氧化工艺
高级氧化工艺优缺点的比较

高级氧化工艺优缺点的比较常用的高级氧化Fenton氧化法,光催化氧化法,电催化氧化法,铁碳微电解氧化法等,现对这几种方案进行比较。
Fenton氧化法:Fenton (芬顿)试剂法是针对一些特别难降解的机有污染物如高COD,利用硫酸亚铁和双氧水的强氧化还原性,生成反应强氧化性的羟基自由基,与难降解的有机物生成自由基,最后有效的氧化分解(芬顿(Fenton )试剂反应机理)其化学反应机制如下:H O +Fe2+fOH-+OH-+Fe3+fFe(OH) !2 2 3随着研究的深入,又把紫外光(UV)、草酸盐(C2O42-)等引入Fenton试剂中,使其氧化能力大大增强。
从广义上说,Fenton法是利用催化剂、或光辐射、或电化学作用,通过H2O2产生羟基自由基(・OH)处理有机物的技术。
光催化氧化法:光化学氧化法包括光激发氧化法(如O3/UV)和光催化氧化法(如TiO2/UV)。
光激发氧化法主要以O3、H202、O2和空气作为氧化剂,在光辐射作用下产生羟基自由基HO・。
光催化氧化法则是在反应溶液中加入一定量的半导体催化剂,使其在紫外光(UV)的照射下产生HO・,两者都是通过HO •的强氧化作用对有机污染物进行处理。
其中,氧化效果较好的是紫外光催化氧化法,它的作用原理是让有机化合物中的C-C、C-N键吸收紫外光的能量而断裂,使有机物逐渐降解,最后以CO2的形式离开体系。
电催化氧化法:电化学氧化法是指通过阳极表面上放电产生的羟基自由基HO •的氧化作用,HO •亲电进攻吸附在阳极上的有机物而发生氧化反应,从而去除污染物。
研究表明,在酸性介质和PbO2固定床电极反应器中,经过5h的降解,苯胺的去除率可达97%以上;在碱性介质中,苯胺和4-氯苯胺在Pb箔上的阳极氧化呈现出一级反应特征,在3h内,这类物质的去除率为99%,而且所有的中间产物也可被彻底氧化。
含有卤代物和硝基化合物的废水通过电化学氧化处理,采用Ti、PbO2或碳纤维阳极,其去除率可达95%以上。
氧化工艺

当
时有:
当
时有:
(3) 热氧化生长的两个阶段 ① 线性阶段
当
时有: 简记为:
tox=B/At
② 抛物线阶段(生长逐渐变慢,直至不可忍受)
当
时有:
简记为:
t ox Bt
B/A被称为线性速率系数;而B被称为抛物线速率系数
硅(100)晶面干氧氧化速率与氧化层厚度的关系
⑤ Na+的中性化:
4 热氧化机制
(1) 基本机理 Si(固态)+ O2 (气态) SiO2 (固态)(>1000 ℃) 热氧化是在Si/SiO2 界面进行,通过扩散与化学反应 实 现 。 O2 或 H2 O 在 生 成 的 二 氧 化 硅 内 扩 散 , 到 达 Si/SiO2界面后再与Si反应。 结果:硅被消耗而变薄,氧化层增厚。 生长1μm厚SiO2约消耗0.45μm厚的硅 dSi =0.45dSiO2
◆硅酸钠 Na2SiO3 Na2O· 2 SiO
◆高岭石
Al2(Si2O5)(OH)4
Al2O3· 2SiO2· 2O 2H
硅酸盐组成的表示方法
硅酸盐的种类很多,结构也很复杂,通常可用 二氧化硅和金属氧化物的形式来表示其组成。 表示方法:金属氧化物写在前面,再写SiO2, 最后写H2O;氧化物之间用“·”隔开。
③ 网络调节剂
④ 网络形成剂
⑤ 本征二氧化硅 无杂质的二氧化硅
二氧化硅的性质
二氧化碳(CO2) 存在 结构
空气 分子晶体,存在CO2分子。 无色气体,熔、沸点低,微溶于 水 CO2+ H2O ⇋H2CO3 CO2+2NaOH=Na2CO3+H2O
二氧化硅(SiO2)
半导体制造工艺之氧化工艺

氧化是最重要的加热过程之一,是一种添加工艺,将氧气加入到硅晶圆后在晶圆表面形成二氧化硅。
硅很容易和氧发生反应,因此自然界中的硅大多以二氧化硅形态存在,如石英砂。
硅很快和氧气发生反应在硅表面形成二氧化硅,反应式可以表示为:Si+O2→SiO2二氧化硅是一种致密物质且能覆盖整个硅表面。
如果要继续硅的氧化过程,氧分子就必须扩散穿过氧化层才能和底下的硅原子产生化学反应。
生长厚的二氧化硅层会使氧气的扩散遇到阻碍而使氧化过程变得缓慢。
当裸露的硅晶圆接触到大气时,几乎立刻就和空气中的氧或湿气产生化学反应生成一层大约10~20Å的二氧化硅,这就是所谓的原生氧化层,室温时这层很薄的二氧化硅可以阻止硅的继续氧化。
图1说明了氧化过程。
图1硅氧化过程示意图氧化过程中的氧是气体,硅来自固态衬底,因此当生长二氧化硅时,就会消耗衬底上的硅,这层薄膜将朝向硅衬底内生长(见图1)。
氧气普遍被使用于形成氧化物的工艺中,如热氧化、化学气相沉积、反应式溅镀沉积,以及刻蚀和剥除光刻胶过程。
氧是地壳中最丰富的元素之一,也是大气中仅次于氮的第二含量元素。
表1是有关氧元素的参数。
表1 氧元素参数列表高温时的热能使氧分子移动得更快,且使氧分子扩散穿过已经形成的氧化层与硅产生化学反应生成更厚的二氧化硅。
温度越高,氧分子移动得就越快,氧化薄膜生长的速度也就越快。
高温生长的氧化薄膜质量比低温生长的薄膜高,所以为了获得高质量的氧化薄膜及较快的生长速率,氧化过程必须在石英炉中高温环境下进行。
氧化是一种很慢的过程,甚至在温度超过1000℃的高温炉中都要花费数小时才能生长出厚度约为5000Å的氧化层。
因此氧化工艺通常是批量过程,可同时处理100~200片的晶圆以获得合理的产量。
干氧氧化工艺干氧氧化的速率比湿氧氧化低,但是氧化薄膜的质量比湿氧氧化的高。
所以薄的氧化层如屏蔽氧化层、垫底氧化层,特别是栅氧化层的生长一般采用干氧氧化工艺。
图2所示为干氧氧化系统示意图。
铝材氧化工艺流程
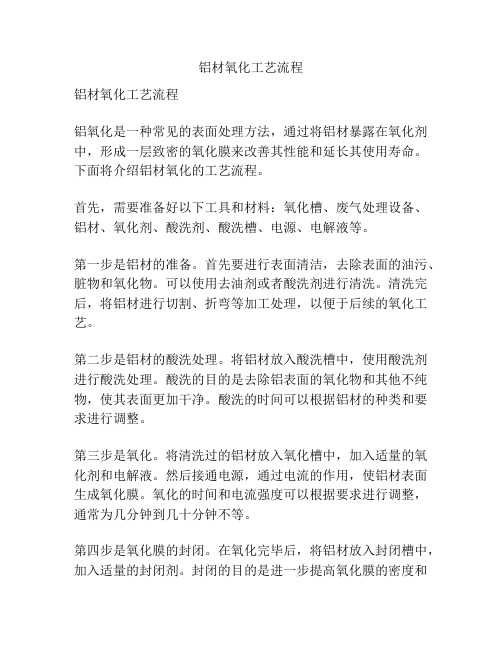
铝材氧化工艺流程铝材氧化工艺流程铝氧化是一种常见的表面处理方法,通过将铝材暴露在氧化剂中,形成一层致密的氧化膜来改善其性能和延长其使用寿命。
下面将介绍铝材氧化的工艺流程。
首先,需要准备好以下工具和材料:氧化槽、废气处理设备、铝材、氧化剂、酸洗剂、酸洗槽、电源、电解液等。
第一步是铝材的准备。
首先要进行表面清洁,去除表面的油污、脏物和氧化物。
可以使用去油剂或者酸洗剂进行清洗。
清洗完后,将铝材进行切割、折弯等加工处理,以便于后续的氧化工艺。
第二步是铝材的酸洗处理。
将铝材放入酸洗槽中,使用酸洗剂进行酸洗处理。
酸洗的目的是去除铝表面的氧化物和其他不纯物,使其表面更加干净。
酸洗的时间可以根据铝材的种类和要求进行调整。
第三步是氧化。
将清洗过的铝材放入氧化槽中,加入适量的氧化剂和电解液。
然后接通电源,通过电流的作用,使铝材表面生成氧化膜。
氧化的时间和电流强度可以根据要求进行调整,通常为几分钟到几十分钟不等。
第四步是氧化膜的封闭。
在氧化完毕后,将铝材放入封闭槽中,加入适量的封闭剂。
封闭的目的是进一步提高氧化膜的密度和耐蚀性。
封闭的时间可以根据要求进行调整。
第五步是工件的清洗和干燥。
将氧化完毕的铝材从封闭槽中取出,进行清洗,去除表面的残留物。
然后进行干燥处理,使铝材表面完全干燥。
最后一步是检验和包装。
将氧化完毕的铝材进行质量检验,检查氧化膜的厚度、均匀性和耐腐蚀性。
通过检验合格后,将铝材进行包装,以防止表面受到污染或损坏。
总的来说,铝材氧化工艺流程包括铝材的准备、酸洗处理、氧化、封闭、清洗和干燥、检验和包装等步骤。
不同材料和要求可能会有所不同,但总的原则是通过清洗、氧化和封闭等处理,提高铝材的表面性能和使用寿命。
这种工艺流程可以广泛应用于铝材的表面处理和防腐蚀等领域。
氧化处理工艺

氧化处理工艺氧化处理工艺是一种将有机物氧化分解为无机物的技术。
该工艺广泛应用于废水处理、垃圾处理和大气污染控制等领域。
氧化处理工艺的步骤通常包括氧化剂的投加,混合和反应等过程。
下面详细介绍氧化处理工艺的原理、类型和应用。
原理:氧化处理技术通过氧化剂的与有机物的反应,使有机物转化为无机物。
氧化反应通常包括以下两种方式:氧化剂和有机物之间的直接反应和氧化剂将有机物转化为更容易氧化的化合物,然后再被氧化剂氧化为无机物。
对于水污染,氧化处理可以将有机物降解为CO2和水,对大气污染,氧化处理则可将有机物氧化为CO2和其他无害气体。
类型:常用的氧化处理方法包括O3氧化、Cl2氧化、H2O2氧化、Fenton氧化和光催化氧化等。
O3氧化:O3氧化是一种通过奥氏体反应将有机物转化为无害有机物的技术。
O3是一种强氧化剂,可将有机物氧化为CO2和H2O。
而且O3处理过程中没有副反应产生,且对环境无二次污染。
Cl2氧化:Cl2氧化操作简单,但由于氯离子本身具有毒性,处理后水中会产生氯离子、有毒化物和对人体有害的三卤甲烷等物质。
因此,Cl2氧化一般不用于废水处理。
H2O2氧化:H2O2氧化是一种较为常见的氧化反应方法,H2O2在钯催化下可分解产生自由氧基,从而与有机物反应并氧化分解为无害的无机物。
Fenton氧化:Fenton氧化利用Fe2+和H2O2生成以Fe3+为催化剂的羟基自由基,具有催化活性,能够高效地将有机物氧化分解。
光催化氧化:光催化氧化是一种新型的氧化处理方法,其主要利用光催化剂将有机物光催化分解为无害物质。
光催化氧化具有能源消耗低、无二次污染等优点,受到广泛关注。
应用:氧化技术的应用范围非常广泛,主要用于水处理和大气污染控制。
废水氧化处理是将工业废水中的有机物降解转化为无机物,以满足工业废水排放的标准。
氧化技术在VOCs处理中也应用广泛,VOCs会对环境造成严重的污染,通过氧化技术的处理可以将这些有机物转化为无害零排放。
氧化处理工艺流程
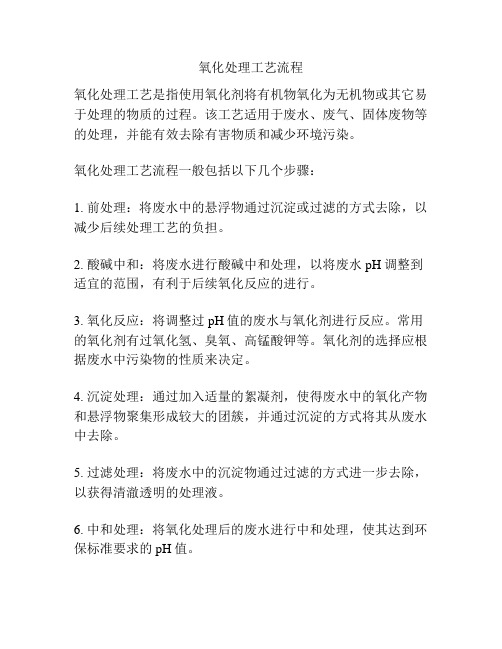
氧化处理工艺流程氧化处理工艺是指使用氧化剂将有机物氧化为无机物或其它易于处理的物质的过程。
该工艺适用于废水、废气、固体废物等的处理,并能有效去除有害物质和减少环境污染。
氧化处理工艺流程一般包括以下几个步骤:1. 前处理:将废水中的悬浮物通过沉淀或过滤的方式去除,以减少后续处理工艺的负担。
2. 酸碱中和:将废水进行酸碱中和处理,以将废水pH调整到适宜的范围,有利于后续氧化反应的进行。
3. 氧化反应:将调整过pH值的废水与氧化剂进行反应。
常用的氧化剂有过氧化氢、臭氧、高锰酸钾等。
氧化剂的选择应根据废水中污染物的性质来决定。
4. 沉淀处理:通过加入适量的絮凝剂,使得废水中的氧化产物和悬浮物聚集形成较大的团簇,并通过沉淀的方式将其从废水中去除。
5. 过滤处理:将废水中的沉淀物通过过滤的方式进一步去除,以获得清澈透明的处理液。
6. 中和处理:将氧化处理后的废水进行中和处理,使其达到环保标准要求的pH值。
7. 二次沉淀:对中和处理后的废水进行二次沉淀处理,以保证废水中的悬浮物和沉淀物得到充分去除。
8. 脱色处理:将废水经过适当的脱色剂处理,以去除废水中的色度物质,提高废水的透明度。
9. 洗涤处理:将废水进行洗涤处理,以除去脱色剂残留和产生的废液。
10. 余热回收:废水处理过程中产生的热能可以通过余热回收技术进行回收利用,减少资源浪费和能源消耗。
最后,经过氧化处理工艺流程处理后的废水可以得到达标排放的水质,从而减少对环境的污染。
此外,氧化处理工艺还能有效地去除废气中的有害物质和处理固体废物,实现资源的回收和再利用。
总之,氧化处理工艺流程在实际应用中具有广泛的适用性和可操作性,可以有效地将有机物氧化为无机物或易于处理的物质,实现废水、废气、固体废物的净化和资源的回收利用。
但在操作过程中需要根据实际情况选择适宜的氧化剂和操作条件,以保证处理效果和经济性。
氧化工艺介绍

氧化工艺介绍以氧化工艺介绍为题,我们将探讨氧化工艺的基本概念、应用领域、工艺流程和相关技术。
一、氧化工艺的基本概念氧化工艺是指通过氧化反应将物质转化为氧化产物的一种化学工艺。
在氧化反应中,物质与氧气发生化学反应,形成氧化产物。
氧化工艺广泛应用于能源、化工、冶金、材料等领域,具有重要的经济和社会价值。
二、氧化工艺的应用领域1. 能源领域:氧化工艺在燃烧、发电和燃料电池等能源转换过程中起着重要作用。
例如,燃烧是一种氧化反应,将燃料与氧气反应产生热能,用于发电和供暖。
2. 化工领域:氧化工艺在化学合成、催化反应和有机合成等过程中具有广泛应用。
例如,氧化反应可以将烯烃氧化成醛、酮等有机化合物,用于生产化工原料和药品。
3. 冶金领域:氧化工艺在冶金炼焦、炼铁和炼钢等过程中扮演重要角色。
例如,炼铁过程中的高炉燃烧反应是一种氧化反应,将铁矿石转化为铁。
4. 材料领域:氧化工艺在材料制备和改性中有着广泛应用。
例如,金属氧化物是一类重要的材料,可以通过氧化反应制备出来,具有特殊的物理和化学性质。
三、氧化工艺的工艺流程氧化工艺的工艺流程可以分为反应前处理、反应过程和产物分离三个主要步骤。
1. 反应前处理:在进行氧化反应之前,需要对原料进行预处理。
预处理可以包括物料研磨、干燥、筛分等步骤,以提高反应效率和产物质量。
2. 反应过程:反应过程是氧化工艺的核心部分,主要是通过控制反应条件来实现氧化反应。
反应条件包括反应温度、反应压力、反应时间和反应物的配比等。
通过调节这些条件,可以控制反应速率和产物选择性。
3. 产物分离:在氧化反应完成后,需要对产物进行分离和纯化。
分离过程可以包括过滤、蒸馏、结晶等步骤,以获得纯净的氧化产物。
四、氧化工艺的相关技术1. 催化剂技术:在氧化反应中,催化剂可以提高反应速率和选择性。
常用的氧化反应催化剂包括金属催化剂、氧化物催化剂和酶催化剂等。
2. 反应工程技术:反应工程技术可以优化氧化反应的工艺条件,提高反应效率和产物质量。
铝件氧化处理工艺

铝件氧化处理工艺
铝件氧化处理工艺是指将铝件表面进行氧化处理,形成一层氧化膜的工艺。
氧化膜具有一定的硬度、耐磨性、耐腐蚀性和绝缘性,能够提高铝件的表面质量和使用寿命。
一般的铝件氧化处理工艺流程包括以下步骤:
1. 清洗:将铝件表面的油污、灰尘等物质清洗干净,常见的清洗方法有机械清洗、化学清洗等。
2. 预处理:对铝件进行活化处理,以增加其表面的活性,常见的预处理方法有酸洗、碱洗等。
3. 氧化:将铝件浸泡在氧化液中,通过电解氧化或化学氧化等方式,使铝件表面与氧化液发生反应,形成一层氧化膜。
4. 封闭:将铝件经过氧化处理后,进行封闭处理,以增加氧化膜的密封性和耐腐蚀性。
以上是一种常见的铝件氧化处理工艺,具体的工艺参数和步骤还会根据不同的应用和要求而有所调整。
不锈钢氧化处理工艺流程

不锈钢氧化处理工艺流程不锈钢氧化处理是一种将不锈钢表面处理成氧化膜的工艺,可以增加不锈钢的耐蚀性和装饰性。
主要包括准备工作、氧化处理、清洗工序和包装封存。
下面将详细介绍不锈钢氧化处理的工艺流程。
一、准备工作1. 确定处理对象:首先,需要确定需要进行氧化处理的不锈钢产品种类和规格,明确处理对象。
2. 设计处理方案:根据不锈钢产品的种类和要求,设计氧化处理的方案,包括氧化处理工艺参数和处理设备选择。
3. 准备材料和设备:准备好氧化处理所需的材料和设备,如氧化剂、清洗液、工艺设备等。
4. 安全防护:在进行氧化处理前,需要做好安全防护工作,包括穿戴防护服、戴防护眼镜等。
二、氧化处理1. 清洗表面:在进行氧化处理前,需要先将不锈钢产品表面进行清洗,去除表面的油污和杂质。
2. 预处理:将清洗后的不锈钢产品放入氧化处理设备中,按照设定的氧化处理参数进行预处理,包括时间和温度等参数。
3. 氧化处理:在预处理完成后,开始进行氧化处理,将不锈钢产品暴露在氧化剂中,使其表面形成氧化膜。
4. 控制处理参数:在氧化处理过程中需要严格控制处理参数,如温度、时间和氧化剂浓度等参数。
5. 冷却处理:处理完成后,将不锈钢产品进行冷却处理,使其表面形成均匀的氧化膜。
三、清洗工序1. 氧化膜去除:将氧化处理后的不锈钢产品进行清洗,去除表面的氧化膜,使其表面光洁。
2. 中和处理:在氧化处理后,还需要进行中和处理,以去除氧化剂残留和中和处理产生的废液。
3. 冷却处理:清洗完成后,将产品进行冷却处理,以确保其表面不受影响。
四、包装封存1. 包装:对清洗后的不锈钢产品进行包装,防止其受到二次污染。
2. 封存:将包装好的不锈钢产品进行封存,存放在干燥通风的地方,避免阳光直射和高温环境。
以上就是不锈钢氧化处理工艺流程的详细介绍,通过严格执行工艺参数和流程要求,可以确保不锈钢产品表面形成优质的氧化膜,提高其耐蚀性和装饰性,延长使用寿命。
希望对不锈钢氧化处理有所帮助。
氧化工艺作业ppt课件

(4)泄漏应急处理
应急行动:迅速撤离泄漏污染区人员至上风处,并 立即隔离150m,严格限制出入。切断火源。建议应 急处理人员戴自给正压式呼吸器,穿防静电工作服。 尽可能切断泄漏源。用工业覆盖层或吸附/吸收剂盖 住泄漏点附近的下水道等地方,防止气体进入。合 理通风,加速扩散。喷雾状水稀释、溶解。构筑围 堤或挖坑收容产生的大量废水。如有可能,将漏出 气用排风机送至空旷地方或装设适当喷头烧掉。漏 气容器要妥善处理,修复、检验后再用。
15
(二)二氧化硫氧化制硫酸工艺
硫酸是化学工业的重要产品之一,也是许多工业生 产的重要化工原料,属于基本化学工业。工业制备 硫酸主要有塔式法、铅室法和接触法。下面主要介 绍接触法。
1、反应物的准备及成分要求 在接触法硫酸生产中,利用沸腾炉将硫铁矿进行焚烧, 制得含有二氧化硫的炉气,为了保证氧化反应的顺 利进行,需要对炉气进行除尘、净化和干燥处理, 除去重金属物质、水分及有害物质,余下的主要是 二氧化硫、氧气和氮气。二氧化硫和氧气在钒催化 剂作用下发生氧化反应,制成三氧化硫,称为二氧 化硫的催化氧化,这是生产硫酸过程中的重要一步。 16
①二氧化硫
无色气体,有强烈刺激性气味。大气主要污染物之一。
浓度高时使人呼吸困难,甚至死亡。易被湿润的粘
膜表面吸收生成亚硫酸、硫酸。对眼及呼吸道粘膜
有强烈的刺激作用。大量吸入可引起肺水肿、喉水
肿、声带痉挛而致窒息。轻度中毒时,发生流泪、
畏光、咳嗽,咽、喉灼痛等;严重中毒可在数小时
内发生肺水肿;极高浓度吸入可引起反射性声门痉
8
(2)混合器生产过程的控制 氧化工段另一个不安全因素是混合器。为避免混
合器内氧浓度局部区域过高而发生着火和爆炸,在设 计和制造中,必须使含氧气体从喷嘴高速喷出,其速度 大大超过含乙烯循环气体的火焰传播速度,并使从喷 嘴平行喷出的多股含氧气体各自与周围的循环气体 均匀混合,从而避免产生氧浓度局部过高的现象,尽量 缩小非充分混合区。此外,还应防止含乙烯循环气体 返回到含氧气体的配管中。
铝氧化工艺流程

铝氧化工艺流程
铝氧化工艺流程是指将铝制品经过特定的处理步骤,使其表面形成一层均匀、致密、耐腐蚀的氧化层的过程。
铝氧化工艺流程通常包括以下几个步骤:预处理、电解氧化、封孔和上色、封闭、清洗与包装。
预处理是铝氧化工艺流程的第一步,主要是为了去除铝制品表面的油污、尘埃和异物。
该步骤通常采用碱洗、酸洗等方法,以确保铝制品表面干净、无杂质。
电解氧化是铝氧化工艺流程的核心步骤,也是形成氧化层的关键。
该步骤采用直流电解的方法,将铝制品作为阴极,放入电解槽中,然后通过电流的作用,使铝表面的氧化层逐渐形成。
电解槽中的电解液一般为硫酸、硫酸铝等溶液。
封孔和上色是铝氧化工艺流程的后续步骤。
在电解氧化后,铝制品表面会形成微小的气孔,需要通过封孔处理来填补这些气孔,使氧化层更加致密。
上色是指通过染色剂将铝制品表面的氧化层染成不同颜色,以满足客户的需求。
封闭是铝氧化工艺流程的最后一步,主要是为了增加氧化层的耐腐蚀性能和机械性能。
该步骤通常采用热水封闭、热油封闭等方法,使氧化层与铝基体更加牢固地结合在一起。
清洗与包装是铝氧化工艺流程的最后两个环节。
清洗是为了将工艺过程中产生的废液和杂质清除掉,以保证铝制品表面的干净。
包装则是将经过铝氧化处理的铝制品进行包装,以防止其
再次被污染或受到损坏。
总的来说,铝氧化工艺流程是一个复杂而精细的过程,需要严格控制工艺参数和操作步骤,才能够得到符合要求的氧化层。
铝氧化可以提高铝制品的表面性能,延长其使用寿命,并且可以根据需要调整其颜色和厚度,广泛应用于航空航天、汽车、建筑等行业。
氧化工艺流程

氧化工艺流程一、表面预处理无论采用何种方法加工的铝材及制品,表面上都会不同程度地存在着污垢和缺陷,如灰尘、金属氧化物(天然的或高温下形成的氧化铝薄膜)、残留油污、沥青标志、人工搬运手印(主要成分是脂肪酸和含氮的化合物)、焊接熔剂以及腐蚀盐类、金属毛刺、轻微的划擦伤等。
因此在氧化处理之前,用化学和物理的方法对制品表面进行必要的清洗,使其裸露纯净的金属基体,以利氧化着色顺利进行,从而获得与基体结合牢固、色泽和厚度都满足要求且具有最佳耐蚀、耐磨、耐侯等良好性能的人工膜。
(一)脱脂铝及铝合金表面脱脂有有机溶剂脱脂、表面活性剂脱脂、碱性溶液脱脂、酸性溶液脱脂、电解脱脂、乳化脱脂。
乳化溶液石蜡三乙醇胺油酸松油水8.0%0.25%0.5%2.25%89% 常温适当水清洗溶液组成以体积记有机溶剂是利用油脂易溶于有机溶剂的特点进行脱脂,常用的溶剂有汽油、煤油、乙醇、乙酸异戊脂、丙酮、四氯化碳、三氯乙烯等。
有机溶剂仅用于小批量小型的或极污秽的制品脱脂处理。
表面活性剂是一些在很低的浓度下,能显着降低液体表面张力的物质。
常用于脱脂的表面活性剂有肥皂、合成洗涤剂、十二烷基硫酸钠、十二烷基苯磺酸钠等。
碱性脱脂溶液的配方非常多,传统工艺采用磷酸钠、氢氧化钠和硅酸钠,其中磷酸钠和硅酸钠有缓蚀、润湿、稳定作用,溶液加热和搅拌有助于获得最好的脱脂效果。
油脂在酸的存在下也能进行水解反应生成甘油和相应的高级脂肪酸。
电解脱脂可用阳极电流、阴极电流或交流电。
在碱性溶液中阴极电流脱脂,阳极最好为镀镍钢板。
其在铝及铝合金表面处理中不常用。
乳化脱脂所用的溶液为互不溶解的水与有机溶剂组成的两相或多相溶液,并添加有降低表面张力及对各相均有亲和力的去污剂。
(二)碱蚀剂碱蚀剂是铝制品在添加或不添加其他物质的氢氧化钠溶液中进行表面清洗的过程,通常也称为碱腐蚀或碱洗。
其作用是作为制品经某些脱脂方法脱脂后的补充处理,以便进一步清理表面附着的油污赃物;清除制品表面的自然氧化膜及轻微的划擦伤。
氧化工艺相关知识

氧化工艺相关知识1、工艺简介氧化为有电子转移的化学反应中失电子的过程,即氧化数升高的过程。
多数有机化合物的氧化反应表现为反应原料得到氧或失去氢。
涉及氧化反应的工艺过程为氧化工艺。
常用的氧化剂有:空气、氧气、双氧水、氯酸钾、高锰酸钾、硝酸盐等。
2、典型工艺乙烯氧化制环氧乙烷;甲醇氧化制备甲醛;对二甲苯氧化制备对苯二甲酸;环己烷氧化制环己酮;天然气氧化制乙炔;丁烯、丁烷、C馏分或苯的氧化制顺丁烯二酸酐;4邻二甲苯或萘的氧化制备邻苯二甲酸酐;对氯甲苯氧化制备对氯苯甲醛(酸);甲苯氧化制备苯甲醛(酸);对硝基甲苯氧化制备对硝基苯甲酸;环己酮/醇混合物的氧化制己二酸;乙二醛硝酸氧化法合成乙醛酸;丁醛氧化制丁酸;氨氧化制硝酸等。
3、工艺危险特点反应原料及产品具有燃爆危险性;反应气相组成容易达到爆炸极限,具有闪爆危险;部分氧化剂具有燃爆危险性,如氯酸钾、高锰酸钾、铬酸酐等都属于氧化剂,如遇高温或受撞击、摩擦以及与有机物、酸类接触,皆能引起火灾爆炸;产物中易生成过氧化物,化学稳定性差,受高温、摩擦或撞击作用易分解、燃烧或爆炸。
4、重点监控单元氧化反应釜;重点监控工艺参数;氧化反应釜内温度和压力;氧化反应釜内搅拌速率;氧化剂流量;反应物料的配比;气相氧含量;过氧化物含量等。
5、安全控制的基本要求反应釜温度和压力的报警和联锁;反应物料的比例控制和联锁及紧急切断动力系统;紧急断料系统;紧急冷却系统;紧急送入惰性气体的系统;气相氧含量监测、报警和联锁;安全泄放系统;可燃和有毒气体检测报警装置等。
6、措施建议涉及氧化工艺的企业应及时委托专业机构进行反应风险评估,并根据评估结果采取相应措施保证工艺安全。
将氧化反应釜内温度和压力与反应物的配比和流量、氧化反应釜夹套冷却水进水阀、紧急冷却系统形成联锁关系,在氧化反应釜处设立紧急停车系统,当氧化反应釜内温度超标或搅拌系统发生故障时自动停止加料并紧急停车。
配备安全阀、爆破片等安全设施。
铝合金氧化工艺流程
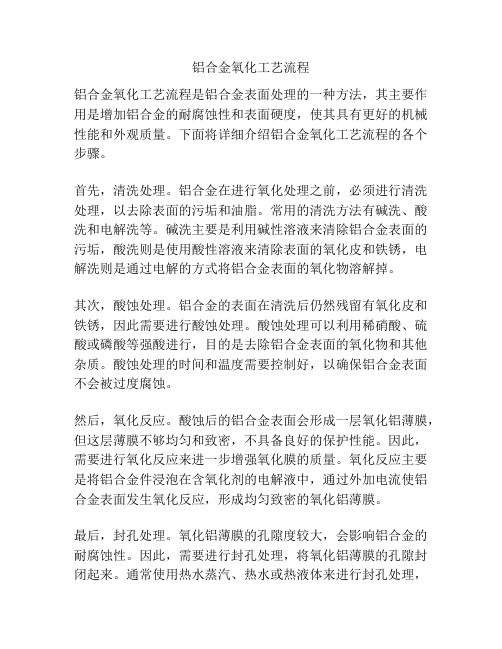
铝合金氧化工艺流程铝合金氧化工艺流程是铝合金表面处理的一种方法,其主要作用是增加铝合金的耐腐蚀性和表面硬度,使其具有更好的机械性能和外观质量。
下面将详细介绍铝合金氧化工艺流程的各个步骤。
首先,清洗处理。
铝合金在进行氧化处理之前,必须进行清洗处理,以去除表面的污垢和油脂。
常用的清洗方法有碱洗、酸洗和电解洗等。
碱洗主要是利用碱性溶液来清除铝合金表面的污垢,酸洗则是使用酸性溶液来清除表面的氧化皮和铁锈,电解洗则是通过电解的方式将铝合金表面的氧化物溶解掉。
其次,酸蚀处理。
铝合金的表面在清洗后仍然残留有氧化皮和铁锈,因此需要进行酸蚀处理。
酸蚀处理可以利用稀硝酸、硫酸或磷酸等强酸进行,目的是去除铝合金表面的氧化物和其他杂质。
酸蚀处理的时间和温度需要控制好,以确保铝合金表面不会被过度腐蚀。
然后,氧化反应。
酸蚀后的铝合金表面会形成一层氧化铝薄膜,但这层薄膜不够均匀和致密,不具备良好的保护性能。
因此,需要进行氧化反应来进一步增强氧化膜的质量。
氧化反应主要是将铝合金件浸泡在含氧化剂的电解液中,通过外加电流使铝合金表面发生氧化反应,形成均匀致密的氧化铝薄膜。
最后,封孔处理。
氧化铝薄膜的孔隙度较大,会影响铝合金的耐腐蚀性。
因此,需要进行封孔处理,将氧化铝薄膜的孔隙封闭起来。
通常使用热水蒸汽、热水或热液体来进行封孔处理,将温度控制在60-90℃之间,时间根据封孔效果的要求而定。
整个铝合金氧化工艺流程主要包括清洗处理、酸蚀处理、氧化反应和封孔处理等几个步骤。
在实际应用中,还可以根据具体需求对这些步骤进行调整和改进,以获得更好的氧化效果和表面质量。
同时,注意控制每个步骤的工艺参数,确保每个工艺步骤的质量稳定和一致性,从而提高铝合金的氧化质量和性能。
压铸铝阳极氧化工艺
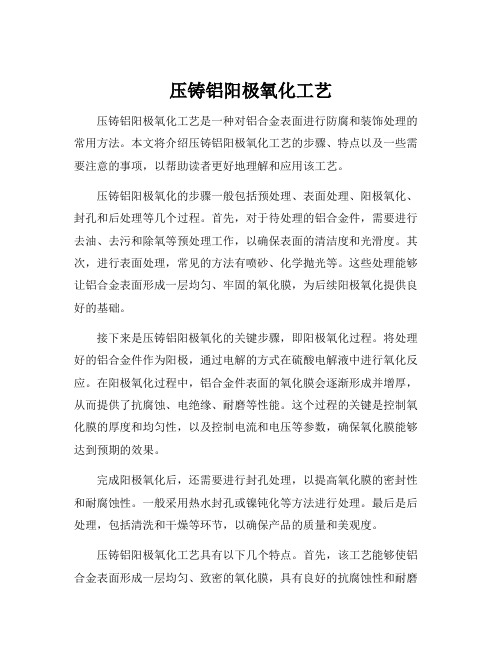
压铸铝阳极氧化工艺压铸铝阳极氧化工艺是一种对铝合金表面进行防腐和装饰处理的常用方法。
本文将介绍压铸铝阳极氧化工艺的步骤、特点以及一些需要注意的事项,以帮助读者更好地理解和应用该工艺。
压铸铝阳极氧化的步骤一般包括预处理、表面处理、阳极氧化、封孔和后处理等几个过程。
首先,对于待处理的铝合金件,需要进行去油、去污和除氧等预处理工作,以确保表面的清洁度和光滑度。
其次,进行表面处理,常见的方法有喷砂、化学抛光等。
这些处理能够让铝合金表面形成一层均匀、牢固的氧化膜,为后续阳极氧化提供良好的基础。
接下来是压铸铝阳极氧化的关键步骤,即阳极氧化过程。
将处理好的铝合金件作为阳极,通过电解的方式在硫酸电解液中进行氧化反应。
在阳极氧化过程中,铝合金件表面的氧化膜会逐渐形成并增厚,从而提供了抗腐蚀、电绝缘、耐磨等性能。
这个过程的关键是控制氧化膜的厚度和均匀性,以及控制电流和电压等参数,确保氧化膜能够达到预期的效果。
完成阳极氧化后,还需要进行封孔处理,以提高氧化膜的密封性和耐腐蚀性。
一般采用热水封孔或镍钝化等方法进行处理。
最后是后处理,包括清洗和干燥等环节,以确保产品的质量和美观度。
压铸铝阳极氧化工艺具有以下几个特点。
首先,该工艺能够使铝合金表面形成一层均匀、致密的氧化膜,具有良好的抗腐蚀性和耐磨性。
其次,氧化膜的厚度和颜色可以通过控制工艺参数进行调节和改变,满足不同需求。
此外,该工艺对环境友好,不产生有害物质,符合环保要求。
在进行压铸铝阳极氧化时,还需注意一些事项。
首先,要选择适合的氧化电解液和工艺参数,以确保氧化膜的质量和均匀性。
其次,要注意控制电流和电压,避免过大或过小对氧化膜产生负面影响。
此外,还要注意控制处理时间,过长可能导致氧化膜变厚或堆积不均匀。
总结起来,压铸铝阳极氧化工艺是一种常用的铝合金表面处理方法,通过预处理、表面处理、阳极氧化、封孔和后处理等过程,能够使铝合金件表面形成具有良好防腐和装饰效果的氧化膜。
高级氧化工艺
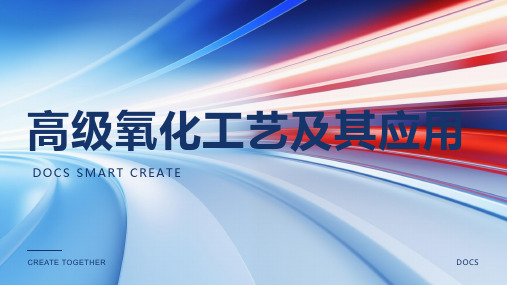
高级氧化工艺在催化剂制备中的应用
催化剂在高级氧化工艺中的作用
高级氧化工艺在催化剂制备中的应用
• 提高自由基的产生和氧化效果
• 利用高级氧化工艺制备新型催化剂
• 降低氧化剂和能源消耗
• 提高催化剂的性能和稳定性
高级氧化工艺在其他领域的发展趋势
高级氧化工艺在环境领域的应用
• 废水处理
高级氧化工艺的氧化机理
高级氧化工艺的主要氧化剂
高级氧化工艺的氧化机理
• ·OH自由基
• 通过产生高活性的自由基来降解有机污染物
• O3
• 降解过程中产生的小分子物质可被进一步氧化
• H2O2
• 最终转化为无害的物质
影响高级氧化工艺效果的因素
氧化剂的种类和浓度
反应条件
污染物性质
• 影响自由基的产生和氧化效果
采用复合氧化工艺
• 结合两种或多种氧化工艺
• 提高氧化效果
• 降低能耗
利用催化剂和助剂
• 使用催化剂提高自由基的产生和氧化效果
• 使用助剂改善反应条件
⌛️
04
高级氧化工艺在废水处理中的应用
废水处理中高级氧化工艺的选择
根据废水性质和污染物的种类
• 选择合适的氧化工艺
• 提高废水处理效果
考虑经济性和实用性
• 氧化剂和催化剂的价格较高
• 工艺操作复杂,需要较高的运行成本
高级氧化工艺的副产物问题
• 氧化过程中产生有毒副产物
• 需要进一步处理以降低环境污染
05
高级氧化工艺在废气处理中的应用
废气处理中高级氧化工艺的选择
根据废气性质和污染物的种类
考虑经济性和实用性
- 1、下载文档前请自行甄别文档内容的完整性,平台不提供额外的编辑、内容补充、找答案等附加服务。
- 2、"仅部分预览"的文档,不可在线预览部分如存在完整性等问题,可反馈申请退款(可完整预览的文档不适用该条件!)。
- 3、如文档侵犯您的权益,请联系客服反馈,我们会尽快为您处理(人工客服工作时间:9:00-18:30)。
⑤ Na+的中性化:
4 热氧化机制
(1) 基本机理 Si(固态)+ O2 (气态) SiO2 (固态)(>1000 ℃) 热氧化是在Si/SiO2 界面进行,通过扩散与化学反应 实 现 。 O2 或 H2 O 在 生 成 的 二 氧 化 硅 内 扩 散 , 到 达 Si/SiO2界面后再与Si反应。 结果:硅被消耗而变薄,氧化层增厚。 生长1μm厚SiO2约消耗0.45μm厚的硅 dSi =0.45dSiO2
硅 胶 及 硅 胶 产 品
硅酸盐
☆硅酸盐是构成地壳岩石的主要成分,自然界中存在 的各种天然硅酸盐矿物,约占地壳质量的5%。 ☆硅酸盐种类很多,多数难溶于水,只有钾、钠盐是 可溶的。硅酸钠(Na2SiO3)溶液俗称水玻璃,又叫泡花碱。
☆硅酸盐结构很复杂,通常可用二氧化硅和金属氧化 物的形式来表示其组成。
◆硅酸钠 Na2SiO3 Na2O· 2 SiO
◆高岭石
Al2(Si2O5)(OH)4
Al2O3· 2SiO2· 2O 2H
硅酸盐组成的表示方法
硅酸盐的种类很多,结构也很复杂,通常可用 二氧化硅和金属氧化物的形式来表示其组成。 表示方法:金属氧化物写在前面,再写SiO2, 最后写H2O;氧化物之间用“·”隔开。
其中:tox 为氧化层厚度;L1 和L2 是特征距离,C1 和 C2是比例常数。
硅的氧化系数
干氧 温度(℃) A(μm) B(μm2/h) τ(h) A(μm) B(μm2/h) 湿氧
800
920 1000
0.37
0.235 0.165
0.0011
0.0049 0.0117
9
1.4 0.37
—
0.5 0.226
查表得知, o C时,A=0.50 m,B=0.203 m 2 /h 920 to 2 At0 (0.1 m)2 +0.5 m 0.1 m = =0.295h 2 B 0.203 m /h 据公式tox 2 Atox B(t )有: A A 2 4 B(t ) tox =0.48 m 2 注意:A tox,这种情况下不能用近似法。
第六章 氧化工艺
二氧化硅的基本特性 二氧化硅膜的用途 二氧化硅膜的制备方法 热氧化机制 热氧化系统
硅的氧化物及硅酸盐构成了地壳中大部 分的岩石、沙子和土壤、约占地壳总量 的90%以上。
二氧化硅(SiO2)
二氧化硅广泛存在 于自然界中,与其 他矿物共同构成了 岩石。天然二氧化 硅也叫硅石,是一 种坚硬难熔的固体。
于是有氧化层厚度与时间的关系:
当
时有:
当
时有:
(3) 热氧化生长的两个阶段 ① 线性阶段
当
时有: 简记为:
tox=B/At
② 抛物线阶段(生长逐渐变慢,直至不可忍受)
当
时有:
简记为:
t ox Bt
B/A被称为线性速率系数;而B被称为抛物线速率系数
硅(100)晶面干氧氧化速率与氧化层厚度的关系
灯型系统 石英托盘 工艺气体 排气 口 十字钨灯 晶圆
干燥压缩 空气通道
工艺气体 进气 口
门
循环 水 入口 传感 器
纵向钨灯
过滤 器 管型高 温计
晶圆感应 高温 计
由示意图可看出,加热源(十字钨灯)在晶园 的上面,这样晶园就可被快速加热。热辐射偶合进入 晶园表面并快度到达工艺温度,由于加热时间很短, 晶园体内温度并未升温,这在传统的反应炉内是不可 能实现的。用这个工艺进行离子注入后的退火,就意 味着晶格破坏修复了,而掺入杂质的分布没有改变。 RTP技术不只是用在“退火工艺”,对于MOS栅 极中薄的氧化层的生长是自然而然的选择,由于器件 尺寸越来越小的趋势使得加在晶园上的每层的厚度越 来越薄,厚度减少最显著的是栅极氧化层。先进的器 件要求栅极厚度小于0.01微米。如此薄的氧化层对于 普通的反应
快速加热工艺(RTP)
快速加热工艺主要是用在离子注入后的退火,目的是消除由于 注入带来的晶格损伤和缺陷。传统上的退火工艺由炉管反应炉来 完成。
普通退火消除缺陷的同时又会带来一些其他的负面影响,比如 ,掺杂的再分布。这又是不希望发生的。这就使得人们在寻找其 它的退火方式,这个方式仍是快速加热工艺。 RTP工艺是基于热辐射原理,参见下图
B:减少硅表面及氧化层的结构缺陷
③ 气源:
气态气源: Cl2 HCl 液态气源: 三氯乙烯C2HCl3(TCE) 氯仿CHCl3(TCA) 都为剧毒物; 半导体工业常用HCl,液态也用氯仿。
④ Cl-Si-O复合体:
SiO2/Si界面过渡区存在大量过剩的Si,其中硅键并未饱 和,所以可以通过反应生成Cl-Si-O复合体。 Si-O键能(870kJ/mol)> Si-Cl键能(627kJ/mol),所 以在高温下,有氧和水汽存在时,会使Cl-Si键离解。
原理: 氧化剂扩散到SiO2/Si界面与硅反应。 Si + O2 SiO2
>1000度
随着氧化层的增厚,氧气扩散时间延长,生 长速率减慢。
(2)水汽氧化
气源:气泡发生器或氢氧合成气源
① 气泡发生器 缺点: A:水温易波动 B:气泡发生器可能成为污染源
② 氢氧合成氧化 优点: A:容易得到干净和干燥的气体 B:气体流量精确可控 因此②是LSI和VLSI中比较理想的氧化技术 易爆炸性(解决办法:氧气过量)
源区 消声器
中央区
装载区
氧化 炉管
比例 控制器
温度 O
平区 距离
快速升温反应炉
随着晶园尺寸越来越大,升温降温时间会增加,成本也越来越 高。解决这个问题的手段就是确保最大批量,但这又会减慢流程 。为了解决这个问题,引进了快速升温、小批量生产的反应炉, 这就是大功率加热的小型水平炉。通常反应炉每分钟升温几度, 而快速升温反应炉每分钟升温十几度。小容量的低效率缺陷由快 速的反应时间来补偿。
—
0.203 0.287
1100
1200
0.09
0.04
0.027
0.045
0.076
0.027
0.11
0.05
0.51
0.72
其中:τ是考虑到自然氧化层的因素,250Å左右。
计算在120分钟内,920℃水汽氧化(640Torr)过程中生长 的二氧化硅层的厚度。假定硅片在初始状态时已有1000埃的 氧化层。
④ 网络形成剂
⑤ 本征二氧化硅 无杂质的二氧化硅
二氧化硅的性质
二氧化碳(CO2) 存在 结构
空气 分子晶体,存在CO2分子。 无色气体,熔、沸点低,微溶于 水 CO2+ H2O ⇋H2CO3 CO2+2NaOH=Na2CO3+H2O
二氧化硅(SiO2)
存在于岩石中,硅石、石英、 水晶、硅藻土 原子晶体,不存在SiO2分子
(3) 绝缘介质 SiO2介电性质良好: ① IC器件的隔离和多层布线的电隔离
②
MOSFET的栅电极
③
MOS电容的绝缘介质
3 二氧化硅膜的制备方法
氧化工艺的定义
在硅或其它衬底上生长一层二氧化硅膜。
制备二氧化硅膜的方法有:热生长氧化法、化学气 相沉积等。但目前主要使用的还是热生长氧化法。
1. 硅暴露在空气中,则在室温下即可产生二氧化硅层,厚 度约为250埃。
迪尔-格罗夫氧化模型
NG NGS NOS NS 度 tox
hG: 气相质量转移系数
气体内部氧化剂浓度 SiO2表面外侧氧化剂浓度 SiO2表面内侧氧化剂浓度 SiO2/Si界面处氧化剂浓 SiO2薄膜的厚度
F1:氧化剂由气体内部传输到气体和氧化物界面的粒子流密度,即单位 时间通过单位面积的原子数或分子数。
D0:氧化剂在SiO2中的扩散系数。 F2 :氧化剂扩散通过已生成的二氧化硅到达SiO2/Si界面的 扩散流密度。
Ks:表面化学反应速率常数
F3 :SiO2/Si界面处,氧化剂和硅反应生成新的SiO2 层的反 应流密度。
假设氧化过程为平衡过程,且氧化气体为理想气体, 则平衡态下应有: F1 = F2 = F3
2. 如果需要得到更厚的氧化层,必须在氧气气氛中加热。
3. 硅的氧化反应是发生在Si/SiO2界面,这是因为:Si在
SiO2中的扩散系数比O的扩散系数小几个数量级。
热生长氧化法优点:致密、纯度高、膜厚均匀等;
缺点:需要暴露的硅表面、生长速率低、需要高温。
2、热氧化生长方法
热氧化生长方法是最常用的得到二氧化硅薄膜的方法。 分类: (1)干氧氧化 (2)水汽氧化 (3)湿氧氧化 (4)掺氯氧化
B 禁锢污染物——落在晶圆上的污染物(主要是移动的离 子污染物)在二氧化硅的生长过程中被禁锢在二氧化硅膜 中,在那里对器件的伤害最小。
(2) 掺杂阻挡层(作为杂质扩散的掩蔽膜) 选择二氧化硅的理由: A 杂质在二氧化硅中的运行速度 低于在硅中的运行速度 B 二氧化硅的热膨胀系数与硅接 近
二氧化硅起掩蔽作用的条件: A:D二氧化硅<<D硅 B:二氧化硅膜有足够的厚度 对于B、P、As等元素,D二氧化硅 <<D硅,因此二氧化硅可以 作为杂质扩散的掩蔽膜。
硅酸钠:Na2SiO3可以写成Na2O · 2 SiO 高岭石:Al2(Si2O5)(OH)4 Al2O3 · 2SiO2 · 2O 2H 钙长石:CaAl2SiO6 CaO · 2O3 · 2 Al SiO
高岭石
2、二氧化硅膜的用途
(1) 表面钝化 A 保护器件的表面及内部——二氧化硅密度非常高,非 常硬,保护器件免于沾污、损伤和化学腐蚀。
பைடு நூலகம்
几个概念
① 桥键氧原子
位于四面体之间,为两个硅原子 所共有的氧原子称桥键氧原子。
② 非桥键氧原子