安全带校核
安全带设计指南00
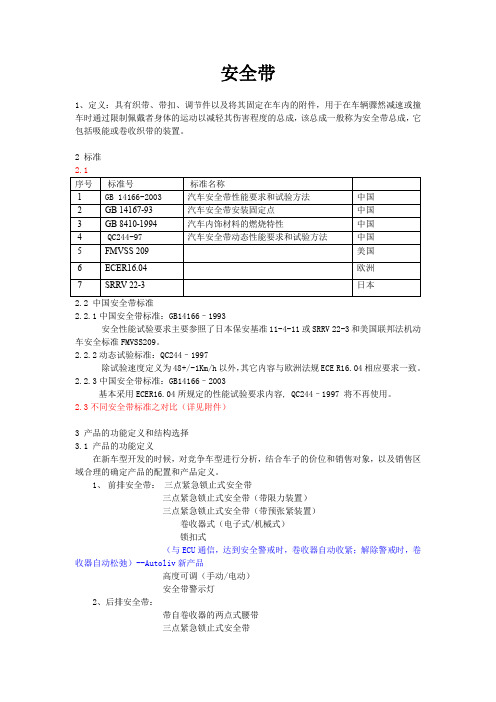
安全带1、定义:具有织带、带扣、调节件以及将其固定在车内的附件,用于在车辆骤然减速或撞车时通过限制佩戴者身体的运动以减轻其伤害程度的总成,该总成一般称为安全带总成,它包括吸能或卷收织带的装置。
2 标准2.12.2.1中国安全带标准:GB14166–1993安全性能试验要求主要参照了日本保安基准11-4-11或SRRV 22-3和美国联邦法机动车安全标准FMVSS209。
2.2.2动态试验标准:QC244–1997除试验速度定义为48+/-1Km/h以外,其它内容与欧洲法规ECE R16.04相应要求一致。
2.2.3中国安全带标准:GB14166–2003基本采用ECER16.04所规定的性能试验要求内容, QC244–1997 将不再使用。
2.3不同安全带标准之对比(详见附件)3 产品的功能定义和结构选择3.1 产品的功能定义在新车型开发的时候,对竞争车型进行分析,结合车子的价位和销售对象,以及销售区域合理的确定产品的配置和产品定义。
1、前排安全带:三点紧急锁止式安全带三点紧急锁止式安全带(带限力装置)三点紧急锁止式安全带(带预张紧装置)卷收器式(电子式/机械式)锁扣式(与ECU通信,达到安全警戒时,卷收器自动收紧;解除警戒时,卷收器自动松弛)--Autoliv新产品高度可调(手动/电动)安全带警示灯2、后排安全带:带自卷收器的两点式腰带三点紧急锁止式安全带三点紧急锁止式安全带(带预张紧装置)3、中间安全带:两点式腰带带自卷收器的两点式腰带三点紧急锁止式安全带3.2产品结构选择尽量在现有的产品结构中选择需要的产品。
比如:卷收器、锁舌、锁扣、导向件、高度调节器、紧固件(螺栓、螺母、螺钉、调整滚子)。
其他紧固件用垫圈、螺钉等尽量采用汽标件。
Autoliv的产品详见附页,可以在其中进行选择合适的产品结构。
3.3安装固定点螺孔尺寸按照GB14167-93的要求:安装固定点螺孔尺寸为7/16″-20UNF2A或2B。
安全带检验方法共7页

安全带检验方法本标准适用于高处围杆,悬挂和攀登作业。
安全带各部件和整体要做负荷试验。
分静负荷和冲击试验两部分。
1 静负荷试验和要求1.1 安全带各部件(包括带、绳、金属配件和使用的缝线)和围杆带、绳整体做静负荷试验,按GB6095—85《安全带》的规定进行,合格后才准组装成安全带。
整体围杆带或绳做4412.7N(450kgf)静负荷测试,合格后,才能批量生产。
1.2 试验设备49000N(5t)拉力试验机1台;980.6N(100kg)拉力试验机1台;试验架一座;0.5t卷扬机1台;整体静负荷试验装置一套如图10。
1.3 各部件检验情况1.3.1 安全带、绳的试件结构尺寸见图1、图2。
绳的两端应插成3~4道的花的绳环。
1―缝线;2―铆钉;3―带图1 带的试件尺寸1―绳环;2―编结花;3―绳图2 绳的试件尺寸1.3.2 金属配件的试件结构尺寸应符合设计要求。
1.3.3 安全钩静负荷试验连接形式,见图3、图4、图5、图6、图7。
1―夹具;2―扁钢钩;A、B―加力处图3 扁钢钩测试图1―夹具;2―圆钢钩;A、B―加力处图4 圆钢钩测试图]1―绳;2―自锁钩;3―夹具;A、B―加力处图5 封闭式自锁钩测试图1―绳;2―开启式自锁钩;3―挂钩;4―夹具;A、B―加力处图6 开启式自锁钩测试图1、4―夹具;2―挂钩框;3―攀登钩;A、B―加力处图7 攀登挂钩测试图1.3.4 各种连接环静负荷试验的连接形式,见图8。
1―板构夹具;2―半圆环;3―U型环夹具;4―圆环;5―三角环;6―品字环;7―8字环图8 连接环或试验用具图1.3.5 安全带卡子静负荷试验连接形式,见图9。
1、3―夹具;2―腰带扣;A、B―加力处图9 腰带扣测试图围杆带或绳做整体测试的连接形式,见图10。
1―夹具;2―安全带;3―半圆环;4―钩;5―三角环;6―围杆带或围杆绳;7―木轮;A―加力处;B―固定端图10 围杆带或绳整体静负荷试验图1.5 缝线试验将线栓在夹具上做拉力试验,要求破断负荷为156.8N(16kgf),拉断速度100mm/min。
汽车安全带固定点
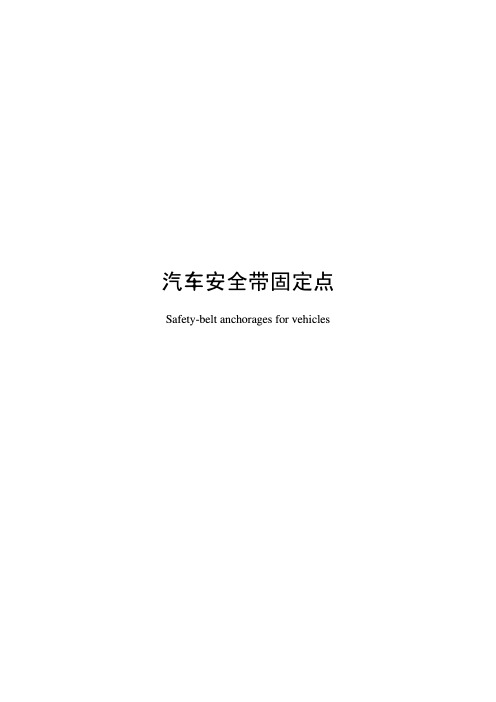
汽车安全带固定点
1 范围
本标准规定了汽车安全带安装固定点的位置、 强度要求和试验方法。 本标准适用千本公司生产的M1类和N类汽车上前向和后向座椅成年乘员用安全带固定点。
2 规范性引用文件
下列文件对千本文件的应用是必不可少的。凡是注日期的引用文件,仅所注日期的版本适用千本文 件。 凡是不注日期的引用文件, 其最新版本(包括所有的修改单)适用千本文件。
时 Qz 杖沪 土1沪
',
j j.
「
'I j
丿l f
I Ii /
j'
,f .
!lJ Ll丰帝扣
fl. l
伪O
J
J
r ·} ”
I
I L
v / ,.
L上
万
j f
( l, .
ll 丰扣纠
气•.
图1
4.3.2.3 如图2所示, 后排座椅安全带下有效固定点的角度: a) 对千M1类车辆的后排座椅, QI (非带扣侧)和a 2 C带扣一侧)应在30° �so 0 。 如果后排座 椅是可调的, 则在所有正常移动位置, 上述要求均有效; b) 对千N类车辆的长条座椅和带有调节机构且靠背小千 20° 的座椅, 以及正常使用位置上的其 他后排座椅, QI (非带扣侧)和a 2 C带扣一侧)允许在 20° �so 0 之间。
4
注4: CY 平面的定义:过 C 点的水平面为 CY 平面。 C 点位于 R 点垂直上方 450 mm 处, 即 CR=450 mm; 如果 s;,,:zso mm
时且用 BR= 260 mm+O. 8 XS 计算, 则 CR=500 mm。 注5: S 值是安全带上有效固定点至 P 平面的距离, S 值不得小千 140 mm。 注6: p平面的定义: P 平面是平行于车辆纵向中心平面的平面。 如果乘坐位置是由座椅的形状确定的, 则 P 平面为
车辆总布置人机工程设计的一般步骤
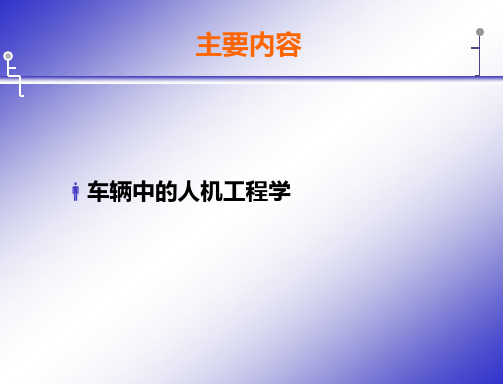
眼椭圆
眼椭圆
驾驶员眼椭圆与视野设计
驾驶员的手伸及界面及操作件的合理布置
足蹬力 手操舵力 手柄的设计 坐姿下驾驶员双手对方向盘的手操舵力与方向盘倾角 (侧视图上方向盘平面与水平之间的夹角)有密切的 关系。方向盘平面越接近水平即倾角越小,手操舵力 越大。但是可以转动方向盘的角度值变小,如图2-5所 示。此时对应的座椅靠背也比较垂直,驾驶员坐姿相 应地也比较平直。
驾驶员眼椭圆与视野设计
眼椭圆应用之轿车仪表板盲区 汽车行驶过程中,驾驶员需要经 常观察仪表板上的信息。在观察 时,驾驶员的视线会受到方向盘 的阻挡,方向盘的轮毂、轮辐和 轮缘在仪表板上形成相应的盲区 称之为仪表板盲区
驾驶员眼椭圆与视野设计
轿车驾驶员的前方视野
驾驶员的手伸及界面及操作件的合理布置
驾驶员的手伸及界面及操作件的合理布置
驾驶员手伸及范围的 分区 基准平面:指与汽车 纵向对称平面平行的 与座椅参考点(设计 时采用的H点)左右相 距50mm的两平面。
驾驶员的手伸及界面及操作件的合理布置
1区:位于参考平面左侧,由下列表面形成的区域: A)平行于方向盘平面且向上相距20mm的平面; B)平行于方向盘平面且向下相距170mm的平面; C)沿方向盘轮圈外缘向外扩展100mm的圆柱面。 该圆柱面的中心线与方向盘轴线共线。 D)通过方向盘轴线的两垂直相交平面。两垂直相交平面与 参考平面之间的夹角分别为40º,130º。
驾驶员的手伸及界面及操作件的合理布置
安全带法规校核
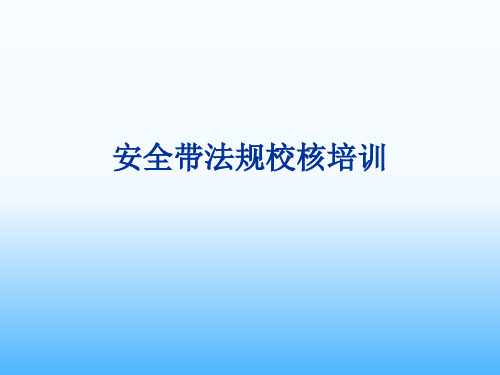
按照法规步骤作出上下固定点要求的角度、距离等画出规定区域
与法规相关要求值作比较,确定是否满足法规要求
安全带上部安装固定点区域
(说明:对于高度可调的安全带固定点,暂时没有相关的法规要求,有 待今后进一步的研究)
国标规定上部固定点区域
安全带法规校核培训
安全带简介
❖ 安全带定义:具有织带、带扣、调节件以及将其固定在车内的附件,用于在车辆骤然减速或撞车时通过 限制佩戴者身体的运动以减轻其伤害程度的总成,该总成一般称为安全带总成,它包括吸能或卷收织带 的装置。
❖ 1885年,安全带已经出现并使用在马车上,目的是防止乘客从马车中甩下去。1902年5月20日,美国 纽约举行汽车竞赛。参加竞赛的人中,有一位叫沃尔特·贝克的工程师,驾驶一辆鱼雷牌电动汽车,车 上除他外,还有一位技工。贝克在座位上钉上了一根带子套在身上以防不测,竞赛开始后,正在高速飞 驰的“鱼雷”碰到一根露出路面的钢轨,腾空而起,然后闯入人群,当场压死2人,伤数十人,可贝克 和那位技工却安然无恙。当时报纸报道了车辆带来惨重伤亡,却没有注意车上人是怎样幸免遇难的。
安全带的功能原理与分类
❖ 安全带的功能
安全带主要有两个方面的功能: ❖ 1、在车辆发生安全事故时,将因惯性前冲的乘客拦截下来,并将乘客受力的时间延长,
从而分散瞬间的受力。 ❖ 2、将乘客束缚在一定的空间里,有效的减少乘客与室内其他可能对其造成伤害的部件的
可能性,主要有仪表板、方向盘、前风挡玻璃,还包括座椅边缘。
紧急锁止式安全带(ELR)
简易式安全带
* 简易式安全带没有自动锁止功能,可允许织带自由拉出,扣上带扣时乘客必须
安全带固定点法规符合性校核

500; • D点的确定:DR=315mm+1.8S,但当S≤200 mm时,DR=675 mm
; • B点的确定:BR=260mm+S。但当S≥280 mm时,制造商可选用BR
=260mm+0.8S; • 躯干基准线的确定:对M1与N1类车辆,使与RC线成25º的一条直线
• 2.正确佩戴时安全带应无滑脱的危险; • 3.织带与车辆或座椅构架上凸出零件接触应无损伤织带的
危险; • 4.对于可改变位置的固定点(该固定点既便于乘员进人车
辆,且能约束乘员),本标准中的规定应适用于处于有效 约束位置时的固定点。
安全带固定点的最低数量
• 1.所有前向和后向座椅处的安全带固定点最低数量应符合下表的规定;
安全带固定点法规符合性校核
安全带总成的定义
• 具有织带、带扣、调节件以及将其固定在车内的附件,用于在车辆骤 然减速或撞车时通过限制佩戴者身体的运动以减轻其伤害程度的总成 ,该总成一般称为安全带总成,它包括吸能或卷收织带的装置。
目的 对安全带固定点进行法规符合性分析,确保设计满足企
业、行业、国家法规要求。
长120mm的线段;
•
XJ1:从X点沿垂直于RZ和ZX确定的平面的直线,向前截取长
60mm的线段。
•
J2点与J1点相对于过躯干线的纵向铅垂平面对称,该躯干线为安
放在座椅上的人体模型的躯干线。当用双开门为前后座椅提供通道,
且上定点在B柱上时,固定点系统应不妨碍乘员上下车;
安全带固定点的位置
3.2 安全带上有效固定点应位于垂直于座椅纵向中心面并与躯干线成 65°角的FN平面下方。对于后排座椅,此夹角可减小至60°。FN 平面与躯干线相交于D点,此时须保证DR=315mm+1.8S,但当 S≤200 mm时,DR=675 mm; 3.3 安全带上有效固定点应在垂直于座椅纵向中心面并与躯干线成 120°角且相交于B点的FK平面后方,此时须保证BR=260mm+S。 但当S≥280 mm时,制造商可选用BR=260mm+0.8S; 3.4 S值不得小于140 mm; 3.5 安全带上有效固定点应位于通过R点并垂直于车辆纵向中心平面 的铅垂平面之后; 3.6 安全带上有效固定点应在通过C点的水平面上方。
王云-座椅舒适性校核2015.10.21

(°)
脚角
(°)
表1 驾驶员坐姿推荐值
第4页/共44页
舒适参考范围 250~405 20~30 95~115 100~145 87~110
五、校核步骤
前排乘客舒适坐姿推荐值,见表2:
符号
尺寸名称
舒适参考范围
H31 R点到踵点的垂直距离 (mm)
127~405
A41 靠背角
(°)
20~75
A43 躯干与大腿夹角
L53-2 R点到踵点的水平距离 (mm)
A40-2 靠背角
(°)
A42-2 躯干与大腿夹角
(°)
A57-2 大腿与水平面夹角 (°)
A44-2 膝角
(°)
L46-2 脚角
5.2 软件分析校核步骤
表3后排乘客(舒°适)坐姿推荐值
舒适参考范围 127~405 —— 20~75 90~115 —— 90~145 95~130
5.3.3 后排乘员布置 依据硬点报告中相关硬点,按5.3.1方法操作,其中人体类型选择“乘员”,后排脚底面 与地毯成0度,测量所做假人坐姿角度是否满足表3要求。 注:SAE人体皆按5.3.1中步骤进行建立。 5.3.4 国标5%女性乘员布置 5.3.3.1中国国标5%假人与SAE假人人体坐姿的不同之处为在UG软件中“人体模型尺寸” 选择“自定义”,然后按照GBT 15759-1995进行尺寸的输入,输入R点位GB 5%女性人 体R点坐标值,如图7所示:
5.1 输入数据
数模:油门踏板(1108分组),地毯数模(5109分组)
硬点及参数:各排座椅R点、靠背角、踵点AHP、踏板角PRP(或踏板点)、方向盘中
心点、方向盘最大外径、方向盘倾角。
5.2 标准要求
QJM J01077-2018 安全带有效固定点法规校核规范

Q/JM J01077-2018安全带有效固定点法规校核规范1 目的和范围本规范规定了本公司车辆安全带有效固定点法规校核的一般要求。
本规范适用于本公司所有研发车辆的安全带有效固定点设计及校核。
2 引用文件下列文件对于本文件的应用是必不可少的。
凡是注日期的引用文件,仅注日期的版本适用于本文件。
凡是不注日期的引用文件,其最新版本(包括所有的修改单)适用于本文件。
GB 14167-2013 汽车安全带安装固定点、ISOFIX固定点系统及上拉带固定点EEC-R 14 关于机动车安全带安装固定点认证的统一规定76/115/EEC 机动车辆安全带固定点3 技术要求3.1 M1类车辆的前排座椅。
M1类车辆的a1(非带扣侧)应在30°~80°范围内,a2(带扣侧)应在45°~80°范围内。
前排座椅所有可正常移动的位置,角度要求同上。
在所有正常乘坐位置,a1和a2中至少有一个是恒定值时(如固定点在座椅上),其值应为60°±10°。
3.2 M1类车辆后排座椅。
对M1类车辆,所有后排座椅的a1和a2应在30°~80°范围内;如果后排座椅是可调的,则在所有正常移动位置,上述要求均有效。
3.3分别通过同一安全带的两个下固定点L1、L2且平行于车辆纵向中心平面的两个垂直平面间的距离不得小于350mm。
对M1和N1类车辆的后排中央乘坐位置,若相对其他乘坐位置是不可移位的,则上述距离不可小于240mm。
座椅的纵向中心平面应在L1和L2点之间,且距离至少为120mm。
3.4安全带上有效固定点应在垂直于座椅纵向中心面并与躯干线成65°角的FN平面下方。
对于后排座椅,此夹角可减小至60°。
FN平面与躯干线相较于D点,此时须保证DR=315mm+1.8S,但当S≤200mm 时,DR=675mm。
见图1。
3.5 安全带上有效固定点应该在垂直于座椅纵向中心面并与躯干线成120°角且相交于B点的FK平面后方,此时须保证BR=260mm+S。
汽车前排三点式安全带布置及校核方法的研究
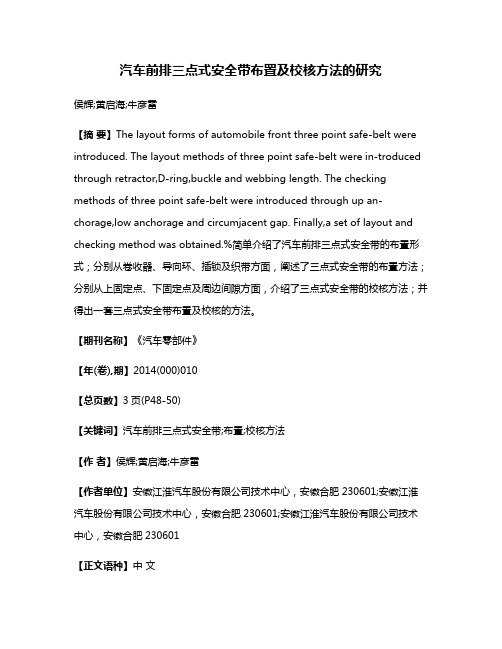
汽车前排三点式安全带布置及校核方法的研究侯辉;黄启海;牛彦雷【摘要】The layout forms of automobile front three point safe-belt were introduced. The layout methods of three point safe-belt were in-troduced through retractor,D-ring,buckle and webbing length. The checking methods of three point safe-belt were introduced through up an-chorage,low anchorage and circumjacent gap. Finally,a set of layout and checking method was obtained.%简单介绍了汽车前排三点式安全带的布置形式;分别从卷收器、导向环、插锁及织带方面,阐述了三点式安全带的布置方法;分别从上固定点、下固定点及周边间隙方面,介绍了三点式安全带的校核方法;并得出一套三点式安全带布置及校核的方法。
【期刊名称】《汽车零部件》【年(卷),期】2014(000)010【总页数】3页(P48-50)【关键词】汽车前排三点式安全带;布置;校核方法【作者】侯辉;黄启海;牛彦雷【作者单位】安徽江淮汽车股份有限公司技术中心,安徽合肥230601;安徽江淮汽车股份有限公司技术中心,安徽合肥230601;安徽江淮汽车股份有限公司技术中心,安徽合肥230601【正文语种】中文0 引言汽车安全带是一种安全装置,它能在汽车发生碰撞或急拐弯时,约束乘员尽可能保持原有的位置而不移动和转动,避免乘员与车内坚硬部件发生碰撞而造成伤害,因此安全带成为汽车设计开发中必不可少的被动安全配置。
安全带的布置及校核除必须满足国家强制法规外,还需考虑安全带的装配要求及性能要求,确保安全带与车身钣金及座椅结构匹配,并给乘员提供必要的保护及驾乘舒适性。
汽车安全带布置及设计方法

汽车安全带布置及设计方法摘要:安全带作为汽车安全装置的重要组成部分,是一种在汽车碰撞事故中保证乘员不受伤害的装置,其性能的优劣直接关系到乘员的安全。
汽车安全带设计的原则是,在汽车碰撞事故中,最大限度地保护乘员不受伤害。
但是由于人体结构的特殊性,即使是最先进的安全带,也无法达到完全保护乘员的目的。
因此,为了保证乘员在事故中不受伤害,就需要合理设计安全带,使其能有效地吸收碰撞能量、减小撞击力对人体的伤害程度。
关键词:汽车安全带;布置;设计方法1安全带系统的组成(1)一般汽车安全带都由肩带、腰带、系带及搭扣四部分组成。
其基本功能是通过安全带骨架把人固定在座椅上,使人与车形成一个整体,从而避免发生碰撞时乘员被甩出车外;同时,由于安全带骨架的弹性变形,使乘员的身体始终与座椅靠背紧密接触,从而有效地减少了乘员在事故中的伤亡。
(2)搭扣与搭扣控制机构:搭扣和搭扣控制机构是汽车安全带的重要组成部分,其作用是当汽车发生碰撞时,通过控制装置将安全带从座椅上抽出,以防止安全带缠绕在人体上。
(3)搭扣:搭扣一般安装在人体胸部靠前的位置,其作用是与肩部搭扣相配合,形成一个整体结构,同时使搭扣不直接接触人体皮肤。
(4)安全带调节器:用于调节和固定安全带长度及松紧度。
其作用是在汽车碰撞时及时切断安全带与人体接触的电源,从而达到保护乘员安全的目的。
2安全带的位置布置2.1座椅靠背与后悬置座椅靠背与后悬置安装距离一般有两种,一种是座椅靠背与后悬置之间安装距离为100 mm,另一种是座椅靠背与后悬置之间安装距离为200 mm。
对于第二种情况,座椅靠背与后悬置的安装位置相对于第一种情况更为靠近,因此需要考虑的因素也更多。
在设计过程中,应注意座椅靠背与后悬置之间的安装位置,首先要考虑到的是座椅靠背的刚度。
根据相关标准,当座椅靠背与后悬置之间的安装距离为100 mm~200 mm时,要保证其刚度大于600 kN/m;当座椅靠背与后悬置之间的安装距离为200 mm~300 mm时,要保证其刚度大于700 kN/m;当座椅靠背与后悬置之间的安装距离为300 mm~500 mm时,要保证其刚度大于800 kN/m。
汽车人机校核(总布置)

多学科交叉
在此添加您的文本16字
结合心理学、人机工程学、设计美学等多个学科的理论和 方法,提高人机校核的全面性和准确性。
在此添加您的文本16字
虚拟现实与仿真技术
在此添加您的文本16字
利用虚拟现实和仿真技术,构建更加真实、全面的模拟环 境,以便更准确地预测和评估人机交互的效果。
THANK YOU
汽车人机校核(总布置)
目
CONTENCT
录
• 人机校核概述 • 人体模型介绍 • 驾驶员人机校核 • 乘员人机校核 • 行人保护人机校核 • 总结与展望
01
人机校核概述
人机校核的定义和目的
定义
人机校核是对汽车内部空间、驾驶员和乘客的操作界面以及车辆 外部环境进行评估的过程,以确保驾驶员和乘客在使用过程中的 舒适性和安全性。
02
人体模型介绍
人体模型的选择
静态人体模型
用于评估汽车内部空间和座椅设计的合理性,确保 乘客的舒适性和安全性。
动态人体模型
用于模拟汽车行驶过程中乘客的姿态和行为,预测 可能出现的碰撞和伤害风险。
人体模型比例
选择与实际人体比例相符合的人体模型,以便更准 确地模拟乘客在汽车内的行为和姿态。
人体模型的参数
案例二
某轿车车型的人机校核。针对不同体型乘员进行校核,发现某一体型乘员在车内坐姿不舒适,经过调整座椅设计, 提高了该体型乘员的舒适性。
05
行人保护人机校核
行人保护人机校核的内容
头部碰撞区域校核
校核发动机罩、前挡风玻璃、前保险杠等部 位是否会对行人的头部造成严重伤害。
脚部碰撞区域校核
校核前保险杠、前格栅等部位是否会对行人 的脚部造成严重伤害。
安全带检验方法
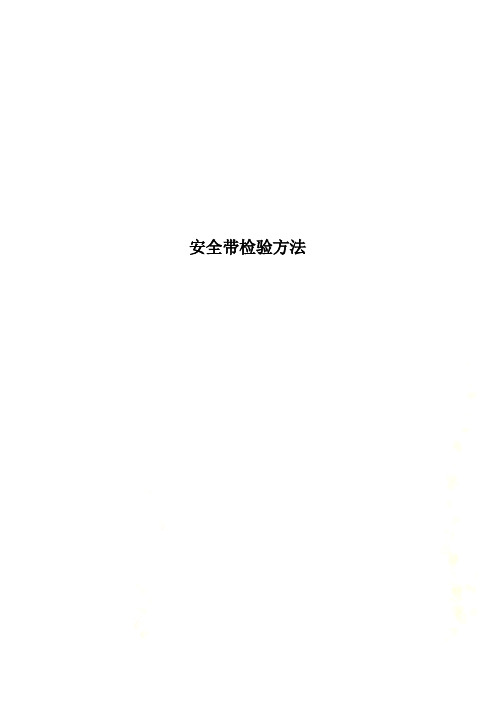
安全带检验方法安全带检验方法(GB 6095—2009 中华人民共和国国家质量监督检验检疫总局中国国家标准化管理委员会2009年4月13日发布2009年12月1日实施)前言本标准5.1.1.4~5.1.1.8、5.1.2.3~5.1.2.7、5.1.3.2~5.1.3.17、5.2.5.3和第7章为强制条款,其余为推荐性条款。
本标准代替GB 6095—1985《安全带》。
本标准与GB 6095—1985相比主要变化如下:——增加、修改了围杆作业安生带、区域限制安全带、坠落悬挂安全带等术语和定义;——增加了区域限制安全带的内容;——增加了材料、外观、结构等技术要求;——增加了阻燃、抗腐蚀、适合特殊环境等特殊技术性能要求;——修改丁安全绳、自锁器、缓冲器等术语和定义;——修改了安全带的分类;——删除了材料、使用保管、运输和储存章节;——增加了附录A;——增加了附录B;——增加了附录C。
本标准附录A、附录B为资料性附录,附录C为规范性附录。
本标准由国家安全生产监督管理总局提出。
本标准由全国个体防护装备标准化技术委员会(SAC/TC 112)归口。
本标准负责起草单位:北京市劳动保护科学研究所。
本标准参加起草单位:斯博瑞安(中国)安全防护设备有限公司、泰州市华泰劳保用品有限公司、乐清市华东安全器材厂、江苏曼杰克有限公司。
本标准主要起草人:杨文芬、肖义庆、臧兰兰、陆冰、陈倬为、邓宝举、章康明、王俊本。
本标准所代替标准的历次版本发布情况为:——GB 6095—1985。
1 范围本标准规定了安全带的分类和标记、技术要求、检验规则及标识。
本标准适用于高处作业、攀登及悬吊作业中使用的安全带。
本标准适用于体重及负重之和不大于100kg的使用者。
本标准不适用于体育运动、消防等用途的安全带。
2 规范性引用文件下列文件中的条款通过本标准的引用而成为本标准的条款。
凡是注日期的引用文件,其随后所有的修改单(不包括勘误的内容)或修订版均不适用于本标准,然而,鼓励根据本标准达成协议的各方研究是否可使用这些文件的最新版本。
安全带检测方法课件

安全带检测的意义
提高道路交通安全
落实法规要求 规范驾驶行为
安全带检测的方法分类
基于图像视觉的检测方法
通过相机拍摄车内图像,利用图像处 理技术识别乘坐人员是否系好安全带。
通过调节器的调安全性。
通过固定件的固定,将织带固定 在车辆座椅或结构上,以提供可
靠的支撑。
外观检测法
直接观察法 显微镜观察法
力学性能检测法
拉伸试验 压缩试验
电磁检测法
磁粉探 伤
涡流探伤
利用电磁感应原理,检测安全带内部 的缺陷和损伤。
超声波检测法
准确性和可靠性 法律法规的完善 用户接受度
基于传感器的检测方法
基于人工智能的检测方法
利用机器学习算法对车辆行驶数据进 行挖掘和分析,预测乘坐人员是否系 好安全带。
在座椅下方安装传感器,检测乘坐人 员是否系好安全带。
安全带检测的应用场景
车辆出库前检测
高速公路收费站检测
车载设备检测
安全带的结构组成
织带
扣环
由高强度人造纤维制成, 是安全带的主要承载部件。
汽车安全带检测案例
01
02
03
汽车安全带概述
安全带检测技术
安全带检测标准
飞机安全带检测案例
飞机安全带概述
安全带检测技术
安全带检测标准
工程机械安全带检测案例
工程机械安全带概述
01
安全带检测技术
02
安全带检测标准
03
安全带检测技术的发展趋势
01
安全带、安全网检查试验制度(二篇)

安全带、安全网检查试验制度安全带和安全网是保障人员在高空作业和高速交通工具中的安全的重要设备。
为了确保安全带和安全网的质量和可靠性,制定安全带和安全网检查试验制度是必不可少的。
本文将以____字的篇幅,分别介绍安全带和安全网的检查试验制度。
一、安全带检查试验制度一、背景和必要性安全带是一种用于固定和保护人身安全的装备,广泛应用于高空作业、登山攀岩、工业生产等领域。
为了确保安全带的质量和使用效果,制定安全带检查试验制度是必不可少的。
二、检查试验内容和要求1.外观检查:检查安全带外观是否完好、无明显磨损和破损。
2.材料检查:检查安全带的材料是否符合相关标准,如强度、耐磨性等。
3.结构检查:检查安全带的结构是否合理、牢固,起扣件是否完好。
4.使用寿命检查:依据相关标准,进行安全带的使用寿命检查,判断是否需要更换。
5.性能试验:包括断裂试验、抗拉试验等,检查安全带的承载能力和防护效果。
三、检查试验的方法和步骤1.领取安全带样品,并进行外观检查,记录各项指标。
2.对安全带进行材料检查,使用相应的仪器测试材料的强度、耐磨性等。
3.对安全带的结构进行检查,包括检查起扣件的牢固性和安全带的结构的合理性。
4.根据相关标准或制定的检测方法,进行安全带的使用寿命检查。
5.进行性能试验,包括断裂试验、抗拉试验等,检查安全带的承载能力和防护效果。
6.根据检验结果,制定后续的处理措施,如更换损坏的安全带等。
四、检查试验后的结果处理1.根据检验结果,对安全带的质量进行评估,判断是否符合相关标准和要求。
2.将检验结果记录在检查记录表中,并保存相关资料。
3.对不合格的安全带进行处理,如更换、修理或报废。
4.对合格的安全带进行标识,例如粘贴合格标签等。
五、安全带检查试验制度的实施1.制定安全带检查试验制度的文件,明确检验的目的、内容和要求。
2.确定检验的频率,如每季度、每半年或每年进行一次检验。
3.确定检验的责任人和检验机构,确保检验的独立性和客观性。
- 1、下载文档前请自行甄别文档内容的完整性,平台不提供额外的编辑、内容补充、找答案等附加服务。
- 2、"仅部分预览"的文档,不可在线预览部分如存在完整性等问题,可反馈申请退款(可完整预览的文档不适用该条件!)。
- 3、如文档侵犯您的权益,请联系客服反馈,我们会尽快为您处理(人工客服工作时间:9:00-18:30)。
3. 安全带布置设计要求Biblioteka 3.1 安全带下有效固定点位置
3.1.1 M1类车辆的前排座椅
M1类车辆的α1(非带扣侧)应在30°-80°范围内,α2(带扣侧)应在45°-80 范围内。前排座椅所有可正常移动的位置,角度要求同上。在所有正常乘坐位 置,α1和α2中至少有一个是恒定值时(如固定点在座椅上),其值应为60±10° 。对于带有调节机构的可调座椅,当靠背角小于20°时,α1可以低于以上规定 的最小值(30°),但在任何正常使用位置均不得小于20°,参见图1、2。
图1 安全带下侧固定点(非带扣侧) 1.2 安全带下侧固定点(带扣侧,带扣固定于座椅上)
图2 安全带下侧固定点(带扣侧)
2.3 后排中间座椅安全带两固定点距离车辆纵向对称平面不得小于120mm且分列于 车辆纵向对称平面两侧,两者之间的距离不得小于350mm,如图3。
图3 后排中央座椅位置校核 1.4 前排安全带上有效固定点位置
安全带位置校核设计指南
一、 目的
为统一各车型安全带布置校核程序及输出结果,特制定本规范。
二、 适用范围
适用于乘用车研究院内各车型安全带位置的校核。
三、 规范内容
1. 规范引用标准
汽车安全带安装固定点报批稿
2. 相关定义
2.1 L1和L2点:同一安全带的两个下部有效固定点位置。
2.2
1和 2:分别为通过R点、L1点和R点、L2点,且垂直于车辆纵向中心
R-II长轴距安全带位置校核 1. R-II安全带固定点位置校核 1.1 安全带下侧固定点(非带扣侧)
R-II安全带下侧固定点(非带扣侧)均在车身上,且前排和中排座椅可调、第 三排座椅固定,因此对R-II而言,前排及中排座椅在所有正常移动位置时及第三 排座椅,α1应在30°-80°范围内,法规允许的安全带下侧固定点区域(非带扣侧) 如图1所示:
图3 安全带上有效固定点范围(俯视图) 4. 校核步骤 4.1前排座椅下固定点校核:按照3.1.1和3.1.3条中的要求作出法规允许的安全带 固定点区域,检查安全带实际固定点是否在允许的区域内以判断安全带固定点是 否满足要求。 4.2后排座椅下固定点校核:按照3.1.2和3.1.4条中的要求作出法规允许的安全带 固定点区域,检查安全带实际固定点是否在允许的区域内以判断安全带固定点是 否满足要求。 4.3后排中央座椅的下固定点校核:按照3.1.5条中的要求进行校核,判断是否满 足法规要求。
面的平面与水平面之间的夹角,如图1所示。
2.3 P平面的位置规定如下:
2.3.1 如果乘坐位置是由座椅形状确定的,P平面即为座椅的中心平面;
2.3.2 在不能确定乘坐位置的情况下:
2.3.2.1 对于驾驶员座椅,P平面为通过的方向盘中心且平行于汽车纵向中心面的 铅垂平面(可调式方向盘应位于正中位置)。
图4 前排安全带上固定点
图6 后排安全带上固定点 2.结论 由于CAS数据中缺少安全带固定点的具体位置,本文档给出了其布置的大致范围。
3.1.2 M1类车辆后排座椅
对M1类车辆,所有后排座椅的α1和α2应在30°-80°范围内;如果后排座椅是可调 的,则在所有正常移动位置,上述要求均有效。
3.1.3 M1类以外车辆的前排座椅
对M1类以外车辆的前排座椅的所有正常移动位置,α1和α2应在30°-80°之 间;对于最大总质量不超过3500kg车辆的前排座椅的所有正常使用位置,α1和α 2中至少有一个是恒定值时(如固定点在座椅上),其值应为60±10°。 3.1.4 M1类以外车辆后排座椅和特殊前排或后排座椅
2.3.2.2 对于前排外侧乘员座椅,P平面应为与驾驶员座椅的P平面相对称平面。
2.3.2.3 对于后排外侧乘员位置的P平面,应为车辆纵向平面的距离为A的平面, 由制造商按下述条件确定: 若长条座椅仅用于乘坐两人时,A>200mm; 若长条座椅乘坐超过两人时,A>300mm。 2.4 S为安全带上有效固定点至平行于车辆纵向中心平面的基准平面P的距 离,单位为mm。
4.4 按照3.2.2、3.2.3、3.2.5以及3.2.6条的要求作出相应的四个平面,检查安 全带实际的上有效固定点是否在允许的范围内以判断安全带固定点是否满足法规 要求。若安全带有附加固定点,则按照3.2.1和3.2.7条中的要求进行校核并判断 是否满足法规要求。 5. 结论
针对4.1至4.4项的校核结果,判断车辆安全带的上下实际固定点是否满足法 规要求。 附件1:安全带固定位置校核实例
3.2.2 安全带上有效固定点应位于垂直于座椅纵向中心面并与躯干线成65°角 的FN平面下方。对于后排座椅,此夹角可减小至60°。FN平面与躯干线相交于D 点,此时须保证DR=315mm+1.8S,但当S≤200mm时,DR=675mm。 3.2.3 安全带上有效固定点应在垂直于座椅纵向中心面并与躯干线成120°角 且相交于B点的FK平面后方,此时须保证BR=260mm+S。但当S≥280mm时,制造商可 选用BR=260mm+0.8S。 3.2.4 S值不得小于140mm。 3.2.5 安全带上有效固定点应位于通过R点并垂直于车辆纵向中心平面的铅垂 平面之后,如图1所示。 3.2.6 安全带上有效固定点应在通过2.5条规定的C点的水平面上方。 3.2.7 除3.2.1条规定的上有效固定点外,若满足下述条件之一,可以装备另 外的附加上有效固定点: 3.2.7.1 附加固定点应符合3.2.1至3.2.6的要求。 3.2.7.2 无需借助工具应能使用附加固定点。该固定点应符合3.2.5和3.2.6的 要求,并处于图1所示沿铅垂方向上下各80mm所确定的区域内。 3.2.7.3 符合3.2.6规定要求的全背带式安全带的固定点应位于通过躯干线的横 向平面之后,并处于下述位置: 3.2.7.3.1 对于单固定点,位于通过3.2.1规定的J1和J2点的两个铅垂面夹角内, 其水平截面见图3。 3.2.7.3.2 对于两个固定点, 固定点可位于上述二点之一的夹角内,同时其中一 固定点是另一个固定点相对于2.3中规定的座椅的P平面的对称点,且二者间的距 离不大于50mm。
图1 安全带有效固定点范围(侧视图)
图2 安全带有效固定点范围(俯视图) 3.2 安全带上有效固定点位置 3.2.1 如果因采用织带导向件或类似装置而影响安全带上有效固定点位置 时,应根据织带纵向中心线通过J1点时固定点的位置的情况来确定有效固定点位 置。从R点开始,用下述三条线段确定J1点: RZ: 从R点向上沿躯干线截取长530mm的线段; ZX: 从Z点沿垂直于汽车纵向中心面的直线,向固定点方向截取长120mm的线 段; X J1:从X点沿垂直于RZ和ZX确定的平面的直线,向前截取长60mm的线段。 J2点与J1点相对于过人体模型躯干线的纵向铅垂平面对称,当用双开门为前后座 椅提供通道,且上固定点在B柱上时,固定点系统应不妨碍乘员上下车。
其中前排安全带上固定点与前排座椅(单侧)中心线的Y向距离按原Refine 安全带的位置选取,S=267mm,大于标准要求的140mm。按照3.2.2、3.2.3、3.2.5 及3.2.6条的规定作出相应的四个平面,如图6中红色阴影区域所示。由于R-II前 排座椅安全带配备有高度调节器,属于附加固定点,因此按照3.2.7条的要求作出 附加固定点法规要求区域,如图4中蓝色阴影区域所示。