射线的无损检测技术
射线无损检测重点工作总结
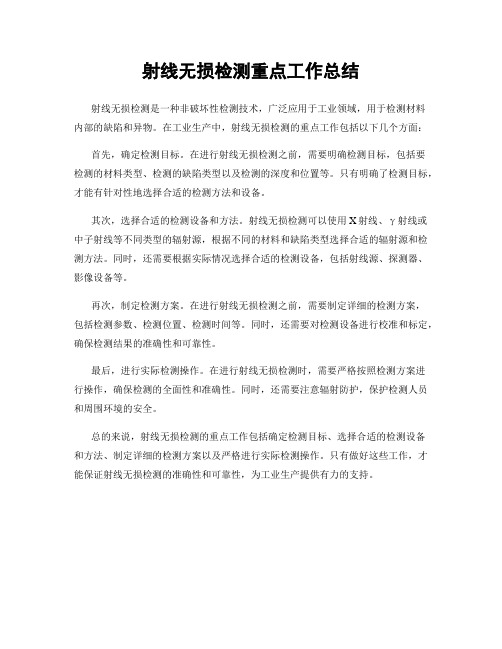
射线无损检测重点工作总结
射线无损检测是一种非破坏性检测技术,广泛应用于工业领域,用于检测材料
内部的缺陷和异物。
在工业生产中,射线无损检测的重点工作包括以下几个方面:首先,确定检测目标。
在进行射线无损检测之前,需要明确检测目标,包括要
检测的材料类型、检测的缺陷类型以及检测的深度和位置等。
只有明确了检测目标,才能有针对性地选择合适的检测方法和设备。
其次,选择合适的检测设备和方法。
射线无损检测可以使用X射线、γ射线或中子射线等不同类型的辐射源,根据不同的材料和缺陷类型选择合适的辐射源和检测方法。
同时,还需要根据实际情况选择合适的检测设备,包括射线源、探测器、影像设备等。
再次,制定检测方案。
在进行射线无损检测之前,需要制定详细的检测方案,
包括检测参数、检测位置、检测时间等。
同时,还需要对检测设备进行校准和标定,确保检测结果的准确性和可靠性。
最后,进行实际检测操作。
在进行射线无损检测时,需要严格按照检测方案进
行操作,确保检测的全面性和准确性。
同时,还需要注意辐射防护,保护检测人员和周围环境的安全。
总的来说,射线无损检测的重点工作包括确定检测目标、选择合适的检测设备
和方法、制定详细的检测方案以及严格进行实际检测操作。
只有做好这些工作,才能保证射线无损检测的准确性和可靠性,为工业生产提供有力的支持。
无损检测(射线,超声)
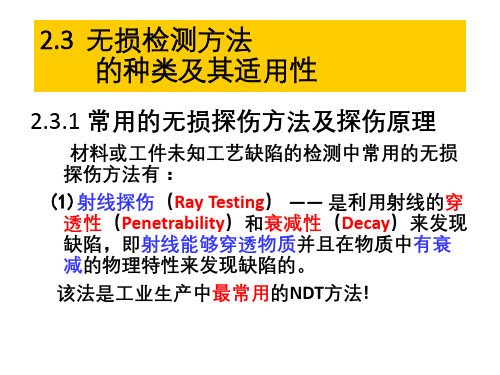
3.1.3 射线的产生
射线的性质,有利、有弊,应该科学地加以利 用和防范!射线学就是研究如何利用与防范射线 的科学。下面介绍产生x射线的主要设备: (1)x光管基本组成: • 阴极部件:灯丝(钨丝)——发射电子; 阴极罩——聚焦电子。 • 阳极部件:阳极靶——接收电子; 冷却介质——散热作用。 • 真空管——玻璃或金属陶瓷制作的真空外罩。
2.3.1 常用的无损探伤方法及探伤原理
(2)超声波探伤(Ultrasonic testing)—— 是利用超声波在 物质中传播(Propagation)、反射(Reflection)和 (Decay)等物理性质来发现缺陷的。 该法与射线探伤法形成优势互补. (3)磁力探伤(Magnetic testing)—— 是通过对铁磁材料 进行磁化所产生的漏磁场(Leakage magnetic field) 来发现其表面及近表面缺陷的。 在黑色金属( ferrous metal )的表面检测中应用广泛.
3.1.2 射线的性质 (1)不可见,直线传播—具有隐蔽性和指向性; (2)不带电,因而不受电磁场影响—电中性; (3)能穿透物质,但有衰减—具有穿透性和衰减性; 对同1种射线而言,功率越大,穿透性越强,衰减越慢; (4)能与某些物质产生光化作用,使荧光物质发光;可 使胶片感光—可成像; (5)能使某些气体电离—即产生电离辐射; (6)与光波一样,有反射、折射、干涉现象; (7)能产生生物效应,伤害和杀死生物细胞 —对人体有害。(此点非常重要)
2.3 无损检测方法 的种类及其适用性
2.3.1 常用的无损探伤方法及探伤原理
材料或工件未知工艺缺陷的检测中常用的无损 探伤方法有: (1)射线探伤(Ray Testing) —— 是利用射线的穿 透性(Penetrability)和衰减性(Decay)来发现 缺陷,即射线能够穿透物质并且在物质中有衰 减的物理特性来发现缺陷的。 该法是工业生产中最常用的NDT方法!
无损检测领域中射线技术的应用与发展

无损检测领域中射线技术的应用与发展射线检测是无损检测的重要分支,在各领域都有重要的应用。
它的全面质量管理包括很多方面的内容,本文向您简单介绍一下射线技术的应用与发展。
1.射线检测技术的应用射线检测技术是利用射线(X射线、射线、中子射线等)穿过材料或工件时的强度衰减,检测其内部结构不连续性的技术。
穿过材料或工件的射线由于强度不同在X射线胶片上的感光程度也不同,由此生成内部不连续的图像,从而实现对材料的无损检测。
(1)早期使用在石油工业.分析钻井岩芯。
(2)在航空工业用于检验与评价复合材料和复合结构。
评价某些复合件的制造过程。
也用于一系列情况下样件的评价;这种检测与评价过程,大大简化了取样破坏分析过程。
(3)检测大型固体火箭发动机,这样的射线系统使用电子直线加速器X射线源,能量高迭25MeV,可检验直径达3m的大型同体火箭发动机。
(4)检验小型、复杂、精密的铸件和锻件,进行缺陷检验和尺寸测量。
(5)检查工程陶瓷和粉末冶金产品制造过程发生的材料或成分变化,特别是对高强度、形状复杂的产品。
(6)组件结构检查。
2.射线检测技术的发展(1)数字射线照相技术时代。
1990年,R.Halmshaw和N.A.Ridyard在《英国无损检测杂志》上发表题为“数字射线照相方法评述”的文章,在评述了各种数字射线照相方法的发展之后认为,数字射线照相时代已经到来。
近年来射线检测技术发展的基本特点是数字图象处理技术广泛应用于射线检测。
射线层析检测和实时成像检测技术的重要基础之一是数字图象处理技术,即使常规胶片射线照相技术,也在采用数字图象处理技术。
(2)今后重点应用的技术。
1994年HaroldBerger在美国《材料评价》发表的“射线无损检测的趋势”中提出,在20世纪的最后10年和21世纪的初期,下列技术将得到广泛应用:①数字X射线实时检测系统在制造、在役检验和过程控制方面。
②具有数据交换、使用NDT工作站的计算机化的射线检测系统。
5大无损检测技术之射线检测,射线检测原理、设备介绍

5⼤⽆损检测技术之射线检测,射线检测原理、设备介绍是5⼤⽆损检测技术中的⼀种,通常聊到射线检测,⼤家⾃然会联想到医院的射线检测设备。
其实,它们便是应⽤了技术的产品。
为增进⼤家对射线检测的认识,本⽂将对射线检测、射线检测原理以及射线检测设备予以介绍。
如果你对检测、射线检测技术具有兴趣,不妨继续往下阅读哦。
⼀、射线检测射线检验通常简称为:RT,是⽆损检测⽅法的⼀种。
当强度均匀的射线束透照射物体时,如果物体局部区域存在缺陷或结构存在差异,它将改变物体对射线的衰减,使得不同部位透射射线强度不同。
这样,采⽤⼀定的检测器(例如,射线照相中采⽤胶⽚)检测透射射线强度,就可以判断物体内部的缺陷和物质分布等,从⽽完成对被检测对象的检验。
射线检验常⽤的⽅法有X射线检验、γ射线检验、⾼能射线检验和中⼦射线检验。
对于常⽤的⼯业射线检验来说,⼀般使⽤的是X射线检验和γ射线检验。
⼆、射线检验原理X和γ射线的波长短,能够穿过⼀定厚度的物质,并且在穿透的过程中与物质中的原⼦发⽣相互作⽤。
这种相互作⽤引起辐射强度的衰减,衰减的程度⼜同受检材料的厚度、密度和化学成分有关。
因此,当材料内部存在某种缺陷⽽使其局部的有效厚度、密度和化学成分改变时,就会在缺陷处和周围区域之间引起射线强度衰减的差异。
如果⽤适当介质将这种差异记录或显⽰出来,就可据以评价受检材料的内部质量。
X射线检验和γ射线检验,基本原理和检验⽅法⽆原则区别,不同的只是源的获得⽅式。
X射线源是由各种、电⼦感应加速器和直线加速器构成的从低能(⼏千电⼦伏)到⾼能(⼏⼗兆电⼦伏)的系列,可以检查厚⾄ 600mm的钢材。
γ射线是放射性同位素在衰变过程中辐射出来的。
三、射线检测设备(⼀)X射线机⼯业射线照相探伤中使⽤的低能X射线机,简单地说是由四部分组成:射线发⽣器(X射线管)、⾼压发⽣器、冷却系统、控制系统。
当各部分独⽴时,⾼压发⽣器与射线发⽣器之间应采⽤⾼压电缆连接。
按照的结构,X射线机通常分为三类,便携式X射线机、移动式X射线机、固定式X射线机。
X射线无损检测的应用及发展趋势

X射线无损检测的应用及发展趋势摘要:X射线无损技术在各个领域的产品缺陷检测中得到了广泛应用,对于我国各类产品及材料的质量检测具有非常重要的效用。
在以后的产品材料检测中,应尽量与计算机技术相融合,由此使X射线无损检测技术实现自动化,进而提高X射线无损检测技术应用水平,为我国的材料检测提供更优质的技术支撑,并同时对材料质量进行高效管控。
关键词:X射线;无损检测;应用1X射线无损检测原理当辐射入射在物体表面上的时候,物质原子和入射光子便会产生相互作用,这时射线强度会因吸收、散射等原因而不断被弱化。
强度降低程度完全与材料衰减系统和穿透厚度有较大的关系。
如被穿透物其存在局部缺陷,而其与构成缺陷类的材料相比衰减系统是存在差别的,局部区域与相邻区域间所形成的透过射线强度会各有不同,存在较大的差异性,通过这些差异性可以判定所检测的物体是不是存在缺陷。
射线穿透过被检测对象以后,由此生成一幅射线强度分布潜像。
在被检测对象背面安放一个检测仪,可获得此潜像的投影,通过相应的技术处理以后,便能够将潜像转变成人肉眼能够看到的一幅二维平面图。
2X射线无损检测方法分类2.1 X射线照相法X射线在穿透被照对象时,存在缺陷的位置其吸收射线的能力和基体都是有所不同的,例如:空隙中有空气那么其射线吸收能力会比基体吸收能力低很多,因此,无缺陷位置处的X射线强度比有缺陷位置处的射线强度低。
对于存在缺陷的位置需要使用更多X射线粒子,由此造成在X射线胶片上产生黑度面积非常大的一幅缺陷图。
缺陷检测最终结果与被检材料的性质、缺陷的厚度有较大的关系。
2.2 实时成像检测借助真空管中的X射线敏感荧光屏将无法看到的X射线图转化成可见的光子图像,之后借助光电阴极把可见光子转变成与之相适的电子,再利用数千eV电压来对电子进行加速,同时将其聚焦在荧光显示屏上,最终形成经过好几十倍增强后的可见光图像。
然而通过图像增强器所输出的可以人肉眼看到的光图像是无法直接用来观察的,必须用摄像机将经由图像增强所形成的光信号转变成电信号,之后利用电缆将图像传送至计算机系统当中,同时对图像做相应的处理以后再上传到显示器屏幕上,以让检测人员可以对图像进行观察和分析[2]。
无损检测方法射线检测

Χ射线检测是利用Χ射线通过物质衰减程度与被通过部位 的材质、厚度和缺陷的性质有关的特性,使胶片感光成黑度不 同的图像来实现的。当一束强度为I0的Χ射线平行通过被检测 试件(厚度为d)后,其强度Id由式(6-31)表示。 若被测试件表 面有高度为h的凸起时,则Χ射线强度将衰减为
Ih I0e(dh)
15
第6章 常用无损检测方法
图6-39 荧光增感屏构造示意图
16
第6章 常用无损检测方法
2)
金属增感屏在受射线照射时产生β射线和二次标
识X射线对胶片起感光作用。如果射线能量不能使金 属屏的原子电离或激发, 则不起增感作用,相反还 会吸收一部分软射线。如铅增感屏, 当管电压低于 80 kV时,则基本上无增感作用。 在生产实践中,多 采用铅、锡等原子序数较高的材料作金属增感屏,因 为铅的压延性好,吸收散射线的能力强。
7
第6章 常用无损检测方法
图6-35 X射线检测原理
8
第6章 常用无损检测方法 2. Χ
Χ射线检测常用的方法是照相法,即利用射线感光材料 (通常用射线胶片),放在被透照试件的背面接受透过试件后的 Χ射线, 如图6-36所示。胶片曝光后经暗室处理,就会显示 出物体的结构图像。根据胶片上影像的形状及其黑度的不均匀 程度,就可以评定被检测试件中有无缺陷及缺陷的性质、形状、 大小和位置。此法的优点是灵敏度高、直观可靠、重复性好, 是Χ射线检测法中应用最广泛的一种常规方法。由于生产和科 研的需要,还可用放大照相法和闪光照相法以弥补其不足。 放大照相可以检测出材料中的微小缺陷。
(6-36)
6
第6章 常用无损检测方法
又如在被测试件内,有一个厚度为x、吸收系数为μ′的某 种缺陷, 则射线通过后,强度衰减为
X射线的无损检测技术

X射线的无损检测技术一前言无损检测方法是利用声、光、电、热、磁及射线等与被测物质的相互作用,在不破坏和损伤被测物质的结构和性能的前提下,检测材料、构件或设备中存在的内外部缺陷,并能确定缺陷的大小、形状和位置。
无损检测的技术有很多,包括:染料渗透检测法、超声波检测法、强型光学检测法、渗透检测法、声发射检测法,以及本文介绍的x 射线检测法。
X射线无损探伤是工业无损检测的主要方法之一,是保证焊接质量的重要技术,其检测结果己作为焊缝缺陷分析和质量评定的重要判定依据,应用十分广泛。
胶片照相法是早期X射线无损探伤中常用的方法。
X射线胶片的成像质量较高,能够准确地提供焊缝中缺陷真实信息,但是,该方法具有操作过程复杂、运行成本高、结果不易存放且查询携带不方便等缺点。
由于电子技术的飞速发展,一种新型的X射线无损检测方法“X射线工业电视”已应运而生,并开始应用到焊缝质量的无损检测当中。
X射线工业电视己经发展到由工业CCD摄像机取代原始X射线无损探伤中的胶片,并用监视器(工业电视)实时显示探伤图像,这样不仅可以节省大量的X射线胶片,而且还可以在线实时检测,提高了X射线无损检测的检测效率。
但现在的X射线工业电视大多还都采用人工方式进行在线检测与分析,而人工检测本身存在几个不可避免的缺点,如主观标准不一致、劳动强度大、检测效率低等等。
x射线无损探伤计算机辅助评判系统的原理可以用两个“转换”来概述:首先X射线穿透金属材料及焊缝区域后被图像增强器所接收,图像增强器把不可见的X射线检测信息转换为可视图像,并被CCD摄像机所摄取,这个过程称为“光电转换”;就信息量的性质而言,可视图像是模拟量,它不能被计算机所识别,如果要输入计算机进行处理,则需要将模拟量转换为数字量,进行“模/数转换”,即经过计算机处理后将可视图像转换为数字图像。
其方法是用高清晰度工业CCD摄像机摄取可视图像,输入到视频采集卡当中,并将其转换为数字图像,再经过计算机处理后,在显示器屏幕上显示出材料内部缺陷的性质、大小和位置等信息,再按照有关标准对检测结果进行等级评定,从而达到焊缝焊接质量的检测和分析。
五大常规无损检测技术之一:射线检测(RT)的原理和特点

五大常规无损检测技术之一:射线检测(RT)的原理和特点射线检测(Radiographic Testing),业内人士简称RT,是工业无损检测(Nondestructive Testing)的一个重要专业门类。
射线检测主要的应用是探测工件内部的宏观几何缺陷。
按照不同特征,可将射线检测分为多种不同的方法,例如:X射线层析照相(X-CT)、计算机射线照相技术(CR)、射线照相法,等等。
射线照相法是五大常规无损检测技术之一,其他四种是:超声检测(Ultrasonic Testing):A型显示的超声波脉冲反射法、磁粉检测(MagneticParticle Testing)、渗透检测(Penetrant Testing)、涡流检测(Eddy Current Testing).第一行左起一:固定式磁粉探伤机;第一行左起二:射线检测室的防护屏蔽门。
第二行左起一:便携式X射线管;第二行左起二:A型显示的模拟式超声波探仪。
射线照相法,利用X射线管产生的X射线或放射性同位素产生的γ射线穿透工件,以胶片作为记录信息的器材的无损检测方法。
该方法是最基本、应用最广泛的的一种射线检测方法,也是射线检测专业培训的主要内容。
射线照相法的原理射线检测,本质上是利用电磁波或者电磁辐射(X射线和γ射线)的能量。
射线在穿透物体过程中会与物质发生相互作用,因吸收和散射使其强度减弱。
强度衰减程度取决于物质的衰减系数和射线在物质中穿透的厚度.详情请看:铅门为什么可以防止核辐射?射线照相法的原理:如果被透照物体(工件)的局部存在缺陷,且构成缺陷的物质的衰减系数又不同于试件(例如在焊缝中,气孔缺陷里面的空气衰减系数远远低于钢的衰减系数),该局部区域的透过射线强度就会与周围产生差异。
把胶片放在适当位置使其在透过射线的作用下感光,经过暗室处理后得到底片。
射线穿透工件后,由于缺陷部位和完好部位的透射射线强度不同,底片上相应部位等会出现黑度差异.射线检测员通过对底片的观察,根据其黒度的差异,便能识别缺陷的位置和性质。
dr无损检测实操评分
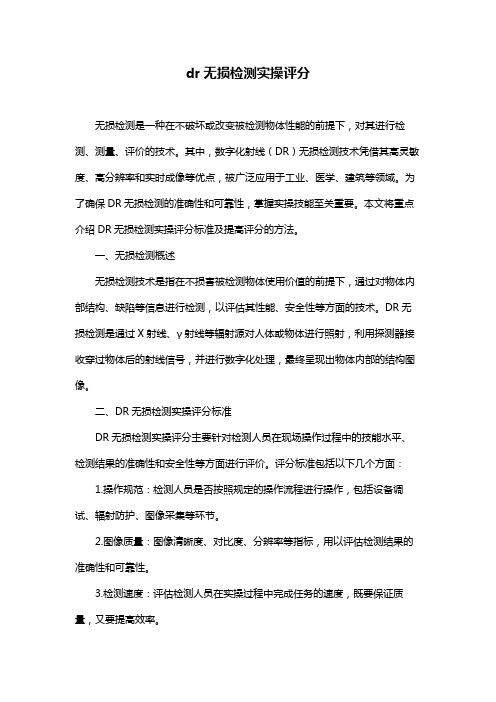
dr无损检测实操评分无损检测是一种在不破坏或改变被检测物体性能的前提下,对其进行检测、测量、评价的技术。
其中,数字化射线(DR)无损检测技术凭借其高灵敏度、高分辨率和实时成像等优点,被广泛应用于工业、医学、建筑等领域。
为了确保DR无损检测的准确性和可靠性,掌握实操技能至关重要。
本文将重点介绍DR无损检测实操评分标准及提高评分的方法。
一、无损检测概述无损检测技术是指在不损害被检测物体使用价值的前提下,通过对物体内部结构、缺陷等信息进行检测,以评估其性能、安全性等方面的技术。
DR无损检测是通过X射线、γ射线等辐射源对人体或物体进行照射,利用探测器接收穿过物体后的射线信号,并进行数字化处理,最终呈现出物体内部的结构图像。
二、DR无损检测实操评分标准DR无损检测实操评分主要针对检测人员在现场操作过程中的技能水平、检测结果的准确性和安全性等方面进行评价。
评分标准包括以下几个方面:1.操作规范:检测人员是否按照规定的操作流程进行操作,包括设备调试、辐射防护、图像采集等环节。
2.图像质量:图像清晰度、对比度、分辨率等指标,用以评估检测结果的准确性和可靠性。
3.检测速度:评估检测人员在实操过程中完成任务的速度,既要保证质量,又要提高效率。
4.安全性:评估检测过程中辐射防护措施是否到位,以确保操作人员和他人的安全。
三、实操评分具体步骤1.设备准备:检查DR设备是否正常运行,辐射源、探测器等部件是否齐全。
2.设备调试:根据被检测物体的性质和检测要求,调整设备参数,确保图像质量。
3.辐射防护:设置辐射防护设施,确保操作人员和他人安全。
4.图像采集:根据检测标准和要求,进行图像采集。
5.图像处理:对采集到的图像进行去噪、增强、分割等处理,以提高图像质量。
6.结果分析:分析图像中物体的内部结构、缺陷等信息,得出检测结果。
四、提高DR无损检测实操评分的方法1.加强培训:提高操作人员对DR无损检测的理论知识和实操技能水平。
2.优化设备:选购高性能的DR设备,提高检测质量和效率。
无损检测方法

无损检测方法
无损检测是一种非破坏性的检测方法,主要用于检测材料或零部件的内部质量和结构缺陷,例如裂纹、气孔、杂质等。
它可以通过不同的物理原理和技术手段来实现。
下面将介绍几种常用的无损检测方法。
一、X射线检测
X射线检测是利用X射线的穿透性质来检测材料内部的缺陷的一种方法。
该方法具有穿透力强、检测效率高的特点,适用于各种材料的检测。
在检测过程中,通过测量射线透射过程中的吸收和散射情况,可以确定材料的内部结构和缺陷。
二、超声波检测
超声波检测是利用超声波在材料中传播的特性来检测材料的内部缺陷的一种方法。
该方法采用超声波探测器向被测材料发射超声波,并记录超声波的传播时间和强度。
通过分析实测数据可以确定材料的内部结构和缺陷。
三、涡流检测
涡流检测是利用涡流感应现象来检测材料表面和近表面的缺陷的一种方法。
该方法通过将交变电流通过探测线圈引入被测材料中,当线圈靠近材料表面时,由于磁感应强度的变化,会产生涡流。
通过测量涡流的强度和分布情况,可以确定材料的表面和近表面的缺陷。
四、磁粉检测
磁粉检测是利用磁场分布的变化来检测材料表面和近表面缺陷
的一种方法。
该方法通过在被测材料表面或近表面施加磁场,并在磁场作用下将磁粉粘附在缺陷处。
通过观察磁粉的分布情况,可以确定材料的表面和近表面的缺陷。
以上介绍的是常用的几种无损检测方法,它们各具特点,在不同的检测场景中都有广泛应用。
无损检测方法能够实现对材料和零部件的内部结构和缺陷的快速、准确检测,对于保证产品质量和安全具有重要意义。
射线无损检测技术的原理与应用

射线无损检测技术的原理与应用射线无损检测技术是一种非破坏性测试方法,利用射线的穿透能力对材料进行检测和分析,常用于工业领域中对物体内部缺陷、结构和特性的评估。
本文将介绍射线无损检测技术的原理以及其在不同领域的应用。
射线无损检测技术主要包括放射性同位素源和电子加速器两种形式。
放射性同位素源根据放射性元素的不同类型,通常采用γ射线、X射线和中子射线进行检测。
γ射线是由放射性同位素产生的高能量电磁波,具有穿透力强且波长短的特点。
X射线是通过电子加速器产生的高能X射线,与γ射线性质相似。
中子射线是通过放射性同位素通过裂变产生的中子,具有较高的穿透能力和较低的散射能力。
射线无损检测技术的原理是根据射线在不同物质中的吸收和散射特性来检测物体的内部结构以及缺陷。
当射线穿过物体时,会与物质内的原子相互作用,发生吸收和散射。
吸收是指射线被物质中的原子吸收而减弱或消失;散射是指射线与物质中的原子相互作用后改变了方向。
射线无损检测技术在工业应用中具有广泛的应用场景。
在航空航天领域,射线无损检测技术常用于检测航空器的机身、发动机和航空梁等零部件的缺陷和疲劳裂纹,以确保其结构安全可靠。
在汽车制造领域,射线无损检测技术可用于检测汽车发动机缸体、传动系统、车轮和刹车系统等关键零部件的缺陷和变形,提高汽车的安全性和可靠性。
在核能领域,射线无损检测技术可用于对反应堆设备和燃料元件进行检测,以保障核能设施的安全运行。
在金属加工和焊接行业,射线无损检测技术可用于检测焊接接头的质量以及金属材料的裂纹和缺陷,确保产品的质量合格。
此外,射线无损检测技术还可以应用于建筑、电子、管道和制药等行业,对各类材料和产品进行缺陷检测和质量控制。
尽管射线无损检测技术在工业领域中具有广泛应用,但也存在一些潜在的风险。
射线辐射对人体健康有一定的危害性,必须进行严格的辐射防护和安全措施。
同时,射线无损检测技术需要专业人员进行操作和解读结果,准确性和可靠性受到操作者的经验和技术水平的影响。
使用无损检测技术进行射线检测的操作步骤与技巧

使用无损检测技术进行射线检测的操作步骤与技巧无损检测技术是一种非破坏性的检测方法,可以用于检测材料内部的缺陷和疾病。
其中,射线检测是无损检测技术中的一种常见方法。
本文将介绍使用无损检测技术进行射线检测的操作步骤和一些技巧。
一、操作步骤1. 准备工作在进行射线检测之前,首先要准备好必要的设备和材料。
这包括射线源、辐射检测器、辐射防护设备、标记工具等。
2. 确定检测对象和目的根据需要,确定要检测的对象和检测的目的。
例如,检测焊接缺陷、测量材料的密度等。
3. 设定检测参数根据实际需求,设定合适的检测参数。
这包括射线源的放射剂量、检测距离、曝光时间等。
4. 辐射防护措施在进行射线检测时,应采取适当的辐射防护措施,以保护操作人员的安全。
这包括穿戴防护服、佩戴防护装备,确保检测区域的限制和警示等。
5. 放置射线源和辐射检测器将射线源和辐射检测器放置在合适的位置。
射线源应放置在距离检测对象一定距离的位置,而辐射检测器应保持相对于射线源的恰当位置,以接收射线经过物体后的弱信号。
6. 进行射线照射启动射线源,并在设定的参数下进行射线照射。
确保照射时间足够长,并保持辐射源和检测器的相对位置不变。
7. 数据采集与分析将辐射检测器采集到的数据进行记录,并进行分析。
可以使用计算机软件等辅助工具来处理数据,以便更好地识别和评估缺陷和疾病。
8. 结果评估与报告根据检测结果,对目标物体进行评估,并生成相应的检测报告。
检测报告应包括检测结果、缺陷的位置和性质、建议的修复方法等。
二、技巧1. 注意辐射安全射线检测过程中,要严格遵守辐射安全规定,确保操作人员的健康安全。
限制人员停留时间、使用防护设备等都是常见的辐射安全措施。
2. 选择合适的射线源和检测器选择适合检测对象和目的的射线源和辐射检测器。
不同的射线源和检测器有不同的特点和应用范围,根据需要进行选择。
3. 确定合适的曝光时间和射线剂量曝光时间和射线剂量的选择对得到准确的检测结果很重要。
无损检测射线底片评定技术

一、底片评定的基本要求评片工作一般包括下面的内容:1)评定底片本身质量的合格性;2)正确识别底片上的影像;3)依据从已知的被检工件信息和底片上得到的影像信息,按照验收标准或技术条件对工件质量作出评定;4)记录和资料。
1.底片质量要求(1)灵敏度:从定量方面而言,是指在射线底片可以观察到的最小缺陷尺寸或最小细节尺寸;从定性方面而言,是指发现和识别细小影像的难易程度。
在射线底片上所能发现的沿射线穿透方向上的最小尺寸,称为绝对灵敏度,此最小缺陷尺寸与透照厚度的百分比称为相对灵敏度。
用人工孔槽,金属丝尺寸(像质计)作为底片影像质量的监测工具而得到的灵敏度又称为像质计灵敏度。
要求:底片上可识别的像质计影像、型号、规格、摆放位置,可观察的像质丝号是否达到标准规定要求等,满足标准规定为合格。
(2)黑度:为保证底片具有足够的对比度,黑度不能太小,但因受到观片灯亮度的限制,底片黑度不能过大。
底片黑度测定要求:按标准规定,其下限黑度是指底片两端搭接标记处的焊缝余高中心位置的黑度,其上限黑度是指底片中部焊缝两侧热影响区(母材)位置的黑度。
只有当有效评定区内各点的黑度均在规定的范围内方为合格。
(底片黑度有一定的范围,才有可能成为影像)底片评定范围内的黑度应符合下列规定A级:1.5≤D≤4.5;AB级 2.0≤D≤4.5;B级:2.3≤D≤4.5;透照小径管或其它截面厚度变化大的工件时,经合同各方同意,AB级最低黑度可降低至1.5,B级最低黑度可降低至2.0。
采用多胶片技术时,单片观察时单片的黑度应符合以上要求,A级允许以双片叠加观察,双片迭加观察时单片黑度应不低于1.3。
对评定范围内黑度D>4.5的底片,如有计量检定报告证明所用观片灯的亮度能满足要求,并经合同各方同意,允许进行评定。
(3)标记:底片上标记的种类和数量应符合有关标准和工艺规定,标记影像应显示完整、位置正确。
常用标记分为识别标记:如产品编号、焊接接头编号、部位编号和透照日期。
无损检测技术中的射线照相操作技巧
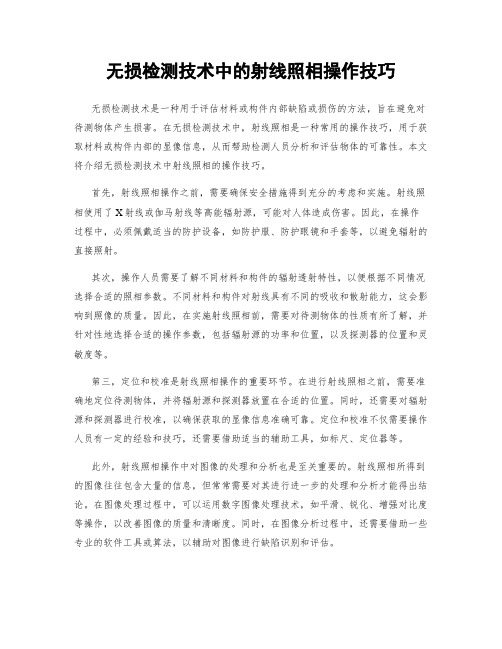
无损检测技术中的射线照相操作技巧无损检测技术是一种用于评估材料或构件内部缺陷或损伤的方法,旨在避免对待测物体产生损害。
在无损检测技术中,射线照相是一种常用的操作技巧,用于获取材料或构件内部的显像信息,从而帮助检测人员分析和评估物体的可靠性。
本文将介绍无损检测技术中射线照相的操作技巧。
首先,射线照相操作之前,需要确保安全措施得到充分的考虑和实施。
射线照相使用了X射线或伽马射线等高能辐射源,可能对人体造成伤害。
因此,在操作过程中,必须佩戴适当的防护设备,如防护服、防护眼镜和手套等,以避免辐射的直接照射。
其次,操作人员需要了解不同材料和构件的辐射透射特性,以便根据不同情况选择合适的照相参数。
不同材料和构件对射线具有不同的吸收和散射能力,这会影响到照像的质量。
因此,在实施射线照相前,需要对待测物体的性质有所了解,并针对性地选择合适的操作参数,包括辐射源的功率和位置,以及探测器的位置和灵敏度等。
第三,定位和校准是射线照相操作的重要环节。
在进行射线照相之前,需要准确地定位待测物体,并将辐射源和探测器放置在合适的位置。
同时,还需要对辐射源和探测器进行校准,以确保获取的显像信息准确可靠。
定位和校准不仅需要操作人员有一定的经验和技巧,还需要借助适当的辅助工具,如标尺、定位器等。
此外,射线照相操作中对图像的处理和分析也是至关重要的。
射线照相所得到的图像往往包含大量的信息,但常常需要对其进行进一步的处理和分析才能得出结论。
在图像处理过程中,可以运用数字图像处理技术,如平滑、锐化、增强对比度等操作,以改善图像的质量和清晰度。
同时,在图像分析过程中,还需要借助一些专业的软件工具或算法,以辅助对图像进行缺陷识别和评估。
最后,射线照相操作结束后,对辐射源和探测器进行必要的安全处理。
射线照相使用的辐射源具有一定的放射性,因此在操作结束后,必须妥善处理辐射源,避免造成环境污染和人员伤害。
此外,还需要对探测器进行清洁和维护,以确保下次使用时的正常工作。
最新五大常规无损检测技术之一:射线检测(rt)的原理和特点复习进程

五大常规无损检测技术之一:射线检测(RT)的原理和特点射线检测(Radiographic Testing),业内人士简称RT,是工业无损检测(Nondestructive Testing)的一个重要专业门类。
射线检测主要的应用是探测工件内部的宏观几何缺陷。
按照不同特征,可将射线检测分为多种不同的方法,例如:X射线层析照相(X-CT)、计算机射线照相技术(CR)、射线照相法,等等。
射线照相法是五大常规无损检测技术之一,其他四种是:超声检测(Ultrasonic Testing):A型显示的超声波脉冲反射法、磁粉检测(MagneticParticle Testing)、渗透检测(Penetrant Testing)、涡流检测(Eddy Current Testing)。
第一行左起一:固定式磁粉探伤机;第一行左起二:射线检测室的防护屏蔽门。
第二行左起一:便携式X射线管;第二行左起二:A型显示的模拟式超声波探仪。
射线照相法,利用X射线管产生的X射线或放射性同位素产生的γ射线穿透工件,以胶片作为记录信息的器材的无损检测方法。
该方法是最基本、应用最广泛的的一种射线检测方法,也是射线检测专业培训的主要内容。
射线照相法的原理射线检测,本质上是利用电磁波或者电磁辐射(X射线和γ射线)的能量。
射线在穿透物体过程中会与物质发生相互作用,因吸收和散射使其强度减弱。
强度衰减程度取决于物质的衰减系数和射线在物质中穿透的厚度。
详情请看:铅门为什么可以防止核辐射?射线照相法的原理:如果被透照物体(工件)的局部存在缺陷,且构成缺陷的物质的衰减系数又不同于试件(例如在焊缝中,气孔缺陷里面的空气衰减系数远远低于钢的衰减系数),该局部区域的透过射线强度就会与周围产生差异。
把胶片放在适当位置使其在透过射线的作用下感光,经过暗室处理后得到底片。
射线穿透工件后,由于缺陷部位和完好部位的透射射线强度不同,底片上相应部位等会出现黑度差异。
射线检测员通过对底片的观察,根据其黒度的差异,便能识别缺陷的位置和性质。
X射线的无损检测技术

X射线的无损检测技术无损检测(Non-Destructive Testing,简称NDT)是指在不破坏物体的完整性和功能的前提下,利用其中一种物理现象或者原理对物体进行检测和评价的一种技术。
在现代工业生产中,无损检测被广泛应用于材料的缺陷检测、质量控制和产品的评估等领域。
其中,X射线无损检测技术作为一种常用的方法,在工业领域发挥着重要的作用。
X射线是一种具有较高穿透能力和能够形成影像的电磁辐射。
X射线无损检测技术利用X射线在物体内部的吸收、散射和透射特性,通过探测被检物体产生的X射线影像,进行缺陷的探测和评价。
X射线无损检测技术主要包括X射线透射成像、X射线散射成像和X射线衍射等方法。
X射线透射成像主要利用X射线的穿透能力,将被检物体放置在X射线源和探测器之间,通过探测器记录X射线透射过程中的变化,获得物体内部结构的影像。
这种方法可以用于检测各种类型的缺陷,如裂纹、气孔、夹杂等。
X射线透射成像技术在航空航天、汽车工业、电子工业等领域得到了广泛应用。
X射线散射成像则是利用被检物体散射X射线的特性,通过记录散射X射线的位置和强度,获得物体表面或者物体内部的散射图像。
这种方法主要用于具有复杂几何形状的物体或者在X射线透射成像中无法进行有效检测的情况下。
X射线散射成像技术在化工、食品、药品等领域得到了广泛应用。
X射线衍射是利用X射线入射被检物体的表面或者内部,通过物体晶体结构中的原子间距和晶面的衍射效应,探测物体的晶体结构和材料的组分。
这种方法主要用于金属材料的组织结构研究和质量评价,对于金属的相变、应力松弛和组织退火等过程具有重要价值。
X射线无损检测技术具有以下优势:1.非接触性:X射线无损检测技术无需物与设备直接接触,可以避免因接触而带来的污染和损伤。
2.全面性:X射线无损检测技术可以对物体的表面和内部进行检测,能够探测到各种类型的缺陷,并且可以分析物体的组织结构和成分。
3.高效性:X射线无损检测技术具有快速、准确的特点,可以实现对大量物体的快速检测和评价。
x射线无损检测技术原理
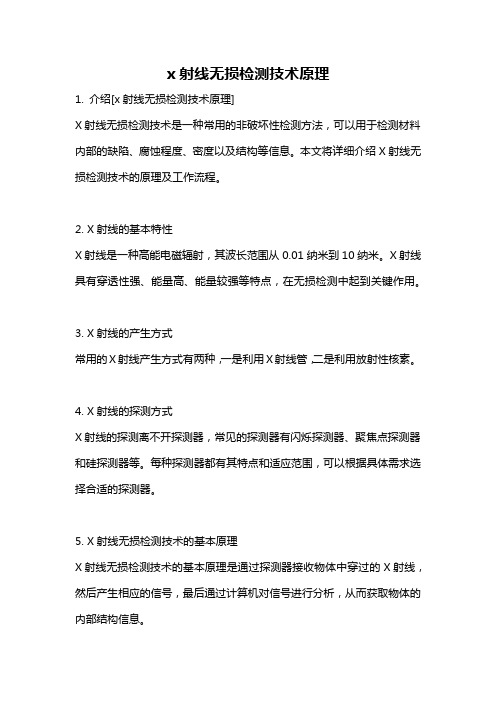
x射线无损检测技术原理1. 介绍[x射线无损检测技术原理]X射线无损检测技术是一种常用的非破坏性检测方法,可以用于检测材料内部的缺陷、腐蚀程度、密度以及结构等信息。
本文将详细介绍X射线无损检测技术的原理及工作流程。
2. X射线的基本特性X射线是一种高能电磁辐射,其波长范围从0.01纳米到10纳米。
X射线具有穿透性强、能量高、能量较强等特点,在无损检测中起到关键作用。
3. X射线的产生方式常用的X射线产生方式有两种,一是利用X射线管,二是利用放射性核素。
4. X射线的探测方式X射线的探测离不开探测器,常见的探测器有闪烁探测器、聚焦点探测器和硅探测器等。
每种探测器都有其特点和适应范围,可以根据具体需求选择合适的探测器。
5. X射线无损检测技术的基本原理X射线无损检测技术的基本原理是通过探测器接收物体中穿过的X射线,然后产生相应的信号,最后通过计算机对信号进行分析,从而获取物体的内部结构信息。
6. X射线的衰减规律当X射线穿过物体时,会发生衰减。
衰减规律与物体的密度、厚度以及内部结构有关。
通过测量X射线的衰减程度,可以推断物体的内部结构。
7. X射线的成像方法常见的X射线成像方法有放射性成像和计算机断层成像。
其中,放射性成像是利用放射性核素在物体内部的分布图像进行成像,计算机断层成像则是通过旋转X射线管和探测器,根据不同方向的射线信息进行成像。
8. X射线无损检测的应用领域X射线无损检测技术广泛应用于工业领域,常见的应用包括飞机、汽车、桥梁、建筑材料以及电子设备等。
通过X射线无损检测技术,可以及时发现材料内部的缺陷或问题,帮助进行及时维修和处理。
9. X射线无损检测的优势和局限性X射线无损检测技术具有非破坏性、高分辨率、快速准确等优点,可以提高工作效率和材料质量。
然而,X射线无损检测技术也存在一些局限性,如成本较高、对人体有一定的辐射危害等。
10. X射线无损检测技术的发展趋势随着科技的不断进步和应用需求的增加,X射线无损检测技术将面临更多的挑战和机遇。
无损检测技术中的射线检测与电磁检测对比

无损检测技术中的射线检测与电磁检测对比无损检测技术是一门应用广泛的科学技术,通过一系列的非侵入性检测方法,能够在不破坏被测物体的情况下,获取其内部和外部的缺陷信息。
在无损检测技术中,射线检测和电磁检测是常用的两种方法。
本文将从原理、应用范围和优缺点三个方面对射线检测和电磁检测进行对比。
首先,射线检测和电磁检测在原理上存在明显的差异。
射线检测主要利用射线的物理特性,如透射、散射和吸收等,通过探测器捕捉射线的强度变化,进而推断被测物体的内部结构和缺陷情况。
常见的射线检测方法包括X射线检测和γ射线检测。
而电磁检测则是利用电磁波与物体相互作用的原理,通过探测电磁波的反射、透射、吸收等信号变化,从而获取被测物体的结构和性能信息。
常见的电磁检测方法包括红外热像仪、超声波检测和涡流检测等。
其次,射线检测和电磁检测在应用范围上有所差异。
射线检测在工业领域广泛应用于金属和合金材料的检测,特别是在焊接、铸造和压力容器等制造工艺中,可以检测到材料的裂纹、气孔、夹杂物等缺陷。
射线检测存在的一个主要问题是辐射危害,尤其对操作人员的健康造成潜在威胁。
相比之下,电磁检测方法则可以无需辐射,适用于广泛的材料类型,包括金属、塑料、复合材料等。
电磁检测在航空、汽车、电子、医疗等行业有着广泛的应用,可以用于检测材料的疲劳裂纹、导热性能、电气性能等。
最后,射线检测和电磁检测在优缺点方面也存在一些差异。
射线检测具有穿透力强、检测精度高的特点,可以检测到微小的缺陷,在金属材料的检测中有着不可替代的优势。
但是,射线检测对操作人员的辐射危害较大,需要严格的安全控制和防护措施。
电磁检测方法则相对安全,但是对于较深层次的缺陷或杂质的检测效果相对较差。
电磁检测技术还受到环境干扰的影响,可能会引入误差。
因此,在具体应用中,需要根据被检测物体的类型、缺陷的要求以及操作人员的安全等因素综合考虑选择适当的无损检测方法。
综上所述,射线检测和电磁检测是无损检测技术中常用的两种方法。
- 1、下载文档前请自行甄别文档内容的完整性,平台不提供额外的编辑、内容补充、找答案等附加服务。
- 2、"仅部分预览"的文档,不可在线预览部分如存在完整性等问题,可反馈申请退款(可完整预览的文档不适用该条件!)。
- 3、如文档侵犯您的权益,请联系客服反馈,我们会尽快为您处理(人工客服工作时间:9:00-18:30)。
X射线得无损检测技术一前言无损检测方法就是利用声、光、电、热、磁及射线等与被测物质得相互作用,在不破坏与损伤被测物质得结构与性能得前提下,检测材料、构件或设备中存在得内外部缺陷,并能确定缺陷得大小、形状与位置。
无损检测得技术有很多,包括:染料渗透检测法、超声波检测法、强型光学检测法、渗透检测法﹑声发射检测法,以及本文介绍得x射线检测法。
X射线无损探伤就是工业无损检测得主要方法之一,就是保证焊接质量得重要技术,其检测结果己作为焊缝缺陷分析与质量评定得重要判定依据,应用十分广泛。
胶片照相法就是早期X射线无损探伤中常用得方法。
X射线胶片得成像质量较高,能够准确地提供焊缝中缺陷真实信息,但就是,该方法具有操作过程复杂、运行成本高、结果不易存放且查询携带不方便等缺点。
由于电子技术得飞速发展,一种新型得X射线无损检测方法“X 射线工业电视”已应运而生,并开始应用到焊缝质量得无损检测当中。
X射线工业电视己经发展到由工业CCD摄像机取代原始X 射线无损探伤中得胶片,并用监视器(工业电视)实时显示探伤图像,这样不仅可以节省大量得X射线胶片,而且还可以在线实时检测,提高了X射线无损检测得检测效率。
但现在得X射线工业电视大多还都采用人工方式进行在线检测与分析,而人工检测本身存在几个不可避免得缺点,如主观标准不一致、劳动强度大、检测效率低等等。
x射线无损探伤计算机辅助评判系统得原理可以用两个“转换”来概述:首先X射线穿透金属材料及焊缝区域后被图像增强器所接收,图像增强器把不可见得X射线检测信息转换为可视图像,并被CCD摄像机所摄取,这个过程称为“光电转换”;就信息量得性质而言,可视图像就是模拟量,它不能被计算机所识别,如果要输入计算机进行处理,则需要将模拟量转换为数字量,进行“模/数转换”,即经过计算机处理后将可视图像转换为数字图像。
其方法就是用高清晰度工业CCD摄像机摄取可视图像,输入到视频采集卡当中,并将其转换为数字图像,再经过计算机处理后,在显示器屏幕上显示出材料内部缺陷得性质、大小与位置等信息,再按照有关标准对检测结果进行等级评定,从而达到焊缝焊接质量得检测与分析。
二 X射线无损检测系统结构与原理射线无损探伤缺陷自动检测系统得硬件组成与结构如图1所示。
系统主要由三个部分组成:信号转换部分、图像处理部分及缺陷位置得获取与传输部分。
图1系统结构图信号转换部分主要由X光光源、螺旋钢管、传送车、图像增强器、反射器以及CCD摄像机组成,信号转换部分得主要功能就是完成从x射线到可见光得信息载体转换以及可见光到可视图像得光电转换。
螺旋钢管首先被放置到传送车上,传送车在承载螺旋钢管前进得同时,车上得旋转滚轮带动螺旋钢管旋转,这样可以保证螺旋钢管得螺旋焊缝始终保持在CCD摄像机得正下方,CCD摄像机就可以始终摄取到螺旋焊缝得探伤图像。
由X光光源发出得X射线穿透螺旋钢管及焊缝区域后,被图像增强器接收,图像增强器将不可见得X射线探伤信息转换为可见光探伤信息,再通过反射镜反射到CCD摄像机当中,CCD摄像机再将光信号转换为电信号(模拟数据),完成光电转换,并将探伤图像送入图像处理部分。
在信号转换部分中,CCD摄像机将摄取到得探伤图像以帧得形式送入图像处理部分得视频采集卡当中,同时在图像处理部分中得监视器(工业电视)上实时显示这帧原始探伤图像(模拟图像)。
如果在焊缝区域中存在气孔、夹渣或未焊透等缺陷时,由于与背景区域(焊缝区域)相比较,缺陷区域透过得X射线较多,所以在监视器(工业电视)上显示得探伤图像中就会形成一个亮点或者一条亮线,图像处理部分也正就是利用这个特点来检测每一帧探伤图像中就是否存在缺陷得。
图像处理部分中主要包括监视器(工业电视),视频采集卡,计算机,计算机显示器等设备,图像处理部分得功能主要包括采集、显示、处理并存储所采集到得探伤图像数据。
由CCD摄像机摄取到得探伤图像数据(模拟数据)首先被送入监视器,并在监视器上实时显示,同时该探伤图像数据被输入到视频采集卡当中,经过视频采集卡进行采样、量化与编码之后将其数字化。
数字化后得探伤图像同样以帧得形式送入到计算机当中,在计算机中通过下述基于模糊识别准则得模糊缺陷检测算法来检测每一帧探伤图像中就是否存在缺陷(本文将在后续详细介绍该模糊缺陷检测算法),并在计算机显示器上实时显示检测结果,同时将检测结果存储到计算机得存储器当中,以备后续得查找与验证。
缺陷位置得获取与传输部分主要由AT89C2051单片机、旋转编码器、Max232芯片、ADAM一4520模块与传输线等组成,缺陷位置得获取与传输部分得主要功能就是获取并传输缺陷得位置信息、系统利用AT89C2051单片机并通过日本欧姆龙公司生产得旋转编码器将位移信号转换为脉冲信号,通过脉冲信号得个数来一记录传送车得位移信号,再通过串行通信接口将位移信号传送给计算机进行处理,从而确定缺陷得位置信息。
三缺陷检测流程在本文设计并实现得X射线无损探伤缺陷自动检测系统中,缺陷得自动检测与识别部分就是系统得核心部分,该部分得程序流程可分为如下几个步骤:l)程序初始化:完成程序开始运行时,一些变量得定义与赋值以及视频采集卡得初始化工作;2)图像采集与串行通信接口初始化:利用视频采集卡采集X射线探伤图像,并同时初始化串行通信接口,完成串行通信得初始连接;3)图像预处理与获取位置信息:完成一些必要得图像预处理运算,从而保证模糊缺陷检测算法得有效检测;获取螺旋钢管前进得位置信息,以保证计算缺陷位置信息时使用:4)检测缺陷:应用模糊缺陷检测算法,检测当前X射线探伤图像中就是否有缺陷存在,并在探伤图像中标记检测到得缺陷;5)缺陷得识别:计算缺陷得一些基本信息,如:大小、个数与位置等信息,并按照一定得标准,对检测到得缺陷进行统一得识别与判定;6)缺陷就是否超标:判断缺陷就是否超出标准,如果超出标准,则发送喷标信号,在螺旋钢管上标记超出标准得缺陷;如果没有缺陷超出标准,则程序返回到初始状态,准备下一帧X射线探伤图像得采集、检测与识别。
缺陷自动检测与识别部分得程序流程框图如图2所示。
图三缺陷检测流程图四缺陷检测算法原理若在焊缝区域中存在气孔、夹渣以及未焊透等缺陷时,因为缺陷区域穿透得X射线较多,而相对来说周围背景区域X射线得透射量较少,所以在探伤图像中,缺陷区域就会形成一个亮点或者一条亮线。
这样在视觉上就可以根据探伤图像中,某一个区域就是否比其周围背景区域更加明亮来判断该区域就是否就是缺陷区域,而从图像处理得角度来瞧,可以根据探伤图像中像素灰度值得大小来判断一个区域就是否就是缺陷区域。
首先从人类视觉得角度出发,观察一下缺陷检测人员就是如何判断一个区域就是否就是缺陷区域。
如果一个区域比周围背景区域明亮,检测人员会认为这个区域可能就是缺陷区域,随着耐区域亮度差得继续加大,检测人员会一认为这个区域就是缺陷区域得可能性较大,甚至认为这个区域一定就是缺陷区域。
反之,如果一个区域与周围背景区域得亮度差不多,那么检测人员就会认为这个区域不就是缺陷区域,而就是背景区域。
在这里应该注意一个问题,人类视觉中得“亮度代或者说就是“明亮程度”,不仅仅就是指区域中像素得灰度平均值,而且还与区域中像素得空间方差特性(一定区域内像素灰度值变化得剧烈程度)有关。
也就就是说仅仅有着较高得灰度平均值还不够,或者说还不足以使缺陷检测人员确信这个区域就就是缺陷区域。
举一个特殊得例子,如果一个区域内有几个灰度值极大得点(实际上就就是几个恶性得随机噪声),它们仍然会使整个区域得灰度平均值较高,但这个区域却不就是缺陷,瞧起来也不比其周围背景区域“明亮”,因为这个区域只就是包含了几个恶性随机噪声得背景区域,而并非就是缺陷区域。
所以人类视觉中得“亮度”指得就是,除了有着较高得空间对比度(即灰度平均值)之外,还需要有着较低得空间方差特性,也就就是说,瞧起来还要“亮”得比较“均匀”。
在X射线探伤图像中,当缺陷区域与噪声区域呈现相同得空间对比度特性时(区域得平均灰度值相同),缺陷区域得方差特性显然要比噪声区域得空间方差特性低(区域得灰度值变化程度小);而当缺陷区域与噪声区域呈现相同得空间方差特性时,缺陷区域得空间对比度又必然要比噪声区域得空间对比度高。
所以在本文所采用得模糊缺陷检测算法中,对于具有相同空间对比度特性得区域来说,它得空间方差特性越小,就越有理由相信这个区域就是缺陷区域,其模糊隶属度得值就越高,反之就越低;而对于具有相同空间方差特性得区域来说,它得空间对比度特性越低,这个区域就是缺陷区域得可能性就越小,其模糊隶属度得值就越低,反之也就越高,这就就是模糊缺陷检测算法得基本原理,模糊缺陷检测算法中采用得模糊规则就就是基于此而形成得。
在本文采用得模糊缺陷检测算法中,一个重要得参数就是空间对比度参数中两个对比区域(检测区域与比较区域)之间得距离。
距离得大小对空间对比度参数得可靠性影响很大,无论过大或过小均无法正确反映所要比较两个区域真实得空间对比度特性。
一方面,当检测区域与比较区域之间得距离过小时,对于较大得缺陷来说,其反映得可能就是缺陷区域内部之间得空间对比度特性,并不就是所希望得到得缺陷区域与周围背景区域得空间对比度特性;另一方面,当检测区域与比较区域之间得距离过大又会失去缺陷区域与“周围”背景区域比较得意义,距离越大,两个区域之间得相关性就越小,空间对比度特性得意义也就越小。
所以检测区域与比较区域之间得距离大小应当适中,不易过大也不易过小,既要能准确反映出缺陷区域与其周围背景区域之间得对比度特性,又要能跳出较大得缺陷区域,防止缺陷区域内部之间得空间对比度得比较,具体情况如图4所示,其中,D为检测区域,E为比较区域,d为它们之间得距离。
在程序实现方面上,本文在远区域与近区域各选取了一个比较区域,将远、近两个比较区域计算出来得灰度平均值相加后再平均,即取远、近两个比较区域得平均值,这样在一定程度上就可以减少上述现象得发生。
图4 距离对检测效果得影响在本文所介绍得X射线无损探伤缺陷自动检测系统中,采用得模糊缺陷检测算法就就是基于上述介绍得模糊准则而实现得,即通过模糊理论来判断焊缝区域中就是否有缺陷存在。
所有需要检测得灰度探伤图像均就是由CCD摄像机摄取,并由视频采集卡数字化,再经过计算机处理之后,将结果保存在计算机得硬盘中。
灰度图像得灰度级为256,大小为768x576个像素。
所得得灰度探伤图像首先经焊缝提取方法,将焊缝区域大致确定出来,然后在大致确定出来得焊缝区域中以过滤得形式应用模糊缺陷检测算法,便可以准确得检测出焊缝区域中得缺陷及其具体位置所在。
由于各个X射线探伤系统得成像质量不尽相同,同时不同直径钢管得成像情况也有差别,所以产生得X射线探伤图像得质量差别比较大。