方案十四(注氨钝化方案)
钝化方案

钝化方案、1.1 建立汽油循环警告: 液态汽油将被引入油气回收装置,从现在开始要严格遵守有关的安全规程。
从现在开始需要油库辅助工作。
确认油气入口切断阀是关闭的,并确认活性炭床的所有出入口阀门是关闭的。
1 将汽油供给和返回线上的盲板拆除,并打开进油球阀和回油球阀,保证油气回收装置汽油的供给和返回畅通。
2 通过上位机,访问操作员画面,并进入电动阀操作画面,打开EBV01和EBV02。
3 开启EBV02,汽油会通过EBV02进入油气回收装置,通过吸收塔底的磁浮子液位计和上位画面的液位指示,观察汽油的液位,当达到40%时,启动回油泵,由于回油泵为变频器控制,其会根据液位调节频率,从而维持吸收塔的液位平衡。
4 检查高液位停车报警,在电动阀操作画面,手动开启EBV02,当EBV02开启到位,启动进油泵,使吸收塔液位上升至高限报警,再使其重新恢复正常液位。
5 检查低液位停车报警,在电动阀操作画面,手动开启EBV01,当EBV01开启到位,启动回油泵,使吸收塔液位下降至低限报警,再使其重新恢复正常液位。
6 此时系统就准备开始预处理活性炭床。
1.2活性炭床预处理过程1 开始时所有的阀门处于关闭状态,打开一个再生阀(MOV04、MOV06),将活性炭床抽真空,当活性炭床的空气都被排出,并且真空泵接近绝对真空时,手动关闭再生阀,并按下紧急停车按钮,这时可以检查系统是否存在泄露。
2 在检查完泄露后,通过吸附罐底部的放气口向活性炭床注入氮气,当活性炭床的压力接近大气压时,向系统的其余部分注入氮气,将吸收塔中的大部分空气置换为氮气,这时系统可以开始活性炭床的循环。
3改变阀门的开关位置开始循环,所有放空阀处于开启位置,入口阀一个关闭,另一个开启,再生阀一个关闭,一个开启,再生阀开启的活性炭床的入口阀应当是关闭的,这样可以构成气体的循环,注意再生阀的开度,要保证在循环过程中真空泵电机的电流不超过铭牌上所标识的电流。
4 设置真空泵变频器低速为15HZ,通过PLC控制系统开启电动阀MOV03和MOV05, 启动泵P-101通过PLC控制系统切换电动阀MOV01、MOV06和MOV02和MOV04给吸附罐的活性炭进行钝化。
尿素合成塔升温钝化方案

尿素合成塔升温钝化方案1、主控岗位接升温通知后引蒸汽,注意动作缓慢,排尽蒸汽管道中积水,防止液击;2、全开合成塔底部导淋阀和PV204压力调节阀,关PV204前后截止阀,引蒸汽至合成塔根部截止处,调节入塔蒸汽压力低于0.2MPa后,开PV204前截止阀进行合成塔升温,在塔顶温度未见起跳前严禁加大蒸汽量,防止起跳幅度小于30℃,当塔顶温度起跳后则以此点为参照物开始合成塔升温;3、升温钝化分三个阶段,常温至塔各点温度达100℃为第一阶段,此阶段升温速率在6~8℃/h。
100℃后恒温10小时加入纯氧(或空气)进行衬里钝化,此阶段为第二阶段。
钝化结束后以8~10℃/h的速率升至塔顶底约150℃,此阶段为第三阶段;4、升温开始时以塔顶温度为准控制升温速率,在塔中、下壁温度不见起跳时不可急于加大蒸汽量,只要控制好热点温度在指标内上升即可,待合成塔通蒸气到一定时间后(约8~10小时),塔中壁温度将突然起跳(要力求控制起跳温度在30℃内),此后升温参照塔壁中部温度进行。
当中壁温度升至约7~8小时后,塔下壁温度才产生起跳(起跳幅度仍力求30℃内),此后以下壁温度控制升温速率。
当温度到达塔底温度上升时,则以塔底温度控制升温速率,同时注意维持塔顶底温及外筒体壁温度与上、下两点温度之差均小于50℃;5、待塔底温度达100℃时,与蒸汽同时通入纯氧(或仪表空气)钝化内衬,升温转入钝化阶段,控制合成塔温度100℃~120℃并保持恒温,时间10小时,如用纯氧钝化,控制加氧速度为每小时一瓶;6、钝化结束后,加可大蒸汽补加量,把升温速度提到8~10℃/h,转入升温第三阶段,升温过程中应使塔内具有一定蒸汽压,如塔底导淋阀冒出大量蒸汽,则必须把导淋阀开度关小一些,注意塔底导淋应有汽液连续排出,塔底不可存液;7、待塔顶底温度达150℃,塔壁各点温度至120℃左右时,合成塔升温结束;8、升温期间如遇断蒸汽时,应及时打开塔顶取样阀和塔底导淋阀,让塔与大气联通防止衬里受损;此方案当否,请领导批示:尿素车间年月日。
升温钝化方案

高压系统升温钝化方案1)一般准备a. 所有工器具,消防、防护用品必须准备齐全好用。
、b. 全部仪表处于备用状态,所有切断伐、排放伐、分析取样伐处于关闭状态,打开全部仪表的根部伐,凡有手轮的调节伐,必须将手轮全部退出。
c. 配合主控调试所有调节伐是否灵活好用,主控伐位与现场伐位是否一致。
2)冷却水系统建立接班长或主控通知:A、打开上水总伐副线伐,开上水总管排气伐,待出水后关闭。
稍开冷却水上回水总伐,(主控注意打开PPV2801)关闭上水总伐副线伐。
打开各冷却器高点排气伐,缓慢打开废水冷却器C301、高调水冷却器C202、常压吸收塔循环冷却器C206、低调水冷却器C205、低压吸收塔循环冷却器C212、蒸汽冷凝液冷却器C209、回流冷凝器C304、蒸汽冷凝液冷却器C210的上回水伐,,待出水后关闭排气伐,(注意二次排气)全开总管上水伐,用总管回水伐控制上水压力0.4Mpa。
回水压力0.2Mpa,使上回水压差保持在0.2 Mpa。
B、打开冷凝液泵、锅炉给水泵、水解泵、熔融泵、高调水泵、氨泵、甲铵泵的轴承、变速箱、油冷器、泵体等冷却水上回水伐,建立冷却水。
(注意打开倒淋、丝堵排气)C、稍打开大颗粒系统冷却水总管上回水伐,打开TV2604前后切断伐,付线伐,(主控打开TV2604伐)最终产品冷高点排气伐,出水后关闭。
打开流化、第一产品冷、雾化、洗涤风机冷却水上回水伐及雾化风机油冷器上回水伐,建立冷却水。
(注意打开最终产品冷高点排气伐进行二次排气)3)设备充液接班长或主控通知,给以下设备充液a. 蒸汽冷凝液槽F210充液打开界区来的脱盐水总伐,及进F210的切断伐,充液至LI904为80%液位,当J210泵开起后,打开LPV904前后切断伐。
主控通过LPV904控制蒸汽冷凝液槽80%,投自控。
b. 锅炉给水罐F211充液打开J210泵至F211的LPV2901-2前切断伐,主控打开LPV2901-2,关闭LIC2905。
氨合成催化剂装填升温方案

目录1、74-1-H/74-1型催化剂装填升温还原参考方案2、74-1-H/74-1型催化剂生产工艺简图3、74-1-H/74-1型催化剂钝化方案4、74-1-H/74-1型催化剂的计算机模拟计算NC(ICI)74-1-H /74-1型氨合催化剂装填和升温还原参考方案1、总则德州华鲁恒升化工股份有限公司拟采用南化催化剂厂生产的NC(ICI)74-1-H /74-1(以下简称为74-1-H、74-1)型氨合成催化剂,用于新建的三十万吨/年的的合成氨装置中。
为了配合华鲁集团顺利完成这次工作,中国石化集团南京化学工业有限公司催化剂厂对催化剂的装填和升温还原工作特制作此参考方案。
2、技术要求2.1 催化剂装填要均匀密实,避免出现架桥和沟流现象,保证合成气体均匀分布。
2.2 催化剂升温还原要平稳,要防止水汽超标而引起的反复氧化还原现象的发生,还原要彻底,使催化剂发挥最佳性能。
3、催化剂装填要求氨合成塔催化剂筐共分三床层,装填时先装入第三床层氧化态催化剂(最下面一层,74-1),次之装填第二层(74-1),最后装填第一床层预还原催化剂(74-1-H)。
3.1 装填前准备工作3.1.1 对合成塔内件进行全面的检查,确认内件完好后,对内件催化剂筐壁进行清理,去除油污等杂物。
3.1.2 对内件进行一次试安装,以确保安装质量。
3.1.3 安装一个装催化剂的平台,备好过筛工具(包括1×1mm网孔的筛网、振动筛、运输和开桶工具等)。
3.1.4 备好吊桶,手提铁桶,1000Kg的磅称,起动吊车。
3.1.5 用干净的白布把内件与催化剂筐环隙等气体及所有气体通道密封,防止装填时催化剂进入,堵塞气体通道。
3.1.6 安装好塔内照明装置(必须是安全电压)。
安装进入塔内连接振动器的电源(注意应加装漏电保护装置)。
3.1.7 按要求必须先进行催化剂装填堆密度的试验。
取一个直径为800mm,高约为1500mm的圆柱形铁桶,事先计出每装入300mm高度所需的催化剂重量。
酸洗钝化液配方范文

酸洗钝化液配方范文配方:1. 硫酸(纯度98%):100 ml2.铬酸钠(纯度99%):50g3.萘酚(纯度99%):5g4. 硝酸(纯度65%):100 ml5. 氢氟酸(纯度40%):30 ml6.氯化铵(纯度99%):20g7. 氨氢氟酸(纯度40%):50 ml8.腐蚀抑制剂(如苯并噻啉类):3g9.清水:适量操作步骤:1. 在实验台上取一个混合容器,加入100 ml硫酸,然后缓慢加入50 g铬酸钠。
2.继续搅拌溶解铬酸钠,直至完全溶解并形成均匀的溶液。
3.加入5g萘酚,继续搅拌均匀。
4. 将100 ml硝酸缓慢倒入上述溶液中,并搅拌均匀。
5. 缓慢倒入30 ml氢氟酸,注意避免氢氟酸的腐蚀性,必要时佩戴防护手套、护目镜等个人防护用具。
6.加入20g氯化铵,继续搅拌。
7. 缓慢倒入50 ml氨氢氟酸,搅拌均匀。
8.最后加入3g腐蚀抑制剂(如苯并噻啉类),继续搅拌均匀。
9.最后加入适量清水,调节溶液的酸碱度和浓度至适宜的水平,搅拌均匀。
注意事项:1.在配制或使用酸洗钝化液时,需佩戴防护手套、护目镜等个人防护用品,避免溅入眼睛或接触皮肤,以免造成损伤。
2.氢氟酸具有极强的腐蚀性,需注意小心操作,避免发生事故。
3.配制过程中可根据具体情况调节溶液的酸碱度和浓度,以达到最佳的钝化效果。
4.配制好的酸洗钝化液应放置在密闭容器中保存,避免与空气中的杂质接触。
以上是一种常见的酸洗钝化液的配方,不同的金属和应用对象可能需要不同的配方。
在配制和使用过程中应严格遵守相关的化学实验安全操作规范,并根据实际需要进行调整。
注氮方案及安全技术措施
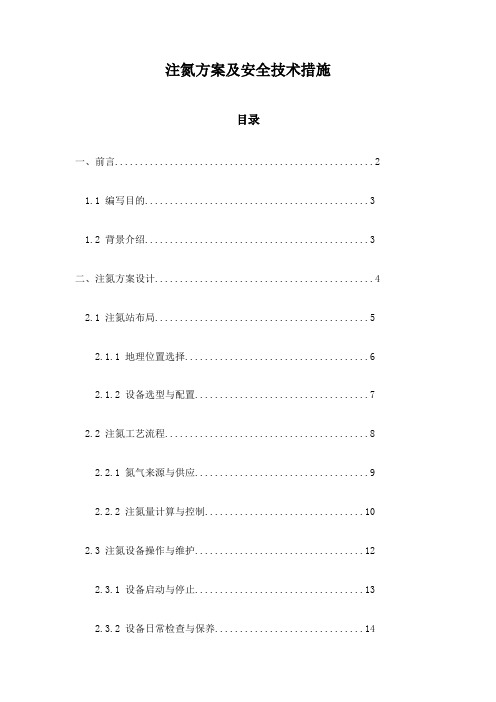
注氮方案及安全技术措施目录一、前言 (2)1.1 编写目的 (3)1.2 背景介绍 (3)二、注氮方案设计 (4)2.1 注氮站布局 (5)2.1.1 地理位置选择 (6)2.1.2 设备选型与配置 (7)2.2 注氮工艺流程 (8)2.2.1 氮气来源与供应 (9)2.2.2 注氮量计算与控制 (10)2.3 注氮设备操作与维护 (12)2.3.1 设备启动与停止 (13)2.3.2 设备日常检查与保养 (14)三、安全技术措施 (15)3.1 安全防护措施 (16)3.1.1 防火防爆措施 (17)3.1.2 个人防护装备配置 (18)3.2 应急处理预案 (19)3.2.1 注氮过程中可能发生的突发事件 (20)3.2.2 应急响应流程与责任人 (22)3.3 安全培训与教育 (23)3.3.1 员工安全培训计划 (25)3.3.2 安全知识竞赛与演练 (26)四、注氮方案实施与监控 (27)4.1 施工进度安排 (28)4.2 工程质量监督与验收 (29)4.3 运行管理与维护保障 (30)五、结语 (31)5.1 方案总结 (32)5.2 后续工作建议 (33)一、前言在工业生产中,注氮技术因其成本低廉、操作简便、高效环保等优点,被广泛应用于煤层气开采、油气输送管线防护、粮库和冷库密封保护,以及防止常规方法难以管理的可燃气体积聚物等场所的安全防护中。
针对这些应用场景,本文档旨在详细阐述注氮技术的实施方案及其必要配套的安全技术措施,以达到安全与效率的双重提升。
在设计和执行注氮方案时,我们必须考虑到潜在的爆炸风险、氮气纯度对设施的不良影响,以及可能对环境和操作人员可能构成的危害。
还需保证氮气的平稳、精准注入,以及确保系统兼容性和安全监控系统的有效性。
本方案的安全技术措施将遵循行业最佳实践,并严格遵守现行的法律法规与标准,以保障人、机、环的安全,降低事故发生的可能性,指导各相关角色及团队在实施过程中制定更为详尽的安全预案和操作流程。
齐鲁石化公司胜利炼油厂连续重整装置实习报告

1 实习车间概况1.1 概述化工作为工业发展的前提产业,随着经济全球化的发展,与中国面临的压力与挑战的日益增大,化工的发展与清洁化工越来越重要。
作为21世纪的建设者,我们积极参加去中国石化集团齐鲁石化公司胜利炼油厂的实习,以实现理论与实际得结合。
齐鲁石化公司胜利炼油厂连续重整装置采用连续重整工艺,通过原料预处理、重整反应及催化剂连续再生三个工序,把低辛烷值的石脑油变成富含芳烃的高辛烷值汽油组分,重整反应部分采用法国IFP二代超低压连续重整专利技术,只购买专利使用权,由中石化石油化工科学研究院提供设计基础数据,北京设计院作基础设计(工艺包)和工程设计。
采用国产重整催化剂RC-011和国产预加氢催化剂RS-1。
1.2 加氢预处理装置1.2.1装置概况齐鲁石化公司胜利炼油厂加氢裂化装置,装置建设规模为140万t/a (175t/h),装置设计运转周期为8000h(11个月)。
装置由反应、分馏、吸收稳定、气体脱硫及溶剂再生和氢气提纯(PSA)等部分组成。
主要产品是液化气、石脑油、航煤、柴油和尾油,同时副产部分气体。
设计的轻质油品转化率为60%,其中尾油用做蒸汽裂解制乙烯的原料。
随着世界重质原油与含硫(高硫)原油产量增大,炼油厂加工重质、高硫原油的比例越来越大,石油化工原料需求增长强劲,低硫、超低硫清洁燃料生产进程加快,推动了炼油企业装置结构的调整步伐,加氢裂化工艺原料适用性强,生产方案灵活,液体产品收率高,产品质量好,已经成为炼油企业原油二次加工、重油轻质化最重要的加工手段之一。
中国石化齐鲁分公司胜利炼油厂(简称胜炼)1.4 Mt/a加氢裂化装置由中国石化北京设计院设计,属齐鲁乙烯二轮改造重点配套项目,装置采用国产单段双剂串联一次通过工艺,包括反应、分馏、吸收稳定、气体脱硫、溶剂再生及PSA 氢提浓单元。
装置以直馏减压蜡油和焦化蜡油为原料,主要生产石脑油、航煤、柴油和尾油,2001年3月装置一次开车成功。
低压合成甲醇催化剂钝化方案

C307型合成甲醇催化剂钝化方案
一、钝化应具备的条件及准备工作
1、详细对合成系统设备、仪表、阀门、取样点作全面检查。
2、格氮气、空气、冷软水备用。
3、场胶管备用。
4、循环机完好备用。
5、分析取样器具、仪器完好,齐全备用。
二、钝化方法
循环机满量运行,系统压力保持0.7Mpa,出口温度保持在150℃左右,塔出口分析CO+H2+CO2≤0.3%为合格。
系统气体循环,初始控制进塔气体中氧含量≤0.2%,以塔入口取样分析,逐步提高入塔气中的氧浓度,直至出口氧含量达20%,出口温度≤150℃,钝化结束。
三、具体钝化步骤:
1、用氮气对系统进行置换,分析塔出口CO+H2+CO2≤0.3%为合格。
2、系统置换合格后,系统压力保持0.7Mpa,温度控制在150℃,开始配入
O 2,塔进口取样分析,每半小时一次。
起始O
2
浓度为0.2%,在温升不大于25℃
的情况下,逐步提高氧含量,直至氧含量为20%,继续钝化5小时,钝化结束。
四、钝化终点的判断
1、塔进出口氧含量无变化或变化不大。
2、塔出口无明显温升。
五、注意事项
1、塔出口分析CO+H2+CO2≤0.3%,确定合格后,才准系统配氧。
2、配氧钝化,必须小心谨慎,有专人负责指挥。
3、配氧过程中,发现汽包压力上升趋势加快,塔出口温度上升幅度较大时,应减少配氧,加大上水量,降低温度,待温度正常后重新配氧。
4、环机故障停止运转后,应立即停止配氧,塔后放空,补充合格氮气。
5、配氧时,由于催化剂活性较高,遇氧反应强烈,应严格控制起始配氧浓度和配氧速率。
不锈钢储罐酸洗钝化施工方案

不锈钢储罐酸洗钝化施工方案一、前言二、工程概况三、施工方案1.施工前准备2.酸洗钝化工艺流程3.施工安全措施四、施工组织与管理五、质量控制六、验收标准七、总结不锈钢储罐酸洗钝化施工方案一、前言本文档是针对储罐区二期工程不锈钢储罐酸洗钝化的施工方案,旨在保证施工质量、安全和进度的同时,确保环境保护和节能减排。
本方案由___制定,供施工人员参考。
二、工程概况储罐区二期工程是为了满足公司扩建生产规模的需要,新建的储罐区。
其中不锈钢储罐是存储特殊液体的重要设备,具有耐腐蚀、密封性好等特点。
为了确保不锈钢储罐的使用寿命和安全性,需要进行酸洗钝化处理。
三、施工方案1.施工前准备在施工前,应对施工区域进行清理,确保施工区域干净整洁,避免杂物影响施工质量。
同时,应对施工人员进行安全教育培训,确保施工人员具备相关技能和安全意识。
2.酸洗钝化工艺流程酸洗钝化是将不锈钢储罐表面的氧化物和污垢去除,形成一层致密的钝化膜,以提高其耐腐蚀性能。
具体工艺流程如下:1)清洗:用清水清洗储罐表面,去除表面的杂物和污垢。
2)酸洗:采用稀硝酸和稀氢氟酸混合液进行酸洗,去除不锈钢表面的氧化物和污垢。
3)中和:用氨水对酸洗液进行中和处理,以达到环保要求。
4)钝化:采用稀硝酸和稀氢氟酸混合液进行钝化处理,形成一层致密的钝化膜。
3.施工安全措施在施工过程中,应加强安全管理,确保施工人员的人身安全和设备安全。
具体措施如下:1)施工人员应佩戴个人防护用品,如防护服、防护眼镜等。
2)施工现场应设置警示标志,明确危险区域和安全通道。
3)施工过程中应加强通风换气,确保空气新鲜。
四、施工组织与管理在施工过程中,应加强施工组织与管理,确保施工进度和质量。
具体措施如下:1)制定详细的施工计划,明确施工任务和时间节点。
2)对施工人员进行分工,明确责任和任务。
3)加强现场监督和检查,及时发现和解决问题。
五、质量控制在施工过程中,应加强质量控制,确保施工质量。
具体措施如下:1)制定详细的施工规范和操作规程,确保施工符合标准和要求。
纯化水管道施工方案计划及钝化文本记录

纯化水管道施工方案计划及钝化文本记录不锈钢管道安装技术交底一、工程概况1.工程概述上海XX公司工程管道清洁度要求高,部分管道内部需抛光处理;输送介质主要为纯化水,对焊接工艺要求严格;,施工用火严格管理;连接管道焊环厚度较薄,易产生焊接变形,要采取预防措施。
3.施工依据施工图。
施工及验收规范(标准)。
装置区工艺管道工程施工组织设计。
二、施工准备1.操作人员操作人员以管工、电焊工为主,2.施工用料及施工措施用料施工用料按材料计划备齐施工材料,及时送到现场,能配套及陆续供应。
主要包括管材和相应的管件、阀门、法兰及焊接材料等。
施工措施用料施工措施用料主要为搭设预制平台及预制件存放垫隔的木方(板)及橡胶片,系统试验吹扫用的管材和阀门等材料。
3.主要施工机具主要施工机具为电焊机、鼠弧焊机、砂轮切割机、坡口机、空气压缩机、电动试压泵、导链、千斤顶、焊条烘干箱、焊条保温箱、手握砂轮机、水平尺、直角尺、尼龙绳及非碳钢手锤。
三、安装工艺1.管道预制使用的管材、阀门、管件等应符合设计要求及规范规定。
预制应在非碳钢材质的平台上制作,预制段尺寸按修正后的管段图进行,保证运输、吊装条件及有可调整的余地。
切割管子采用砂轮切割机切割,应彻底修磨其表面。
端面倾斜偏差为管子外径的1%且不大于2mm。
坡口加工坡口加工采用坡口机、手握砂轮机等方式进行,管壁厚度w3mm的开“”形坡口(不开坡口),管壁厚度大于372mm的开单面6070V”形坡口,钝边厚度11.5mm,加工后的坡口斜面及钝边端面的不平度不应大.5mm,角度应符合要求。
2.管道焊接焊接方式不锈钢管道焊接主要采用瀛弧焊、瀛弧焊封底手工电弧焊填充盖面(管内充敏气保护)及承插电弧焊方式进行。
焊接材料1)0Cr18N9、1Cr18N9T、材质采用EO10Nb5C以上进行,当环境温度在6(25PPm)。
2.2冲洗时,宜采用最大流量,流速不得低1.5m/S。
2.3排放水应引入可靠的排水井或沟中,排放管的截面积不得小于被冲洗管截面积的60%排水时,不得形成负压。
化学清洗后的钝化处理

化学清洗后的钝化处理(总4页)--本页仅作为文档封面,使用时请直接删除即可----内页可以根据需求调整合适字体及大小--化学清洗后的钝化处理摘要介绍化工设备在化学清洗后进行钝化处理的必要性以及相关的钝化处理技术的原理钝化剂性能处理工艺并指出使用环保型的钝化剂是今后钝化工艺的发展方向关键词化学清洗钝化预膜1 前言在化工行业中大量使用锅炉换热器管道贮罐反应器等设备在运行一段时间后这些设备会因工艺介质的沉积黏附和工艺介质对设备的腐蚀而结成壁垢附着在设备表面,从而引起降低传热降低流速堵塞和引起垢下腐蚀等问题给生产带来危害。
解决这些问题的有效途径是进行清洗,除去垢层。
并且随着石油化工等行业的发展需要清洗的设备越来越多因此化学清洗对于维护设备就显得非常重要。
化学清洗后,除去了垢层的金属设备表面会露出金属本体因化学清洗多为酸碱液经过化学清洗后,金属表面会变得异常活泼,在接触外界(如空气等)很容易使金属表面被再次腐蚀生锈因此在化学清洗后必须要进行钝化处理,使设备表面形成保护膜延长设备的使用寿命。
化学清洗后的钝化处理,能够有效地保护设备,所以它是整个化学清洗过程中的一个重要环节,具有重要的意义。
2 钝化原理金属设备经过化学清洗后,金属表面处于活化状态与氧接触很容易产生腐蚀通过一定的处理后来达到使它不易被腐蚀的目的。
钢铁处于活泼状态时在清洗后的水冲洗中腐蚀主要是受水的pH 氧浓度和时间的影响因此在钝化前要处理好水冲洗过程使在钝化处理之前有一个洁净度良好的金属表面。
如果水冲洗时间过长或其他因素影响,可以在钝化前对清洗设备进行漂洗处理。
各种钝化工艺其原理各有不同,总体上可分为形成氧化性膜和沉积性膜吸附膜两类钝化工艺。
氧化性膜钝化工艺主要是使用具有氧化性的钝化剂进行处理,使钢铁表面形成致密Y的氧化铁膜,合金钢中形成Y氧化铁膜和含铬的氧化性膜。
吸附膜钝化工艺,主要是利用各种无机盐的溶液对金属进行处理。
由于各种不同的金属盐在水中的溶度积不同,形成的难溶盐在金属表面沉积而形成致密的钝化膜。
加氢裂化催化剂

加氢裂化剂
多产石脑油和催化重整原料: 以石脑油和催化重整原料为主要的产品时,要选用 轻油型加氢裂化催化剂及采用全循环工艺流程。这 类催化剂的强酸性和中等加氢活性有利于反应物分 子的异构化、歧化、芳构化、加氢(脱氢)、氢转 移和C-C键断裂,是产物中烷烃的异构烃与正构烃 之比高,保留单环结构,石脑油芳潜较高。加氢组 分还能延缓生焦速度、保护裂解活性中心,使催化
加氢裂化剂
酸性组分: 酸性组分是裂解活性的主要来源,其酸性的强弱依 次为分子筛、无定型硅铝和氧化铝。按提供酸性的 载体结构分可以非为无定型和晶型两种,前者以氧
化铝和无定型硅铝为代表。后者以分子筛为代表。
一般来说分子筛比无定型载体提供更多的酸性中心
和更强的酸性。
加氢裂化剂
加氢组分: 加氢裂化剂的加氢活性主要由加氢金属提供。按照 活性和价值可分为贵金属和非贵金属两大类。 钨、钼一般用作主催化金属,在催化剂中含量较高, 它们除了可催化加(脱)氢以外,还可催化醇类脱 水(水合)反应和聚合反应。在压力下可以催化链
金属组分主要提 供加氢活性及能
需的孔结构,担载 分散金属均匀的有 效表面积和一定的 酸性,同时改善催 化剂的压碎、耐磨 强度与热稳定性;加 氢精制剂的载体主 要为Al2O3。
够加速C-N键氢
解的弱酸性,由 Vl B族或Ⅷ族的
金属。
加氢裂化剂
功能:提供酸性:B酸、L酸
功能:提供加氢(脱氢)活性
种类: 贵金属: Mo、W、Ni、Co
保护剂
保护剂是一个广义上的名词,包括一般意义上的保护剂、 脱金属剂,目的是改善被保护催化剂的进料条件,抑制杂
质对被保护催化剂孔道堵塞与活性中心被覆盖,即脱除机
械杂质、胶质、沥青质及金属化合物,保护被保护催化剂 的活性和稳定性,延长催化剂的运转周期。 保护剂一般由惰性物质、具有微量或少量加氢活性的催化 剂组成,采用分级技术装填于反应器顶部 .
- 1、下载文档前请自行甄别文档内容的完整性,平台不提供额外的编辑、内容补充、找答案等附加服务。
- 2、"仅部分预览"的文档,不可在线预览部分如存在完整性等问题,可反馈申请退款(可完整预览的文档不适用该条件!)。
- 3、如文档侵犯您的权益,请联系客服反馈,我们会尽快为您处理(人工客服工作时间:9:00-18:30)。
注氨钝化方案1、催化剂钝化目的新的加氢裂化催化剂经过硫化后具有较高的裂化活性。
为了适度抑制其使用初期的高活性,减少催化剂在开工初期的活性损失,提高催化剂的稳定性,防止和避免反应系统进油过程中可能出现的温度飞升现象,在反应系统引进设计原料油前用低氮油和注入液氨对催化剂进行钝化,以确保催化剂和生产的安全。
引低氮油和注入无水液氨是有效抑制催化剂初活性的钝化方法。
注入的无水液氨被催化剂吸附后,会抑制催化剂的初活性,随着反应温度的升高和运转时间的延续,催化剂吸附的氨会逐渐的解吸流失,催化剂又能恢复其正常活性。
2、准备工作2.1、D-111收液氨工作已经完成。
2.2、确认P-106单机试运合格。
2.3、新氢压缩机、循环氢压缩机、反应进料泵、注水泵等关键设备应处于好用状态。
2.4、装置全部仪表、控制系统已投用,冷氢调节阀开关灵活。
2.5、与调度联系好再准备一定数量的开工柴油,数量约3000吨,要求总氮量含<100μg/g,含水量<0.01w%,干点<350℃。
2.6、催化剂硫化结束。
2.7、分馏系统长循环热油运,具备接受反应生成油的条件,且循环油含水量<0.01w%。
3 、引开工低氮油3.1引低氮油入装置条件R101入口温度:150℃R102入口温度:150℃D105压力:14.0MPaD105温度:<50℃F101流量:200000Nm3/h(氢油比700:1),纯度不小于85%(V),硫化氢浓度不小于0.1%(V)。
3.2引油步骤3.2.1催化剂硫化结束后,调节好钝化所需工艺条件。
必须保证不断注入硫化剂,直至装置进料中设计原料油占75%,以维持循环氢中H2S含量≮0.1%(V)。
3.2.2确认分馏系统保持热油运,各液面平稳。
3.2.3联系罐区向装置引钝化用低氮油,控制D102液位60%。
3.2.4启动反应进料泵P-102,最小流量控制阀投用,反应系统进油,催化剂润湿。
开始的进料流率约35 t/h。
同时注意控制F-101出口温度控制平稳。
开工油进入反应器与催化剂接触,由于吸附热会使反应器里催化剂床层产生温度波,有时温升可高达30℃以上,因此在开始引进低氮油时,进料速率不能太快。
在温波已通过各反应器后,而且在高压分离器出现一定液位后,把进料率逐渐增加至70 t/h。
调节加热炉的燃烧条件,保持R101的入口温度为150℃,增开A101风机,保持D105温度为<50℃。
将R-101、R-102各路急冷氢投自动,设定控制温度150℃。
3.2.5注意观察热高分D103液面,D103出现液面后,反应进料速率提至140t/h,并逐渐把D103压力提至正常操作压力(提量的同时,调整加热炉炉膛温度,保证R101入口温度为150℃。
调整E101温控旁路阀,保证热高分入口温度>121℃。
)3.2.6分馏部分循环正常,随时能接收进料。
当D-103液位达到60%后,切断过滤器后至低分的原料油循环线,关闭D-104冲压氮气阀门(加好盲板),通过D103液控阀向D-104切油,当D104液位达到60%后,向C-201减油。
启动热低分气空冷A102,控制低压闪蒸罐D110入口温度<50℃,关闭D110顶充氮气线,并家盲板隔离。
当D110液位达到60%时向C201减油。
通过A101变频控制高分气冷后温度,当D-105液位达到60%后,关闭D-106冲压氮气阀门(加好盲板),通过D105向D-106减油,达到60%后向分馏系统减油。
监视控制D-105、D-106界位,当界位达到50%后向后路切水。
此时,一定要投用D-106顶压力控制,同时停止低压氮气充压,逐渐调节低分系统压力达到设计值2.5MPa(G)。
在确保尾油没有水的情况下,仍利用长循环将其循环到新鲜进料缓冲罐D-101。
同时,除了需维持液位外,停止再加入低氮开工油,维持从进料缓冲罐(D-101)到R-101的进油率为140t/h时的大循环。
3.2.7建立装置大循环3.2.7.1D103液位达正常后,开始向热低分D104减油,并逐渐将D104压力升至2.5MPa,建立液位后,建立装置大循环,维持反应器进料流率140t/h。
装置大循环流程:D102→P102/A、B→F101→R101→R102→D103→D104→C201→C202→A208→D100D100 P101 E108 SR101 D102。
3.2.7.2各容器、塔液面平稳后,低氮油停止入装置,可改界区外循环(在升温过程中,如塔、容器液面下降,可用界区低氮油补充)。
3.2.8引软化水进装置,建立D108液位及氮封。
4 、注氨钝化4.1先打开注氨点入口第一道阀(Y型止回截止阀),逐步关小返回阀,将P-106出口压力憋至16.0MPa(G),之后稍开液氨注入反应器入口的第二道阀,开始向系统注氨。
注入液氨的操作要特别的小心,防止反应器气体回窜。
以800kg/h(要求催化剂厂商确认)的速率向F101入口循环氢中注入无水氨。
每30分钟分析一次循环氢中的硫化氢及氨含量。
注意注氨后由于氨和循环氢中的硫化氢中和,将使循环氢中的硫化氢浓度大幅度降低,在注氨的同时,应不断向反应系统注入DMDS,保证循环氢中的硫化氢浓度不小于0.1%(V)。
4.2将R101入口温度提至230℃,R102入口温度升至205℃,注意升温速度为15℃/h,升温过程中,如反应器任一床层温升超过10℃,则停止升温,直至床层温升降低至6℃。
启动所有急冷氢控制点,并投入自动。
通过冷氢调节R102各床层入口温度比上一床层的入口低3℃。
4.3注氨后两小时,启动P103向A101入口注水,注水量11t/h。
注水24小时内,把R102入口温度升至230℃,以便使催化剂上吸附的水份减至最小。
4.4注水后立即分析D105排水中的氨含量,以后每半小时作一次上述分析。
在D105排水中测出氨含量之前,不要把R101入口温度升至230℃以上,或将R102入口温度升至205℃以上。
4.5在注氨顺利的情况下,7–8h后,高分水中会有明显的氨气味道出现,当高压分离器出来的污水中氨含量达到0.8%(w)时,即认为氨已经大量穿透,适当降低注氨速率,维持酸性水中氨含量为0.8~1.5%(w)。
必须保持注液氨设施的操作,直至反应进料中的设计原料油占75%为止(开工低氮油占25%)。
在此期间,不允许注氨速率低于60 Kg/h,否则需要把R-102的温度降低到230℃或230℃以下。
4.6将D105、D106污水送至污水汽提装置。
5、反应器升温5.1氨穿透后,以15℃/h的速度把R101入口温度升至325℃,升温期间,如R101总床层温升超过30℃,则停止升温,保持入口温度恒定,直至温升降至30℃以下。
5.2 R101升温同时,以15℃/h的速度把R102入口温度升至315℃。
通过用急冷氢自动控制每一床层≯3℃的降温。
如R-102中任一床层的温升超过10℃,则保持入口温度恒定,直至温升低于6℃为止。
按照降温分布曲线使R-102保持在初步裂化条件。
直至R-101切换为100%的设计进料为止(进料油中不再含有低氮开工油)。
5.3视各塔、容器液面情况,从装置外补充低氮油,以维持液面。
5.4反应升温同时,逐渐升高分馏部分的温度。
5.5催化剂钝化完毕时的工艺条件(1)R-101入口温度:325℃。
(2)R-102入口温度:315℃。
(3)反应器总温升:不大于30℃。
(4)高分压力:14.0MPa。
(5)循环氢中硫化氢含量:不小于0.1%(V)。
(6)循环氢纯度:不小于85%。
6、切换设计进料(VGO)6.1反应系统进油前的准备工作1、联系调度和罐区,准备送设计的原料油,同时准备好收加氢裂化外排尾油的储罐(2000~3000t)。
2、反应系统钝化操作完成。
3、新氢压缩机、循环机系统运转正常。
4、分馏系统具备开工条件。
从C-201塔底采样分析热油运后的低氮油含水和杂质量合乎要求:水含量不大于300ppm;总氮含量不大于100ppm;铁含量不大于0.8ppm。
5、装置内开工安全措施全部就位。
6.2注意事项与要求1、进油前要控制好反应系统各个操作参数。
2、进油开始后,要注意监视反应器床层温度的变化。
如果温度过高,少量用冷氢,必要时可以适当降低R-101入口温度。
3、切换原料油不要急,要等反应器温度平稳和精制产物中氮含量合格后再进行下一步操作。
4、在进原料油过程中,一定注意及时分析精制产物中的氮含量,保证不大于控制指标。
5、要保证循环氢纯度不小于85%。
要保证循环氢中硫化氢浓度不小于0.1%(V),如果低于此值应向系统中补充硫。
6、反应系统进油后,分馏系统要随时调整操作,以尽量地生产出合格产品。
7、压缩机和加热炉系统的操作要保持稳定。
钝化期间分析项目表6.3当装置具备了换进原料油的条件,即可开始换设计进料,同时分馏产品改走不合格线。
为安全平稳操作,由低氮开工油到换进100%的设计进料,分四个阶段进行,在增加25%的设计进料的同时减少25%的低氮开工油,且每一阶段不可低于3小时。
原料油进装置量由FIC3101、FIC3140指示确定,进反应系统的低氮循环油量由FIC3234指示确定。
在提温、提量的过程中严格控制每一床层温升≯5℃。
6.3.1进25%设计进料(进料量140 t/h,VGO 35 t/h,低氮油105 t/h)(1)进VGO前1小时,装置分馏闭路循环改为开路循环,外送尾油(柴油),同时从开工低氮油线收低氮油,稳定各容器液位。
(2)用FIC3105控制VGO流量为35t/h,FI3106低氮油流量为105t/h,维持R101进料流率为140t/h。
(3)根据C201、C202液面,把多余油送出装置。
在开工期间,送出装置的油不应再返回装置。
(4)进设计进料后,开始每小时一次采样分析R101流出物中氮含量,R101床层温度按控制R101流出物中碱氮含量不大于1ppm,总氮含量不大于5ppm的原则进行调节。
(5)切换设计进料期间,R102各床层温度遵循如下原则:①各床层入口温度按3℃温降分布控制。
②各床层温升应基本保持一致,且各床层温升不得超过5℃。
③冷氢阀开度控制在25%左右。
④提温过程中应注意,等温波传递到达下一床层之后才可以继续提温,严密监视床层单点温度,一旦温度有快速上升趋势时,应及时降温。
⑤R-102的入口温度低于R-101出口温度≯25℃以内6.2进50%设计进料(进料量140 t/h,VGO 70 t/h,低氮油70t/h)(1)把设计进料(VGO)流率增加至70t/h,同时把低氮油流率降至70t/h,维持R101进料140t/h,尾油视C201、C202液面送出装置。
(2)继续控制R102的入口温度比R101出口≯25℃,保持R102每个床层的温升低于5℃。