 2TiO 4)之间、介于赤铁矿(Fe 2O 3)和钛铁矿(FeO·TiO 2)之间、高铁假板钛矿(Fe 2TiO 5)和亚铁假板钛矿(FeTi 2O 5)之间,存在着完全固溶体,它们被认为是立方晶系的尖晶石相、菱形晶系的α-氧化铁固溶体和M 3O 5固溶体. 在达到1300℃并充分反应后,开始还原出假板钛矿,这与XRD 的分析结果相吻合.假板钛矿的生成能够有效提高球团的还原性能,一方面是因为用碳还原假板钛矿的速度要比还原钛铁矿和假金红石的速度快得多;另一方面钛铁矿从坚固的尖晶石结构变为不稳定的假板钛矿结构,形成大量空隙,改善了后续还原过程的动力学条件.增刊1 刘征建等:钒钛磁铁矿含碳球团转底炉直接还原实验研究555 结 论(1) 钒钛磁铁矿精矿粉与煤粉混合造球时,通过控制合适的压球机压力和转速、添加适量的水分和粘结剂可以保证其强度满足转底炉生产的要求.(2) 鼓风干燥和抽风干燥两种形式的干燥效果没有明显差别,风速控制在1 m/s,烘干10~15 min,脱水率可达到90%以上,完全满足生产要求.(3) 综合考虑3个因素对金属化率和抗压强度的影响以及工艺流程的实际要求,得出最优的实验方案是:C/O为1.3,焙烧温度为1330℃,焙烧时间为25 min.(4) 从9组实验得到金属化球团的XRD分析结果可以看出,金属铁均已经明显出现,尤其在金属化率较高的3#实验(85.99%)和5#实验(88.86%)制得的金属化球团中可以明显看到假板钛矿的出现,提高了球团的还原性能.参考文献:[1] 洪流,丁跃华,谢洪恩. 钒钛磁铁矿转底炉直接还原综合利用前景 [J]. 金属矿山,2007, (5): 10−13.[2] 胡俊鸽,吴美庆,毛艳丽. 直接还原炼铁技术的最新发展 [J]. 钢铁研究,2006, 34(2): 53−57. [3] 朱荣,任江涛,刘纲,等. 转底炉工艺的发展与实践 [J]. 北京科技大学学报,2007, 29(增刊1): 171−174.[4] 王定武. 转底炉工艺生产直接还原铁的现况和前景 [J]. 冶金管理,2007, (12): 53−55.[5] 黄洁. 谈转底炉的发展 [J]. 中国冶金,2007, 17(4): 23−25.[6] 杨保祥. 直接还原炼铁工艺现状及攀枝花钒钛磁铁矿处理工艺选择 [J]. 攀枝花科技与信息,2006, 31(3): 4−8.[7] 黄典冰,孔令坛,林宗彩. 生球干燥过程及其数学模型 [J]. 金属学报,1992, (12): 52−57.[8] Nagata K, Kojima R, Murakami T, et al. Mechanisms of Pig-ironMaking from Magnetite Ore Pellets Containing Coal at Low Temperature [J]. ISIJ Int., 2001, 41(11): 1316−1323.[9] Kasai E, Kitajima T, Kawaguchi T. Carbothermic Reduction in theCombustion Bed Packed with Composite Pellets of Iron Oxide and Coal [J]. ISIJ Int., 2000, 40(9): 842−849.[10] 郭汉杰. 冶金物理化学教程(第2版) [M]. 北京:冶金工业出版社,2004. 16.[11] 陈魁. 试验设计与分析(第2版) [M]. 北京:冶金工业出版社,1977. 78−81.[12] 徐萌,张建良,孔令坛,等. 以转底炉技术利用钛资源的基础研究 [J]. 有色金属(冶炼部分), 2005, (3): 24−29.[13] Sohn I, Fruehan R J. The Reduction of Iron Oxides by V olatiles in aRotary Hearth Furnace Process: Part Ⅲ. The Simulation of V olatile Reduction in a Multi-layer Rotary Hearth Furnace Process [J]. Metall.Mater. Trans. B: Process Metall. Mater. Process., 2006, 37(2): 231−238.Research on Direct Reduction of Coal-containing Pellets ofVanadic-titanomagnetite by Rotary Hearth FurnaceLIU Zheng-jian, YANG Guang-qing, XUE Qing-guo, ZHANG Jian-liang, YANG Tian-jun(University of Science and Technology Beijing, Beijing 100083, China)Abstract: The direct reduction of vanadic-titanomagnetite by rotary hearth furnace was studied in laboratory. The vanadic-titanomagnetite was mixed with coal and bentonite, then the green balls were made by pelletizer, and dried by hot gas which was produced by burning the hot gas of liquefied petroleum gas and air. The influential factors of metallized pellet strength and metallization rate, such as C/O, roasting temperature, roasting time, were examined by orthogonal experiments. The C/O, roasting temperature and roasting time of the optimum scheme were 1.3, 1300℃ and 25 min respectively. Pseudobrookite was found in pellets with high metallization rate by XRD.Key words: comprehensive utilization of resources; vanadic-titanomagnetite; rotary hearth furnace; direct reduction。
第四章钒钛磁铁矿直接还原工艺

4.1 回转窑还原工艺4.1.1 回转窑还原工艺流程预热带和还原带两部分。
在预热带物料没有大量吸热的反应,水当量小,虽然热速度比较小,但物料温升却比较大。
由于铁矿石与还原剂密切接触,还原反应约在700℃开始。
物料进入还原带后,还原反应大量进行,反应产生的CO从料层表面逸出,形成保护层,料层内有良好还原气氛。
料层逸出气体与空气燃烧形成稳定的氧化或弱氧化气氛。
因此回转窑还原有两种不同的气体。
窑内还原反应分为二步:CO2 + C = 2CO (1)F n O m + mCO = nFe + mCO2(2)气化反应在高炉冶炼过程是不希望的,而回转窑过程则是不可少的,进行得越快,越有利于窑内还原反应。
在不致产生结圈的前提下,窑内维持较高的温度,不仅有利于燃烧反应快速进行,而且使其窑头喷入的粉煤,窑中加入煤的燃烧生成的CO浓度增加,气化反应得以顺利发展,有利于窑内钒钛磁铁矿的还原反应。
由于气化属增压反应,窑内压力增加对反应不利,所以,当回转窑为了防止大量吸入冷空气而采用正压操作时,其正压值应当尽量的小,做到两兼顾。
攀枝花钒钛磁铁矿由于共生有钒钛等元素,因而它的还原是一个复杂的过程。
尤其在回转窑内,还原剂有气态的CO,H2(H2主要来自煤挥发物和少量的水的反应产物)以及固态的C,而且CO的还原作用又受煤气化反应的制约,这就更增加了过程的复杂性。
通过热力学和动力学的分析,在回转窑的特定条件下,C的还原作用是较为次要的,所以有时为了对窑内铁氧化物的还原过程进行分析计算,将过程简化为还原剂主要是CO和H2,而略去C在其中的直接还原作用。
钒钛磁铁矿球团在回转窑中用煤粉还原的还原历程可以简写为:7)回转窑脱硫入窑硫少量由铁矿石带入,大量(60%~90%)是还原剂和燃烧煤带入的。
钒钛磁铁矿中硫主要呈FeS2,FeS和磁黄铁矿形态。
矿石入窑后,随着温度升高,FeS2开始分解(300~600℃),900℃分解激烈进行。
煤中硫的形态复杂,多为有机硫、硫化物(FeS2,FeS,磁黄铁矿)和硫酸盐(CaSO4,Fe2(S04)3)三种形态。
钒钛磁铁矿非高炉冶炼技术

钒钛磁铁矿非高炉冶炼技术
听说钒钛磁铁矿非高炉冶炼技术挺牛的,听说这技术能让钢铁
生产更环保,还能提高产品质量。
这对于咱们这种用惯了传统高炉
冶炼的人来说,简直是打开了新世界的大门。
你知道吗,直接还原炼铁这种工艺,就是不用高炉,用煤、气
体或者液态燃料把铁矿石里的氧化铁给还原了。
这方法好处多得很,能选择性地还原矿石里的元素,而且操作起来也简单,真是省时省力。
对了,还有熔融还原炼铁这种技术,也是非高炉冶炼的一种。
这方法用焦煤冶炼液态热铁水,过程分为两步,固态预还原和熔态
终还原。
听起来有点复杂,但效果是真的好,铁水质量高,能耗还低。
听说这非高炉冶炼技术还能带动其他产业发展呢,比如氢基直
接还原这种技术,虽然现在主要是外国人掌握的,但咱们也在努力
突破技术封锁,争取有自己的核心技术和装备。
这不仅仅是为了钢
铁工业的可持续发展,更是为了把钒、钛这些战略资源给好好利用
起来。
上次参加了个钒钛磁铁矿非高炉冶炼技术的研讨会,大家都在
热烈讨论怎么开发这项技术,怎么让它产业化。
大家都觉得,这技
术要是搞好了,钢铁生产不仅更有效率,还能更环保,对咱们国家
的钢铁工业来说,绝对是个大利好。
说到底,钒钛磁铁矿非高炉冶炼技术就是钢铁工业进步的一个
缩影。
它让咱们看到了钢铁生产的新可能,也让咱们对未来充满了
期待。
希望这技术能快点发展起来,让咱们的钢铁工业更上一层楼!。
2024年钒钛磁铁矿市场环境分析
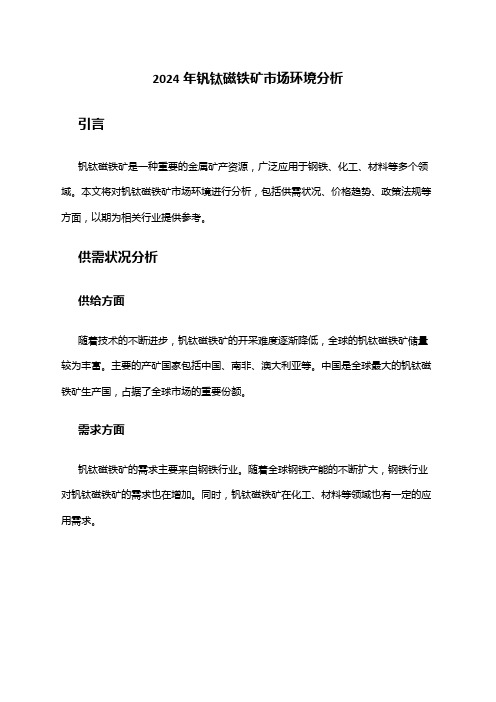
2024年钒钛磁铁矿市场环境分析引言钒钛磁铁矿是一种重要的金属矿产资源,广泛应用于钢铁、化工、材料等多个领域。
本文将对钒钛磁铁矿市场环境进行分析,包括供需状况、价格趋势、政策法规等方面,以期为相关行业提供参考。
供需状况分析供给方面随着技术的不断进步,钒钛磁铁矿的开采难度逐渐降低,全球的钒钛磁铁矿储量较为丰富。
主要的产矿国家包括中国、南非、澳大利亚等。
中国是全球最大的钒钛磁铁矿生产国,占据了全球市场的重要份额。
需求方面钒钛磁铁矿的需求主要来自钢铁行业。
随着全球钢铁产能的不断扩大,钢铁行业对钒钛磁铁矿的需求也在增加。
同时,钒钛磁铁矿在化工、材料等领域也有一定的应用需求。
价格趋势分析国际市场价格钒钛磁铁矿的价格受到供需状况、全球经济形势、政策法规等多个因素的影响。
近年来,钒钛磁铁矿的价格呈现较大波动。
全球经济放缓、需求减少等因素可能导致价格下跌,而供给不足、政策支持等因素可能导致价格上涨。
国内市场价格中国是全球最大的钒钛磁铁矿生产国和消费国,国内市场价格受到国际市场价格、国内供需状况、政策法规等因素的综合影响。
近年来,国内钒钛磁铁矿的价格同样呈现较大波动。
政策法规分析国际政策法规钒钛磁铁矿作为一种重要的金属矿产资源,受到国际政策法规的监管。
各国政府通过限制出口、实行关税、加强环境保护等手段来控制钒钛磁铁矿的开采和流通。
国内政策法规中国政府对钒钛磁铁矿的开采和利用也有一系列的政策法规进行监管。
近年来,中国政府加大了对环境保护的力度,对违规开采、污染等行为进行了打击。
同时,政府还通过优惠税收、加强技术研发支持等手段来促进钒钛磁铁矿产业的健康发展。
结论钒钛磁铁矿市场环境受到多个因素的共同影响,供需状况、价格趋势、政策法规等都对市场产生着重要影响。
同时,全球经济形势、技术进步等因素也会对钒钛磁铁矿市场环境产生重要影响。
因此,相关行业应密切关注市场动态,制定合理的发展战略,以应对市场的变化。
-=-周渝生 中国直接还原铁技术发展及市场供需分析 (终稿)
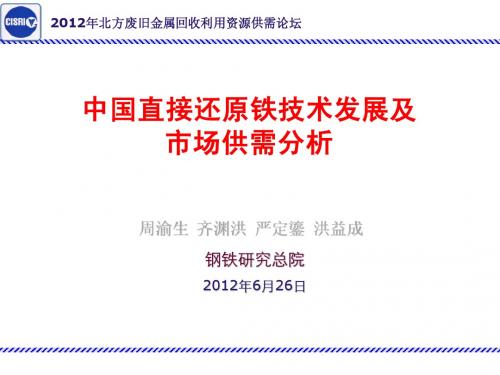
粘结,炉内不必设置机械破碎装置。
5.加压煤制气工艺是我国发展直接还原新工艺的基础和条件 煤气化是煤基DRI、发电、供热多联产工艺过程的共性和关 键技术。在过去20年间,煤气化技术取得极大发展,几乎世界 上所有类型的煤气化技术的生产装置都能在中国找到。很难说 现在有哪一种煤气化技术可以占有绝对优势,每种煤气化技术
2012年北方废旧金属回收利用资源供需论坛
中国直接还原铁技术发展及 市场供需分析
周渝生 齐渊洪 严定鎏 洪益成 钢铁研究总院
2012年6月26日
内 容 提 要
1.中国近几年铁产量及直接还原铁的产量和比例 2.废钢比提高将推动我国直接还原的发展 中国目前DRI发展及 市场需求 3.低品质难选含铁原料用转底炉炼粒铁是煤基DRI的创新方向 4.气基竖炉直接还原工艺技术是我国直接还原的主要发展方向 5.加压煤制气工艺是我国发展直接还原新工艺的基础和条件
平均容积仅600m3左右,导致我国钢铁行业的劳动生
产率较低、总能耗和CO2排放量很高。2011年全球粗
钢产量15.27亿吨,其中中国粗钢产量6.83亿吨,占全
球粗钢产量44.73%。
1.中国近几年铁产量及直接还原铁的产量和比例
2011年世界生铁产量为10.8亿t,中国的生铁产量 6.297亿t,占世界的比重58.31%,铁钢比高达0.922。 2011年世界直接还原铁(DRI/HBI)总产量约为6347 万吨,约为世界生铁产量9.52亿吨的6.67%。 2011年中国直接还原铁(DRI/HBI)年产量约为60万 吨,约占生铁年产量6.297亿吨的0.095%,中国的DRI 产量不到高炉生铁产量的千分之一。
2023年钒钛磁铁矿行业市场分析现状

2023年钒钛磁铁矿行业市场分析现状钒钛磁铁矿是一种重要的金属矿石,广泛应用于冶金、化工、建材等领域。
钒钛磁铁矿的开采和利用对于推动相关产业的发展具有重要意义。
本文将从市场规模、供需情况、行业竞争和发展前景等方面对钒钛磁铁矿行业进行市场分析。
一、市场规模钒钛磁铁矿是一种具有丰富资源的矿石,其产量和储量居全球前列。
目前全球每年开采的钒钛磁铁矿约为1亿吨,其中中国占全球产量的70%以上。
预计未来几年,由于对高品质钒钛磁铁矿的需求增加,全球钒钛磁铁矿市场规模将保持稳定增长。
二、供需情况1.供应方面:目前,全球钒钛磁铁矿的供应主要依赖于中国、澳大利亚和南非等国家。
中国是全球最大的钒钛磁铁矿生产国,占据全球市场份额的70%以上。
同时,中国也是全球最大的钒钛磁铁矿消费国,国内市场需求旺盛。
2.需求方面:钒钛磁铁矿广泛应用于钢铁、化工、冶金等重要行业。
随着全球经济的发展和工业化进程的加快,对钒钛磁铁矿的需求将持续增长。
特别是近年来,随着新能源汽车、特高压输电、航天航空等高技术产业的快速发展,对钒钛磁铁矿的需求更加迫切。
三、行业竞争目前全球钒钛磁铁矿行业呈现的竞争格局是中国企业的主导。
中国拥有丰富的钒钛磁铁矿资源和成熟的加工技术,占据了全球市场的绝对优势。
同时,中国的钒钛磁铁矿行业也面临着来自澳大利亚、南非等国际竞争对手的挑战。
这些国家拥有更高品质、更先进的钒钛磁铁矿资源,具备一定的竞争力。
四、发展前景1.产业升级:随着全球对环境保护的要求越来越高,钒钛磁铁矿行业将面临产业升级的挑战。
未来,钒钛磁铁矿行业需要加强技术创新,提高资源利用率和环境保护水平,推动产业的可持续发展。
2.市场拓展:随着全球经济一体化的深入发展,国际市场对钒钛磁铁矿的需求将不断增加。
中国企业需要积极开拓海外市场,加强国际合作,提高在国际市场的竞争力。
3.产业调整:钒钛磁铁矿行业需要加强产业调整,提高产业链的价值增长能力。
通过加强与上下游行业的合作,促进钒钛磁铁矿的深度加工和利用,提高产品附加值和市场竞争力。
2024年钒钛磁铁矿市场前景分析

钒钛磁铁矿市场前景分析引言钒钛磁铁矿作为一种重要的钢铁原料,对于全球钢铁行业具有重要意义。
随着全球经济的快速发展,钢铁需求的增长对钒钛磁铁矿市场的需求也带来了新的机遇。
本文将对钒钛磁铁矿市场的前景进行分析,包括市场规模、需求驱动力和挑战等方面。
市场规模钒钛磁铁矿市场在过去几年呈现稳步增长的趋势,并且预计在未来几年内仍将保持良好的增长势头。
根据市场研究数据显示,2019年全球钒钛磁铁矿市场规模约为XX亿美元,预计到2025年将增长到XX亿美元。
这主要受益于亚太地区的快速发展以及建筑和基础设施投资的增加。
需求驱动力1. 钢铁需求增长随着全球经济的发展,钢铁需求持续增长,推动了钒钛磁铁矿市场的发展。
钒钛磁铁矿作为一种重要的钢铁原料,其市场需求与钢铁产量密切相关。
尤其是在新兴市场经济体的快速工业化进程中,钢铁产量不断增加,对钒钛磁铁矿的需求也随之增长。
2. 新能源发展新能源行业的发展对钒钛磁铁矿的需求也起到了促进作用。
钒钛磁铁矿在储能电池和风力发电等领域具有广泛的应用前景。
随着可再生能源的重要性日益凸显,新能源行业的发展将进一步推动钒钛磁铁矿市场的增长。
挑战与机遇1. 市场供应紧张目前,全球钒钛磁铁矿市场供应仍然相对紧张。
主要供应国家如中国、南非和澳大利亚等都面临了一系列的挑战,如资源限制、环境限制和运输成本增加等。
供应紧张可能导致钒钛磁铁矿价格的上涨,从而影响市场的发展。
2. 环境保护压力增加由于钒钛磁铁矿的开采和加工可能对环境造成一定的影响,环境保护压力也在不断增加。
各国政府出台了一系列环境保护政策和法规,加大对钒钛磁铁矿行业的监管力度。
这对钒钛磁铁矿企业来说既是挑战,也是机遇。
钒钛磁铁矿企业需要加强环保意识,推动绿色发展,以应对市场的挑战。
结论钒钛磁铁矿市场具有广阔的发展前景。
全球钢铁需求的增长和新能源行业的发展将推动钒钛磁铁矿市场的增长。
然而,市场供应紧张和环境保护压力也是钒钛磁铁矿行业所面临的挑战。
- 1、下载文档前请自行甄别文档内容的完整性,平台不提供额外的编辑、内容补充、找答案等附加服务。
- 2、"仅部分预览"的文档,不可在线预览部分如存在完整性等问题,可反馈申请退款(可完整预览的文档不适用该条件!)。
- 3、如文档侵犯您的权益,请联系客服反馈,我们会尽快为您处理(人工客服工作时间:9:00-18:30)。
我国钒钛磁铁矿直接还原分析
摘要
本文概括地介绍了我国钒钛磁铁矿资源分布情况。
钒钛磁铁矿是重要的资源,世界各国的研究及生产实践表明,使用高炉冶炼法钒钛磁铁矿是难以冶炼的铁矿石。
因此钒钛磁铁矿冶炼大量使用非高炉冶炼法,即采用直接还原法。
本文详细地阐述了直接还原法中隧道窑、回转窑、转底炉、竖炉这四种常见炉的结构、反应原理、国内工艺现状及反应特点,并指出了我国钒钛磁铁矿直接还原工艺的发展方向。
关键词钒钛磁铁矿直接还原隧道窑回转窑转底炉竖炉
前言
目前国外钒钛磁铁矿主要分布在南非、前苏联、新西兰、加拿大、印度等地。
我国钒钛磁铁矿矿床分布广泛,储量吩咐,储量和开采量居全国铁矿的第3位。
已探明储量98.3亿吨,远景储量达300亿吨以上,主要分布在四川攀枝花地区、河北承德地区、陕西洋县、甘肃什斯镇、广东兴宁几山西代县等地区。
钒钛磁铁矿冶炼的利用问题,远在上19世纪上半叶,瑞典、挪威、美国、英国都进行过试验,均未取得结果。
20世纪30年代开始日本、前苏联开始在不同容积的高炉上研究冶炼钒钛磁铁矿的工艺,结论是:炉渣中TiO2 限制在16%以下,实际生产中采用配10%—15%的普通矿冶炼含钒生铁,渣中TiO2为9%—10%,TiO2含量越高冶炼难度越大。
世界各国的研究及生产实践表明,钒钛磁铁矿是难以冶炼的铁矿石。
通过多年的努力,钒钛磁铁矿已解决高炉冶炼等多项技术难题,逐渐形成了以高炉-转炉流程为主的综合回收其中铁、钒和钛的技术路线,实现了铁、钒和钛元素的大规模化利用,形成了铁钒钛系列产品的大规模工业生产能力。
然而高炉-转炉流程最大的缺点是:为了利用钒钛磁铁矿中的铁和钒浪费了大量的高钛型炉渣,造成钛资源的严重浪费,又造成很大的污染,从而形成了巨大的环境压力,所以开发适宜钒钛磁铁矿综合回收利用的工艺流程势在必行。
本文对钒钛磁铁矿煤基直接还原工艺的炉体结构、原理、特点、现状、投资价格进行简单探讨,指出煤制气-竖炉直接还原工艺为还原钒钛磁铁矿的发展提供新的途径。
直接还原指在低于矿石熔化温度下,通过固态还原把铁矿石炼制成铁的工艺过程。
直接还原铁的特点是碳、硅含量低,成分类似钢,实际上也代替废钢用于炼钢。
作为传统工艺的补充,钒钛磁铁矿直接还原工艺以其环保、原料广泛的特点受到了市场的青睐。
按还原剂的不同,直接还原工艺分为煤基直接还原和气基直接还原。
气基直接还原方式生产直接还原铁在国外一直占有较大的市场份额。
我国煤基直接还原钒钛磁铁矿已经得到了广泛的应用。
隧道窑、回转窑、转底炉和竖炉的结构与还原原理
隧道窑结构与还原原理
结构:隧道窑的横截面为上部呈圆拱形,下部呈长方形,其长度从30—200m 不等,是从砖窑移植过来的。
隧道窑底部铺设有铁轨,窑车在铁轨上进行,物料放在还原罐内,还原罐整齐地放在窑车上,窑车在隧道窑内缓慢进行。
原理:隧道窑生产直接还原铁工艺是将铁原料、还原剂、脱硫剂按工艺要求加工好,按照一定的比例和装料方法,分别装入还原罐中,放在台车上推入隧道窑中,通入煤气点燃,料罐中的原料经预热,在1000—1200°C的温度条件下还原,在保持足够的还原时间和冷却时间后,得到直接还原铁。
回转窑结构与还原原理
结构:回转窑是一个倾斜放置的旋转圆筒体,其内壁上砌有耐火材料。
规格为筒体内径有效长度表示。
原理:窑体旋转很慢,由钒钛磁铁矿、细粒煤及脱煤及脱硫剂组成的物料在摩擦力作用下被窑体带起,超过物料运动角后,在重力作用下,自堆尖滚落到底部。
因窑体倾斜,物料也前移一段距离。
同一回转窑内,物料在窑内的停留时间与填充率成正比。
转底炉结构与还原原理
结构:转底炉(RHF)工艺的主体设备转底炉是由轧钢使用的环形加热炉演变而来,是一个平坦的、内有耐火材料衬的可以转动的环形高温窑炉。
其烧嘴位于炉膛上部,所用燃料可以是天然气、燃油、煤粉等。
原理:转底炉直接还原技术是铁矿粉(或红土镍矿、钒钛磁铁矿、硫酸渣或冶金粉尘、除尘灰、炼钢污泥等)经配料、混料、制球和干燥后的含碳球团加入到具有环形炉膛和可转动的炉底的转底炉中,在1350 ℃左右炉膛温度下,在随着炉底旋转一周的过程中,铁矿被碳还原。
竖炉结构与还原原理
结构:竖炉主要由烟罩、炉体钢结构、炉体砌砖、导风墙和干燥床、卸料器、供风和煤气管路等结构组成,分为上料系统、还原段、冷却段、排料系统、尾气净化系统等。
原理:竖炉还原流程由竖炉还原带、炉顶煤气换热器、炉顶煤气激冷/洗涤系统、工艺气循环压缩机、压缩机二次冷却器、CO2吸收器、工艺气加湿器和工艺气加热器等组成。
炉料在竖炉里下降,并逐步完成还原过程。
国内隧道窑、回转窑、转底炉和竖炉在煤基直接还原工艺中的现状
国内隧道窑工艺现状
隧道窑在还原工艺上是最成熟的,2002年中南工业大学、中南矿业研究院与攀钢合作完成了隧道窑罐混合还原剂还原的实验,取得了较好的效果。
现如今我国已建成和正在建设的隧道窑有100多座,随着直接还原铁需求量大增,隧道窑直接还原铁技术也得到不断完善。
钒钛磁铁矿攀枝花攀阳钒钛工贸有限公司通过四年产业化中试,于2009年建成了一条年产能2万t的遂道窑煤基直接还原
处理钒钛磁铁矿工业生产线,实现了产业化生产。
该工艺流程采用钒钛铁精矿粉与还原剂混合压块、装罐,罐放在窑车上直接进入隧道窑进行还原,制备成金属化物料,金属化物料再进行电炉熔分,实现钒、钛分离,产品为生铁和钛渣。
国内回转窑工艺现状
我国先后进行过回转窑试验的有攀钢西昌410厂、福州回转窑等,20世纪90年代,我国建设了一批用于直接还原普通铁精矿的回转窑,由于回转窑对原料的要求苛刻,能耗高,投资高,运行费用高,生产运行的稳定难度大,生产难扩大等原因在中国得不到很好的发展。
国内转底炉工艺现状
我国对转底炉工艺的研究有一定的历史,其中转底炉煤基热风熔融炼铁工艺,又称恰普法,是由北京科技大学冶金与生态工程学院冶金喷枪研究中心在转底炉直接还原基础上开发的新炼铁工艺。
攀枝花学院与四川龙蟒矿冶公司的科研人员从2004年起就开始进行该工艺研究,经过4年多大量艰苦努力,获得了重大技术突破,获得了高水平研究成果,为产业化提供打下了坚实基础。
目前,四川龙蟒集团攀枝花矿冶公司在攀枝花进行产业化建设,取得较好的经济效益。
但由于转底炉直接还原工艺中必须“内配煤”,因而对含钛炉渣造成了严重的污染,降低了TiO2的品位。
国内竖炉工艺现状
近年来,中国众多工作者对煤制气-竖炉直接还原铁生产进行了大量调查、研究工作,为中国采用煤制气-坚炉直接还原技术奠定了良好的基础。
但煤制气方法的选择、煤选择、煤制气-坚炉工艺的多联产的组合的选择及相关装备等问题还有进一步深入研究和探讨。
辽宁海城四型钢公司以煤制气为还原气,氧化球团为原料的竖炉项目,是竖炉是引进墨西哥希尔萨的HyL-ZR装置,设计生产能力为50万t/a;煤制气采用恩德法(流化床)单炉生产能力为40000m3/h。
隧道窑、回转窑、转底炉和竖炉在煤基直接还原工艺中的特点
隧道窑工艺特点:目前隧道窑直接还原铁工艺已经很成熟,对原料要求宽松具有灵活性,紧靠装灌方式不同,对原料的含水量有不同的要求,但是存在着流程过长,效率低,能耗高,生产周期长,污染严重,产品质量不稳定等,不适合用于处理大规模的钒钛磁铁矿。
生产实践表明,隧道窑生产直接还原铁还原时间超过50h。
回转窑工艺特点:回转窖对原料的冶金性能要求苛刻,要求球团必须具有足够的机械强度,较低的低温粉化率,还原过程中及还原过后必须有足够的耐磨强度和抗压强度。
回转窑内容易结圈,生产流程长,产品成本高,质量差。
转底炉工艺特点:工艺流程短,对原料要求宽松,对球团/压块的强度要求低原料适应性强,炉料不容易粘接、结圈,还原温度高、还原时间短(入炉到出炉20~30分钟),还原的金属化率高,生产效率高,可以很容易地开炉、停炉和
调整产量。
竖炉工艺特点:要求较高的还原气温度。
此外竖炉对球团的机械强度要求较高,较低的低温粉化率和还原膨胀率,还原过后球团必须有足够的强度,产品质量高、自动化程度高,能耗在现行还原方法中最低,可以大型化生产且符合国家节能减排的要求。
投资比较
按年产50万吨还原产品工艺投资估算的话:隧道窑、回转窑转底炉、天然气-竖炉、煤制气-竖炉分别投资人民币(亿元)2.5~3.0、7.0~8.0、7.5~10.0、5.0~6.0、7.0~7.5、9.0~10.0。
我们可见各种不同炉型在煤基直接还原钒钛磁铁矿的设备投资金额各不相同。
结论
隧道窑工艺能耗高,污染严重不符合国家“节能减排”的发展要求,不适宜在还原钒钛磁铁矿中发展此工艺;回转窑对原料要求苛刻,工艺成本高,流程长,产品质量差。
转底炉工艺流程短,对原料要求宽松,对球团/压块的强度要求低原料适应性强。
但是回转窑与转底炉这两种工艺只适用于中小型生产线进行生产。
气基竖炉可用于大规模处理钒钛磁铁矿,煤制气-竖炉直接还原工艺为还原钒钛磁铁矿的发展提供了新的途径,我国有丰富的煤炭资源,国内有成熟的煤制气技术和长期运行的经验。
虽然现在高炉冶炼还是主要的冶炼钒钛磁铁矿的方法,但是直接还原冶炼钒钛磁铁矿在不久的将来便可以成为冶炼钒钛磁铁矿的主要方法。
气基-竖炉直接还原钒钛磁铁矿工艺未来应用前景十分广阔,将逐步改变我国的煤基直接还原钒钛磁铁矿生产的格局,出现了一片大好的发展热潮。