真实应力—应变曲线拉伸实验
实验六 真实应力—应变曲线的测定(有一张白纸)
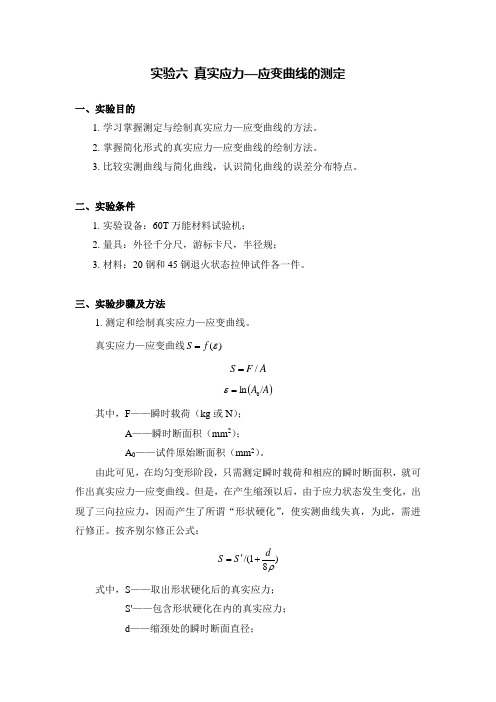
实验六 真实应力—应变曲线的测定一、实验目的1. 学习掌握测定与绘制真实应力—应变曲线的方法。
2. 掌握简化形式的真实应力—应变曲线的绘制方法。
3. 比较实测曲线与简化曲线,认识简化曲线的误差分布特点。
二、实验条件1. 实验设备:60T 万能材料试验机;2. 量具:外径千分尺,游标卡尺,半径规;3. 材料:20钢和45钢退火状态拉伸试件各一件。
三、实验步骤及方法1. 测定和绘制真实应力—应变曲线。
真实应力—应变曲线)(εf S =A F S /=()A A /ln 0=ε其中,F ——瞬时载荷(kg 或N ); A ——瞬时断面积(mm 2); A 0——试件原始断面积(mm 2)。
由此可见,在均匀变形阶段,只需测定瞬时载荷和相应的瞬时断面积,就可作出真实应力—应变曲线。
但是,在产生缩颈以后,由于应力状态发生变化,出现了三向拉应力,因而产生了所谓“形状硬化”,使实测曲线失真,为此,需进行修正。
按齐别尔修正公式:)81/(ρdS S +'= 式中,S ——取出形状硬化后的真实应力; S'——包含形状硬化在内的真实应力; d ——缩颈处的瞬时断面直径;ρ——缩颈处试件外形瞬时曲率半径。
因此,在产生缩颈之后,除以测定瞬时载荷F 、缩颈处瞬时直径d 以外,还需要测定相应瞬时试件外形的曲率半径ρ,才能绘制出实测的真实应力—应变曲线。
2. 绘制简化真实应力—应变曲线 (1)n B S ε=简化真实应力—应变曲线 式中,B ——材料常数; n ——加工硬化指数。
因为b n ε=,b b b S B εε/=于是上式可写为:bb b S S εεε⎪⎪⎭⎫⎝⎛=式中,S b ——刚产生缩颈时即失稳点的真实应力; b ε——失稳点的真实应力。
由此可见,只要准确测定失稳点的真实应力和真实应变,就能作出该种简化应力应变曲线。
(2)简化真实应力—应变曲线,即真实应力—应变曲线在塑性失稳点上所作的切线。
真实应力-应变曲线
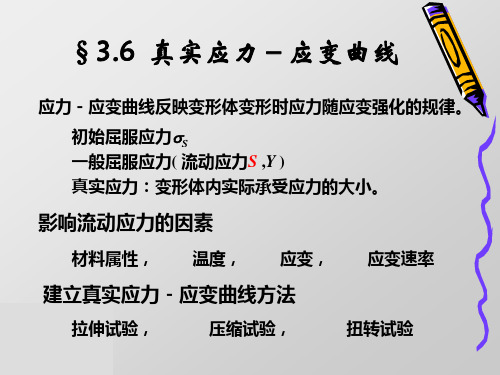
§3.6 真实应力-应变曲线
应力-应变曲线反映变形体变形时应力随应变强化的规律。
初始屈服应力S
一般屈服应力( 流动应力S ,Y ) 真实应力:变形体内实际承受应力的大小。
影响流动应力的因素
材料属性, 温度, 应变, 应变速率
建立真实应力-应变曲线方法
拉伸试验,
压缩试验,
扭转试验
流动应力S 的公式表达形式
失稳点b,Fb = Fmax。
dF A0 edS Sed 0
dS Sd 0
dS
d
b
Sb
二、 压缩试验曲线
拉伸试验曲线:失稳,精确范围( < 0.3); 压缩试验曲线:摩擦(S ),精确范围( 2);
1、直接消除摩擦的圆柱体压缩法
S
P A
P A0e
ln H0
H
2、外推法 摩擦力影响和式样尺寸D0/H0 有关,根据不同的D0/H0 , 外推出D0/H0 = 0时的S,得到 真实应力-应变曲线。
1 1
Fd F(0)
1、拉伸图和条件应力-应变曲线
0
F A0
l
l0
b d
c
Fb= Fmax
Fp Fc
三个变形阶段:
ph
特征点:弹性极限点p,屈服点c,失稳点b,断裂点k。
?
k
Δl()
2、真实应力-应变曲线 用真实应力与应变表示的曲线。
S( ) ; S( ) ; S( )
2 2t
24
1 3 平面应变问题
2
3
1 2 2 2 3 2 3 1 2
2 3
6 1 1.1551
S 800 0.25
8001.151 0.25 443
真实应力-真实应变曲线的测定
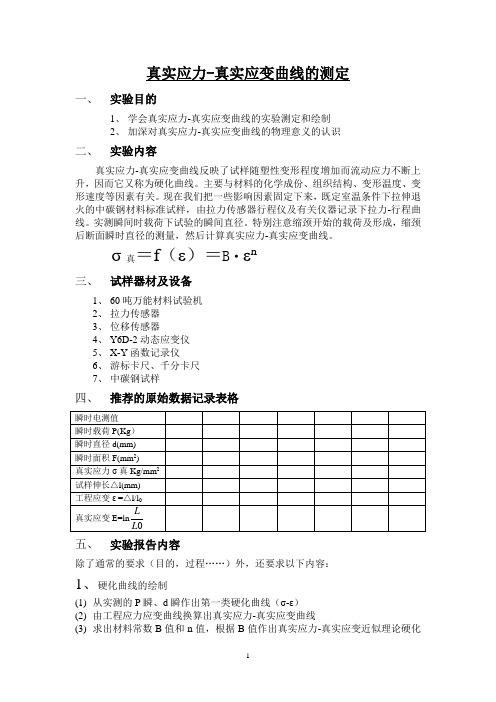
真实应力-真实应变曲线的测定一、实验目的1、学会真实应力-真实应变曲线的实验测定和绘制2、加深对真实应力-真实应变曲线的物理意义的认识二、实验内容真实应力-真实应变曲线反映了试样随塑性变形程度增加而流动应力不断上升,因而它又称为硬化曲线。
主要与材料的化学成份、组织结构、变形温度、变形速度等因素有关。
现在我们把一些影响因素固定下来,既定室温条件下拉伸退火的中碳钢材料标准试样,由拉力传感器行程仪及有关仪器记录下拉力-行程曲线。
实测瞬间时载荷下试验的瞬间直径。
特别注意缩颈开始的载荷及形成,缩颈后断面瞬时直径的测量,然后计算真实应力-真实应变曲线。
σ真=f(ε)=B·εn三、试样器材及设备1、60吨万能材料试验机2、拉力传感器3、位移传感器4、Y6D-2动态应变仪5、X-Y函数记录仪6、游标卡尺、千分卡尺7、中碳钢试样四、推荐的原始数据记录表格五、实验报告内容除了通常的要求(目的,过程……)外,还要求以下内容:1、硬化曲线的绘制(1)从实测的P瞬、d瞬作出第一类硬化曲线(σ-ε)(2)由工程应力应变曲线换算出真实应力-真实应变曲线(3)求出材料常数B值和n值,根据B值作出真实应力-真实应变近似理论硬化曲线。
2、把真实应力-真实应变曲线与近似理论曲线比较,求出最大误差值。
3、实验体会六、实验预习思考题1、 什么是硬化曲线?硬化曲线有何用途?2、 真实应力-真实应变曲线和工程应力应变曲线的相互换算。
3、 怎样测定硬化曲线?测量中的主要误差是什么?怎样尽量减少误差?附:真实应力-真实应变曲线的计算机数据处理一、 目的初步掌握实验数据的线性回归方法,进一步熟悉计算机的操作和应用。
二、 内容一般材料的真实应力-真实应变都是呈指数型,即σ=B εn 。
如把方程的二边取对数:ln σ=lnB+nln ε,令 y =ln σ;a =lnB ;x =ln ε 则上式可写成y =a+bx成为一线性方程。
在真实应力-真实应变曲线试验过程中,一般可得到许多σ和ε的数据,经换算后,既有许多的y 和x 值,在众多的数值中如何合理的确定a 和b 值使大多数实验数据都在线上,这可用最小二乘法来处理。
实验方法:应力与应变曲线的测定
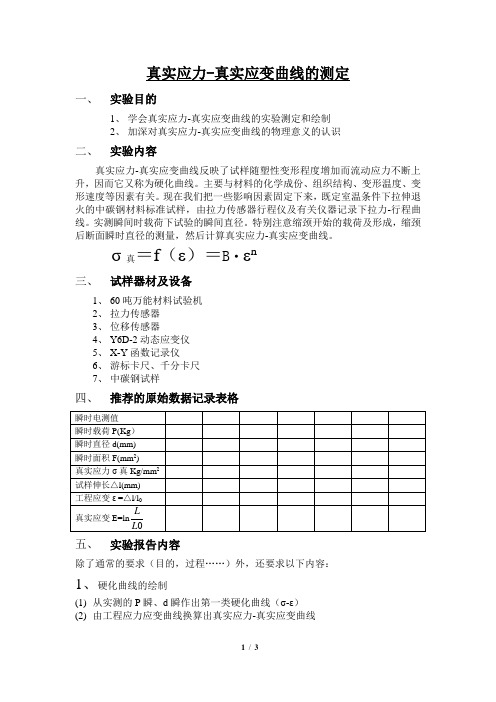
真实应力-真实应变曲线的测定一、实验目的1、学会真实应力-真实应变曲线的实验测定和绘制2、加深对真实应力-真实应变曲线的物理意义的认识二、实验内容真实应力-真实应变曲线反映了试样随塑性变形程度增加而流动应力不断上升,因而它又称为硬化曲线。
主要与材料的化学成份、组织结构、变形温度、变形速度等因素有关。
现在我们把一些影响因素固定下来,既定室温条件下拉伸退火的中碳钢材料标准试样,由拉力传感器行程仪及有关仪器记录下拉力-行程曲线。
实测瞬间时载荷下试验的瞬间直径。
特别注意缩颈开始的载荷及形成,缩颈后断面瞬时直径的测量,然后计算真实应力-真实应变曲线。
σ真=f(ε)=B·εn三、试样器材及设备1、60吨万能材料试验机2、拉力传感器3、位移传感器4、Y6D-2动态应变仪5、X-Y函数记录仪6、游标卡尺、千分卡尺7、中碳钢试样四、推荐的原始数据记录表格五、实验报告内容除了通常的要求(目的,过程……)外,还要求以下内容:1、硬化曲线的绘制(1)从实测的P瞬、d瞬作出第一类硬化曲线(σ-ε)(2)由工程应力应变曲线换算出真实应力-真实应变曲线(3) 求出材料常数B 值和n 值,根据B 值作出真实应力-真实应变近似理论硬化曲线。
2、把真实应力-真实应变曲线与近似理论曲线比较,求出最大误差值。
3、实验体会六、实验预习思考题1、 什么是硬化曲线?硬化曲线有何用途?2、 真实应力-真实应变曲线和工程应力应变曲线的相互换算。
3、 怎样测定硬化曲线?测量中的主要误差是什么?怎样尽量减少误差?附:真实应力-真实应变曲线的计算机数据处理一、 目的初步掌握实验数据的线性回归方法,进一步熟悉计算机的操作和应用。
二、 内容一般材料的真实应力-真实应变都是呈指数型,即σ=B εn 。
如把方程的二边取对数:ln σ=lnB+nln ε,令 y =ln σ;a =lnB ;x =ln ε 则上式可写成y =a+bx成为一线性方程。
在真实应力-真实应变曲线试验过程中,一般可得到许多σ和ε的数据,经换算后,既有许多的y 和x 值,在众多的数值中如何合理的确定a 和b 值使大多数实验数据都在线上,这可用最小二乘法来处理。
材料拉伸试验应力-应变曲线
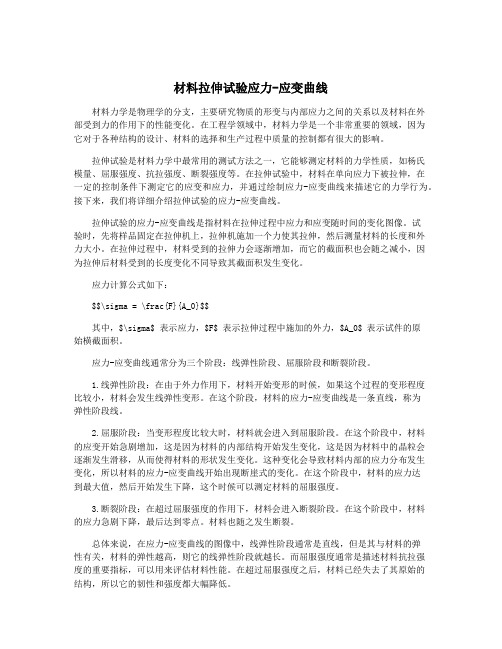
材料拉伸试验应力-应变曲线材料力学是物理学的分支,主要研究物质的形变与内部应力之间的关系以及材料在外部受到力的作用下的性能变化。
在工程学领域中,材料力学是一个非常重要的领域,因为它对于各种结构的设计、材料的选择和生产过程中质量的控制都有很大的影响。
拉伸试验是材料力学中最常用的测试方法之一,它能够测定材料的力学性质,如杨氏模量、屈服强度、抗拉强度、断裂强度等。
在拉伸试验中,材料在单向应力下被拉伸,在一定的控制条件下测定它的应变和应力,并通过绘制应力-应变曲线来描述它的力学行为。
接下来,我们将详细介绍拉伸试验的应力-应变曲线。
拉伸试验的应力-应变曲线是指材料在拉伸过程中应力和应变随时间的变化图像。
试验时,先将样品固定在拉伸机上,拉伸机施加一个力使其拉伸,然后测量材料的长度和外力大小。
在拉伸过程中,材料受到的拉伸力会逐渐增加,而它的截面积也会随之减小,因为拉伸后材料受到的长度变化不同导致其截面积发生变化。
应力计算公式如下:$$\sigma = \frac{F}{A_0}$$其中,$\sigma$ 表示应力,$F$ 表示拉伸过程中施加的外力,$A_0$ 表示试件的原始横截面积。
应力-应变曲线通常分为三个阶段:线弹性阶段、屈服阶段和断裂阶段。
1.线弹性阶段:在由于外力作用下,材料开始变形的时候,如果这个过程的变形程度比较小,材料会发生线弹性变形。
在这个阶段,材料的应力-应变曲线是一条直线,称为弹性阶段线。
2.屈服阶段:当变形程度比较大时,材料就会进入到屈服阶段。
在这个阶段中,材料的应变开始急剧增加,这是因为材料的内部结构开始发生变化,这是因为材料中的晶粒会逐渐发生滑移,从而使得材料的形状发生变化。
这种变化会导致材料内部的应力分布发生变化,所以材料的应力-应变曲线开始出现断崖式的变化。
在这个阶段中,材料的应力达到最大值,然后开始发生下降,这个时候可以测定材料的屈服强度。
3.断裂阶段:在超过屈服强度的作用下,材料会进入断裂阶段。
基于压缩试验确定真实应力-应变曲线

1.由于受到塑性失稳的限制, 1.由于受到塑性失稳的限制,拉伸实验曲线对数应变 ∈≈1.0左右, 由于受到塑性失稳的限制 其精确段为 ∈< 0.3 。而实际变形的应变往往大得多,因此拉 内 而实际变形的应变往往大得多, 伸实验曲线是不够用的。 伸实验曲线是不够用的。 要获得大变形下的真实应力-应变曲线,就需要用到压缩实验。 要获得大变形下的真实应力-应变曲线,就需要用到压缩实验。 2.压缩实验需要解决的问题 2.压缩实验需要解决的问题 由于试件与工具之间存在摩擦,就会改变其单向均匀压缩状态, 由于试件与工具之间存在摩擦,就会改变其单向均匀压缩状态, 并出现鼓形。因而,消除接触面间的摩擦是求得真实曲线的关键。 并出现鼓形。因而,消除接触面间的摩擦是求得真实曲线的关键。
图3-59a是圆柱压缩实验简图。上下垫板经淬火、回火、磨削 59a是圆柱压缩实验简图 上下垫板经淬火、回火、 是圆柱压缩实验简图。 和抛光。 和抛光。
a)
b)
c)
图3-59圆柱压缩实验及其试件 59圆柱压缩实验及其试件
D0 。 为了减小接触面间的摩擦, 试件尺寸取 D0 = 20 30mm, =1 为了减小接触面间的摩擦,可 H0
H 试件压缩前、 式中 H0、 −试件力为
Y =P= P ∈ A A0e
A− 试件压缩前、后的横截面面积; 式中 A 0、 试件压缩前、后的横截面面积; 轴向载荷。 P−轴向载荷。
在试件的端面上车出沟槽或浅坑( 59b、 ),以便保存润滑 在试件的端面上车出沟槽或浅坑(图3-59b、c),以便保存润滑 剂。
3.实验时需要注意的问题 3.实验时需要注意的问题 (1)每压缩10%的高度,记录一次压力和实际高度,并将 每压缩10%的高度 记录一次压力和实际高度, 的高度, 试件和垫板擦净,重新加润滑剂,再重复上述过程。 试件和垫板擦净,重新加润滑剂,再重复上述过程。 (2)如果试件出现鼓形,需要将鼓形车去,并使试件尺寸 如果试件出现鼓形,需要将鼓形车去, 再重复以上压缩过程, 仍保持 D =1 ,再重复以上压缩过程,直至∈= 1.2 或 试件 H 出现微裂纹为止 根据记录下的各次压缩量和压力, 根据记录下的各次压缩量和压力,利用下面公式计算出压 缩时的真实应力和对数应变。 缩时的真实应力和对数应变。
真实应力应变曲线
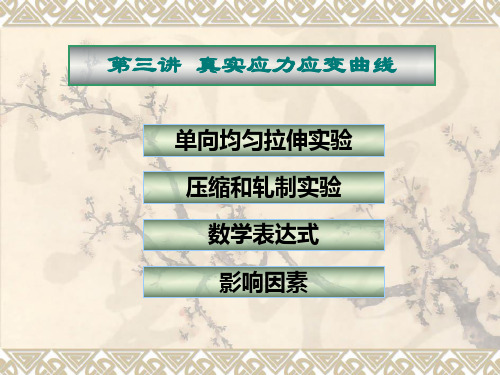
基于拉伸实验确定真实应力-应变曲线
2、真实应力-应变曲线
真实应力-应变曲线分类
真实应力,简称真应力,也就是瞬时的流动应力Y,用单向均匀拉
伸(或压缩)时各加载瞬间的载荷P与该瞬间试样的横截面积A之比
来表示,则
YP A
真实应力-应变曲线可分为三类:
(1)Y ;(2)Y ;(3)Y
基于拉伸实验确定真实应力-应变曲线
2、变形速度对真实应力-应变曲线的影响 速度增加→位错运动加快→ 需要更大的切应力→流动应力提高 速度增加→硬化得不到恢复→ 流动应力提高
但如果速度很大→温度效应大→ 流动应力降低
在冷变形时,温度效应显著,强化被软化所抵消,最终表现出的是: 变形速度的影响不明显,动态时的真实应力—应变曲线比静态时略高 一点,差别不大。
基于拉伸实验确定真实应力-应变曲线
1、标称应力(名义应力、条件应力)-应变曲线
标称应力-应变曲线上的三个特征点
oc(弹性变形阶段)——cb(均匀塑性变 形阶段)——bk(局部塑性变形阶段)
屈服点c:
弹性变形与均匀塑性变形的分界点,对应
应力为屈服点 s ,或屈服强度 0.2
基于拉伸实验确定真实应力-应变曲线
Y- ∈曲线的修正
由于缩颈,即形状变化而产生应力升高的现象称 形状硬化。
基于压缩实验和轧制实验确定真实应力-应变曲线
1.基于圆柱压缩实验确定真实应力—应变曲线
拉伸Y- ∈曲线受塑性失稳的限制,精度较低, ∈<0.3,实际塑性成
形变形量较大,如锻造≤1.6,反挤≤2.5,拉伸试验曲线不够用。需要
压缩Y- ∈曲线。
换算:σ1=0, σ3=p, ∈2=0, σ2=p/2
1
2
拉伸试验应力应变曲线

拉伸试验应力应变曲线
拉伸试验是材料力学性能测试中常用的一种试验方法,用于测定材料在拉伸过程中的应力应变关系。
下面是拉伸试验中典型的应力应变曲线的一般特征:
1. 弹性阶段(OA 段):
在拉伸试验开始时,应力应变曲线呈现线性关系,材料在这个阶段表现出弹性行为。
在弹性阶段,材料在去除载荷后能够完全恢复到原来的形状,没有永久变形。
2. 屈服阶段(AB 段):
当应力增加到一定值时,材料开始出现屈服现象,应力应变曲线出现非线性部分。
屈服阶段的起始点称为屈服点(yield point),此时材料开始发生塑性变形。
3. 塑性阶段(BC 段):
在屈服点之后,材料进入塑性阶段,应力应变曲线呈现非线性关系。
在这个阶段,材料发生永久性变形,即使去除载荷也无法完全恢复到原来的形状。
4. 强化阶段(CD 段):
在塑性阶段之后,应力应变曲线继续上升,但斜率逐渐减小。
这
个阶段称为强化阶段,材料的强度逐渐增加,但塑性变形也在不断增加。
5. 颈缩阶段(DE 段):
当应力达到材料的极限强度时,材料开始出现颈缩现象,即局部截面缩小。
在颈缩阶段,应力应变曲线迅速下降,最终导致材料断裂。
需要注意的是,拉伸试验应力应变曲线的具体形状和特征会因材料的性质和试验条件而有所不同。
以上描述的是一般情况下典型的应力应变曲线特征。
绘制拉伸真实应力应变曲线s
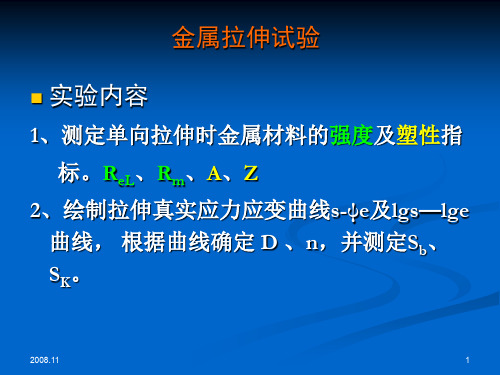
3
金属拉伸试验
3、强度性能指标
(抗拉强度Rm)
4、塑性性能指标
(断后伸长率A、屈服点伸长率Ae、最大力下的 总伸长率Agt、最大力下的非比例伸长率Ag和断面 收缩率Z)。
2008.11
4
金属拉伸试验
1、物理屈服性能指标 具有物理屈服现象的金属材料,其拉伸曲
线有如下几种类型。
2008.11
5
金属拉伸试验
拉伸试验---是金属材料力学性能测试中最 重要的试验方法之一。
2008.11
2
金属拉伸试验
一、测定金属材料的强度及塑性指标 1、物理屈服性能指标
(上屈服强度ReH、下屈服强度ReL)
2、规定微量塑性伸长强度指标
(规定非比例延伸强度RP、规定总延伸强度Rt、 规定残余延伸强度Rr)
2008.11
Re L
FeL So
2008.11
6
金属拉伸试验
ReH
FeH So
ReL
FeL So
2008.11
7
金属拉伸试验
ReH
FeH So
ReL
FeL So
2008.11
8
金属拉伸试验
ReH
FeH So
ReL
FeL So
2008.11
9
ab
金属拉伸试验
2、规定微量塑性伸长强度指标
规定非比例延伸强度 ( Rp )
2008.11
12
金属拉伸试验
3、强度性能指标 (抗拉强度Rm) 抗拉强度(Rm) ---试样拉伸过程中最大试验
力所对应的应力。
Rm
06第六章 真实应力应变曲线
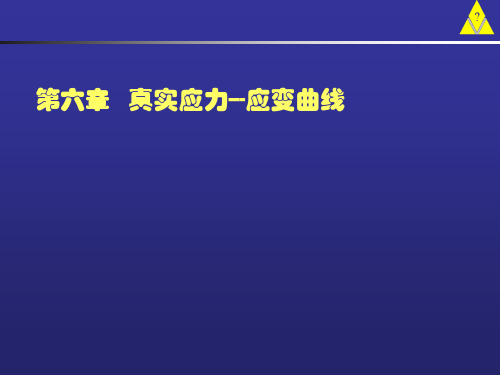
ln ln k n ln
(比较直线方程: y=kx+b)
可见,在 ln ln 双对数坐标系里,硬化曲线变为一条直线, 直线的斜率为 n 在 y 轴上的截距为 k 的对数。
§8.6 压缩试验曲线简介
思考题:下面三种板试样,哪一种均匀应变大?
?
?
练习:成形前在薄板上做直径为 d 的圆网格。设在变形后某自由 表面处网格变为长轴为 a 短轴为 b 的椭圆。已知材料满足
?
真应力
P F
; 真应变
dl d l
l ln l0
真应变表达的优点:
可加性 可比性
§6.3 真实应力--应变曲线的绘制
?
P
S
l
载荷--位移
e
名义应力--名义应变
真应力--真应变
P
l
P S F0 l e l0
P P F0 l S S (1 e) F F0 F l0 l0 l ln ln( 1 e) l0
n=1
1>n>0 n=0
?
设某材料的应力应变关系为:
k n
d 失稳时,材料应力--应变关系满足: nk n 1 k n d
失稳时,材料所能获得的最大均匀应变为:
n
由此可见,加工硬化指数 n不仅是一个硬化指标,也是一个塑性 指标。材料的加工硬化能力于其塑性变形的能力成正比。
k n
试计算1)应变分量;2)应力分量 d
a
b
始标距长度
显而易见,名义应力和名义应变不是材料真实所受的应力和应变。
?
P P(S F0 )
应力应变曲线实验报告
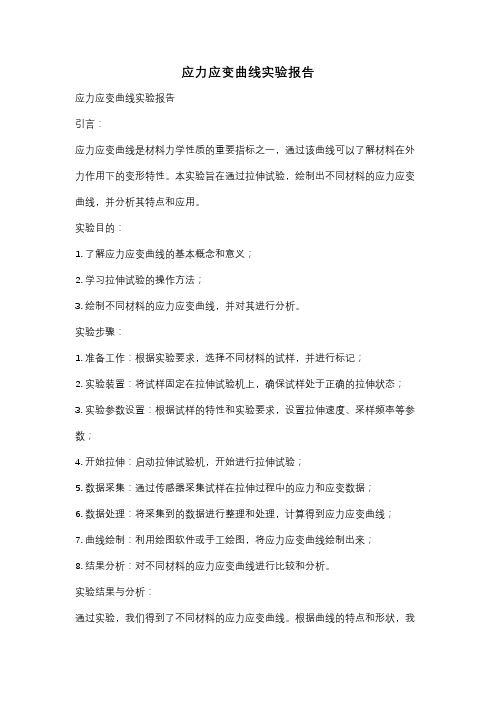
应力应变曲线实验报告应力应变曲线实验报告引言:应力应变曲线是材料力学性质的重要指标之一,通过该曲线可以了解材料在外力作用下的变形特性。
本实验旨在通过拉伸试验,绘制出不同材料的应力应变曲线,并分析其特点和应用。
实验目的:1. 了解应力应变曲线的基本概念和意义;2. 学习拉伸试验的操作方法;3. 绘制不同材料的应力应变曲线,并对其进行分析。
实验步骤:1. 准备工作:根据实验要求,选择不同材料的试样,并进行标记;2. 实验装置:将试样固定在拉伸试验机上,确保试样处于正确的拉伸状态;3. 实验参数设置:根据试样的特性和实验要求,设置拉伸速度、采样频率等参数;4. 开始拉伸:启动拉伸试验机,开始进行拉伸试验;5. 数据采集:通过传感器采集试样在拉伸过程中的应力和应变数据;6. 数据处理:将采集到的数据进行整理和处理,计算得到应力应变曲线;7. 曲线绘制:利用绘图软件或手工绘图,将应力应变曲线绘制出来;8. 结果分析:对不同材料的应力应变曲线进行比较和分析。
实验结果与分析:通过实验,我们得到了不同材料的应力应变曲线。
根据曲线的特点和形状,我们可以对材料的力学性质进行评估和比较。
首先,我们观察到曲线的线性阶段,即弹性阶段。
在这个阶段,应变与应力成正比,材料表现出良好的弹性回复能力。
弹性模量可以通过斜率计算得到,是衡量材料刚性的重要指标。
其次,曲线进入非线性阶段,即屈服阶段。
在这个阶段,材料开始发生塑性变形,应力随应变增加而逐渐增大。
屈服强度是材料的重要特征之一,它表示了材料开始发生塑性变形的能力。
随后,曲线进入极限强度阶段,即材料的最大承载能力。
在这个阶段,应力达到最大值,材料即将发生破坏。
极限强度是衡量材料抗拉强度的重要指标。
最后,曲线进入断裂阶段,即材料发生破坏和断裂。
在这个阶段,应力急剧下降,材料失去了原有的结构和强度。
结论:通过本实验,我们了解了应力应变曲线的基本特点和意义。
不同材料的曲线形状和特征不同,这与材料的组成、结构和加工方式有关。
塑性成形原理-36-真实应力应变曲线
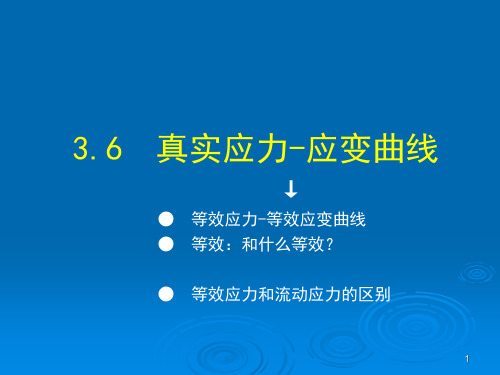
2 2 2 2 2 (1 2 ) ( 2 3 ) (3 1 ) 3 3 3
★ 教材P139公式错,正确公式见P90式(3-65)
22
3、 曲线转换 把
4
如果按应变的计算方法,则:
70 1 ln 50 0.336 80 2 ln 0.134 70 80 总 ln 50 0.470 1 2
显然,总应变等于各阶段应变之和,但延 伸率则不等!
5
习题25:
前文已证明,线弹性条件下,有:
2) 等效应力和流动应力的概念。
12
四、计算真实应力和真实应变,作出曲线
P A
l1 ln l0
13
3.6.3 外推法 压缩实验中试样直径越大,摩擦的影响就 越大,变形体偏离单向应力状态就越远,为了 减小摩擦的影响,可以减小试样直径。 │ ↓ 当试样直径为 0时,摩擦的影响就没了
14
用途:多用于板料成形(板条试样)
注意:前面讲的几何方程描述的是不是真实应 变?
8
3.6.2 压缩试验曲线
P A
l1 ln l0
注意:单向压缩时试样上各点的应力状态 如何确定各点的应力、应变?
9
一、试样尺寸 初始直径D0=φ20~30mm, 初始高度H0=D0
二、润滑 在试样端面车出浅坑或凹槽,并加入润滑 剂,以使变形体各处尽量接近于单向压应力状 态。
知道前面为什么要凑等效应力、等效应变的系数了吗?
3
★ 看一下 延伸率和应变 之间的关系…
把一个初始长度为50的试样单向拉伸到长 70,然后再拉伸到长80,求两次拉伸的延伸率 和总的延伸率:
真实应力-应变曲线2014

F0 F e
dS Sd 0
F0 ∴ P S e
b
S Sb
29
在塑性失稳点处,P有极大值,
∴
dS Sb d
dS Sb d
dS AC Sb d AB
显然AC= Sb
AB=↔=1
S Sb
b
C 拉伸真实应力-应变曲线 在失稳点所作的切线的 斜率为Sb,该切线与横坐 标的交点到失稳点横坐 标间的距离为↔=1,这 就是真实应力-应变曲线 在失稳点上所作切线的 特性。 B
Pb
Ps Pe
o
3
△L
%
变换:P/S0 = σ (MPa) S0 为试样原始截面积(mm2) △L/ L0 = ε ( %) L0 为试样标距长度 转化:纵坐标:以应力σ表示,横坐标:以应变ε表示,
4
真实应力—应变曲线通常是由实验建立,实质上 可以看成是塑性变形时应力应变的实验关系。
5
6
金 属 塑 性 成 形 原 理
• 一、基于拉伸实验确定真实应力—应变曲线
单向拉伸的应力状态为 应变状态为 在单向拉伸时
1,
2 3 0
1 ,
2 3
1
1
2
1
应 力 应 变 曲 线
因此,单向拉伸试验得到的的σ—ε 曲线可以推广到复杂应 力,也就是在这种变形条件下的 曲线,因而具有普遍 意义。
D/H→0, S -∈曲线最低。因摩擦影响消除。但D/H=0的 试样实际上是不存在的。
36
采用外推的方法,间接推出D/H=0的真实应力,进 而求出真实应力-应变曲线。
37
四种圆柱,分别为D/H=0.5,1.0,,2.0,3.0。
第4章 真实应力——应变曲线

一、拉伸图和条件应力-应变曲线
条件应力----应变曲线 最大拉力点b----强度极限。b点以后继续拉伸 ,试样断面出现局部收缩,形成所谓缩颈,此后,应力逐渐减小,曲 线下降,直至k点发生断裂。
对于大多数金属,没有明显的屈服点(屈服平台),典型的应力-应变曲线如下图 所示。这时的屈服应力规定用ε=0.2%时的应力表示,即σ0.2
n=0 理想刚塑性 线弹性
抛物线型真实应力——应变曲线的经验方程
在失稳点b处, 由于
只要知道失稳点的真实应力Sb和对数应变∈b ,抛物线型真实应力——应变曲线方程即可 求得。
(2) 初始屈服应力 的冷变形金属材料
➢刚塑性硬化材料模型 刚塑性非线性硬化材料模型
的数学表达式为
S
➢适合于预先经过冷加工 s
该斜线与横坐标轴的交点到失稳点横坐标的距离为 = 1 。
四、真实应力——应变曲线的简化形式
一般由实验得到的真应力—真应变曲线(等效应力—等效 应变曲线)比较复杂,不能用简单的函数形式来描述,在应用方 面也不方便。因此通常都将实验得到的曲线处理成可以用某种函 数表达的形式
(1)抛物线形状
幂指数硬化材料模型
包申格效应:随加载路线和方向不同而屈服应力降低的现象。
二、拉伸时的真实应力——应变曲线
(一)
真实应力 相对伸长 相对断面收缩
F试样瞬时断面积。
对数应变(真实应变) l——试样的瞬时长度 dl——瞬时的长度改变量
当试样l0拉伸至l1时,总的真实应变为:
在出现缩颈以前,试样处于均匀拉伸状态:
当在小变形时 ,可以认为,
的金属材料。材料在屈 服前为刚性的,屈服后 硬化曲线接近于抛物线
真实应力应变曲线

(0 p)2 ( p p)2 ( p 0)2 22
3p 2
3 2
(1 2 )2 (2 3)2 (3 1)2
3 2
( 3 0)2 (0 3)2 (3 3)2
2 3
3
记录下p和∈3,按上式算出 和 ,画出 ~ 曲线。
在高温变形时温度效应小,变形速度的强化作用显著,动态热变形 时的真实应力—应变曲线比静态时高出很多。
温变形时的动态真实应力—应变曲线比静态时的曲线增高的程度小于 热变形时的情况。
高温时速度影响大,低温时影响小
本章小结
❖ 应力、应变关系的特点 ❖ 增量理论本构方程 ❖ 全量理论本构方程 ❖ 真实应力应变曲线
2、变形速度对真实应力-应变曲线的影响 速度增加→位错运动加快→ 需要更大的切应力→流动应力提高 速度增加→硬化得不到恢复→ 流动应力提高
但如果速度很大→温度效应大→ 流动应力降低
在冷变形时,温度效应显著,强化被软化所抵消,最终表现出的是: 变形速度的影响不明显,动态时的真实应力—应变曲线比静态时略高 一点,差别不大。
基于拉伸实验确定真实应力-应变曲线
2、真实应力-应变曲线 真实应力-应变曲线的绘制 Y- ε曲线, Y- ψ曲线:以σ- ε曲线为基础
A0 l 1
A l0
A A0
1
Y P P (1 ) (1 )
A A0
A0 A 1 A 1 l0
形变形量较大,如锻造≤1.6,反挤≤2.5,拉伸试验曲线不够用。需要
压缩Y- ∈曲线。
压缩试验的优点: ∈压>>1还是均匀变形, ∈可达到2或更大,如 ∈铜=3.9
缺点:摩擦
真实应力—应变曲线拉伸实验
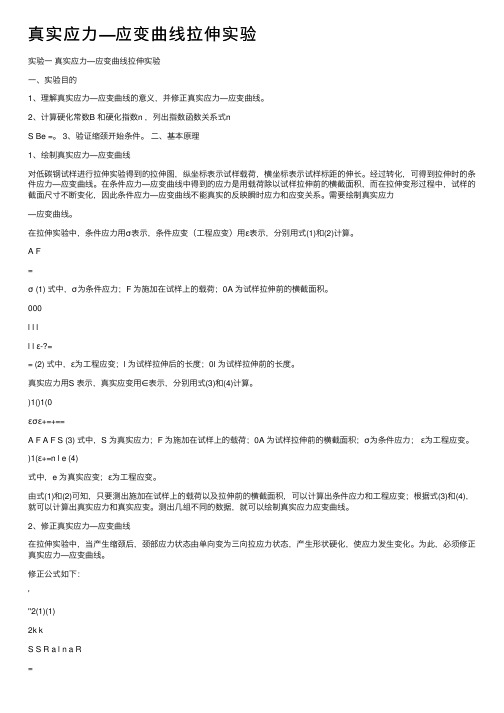
真实应⼒—应变曲线拉伸实验实验⼀真实应⼒—应变曲线拉伸实验⼀、实验⽬的1、理解真实应⼒—应变曲线的意义,并修正真实应⼒—应变曲线。
2、计算硬化常数B 和硬化指数n ,列出指数函数关系式nS Be =。
3、验证缩颈开始条件。
⼆、基本原理1、绘制真实应⼒—应变曲线对低碳钢试样进⾏拉伸实验得到的拉伸图,纵坐标表⽰试样载荷,横坐标表⽰试样标距的伸长。
经过转化,可得到拉伸时的条件应⼒—应变曲线。
在条件应⼒—应变曲线中得到的应⼒是⽤载荷除以试样拉伸前的横截⾯积,⽽在拉伸变形过程中,试样的截⾯尺⼨不断变化,因此条件应⼒—应变曲线不能真实的反映瞬时应⼒和应变关系。
需要绘制真实应⼒—应变曲线。
在拉伸实验中,条件应⼒⽤σ表⽰,条件应变(⼯程应变)⽤ε表⽰,分别⽤式(1)和(2)计算。
A F=σ (1) 式中,σ为条件应⼒;F 为施加在试样上的载荷;0A 为试样拉伸前的横截⾯积。
000l l ll l ε-?== (2) 式中,ε为⼯程应变;l 为试样拉伸后的长度;0l 为试样拉伸前的长度。
真实应⼒⽤S 表⽰,真实应变⽤∈表⽰,分别⽤式(3)和(4)计算。
)1()1(0εσε+=+==A F A F S (3) 式中,S 为真实应⼒;F 为施加在试样上的载荷;0A 为试样拉伸前的横截⾯积;σ为条件应⼒;ε为⼯程应变。
)1(ε+=n l e (4)式中,e 为真实应变;ε为⼯程应变。
由式(1)和(2)可知,只要测出施加在试样上的载荷以及拉伸前的横截⾯积,可以计算出条件应⼒和⼯程应变;根据式(3)和(4),就可以计算出真实应⼒和真实应变。
测出⼏组不同的数据,就可以绘制真实应⼒应变曲线。
2、修正真实应⼒—应变曲线在拉伸实验中,当产⽣缩颈后,颈部应⼒状态由单向变为三向拉应⼒状态,产⽣形状硬化,使应⼒发⽣变化。
为此,必须修正真实应⼒—应变曲线。
修正公式如下:'''2(1)(1)2k kS S R a l n a R=++ (5)式中,''k S 为缩颈处修正的真实应⼒;'k S 为缩颈处没有修正的真实应⼒;a 为缩颈处半径;R 为缩颈处试样外形的曲率半径。
基于压缩试验确定真实应力应变曲线标准版文档

1.由于受到塑性失稳的限制,拉伸实验曲线对数应变 1 .0 左 右 , 其精确段为 0.3内 。 而实际变形的应变往往大得多,因此拉
伸实验曲线是不够用的。 要获得大变形下的真实应力-应变曲线,就需要用到压缩实验。
2.压缩实验需要解决的问题 由于试件与工具之间存在摩擦,就会改变其单向均匀压缩状态, 并出现鼓形。因而,消除接触面间的摩擦是求得真实曲线的关键。
ln
H0 H
式中 H 0 、H 试件压缩前、后的高度压缩时真实应力为来自YP AP
A0e
式中 A 0、A 试件压缩前、后的横截面面积;
P 轴向载荷。
(根2仍出)据缩现保如记时微持果录的裂HD试下真纹件1的实为出,再各应止现重次力鼓复压和形以缩对,上量数需压和应要缩压变将过力。鼓程,形,利车直用去至下,面并公1使式.2试计或件算尺试出寸件压 为伸因伸 伸要为伸(a伸为在式二压 为式根(式 式伸a要根上上在式(伸上图(根为() )了实而实实获了实2实了试中、缩了中据2中中实获据下下试中2实下31据了2) ) ) -) )5减 验 , 验验 得 减 验 验 减 件 实减 记 验 得 记 垫 垫 件 验 垫 记 减基9如如如每如小曲消曲 曲大小曲曲小的验 小录曲大录板板的曲板录小圆、、 、、于、果果果压果接线除线 线变接线线接端需 接下线变下经经端线经下接柱压试试试缩试试试 试试触是接是 是形触是是触面要 触的是形的淬淬面是淬的触压试缩件件件件1件件 件件面不触不 不下面不不面上解 面各不下各火火上不火各面缩0件试出出出出%压压 压压间够面够 够的间够够间车决 间次够的次、、车够、次间实压验现现现现的缩缩 缩缩的用间用 用真的用用的出的 的压用真压回回出用回压的验bb缩确鼓鼓鼓鼓高))前前 前前摩的的的 的实摩的的摩沟问 摩缩的实缩火火沟的火缩摩及前定形 形 形 形度、、 、、擦。摩。。应擦。。擦槽题擦量。应量、、槽。、量擦其、真,,,,,后后 后后,擦力,,或,和力和磨磨或磨和,试后实需需需需记的的 的的可是可可浅可压压削削浅削压可--件的应应应要要要要录横横 横横求坑力力和和坑和力高力变变将将将将一截截 截截得(,,抛抛(抛,度-曲曲鼓鼓鼓鼓次应cc面面 面面真图利利光光图光利))线线形形形形压变面面 面面实用用。。。用33,,车车车车--力曲55积积 积积曲下下下就就99去去去去和线;; ;;线面面面bb需需,,,,实、、的公公公要要并并并并际cc关式式式) )用用使使使使高键计计计,,到到试试试试度。算算算以以压压件件件件,出出出便便缩缩尺尺尺尺并压压压保保实实寸寸寸寸将缩缩缩存存验验仍仍仍仍试时时时润润。。保保保保件的的的滑滑持持持持和真真真垫实实实板应应应擦力力力,,,,再再再再净和和和重重重重,对对对复复复复重数数数以以以以新应应应上上上上加变变变压压压压润。。。缩缩缩缩滑过过过过剂程程程程,,,,,再直直直直重至至至至复上述过程或或或或。试试试试件件件件出出出出现现现现微微微微裂裂裂裂纹纹纹纹为为为为止止止止
拉伸实验报告

拉伸实验报告拉伸实验报告⼀、实验⽬的1、掌握如何正确进⾏拉伸实验的测量;2、通过对拉伸实验的实际操作,测定低碳钢的弹性模量E、屈服极限бs、强度极限бb 、延伸率δ、截⾯收缩率ψ;3、观察在拉伸过程中的各种现象,绘制拉伸图(P―Δ曲线) ;4、通过适当转变,绘制真应⼒-真应变曲线S-e,测定应变硬化指数n ,并了解其实际意义。
⼆、实验器材与设备1、电⼦万能材料试验机(载荷、变形、位移)其设备如下:主机微机处理系统测试控制CSS-442002、变形传感器(引申仪)型号∶YJ Y ―11 标距 L ∶50 mm量程 ΔL ∶ 25mm 3、拉伸试件为了使试验结果具有可⽐性,按GB228-2002规定加⼯成标准试件。
其标准规格为:L 0=5d 0,d 0=10mm 。
试件的标准图样如下:标准试件图样三、实验原理与⽅法1、低碳钢拉伸随着拉伸实验的进⾏,试件在连续变载荷作⽤下经历了弹性变形阶段、屈服阶段、强化阶段以及局部变形阶段这四个阶段。
其拉伸⼒——伸长曲线如下:夹持部分⼯作部分过渡部分弹性阶段屈服阶段强化阶段局部变形阶段低碳钢的拉伸⼒——伸长曲线2、低碳钢弹性模量E的测定在已经获得的拉伸⼒—伸长曲线上取伸长长度约为标距的1%~8%的相互距离适当的两点(本实验选取了伸长为4%和8%的两点),读出其⼒和伸长带⼊相关的计算公式计算出弹性模量E。
3、应变硬化指数n的测定在⾦属整个变形过程中,当外⼒超过屈服强度之后,塑性变形并不是像屈服平台那样连续流变下去,⽽需要不断增加外⼒才能继续进⾏。
这表明⾦属材料有⼀种阻⽌继续塑性变形的能⼒,这就是应变硬化性能。
塑性应变是硬化的原因,⽽硬化则是塑性应变的结果。
应变硬化是位错增值,运动受阻所致。
准确全⾯描述材料的应变硬化⾏为,要使⽤真实应⼒——应变曲线。
因为⼯程应⼒——应变曲线上的应⼒和应变是⽤试样标距部分原始截⾯积和原始标距长度来度量的,并不代表实际瞬时的应⼒和应变。
当载荷超过曲线上最⼤值后,继续变形,应⼒下降,此与材料的实际硬化⾏为不符。
- 1、下载文档前请自行甄别文档内容的完整性,平台不提供额外的编辑、内容补充、找答案等附加服务。
- 2、"仅部分预览"的文档,不可在线预览部分如存在完整性等问题,可反馈申请退款(可完整预览的文档不适用该条件!)。
- 3、如文档侵犯您的权益,请联系客服反馈,我们会尽快为您处理(人工客服工作时间:9:00-18:30)。
实验一 真实应力—应变曲线拉伸实验
一、实验目的
1、理解真实应力—应变曲线的意义,并修正真实应力—应变曲线。
2、计算硬化常数B 和硬化指数n ,列出指数函数关系式n
S Be =。
3、验证缩颈开始条件。
二、基本原理
1、绘制真实应力—应变曲线
对低碳钢试样进行拉伸实验得到的拉伸图,纵坐标表示试样载荷,横坐标表示试样标距的伸长。
经过转化,可得到拉伸时的条件应力—应变曲线。
在条件应力—应变曲线中得到的应力是用载荷除以试样拉伸前的横截面积,而在拉伸变形过程中,试样的截面尺寸不断变化,因此条件应力—应变曲线不能真实的反映瞬时应力和应变关系。
需要绘制真实应力
—应变曲线。
在拉伸实验中,条件应力用σ表示,条件应变(工程应变)用ε表示,分别用式(1)和(2)计算。
A F
=
σ (1) 式中,σ为条件应力;F 为施加在试样上的载荷;0A 为试样拉伸前的横截面积。
000
l l l
l l ε-∆=
= (2) 式中,ε为工程应变;l 为试样拉伸后的长度;0l 为试样拉伸前的长度。
真实应力用S 表示,真实应变用∈表示,分别用式(3)和(4)计算。
)1()1(0
εσε+=+==
A F A F S (3) 式中,S 为真实应力;F 为施加在试样上的载荷;0A 为试样拉伸前的横截面积;σ为条件应力; ε为工程应变。
)1(ε+=n l e (4)
式中,e 为真实应变;ε为工程应变。
由式(1)和(2)可知,只要测出施加在试样上的载荷以及拉伸前的横截面积,可以计算出条件应力和工程应变;根据式(3)和(4),就可以计算出真实应力和真实应变。
测出几组不同的数据,就可以绘制真实应力应变曲线。
2、修正真实应力—应变曲线
在拉伸实验中,当产生缩颈后,颈部应力状态由单向变为三向拉应力状态,产生形状硬化,使应力发生变化。
为此,必须修正真实应力—应变曲线。
修正公式如下:
'
''2(1)(1)
2k k
S S R a l n a R
=
++ (5)
式中,''
k S 为缩颈处修正的真实应力;'
k S 为缩颈处没有修正的真实应力;a 为缩颈处半径;R 为缩颈处试样外形的曲率半径。
实验中只要测出缩颈处直径和缩颈处试样外形的曲率半径,代入式(5),即可求出缩颈处修正后的真实应力。
3、计算硬化常数B 和硬化指数n
假设真实应力—应变曲线可近似地用指数函数关系式(6)来表示
n S Be = (6)
式中,S 为真实应力;B 为硬化常数;n 为硬化指数。
在真实应力—应变曲线中,任取两点,其函数关系式如下:
11n S Be = ; 22n S Be =
两端取对数得:
11l nS l nB nl ne =+ ; 22l nS l nB nl ne =+
整理得:
1122S e l n
nl n S e = 1212(/)(/)
ln S S n ln e e = (7)
将真实应力和真实应变的数值代入式(7), 即可求出硬化指数n 。
将硬化指数n 代入式(6),即可求出硬化常数B 。
从而可以写出指数函数表达式。
4、验证缩颈开始条件
(1) 当应变强化速率与真实应力相等时开始发生缩颈。
计算出缩颈时的真实应力与应变强化速率,比较二者是否相等。
最大载荷点处:
dS
S de
= (2) 缩颈开始时真实应变与加工硬化指数相等。
计算出缩颈时的真实应变与加工硬化指数,比较二者是否相等。
最大载荷点处:n e =
三、实验方法和步骤
1、采用低碳钢试样,拉伸前在试样上打好标距,并测出其直径。
2、把试样在试验机上进行拉伸,直至断裂为止,记录屈服载荷,最大拉伸载荷以及断裂载荷。
3、从试验机上卸下试样,测量拉伸后试样的总长度,试样拉伸后的直径,缩颈断裂处
的半径,缩颈部分圆弧对应弦长度。
4、计算屈服时刻、最大载荷时刻以及断裂时刻对应的条件应力、工程应变,真实应力和真实应变,并绘制出没有经过修正的真实应力应变曲线。
5、计算缩颈处试样外形的曲率半径,根据公式(5)计算断裂处的真实应力,修正真实应力—应变曲线。
6、在真实应力—应变曲线中任取两点,计算其真实应力和真实应变,根据公式(6) 和
(7)计算硬化常数和硬化指数,并写出指数函数表达式。
四、实验报告要求
1、列出实验数据,记录在表1中。
2、分别绘制出没有修正以及经过修正后的真实应力—应变曲线。
3、计算硬化常数和硬化指数,并写出指数函数表达式。
4、通过计算验证是否满足缩颈开始条件。
表1 拉伸前后实验数据。