第7章数控铣削(加工中心)编程
数控加工中心编程

千里之行,始于足下。
数控加工中心编程数控加工中心编程是通过编写指令程序,控制数控加工中心实现自动加工的过程。
在进行数控加工中心编程时,需要考虑几个方面的因素,包括数控加工中心的坐标系、工件的具体形状和尺寸以及加工工艺等。
数控加工中心编程的基本步骤如下:1.了解数控加工中心的坐标系:数控加工中心的坐标系包括绝对坐标系和相对坐标系,需要根据实际情况选择合适的坐标系。
2.确定刀具和工件的坐标系:刀具和工件的坐标系有时候可能与数控加工中心的坐标系不同,因此需要先确定刀具和工件在数控加工中心中的坐标系。
3.绘制工件图形:根据工件的形状和尺寸,使用CAD软件或其他绘图软件绘制出工件的几何图形。
4.确定切削路径:根据工艺要求和加工的顺序,确定切削路径,包括走刀路径、刀轨和切入切出点等。
5.选择加工刀具:根据工件的材料和形状,选择合适的刀具,并确定切削参数,如切削速度、进给速度和切削深度等。
6.编写加工程序:根据确定的切削路径和刀具选择,编写数控加工中心的加工程序,包括刀具补偿、速度和进给控制等。
7.仿真和优化:在加工之前,可以使用数控软件进行仿真和优化,检查程序中的错误和潜在问题,并进行必要的修正和优化。
第1页/共3页锲而不舍,金石可镂。
8.上传程序到数控加工中心:将编写好的加工程序上传到数控加工中心,并进行机床的调试和预热工作。
9.加工:进行数控加工中心的加工操作,通过控制系统的指令,实现切削、进给和速度等操作。
10.检验和修正:在加工完成后,对加工件进行检验,检查尺寸和表面质量是否满足工艺要求,如果有问题,及时修正。
在进行数控加工中心编程时,需要注意以下几个方面的问题:1.编程语言:数控加工中心编程常用的语言有G代码和M代码,需要熟悉这两种语言的编写规范和功能。
2.刀具半径补偿:根据不同的刀具,需要进行相应的刀具半径补偿,以保证加工尺寸的准确性。
3.切削参数:不同的工件材料和形状,需要调整不同的切削参数,如切削速度、进给速度和切削深度等。
第七章数控车床自动编程
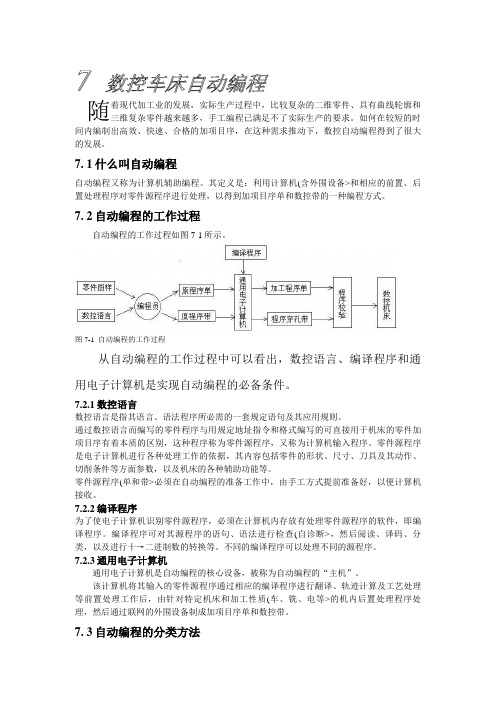
着现代加工业的发展,实际生产过程中,比较复杂的二维零件、具有曲线轮廓和三维复杂零件越来越多,手工编程已满足不了实际生产的要求。
如何在较短的时间内编制出高效、快速、合格的加项目序,在这种需求推动下,数控自动编程得到了很大的发展。
7. 1什么叫自动编程自动编程又称为计算机辅助编程。
其定义是:利用计算机(含外围设备>和相应的前置、后置处理程序对零件源程序进行处理,以得到加项目序单和数控带的一种编程方式。
7. 2自动编程的工作过程自动编程的工作过程如图7-1所示。
图7-1 自动编程的工作过程从自动编程的工作过程中可以看出,数控语言、编译程序和通用电子计算机是实现自动编程的必备条件。
7.2.1数控语言数控语言是指其语言、语法程序所必需的一套规定语句及其应用规则。
通过数控语言而编写的零件程序与用规定地址指令和格式编写的可直接用于机床的零件加项目序有着本质的区别,这种程序称为零件源程序,又称为计算机输入程序。
零件源程序是电子计算机进行各种处理工作的依据,其内容包括零件的形状、尺寸、刀具及其动作、切削条件等方面参数,以及机床的各种辅助功能等。
零件源程序(单和带>必须在自动编程的准备工作中,由手工方式提前准备好,以便计算机接收。
7.2.2编译程序为了使电子计算机识别零件源程序,必须在计算机内存放有处理零件源程序的软件,即编译程序。
编译程序可对其源程序的语句、语法进行检查(自诊断>,然后阅读、译码、分类,以及进行十→二进制数的转换等。
不同的编译程序可以处理不同的源程序。
7.2.3通用电子计算机通用电子计算机是自动编程的核心设备,被称为自动编程的“主机”。
该计算机将其输入的零件源程序通过相应的编译程序进行翻译、轨迹计算及工艺处理等前置处理工作后,由针对特定机床和加工性质(车、铣、电等>的机内后置处理程序处理,然后通过联网的外围设备制成加项目序单和数控带。
7. 3自动编程的分类方法随自动编程一般可按所用设备(编程系统>、插补类型和编程语言等进行分类,目前多按所用设备(除数控机床已具备其直接编程功能外>分类。
数控机床编程技术习题答案
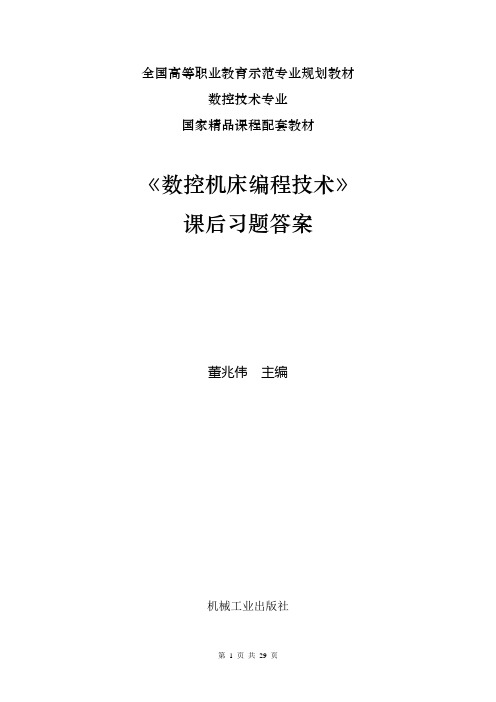
全国高等职业教育示范专业规划教材数控技术专业国家精品课程配套教材《数控机床编程技术》课后习题答案董兆伟主编机械工业出版社第1章数控机床编程基础1.数控加工的过程如何?首先对零件图纸进行工艺性分析,根据零件的形状、尺寸和技术要求等,确定加工方案。
编制数控加工程序,输入到数控机床的数控装置中,数控装置对程序进行译码、运算和逻辑处理后,以脉冲的形式对伺服机构和辅助装置发出各种动作指令,伺服机构将来自数控装置的脉冲指令进行放大并转换成机床移动部件的运动,使刀具与工件及其他辅助装置严格地按照加工程序规定的顺序、轨迹和参数有条不紊地工作,从而加工出零件。
2.数控机床是由哪几个部分组成的?各部分的作用是什么?数控机床是典型的机电一体化产品,主要由程序载体、输入/输出装置、数控装置、伺服系统、反馈装置和机床本体等几部分组成。
⑴程序载体人和数控机床联系的媒介物(也称程序介质、输入介质、信息载体)控制介质可以是穿孔带,也可以是穿孔卡、磁带、磁盘或其他可以储存代码的载体,有些直接集成在CAD/CAM 中。
⑵输入输出装置输入输出装置是机床与外部设备的接口,主要有纸带阅读机、软盘驱动器、RS232C串行通信口、MDI方式等。
⑶数控装置数控装置是数控机床的中枢,在普通数控机床中一般由输入装置、存储器、控制器、运算器和输出装置组成。
数控装置接收输入介质的信息,并将其代码加以识别、储存、运算,输出相应的指令脉冲以驱动伺服系统,进而控制机床动作。
⑷伺服系统其作用是把来自数控装置的脉冲信号转换成机床移动部件的运动,包括信号放大和驱动元件。
其性能好坏直接决定加工精度、表面质量和生产率。
⑸检测反馈系统其作用是对机床的实际运动速度、方向、位移量以及加工状态进行检测,将测量结果转化为电信号反馈给数控装置,通过比较,计算实际位置与指令位置之间的偏差,并发出纠正误差指令。
⑹机床本体机床本体是数控机床的主体,由机床的基础大件(如床身、底座)和各运动部件(如工作台、床鞍、主轴等)所组成。
数控铣削加工中心编程

加工中心是一种工艺范围较广的数控加工机床,能实现 三轴或三轴以上的联动控制,进行铣削(平面、轮廓、 三维复杂型面)、镗削、钻削和螺纹加工。加工中心特 别适合于箱体类零件和孔系的加工。加工工艺范围如图 所示。
第7章 数控铣削(加工中心)编程
铣削加工
钻 削 加 工
螺纹加工
G54;
定义坐标
G00X155.0Y40.0S300; a X、Y轴移动到下刀点上方,设置转速
G43H01Z50.0M03; b 刀具长度补偿,Z轴下移到安全高度,主轴正转
G01Z0F600.0;
c Z轴以较大进给量切削到Z0
X-155.0F200.0;
d
G00Y-40.0;
e
G01X155.0;
f
第7章 数控铣削(加工中心)编程
镗 削 加 工
加工中心适合单件、中小批量的生产,加工对象主要是形状复杂、工序较 多、精度要求高,一般机床难以加工或需使用多种类型的通用机床、刀具 和夹具,经多次装夹和调整才能完成加工的零件。
第7章 数控铣削(加工中心)编程
二、数控铣床(加工中心)的编程特点
1.数控铣床(加工中心)可用绝对值编程或增量值 (相对坐标)编程,分别用G90/G91指定。
第7章 数控铣削(加工中心)编程
2.M功能
M06,M98,M99 在同一程序段中若有两个M代码出现时,虽其动作不相 冲突,但以排列在最后面的代码有效,前面M代码被忽 略而不执行。 注:M代码分为前指令码和后指令码,前指令码和同一 程序段中的移动指令同时执行,后指令码在同段的移动 指令完后才执行。
第7章 数控铣削(加工中心)编程
第7章 数控铣削(加工中心)编程
数控铣削加工工艺与编程实例

第三章
数控铣床与加工中心编程与操作
3)钻各光孔、螺纹孔的中心孔。φ12H8mm孔精度等级 IT7,表面粗糙度Ra值为0.8μm,为保证垂直度,防止钻 偏,按钻中心孔→钻孔→扩孔→铰孔加工方案。
第三章
数控铣床与加工中心编程与操作
4)钻、扩、锪、铰φ12H8mm光孔和φ16mm的台阶孔; φ16mm孔在φ12mm孔基础上锪至要求尺寸即可。
第三章
数控铣床与加工中心编程与操作
3.6 典型零件的编程与操作
3.6.1 平面外轮廓零件的编程与操作
平面外轮廓零件如图3-99所示。 已知毛坯尺寸为 62mm×62mm×21mm的长方 料,材料为45钢,按单件生产 安排其数控加工工艺,试编写 出凸台外轮廓加工程序并利用 数控铣床加工出该零件。
第三章
第三章
数控铣床与加工中心编程与操作
2.编制参考程序 1)认真阅读零件图,确定工件坐标系。根据工件坐标系 建立原则,X、Y向加工原点选在φ60H7mm孔的中心, Z向加工原点选在B面(不是毛坯表面)。工件加工原点 与设计基准重合,有利于编程计算的方便,且易保证零 件的加工精度。Z向对刀基准面选择底面A,与工件的定 位基准重合,X、Y向对刀基准面可选择φ60H7mm毛坯 孔表面或四个侧面。 2)计算各基点(节点)坐标值。如图3-112所示各圆的 圆心坐标值见表3-32。
第三章
4.评分标准
数控铣床与加工中心编程与操作
第三章
数控铣床与加工中心编程与操作
1.确定加工工艺 (1)加工工艺分析 按长径比的大小,孔可分为深孔和浅孔两类。 (2)加工过程 确定加工顺序时,按照先粗后精、先面后孔的原则,其 加工顺序为: 1)编程加工前,应首先钻孔前校平工件、用中心钻钻 6×φ8mm的中心孔; 2)同φ10mm铣刀铣削型腔; 3)用φ8mm钻头钻6×φ8mm的通孔,加工路线: L→M→N→I→J→K;
数控铣床的程序编程
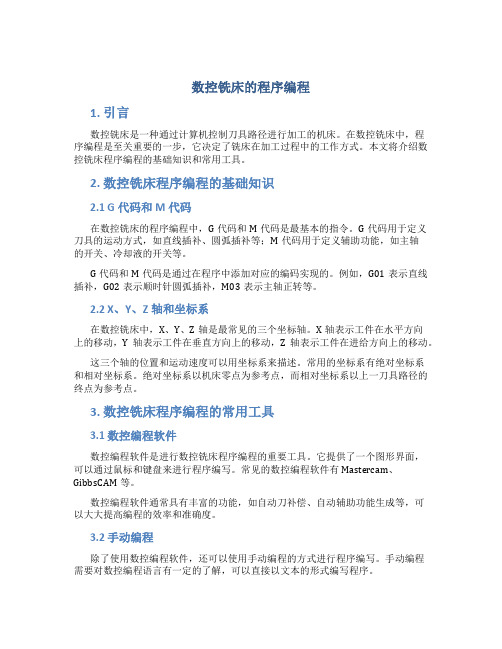
数控铣床的程序编程1. 引言数控铣床是一种通过计算机控制刀具路径进行加工的机床。
在数控铣床中,程序编程是至关重要的一步,它决定了铣床在加工过程中的工作方式。
本文将介绍数控铣床程序编程的基础知识和常用工具。
2. 数控铣床程序编程的基础知识2.1 G代码和M代码在数控铣床的程序编程中,G代码和M代码是最基本的指令。
G代码用于定义刀具的运动方式,如直线插补、圆弧插补等;M代码用于定义辅助功能,如主轴的开关、冷却液的开关等。
G代码和M代码是通过在程序中添加对应的编码实现的。
例如,G01表示直线插补,G02表示顺时针圆弧插补,M03表示主轴正转等。
2.2 X、Y、Z轴和坐标系在数控铣床中,X、Y、Z轴是最常见的三个坐标轴。
X轴表示工件在水平方向上的移动,Y轴表示工件在垂直方向上的移动,Z轴表示工件在进给方向上的移动。
这三个轴的位置和运动速度可以用坐标系来描述。
常用的坐标系有绝对坐标系和相对坐标系。
绝对坐标系以机床零点为参考点,而相对坐标系以上一刀具路径的终点为参考点。
3. 数控铣床程序编程的常用工具3.1 数控编程软件数控编程软件是进行数控铣床程序编程的重要工具。
它提供了一个图形界面,可以通过鼠标和键盘来进行程序编写。
常见的数控编程软件有Mastercam、GibbsCAM等。
数控编程软件通常具有丰富的功能,如自动刀补偿、自动辅助功能生成等,可以大大提高编程的效率和准确度。
3.2 手动编程除了使用数控编程软件,还可以使用手动编程的方式进行程序编写。
手动编程需要对数控编程语言有一定的了解,可以直接以文本的形式编写程序。
手动编程的优点是灵活性高,可以根据实际需求进行自由组合和调整。
但是对于初学者来说,手动编程的学习曲线较陡,需要一定的时间和经验积累。
4. 数控铣床程序编程的步骤4.1 确定加工工序在进行数控铣床程序编程之前,首先需要确定加工的工序。
例如,确定需要进行的切削和非切削操作,以及加工顺序等。
4.2 设计刀具路径在确定了加工工序之后,需要设计刀具路径。
数控铣床加工中心编程与操作讲义(PPT 34张)
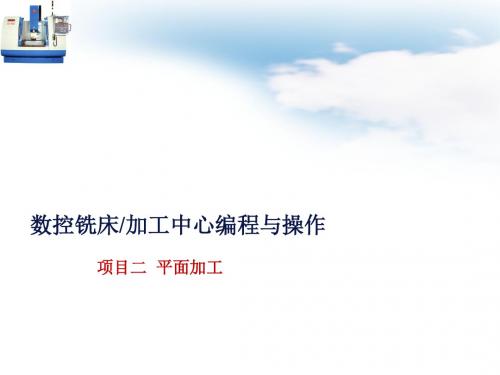
数控铣床/加工中心常用刀具
【知识准备】
(二)数控铣床/加工中心加工平面常用刀具
整体式面铣刀
【知识准备】
(二)数控铣床/加工中心加工平面常用刀具
硬质合金整体焊接式面铣刀
【知识准备】
(二)数控铣床/加工中心加工平面常用刀具
硬质合金可转位式面铣刀
1-刀垫 2-轴向支撑块 3-可转位刀片
【知识准备】
三、任务实施
(一)工艺分析 (二)编写加工程序 (三)数控加工
1.安装刀具与装夹工 件 2.数控程序的输入与 校验 3.数控自动运行操作 (1)程序校验 (2)自动运行操作过 程
【任务实施】
1)在系统控制面板下,按下“自动加工F1” 按键,进入程序运行子菜单;
2)在程序运行子菜单下,可以自动运行零件程序。
【技能目标】
1
熟悉平面铣削工艺特点
2
学会一般平面铣削工艺设计编程
3
具有加工平面的实践能力
二、知识准备
(一)数控铣床/加工中心用铣平面夹具
(a)
(b)
(c)
(d)
a) 螺旋夹紧式通用平口钳 b)液压式正弦规平口钳 b) c) 气动式精密平口钳 d) 液式压精密平口钳
【知识准备】
(二)数控铣床/加工中心加工平面常用刀具
(三)平面铣削工艺
周边铣削
【知识准备】
(三)平面铣削工艺
端面铣削
【知识准备】
(三)平面铣削工艺
水平面加工
【知识准备】
(三)平面铣削工艺
50 10 φ10
10 40 7
67
行切法铣削平面
2
【知识准备】
(四)数控编程规则
1.小数点编程 2.米、英制编程 G21/G20 3.平面选择指令 G17/G18/G19 4.绝对值/增量值编程 G90/G91 (1)绝值编程G90 (2)增量值编程G91
数控铣削编程基础知识
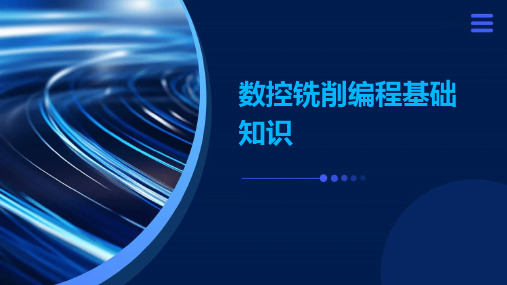
为了提高加工效率和加工质量,可以采用分层铣削的方式,逐 步去除材料,同时需要合理规划刀具路径,避免过切和残留。
实例三:固定轴曲面轮廓铣削编程
固定轴曲面轮廓铣削编程用于加工曲面 零件,可以通过控制刀轴的角度和位置 ,实现复杂曲面的加工。
在编程过程中,需要定义曲面的几何形状和 加工参数,如切削深度、刀轴角度、进给速 度等。
曲面铣削编程需要考虑到曲面的曲 率变化和刀具的半径补偿,以避免 过切和残留,同时需要合理规划刀 具路径,提高加工效率和加工质量 。
05
CATALOGUE
数控铣削编程的优化与提高
提高编程效率的方法
熟练掌握编程语言
熟悉G代码和M代码,掌握常用指令和格式 ,减少编程错误和调试时间。
模块化编程
将常用的程序段编写成模块,通过主程序调 用,减少重复编写工作。
理解不同材料对切削速度、进给速度和切削深 度的要求。
材料热处理
了解材料热处理对切削加工的影响,如硬度、韧性等。
03
CATALOGUE
数控铣削编程的工艺流程
零件的工艺分析
01
零件图样分析
对零件图样进行详细解读,了解 零件的形状、尺寸、精度等要求 。
02
材料特性分析
03
加工工艺性分析
了解零件所使用的材料特性,如 硬度、韧性等,以选择合适的刀 具和加工参数。
优化程序结构
合理安排程序流程,减少不必要的计算和重 复操作,提高程序执行效率。
利用高级功能
利用数控系统的高级功能,如自动编程、图 形编程等,简化编程过程,提高效率。
优化刀具路径的策略
合理选择刀具
根据加工需求选择合适的刀具,包括 刀具材料、刀具几何参数等,以提高 加工效率和刀具寿命。
第7章数控铣削编程与加工应用实例

这种情况下,若用同一把刀进行挖槽加工,则要求刀具在轮 廓边界1上连续切削时,使用一次刀具半径补偿;当刀具在轮廓边界2 上连续切削时,要撤消前次刀具半径补偿,重新建立新的刀具半径补 偿值,粗加工后,根据实测及各自公差的要求对刀补值作不同的修改, 调整后再进行精加工。
上一页 下一页 返回
7.2 挖槽加工实例
4)铣削图7-4(c)所示的凸台轮廓时,亦可看作挖槽加工的特例。 但此时不能用图纸所示的外轮廓作为加工边界,因为将这轮廓作为边 界时,角上的部分材料可能铣不掉,见图7-9(a)所示,1、2、3、4分别 为4个角残留的材料。此时可改为以边界2作为挖槽加工边界,4个角上 就不会留下残余材料。见图7-9(b)所示。
铣削工件外轮廓,通常采用高速钢或硬质合金的立铣刀,下刀点 选择在工件实体外,并使切入点位置和方向尽可能沿工件轮廓切向延 长线方向。刀具切入和切出时要注意避让夹具,并要避免碰到工件上 不该切削的部位。切出工件时仍要尽可能沿工件轮廓切向延长线方向 切出工件,以利于刀具受力平稳同时尽可能保证工件轮廓过度处无明 显接痕。
2)选择加工机床:用立式三坐标数控铣床较为合适 3)加工工序与工步的划分及走刀路线的确定 根据图样分析,凸台加工时材料的切削量不大,而且材料的切削 性能较好,选择φ20的圆柱形直柄立铣刀,材料为高速钢(HSS),沿 轮廓铣削一周即可去处余量,考虑实习用机床主轴刚性不够,深度 6mm,采用分层加工每次切深3mm。
(1)图7-3中基点A的坐标计算
在Rt△O1CD中,
全套电子课件:数控铣床加工中心编程与操作(fanuc系统)
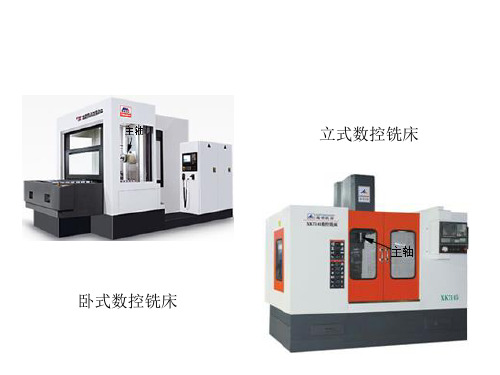
坐标轴的移动指令
圆弧的半径;固定循环的参数 圆心坐标;固定循环的参数
指定进给速度 指定主轴转速 指定刀具号(T0~T99) 机床辅助动作(M0~M99) 指定刀具补偿号(00~99) 指定暂停时间,单位为s 指定子程序号 子程序的重复次数,固定循环的重复次数 固定循环参数
(2)地址字
2.工件坐标系原点的选择要尽量满足编程简单、 尺寸换算少、引起的加工误差小等条件。
3.尽量选在精度较高的工件表面上,以提高被加 工零件的加工精度。
4.将工件坐标系原点选择在零件的尺寸基准上, 这样便于坐标值的计算,减少手工计算量。
5.Z轴工件坐标系原点通常选在工件的上表面。 6.X轴、Y轴工件坐标系原点设在与零件的设计基
(1) 程序号 FANUC系统用地址符O及后续的四位数字表示程序
号,取值范围为O0000~O9999。 在书写程序号时应注意:
1)程序号必须写在程序的最前面,并单独占一 行。
2)O0000和O8000以后的程序号,在系统中有特 殊的用途,因此,应尽量避免在普通数控加工程序 中使用。
3)数字前的零可以省略不写。如O0001可以省略 为O1。
立式数控铣床 卧式数控铣床
(2)数控铣床的加工对象 数控铣床可以对零件的二维轮廓或三维轮廓
进行加工,如平面轮廓、斜面轮廓、曲面轮廓, 还可以对孔类零件进行加工,如钻孔、扩孔、锪 孔、铰孔、镗孔和攻螺纹等。
数控铣床加工零件
3.加工中心
加工中心是从数控铣床发展而来的,与数控 铣床的最大区别在于加工中心具有自动交换加工 刀具的能力,通过在刀库中安装不同用途的刀具, 可以在一次装夹中通过自动换刀装置改变主轴上 的加工刀具,实现多种加工功能。
数控铣削简单编程(★)

数控铣削简单编程(★)第一篇:数控铣削简单编程数控铣削简单编程长轴80,短轴50的椭圆 O0001#50=0#51=40#52=25#53=6.28G54G01X0Y0Z5M03S1200M08Z-3WHILE#50LE#53 #55=#51*COS[#50] #56=#52*SIN[#50]G42G01X[#55]Y[#56]F80D01 #50=#50+0.05ENDWG40G00Z30X100Y60M05M08M30第二篇:数控铣削电子教案模块一基础部分课题一数控铣床概述铣床是用铣刀对工件进行铣削加工的机床。
铣床除能铣削平面、沟槽、轮齿、螺纹和花键轴外,还能加工比较复杂的型面,效率较刨床高,在机械制造和修理部门得到广泛应用。
数控铣床与加工中心的主要区别:数控铣床没有刀库和自动换刀功能。
加工中心就是带有刀库且具有自动换刀功能的数控铣床。
任务一数控铣床的分类1.按数控系统的功能可分为以下几类(1)经济型数控铣床经济型数控铣床一般是在普通立式铣床或卧式铣床的基础上改造而来的,采用经济型数控系统,成本低,机床功能较少,主轴转速和进给速度不高,主要用于精度要求不高的简单平面或曲面零件的加工。
(2)高速铣削数控铣床一般把主轴转速在8000~40000r/min的数控铣床称为高速铣削数控铣床,其进给速度可达10~30m/min。
这种数控铣床采用全新的机床结构、功能部件和功能强大的数控系统,并配以加工性能优越的刀具系统,可对大面积的曲面进行高效率、高质量的加工。
(3)全功能数控铣床全功能数控铣床一般采用半闭环或闭环控制,控制系统功能较强,数控系统功能丰富,一般可实现四坐标或以上的联动,加工适应性强,应用广泛。
2.按主轴布置形式可分为以下几类(1)立式数控铣床立式数控铣床的主轴轴线与工作台面垂直,是数控铣床中最常见的一种布局形式。
立式数控铣床一般为三左边(X、Y、Z)联动,其各坐标的控制方式主要有以下两种:①工作台纵、横向移动并升降,主轴只完成主运动。
数控铣削加工编程

数控铣削加工编程
数控铣削加工编程,简称CNC编程,在现代制造业中已成为一项重要的技术。
CNC编程是一种利用计算机来控制数控铣床执行加工操作的技术。
因其高效、精度高、可重复性强等优点,被广泛应用于制造业的各个领域,例如航空、汽车、船舶、电子等。
CNC编程需要掌握的知识点包括机床操作、数学知识、材料学、CAD设计和计算机编程等。
CNC编程的程序是由一系列指令组成的,它们控制着数控铣床上加工工具的动作。
这些指令包括插补指令、运动控制指令、曲线运动指令和其他的一些控制指令等。
CNC编程需要掌握的核心技术包括:数控编程语言掌握、数学运算及几何知识、机床特性及工艺技术掌握、CAD/CAM
软件应用及知识体系的建立以及数控加工的实际操作和调整技能等,需要对机床工作原理和实际操作有充分的理解,具备较强数学思维能力和分析能力,能够快速准确地进行计算和分析。
在进行CNC编程时,需要先制定工作计划,明确加工零件的要求和工作参数,编写程序,然后将程序导入数控铣床的控制系统中。
在加工过程中,需要根据实际情况进行调整和调试,确保加工质量符合要求。
CNC编程具有很多优点,例如提高了加工效率,降低了人为干扰的影响,提高了加工精度和稳定性,减少了人工操作的劳动强度和工作时间等。
同时,由于CNC编程具有高度一致性和可重复性,因此可以缩短制造周期,提升产能。
总之,CNC编程是现代制造业中必不可少的一项技术,它在工业制造、航空航天、汽车制造、电子制造等领域中得到了广泛的应用。
掌握CNC编程技术,对于从事这些行业工作的人员来说,是一项必要的技能。
数控铣(加工中心)编程与操作

第一章概述数控铣床是在一般铣床的基础上发展起来的一种自动加工设备,两者的加工工艺基本相同,结构也有些相似。
数控铣床有分为不带刀库和带刀库两大类。
其中带刀库的数控铣床又称为加工中心。
数控加工中心是由机械设备与数控系统组成的适用于加工复杂零件的高效率自动化机床。
数控加工中心是目前世界上产量最高、应用最广泛的数控机床之一。
它的综合加工能力较强,工件一次装夹后能完成较多的加工内容,加工精度较高,就中等加工难度的批量工件,其效率是普通设备的5~10倍,特别是它能完成许多普通设备不能完成的加工,对形状较复杂,精度要求高的单件加工或中小批量多品种生产更为适用。
它把铣削、镗削、钻削、攻螺纹和切削螺纹等功能集中在一台设备上,使其具有多种工艺手段。
加工中心按照主轴加工时的空间位置分类有:卧式和立式加工中心。
按工艺用途分类有:镗铣加工中心,复合加工中心。
按功能特殊分类有:单工作台、双工作台和多工作台加工中心。
单轴、双轴、三轴及可换主轴箱的加工中心等。
第一节加工中心的组成及分类—、加工中心的组成从主体上看,加工中心主要由以下几大部分组成:1.基础部件基础部件是加工中心的基础结构,它主要由床身、工作台、立柱三大部分组成。
这三部分不仅要承受加工中心的静载荷,还要承受切削加工时产生的动载荷。
所以要求加工中心的基础部件,必须有足够的刚度,通常这三大部件都是铸造而成。
2.主轴部件主轴部件由主轴箱、主轴电动机、主轴和主轴轴承等零部件组成。
主轴是加工中心切削加工的功率输出部件,它的起动、停止、变速、变向等动作均由数控系统控制。
主轴的旋转精度和定位准确性,是影响加工中心加工精度的重要因素。
3.数控系统加工中心的数控系统由CNC装置、可编程序控制器、伺服驱动系统以及面板操作系统组成,它是执行顺序控制动作和加工过程的控制中心。
CNC装置是一种位置控制系统,其控制过程是根据输人的信息进行数据处理、插补运算,获得理想的运动轨迹信息,然后输出到执行部件,加工出所需要的工件。
数控加工仿真与实训第1篇-第7章数控铣床和加工中心编程要点及指令

7.1.3 机床参考点
机床参考点由机床行程限位开关和基 准脉冲来确定,它与机床坐标系原点有着 准确的位置关系。
7.2 数控铣削加工编程特点
第一篇 基础操作
第7章 数控铣床和加工中心编程要点及指令
7.1
7.2 7.3
数控铣床和加工中心的坐标系
数控铣削加工编程特点 数控系统的功能
7.1 数控铣床和加工中心的坐标系
7.1.1 机床坐标系
数控铣床和加工中心的机床原点一般 取在X、Y、Z坐标轴的正方向极限位置上, 如图1-7-1所示。
7.1.2 工件坐标系
7.3.2 辅 助 功 能
常用的M指令功能如表1-7-2所示。
7.3.3 其他功能指令
1.进给功能(F功能)
(1)切削进给速度 (2)快速进给
2.主轴功能(S功能) 3.刀具功能(T功能) 4.刀具补偿功能(H功能)
1.工件坐标系的确定及程序原点 的设置 2.安全高度的确定
在安全高度位置,刀具中心(或刀尖) 所在的平面也称为安全面,如图1-7-2所示。
3.进刀、退刀方式的确定
对于二维轮廓的加工,一般要求从侧 向进刀或沿切线方向进刀,尽量避免垂直 进刀,如图1-7-3所示。
4.刀具半径补偿的建立
在建立刀具半径补偿定好的 切入点和进刀方式协调,保证刀具的半径 补偿,如图1-7-4所示。
5.刀具半径的确定
对于铣削加工,精加工刀具半径选择 的主要依据是零件加工轮廓和所加工轮廓 凹处的最小曲率半径或圆弧半径,刀具半 径应小于该最小曲率半径值,如图1-7-5所 示。
数控铣削编程
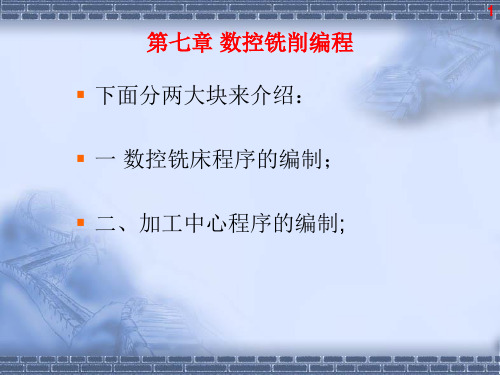
10
5 数控系统和铣削加工的主要功能 1点位控制功能
此功能可以实现对相互位置精度要求很高的孔系加工; (2)连续轮廓控制功能
此功能可以实现直线、圆弧的插补功能及非圆曲线的加工。 (3)刀具半径补偿功能
此功能可以根据零件图样的标注尺寸来编程;而不必考虑所用刀具的 实际半径尺寸,从而减少编程时的复杂数值计算。 (4)刀具长度补偿功能
该功能可将编好的加工程序在加工平面内旋转任意角 度来执行;
(7)子程序调用功能
有些零件需要在不同的位置上重复加工同样的轮廓形 状;将这一轮廓形状的加工程序作为子程序,在需要的位 置上重复调用,就可以完成对该零件的加工。
(8)宏程序功能
该功能可用一个总指令代表实现某一功能的一系列指 令,并能对变量进行运算,使程序更具灵活性和方便性。
27
2 安全高度的确定 对于铣削加工中心加工零件时;开始段和结束段采用快速移动定
位,节省空刀时间; 起刀点和退刀点必须离开零件表面一定的安全 高度,避免撞刀。
通常在安全高度之上完成刀具长度补偿。安全高度不能设得太 小,也不能设得太大。如安全高度定为50mm。 3、进刀/退刀方式的确定
▪ 2侧固式刀柄 ▪ 它采用侧向夹紧;适用于切削力大的
加工,但一种尺寸的刀具需对应配备 一种刀柄,规格较多;
24
莫式锥度刀柄
侧固式刀柄
▪ 3ER弹簧夹头刀柄 ▪ 它采用ER型卡簧;夹紧力不大,
适用于夹持直径在16mm以下的 铣刀;
▪ (4)钻夹头式刀柄 ▪ 它有整体式和分离式两种,
用于装夹直径在13mm以下的中 心钻 直柄麻花钻等。
键槽铣刀主要用于铣槽面 键槽等;
三面刃铣刀
立铣刀
键槽铣刀
加工沟槽的铣刀
数控铣床及加工中心编程课件

为制造业提供更高效、更精准的加工设备。
数控铣床及加工中心的应用前景
航空航天领域
数控铣床及加工中心在航空航天 领域的应用越来越广泛,特别是 在加工复杂曲面、薄壁零件等方
面具有显著优势。
汽车制造领域
数控铣床及加工中心在汽车制造 领域的应用也越来越广泛,特别 是在加工铝合金等轻质材料方面
具有显著优势。
能源领域
轮廓铣削的编程实例
总结词
轮廓铣削是一种用于加工工件轮廓的铣削方式,常用于加工 各种形状的零件表面。
详细描述
轮廓铣削的编程实例包括选择合适的刀具、确定切削参数、 编写程序等步骤。在程序中,需要定义刀具号、刀具补偿号 、主轴转速、进给速度等参数,同时根据工件材料和加工要 求选择合适的切削参数。
型腔铣削的编程实例
特点
数控铣床及加工中心具有高精度 、高效率、高自动化等优点,但 同时存在设备昂贵、操作复杂等 缺点。
02
数控铣床及加工中心编 程基础
数控编程的基本概念
数控编程的定义
数控编程是一种使用数字和字母控制机床的方法,用于生产具有特 定形状和尺寸的零件。
数控编程的重要性
数控编程使得机床能够准确地按照预设的指令进行操作,从而生产 出符合要求的零件。
。
3. 宏编程:使用宏命令和变 量,根据加工需求编写程序。
数控编程的指令系统
G代码和M代码
数控编程中使用最广泛的两种指令系统,G代码用于控制机床的移动轨迹,M 代码用于控制机床的辅助动作。
其他指令系统
除了G代码和M代码外,还有其他一些指令系统,如ISO标准、FANUC等,这些 指令系统各有特点,根据机床型号和控制系统选择合适的指令系统。
加工能力
包括最大加工尺寸 、最大加工重量等 。
数控铣(加工中心)编程与加工 教程

数控铣(加工中心)编程与加工教程XYZCNC附录一 HNC-21M编程指令附录二 HNC-21T编程指令附录三 GSK928TE编程指令附录四线切割3B编程指令附录五数控车工职业技能鉴定(中级)考核大纲附录六数控铣工职业技能鉴定(中级)考核大纲项目一数控铣床(加工中心)仿真加工一、【实训技能目标】? 掌握宇龙仿真软件的启动与基本设置? 会用宇龙仿真软件进行数控加工二、【准备工作】1、图纸图3.1.02、如图3.1.0所示,毛坯为80×80×20mm,试对其进行仿真加工;加工程序如下(HNC-21M数控系统)%3130G54 G00 X0 Y0 Z50M03 S600G00 X-25 Y-25G00 Z5G01 Z-3 F80G01 Y25 F100G01 X25G01 Y-25G01 X-25G00 Z50G00 X0 Y0M05M30三、【拓展延伸】1、仿真软件介绍宇龙数控仿真软件有若干版本,本文是以宇龙3.8版为例进行演示说明的,此外还有4.0版。
能够完成数控仿真的软件除了宇龙仿真之外,还有德国“MTS”数控编程仿真系统、宇航仿真、斯沃仿真以及各大数控厂家自己开发的一些仿真软件,也能够完成对特定系统数控机床的仿真加工。
2、思考与应用本文数控仿真对刀完成后,工件坐标原点建立在毛坯件的中心,若是把工件坐标系原点建立在毛坯左下角,应该如何对刀?项目二 X、Y、Z形状的加工一、【实训技能目标】? 会使用数控仿真软件加工零件模型? 会进行常用对刀操作? 会编写数控加工工艺卡片二、【准备工作】1、准备内容表3.2.0刀具φ6?二刃鍵槽铣刀 1把量具 0~150mm游标卡尺 1把材料 PVC板料110×50×20mm 1块 2、关键指令G54~G59:坐标系选择指令G00指令——快速定位指令G01指令——直线插补指令三、【零件图样】1、如图3.2.0所示,毛坯尺寸为110×50×20mm,依照铣刀中心轨迹编写一个程序,字深2?,试进行仿真加工。
- 1、下载文档前请自行甄别文档内容的完整性,平台不提供额外的编辑、内容补充、找答案等附加服务。
- 2、"仅部分预览"的文档,不可在线预览部分如存在完整性等问题,可反馈申请退款(可完整预览的文档不适用该条件!)。
- 3、如文档侵犯您的权益,请联系客服反馈,我们会尽快为您处理(人工客服工作时间:9:00-18:30)。
第7章 数控铣削<加工中心)编程7.1 数控铣削(加工中心>编程概述加工中心(Machining Center>是具有刀库,能够自动换刀的镗铣类机床。
加工中心除自动换刀之外与数控铣床基本一致。
一、数控铣床<加工中心)的加工特点加工中心是一种工艺范围较广的数控加工机床,能实现三轴或三轴以上的联动控制,进行铣削<平面、轮廓、三维复杂型面)、镗削、钻削和螺纹加工。
加工中心特别适合于箱体类零件和孔系的加工。
加工工艺范围如图所示。
图1 铣削加工 图2 钻削加工 图3 螺纹加工图4 镗削加工加工中心特别适合单件、中小批量的生产,其加工对象主要是形状复杂、、工序较多、精度要求高,一般机床难以加工或需使用多种类型的通用机床、刀具和夹具,经多次装夹和调整才能完成加工的零件。
二、数控铣床<加工中心)的编程特点1.数控铣床<加工中心)可用绝对值编程或增量值<相对坐标)编程,分别用G90/G91指定。
2.手工编程只能用于简单编程,对复杂的编程广泛采用CAM自动编程。
三、数控铣床<加工中心)的选择加工中心分立式、卧式和复合;三轴或多轴。
最常见的是三轴立式加工中心。
立式加工中心的主轴垂直于工作台,主要适用于加工板材类、壳体类零件,形状复杂的平面或立体零件、以及模具的内、外型腔等,应用范围广泛。
卧式加工中心的主轴轴线与工作台台面平行,它的工作台大多为由伺服电动机控制的数控回转台,在工件一次装夹中,通过工作台旋转可实现多个加工面的加工,适用于加工箱体、泵体、壳体等零件加工。
复合加工中心主要是指在一台加工中心上有立、卧两个主轴或主轴可90°改变角度,因而可在工件一次装夹中实现五个面的加工。
四、数控铣床<加工中心)刀具加工中心对刀具的基本要求是:✓良好的切削性能能承受高速切削和强力切削并且性能稳定;✓较高的精度刀具的精度指刀具的形状精度和刀具与装卡装置的位置精度;✓配备完善的工具系统满足多刀连续加工的要求。
加工中心的刀具主要有:立铣刀、面铣刀、球头刀、环形刀<牛鼻刀)、钻头、镗刀等。
面铣刀常用于端铣较大的平面;立铣刀的端刃切削效果差,不能作轴向进给;球头刀常用于精加工曲面,刀具半径需要小于内凹曲面半径。
五、工件坐标原点的选择理论上讲工件坐标原点设置在任何地方都可以,但实际中需要考虑:工件坐标系采用与机床运动坐标系一致的坐标方向;工件坐标系的原点要选择便于测量或对刀,同时要便于编程中坐标值的计算。
工件坐标原点选择原则:<1)工件坐标原点应选在零件图的尺寸基准上,便于坐标值的计算。
<2)对称的零件,工件坐标原点应设在对称中心上,便于对刀。
<3)Z轴零点,一般设在工件最高表面。
<4)对于一般零件,通常设在工件外轮廓的某一角上。
<5)毛坯材料通常把坐标原点设在工件上表面中心处。
六、安全高度的确定对于铣削<加工中心)加工零件时,开始段和结束段采用快速移动定位,节省空刀时间。
起刀点和退刀点必须离开零件表面一定的安全高度,避免撞刀。
如图所示,数控铣削<加工中心)刀具路径的开始段通常设为:①Z坐标不变,X、Y移动到下刀点的正上方,设置转速,刀具转动;②X、Y坐标不变,Z轴向下移动到安全高度,进行刀具长度补偿;③刀具沿Z轴方向切削到一定深度,通常刀具在轮廓外或在工艺孔内下刀,避免切削到材料④沿轮廓的切入段切削进给,进行刀具半径补偿。
通常在安全高度之上完成刀具长度补偿。
安全高度不能设得太小,也不能设得太大。
如安全高度定为50mm。
七、顺铣和逆铣对加工的影响在铣削加工中,采用顺铣还是逆铣方式是影响加工表面粗糙度的重要因素之一。
铣削方式的选择应视零件图样的加工要求,工件材料的性质、特点以及机床、刀具等条件综合考虑。
通常,因为数控机床传动采用滚珠丝杠结构,其进给传动间隙很小,顺铣的工艺性就优于逆铣。
在铣削加工零件轮廓时应尽量采用顺铣加工方式;同时,为了降低表面粗糙度值,提高刀具耐用度,对于铝镁合金、钛合金和耐热合金等材料,尽量采用顺铣加工;但如果零件毛坯为黑色金属锻件或铸件,表皮硬而且余量一般较大,这时采用逆铣较为合理。
如图 a 所示为采用顺铣切削方式精铣外轮廓,图b 所示为采用逆铣切削方式精铣型腔轮廓。
八、进刀/退刀方式的确定加工外轮廓时,立铣刀从安全高度下降到切削高度,应离开工件毛坯边缘一定距离,不能直接下刀切削到工件,以免发生危险。
对于型腔的粗铣加工,立铣刀应从工艺孔进刀,再横向进行型腔加工。
进刀段、退刀段通常沿轮廓的切线方向。
通常在此建立或取消刀具半径补偿,因此,可把此段设为直线或直线加圆弧。
九、数控系统功能常用的数控系统以及常用功能指令的类别及特点在前面已经学习过。
我们只介绍FANUC 0i –M 系统常用G 指令。
与数控车床不同的指令包括:1.G 功能<1)刀补、圆弧平面选择:G17、G18、G19<2)返回参考点:G28X_Y_Z_;式中X_Y_Z_为中间点的坐标值,用于加工中心回参考点结束程序或换刀,可自动取消刀具长度补偿。
<3)刀具半径补偿:G41/G42D_<4)刀具长度补偿:G43/G44Z_Hxx 。
Z 坐标值为刀补后刀位点移动到的坐标值。
相当于G43/G 44 HxxG00 Z_<5)取消刀具长度补偿:G49 或G43/G44H00<6)工件坐标系的设置:G54~G59,通常按约定选用G54。
<7)固定循环:G73、G74、G76、G80~G86 用于孔加工。
<8)绝对坐标/增量坐标指令:G90/G91 都用相同字母X_Y_Z_<9)每分/每转进给:G94/G95<10)固定循环返回起始点/返回R 点:G98/G992.M 功能M06,M98,M99在同一程序段中若有两个M 代码出现时,虽其动作不相冲突,但以排列在最后面的代码有效,前面M 代码被忽略而不执行。
图 a>顺铣 图 b>逆铣注:M代码分为前指令码和后指令码,前指令码和同一程序段中的移动指令同时执行,后指令码在同段的移动指令完后才执行。
十、切削用量的选择进给量和转速各有两个单位。
在数铣<加工中心)编程时常用单位是转速S(r/min>,进给量F(m m/min>。
例7-1使用Φ80mm,6齿的面铣刀,铣削碳钢表面,已知切削速度νc=100m/min。
f z=0.08mm/齿,求主轴转速n及进给量νf。
n=1000νc/πD=[1000×100/(3.14×80>]=400 r/minνf= f z×z×n=(0.08×6×400> =192 mm/min7.2 数控铣<加工中心)的编程要点一、初始状态的设置为了保证程序的运行完全,通常在程序开始时设定初始状态。
G90、G80、G40、G17、G49、G21G90:绝对坐标G80:取消循环G40:取消刀具半径补偿G17:选择刀径补偿和圆(弧>加工平面为XY平面G49:取消刀具长度补偿G21:尺寸单位为公制二、工件坐标系的选定毛坯材料通常把坐标原点设在工件上表面中心处。
用G54~G59定义工件坐标系,通常按约定用G54。
G54为零点偏置法。
与刀具的起始位置无关。
在数控机床上,通过对刀并在数控系统面板上设置工件坐标原点与机床坐标原点的距离。
三、换刀指令加工中心具有自动换刀功能,不同的加工中心,其换刀过程是不完全一样的,通常选刀和换刀可分开进行<我们所用加工中心不是这种情况换刀),选刀动作可与机床的加工同时进行,即利用切削时间进行选刀。
多数加工中心都规定了固定的换刀点位置,各运动部件只有移动到这个位置,才能开始换刀动作。
换刀完毕后需要启动主轴,方可进行后面程序内容的加工。
T01…M06四、刀具长度补偿G43刀具长度正补偿,G44刀具长度负补偿,通常用刀具正补偿G43。
格式:G43/G44Z_HxxZ坐标值为刀补后刀位点移动到的坐标点。
Hxx刀具长度补偿值在数控机床上的填写位置是H后面数值指定的存储单元。
如:G00G43Z50.0H01G43H01G00Z50.0相当于G43/G44HxxG00Z50.0使用G43或G44指令刀长补偿时,只能有Z轴的移动量,若有其他轴向的移动,则会出现报警。
正补偿:将Z坐标尺寸字与H代码中长度补偿的量相加,按其结果进行Z轴运动。
负补偿:将Z坐标尺寸字与H中长度补偿的量相减,按其结果进行Z轴运动。
取消刀具长度补偿:G49或G43/G44H00例7-2在立式数控铣床上按如图所示的走刀路线铣削工件上表面,已知主轴转速为300r/min,进给量为200mm/min。
试编制加项目序(刀具直径φ100>。
参考程序如下:O7001;程序名G90G80G40G49G17G21;初始化相关G功能G54;定义坐标G00X155.0Y40.0S300; aX、Y轴移动到下刀点的正上方,设置转速G43H01Z50.0M03; b刀具长度补偿,Z轴下移到安全高度,主轴正转G01Z0F600.0; c Z轴以较大进给量切削到Z0X-155.0F200.0; dG00Y-40.0; eG01X155.0; fG00Z300.0M05G49;g Z轴上升到换刀点,主轴停转,取消刀长补偿X250.0Y180.0;h 回刀具起始点,工件台移动到适当的位置M30;程序结束五、刀具半径补偿刀径补偿的作用:利用刀具半径补偿功能,可按加工工件轮廓编程,即使刀具在因磨损、重磨或更换后直径发生改变,或者零件的尺寸有加工误差时只需改变半径补偿参数,仍用同一个程序;刀具半径补偿值不一定等于刀具半径值,用同一个程序通过改变刀具半径的刀补量,可以对零件轮廓进行粗、精加工。
如图所示,应用刀具半径补偿指令加工时,刀具的中心始终与工件轮廓相距一个刀具半径距离。
当刀具磨损或刀具重磨后,刀具半径变小,只需在刀具补偿值中输入改变后的刀具半径,而不必修改程序。
在采用同一把半径为R的刀具,并用同一个程序进行粗、精加工时,设精加工余量为△,则粗加工时设置的刀具半径补偿量为R+△,就能在粗加工后留下精加工余量△,精加工时设置的刀具半径补偿量为R。
运动情况见图。
格式:G41/G42D刀具半径左补偿与顺铣相对应,反之,则右补偿与逆铣对应。
刀具半径补偿偏置寄存器号D,其偏置量的大小在操作面板的偏置寄存器中设定。
刀具半径补偿的三个过程:刀具半径补偿在直线段建立;补偿状态下加工零件;在直线段取消刀具半径补偿。
可用如下程序格式:图刀具半径补偿的作用G00/G01 G41/G42 X YD建立补偿程序段…… 轮廓切削程序段……G00/G01 G40 X Y 补偿撤消程序段其中:G41/G42程序段中的X 、Y 值是建立补偿直线段的终点坐标值;G40程序段中的X 、Y 值是撤消补偿直线段的终点坐标;在建立刀具半径补偿以后,不能出现连续两个程序段无选择补偿坐标平面的移动指令,否则数控系统因无法正确计算程序中刀具轨迹交点坐标,可能产生过切现象。