图解芯片制作工艺流程图课件
图解芯片制作工艺流程图
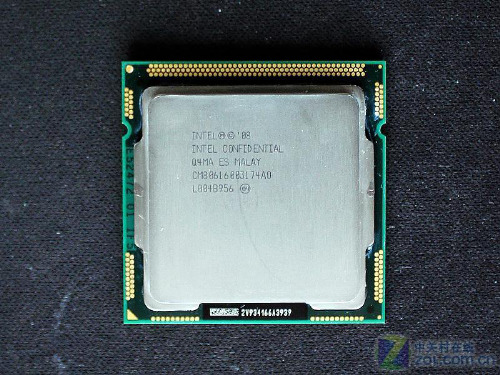
33
34
放置晶圆的黑盒子
35
36
单个内核:内核级别。从晶圆上切割下来的单个内核,这 里展示的是Core i7的核心。
37
封装:封装级别,20毫米/1英寸。衬底(基片)、内核、散 热片堆叠在一起,就形成了我们看到的处理器的样子。衬 底(绿色)相当于一个底座,并为处理器内核提供电气与机 械界面,便于与PC系统的其它部分交互。散热片(银色)就 是负责内核散热的了。
的硅,学名电
子级硅(EGS),
平均每一百万
个硅原子中最
多只有一个杂
质原子。此图
展示了是如何
通过硅净化熔
炼得到大晶体
的,最后得到
的就是硅锭
(Ingot)。
8
单晶硅锭:整体基本呈圆柱形,重 约100千克,硅纯度99.9999%。
9
10
处 理 晶 圆 的 机 器
11
硅锭切割:横向切割成圆形的单个硅片,也就是我们常说 的晶圆(Wafer)。顺便说,这下知道为什么晶圆都是圆形 的了吧?
25
铜层:电镀完成后,铜离子沉积在晶圆表面,形 成一个薄薄的铜层。
26
抛光:将多余的铜抛光掉,也就是磨光晶圆表面。
27
金属层:晶体管级别,六个晶体管的组合,大约500纳米。在不同晶 体管之间形成复合互连金属层,具体布局取决于相应处理器所需要的 不同功能性。芯片表面看起来异常平滑,但事实上可能包含20多层复 杂的电路,放大之后可以看到极其复杂的电路网络,形如未来派的多 层高速公路系统
20
光刻胶:再次浇上光刻胶(蓝色部分),然后光刻, 并洗掉曝光的部分,剩下的光刻胶还是用来保护 不会离子注入的那部分材料。
21
离子注入(Ion Implantation):在真空系统中,用经过加 速的、要掺杂的原子的离子照射(注入)固体材料,从而在 被注入的区域形成特殊的注入层,并改变这些区域的硅的 导电性。经过电场加速后,注入的离子流的速度可以超过 30万千米每小时。
集成电路制造工艺课件——芯片制造流程课件PPT
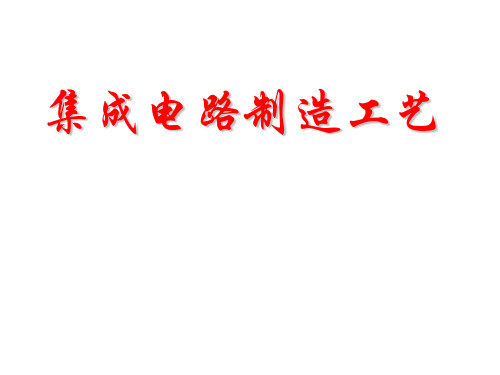
• 反应离子刻蚀(Reactive Ion Etching,简称为 RIE):通过活性离子对衬底的物理轰击和化学 反应双重作用刻蚀。具有溅射刻蚀和等离子 刻蚀两者的优点,同时兼有各向异性和选择 性好的优点。目前,RIE已成为VLSI工艺中应 用最广泛的主流刻蚀技术
N+
P+
有源区
集成电路的内部单元(俯视图)
晶体管光学照片
8mm低噪声放大器版图
晶体管SEM照片
沟道长度为0.15微米的晶体管 栅长为90纳米的栅图形照片
100 m 头发丝粗细
30m
50m 30~50m (皮肤细胞的大小)
1m 1m (晶体管的大小)
90年代生产的集成电路中晶体管大小与人 类头发丝粗细、皮肤细胞大小的比较
N沟道MOS晶体管
CMOS集成电路(互补型MOS集成电路): 目前应用最为广泛的一种集成电路,约占 集成电路总数的95%以上。
集成电路制造工艺
• 图形转换:将设计在掩膜版(类似于照相
底片)上的图形转移到半导体单晶片上
• 掺杂:根据设计的需要,将各种杂质掺杂
在需要的位置上,形成晶体管、接触等
• 制膜:制作各种材料的薄膜
杂质掺杂
• 掺杂:将需要的杂质掺入特定的半 导体区域中,以达到改变半导体电 学性质,形成PN结、电阻、欧姆接 触
行为仿真
是
综合、优化——网表
否 时序仿真
是 布局布线——版图
—设计业—
后仿真 是
Sing off
集成电路芯片设计过程框架
否
From 吉利久教授
芯片制造过程 —制造业—
芯片工艺流程
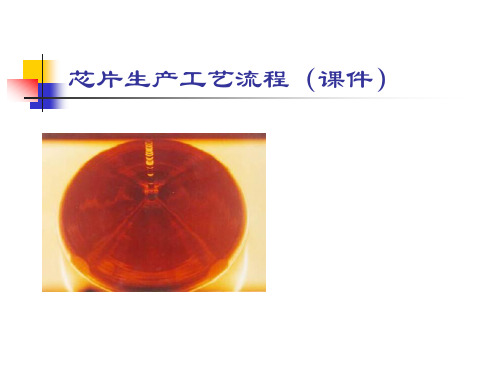
离子注入
基区扩散
发射区光刻
发射区预淀积
发射区扩散(*)
发射区低温氧化(*)
氢气处理
N+光刻(适用于P型片)
N+淀积扩散(适用P型片)
N+低温氧化(适用P型片)
氢气处理(适用P型片)
3B光刻
铝蒸发
四次光刻
氮氢合金
AL上CVD
2
氮气烘焙(适用N型片)
2
五次光刻
2
中测抽测
单项工艺-CVD(4)
玻璃的解吸
单项工艺-CVD(5)
单相工艺-离子注入(1)
单相工艺-离子注入(2)
单相工艺-离子注入(3)
单相工艺-蒸发(1)
蒸发原理示意图
单相工艺-蒸发(2)
溅射原理示意图
单相工艺-蒸发(3)
单相工艺-清洗
基础认知
衬底材料
外延层
扩散层
一次氧化
基区光刻
干氧氧化
单项工艺-光刻(6)
显影/漂洗
-将圆片进行显影/漂洗,不需要的 的光刻胶溶解到有机溶剂。
坚
膜
-硬化光刻胶。 -增加与硅片的附着性。
腐蚀
-干法腐蚀/湿法腐蚀
去胶
单项工艺-光刻(7)
光刻工艺过程
单项工艺-CVD(1)
单项工艺-CVD(2)
初级离子气体被吸收到硅片表面
单项工艺-CVD(3)
初级离子气体在硅片表面分解
2
测试系统
减薄、抛光
2 减薄和抛光部分
蒸金/银
2
背金合金
2
芯片测试
2
测试系统
N型片制造(一般)工艺流程
P型片制造(一般)工艺流程
图解芯片制作工艺流程图讲解学习

单晶硅锭:整体基本呈圆柱形,重 约100千克,硅纯度99.9999%。
7
8
处 理 晶 圆 的 机 器
9
• 硅锭切割:横向切割成圆形的单个硅片,也就是我们常说 的晶圆(Wafer)。顺便说,这下知道为什么晶圆都是圆形 的了吧?
10
• 晶圆:切割出的晶圆经过抛光后变得几乎完美无瑕,表面甚至可以当 镜子。事实上,Intel自己并不生产这种晶圆,而是从第三方半导体企 业那里直接购买成品,然后利用自己的生产线进一步加工,比如现在 主流的45nm HKMG(高K金属栅极)。值得一提的是,Intel公司创立之 初使用的晶圆尺寸只有2英寸/50毫米。
图解芯片制作工艺流程图
INTEL 图解芯片制作工艺流程
共九个步骤
2
3
• 沙子:硅是地壳内第二丰富的元素,而脱氧后的沙子(尤 其是石英)最多包含25%的硅元素,以二氧化硅(SiO2)的 形式存在,这也是半导体制造产业的基础。
4
5
• 硅熔炼:12 英寸/300毫米 晶圆级,下同。 通过多步净化 得到可用于半 导体制造质量 的硅,学名电 子级硅(EGS), 平均每一百万 个硅原子中最 多只有一个杂 质原子。此图 展示了是如何 通过硅净化熔 炼得到大晶体 的,最后得到 的就是硅锭 (Ingot)。
38
• 零售包装:制造、测试完毕的处理器要么 批量交付给OEM厂商,要么放在包装盒里 进入零售市场。这里还是以Core i7为例。
39
汇报完毕
谢谢指导!
此课件下载可自行编辑修改,仅供参考! 感谢您的支持,我们努力做得更好!谢谢
18
• 光刻胶:再次浇上光刻胶(蓝色部分),然后光刻, 并洗掉曝光的部分,剩下的光刻胶还是用来保护 不会离子注入的那部分材料。
芯片制造过程课件
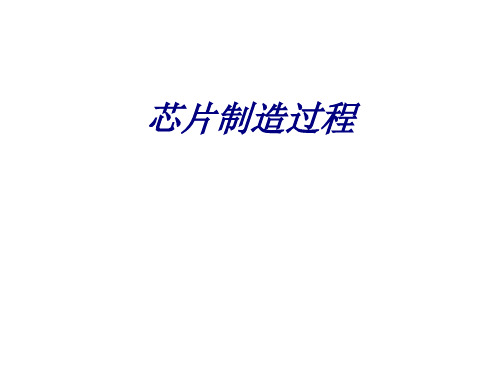
封装:封装级别,20毫米/1英寸。衬底(基片)、内核、散热片堆叠在一起,就形成了我 们看到的处理器的样子。衬底(绿色)相当于一个底座,并为处理器内核提供电气与机械 界面,便于与PC系统的其它部分交互。散热片(银色)就是负责内核散热的了。
处理器:至此就得到完整的处理器了(这里是一颗Core i7)。
单晶硅锭:整体基本呈圆柱形,重约100千克,硅纯度99.9999%。 第一阶段合影
硅锭切割:横向切割成圆形的单个硅片,也就是我们常说的晶圆(Wafer)。顺便说, 这下知道为什么晶圆都是圆形的了吧?
晶圆:切割出的晶圆经过抛光后变得几乎完美无瑕,表面甚至可以当镜子。
事实上,Intel自己并不生产这种晶圆,而是从第三方半导体企业那里直接购买成品, 然后利用自己的生产线进一步加工,比如现在主流的45nm HKMG(高K金属栅极)。 值得一提的是,Intel公司创立之初使用的晶圆尺寸只有2英寸/50毫米。
晶圆切片(Slicing):晶圆级别,300毫米/12英寸。将晶圆切割成块,每一块就是一个 处理器的内核(Die)。
丢弃瑕疵内核:晶圆级别。测试过程中发现的有瑕疵的内核被抛弃,留下完好的准 备进入下一步。
第八阶段合影
单个内核:内核级别。从晶圆上切割下来的单个内核,这里展示的是Core i7的核心。
蚀刻:使用化学物质溶解掉暴露出来的晶圆部分,而剩下的光刻胶的使命宣告完成,全部清除后就可以看到设计好 的电路图案。
第四阶段合影
光刻胶:再次浇上光刻胶(蓝色部分),然后光刻,并洗掉曝光的部分,剩下的光刻 胶还是用来保护不会离子注入的那部分材料。
金属层:晶体管级别,六个晶体管的组合,大约500纳米。在不同晶体管之间形成复 合互连金属层,具体布局取决于相应处理器所需要的不同功能性。
图解芯片制作工艺流程

• 清除光刻胶:离子注入完成后,光刻胶也 被清除,而注入区域(绿色部分)也已掺杂, 注入了不同的原子。注意这时候的绿色和 之前已经有所不同。
22
• 晶体管就绪:至此,晶体管已经基本完成。 在绝缘材(品红色)上蚀刻出三个孔洞,并填 充铜,以便和其它晶体管互连。
23
• 电镀:在晶圆上电镀一层硫酸铜,将铜离子沉淀 到晶体管上。铜离子会从正极(阳极)走向负极(阴 极) 。
39
• 零售包装:制造、测试完毕的处理器要么 批量交付给OEM厂商,要么放在包装盒里 进入零售市场。这里还是以Core i7为例。
40
19
• 光刻胶:再次浇上光刻胶(蓝色部分),然后光刻, 并洗掉曝光的部分,剩下的光刻胶还是用来保护 不会离子注入的那部分材料。
20
• 离子注入(Ion Implantation):在真空系统中,用经过加 速的、要掺杂的原子的离子照射(注入)固体材料,从而在 被注入的区域形成特殊的注入层,并改变这些区域的硅的 导电性。经过电场加速后,注入的离子流的速度可以超过 30万千米每小时。
37
• 处理器:至此就得到完整的处理器了(这里是一颗 Core i7)。这种在世界上最干净的房间里制造出来 的最复杂的产品实际上是经过数百个步骤得来的, 这里只是展示了其中的一些关键步骤。
38
• 等级测试:最后一次测试,可以鉴别出每一颗处理器的关 键特性,比如最高频率、功耗、发热量等,并决定处理器 的等级,比如适合做成最高端的Core i7-975 Extreme,还 是低端型号Core i7-920。
32
33
• 放置晶圆的黑盒子
34
35
• 单个内核:内核级别。从晶圆上切割下来 的单个内核,这里展示的是Core i7的核心。பைடு நூலகம்
芯片制造过程课件
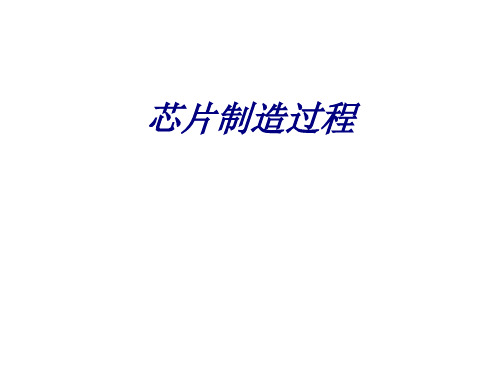
第五阶段合影
晶体管就绪:至此,晶体管已经基本完成。在绝缘材(品红色)上蚀刻出三个孔洞, 并填充铜,以便和其它晶体管互连。
电镀:在晶圆上电镀一层硫酸铜,将铜离子沉淀到晶体管上。铜离子会从正极(阳极) 走向负极(阴极)。
铜层:电镀完成后,铜离子沉积在晶圆表面,形成一个薄薄的铜层。
第六阶段合影
抛光:将多余的铜抛光掉,也就是磨光晶圆表面。
光刻:由此进入50-200纳米尺寸的晶体管级别。一块晶圆上可以切割出数百个处理 器,不过从这里开始把视野缩小到其中一个上,展示如何制作晶体管等部件。晶体 管相当于开关,控制着电流的方向。
现在的晶体管已经如此之小,一个针头上就能放下大约3000万个。 第三阶段合影
溶解光刻胶:光刻过程中曝光在紫外线下的光刻胶被溶解掉,清除后留下的图案和 掩模上的一致。
金属层:晶体管级别,六个晶体管的组合,大约500纳米。在不同晶体管之间形成复 合互连金属层,具体布局取决于相应处理器所需要的不同功能性。
芯片表面看起来异常平滑,但事实上可能包含20多层复杂的电路,放大之后可以看 到极其复杂的电路网络,形如未来派的多层高速公路系统。
第七阶段合影
晶圆测试:内核级别,大约10毫米/0.5英寸。图中是晶圆的局部,正在接受第一次 功能性测试,使用参考电路图案和每一块芯片进行对比。
单晶硅锭:整体基本呈圆柱形,重约100千克,硅纯度99.9999%。 第一阶段合影
硅锭切割:横向切割成圆形的单个硅片,也就是我们常说的晶圆(Wafer)。顺便说, 这下知道为什么晶圆都是圆形的了吧?
晶圆:切割出的晶圆经过抛光后变得几乎完美无瑕,表面甚至可以当镜子。
事实上,Intel自己并不生产这种晶圆,而是从第三方半导体企业那里直接购买成品, 然后利用自己的生产线进一步加工,比如现在主流的45nm HKMG(高K金属栅极)。 值得一提的是,Intel公司创立之初使用的晶圆尺寸只有2英寸/50毫米。
图解芯片制作工艺流程

28
29
• 晶圆测试:内核级别,大约10毫米/0.5英寸。图 中是晶圆的局部,正在接受第一次功能性测试, 使用参考电路图案和每一块芯片进行对比。
30
• 晶圆切片(Slicing):晶圆级别,300毫米 /12英寸。将晶圆切割成块,每一块就是一 个处理器的内核(Die)。
31
• 丢弃瑕疵内核:晶圆级别。测试过程中发 现的有瑕疵的内核被抛弃,留下完好的准 备进入下一步。
12
• 芯 片 加 工 无 尘 车 间
13
14
• 光刻胶(Photo Resist):图中蓝色部分就是在晶圆旋转过 程中浇上去的光刻胶液体,类似制作传统胶片的那种。晶 圆旋转可以让光刻胶铺的非常薄、非常平。
15
16
• 光刻:光刻胶层随后透过掩模(Mask)被曝光在紫外线(UV)之下,变 得可溶,期间发生的化学反应类似按下机械相机快门那一刻胶片的变 化。掩模上印着预先设计好的电路图案,紫外线透过它照在光刻胶层 上,就会形成微处理器的每一层电路图案。一般来说,在晶圆上得到 的电路图案是掩模上图案的四分之一。
在真空系统中用经过加速的要掺杂的原子的离子照射注入固体材料从而在被注入的区域形成特殊的注入层并改变这些区域的硅的导电性
1
2
INTEL 图解芯片制作工艺流程
共九个步骤
3
4
• 沙子:硅是地壳内第二丰富的元素,而脱氧后的沙(尤 其是石英)最多包含25%的硅元素,以二氧化硅(SiO2)的 形式存在,这也是半导体制造产业的基础。
21
• 清除光刻胶:离子注入完成后,光刻胶也 被清除,而注入区域(绿色部分)也已掺杂, 注入了不同的原子。注意这时候的绿色和 之前已经有所不同。
22
• 晶体管就绪:至此,晶体管已经基本完成。 在绝缘材(品红色)上蚀刻出三个孔洞,并填 充铜,以便和其它晶体管互连。
芯片制作流程图
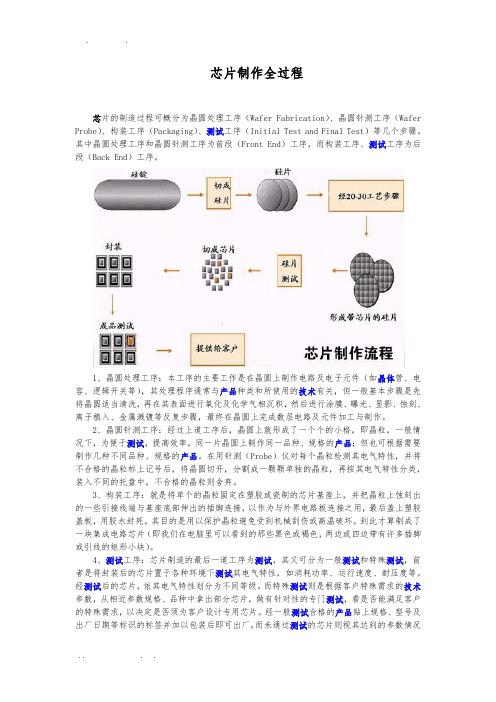
芯片制作全过程芯片的制造过程可概分为晶圆处理工序(Wafer Fabrication)、晶圆针测工序(Wafer Probe)、构装工序(Packaging)、测试工序(Initial Test and Final Test)等几个步骤。
其中晶圆处理工序和晶圆针测工序为前段(Front End)工序,而构装工序、测试工序为后段(Back End)工序。
1、晶圆处理工序:本工序的主要工作是在晶圆上制作电路及电子元件(如晶体管、电容、逻辑开关等),其处理程序通常与产品种类和所使用的技术有关,但一般基本步骤是先将晶圆适当清洗,再在其表面进行氧化及化学气相沉积,然后进行涂膜、曝光、显影、蚀刻、离子植入、金属溅镀等反复步骤,最终在晶圆上完成数层电路及元件加工与制作。
2、晶圆针测工序:经过上道工序后,晶圆上就形成了一个个的小格,即晶粒,一般情况下,为便于测试,提高效率,同一片晶圆上制作同一品种、规格的产品;但也可根据需要制作几种不同品种、规格的产品。
在用针测(Probe)仪对每个晶粒检测其电气特性,并将不合格的晶粒标上记号后,将晶圆切开,分割成一颗颗单独的晶粒,再按其电气特性分类,装入不同的托盘中,不合格的晶粒则舍弃。
3、构装工序:就是将单个的晶粒固定在塑胶或瓷制的芯片基座上,并把晶粒上蚀刻出的一些引接线端与基座底部伸出的插脚连接,以作为与外界电路板连接之用,最后盖上塑胶盖板,用胶水封死。
其目的是用以保护晶粒避免受到机械刮伤或高温破坏。
到此才算制成了一块集成电路芯片(即我们在电脑里可以看到的那些黑色或褐色,两边或四边带有许多插脚或引线的矩形小块)。
4、测试工序:芯片制造的最后一道工序为测试,其又可分为一般测试和特殊测试,前者是将封装后的芯片置于各种环境下测试其电气特性,如消耗功率、运行速度、耐压度等。
经测试后的芯片,依其电气特性划分为不同等级。
而特殊测试则是根据客户特殊需求的技术参数,从相近参数规格、品种中拿出部分芯片,做有针对性的专门测试,看是否能满足客户的特殊需求,以决定是否须为客户设计专用芯片。
芯片工艺流程演示文稿
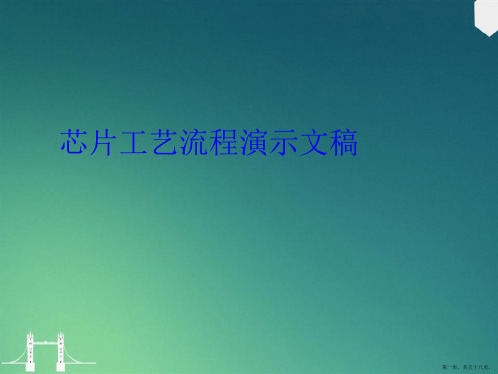
单相工艺-离子注入(1)
第二十四页,共五十八页。
单相工艺-离子注入(2)
第二十五页,共五十八页。
单相工艺-离子注入(3)
第二十六页,共五十八页。
单相工艺-蒸发(1)
蒸发原理示意图
第二十七页,共五十八页。
单相工艺-蒸发(2)
溅射原理示意图
第二十八页,共五十八页。
单相工艺-蒸发(3)
第二十九页,共五十八页。
芯片工艺流程演示文稿
第一页,共五十八页。
优选芯片工艺流程ppt
第二页,共五十八页。
单晶拉制(1)
第三页,共五十八页。
单晶拉制(2)
第四页,共五十八页。
单晶拉制(3)
第五页,共五十八页。
单晶拉制(4)
第六页,共五十八页。
单晶拉制(5)
第七页,共五十八页。
环境和着装
第八页,共五十八页。
单项工艺-扩散(1)
匀胶
-用弧光灯将光刻版上的图案转 移 到光刻胶上。
第十六页,共五十八页。
单项工艺-光刻(6)
显影/漂洗
-将圆片进行显影/漂洗,不需要的的光
刻胶溶解到有机溶剂。
坚
膜
-硬化光刻胶。
-
增加与硅片的附着性。
腐蚀
-干法腐蚀/湿法腐蚀
去胶
第十七页,共五十八页。
单项工艺-光刻(7)
光刻工艺过程
第十八页,共五十八页。
单项工艺-CVD(1)
第十九页,共五十八页。
单项工艺-CVD(2)
初级离子气体被吸收到硅片表面
第二十页,共五十八页。
单项工艺-CVD(3)
初级离子气体在硅片表面分解
第二十一页,共五十八页。
《芯片制造工艺》课件
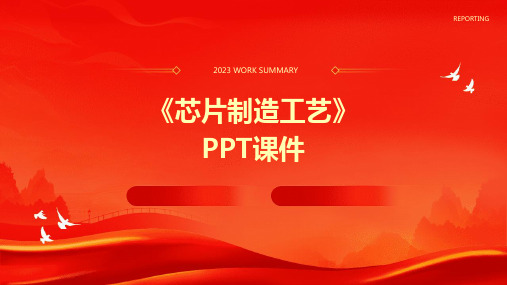
刻蚀机和镀膜机则分别用 于在晶圆表面刻蚀和沉积 材料,形成电路和器件结 构。
封装设备
封装设备是将制造好的芯片封装在管壳中,以保护芯片 并便于使用。
塑封机用于将芯片封装在塑料或陶瓷管壳中,打标机则 用于在管壳上打上标识,便于识别和追踪。
芯片制造工艺技术
薄膜制备技术
01
02
03
化学气相沉积
利用化学反应在芯片表面 形成固态薄膜,常用方法 包括热 CVD、等离子体增 强 CVD 和原子层沉积。
物理气相沉积
通过物理方法将材料原子 或分子沉积到芯片表面, 形成固态薄膜,包括真空 蒸发镀膜和溅射镀膜。
分子束外延
在单晶基底上以单层原子 精度控制生长单晶薄膜的 技术。
光刻技术
光学光刻
利用光线透过掩模投射到光敏材 料上,形成电路图形的光刻技术
。
X 射线光刻
利用 X 射线通过掩模投射到光敏 材料上,形成电路图形的光刻技术 。
离子束光刻
利用离子束通过掩模投射到光敏材 料上,形成电路图形的光刻技术。
刻蚀技术
等离子刻蚀
利用等离子体进行刻蚀的技术,可以实现各向异性刻蚀。
存储器优势
三星电子在存储器领域具有显著优势,其DRAM和 NAND闪存芯片在全球市场份额中占据领先地位。
产业链拓展
三星电子不仅在芯片制造领域有所建树,还 通过拓展产业链,涉足手机、电视等电子产 品领域。
中芯国际的芯片制造工艺
1 2
成熟工艺技术
中芯国际在成熟工艺技术方面具有较强的实力, 能够提供多种制程技术的芯片制造服务。
主要包括塑封机、打标机、测试机等。 测试机则用于测试封装好的芯片性能是否符合要求。
芯片工艺流程.ppt

2020/12/11
初级离子气体被吸收到硅片表面
单项工艺-CVD(3)
2020/12/11
初级离子气体在硅片表面分解
单项工艺-CVD(4)
2020/12/11
玻璃的解吸
单项工艺-CVD(5)
2020/12/11
单相工艺-离子注入(1)
2020/12/11
单相工艺-离子注入(2)
2020/12/11
。2020年12月11日星期五2020/12/112020/12/112020/12/11
• 15、会当凌绝顶,一览众山小。2020年12月2020/12/112020/12/112020/12/1112/11/2020
• 16、如果一个人不知道他要驶向哪头,那么任何风都不是顺风。2020/12/112020/12/11December 11, 2020
扩散层
一次氧化
2020/12/11
基区光刻
2020/12/11
干氧氧化
2020/12/11
离子注入
2020/12/11
基区扩散
2020/12/11
发射区光刻
2020/12/11
发射区预淀积
2020/12/11
发射区扩散(*)
2020/12/11
发射区低温氧化(*)
2020/12/11
2020/12/11
检查用显微镜
单项工艺-光刻(4)
清洗
淀积/生长隔离层
(SiO2 Si3N4 金属…)
匀胶
-HMDS喷淋(增加Si的粘性) -匀光刻胶
2020/12/11
单项工艺-光刻(5)
前烘
-增加黏附作用 -促进有机溶剂挥发
对版
- 1、下载文档前请自行甄别文档内容的完整性,平台不提供额外的编辑、内容补充、找答案等附加服务。
- 2、"仅部分预览"的文档,不可在线预览部分如存在完整性等问题,可反馈申请退款(可完整预览的文档不适用该条件!)。
- 3、如文档侵犯您的权益,请联系客服反馈,我们会尽快为您处理(人工客服工作时间:9:00-18:30)。
PPT学习交流
38
• 等级测试:最后一次测试,可以鉴别出每一颗处理器的关 键特性,比如最高频率、功耗、发热量等,并决定处理器 的等级,比如适合做成最高端的Core i7-975 Extreme,还 是低端型号Core i7-920。
PPT学习交流
39
• 零售包装:制造、测试完毕的处理器要么批量交 付给OEM厂商,要么放在包装盒里进入零售市场。 这里还是以Core i7为例。
PPT学习交流
17
• 光刻:由此进入50-200纳米尺寸的晶体管级别。一块晶圆 上可以切割出数百个处理器,不过从这里开始把视野缩小 到其中一个上,展示如何制作晶体管等部件。晶体管相当 于开关,控制着电流的方向。现在的晶体管已经如此之小, 一个针头上就能放下大约3000万个。
PPT学习交流
18
• 溶解光刻胶:光刻过程中曝光在紫外线下的光刻 胶被溶解掉,清除后留下的图案和掩模上的一致。
6
PPT学习交流
• 硅熔炼:12英 寸/300毫米晶 圆级,下同。 通过多步净化 得到可用于半 导体制造质量 的硅,学名电 子级硅(EGS), 平均每一百万 个硅原子中最 多只有一个杂 质原子。此图 展示了是如何 通过硅净化熔 炼得到大晶体 的,最后得到 的就是硅锭 (Ingot)。
7
单晶硅锭:整体基本呈圆柱形,重 约100千克,硅纯度99.9999%。
PPT学习交流
40
汇报完毕
谢谢指导!
PPT学习交流
41
23
• 电镀:在晶圆上电镀一层硫酸铜,将铜离子沉淀 到晶体管上。铜离子会从正极(阳极)走向负极(阴 极)。
PPT学习交流
24
• 铜层:电镀完成后,铜离子沉积在晶圆表面,形 成一个薄薄的铜层。
PPT学习交流
25
• 抛光:将多余的铜抛光掉,也就是磨光晶圆表面。
PPT学习交流
26
• 金属层:晶体管级别,六个晶体管的组合,大约500纳米。在不同晶体 管之间形成复合互连金属层,具体布局取决于相应处理器所需要的不 同功能性。芯片表面看起来异常平滑,但事实上可能包含20多层复杂 的电路,放大之后可以看到极其复杂的电路网络,形如未来派的多层 高速公路系统
PPT学习交流
21
• 清除光刻胶:离子注入完成后,光刻胶也被清除, 而注入区域(绿色部分)也已掺杂,注入了不同的原 子。注意这时候的绿色和之前已经有所不同。
PPT学习交流
22
• 晶体管就绪:至此,晶体管已经基本完成。在绝 缘材(品红色)上蚀刻出三个孔洞,并填充铜,以便 和其它晶体管互连。
PPT学习交流
PPT学习交流
36
• 封装:封装级别,20毫米/1英寸。衬底(基片)、内核、散热 片堆叠在一起,就形成了我们看到的处理器的样子。衬底 (绿色)相当于一个底座,并为处理器内核提供电气与机械界 面,便于与PC系统的其它部分交互。散热片(银色)就是负 责内核散热的了。
PPT学习交流
37
• 处理器:至此就得到完整的处理器了(这里是一颗 Core i7)。这种在世界上最干净的房间里制造出来 的最复杂的产品实际上是经过数百个步骤得来的, 这里只是展示了其中的一些关键步骤。
PPT学习交流
8
PPT学习交流
9
PPT学习交流
处 理 晶 圆 的 机 器
10
• 硅锭切割:横向切割成圆形的单个硅片,也就是我们常说 的晶圆(Wafer)。顺便说,这下知道为什么晶圆都是圆形的 了吧?
PPT学习交流
11
• 晶圆:切割出的晶圆经过抛光后变得几乎完美无瑕,表面甚至可以当 镜子。事实上,Intel自己并不生产这种晶圆,而是从第三方半导体企 业那里直接购买成品,然后利用自己的生产线进一步加工,比如现在 主流的45nm HKMG(高K金属栅极)。值得一提的是,Intel公司创立之初 使用的晶圆尺寸只有2英寸/50毫米。
PPT学习交流
31
• 丢弃瑕疵内核:晶圆级别。测试过程中发现的有 瑕疵的内核被抛弃,留下完好的准备进入下一步。
PPT学习交流
32
PPT学习交流
33
• 放置晶圆的黑盒子
PPT学习交流
34
PPT学习切割下来的单个 内核,这里展示的是Core i7的核心。
PPT学习交流
27
PPT学习交流
28
PPT学习交流
29
• 晶圆测试:内核级别,大约10毫米/0.5英寸。图中 是晶圆的局部,正在接受第一次功能性测试,使 用参考电路图案和每一块芯片进行对比。
PPT学习交流
30
• 晶圆切片(Slicing):晶圆级别,300毫米/12英寸。 将晶圆切割成块,每一块就是一个处理器的内核 (Die)。
PPT学习交流
1
PPT学习交流
2
INTEL 图解芯片制作工艺流程
共九个步骤
PPT学习交流
3
PPT学习交流
4
• 沙子:硅是地壳内第二丰富的元素,而脱氧后的沙子(尤其 是石英)最多包含25%的硅元素,以二氧化硅(SiO2)的形式 存在,这也是半导体制造产业的基础。
PPT学习交流
5
PPT学习交流
PPT学习交流
19
• 光刻胶:再次浇上光刻胶(蓝色部分),然后光刻, 并洗掉曝光的部分,剩下的光刻胶还是用来保护 不会离子注入的那部分材料。
PPT学习交流
20
• 离子注入(Ion Implantation):在真空系统中,用经过加速 的、要掺杂的原子的离子照射(注入)固体材料,从而在被注 入的区域形成特殊的注入层,并改变这些区域的硅的导电 性。经过电场加速后,注入的离子流的速度可以超过30万 千米每小时。
PPT学习交流
12
PPT学习交流
•芯 片 加 工 无 尘 车 间
13
PPT学习交流
14
• 光刻胶(Photo Resist):图中蓝色部分就是在晶圆旋转过程 中浇上去的光刻胶液体,类似制作传统胶片的那种。晶圆 旋转可以让光刻胶铺的非常薄、非常平。
PPT学习交流
15
PPT学习交流
16
• 光刻:光刻胶层随后透过掩模(Mask)被曝光在紫外线(UV)之下,变得 可溶,期间发生的化学反应类似按下机械相机快门那一刻胶片的变化。 掩模上印着预先设计好的电路图案,紫外线透过它照在光刻胶层上, 就会形成微处理器的每一层电路图案。一般来说,在晶圆上得到的电 路图案是掩模上图案的四分之一。