各种热处理工艺代号及技术条件的标注方法
铸钢件的热处理方式
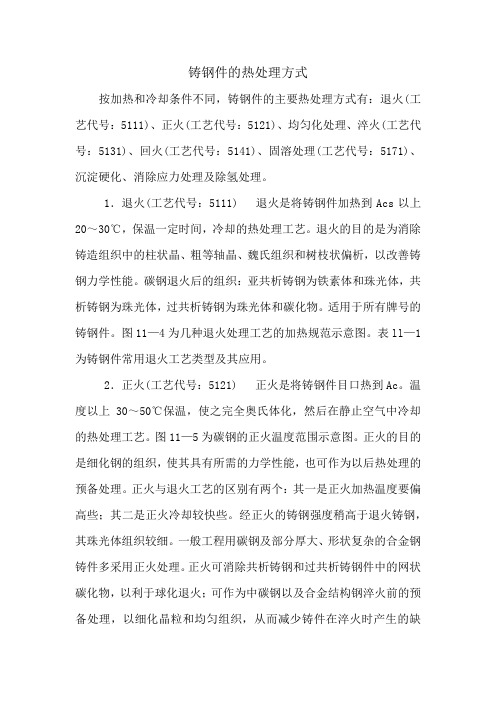
铸钢件的热处理方式按加热和冷却条件不同,铸钢件的主要热处理方式有:退火(工艺代号:5111)、正火(工艺代号:5121)、均匀化处理、淬火(工艺代号:5131)、回火(工艺代号:5141)、固溶处理(工艺代号:5171)、沉淀硬化、消除应力处理及除氢处理。
1.退火(工艺代号:5111) 退火是将铸钢件加热到Acs以上20~30℃,保温一定时间,冷却的热处理工艺。
退火的目的是为消除铸造组织中的柱状晶、粗等轴晶、魏氏组织和树枝状偏析,以改善铸钢力学性能。
碳钢退火后的组织:亚共析铸钢为铁素体和珠光体,共析铸钢为珠光体,过共析铸钢为珠光体和碳化物。
适用于所有牌号的铸钢件。
图11—4为几种退火处理工艺的加热规范示意图。
表ll—1为铸钢件常用退火工艺类型及其应用。
2.正火(工艺代号:5121) 正火是将铸钢件目口热到Ac。
温度以上30~50℃保温,使之完全奥氏体化,然后在静止空气中冷却的热处理工艺。
图11—5为碳钢的正火温度范围示意图。
正火的目的是细化钢的组织,使其具有所需的力学性能,也可作为以后热处理的预备处理。
正火与退火工艺的区别有两个:其一是正火加热温度要偏高些;其二是正火冷却较快些。
经正火的铸钢强度稍高于退火铸钢,其珠光体组织较细。
一般工程用碳钢及部分厚大、形状复杂的合金钢铸件多采用正火处理。
正火可消除共析铸钢和过共析铸钢件中的网状碳化物,以利于球化退火;可作为中碳钢以及合金结构钢淬火前的预备处理,以细化晶粒和均匀组织,从而减少铸件在淬火时产生的缺陷。
3.淬火(工艺代号:5131) 淬火是将铸钢件加热到奥氏体化后(Ac。
或Ac•以上),保持一定时间后以适当方式冷却,获得马氏体或贝氏体组织的热处理工艺。
常见的有水冷淬火、油冷淬火和空冷淬火等。
铸钢件淬火后应及时进行回火处理,以消除淬火应力及获得所需综合力学性能。
图11—6为淬火回火工艺示意图。
铸钢件淬火工艺的主要参数:(1)淬火温度:淬火温度取决于铸钢的化学成分和相应的临界温度点。
金属热处理工艺的分类及代号

金属热处理工艺的分类及代号金属热处理工艺的分类及代号(GB/T12693-90)1.分类:热处理分类由基础分类和附加分类组成.(1)基础分类根据工艺类型、工艺名称和实践工艺的加热方法,将热处理工艺按三个层次进行分类,见附录表1-1.(2)附加分类对基础分类中某些工艺的具体条件的进一步分类.包括退火、正火、淬火、化学热处理工艺加热介质(附录表1-2);退火冷却工艺方法(附录1-3);淬火冷却介质或冷却方法(附录表(1-4);渗碳和碳氮共渗的后续冷却工艺(附录表1-5),以及化学热处理中非金属、渗金属、多元共渗、熔渗四种工艺按元素的分类.2.代号(1)热处理工艺代号标记规定如下:5热处理 X工艺类型 X工艺名称 X 加热方法附加分类工艺代号(2)基础工艺代号用四位数字表示.第一位数字“5”为机械制造工艺分类与代号中表示热处理的工艺代号;第二,三,四位数字分别代表基础分类中的第二,三,四层次中的分类代号。
当工艺中某个层次不需分类时,该层次用0代号。
(3)附加工艺代号它用英文字母代表。
接在基础分类工艺代号后面。
具体代号见附录表1-2至附录表1-5。
(4)多工序热处理工艺代号多工序热处理工艺代号用破折号将各工艺代号连接组成,但除第一工艺外,后面的工艺均省略第一位数字“5”,如5151-331G表示调质和气体渗碳。
(5)常用热处理工艺代号见附录表1-6。
附录表1-1.热处理工艺分类及代号工艺总称代号工艺类型代号工艺名称代号加热方法代号热处理 5 整热处理体1退火 1加热炉 1正火 2淬火 3感应 2正火和淬火 4调质 5火焰 3稳定化处理 6固溶处理,水韧处理7固溶处理和时效8表面热处理2表面淬火和回火 1电阻 4物理气相沉淀 2化学气相沉淀 3激光 5等离子体化学气相沉淀 4化学热处理3渗碳 1 电子束6碳氮共渗 2渗氮 3 等离子体7氮碳共渗 4渗其他非金属 5其他8渗金属 6多元共渗7溶渗8附录表1-2.加热介质及代号加热介质固体液体气体真空保护气氛可控气氛流态床代号S L G V P C F附录表1-3退火工艺代号退火工艺去应力扩散再结晶石墨化去氢退火球化退火等温退火代号o d r g h s n附录表1-4淬火冷却介质和冷却方法及代号冷却介质和方法空气油水盐水有机水溶液盐浴压力淬火双液淬火分级淬火等温淬火形变淬火冷处理代号a o wb y s p d m n f z附录表1-5渗碳,碳氮共渗后冷却方法及代号冷却方法直接淬火一次加热淬火二次加热火表面淬火代号g r t b附录表1-6常用热处理工艺及代号工艺代号工艺代号热处理 5000 石墨化退火5111g感应加热热处理 5002 去氢退火5111h火焰热处理 5003 球化退火5111s激光热处理 5005 等温退火5121电子束热处理 5006 正火5121离子热处理 5007 淬火5131真空热处理 5000V 空冷淬火5131a保护气氛热处理 5000P 油冷淬火5131o可控气氛热处理 5000C 水冷淬火5131w流态床热处理 5000F 盐水淬火5131b有机水溶液淬火5131y整体热处理 5100 盐浴淬火5131s退火 5111 压力淬火5131p去应力退火 5111o 双价质淬火5231d扩散退火 5111d 分级淬火5131m再结晶退火 5111r 等温淬火5131n变形淬火 5131f 表面淬火和回火 521淬火及冷处理 5131z 感应淬火和回火5212感应加热淬火 5132 火焰淬火和回火 5213真空加热淬火 5131V 电接触淬火和回火 5214保护气氛加热淬火 51312P 激光淬火和回火 5215可控气氛加热淬火 5131C 电子束淬火和回火 5216流态床加热淬火 5131F 物理气相沉积5228盐浴加热分级淬火 5131L 化学气相沉积5238盐浴加热分级淬火 5131mL 等离子体化学气相沉积5248盐浴加热盐浴分级淬火513Ls+m淬火和回火 514 化学热处理530调质 5151 渗碳521稳定化处理 5161 固体渗碳5311S固溶处理,水韧处理5171 液体渗碳5311L固溶处理和时效 5181 气体渗碳5311G表面热处理5200。
热处理标准

热处理相关标准汇总一、热处理基础GB/T 7232—1999 金属热处理工艺术语GB/T 8121-1987 热处理工艺材料名语术语GB/T 12603—1990 金属热处理工艺分类及代号 GB/T 13324-1991 热处理设备术语JB/T 8555-1997 热处理技术要求在零件图样上的表示方法JB/T 9208—1999 可控气氛分类及代号二、工艺方法GB/T 16923-1997 钢件的正火与退火GB/T 16924—1997 钢件的淬火与回火GB/T 18177—2000 钢件的气体渗氮GB/T 18683—2002 钢铁件激光表面淬火JB/T 3999—1999 钢件的渗碳与碳氮共渗淬火回火JB/T 4155-1999 气体氮碳共渗JB/T 4202—1999 钢的锻造余热淬火回火处理JB/T 4215-1996 渗硼JB/T 4218-1994 硼砂熔盐渗金属JB/T 6048-1992 盐浴热处理JB/T 6956-1993 离子渗氮JB/T 7500—1994 低温化学热处理工艺方法选择通则JB/T 7529—1994 可锻铸铁热处理JB/T 7711-1995 灰铸铁件热处理JB/T 7712-1995 高温合金热处理JB/T 8418—1996 粉末渗金属JB/T 8929-1999 深层渗碳JB/T 9197-1999 不锈钢和耐热钢热处理JB/T 9198—1999 盐浴硫氮碳共渗JB/T 9200—1999 钢铁件的火焰淬火回火处理JB/T 9201-1999 钢铁件的感应淬火回火处理JB/T 9207-1999 钢件在吸热式气氛中的热处理JB/T 9210—1999 真空热处理三、质量检验及评定GB/T 224-1987 钢的脱碳层深度测定法GB/T 225—1988 钢的淬透性末端淬火试验方法GB/T 226—1991 钢的低倍组织及缺陷酸蚀检验法GB/T 227-1991 工具钢淬透性试验方法GB/T 1979—2001 结构钢低倍组织缺陷评级图GB/T 4335-1984 低碳钢冷轧薄板铁素体晶粒度测定法GB/T 4462-1984 高速工具钢大块碳化物评级图GB/T 5617—1985 钢的感应淬火或火焰淬火后有效硬化层深度的测定GB/T 6401-1986 铁素体奥氏体型双相不锈钢中α—相面积含量金相测定法GB/T 9450-1988 钢件渗碳淬火有效硬化层深度的测定和校核GB/T 9451—1988 钢件薄表面总硬化层深度或有效硬化层深度的测定。
企业技术标准的编号方法(企业标准)

企业技术标准的编号方法(企业标准)企业技术标准的编号方法本标准规定了企业技术标准编号的基本要求、代号的组成及编号管理等。
适用于企业技术标准的编号。
基本要求企业标准按一个标准一个代号的原则编号,不同的标准不得使用相同的代号,反之,相同的标准不得使用不同的代号。
各部门在编制企业技术标准时,也应当按照本编号系统进行编号。
企业技术标准代号的组成XXX的企业技术标准的代号由企业代号、顺序号和版次组成。
顺序号由四位阿拉伯数字组成,按依次递增顺序编定。
版次用英文字母的大写表示,以A、B、C……(除I、O外)的顺序编定。
表1企业技术标准和技术管理标准分组表本表列出了企业技术标准和技术管理标准的大类代号和小类,以及顺序号分段。
企业技术标准按类别对顺序号进行了分组。
大类代号包括标准化综合、产品图样和设计文件的基本要求、工艺文件的基本要求、检验、计量文件的基本要求、综合技术标准、信息及档案管理、编码标准、术语标准、法定计量单位和其他。
小类代号包括公差配合、形位公差、结构要素、表面粗糙度、螺纹、键、齿轮、制图、设计符号、代号、术语、标志、设计指导性标准、计算机辅助设计、环境、安全、卫生标准、产品包装、贮运、标识标准、通用工艺标准、机械加工、冷冲压、热工艺(热处理、铸、锻、焊接)、绝缘工艺、非金属件加工工艺、表面处理(涂装、电镀)、工艺环境、安全、卫生标准、定额和其他。
顺序号分段从0000到1999,按照不同的小类代号进行分组。
没有明显的格式错误或有问题的段落需要删除。
以下是对每段话的小幅度改写:II。
设计标准在设计过程中,需要考虑使用的材料。
这些材料包括电工合金、精密合金、其他金属、电线电缆、绝缘材料、石油制品、涂装材料、化工材料、橡胶、塑料、胶粘剂以及其他材料。
此外,还需要考虑使用的标准紧固件、外购件和零部件,以及零部件的包装和贮运。
III。
材料标准在使用材料时,需要遵守相关的材料标准。
这些标准包括电工合金、精密合金、其他金属、电线电缆、绝缘材料、石油制品、涂装材料、化工材料、橡胶、塑料、胶粘剂以及其他材料的标准。
钢的表面热处理

热处理工艺的应用
热处理技术条件是指对零件采用的热处理方法以及所应达到的
性能要求的技术性的文件。具体应根据零件性能要求,在零件 图样上标出,内容包括最终热处理方法(如调质、淬火、回火、 渗碳等)以及应达到的力学性能判据等,作为热处理生产及检 验时的依据。力学性能通常只标出硬度值,且有一定误差范围, 如弹簧淬火回火硬度45~50HRC。
表4-7 加热方式及代号
加热 方式
可控气 氛(气
体)Leabharlann 真 空盐浴 (液 体)
感 应
火 激 电子 等离 固体 液态 电接 焰 光 束 子体 装箱 床 触
代号
01
0 2
03
04 05 06 07 08 09 10 11
表4-8 退火工艺及代号
退火 工艺
代号
去应 力退
火
St
均匀 化退
火
H
再结 晶退
火
R
石墨 化退
• 不仅改变了钢表面的组织,而且表面层的化学成分也发生了 变化,因而能更有效地改变零件表层的性能。
• 根据渗入元素分类:渗碳、渗氮、碳氮共渗、渗硼、渗金属 等。
• 化学热处理的基本过程
分解
吸收
扩散
(1)钢的渗碳及其应用
• 渗碳——将钢件置于渗碳介质中加热并保温,使碳原子渗 入工件表层的化学热处理工艺。
热处理工艺分类及代号热处理工艺分类及代号工艺总称总称代号工艺类型类型代号工艺名称名称代号整体热处理表面热处理化学热处理表47加热方式及代号加热方式可控气固体装箱液态代号01030405060708091011表48退火工艺及代号退火工艺脱氢退火退火等温退火完全退火不完代号st表49淬火冷却介质和冷却方法及代号冷却介热处理工序位置安排11预先热处理工序位置退火正火调质预先热处理工序位置退火正火调质安排在毛坯生产之后切削加工之前或粗加工之后半精加安排在毛坯生产之后切削加工之前或粗加工之后半精加工之前
模具的抛光技术
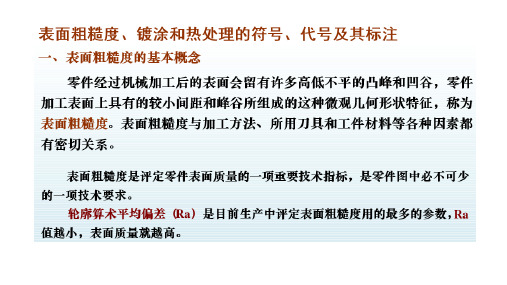
即使最佳的材质也会被毁掉的。 2.4 抛光前的表面状况: 对EDM钢材表面进行打磨要比其他进行传统的机器加工 及热处理的表面难些。因EDM(即电火花)加工易在工模表面形成薄薄的一层加硬层。这一层的硬度要比母体的硬度 高,必须除去表面更硬的一层,要比原母体材质更难于打磨。EDM后再作回火处理也可改善抛光性能。 3.0 典型 的抛光程序: 机器加工 铣削加工 车削加工 磨削加工 EDM加工 粗打磨 油石粒度号 粗 80# 120# 150# 180# 220# 320# 细 400# 精打磨 砂纸粒度号 粗 320# 400# 600# 800# 1000# 细 1200# 抛光 钻石膏粒度号 粗 45μm 25μm 15μm 10μm 6μm,3μm 细 1μm 3.1 通常情况下,工模在经过不同的机器加工后,应采用如下流程: ◆ 在铣削加 工后,粗打磨、精打磨、抛光; ◆ 在磨削加工后,粗打磨、精打磨、抛光; ◆ 在EDM电加工后,精打磨、抛 光; 3.2 打磨: 打磨是后面抛光作业成功的基础,通过打磨将机器加工时留下的刮痕去除掉,使表面更平整,打 磨时需留意: a.打磨过程中不应产生大量的热与压力,这些会影响到材料的结构及硬度,应有充足的冷却剂。 b.
可採用渗氮或渗碳的热处理方法增加钢材的表面硬度。 4.2 针孔: 一般ቤተ መጻሕፍቲ ባይዱ抛光过程中会产生的非常细小 的针孔,这是由于一层已在抛光时磨掉熔渣物造成的,该溶渣物以坚硬的氧化物形态存在。在这一过程中 常见的重要因素有: ◆抛光时间及压力; ◆钢材的纯度,尤其是有关的熔渣物; ◆抛光使用工具; ◆磨
料 为何会出现针孔原因之一是母体材质及熔渣硬度不同。在抛光过程中,磨去母体的速度高于磨去熔渣
铝及铝合金热处理工艺
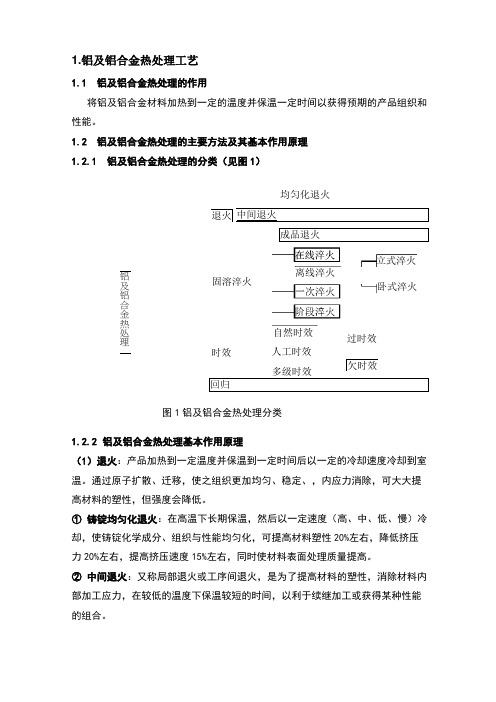
1.铝及铝合金热处理工艺1.1 铝及铝合金热处理的作用将铝及铝合金材料加热到一定的温度并保温一定时间以获得预期的产品组织和性能。
1.2 铝及铝合金热处理的主要方法及其基本作用原理 1.2.1 铝及铝合金热处理的分类(见图1)均匀化退火中间退火成品退火回归图1铝及铝合金热处理分类1.2.2 铝及铝合金热处理基本作用原理(1)退火:产品加热到一定温度并保温到一定时间后以一定的冷却速度冷却到室温。
通过原子扩散、迁移,使之组织更加均匀、稳定、,内应力消除,可大大提高材料的塑性,但强度会降低。
① 铸锭均匀化退火:在高温下长期保温,然后以一定速度(高、中、低、慢)冷却,使铸锭化学成分、组织与性能均匀化,可提高材料塑性20%左右,降低挤压力20%左右,提高挤压速度15%左右,同时使材料表面处理质量提高。
② 中间退火:又称局部退火或工序间退火,是为了提高材料的塑性,消除材料内部加工应力,在较低的温度下保温较短的时间,以利于续继加工或获得某种性能的组合。
退火 铝及铝合金热处理固溶淬火时效 人工时效 多级时效欠时效离线淬火卧式淬火立式淬火自然时效过时效③完全退火:又称成品退火,是在较高温度下,保温一定时间,以获得完全再结晶状态下的软化组织,具有最好的塑性和较低的强度。
(2)固溶淬火处理:将可热处理强化的铝合金材料加热到较高的温度并保持一定的时间,使材料中的第二相或其它可溶成分充分溶解到铝基体中,形成过饱和固溶体,然后以快冷的方法将这种过饱和固溶体保持到室温,它是一种不稳定的状态,因处于高能位状态,溶质原子随时有析出的可能。
但此时材料塑性较高,可进行冷加工或矫直工序。
①在线淬火:对于一些淬火敏感性不高的合金材料,可利用挤压时高温进行固溶,然后用空冷(T5)或用水雾冷却(T6)进行淬火以获得一定的组织和性能。
②离线淬火:对于一些淬火敏感性高的合金材料必须在专门的热处理炉中重新加热到较高的温度并保温一定时间,然后以不大于15秒的转移时间淬入水中或油中,以获得一定的组织和性能,根据设备不同可分为盐浴淬火、空气淬火、立式淬火、卧式淬火。
热处理工艺的应用

1.1 热处理零件的结构工艺性
零件的结构形状对热处理质量影响 较大。零件截面尺寸的变化,直接影响:
淬火后的淬透层深度 淬火应力在工件的分布 对变形产生很大影响 零件几何形状对淬火变 形与开裂的影响更为显 著。
1.1 热处理零件的结构工艺性
在进行热处理零件的结构设计时一 般应注意以下几点:
避免截面厚薄相差悬殊,合理安排 孔洞和键槽; 避免尖角和棱角; 尽量采用封闭、对称结构; 采用组合结构。
1.1 热处理零件的结构工艺性
列举 几种 常见 零件 不正 确的 结构 设计 及其 改进 结构
1.1 热处理零件的结构工艺性
如果改进零件的结构形状后仍难达到热处理 要求时,就应采取其他措施来防止和减少变形开裂 等热处理缺陷。例如:
➢合理安排工艺线路; ➢修改工件热处理技术条件; ➢根据热处理变形规律妥善安排冷 热加工配合,调整变形和公差; 预留一定加工余量; ➢更换材料和改进热处理操作工艺 方法等
1.2 零件的热处理技术条件
热处理技术条件的内容包括:
热处理的方法及热处理后应达到的力学性 能。 对于一般零件只标出硬度值,对重要零件 应标出强度、塑性、韧性指标或金相组织 要求, 对于化学热处理零件还应标注渗透层部位 和渗层的深度。
1.2 零件的热处理技术条件
处理工艺代号标记规定如下:
热处理工艺代号由基础分类工艺代号及附加 分类工艺代号组成。在基础分类中按照工艺类型、 工艺名称和实现工艺的加热方法三个层次进行分类, 均有相应代号对应,见下表。
1.3 热处理工序位置的确定
最终热处理工序位置的确定
最终热处理包括各种淬火+回火及化学热处理。 零件经这类热处理后硬度较高,除可以磨削加工外,一般 不宜进行其他切削加工,故其工序位置一般均安排在半精 加工之后、磨削加工(精加工)之前。在生产过程中,由 于零件选用毛坯和工艺过程不同,热处理工序会有所增减。 因此工序位置的安排必须根据具体情况灵活运用。例如要 求精度高的零件,在切削加工之后,为了消除加工引起的 残余应力,以减小零件变形,在粗加工后可安排去应力退 火。
机械制造基础第十四章机械零件材料的选用与加工工艺分析习题解答

第十四章零件选材与加工工艺分析习题解答14-1 选择材料的一般原则有哪些? 简述它们之间联系。
答:选择材料的一般原则有①材料的使用性能应满足零件的使用要求;②) 材料的工艺性应满足加工要求;③选材时,还应充分考虑经济性。
在选用材料时,必须了解我国的资源和生产情况,从实际情况出发,全面考虑材料的使用性能、工艺性能和经济性等方面的因素,以保证产品性能优良、成本低廉、经济效益最佳。
14-2 什么是零件的失效? 一般机械零件的失效方式有哪几种?答:所谓失效是指:①零件完全破坏,不能继续工作;②严重损伤,继续工作很不安全;③虽能安全工作,但已不能满意地起到预定的作用。
一般零件的失效方式有:断裂、表面损伤、磨损、疲劳破坏、过量变形等。
14-3 生产批量对毛坯加工方法的选择有何影响?答:毛坯选择要考虑加工成本,成本与生产批量有关系:①在单件小批量生产的条件下,应选用常用材料、通用设备和工具、低精度、低生产率的毛坯生产方法。
②在大批量生产的条件下,应选用专用材料、专用设备和工具以及高精度高生产率的毛坯生产方法。
这样,毛坯的生产率高、精度高。
虽然专用材料、专用工艺装备增加了费用,但材料的总消耗量和切削加工工时会大幅度降低,总的成本也较低。
③单件、小批生产时,对于铸件应优先选用灰铸铁和手工砂型铸造方法;对于锻件应优先选用碳素结构钢和自由锻方法;在生产急需时,应优先选用低碳钢和手工电弧焊方法制造焊接结构毛坯。
④在大批量生产中,对于铸件应采用机器造型的铸造方法,锻件应优先选用模型锻造方法,焊接件应优先选用低合金高强度结构钢材料和自动、半自动的埋弧焊、气体保护焊等方法制造毛坯。
14-4 毛坯的选择原则是什么? 它们之间的相互关系如何?答:毛坯的选择原则是:保证零件的使用要求;降低制造成本,满足经济性;考虑实际生产条件。
三条原则是相互联系的,考虑时应在保证使用要求的前提下,力求做到质量好、成本低和制造周期短。
14-5 热处理的技术条件包括哪些内容? 如何在零件图上标注?答:热处理技术条件的内容包括:零件最终的热处理方法、热处理后应达到的力学性能指标等。
金属热处理工艺的分类及代号

附录1 金属热处理工艺的分类及代号(GB/T12693-90)一、分类热处理分类由基础分类和附加分类组成。
1. 基础分类根据工艺类型、工艺名称和实现工艺的加热方法,将热处理工艺按三个层次进行分类,见附录表1-1。
2. 附加分类对基础分类中某些工艺的具体条件的进一步分类。
包括退火、正火、淬火、化学热处理工艺加热介质(附录表1-2); 退火工艺方法(附录表1-3); 淬火冷却介质或冷却方法(附录表1-4); 渗碳和碳氮共渗的后续冷却工艺(附录表1-5), 以及化学热处理中非金属、渗金属、多元共渗、熔渗四种工艺按渗入元素的分类。
二、代号1. 热处理工艺代号标记规定如下:2. 基础工艺代号用四位数字表示。
第一位数字“5”为机械制造工艺分类与代号中表示热处理的工艺代号; 第二、三、四位数字分别代表基础分类中的第二、三、四层次中的分类代号。
当工艺中某个层次不需分类时, 该层次用0代替。
3. 附加工艺代号它用英文字母表示。
接在基础分类工艺代号后面。
具体代号见附录表1-2至1-5。
4. 多工序热处理工艺代号多工序热处理工艺代号用破折号将各工艺代号连接组成, 但除第一工艺外, 后面的工艺均省略第一位数字“5”, 如5151-331G表示调质和气体渗碳。
5. 常用热处理工艺代号见附录表1-6。
附录1表1-1 热处理工艺分类及代号附录1表1-2 加热介质及代号附录1表1-3 退火工艺代号附录1表1-4 淬火冷却介质和冷却方法及代号附录1表1-5 渗碳、碳氮共渗后冷却方法及代号附录1表1-6 常用热处理工艺及代号。
热处理代号和材料标注方法
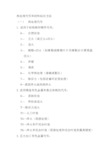
热处理代号和材料标注方法(一)热处理代号1. 适用于结构钢和铸件代号:0—自然状态1—正火(或正火+回火)2—退火3—精锻+回火(如精锻或精辊叶片在精锻后只需高温回火)4—淬硬5—调质6—化学热处理(渗碳或氮化)7—除应力(包括活塞环定型处理)9—表面淬火或局部淬火2.适用铸造有色金属和奥氏体钢的代号:0—原始状态1—再结晶退火T—除应力退火T1—人工时效T4—淬火(固溶处理)T5—淬火和不完全时效T6—淬火和完全时效(固溶处理和完全时效到最高硬度)3.压力加工有色金属代号:0—原始状态M—退火C—淬火CZ—淬火和自然时效CS—淬火和人工时效(二)材料的标注方法:1.零件的材料或毛坯(包括铸锻件)如不作任何处理,也不作机械性能检查,则只标材料牌号(其热处理代号“0”在图纸上不标注)如:A3,20,35,ZQSn6-6-3。
2.零件的材料或毛坯在热处理后,不作硬度及机械性能检查者则只标注材料牌号和热处理代号:如:45-1,若有几种热处理,可用热处理代号按工艺路线顺序逐项填写:如:15CrMoA-1+7。
3.有些材料的技术条件,有几种检查组别,但强度等级只有一种或可按材料截面尺寸来决定强度等级,只注明材料牌号,热处理代号和检查组别:如:45-5(Ⅱ)35CrMoA-5(Ⅱ)4.有些材料的技术条件,有几种组别,在同一热处理状态中有不同的强度等级,则注明材料牌号、热处理代号强度等级和检查组别,不需要规定检查组别时,检查组别可省略。
25Cr2MoV A-5 25Cr2MoV A-5 如:735-Ⅲ7355. 有些零件或者是比较重要或者是技术要求比较复杂,用上述标注方法不能说明全部要求者,则应注明标准号,在同一热处理状态中有不同的强度级别时,还应注明强度级别。
35CrMoA-5 35CrMoA-5 如:Q/CCF M 3003-2003 590×Q/CCF M 3003-20036. 大锻件如叶轮、铸造轴、整体转子等的材料标注方法钢号锻件级别×标准编号7. 铸钢件:铸铁、铜件:材料牌号类别材料牌号标准号标准号8.铸铁件及有色金属等直接按上述方法标注可能引起误解时,热处理代号加上括号。
热处理代号

金属热处理工艺的分类及代号 一、分类热处理分类由基础分类和附加分类组成。
1.基础分类根据工艺总称、工艺类型和工艺名称,将热处理工艺按三个层次进行分类,见附录表1-1。
2.附加分类对基础分类中某些工艺的具体条件的进一步分类。
包括退火、正火、淬火、化学热处理工艺加热方式(附录表1-2);退火工艺方法(附录表1-3);淬火冷却介质或冷却方法(附录表1-4)分类。
二、代号1.热处理工艺代号标记规定如下:5 ´ ´ - 表1-2中的内容 表1-3、表1-4中的英文字头及化学符号附加分类工艺代号基础分类工艺代号工艺名称工艺类型热处理2.基础工艺代号用四位数字表示。
第一位数字“5”为机械制造工艺分类与代号中表示热处理的工艺代号;第二、三位数字分别代表工艺类型、工艺名称代号(表1-1)。
3.附加工艺代号(1)当对基础工艺中的某些具体实施条件有明确要求时,使用附加分类工艺代号。
附加工艺代号接在基础分类工艺代号后面,其中加热方式采用两位数字,退火工艺、淬火介质和冷却方法则采用英文字头。
具体代号见表1-2至1-4。
(2)附加分类工艺代号按表1-2至1-4顺序标注,当工艺在某个层次不需进行分类时,该层次用0代替。
(3)当对冷却介质及冷却方法需要用1-4中两个以上字母表示时,用加号将两个或几个字母连接起来,如H+M 代表盐浴分级淬火。
(4)化学热处理中,没有表面渗入元素的各种工艺,如多元共渗、渗金属、渗其他非金属,可以在其代号后用括号表示出渗入元素的化学符号。
4.多工序热处理工艺代号用破折号将各工艺代号连接组成,但除第一工艺外,后面的工艺均省略第一位数字“5”,如515-33-01表示调质和气体渗氮。
表1-1 热处理工艺分类及代号(摘自GB/T12603-2005)表1-2 加热方式及代号(摘自GB/T12603-2005)表1-3 退火工艺代号(摘自GB/T12603-2005)表1-4 淬火冷却介质和冷却方法及代号(摘自GB/T12603-2005)表1-5 常用热处理工艺及代号。
各种热处理工艺代号及技术条件的标注方法
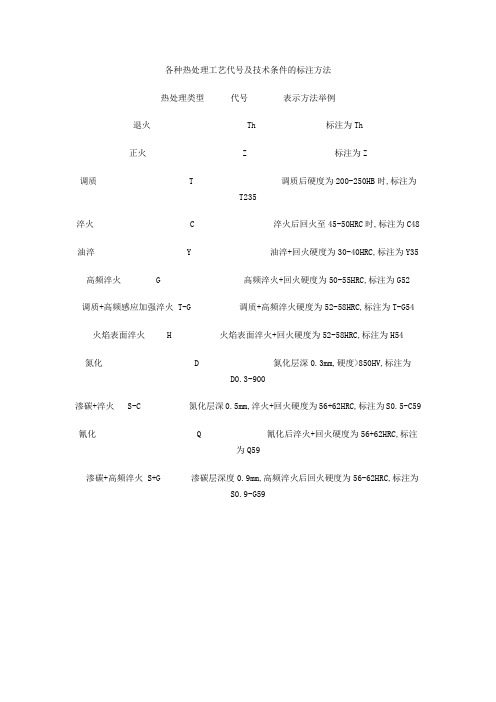
各种热处理工艺代号及技术条件的标注方法
热处理类型代号表示方法举例
退火 Th 标注为Th
正火 Z 标注为Z
调质 T 调质后硬度为200-250HB时,标注为T235
淬火 C 淬火后回火至45-50HRC时,标注为C48
油淬 Y 油淬+回火硬度为30-40HRC,标注为Y35
高频淬火 G 高频淬火+回火硬度为50-55HRC,标注为G52
调质+高频感应加强淬火 T-G 调质+高频淬火硬度为52-58HRC,标注为T-G54 火焰表面淬火 H 火焰表面淬火+回火硬度为52-58HRC,标注为H54
氮化 D 氮化层深0.3mm,硬度>850HV,标注为D0.3-900
渗碳+淬火 S-C 氮化层深0.5mm,淬火+回火硬度为56+62HRC,标注为S0.5-C59 氰化 Q 氰化后淬火+回火硬度为56+62HRC,标注为Q59
渗碳+高频淬火 S+G 渗碳层深度0.9mm,高频淬火后回火硬度为56-62HRC,标注为
S0.9-G59。
热处理工艺代号及技术条件的标注方法
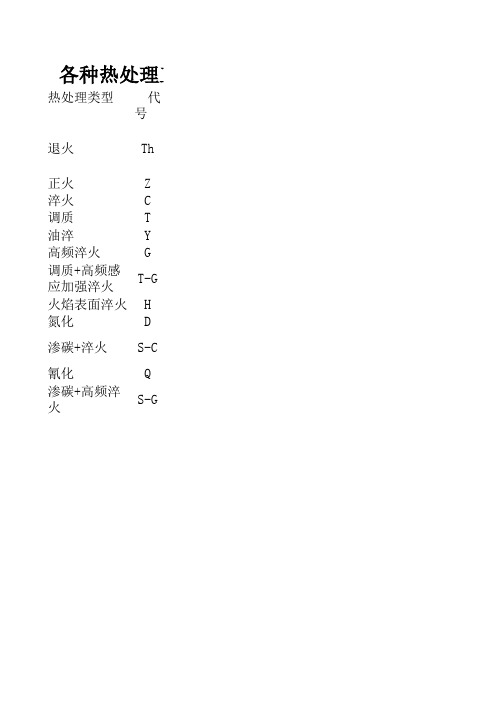
调质+高频淬火硬度为52-58HRC,标注为T-G54
火焰表面淬火+回火硬度为52-58HRC,标注为H54 氮化层深0.3mm,硬度>850HV,标注为D0.3-900 氮化层深0.5mm,淬火+回火硬度为56+62HRC,标注 为S0.5-C59 氰化后淬火+回火硬度为56+62HRC,标注为Q59 渗碳层深度0.9mm,高频淬火后回火硬度为5662HRC,标注为S0.9-G59
各种热处理工艺代号及技术条件的标注方法
热处理类型 代 号
退火火
C
调质
T
油淬
Y
高频淬火
G
调质+高频感 应加强淬火
T-G
火焰表面淬火 H
氮化
D
渗碳+淬火 S-C
氰化
Q
渗碳+高频淬 火
S-G
热处理工艺代号及技术条件的标注方法
表示方法举例
标注为Th
标注为Z 淬火后回火至45-50HRC时,标注为C48
热处理工艺分类及代号(GB

工艺总称
代号
工艺类型
代号
工艺名称
代号
加热方法
代号
热处理
5
整体热处理
1
退火
1
加热炉
1
正火
2
淬火
3
感应
2
淬火和回火
4
调质
5
稳定化处理
6
火焰
3
回溶处理、水韧处理
7
固溶处理和时效
8
电阻
4
表面热处理
2
表面淬水和回水
1
物理气相沉积
2
化学气相沉积
3
激光
5
等离子体化学气相沉积
炼钢用轨道板、气缸套、齿轮、机床立柱、齿轮箱体、机床机身、磨床转体、液压缸、泵体、阀体
HT300
承受高弯曲应力、拉应力、要求保持高度气密性的铸件,如重型机床床身、多轴机床主轴箱、卡盘齿轮、高压液压缸、泵体、阀体
HT350
轧钢滑板、辊子、炼焦柱塞、圈筒混合机齿圈、支承轮座、挡轮座
4
化学热处理
3
渗碳
1
电子束
6
碳氮共渗
2
渗氮
3
氮碳共渗
4
等离子体
7
渗其它非金属
5
渗金属
6
其它
8
多元共渗
7
熔渗
8
加热介质及代号
加热介质
固体
液体
气体
真空
保护气氛
可控气氛
液体床
代号
S
L
G
V
P
C
F
退火工艺及代号
退火工艺
(整理)铜及铜合金状态表示方法编制说明
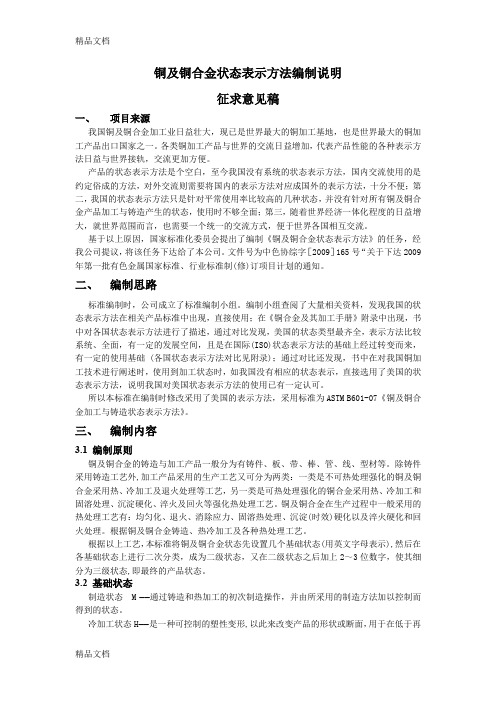
铜及铜合金状态表示方法编制说明征求意见稿一、项目来源我国铜及铜合金加工业日益壮大,现已是世界最大的铜加工基地,也是世界最大的铜加工产品出口国家之一。
各类铜加工产品与世界的交流日益增加,代表产品性能的各种表示方法日益与世界接轨,交流更加方便。
产品的状态表示方法是个空白,至今我国没有系统的状态表示方法,国内交流使用的是约定俗成的方法,对外交流则需要将国内的表示方法对应成国外的表示方法,十分不便;第二,我国的状态表示方法只是针对平常使用率比较高的几种状态,并没有针对所有铜及铜合金产品加工与铸造产生的状态,使用时不够全面;第三,随着世界经济一体化程度的日益增大,就世界范围而言,也需要一个统一的交流方式,便于世界各国相互交流。
基于以上原因,国家标准化委员会提出了编制《铜及铜合金状态表示方法》的任务,经我公司提议,将该任务下达给了本公司。
文件号为中色协综字[2009]165号“关于下达2009年第一批有色金属国家标准、行业标准制(修)订项目计划的通知。
二、编制思路标准编制时,公司成立了标准编制小组。
编制小组查阅了大量相关资料,发现我国的状态表示方法在相关产品标准中出现,直接使用;在《铜合金及其加工手册》附录中出现,书中对各国状态表示方法进行了描述,通过对比发现,美国的状态类型最齐全,表示方法比较系统、全面,有一定的发展空间,且是在国际(ISO)状态表示方法的基础上经过转变而来,有一定的使用基础 (各国状态表示方法对比见附录);通过对比还发现,书中在对我国铜加工技术进行阐述时,使用到加工状态时,如我国没有相应的状态表示,直接选用了美国的状态表示方法,说明我国对美国状态表示方法的使用已有一定认可。
所以本标准在编制时修改采用了美国的表示方法,采用标准为ASTM B601-07《铜及铜合金加工与铸造状态表示方法》。
三、编制内容3.1 编制原则铜及铜合金的铸造与加工产品一般分为有铸件、板、带、棒、管、线、型材等。
除铸件采用铸造工艺外,加工产品采用的生产工艺又可分为两类:一类是不可热处理强化的铜及铜合金采用热、冷加工及退火处理等工艺,另一类是可热处理强化的铜合金采用热、冷加工和固溶处理、沉淀硬化、淬火及回火等强化热处理工艺。
热处理基础知识

二、热处理技术要求的表示方法
• 1、热处理工艺方法的表示 (1)国家标准JB/T 6609-1993的规定
热处理工艺方法 名称 退火 正火 调质 淬火 字母 Th Z T C
热处理技术要求表示举例
汉字表示 退火 正火 调质220~250HBS 淬火42~47HRC 感应淬火48~53HRC 火焰淬火42~47HRC 渗碳层深0.8~1.2mm 淬火硬度58~63HRC 代号表示 Th Z T235 C42 G48 H42 S0.8-C58
200~230 220~250 250~280 280~300 35~40 42~47 45~50 48~53 58~63 60~65 ≥ 450 ≥ 500 ≥ 850 ≥ 900
一、热处理技术要求的表示方法
3、表面硬度的表示
表一:常用硬度对照表
硬度
HRC 17 20 25 30 35 40 45 50 55 60 65 70 HV 211 226 255 289 329 377 436 509 599 713 856 1037 HB 211 225 251 283 323 370 424 488 -
•
加热温度是热处理工艺的重要工艺参数 之一,选择和控制加热温度 ,是保证热处 理质量的主要问题。加热温度随被处理的 金属材料和热处理的目的不同而异,但一 般都是加热到相变温度以上,以获得高温 组织。另外转变需要一定的时间,因此当 金属工件表面达到要求的加热温度时,还 须在此温度保持一定时间,使内外温度一 致,使显微组织转变完全,这段时间称为 保温时间。采用高能密度加热和表面热处 理时,加热速度极快,一般就没有保温时 间,而化学热处理的保温时间往往较长。 冷却也是热处理工艺过程中不可缺少的 步骤,冷却方法因工艺不同而不同,主要 是控制冷却速度。一般退火的冷却速度最 慢,正火的冷却速度较快,淬火的冷却速 度更快。但还因钢种不同而有不同的要求, 例如空硬钢就可以用正火一样的冷却速度 进行淬硬。
调质处理标注
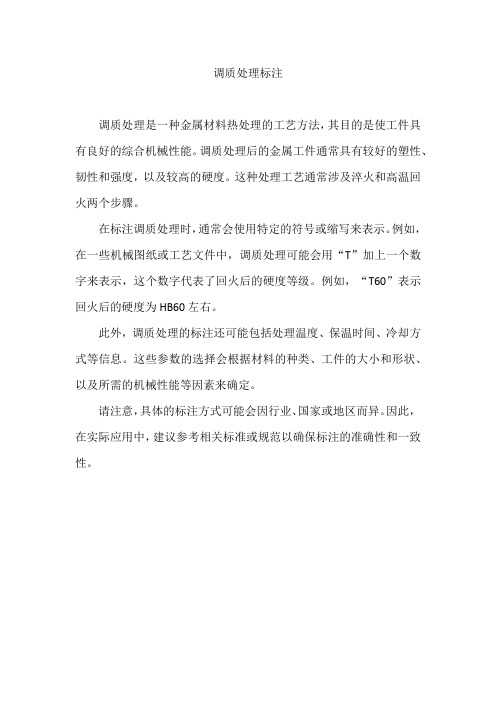
调质处理标注
调质处理是一种金属材料热处理的工艺方法,其目的是使工件具有良好的综合机械性能。
调质处理后的金属工件通常具有较好的塑性、韧性和强度,以及较高的硬度。
这种处理工艺通常涉及淬火和高温回火两个步骤。
在标注调质处理时,通常会使用特定的符号或缩写来表示。
例如,在一些机械图纸或工艺文件中,调质处理可能会用“T”加上一个数字来表示,这个数字代表了回火后的硬度等级。
例如,“T60”表示回火后的硬度为HB60左右。
此外,调质处理的标注还可能包括处理温度、保温时间、冷却方式等信息。
这些参数的选择会根据材料的种类、工件的大小和形状、以及所需的机械性能等因素来确定。
请注意,具体的标注方式可能会因行业、国家或地区而异。
因此,在实际应用中,建议参考相关标准或规范以确保标注的准确性和一致性。
- 1、下载文档前请自行甄别文档内容的完整性,平台不提供额外的编辑、内容补充、找答案等附加服务。
- 2、"仅部分预览"的文档,不可在线预览部分如存在完整性等问题,可反馈申请退款(可完整预览的文档不适用该条件!)。
- 3、如文档侵犯您的权益,请联系客服反馈,我们会尽快为您处理(人工客服工作时间:9:00-18:30)。
各种热处理工艺代号及技术条件的标注方法
热处理类型代号表示方法举例
退火 Th 标注为Th
正火 Z 标注为Z
调质T 调质后硬度为200-250HB时,标注为T235
淬火 C 淬火后回火至45-50HRC时,标注为C48
油淬Y 油淬+回火硬度为30-40HRC,标注为Y35
高频淬火 G 高频淬火+回火硬度为50-55HRC,标注为G52
调质+高频感应加强淬火T-G 调质+高频淬火硬度为52-58HRC,标注为T-G54
火焰表面淬火 H 火焰表面淬火+回火硬度为52-58HRC,标注为H54
氮化 D 氮化层深0.3mm,硬度>850HV,标注为D0.3-900
渗碳+淬火S-C 氮化层深0.5mm,淬火+回火硬度为56+62HRC,标注为S0.5-C59
氰化 Q 氰化后淬火+回火硬度为56+62HRC,标注为Q59
渗碳+高频淬火S+G 渗碳层深度0.9mm,高频淬火后回火硬度为56-62HRC,标注为S0.9-G59。