公差与粗糙度对应关系
公差与粗糙度对应关系

公差与粗糙度对应关系公差和粗糙度是制造工程中两个重要的概念。
公差是指零件尺寸允许的最大偏差范围,而粗糙度则是表面的不光滑程度。
它们之间存在一定的对应关系,本文将就此进行探讨。
公差和粗糙度在制造工程中是必不可少的。
公差是为了保证零件的尺寸精度,在制造过程中会存在一定的误差,而公差的设置可以容许这些误差的存在,确保零件能够正常使用。
而粗糙度则是表面质量的指标,直接影响着零件的摩擦、密封和耐磨性能。
因此,公差和粗糙度的合理设置对于零件的质量和性能至关重要。
公差与粗糙度之间的对应关系主要体现在制造工艺中。
在零件的设计和制造中,需要根据零件的功能和使用要求来确定公差和粗糙度的要求。
一般来说,公差的要求越高,制造工艺的难度越大,对设备和工艺的要求也越高;而对于粗糙度的要求,需要根据零件的表面功能来确定,如需要有良好的密封性能,则需要较低的粗糙度要求。
在实际的制造过程中,公差和粗糙度的对应关系需要综合考虑多个因素。
首先是制造工艺的能力。
如果制造工艺无法满足较高的公差要求,则需要适当调整粗糙度的要求,以确保零件的尺寸精度;反之亦然。
其次是零件的功能和使用要求。
如果零件需要有较高的密封性能,则需要较低的粗糙度要求,以确保表面的平滑度和光洁度;而如果零件的功能主要是传递力或保持定位,则对粗糙度的要求可以适当放宽。
公差和粗糙度的对应关系还需要考虑到成本因素。
公差的要求越高,制造成本也会相应增加,特别是对于精密零件来说;而粗糙度的要求则主要涉及到表面处理和后续加工的成本。
因此,在确定公差和粗糙度的要求时,需要综合考虑制造成本和零件的功能要求,以寻找最佳的平衡点。
总结起来,公差和粗糙度是制造工程中不可分割的两个概念,它们之间存在一定的对应关系。
合理的公差和粗糙度设置能够确保零件的尺寸精度和表面质量,从而保证零件的功能和性能。
在确定公差和粗糙度要求时,需要综合考虑制造工艺的能力、零件的功能和使用要求以及成本因素,以达到最佳的效果。
公差等级与粗糙度的关系

公差等级与粗糙度的关系表面粗糙度是反映零件表面微观几何形状误差的一个重要技术指标,是验证零件表面质量的主要依据;它选择的合理与否,直接关系到产品的质量,使用寿命和生产成本。
机械零件表面粗糙度的选择有3种方法,即计算法、试验法和类比法。
在机械零件设计中应用最普遍的是类比法,此方法简单有效。
运用类比法需要有充足的参考资料。
现有的各类机械设计手册中都提供了较全面的资料和文献。
最常用的是与公差等级相适应得表面粗糙度。
通常情况下公差越小,机械零件的表面粗糙度值也越小,但是他们之间不存在固定的函数关系。
一些装饰表面除外。
在实践工作中,对于不同类型的机器,其零件在相同尺寸公差的条件下,对表面粗糙度的要求是有差别的。
这就是配合的稳定性问题。
在机械零件的设计和制造过程中,对于不同类型机器,其零件配合稳定性和互换性的要求是不同的。
在现有的机械零件设计手册中,主要有以下三种类型。
第一类主要用于精密机械,对配合的稳定性要求很高,要求零件在使用过程中和多次装配后,其零件的磨损极限不超过公差值的10%;这主要应用在精密仪器、仪表、精密量具的表面、极其重要零件表面的摩擦面,如气缸的内表面精密机床的主轴颈、坐标镗床的主轴颈等。
第二类主要用于精密机械,对配合的稳定性要求较高,要求零件的磨损极限不超过公差值得25%,要求有很好密和的接触面,其主要应用在机床、工具、与滚动轴承配合的表面、销锥孔,还有相对运动速度较高的接触面如华东轴承的配合面、齿轮的轮齿工作面等。
第三类主要用于通用机械,要求机械零件的磨损极限不超过尺寸公差的50%,没有相对运动的零件接触面,如箱盖、套筒,要求紧贴的表面、键和键槽的工作面;相对运动速度不高的接触面,如支架孔、衬套、带轮轴孔的工作表面、减速器等。
公差等级与表面粗糙度关系对应表格:详见附件表格在机械零件设计中按尺寸公差选择表面粗糙度数值时。
应根据不同类型的机器,选择相应的表值。
仅供设计时参考!表1公差等级与表面粗糙度值(用于精密机械)表2公差等级与表面粗糙度值(用于普通精密机械)表3公差等级与表面粗糙度值(用于通用机械)。
形位公差、尺寸公差以及表面粗糙度三者之间的关系
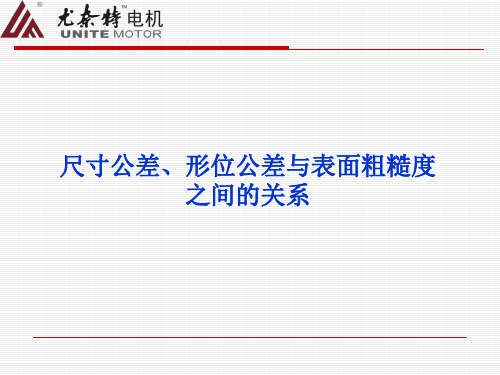
使用时,一般标注了圆柱度就没有必要再标 注圆度,直线度。如果一定要单独标注圆度、 直线度,则其公差值必须小于圆柱度公差值 (见下图),以表示设计上对径向或轴向形状 公差提出进一步要求。
3、最大实体要求及其可逆要求 在图样上,形位公差框格内的公差值或基准 字母后标注符号 M 时,分别表示被测要素 和基准要素采用最大实体要求。若在被测要 素的形位公差值后的符号 M 后标注 R 时, 则表示可逆要求用于最大实体要求。
(1)最大实体要求应用于被测要素 最大实体要求应用于被测要素时,被测要素 的形位公差值是在该要素处于最大实体状时 给定的。当被测要素的实际轮廓偏离其最大 实体状态,即局部实际尺寸偏离最大实体尺 寸时,形位误差值可超出在最大实体状态下 给出的形位公差值,其最大的超出量等于被 测要素的尺寸公差;同时,其局部实际尺寸 不得超越其最大实体和最小实体尺寸。
(3)最大实体要求应用于基准要素 最大实体要求应用于基准要素时,基准应遵守相应 的边界。即其体外作用尺寸偏离其相应的边界尺寸 时,则允许基准要素在一定范围内浮动。其浮动范 围等于基准要素的体外作用尺寸与相应的边界尺寸 之差。显然,基准要素偏离到最小实体状态时,其 浮动范围达到最大。 下图a所示为外圆轴线对外圆轴线的同轴度公差。 被测要素与基准要素同时采用最大实体要求。当被 测要素处于最大实体状态时,其轴线对基准A的同 轴度公差为Ф0.04mm,如图b所示。
从公差带图可见,当实际尺寸处处为最大实 体状态时,其形位公差为零;随着实际尺寸 偏离最大实体尺寸而减小时,则允许的形位 误差f就可以相应增大,其最大增加量等于尺 寸公差0.03mm,这表明尺寸公差可转化为 形位公差。 由此可见,包容要求是将实际尺寸和形位误 差同时控制在尺寸公差范围内的一种公差要 求。
尺寸公差、形位公差、表面粗糙度三者的关系
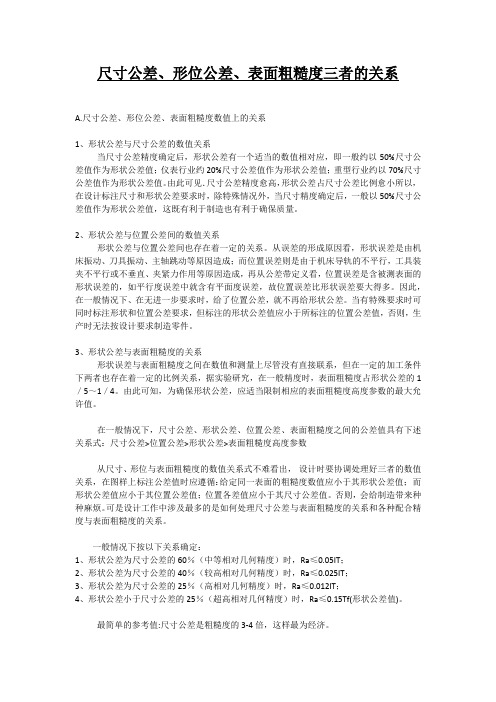
尺寸公差、形位公差、表面粗糙度三者的关系A.尺寸公差、形位公差、表面粗糙度数值上的关系1、形状公差与尺寸公差的数值关系当尺寸公差精度确定后,形状公差有一个适当的数值相对应,即一般约以50%尺寸公差值作为形状公差值;仪表行业约20%尺寸公差值作为形状公差值;重型行业约以70%尺寸公差值作为形状公差值。
由此可见.尺寸公差精度愈高,形状公差占尺寸公差比例愈小所以,在设计标注尺寸和形状公差要求时,除特殊情况外,当尺寸精度确定后,一般以50%尺寸公差值作为形状公差值,这既有利于制造也有利于确保质量。
2、形状公差与位置公差间的数值关系形状公差与位置公差间也存在着一定的关系。
从误差的形成原因看,形状误差是由机床振动、刀具振动、主轴跳动等原因造成;而位置误差则是由于机床导轨的不平行,工具装夹不平行或不垂直、夹紧力作用等原因造成,再从公差带定义看,位置误差是含被测表面的形状误差的,如平行度误差中就含有平面度误差,故位置误差比形状误差要大得多。
因此,在一般情况下、在无进一步要求时,给了位置公差,就不再给形状公差。
当有特殊要求时可同时标注形状和位置公差要求,但标注的形状公差值应小于所标注的位置公差值,否则,生产时无法按设计要求制造零件。
3、形状公差与表面粗糙度的关系形状误差与表面粗糙度之间在数值和测量上尽管没有直接联系,但在一定的加工条件下两者也存在着一定的比例关系,据实验研究,在一般精度时,表面粗糙度占形状公差的1/5~1/4。
由此可知,为确保形状公差,应适当限制相应的表面粗糙度高度参数的最大允许值。
在一般情况下,尺寸公差、形状公差、位置公差、表面粗糙度之间的公差值具有下述关系式:尺寸公差>位置公差>形状公差>表面粗糙度高度参数从尺寸、形位与表面粗糙度的数值关系式不难看出,设计时要协调处理好三者的数值关系,在图样上标注公差值时应遵循:给定同一表面的粗糙度数值应小于其形状公差值;而形状公差值应小于其位置公差值;位置各差值应小于其尺寸公差值。
尺寸公差形位公差、表面粗糙度数值上的关系
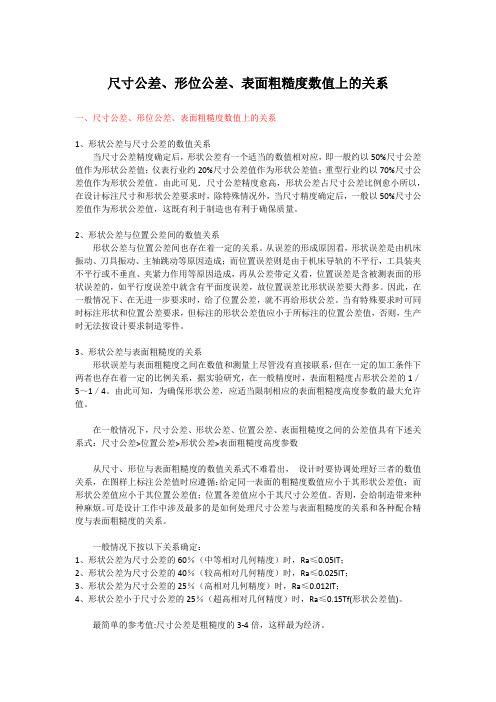
尺寸公差、形位公差、表面粗糙度数值上的关系一、尺寸公差、形位公差、表面粗糙度数值上的关系1、形状公差与尺寸公差的数值关系当尺寸公差精度确定后,形状公差有一个适当的数值相对应,即一般约以50%尺寸公差值作为形状公差值;仪表行业约20%尺寸公差值作为形状公差值;重型行业约以70%尺寸公差值作为形状公差值。
由此可见.尺寸公差精度愈高,形状公差占尺寸公差比例愈小所以,在设计标注尺寸和形状公差要求时,除特殊情况外,当尺寸精度确定后,一般以50%尺寸公差值作为形状公差值,这既有利于制造也有利于确保质量。
2、形状公差与位置公差间的数值关系形状公差与位置公差间也存在着一定的关系。
从误差的形成原因看,形状误差是由机床振动、刀具振动、主轴跳动等原因造成;而位置误差则是由于机床导轨的不平行,工具装夹不平行或不垂直、夹紧力作用等原因造成,再从公差带定义看,位置误差是含被测表面的形状误差的,如平行度误差中就含有平面度误差,故位置误差比形状误差要大得多。
因此,在一般情况下、在无进一步要求时,给了位置公差,就不再给形状公差。
当有特殊要求时可同时标注形状和位置公差要求,但标注的形状公差值应小于所标注的位置公差值,否则,生产时无法按设计要求制造零件。
3、形状公差与表面粗糙度的关系形状误差与表面粗糙度之间在数值和测量上尽管没有直接联系,但在一定的加工条件下两者也存在着一定的比例关系,据实验研究,在一般精度时,表面粗糙度占形状公差的1/5~1/4。
由此可知,为确保形状公差,应适当限制相应的表面粗糙度高度参数的最大允许值。
在一般情况下,尺寸公差、形状公差、位置公差、表面粗糙度之间的公差值具有下述关系式:尺寸公差>位置公差>形状公差>表面粗糙度高度参数从尺寸、形位与表面粗糙度的数值关系式不难看出,设计时要协调处理好三者的数值关系,在图样上标注公差值时应遵循:给定同一表面的粗糙度数值应小于其形状公差值;而形状公差值应小于其位置公差值;位置各差值应小于其尺寸公差值。
公差粗糙度形位公差关系
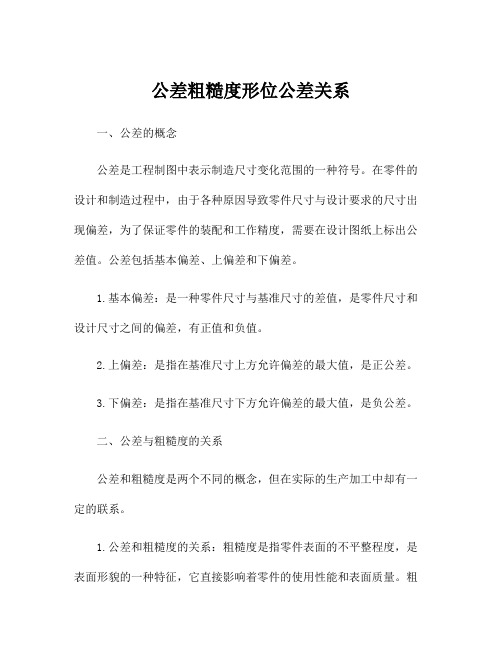
公差粗糙度形位公差关系一、公差的概念公差是工程制图中表示制造尺寸变化范围的一种符号。
在零件的设计和制造过程中,由于各种原因导致零件尺寸与设计要求的尺寸出现偏差,为了保证零件的装配和工作精度,需要在设计图纸上标出公差值。
公差包括基本偏差、上偏差和下偏差。
1.基本偏差:是一种零件尺寸与基准尺寸的差值,是零件尺寸和设计尺寸之间的偏差,有正值和负值。
2.上偏差:是指在基准尺寸上方允许偏差的最大值,是正公差。
3.下偏差:是指在基准尺寸下方允许偏差的最大值,是负公差。
二、公差与粗糙度的关系公差和粗糙度是两个不同的概念,但在实际的生产加工中却有一定的联系。
1.公差和粗糙度的关系:粗糙度是指零件表面的不平整程度,是表面形貌的一种特征,它直接影响着零件的使用性能和表面质量。
粗糙度通常以Ra值来表示,公差是用于标示零件尺寸偏差的一种符号。
在零件制造过程中,为了达到设计要求的尺寸精度,通常会对零件的粗糙度进行控制,以确保零件的尺寸精度和表面质量。
2.控制粗糙度的方法:在设计制图中可以通过公差的设置来控制零件的粗糙度,例如可以通过公差的设计来控制零件的尺寸偏差,从而影响零件的表面粗糙度。
另外,还可以通过选择合适的加工工艺和加工方法来控制零件的粗糙度,例如采用精密加工设备和刀具,采用精密切削工艺等。
三、公差与形位公差的关系形位公差是用来表示零件几何形状和位置的误差值的一种符号。
形位公差包括圆度公差、圆度公差、直平度公差、倾斜度公差等。
形位公差是一种对零件几何形状和位置误差的要求,它与公差有一定的联系。
1.公差与形位公差的关系:形位公差和公差是两个不同的概念,但在实际的生产加工中有一定的联系。
形位公差用于描述零件几何形状和位置的误差范围,而公差用于描述零件尺寸的变化范围。
在零件的设计和制造过程中,需要同时考虑形位公差和公差的影响,在设计图纸上标明形位公差和公差值,以确保零件的几何形状和位置精度。
2.影响形位公差的因素:公差的设置会影响形位公差的实际控制效果。
最新公差等级与粗糙度的关系
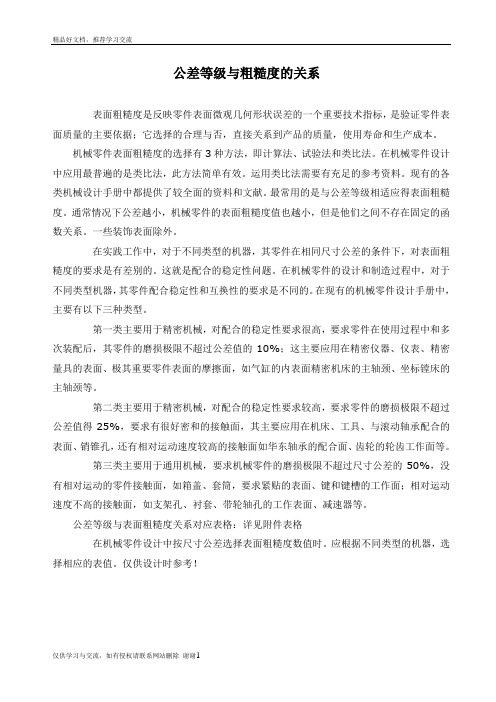
公差等级与粗糙度的关系表面粗糙度是反映零件表面微观几何形状误差的一个重要技术指标,是验证零件表面质量的主要依据;它选择的合理与否,直接关系到产品的质量,使用寿命和生产成本。
机械零件表面粗糙度的选择有3种方法,即计算法、试验法和类比法。
在机械零件设计中应用最普遍的是类比法,此方法简单有效。
运用类比法需要有充足的参考资料。
现有的各类机械设计手册中都提供了较全面的资料和文献。
最常用的是与公差等级相适应得表面粗糙度。
通常情况下公差越小,机械零件的表面粗糙度值也越小,但是他们之间不存在固定的函数关系。
一些装饰表面除外。
在实践工作中,对于不同类型的机器,其零件在相同尺寸公差的条件下,对表面粗糙度的要求是有差别的。
这就是配合的稳定性问题。
在机械零件的设计和制造过程中,对于不同类型机器,其零件配合稳定性和互换性的要求是不同的。
在现有的机械零件设计手册中,主要有以下三种类型。
第一类主要用于精密机械,对配合的稳定性要求很高,要求零件在使用过程中和多次装配后,其零件的磨损极限不超过公差值的10%;这主要应用在精密仪器、仪表、精密量具的表面、极其重要零件表面的摩擦面,如气缸的内表面精密机床的主轴颈、坐标镗床的主轴颈等。
第二类主要用于精密机械,对配合的稳定性要求较高,要求零件的磨损极限不超过公差值得25%,要求有很好密和的接触面,其主要应用在机床、工具、与滚动轴承配合的表面、销锥孔,还有相对运动速度较高的接触面如华东轴承的配合面、齿轮的轮齿工作面等。
第三类主要用于通用机械,要求机械零件的磨损极限不超过尺寸公差的50%,没有相对运动的零件接触面,如箱盖、套筒,要求紧贴的表面、键和键槽的工作面;相对运动速度不高的接触面,如支架孔、衬套、带轮轴孔的工作表面、减速器等。
公差等级与表面粗糙度关系对应表格:详见附件表格在机械零件设计中按尺寸公差选择表面粗糙度数值时。
应根据不同类型的机器,选择相应的表值。
仅供设计时参考!仅供学习与交流,如有侵权请联系网站删除谢谢1表1公差等级与表面粗糙度值(用于精密机械)仅供学习与交流,如有侵权请联系网站删除谢谢2表2公差等级与表面粗糙度值(用于普通精密机械)表3公差等级与表面粗糙度值(用于通用机械)管仲列传管仲夷吾者,颍上人也。
表面粗糙度与尺寸公差、形状公差的综合关系
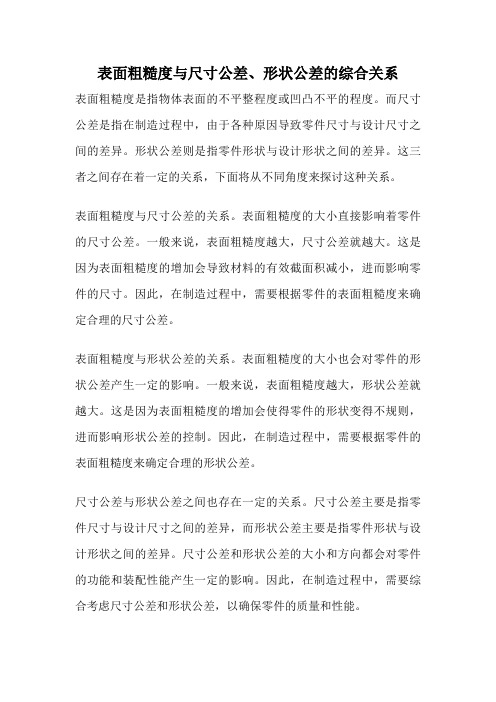
表面粗糙度与尺寸公差、形状公差的综合关系表面粗糙度是指物体表面的不平整程度或凹凸不平的程度。
而尺寸公差是指在制造过程中,由于各种原因导致零件尺寸与设计尺寸之间的差异。
形状公差则是指零件形状与设计形状之间的差异。
这三者之间存在着一定的关系,下面将从不同角度来探讨这种关系。
表面粗糙度与尺寸公差的关系。
表面粗糙度的大小直接影响着零件的尺寸公差。
一般来说,表面粗糙度越大,尺寸公差就越大。
这是因为表面粗糙度的增加会导致材料的有效截面积减小,进而影响零件的尺寸。
因此,在制造过程中,需要根据零件的表面粗糙度来确定合理的尺寸公差。
表面粗糙度与形状公差的关系。
表面粗糙度的大小也会对零件的形状公差产生一定的影响。
一般来说,表面粗糙度越大,形状公差就越大。
这是因为表面粗糙度的增加会使得零件的形状变得不规则,进而影响形状公差的控制。
因此,在制造过程中,需要根据零件的表面粗糙度来确定合理的形状公差。
尺寸公差与形状公差之间也存在一定的关系。
尺寸公差主要是指零件尺寸与设计尺寸之间的差异,而形状公差主要是指零件形状与设计形状之间的差异。
尺寸公差和形状公差的大小和方向都会对零件的功能和装配性能产生一定的影响。
因此,在制造过程中,需要综合考虑尺寸公差和形状公差,以确保零件的质量和性能。
表面粗糙度、尺寸公差和形状公差之间存在着一定的关系。
在制造过程中,需要根据零件的要求和使用环境来确定合理的表面粗糙度、尺寸公差和形状公差。
只有在合理范围内控制好这三者之间的关系,才能制造出符合要求的优质零件。
因此,对于制造企业和工程师来说,深入研究和理解表面粗糙度、尺寸公差和形状公差之间的综合关系,是提高产品质量和市场竞争力的重要途径之一。
尺寸公差配合与表面粗糙度分析

F7 G 7 H 7 JS 7 K 7 M 7 N 7 P 7 R 7 S 7 6 h 6 h 6 h 6 h 6 h 7 h 7 h 6
E8 F 8
H8 JS 8 K 8 M 8 N 8
h7
h7 h 7
h7 h 7 h 7 h 7 h 7
E8 F8
例1
查表写出φ18
H f
78的极限偏差数值。
解:
从配合表可知,Hf
8 7
是基孔制的优先配合,其中H8是基
准孔的公差代号;f7是配合轴的公差代号。
(1)φ18H8基准孔的极限偏差,可由附录附表中查出。在
表中由基本尺寸从大于14至18的行和公差带H8的列相交处
查得 +0.027 0
这就是基准孔的上、下偏差,所以 φ18H8
H 6 H 7 H 7 H7 H7 H7 H7 H7 H7 H7 H7 H7 H7 H7 H7 H7
f 6 g 6 h 6 Js6 k6 m6 n6 p6 r6 s6 t6 u6 v6 x6 y6 z6 H 8 H 8 H 8 H 8 H8 H8 H8 H8 H8 H8 H8 H8 H8
e 7 f 7 g 7 h 8 Js7 k7 m7 n7 p7 r7 s7 t7 u7
• 实际偏差:实际尺寸减基本尺寸的代数差。 • 极限偏差:极限尺寸减去基本尺寸。极限偏差又分上偏差
(ES、es)和下偏差(EI、ei)。 ES=Dmax-D es=dmax-d EI=Dmin-D ei=dmin-d • 公差:允许尺寸的变动量。等于最大极限尺寸与最小极限 尺寸之代数差的绝对值。孔、轴的公差分别用Th和Ts表示。 Th=︱ Dmax- Dmin ︱= ︱ ES-EI︱ Ts=︱ dmax- dmin ︱= ︱ es-ei︱
形位公差、尺寸公差以及表面粗糙度

不同位置表面代号的注 法。符号的尖端必须从材料 外指向表面。
⑶ 表面粗糙度符号的意义
符号 意 义 及 说 明
基本符号,表示可用任何方法获得的表面, (单独使用无意义)仅适用于简化代号标 注。
表示用去除材料的方法获得的表面。 例如:车、铣、钻、磨、剪切、抛光、腐 蚀、电火花加工等
表示用不去除材料的方法获得的表面。 例如:铸、缎、冲压、热轧、冷轧、粉末热 金等方法。或用于保持原供应状况的表面。
3、形状公差与表面粗糙度的关系 形状误差与表面粗糙度之间在数值和测量上尽管没有直 接联系,但在一定的加工条件下两者也存在着一定的比例 关系,据实验研究,在一般精度时,表面粗糙度占形状公 差的1/5~1/4。由此可知,为确保形状公差,应适当限 制相应的表面粗糙度高度参数的最大允许值。 在一般情况下,尺寸公差、形状公差、位置公差、表面粗 糙度之间的公差值具有下述关系式:尺寸公差>位置公差> 形状公差>表面粗糙度高度参数
2、形状公差与位置公差间的数值关系 形状公差与位置公差间也存在着一定的关系。从误差的形 成原因看,形状误差是由机床振动、刀具振动、主轴跳动等 原因造成;而位置误差则是由于机床导轨的不平行,工具装 夹不平行或不垂直、夹紧力作用等原因造成,再从公差带定 义看,位置误差是含被测表面的形状误差的,如平行度误差 中就含有平面度误差,故位置误差比形状误差要大得多。因 此,在一般情况下、在无进一步要求时,给了位置公差,就 不再给形状公差。当有特殊要求时可同时标注形状和位置公 差要求,但标注的形状公差值应小于所标注的位置公差值, 否则,生产时无法按设计要求制造零件。
3.2
3.2
基准符号画法
基准代号由基准符号、圆圈、连 线和字母组线。 基准符号用粗实线,长度2h。 基准代号的圆圈用细实线绘制, 直径2h 连线用细视线,长度h
尺寸公差与表面粗糙度

05 总结与展望
总结
尺寸公差与表面粗糙度是机械加工中的重要参数,它 们对产品的性能和可靠性有着显著的影响。
随着科技的不断发展,对尺寸公差与表面粗糙度的要 求也越来越高,这需要我们不断探索新的加工方法和
测量技术,以提高产品的质量和性能。
在实际应用中,应综合考虑尺寸公差与表面粗糙度的 关系,以及它们对产品性能的影响,以制定合理的加
工和测量方案。
展望
随着数字化和智能化技术的不断发展,未来的机械加工将更加依赖于先进的测量技术和数据分析方法。
新的加工方法和材料将对尺寸公差与表面粗糙度提出更高的要求,需要我们不断探索和创新,以适应新 的市场需求。
在未来,尺寸公差与表面粗糙度的研究将更加注重跨学科的合作和交流,以推动相关领域的发展和进步。
测量精度
测量精度对结果的影响很大,因此需要选择精度 合适的测量工具和正确的测量方法,以获得准确 的测量结果。
03 尺寸公差与表面粗糙度的 控制方法
加工工艺控制
加工方法选择
根据零件材料、结构、精度要求等选择合适的加工方 法,如车削、铣削、磨削等。
加工余量分配
合理分配各工序的加工余量,确保最终加工尺寸的精 度。
02
表面粗糙度越高,摩擦系数越大,磨损速度越快,从而影响零
件的耐磨性。
表面粗糙度对零件疲劳强度的影响
03
表面粗糙度越高,应力集中越严重,疲劳裂纹容易形成和扩展,
降低零件的疲劳强度。
尺寸公差对表面粗糙度的影响
尺寸公差越小,表面粗糙度越低
在加工过程中,尺寸公差越小,切削深度、进给量等工艺参数越小,从而减小 表面粗糙度。
热处理工艺
控制零件的热处理工艺,以减小变形和组织不均匀性 对尺寸精度的影响。
尺寸公差,形状公差与表面粗糙度的关系
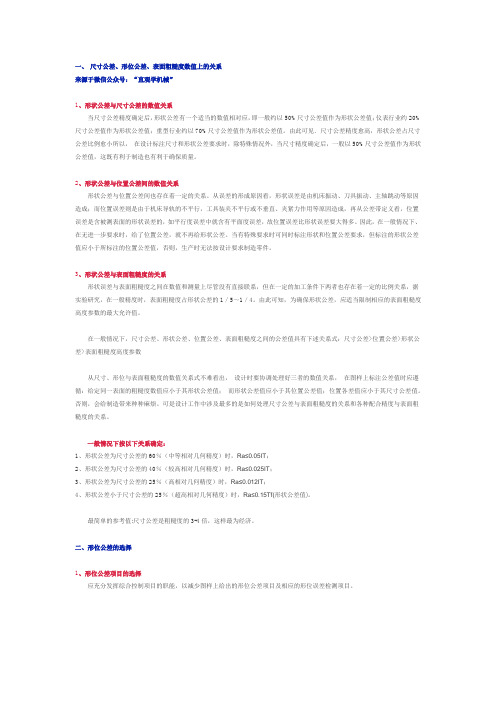
一、尺寸公差、形位公差、表面粗糙度数值上的关系来源于微信公众号:“直观学机械”1、形状公差与尺寸公差的数值关系当尺寸公差精度确定后,形状公差有一个适当的数值相对应,即一般约以50%尺寸公差值作为形状公差值;仪表行业约20%尺寸公差值作为形状公差值;重型行业约以70%尺寸公差值作为形状公差值。
由此可见.尺寸公差精度愈高,形状公差占尺寸公差比例愈小所以,在设计标注尺寸和形状公差要求时,除特殊情况外,当尺寸精度确定后,一般以50%尺寸公差值作为形状公差值,这既有利于制造也有利于确保质量。
2、形状公差与位置公差间的数值关系形状公差与位置公差间也存在着一定的关系。
从误差的形成原因看,形状误差是由机床振动、刀具振动、主轴跳动等原因造成;而位置误差则是由于机床导轨的不平行,工具装夹不平行或不垂直、夹紧力作用等原因造成,再从公差带定义看,位置误差是含被测表面的形状误差的,如平行度误差中就含有平面度误差,故位置误差比形状误差要大得多。
因此,在一般情况下、在无进一步要求时,给了位置公差,就不再给形状公差。
当有特殊要求时可同时标注形状和位置公差要求,但标注的形状公差值应小于所标注的位置公差值,否则,生产时无法按设计要求制造零件。
3、形状公差与表面粗糙度的关系形状误差与表面粗糙度之间在数值和测量上尽管没有直接联系,但在一定的加工条件下两者也存在着一定的比例关系,据实验研究,在一般精度时,表面粗糙度占形状公差的1/5~1/4。
由此可知,为确保形状公差,应适当限制相应的表面粗糙度高度参数的最大允许值。
在一般情况下,尺寸公差、形状公差、位置公差、表面粗糙度之间的公差值具有下述关系式:尺寸公差>位置公差>形状公差>表面粗糙度高度参数从尺寸、形位与表面粗糙度的数值关系式不难看出,设计时要协调处理好三者的数值关系,在图样上标注公差值时应遵循:给定同一表面的粗糙度数值应小于其形状公差值;而形状公差值应小于其位置公差值;位置各差值应小于其尺寸公差值。
表面粗燥度与公差等级对照表

>6.3~10
>3.2~6.3
>1.6~3.2 >0.8~1.6 >0.4~0.8 >0.2~0.4 >0.1~0.2
毛坯经粗加工后的表面(粗车、切断、粗刨、钻及镗) 焊接前的焊缝表面 支架、箱体、粗糙的手柄、离合器等不与其它零件接触的表面;轴的端面、倒角、不重 要的安装支承表面,穿螺钉、铆钉的孔的表面等 不重要零件的非配合表面;如支柱、轴、支架、外壳、衬套、端盖等的端面。紧固件的 自由表面,螺栓、螺钉、双头螺拄和螺母的表面。不要求定心及配合特性的表面:螺栓孔、 螺钉孔和铆钉孔等表面,飞轮、皮带轮、联轴节、凸轮、偏心轴的侧面,平键及键槽上下面, 楔键侧面,花键非定心表面,齿顶圆表面。不重要的联结配合表面 按 IT10~IT11 制造的零件配合表面。和其它零件连接而形成配合的表面;外壳、座架、 端盖、凸耳端面、扳手和手轮的外圆。要求有定心及配合特性的固定支承面;定心的轴肩, 键及键槽的工作表面。不重要的紧固螺纹的表面。非传动用的梯形螺纹、锯齿形螺纹表面。 齿轮的非工作表面,燕尾槽的表面,低速下工作的滑动轴承和轴的摩擦表面。张紧链轮、导 向滚动轮孔与轴的配合表面、对工作精度及可靠性有影响的连杆机构的铰接表面。低速工作 下的支承轴肩、止推滑动轴承及中间垫片的工作表面,滑块及导向面(速度 20~50 米/分) 按 IT8~IT9 制造的零件配合表面。要求粗略定心的配合表面及固定支承面;衬套、轴承 和定位销的压入孔。不要求定心配合特性的活动支承面;活动关节、花键结合,8级齿轮的 齿面,传动螺纹工作面,低速传动的轴颈、楔形键及槽沟的上下面,轴承座凸肩表面(对中 心用)、端盖内侧面。滑块及导向面,三角皮带轮槽表面,电镀前的金属表面。轴与毡圈摩擦 面 按 IT6~IT8 级制造的零件配合表面。销孔与圆柱销的表面。齿轮、涡轮、套筒的配合表 面;与 0 级(G 级)精度滚动轴承配合的孔,中速转动的轴颈,过盈配合的 7 级孔(H7),间 隙配合的 3~9 级孔(H8~H9)。花键轴上的定心表面,不要求保证定心及配合特性的活动支 承面。安装直径在 180mm 以下的滚动轴承机体孔(按 IT7 级镗出的)和滚动轴承紧靠在一起 的零件端面 按 IT6 级制造的轴与 IT7 级的孔配合,且要求长久保持配合性质稳定的零件配合表面; 在有色金属零件上镗制安装滚动轴承的 IT6 级的内孔表面;与 G、B 级精度滚动轴承相配合的 轴颈面,偏心轴、精密螺杆、齿轮轴的表面;背蜗齿轮的配合表面。曲轴及凸轮轴的工作轴 颈;传动螺杆(丝杠)的工作表面、活塞销孔。7 级精度齿轮工作表面,7~8 级蜗杆齿面, 与橡胶油封配合的轴颈 按 IT5~IT6 级制造的零件配合表面;如小直径精确心轴及转轴的配合表面。顶尖的圆锥 面,与 E、D、C 级精密滚动轴承相配合的轴颈表面,高精度齿轮(3、4、5 级)的工作表面; 发动机曲轴及凸轮轴的工作表面;液压油缸和柱塞的表面,喷雾器、活塞泵缸套内表面,齿 轮泵轴颈。工作时承受反复应力的重要零件表面 在摩擦条件下工作且其稳定性直接决定着机构的工作精度表面;高精度较重要的轴;圆 柱形及菱形重要的导轮表面;阀的工作表面;精密滚动轴承的座圈滚道;气缸内表面;活塞 销的外表面 特别精密的滚珠轴承套筒滚道,滚动轴承滚珠及滚柱表面;摩擦离合器的摩擦表面;精 密机床的轴颈;极限量规的测量面 特别精密或特别高速滚动轴承的滚珠、滚柱表面;测量仪器;中等精密度间隙配合零件 的工作表面;柴油发动机的高压油泵中柱塞套的配合表面
零件表面粗糙度与尺寸公差
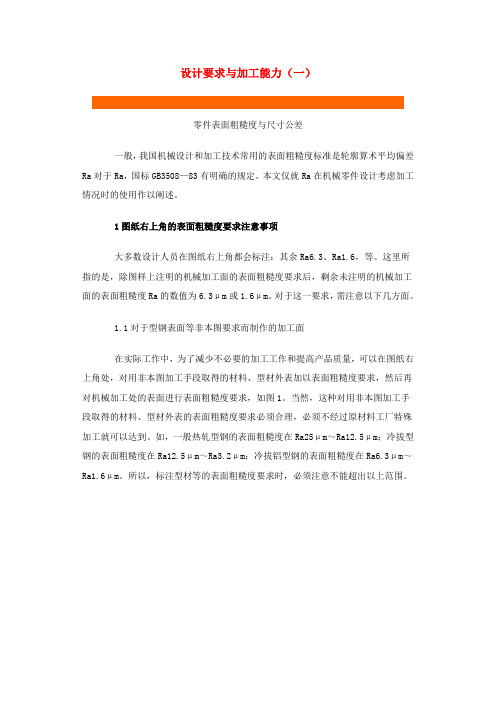
设计要求与加工能力(一)零件表面粗糙度与尺寸公差一般,我国机械设计和加工技术常用的表面粗糙度标准是轮廓算术平均偏差Ra对于Ra,国标GB3508—83有明确的规定。
本文仅就Ra在机械零件设计考虑加工情况时的使用作以阐述。
1图纸右上角的表面粗糙度要求注意事项大多数设计人员在图纸右上角都会标注:其余Ra6.3、Ra1.6,等。
这里所指的是,除图样上注明的机械加工面的表面粗糙度要求后,剩余未注明的机械加工面的表面粗糙度Ra的数值为6.3μm或1.6μm。
对于这一要求,需注意以下几方面。
1.1对于型钢表面等非本图要求而制作的加工面在实际工作中,为了减少不必要的加工工作和提高产品质量,可以在图纸右上角处,对用非本图加工手段取得的材料、型材外表加以表面粗糙度要求,然后再对机械加工处的表面进行表面粗糙度要求,如图1。
当然,这种对用非本图加工手段取得的材料、型材外表的表面粗糙度要求必须合理,必须不经过原材料工厂特殊加工就可以达到。
如,一般热轧型钢的表面粗糙度在Ra25μm~Ra12.5μm;冷拔型钢的表面粗糙度在Ra12.5μm~Ra3.2μm;冷拔铝型钢的表面粗糙度在Ra6.3μm~Ra1.6μm。
所以,标注型材等的表面粗糙度要求时,必须注意不能超出以上范围。
1.2对于用铸造、锻造、焊接等本图要求而制作的毛坯件在使用铸造、锻造、焊接制作毛坯时,尤其是型腔件,对它们的机械加工往往是一部分,而不是全部加工。
此时,设计人员一般在图纸右上角处标上:其余Ra6.3。
这里的Ra6.3μm仅仅是指对型腔件要求进行机械加工部分,除去图纸上已经有表面粗糙度要求的_部分外表面加以表面粗糙度要求而已,并没有对非机械加工部分(如铸造、锻造)的外表加以表面粗糙度要求。
所以,为了不产生混淆,有必要对工件全面要求,就是在对机械加工处的表面进行表面粗糙度要求之前,对用铸造、锻造、焊接等本图要求而制作的毛坯件的外表进行表面粗糙度要求,如图2。
4-公差配合与表面粗糙度
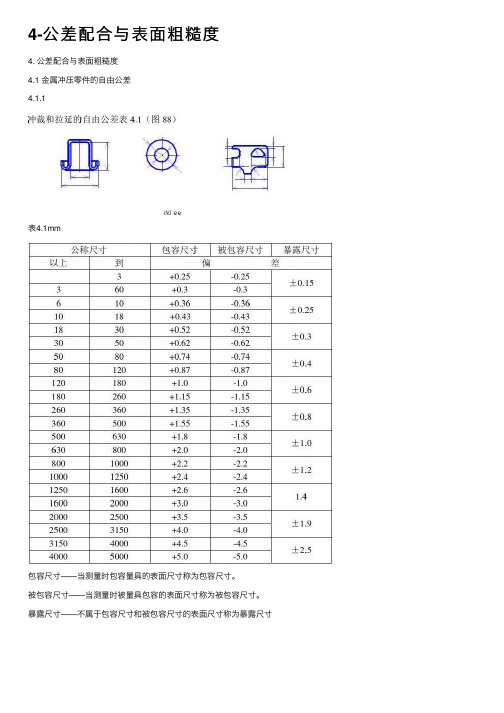
4-公差配合与表⾯粗糙度4. 公差配合与表⾯粗糙度4.1 ⾦属冲压零件的⾃由公差4.1.1表4.1mm包容尺⼨——当测量时包容量具的表⾯尺⼨称为包容尺⼨。
被包容尺⼨——当测量时被量具包容的表⾯尺⼨称为被包容尺⼨。
暴露尺⼨——不属于包容尺⼨和被包容尺⼨的表⾯尺⼨称为暴露尺⼨4.3(图90)表4.3mm4.1.44.1.5 属于与同⼀零件联接的孔中⼼距、孔与边缘距离以及也组之间的⾃由公差和位置表4.5 mm4.1.6 翘曲⾯的⾃由公差表4.6(图93)表4.6 mm注:1)零件按正常⼯艺加⼯,若由于弹性翘曲所引起的偏差超过上表之值,但仍能保证装配零件⽅便时,仍是允许的。
2)4.2 公差配合在图⾯中的注法 4.2.1 尺⼨公差在零件图中的注法 1)标注公差带代号(图94)2)标注极限偏差(图95)基本尺⼨注在同⼀线上;的字体⼩⼀号;⼩数点必须对齐,数字“0点前的个位数对齐(图a )。
当上、下偏差值相同时,号,同(图b )。
3)公差带代号与极限偏差⼀起标注(图96)号。
4.2.2 1)标注极限偏差(图97)2)模具总图常⽤配合关系⽤直接注明配合关系的⽂字注法(1)两导向⾯间的尺⼨后⾯加注“滑配”两字表达装配关系。
(2)镶块和窝座的装配关系在配合⾯尺⼨的后⾯加注“配⼊”两字。
(3)反侧块配合⾯注出“⽆间隙滑配。
” 4.3 基孔制常⽤的配合基准表4.7表4.7模具结构常⽤配合标准表4.8表4.84.4 基孔制⼆级精度公差表4.9表4.9 µm4.5 ⼏种冲模零件的制造公差4.5.1 规则形状(圆形、⽅形)凸模和凹模的制造公差表4.9表4.9mm4.5.2曲线形状的凸模或凹模的单⾯制造公差δ凸、δ凹表4.10表4.10mm1)本表所列公差,根据冲模类型只在凸模(冲孔时)或凹模(落料时)⼀个零件上标注,⽽另⼀件则注明配作间隙。
2)公差的⽅向(“+”或“-”)和位置,根据冲压件的公差⽅向和⼤⼩⽽定。
4.5.3固定板⽅孔、槽及底板窝座的公差表4.11表4.11mm注:图纸上只标注尺⼨偏差;形位公差在图中不标,它属于通⽤技术条件,在加⼯中必须保证其要求。
公差原则和表面粗糙度

模厂技术部标准化组
标准化基础培训系列
四、表面粗糙度代[符]号及其注法 4.2.2 加工方法、涂镀和其它表面处理 如该表面的粗糙度要求由指定的加工方法获得时,可用文字 标注在符号长边的横线上面,如图10
图10
加工方法的代号示例
如该表面的粗糙度要求是由镀(涂)覆或其它表面处 理方法获得,可以将要求注在符号长力的横线上面,如图 11,也可以在技术要求中说明。
图4
轮廓的算术平均中线
模厂技术部标准化组
标准化基础培训系列
三、表面粗糙度的评定标准 3.2 表面粗糙度的评定参数 国标规定:表面粗糙度的评定参数应从算术平均编差Ra、 算术平均编差Ra 算术平均编差Ra 微观不平度十点高度Rz 轮廓最大高度Ry Rz和轮廓最大高度Ry三个中选取。除了这 微观不平度十点高度Rz 轮廓最大高度Ry 三个高度参数外,国标又规定了轮廓微观不平度的平均间距Sm 轮廓微观不平度的平均间距Sm 轮廓微观不平度的平均间距 、轮廓单峰平均间距S和轮廓支承长度率tp 轮廓单峰平均间距S 轮廓支承长度率tp三个评定间距特性的 轮廓支承长度率tp 轮廓单峰平均间距 附加参数,以便根据表面的功能需要选用。 3.2.1 高度特性参数 由于算术平均偏差Ra参数能充分反映表面微观几何形状 高度方面的特性,测量方法较为简便,是比较普遍采用的评 定参数。 用轮廓仪检测,测得的Ra值越大,则表示表面越粗糙。
标准化基础培训系列
四、表面粗糙度代[符]号及其注法 4.2.1 表面粗糙度高度参数
表面粗糙度高度参数注写示例及意义见表5。从表5中可知:Ra本 身符号可不标写,只写数值即可;Rz与Ry除注出数值外,还应标出Rz 或Ry符号
模厂技术部标准化组
标准化基础培训系列
四、表面粗糙度代[符]号及其注法 表5 表面粗糙度高度参数值的标注示例及其意义
公差与粗糙度对应关系

公差与粗糙度对应关系一、引言在制造和加工过程中,公差和粗糙度是两个非常重要的概念。
公差是指零件尺寸与设计要求之间的差距,而粗糙度则是指零件表面的光滑程度。
公差和粗糙度的关系密切影响着产品的质量和可靠性。
本文将探讨公差和粗糙度之间的对应关系,以及其对产品性能的影响。
二、公差与粗糙度的定义公差是指在设计和制造过程中,由于各种原因导致的尺寸偏差。
公差是为了保证产品的互换性和可制造性而设置的。
它包括了上下限公差和公差带,用于决定产品尺寸的允许范围。
粗糙度是指零件表面的不规则程度。
它反映了表面的光滑程度和加工精度。
粗糙度可以通过测量表面的纵向和横向波动来表示,常用的指标有Ra、Rz等。
三、公差与粗糙度的关系公差和粗糙度之间存在一定的对应关系。
一般来说,公差越小,要求的零件尺寸越接近设计要求,表面质量越高,粗糙度越小。
而公差越大,尺寸偏差和表面质量要求越宽松,粗糙度也相应增加。
具体来说,当公差要求高时,加工过程需要更高的精度和控制能力,以保证尺寸的精确度和表面的光滑度。
这样可以有效减小表面的粗糙度,提高产品的质量。
四、公差与粗糙度对产品性能的影响公差和粗糙度对产品的性能有着直接的影响。
首先,公差的控制能力直接关系到产品的装配性能和互换性。
如果公差过大,零部件之间的配合会出现问题,导致装配困难或者无法装配。
而精确控制公差可以保证零部件的互换性,提高产品的装配效率。
粗糙度对产品的摩擦和磨损性能有着重要的影响。
表面粗糙度较大的零件,摩擦系数较高,容易产生摩擦热和磨损,影响产品的寿命和可靠性。
而表面粗糙度较小的零件,摩擦系数较低,摩擦磨损也相应减小。
公差和粗糙度还会对产品的密封性和气密性产生影响。
公差的控制能力决定了零部件之间的间隙,而间隙的大小直接关系到产品的密封性能。
粗糙度的控制能力则影响着密封面的接触质量和密封效果。
五、公差与粗糙度的控制方法为了保证产品的质量和性能,需要对公差和粗糙度进行有效的控制。
公差的控制可以采用合理的加工工艺和设备,以及准确的测量和检验手段。
- 1、下载文档前请自行甄别文档内容的完整性,平台不提供额外的编辑、内容补充、找答案等附加服务。
- 2、"仅部分预览"的文档,不可在线预览部分如存在完整性等问题,可反馈申请退款(可完整预览的文档不适用该条件!)。
- 3、如文档侵犯您的权益,请联系客服反馈,我们会尽快为您处理(人工客服工作时间:9:00-18:30)。
公差与粗糙度对应关系
一、引言
在制造和加工过程中,公差和粗糙度是两个常用的术语。
公差是指零件尺寸允许的偏差范围,而粗糙度则描述了表面的光滑程度。
公差和粗糙度之间存在一定的对应关系,本文将探讨公差与粗糙度之间的关系。
二、公差的定义与应用
公差是指在制造和加工过程中,零件尺寸允许的偏差范围。
公差的大小决定了零件的质量,合理的公差设计可以保证零件的互换性和可靠性。
公差通常分为尺寸公差和形位公差两种。
1. 尺寸公差
尺寸公差是指零件的长度、直径、厚度等尺寸大小的偏差范围。
常见的尺寸公差包括基本尺寸、上偏差和下偏差。
上偏差表示零件的尺寸允许偏大的范围,下偏差表示零件的尺寸允许偏小的范围。
2. 形位公差
形位公差是指零件间的相对位置关系的偏差范围。
常见的形位公差包括平面度、圆度、直线度等。
形位公差的设计可以保证零件的装配精度和工作性能。
三、粗糙度的定义与测量
粗糙度是指表面的光滑程度,也称为表面质量。
粗糙度的大小对零件的摩擦、密封、润滑等性能有很大影响。
粗糙度通常使用Ra值来表示,单位为微米(μm)。
粗糙度的测量可以使用表面粗糙度仪来进行。
表面粗糙度仪通过感应表面的微小起伏,将其转化为电信号,并通过测量和分析来得出粗糙度数值。
四、公差与粗糙度的关系
公差和粗糙度虽然描述了不同的特性,但它们之间存在一定的关系。
1. 公差对粗糙度的影响
公差的大小会直接影响零件的尺寸和形状,从而影响零件表面的光滑程度。
公差较小的零件往往具有较高的表面质量,而公差较大的零件则可能具有较低的表面质量。
2. 粗糙度对公差的影响
粗糙度的大小也会对零件的公差设计产生影响。
在设计公差时,需要考虑表面粗糙度的影响,避免表面质量过差导致公差范围无法满足要求。
3. 公差和粗糙度的协调
在实际应用中,公差和粗糙度需要相互协调,以保证零件的质量和性能。
合理的公差设计可以控制零件的尺寸和形状,而适当的粗糙
度要求可以保证零件的表面质量。
五、公差与粗糙度的优化
在实际制造和加工过程中,需要根据具体情况对公差和粗糙度进行优化。
1. 公差优化
合理的公差设计可以提高零件的互换性和可靠性。
在公差设计时,需要考虑零件的功能要求、工艺条件和成本等因素,以确定合适的公差范围。
2. 粗糙度优化
粗糙度的优化可以提高零件的摩擦、密封、润滑等性能。
在粗糙度优化时,需要考虑零件的材料、表面处理和加工工艺等因素,以确定合适的粗糙度要求。
六、结论
公差和粗糙度是制造和加工过程中常用的术语,它们描述了零件尺寸和表面质量的特性。
公差和粗糙度之间存在一定的关系,合理的公差设计和粗糙度要求可以保证零件的质量和性能。
在实际应用中,需要根据具体情况对公差和粗糙度进行优化,以满足零件的功能和工艺要求。