第二节盘套类零件工艺设计第二节盘类零件的制造工艺(精)
盘套类零件加工工艺 PPT

案例教学
一单元 盘套类零件的功用、结构特点、技术要求、材料与毛坯
(一)盘类零件 1、盘类零件的功用及结构特点
盘类零件在机器中主要起支承、连接作用。 主要由端面、外圆、内孔等组成,一般零件直 径大于零件的轴向尺寸,如齿轮、带轮、法兰盘、 端盖、模具、联轴节、套环、轴承环、螺母、垫圈 等。 一般用于传递动力、改变速度、转换方向或起 支承、轴向定位或密封等作用。 零件上常有轴孔;常设计有凸缘、凸台或凹坑 等结构;还常有较多的螺孔、光孔、沉孔、销孔或 键槽等结构;有些还具有轮辐、辐板、肋板以及用 于防漏的油沟和毡圈槽等密封结构。 各类盘类零件见图2-3(1)(2)所示。
盘套类零件加工工艺的设计与实施
重点:
1. 盘套类零件的加工工艺分析; 2. 盘套类零件的定位基准确定; 3. 盘套类零件的加工路线的确定; 4. 加工经济性分析。
难点:
盘套类零件的加工路线的确定及加工经济性分析。
盘套类零件加工工艺的设计与实施
第二部分 过程设计描述
该情境的学习与工作流程如下图:
资讯
分组点评 每小组选派4人(含组长),对前期所进行的资讯内容中的1、2、
3项进行畅谈。最后由老师进行归类评述,并对资讯方法进行点评 和指导。
学习情景2 常规特征零件的数控车削加工
大家有疑问的,可以询问和交流
精品课程
可以互相讨论下,但要小声点
9
盘套类零件加工工艺的设计与实施
第三部分 学习情境
步骤一:资讯
图2-4 套筒类零件案例
a)滑动轴承 b)滑动轴承 c)钻套 d)衬套 e)气缸 套 f)油缸
盘套类零件加工工艺的设计与实施
第三部分 学习情境
步骤一:资讯
案例教学 一单元 盘套类零件的功用、结构特点、技术要求、材料与毛坯
盘类零件的加工工艺分析

2)+35外 圆 面选 用 公 差 等 级 为 1T6, 上偏 差 为 0,下 用通用的机床设备。
偏 差 为一0.016 ml/1,对 +20H7的 同轴 度要 求 为 0.02 mm,
机床 夹 具 是工 件在 机 床 上进 行切 削 过程 中 ,保 证 f:
表 粗 糙度 为 RaO.8 、
表 面粗 糙度 为 尺00.8。
定心 卡盘 安装 。采 用三 爪 白定心 卡 盘装夹 外 圆时 ,为 保证
4)+20内孔选用公差 等级为 IT7,上 偏差为 0.021 mm, 定位 的可靠 性 ,通 常采 用 反 爪装 夹 方 法 (限制 了工 件 的 5
下偏 差 为 0,表 面粗 糙 度为 Ra1.6。
法兰盘及轴承环等。盘类零件用于传递动力 、转换方向或 为 后续 加T 的精 准 。根 据粗 基 准 的选 择 原则 ,选 取 毛坯
起 轴 向定 位 及密 封等 作用 。为 加强 支 承 ,盘类 零 件上 常设 西35外 网端 面作 为粗基 准 ,在 车床 卜选用 三爪 卡盘 装 夹工
有凸台 、凹坑等,此外 ,为与其它零件连接 ,盘类零件上还 件 ,以消 除法 兰盘 毛坯件 的 自由度 ,达到完 全定位 的 目的 。
个 自由度 );在对 内孔 进 行 装 夹 时 ,利 用 三 爪 卡 盘 离心 力
5)宽 度 为 34 Illnl的 左 右 两 端 面 的 表 面 粗 糙 度 为 的作 用 完成 对法 兰 盘零 件 的定 位 和夹 紧 。2)专 用 夹 具安
尺 a6.3。
装 。利用 外 圆作 径 向定 位 基准 时 ,选 用定 位环 作 为定 位
工 ,毛坯铸造完毕后 ,进行人工时效处理 ,以
消除 毛 坯 内部 的残余 应 力 ,避 免 在机 械 加 工
盘套类零件加工工艺的设计与编制
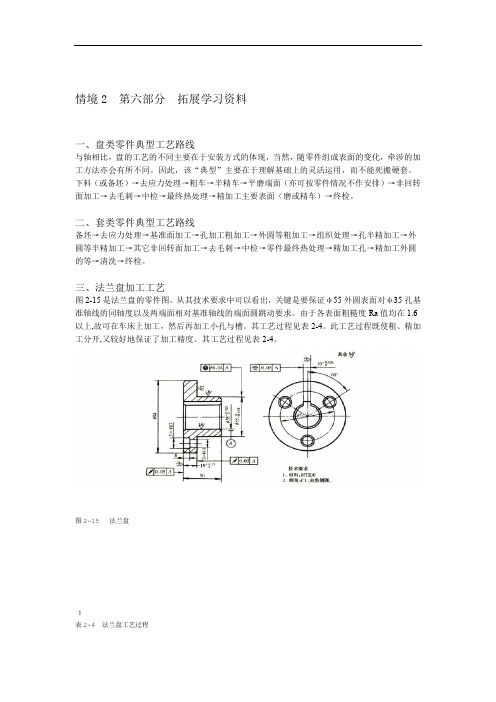
情境2 第六部分拓展学习资料一、盘类零件典型工艺路线与轴相比,盘的工艺的不同主要在于安装方式的体现,当然,随零件组成表面的变化,牵涉的加工方法亦会有所不同。
因此,该“典型”主要在于理解基础上的灵活运用,而不能死搬硬套。
下料(或备坯)→去应力处理→粗车→半精车→平磨端面(亦可按零件情况不作安排)→非回转面加工→去毛刺→中检→最终热处理→精加工主要表面(磨或精车)→终检。
二、套类零件典型工艺路线备坯→去应力处理→基准面加工→孔加工粗加工→外圆等粗加工→组织处理→孔半精加工→外圆等半精加工→其它非回转面加工→去毛刺→中检→零件最终热处理→精加工孔→精加工外圆的等→清洗→终检。
三、法兰盘加工工艺图2-15是法兰盘的零件图。
从其技术要求中可以看出,关键是要保证φ55外圆表面对φ35孔基准轴线的同轴度以及两端面相对基准轴线的端面圆跳动要求。
由于各表面粗糙度Ra值均在1.6以上,故可在车床上加工,然后再加工小孔与槽。
其工艺过程见表2-4。
此工艺过程既使粗、精加工分开,又较好地保证了加工精度。
其工艺过程见表2-4。
图2-15 法兰盘1表2-4 法兰盘工艺过程四、中心架和跟刀架中心架和跟刀架图2-162在加工细长轴或长套筒零件时,为了防止其弯曲变形,必须使用中心架或跟刀架作为辅助支承。
中心架上有三个等分布置并能单独调节伸缩的支承爪。
使用时,用压板、螺钉将中心架固定在床身导轨上,调节支承爪,使工件轴线与主轴轴线重合,且支承爪与工件表面的接触应松紧适当,如图2-16所示。
跟刀架上一般有两个能单独调节伸缩的支承爪,它们分别安在工件的上面和车刀的对面,如图2-16所示。
五、互为基准原则两个被加工表面之间位置精度较高,要求加工余量小而均匀时。
互为基准图2-17六、找正法装夹工件(1)直接找正法用百分表、划针或目测在机床上直接找正工件的有关基准,使工件占有正确的位置称为 2-18所示。
直接找正法。
单件和小批生产。
直接找正法如图)划线找正法(2使工件获得正确的位置称划在机床上用划线盘按毛坯或半成品上预先划好的线找正工件,所示。
盘类零件的制造工艺和套类零件的制造工艺
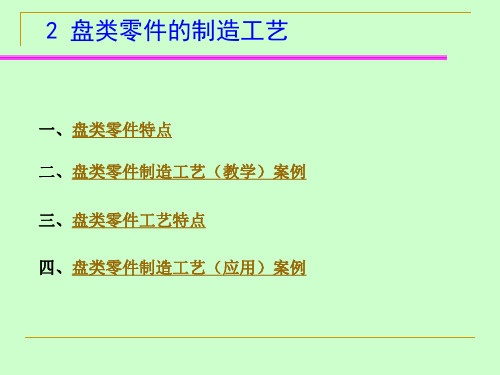
Байду номын сангаас 零件加工工艺过程卡
二、盘类零件制造工艺(教学)案例
5、零件加工仿真
支承块加工仿真
二、盘类零件制造工艺(教学)案例
6、本零件加工小结 (1)零件安装 (2)表面加工 (3)主要表面保证
三、盘类零件工艺特点
1、毛坯选择 2、基准选择 3、安装方案 (1)采用三爪卡盘安装 (2)用专用夹具安装 (3)用虎钳安装 4、表面加工方法 5、典型工艺路线 下料(或备坯)→ 去应力处理 → 粗车 → 半精 车 → 平磨端面(亦可按零件情况不作安排)→ 非回转面 加工 → 去毛刺 → 中检 → 最终热处理 → 精加工主要 表面(磨或精车)→ 终检
零件加工工艺过程卡
二、套类零件制造工艺案例
3、零件加工过程
轴套加工过程
三、套类零件制造工艺特点
1、毛坯选择 2、套类零件的基准与安装 3、主要表面的加工 4、典型工艺路线 备坯→ 去应力处理 → 基准面加工 → 孔加工粗加 工 → 外圆等粗加工 → 组织处理 → 孔半精加工 → 外圆 等半精加工 → 其它非回转面加工 → 去毛刺 → 中检→ 零件最终热处理 → 精加工孔 → 精加工外圆的等 → 清洗 →终检
2 盘类零件的制造工艺
一、盘类零件特点
二、盘类零件制造工艺(教学)案例 三、盘类零件工艺特点 四、盘类零件制造工艺(应用)案例
一、盘类零件特点
1、盘类零件一般功用
2、结构特点 3、技术要求
二、盘类零件制造工艺(教学)案例
案例3:支承块加工
零 件 三 维 图
二、盘类零件制造工艺(教学)案例
零件图
四、盘类零件制造工艺(应用)案例
3、零件加工过程
连接盘加工仿真
盘类零件加工工艺设计、编程与加工
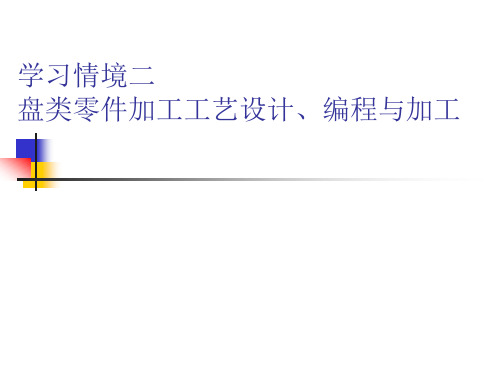
2.盘套零件的工艺 盘套类零件的基本工艺路线如下图2.2所示。
图2.2 基本工艺路线
二、孔加工方法及刀具 1.孔加工的常用方法及刀具 孔的加工方法通常有钻孔、扩孔、车孔和铰孔。
钻孔的常用刀具是麻花钻。钻孔属于粗加工,其尺寸精度一 般可达IT11~IT12,表面粗糙度Ra12.5~25µm。
二、复合固定循环
复合循环有三类,分别是内(外)径粗车复合循环G71,端 面粗车复合循环G72,封闭轮廓复合循环G73。图2.15所示 为端面粗车复合循环G72的运动轨迹。
程序段格式如下:
G72 U(△d) R(e) P(ns) Q(nf) X(△u) Z(△w) F_ S_ T_
N(ns) ……
四、外径切槽循环G75 外径切槽循环G75的循环路径如图1.20所示。 格式:G75 X(U)_ X(W)_ R(e)_ Q(ΔK)_ I(i)_ F_ 说明:G75指令在HNC-21 7.11版以后及HNC-18 4.03版以
后改动为可以实现三种切槽方式,每种方式的编程说明如下。
1.逐次进给到槽底方式,其动作顺序如图1.20所示:A->B>C->D->E->F->G->H->I->J->A->K->.
铰孔是用铰刀对未淬硬孔进行精加工的一种加工方法。铰孔 的刀具是铰刀。铰刀是尺寸精确的多刃刀具,铰孔的质量好、 效率高、操作简单,其精度可达IT7~IT9,表面粗糙度可达 Ra0.4 µm。
2.车孔 车孔的刀具及加工方法如下所示 (1)内孔车刀。根据加工情况,内孔车刀可以分为
通孔车刀和盲孔车刀两种,如图2.3所示。
(4)车台阶孔的工艺方法。
①车直径较小的台阶孔时,按先粗、精车小 孔,再粗、精车大孔的方法进行。
盘套类零件的加工工艺

③切削速度的选用,在被加工直径相同的条件下, 加工内孔的切削速度应是加工外圆的切削速度的 70%~80%。
三、盘套类零件的定位和装夹方法
(1)定位基准的选择。选择粗基准时, 尽量选择不加工表面或能牢固、可靠地 进行装夹的表面。选择精基准时,最好 满足基准重合原则,采用设计基准或装 配基准作为定位基准,并且尽量与测量 基准重合。盘套类零件在加工时的定位 基准主要是外圆和内孔。
图2.1 常用盘套类零件
2.盘套零件的工艺 盘套类零件的基本工艺路线如下图2.2所示。
图2.2 基本工艺路线
二、孔加工方法及刀具 1.孔加工的常用方法及刀具 孔的加工方法通常有钻孔、扩孔、车孔和铰孔。
钻孔的常用刀具是麻花钻。钻孔属于粗加工,其尺寸精度一 般可达IT11~IT12,表面粗糙度Ra12.5~25µm。
③充分加注切削液。切削液有润滑、冷却、清洗、 防锈等作用。
④合理选择刀具几何参数和切削用量。 ⑤内孔的加工特点。加工内孔时刀具在内孔中切削,
刀杆截面租受内孔直径的影响,要求刀杆不能与工 件发生干涉,且要留有排屑的空间,故刀杆细长, 刚性较差;刀具在内孔中切削,其散热、冷却润滑、 排屑都较为困难,因此对刀具材料的要求也较高; 刀具在切削过程中不便观察、排屑困难,尺寸及表 面质量较难控制,故对操作者的操作技能要求很高; 切削内孔时,进退刀方向与切削外圆时方向相反。
图2.3 内孔车刀 (a)通孔车刀 (b)盲孔车刀 (c)双后角
(2)内孔车刀的选用。常用的内孔车刀有3种不同 截面形状的刀柄,即圆柄、矩形柄和正方形柄。普 通型和模块式的圆柄车刀多用于车削中心和数控车 床上,如图2.6(a)所示。矩形和方形柄多用于普 通车床,如图2.6(b)所示。
图2.6 不同刀柄的内孔刀 (a)圆柄 (b)方柄
盘套类零件加工工艺共46页文档
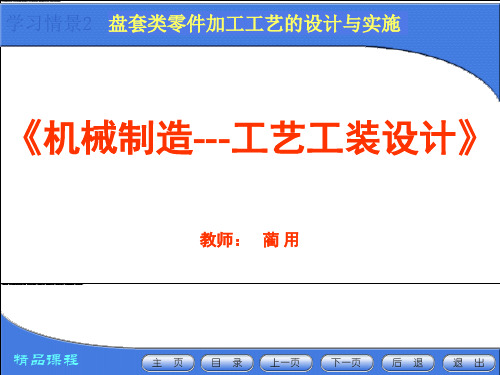
产品名称及型号____________零件名称____________零件图号____________
工艺规程号________________
材料_____________数量__________ 完工日期_________工时记录__________总页数________小组序号________
图2-3(1) 盘类零件案例
(a)支承盖
(b)法兰盘 (c)主轴承盖
图2-3(2) 盘类零件案例
精品课程
学习情景2 盘常套规类特零征件零加件工的工数艺控的车设削计加与工实施
第三部分 学习情境
步骤一:资讯
案例教学 一单元 盘套类零件的功用、结构特点、技术要求、材料与毛坯
(一)盘类零件 2、技术要求
盘类零件往往对支承用端面有较高平面度及轴向尺寸精度和两端面平行度要求; 对转接作用中的内孔等有与平面的垂直度要求,外圆、内孔间的同轴度要求等。
本情境采用单班分组方式教学,每班分3组。
精品课程
学习情景2 盘常套规类特零征件零加件工的工数艺控的车设削计加与工实施
第三部分 学习情境
步骤一:资讯
学生自由组合分成3个小组(各组选出组长1名),各组根据任务工作单和 资讯工作单完成必要的信息搜集,每组选4人准备发言。
编号:01
西京学院机械工程训练中心工艺编制任务工作单
学习情景2 盘常套规类特零征件零加件工的工数艺控的车设削计加与工实施
《机械制造---工艺工装设计》
教师: 蔺 用
精品课程
西京学院机械工程训练中心
学习情景2 盘常套规类特零征件零加件工的工数艺控的车设削计加与工实施
第一部分:学习任务描述
工艺科现有一批零件的工艺设计任务,其中有齿轮坯及联接套等两种零件, 科室将这两种零件的工艺设计任务交给你,要求你完成对其进行机械加工工艺编 制的任务。零件产品图如图2-1、图2-2所示:
套盘类零件加工工艺共24页文档
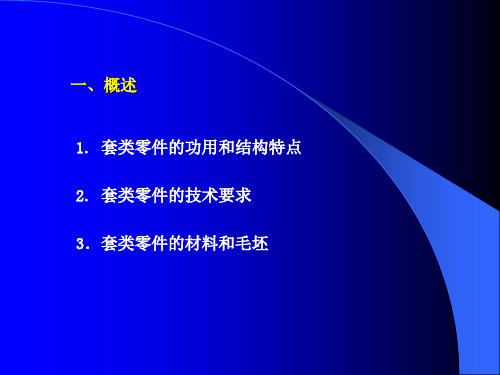
合的活塞上有密封圈,要求较低,一般取IT9。
外圆表面一般是套类零件本身的支承面,常以过盈配合
或过渡配合同箱体或机架上的孔连接。外径的尺寸精度通常
为IT6~IT7。也有一些套类零件外圆表面不需加工。
(2)几何形状精度
内孔的形状精度,应控制在孔径公差以内,有
些精密轴套控制在孔径公差的1/2—1/3,甚至更
(5)工序60、65 这两个工序是精加工工序。对于 外圆和内孔的精加工工序,一般常采用“先孔 后外圆”的加工顺序,因为孔定位所用的夹具 比较简单。 在工序60中,用Φ112外圆及其端面定位 用Φ112外圆夹紧。为了减小夹紧变形,故采 用均匀夹紧的方法,在工序中对A、B和D面采 用一次安装加工,其目的是保证垂直度和同轴 度。 在工序65中加工外圆表面时,采用A、B和 D面定位,由于A、B和D面是在工序60中一次安 装加工的,相互位置比较准确,所以为了保证 定位的稳定可靠,采用这一组表面作为定位基 准。
3.轴套加工工艺分析
(1)工序5、10、15 这三个工序组成粗加工阶段。 工序5采用大外圆及其端面作为粗基准,加工外圆,为下
一工序准备好定位基准,同时切除内孔的大部分余量。 工序10是加工大外圆及其端面,并加工大端内腔。这一
工序的目的是切除余量,同时也为下一工序准备定位基准。 工序15是加工外圆表面,用工序10加工好的大外圆及其
严。对于长的套件除了圆度要求外,还应注意孔的
圆柱度。
外圆表面的形状精度控制在外径公差以内。
(3)相互位置精度
当内孔的最终加工是在装配后进行时,套类零件本身的内外
圆之间的同轴度要求较低;如最终加工是在装配前完成则要求较
高,一般为0.01~0.05mm。当套类零件的外圆表面不需加工时,
盘套类零件加工工艺.
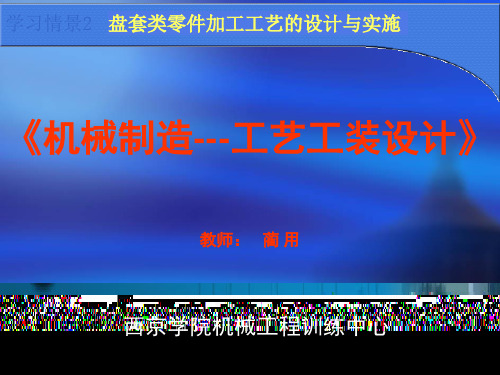
3、盘类零件的材料与毛坯
盘类零件常采用钢、铸铁、青铜或黄铜制成。孔径小的盘一般选择热轧或冷拔棒 料,根据不同材料,亦可选择实心铸件,孔径较大时,可作预孔。若生产批量较大, 可选择冷挤压等先进毛坯制造工艺,既提高生产率,又节约材料。
精品课程
学习情景2 盘套类零件加工工艺的设计与实施 常规特征零件的数控车削加工 第三部分 学习情境
精品课程
学习情景2 盘套类零件加工工艺的设计与实施 常规特征零件的数控车削加工 第三部分 学习情境
步骤一:资讯
案例教学
一单元 盘套类零件的功用、结构特点、技术要求、材料与毛坯
(一)盘类零件 1、盘类零件的功用及结构特点
盘类零件在机器中主要起支承、连接作用。
主要由端面、外圆、内孔等组成,一般零件直 径大于零件的轴向尺寸,如齿轮、带轮、法兰盘、 端盖、模具、联轴节、套环、轴承环、螺母、垫圈 等。 一般用于传递动力、改变速度、转换方向或起 支承、轴向定位或密封等作用。 零件上常有轴孔;常设计有凸缘、凸台或凹坑 等结构;还常有较多的螺孔、光孔、沉孔、销孔或 键槽等结构;有些还具有轮辐、辐板、肋板以及用 于防漏的油沟和毡圈槽等密封结构。 各类盘类零件见图2-3(1)(2)所示。
孔与外圆一般具有较高的同轴度要求;端面与孔轴线(亦有外圆的情况)的垂直度要求; 内孔表面本身的尺寸精度、形状精度及表面粗糙度要求;外圆表面本身的尺寸、形状精度及 表面粗糙度要求等。 尺寸精度: 内孔是套类零件起支承作用或导向作用的最主要表面,它通常与运动着的轴、刀具或活 塞等相配合。内孔直径的尺寸精度一般为IT7,精密轴套有时取IT6,油缸由于与其相配合的 活塞上有密封圈,要求较低,一般取IT9。 外圆表面一般是套类零件本身的支承面,常以过盈配合或过渡配合同箱体或机架上的孔 连接。外径的尺寸精度通常为IT6~IT7。也有一些套类零件外圆表面不需加工。
盘形类零件的数控编程及加工工艺规程设计 毕业论文

盘形类零件的数控编程及加工工艺规程设计摘要数控技术及数控机床在当今机械制造业中的重要地位和巨大效益,显示了其在国家基础工业现代化中的战略性作用,并已成为传统机械制造工业提升改造和实现自动化、柔性化、集成化生产的重要手段和标志。
数控技术及数控机床的广泛应用,给机械制造业的产业结构、产品种类和档次以及生产方式带来了革命性的变化。
数控机床是现代加工车间最重要的装备。
它的发展是信息技术(1T)与制造技术(MT)结合发展的结果。
现代的CAD/CAM、FMS、CIMS、敏捷制造和智能制造技术,都是建立在数控技术之上的。
掌握现代数控技术知识是现代机电类专业学生必不可少的。
本次设计内容介绍了盘形类零件数控加工的特点、加工工艺分析以及数控编程的一般步骤,并通过一定的实例详细的介绍了数控加工工艺的分析方法。
关键词:数控技术加工工艺编程NC and NC machine tool technology in today's machine manufacturing industry in an important position and great benefits that its national infrastructure in the industrial modernization of the strategic role and has become a traditional machinery manufacturing industries to transform and enhance automation, flexible, Integrated production and an important means of signs. NC technology and the widespread application of NC machine tools, machinery manufacturing to the industrial structure, product variety and quality and production methods brought about a revolutionary change. NC machine tool processing workshop is the most important modern equipment. It is the development of information technology (1 T) and manufacturing technology (MT) with the result of the development. Modern CAD / CAM, FMS, CIMS, agile manufacturing and intelligent manufacturing technology, are built on the technology in the NC. NC master modern technology of modern machinery and electronic knowledge is essential to professional students.The design of the content on the characteristics of the NC, processing and analysis of the general steps NC programming. And, through a detailed example of the NC on the process of analysis.KEY WORDS: NC programming technology processing technology目录前言 (1)第一章数控编程概况 (2)§1.1 数控编程及其发展前景 (2)§1.2 数控车床程序编制的两种方法 (3)第二章盘形类零件的编程设计 (4)§2.1 盘形类零件编程的基本步骤 (4)§2.2 盘形编程时控制尺寸精度的方法 (11)§2.3 对点与换刀点的确定 (12)第三章盘形类零件加工工艺设计分析 (13)§3.1 数控加工工艺和流程 (13)§3.2 盘形类零件的工艺流程 (13)§3.3制定盘形类零件工艺应注意的几点 (14)§3.4 盘形类零件加工工艺的具体步骤 (15)第四章盘形零件的工艺规程设计 (16)§4.1 盘形零件工艺规程设计实例 (16)§4.2加工方法的选择与加工方案的确定 (17)§4.3 盘形类零件数控加工路线的确定 (18)总结 (19)参考资料 (20)致谢 (21)前言此次论文是针对盘形类零件的数控车床编程和加工工艺规程设计的。
工艺第二章 典型零件的加工--盘套类
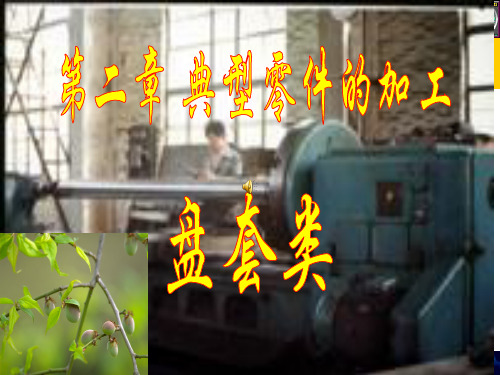
一、保证盘套类零件加工精度的方法: 保证盘套类零件加工精度的方法: 保证盘套类零件各表面位置精度的方法: 1、保证盘套类零件各表面位置精度的方法: 从盘套类零件的技术要求可知, 从盘套类零件的技术要求可知,其主要位置精度 是内、 是内、外圆表面的同轴度及端面与轴线之间的垂直度 方法: 要求 加工 一 方法: 1 一 加工方法 位置精度 内外表面及端面的加工: 内外表面及端面的加工: 工件的 ,可 是, 是, 加工方法的工 的盘套类零件
第 二 章 典 型 零 件 的 加 工 — 盘 套 类
2、防止盘套类在加工过程中变形的措施 盘套类零件孔壁较薄,加工中常因夹紧力、 盘套类零件孔壁较薄,加工中常因夹紧力、切削 力、残余应力和切削热等因素的影响而产生变形。为 残余应力和切削热等因素的影响而产生变形。 了防止变形,应注意以下几点: 了防止变形,应注意以下几点: 为减少切削力与切削热的影响: (1)为减少切削力与切削热的影响:粗、精加工应分 , 变形在精加工过程中 以 为减少夹紧力的影响: (2)为减少夹紧力的影响:工 夹紧 夹紧。 为 夹紧。 精 较 的精 套 ( 孔的 变形, 为 1 ) 的 变形, 较 的 , 孔 ,在 夹紧力。 加 夹紧力。
砂轮直径小, 砂轮直径小,磨 砂轮,为此, 砂轮,为此, 径 因此,磨孔的 因此, 磨 低。 低。 , 磨削
第 二
3)磨削质量的控制不如磨外圆方便。 磨削质量的控制不如磨外圆方便。
章 典 型 零 件 的 加 工 — 盘 套 类
这是因为,砂轮与内孔表面的接触面积大, 这是因为,砂轮与内孔表面的接触面积大,发热 量大,冷却排屑条件差,工件易产生热变形; 量大,冷却排屑条件差,工件易产生热变形;受内孔 直径的限制,砂轮轴一般细长,刚性弱, 直径的限制,砂轮轴一般细长,刚性弱,易产生弯曲 变形, 磨削的内孔产生内圆 变形, 差;为 差; 差, 径 量 磨 。因 , 磨削质量的控制不如磨外圆方便。 磨削质量的控制不如磨外圆方便。
- 1、下载文档前请自行甄别文档内容的完整性,平台不提供额外的编辑、内容补充、找答案等附加服务。
- 2、"仅部分预览"的文档,不可在线预览部分如存在完整性等问题,可反馈申请退款(可完整预览的文档不适用该条件!)。
- 3、如文档侵犯您的权益,请联系客服反馈,我们会尽快为您处理(人工客服工作时间:9:00-18:30)。
第二节 盘、套类零件工艺设计一、盘、套类零件特点(一)盘类零件1、功用盘类零件在机器中主要起支承、连接作用。
2、结构特点盘类零件主要由端面、外圆、内孔等组成,一般零件直径大于零件的轴向尺寸。
3、技术要求盘类零件往往对支承用端面有较高平面度及轴向尺寸精度及两端面平行度要求;对转接作用中的内孔等有与平面的垂直度要求,外圆、内孔间的同轴度要求等。
(二)套类零件1、功用套类零件在机器中主要起支承和导向作用。
2、结构特点零件主要由有较高同轴要求的内外圆表面组成,零件的壁厚较小,易产生变形,轴向尺寸一般大于外圆直径。
3、主要技术要求孔与外圆一般具有较高的同轴度要求;端面与孔轴线(亦有外圆的情况)的垂直度要求;内孔表面本身的尺寸精度、形状精度及表面粗糙度要求;外圆表面本身的尺寸、形状精度及表面粗糙度要求等。
二、盘、套类零件制造工艺(教学)案例案例3:支承块加工。
零件图三维图1、零件工艺性分析(1)零件材料:45钢。
切削加工性良好。
刀具材料及几何参数选择同案例1。
(2)零件组成表面:两端面,外圆面,中间孔及沉孔,安装孔,侧面,十字槽,倒角等。
(3)零件结构分析:两端面起支承作用,光度要求高,轴向尺寸在安装后通过配磨保证两件等高。
轴向尺寸小,为典型的盘类零件。
(4)主要技术条件:端面粗糙度要求Ra0.4µm两端面保证平行。
2、零件工艺设计(1)毛坯选择按零件形状及要求,可选棒料。
(2)基准及安装方案分析该零件的主要基准无疑为两端面,安装孔及十字槽等表面加工均为端面作定位基准,侧表面位置,孔的中心考虑精度要求不高,且该零件为单件生产,采用划线确定;两平面的平行度则采用互为基准的方法保证。
(3)零件表面加工方法按端面Ra0.4µm的要求,其终加工方法选择精磨。
为确保零件安装平整,安装孔应与端面垂直,在加工安装孔,铣十字槽前先粗磨好平面,孔及槽等表面加工后再精磨平面。
侧面采用铣削,安装孔采用钻削,中间孔及沉孔可采用车削。
(4)零件机加工艺路线下料—车—车—平磨—划线—钻—铣侧面—铣槽—去毛刺—平磨3、设备、工装选择该零件加工所选设备有卧式车床、铣床、立式铣床、钻床、平磨等。
零件安装用夹具选择主要有三爪卡盘、虎钳、磁力吸盘等。
刀具选择时注意定尺寸刀具的尺寸对应,不通孔加工应用盲孔车刀。
量具选用游标卡尺。
4、填写工艺文件56、本零件加工小结(1)零件安装:由于圆盘轴向尺寸较小,采用三爪卡盘直接装夹易使工件不平(定位不足),往往采用反爪安装,并保证与另一端面的平行度;其它表面加工(铣、钻),由于该零件属单件生产,故尽量选择通用夹具(如虎钳),平磨时采用磁力吸盘安装非常方便。
(2)表面加工:粗、半精加工仍以车为主,其余表面按其形状选择适当方法:侧面、槽采用铣削,安装孔采用钻削,为保证这些表面在零件上的位置精度,加工前先平磨基准。
(3)主要表面保证:互为基准磨削两端面,既可保证平行度,又能满足尺寸要求。
案例4:轴套加工零件图三维图1、零件工艺性分析(1)零件材料:45钢。
切削加工性良好。
刀具材料及其几何参数选择方案同案例1。
(2)零件组成表面:外圆表面(Φ100,Φ60),内表面(Φ44),型孔,两端面,内、外台阶面,内、外退刀槽,内、外倒角(3)主要表面分析:Φ44内孔既是支承其它零件的支承面,亦是本零件的主要基准面;Φ60外圆及其台阶面亦用于支承其它零件。
(4)主要技术条件:Φ60外圆与Φ44内孔的同轴度控制在0.03mm范围内;台阶面与Φ44内孔的垂直度控制在Φ44内孔本身的尺寸公差为mm;粗糙度Ra0.8μm;零件热处理硬度HRC50~55。
2、零件制造工艺设计(1)毛坯选择:根据零件材料为45钢,生产类型为中批生产,零件直径尺寸差异较大,零件壁薄、刚度低、易变形,加工精度要求较高,零件需经淬火处理等多方面因素,在棒料与模锻间作出选择:模锻件。
(2)基准分析:主要定位基准应为Φ44内孔中心;加工内孔时的定位基准则为Φ60外原中心。
(3)安装方案:加工大端及内孔时,可直接采用三爪卡盘装夹;粗加工小端可采用反爪夹大端,半精、精加工小端时,则应配心轴,以Φ44孔定位轴向夹紧工件。
型孔加工时,可采用分度头安装,将主轴上抬90º,并采用直接分度法,保证3×Φ6在零件圆周上的均分位置。
对大端的四个螺钉过孔则采用专用夹具安装:以大端面及Φ44孔作主定位基准,型孔防转,工件轴向夹紧。
(4)零件表面加工方法:Φ44内孔,采用精磨达到精度及粗糙度要求;外圆及其台阶面采用磨削加工;其余回转面以半精车满足加工要求;型孔在立铣上完成;四个安装孔采用钻削。
(5)热处理安排:因模锻件的表层有硬皮,会加速刀具磨损和钝化,为改善切削加工性,模锻后对毛坯进行退火处理,软化硬皮;零件的终处理为淬火,由于零件壁厚小,易变形,加之零件加工精度要求高,为尽量控制淬火变形,在零件粗加工后安排调质处理作预处理。
(6)其它工序安排:转换车间前应安排中间检验,易出现毛刺工序后安排去毛刺。
(7)设备、工装选择:设备选择有卧式车床、立式铣床、钻床、内圆磨床及外圆磨床。
专用夹具有心轴式车床夹具及磨床夹具;钻孔夹具。
定尺寸刀具有Φ6立铣刀、Φ10麻花钻、内外切槽刀。
所用量具有卡尺、内径千分尺等。
(8)填写工艺文件3三、盘、套类零件制造工艺特点(一)盘类零件1、毛坯选择盘类零件常采用钢、铸铁、青铜或黄铜制成。
孔径小的盘一般选择热轧或冷拔棒料,根据不同材料,亦可选择实心铸件,孔径较大时,可作预孔。
若生产批量较大,可选择冷挤压等先进毛坯制造工艺,既提高生产率,又节约材料。
2、基准选择根据零件不同的作用,零件的主要基准会有所不同。
一是以端面为主(如支承块)其零件加工中的主要定位基准为平面;二是以内孔为主,由于盘的轴向尺寸小,往往在以孔为定位基准(径向)的同时,辅以端面的配合;三是以外圆为主(较少),与内孔定位同样的原因,往往也需要有端面的辅助配合。
3、安装方案(1)用三爪卡盘安装用三爪卡盘装夹外圆时,为定位稳定可靠,常采用反爪装夹(共限制工件除绕轴转动外的五个自由度);装夹内孔时,以卡盘的离心力作用完成工件的定位、夹紧(亦限制了工件除绕轴转动外的五个自由度)。
(2)用专用夹具安装以外圆作径向定位基准时,可以定位环作定位件;以内孔作径向定位基准时,可用定位销(轴)作定位件。
根据零件构形特征及加工部位、要求,选择径向夹紧或端面夹紧。
(3)用虎钳安装生产批量小或单件生产时,根据加工部位、要求的不同,亦可采用虎钳装夹(如支承块上侧面、十字槽加工)。
4、表面加工零件上回转面的粗、半精加工仍以车为主,精加工则根据零件材料、加工要求、生产批量大小等因素选择磨削、精车、拉削或其它。
零件上非回转面加工,则根据表面形状选择恰当的加工方法,一般安排于零件的半精加工阶段。
5、工艺路线与轴相比,盘的工艺的不同主要在于安装方式的体现,当然,随零件组成表面的变化,牵涉的加工方法亦会有所不同。
因此,该“典型”主要在于理解基础上的灵活运用,而不能死搬硬套。
下料(或备坯)→去应力处理→粗车→半精车→平磨端面(亦可按零件情况不作安排)→非回转面加工→去毛刺→中检→最终热处理→精加工主要表面(磨或精车)→终检(二)套类零件1、毛坯选择套类零件的毛坯主要根据零件材料、形状结构、尺寸大小及生产批量等因素来选。
孔径较小时,可选棒料,也可采用实心铸件;孔径较大时,可选用带预孔的铸件或锻件,壁厚较小且较均匀时,还可选用管料。
当生产批量较大时,还可采用冷挤压和粉末冶金等先进毛坯制造工艺,可在提高毛坯精度提高的基础上提高生产率,节约用材。
2、套类零件的基准与安装套类零件的主要定位基准毫无疑问应为内外圆中心。
外圆表面与内孔中心有较高同轴度要求,加工中常互为基准反复加工保证图纸要求。
零件以外圆定位时,可直接采用三爪卡盘安装;当壁厚较小时,直接采用三爪卡盘装夹会引起工件变形,可通过径向夹紧、软爪安装、采用刚性开口环夹紧或适当增大卡爪面积等方面解决;当外圆轴向尺寸较小时,可与已加工过的端面组合定位,如采用反爪安装,工件较长时,可采用“一夹一托”法安装。
零件以内孔定位时,可采用心轴安装(圆柱心轴、可胀式心轴);当零件的内、外圆同轴度要求较高时,可采用小锥度心轴和液塑心轴安装。
当工件较长时,可在两端孔口各加工出一小段60度锥面,用两个圆锥对顶定位。
当零件的尺寸较小时,尽量在一次安装下加工出较多表面,既减小装夹次数及装夹误差,并容易获得较高的位置精度。
零件也可根据工件具体的结构形状及加工要求设计专用夹具安装。
3、主要表面的加工套类零件的主要表面为内孔。
内孔加工方法很多。
孔的精度、光度要求不高时,可采用扩孔、车孔、镗孔等;精度要求较高时,尺寸较小的可采用铰孔;尺寸较大时,可采用磨孔、珩孔、滚压孔;生产批量较大时,可采用拉孔(无台阶阻挡);有较高表面贴合要求时,采用研磨孔;加工有色金属等软材料时,采用精镗(金刚镗)。
4、典型工艺路线备坯→ 去应力处理 → 基准面加工 → 孔加工粗加工 → 外圆等粗加工 → 组织处理 → 孔半精加工 → 外圆等半精加工 → 其它非回转面加工 → 去毛刺 → 中检→ 零件最终热处理 → 精加工孔 → 精加工外圆的等 → 清洗 →终检。
四、盘类零件制造工艺应用案例案例5:连接盘加工零件图三维图1、零件工艺性分析(1)零件材料:HT200。
切削加工性良好,但为脆性材料,为防止加工中冲击(产生崩碎切屑)使刀具崩刃,可适当减小刀具前角。
刀具材料选择范围较大,高速钢与YG类硬质合金均可。
(2)零件组成表面:各外圆,内孔,内圆锥面,两端面及台阶面,外环槽,孔内键槽,4×Φ10小孔。
(3)主要表面分析:Φ180内孔,为零件安装中与轴的配合孔,也是该零件的主要基准面;端面B,为零件安装中的轴向定位基准,也是该零件的主要基准面之一;Φ420、Φ530外圆、外环槽及左端面均为与其它零件的配合面。
(4)主要技术条件:Φ420、Φ530外圆与Φ180内孔中心的同轴度要求分别为0.06和0.08mm;右端面B与Φ180内孔中心的垂直度保证为0.1mm;左端面与右端面B的平行度保证为0.1mm;2、零件制造工艺设计(1)毛坯选择根据零件材料、形状及尺寸及生产批量等因素,选砂型铸件。
(2)基准分析根据零件图上各要求,零件加工中主要定位基准应为Φ180孔(径向)和右端面B(轴向及与机床主轴的相对位置),在加工Φ180孔及右端面B时,则应选择与Φ180孔有同轴度要求的Φ530外圆面及与右端面有平行度要求的左端面。
(3)安装方案加工Φ180孔及右端面时,可采用三爪卡盘装夹(粗加工时直接装夹,半精加工后,反爪安装);加工其它回转面时,粗加工可用三爪以离心力作用夹Φ180内孔并支靠B面,半精加工后,可用心轴以A、B面定位,轴向夹紧安装;加工4×Φ10小孔时,可采用钻模安装;以A、B面主定位,键槽侧面可防转。