浪费识别与消除共56页文档
如何发现浪费和消除浪费

不稳定的生产过程 生产能力不平衡 缺乏灵活性 易产生废品 按时交货能力差
库存的浪费
• 成品、半成品、零件及物料的存货,是不会产生任 何附加价值的,反而增加了营运的成本。
•库存
•检查 •延迟
•废料
•供应商 •的过失
•改变 •顺序
•生产问题
•文件 •订单处 •决策 •延迟 •理延迟 •缓慢
浪费8、管理的浪费
1. 管理浪费是由于事先管理不到位而造成的问题 2. 科学的管理应该是具有相当的预见性,有合理
2.3材料虽已备齐,但制造通知单或设计图并未送 来,导致等待
•#7-2-2:成本突破—企业生产中的八大浪费
浪费3:停滞(等待)的浪费(2)
3 缺料的浪费
4
设备、工具 故障的浪费
5
安排人员过 多的浪费
3.1是否前工序/工段的能力供应不上? 3.2是否仓库没有物料? 3.3还是仓库有物料,物料员配送不及时? 4.1生产线运转出现了故障吗? 4.2设备、工装夹具出现了故障吗? 4.3是因为没有及时点检而提前发现隐患吗? 4.4是因为没有提前维护而导致出现故障吗? 5.0生产能力是否过剩? 5.1安排人员是否过多? 5.2没有按照标准工位设定表安排人员生产吗?
方向的动作?
5.1每个作业循环的动作顺序不同(没有明显的周期性 )
6.1没有掌握最佳的作业方法,经常出现有时做的好,有 时做的不好的情况?
•#7-2-2:成本突破—企业生产中的八大浪费
浪费7:动作的浪费(2)
7
动作幅度太大的浪 费
8
转身角度太大的浪 费
9
伸臂、踮脚动作的 浪费
10 弯腰动作的浪费
7.1动作从左到右或从上到下的幅度是否过大(脚不移 动,没有转身)?
七大浪费的识别与消除
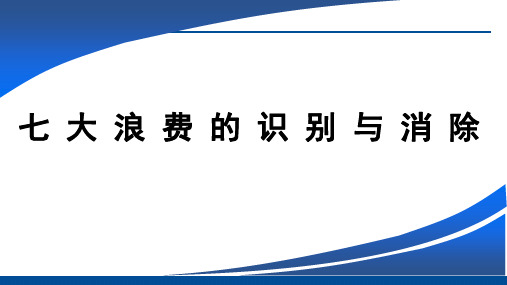
16
11、浪费的识别与消除—库存浪费的消除
消除措施:
➢ 不大批量生产:改善换模方法、缩短换模时间,降低在制品库存。 ➢ 不批量搬运:工序间在制品库存改善:合理调配作业顺序和均衡作业
量,使工序间作业循环时间吻合节拍时间。 ➢ 不大批量:成品与整机库存改善:杜绝延迟发货,对商品制造订单流
8
3、浪费的识别与消除—制造过多浪费的消除
消除措施:
➢ 顾客为中心的弹性生产系统 ➢ 单件流动-一个流生产线 ➢ 看板管理 ➢ 快速换线换模 ➢ 少人化的作业方式 ➢ 均衡化生产
9
4、浪费的识别与消除—等待的浪费
定义:无法保证可卖出的产品做了太多生产比顾客要求多得多的产品或是在顾客要 求之前提前生产。
11
6、浪费的识别与消除—搬运的浪费
定义:搬运的浪费是指在生产过程中出现的必要的堆积、放置、移动及整理。
表现形式:
➢ 物品移动所需空间、时间、人员以及工具占用浪费。 ➢ 增加了搬运的费用,造成成本增加。 ➢ 搬运过程中存在安全隐患。 ➢ 物品在搬运中造成丢失或损坏。 ➢ 增加劳动强度,降低工作效率
19
14、浪费的识别与消除—不良品返修的浪费
定义:指企业内生产过程中没有按照工艺要求及标准生产,达不到顾客要求的产品 造成的浪费。
表现形式:
➢ 人在制造(加工)过程中,没有按照工艺要求和质量 要求生产而产生的不良。
➢ 由于物的不合格(设备、物料、生产线)布局的不合理 性迫使人作出多余的不良。
20
12
7、浪费的识别与消除—搬运浪费的消除
消除措施:
➢ U型设备配置 ➢ 一个流生产方式 ➢ 站立作业 ➢ 避免重新堆积、重新包装
生产过程中的浪费源识别与消除
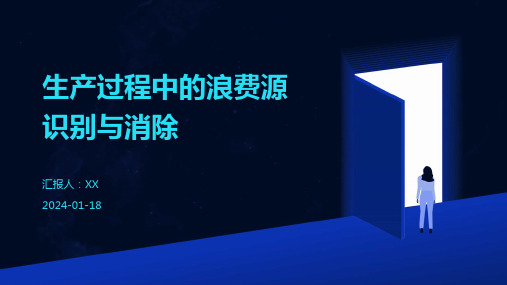
02
识别浪费方法
观察法
现场观察
01
直接在生产现场进行观察,记录生产过程中的各种浪费现象。
工人访谈
02
与生产线上的工人进行交谈,了解他们对生产过程中浪费现象
的看法和意见。
视频监控
03
通过安装摄像头监控生产现场,记录并分析生产过程中的浪费
现象。
调查法
01
问卷调查
向生产线上的工人和管理人员发 放问卷,收集他们对生产过程中 浪费现象的看法和建议。
信息化技术应用
生产计划优化
利用信息化技术,实现生产计划的动态调整 和优化,提高生产计划的准确性和可执行性 。
生产过程监控
通过传感器、物联网等技术手段,实时监控生产过 程,及时发现并处理异常情况。
数据分析与挖掘
运用大数据、人工智能等技术,对生产数据 进行深度分升
加工浪费
过度加工、错误加工等造成的 物料和能源浪费。
浪费对企业影响
成本增加
浪费直接导致企业成本上升, 降低盈利能力。
效率下降
浪费使得生产过程不顺畅,降 低生产效率。
质量问题
过度加工、错误加工等浪费可 能导致产品质量不稳定,影响 客户满意度。
环境压力
能源和物料浪费会给环境带来 负面影响,增加企业环保压力
通过价值流分析、作业研究等方法识别生产过程中的浪费,包括过度生 产、等待、运输、过度加工、库存、动作和不良品等七种浪费。
03
持续改进
精益生产强调持续改进,通过消除浪费、提高生产效率和质量,不断追
求更高的目标。
5S管理法应用
5S定义
5S即整理(Seiri)、整顿(Seiton)、清扫(Seiso)、清洁( Seiketsu)和素养(Shitsuke),是一种现场管理的方法。
浪费的识别与消除
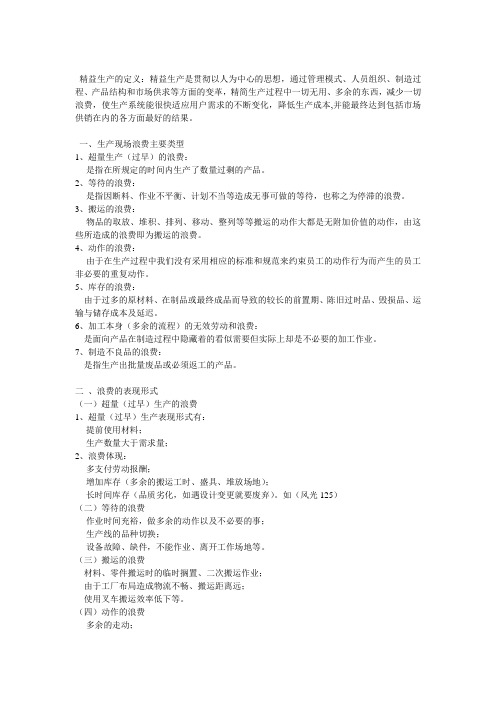
精益生产的定义:精益生产是贯彻以人为中心的思想,通过管理模式、人员组织、制造过程、产品结构和市场供求等方面的变革,精简生产过程中一切无用、多余的东西,减少一切浪费,使生产系统能很快适应用户需求的不断变化,降低生产成本,并能最终达到包括市场供销在内的各方面最好的结果。
一、生产现场浪费主要类型1、超量生产(过早)的浪费:是指在所规定的时间内生产了数量过剩的产品。
2、等待的浪费:是指因断料、作业不平衡、计划不当等造成无事可做的等待,也称之为停滞的浪费。
3、搬运的浪费:物品的取放、堆积、排列、移动、整列等等搬运的动作大都是无附加价值的动作,由这些所造成的浪费即为搬运的浪费。
4、动作的浪费:由于在生产过程中我们没有采用相应的标准和规范来约束员工的动作行为而产生的员工非必要的重复动作。
5、库存的浪费:由于过多的原材料、在制品或最终成品而导致的较长的前置期、陈旧过时品、毁损品、运输与储存成本及延迟。
6、加工本身(多余的流程)的无效劳动和浪费:是面向产品在制造过程中隐藏着的看似需要但实际上却是不必要的加工作业。
7、制造不良品的浪费:是指生产出批量废品或必须返工的产品。
二、浪费的表现形式(一)超量(过早)生产的浪费1、超量(过早)生产表现形式有:提前使用材料;生产数量大于需求量;2、浪费体现:多支付劳动报酬;增加库存(多余的搬运工时、盛具、堆放场地);长时间库存(品质劣化,如遇设计变更就要废弃)。
如(风光125)(二)等待的浪费作业时间充裕,做多余的动作以及不必要的事;生产线的品种切换;设备故障、缺件,不能作业、离开工作场地等。
(三)搬运的浪费材料、零件搬运时的临时搁置、二次搬运作业;由于工厂布局造成物流不畅、搬运距离远;使用叉车搬运效率低下等。
(四)动作的浪费多余的走动;不按照定时定位置管理进行作业;作业时将零部件取出集中搁在一起;单手作业等等。
(五)库存的浪费没有设置最大、最小库存量,库存量大;为了换型而准备的库存量过大;线上库存停留时间长;(加工周期及周转天过长)有长期在库的死库存品等等。
认识浪费与消除浪费PPT课件

精益管理的核心
彻底消除无效劳动与浪费
实施精益管理,必须从消除一切无效劳动与浪费开始。
(一)什么是无效劳动与浪费?
无效劳动与浪费:消耗了资源,增加了成本,但是没有 创造价值(或使附加值增加)的一切活动;也包括虽然创造 了价值,但耗费资源过高的工作。
浪费的表现
(二)无效劳动与浪费的表现
日本丰田汽车公司归纳为以下7种:
市场占有率(%)
冰箱
空调 洗衣机 产品
本企业 A企业 B企业
2004-2005年汽车销量对比 (单位:万辆)
1000
917
900 809
800 700
13.35% 643.2 681.8
600
471.9 487.2
500
400
6.00%
300
200
3.24%
100
0
通用
福特
戴克
809 747
16.00% 14.00% 12.00%
25
谢谢聆听
· 学习就是为了达到一定目的而努力去干, 是为一个目标去 战胜各种困难的过程,这个过程会充满压力、痛苦和挫折
Learning Is To Achieve A Certain Goal And Work Hard, Is A Process To Overcome Various Difficulties For A Goal
1、了解现状,找出问题 2、分析产生问题的原因 3、确定改善课题 4、制定改善方案(目标、措施、、费用、进度计划) 5、改善方案的优化、论证、审批 6、实施改善方案 7、评价改善效果,改善成果发表 8、巩固与标准化,奖励
写在最后
成功的基础在于好的学习习惯
七大浪费识别与消除

没有附加价值
没价值但必要
有价值
Does not add value to the output, and customer isn’t willing to pay for.
Eliminate去除
Does not add value to output, customer will not pay for, but is necessary. (Legal, Safety, Etc.)
生产过剩的浪费(一)
最大的浪费-浪费的源头
1. 提前使用掉了有限的资源/费用投入(材料费、人工费、其他消耗等)
2. 掩盖工程能力不平衡的问题,投入过多 3. 造成在制品积压,生产周期长 4. 会产生搬运和不良的浪费 5. 需要增加仓库放置(库存)、管理人员、办公桌/电脑……
10
生产过剩的浪费(一)
•人员多能工化、设备小型化 •快速切换改善-小批量生产 •工程能力平衡 •均衡化生产 •以顾客需求的准时化生产系统
搬运的浪费(二)
定义:不符合精益生产(JIT原则)的一切物料搬运活动
(不必要的移动及把东西暂放在一旁)
Байду номын сангаас
表现形式(典型的) :
长距离搬运在制品; 区域之间或楼层之间的搬运 缺乏效率的运输; 进\出仓库或在流程之间搬运原材料、零件或最终成品( 把物品暂时放在某处,囤积到预定量再转移到别处)。
浪费识别及改善
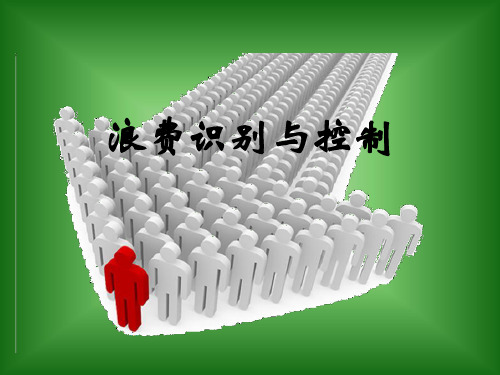
不必要的非增值活动 不必要的非增值活动:七大浪费
最大的浪费——制造过剩 最常见的浪费——等待 最隐蔽的浪费——加工本身 产 最可惜的浪费——制造不良 最不能容忍的浪费——库存 最没有价值的浪费——动作
最易被忽视的浪费——搬运
一、浪费的识别
1、最大的浪费——制造过剩
制造过剩浪费:是指制造过多或过早造成库存而产 生的浪费。
生产过剩的改善思路
需要量(销售量)为100个/日
提高表面效率
100个/10人→120个/10人 生产了多于销售量的产品,不 能实现实质性降低成本,反而 会增加成本。
提高真正效率
100个/10人→100个/9人 以更少的人员生产了可销售量 产品,实现了实质性的降低成 本。
致力于真正效率的提高,而不是表面效率的提高
降低移动批量→单件流动化
裁 剪 100
冲 100 压
0
加 100 工
0
抛 100 光
0
100
100分钟 + 100分钟 + 100分钟 + 100分钟 = 400分钟 (中转库存400个,成品库存100个) 转换成 裁剪 1分钟 冲压 加工
抛光
100
104分钟 100分钟 1分钟 1分钟 (周期时间缩短成104分钟,中转库存4个,成品库存100个)
2、最常见的浪费——等待
等待的浪费:由于某种原因造成的机器或人员的等待
浪费的消除与改善方法-完善版

卖方市场;消极被动; 企业类别:
高新产品 垄断产品 国内的铁路、民航等
浪费 - 6
不同的经营思想
售价中心型:
以售价为中心,当市场售价降低时,利润 随之减少。
计算公式:利润=售价-成本
市场好时有较高的利润;市场差时利润大 幅度降低;
企业类别:
在现场管理中,为了杜绝这些资源的浪费,有 必要竭尽全力将生产三要素的人、物、设备的投入 资源控制在最低限度,将Q、D、C的产量最大限 度地提高。
浪费 - 16
(3)杜绝因错误工作方法造成的浪费 工作方法浪费中,有以下几种浪费:随着时间的
推移人及生产条件都会发生变化,往往特意加以改 善的内容又回到了原来的程度,称之为“缺乏连续 性而造成的浪费”;各种各样的人讨论相同的事情 ,则不能谋求技术诀窍的有效活用,称之为“不执 行标准化造成的浪费”;只考虑自己责任范围的利 益而工作,如果考虑全体的利益则存在效率更高的 方法,称之为“个别合理浪费”。
浪费 - 21
全面生产系统的浪费
生产要素的5MQS: Man(人) Machine(机器) Material(物料) Method(作业方法) Management(管理) Quality(品质) Safety(安全)
浪费 - 22
5MQS的浪费
分类
浪费
说明
1. 行走的浪费
人 2. 监视的浪费
浪费 - 30
制造过多的Muda:对策
要考虑到下一个流程或下一条生产线的正确生产速 度;而不要只尽所能,在本流程生产过多的产品。
不要让作业员有生产伸缩的充分空间。 不要让每一流程或生产线有提高自己的生产力的利
益。 不要因为有不合格品而想提高直通率。 不要因为有多余的产能而容许机器生产多于所需之
浪费的识别与消除
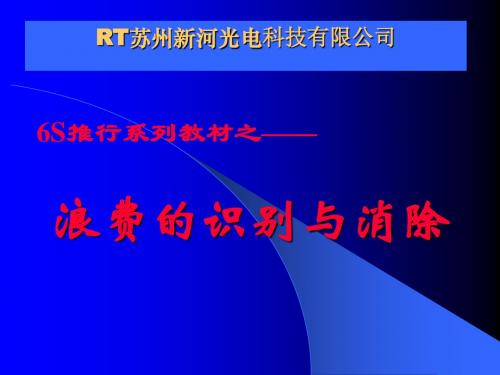
等待造成的浪费
原因
– Inconsistent Work Methods工作方法的不一致 – Long Machine Change Over Times 长时间的机 器换装 – Poor Machine/People Effectiveness 人/机配合 效果差 – Lack of Proper Machine 缺乏合适的机器
过量生产的浪费
原因: . 过程能力不足 . J.I.C. Reward System JIC顾客响应系统失灵 . 缺乏沟通 . 部门(局部)最优化 . 在不适当的地方自动化 . 换装(换线/换模)时间长 . 成本计算的习惯 . 机器有效运行时间短/预防维护不够 . 缺乏协调的计划 . 关注销售预测,而不是客户的需求(消耗量)。
浪费的识别和消除
浪费的种类: . 过量生产 . 纠正 . 材料移动 . 不必要的加工 . 存货 . 等待 . 动作 . 缺乏员工的参与 造成浪费的原因: – 超负荷 – 不均衡 – 过程控制方法
过量生产的浪费
定义: . 生产大于需求 . 生产快于需求
过量生产的浪费
特点: . 货物储备/先做出来 . 设备富余,或设备的产能过大 . 供应及生产各阶段产能不平衡 . 作业员太多 . 产能/投资过大 . 不合格品比例高 . 生产批量大 . 问题被掩盖(计划混乱、不合格事件、设备管理) . 存货管理复杂
动作的浪费
原因:
– 设备,办公室及工厂布局Equipment, Office & Plant Layout – 作业场所缺乏组织Lack of Work Place Organization – 机器/人力产生的低效率Poor Machine/Man Effectiveness – 工作方法不一致Inconsistent Work Methods – 大批量 Large Batch Sizes
识别消除浪费

3、设备改善
•缩短送、回的行程时间 •缩短加工时间以外的动作 •解决短时间停机问题
4、提高品质
•彻底杜绝问题的第二次发 生,提高FTT •在生产线上保证产品质量
现象: 在制品库存过多、叠放。 问题: 1、质量:挤压变形; 2、无法保证先进先出; 3、工位不平衡、设备等问题不能暴露出来。 解决措施:在制品库存量设定为1—3个,整改盛具保证零 件分开放置。
2.关于操作场所布置:
(1)工具、物料应放于固定位置; (2)工具、物料及装置应置于工作者之前方近处; (3)零件物料的供给,应尽可能地利用其重量“堕放”至工作者手边; (4)“堕放”配送方法应尽可能多的利用于生产线; (5)工具、物料应依照最佳之工作顺序排列; (6)应有适当的照明设备,使视觉满意舒适; (7) 坐椅及工作台高度,应使工作者坐、立适宜; (8)工作椅样式及高度,应可使工作者保持良好的姿势。
需解决的突出问题
七 大 浪 费
计 划 变 更
设 备 七 大 损 失
转 换 时 间
顺序投料
改 善 前
改 善 后
七大浪费-库存(续)
Seven Forms Of Waste - Inventory
产生库存的原因:
生产过剩 未设定合理的最小、最大库存量 在线停留时间过长 质量低劣 工位不平衡 消除浪费的方法与思路: 为换型准备的库存量过大 生产计划均衡化 运用拉动系统 建立最小、最大库存量,并持续改进 建立一个流的生产方式 开展工位平衡 实施快速转换
降低成本、提高效率、改善质量,从而走上持续 发展道路的先决条件。
希望您也能“慧眼识浪费”。
七大浪费-纠错
Seven Forms Of Waste - Correction
如何消除浪费
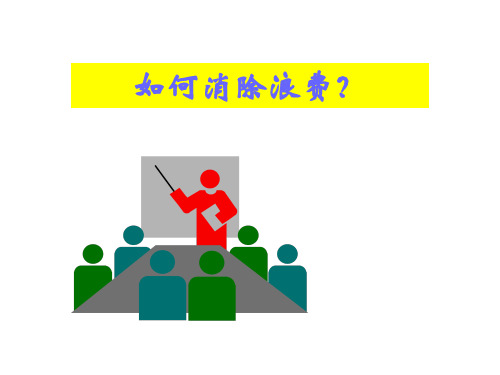
一、认识浪费
顾客是不会付钱给那些没有附加价值的活动。 但为什么有那么多人,在现场里从事许多没 有附加价值 的活动呢?
一、认识浪费
原材料 2
Value
3
Value
4
Value
…...
成品
…...
资源
资源
资源
—— 人/机
• 若人/机不是从事有附加价值的动作,就是进行无附加 价值的动作,它就是Muda。
较远。
7、转身角度太大的浪费
作业点与作 业者之间角度超出 适合范围,需要配
合转身动作完成。
8、动作之间没有配合好的浪费
动作与动作之间有停顿和迟疑,缺乏连续性 和节奏性。
9、不了解作业技巧的浪费
作业修正调整后不习惯或不熟练,出现有时 候跟不上的浪费。
10、伸背动作的浪费
零件、作业
位置太高,作业
者要踮起脚来才 够得着。
– 机器发出尖锐的声音,必须予以去除。
作业员、机器以及工作之流程,处在一种费劲的状
态就表示出现了Muri。
浪费 Muda
现场所发现的Muda,主要 表现为以下七种形式: A、过量生产的Muda; B、库存的 Muda; C、不良品的 Muda; D、动作的 Muda; E、加工的 Muda; F、等待的 Muda; G、搬运的 Muda。
有助于发掘需要关注的地方,以及迫使要去面对 处理的问题。
JIT体系所追求的目标:
当存货的水位持续下降至“一个流”的生产线时,
“改善”就成为每日必行的活动。
C、不良品的Muda
• 不良品的Muda是指在工厂内发生不良品,需要进行处置的时间、 人力和物力上的浪费。如: —产品报废; —材料损失; —人工设备资源损失; —出货延误取消订单; —信誉下降。 * 而且,品质不良经常会干扰正常的生产。