第二章 塑料制品设计
(第2讲)第二章 塑料制品设计 第二节
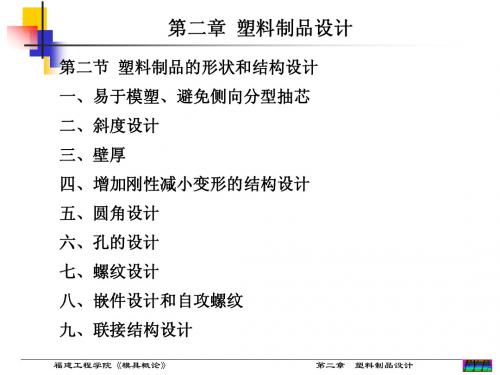
截面突变
福建工程学院《模具概论》
第二章 塑料制品设计
五、圆角设计
除特殊要求外,塑件转角处均应采用圆弧过渡。 除特殊要求外,塑件转角处均应采用圆弧过渡。
圆角作用一:减小应力集中, 圆角作用一:减小应力集中, 避免塑件开裂,过早破坏。 避免塑件开裂,过早破坏。 圆角作用二: 圆角作用二:改善熔体充模 特性,避免流痕和充不满。 特性,避免流痕和充不满。
第二章 塑料制品设计
四、增加刚性减小变形的结构设计
方法三:采用预变形补偿;需要有完善的成型性能数据库 方法三:采用预变形补偿;
有时为补偿视觉误差也可采用类似的外凸圆弧结构,如电 有时为补偿视觉误差也可采用类似的外凸圆弧结构, 补偿视觉误差也可采用类似的外凸圆弧结构 视机壳、汽车覆盖件…… 视机壳、汽车覆盖件
福建工程学院《模具概论》
第二章 塑料制品设计
三、壁厚 壁厚推荐值见表2-2-2、表2-2-3 、 壁厚推荐值见表
福建工程学院《模具概论》
第二章 塑料制品设计
三、壁厚 壁厚推荐值见表2-2-2、表2-2-3 、 壁厚推荐值见表
福建工程学院《模具概论》
第二章 塑料制品设计
三、壁厚 壁厚均匀性设计
福建工程学院《模具概论》
第二章 塑料制品设计
五、圆角设计
电镀件、静电喷涂和热喷涂件, 电镀件、静电喷涂和热喷涂件,过渡圆角有利于镀层或涂 层厚度均匀。 层厚度均匀。 电镀层厚度不均匀
福建工程学院《模具概论》
第二章 塑料制品设计
六、孔的设计
1、孔径与间距的关系 、 孔与孔边缘、孔与内外缘之间距离应不小于孔径。 孔与孔边缘、孔与内外缘之间距离应不小于孔径。
第二章 塑料制品设计
第二节 塑料制品的形状和结构设计 一、易于模塑、避免侧向分型抽芯 易于模塑、 二、斜度设计 三、壁厚 四、增加刚性减小变形的结构设计 五、圆角设计 六、孔的设计 七、螺纹设计 八、嵌件设计和自攻螺纹 九、联接结构设计
塑料制品的设计概述

2. 和塑料有关的原因
1)不同厂家生产的塑料的标准收缩率的变化 2)不同批量塑料的成型收缩率、流动性、结 晶化程度的差异 3)再生塑料的混合、着色剂等添加物的影响 4)塑料中的水分以及挥发和分解气体的影响
3. 和成型工艺有关的原因
1)由于成型条件变化造成的成型收缩率的波动 2)成型操作变化的影响 3)脱模顶出时的塑料变形、弹性恢复
第三节 金属嵌件的设计 一、 金属嵌件的形式
二、金属嵌件的设计原则 1)圆形或对称形状; 2)壁厚(金属嵌件周围的塑料层厚度); 3)倒角; 4)定位; 5)自由伸出长度≤2d; 6)降低生产效率,且生产不易自动化。
金属嵌件周围的塑料层厚度
Байду номын сангаас
(mm)
第四节 尺寸精度与表面粗糙度
一、 影响尺寸精度的因素 1. 和模具有关的原因: 1)模具的形式或基本结构 2)模具的加工制造误差 3)模具的磨损、变形、热膨胀
外形以大端为基准,斜度由缩小方向取得。
3. 制品壁厚
(1)制品必须有足够的强度和刚度;
(2)塑料在成型时有良好的流动状态;
(3)脱模; (4)壁厚均匀,否则使制品变形或产生缩孔、凹
陷及填充不足等缺陷。
(5)热固性塑料的小型塑件,壁厚取1.6~2.5mm, 大型塑件取3.2~8mm。
(6)热塑性塑料的小型制件,壁厚取1.75~ 2.30mm,大型制件2.4~6.5mm。
高密度聚乙烯:
耐冲击性能强,低温下韧性好, 适合制造寒 冷地区使用的货箱及冷藏室中使用的制品;
适应气候的能力强,如啤酒瓶周转箱,室外 垃圾箱等。
二、成型工艺对制品几何形状的要求
塑料制品的内外形状 脱模斜度 制品壁厚 加强肋 圆角 孔 支承面 标志及花纹
塑料制品设计
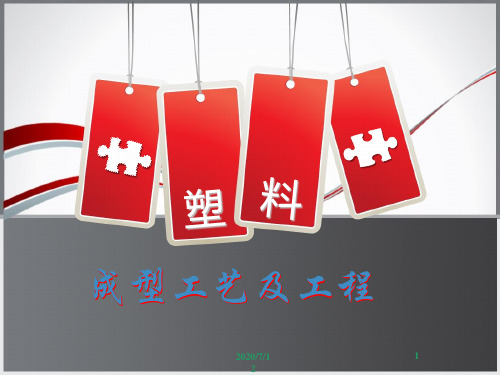
2.1 塑件的几何形状及结构设计
2.脱模斜度
为了便于塑件脱模,防止脱模时擦伤塑件,必 须在塑件内外表面脱模方向上留有足够的斜度α,
在模具上称为脱模斜度。
脱模斜度取决于 塑件的形状、壁厚 及塑料的收缩率,
一般取30 ′~1°30′
。
2.1 塑件的几何形状及结构设计 2.脱模斜度 脱模斜度表示方法:
2.1 塑件的几何形状及结构设计
6.孔的设计
(1) 孔的极限尺寸
模塑通孔要求孔径比(长度与孔径的比值)要小些
(2)孔间距 孔与孔间、孔与塑件边缘间距离应足够大 (3)孔的类型 通孔、盲孔和异形孔
通孔、盲孔加工方法: 直接模塑出来 模塑成盲孔再钻孔通 塑件成型后再钻孔
异形孔设计实例
2 .2 塑件螺纹的设计
加强筋与 支承面间 留有间隙
2.1 塑件的几何形状及结构设计
4.塑件的支承面 通常塑件一般不以整个平面作为支承面,而是
以底脚或边框为支承面。
2.1 塑件的几何形状及结构设计 4.塑件的支承面 支承面结构形式
2.1 塑件的几何形状及结构设计
5.圆角 在满足使用要求的前提下,制件的所有的ቤተ መጻሕፍቲ ባይዱ角尽
可能设计成圆角,或者用圆弧过渡。
• 中心距尺寸偏差数据除以2,冠(+-)
一般配合部分尺寸精度高于非配合部分尺寸 精度。
模具尺寸精度比塑件尺寸精度高2-3级。
1.3 塑件的表面质量
表面质量
表面粗糙度、光亮程度 色彩均匀性 表面缺陷:缩孔、凹陷 推杆痕迹 对拼缝、熔接痕、毛刺等
一般模具表面粗糙度要比塑件的要求高 1~2级
2 塑件结构设计及典型实例
1.2 塑件的尺寸和精度
2.塑件的精度
塑料制品与模具设计-塑料制品的设计
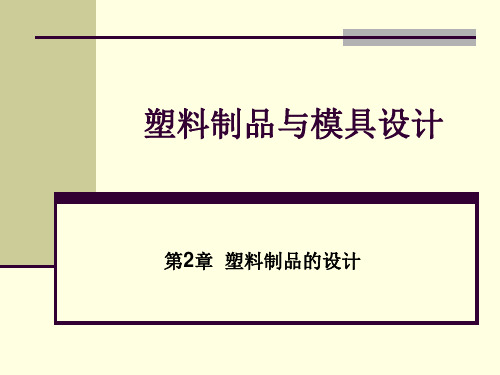
③选用精度等级对应考虑脱模斜度对尺寸和公 差的影响。
3.尺寸精度选用标准
具体选用塑件尺寸精度是根据我国原机械部制 定的SJl372—78塑料制品尺寸公差标准。
本标配。
公差数值表
精度等级的选用
更重要的是市场需求所决定的生产批量。在获得相当 规模的批量定单后,才可投资昂贵的模具和高效的设 备。
Question 1:
使用所选的加工方法能否得到部件的基本外形?
Question 2:
部件是多大?
Question 3:
需要什么样的复杂程度?
Question 4:
部件需要多少结构?
Question 5:
GB/T 14486-1993 工程塑料模塑塑 料件尺寸公差
常用材料模塑件公差等级的选用
受模具活动部分影响的尺寸,其公差为本标准规定的 公差值与附加值之和。
如:2级精度的附加值为0.05mm; 3—5级精度的附加 值为0.1mm; 6—8级精度的附加值为0.2mm。
用于孔时取表中数值冠以(十)号,用于轴时取表中数 值冠以(一)号,用于长度尺寸时取表中数值之l/2冠以 (±)号。
2. 精度
影响塑料模具精度的因素很复杂,其主要因素有如下 几方面: (1)成型材料
塑料本身收缩范围大,原料含水分及挥发物虽、原料 的配制工艺、批量大小、保存方法和保存时间等不同, 都会造成收缩不稳定。 (2)成型条件
成型时所确定的温度、压力、时间等成型条件,都直 接影响成型收缩。 (3)塑件形状
能否达到表面结构?
Question 6:
能否接受加工方法的成本结构?
2.1.4 塑料制品失效分析
1.塑料制品失效的影响因数 ①负载 作用于塑料件的负载有拉伸、压缩、弯曲、剪切和扭
2-塑料制品设计解析

a)旋向相同、螺距相等;b)旋向不同或螺距不同
三、齿轮的设计
1. 相同结构的齿轮应使用相同的塑料。 2. 齿轮内孔与轴采用过渡配合的方式,避免用键槽连接
方式,而用扁轴连接方式。
四、嵌件的设计
嵌件:在塑料成型中将金属或其他材料的结构件直接嵌入 塑件,使它们与塑件成为一个不可拆卸的整体
目的:增加塑件局部的强度、硬度、耐磨性、导电性、导 磁性等或延长塑件的使用寿命
由于塑料冷却后产生收缩,会紧紧地包在凸模上,或由于粘 附作用,塑件紧贴在型腔内,为了便于塑件脱模,并防止脱 模时擦伤塑件表面,设计塑件时必须考虑塑件内外表面沿脱 模方向具有合理的斜度,称为脱模斜度。
脱模斜度大小影响因素:塑料的性质、收缩率、摩擦系 数、塑件的几何形状和壁厚以及塑件的部位等
脱模斜度选取原则:
3) 对穿孔(互相垂直或斜交的孔),两个孔的型芯不能互 相嵌合(图左),应注意设计成能设置型芯的结构(右 图)
4)异形孔
斜孔或形状复杂的孔可采用拼合的方法来成形,避免侧向抽 芯。
7. 塑件的表面形状
为了在开模时容易取出塑件, 应尽可能避免侧向凹凸或与塑件 脱模方向垂直的孔而减少或消除 不必要的侧向抽芯等复杂的模具 结构,以简化模具结构。
6~8
热塑性塑件的最小壁厚参考值/mm
塑料名称 最小壁厚
聚苯乙烯
0.75
改性聚苯乙烯
0.75
聚乙烯
0.60
聚氯乙烯(硬) 1.15
聚氯乙烯(软) 0.85
聚丙烯
0.85
聚甲醛
0.80
聚碳酸酯
0.95
聚酰胺
0.45
聚苯醚
1.20
小型塑件推荐壁厚
1.25 1.25 1.25 1.60 1.25 1.45 1.40 1.80 0.75 1.75
第二章塑料制品设计

第2章 塑料制品设计
2.1塑料制品的工艺性
2.1.2塑件的尺寸和精度
(2).塑件的精度
A项:不受模具活动部分影响的尺寸公差值 B项:受模具活动部分影响的尺寸公差值 P29
第2章 塑料制品设计
2.1塑料制品的工艺性
2.1.2 塑件的尺寸和精度
(2).塑件的精度 尺寸精度的确定: 对于塑件上孔的公差可采用基准孔,可取表 中数值冠以(+)号。 + 对于塑件上轴的公差可采用基准轴,可取表 中数值冠以(-)号。 - 一般配合部分尺寸精度高于非配合部分尺寸 精度。 模具尺寸精度比塑件尺寸精度高2-3级。 影响塑件精度的直接或间接原因见表2-2
第2章 塑料制品设计
2.1塑料制品的工艺性
2.1.3塑件的表面质量
表面粗糙度、光亮程度 色彩均匀性
表面质量
表面缺陷:缩孔1~2级 不同加工方法及不同材料所能达到的塑件表面粗 糙度见表2-5 糙度见表2
第2章 塑料制品设计
2.2塑件结构设计及典型实例
2.2.1塑件的几何形状及结构设计 塑件的几何形状及结构设计
塑料制品的结构设计包括壁厚、脱模斜度、加 强肋、支承面、圆角、孔的设计及塑件的表面 形状等方面 1.塑件的表面形状(教材P45) 塑件的内外表面形状应尽可能保证有利于成型 见 教 材 表 2-18
第2章 塑料制品设计
2.2.1塑件的几何形状及结构设计 1.表面形状
装配附件、 凸台 —— 是用来增强孔或装配附件、或为塑件提 供支撑的截锥台或支撑块
凸台设计要点: 凸台一般应位于边角部位 其几何尺寸应小 其高度不应超过直径的两倍
第2章 塑料制品设计
2.2.1塑件的几何形状及结构设计 7.塑件的凸台与角撑
凸台设计实例
第2章 塑料制品的设计(后面部分)

2.2 尺寸精度与表面质量 2.2.3 表面质量
1、塑件制品的表面质量要求: ①表面粗糙度要求。 ②表面光泽性、色彩均匀性要求。 ③云纹、冷疤、表面缩陷程度要求。 ④熔结痕、毛刺、拼接缝及推杆痕迹等 缺陷的要求。
2.2 尺寸精度与表面质量 2.2.3 表面质量
2、型腔表面粗糙度要求
①一般,型腔表面粗糙度要求达0.20.4mm。 ②透明制品型腔和型芯粗糙度一致。 ③非透明制品的隐蔽面可取较大粗糙 度,即型芯表面相对型腔表面略为粗糙。
2.4.5 增加刚性减少变形的其他措施
将薄壳状的塑件设计为球面,拱曲面等, 可以有效地增加刚性、减少变形。 薄壁容器的沿口是强度、刚性薄弱处赐 于开裂变形损坏,故应按照下图所示方法来 给予加强。 当塑件较大、较高时,可在其内壁及外 壁设计纵向圆柱、沟槽或波纹状形式的增强 结构。
2.4.6
塑件支承面的设计
2.4.8 塑件上孔的设计
孔与孔的距离,孔边至塑件边缘距离 应不小于孔径。固定用孔因承受较大负荷, 可设计周边增厚来加强。如图3-23所示。 塑件上的孔分通孔和盲孔两大类,下 面分别介绍它的成型方法。 成型通孔时型芯的这三种结构形式, 是根据通孔大小和深度的具体情况从而满 足型芯足够的抗弯能力的需要出发而设计。 如图3-24
2.4.1
脱模斜度设计
在压塑成型深度较大的塑件时, 不但要求阴阳模均有脱模斜度,而且 还希望阳模的斜度大于阴模的斜度。 在压模闭合时,由于尖劈作用使塑件 上部密度得: *保证塑件的使用时的强度和刚度。 *使塑料熔体充满整个型腔。 塑件壁厚过小,则塑料充模流动的阻力很 大,对于形状复杂或大型塑件成型较困难。 塑件壁厚过大,则不但浪费塑料原料,而 且还给成型带来困难,尤其降低了塑件的生 产率,还给塑件带来内部气孔、外部凹陷等 缺陷。 所以正确设计塑件的壁厚非常重要。壁厚 取值应当合理。
塑料制品的结构设计PPT教案

光泽性取决于塑胶的原生状态; 颜色取决于真空镀本身; 真空镀的产品不耐磨,一般要在真空
镀后喷UV提高耐磨性。
6
塑胶表面电 塑胶电镀
镀
能有不同的颜色, 不同的光泽, 但不能制作半 透的 。
光泽性取决于塑胶的原生状态; 颜色取决于电镀本身; 电镀产品本身耐磨性好; 有些塑胶原料不能电镀
10.嵌件:
①塑件中镶入嵌件的目的: 增加局部强度、硬度、耐磨、导磁、导电性能,加强
一般来说,塑件高度在25mm以下者可不考虑脱模斜度。 但是,如果塑件结构复杂,即使脱模高度仅几毫米,也必须 认真设计脱模斜度。
1.脱模斜度:减小开模力和脱模力。
为了便于塑件脱模,防止脱模时擦伤塑件,必须在塑件内
外表面脱模方向上留有足够的斜度α,在模具上称为脱模斜 度。
大小:取决制品壁厚、收缩率、形状和部位。 30’-1º30’
注意事项
模具型腔表面抛 塑胶表面光滑,光 模具表面尺寸精度越高,表面光洁度越
光
亮。
高,零件的光泽越均匀。
2
塑胶原生纹 对模具表面抛光 塑胶表面呈现微小 蚀纹板分为光纹,半光纹,亚光纹;
面
的基础上再
的纹理,同时 粗纹一般不与喷油联用;
饰纹
表面有不同的 蚀纹板越细越不耐刮花;
光泽状态。
亚光纹易刮花。
3
塑胶表面喷 对塑胶表面进 能得到不同的颜色, 喷漆有亮光效果和亚光效果,喷漆能
工艺、外观要人性化。 (模具结构简单,制造方便)
塑件的工艺性 ——是塑件对成型加工的适应性. 塑件工艺性设计包括 :塑料材料选择、尺寸精度和表面粗糙度、塑件结构. 塑件工艺性设计的特点:应当满足使用性能和成形工艺的要求,力求做到
结构合理、造型美观、便于制造。
第二章模塑制品的设计

原料特性:
对制品尺寸制约最明显的是物料的的充模流 动性。物料充模流动性常用成型加工状态下的最 大流动距离比表示。 最大流动距离指的是:物料在某种加工状态 下,在流动通道内所能流动的最大长度与流动通 道厚度之比 “L/t ”。 显然,流动比大的物料,充模流动性好,制 品尺寸与厚度之比可 相对大些;相反,若用流动 性小的物料,因充模流动性差,制品尺寸与厚度 之比不能太大。否则,易造成充模不满、熔接不 良等缺陷。
表2-1-1
表2-1-2
图2-1-1
除国家标准外,根据用户要求,制品精度等 级及尺寸公差亦可按照其它标准设计。 目前可供参考的塑料制品尺寸公差标准有 国外标准:德国DIN16901;英国BPF;前苏 联POCT11710-71;瑞士VSM77012;美国塑料工 业协会(SPI)标准等。其中,德国的DIN标准在 国际上应用最广。 部颁标准:原四机部SJ1372-78 、原五机部 WJ1266-81。这是国标颁布前国内通用的塑料模 塑制品尺寸公差标准。
从模具设计制造的角度考虑合理的制品设计应在满足制品使用要求的前提下尽可能的简化模具结构满足模塑工艺对制品结构工艺性的要求以保证模具制造的可行性易行性尽可能降低模具费用缩短制模周期
第2章
模塑制品的设计
2.1 模塑制品设计原则 2.2 模塑制品设计要点
本章学习要求:
1.了解模塑制品和连续型材的类型特点 2.掌握模塑制品的设计原则及设计要点
另一类是以注射、压制等间歇成型工艺生产 的,结构尺寸完全由模具决定的模塑制品。如, 杯子、盆、框、电器壳体、机械零件、二次成型 坯料等。
模塑制品结构一般比较复杂,结构工艺性 要求高。其结构设计对模具设计制造的可行 性、易行性影响很大。 本章仅从模具设计制造的角度就模塑制品 设计作一简介。
塑料制品设计--塑料制品设计基础 ppt课件
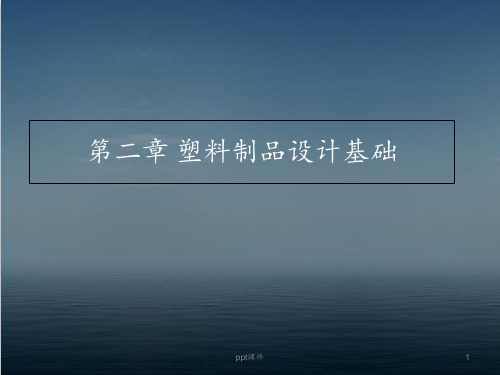
– 性能——指制品的力学、热力学、物理和化 学等性能。
ppt课件
5
• 2)选择材料 考虑制品的功能、性 能、加工性和生产成本;
• 3)确定加工方法 根据制品的形状、 大小、精度和生产成本选择;
• 4)对制品进行失效分析 对制品在 使用环境下失效形式,进行预测性计算或 相应的测试。
– 因热膨胀系数大,交替的冷缩热胀使塑料制品联接 处开裂。
• 聚酰胺(PA)
– PA含水量高,在高温下加工水解导致材料降解; – 固化时间过短,结晶不足,晶粒粗,而韧性差; – 使用环境湿度变化大,因吸水膨胀尺寸超出公差。
ppt课件
24
1.3 塑料的力学特性
• 1.3.1 静载荷下的形变行为
• 1.3.1.1 应变特性 • 1、应力—应变行为 • 影响塑料力学性能的主要因素:材料、温
ppt课件
10
材料 LDPE HDPE LLDPE PP
塑料的热性能
熔体流动速率 维卡软化温度0C
1.1
83
1.1
127
0.85
101
1.0
154
ppt课件
11
• 3) 物理性能 密度、渗透性(表1.24)、电性能、光学性能。
• 4) 化学性能 耐腐蚀性、耐候性(表 1.2-7) 、吸水性(表1.2-3) 、可燃 性(表1.2-5) 。
形的起点。塑料制 品的极限应力应少 于屈服点的应力。
ppt课件
21
• 2) 蠕变和松驰失效
– 长期负载作用的塑料件会产生蠕变形 变,最终会蠕变断裂。如密封件变松 失效。
• 3) 冲击失效
– 在冲击下变形和断裂。负荷作用时间 极短,变形速率很高。如脆性材料PS 等制品的破坏。
第二章塑料制件设计.pptx

塑料制件设计视塑料成型方法和塑料品种性 能不同而有所差异,本章主要讨论塑料制件中产 量最大的压制、注射、压铸成型塑件的设计,对 压缩空气、真空、中空成型制品的设计及挤出制 品的设计将在相应的章节中介绍。
设计塑件时必须考虑以下几方面的因素:
(1)塑料的物理机械性能,如强度、刚性、 韧性、弹性、吸水性以及对应力的敏感性。
2、成型通孔型Байду номын сангаас的安装方法,孔深与孔径的关系
孔深与孔径的关系:一端固定时,压制L=2D,注
塑L=4~6D,一端固定另一端支撑时孔深L可翻倍
3、成型盲孔型芯的安装方法,孔深与孔径的关系
盲孔,盲孔只能用一端固定的型芯来成型。因 此其深度应浅于通孔。根据经验,注射成型或压 铸成型时,孔深应小于4d。压制成型时孔的深 度,则应更浅些,平行于压制方向的孔一般不超 过2.5d,垂直于压制方向的孔深为2d。直径过 小(例如小于1.5毫米)或深度太大(大于以上值) 的孔最好用成型后再经机械加工的办法来获得。 如能在模塑时在钻孔位置压出定位浅孔,则给后 加工带来很大方便。
压制成型深度较大的制品时,不单要求阴 阳模均应有足够的斜度,而且希望阳模的斜度 大于阴模斜度。
三、壁厚设计
1、壁厚对成型工艺的影响 2、最小壁厚尺寸应满足的几个要求 P13 3、建议壁厚值 P13 4、塑件壁厚设计示例
四、增加刚性减小变形的结构设计
1、增设加强筋。加强筋设计的原则和注意事项 2、薄壳状的制件可制成球面或拱面 3、设计示例
以上前四条主要是指塑料性能特点,后两条 主要是考虑模具结构特点。
塑件设计的主要内容包括塑件的形状、尺 寸、精度、表面光洁度、壁厚、斜度、以及塑 件上加强筋、支承面、孔、圆角、螺纹、嵌件 等的设置。此外塑件美术造型设计是不可忽视 的,但不在本文讨论范围之内。
塑料制品的工艺性设计

塑料制品的工艺性设计塑料制品的结构设计又称塑料制品的功能特性设计或塑料制品的工艺性。
第一节 塑料制品设计的一般程序1、详细了解塑料制品的功能、环境条件和载荷条件2、选定塑料品种3、制定初步设计方案,绘制制品草图(形状、尺寸、壁厚、加强筋、孔的位置等)4、样品制造、进行模拟试验或实际使用条件的试验5、制品设计、绘制正规制品图纸6、编制文件,包括塑料制品设计说明书和技术条件等。
第二节 塑料制品设计的一般原则1、在选料方面需考虑: (1) 塑料的物理机械性能,如强度、刚性、韧性、弹性、吸水性以及对应力的敏感性等; (2) 塑料的成型工艺性,如流动性、结晶速率,对成型温度、压力的敏感性等; (3) 塑料制品在成型后的收缩情况,及各向收缩率的差异。
2、在制品形状方面:能满足使用要求,有利于充模、排气、补缩,同时能适应高效冷却硬化(热塑性塑料制品)或快速受热固化(热固性塑料制品)等。
3、在模具方面:应考虑它的总体结构,特别是抽芯与脱出制品的复杂程度。
同时应充分考虑模具零件的形状及其制造工艺,以便使制品具有较好的经济性。
4、在成本方面:要考虑注射制品的利润率、年产量、原料价格、使用寿命和更换期限,尽可能降低成本。
第三节 塑料制品的收缩塑料制品在成型过程中存在尺寸变小的收缩现象,收缩的大小用收缩率表示。
%10000×−=L LL S 式中S ——收缩率;L 0——室温时的模具尺寸; L ——室温时的塑料制品尺寸。
影响收缩率的主要因素有:(1) 成型压力。
型腔内的压力越大,成型后的收缩越小。
非结晶型塑料和结晶型塑料的收缩率随内压的增大分别呈直线和曲线形状下降。
(2) 注射温度。
温度升高,塑料的膨胀系数增大,塑料制品的收缩率增大。
但温度升高熔料的密度增大,收缩率反又减小。
两者同时作用的结果一般是,收缩率随温度的升高而减小。
(3) 模具温度。
通常情况是,模具温度越高,收缩率增大的趋势越明显。
(4) 成型时间。
- 1、下载文档前请自行甄别文档内容的完整性,平台不提供额外的编辑、内容补充、找答案等附加服务。
- 2、"仅部分预览"的文档,不可在线预览部分如存在完整性等问题,可反馈申请退款(可完整预览的文档不适用该条件!)。
- 3、如文档侵犯您的权益,请联系客服反馈,我们会尽快为您处理(人工客服工作时间:9:00-18:30)。
不合理
合理
二、 形状和结构设计
5.加强筋及增强措施 设计要求: ③ 尽量采用数个高度较矮的筋代替孤立的高筋,筋与筋之间的 距离应大于壁厚的两倍。 ④ 加强筋的设置方向应与受力方向一致,并尽可能与熔体流动 方向一致。同一面上,如果设置多根加强筋,其分布排列应 互相错开,以减少收缩不均引起的变形。
不合理
1.形状
左图塑件的内侧有凸起,需采用由侧向抽芯机构驱动的组合式型 芯,模具制造困难。 右图避免了组合式型芯,模具结构简单。
内侧凹的改进
1.形状
不合理
合理
2.结构
当塑件的内外侧凹陷较浅,同时成型塑件的 塑料为聚乙烯、聚丙烯、聚甲醛这类在脱模温度 下仍带有足够弹性的塑料时,模具可采取强制脱 模。 为使强制脱模时的脱模阻力不要过大引起塑件 损坏和变形,塑件侧凹深度必须在要求的合理范 围内,同时还要重视将凹凸起伏处设计为圆角或 斜面过渡结构。
塑件壁厚常用值:
热固性料:小件壁厚取1.6~2.5mm;大件取3.2~8mm;最大不宜大于10mm; 脆性料壁厚不小于3.2mm。
热塑性料:常取2~4mm;一般不小于0.6~0.9mm;最小可达0.25mm。
见教材表3-19、3-20
二、 形状和结构设计
4.塑件的壁厚 设计要点: 塑件应有一定的厚度才能具有足够的强度和刚度,即使产品设计时 对塑件的强度要求不高,为了承受脱模推出力,也要考虑塑件应有一定 的壁厚, 应合理设计壁厚。 1)壁厚太厚,收缩率加大,塑件变形大,冷却时间处长,易产生内 部气孔、外部凹陷、生产效率低。 2)壁厚太薄,强度和刚度下降,影响使用性能,成型时流动阻力大, 成型困难,成型后脱模困难。
第二章 塑料制品设计
电动车塑件
汽车塑件
家电塑件
日常用品塑件
主要内容 一、 塑件设计原则 二、 形状和结构设计 三、 尺寸精度与表面质量
§1、塑件的工艺性
塑件的工艺性 ——是塑件对成型加工的适应性
塑件工艺性设计包括 :塑料材料选择、尺寸精
度和表面粗糙度、塑件结构
塑件工艺性设计的特点:应当满足使用性能和 成形工艺的要求,力求做到结构合理、造型美 观、便于制造。
一、塑件设计原则: • 满足使用要求和外观要求 • 在保证塑件的使用性能、物理、化学、介电性 能与力学性能等的前提下,尽量选用价格低廉 和成形性能较好的塑料,并力求结构简单、壁 厚均匀、成形方便。 • 在设计塑件时应考虑其模具的总体结构,使模 具型腔易于设计制造,模具抽芯和推出机构简 单,尽量简化模具结构。 • 在设计塑件时,应考虑原料的成形工艺性,如 流动性、收缩性等,塑件形状便于成型加工。
二、 形状和结构设计 3.脱模斜度选取原则 (7)塑件侧面带文字、图案时,脱模斜度取10°~15°; 塑件侧面带花纹时,脱模斜度取4°~ 6 °;
利用脱模斜度的楔 形效应,提高压缩 模塑件上部密度。
二、 形状和结构设计
4.塑件的壁厚
塑件壁厚对质量和成型周期影响很大。
壁厚太薄:强度、刚度差,充模难; 壁厚太厚:浪费原料,成型周期长,内部缺陷增加; 壁厚设计原则:同一个塑件壁厚应尽可能均匀,壁厚差不大于3。 见教材表3-18
三、 塑料螺纹设计
3、设计要点: ①为减小螺距积累误差,螺纹配合长度应小于螺纹直径的1.5~2倍 ②外螺纹直径不小于4mm,内螺纹直径不能小于2mm,螺距不小于0.7mm ③模塑螺纹起止端不能设计退刀槽,也不宜用过渡锥面结构。螺纹端 部有大于0.2~0.8mm的无螺纹区,防止螺纹崩裂变形,以提高该处螺纹强 度并使得模具结构简单。
二、 形状和结构设计 3.脱模斜度选取原则: (1)沿脱模方向必须设置足够的脱模斜度;
塑件内表面脱模斜度通常大于外表面; 脱模斜度取值:热塑性料0.5°~3°;热固性料0.5°~1° 性能硬而脆的塑件,其脱模斜度比柔韧的大
注:收缩率大的塑件应取较大的脱模斜度。
塑料名称
型腔(a)
聚酰胺通用级 聚酰胺增强级 聚 乙 烯
直径小于1.5mm或深度大于孔径的 4 倍时,一般用成型后再机械加工的方法 获得。
注:压缩成形时尤应注 意,通孔深度应不超 过孔径的3.75倍
二、 形状和结构设计
8.孔的设计
5 ) 盲孔 盲孔只能用一端固定的型芯来成型。为避免型 芯弯曲,对于注射和压注成型,孔深不得大于孔径 的4倍;对于压缩成型,平行与施压方向的孔深度 为孔径的2倍.
整面支承,变 形后放置不稳。
支承面结构要合理,宜采用3~4个小凸台或凸缘支撑。
二、 形状和结构设计 6.支承面和凸台
二、 形状和结构设计 6.支承面和凸台 固定用的凸耳或台阶应有足够的强度,以 承受紧固时的作用力。应避免台阶突然过渡和 支承面过小,凸耳应用加强筋加强。
二、 形状和结构设计 7、圆角设计
除特殊要求外,塑件转角处均应采用圆弧过渡。 1.减小应力集中,提高了塑件强度及美观。使 模具在淬火和使用时避免产生应力集中而开裂, 提高模具的坚固性。
2.改善熔体充模特性,避免流痕和充不满。同 时利于脱模。
圆角取值:内圆角半径应达壁厚的1/4以上。
过渡圆角对充模的影响:酚醛模压成型
多处充不满
电镀件、静电喷涂和热喷涂件,过渡圆角有利于镀层或涂 层厚度均匀。 电镀层厚度不均匀
聚甲基丙烯甲脂 聚苯乙烯 ABS塑料 聚碳酸脂 聚甲醛 热固性塑料
二、 形状和结构设计 3.脱模斜度 选取原则: (2)脱模斜度的取向应根据塑件的内外形尺寸而定,塑件内孔 以型芯小端准,斜度沿扩大方向变出,塑件外形以型腔大端为 准,斜度沿减少方向标出
二、 形状和结构设计 3.脱模斜度 选取原则:
螺纹牙形
常用
重载
重载
单向受力
瓶盖常用
少用
三、 塑料螺纹设计
1、塑件上螺纹成型可用以下三种成型方法 ①模具成型 ②机械加工制作 ③在塑件内部镶嵌金属螺纹构件。 2、模塑螺纹的性能特点: ①模塑螺纹强度较差,一般宜设计为粗牙螺纹。 ②模塑螺纹的精度不高,一般低于GB3级。 3. 螺纹设计的基本原则: 螺纹选用:细小螺纹一般采用自攻螺钉联接,只成型底孔; 细牙螺纹不宜选用,可采用金属嵌件解决; 常拆卸和锁紧力大的螺纹也可用金属嵌件。
成型方法 :类似通孔。
二、 形状和结构设计
8.孔的设计
6 )异形孔设计: 斜孔或形状复杂的孔可采用拼合的方法来成形,避免侧向抽芯。
二、 形状和结构设计
8.孔的设计
7 )对于细长型芯,为防止其弯曲变形,在不影响塑
件的条件下,可在塑件的下方设支承柱来支撑。
二、 形状和结构设计
8.孔的设计
8) 对穿孔应注意设计成能设置型芯的结构
二、 形状和结构设计
4.塑件的壁厚 5)应根据塑件外形 尺寸及塑料品种合 理选择塑件的壁厚。
设计要点:
二、 形状和结构设计
4.塑件的壁厚 改善措施:
二、 形状和结构设计
4.塑件的壁厚 改善措施:
二、 形状和结构设计
4.塑件的壁厚 改善措施:
二、 形状和结构设计
5.加强筋及薄壁容器设计
增加塑件刚强度:单纯增加壁厚是不合理的,会带来成型 问题。 方法一:增设加强筋;
方法二:采用高刚度结构,如球面、拱形面、凸缘或皱折;
方法三:采用预变形补偿;需要有完善的成型性能数据库
有时为补偿视觉误差也可采用类似的外凸圆弧结构,如电 视机壳、汽车覆盖件……
二、 形状和结构设计
5.加强筋及薄壁容器设计
加强筋的作用: ① 在不增加壁厚的情况下提高塑件强度、刚度,避 免翘曲变形。 ② 在一定程度上可以改善塑料的充模流动性。
二、 形状和结构设计 1.形状 2.结构 3.脱模斜度 4.塑件的壁厚 5.加强筋及增强措施 6.支承面和凸台 7.圆角设计 8.孔的设计 9.符号、文字及标记的设计 10.铰链设计 11.齿轮的设计
二、 形状和结构设计 1.形状
塑件内外表面的形状设计除满足其使用性能外,应易于成型,尽 量避免侧抽芯结构设计。 侧面有孔时,通过改变孔的位置或形状来避免侧抽芯。
二、 形状和结构设计 9.符号、文字及标记的设计
①图案一般应设计为凸 形,方便加工 ②成型深度0.3mm左右 ③尽量将图案(字)刻在 与脱模方向垂直的面 上 ④为保证塑件的凸字在 使用过程中不被磨损, 可采用在凸字周围设 装饰边框。
二、 形状和结构设计
10.齿轮的设计
设计时应避免模塑、装配和使用塑料齿轮时产生内 应力或应力集中;避免收缩不均而变形。为此,塑料轮要 尽量避免截面突变,应以较大圆弧进行转角过渡,宜采用 过渡配合和用非圆孔连接,不应采用过盈配合和键连接。
合理
二、 形状和结构设计
5.加强筋及增强措施
设计要求: ⑤ 在布置加强筋时,应避免或减少塑料的局部集中。
二、 形状和结构设计
5.加强筋及增强措施
设计要求: ⑥ 一些加强筋会引起塑件局部凹陷,可采用以下措施 来修饰和隐藏。
二、 形状和结构设计
5.加强筋及增强措施
设计要求: ⑦将薄壳状的塑件设计为球面,拱曲面等,可 以有效地增加刚性、减少变形。
脱模斜度 型芯(b)
25´~40´ 20´~40´ 25´~45´ 30´~1° 30´~1° 30´~1° 30´~1° 30´~1° 20´~1°
20´~40´ 20´~50´ 20´~45´ 35´~1°30´ 35´~1°30´ 40´~1°20´ 30´~1° 35´~1°30´ 20´~1°
一、塑料材料的选择(分析)
塑料的选材包括:选定塑料基体聚合物(树脂) 种类、塑料具体牌号、添加剂种类与用量等 塑料原料选择方法:
使用环境(不同的温度、湿度及介质条件、不同的受 力类型选择不同的塑料)
使用对象(根据国别、地区、民族和具体使用者的
不同选材 )
按用途进行分类 (按应用领域 、功能 )