如何识别8大浪费
生产中八大浪费PPT课件
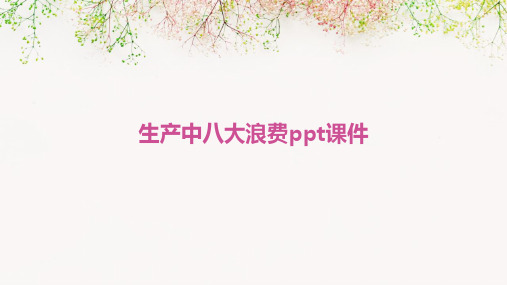
对员工反馈的信息进行及时处理和 跟进,确保问题得到解决和落实。
案例分析法
选择典型案例
经验借鉴
选择生产过程中具有代表性和普遍性 的浪费案例进行分析。
从案例中提炼出可供借鉴的经验和教 训,为减少类似浪费提供参考。
案例剖析
对选定的案例进行深入剖析,了解浪 费的具体情况和原因。
04
减少和消除策略
管理浪费
定义
管理浪费是指企业管理中不必要 的环节、流程或制度所造成的资 源、时间和成本的浪费。
危害
增加管理成本、降低管理效率; 影响企业决策效果和响应速度; 可能导致企业失去市场机会和竞 争优势。
解决方法
优化管理流程和组织结构,减少 不必要的管理环节和制度;实施 信息化和数字化管理手段,提高 管理效率和决策效果;加强员工 培训和管理素质提升,提高员工 对管理要求的认知和执行能力。
设备利用率提高
合理安排生产计划,充分利用设备产能,避免设备闲置和浪费。加强Βιβλιοθήκη 工培训和技能提升员工技能培训
01
针对员工岗位需求,制定个性化的培训计划,提高员工技能水
平和操作效率。
多能工培养
02
鼓励员工学习多种技能,培养多能工,提高员工适应性和灵活
性。
员工激励机制
03
建立合理的激励机制,激发员工积极性和创造力,促进员工持
生产中常见浪费现象
过度生产
生产超出实际需求或计划的产品,导致库存积压和 资金占用。
等待时间
设备或员工在等待下一道工序或资源时产生的空闲 时间。
运输浪费
不必要的物料搬运和运输,以及由此产生的时间和 资源消耗。
生产中常见浪费现象
01
02
现场8大浪费和改善原则

现场8大浪费和改善原则在生产和工作流程中,消除浪费是提高效率和效益的关键。
"现场8大浪费"是一种识别和消除生产过程中无效率和无效能的方法,源自于精益生产(Lean Manufacturing)的概念。
这些浪费包括:一、现场8大浪费1.过量生产:生产超过需求的产品,导致库存积压和资金占用。
2.等待时间:工人或机器因等待材料、信息或指令而闲置。
3.运输:不必要的产品或材料搬运,增加时间和成本。
4.过度加工:超出客户需求的加工,导致资源浪费。
5.库存:过多的原材料、在制品或成品库存,占用空间和资金。
6.运动:工人不必要的运动,如寻找工具或材料。
7.缺陷:产品质量问题导致的返工或报废。
8.未充分利用员工的创造力:未充分发挥员工的潜力和创新能力。
二、改善原则为了减少这些浪费,可以采用以下改善原则:1.持续改进(Kaizen):鼓励持续寻求小幅度的改进,而不是偶尔的大规模变革。
2.精益思维(Lean Thinking):专注于增加价值活动,减少无价值活动。
3.5S(整理、整顿、清扫、清洁、素养):创造整洁有序的工作环境,提高效率和安全。
4.标准化工作:建立标准操作程序,确保一致性和质量。
5.拉动系统(Kanban):基于需求生产,减少库存和过量生产。
6.一件流(One Piece Flow):减少在制品,通过连续流动提高效率。
7.问题解决:鼓励员工识别问题并积极参与解决方案的制定。
8.赋权与培训:提高员工技能,赋予他们更大的责任和决策权。
通过识别和消除这些浪费,企业可以提高生产效率,减少成本,并提高产品质量和客户满意度。
这不仅是生产和运营的关键,也是整个企业文化和长期成功的基石。
生产现场管理的8大浪费

想要打败敌人必先了解敌人,对于车间现场管理来讲,浪费恐怕是最大的敌人。
因为浪费,企业付出了高额的生产成本还毫不知情;因为浪费,本来2个人能完成的工作偏偏需要5个人;因为浪费,企业付出大量的人力成本。
凡是不能创造价值的活动都称之为浪费,想要消除车间现场管理中的浪费,一定要认识这八项浪费现象。
所谓不良、返修的浪费,指的是由于制衣厂内出现不良品,需要进行处置的时间、人力、物力上的浪费,以及由此造成的相关损失。
这类浪费具体包括:材料的损失、不良品变成废品;设备、人员和工时的损失;额外的返修、QC、追加检查的损失;有时需要降价处理服装,或者由于耽误出货而导致工厂信誉的下降。
加工的浪费也叫过分加工的浪费,主要包含两层含义:第一是多余的缝制和过分精确的加工,例如实际缝制针脚过多造成资源浪费;第二是需要多余的作业时间和辅助设备,还要增加生产用电等能源的浪费,另外还增加了管理的工时。
动作的浪费现象在很多服装企业的生产线中都存在,常见的动作浪费主要有以下12种:两手空闲、单手空闲、作业动作突然停止、作业动作过大、左右手交换、步行过多、转身的角度太大,移动中变换“状态”、不明技巧、伸背动作、弯腰动作以及重复动作和不必要的动作等等,这些动作的浪费造成了时间和体力上的不必要消耗。
搬运是一种不产生附加价值的动作,而不产生价值的工作都属于浪费。
搬运的浪费具体表现为放置、堆积、移动、整列等动作浪费,由此而带来物品移动所需空间的浪费、时间的浪费和人力工具的占用等不良后果。
国内目前有不少服装企业管理者认为搬运是必要的,不是浪费。
因此,很多人对搬运浪费视而不见,更谈不上去消灭它。
也有一些服装企业利用传送带或机器搬运的方式来减少人工搬运,这种做法是花大钱来减少工人体力的消耗,实际上并没有排除搬运本身的浪费。
按照过去的管理理念,人们认为库存虽然是不好的东西,但却是必要的。
其实库存是没有必要的,甚至库存是万恶之源。
例如,有些服装企业生产线出现故障,造成停机、停线,但由于有库存而不至于断货,这样就将故障造成停机、停线的问题掩盖住了,耽误了故障的排除。
仓库现场管理八大浪费
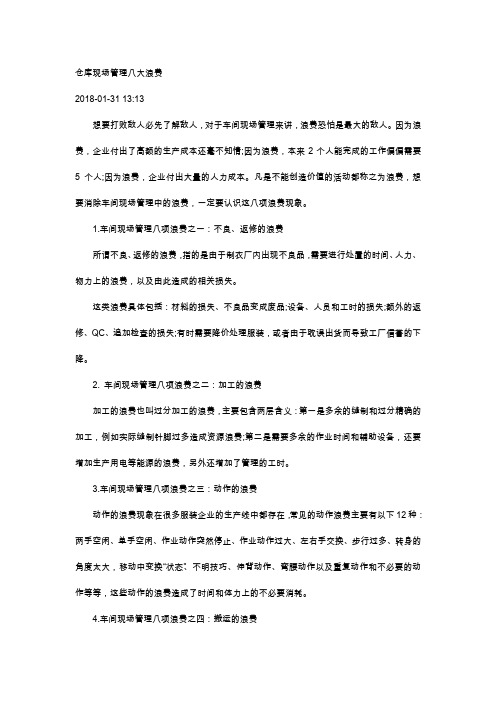
仓库现场管理八大浪费2018-01-31 13:13想要打败敌人必先了解敌人,对于车间现场管理来讲,浪费恐怕是最大的敌人。
因为浪费,企业付出了高额的生产成本还毫不知情;因为浪费,本来2个人能完成的工作偏偏需要5个人;因为浪费,企业付出大量的人力成本。
凡是不能创造价值的活动都称之为浪费,想要消除车间现场管理中的浪费,一定要认识这八项浪费现象。
1.车间现场管理八项浪费之一:不良、返修的浪费所谓不良、返修的浪费,指的是由于制衣厂内出现不良品,需要进行处置的时间、人力、物力上的浪费,以及由此造成的相关损失。
这类浪费具体包括:材料的损失、不良品变成废品;设备、人员和工时的损失;额外的返修、QC、追加检查的损失;有时需要降价处理服装,或者由于耽误出货而导致工厂信誉的下降。
2. 车间现场管理八项浪费之二:加工的浪费加工的浪费也叫过分加工的浪费,主要包含两层含义:第一是多余的缝制和过分精确的加工,例如实际缝制针脚过多造成资源浪费;第二是需要多余的作业时间和辅助设备,还要增加生产用电等能源的浪费,另外还增加了管理的工时。
3.车间现场管理八项浪费之三:动作的浪费动作的浪费现象在很多服装企业的生产线中都存在,常见的动作浪费主要有以下12种:两手空闲、单手空闲、作业动作突然停止、作业动作过大、左右手交换、步行过多、转身的角度太大,移动中变换“状态”、不明技巧、伸背动作、弯腰动作以及重复动作和不必要的动作等等,这些动作的浪费造成了时间和体力上的不必要消耗。
4.车间现场管理八项浪费之四:搬运的浪费搬运是一种不产生附加价值的动作,而不产生价值的工作都属于浪费。
搬运的浪费具体表现为放置、堆积、移动、整列等动作浪费,由此而带来物品移动所需空间的浪费、时间的浪费和人力工具的占用等不良后果。
国内目前有不少服装企业管理者认为搬运是必要的,不是浪费。
因此,很多人对搬运浪费视而不见,更谈不上去消灭它。
也有一些服装企业利用传送带或机器搬运的方式来减少人工搬运,这种做法是花大钱来减少工人体力的消耗,实际上并没有排除搬运本身的浪费。
1-如何识别8大浪费-ok解析

Lean Training 24
精益生产中的八大铺张 铺张2、库存的铺张
库存包括: 零部件、材料的库存 半成品的库存 成品的库存 已向供给商订购的在途物料 已发货的在途成品
Lean Training 25
精益生产中的八大铺张
欧美VS日本
库存的好处: 通过库存可以得到: 平稳的生产过程 准时交货 避开故障的影响 经济性地生产 高利用率
“ Training 11
精益生产中的八大铺张
• 产生效率低下的主要缘由 • 生产线不平衡,造成员工在生产过程中等待 • 常常断料,需要的料没有,没用的料一大堆 • 生产中搬运现象过多 • 生产人员进展线外物料拿取 • 品质问题不断 • 设备不断出故障
是指假设可以选择,客户情愿付 钱购置的活动与作业。
不增值 (Non Value Added〕 活动
那些花费时间或资源的活动,但 却对满足客户的没有任何帮助的 活动
必需的非增值活动(BNVA) : 是非增值的,但是对于未经改 进的现有的操作程序却是 必需的 活动。例如检验,搬运等。
Lean Training 7
精益生产中的八大铺张 增值在生产活动比例
Lean Training 8
回忆--价值
什么是“增值”
• Important to the customer. 对客户很重要。 • Transformation of information or material. • 转变了信息或原料。change • DONE RIGHT THE FIRST TIME. 一次做对。 •correct
• 职能组织构造 • 过度把握 • 没有后援/穿插培训 • 工作量不平衡 • 没有决策原则 • 没有可视化把握 • 工作场所缺乏有效组织 • 供给商质量 • 零部件供给质量不全都
八大浪费识别与改善

人 的 浪 费 材 料 的 浪 费 设 备 的 浪 费 1. 2. 3. 4. 5. 1. 2. 3. 4. 5. 1. 2. 3. 4. 5.
浪费
行走的浪费 监视的浪费 寻找的浪费 动作的浪费 职责不清的浪费 原料的浪费 螺栓的浪费 焊接的浪费 功能的浪费 不良报废的浪费 大型机械的浪费 通用机械的浪费 传送带的浪费 压缩机的浪费 故障的浪费
24
Ⅰ、浪费——七大浪费详解
6、过盈生产的浪费——过多的生产 现在不使用的部品过多的生产
[ 思考 ] 『物停滞时产生搬运的浪 费』☞ In-line 化
安徽水联水务科技有限公司 ▕ ***
***内部培训资料禁止外泄
17
Ⅰ、浪费——七大浪费详解
2、搬运的浪费——原因与改善方向
说明 不必要的搬运 物品的移动,保管等 长距离的搬运 活性度的恶化等问题
搬运的浪费
内容 • 空间的浪费使用 • 生产性低下 • 搬运工时的增减 • 搬运设备的增加 • 划伤、磕碰
库存的浪费
内容 • 交付期过长 • 压制了改善欲望 • 空间的浪费使用 • 搬运、检查的发生 • 运转资金的增加
对策 对于库存的意识改变 U字形生产 平均化生产 生产精通化 看板的彻底管理 准备、交换标准化 安徽水联水务科技有限公司 ▕ ***
原因 a) “库存是理所应当”的 错误 意识 b) 设备布局不好 c) 批量性生产 d) 先行生产 ***内部培训资料禁止外泄
优秀的工厂也有生产的浪费! 要想去除浪费首先会分浪费!
4.制造(加工)自身的浪费 — 做不必要的事
5.动作的浪费 —动 6.过盈生产的浪费 —过多的 生产 7.做不良的浪费 —出作业不 良 安徽水联水务科技有限公司 ▕ ***
精益生产之八大浪费培训

精益生产之八大浪费培训精益生产是一种通过持续改进和优化生产过程,减少浪费,提高效率的管理方法。
根据精益生产理念,有八大种类的浪费,分别是:过产、等待、运输、过加工、库存、运动、制造缺陷和不必要的动作。
以下是关于这八大浪费的培训内容。
1. 过产:过产是指生产数量超过需求的情况,通常是由于生产计划不准确或生产线设定不合理导致的。
培训中应教授如何制定准确的生产计划,提高生产线的灵活性,并在必要时采取合理的工序调整。
2. 等待:等待是指生产过程中的停工或停滞,可能是由于设备故障、缺少原材料或其他原因引起的。
培训中应重点介绍如何优化设备维护计划,提前准备原材料,并确保及时供应以减少生产线上的等待时间。
3. 运输:运输是指在生产过程中不必要的物料搬运和运输。
培训中应教授如何优化生产布局,减少物料的搬运距离,并合理规划物料存储位置,以降低运输的浪费。
4. 过加工:过加工是指对产品进行超出需求范围的加工。
培训中应着重介绍如何评估产品需求,制定合理的加工标准,并确保每个工序都有明确的目标和要求,避免不必要的过加工。
5. 库存:库存是指生产过程中积压的未完成产品数量,其中包括在制品、原材料和成品。
培训中应教授如何通过优化生产计划、采用just-in-time (JIT) 生产方式以及改进供应链管理来减少库存。
6. 运动:运动是指工人在生产过程中的不必要的移动和动作。
培训中应教授如何优化生产布局,将相关设备和物料放置在便捷的位置,从而减少工人的移动和动作,提高生产效率。
7. 制造缺陷:制造缺陷是指在生产过程中出现的质量问题,需要重新加工或修复。
培训中应着重强调质量控制的重要性,教授如何通过使用质量管理工具和技术,如 Six Sigma 方法,以及提供员工培训和持续监测来减少制造缺陷。
8. 不必要的动作:不必要的动作是指在生产过程中不必要的工作步骤或冗余操作。
培训中应强调流程优化的重要性,通过员工参与和持续改进来识别和消除不必要的动作,从而提高生产效率。
4-八大浪费

5
如何消除八大浪费
2
知梦行文一
6
如何消除八大浪费
2
知梦行文一
7
如何消除八大浪费
2
知梦行文一
8
如何消除的费
2
知梦行文一
9
使用实例:
小节
增加8大浪费 Checklist
综合运用IE各大工具,我们xxx工程部完全有能力制作出一份 全面的,系统的,实用的Checklist 来识别并消除工厂的各种 浪费,以提升运营效益。届时,只要对照Checklist来一项一项核对,谁都知道哪里需要改善,怎么去改善,真正实现全员 参与,持续改进!
知梦行文一
1
知梦行文一
6
6.库存的浪费
库存隐藏问题点,造成下列后果,没有管理的紧张感,阻碍改进:库存量一多 ,因机械故障、不良产品所带来的不利后果不能马上显现出来,因而也不会产 生对策。由于有了充足的库存,出现问题时可以用库存先顶上,问题就可以慢 慢解决甚至不用解决,最起码是被掩盖住了,不急迫了,不会被上级追究了, 于是乎本部门的工作成绩就出来了;设备能力及人员需求的误判:由于库存量 的存在,设备能力不平衡时也看不出(库存越多,越不容易看出来)。人员是 否过剩,也无法了解。由于有较多的库存,供应部门需要增加人员,制造一线 需要更多的人员来生产产品用于补充库存,需要增添设备来保证生产库存所需 要的设备能力,从而形成新一轮的浪费;到底为什么要有库存量,最大的理由 是“怕出问题”——出现故障怎么办?会不会因部分设备出问题,而影响整条 生产线或工厂的生产呢?于是乎为了不使影响扩大,库存便成了必要,众多的 问题也被隐藏起来,所有进步、赚钱(发现问题、解决问题就是赚钱)的步调 自然变慢了。
1
知梦行文一
0
生产现场常见浪费及识别方法(浪费的概念,生产现场七大浪费,相关术语,识别浪费)

✓ 产品停滞在仓库的情况也是等待浪费
• 生产线的品种切换。 • 时常因缺料而使机器闲置。 • 机器设备时常发生故障。 • 生产线未能取得平衡。 • 有劳逸不均的现象。
二、生产现场的七大浪费
2、加工本身的浪费
加工本身的浪费
现在正做的作业是否真的 必要?为什么要这么做?
摈弃现有的想法、方式、基准。
到现场,看现物,掌握现象。
[三现原则] 到
现 场
看 现 物
掌握 现象
三、相关术语
要认识潜在浪费要素在哪里发生?发生多少? 怎么发生?是否一定要发生?
不可信, 再检查!
工具在哪?
还是不良!
又没电了!
累死了
XX毛坯 在哪?
什么、在哪里、有多少、 怎么、为什么发生?
三、相关术语
二、生产现场的七大浪费
虽然制造的产品不同,但在工厂发现的典型的浪费类型是类似的
1 等待浪费 2 加工本身的浪费 3 动作浪费 4 库存浪费
5 制造不良的浪费 6 生产过剩浪费 7 搬运浪费
二、生产现场的七大浪费
1、等待浪费
对不起, 请少等 会儿...
还没 好 吗?.
人
等
设备
待
物
作业
✓ 只把人或设备的等待,看做等待浪费 的情况较多
库存的浪费
利用库存回避工厂 的许多问题。
在这种意识下发生的。
• 产生不必要的搬运、堆积、放置、防护、 寻找等浪费的时间、空间和动作。
• 资金占用(损失利息)及额外的管理费用。 • 物品的价值衰减,变成呆料、废料。 • 占用空间和通道,造成多余的仓库建设投
资或租金投入。
生产现场常见浪费及识别方法

生产现场常见浪费及识别方法
浪费的概念
浪费是指实际需求和应当投入的资源之间,实际投入资源过多的情况。
它并非只指金钱,也可以是人力、物力等劳动资源的过多投入,以至于导
致系统效率降低。
必须要熟悉它的概念,不但知道了解它,而且要清楚浪
费的定义,这样才能有效减少浪费,提高效率,发挥最大价值。
生产现场七大浪费
1、过程等待:当当前进行的工作因等待物料、没有及时调整机器,
设备,等待一些特殊情况或问题的解决而被迫停止时,就产生了过程等待
的浪费。
2、过多加工:当任何地方都不符合和客户预期或者所需的标准时,
就可能存在过多加工的问题,例如上面加工的超出客户的要求,超出需求
的特殊处理,或长度不足以够一次性输送时,都会产生过多加工的浪费。
3、运输:运输浪费主要是指在生产和成品库存的移动过程中所用的
时间、人力和能源上的浪费。
比如物料在做搬运时,空距行走搬运,物料
的搬运距离太长,搬运途中浪费时间,运输设备的搬运距离太长等等,都
会产生运输浪费。
4、过度库存:如果公司的库存水平超出它的实际生产需求,就会产
生过度库存,而过度库存又会造成物料、货币和空间的浪费。
八大浪费识别评优规则
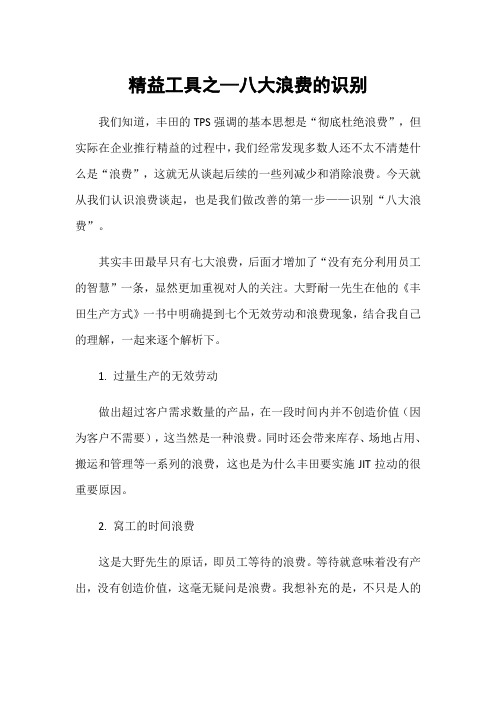
精益工具之—八大浪费的识别我们知道,丰田的TPS强调的基本思想是“彻底杜绝浪费”,但实际在企业推行精益的过程中,我们经常发现多数人还不太不清楚什么是“浪费”,这就无从谈起后续的一些列减少和消除浪费。
今天就从我们认识浪费谈起,也是我们做改善的第一步——识别“八大浪费”。
其实丰田最早只有七大浪费,后面才增加了“没有充分利用员工的智慧”一条,显然更加重视对人的关注。
大野耐一先生在他的《丰田生产方式》一书中明确提到七个无效劳动和浪费现象,结合我自己的理解,一起来逐个解析下。
1. 过量生产的无效劳动做出超过客户需求数量的产品,在一段时间内并不创造价值(因为客户不需要),这当然是一种浪费。
同时还会带来库存、场地占用、搬运和管理等一系列的浪费,这也是为什么丰田要实施JIT拉动的很重要原因。
2. 窝工的时间浪费这是大野先生的原话,即员工等待的浪费。
等待就意味着没有产出,没有创造价值,这毫无疑问是浪费。
我想补充的是,不只是人的等待,还应该包括机器、物料的等待都是浪费,一切没有流动起来的资源都是浪费。
3. 搬运的无效劳动这在车间现场随处可见,不管是人为的搬运、叉车的搬运,还是机械手的搬运,统统都是浪费。
所以,我们不要以为高效率的自动化就一定很精益,这是多数人的误区,只要存在搬运就一定是浪费。
我们要消除搬运浪费,而非用自动化来掩盖。
4. 加工本身的无效劳动和浪费在产品的加工环节,过程是否都有必要,是否都在增值(即客户是否愿意买单),这是判断加工过程是否存在浪费的唯一标准。
加工中的多余环节,比如产品清洗和100%挑选,这其实并不增值,只是我们加工过程不能保证零件的外观清洁度和残次品的混入,这当然是浪费。
5. 库存的浪费都说“库存是万恶之源”,的确如此,库存会带来的浪费不胜枚举,比如资金占用、场地占用、管理成本、质量风险、搬运等等。
所以,如果我们能真正减少甚至消灭原材料库存、半成品库存、成品库存,你的企业不精益都没人相信。
8种浪费
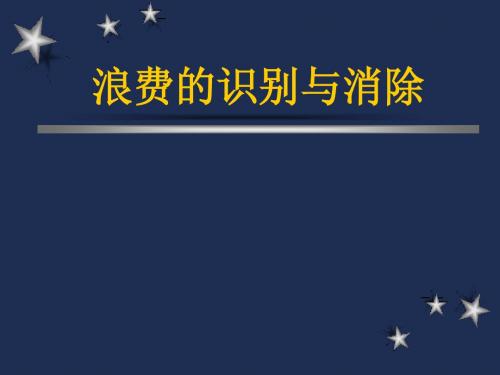
Waste of Motion 动作的浪费
Definition定义: Any Movement of People or Machines Which Does NotAdd Value to the Product/Service 任何不会给产品/服 务带来增值的人员或机器的动作
Waste of Motion
• 问题被掩盖(计划混乱、不合格事件、设备管理) • 存货管理复杂
过量生产的浪费
原因:
• 过程能力不足 • J.I.C. Reward System JIC顾客响应系统失灵 • 缺乏沟通 • 部门(局部)最优化 • 在不适当的地方自动化 • 换装(换线/换模)时间长 • 成本计算的习惯 • 机器有效运行时间短/预防维护不够 • 缺乏协调的计划 • 关注销售预测,而不是客户的需求(消耗量)。
Characteristics特点:
– People Waiting for Machine人等机器
– Machine Waiting for People机器等人
– People Waiting for People人等人 – Unbalanced Operations (Work)不平衡的操作
– Lack of Concern for Equipment Breakdowns
• 不当的工厂布局 • 较大的缓冲储存
过多处理过程的浪费
定义
Effort Which Adds No Value to a Product / Service.Enhancements Which are Transparent to the Customers, orWork Which Could be Combined with Another Purpose. 指对于产品/服务没有增值的努力。对客户来说增强是明显的,或者该工 作是可以和其它的目的相结合的。
精益生产中浪费识别有何技巧
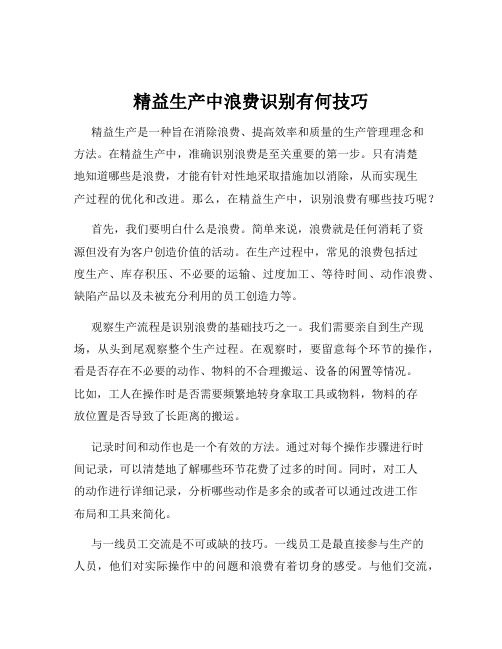
精益生产中浪费识别有何技巧精益生产是一种旨在消除浪费、提高效率和质量的生产管理理念和方法。
在精益生产中,准确识别浪费是至关重要的第一步。
只有清楚地知道哪些是浪费,才能有针对性地采取措施加以消除,从而实现生产过程的优化和改进。
那么,在精益生产中,识别浪费有哪些技巧呢?首先,我们要明白什么是浪费。
简单来说,浪费就是任何消耗了资源但没有为客户创造价值的活动。
在生产过程中,常见的浪费包括过度生产、库存积压、不必要的运输、过度加工、等待时间、动作浪费、缺陷产品以及未被充分利用的员工创造力等。
观察生产流程是识别浪费的基础技巧之一。
我们需要亲自到生产现场,从头到尾观察整个生产过程。
在观察时,要留意每个环节的操作,看是否存在不必要的动作、物料的不合理搬运、设备的闲置等情况。
比如,工人在操作时是否需要频繁地转身拿取工具或物料,物料的存放位置是否导致了长距离的搬运。
记录时间和动作也是一个有效的方法。
通过对每个操作步骤进行时间记录,可以清楚地了解哪些环节花费了过多的时间。
同时,对工人的动作进行详细记录,分析哪些动作是多余的或者可以通过改进工作布局和工具来简化。
与一线员工交流是不可或缺的技巧。
一线员工是最直接参与生产的人员,他们对实际操作中的问题和浪费有着切身的感受。
与他们交流,倾听他们的意见和建议,往往能够发现一些被管理层忽视的浪费现象。
他们可能会提到某些工具不好用导致工作效率低下,或者某些工作流程不合理增加了他们的工作量。
分析数据同样重要。
收集生产过程中的各种数据,如产量、质量、库存水平、设备利用率等,并对这些数据进行分析。
通过数据的对比和趋势分析,可以发现潜在的浪费问题。
例如,如果库存水平一直居高不下,可能意味着存在过度生产或者预测不准确的问题。
采用价值流图分析(VSM)是一种系统性的浪费识别方法。
价值流图是一种可视化工具,它可以展示从原材料到成品交付给客户的整个流程中的信息流和物流。
通过绘制价值流图,可以清晰地看到哪些环节存在停滞、哪些环节产生了大量库存、哪些环节的增值时间比例低等问题,从而全面识别浪费。
如何识别与消除七大浪费
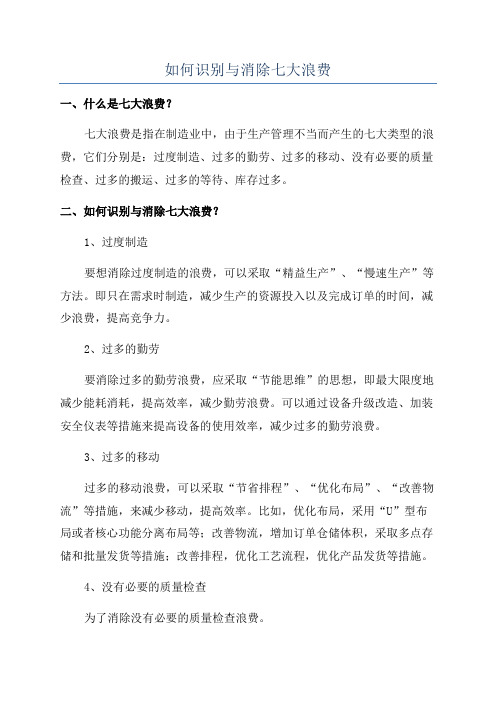
如何识别与消除七大浪费
一、什么是七大浪费?
七大浪费是指在制造业中,由于生产管理不当而产生的七大类型的浪费,它们分别是:过度制造、过多的勤劳、过多的移动、没有必要的质量检查、过多的搬运、过多的等待、库存过多。
二、如何识别与消除七大浪费?
1、过度制造
要想消除过度制造的浪费,可以采取“精益生产”、“慢速生产”等方法。
即只在需求时制造,减少生产的资源投入以及完成订单的时间,减少浪费,提高竞争力。
2、过多的勤劳
要消除过多的勤劳浪费,应采取“节能思维”的思想,即最大限度地减少能耗消耗,提高效率,减少勤劳浪费。
可以通过设备升级改造、加装安全仪表等措施来提高设备的使用效率,减少过多的勤劳浪费。
3、过多的移动
过多的移动浪费,可以采取“节省排程”、“优化布局”、“改善物流”等措施,来减少移动,提高效率。
比如,优化布局,采用“U”型布局或者核心功能分离布局等;改善物流,增加订单仓储体积,采取多点存储和批量发货等措施;改善排程,优化工艺流程,优化产品发货等措施。
4、没有必要的质量检查
为了消除没有必要的质量检查浪费。
8大浪费识别和改善制度理念
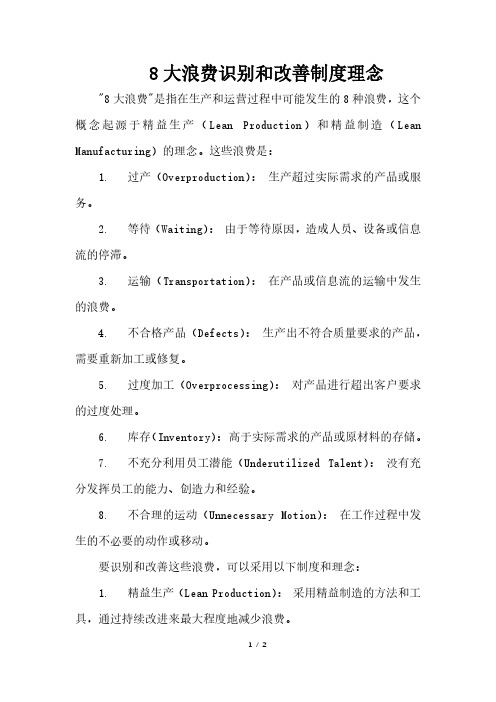
8大浪费识别和改善制度理念"8大浪费"是指在生产和运营过程中可能发生的8种浪费,这个概念起源于精益生产(Lean Production)和精益制造(Lean Manufacturing)的理念。
这些浪费是:1. 过产(Overproduction):生产超过实际需求的产品或服务。
2. 等待(Waiting):由于等待原因,造成人员、设备或信息流的停滞。
3. 运输(Transportation):在产品或信息流的运输中发生的浪费。
4. 不合格产品(Defects):生产出不符合质量要求的产品,需要重新加工或修复。
5. 过度加工(Overprocessing):对产品进行超出客户要求的过度处理。
6. 库存(Inventory):高于实际需求的产品或原材料的存储。
7. 不充分利用员工潜能(Underutilized Talent):没有充分发挥员工的能力、创造力和经验。
8. 不合理的运动(Unnecessary Motion):在工作过程中发生的不必要的动作或移动。
要识别和改善这些浪费,可以采用以下制度和理念:1. 精益生产(Lean Production):采用精益制造的方法和工具,通过持续改进来最大程度地减少浪费。
2. 5S方法:整顿、整理、清扫、清洁、素养是5S方法的关键步骤,有助于提高工作效率、减少浪费。
3. 持续改进(Continuous Improvement):实施Kaizen(改善)文化,鼓励员工参与改进工作流程和去除浪费的活动。
4. 价值流映射(Value Stream Mapping):通过绘制价值流图,识别和分析价值流中的浪费,以便有针对性地进行改进。
5. JIT(Just-In-Time)生产:通过减少库存,根据实际需求进行生产,降低过产和库存浪费。
6. 质量管理:强调预防性的质量管理,减少不合格产品的产生。
7. 员工培训和发展:提供培训和发展机会,充分发挥员工的潜能,鼓励创新和改进。
如何识别八大浪费

如何识别八大浪费课程描述:俗语说:节约好比燕衔泥,浪费好比河决堤。
不要忽视生产过程中的任何看似微小的浪费,不要让“千里之堤溃于蚁穴”。
本课程将结合实际案例,向您详细阐述如何识别八大浪费,如何有效减少其造成的损失。
解决方案:他山之石,可以攻玉!虽然不同行业在“识别八大浪费”时都有自己的方法与技巧,但万变不离其宗!接下来我们从实战经验中给大家总结一些方法技巧,以便大家参考。
一般来讲,识别八大浪费时要掌握以下三个要点:一,判断原则。
二,单独的识别方法。
三,万能识别法。
八大浪费的判断原则包括浪费的存在是否为必须、浪费是否能增值、浪费是否为最少量三个。
八大浪费包括库存的浪费、搬运的浪费、加工的浪费、加工过多过早的浪费、动作的浪费、管理的浪费、等待的浪费、品质的浪费,下面主要介绍一下如何识别“等待的浪费”和“品质的浪费”。
识别“等待的浪费”的方法主要有三个:一,以工时平衡率为标准进行考核。
若算出来的工时低于标准数值,就说明生产中存在等待的浪费。
公司可根据自身情况自行设置工时平衡率,一般来讲,这个数值大于85%。
二,安排专门的生产线督导或车间作业指导培训师进行现场巡视查看。
一旦发现存在等待的浪费,要当场矫正。
三,对照作业指导书,尤其是其中的人机作业分析、三级表等,以此识别等待的浪费,并及时矫正错误,减少浪费。
识别“品质的浪费”的方法主要有三个:一,检测原材料、待制品、成品等各个环节产品的合格率。
若合格率只有70%,就说明产品中存在30%的不合格品。
公司可在返修过程中通过查看30%的合格品中可再利用的非增值产品比例,判断生产中存在多少“品质的浪费”。
在此过程中,经营者将其按一定的公式换算为成本,就可以大概了解品质浪费的程度。
二,分析CPK(读字母)指标,一般来讲,低于或高于CPK指标的产品都存在品质的浪费。
企业可通过强化员工质量意识、提高关键工序员工技能、增添工装夹具等措施减少品质的浪费。
三,直接在设计中进行识别。
生产现场常见浪费及识别方法

生产现场常见浪费及识别方法概述生产过程中,浪费是一种很常见的问题,也是影响生产效率的主要因素之一。
所谓浪费,就是在生产过程中出现的无效和不必要的环节、步骤和资源的消耗。
浪费分为七种类型:超产、等待、运输、处理、库存、运动和设计。
本文将介绍这七种浪费的具体定义和识别方法,以帮助生产现场更好地寻找和解决生产过程中存在的浪费,提高生产效率。
七种浪费及识别方法1. 超产超产是指在订单未完成时,继续生产大量商品,使得完成后的部分商品库存积压,造成资源和资金的浪费。
识别超产的方法有:•对订单进行详细的计划和控制,以保证生产数量与需求匹配。
•使用拉动生产方式,按需求生产,不压盘。
•实施短周期制造,分批生产并及时交付给下一工站,减少库存。
2. 等待等待是指生产过程中因为资源不足或者机器维护等原因而导致的停滞,造成效率低下。
识别等待的方法有:•摆脱“瓶颈资源”,利用合理的资源分配,并建立适当的备件库。
•优化生产计划,避免因为等待而导致生产进程停滞。
•加强机器保养保修,减少机器故障率,降低等待的时间。
3. 运输运输是指在产品生产流程中的物料或者成品的搬运转移,造成人力、时间和其他资源的浪费。
识别运输的方法有:•对物流流程进行优化,简化交付方式和流程,以加快产品交付速度。
•重新构建供应链,选择能够满足时限要求的供应商。
•采用先进物流管理系统,整合物流信息,降低运输时间和成本。
4. 处理处理是指在生产过程中,不必要的工程流程,包括重复操作和不必要的检查等,使得生产过程贻误。
识别处理的方法有:•实行标准化工艺流程,减少重复的工艺步骤。
•根据不同产品的特点进行人力资源的分组,使得高效利用各种人力资源。
•引进先进的生产设备,减少不必要的操作和检查,提高生产效率。
5. 库存库存是指在产品物料制造和销售过程中存放时间过长,采购量不当等问题,导致生产成本的提高和资源的浪费问题。
识别库存的方法有:•实行零库存设计,即根据需求生产商品,避免过多库存。
如何在精益管理中有效识别并消除浪费

如何在精益管理中有效识别并消除浪费在当今竞争激烈的商业环境中,企业都在寻求提高效率、降低成本和提升质量的方法。
精益管理作为一种被广泛认可的管理理念和方法,其核心目标就是消除浪费,以最小的资源投入创造最大的价值。
然而,要实现这一目标,首先需要有效地识别各种浪费形式。
一、什么是精益管理中的浪费精益管理中的浪费,并非仅仅指物质的浪费,而是涵盖了一系列不增值的活动和流程。
常见的浪费类型包括:1、过度生产这是指生产的产品或提供的服务超过了客户的即时需求。
过度生产不仅占用了资源,还可能导致库存积压、增加成本以及产品过时的风险。
2、库存浪费过多的库存占用了资金、空间和管理成本,同时也掩盖了生产过程中的问题,如质量缺陷、供应不稳定等。
3、等待浪费人员、设备或流程因为等待其他环节的完成而闲置,造成时间和效率的损失。
4、运输浪费不必要的物料、产品搬运和运输,增加了成本,降低了效率,还可能导致产品损坏。
5、过度加工在产品或服务中添加了客户不需要的功能或特性,增加了成本却没有带来相应的价值。
6、动作浪费员工在工作中的不必要动作,如寻找工具、物品摆放不合理导致的重复动作等。
7、缺陷浪费产品或服务的质量缺陷导致的返工、报废和客户不满,增加了成本和时间。
8、未充分利用员工的才智员工的知识、技能和创造力没有得到充分发挥,是一种潜在的浪费。
二、如何识别浪费1、价值流分析绘制产品或服务从原材料到交付给客户的整个价值流图,清晰地展示每个环节的信息流和物流。
通过价值流分析,可以直观地发现流程中的停滞、迂回和浪费现象。
例如,一家制造企业通过价值流分析发现,在零部件加工环节与组装环节之间,存在大量的在制品库存,导致生产周期延长,这就是明显的库存浪费。
2、现场观察深入工作现场,观察员工的实际操作和流程运行情况。
注意员工的动作、物料的流动、设备的使用等细节,往往能发现隐藏的浪费。
比如,在一个车间中,观察到工人需要频繁地走动去拿取工具,这就揭示了工具摆放不合理导致的动作浪费。
八大浪费识别2017

定义:所谓制造过早(多)就是前制程制造太早/过多,大于客户(或后制 程)当期的最小需要量。 真假效率 在同样的时间内,生产愈多的产品 ---假效率 建立在市场每日的需要基数上,朝以最少的人力来生产出需 要的量,也就是非定员制的生产方式。 ---真正的效率 例子﹕市场上每日需求100个产品 原来﹕10人 1日 100个 现在﹕10人 1日 125个(假效率) 现在﹕ 8人 1日 100个(真效率)
3
二、1. 制造过剩的浪费
产生原因:
• • • • 生产计划方面:排周生产计划,一天内的生产排配权利下放到制程 内部制造能力弱的补偿问题:如品质差 产能不平衡及流程不顺方面:制程产能不平衡 其他:保障昂贵设备的稼动率
4
二、2. 库存的浪费
定义:库存是生产过程中停滞物料的总称。一般分为原物料、在制品 WIP、成品三大类.
12
二、6. 动作的浪费
定义:动作浪费指生产中在动作上的不合理而导致的时间、效率、场 地、人员及人身等方面的浪费
常见的动作浪费现象主要有以下12种: 1)两手空闲; 2)单手空闲; 3)作业动作突然停止; 4)作业动作过大; 5)左右手交换; 6)步行过多; 7)转身动作太大; 8)移动中变换“状态”; 9)不明技巧; 10)伸背动作; 11)弯腰动作; 12)重复动作和不必要的动作等。
• 产品不良了,在宣布 报废之前,我们可能 要处理、挑选、检查、 维修,把部分不良品 转成良品,这一过程 中的全部付出都是浪 费,因为客户不会为 我们的上述作业负担 一分钱,这其中包含 我们的时间、人力、 设备、场地、辅材等
- 1、下载文档前请自行甄别文档内容的完整性,平台不提供额外的编辑、内容补充、找答案等附加服务。
- 2、"仅部分预览"的文档,不可在线预览部分如存在完整性等问题,可反馈申请退款(可完整预览的文档不适用该条件!)。
- 3、如文档侵犯您的权益,请联系客服反馈,我们会尽快为您处理(人工客服工作时间:9:00-18:30)。
Lean Training 18
精益生产中的八大浪费 浪费的根源
• 布局(距离) • 过长的切换时间 • 过程能力弱 • 职能组织结构 • 过度控制 • 没有后援/交叉培训 • 工作量不平衡 • 没有决策原则 • 没有可视化控制 • 工作场所缺乏有效组织 • 供应商质量 • 零部件供应质量不一致
• 设备维护差
现场常见问题
发生场所
备注
Lean Training 16
精益生产中的八大浪费
浪费固化的过程
发现
发现浪费,但没办法 解决,只能应付了事
浪费存在好像有必要
暂时增加库存应对一下
领导说的认可浪费
应该保持库存
习惯化惰性造成浪费
既成事实 长期存在谁也 不认为不合理
库存已成习惯与应该
管理制度无意识浪费
形成浪费
• 绝对最少
– 增加产品价值所绝对必须的物料、设备、 – 人力、场地和时间等要素
“理解和识别浪费是消除或者减少浪费的第一步”
Lean Training 11
精益生产中的八大浪费
• 产生效率低下的主要原因 – 生产线不平衡,造成员工在生产过程中等待 – 经常断料,需要的料没有,没用的料一大堆 – 生产中搬运现象过多 – 生产人员进行线外物料拿取 – 品质问题不断 – 设备不断出故障
Lean Training 23
精益生产中的八大浪费
制造过多的浪费:对策
• 要考虑到下一个流程或下一条生产线的正确生产速度;而不要只 尽所能,在本流程生产过多的产品。 • 不要让作业员有生产伸缩的充分空间。 • 不要让每一流程或生产线有提高自己的生产力的利益。 • 不要因为有不合格品而想提高直通率。 • 不要因为有多余的产能而容许机器生产多于所需之量。 • 不要因为引进了昂贵的机器设备,而为折旧费的分摊,提高稼动 率,生产过多的产品。
• 工作方法差 • 缺少培训
• 缺乏符合性
• 管理技能低下 • 计划安排低效 • 绩效测量方法不一致
浪费常常就在我们眼前,但我们却视而不见. 我们必须学习系统化地…从新的角度. 从通 过流程的“事物”的角度观察和思考.
Lean Training 19
精益生产中的八大浪费 浪费1、制造过多/过早的浪费
7. 生产过多/过早的浪费 Over production
Inventory
Lean Training 13
精益生产中的八大浪费
浪费举例
浪费
有缺陷的产品
过度生产 多余库存 过多的加工 过多的处理
举例
• 供应商提供的部件错误 • 不完整的信息 • 低产出率,花110的精力生产100 • 生产多于需求 • 库存投资在闲置 • 每个复印机旁都有纸 • 30%的时寻找部件、工具 • 纸张未放在复印机旁 • 多余的手工劳动 • 职能部门签字 • 布局不合理 • 流程交汇点 • 投资等待下一个“事件” • 批量,签字流程
Lean Training 6
回顾--价值 如何定义增值活动和不增值活动?
增值 (Value Added)活动
是指如果可以选择,客户愿意付 钱购买的活动与作业。
不增值 (Non Value Added) 活动
那些花费时间或资源的活动,但 却对满足客户的没有任何帮助的 活动
必须的非增值活动(BNVA) :
3
囤积不良品的浪费
3.2存放期间有产生不良的隐患吗? 3.3存放期间产品规格和要求发生变化了吗?
Lean Training 29
精益生产中的八大浪费
库存的浪费
存货的浪费主要表现在: • 零部件、产品陈旧导致削价与报废损失; • 流动资金占用损失; • 人工场地损失; • 隐藏不良品损失; • 隐藏产能不平衡与过剩损失; • 隐藏机器故障损失; • ……
10%
< 2%
storage(wait)储藏 (等待) 70-80%
检查 处理 5-10% 1-5%
< 18%
0 > 80%
注及 3 是浪费; 活动 4是增值的
一旦 ‘产品’ 停留, 我们就产生了浪费。 想想流动 !
你的流程为什么不能流动? 现在你需要确认浪费的来源!
Lean Training 30
如:我们的客户需要它!
再问为什么! •可能客户要求,我们可以要求有所变化 •可能客户要求因为我们告诉他们我们可以做 •可能这不是客户真正要求的。
许多限制的因素和障碍是我们自己造成的。
Lean Training 3
挑战现有状态:5个“为什么”
精益管理解决问题的流程中就包括了5个“为什么”。在提问以前,首 先: • 了解问题 •与标准(如果有)进行比较 • 深入问题现场 • 了解问题的相对重要性、严重性和发生频率 • 确定“原因点” • 发现问题的地点,可能的原因是什么 • 通过5个“为什么”发现问题的真正根源
所有要思考的活动都包括这三项 ‘value added’. 增值。
Lean Training 9
精益生产中的八大浪费
Lean Training 10
精益生产中的八大浪费
什么是浪费?(Muda)
• 不增加价值的活动,就是浪费;
• 尽管是增加价值的活动,所用的资源超过了
“绝对最少”的界限,也是浪费。
说明
• 客户投诉 • 返工、废料、保修 • 额外的成本 • 报废、清点、保存
• 较长的交付时间、返工、丢失
• 高成本、数量总是不对 • 增值的障碍 • 人机工程学、安全 • 技巧的低效使用 • 没有决策原则 • 投资掩盖低效 • 批量处理、没有流动 • 投资低效 • 低效的内置
运输
等候
检查所有的浪费、瓶颈和所有客户问题,优化处理。
如何识别浪费
回顾--价值
什么是“价值流”?
• “价值流”是为客户创造价值所需要的一系列行动。 • 包括增值和非增值步骤。
什么是消除浪费?
• 在思考任何流程时-工厂、行政管理和工程,通常会发现总的流程交付时间中只有5% 甚至更少的时间是增值时间。 • 传统思维使我们更关注如何加快这5%。 • 精益生产思维则通过消除浪费,而将注意力放在95%的机会上。
Lean Training 21
精益生产中的八大浪费
制造过多/过早的浪费
• 还增加了搬运、堆积的浪费,带来庞大的库存量。 • 此外,制造过多或过早,会,利息负担增加,不可避 免地增加了贬值的风险。
Lean Training 22
精益生产中的八大浪费
制造过多/过早的后果
• • • • • • • • • • • 增加额外的空间以储存多余的存货 增加搬运和管理成本 先行生产而导致不同步的时间和空间浪费; 使得制品周期变长、空间变大 货架台、材料搬运等的增加; 放置地、仓库等存储空间的占用; 在库的发生与管理工时的增加; 利率利息负担负担的增加; 提早耗用原材料,生产用电、气、油、水等能源的浪费 浪费人力及设施 增加机器负荷
Lean Training 24
精益生产中的八大浪费
浪费2、库存的浪费
库存包括: • 零部件、材料的库存 • 半成品的库存 • 成品的库存 • 已向供应商订购的在途物料 • 已发货的在途成品
Lean Training 25
精益生产中的八大浪费
欧美VS日本
库存的好处: • 通过库存可以得到: – 平稳的生产过程 – 及时交货 – 避免故障的影响 – 经济性地生产 – 高利用率
维修人员的技能有限,每次出了故障只能找厂家维修,当厂家时间难以确 定时只能应付生产。
在前期购买设备时,厂家没有给技术人员培训,没有移交设备的操作保养 标准等。
Lean Training 5
回顾--价值
产品活动及浪费
你的流程中的‘产品’有4个活动可以参与
一般情况 世界级
transportation 运输 inspection processing
一旦通过问5个“为什么”确定了问题的根本原因,必须: 1)形成适当的对策。 2)在评价对策的效率后,必须使对策标准化。 3)可能需要改变流程文件、操作指导书和程序文件。
Lean Training 4
5WHY --5个为什么案例参考
1)、改进前问题:在现场巡检时发现地下有水
2)、问题分析:为何有水滴落?现场访谈时员工的解释不一, 有说 “冲洗产品的残夜”,有说“装满后溢出的” 。 利用“五个为什么?”进行了分析,结果如下: ● 第一个:为什么地面有水?----》从传送带上代过来的 ● 第二个:为什么传送带有水?--》灌装时溢出,滴在传送带上 ● 第三个:为什么会溢出?------》灌装时没有控制精度 ● 第四个:为什么没有控制精度?--》精度感应器坏了 ● 第五个:为什么精度感应器坏?--》没有定期保养和检修 3)、通过追根究底地提问,找到了问题的症结,确认根本原因是: 没有对灌装机的精度控制感应器进行过保养和检修,
我们是如何“浪费”的?
• 缺陷 •过度生产 •过多的移动 •多余库存 •等候 •过度处理
• 运输
Lean Training 2
学会观察和问为什么
我们每天都生活在流程中。因此,我们常常无法看清我们身边的浪费和低 效。 我们必须学会“观察”。我们也必须问“为什么”。 我们为什么要做? 为什么我们这样做? 我们的程序和方法通常随时间而改变,最初的目的可能不复存在。
精益的观点: 库存掩盖的问题:
不稳定的生产过程 生产能力不平衡 缺乏灵活性 易产生废品 按时交货能力差
Lean Training 26
精益生产中的八大浪费
库存的浪费
• 成品、半成品、零件及物料的存货,是不会产生任何 附加价值的,反而增加了营运的成本。
库 存
检查 延迟
废料
供应商 的过失 改变 顺序 文件 延迟 订单处 理延迟 决策 缓慢