非高炉炼铁第三章重点设备介绍(上)
(完整版)高炉炼铁工艺流程及主要设备简介
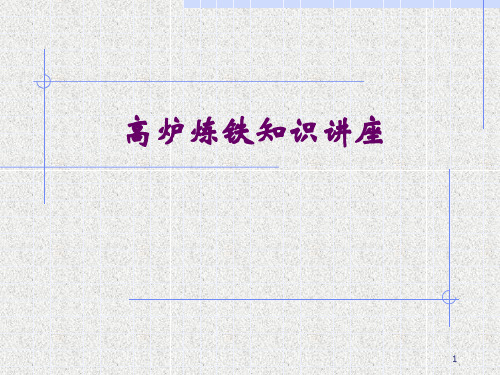
三、高炉冶炼主要设备简介
1、高炉 高炉炉本体较为复杂。 横断面为圆形的炼铁竖炉。用 钢板作炉壳,壳内砌耐火砖内衬。高炉本体自上而下 分为炉喉、炉身、炉腰、炉腹 、炉缸5部分。高炉生 产时从炉顶装入铁矿石、焦炭、造渣用熔剂(石灰 石),从位于炉子下部沿炉周的风口吹入经预热的空 气。在高温下焦炭中的碳同鼓入空气中的氧燃烧生成 的一氧化碳和氢气,在炉内上升过程中除去铁矿石中 的氧,从而还原得到铁。炼出的铁水从铁口放出。铁 矿石中未还原的杂质和石灰石等熔剂结合生成炉渣, 从渣口排出。产生的煤气从炉顶排出,经除尘后,作 为热风炉、加热炉、焦炉、锅炉等的燃料。高炉冶炼 的主要产品是生铁 ,还有副产高炉渣和高炉煤气。
1—高炉;2—重力除尘器;3 — 布袋除尘器; 4—调压阀组
23
三、高炉冶炼主要设备简介 重力除尘
24
三、高炉冶炼主要设备简介
箱体除尘: 由重力除尘后的荒煤气进入箱体进行布 袋过滤,最后成为净煤气。要求净煤气 粉尘量小于10毫克。
25
高炉冶炼主要设备简介
刮板机
26
高炉冶炼主要设备简介
27
高炉冶炼主要设备简介
炉渣和生铁定期通过铁口外排。通过炉前撇渣器进行渣 铁分离,铁水通过铁水罐运到炼钢或铸铁。炉渣经过 水淬后,输送到渣场。
高炉炼铁的主产品是生铁,副产品是高炉煤气、水渣、 炉尘。
5
二、高炉炼铁原理
6
三、高炉冶炼主要设备简介
高护炼铁设备组成有:①高炉本体;②供料设备;③ 送风设备;④喷吹设备;⑤煤气处理设备;⑥渣铁处 理设备。 通常,辅助系统的建设投资是高炉本体的4~5倍。生 产中,各个系统互相配合、互相制约,形成一个连续 的、大规模的高温生产过程。高炉开炉之后,整个系 统必须日以继夜地连续生产,除了计划检修和特殊事 故暂时休风外,一般要到一代寿命终了时才停炉。 高炉炼铁系统(炉体系统、渣处理系统、上料系统、 除尘系统、送风系统)主要设备简要介绍一下。
非高炉炼铁

非高炉炼铁一、非高炉炼铁的发展高炉炼铁是炼铁生产的主题,经过长期的发展,它的技术已经非常成熟。
但它也存在固有的不足,即对冶金焦的强烈依赖。
但随着焦煤资源的日渐贫乏,冶金焦价格越来越高。
因此,使炼铁生产摆脱对冶金焦的依赖是开发非高炉炼铁的原动力。
经过数百年的发展,至今已形成了以直接还原和熔融还原为主的现代化非高炉炼铁工业体系。
现代化钢铁工艺流程主体由四部分构成,焦炉、造块设备(例如烧结机)、高炉和转炉。
高炉使用冶金焦为主题能源,他是由焦煤经炼焦得到。
高炉的产品是液态生铁,它经转炉冶炼成转炉钢。
熔融还原的产品相当于高炉铁水。
高炉使用冶金焦,熔融反应则使用非焦煤。
这样就使炼铁摆脱了对冶金焦的依赖。
直接还原的产品是在熔点以下还原得到固态金属铁,称为直接还原铁(DRI),又称海绵铁。
直接还原的流程可分为煤基直接还原、气基直接还原和电热直接还原三大类。
煤基直接还原以煤为主要能源,主要是使用回转炉为主体设备的流程。
气基直接还原以天然气为主题能源。
包括竖炉、反应罐和流化床流程。
电热直接还原以电力为主要能源,是使用电热竖炉直接还原流程。
熔融还原的主体能源主要分为三种:非焦煤,焦炭和电力。
熔炼设备是熔融还原流程的精华。
还原设备决定了适用原料的性质。
例如流化床可直接处理粉料,竖炉则适用于处理块状炉料。
二、重点设备分析直接还原的核心装置是一个还原单元。
占有重要地位的还原设备有竖炉,反应罐,回转炉和流化床。
熔融还原的核心装置时一个还。
原单元和一个熔炼造气单元。
最受重视的还原设备是竖炉和流化床,最重要的熔炼造气设备是煤炭流化床和铁浴炉。
竖炉是一种成熟的还原设备。
除了产量在海绵铁工业中高居榜首外,熔融还原也将它作为还原单元最实际的选择。
目前唯一的工业化二步法熔融还原流程COREX即使用竖炉还原单元。
作为还原设备,流化床的地位非常微妙。
海绵铁工业中流化床的生产能力并不大。
但他具有一个竖炉无法比拟的优点:可直接使用粉矿。
这个特点使流化床成为熔融还原中最受青睐的还原设备。
《钢铁是怎样炼成的》每章概括(精简版)
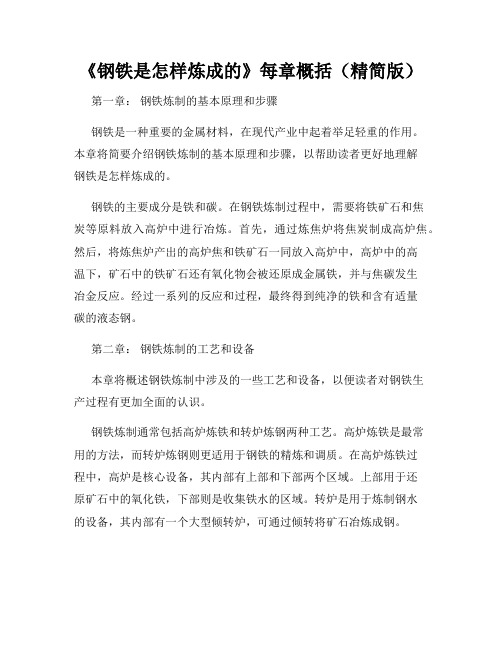
《钢铁是怎样炼成的》每章概括(精简版)第一章:钢铁炼制的基本原理和步骤钢铁是一种重要的金属材料,在现代产业中起着举足轻重的作用。
本章将简要介绍钢铁炼制的基本原理和步骤,以帮助读者更好地理解钢铁是怎样炼成的。
钢铁的主要成分是铁和碳。
在钢铁炼制过程中,需要将铁矿石和焦炭等原料放入高炉中进行冶炼。
首先,通过炼焦炉将焦炭制成高炉焦。
然后,将炼焦炉产出的高炉焦和铁矿石一同放入高炉中,高炉中的高温下,矿石中的铁矿石还有氧化物会被还原成金属铁,并与焦碳发生冶金反应。
经过一系列的反应和过程,最终得到纯净的铁和含有适量碳的液态钢。
第二章:钢铁炼制的工艺和设备本章将概述钢铁炼制中涉及的一些工艺和设备,以便读者对钢铁生产过程有更加全面的认识。
钢铁炼制通常包括高炉炼铁和转炉炼钢两种工艺。
高炉炼铁是最常用的方法,而转炉炼钢则更适用于钢铁的精炼和调质。
在高炉炼铁过程中,高炉是核心设备,其内部有上部和下部两个区域。
上部用于还原矿石中的氧化铁,下部则是收集铁水的区域。
转炉是用于炼制钢水的设备,其内部有一个大型倾转炉,可通过倾转将矿石冶炼成钢。
除了高炉和转炉之外,钢铁炼制还涉及到一系列的辅助设备,比如炼焦炉、氧气压缩机、脱硫设备等。
这些设备在钢铁炼制过程中扮演重要的角色,确保产出的钢铁质量稳定。
第三章:钢铁炼制的环境和能源问题钢铁炼制是一个能耗较高且对环境有一定影响的过程。
本章将简要介绍钢铁炼制所面临的环境和能源问题,并探讨一些改进措施。
在钢铁炼制过程中,需要大量的能源供给,尤其是炼铁过程中需要高温下的燃烧反应。
这不仅导致能源的消耗,也会对环境产生影响,如二氧化碳和其他废气的排放。
钢铁企业逐渐采用清洁能源、提高能源利用效率和优化生产工艺等措施来减少环境和能源问题。
此外,钢铁炼制还会产生一定的固体废弃物和水污染。
为了解决这些问题,钢铁企业也在积极探索废弃物资源化利用和水资源回收利用等措施,以减少对环境的负面影响。
第四章:钢铁炼制的发展趋势和挑战最后一章将简要讨论钢铁炼制的发展趋势和当前面临的挑战。
非高炉炼铁--重点设备介绍
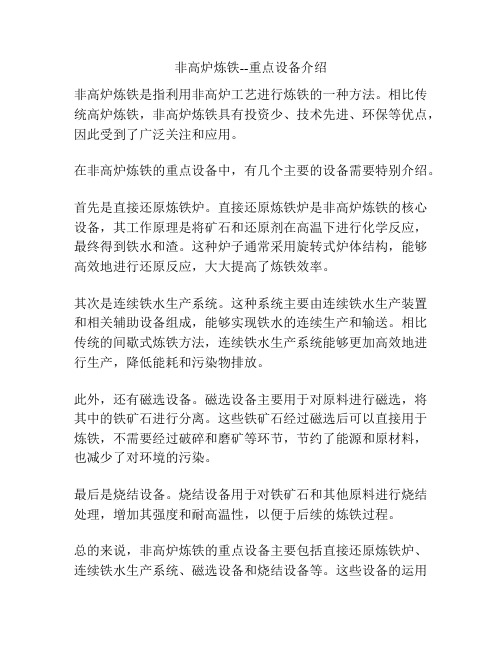
非高炉炼铁--重点设备介绍
非高炉炼铁是指利用非高炉工艺进行炼铁的一种方法。
相比传统高炉炼铁,非高炉炼铁具有投资少、技术先进、环保等优点,因此受到了广泛关注和应用。
在非高炉炼铁的重点设备中,有几个主要的设备需要特别介绍。
首先是直接还原炼铁炉。
直接还原炼铁炉是非高炉炼铁的核心设备,其工作原理是将矿石和还原剂在高温下进行化学反应,最终得到铁水和渣。
这种炉子通常采用旋转式炉体结构,能够高效地进行还原反应,大大提高了炼铁效率。
其次是连续铁水生产系统。
这种系统主要由连续铁水生产装置和相关辅助设备组成,能够实现铁水的连续生产和输送。
相比传统的间歇式炼铁方法,连续铁水生产系统能够更加高效地进行生产,降低能耗和污染物排放。
此外,还有磁选设备。
磁选设备主要用于对原料进行磁选,将其中的铁矿石进行分离。
这些铁矿石经过磁选后可以直接用于炼铁,不需要经过破碎和磨矿等环节,节约了能源和原材料,也减少了对环境的污染。
最后是烧结设备。
烧结设备用于对铁矿石和其他原料进行烧结处理,增加其强度和耐高温性,以便于后续的炼铁过程。
总的来说,非高炉炼铁的重点设备主要包括直接还原炼铁炉、连续铁水生产系统、磁选设备和烧结设备等。
这些设备的运用
使得非高炉炼铁在提高炼铁效率、降低成本、减少环境污染等方面具有显著优势。
随着科技的不断发展,相信非高炉炼铁的设备和工艺会更加完善,为炼铁行业的可持续发展做出更大的贡献。
帮您了解高炉炼铁所用主要设备!因为了解,所以更专业!
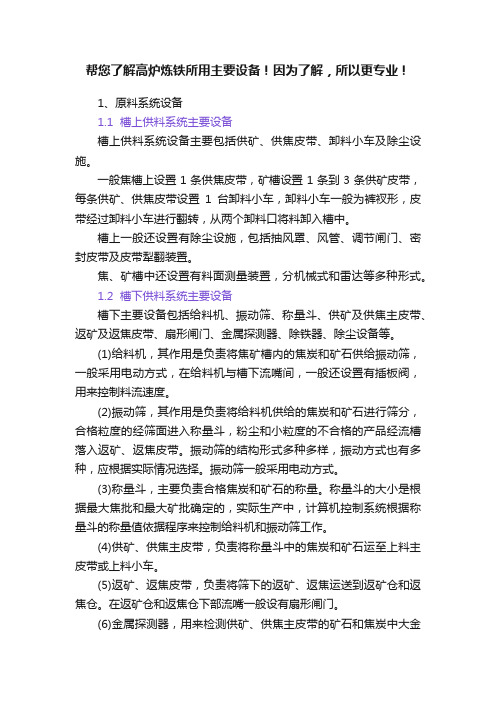
帮您了解高炉炼铁所用主要设备!因为了解,所以更专业!1、原料系统设备1.1 槽上供料系统主要设备槽上供料系统设备主要包括供矿、供焦皮带、卸料小车及除尘设施。
一般焦槽上设置1条供焦皮带,矿槽设置1条到3条供矿皮带,每条供矿、供焦皮带设置1台卸料小车,卸料小车一般为裤衩形,皮带经过卸料小车进行翻转,从两个卸料口将料卸入槽中。
槽上一般还设置有除尘设施,包括抽风罩、风管、调节闸门、密封皮带及皮带犁翻装置。
焦、矿槽中还设置有料面测量装置,分机械式和雷达等多种形式。
1.2 槽下供料系统主要设备槽下主要设备包括给料机、振动筛、称量斗、供矿及供焦主皮带、返矿及返焦皮带、扇形闸门、金属探测器、除铁器、除尘设备等。
(1)给料机,其作用是负责将焦矿槽内的焦炭和矿石供给振动筛,一般采用电动方式,在给料机与槽下流嘴间,一般还设置有插板阀,用来控制料流速度。
(2)振动筛,其作用是负责将给料机供给的焦炭和矿石进行筛分,合格粒度的经筛面进入称量斗,粉尘和小粒度的不合格的产品经流槽落入返矿、返焦皮带。
振动筛的结构形式多种多样,振动方式也有多种,应根据实际情况选择。
振动筛一般采用电动方式。
(3)称量斗,主要负责合格焦炭和矿石的称量。
称量斗的大小是根据最大焦批和最大矿批确定的,实际生产中,计算机控制系统根据称量斗的称量值依据程序来控制给料机和振动筛工作。
(4)供矿、供焦主皮带,负责将称量斗中的焦炭和矿石运至上料主皮带或上料小车。
(5)返矿、返焦皮带,负责将筛下的返矿、返焦运送到返矿仓和返焦仓。
在返矿仓和返焦仓下部流嘴一般设有扇形闸门。
(6)金属探测器,用来检测供矿、供焦主皮带的矿石和焦炭中大金属件,以免损坏皮带和炉顶设备。
(7)除铁器,用来清除矿石和焦炭中金属件。
(8)除尘设备,主要包括抽风罩、风管、调节闸门。
一般槽上槽下共用一台除尘器,分电除尘和布袋除尘两种。
电除尘器运行可靠、费用低,但除尘效果不如布袋除尘好。
布袋除尘运行费用高、维护量大,但除尘效果好。
第三章_非高炉炼铁重点设备介绍(下)
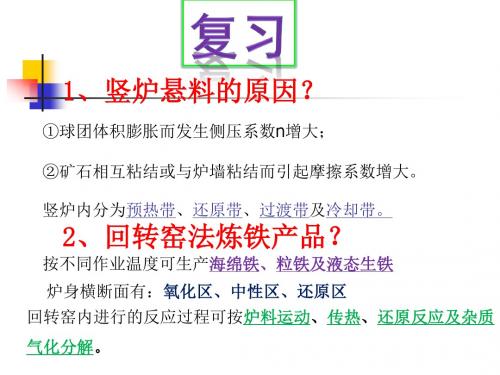
3.2.2 流化参数
临界流化条件:气流对料层向上的摩擦力等于料层的 质量。由此可得: 整理得:
式中: S——流化床截面积;Lmf——临界流化床高度; εmf——临界流化床孔隙率;ρs——固体颗粒密度。 固定床压将为:
umf的二次方程:
如Rep很低,压降以粘度损失为主,忽略动能损失, 有: 很高,压降以动能损失为主可忽略粘度损失,有:
3.4 熔炼造气煤炭流化床
3.4.1 熔炼煤的有效热值
热收入——煤的燃烧; CH4和H2O比例很低,可忽略H2的热效应; 干基热量为Qd;
煤在熔炼过程中放出的全部热量(Q)为碳素燃烧热和煤灰成渣热之和,
Q包括造气热(Qg,干基造气热Qgd)和熔炼煤的有效热值(Qe,干基有
效热值Qed);
Du和Pu是粒度的函数。
粒度较小(0.1mm)时, pu较大,ut和umf相对差别很
大,u0的控制和床层的提高
较容易。利于提高产率和还 原气体利用率。但粒度太低, 易粘结失流。
粒度较大时,Du较大,流速控
制容易。但umf提高幅度较ut显著, 会造成床层极限高度Lmax降低和 还原气利用率降低的问题。
1、竖炉悬料的原因?
①球团体积膨胀而发生侧压系数n增大;
②矿石相互粘结或与炉墙粘结而引起摩擦系数增大。
竖炉内分为预热带、还原带、过渡带及冷却带。
2、回转窑法炼铁产品?
按不同作业温度可生产海绵铁、粒铁及液态生铁 炉身横断面有:氧化区、中性区、还原区 回转窑内进行的反应过程可按炉料运动、传热、还原反应及杂质 气化分解。
3.3.4 还原速度与气体利用率
流化床的反应条件:
匀,尾气还原需最低与FeO和Fe平衡,还原气利用率
高炉安全生产的主要工艺过程及主要设备(三篇)
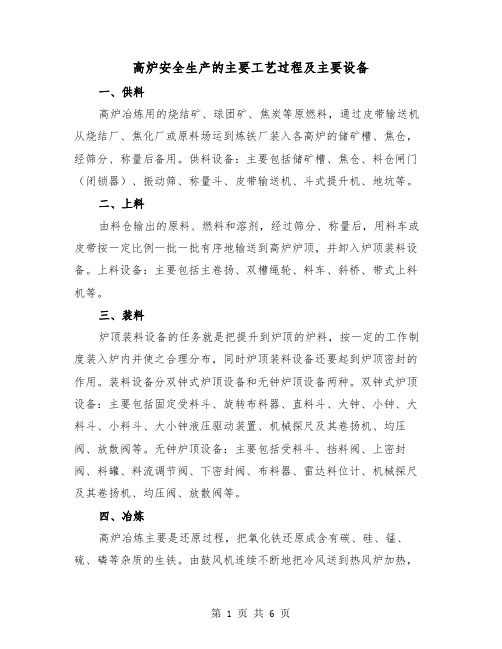
高炉安全生产的主要工艺过程及主要设备一、供料高炉冶炼用的烧结矿、球团矿、焦炭等原燃料,通过皮带输送机从烧结厂、焦化厂或原料场运到炼铁厂装入各高炉的储矿槽、焦仓,经筛分、称量后备用。
供料设备:主要包括储矿槽、焦仓、料仓闸门(闭锁器)、振动筛、称量斗、皮带输送机、斗式提升机、地坑等。
二、上料由料仓输出的原料、燃料和溶剂,经过筛分、称量后,用料车或皮带按一定比例一批一批有序地输送到高炉炉顶,并卸入炉顶装料设备。
上料设备:主要包括主卷扬、双槽绳轮、料车、斜桥、带式上料机等。
三、装料炉顶装料设备的任务就是把提升到炉顶的炉料,按一定的工作制度装入炉内并使之合理分布,同时炉顶装料设备还要起到炉顶密封的作用。
装料设备分双钟式炉顶设备和无钟炉顶设备两种。
双钟式炉顶设备:主要包括固定受料斗、旋转布料器、直料斗、大钟、小钟、大料斗、小料斗、大小钟液压驱动装置、机械探尺及其卷扬机、均压阀、放散阀等。
无钟炉顶设备:主要包括受料斗、挡料阀、上密封阀、料罐、料流调节阀、下密封阀、布料器、雷达料位计、机械探尺及其卷扬机、均压阀、放散阀等。
四、冶炼高炉冶炼主要是还原过程,把氧化铁还原成含有碳、硅、锰、硫、磷等杂质的生铁。
由鼓风机连续不断地把冷风送到热风炉加热,再通过炉缸周围的风口进入高炉。
由炉顶加入的焦炭和风口鼓入的热空气等燃烧后产生大量的煤气和热量,使矿石源源不断地熔化、还原。
产生的铁水和熔渣储存在高炉炉缸内,定期地由铁口和渣口排出。
主要设备有热风炉设备、高炉炉体设备等。
热风炉设备:主要包括热风炉本体、燃烧器、冷风阀、热风阀、切断阀、调节阀、烟道阀、倒流休风阀、混风阀、助燃风机、引风机、热管换热器、热风直管等。
高炉炉体设备:主要包括高炉本体、煤气上升管、煤气下降管、风口装置(包括鹅颈管、短接、弯头、直吹管、风口套等)、高炉冷却设备(包括冷却壁、冷却板、支梁水箱等)等。
五、产品处理在渣铁处理中,出铁前先从渣口放出熔渣,流入渣罐车的炉渣运至渣场或就在炉前冲成水渣。
第3章高炉炼铁设备
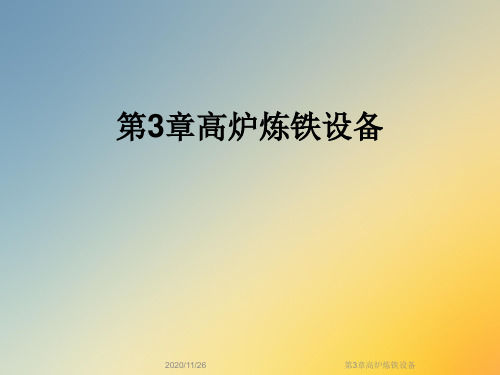
• 碱性熔剂— 石灰、 • 石灰石、白云石 • 酸性熔剂— 硅石 • 特殊熔剂— 萤石
• 高炉、转炉炉尘 • 残铁 • 轧钢铁皮 • 硫酸渣
•高炉炼 第3章高炉炼铁设备
•高炉炼铁基本概念 •3. 1
•高炉燃料
•固体燃料
•气体燃料
•焦 炭
•煤 粉 •焦炉煤气
•高炉煤气
•用于高炉本体
•用于热风炉
•高炉炼 第3章高炉炼铁设备
•
燃料比:550kg/tFe
•
综合焦比:535kg/tFe
•
冶炼强度:0.822t/m3·d
•高炉炼 第3章高炉炼铁设备
•高炉炼铁工艺设备 •3.
•3.2.1 高炉本体(Blast Furnace Body)
2
➢ 钢结构 ➢ 炉衬 ➢ 冷却设备 ➢ 送风装置 ➢ 检测仪器设备
•高炉炼 第3章高炉炼铁设备
• 一般为0.8 ~ 1.0 t/(m3·d)
•7、综合冶炼强度(I∑)
• 定义:将喷入高炉的煤粉折算成相应数量的焦炭后计算的冶炼
强度[t/(m3·d)]
• 大型或超大型高炉达到1.2 ~ 1.6 t/(m3·d)
•高炉炼 第3章高炉炼铁设备
•高炉炼铁基本概念 •3. 1
•高炉有效容积利用系数=冶炼强度/焦比
第3章高炉炼铁设备
2020/11/26
第3章高炉炼铁设备
•高炉炼铁基本概念 •3.
• 高炉炼铁 是为炼钢提供铁原料的主要方法
1
•高炉在钢铁联合企业中的地位
•高炉炼 第3章高炉炼铁设备
•高炉炼铁基本概念 •3. 1
•高炉原料
•铁矿石
•熔 剂
•其他含铁代用 品
• 天然块矿 • 人造富矿 • 烧结矿 • 球团矿
炼铁机械设备介绍(PPT 60页)

• 冲制箱是对熔渣进行水淬粒化熔渣的 设备, 主要由箱体、 喷嘴板、 喷嘴 组成。主要规格:喷嘴开孔板面积: 上室 24040 ㎜ 2,下室 28947 ㎜ 2; 喷嘴出水压力 0.22-0.25Mpa;进水口 法兰 DN500mm。
4.热风炉设备
• 高炉配三座顶燃式热风炉。采用高炉煤气作为燃 料,在拱顶设有环形陶瓷主燃烧器,燃烧完全、 稳定,烟气分布均匀,燃烧效率高。燃烧产生的 高温烟气在蓄热室断面上分布均匀,新型的格子 砖加热面积大、传热系数高,改善了蓄热室的换 热效果,容易实现高风温;热风炉拱顶、炉墙、 格幼┘ 挛榷ㄐ裕徊捎热风炉废气预热技术,预热助燃空 气与煤气,提高热风炉的燃烧温度和热风温度。3 座热风炉设置 2 台助燃风机,一用一备。
故障及处理
• 2.1各阀或翻板不摆动故障,翻板轴部卡料 (清理)、液压阀卡阀(捅阀或更换)、 液压缸内泄(更换)、液压管道漏油或胶 管崩裂(焊接或更换)、接头密封失效泄 漏(更换);
2.2无法均压或罐压放不掉:液压缸与阀 杆、阀杆与阀盖联接失效脱开(重新联 接)、液压系统故障; 2.3料流调节角度失控:液压油有杂质 (化验并更换)、比例阀坏(更换)、 液控单向阀泄漏(更换)、连杆销轴间 隙大(更换);
• 液压系统出现故障有大多原因是由于液压 油不清洁所引起,因此,保持液压油的
• 清洁度是日常维护工作的主要内容之一。 液压站一般均设有循环过滤系统,应经常 开动过滤器并检查其滤芯,每月检查一次 液压油的清洁度,应达到NAS10~11级。检 查液压系统时注意不要使灰尘和污物进入 此系统。
• KD400型液压泥炮本体上的大部分O形密 封圈及V型圈等均采用广州机床研究所密封 分析产品。本体上多处铜套采用自润滑铜 套,不用注入润滑油脂,使用寿命在半年 至一年以上,不过应3个月检查一次,如出 现间隙过大时,应更换新自润滑铜套。
炼铁设备知识点总结
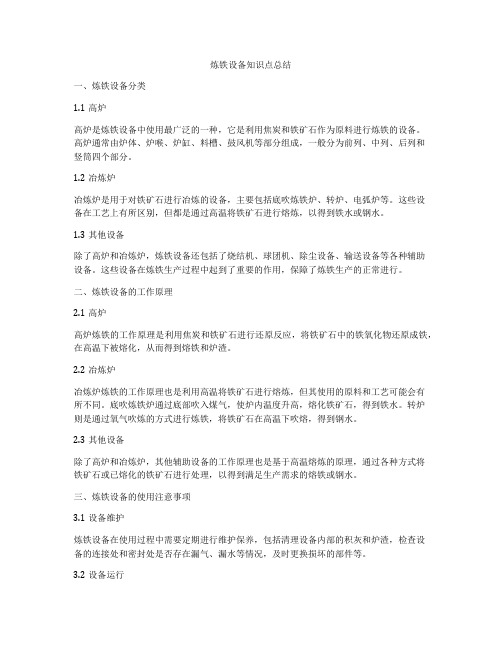
炼铁设备知识点总结一、炼铁设备分类1.1高炉高炉是炼铁设备中使用最广泛的一种,它是利用焦炭和铁矿石作为原料进行炼铁的设备。
高炉通常由炉体、炉喉、炉缸、料槽、鼓风机等部分组成,一般分为前列、中列、后列和竖筒四个部分。
1.2冶炼炉冶炼炉是用于对铁矿石进行冶炼的设备,主要包括底吹炼铁炉、转炉、电弧炉等。
这些设备在工艺上有所区别,但都是通过高温将铁矿石进行熔炼,以得到铁水或钢水。
1.3其他设备除了高炉和冶炼炉,炼铁设备还包括了烧结机、球团机、除尘设备、输送设备等各种辅助设备。
这些设备在炼铁生产过程中起到了重要的作用,保障了炼铁生产的正常进行。
二、炼铁设备的工作原理2.1高炉高炉炼铁的工作原理是利用焦炭和铁矿石进行还原反应,将铁矿石中的铁氧化物还原成铁,在高温下被熔化,从而得到熔铁和炉渣。
2.2冶炼炉冶炼炉炼铁的工作原理也是利用高温将铁矿石进行熔炼,但其使用的原料和工艺可能会有所不同。
底吹炼铁炉通过底部吹入煤气,使炉内温度升高,熔化铁矿石,得到铁水。
转炉则是通过氧气吹炼的方式进行炼铁,将铁矿石在高温下吹熔,得到钢水。
2.3其他设备除了高炉和冶炼炉,其他辅助设备的工作原理也是基于高温熔炼的原理,通过各种方式将铁矿石或已熔化的铁矿石进行处理,以得到满足生产需求的熔铁或钢水。
三、炼铁设备的使用注意事项3.1设备维护炼铁设备在使用过程中需要定期进行维护保养,包括清理设备内部的积灰和炉渣,检查设备的连接处和密封处是否存在漏气、漏水等情况,及时更换损坏的部件等。
3.2设备运行炼铁设备在运行过程中需要严格遵守相关的操作规程,严禁超负荷运行或超过设备的设计参数进行操作。
在使用过程中要密切关注设备的运行状态,及时处理异常情况。
3.3安全生产炼铁设备是属于高温高压设备,在使用过程中必须严格遵守安全操作规程,做好防火防爆措施,保障生产人员的人身安全。
3.4环保要求炼铁设备在使用过程中也需要关注其对环境的影响,采取相应的措施减少排放物对环境的影响,同时符合国家相关的环保标准和要求。
高炉炼铁设备详解
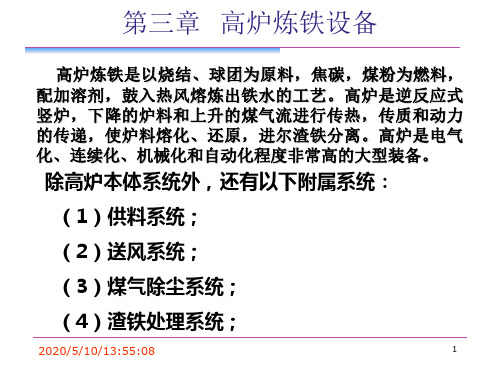
2013-5-8/10:40:16
26
铁合金
铁合金是指铁与一种或几种元素组成的中间 合金,主要用于炼钢脱氧或作为合金添加剂, 当采用金属热还原法生产其它铁合金和有色 金属时作还原剂(详见第七章)。如:硅铁、 锰铁。
2013-5-8/10:40:16
27
炉渣
炉渣是炉料在冶炼过程中不能进到生铁和 钢中的氧化物、硫化物等形成的熔融体。 其主要成分是CaO、MgO、SiO2、 Al2O3等。 根据冶炼方法的不同,钢铁生产产生的炉 渣分为高炉渣和炼钢渣,按炉渣中含有不 同的化学成分又可分为碱性渣和酸性渣。
50热风炉热风炉是高温热交换器热风炉是高温热交换器燃烧高炉煤气加热耐火砖蓄燃烧高炉煤气加热耐火砖蓄热体热体通过热交换使高炉鼓风预热到约通过热交换使高炉鼓风预热到约12001200再鼓入高炉风口内进行燃烧高炉风口内进行燃烧
第三章 高炉炼铁设备
高炉炼铁是以烧结、球团为原料,焦碳,煤粉为燃料, 配加溶剂,鼓入热风熔炼出铁水的工艺。高炉是逆反应式 竖炉,下降的炉料和上升的煤气流进行传热,传质和动力 的传递,使炉料熔化、还原,进尔渣铁分离。高炉是电气 化、连续化、机械化和自动化程度非常高的大型装备。
2013-5-8/10:40:16
5
原料供应系统
皮带上料↓
上料系统↑
2013-5-8/10:40:16 2013-5-8/10:40:16
6
6
2013-5-8/10:40:16
7
2013-5-8/10:40:16
武钢五号高炉上料主皮带
8
送风系统
2013-5-8/10:40:16
9
任务是保证连续可靠地供给高炉冶炼
31
2013-5-8/10:40:16
金属冶炼中的设备及工具介绍

汇报人:可编辑 2024-01-06
CONTENTS
目录
• 金属冶炼设备 • 金属冶炼工具 • 金属冶炼中的安全设备与工具 • 新技术与未来发展
CHAPTER
ห้องสมุดไป่ตู้01
金属冶炼设备
炼铁设备
01
02
03
高炉
用于将铁矿石还原成液态 铁,是炼铁过程中最主要 的设备。
直接还原炉
采用非高炉炼铁工艺,通 过直接还原方式将铁矿石 转化为海绵铁。
用于金属板材和管材的轧制,根据用途可分为热轧机 和冷轧机。
矫直机
用于对轧制后的金属板材进行矫直,提高板材的平直 度和表面质量。
剪切机
用于金属板材和管材的定尺剪切,以满足不同规格和 长度要求。
CHAPTER
02
金属冶炼工具
耐火材料
耐火材料
性能
在金属冶炼过程中,耐火材料是必不 可少的工具之一。它能够承受高温环 境,为金属熔炼提供良好的保护。
新材料的应用
高性能耐火材料
研发和采用高性能的耐火材料,提高冶炼设备的耐高温、耐磨损 性能,延长设备使用寿命。
新型过滤材料
采用新型的过滤材料,对金属溶液进行高效过滤,提高产品质量和 减少废品率。
高强度结构材料
采用高强度结构材料,减轻设备重量,提高设备刚度和稳定性,降 低能耗和生产成本。
自动化与智能化发展
耐火材料的性能主要取决于其化学成 分、矿物组成和显微结构。优质的耐 火材料应具备较高的耐火度、热稳定 性和抗侵蚀性。
种类
耐火材料有多种类型,如粘土、高岭 土、莫来石等,它们具有不同的物理 和化学性质,适用于不同的冶炼工艺 。
冶炼炉辅助工具
非高炉炼铁技术重点是以煤代焦 DRI最佳装备是煤基竖炉

非高炉炼铁技术重点是以煤代焦 DRI最佳装备是煤基竖炉陈守明我国粗钢产量连续高速增长,2011年达6.995亿吨,占全球粗钢产量45%;但产业结构不合理,工艺以高炉炼铁-转炉炼钢长流程为主,铁钢比高、电炉钢比例小,能源资源消耗大、生产成本高,经济效益一路下滑,优化结构、节能增效势在必行。
直接还原铁(DRI)不仅是一种重要的冶金原料,由于不以焦炭为主要能源,称非高炉炼铁,是一种节能增效的冶金新工艺。
发展DRI产业不仅可以为电炉炼钢、转炉炼钢、高炉炼铁、铸造等产业提供大量优质冶金炉料,有助于这些企业节能增效,而且节省大量焦炭,对于缓减高炉炼铁焦炭供应紧张局面、降低成本有利。
同时,国内中小铁矿和非炼焦煤的综合利用、提高附加值,可促进中西部地区经济发展。
国家工信部2011年底颁发的《钢铁工业“十二五”发展规划》中,“重点领域和任务”的技术创新重点第一项即非高炉炼铁技术。
中国DRI多年来产量始终在几十万吨徘徊,主要因为工艺、装备未根据国情自主创新,未显示节能减排优势,工程投资大、生产成本高,经济效益不理想。
DRI工艺按还原剂分为气基法和煤基法,按主体设备分有竖炉法、隧道窑法、回转窑法、转底炉法等。
根据冶金原理和中国能源资源结构、经济技术条件,煤基法比较适宜;按机械和热工原理,这几类工业炉窑虽然都能生产DRI,但竖炉是其优选优化成果,性能更好。
炼铁理论和生产实践均可证明,煤基竖炉DRI能耗低、工程投资少,可取的更好效益。
1 煤基竖炉DRI工艺节能的理论根据1.1 DRI流程短炼铁是钢铁冶金上游工序。
考察钢铁生产流程,如图1所示,流程最短、能耗最低路线是从铁矿石直接炼钢的虚线ideal Route。
但这一路线很难实现,因为还原与升温同时进行,高温下金属铁融化后,还原剂中的碳即渗入铁中,铁水含碳量大于钢的标准。
为了得到含碳量较低的钢,不得不增加炼钢工序,将铁水中的碳再氧化脱去。
现代钢铁生产的高炉-转炉炼钢流程就是这样,称作二步法炼钢。
非高炉炼铁重点设备介绍(上)56页共58页文档

36、如果我们国家的法律中只有某种 神灵, 而不是 殚精竭 虑将神 灵揉进 宪法, 总体上 来说, 法律就 会更好 。—— 马克·吐 温 37、纲纪废弃之日,便是暴政兴起之 时。— —威·皮 物特
38、若是没有公众舆论的支持,法律 是丝毫 没有力 量的。 ——菲 力普斯 39、一个判例造出另一个判例,它们 迅速累 聚,进 而变成 法律。 ——朱 尼厄斯
40、人类法律,事物有规律,这是不 容忽视 的。— —爱献 生
谢谢!
36、自己的鞋子,自己知道紧在哪里。——西班牙
37、我们唯一不会改正的缺点是软弱。——拉罗什福科
xiexie! 38、我这个人走得很慢,但是我从不后退。——亚伯拉罕·林肯
39、勿问成功的秘诀为何,且尽全力做你应该做的事吧。——美华纳
40、学而不思则罔,思而不学则殆。——孔子
高炉炼铁工艺流程及主要设备简介
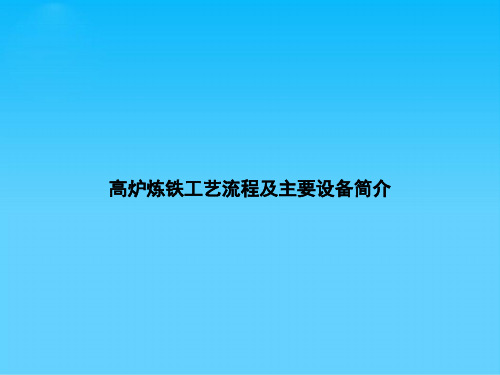
二、高炉炼铁原理
三、高炉冶炼主要设备简介
高护炼铁设备组成有:①高炉本体;②供料设备;③ 送风设备;④喷吹设备;⑤煤气处理设备;⑥渣铁处 理设备。 通常,辅助系统的建设投资是高炉本体的4~5倍。生 产中,各个系统互相配合、互相制约,形成一个连续 的、大规模的高温生产过程。高炉开炉之后,整个系 统必须日以继夜地连续生产,除了计划检修和特殊事 故暂时休风外,一般要到一代寿命终了时才停炉。 高炉炼铁系统(炉体系统、渣处理系统、上料系统、 除尘系统、送风系统)主要设备简要介绍一下。
一、高炉炼铁工艺流程详解
炼铁工艺流程图
烧结料 球团料 焦炭 杂品
上料皮带机 振筛
槽下振筛
中
料仓
皮带机
间 仓
铁包 铁路 炼钢
铁 水 沟
渣铁 分离器
铁水大沟
料车
高炉
渣 沟
冲渣水管道
渣沟
供回 水水 管管 道道
净环水泵房
冷却塔
鼓风机
热风炉
助燃风机
煤气外网管道
重力 除尘
布袋 除尘
调压阀组 TRT发电
渣池 水渣场
下密接近开关
三、高炉冶炼主要设备简介
气密箱(布料器) 喉管通径:
500mm; 倾 动速度:
0~8°/s; 溜槽旋转速度:
9.8r/min; 公称压力:
0.2MPa 正常控制温度:
≤70℃ 冷却水压力:
0.2MPa
三、高炉冶炼主要设备简介
溜槽:L=1600 高护炼铁设备组成有:①高炉本体;
铁矿石中未还原的杂质和石灰石等熔剂结合生成炉渣,从渣口排出。 要求净煤气粉尘量小于10毫克。
- 1、下载文档前请自行甄别文档内容的完整性,平台不提供额外的编辑、内容补充、找答案等附加服务。
- 2、"仅部分预览"的文档,不可在线预览部分如存在完整性等问题,可反馈申请退款(可完整预览的文档不适用该条件!)。
- 3、如文档侵犯您的权益,请联系客服反馈,我们会尽快为您处理(人工客服工作时间:9:00-18:30)。
冷却带的传热过程与预热带类似。 冷却带中易发生析碳反应(2CO→C+CO2)。
后果:析碳过多,阻碍气流,降低冷却作用。
原因:冷却带处于CO分解反应易发生温度区,新还 原的金属铁具有析碳反应的触媒效应。
措施:保证一定的冷却煤气氧化度。
3.1.3 还原过程
(1)竖炉还原数学模型
简化的一步未反应核模型的导出式:
杂质去除方式;
踏实,奋斗,坚持,专业,努力成就 未来。20.12.1020.12.10Thurs day, December 10, 2020
弄虚作假要不得,踏实肯干第一名。08:11:4008:11: 4008:1112/10/2020 8:11:40 AM
安全象只弓,不拉它就松,要想保安 全,常 把弓弦 绷。20.12.1008:11:4008:11Dec-2010-Dec-20
传热方式
窑尾部分 窑头部分
炉气热辐射
<50% >80%
气流与炉料对流 ≈30% ≈10%
炉墙对炉料导热 ≈30% <5%
实际回转窑内,气流-炉料呈逆流运动,可有五种 传热途径。
令回转窑内预热段炉料吸收热量为Q。 解出:
当入窑炉料温度tso=0时,有: 预热段炉料温度按升高至800℃,预热段长度为
减小预热段长度的分析:
增大加热面积。
减小炉料填充率。一般填充率<20%,如过小,则 还原条件变坏,所以扩大加热面积作用有限。
增加传热系数。
传热方式为对流(70%)和辐射(25%),操作 温度受限制,气流速度不能过大,所以提高传热 系数可能性不大。
提高尾气温度。有效
尾气温度不能小于500℃,一般多控制在600~ 800℃。 热效率降低(废气热能利用)。
正常情况下回转窑处于塌落、滚落和瀑布型落下三 种状态中。
(2)炉料停留时间
由于回转窑不断转动,有摩擦力,炉料不断被推进。 炉料轴心方向的推进速度为ωs。
式中:K——窑体转动一周带炉料下落的次数; N——窑体转速,r/min; S——炉料被带起一次所推进的距离,m。
则炉料停留时间为:
式中:L——窑体长度,m。
长度计算; 还原过程:浓度场派生效应;温度场派生效
应;最佳煤气H2/(H2+CO);反应空区;影响 竖炉生产率的操作因素
3.2 回转窑
3.2.1 回转窑法炼铁过程
最重要的固体还原剂直接还原工艺。 按不同作业温度可生产海绵铁、粒铁及液态生铁,
其中低温作业的回转窑海绵铁法最有意义。 原料:细粒煤(0~3mm),脱硫剂(0~3mm石灰
石、白云石),块铁矿(5~20mm)。 炉体稍有倾斜(4%),转速4r/m。窑头外侧有烧
嘴燃烧燃料(煤粉、煤气或然油),废气炉尾排出, 炉气与炉料逆向运动。
炉料在预热段加热,蒸发水分及分解石灰石;在 800℃以后,再进行固体碳还原。
放出CO再氧化区被氧化,提供热量。
炉身横断面有:氧化区、中性区、还原区。 回转窑内进行的反应过程可按炉料运动、传热、还
温度场效应:H2↑→温度↓→还原速度↓ 最佳煤气成分:矿石还原度在某一煤气成分 ( H2/H2+CO)下达到最大值。它与移动床温度条件, 即操作条件和矿石的特性参数有关。
数模计算结果: H2/H2+CO≈0.3 实际生产: H2/H2+CO>0.5, H2+CO>0.75
应舍弃追求使用高H2煤气的观点
重于泰山,轻于鸿毛。08:11:4008:11: 4008:11Thurs day, December 10, 2020
不可麻痹大意,要防微杜渐。20.12.1020.12.1008:11:4008: 11:40December 10, 2020
加强自身建设,增强个人的休养。2020年12月10日 上午8时 11分20.12.1020.12.10
原反应及杂质气化分解。
3.2.2 炉料运动
(1)炉料运动方式 滑落:如果炉料与炉衬之间摩擦力太小,不足以带动
炉料,则炉料不断产生上移和滑落而且炉料颗粒不混 合,炉料与气流的传热现象处于近似停滞状态; 塌落:炉料与炉衬间有足够的摩擦力,但窑的转速很 小时,则炉料反复被带起,达到一定高度而蹋落; 滚落:当窑体转速加快时,则炉料由塌落进入滚动落 下的状态,这是回转窑炉料的正常运动状态; 瀑布型落下:进一步加快转速,带动的炉科则离开料 层放落形成瀑布状落下; 离心转动;转速太快,则炉料随窑壁离心转动而不落 下,这是不允许在回转窑中产生的现象。
1)浓度场派生效应:床层中煤气有效成分的浓度与 还原进程的关系。 矿石还原度↑→还原性气体浓度↓→还原反应推动 力(CA-CB/Ke)↓→阻碍矿石还原度↑,反之亦然。 结果:减弱操作参数(矿石粒度、矿石还原性、 还原气体入炉成分等)对矿石还原程度的影响。
2)温度场派生效应:任何影响反应床温度分布 的因素都会对还原过程产生显著的影响;反之,矿 石还原度的变化对床层温度场也有一定的影响,即 温度场变化对矿石还原有“反馈”作用。
而: 由物料平衡:
由热平衡得:
联立以上方程式即为移动床还原过程完整的数学 模型的微分方程组,可用于描述稳态条件下的竖炉 还原过程。
边界条件:气体出口处:Z=0,R=0; 气体入口处:Z=Zi;tg=tgi; CA=CAi;P=Pi。
(2)竖炉中矿石还原过程的特点
主要特点在于移动床反应器内存在两种影响矿石 还原过程的因素,即床层中还原气体的浓度场和 炉料与煤气的温度场。
抓住每一次机会不能轻易流失,这样 我们才 能真正 强大。20.12.102020年 12月10日星期 四8时11分40秒20.12.10
谢谢大家!
3.2.4 回转窑还原过程
(1)数学模型 还原段的数学模型应结合固体碳还原速率方程。
回转窑还原段中可认为CO→100%,Kb→∞。 或
回转窑操作温度(900~1000℃)下, 矿石的还原速度很快,上式中前项的值大 大高于后项之值,因此碳的气化反应是回 转窑中还原过程的限制环节。
(2)影响还原的因素
炉料顺行的条件:有效重力F≥0。根据Janssen公式:
式中:D——竖炉直径,m; M——炉料堆比重,kg/m3; f——炉料与炉墙摩擦系数; n——侧压系数。
高炉中,△P/Z→M,即F→0,下料不顺; 竖炉中,△P/Z 较小(2Pa/m3),M较大
(2000Pa/m3),竖炉不会因为煤气浮力引起悬料。 竖炉悬料的原因:
代入(3)得: 又由(1)、(2)得: 两式相减得:
积分得:
(4) (5入(5)得:
代入(5)得:
(6)
联立(4)、(6)得:
一般情况下, tso →0,则:
而: 由上两式可求炉内温度分布,此外可求出预热带高度。 如:定义预热带结束的标志为tg=ts+10℃,则:
如:煤气H2/H2+CO对还原过程的影响。 H2多,矿石还原度的↑使床层温度↓,阻碍还原 CO多,矿石还原度的↑使床层温度↑,促进还原
即温度场的变化可对铁矿石的还原过程产生一种 反馈作用,作用的效果由煤气中H2和CO相对含量所 决定。
3)最佳煤气H2/H2+CO
动力学:H2↑→反应速率常数和扩散系数↑→还原 速度显著↑
好的事情马上就会到来,一切都是最 好的安 排。上 午8时11分40秒 上午8时11分08:11:4020.12.10
每天都是美好的一天,新的一天开启 。20.12.1020.12.1008: 1108:11:4008: 11:40Dec-20
务实,奋斗,成就,成功。2020年12月10日 星期四8时11分 40秒T hursday , December 10, 2020
➢ 碳的反应性(Rb)。影响重大。 ➢ 配碳量。Mc↑,还原速度↑。常配加过剩碳量,
为理论值的100~200%。 ➢ 温度。T↑,促进还原,对气化尤为明显。受
限于灰分熔点及矿石的软化点。使窑内温度 有控制地达到最高极限是重要的操作原则。 ➢ 填充率。↑填充率,↓矿石氧化程度,有利于 矿石还原。受限于传热。 ➢ 触媒效应。Li、Na、K改善接触条件。
一般可用经验公式确定炉料在回转窑中的停留 时间 。
对于粉料:
式中:θ——炉料堆角;P——窑体斜度,rad; D——窑径。
对于颗粒炉料和球团矿:
式中: θ‘——堆角增量;
R——窑半径,m; g——重力加速度。
回转窑的利用系数
式中:ψ——填充率,%; ——总的停留时间,s;
(3)传热过程
炉料必须加热到800℃才能开始金属铁的还原。 预热段占回转窑长度40%。
4)反应空区:还原反应停滞的反应空间。 特点:Fe2O3→Fe3O4的还原过程已全部结束,而
Fe3O4→FexO的还原仍没有发生,此时矿石还原度 为0.111。
床层温度较低,气相浓度较小就易发生。
5)影响竖炉生产率的操作因素 操作因素→还原速度→生产率
温度:提高入炉煤气温度,有利于提高生产率。
煤气流量:流量↑,气固比↑,炉内平均温度↑,推 动力(CA-CB/Ke)↑,促进还原,但利用率↓
矿石入炉粒度:缩小矿石粒度能提高矿石还原速度, 但实际效果不明显。
矿石粒度减小同时有利于传热和冷却,从而提高生 产率。
但需满足炉料透气性的限制。
3.1 还原竖炉学习重点
炉料运动:顺行条件;悬料原因; 传热过程:还原剂、炉料温度分布;预热带
3.2.5 硫及有害杂质的去除
脱硫:燃料及矿石中硫→气流。 回转窑气流中H2少,气态硫以COS为主。 COS可被CaO和Fe吸收,CaO更易吸收,故CaO多,
气化脱硫率也愈低。
回转窑中CaS脱硫机理。
脱硫剂:白云石
不利影响:减少硫的挥发率;增加燃料消耗,同时 增加入炉流量;降低炉料含铁量,降低生产率。
预热带主要进行气-固相的热交换过程。
对于料柱中一微元段dZ,由热平衡有: