1#高炉冷却壁
1是啥意思
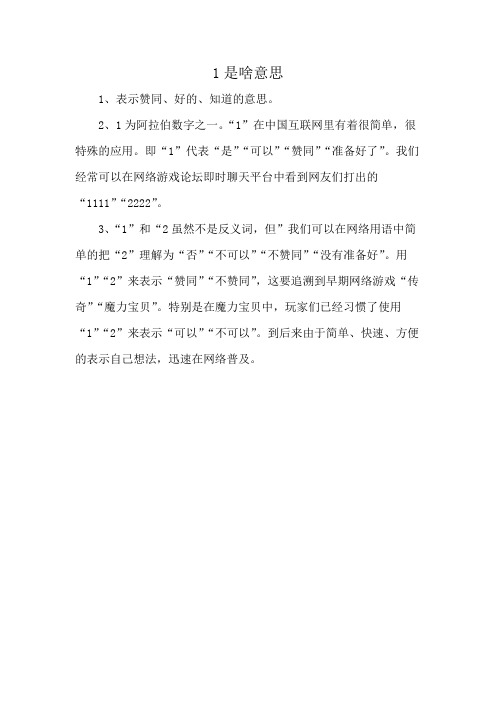
1是啥意思
1、表示赞同、好的、知道的意思。
2、1为阿拉伯数字之一。
“1”在中国互联网里有着很简单,很特殊的应用。
即“1”代表“是”“可以”“赞同”“准备好了”。
我们经常可以在网络游戏论坛即时聊天平台中看到网友们打出的“1111”“2222”。
3、“1”和“2虽然不是反义词,但”我们可以在网络用语中简单的把“2”理解为“否”“不可以”“不赞同”“没有准备好”。
用“1”“2”来表示“赞同”“不赞同”,这要追溯到早期网络游戏“传奇”“魔力宝贝”。
特别是在魔力宝贝中,玩家们已经习惯了使用“1”“2”来表示“可以”“不可以”。
到后来由于简单、快速、方便的表示自己想法,迅速在网络普及。
二年级一就造句大全

二年级一就造句大全1、太阳一出来,地上就像下了火。
2、从某种意义上说,一个人心中有什么,他看到的就是什么。
3、这家店一开,就会有很多人来。
4、蚕很可怜。
它很小,一不小心就会被人踩死,我们班的男生还把蚕捏来玩叠罗汉,结果最下面一条被压死了。
有的用铅笔去戳一个同学的蚕,蚕流了许多“血”,后来就死了,我暗暗为它们悲伤。
5、我的爸爸长着一张瘦黄的脸,头发黑黑的,双眼乌黑发亮,他一笑,雪白的牙就露了出来,别提有多帅气了。
6、一眨眼间,太阳就露出了额头和眉毛了,通红的太阳,就像一个小孩鼓足了劲,把脸弄得通红想往上跳一般,太阳露出眼睛了,突然,太阳努力往上一跃,整个笑容都露出来了,东方顿时变得金光灿灿。
7、铃声一响,同学们就马上进了教室。
8、我一打开博客,优美的音乐就响起来了。
9、歌声给我力量。
每当写博文的时候,听上一首歌,敲击着键盘就别有一番铿锵的足音。
似乎那音乐给了我莫名其妙的一股力量,让我有一种说不出的激动感。
10、我一打窗户,清新的空气就扑面而来。
11、战士们一个个冲上去,挥舞着大刀浴血奋战,一个倒下了,另一个就替上去,一个战士浑身划得稀烂,在倒下去的一刻,还高喊口号,悲壮极了!12、诚信像一面镜子,一旦打破,你的人格就会出现裂痕。
13、秋姑娘不知不觉地来到人间,她一来就不停地忙起来。
她给高粱抹红了“脸蛋”;给玉米穿上了桔红色的“裙子”;给稻谷穿上了金色的“西装”。
一阵阵秋风吹来,稻谷连忙弯下了身子,像在给秋姑娘致谢。
14、一般青年的任务,尤其是共产主义青年团及其他一切组织的任务,可以用一句话来表示,就是要学习。
15、涓涓细流一旦停止了喧哗,浩浩大海也就终止了呼吸。
16、欢乐的曙光还没有照射到峡谷里,但它已经把我们头上两边峭壁的顶端染上黄澄澄的颜色,长在岩壁深罅里的叶子稠密的灌木,只要一阵微风吹过,就把一阵银雨撒在我们身上。
17、人的一生就是体道,悟道,最后得道的过程。
18、喷泉的高度不会超过它的源头,一个人的事业也是这样,他的成就决不会超过自己的信念。
越南语1

cao(高) thấp(低)nhanh快 chậm慢mớI 新cũ旧dài 长ngắn短già老 trẻ年轻nhiều 多ít少lớn大 nhỏ小rộng宽 hẹp 窄tốt好 xấu坏đẹp (xinh)漂亮美丽đẹp trai帅 xấu丑nóng热 lạnh (rét )冷sạch干净 bẩn脏khoẻ mạnh健康 mập béo胖ốm (gầy)瘦vui (mừng, sướng)高兴开心 buồn烦闷bình tĩnh 冷静cang thẳng紧张no (饱)---- đói (饿)cưối (末)sau(后)---- trước(前)tròn (圆)---- vuông(方)hơn (多)---- kém(少)phải (右)(是)---- trái (左)(非)chấm đưt (结束)---- bấc đầu(开始)bán chạy (畅销)---- bán ế(滞销)trên (上)---- dưới (下)trong (里)---- ngoài (外)đen (黑)---- trắng(白)gần (近)---- xa (远)nghèo (穷)---- giầu (富)Bài 1第一单元1 . Xin cha o您好Chào anh哥哥你好Chào ông先生您好Chào chị姊姊妳好Chào cô小姐妳好Chào em妹妹,弟弟你好Bài 2第二單元2. Anh khỏe không ? 你好吗?Khoẻ , cám ơn好、谢谢Vân thường 还好Không khỏe lắm 不是很好3. Tạm biệt 再見Hẹn gặp lại 再会Bài 3第三單元1. ăn cơm吃飯phở , mì , bún河粉, 面, 米粉2. uống nước 喝水cà-phê , trà , nước tra i cây咖啡, 茶, 果汁Bài 4第四单元14. trăm百15. ngàn千16. mười nga n十千17. đồng 元Bài 5 第五单元1. Cái này bao nhiêu tiền ? 这个多少钱?Cái này giá 299 đồng 這個價錢299元2. đắt qua很贵喔rẻquá好便宜喔Cũng tạm 还好Bài 6 第六单元3. Bớt ặôt chu t được không ? 降價一点可以吗?Không được đâu不行啊/ 不可以啊Bớt anh 10 đồng 降價10 元Tính rẻanh 10 đồng 便宜你10元Bài 7 第七单元1. Cám ơn谢谢Không co chi不用谢Đừng kha ch sa o不客气2. Xin lỗi 对不起Không sao đâu沒关系Không sao 沒事Bài8 : 表達需求*muốn : 想要1. Tôi muốn ăn mì我想吃面2. Tôi muốn uống nước 我想喝水3. Tôi muốn đi nha vệ sinh 我想上厕所Bài 9第9单元3. Làm ơn cho tôi một tô phở麻烦給我一碗河粉4. Làm ơn cho tôi mượn cây du /cái ô麻煩給我借(借我)雨傘5. Làm ơn cho tôi hỏi , nhà vệ sinh ởđâu ?麻烦、请问,厕所在哪里?Ở đằng kia 在那边Bài 10第10单元Anh ăn cơm chưa ?你吃饭了沒有?- ăn rồi 吃了- chưa还沒有Anh thích ăn gì? 你喜欢吃什么?Tôi thích ăn phởbò我喜欢吃牛肉河粉Bài 11人稱代名詞1. Tôi 我2. Anh / ông 你/您3. cô / chị / bà妳/姐姐/您4. em 她/他Bài 12 : 人稱代名詞*他anh ấy (ảnh)/ ông ấy (ổng)他côấy (cô)/ chịấy (chỉ) / bà ấy 她em ấy 他/她nó牠(它)/他Bài 13 : giới thiệu 介紹*là是1. anh ấy la gia o viên他是教员2. chịấy la sinh viên她是大学生3. em ấy la học sinh 她是学生Bài 14 : sở hữu 所有形態1. mẹ của tôi 我的妈妈2. vợ của tôi 我的太太3. chị của tôi 我的妹妹4. bạn của tôi 我的朋友 ......của tôi 我的....Bài 15 : Câu tính từ形容句子1. Cái này đẹp lắm !这个很漂亮2. Cái này khó quá!这个很难3. Cái này quá xấu !这个太醜4. Cái này rất dễ!这个很容易Cái này .... 这个.....Bài 16 : Tự giới thiệu 自我介紹1. Tôi đa kết hôn rồi . 我已经结婚了2. Tôi vẫn co n độc thân . 我仍单身3. Tôi đa co bạn ga i . 我已有女友.4. Tôi đa co bạn trai rồi . 我已有男友了tôi đã...我已Bài 17 : Giới thiệu 介紹1. Vợ của tôi đẹp lắm 我的太太很漂亮2. Chị của tôi kho lắm 我的姊姊很挑剔(脾气不好)3. Mẹ của tôi dễ lắm 我妈妈很忠厚(脾气很好)Bài 18 : ngày tháng日期Hôm kia 前天Hôm qua 昨天Hôm nay 今天Ngày mai明天Ngày mốt 后天Hôm qua la nga y 9 . 今天是9 号Hôm nay la nga y 10 . 今天是10号Bài 19 : Thì quá khứ过去式Hôm qua , anh (cô)đa la m gì? 昨天你(妳)(已经)做什么?Tôi đa ởnhà . 我(已经)在家 .Tôi đa kết hôn 2 năm rồi . 我已经结婚两年了 .Tôi ăn cơm rồi . 我吃饭了 .Bài 21 : Thì tiếp diễn 正在进行式Anh (cô)đang la m gì? 你(妳)正在做什么?Tôi đang ăn cơm .我正在吃饭.Tôi đang đi chợ我正去市场(指买菜)Tôi đang học tiếng Việt . 我正在学越南語 .Tôi đang...我正在.........Bài 22Thì tương lai未來式Ngày mai , anh (cô)sẽđi đâu ?明天你(妳)将去那里?Tôi sẽđi Việt nam . 我将去越南 .Tôi sẽđi Đa i bắc chơi .我将去台北玩 .Tôi sẽ kết hôn . 我将结婚.Tôi sẽ.......... 我将..........Bài 23 : Thời gian 时间Bây giờlà mấy giờ ? 現在是几点?Bây giờlà 8 giờsáng . 現在是早上8点。
1的数学符号

1的数学符号
在数学中,“1”通常可以用阿拉伯数字表示,也可以用罗马数字“Ⅰ”表示。
同时,在某些特定的数学领域或公式中,可能会用到其他的符号或表示方式,例如在概率论中可以用字母“p”表示概率等于1的情况。
因此,具体的数学符号还需要根据不同的数学领域和公式进行判断和选择。
在数学中,数字1它有多个释义,以下为其中几个常见的含义:
1. 在集合论中,1表示所有非空有限集合的个数,即第一可数序集的势。
2. 在数学逻辑中,1表示逻辑真值“真”,即所有命题的真实性。
3. 在代数中,1表示乘法单位元,任何数乘以1都等于其本身。
4. 在几何学中,1表示长度、距离等度量单位的基准值。
5. 在概率论中,1表示必然事件发生的概率,即概率为1的事件。
需要注意的是,具体的数学符号还需要根据不同的数学领域和公式进行判断和选择。
因此,对于数字1的数学符号,需要结合具体上下文来理解其含义。
数学中1和一的区别

数学中1和一的区别
一、1和一的区别
在数学中,1和一表示的含义是不同的,它们在使用上也存在差异:
1. 表示数字
1表示数字1,是一个阿拉伯数字的符号,它表示一个数值,是一种抽象的表示。
一表示字母“I”,不表示数字,它是一种特定的文字表达,可以用来表示单词“一”,如“一只猫”。
2. 表示比较
1表示比较时,它表示数量的多少,用来表示两个或多个数量中最少的数量,如“有1个猫”,表示最少有一只猫;
一表示比较时,它表示顺序,用来表示两个或多个次序中第一个次序,如“第一步”,表示最先做的一步。
3. 表示乘法
1也可以表示乘法,比如2×1=2,表示乘数2乘以1,结果是2;
一表示乘法时,它表示乘数的单位,如3×一=3,表示乘数3乘以一,即3单位,结果是3。
4. 表示概念
1表示单一,它表示一个数量,假设一个容器中只有一个物体,那么这个容器中物体的数量可用1表示;
一表示全体,它表示一个集合整体,如可以用一表示几只猫,表
示这几只猫是一个整体,是一个集合。
日语二级语法1
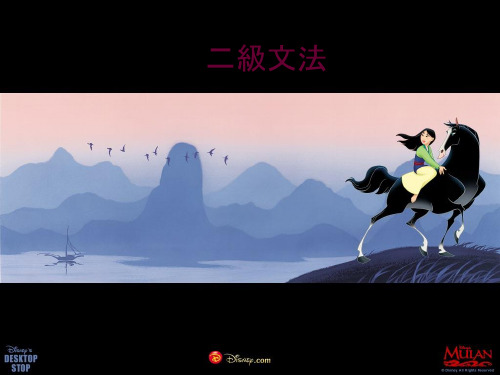
12、おかげで
意味:効果・利益、また望ましくない結果や影響にもいう。(よく 良い結果に使う。皮肉の使い方もある。) 接続:各品詞の連体形 例文: 1、川があるおかげで夏は涼しい。 2、広くなったおかげで掃除が大変だ。 3、先生のおかげで、試験に合格した。 練習: 1、由于住在海边,所以能吃到新鲜的鱼。 うちが海に近いおかげで、新鮮な魚が食べられる。 2、工作能够提前完成,多亏了田中先生的帮助。 仕事が速く済んだのは、田中さんのおかげだ。 3、由于科学技术的发展,我们的生活方便多了。 科学技術が発達したおかげで、我々の生活は便利になった。
19、
か
ないかのうちに
意味:…とほぼ同時に 接続:動詞のた形/終止形+動詞のない形 例文: 1、空が暗くなったかならないかのうちに、大雨が降り出した。 2、母親は子供が小学校へ入ったか入らないかのうちに、働きに出た。 練習: 1、嗜烟如命的他,刚吸完一支烟,又点起另一支烟。 ヘビースモーカーの彼は、タバコを一本吸い終わったか終わらないか のうちに、また次のタバコに火をつけた。 2、铃声刚刚响起,老师就走进了教室。 チヤイムが鳴るか鳴らないかのうちに、先生が教室に入ってきた。
11、得る(うる、えない)
意味:可能の意を表す。…することができる。 接続:動詞の連用形 例文: 1、…ということも十分ありうる。 2、集めうる限りの材料をみな集める。 3、できうることならば、もう少し日時がほしい。 練習: 1、只要能想到的办法都用尽了,仍然解决不了问题。 考え得るかぎりの手は尽くしたが、問題に解決には至らなかった。 2、要是早些发出警报的话,或许能够避免灾难。 あれは警報を早く出していれば、防(ふせ)ぎ得た災害かもしれな い。 3、我想在这么低矮的山上不会遇难。 こんな低い山で遭難(遭難)することはあり得ないと思う。
1_1词汇与翻译
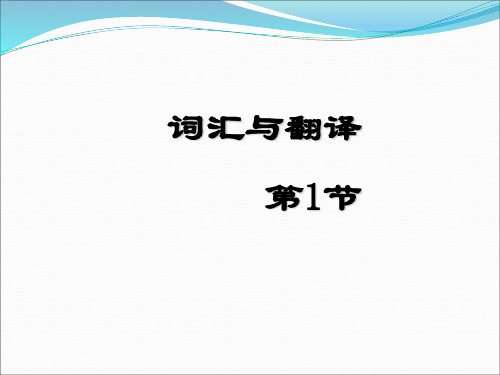
译文2:远山好像刚刚出浴,变得十分明媚。那连天的起伏 线,苍绿如黛的山垅以及大腹便便的山腰,似乎伸手就会 落上指尖,令人心旷神怡。
例9:誰でも、どうせ別れるなら美しく別 れたい。互いに恨まず、恨まれず別れたい と思う。
それは男も女も同じである。
だが、真実愛し合った愛は、往々にしてき れいごとでは済まされない。互いに傷つき、 罵り合い、痛めあって別れる。
そこにこそ、人間のはかりがたい、理屈ど おりに行かない、おろかで哀しいところが ある。
译文2:我“生”不由己,如同野草,如同路边的小石子。在 “生”不由己的宿命之中,我想竭尽全力地活下去。虽然这样 很难,但由于认清了自己的命运,所以多少有些安慰。
下面再看第二层关系的实例。
例7:「フランスの科学者が国際会議でフランス語 を使わないのは、フランス語を裏切るものであ る。」と、ドゴール大統領が自国の科学アカデミー をしかったという。わたしはフランス文化の偉大な 姿の一こまをここにみる。そして、この「フラン ス」という部分を「日本語」におきかえて、あわれ な日本語を守るための教訓にしたいと思う。……愛 国心の形を説く政治家たちは、ドゴールのようには 日本語への愛を口にしたためしがない。外国語の代 わりに日本語を生かそうとする学者も少ない。流行 作家たちの作品も、日本語の手本にすることはでき ない。
词汇与翻译 第1节
第一节 辞典与翻译的选词、选义
辞典对翻译的意义主要体现在词汇翻译层面上,而较少涉 及句法内容。一篇译文实际上是由数以千百计的译词组成, 词汇已成为翻译的最基本单位。很多情况下,离开辞典的帮 助,翻译很难顺利进行,辞典是一位真正的“幕后英雄”。 不过,另一方面,如果百分之百地听任它的指点和调遣,也 并不能保证译文就不出问题。译者和辞典之间的关系是辩证 而微妙的,翻译既离不开辞典,却又不能对它百依百顺。因 为决定文章中每个词语意义的只能是它的语境。再权威的辞 典也不可能收尽每一个词语的所有使用语境并由此给出释义。 事实上,辞典编纂本身也是动态的,需要与时俱进不断修订。 简言之,我们可以说,词义既是由辞典决定的,又不完全由 辞典决定,最终决定词义的是语境。这是译学的一条重要原 则,关系到译文的成败优劣,不可等闲视之。
1。词语的翻译

苛政猛于虎
《礼记》
孔子过泰山侧,有妇人哭于墓者而哀。 夫子式而听之,使子路问之,曰:“子 之哭也,壹似重有忧者。” 而曰:“然, 昔者吾舅死于虎,吾夫又死焉,今吾子 又死焉。” 夫子曰:“何为不去也?” 曰:“无苛政。” 夫子曰:“小子识之, 苛政猛于虎也。”
Tyranny is Fiercer than a tiger
• 昨天我打热线询问了一些关于如何购买、 安装使用ADSL的问题。 • Yesterday I asked some questions through the hot line about buying, installing and using ADSL. • 连长正在审问战俘。 • The company commander was interrogating a prisoner of war.
• • • • • • •
Stylistic meaning 别了,司徒雷登! Farewell, Leighton Stuart! 禁止赌博。 Gambling is prohibited. 她特别喜欢唱卡拉OK。 She is especially fond of singing through karaoke set. • 以上事实说明中国出口产品越来越受国外顾客的青 睐。 • The above facts lead to the conclusion that Chinese Export commodities have enjoyed growing favor among buyers abroad.
• 克明:觉新哪,你听着! Keming: Juexin, I want you to pay particular attention to this. • 在我的后园,可以看见墙外有两株树,一 株是枣树,还有一株也是枣树。 Behind the wall of my backyard you can see two trees. One is a date tree, the other is also a date tree.
视听语言1
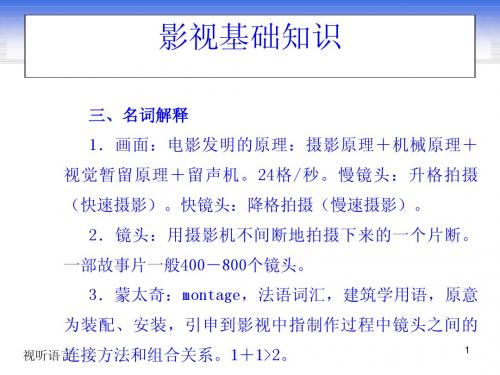
5
常规蒙太奇剪辑( 第四章 常规蒙太奇剪辑(一) 关于剪辑的基本概念
第一节 剪辑 剪辑,film editing, schnitt, montage.将拍摄的胶片 组接到一起。 最初的剪辑目的是为了将导演要述说的一个故事说 明白就成了。 当电影创作者开始意识到,把各种组接方式会带来 不同的效果,电影语言就这样产生了。 剪辑分:创新者的剪辑、匠艺师式的剪辑。
视听语言
28
无技巧转换( 的几种方式: 二、 无技巧转换(切)的几种方式:
• 两极镜头的切换 • 利用故事情节因素进行转场。 • 利用利用画面的造型因素进行转场。 • 利用动作的接续进行切换。 • 利用声音进行接续的切换。 • 利用黑场进行切换。 • 利用特写镜头进行切换。 • 表现视觉错觉的切换。
视听语言
3
影视基础知识
7.镜头的运动: 原则:平、准、稳、匀。 (1)推:摄影机顺着光学轴线向被摄体移动,景别 越来越小。 (2)拉:摄影机顺着光学轴线远离被摄体移动,景 别越来越大。 (3)摇:摄影机不动,机身作上下、左右、旋转等 运动。 (4)移(平移、横移):摄影机沿水平面作各方面 移动。 (5)跟:摄影机跟随运动的被摄体拍摄。
12
视听语言
(二)镜头的情绪长度 1、镜头的情绪长度 在剪接中,以人物的内在感情或景物所表达的情 绪因素来确定的镜头长度,叫做镜头的情绪长度。 2、要点:通常比同内容的叙述长度要长。 (1)特写、近景延长时间 (2)动作之前留出情绪反应时间 (3)动作之后留出情绪延续时间 (4)空镜头的运用
视听语言
主体静止 根据画面造型因素及内容需要选择 主体静止 编辑点 主体运动 上一运动完成后,与下一镜头组接 主体静止 需要选上一镜头的静止因素 主体静止 上一镜头从静到动以后,与下一镜 主体运动 头组接 主体运动 根据动作并结合画面造型因素选择 主体运动 剪辑点
从数字成语中看中国人的数字文化心1[2][2]
![从数字成语中看中国人的数字文化心1[2][2]](https://img.taocdn.com/s3/m/7b1fdf63783e0912a2162a38.png)
从数字成语看中国人的数字文化心理摘要成语作为现代汉语词汇中的一个大类,就像语言中的活化石,历史悠久而又具有价值,其自身蕴涵的深刻内涵为我们了解中国文化,研究中国人的心理提供了宝贵而丰富的材料。
成语中的数字成语是成语中的特殊一族。
它所折射出的中国文化不仅仅有生活、学习观念,制度方面的,还有中国特殊的数文化。
数文化与其它文化有机结合,特有的中国文化体现出特有的中国人的心理。
如“一穷二白”反映人们的生活水平;“道高一尺,魔高一丈,一尘不染,五体投地”则是佛教思想的反映;“三从四德,三妻四妾”是古代婚姻制度的反映等。
关键词成语数字成语数字文化心理语言承载着文化的信息,任何民族语言多是该民族文化的一种符号形态。
我国是世界上历史最为悠久的国家之一,汉语也是世界上古老而又发达的语言之一,它不仅有丰富的词汇和各种形式的固定短语,而且这些词汇和固定短语同样有着丰富的意义。
在上下五千年的历史长河中,涌现出大量的神话传说、寓言故事、历史事件,它们都是我国文化遗产的重要组成部分。
人们将这些神话传说、寓言故事、历史事件凝固在四字格中,同时赋予了它们特定的含义,发展为成语,大大的丰富了汉语的语言宝座。
因而成语的来源大多是历史故事,古代寓言,或者书面语言中现成的语句,其固定结构形式和组合成分,具有特定的语义内涵,这就使得一个成语比一个普通的词语具有更大的信息量。
因此,整个成语系统也比一般的词汇更能完整的表现出一个民族的文化内涵。
成语是语言中经过长期使用,锻炼而形成的固定短语,它是比词大而语法功能又相当于词的语言单位。
成语的意义通过成语整体来表示,而不是其构成成分的简单相加,使得成语意义定型,具有定型化的特点。
如“怒发冲冠”不是说一生气头发都能把帽子顶起来,而是形容异常愤怒。
成语的结构也是定型的,包括结构成分的定型和结构关系的定型。
成语成分不能随意改动,如“说三道四”不能换成“说五道六”,“说一不二”不能变成“说七不八”等等,这是因为成语结构的成分都是经过历史的进化慢慢定型的,一经定型就不能随意改变。
临淄历代进士名录1

临淄进士榜一、隋、唐、宋、元时期进士16人:房玄龄:今临淄人。
隋开皇十八年(596年)进士、状元。
李伯鱼:今临淄人。
唐开元六年(718年)进士、状元。
安雅:今临淄人。
唐天宝二年(743年)以前进士。
崔蠡:今临淄皇城镇人。
唐元和五年(810年)进士。
崔黯:今临淄皇城镇人。
唐大和二年(828年)进士。
晏墉:今临淄人。
唐咸通二年(861年)进士。
晏殊之始祖。
司空图:今临淄人。
唐咸通十年(869年)进士。
张道古:今临淄人。
唐景福年间(892年、893年)进士。
李成:今临淄人。
北宋开宝年间(968——975年)进士。
麻景孙:今临淄皇城镇麻家卸村人。
北宋太平兴国(976—983年)进士。
麻温其:今临淄皇城镇麻家卸村人。
北宋大中祥符(1008—1016年)进士。
麻温舒:今临淄皇城镇麻家卸村人。
北宋真宗大中祥符二年(1009)进士,探花。
赵师民:今临淄人。
北宋天圣八年(1030年)进士。
王辟之:今临淄人。
北宋治平四年(1067年)进士。
贾同:今临淄人。
北宋真宗时(998—1022年)进士。
王胡书:今临淄齐都镇人。
元代进士。
二、明朝时期进士7人:1、文进士6人:丁恒:今临淄人。
明洪武二十一年(1388)进士,三甲第8名。
李质:今临淄人。
明洪武三十年丁丑科(1397)夏榜进士,二甲第3名。
王嘉言:今临淄齐都镇人。
明嘉靖三十五年丙辰科(1556年)进士,三甲117名。
韩介:今临淄齐都镇西门村人(原籍南高阳村)。
明万历八年(1580年)进士,三甲182名。
唐焕:今临淄金山镇南仇村人。
明万历四十四年(1616年)进士,二甲24名。
薛近洙:今临淄金岭镇人。
明万历四十四年丙辰科(1616年)进士,三甲270名。
2、武进士1人徐八(字雨川):今临淄敬仲镇徐家圈村人,明朝武进士。
三、清朝时期进士33人1、文进士24人谢宾王:今临淄齐都镇西门村人。
清顺治三年(1646年)进士,三甲223名。
扈标:今临淄敬仲镇扈王村人。
清顺治三年(1646年)进士,三甲230名。
以1、3、bc1开头的比特币地址都有啥区别?转账手续费那种便宜,隔离见证地址为什么手续费便宜?

以1、3、bc1开头的⽐特币地址都有啥区别?转账⼿续费那种便宜,隔离见证地址为什么⼿续费便宜?以 1、3、bc1 开头的⽐特币地址都有啥区别?转账⼿续费那种便宜,隔离见证地址为什么⼿续费便宜?⽐特币地址是由26~34位字母和数字组成的字符串。
⽐特币的地址的前缀(开头的字符)我们常见的⽐特币地址前缀有: 1、3、bc1。
它们有什么区别?哪⼀个的转账⼿续费更便宜呢?要说清楚这些,我们得结合⽐特币地址的分类。
⽐特币地址的分类如下:1、传统地址1开头的地址,被称为传统地址 ( Legacy Address )。
这就是最原始的⽐特币地址,⽐如:创世地址:1A1zP1eP5QGefi2DMPTfTL5SLmv7DivfNa,属于中本聪。
该地址内初始50个BTC,后来,⽐特币爱好者不断往该地址转⼊BTC,以表达对中本聪的敬意,写⽂章这⼀刻,BTC 余额:68.13424603个。
1 开头的地址,采⽤ P2PKH ,P2PKH(Pay-to-Pubkey Hash),⽀付公钥哈希,即⽐特币交易输⼊输出脚本,采⽤公钥及公钥哈希。
1开头的传统地址,上线⾄今,⼀直被⽀持,我们可以从它发送 BTC 到下⾯介绍的多签地址和隔离见证地址。
2、多签地址3开头的地址,⽐如 3EktnHQD7RiAE6uzMj2ZifT9YgRrkSgzQX。
2012年的⽐特币改进提案中,新增 P2SH 的地址。
P2SH (Pay-to-Script-Hash),⽀付脚本哈希,即⽐特币交易输⼊输出脚本,采⽤赎回脚本及赎回脚本哈希。
其地址结构类似于 P2PKH,但它⽀持⽐传统地址更复杂的功能。
P2SH 脚本函数最常⽤于 multisig 地址,这些地址可以指定多重数字签名来授权事务。
举个例⼦:某个3开头的地址由三⼈控制,其中,任意两⼈同意,便可发起转账。
隔离见证地址隔离见证是⼀种区块链扩容的⽅法,已在⽐特币和莱特币上成功实施。
我们常见的部分 3 开头的地址,和 bc1 开头的⽐特币地址,就是隔离见证地址。
一,就什么造句
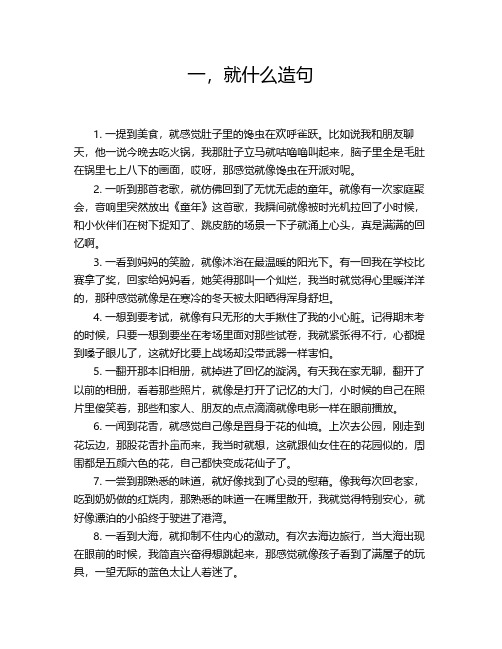
一,就什么造句1. 一提到美食,就感觉肚子里的馋虫在欢呼雀跃。
比如说我和朋友聊天,他一说今晚去吃火锅,我那肚子立马就咕噜噜叫起来,脑子里全是毛肚在锅里七上八下的画面,哎呀,那感觉就像馋虫在开派对呢。
2. 一听到那首老歌,就仿佛回到了无忧无虑的童年。
就像有一次家庭聚会,音响里突然放出《童年》这首歌,我瞬间就像被时光机拉回了小时候,和小伙伴们在树下捉知了、跳皮筋的场景一下子就涌上心头,真是满满的回忆啊。
3. 一看到妈妈的笑脸,就像沐浴在最温暖的阳光下。
有一回我在学校比赛拿了奖,回家给妈妈看,她笑得那叫一个灿烂,我当时就觉得心里暖洋洋的,那种感觉就像是在寒冷的冬天被太阳晒得浑身舒坦。
4. 一想到要考试,就像有只无形的大手揪住了我的小心脏。
记得期末考的时候,只要一想到要坐在考场里面对那些试卷,我就紧张得不行,心都提到嗓子眼儿了,这就好比要上战场却没带武器一样害怕。
5. 一翻开那本旧相册,就掉进了回忆的漩涡。
有天我在家无聊,翻开了以前的相册,看着那些照片,就像是打开了记忆的大门,小时候的自己在照片里傻笑着,那些和家人、朋友的点点滴滴就像电影一样在眼前播放。
6. 一闻到花香,就感觉自己像是置身于花的仙境。
上次去公园,刚走到花坛边,那股花香扑鼻而来,我当时就想,这就跟仙女住在的花园似的,周围都是五颜六色的花,自己都快变成花仙子了。
7. 一尝到那熟悉的味道,就好像找到了心灵的慰藉。
像我每次回老家,吃到奶奶做的红烧肉,那熟悉的味道一在嘴里散开,我就觉得特别安心,就好像漂泊的小船终于驶进了港湾。
8. 一看到大海,就抑制不住内心的激动。
有次去海边旅行,当大海出现在眼前的时候,我简直兴奋得想跳起来,那感觉就像孩子看到了满屋子的玩具,一望无际的蓝色太让人着迷了。
9. 一想到远方的朋友,就有一股思念的潮水涌上心头。
有天晚上,看着天上的月亮,我突然就想起了在外地的好朋友,这种思念就像潮水一样,一波接着一波,我就想立刻打电话跟他聊聊以前的趣事。
- 1、下载文档前请自行甄别文档内容的完整性,平台不提供额外的编辑、内容补充、找答案等附加服务。
- 2、"仅部分预览"的文档,不可在线预览部分如存在完整性等问题,可反馈申请退款(可完整预览的文档不适用该条件!)。
- 3、如文档侵犯您的权益,请联系客服反馈,我们会尽快为您处理(人工客服工作时间:9:00-18:30)。
1#高炉冷却设备烧损原因分析及采取的对策
曹冶民李斌宜
(龙门钢铁集团有限责任公司)
摘要龙钢1#高炉由于设计、设备、冷却制度及操作等方面的原因,造成冷却设备烧损频繁,通过分析,制定出一系列对策,实践证明,效果显著。
关键词冷却设备烧损原因分析对策
1、概述:
龙钢1#高炉有效容积450m3,于2003年元月投产,使用的冷却设备有镶砖冷却壁、光面冷却壁、冷却板以及水冷炉喉钢砖。
由于施工时间紧,设备有缺陷,炉顶设备及炉后上料系统故障频繁,冷却制度不合理及操作方面的影响等原因,造成炉身冷却板大面积烧坏,局部炉壳温度升高,发红、冒煤气甚至冒火星、喷渣,严重影响高炉的正常生产。
2、高炉冷却情况
2.1高炉本体冷却壁简况
1#高炉本体冷却采用半密闭循环冷却系统,壁板结合,密集式冷却,共有冷却壁460块,冷却板224块,水冷炉喉钢砖18块。
从炉底向上共有19段冷却壁,第一至四段(炉底、炉缸区)为光面冷却壁;第五至十四段(炉腹、炉腰、炉身下部区)为镶砖冷却壁;第十五至十九段(炉身上部)为光面冷却壁;冷却板位臵从炉腰至炉身镶嵌在冷却壁夹缝中。
冷却壁的分布情况见表(1)
表(1)1#高炉冷却壁分布情况
2.2冷却水循环系统简况
2.2.1冷却设备
从开炉至2004年5月以前,高炉本体各部位的冷却设备均工作正常,但是从2004年5月中旬炉身下部冷却板开始烧损,截至2006年4月,共计损坏冷却设备60块:其中炉身冷却板41块,占冷却板总数的18.3%,现已全部更换;炉腰冷却板2块,暂时无法更换;炉腹冷却壁3块,2块加外冷却水箱,1块加外喷水;炉喉钢砖损坏14块,现全部灌浆后封死。
具体损坏时间及数目见表(2)
2.2.2炉体冷却系统运行情况
开炉初为了满足冷却要求, 高炉配备常压供水水泵3台,两
开一备;高压供水水泵2台,一开一备,水泵的具体参数见表(3)由于我公司使用的循环水为工业水,水质硬度大,无法达到
软水的要求,为了满足生产的需要,因此在冷却水中配加YH缓腐
阻垢剂和杀菌除藻剂。
加入缓腐阻垢剂的主要作用是控制水中钙、镁离子浓度,降低冷却水的硬度。
加入杀菌除藻剂主要是杀死水
中的藻类。
开炉初炉体各部位的冷却参数见表(4)。
表(2)冷却设备损坏情况
表(3)水泵参数
表(4)高炉本体冷却参数
3、分析冷却设备损坏的原因:
3.1 设计存在缺陷
在设计时炉身冷却板全部为空腔式,中间无隔板,无通道,在砖衬侵蚀完以后,冷却板前端局部温度升高,结垢严重,冷却强度变差,导致冷却板烧坏。
3.2冷却水质差
我公司的冷却水均为工业水,水质硬度大,长期使用后会产生大量的水垢和气泡,同时水池中易产生藻类,加入阻垢剂和杀菌除藻剂后,水质有所改善。
但是由于炉前的工作区域粉尘、烟气较大,大量的灰尘落入环水槽及收集水箱,导致水质中的悬浮物量较大,经常堵塞水管和阀门。
况且自开炉以来,水池从未进行过清理,仅采用定期换水的方法保证水质,导致池底沉积大量泥沙及其它杂物,严重影响冷却效果。
在已更换的冷却板中,发现有17块含有大量的泥沙沉积物和水垢,最严重的泥沙沉积物和水垢约占冷却板容积的1/3。
3.3 制定的冷却制度不合适
结合山西临钢(380m2)的经验,风口区的水压为0.3MPa,风口以上部位的冷却水压比该部位的风压大0.05MPa。
相比之下,1#炉的冷却水压偏低,风口区的水压只有0.12-0.14MPa;炉腹、炉腰的水压0.12-0.14MPa;炉身水压0.12 -0.16MPa;炉喉只有0.08 MPa。
随着水温的升高,会产生大量气泡,冷却水流速降低,冷却强度变差,导致冷却板、冷却壁烧损频繁。
3.4 设备的影响
1#炉设计时采用三座热风炉,七座布袋箱体,开炉初期由于布袋过滤面积偏小,压差过大,布袋破损严重;热风炉蓄热面积偏小,供风温能力低,另外热风出口管道经常发红、开裂,跑风严重。
2003和2004年平均风温只有820℃和845℃。
加上炉顶天轮及炉前设备故障频繁,兑罐不及时,渣铁出不净,布料器工作不正常等原因影响,造成高炉长期慢风、频繁无计划休风,2003和
2004年设备休风率高达2.59%和2.95%。
直到2004年9月,新建8、9、10#布袋和4#热风炉的投运,设备的运行状况才有所好转。
3.5操作方面的影响
从开炉起,1#炉由于种种原因生产一直不顺,使用的风、渣口小套结构为空腔式,无隔板,前端壁太薄,烧损频繁。
2003年1-10月份,共计烧损风、渣口小套500余个,其中6、7月份分别烧坏风、渣口小套61个和74个,对炉况的影响较大。
从十月份开始使用广东产的小套后,风、渣口的烧损才大大降低。
频繁的休风,长期的慢风及偏料,导致边缘煤气流发展,炉墙侵蚀严重,给冷却设备的烧损埋下了隐患。
2004年5月中旬,6、7#风口上方炉身下部冷却板烧坏,大量漏水,导致炉缸冻结,恢复炉况长达一月,频繁加萤石冼炉,破坏了炉墙及渣皮。
2004年5月-12月,共烧坏冷却板23块,占冷却板总数的10.3%。
2005年9月,1、2、3#热风炉大修后,风温提高到1000℃左右,随着高炉的强化冶炼,冷却板及冷却壁的烧损数目增加,炉喉水冷钢砖也出现了严重漏水的情况。
2005年9月至2006年4月,损坏冷却板、冷却壁及炉喉水冷钢砖共37块,占损坏冷却设备总数的61.7%。
尤其是进入2005年11月以后,炉身部位的热电偶温度波动异常,炉腹、炉腰出现跑煤气现象,比较严重的部位炉壳温度升高、发红、甚至冒火星、喷渣的情况。
4、通过以上分析,我们制定以下对策
4.1改变冷却板的构造
重新设计炉身的冷却板的构造,在冷却板中间加一道隔板,使冷却水能直接到达前端,确保一定的冷却强度。
在已更换的41
块冷却板中,未出现烧损,最长的已经使用2年,效果显著。
4.2加大冷却强度
针对我公司的实际情况以及参考兄弟单位的经验,从2005年11月起,提高各层的冷却水压,见表(五)
表(五)各层冷却水压
4.3 上、下部调剂相结合选择适宜的基本操作制度
4.3.1 下部调剂
由于2-3#、12-13#风口上方的冷却壁已经损坏,炉墙侵蚀严重,从2005年11月起,实际生产中采用适当缩小风口面积,减小风口斜度, 加长风口长度的措施,风口面积由原来的0.1383m 2减小到0.1357m2。
调整后炉况稳定顺行,煤气流分布趋于合理,中心气流适当发展,煤气中CO2含量由2005年的16%提高到现在的17 %以上。
具体数据对比见表(六)
表(六)风口布局对比
4.3.2 上部调剂
为适应下部调节, 上部改变装料制度,料制由2OOCC+3CCOO 变为3OOCC+2CCOO再变为3OOCC+1COOC+1CCOO,矿批由12T增加到12.4T再到12.8T,料线由1400mm调为1350mm。
4.3.3 热制度
根据原、燃料的情况选取中硅低硫的热制度,[Si]控制在0.4-0.7%之间,物理热控制在1450℃-1480℃之间;[S] 控制在0.02-0.035%之间;风温1030-1050℃,同时严格控制富氧量,富氧率稳定在2.5%左右。
4.3.4 造渣制度
在稳定炉况和炉温的基础上,提高炉渣碱度,由1.10-1.15 提高至1.15-1.20左右,渣中Mgo的含量控制在8-10%。
在适当提高炉渣碱度后,渣温明显升高,炉缸物理热充足,既改善了渣的流动性,又提高了脱硫效果。
4.4 加强冷却制度的管理
4.4.1每班对配水器排污两次,每2小时检查一次水温差变化及炉壳温度变化情况,做好记录,发现炉壳温度高于120℃时,及时开启外喷水装臵。
4.4.2发现有冷却壁或冷却板漏水,及时采取措施,改串联为单联,关小进水养护,并加外喷水。
4.4.3 短期休风时,适当控制总水压;长期休风时,停高压水,调小常压水。
4.4.4每周召开一次冷却系统专题会,对存在的隐患问题,制定紧急预案。
5、结语
通过采取一系列措施后,从2006年5月开始,冷却板的烧损数目大大减少,炉身、炉腰各部位的温度逐渐平稳,炉况稳定顺行,高炉利用系数提高,煤气的利用率达到40%以上。
特别是加强对炉体各部位的监测管理后,运行效果良好,有力地保证了高炉的安全正常生产。
5.1继续改善入炉原、燃料的质量,优化高炉操作,是目前情况下炉况稳定顺行的前题条件。
5.2加强冷却系统的管理和制定合理的冷却制度是延长一代高炉寿命的重要保证。
5.3缩小风口面积,采用加长风口,减少斜风口的数目,以达到适当发展中心,改善煤气流分布的目的。
5.4对不能更换的冷却板或冷却壁,采用灌浆后封死,加外喷水的方法,效果显著。
5.5计划使用广东汕头产的铜质冷却板,代替本厂制作的简易钢结构冷却板。