甲醇工艺流程简述
甲醇工艺流程介绍

甲醇工艺流程介绍甲醇是一种重要的有机化工产品,广泛应用于化工、医药、农药、塑料、合成纤维等领域。
甲醇的生产工艺主要有四种,包括合成气法、天然气重整法、甲烷水蒸气重整法和木质素液化法。
本文将详细介绍甲醇的生产工艺流程。
一、合成气法合成气法是最常用的甲醇生产工艺,其主要原料是天然气或煤炭。
该工艺流程包括气化、合成气净化、气体转化、甲醇合成和甲醇精制等环节。
首先,将天然气或煤炭进行气化,生成合成气。
气化反应需要高温高压环境下进行,主要反应为C+H2O=CO+H2、气化产物中含有一定量的一氧化碳和氢气。
接下来,对合成气进行净化。
合成气中的杂质如硫化物、氨、氯化物等需要被去除,以保证后续反应的顺利进行。
净化工艺主要包括酸性气体的吸收、氢气和一氧化碳的选择性吸附等。
然后,将净化后的合成气进行转化。
转化主要是通过催化剂的作用,将一氧化碳和二氧化碳转化为甲醇。
转化反应的主要反应为CO+2H2=CH3OH。
该反应需要适宜的温度和压力条件,并且需要选择合适的催化剂。
最后,将合成气中生成的甲醇进行精制。
精制工艺主要包括蒸馏、吸附和冷凝等过程,以去除甲醇中的杂质,得到高纯度的甲醇产品。
二、天然气重整法天然气重整法是一种以天然气为原料生产甲醇的工艺。
该工艺流程包括重整、甲醇合成和甲醇精制等环节。
首先,将天然气进行重整反应,生成合成气。
重整反应主要是将天然气中的甲烷和水蒸气在催化剂的作用下进行反应,生成氢气和一氧化碳。
重整反应的主要反应为CH4+H2O=CO+3H2接下来,将重整反应生成的合成气进行甲醇合成。
甲醇合成反应的条件和催化剂与合成气法相似。
最后,对甲醇进行精制,得到高纯度的甲醇产品。
三、甲烷水蒸气重整法甲烷水蒸气重整法是一种以天然气为原料生产甲醇的工艺。
该工艺流程包括甲烷水蒸气重整、甲醇合成和甲醇精制等环节。
首先,将甲烷进行水蒸气重整反应,生成合成气。
重整反应的主要反应为CH4+H2O=CO+3H2接下来,将重整反应生成的合成气进行甲醇合成。
甲醇精馏工艺流程
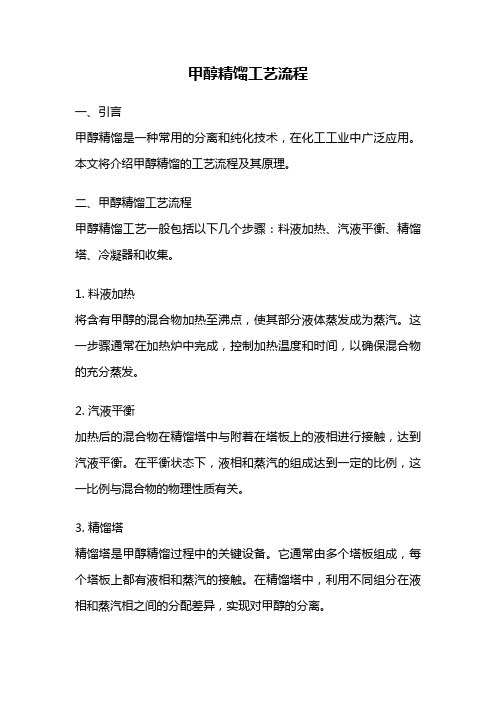
甲醇精馏工艺流程一、引言甲醇精馏是一种常用的分离和纯化技术,在化工工业中广泛应用。
本文将介绍甲醇精馏的工艺流程及其原理。
二、甲醇精馏工艺流程甲醇精馏工艺一般包括以下几个步骤:料液加热、汽液平衡、精馏塔、冷凝器和收集。
1. 料液加热将含有甲醇的混合物加热至沸点,使其部分液体蒸发成为蒸汽。
这一步骤通常在加热炉中完成,控制加热温度和时间,以确保混合物的充分蒸发。
2. 汽液平衡加热后的混合物在精馏塔中与附着在塔板上的液相进行接触,达到汽液平衡。
在平衡状态下,液相和蒸汽的组成达到一定的比例,这一比例与混合物的物理性质有关。
3. 精馏塔精馏塔是甲醇精馏过程中的关键设备。
它通常由多个塔板组成,每个塔板上都有液相和蒸汽的接触。
在精馏塔中,利用不同组分在液相和蒸汽相之间的分配差异,实现对甲醇的分离。
4. 冷凝器精馏塔中的蒸汽进入冷凝器进行冷却,转变为液体。
冷凝器通常采用冷却水循环冷却的方式,使蒸汽迅速冷却,凝结成液体。
冷凝器的效率对甲醇的回收率有重要影响。
5. 收集冷凝后的液体经过收集装置,最终得到纯度较高的甲醇产品。
收集装置通常是一个储存容器,用于收集冷凝后的甲醇液体。
收集后的甲醇可以进一步用于其他工艺或产品的生产。
三、甲醇精馏原理甲醇精馏的原理基于不同组分在液相和蒸汽相之间的分配差异。
在精馏塔中,组分相对挥发性差的物质偏向液相,而相对挥发性较高的物质偏向蒸汽相。
通过不断的汽液平衡和塔板间的传质传热,甲醇与其他组分逐渐分离。
四、总结甲醇精馏是一种常用的分离和纯化技术,其工艺流程包括料液加热、汽液平衡、精馏塔、冷凝器和收集等步骤。
通过控制加热温度和时间,利用精馏塔中的汽液平衡和塔板间的传质传热,可以实现对甲醇的分离和纯化。
甲醇精馏的原理基于不同组分在液相和蒸汽相之间的分配差异。
精馏工艺在化工工业中具有广泛的应用前景。
通过不断改进工艺流程和设备技术,可以提高甲醇精馏的效率和产量,满足不同领域的需求。
天然气制甲醇工艺流程
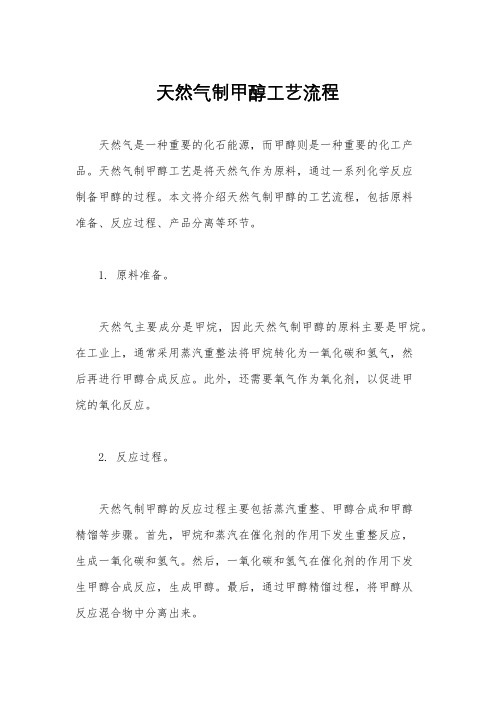
天然气制甲醇工艺流程天然气是一种重要的化石能源,而甲醇则是一种重要的化工产品。
天然气制甲醇工艺是将天然气作为原料,通过一系列化学反应制备甲醇的过程。
本文将介绍天然气制甲醇的工艺流程,包括原料准备、反应过程、产品分离等环节。
1. 原料准备。
天然气主要成分是甲烷,因此天然气制甲醇的原料主要是甲烷。
在工业上,通常采用蒸汽重整法将甲烷转化为一氧化碳和氢气,然后再进行甲醇合成反应。
此外,还需要氧气作为氧化剂,以促进甲烷的氧化反应。
2. 反应过程。
天然气制甲醇的反应过程主要包括蒸汽重整、甲醇合成和甲醇精馏等步骤。
首先,甲烷和蒸汽在催化剂的作用下发生重整反应,生成一氧化碳和氢气。
然后,一氧化碳和氢气在催化剂的作用下发生甲醇合成反应,生成甲醇。
最后,通过甲醇精馏过程,将甲醇从反应混合物中分离出来。
3. 产品分离。
甲醇合成反应产生的混合物中除了甲醇外,还包含未反应的气体和其他杂质。
因此,需要进行产品分离,将甲醇从混合物中提取出来。
通常采用蒸馏、吸附、结晶等方法进行产品分离,得到纯度较高的甲醇产品。
4. 工艺优化。
天然气制甲醇的工艺流程需要根据原料性质、反应条件等因素进行优化。
例如,在蒸汽重整反应中,催化剂的选择、反应温度和压力的控制等都会影响反应的效果。
在甲醇合成反应中,催化剂的活性和选择性对甲醇的产率和纯度有重要影响。
因此,工艺优化是提高天然气制甲醇效率和产品质量的关键。
总之,天然气制甲醇工艺流程包括原料准备、反应过程、产品分离和工艺优化等环节。
通过合理的工艺设计和操作,可以实现天然气向甲醇的高效转化,为化工行业提供了重要的甲醇资源。
甲醇生产流程
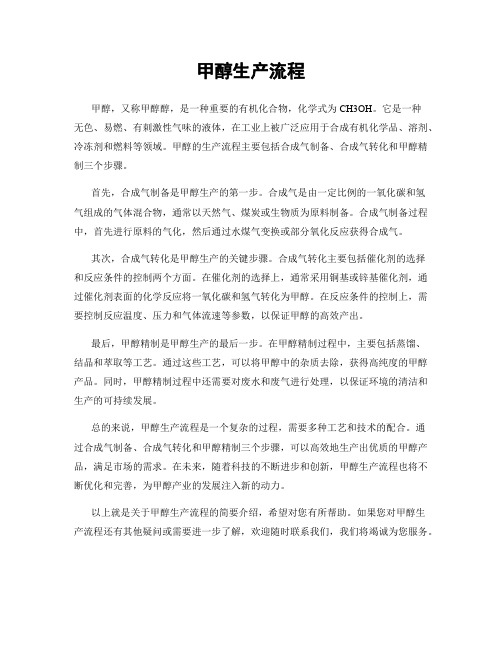
甲醇生产流程甲醇,又称甲醇醇,是一种重要的有机化合物,化学式为CH3OH。
它是一种无色、易燃、有刺激性气味的液体,在工业上被广泛应用于合成有机化学品、溶剂、冷冻剂和燃料等领域。
甲醇的生产流程主要包括合成气制备、合成气转化和甲醇精制三个步骤。
首先,合成气制备是甲醇生产的第一步。
合成气是由一定比例的一氧化碳和氢气组成的气体混合物,通常以天然气、煤炭或生物质为原料制备。
合成气制备过程中,首先进行原料的气化,然后通过水煤气变换或部分氧化反应获得合成气。
其次,合成气转化是甲醇生产的关键步骤。
合成气转化主要包括催化剂的选择和反应条件的控制两个方面。
在催化剂的选择上,通常采用铜基或锌基催化剂,通过催化剂表面的化学反应将一氧化碳和氢气转化为甲醇。
在反应条件的控制上,需要控制反应温度、压力和气体流速等参数,以保证甲醇的高效产出。
最后,甲醇精制是甲醇生产的最后一步。
在甲醇精制过程中,主要包括蒸馏、结晶和萃取等工艺。
通过这些工艺,可以将甲醇中的杂质去除,获得高纯度的甲醇产品。
同时,甲醇精制过程中还需要对废水和废气进行处理,以保证环境的清洁和生产的可持续发展。
总的来说,甲醇生产流程是一个复杂的过程,需要多种工艺和技术的配合。
通过合成气制备、合成气转化和甲醇精制三个步骤,可以高效地生产出优质的甲醇产品,满足市场的需求。
在未来,随着科技的不断进步和创新,甲醇生产流程也将不断优化和完善,为甲醇产业的发展注入新的动力。
以上就是关于甲醇生产流程的简要介绍,希望对您有所帮助。
如果您对甲醇生产流程还有其他疑问或需要进一步了解,欢迎随时联系我们,我们将竭诚为您服务。
甲醇合成工艺流程

甲醇合成工艺流程
《甲醇合成工艺流程》
甲醇是一种重要的化工原料,广泛用于化工、医药、塑料等领域。
甲醇的合成工艺流程是一项复杂的化工过程,需要经过多道工序才能完成。
下面我们来简单介绍一下甲醇合成的工艺流程。
首先,甲醇的合成主要采用的是气相催化法。
该方法以一氧化碳和氢气为原料,经过催化剂的作用,进行一系列化学反应,最终产生甲醇。
整个工艺主要包括气体净化、气体混合、催化反应、产品分离等几个关键步骤。
气体净化是甲醇合成的第一步,主要是通过一系列的吸附、洗涤等操作,将原料气体中的杂质去除,确保进入催化反应器的气体是纯净的。
然后将经过净化的一氧化碳和氢气进行合并混合,按照一定的配比进入催化反应器中。
催化反应是甲醇合成的关键步骤,这一步需要催化剂的作用,将一氧化碳和氢气进行催化转化成甲醇。
催化反应器的设计和操作对反应效率和产物纯度有着重要的影响,需要进行精密控制。
最后,经过催化反应生成的混合气体中含有未反应的气体、甲醇和水等产物,需要进行产品分离。
通过冷凝、蒸馏、吸附等工艺,将甲醇从混合气体中分离出来,得到高纯度的甲醇产品。
以上就是甲醇合成的简要工艺流程,整个过程需要综合考虑原料质量、反应条件、催化剂选择等因素,才能获得高效、可靠的甲醇生产工艺。
随着化工技术的进步,甲醇合成工艺也在不断改进和完善,为甲醇产业的发展提供了更好的支持。
甲醇工艺流程介绍
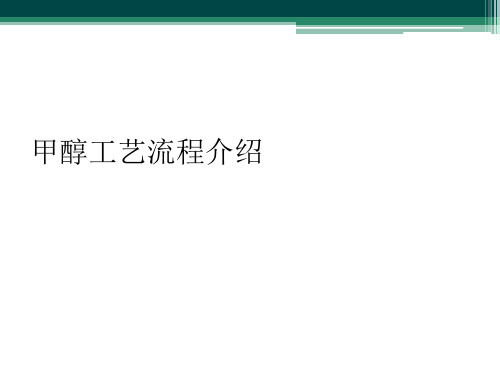
2021/7/17
24
转化工段
本工段的任务是将原料气中的甲烷转化成合成甲醇所用的有效气体 CO和H2。本装置采用加压催化部分氧化法。焦炉气催化部分氧化法, 是将焦炉气中的氧烃类(甲烷、乙烷等)进行部分氧化和蒸汽转化反应, 在转化炉中首先发生H2、CH4与O2的部分氧化燃烧反应,然后气体进入 催化剂层进行甲烷、乙烷等与蒸汽的转化反应。所以这个方法也称为自 热转化法。
甲醇工艺流程介绍
本工艺任务为:将焦炉气(CO:,CO2:,H2:, CH4:,N2:,Ar+O2:,H2S:250mg/m3(标),COS: 250mg/m3(标),CmHn:)通过气体脱硫除去无机硫和有机 硫,使其能够作为转化的原料气,在转化炉内脱硫气与空分 来%氧气燃烧2H2+O2=2H2O放出热供给CH4 + H2O =CO + 3H2甲烷蒸汽转化反应得到组成
2021/7/17
25
2021/7/17
26
2021/7/17
27
饱 和 脱硫气 塔 氧气
去合成压缩
三 分
2021/7/17
加 热 炉
转 化 炉
高 压 蒸 汽 高废
加 热 器
III
低 压 蒸 汽
低废
水
二
冷 器
分
加 热 器
加 热 器 I
一 分
28
工艺流程简述
自脱硫工段来的焦炉气(350℃、2.4MPa(A)),进入转化工段饱和塔 内,与塔顶下来的循环热水接触,使焦炉气被水蒸汽饱和,使出塔气H2O/ 干气比达到0.591:1。饱和塔内循环的热水为本工段回收的工艺冷凝液。 出饱和塔的混合气经蒸汽混合器。 再进入加热炉的一段预热器,温升至 500℃ , 进 入 转 化 炉 顶 部 喷 嘴 。 空 分 送 来 的 压 力 3.0MPa(A) 的 纯 氧 气 及 6.4MPa(G)次高压过热蒸汽(480℃)按比例进入混合罐中,由混合罐出 来的H2O/O2比为1:1比例混合,富氧气进入转化炉顶部喷嘴外层夹套, 焦炉气蒸汽混合气与 富氧气经喷嘴喷出,H2和O2立即发生氧化反应,在 炉膛顶部燃烧,火焰中心温度达1050~1150℃,高温气体随即向下进入转 化催化剂床,发生转化反应:
天然气制甲醇的工艺流程
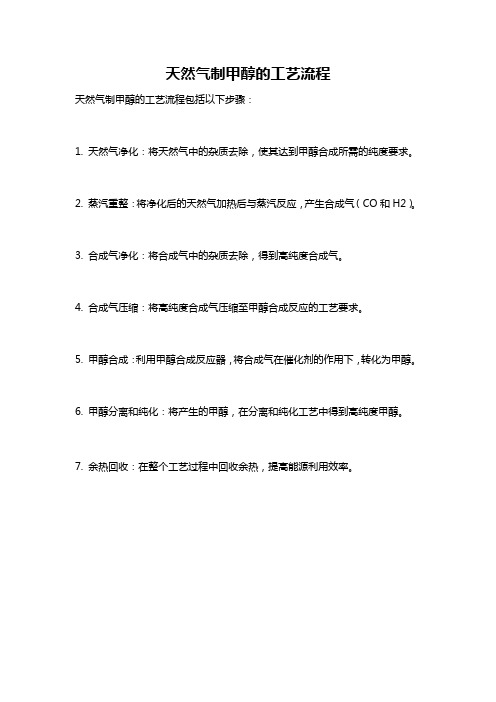
天然气制甲醇的工艺流程
天然气制甲醇的工艺流程包括以下步骤:
1. 天然气净化:将天然气中的杂质去除,使其达到甲醇合成所需的纯度要求。
2. 蒸汽重整:将净化后的天然气加热后与蒸汽反应,产生合成气(CO和H2)。
3. 合成气净化:将合成气中的杂质去除,得到高纯度合成气。
4. 合成气压缩:将高纯度合成气压缩至甲醇合成反应的工艺要求。
5. 甲醇合成:利用甲醇合成反应器,将合成气在催化剂的作用下,转化为甲醇。
6. 甲醇分离和纯化:将产生的甲醇,在分离和纯化工艺中得到高纯度甲醇。
7. 余热回收:在整个工艺过程中回收余热,提高能源利用效率。
甲醇工艺流程简述

甲醇工艺流程简述甲醇是一种无色、挥发性较强的液体化合物,也是常见的有机化学品之一、甲醇的制备工艺流程通常分为合成气制甲醇和天然气制甲醇两种。
下面将对这两种制备工艺流程进行详细的描述。
一、合成气制甲醇工艺流程合成气制甲醇工艺是将天然气(或石油)转化成合成气,然后通过催化反应将合成气转化成甲醇的一种工艺。
合成气主要由一氧化碳和氢气组成,生成甲醇的反应是以一氧化碳为起始物质,经过一系列的反应途径得到甲醇。
1.准备原料:当用天然气作为原料时,首先需要通过净化处理去除其中的杂质,然后将天然气和蒸汽混合,在蒸汽重整反应器中进行催化重整反应,产生合成气。
2.合成气的催化:将合成气送入低压合成气转化反应器,在催化剂的催化下,一氧化碳和氢气发生醇合反应,生成甲醇。
3.分离和纯化:甲醇在反应混合物中以蒸汽的形式存在,需要通过冷凝和分离装置将甲醇与其他组分分离开来。
可以采用常压或低压蒸馏进行分离和纯化。
4.精制和储存:通过精制过程,去除甲醇中的杂质并调节甲醇的含量和纯度,然后将精制后的甲醇储存起来,以备后续使用或销售。
二、天然气制甲醇工艺流程天然气制甲醇工艺是以天然气为原料进行甲醇合成的工艺。
相对于合成气制甲醇,天然气制甲醇工艺更简化,生产成本更低。
1.原料处理:天然气在经过净化处理后,去除其中的硫化物、水、杂质等物质,以减少对催化剂的毒性影响。
2.反应装置:将处理好的天然气与水蒸气混合,进入反应装置,进行催化转化反应。
通常采用气相催化反应器和流化床反应器。
3.催化反应:在反应装置中,天然气与水蒸气经过区域催化剂层,发生反应生成合成气,然后经过醇化层的催化作用,生成甲醇。
4.分离和纯化:通过分离和纯化设备将反应混合物中的甲醇与其他组分进行分离纯化。
一般采用压力和温度以及蒸馏等方法进行分离。
5.精制与储存:将精制后的甲醇进行附加处理,去除其中的杂质和溶解的气体,提高甲醇的纯度。
然后将精制后的甲醇储存在储罐中,供以后使用或销售。
甲醇工艺流程概述

甲醇工艺流程概述(1)焦炉气压缩自气柜来的温度25℃,压力为200mmH2O(表)的焦炉气进入压缩机,经三级压缩后,压力升高到2.5 MPa(表)、温度升高到140℃,经三级出口缓冲器缓冲稳压后进入冷却器,冷却至40℃后由总管送往精脱硫工段。
(2)精脱硫来自焦炉气压缩工段的焦炉气经管道输送到本工段,经过过滤器和预脱硫槽滤去油雾和脱除无机硫后经在转化装置中提温到300℃后,焦炉气经铁钼转化器气体中的有机硫在此转化为无机硫,气体中的氧也在此与氢反应生成水。
加氢转化后的气体含无机硫约245mg/Nm3,进入中温脱硫槽脱去绝大部分的无机硫。
之后经过钴钼转化器将残余的有机硫进行转化,再经中温氧化锌脱硫槽,使气体中的总硫达到0.1ppm。
出氧化锌脱硫槽的气体压力约为2.3 MPa,温度约为350℃送往转化装置。
(3)转化脱硫后的焦炉气与饱和蒸汽混合,经焦炉气预热器、预热炉预热至660℃进入转化炉上部,与预热后的氧气充分混合后自上而下进入催化床层进行氧化反应放出热量,并很快进入催化床层,进行以下反应:① 2H2+O2=H2O+115.48 kcal② 2CH4+O2=2CO+4H2+17.0 kcal③ CH4+H2O=CO+3H2-49.3 kcal④ CH4+CO2=2CO+2H2-59.1 kcal⑤ CO+H2O=CO2+H2+9.8 kcal反应最终按(5)式达到平衡,反应后的转化气由转化炉底部引出,经废热锅炉回收热量副产蒸汽,转化气温度降为540℃。
然后经焦炉气预热器使其温度降为370℃,并经焦炉气初预热器、锅炉给水预热器、再沸器、脱盐水预热器回收热量后,经水冷器进一步冷却并分离掉工艺冷凝液后,送往合成气压缩工段。
(4)合成气压缩来自转化工段的新鲜气,温度40℃,压力2.1 MPa(A),进入合成气压缩机一段压缩后,进入循环段与来自甲醇合成的循环气混合,压缩至 6.0 MPa(A)。
压缩机出口合成气送往甲醇合成。
煤制甲醇的四个工艺过程

煤制甲醇的四个工艺过程煤制甲醇是指利用煤作为原料,通过化学反应将其转化为甲醇的过程。
煤是一种丰富的化石燃料资源,其主要成分是碳、氢、氧、氮和硫等元素。
煤制甲醇的工艺过程主要包括煤气化、气体净化、甲醇合成和甲醇精制四个步骤。
下面将详细介绍这四个工艺过程。
1. 煤气化煤气化是将煤在高温下进行化学反应,将其转化为气体燃料和化工原料的过程。
该过程主要通过两种方法进行:一种是氧气气化,即利用氧气在高温下与煤发生反应,产生合成气和焦炭;另一种是空气气化,即利用空气氧化煤,产生气化气和灰渣。
气化产物中的合成气是煤制甲醇的重要原料,它主要由一氧化碳、二氧化碳、氢气和甲烷等组成。
2. 气体净化气体净化是将煤气化产生的合成气进行净化处理,去除其中的杂质和有害物质的过程。
合成气中的杂质主要包括硫化物、氨、焦油、灰尘等。
这些杂质会对催化剂产生毒性影响,降低甲醇合成的效果。
因此,在甲醇合成之前,需要对合成气进行精细处理和净化。
这一过程主要通过吸附、洗涤、除尘和脱硫等方法进行。
3. 甲醇合成甲醇合成是将净化后的合成气进行化学反应,将一氧化碳和氢气转化为甲醇的过程。
该过程主要通过催化剂催化进行,常用的催化剂包括铜锌基和锌铬基等。
在反应过程中,一氧化碳和氢气在催化剂的作用下发生反应,生成甲醇。
甲醇是一种无色、可燃液体,可以作为燃料、溶剂和化学原料等。
甲醇合成反应具有一定的热力学和动力学特征,需要在适宜的温度、压力和催化剂条件下进行。
4. 甲醇精制甲醇精制是将合成甲醇进行分离和提纯的过程。
在甲醇合成反应中,会生成一些副反应产物和杂质,如二甲醚、水、硫化物等。
这些物质会对甲醇的质量和纯度产生影响,因此需要进行精制处理。
通常采用蒸馏、萃取、吸附、冷却等技术进行甲醇的分离和提纯。
通过这些工艺,可以使甲醇的纯度达到工业要求,并满足不同行业的使用需求。
总结起来,煤制甲醇的四个工艺过程包括煤气化、气体净化、甲醇合成和甲醇精制。
这些过程对于制备高质量的甲醇至关重要,可以充分利用煤资源,实现清洁能源的生产和利用。
甲醇生产工艺流程概况

工艺流程简述1、转化工艺流程概述界区外来的天然气,分成两路,一路原料气通过原料气分离器V-0101分离出其中水、石脑油等冷凝物后,送至燃料气脱硫槽R-0101A/B/C/D脱硫后作为转化炉和开工锅炉的燃料天然气。
另一路原料气通过原料气分离器BS-101分离出其中水、石脑油等冷凝物后,补入一定量从氢回收装置送来的氢气后进入原料气预热器加热,依次通过常温脱硫槽(BR-0101A/B)、高温钴钼加氢脱硫槽(BR-102)、高温氧化锌脱硫槽(R-101 A/B)脱硫,使原料天然气中的总硫含量降到0.1ppm 以下,脱硫后的天然气作为甲醇生产装置的工艺天然气送至原料混合器MIXER中。
在原料混合器MIXER中工艺天然气、1. 9Mpa的工艺蒸汽、CO2,按H2O/C (2.95—3.05):1的比例混合后,通过混合气预热器E-104,加热到500℃,在1.6Mpa的压力下进入一段转化炉。
一段转化炉用天然气、合成驰放气、合成闪蒸气作为燃料为反应提供热量。
混合原料气在850℃温度下通过转化管中触媒层,从一段转化炉出来的转化气,温度760℃,压力1.2MPa 残留甲烷≤10%。
由一段转化炉下部集气总管输至二段转化炉顶混合烧咀,用于优化调节的部分工艺天然气和回收的氢气在集气总管上加入,来自博源联化公司的氧气1.5Mpa、120℃与部分工艺蒸汽混合后从混合烧咀顶部加入;在混合烧咀出口处的转化气与氧气混合在高温下自燃,进行部分燃烧反应放出热量,使入二段转化炉的混合气体温度升至1100℃再次进入二段转化催化剂床层,对残余甲烷进行转化,出二段转化炉的高温转化气1.15Mpa、950℃进入废热锅炉产生高压蒸汽,回收部分热量,并经其它换热器利用余热后,转化气一分为二,一部分进入原甲醇装置天然气预热器出口总管,并经原甲醇装置回收利用余热,最终冷却至40℃分离后入原甲醇装置合成气压缩机压缩入合成。
另一部分通过调节阀控制进入新增的转化B系列后工序,最终冷却至40℃分离后入新增合成气压缩机压缩入合成。
甲醇工艺流程简述

甲醇工艺流程简述嘿,你知道甲醇吗?这可是个相当有趣的东西呢!今天我就来给你讲讲甲醇的工艺流程,就像讲故事一样,可别走神哦。
我有个朋友叫小李,他就在一个生产甲醇的工厂工作。
有一次我去他那儿参观,那可真是让我大开眼界。
甲醇的生产,得从原料说起。
一般来说呢,最常见的原料是天然气、煤炭或者生物质。
这就好比做饭,你得先有米或者面之类的原料吧。
要是用天然气作原料的话,那首先得对天然气进行预处理。
你想啊,天然气从地下采出来,里面可能有各种各样的杂质,就像咱们买回来的菜,上面可能有泥啊土啊的,得洗干净才能下锅。
天然气要把那些硫化物之类的杂质去除掉,这可是很关键的一步。
要是不去掉这些杂质,就像是炒菜的时候锅里有沙子,那后面的反应可就乱套了。
接下来就是转化反应啦。
把经过预处理的天然气和水蒸气混合,然后在高温和催化剂的作用下,发生一系列复杂的化学反应。
这过程就像是一场魔法表演,原本的天然气和水蒸气就变成了合成气,主要是一氧化碳和氢气。
我当时就问小李:“这就像变魔术一样,怎么就变成了新的东西了呢?”小李笑着说:“这就是化学的奇妙之处啊,分子们重新组合就有了新的产物。
”有了合成气之后呢,就到了合成甲醇这一步了。
这就像是盖房子,有了砖(合成气),就开始砌墙(合成甲醇)了。
合成气在特定的反应条件下,在另一种催化剂的作用下,一氧化碳和氢气发生反应生成甲醇。
这个反应条件可严格了,温度、压力都得控制得刚刚好。
我好奇地问小李:“这要是温度或者压力不对了会咋样呢?”小李瞪大了眼睛说:“那可不得了,可能就生成不了甲醇了,或者会产生一些乱七八糟的副产物,就像你本来想烤个蛋糕,结果温度不对,烤成了一块黑乎乎的东西。
”在合成甲醇的过程中,还会有一些没有反应完全的气体,这可不能浪费啊。
就像我们吃饭不能剩太多饭菜一样。
这些未反应的气体要进行循环利用,再送回到反应系统里继续参与反应。
这多像一个循环的生态系统啊,资源充分利用,一点都不浪费。
甲醇合成之后呢,还得进行精制。
甲醇工艺流程说明

目录绪论:第一章工艺流程综述一、焦炉气生产流程二、甲醇生产工艺流程1、空分工艺流程2、精脱硫工艺流程3、转化工艺流程4、合成工艺流程5、甲醇精馏工艺流程第二章基本理论及操作原理1、空分部分2、精脱硫部分3、转化部分4、合成部分5、甲醇精馏部分6、离心式压缩机7、往复式压缩机8、泵类第三章岗位操作法(依据建滔甲醇工艺流程)1、空分岗位2、净化岗位3、合成岗位4、精馏岗位5、空气压缩机6、氧气压缩机7、焦炉气压缩机8、氮气压缩机9、合成气压缩机用焦炉气作原料生产甲醇操作培训教材绪论:焦炭生产过程中,必然伴生出大量荒煤气,荒煤气的主要成分为:H2、CH4、CnHm、CO、CO2,以及少量的N2、O2.焦油、苯,萘、硫化物……。
过去,荒煤气经脱焦油、苯、萘,和粗脱硫后,一部分作为炼焦燃料;其余大部分或做城市燃气,或用做发电厂燃料。
有些地方干脆白白放空燃烧掉了,给周围环境造成严重污染。
我国最重要的煤炭及炼焦生产省份——山西省,目前就处在处处“狼烟”,城乡环境不堪重负的状况。
为使宝贵的煤炭资源得到充分合理的利用,改变我国中西部地区的落后面貌,扭转炼焦企业污染环境的局面,变废为宝,利用焦炉气做化工原料是最佳选择。
根据焦炉煤气的成分,用焦炉煤气生产甲醇、合成氨,应该是成熟的工艺。
他们与用煤、油气,用天然气转化生产甲醇、合成氨,在气体成分比例上有差别,但基本组成上并无差异。
由化工部的二设计院设计,建滔(河北)焦化厂使用的百万吨、/年甲醇装置已为焦炉气综合利用探索出了成功经验。
必将在全国各地兴建起一大批更为先进的企业,结出更加丰硕的成果。
为适应迅速发展的焦炉气生产甲醇操作需要,培养系统综合性的人才,我们把工艺基本原理知识和操作经验教训相结合,汇编成下面的培训教材,并期待在今后的生产实践中不断补充完善。
第一章工艺流程综述一、焦炉气生产流程焦炉气生产流程是指焦炉气的生产、收集、再经过气液分离、洗涤,电捕除焦油,脱硫,除氨,洗脱笨等工序生产出合格焦炉气的工艺过程。
甲醇工艺流程简述
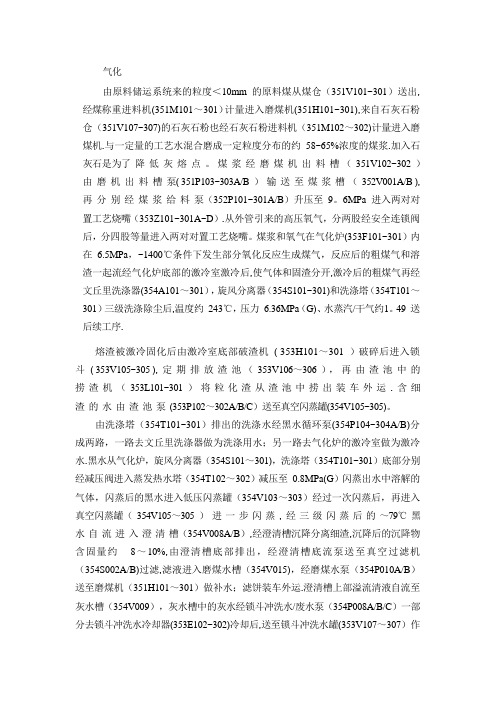
气化由原料储运系统来的粒度<10mm的原料煤从煤仓(351V101~301)送出,经煤称重进料机(351M101~301)计量进入磨煤机(351H101~301),来自石灰石粉仓(351V107~307)的石灰石粉也经石灰石粉进料机(351M102~302)计量进入磨煤机.与一定量的工艺水混合磨成一定粒度分布的约58~65%浓度的煤浆.加入石灰石是为了降低灰熔点。
煤浆经磨煤机出料槽(351V102~302)由磨机出料槽泵( 351P103~303A/B)输送至煤浆槽(352V001A/B ), 再分别经煤浆给料泵(352P101~301A/B)升压至9。
6MPa进入两对对置工艺烧嘴(353Z101~301A~D).从外管引来的高压氧气,分两股经安全连锁阀后,分四股等量进入两对对置工艺烧嘴。
煤浆和氧气在气化炉(353F101~301)内在6.5MPa,~1400℃条件下发生部分氧化反应生成煤气,反应后的粗煤气和溶渣一起流经气化炉底部的激冷室激冷后,使气体和固渣分开,激冷后的粗煤气再经文丘里洗涤器(354A101~301),旋风分离器(354S101~301)和洗涤塔(354T101~301)三级洗涤除尘后,温度约243℃,压力6.36MPa(G)、水蒸汽/干气约1。
49送后续工序.熔渣被激冷固化后由激冷室底部破渣机( 353H101~301)破碎后进入锁斗( 353V105~305 ), 定期排放渣池(353V106~306),再由渣池中的捞渣机(353L101~301)将粒化渣从渣池中捞出装车外运 . 含细渣的水由渣池泵(353P102~302A/B/C)送至真空闪蒸罐(354V105~305)。
由洗涤塔(354T101~301)排出的洗涤水经黑水循环泵(354P104~304A/B)分成两路,一路去文丘里洗涤器做为洗涤用水;另一路去气化炉的激冷室做为激冷水.黑水从气化炉,旋风分离器(354S101~301),洗涤塔(354T101~301)底部分别经减压阀进入蒸发热水塔(354T102~302)减压至0.8MPa(G)闪蒸出水中溶解的气体,闪蒸后的黑水进入低压闪蒸罐(354V103~303)经过一次闪蒸后,再进入真空闪蒸罐(354V105~305)进一步闪蒸, 经三级闪蒸后的~79℃黑水自流进入澄清槽(354V008A/B),经澄清槽沉降分离细渣,沉降后的沉降物含固量约8~10%,由澄清槽底部排出,经澄清槽底流泵送至真空过滤机(354S002A/B)过滤,滤液进入磨煤水槽(354V015),经磨煤水泵(354P010A/B)送至磨煤机(351H101~301)做补水;滤饼装车外运.澄清槽上部溢流清液自流至灰水槽(354V009),灰水槽中的灰水经锁斗冲洗水/废水泵(354P008A/B/C)一部分去锁斗冲洗水冷却器(353E102~302)冷却后,送至锁斗冲洗水罐(353V107~307)作为锁斗的冲洗水,另一部分作为污水,连续排放至污水处理;再有一部分低压灰水泵(354P005A/B/C)灰水去蒸发热水塔与中压闪蒸气逆流接触,传质传热,送至洗涤塔(354T101~301)做为系统补充水循环使用。
甲醇生产工艺流程
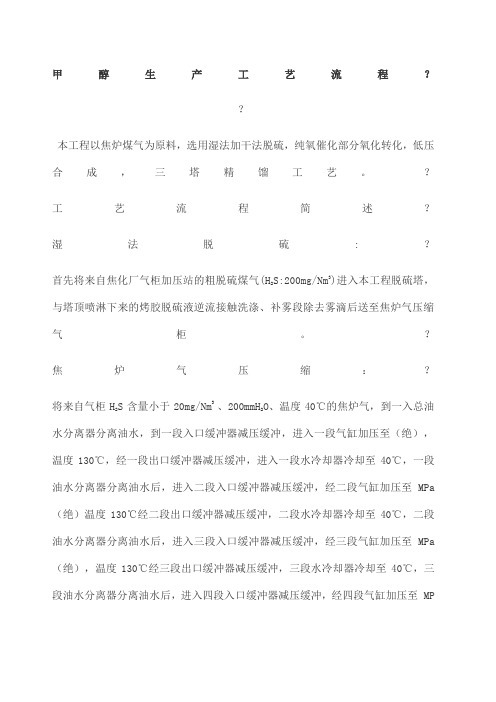
甲醇生产工艺流程??本工程以焦炉煤气为原料,选用湿法加干法脱硫,纯氧催化部分氧化转化,低压合成,三塔精馏工艺。
?工艺流程简述?湿法脱硫:?首先将来自焦化厂气柜加压站的粗脱硫煤气(H2S:200mg/Nm3)进入本工程脱硫塔,与塔顶喷淋下来的烤胶脱硫液逆流接触洗涤、补雾段除去雾滴后送至焦炉气压缩气柜。
?焦炉气压缩:?将来自气柜H2S含量小于20mg/Nm3 、200mmH2O、温度40℃的焦炉气,到一入总油水分离器分离油水,到一段入口缓冲器减压缓冲,进入一段气缸加压至(绝),温度130℃,经一段出口缓冲器减压缓冲,进入一段水冷却器冷却至40℃,一段油水分离器分离油水后,进入二段入口缓冲器减压缓冲,经二段气缸加压至 MPa (绝)温度130℃经二段出口缓冲器减压缓冲,二段水冷却器冷却至40℃,二段油水分离器分离油水后,进入三段入口缓冲器减压缓冲,经三段气缸加压至 MPa (绝),温度130℃经三段出口缓冲器减压缓冲,三段水冷却器冷却至40℃,三段油水分离器分离油水后,进入四段入口缓冲器减压缓冲,经四段气缸加压至 MPa,温度130℃,经四段出口缓冲器减压缓冲,四段水冷却器冷却至40℃,四段油水分离器分离油水后,送精脱硫转化工段。
?转化:?焦炉气来自压缩机的压力,温度40℃的焦炉气经过过滤器(F61201A/B).过滤器分离掉油水与杂质。
再经预脱硫槽脱除大部分无机硫后去转化工段焦炉气初预热器预热300℃、压力。
回精脱硫的一级加氢转化器,气体中的有机硫在此进行加氢转化生成无机硫;不饱和烃生成饱和烃。
加氢后的气体进入中温脱硫槽(D61203ABC)脱除绝大部分的无机硫;之后再经过二级加氢转化器(D61205)将残余的有机硫进行转化;最后经过中温氧化锌(D61204AB)把关。
使出口焦炉气中总硫<后送至转化工序。
??精脱硫来的29196Nm3/h焦炉气总硫和转化废热锅炉自产蒸气h混合进入C60602焦炉气预热器〈壳程〉预热330℃,进入B60601预热炉预热至660℃,进入D606 01转化炉混合室,与来自空分氧气5864m3/h,纯氧和经过B60601上段预热至300℃h自产蒸汽的进入转化炉上段,进行纯氧蒸汽部分氧化燃烧、,温度达950-1250℃≤%。
煤制甲醇工艺流程简述
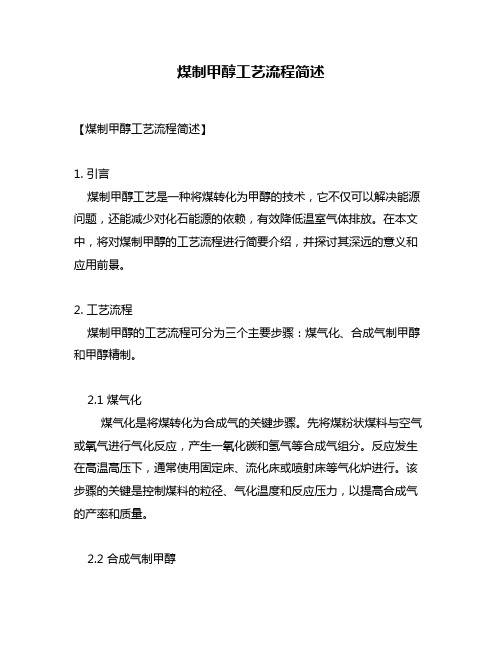
煤制甲醇工艺流程简述【煤制甲醇工艺流程简述】1. 引言煤制甲醇工艺是一种将煤转化为甲醇的技术,它不仅可以解决能源问题,还能减少对化石能源的依赖,有效降低温室气体排放。
在本文中,将对煤制甲醇的工艺流程进行简要介绍,并探讨其深远的意义和应用前景。
2. 工艺流程煤制甲醇的工艺流程可分为三个主要步骤:煤气化、合成气制甲醇和甲醇精制。
2.1 煤气化煤气化是将煤转化为合成气的关键步骤。
先将煤粉状煤料与空气或氧气进行气化反应,产生一氧化碳和氢气等合成气组分。
反应发生在高温高压下,通常使用固定床、流化床或喷射床等气化炉进行。
该步骤的关键是控制煤料的粒径、气化温度和反应压力,以提高合成气的产率和质量。
2.2 合成气制甲醇合成气制甲醇是利用合成气来合成甲醇的过程。
合成气主要由一氧化碳和氢气组成,通过催化剂和适当的反应条件下进行甲醇合成反应。
该反应通常在低温低压的条件下进行,采用缓冲床或流化床反应器,并通过一系列的催化剂进行催化。
此步骤的关键是选择合适的催化剂、控制反应温度和压力,并处理合成气中的杂质,以提高甲醇的纯度和产率。
2.3 甲醇精制甲醇精制是将合成气制得的甲醇进行精制和提纯的过程。
甲醇粗品中通常含有水、氢气、一氧化碳和各类杂质,需要经过一系列的脱水、吸附、分馏等操作,以获得高纯度的甲醇产品。
此步骤的关键是选择适当的精制工艺和精制设备,使甲醇满足工业使用和乙醇汽油等燃料行业的需求。
3. 深远意义和应用前景煤制甲醇工艺具有重要的经济、环境和能源意义。
3.1 经济意义煤制甲醇可以有效利用煤炭资源,降低对原油、天然气等化石能源的依赖程度,提高我国能源安全。
甲醇在化工、医药、农药等领域有着广泛的应用,煤制甲醇工艺的发展将带动产业转型升级,促进经济可持续发展。
3.2 环境意义煤炭的燃烧会释放大量的二氧化硫、氮氧化物和颗粒物,对环境和人类健康造成极大危害。
而甲醇的燃烧过程中,排放的有害气体和颗粒物较少,对大气环境污染较小。
甲醇生产工艺操作流程

甲醇回收蒸馏一、生产流程冷凝器→成品冷却器↑↓↓粗甲醇→预热器→甲醇塔去成品罐二、工艺操作1、开机前准备⑴检查各设备和管道、阀门,将阀门开关到正确位置。
⑵联系供电、供水、供汽部门,按计划时间供电、供水、供汽和空气。
2、开机:打开1、2冷凝器的循环水,3冷凝器的一次水,成品冷却器的一次水,排废泵的冷却水。
通知粗甲醇泵启动,给甲醇塔进料,使塔的液位达到玻璃管液位计的中部停止。
启动进蒸汽阀,使甲醇塔缓缓加热,使塔釜温度达到规定数值。
启动回流泵,使回流罐的液位保持在玻璃管液位计的中部。
待甲醇塔顶温达到64~66℃,塔中温在67~100℃范围内时开始取成品甲醇,同时开始给甲醇塔连续进料。
取甲醇的量和进料量从小到多,慢慢增加,直至达产。
3、停机⑴暂时停机停止甲醇塔进料,继续正常取甲醇,低浓度甲醇另存。
甲醇浓度过低时,停止进蒸汽,待甲醇塔顶温达到30~40℃时,关闭循环水和一次水。
⑵长时间停机停止甲醇塔进料,继续正常取甲醇,低浓度甲醇另存。
进料泵改为加水,塔釜底温104~106℃,塔顶温度101℃,运行1个小时,回流罐的低浓度甲醇另存。
检测无甲醇时停止进蒸汽,待甲醇塔顶温达到30~40℃时,关闭循环水和一次水。
排掉塔釜底的液体排掉冷凝器由型弯底部的液体。
4、操作参数:a、进料浓度40~70%时塔底104~106℃中温67~100℃顶温64~66℃冷凝器3 35℃b、进料浓度96%时塔底92~95℃(开始)中温67~68℃顶温64~66℃冷凝器3 35℃随着塔底废水的增加,其操作参数逐步调整到塔底104~106℃中温67~100℃顶温64~66℃冷凝器3 35℃三、应急预案突然停蒸汽:关掉进料阀门,其它不动。
如果长时间停蒸汽,其它操作按照以上停机顺序进行。
突然停冷却水关掉进料阀门、蒸汽阀门。
- 1、下载文档前请自行甄别文档内容的完整性,平台不提供额外的编辑、内容补充、找答案等附加服务。
- 2、"仅部分预览"的文档,不可在线预览部分如存在完整性等问题,可反馈申请退款(可完整预览的文档不适用该条件!)。
- 3、如文档侵犯您的权益,请联系客服反馈,我们会尽快为您处理(人工客服工作时间:9:00-18:30)。
气化由原料储运系统来的粒度<10mm的原料煤从煤仓(351V101~301)送出,经煤称重进料机(351M101~301)计量进入磨煤机(351H101~301),来自石灰石粉仓(351V107~307)的石灰石粉也经石灰石粉进料机(351M102~302)计量进入磨煤机。
与一定量的工艺水混合磨成一定粒度分布的约58~65%浓度的煤浆。
加入石灰石是为了降低灰熔点。
煤浆经磨煤机出料槽(351V102~302)由磨机出料槽泵(351P103~303A/B)输送至煤浆槽(352V001A/B),再分别经煤浆给料泵(352P101~301A/B)升压至9.6MPa进入两对对置工艺烧嘴(353Z101~301A~D)。
从外管引来的高压氧气,分两股经安全连锁阀后,分四股等量进入两对对置工艺烧嘴。
煤浆和氧气在气化炉(353F101~301)内在6.5MPa,~1400℃条件下发生部分氧化反应生成煤气,反应后的粗煤气和溶渣一起流经气化炉底部的激冷室激冷后,使气体和固渣分开,激冷后的粗煤气再经文丘里洗涤器(354A101~301),旋风分离器(354S101~301)和洗涤塔(354T101~301)三级洗涤除尘后,温度约243℃,压力6.36MPa(G)、水蒸汽/干气约1.49送后续工序。
熔渣被激冷固化后由激冷室底部破渣机(353H101~301)破碎后进入锁斗(353V105~305),定期排放渣池(353V106~306),再由渣池中的捞渣机(353L101~301)将粒化渣从渣池中捞出装车外运。
含细渣的水由渣池泵(353P102~302A/B/C)送至真空闪蒸罐(354V105~305)。
由洗涤塔(354T101~301)排出的洗涤水经黑水循环泵(354P104~304A/B)分成两路,一路去文丘里洗涤器做为洗涤用水;另一路去气化炉的激冷室做为激冷水。
黑水从气化炉,旋风分离器(354S101~301),洗涤塔(354T101~301)底部分别经减压阀进入蒸发热水塔(354T102~302)减压至0.8MPa(G)闪蒸出水中溶解的气体,闪蒸后的黑水进入低压闪蒸罐(354V103~303)经过一次闪蒸后,再进入真空闪蒸罐(354V105~305)进一步闪蒸,经三级闪蒸后的~79℃黑水自流进入澄清槽(354V008A/B),经澄清槽沉降分离细渣,沉降后的沉降物含固量约8~10%,由澄清槽底部排出,经澄清槽底流泵送至真空过滤机(354S002A/B)过滤,滤液进入磨煤水槽(354V015),经磨煤水泵(354P010A/B)送至磨煤机(351H101~301)做补水;滤饼装车外运。
澄清槽上部溢流清液自流至灰水槽(354V009),灰水槽中的灰水经锁斗冲洗水/废水泵(354P008A/B/C)一部分去锁斗冲洗水冷却器(353E102~302)冷却后,送至锁斗冲洗水罐(353V107~307)作为锁斗的冲洗水,另一部分作为污水,连续排放至污水处理;再有一部分低压灰水泵(354P005A/B/C)灰水去蒸发热水塔与中压闪蒸气逆流接触,传质传热,送至洗涤塔(354T101~301)做为系统补充水循环使用。
洗涤塔(354T101~301)不足的洗涤水由变换来的工艺冷凝液和高压锅炉给水补充。
蒸发热水塔(354T102~302)顶的闪蒸气经酸性气冷凝器(354E104~304)冷却后,进入酸性气分离器(354V107~307),分离后的气体去变换工段回收热量,分离后的冷凝液返回灰水槽使用。
自低压闪蒸罐的闪蒸气进入低压闪蒸冷凝器(354E101~301)用循环水冷却后,进入低压闪蒸分离器(354V101~301),分离后的气体高点放空,分离后的冷凝液返回灰水槽使用。
真空闪蒸罐顶的闪蒸气经真空闪蒸冷凝器(354E102~302)用循环水冷却后,送至真空闪蒸分离罐(354V106~306),分离后的气体经真空泵(354P103~303)和真空泵分离罐后放空,真空闪蒸分离罐分离的冷凝液自流进入灰水槽(354V009)使用。
变换变换工序的主要目的是将气化送来的粗煤气中的CO经变换反应部分变换成H2,使变换气H2/CO比满足甲醇合成的要求,并根据不同的温度范围产生不同等级的蒸汽进行工艺余热回收。
来自气化工段的水煤气(243℃,6.40MPa(A),水气比为1.49),进变换系统后分成两股:一股作为配气,进入水煤气废热锅炉Ⅱ(371E005)降温到200℃,同时生产1.1MPa(G)饱和蒸汽送至管网,降温后的水煤气进入第三水分离器(371V005)分离出冷凝液;另一股进入水煤气废热锅炉Ⅰ(371E001)温度降至225℃,并生产1.1MPa(G)饱和蒸汽送至管网,降温后的水煤气经第一水分离器(371V002)分离冷凝液后,经中温换热器/蒸汽过热器(371E002)的中温换热器预热至260℃进入变换炉(371R001),变换炉内装有两段耐硫变换催化剂,气体在变换炉中发生变换反应。
出变换炉的变换气CO含量约为8.82%(干),温度约为442℃,依次经中温换热器/蒸汽过热器(371E002)和变换废热锅炉(371E003)温度降至238℃,同时生产2.5MPa(G)饱和蒸汽经蒸汽过热器过热至380℃送管网。
作为配气的水煤气与出变换废热锅炉(371E003)的变换气混合后经中压锅炉给水加热器(371E006)温度降至188℃,然后经低压废热锅炉(371E004)温度降至169℃进入第二水分离器(371V003),低压废热锅炉同时生产0.5MPaG饱和蒸汽送管网。
经第二水分离器(371V003)分离冷凝液后的变换气依次经低压锅炉给水加热器(371E007)(降至153℃)、脱盐水加热器(371E008)、变换气水冷器(371E009)温度降至40℃,然后进入洗氨塔(371T001)。
在洗氨塔底部分离出冷凝液的变换气再用洗涤水洗掉变换气中的氨后送至低温甲醇洗工段。
第一、二、三水分离器(371V002/003/005)分离出的高温冷凝液都进入变换冷凝液槽(371V004),进行闪蒸,闪蒸后的冷凝液经冷凝液泵Ⅰ(371P001A,B)升压后送至气化工段,闪蒸出的不凝气与来自气化的高闪气一起进入冷凝液汽提塔(371T002)的中部。
洗氨塔底部的变换冷凝液经汽提气冷凝分离器预热后进入冷凝液汽提塔的上部,冷凝液汽提塔用0.5MPaG饱和蒸汽从塔的底部进入进行汽提,塔顶出来的汽提气经汽提气冷凝分离器冷却后,含氨不凝气送至硫回收处理,塔底的冷凝液经冷凝液泵II(P002A,B)升压后送气化。
脱盐水站来的脱盐水进入脱盐水加热器(371E008),与变换气换热温度升至95℃后进入除氧器(371V006),净化、甲醇合成来的蒸汽冷凝液也送入除氧器。
除氧器用本工段产生的0.5MPaG低压蒸汽吹入脱氧,除氧后的锅炉给水分为三股,第一股经低压锅炉给水泵I(371P004A,B)升压后一部分经低压锅炉给水加热器预热至150℃后送至水煤气废热锅炉Ⅰ(371E001)、水煤气废热锅炉Ⅱ(371E005)、低压废热锅炉(371E004),另一部分送气化作为仪表冲洗水;第二股经中压锅炉给水泵(371P005A,B)升压后,一分部分直接送至硫回收,另一部分经中压锅炉给水加热器(371E006)预热至190℃后分别送至变换废热锅炉(371E003)和甲醇合成工段使用;第三股经密封水泵(371P006A,B)升压后,一部分直接送至气化作为水洗塔补充用水和热密封水,另一部分经洗涤水冷却器(371E010)冷却至40℃后分别送至洗氨塔作洗涤水和气化工段作冷密封水用。
变换另设有两台高压锅炉给水泵,用于气化工段备用气化炉的水洗塔开车用。
触媒的升温,硫化在0.4MP(A)采用低压氮气循环进行。
低压氮气经氮气循环风机(371C001)升压后经中温换热器换热升温进入氮气电加热炉(371F001)加热至需要温度,然后进入变换炉进行升温还原,从变换炉出来的循环氮气经中温换热器降温,充分利用热量,从而降低了电能得消耗。
硫化过程需要的硫用二硫化碳计量泵补入循环系统。
低温甲醇洗低温甲醇洗工段的主要任务是利用低温的甲醇作为吸收剂,脱除变换气中的H2S、COS、CO2等酸性气体,为下游甲醇合成装置输送合格的净化气;同时,通过在适当压力下的闪蒸,制备纯度较高的CO2产品气,送往纯碱装置;并通过采取H2S 组分提浓措施,为硫回收工段制备合格的H2S浓度较高的酸性气。
(1)原料气冷却来自上游变换工段压力为 6.0MPaA、温度为40℃的原料气,首先进入绕管式换热器原料气冷却器Ⅰ372E001中,与净化气、CO2产品气、及CO2/N2尾气换热,原料气被冷却到16℃。
随后,原料气进入原料气分离罐372V001分离出其中冷凝下来的液相。
该液体主要是NH3和HCN的水溶液,可直接送回变换工段。
经气液分离后,原料气中的NH3和HCN的浓度进一步大大降低,有利于低温甲醇洗的稳定运行。
原料气被进一步冷却之前,先喷入一股半贫甲醇,降低原料气中水的冰点,防止冷却时结冰而堵塞换热器。
该股半贫甲醇来自主洗甲醇泵372P001A/B。
同时,来自循环气压缩机后冷器372E007的循环气也在此与原料气混合,以回收闪蒸气的有效气成分。
混合后的原料气在绕管式换热器原料气冷却器Ⅱ372E002中与与净化气、CO2 产品气、以及CO2/N2尾气继续换热,被进一步冷却、降温。
(2)H2S/CO2吸收冷却后的原料气首先进入洗涤塔372T001᳔下部的预洗段,彻底除去其中痕量的NH3和HCN组分。
洗涤溶剂为来自脱碳段、经净化气/富碳甲醇换热器372E005 过冷的一小股富甲醇。
离开塔底的预洗甲醇首先经过贫甲醇冷却器Ⅱ372E012回收冷量,再经预洗闪蒸罐372V005闪蒸后,进入热再生塔进行热再生。
经预洗后的气体通过升气管向上进入洗涤塔的脱硫段。
用来自上端脱碳段的无硫甲醇脱除气体中的H2S和COS组分。
无硫甲醇的量采取流量控制,控制与原料之间保持合适的比例。
底部的富硫甲醇通过液位控制,进入中压闪蒸塔372T002进行闪蒸。
脱硫后的气相进一步上升,通过升气管进入洗涤塔372T001的脱碳段下部。
在脱碳段,主要用闪蒸得到的低温半贫甲醇作为洗涤溶剂。
同时在洗涤塔的上端用一股热再生得到的贫甲醇作为精洗甲醇,保证净化气的酸性气含量满足工艺要求。
两股甲醇的用量通过流量控制,具体取决于原料气与洗涤甲醇之间的比例。
由于CO2的溶解为放热反应,因此随着甲醇自上而下不断吸收原料气中的CO2 气,甲醇的温度逐渐升高。
为了降低洗涤剂的温度,保证较好的洗涤效果,在两脱碳段之间设置了洗涤塔段间冷却器372E003以及洗涤塔段间深冷器372E004,降低洗涤甲醇的温度。