PQC 制程检验作业规范
关于品质检验作业流程的规定-PQC

发得快品质检验作业流程指引(PQC)1.目的:合理规范QC部品质检验作业流程,确保对产品的各阶段品质状态进行有效检验与判定,确保产品质量符合客户要求。
2.范围:发得快包装制品有限公司工程打样检验、产品首检、制程巡检等制程品质控制环节。
3.职责:3.1.PQC负责大货生产前的样品及首件检验与生产过程中的品质控制。
3.2 对工程打样的样品检验完成时,要出具样品检验报告,并配合工程完成样品承认书。
3.3 大货生产前要完成首件检验并出具首件检验报告。
3.4 制程中采用不定时巡检,有针对性地对关键工序质量控制点及在制品的关键特性进行巡检,确保在制品符合产品的相关要求,并保持完整的PQC巡检报告。
4.作业流程规定4.1.工程打样检验作业4.1.1. 工程接获跟单/业务通知,按客户要求备料、取料及进行手工制作,打样完成时,通知品检PQC验样。
4.1.2. PQC接获工程通知后,应对完成的样品严格按对应客户品质要求及检验标准进行检验,核对客供资料包括图纸、客供样品实物以及订单等,并出具检验结果。
4.1.3 样品承认书之样品检验报告由检验员签名并呈交品质经理签名确认。
方可随工程打样(注意:有部分客户要求一份样品对应一份检验报告,如打样有5PCS就应有对应的5份样品检验报告)送交客户审批。
4.1.4 经客户批核的样品,如有回转发得快公司使用的,应在使用完后归入样品架放置保留,以利下次同类型产品之生产参照。
4.2 首件检验作业4.2.1.每单大货生产前,必须进行首件检验.4.2.2.首件之定义:生产大货前之第一个在制品或制成品;生产大货前之批量试产之第一在制品或制成品.用于确定试产效果,及大货生产过程的样办参照作用.4.2.3.首件之制作一般情况由生产线组长完成,特殊情况下交由生产经理完成。
当首件制作完成时,生产线应通知巡检PQC到场检验是否合格,未经检验合格的首件不得用于大货生产的参照样办。
未经首件检验环节,不得进行大货生产。
PQC检验程序(含表格)
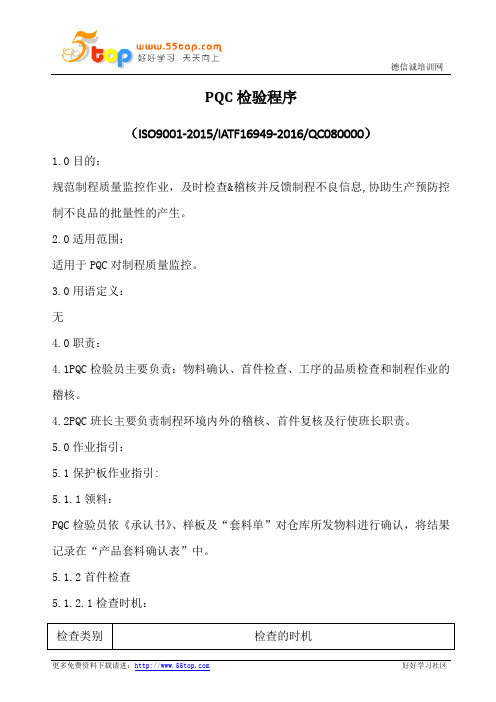
PQC检验程序(ISO9001-2015/IATF16949-2016/QC080000)1.0目的:规范制程质量监控作业,及时检查&稽核并反馈制程不良信息,协助生产预防控制不良品的批量性的产生。
2.0适用范围:适用于PQC对制程质量监控。
3.0用语定义:无4.0职责:4.1PQC检验员主要负责:物料确认、首件检查、工序的品质检查和制程作业的稽核。
4.2PQC班长主要负责制程环境内外的稽核、首件复核及行使班长职责。
5.0作业指引:5.1保护板作业指引:5.1.1领料:PQC检验员依《承认书》、样板及“套料单”对仓库所发物料进行确认,将结果记录在“产品套料确认表”中。
5.1.2首件检查5.1.2.1检查时机:5.1.2.2检查项目5.1.3注意事项:PQC检验员在领料确认时及检查首件时:1)检查产品所有物料的品牌、型号、规格、封装及环保标识是否与《承认书》中“材料清单”规定的是否一致。
2)核对受控样板,确认产品所用的PCB版本、颜色和产品上的材料型号、版本(丝印)颜色、外形是否和样板一致。
5.1.4检查不合格处理:若发现产品有不合格时,知会生产,对其不合格产品进行隔离,加红色拒收标签标识清楚不良原因,按《不合格品控制程序》规定进行处理。
5.2制程检验5.2.1检查标准依《SMT外观检验标准》5.2.2检验方式/要求a.佩戴防静电手环或防静电手套。
b.使用放大镜、显微镜、万用表、电子负载、恒流源、保护板测试仪等检验仪器。
c.目视外观时采用由上而下、由左而右,从90度、45度等多视角进行外观检验。
d.若发现不良缺陷,在不良缺陷处或不良品上贴上红色不良箭头标签。
e.检验项目及标准:检验依照《SMT外观检验标准》、《保护板性能测试QC作业指引》、《承认书》内容及受控样板标准检验。
f.异常反馈/处理:抽检中如果发现有严重品质异常和品质隐患时,必须及时向PQC/生产班长反馈,组织相关部门人员现场分析改善,品质部门进行记录与追踪结果确认。
5PQC检验操作指导书

编号
版本
A
日期
2023.2.18
制定
审核
批准
一、适用范围:公司装配PQC检验。
二、目的:规范装配PQC作业流程,早期预防批量性的异常。三、详细流程如下:
序号
工序流程
操作照《客户需求信息表》、BoM表、设变单、留样、《成品检验规范》、内部联络单、色样以及相关的标准对生产首样进行首件检验;
c.不良品责任单位是否正确(打标产品:划伤、打标不良退打标,来料不良退电镀Γ;多道工序加工的零件:按责任退给供应商);
d.核对无误后,在《退料单》上签字确认。
10
产线返工方案确认
PQC抽检不良需产线返工的,返工流程按技术提供的方案。PQC将返工的结果填写于《成品检验报告》上。
a.检查牙管是否旋到底,钢套不能往下掉
b.锁住后牙管不能倒转;
C.注意是否会划伤。
塞芯子
a.芯子至少2个台阶塞到内管里,不能全部塞进.
装喇叭接头和螺母
a.两端外牙要朝外,六角螺母装在打字套子端;
尺寸检验
a.按成品检验各项尺寸是否符合标准要求;
b.螺纹要求通规通,止规符合标准要求,螺纹小径需要符合要求;
1.5密封测试:70度热水,动压至0.5MPa,保持5分钟。
1.6低压测试:动压水压0.DIPa,转动缠绕接头,不可产生可见的渗漏。
2
首件不合格处理
反馈产线班长,追溯产线的不合格品并要求产线进行隔离标识,避免混料。按《不合格品控制程序》执行。
3
巡检
检验外观
a.巡查物料是否混料;
b.查看产线检验人员操作方式是否存在碰划伤问题;
C.接头与螺母的尺寸深度要注意管控,不可超出标准要求;
PQC检验规则与方法
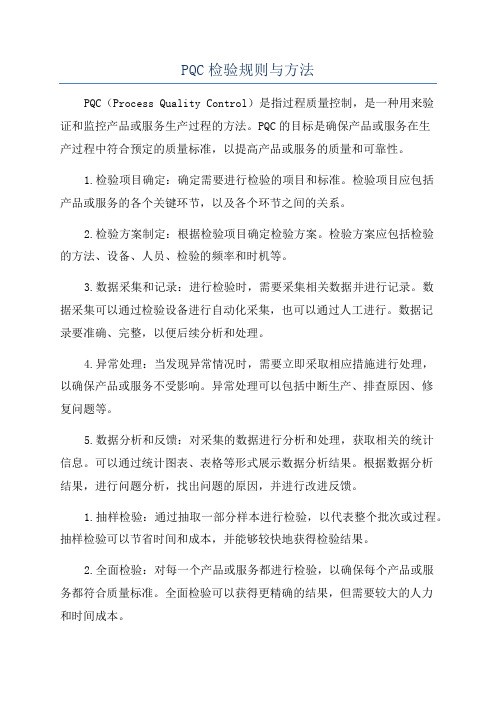
PQC检验规则与方法PQC(Process Quality Control)是指过程质量控制,是一种用来验证和监控产品或服务生产过程的方法。
PQC的目标是确保产品或服务在生产过程中符合预定的质量标准,以提高产品或服务的质量和可靠性。
1.检验项目确定:确定需要进行检验的项目和标准。
检验项目应包括产品或服务的各个关键环节,以及各个环节之间的关系。
2.检验方案制定:根据检验项目确定检验方案。
检验方案应包括检验的方法、设备、人员、检验的频率和时机等。
3.数据采集和记录:进行检验时,需要采集相关数据并进行记录。
数据采集可以通过检验设备进行自动化采集,也可以通过人工进行。
数据记录要准确、完整,以便后续分析和处理。
4.异常处理:当发现异常情况时,需要立即采取相应措施进行处理,以确保产品或服务不受影响。
异常处理可以包括中断生产、排查原因、修复问题等。
5.数据分析和反馈:对采集的数据进行分析和处理,获取相关的统计信息。
可以通过统计图表、表格等形式展示数据分析结果。
根据数据分析结果,进行问题分析,找出问题的原因,并进行改进反馈。
1.抽样检验:通过抽取一部分样本进行检验,以代表整个批次或过程。
抽样检验可以节省时间和成本,并能够较快地获得检验结果。
2.全面检验:对每一个产品或服务都进行检验,以确保每个产品或服务都符合质量标准。
全面检验可以获得更精确的结果,但需要较大的人力和时间成本。
3.在线检验:在产品或服务生产的过程中,通过检测仪器或传感器对关键参数进行实时监测和检测。
在线检验可以及时发现异常情况,并立即采取措施进行处理。
4.离线检验:将已生产完成的产品或服务抽样检验,通过实验室或检验设备进行检验。
离线检验可以对产品或服务进行全面的检验,但需要较长的时间。
PQC检验规则与方法在现代生产中得到广泛应用,不仅可以用来监控产品或服务的质量,还可以用来改进生产过程,提高生产效率和降低成本。
通过合理的检验规则和方法,可以追踪和控制生产过程中的各个环节,确保产品或服务的质量达到预期目标。
PQC检验作业指导书

4.5巡回检验:
首样检验合格后的批量生产,检验员对生产的各个工位以60分钟的巡回间隔进行巡检。巡检结果记录于《巡检报表》中。巡检过程中,对产品的性能及尺寸抽3pcs,外观抽5pcs进行检验。确保产品处于稳定的、符合客户要求的状态下批量性生产。当产品的批量较小,不足60分钟的巡检周期,检验员以不低于2次的检验次数对该产品进行检验。
巡检过程中发现不良品时,用红色不良品标签在不合格品外表面或外包装的醒目位置进行标识,必要时用红色箭头标签指明缺陷位置。并将不良品放置于不良品区内。对正在加工的产品仍存在有不合格的隐患时,通知操作者停止生产,并与操作者、现场主管对不良品产生的原因进行分析,包括可能影响质量的人、机、料、方法、环境。生产部门及时的对不良品进行返修,并采取针对性的纠正和预防措施。当产品材料错误或不良率高于公司规定允许的不良率时,检验人员依照检验结果填写《品质异常报告》交品质部。由品质部根据描述的缺陷分析不良品产生的原因与责任部门。相关责任部门根据不良原因制订临时与永久的改善措施。并将具体方案、责任人员及完成时间记录于《品质异常报告》中。
《产品的标识和可追溯性程序》
《不合格品控制程序》
6.质量记录
《巡检报表》
《首样检验报告》
《工序不合格处理单》
《半成品工序转移单》
PQC检验作业指导书
1.目的
为检验员提供检验规则和检验方法,指导其正确检验从而稳定产品质量。
2.适用范围:
适用于博赢模具有限公司模具制程检验的控制。
3.职责:
生产部负责按照图纸、工艺文件进行生产及对不合格项目进行纠正和预防。
技术部负责制定工艺文件及对新产品的首次加工进行确认。
当某一工序加工完毕后转序时,PQC检验人员对该批产品的重要尺寸、性能、外观按照GB2828-87逐批检查计数抽样程序中正常检查一次抽样方案Ⅱ进行检验。严重缺陷:AQL值为0.65, 轻微缺陷:AQL值为2.5。抽检中发现该工序批不合格时,在《半成品工序转移单》中注明,通知操作人员筛选、返修。
冲压PQC检验规范

冲压PQC检验规范1.目的明确公司所有冲压产品品质标准,确保产品质量持续满足客户需求;为PQC 检验人员作业提供依据。
2.范围适用于公司所有冲压产品的检验。
3.职责3.1品管部QE工程师负责制定此规范。
3.2冲压部PQC按照此规范作业。
4.定义无5.工作程序5.1检验条件5.1.1照明条件,1000+/-200Lux ( 使用D65标准日光灯),光源距被测物表面350~450MM;5.1.2观察角度:被检测面与视线在45度范围内旋转, 左右转动15度范围;5.1.3观察距离:人眼和被测物表面距离为300-350mm;5.1.4观察时间:10+/-5S(检验所有表面);5.1.5检验员视力:单眼裸视或矫正视力在1.0以上且无色盲;5.1.6在此条件下,目测可见的不良现象认为是缺陷。
5.2按生产指令单要求准备好相关检验治/工具、图纸等检验标准,并配戴好防护用品(手套或手指套)后方可接触部品。
5.3尺寸检验:用测量治/工具按相关工程图纸要求对冲压成品进行抽验,并用平台和塞尺检查五金件的平整度必须符合工程图纸要求。
5.4PQC要对冲压产品外观进全数检验。
5.3试装检验(针对后续无腐蚀或电镀工序类产品):用客供机壳对装饰片进行试装配,检查是否有缝大、装配过紧、装配不平整等不良现象。
每送检批抽样10PCS,AC为0、RE为1。
5.4外观检验:5.5检验内容5.6将检验后的产品进行区分、标识、并将检验结果记录在《PQC检验报表》中,交主管进行综合判定。
当检验结果不良品比例大于8% 时需发出《内部品质异常联络单》。
5.7将合格品按要求进行分装入库,不合格品退生产部门按《不合格品控制程序》处理。
6.0相关文件《不合格品控制程序》《内部品质异常联络单》7.0相关表格《PQC检验报表》。
PQC作业规程
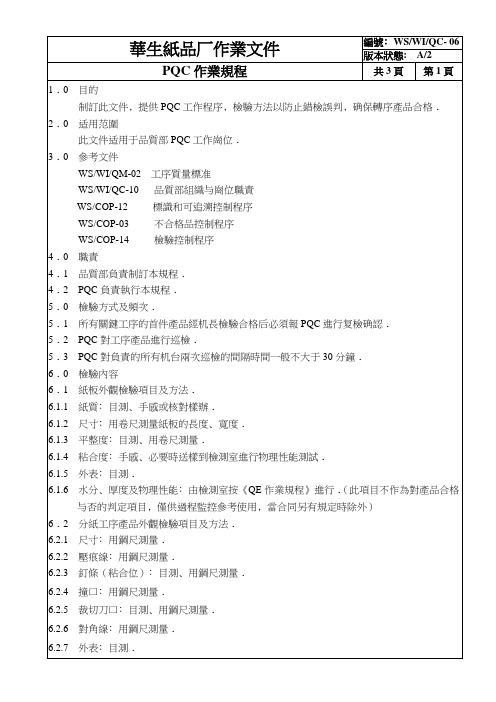
WS/WF/QC-02不合格品評審處 Nhomakorabea單WS/WF/QC-03 PQC檢驗記錄表
WS/WF/QC-05物料報廢申請表
WS/WF/QC-07讓步申請單
WS/WF/QC-21不合格品標識卡
WS/WF/QC-23不良品統計報表(紙板車間)
WS/WF/QC-24不良品統計報表(印刷組)
WS/WF/QC-40生產問題通知單
10﹒0檢驗記錄
10﹒1 PQC檢驗員對所有經檢驗存在質量問題的產品批次均應作記錄﹐關鍵工序所有產品批次(不論是否存在質量問題)均須作記錄﹒
10﹒2經PQC檢驗合格且數量≧500PCS的紙板應予記錄﹒
10﹒3經PQC檢驗合格且數量≧50PCS的紙箱應予記錄﹒
10﹒4 PQC檢驗員將檢驗結果填寫在相應的檢驗記錄中﹐上交品質部審核﹑存檔﹒
6.7.4包裝防護﹕目測﹒
6.7.5其他要求﹕目測﹑對照客戶要求﹒
6.7.6外表﹕目測﹒
7﹒0判定標准﹕按WS/WI/QM-02《工序質量標准》及客戶合同要求進行判定﹒
8﹒0檢驗標識﹕按WS/COP-12《標識和可追溯控制程序》之規定進行處理﹒
9﹒0不合格品按WS/COP-03《不合格品控制程序》相應條款處理﹒
WS/COP-12標識和可追溯控制程序
WS/COP-03不合格品控制程序
WS/COP-14檢驗控制程序
4﹒0職責
4﹒1品質部負責制訂本規程﹒
4﹒2 PQC負責執行本規程﹒
5﹒0檢驗方式及頻次﹒
5﹒1所有關鍵工序的首件產品經机長檢驗合格后必須報PQC進行复檢确認﹒
5﹒2 PQC對工序產品進行巡檢﹒
5﹒3 PQC對負責的所有机台兩次巡檢的間隔時間一般不大于30分鐘﹒
PQC检验作业规范
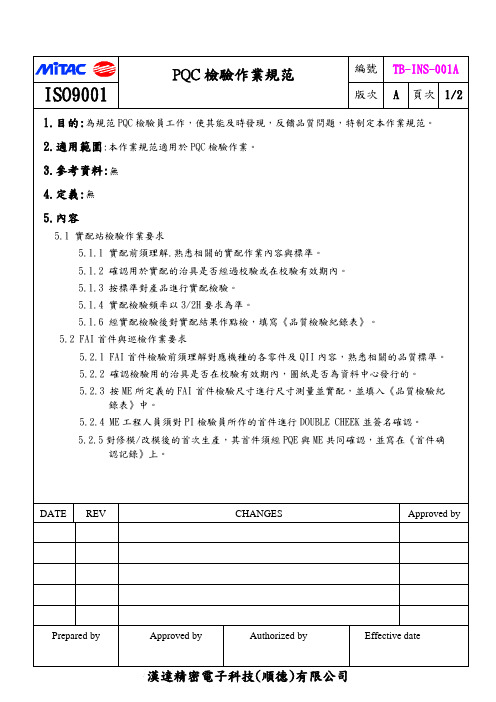
ISO9001
2.適用範圍:本作業規范適用於 PQC 檢驗作業。 3.參考資料:無 4.定義:無 5.內容
5.1 實配站檢驗作業要求 5.1.1 實配前須理解.熟悉相關的實配作業內容與標準。 5.1.2 確認用於實配的治具是否經過校驗或在校驗有效期內。 5.1.3 按標準對產品進行實配檢驗。 5.1.4 實配檢驗頻率以 3/2H 要求為準。
6. 附件
6.1 《制程檢驗報告》(TB-FLO-03A) 6.2 《首件檢驗記錄》(TB-FLO-02A) 6.3 《品質問題反映速報》(QA-INS-03A)
7. 記錄保存
7.1 《制程檢驗報告》-----三個月 7.2 《首件檢驗記錄》-----三個月 7.3 《品質問題反映速報》-----六個月
1.目的:為規范 PQC 檢驗員工作,使其能及時發現,反饋品質問題,特制定本作業規范。
5.1.6 經實配檢驗後對實配結果作點檢,填寫《品質檢驗紀錄表》。 5.2 FAI 首件與巡檢作業要求 5.2.1 FAI 首件檢驗前須理解對應機種的各零件及 QII 內容,熟悉相關的品質標準。 5.2.2 確認檢驗用的治具是否在校驗有效期內,圖紙是否為資料中心發行的。 5.2.3 按 ME 所定義的 FAI 首件檢驗尺寸進行尺寸測量並實配,並填入《品質檢驗紀 錄表》中。 5.2.4 ME 工程人員須對 PI 檢驗員所作的首件進行 DOUBLE CHEEK 並簽名確認。 5.2.5 對修模/改模後的首次生產,其首件須經 PQE 與 ME 共同確認,並寫在《首件 确認記錄》上。 DATE REV CHANGES Approved by
漢達精密電子科技(順德)有限公司
Prepared by
Approved by
Authorized by
PQC制程检验作业指导书(含表格)

PQC制程检验作业指导书(ISO9001:2015)1. 目的:为明确制程检验PQC的工作职责与权限,提高检验人员的工作能力及工作效率,以利于更好的对产品制程质量作管控。
2. 适用范围:2.1 首件检验。
2.2 制程巡检。
2.3 退料检验。
2.4 异常及数据处理。
3. 名词定义:3.1 不合格:不符合规定之要求。
4. 管理重点:4.1 首件检验:4.1.1 生产线于规定的时间内完成首件制作并开立送验单交 PQC 人员进行检验。
4.1.1.1 插配线:新机种前三批送首件且于上线后30分钟内送出。
4.1.1.2 装配及合并线须每批送验且于上线前1H送出。
4.1.2 PQC人员于首件检验前工作:4.1.2.1 核对生产排程并确认该线生产机种须与排程相符。
4.1.2.2 从工程部借出该机种的BOM,从品保部借出该机种的QC工程图,并查阅该机种质量检验规范、及相关的工程变更、技术指令、工程图面等相关数据,并对上述资料作详细了解。
4.1.2.3 依据(2)项资料对生产线各站别材料之规格、版本、SOP及有变更后之材料做确认.4.1.2.4 接到首件后并依之进行检验4.1.3 进行检验:4.1.3.1 依“检验记录表”及首件,确认“检验记录表”所填写的机种名称、品号、批号等内容必须正确,否则退单给生产线更正。
4.1.3.2 依BOM确认首件所用各种包装材料、附件、说明书、保证卡等材料的规格、版本是否正确,如有:错、漏、多、少等仍一不良则判定NG。
4.1.3.3 依质量检验规范检验首件的外观、实际各项功能做检测,以确保质量能符合产品规格要求。
4.1.3.4 将各项检验的结果如实、客观、正确地填写在“检验记录表”上,并作出综合判定。
4.1.3.5 将判定结果告知生产线线长(如NG则需和线长当面确认),并会签认可。
4.1.3.6 PQC首件检验须在1H内完成并送审单位主管。
4.1.4 判定及处理4.1.4.1 若判定OK,生产线即可进行量产。
PQC、FQC检验作业流程作业细则

作業細則名稱PQC/FQC檢驗作業流程作業細則文件編號版次頁次第1頁﹐共1頁1.目的﹕規范PQC/FQC管理作業流程。
2.權責單位﹕主管單位:品保部(PQC/FQC)。
配合單位:生產部、工程部。
3.相關文件:《抽樣檢驗作業指導書》《PQC/FQC檢驗作業規范書》《成品外觀檢驗標准》《半成品外觀檢驗標准》《生產作業指導書》4.相關表單:《半成品抽檢記錄表》《成品檢驗記錄表》《不合格品處理單》《大流程單/檢修流程單》5.作業范圍﹕自〔生產送檢〕至〔PQC/FQC檢驗完成〕之相關作業細則。
6.作業流程說明﹕6.1.半成品檢驗/成品終檢﹕6.1.1.生產半成品視檢/成品終檢OK后﹐并填完整《大流程單/檢修流程單》﹐產品送到PQC/FQC待檢產品指定抽檢區。
6.2.半成品/成品抽檢准備作業﹕6.2.1.PQC/FQC根據產線送檢半成品/成品﹐依其產品型號准備相對應的檢驗文件﹑工冶具。
6.3.外觀/電氣抽樣﹕6.3.1.按《抽樣檢驗作業指導書》﹑《PQC/FQC檢驗作業規范書》進行抽樣作業。
6.4.檢驗﹕6.4.1.PQC/FQC根據《抽樣檢驗作業指導書》﹑《成品外觀檢驗標准》﹑《半成品外觀檢驗標准》﹑《PQC/FQC檢驗作業規范書》﹑《生產作業指導書》及樣品進行外觀檢驗。
6.4.2. PQC/FQC根據相對應產品進行電氣檢驗。
6.4.3.檢驗結果OK時記錄于大流程單﹐填寫于《半成品抽檢/成品檢驗記錄表》,并《半成品抽檢/成品檢驗記錄表》品保PQC/FQC作歸檔。
6.4.4.檢驗結果NG時﹐經QC主管確認不良屬實時開出《不合格品處理單》。
6.4.5.不合格品隨同《大流程單/檢修流程單》﹑《不合格品處理單》退回生產。
6.5.批退品重檢作業流程﹕6.5.1.生產﹑品保對于批退品依照《批退品重檢作業流程》作業。
6.6.下流程作業﹕6.6.1. PQC/FQC檢驗后OK品﹐產品隨流程單一同流入下一流程作業。
核准審核制作日期。
pQC作业指导书

pQC作业指导书1000字pQC是一种新型的质量改进方法,它是基于六西格玛的思想发展而来的。
pQC是Process Quality Control(过程质量控制)的缩写,它重视分析和控制过程中的各种因素,以保证产品和服务的质量。
pQC主要通过三个步骤来实现:确定目标、项目管理和持续改进。
在以下的作业指导书中,我们将详细描述pQC方法的应用,并提供指导来帮助你在未来的质量改进项目中应用这种方法。
一、确定目标1.明确目标:确定项目的具体目标,例如提高产品质量、提高客户满意度等。
目标应该是详细、清晰和可度量的。
2.了解流程:评估整个流程,并确定可能影响流程的因素。
了解流程将帮助你确定影响质量的关键因素。
3.收集数据:收集相关数据,以便明确该流程中的缺陷和机会。
处理这些数据,以便为进一步的分析做准备。
4.分析数据:将收集到的数据进行分析,并确定所有存在的问题、机会和趋势。
分析后,你可以明确该流程中需要改善的方面。
二、项目管理1.选定团队:选择一个由不同部门及不同层次的员工组成的团队。
他们将负责推进改进项目。
在这个团队里,应当包含那些对该流程最有专业知识和经验的人员。
2.明确角色:确保每个人在协作过程中都知道自己的角色和任务。
为了确保项目的成功,保证团队的沟通渠道畅通。
3.制定计划:制定一份详细的计划,涵盖整个改进项目,并确定每个任务的时间表和责任人。
4.实施改进:基于选定的方案和时间表,团队开始执行改进计划。
在这个阶段,每个任务均按照时间表进行,以确保项目的顺利进行。
5.持续考核:考核所有阶段的任务,并跟进项目的进展情况。
在这个阶段,要频繁地与团队成员沟通,确保一切按照计划进行。
三、持续改进1.建立基准:建立基准来评估过程改进的效果。
基准可以是客户满意度度量、产品缺陷率、流程时间等等。
2.跟踪进度:在确定基准之后,跟踪进度并进行评估。
评估结果建议要实时更新,并考虑在项目中进行相关调整。
3.解决问题:分析结果,并解决现存的问题。
PQC检验作业规范

5.2 汽车行业产品允收水准:
5.2.1外觀检验采用VL-Ⅲ抽样计划,允收品質水準AC = 0 RE = 1
5.2.2尺寸(機構)﹕允收品質水準AC = 0 RE = 1
5.2.3電氣采用VL-Ⅳ抽样计划,允收品質水準AC = 0 RE = 1
6. 流程說明﹕
5.抽樣計畫﹕
非汽车行业产品采用ANSI-ASQZ1.4一般檢驗水準II級(適用於外觀﹑電氣功能項目)。
汽车行业产品采用MIL-STD-1916抽样标准(適用於外觀﹑電氣功能項目)
5.1 非汽车行业产品允收水准:
5.1.1外觀﹕允收品質水準AQL 0.4 %
5.1.2尺寸(機構)﹕允收品質水準AC = 0 RE = 1
<<測試規格書>>
當電氣及外觀發生批量性不良或返工后仍有不良時需開立<<品質異常改善追蹤單>>
核准
審核
制作
日期
6.4 生產全檢/返工之產品需再次送PQC檢驗﹐PQC根據抽檢數量進行抽檢﹐若OK則蓋QC章流入下一流程﹐如NG則開<<品質異常改善追蹤單>>并將產品退回生產處理。
6.5 PQC在檢驗中或處于檢驗不合格的狀態時﹐產品不得移轉下一工序。
6.6 若此批產品有不良但未達到批退時﹐生產負責對換良品。
6.7PQC依重點進行加嚴抽樣管控﹐如:當發生客訴時﹐項目不良為OPEN﹑SHORT等﹔產品總的不良率過高﹔產線出現異常。
PQC檢驗作業規范
文 件 編 號
版 次
A0
頁 次
第1頁 共3頁
1.目的﹕防止批量性不良流入下一流程并運用統計方法控制不良率﹐降低不良率﹐以達到提高公司效益之目的。
pqc检验流程及职责

pqc检验流程及职责英文回答:PQC Inspection Procedures and Responsibilities.PQC (Pre-Qualification of Contractors) inspections are a critical part of any construction project. They help to ensure that contractors have the necessary skills, experience, and resources to complete the project safely and efficiently.The PQC process typically involves the following steps:1. Development of PQC criteria. The first step is to develop a set of PQC criteria. These criteria should be based on the specific requirements of the project, and should include factors such as:Experience.Safety record.Financial stability.Quality control.2. Solicitation of bids. Once the PQC criteria havebeen developed, the next step is to solicit bids from potential contractors. The bid solicitation should include the PQC criteria, as well as the project specifications and other relevant information.3. Evaluation of bids. The bids received from potential contractors should be evaluated based on the PQC criteria. The evaluation process should be fair and impartial, and should consider all of the relevant factors.4. Selection of contractor. The final step in the PQC process is to select the contractor that best meets the PQC criteria. The selected contractor should be able to demonstrate that they have the necessary skills, experience, and resources to complete the project safely andPQC inspections are an important part of any construction project. They help to ensure that the project is completed by a qualified contractor, which can help to reduce the risk of delays, cost overruns, and safety hazards.Responsibilities.The following parties have responsibilities in the PQC process:Owner The owner is responsible for developing the PQC criteria and soliciting bids from potential contractors.Engineer The engineer is responsible for evaluating the bids received from potential contractors and selecting the contractor that best meets the PQC criteria.Contractor The contractor is responsible for meeting the PQC criteria and completing the project safely andIt is important for all parties involved in the PQC process to work together to ensure that the project is completed successfully.中文回答:PQC检测流程及职责。
PQC检验手法作业SOP FS-SOP-0506
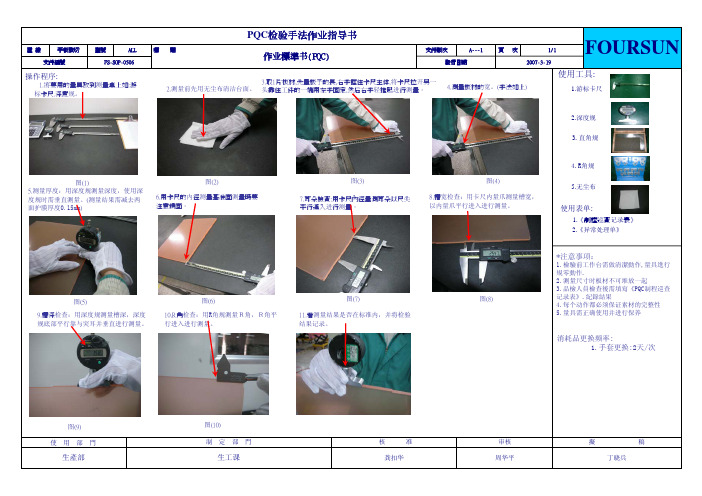
使 用 部 門
FOURSUN
生工课
生產部制 定 部 門
核 准记录表》龚扣华
5.测量厚度:用深度规测量深度,使用深度规时需垂直测量。
(测量结果需减去两面护膜厚度0.15mm )
6.用卡尺的内徑测量基准面测量時要注意鏡面。
7.耳朵檢查:用卡尺內徑量測耳朵以尺尖平行進入进行测量。
8.槽宽检查:用卡尺内量爪测量槽宽,以内量爪平行进入进行测量。
9.槽深检查:用深度规测量槽深,深度规底部平行靠与突耳并垂直进行测量。
10.R角检查:用R角规测量R角,R角平行进入进行测量。
图(9)图(10)
图(5)
图(6)
图(1)
图(2)
图(3)
图(4)
图(7)
图(8)
11.看测量结果是否在标准内,并将检验结果记录。
PQC检验作业指引HYT-SOP-PZ-02
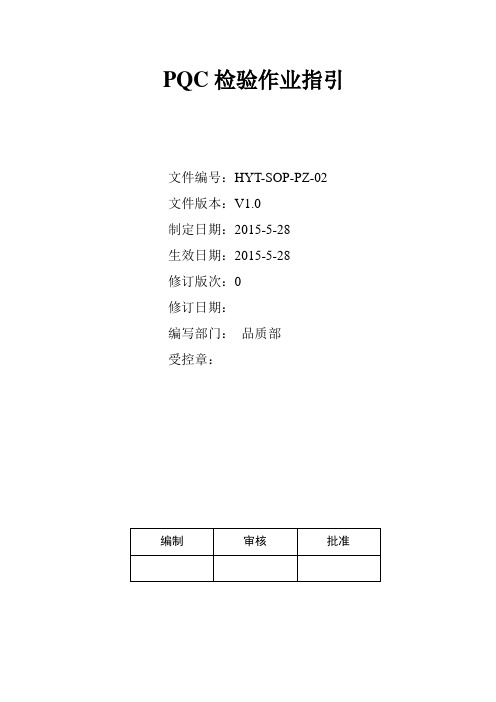
修订次数
修订日期
修订内容(前/后)
修订页次
0
2015-6-26
全部(首次发行)
全部
编制
审核
批准
惠州市汇宇通电子有限公司
PQC检验作业指引
文件编号
HYT-SOP-PZ-02
生效日期
2015-5-28
页码
2/4
一、目的:
规范制程质量监控作业,及时检查&稽核并反馈制程不良信息,协助生产预防控制不良品的批量性的产生。
编制
审核
批准
若发现产品有不合格时,知会生产,对其不合格产品进行隔离,加红色拒收标签标识清楚不良原因,按《不合格品控制程序》规定进行处理。
5.2制程检验
5.2.1检查标准依《SMT外观检验标准》
5.2.2检验方式/要求
a.佩戴防静电手环或防静电手套。
b.使用放大镜、显微镜、万用表、电子负载、恒流源、保护板测试仪等检验仪器。
“型号生产首件确认表”
5.1.3注意事项:
PQC检验员在领料确认时及检查首件时:
1)检查产品所有物料的品牌、型号、规格、封装及环保标识是否与《承认书》中“材料清单”规定的是否一致。
2)核对受控样板,确认产品所用的PCB版本、颜色和产品上.1.4检查不合格处理:
二、适用范围:
适用于PQC对制程质量监控。
三、用语定义:
无
四、职责:
4.1 PQC检验员主要负责:物料确认、首件检查、工序的品质检查和制程作业的稽核。
4.2 PQC班长主要负责制程环境内外的稽核、首件复核及行使班长职责。
五、作业指引:
5.1保护板作业指引:
5.1.1领料:
PQC检验员依《承认书》、样板及“套料单”对仓库所发物料进行确认,将结果记录在“产品套料确认表”中。
PQC检验规范

PQC检验流程规范1. 过程检验程序目的:a) 生产过程中按《作业指导书》及客户要求对产品进行检验,保证产品质量;b) PQC对半成品进行抽检,以监控半成品生产质量波动。
范围:a) 公司所有产品性能及外观检验;责任:除已指定的之外,品质主管分别负责以下程序中的所有运作。
过程检验流程图:(见下页)过程检验员PQC须具备资格条件:1.4.1 高中、中专或以上文化程度;1.4.2 熟悉产品装配工艺要求及客户品质要求;1.4.3 经过3C基础知识及取暖桌过程检验要求的培训并考核合格。
PQC职责和权限:1.5.1 过程检验员PQC按《作业指导书》要求对半成品、加工出货半成品、成品等进行检验;1.5.2 记录和保存检验数据进行统计分析,保存统计分析结果;1.5.3 对生产过程中发生的批量性不合格品,及时汇报并执行《不合格品评审程序》。
PQC运作程序:1.6.1 PQC按《作业指导书》的要求对成品/半成品逐项检验1.6.2 对生产线不良品贴上不良标签放置在指定位置并记录不良原因及数量于《PQC检验记录》。
1.6.3 对不可修的不良品由品质主管确认后可准予报废,同时记录报废原因及数量于《报废品分析报告》。
1.6.4 PQC员每两小时统计不良数量,计算两小时不良率,按《2小时可接受不良数标准》比较品质不良情况,如不良率超过品质目标,PQC员发出《纠正行动通知单》给有关责任部门,责令其采取改善措施以稳定生产质量,并完成《纠正行动通知单》其它内容。
1.6.5 对于批量性不合格按《不合格品评审程序》处理。
1.6.6 每日生产完毕后,PQC及生产主管对《PQC检验记录》作确认后,由PQC作每日统计,并及时公布各生产单位品质情况。
过程及最终检验流程图:。
WI-08030102 PQC检验规范

1、目的
制定明确的PQC作业规范,保证制造过程中的品质得到合理有效的控制,减少不良零件的产生。
2、适用范围
制造过程中的一切品质作业人员。
3、引用文件
3.1《质量手册》
3.2《不合格品管制程序》
3.3《质量记录》
3.4《PQC岗位职责》
3.5《纠正和预防措施》
4、主要职责和权限
4.1.PQC执行制造过程中的零部件检查工作,及时发现问题,并对其做跟踪处理。
4.2.制造基层工作人员及各级管理人员必须密切配合PQC工作,对有品质问题的零件
应积极采取补救措施,并从根本上解决。
5、人员资格要求
所PQC人员必须经过岗位培训,考试合格。
6、检验规范
7、质量记录
7.1《模具零件检收表》
7.2《品质异常处理通知单》7.3《返工通知单》
7.4《报废单》
7.5《工作交制单》
7.6《零件图》。
CNC PQC检验规范
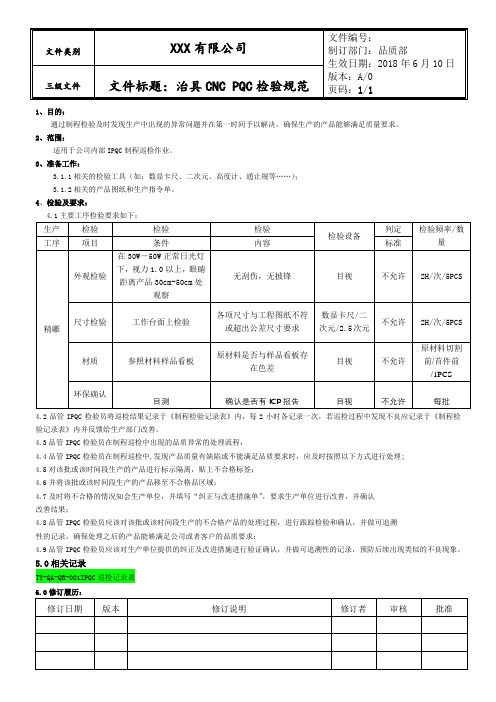
1、目的:
通过制程检验及时发现生产中出现的异常问题并在第一时间予以解决,确保生产的产品能够满足质量要求。
2、范围:
适用于公司内部IPQC制程巡检作业。
3、准备工作:
3.1.1相关的检验工具(如:数显卡尺、二次元、高度计、通止规等……);
3.1.2相关的产品图纸和生产指令单。
4、检验及要求:
4.1主要工序检验要求如下:
4.2品管IPQC检验员将巡检结果记录于《制程检验记录表》内,每2小时各记录一次,若巡检过程中发现不良应记录于《制程检验记录表》内并反馈给生产部门改善。
4.3品管IPQC检验员在制程巡检中出现的品质异常的处理流程:
4.4品管IPQC检验员在制程巡检中,发现产品质量有缺陷或不能满足品质要求时,应及时按照以下方式进行处理;
4.5对该批或该时间段生产的产品进行标示隔离,贴上不合格标签;
4.6并将该批或该时间段生产的产品移至不合格品区域;
4.7及时将不合格的情况知会生产单位,并填写“纠正与改进措施单”,要求生产单位进行改善,并确认
改善结果;
4.8品管IPQC检验员应该对该批或该时间段生产的不合格产品的处理过程,进行跟踪检验和确认,并做可追溯
性的记录,确保处理之后的产品能够满足公司或者客户的品质要求;
4.9品管IPQC检验员应该对生产单位提供的纠正及改进措施进行验证确认,并做可追溯性的记录,预防后续出现类似的不良现象。
5.0相关记录
TY-QA-QR-001IPQC巡检记录表
编写/日期:审核/日期:批准/日期:。
- 1、下载文档前请自行甄别文档内容的完整性,平台不提供额外的编辑、内容补充、找答案等附加服务。
- 2、"仅部分预览"的文档,不可在线预览部分如存在完整性等问题,可反馈申请退款(可完整预览的文档不适用该条件!)。
- 3、如文档侵犯您的权益,请联系客服反馈,我们会尽快为您处理(人工客服工作时间:9:00-18:30)。
8.4<制程檢驗月報表>
8.4.1用于統計每月檢驗結果。
8.4.2 品質月報中附各課檢驗狀況。
8.4.3制式表單﹐使用電子檔。
9. 檢驗流程
產線送待檢產品到指定抽檢區→PQC對數量及型號核對→PQC依據相關檢驗標准及文件進行檢驗→OK則產品轉入后流程→NG則開出檢驗結果報告表→不良由PQC主管判定→判定NG則退回產線→產線依據判定結果處理后送PQC重檢→PQC重檢OK轉入后流程→重檢NG則再退回產線處理
檢 驗 作 業 規 範 書
版本/次
A1
PQC制程檢驗
頁 碼
第1頁共3頁
1. 目的﹕防止生產半成品批量性不良流入下流程。
2. 範圍﹕半成品視檢或/及測試站后﹐所有機種均需以批量為基礎送PQC檢驗。
3. 抽樣計劃
外觀﹑電氣檢驗每批次抽取樣品20pcs(每批次產品數量不超過500pcs)。
4. 允收水準
4.1 外觀﹕允收品質水準AC = 0 RE = 1
6.2電氣(功能)﹕依各產品之功能需求進行檢驗或以儀器設備進行測試。
7. 檢驗設備
依據<<檢驗基準書>>(PQC)所規範的檢驗設備。
核准﹕
審核﹕
制表﹕
日期﹕
檢 驗 作 業 規 範 書
版本/次
A1
PQC制程檢驗
頁 碼
第2頁共3頁
8. 使用表單
8.1<半成品抽檢記錄表>
8.1.1每批產品之檢驗結果記錄。
4.2 電氣﹕允收品質水準AC = 0 RE = 1
4.3 缺點分類
參考IQC檢驗作業規范書之“缺點分類”敘述。
5. 檢驗依據
5.1<<生產作業指導書>>
5.2<<各系列半成品外觀檢驗標准>>
5.3 <<檢驗基准書>> (PQC)
6. 檢驗方法
6.1外觀﹕以距離30cm目視檢驗﹐及以放大鏡﹑20X顯微鏡確認。
核准﹕
審核﹕
制表﹕
日期﹕
檢 驗 作 業 規 範 書
版本/次
A1
PQC制程檢驗
頁 碼
第3頁共3頁
責任者
流程圖
相關表單
生產
品保
品保
生產
品保
生產
<<半成品抽檢記錄表>>
<&;品質異常改善追蹤單>>
核准﹕
審核﹕
制表﹕
日期﹕
8.1.2由單位主管審核。
8.2<<不合格品處理單>>
8.2.1當產品檢驗出現不良時需開出此表單。
8.2.2外觀由PQC主管審核判定。
8.2.3 電氣功能先由PQC主管判定若PQC主管不能判定或有爭議時再由工程部工程師判定。
8.3<品質異常改善追蹤單>
8.3.1 當同批產品連續3次檢驗出現不良時需開出此表單