熔模铸造涂料工艺性能的控制
铸造质量控制

铸造质量控制引言概述:铸造是一种重要的创造工艺,广泛应用于各个行业。
铸造质量控制是确保铸件质量符合要求的关键步骤。
本文将从材料选择、工艺控制、设备维护、工艺改进和质量检测五个方面详细阐述铸造质量控制的重要性和方法。
一、材料选择1.1 确保原材料质量:选择合适的原材料是保证铸件质量的基础。
要求原材料符合国家标准,并进行严格的检验和测试。
1.2 控制合金成份:在铸造过程中,合金成份的控制对于铸件的性能至关重要。
通过精确的配料和严格的质量控制,确保合金成份符合设计要求。
1.3 优化材料熔化过程:材料熔化是铸造的关键步骤,要确保熔化温度、保温时间等参数符合要求,避免杂质温和体的夹杂。
二、工艺控制2.1 确定合适的铸造工艺:根据铸件的形状、尺寸和要求,选择合适的铸造工艺。
包括砂型铸造、金属型铸造、压铸等,确保铸造过程中能够得到良好的铸件质量。
2.2 控制铸造温度和速度:铸造温度和速度对于铸件的凝固过程和组织结构有重要影响。
通过控制熔体温度和冷却速度,避免铸件浮现缩孔、夹杂等缺陷。
2.3 优化浇注系统设计:浇注系统的设计对于铸件质量至关重要。
合理设计浇口、冷却水道等,确保熔体能够均匀地填充模型,避免气孔和缺陷的产生。
三、设备维护3.1 定期检查设备:定期检查铸造设备的状态,包括熔炉、模具、浇注设备等。
确保设备正常运行,避免因设备故障引起的铸件质量问题。
3.2 清洁和保养设备:保持设备的清洁和良好的工作状态对于铸造质量的控制至关重要。
定期清洗设备、更换磨损部件,确保设备的正常工作。
3.3 培训和提高操作技术:铸造工艺的操作技术对于铸件质量的控制有重要影响。
通过培训和提高操作技术,提高操作人员的技术水平,确保工艺的稳定性和一致性。
四、工艺改进4.1 分析和改进工艺缺陷:对于浮现的铸件缺陷,进行详细的分析和改进。
通过改进工艺参数、优化工艺流程等方式,减少缺陷的发生。
4.2 引进新工艺和技术:随着科技的发展,不断引进新的铸造工艺和技术,提高铸件质量和生产效率。
熔模铸造涂料工艺性能的控制

熔模铸造涂料工艺性能的控制一、前言“制壳”是熔模铸造生产中最重要的工序之一。
精铸件的废品与返修品中有60-80%是因型壳质量不良而造成。
型壳质量除受原辅材料(粘结剂、硬化剂及耐火砂粉料)、制壳生产环境(温度、湿度等)和操作者技术水平影响外,其主要的决定性因素是“涂料工艺性能”的优劣。
上述诸多因素直接与型壳强度、高温抗变形能力、透气性、热膨胀率、热化学稳定性等有关。
实践证明,精铸件上许多表面缺陷(毛刺、麻点、结疤、披锋、流纹、气孔分层夹砂等)和型壳的质量事故(穿钢、漏壳、变形、开裂等)常因上述因素产生,其中最重要又薄弱的环节是制壳生产中对涂料工艺性能检测和控制的缺失。
目前国内无论是已有近60年生产生产历史的水玻璃型壳或从国外引进已20年的硅溶胶型壳的企业,生产中绝大多数仍只限于用一个“流杯粘度计”来控制涂料质量。
虽然早在1985年,我国精铸业已颁布了“熔模铸造涂料试验方法”(JB4007-85)行业标准,但至今未能全面贯彻和执行,无疑这正是我国精铸件质量不稳定,返修率、废品率高,一次合格率低,质量事故频繁的重要原因之一。
国外精铸十分重视“涂料质量”的管理[1][2,]日本、美国等早就对硅溶胶涂料工艺性能进行有效的管理和控制。
我国精铸界同仁应认真学习,迎头赶上。
我国目前主要有两种精铸制壳工艺,即水玻璃和硅溶胶涂料。
其工艺性能指标虽然不同但控制和管理方法基本相同。
涂料工艺性能的稳定是精铸件质量稳定的必要条件。
二、涂料工艺性能的内容及定义1、流动性—涂料在蜡模(组)表面流动能力的大小及其流平性和流淌性的高低。
2、覆盖性—涂料在蜡模(组)表面覆盖能力的大小(润湿性或涂挂性能的高低)及在一定流淌时间内,涂料层平均厚度值的大小。
3、致密性—在一定覆盖性和流动性前提下,涂料内部致密程度的高低(粉料的体积浓度)。
4、稳定性—涂料中的粘结剂“胶凝”(老化)程度的高低和速度的快慢(涂料的使用寿命长短)。
5、均匀性—涂料层的均匀及洁净程度。
铸造生产过程质量控制点
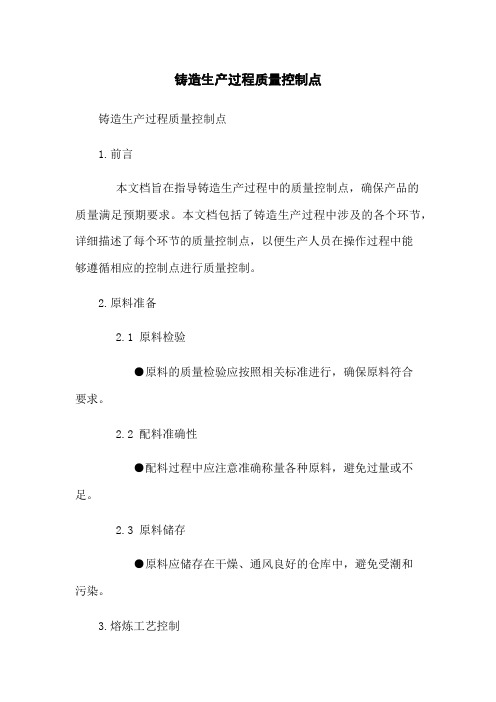
铸造生产过程质量控制点铸造生产过程质量控制点1.前言本文档旨在指导铸造生产过程中的质量控制点,确保产品的质量满足预期要求。
本文档包括了铸造生产过程中涉及的各个环节,详细描述了每个环节的质量控制点,以便生产人员在操作过程中能够遵循相应的控制点进行质量控制。
2.原料准备2.1 原料检验●原料的质量检验应按照相关标准进行,确保原料符合要求。
2.2 配料准确性●配料过程中应注意准确称量各种原料,避免过量或不足。
2.3 原料储存●原料应储存在干燥、通风良好的仓库中,避免受潮和污染。
3.熔炼工艺控制3.1 炉温控制●确保炉温达到合适的熔化点,避免熔炼温度过高或过低。
3.2 熔炼时间控制●控制熔炼时间,使金属能够充分熔化并达到均匀状态。
3.3 炉膛清洁●定期对炉膛进行清洁,清除炉渣和其他杂质。
4.浇注工艺控制4.1 浇注温度控制●控制浇注温度,确保金属在浇注过程中不过热或过冷。
4.2 浇注速度控制●控制浇注速度,使金属能够充分填充模具,并形成理想的形状。
4.3 浇注压力控制●控制浇注压力,确保金属在浇注过程中能够均匀充实。
5.硬化工艺控制5.1 冷却时间控制●控制冷却时间,使铸件能够充分硬化。
5.2 冷却介质控制●选择合适的冷却介质,确保铸件冷却均匀。
5.3 温度检测●对冷却后的铸件进行温度检测,确保其达到硬化要求。
6.表面处理工艺控制6.1 砂型清理●对铸件表面的砂型进行清理,移除可能存在的杂质和砂粒。
6.2 表面修整●对铸件表面进行修整,去除可能存在的凹凸不平的部分。
6.3 防锈处理●对铸件进行防锈处理,防止氧化和腐蚀。
附件:●附件1、原料质量检验标准●附件2、浇注工艺参数记录表●附件3、硬化工艺参数记录表●附件4、表面处理工艺记录表法律名词及注释:●1.法律名词1、注释1●2.法律名词2、注释2●3.法律名词3、注释3。
特种铸造2第二章_熔模铸造
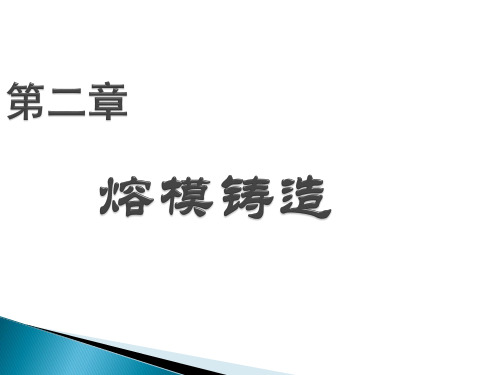
2.2.4.4 熔模的脱模
分型剂的使用:压蜡前在压型内表面涂 敷一层,利于取出熔模。 要求越薄越好
蜡基:一般采用机油、松节油、硅油 树脂基:麻油与酒精混合物或者硅油 压缩空气起模
2.2.5 熔模的组装
1) 焊接法——应用最广泛 电烙铁
2) 粘接法——卯榫结构 3) 机械组装法——大批量、小铸件、高效率
熔化方法 水浴加热
旋转桨叶搅拌法
活塞搅拌法: 带孔活塞往复运动
2. 松香基模料的配制
A 熔化设备:不锈钢电热锅(熔点高) B 注意:加料次序 聚合物、蜡料、松香
3. 模料配制工艺要点:
模料配制过程中应该注意的三点:
A 严格控制温度的升限和在高温下停留的时间。避免模料的 烧损和变质。(防止局部过热) B 合理安排各组元的加热顺序 原则:溶剂优先,互溶在前。
硬度提高,强度下降,凝固温度区间变窄
• 表2-2 石蜡—硬脂酸(1:1)模料的主要性能
2.2.2.2 树脂基模料
• 松香:软化点70~90℃ • 用途 • 常与蜡料、聚合物等混合蜡基模料
• 蜡基模料 • 优点:易于配制(熔点较低),复用性好。 • 不足:软化点过低,收缩率略大,硬脂酸价格过高。
• HB 5352.4-2004 熔模铸造型壳性能试验方法 第4部分:透气性的测定
型壳的制造工艺——涂挂法
熔模铸造型壳: 多层型壳:涂挂法制壳—(浸涂)最常用
喷涂法
刷涂法
对型壳的性能要求:
1 . 型壳的高温强度和高温软化点
型壳的软化点是指型壳强度随温度升高而开始下降 的温度。不同型壳软化点不同。软化点高,高温强度下 降速度小,有利于提高铸件的尺寸精度。
2.3 型壳的制造
铸造生产过程的质量控制
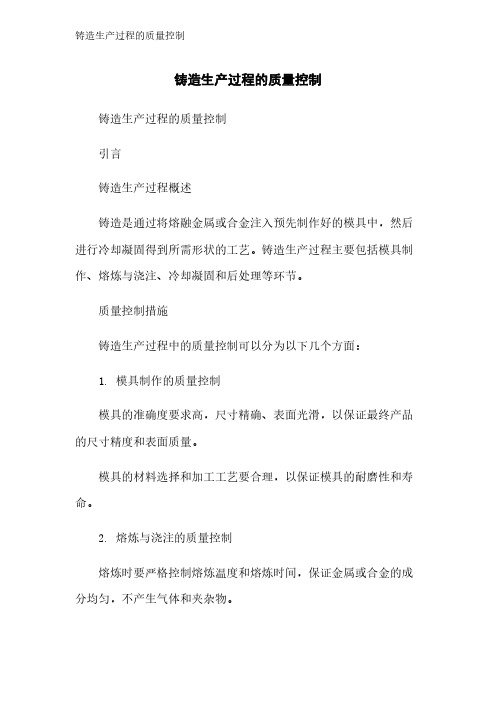
铸造生产过程的质量控制铸造生产过程的质量控制引言铸造生产过程概述铸造是通过将熔融金属或合金注入预先制作好的模具中,然后进行冷却凝固得到所需形状的工艺。
铸造生产过程主要包括模具制作、熔炼与浇注、冷却凝固和后处理等环节。
质量控制措施铸造生产过程中的质量控制可以分为以下几个方面:1. 模具制作的质量控制模具的准确度要求高,尺寸精确、表面光滑,以保证最终产品的尺寸精度和表面质量。
模具的材料选择和加工工艺要合理,以保证模具的耐磨性和寿命。
2. 熔炼与浇注的质量控制熔炼时要严格控制熔炼温度和熔炼时间,保证金属或合金的成分均匀,不产生气体和夹杂物。
浇注时要控制浇注温度和速度,避免产生气孔、夹渣和缩松等缺陷。
3. 冷却凝固的质量控制控制冷却速度和冷却方式,以避免产生组织缺陷,如晶粒过大、晶界不清晰等。
控制凝固过程中的温度变化,以避免产生应力和变形。
4. 后处理的质量控制清理杂质和缺陷,如夹渣、气孔等。
进行热处理、表面处理或机械加工,以改善产品的性能和表面质量。
质量控制方法为了有效控制铸造生产过程中的质量,可以采取以下几种方法:1. 设计质量控制在产品设计阶段,就应考虑产品的铸造性,合理设计产品的几何形状和壁厚,减少可能出现的缺陷和变形。
2. 工艺参数控制对每个工艺环节中的关键参数进行严格控制,如熔炼温度、浇注温度和速度等。
在铸造过程中,通过实时监测温度、压力和流速等参数,进行及时调整和控制。
3. 检测和检验使用各种检测设备和仪器,如X射线探伤仪、超声波检测仪等,对产品进行无损检测,以发现和排除可能存在的缺陷。
进行物理和化学性能的检验,如拉伸试验、硬度测试和成分分析等。
4. 信息化管理建立完善的质量管理体系,进行全过程的质量记录和数据分析,发现问题并采取措施进行改进。
运用信息化技术,实现数据的实时监控和追溯,提高生产过程的透明度和可控性。
结论铸造生产过程的质量控制是确保最终产品质量的重要环节。
通过合理的质量控制措施和方法,可以有效避免铸造过程中可能出现的缺陷和变形,提高产品的质量和性能。
铸造涂料的性能控制与技术发展_下_

五# 铸造涂料方面几项值得一提的进展
近 ;$ 年来% 在铸造涂料的研究# 开发方面不断有新 的思路出现% 有的虽然已问世多年了% 但仍然值得借鉴$
+ ,粘土湿砂型用的涂料
粘土湿砂造型是最古老的工艺% 也是迄今仍然应用 最广的工艺% 传统的做法是在型砂中加入煤粉等辅料以 改善铸件的表面质量% 不用涂料$ 近年来% 随着汽车工 业的发展% 对铸件要求的提高已不仅限于材质和内在质 量% 表面质量也日益受到重视$ 因而% 在粘土湿砂型用 涂料方面也在不断探索$ ;$ 世纪 8$ 年代% 有人在粘土湿砂型表面喷一薄层 醇基石墨涂料% 喷涂后不点燃% 直接合型浇注% 铸件的 表面质量得到显著改善$ :$ 年代% _ 0 ? S L 0 公司研发了一种干粉涂料% 商品名 2 B0 /0 O + $ 涂料是表面涂覆有诺沃腊克酚醛树脂 称是 * C 和胺类硬化剂的锆砂粉% 在小型流态床内分散% 再经专 用的塑料喷嘴喷出$ 涂料颗粒喷出时% 因摩擦而带有静 电荷% 同时因湿砂型含有水分% 有一定的电导率% 这样 就可使涂料颗粒与砂型表面结合$ 浇注时% 由金属液的 热量使涂料表面的树脂熔融# 硬化% 形成涂料层$ 据报 道% 日本有几家铸造厂采用此工艺% 铸件的表面质量改 善% 气孔缺陷减少$ ;# 世纪初% _ 0 ? S L 0 公司又推出了一种粘土湿砂型用 D N @ , a C Q ( 5#$$ + $ 这种涂料是高固体含量 的涂料 * < 的水基涂料% 在大量生产的造型线上喷涂于砂型表面% 喷涂后不需烘干% 有增强砂型的作用% 在减少铸件表面 缺陷方面效果很好% 美国# 日本# 澳大利亚和荷兰都有 铸造厂采用$ 0 ? S L 0 D N @ , a C Q 此后不久% _ 公司又在 * < ( 5#$$ + H PL 0 X S5’$$ + $ 这种 的基础上% 开发了改进型涂料 * < 涂料中加有晶态石墨% 除减少铸件表面缺陷外% 还可以 改善铸件的表面粗糙度$
铸造生产过程质量控制点
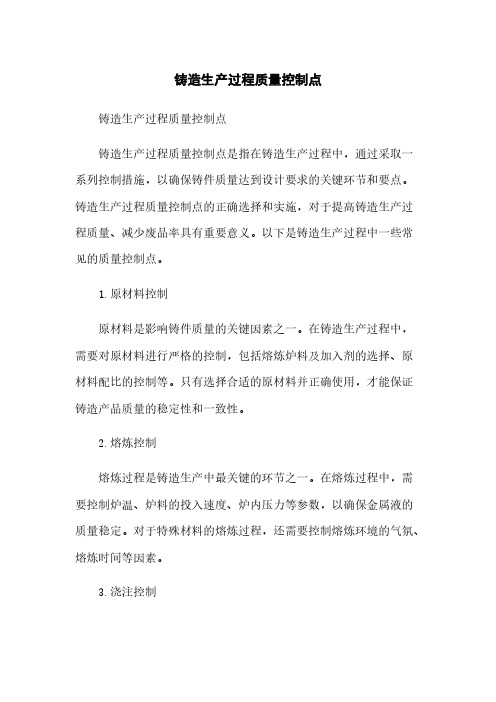
铸造生产过程质量控制点铸造生产过程质量控制点铸造生产过程质量控制点是指在铸造生产过程中,通过采取一系列控制措施,以确保铸件质量达到设计要求的关键环节和要点。
铸造生产过程质量控制点的正确选择和实施,对于提高铸造生产过程质量、减少废品率具有重要意义。
以下是铸造生产过程中一些常见的质量控制点。
1.原材料控制原材料是影响铸件质量的关键因素之一。
在铸造生产过程中,需要对原材料进行严格的控制,包括熔炼炉料及加入剂的选择、原材料配比的控制等。
只有选择合适的原材料并正确使用,才能保证铸造产品质量的稳定性和一致性。
2.熔炼控制熔炼过程是铸造生产中最关键的环节之一。
在熔炼过程中,需要控制炉温、炉料的投入速度、炉内压力等参数,以确保金属液的质量稳定。
对于特殊材料的熔炼过程,还需要控制熔炼环境的气氛、熔炼时间等因素。
3.浇注控制浇注过程是将熔融金属注入到型腔中的过程。
在浇注过程中,需要控制浇注速度、浇注温度、浇注方式等因素,以保证浇注质量和铸件的致密性。
还需要控制浇注过程中金属液的气体排出情况,避免气孔的产生。
4.型腔控制型腔是铸造中形成铸件形状和尺寸的关键部位,对铸件质量有着重要影响。
型腔控制包括型腔设计、制造和维护等环节。
必须确保型腔的准确尺寸和光洁度,避免型腔表面的破损和变形,以确保铸件的形状精度和表面质量。
5.冷却控制冷却过程是铸件从熔融状态到固态过程中的一个关键环节。
在冷却过程中,需要控制冷却速度、冷却介质、冷却时间等因素,以保证铸件组织的均匀性和致密性。
还需要控制冷却过程中的温度梯度,避免铸件产生应力和变形。
6.热处理控制对于某些特殊材料或要求较高的铸件,还需要进行热处理过程。
热处理过程包括加热、保温和冷却等环节。
在热处理过程中,需要控制温度、保温时间、冷却速度等参数,以确保铸件组织的改善和性能的提升。
7.表面处理控制铸件的表面处理是为了提高铸件的表面质量和耐腐蚀性。
表面处理包括喷砂、抛光、电镀等工艺。
在表面处理过程中,需要控制处理剂的使用和浸溶时间,以保证铸件表面的光洁度和处理效果。
熔模铸造的工艺设计要点及注意事项
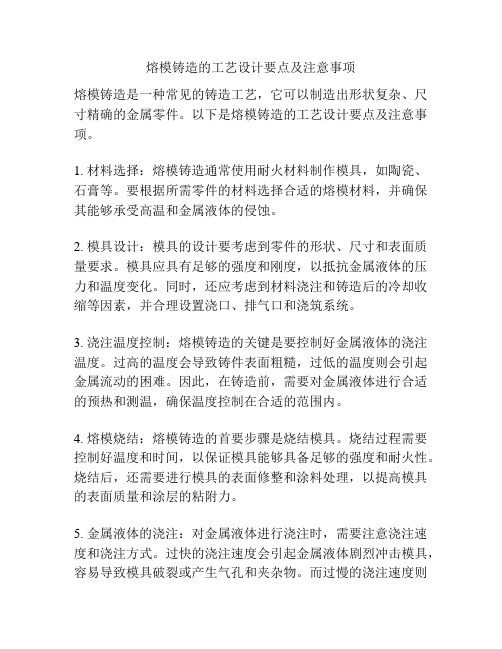
熔模铸造的工艺设计要点及注意事项熔模铸造是一种常见的铸造工艺,它可以制造出形状复杂、尺寸精确的金属零件。
以下是熔模铸造的工艺设计要点及注意事项。
1. 材料选择:熔模铸造通常使用耐火材料制作模具,如陶瓷、石膏等。
要根据所需零件的材料选择合适的熔模材料,并确保其能够承受高温和金属液体的侵蚀。
2. 模具设计:模具的设计要考虑到零件的形状、尺寸和表面质量要求。
模具应具有足够的强度和刚度,以抵抗金属液体的压力和温度变化。
同时,还应考虑到材料浇注和铸造后的冷却收缩等因素,并合理设置浇口、排气口和浇筑系统。
3. 浇注温度控制:熔模铸造的关键是要控制好金属液体的浇注温度。
过高的温度会导致铸件表面粗糙,过低的温度则会引起金属流动的困难。
因此,在铸造前,需要对金属液体进行合适的预热和测温,确保温度控制在合适的范围内。
4. 熔模烧结:熔模铸造的首要步骤是烧结模具。
烧结过程需要控制好温度和时间,以保证模具能够具备足够的强度和耐火性。
烧结后,还需要进行模具的表面修整和涂料处理,以提高模具的表面质量和涂层的粘附力。
5. 金属液体的浇注:对金属液体进行浇注时,需要注意浇注速度和浇注方式。
过快的浇注速度会引起金属液体剧烈冲击模具,容易导致模具破裂或产生气孔和夹杂物。
而过慢的浇注速度则会导致金属液体凝固不完全。
此外,还需注意金属液体的均匀浇注,避免产生冷隔。
6. 冷却和晾热处理:在铸造完成后,需要对铸件进行冷却和晾热处理。
冷却过程应缓慢进行,以防止因温度变化引起的热应力和变形。
晾热处理有助于提高铸件的机械性能和组织均匀性。
总之,熔模铸造的工艺设计要点及注意事项包括材料选择、模具设计、浇注温度控制、熔模烧结、金属液体的浇注和冷却晾热处理等。
合理的工艺设计能够确保铸件的质量和精度,提高生产效率和产品品质。
继续写:7. 模具温度控制:熔模铸造中,模具温度的控制是非常重要的。
模具的温度过高会导致模具磨损加剧,模具寿命减少,并且可能引起铸件的气孔和缺陷。
熔模铸造的工艺过程及防止缺陷产生的方法
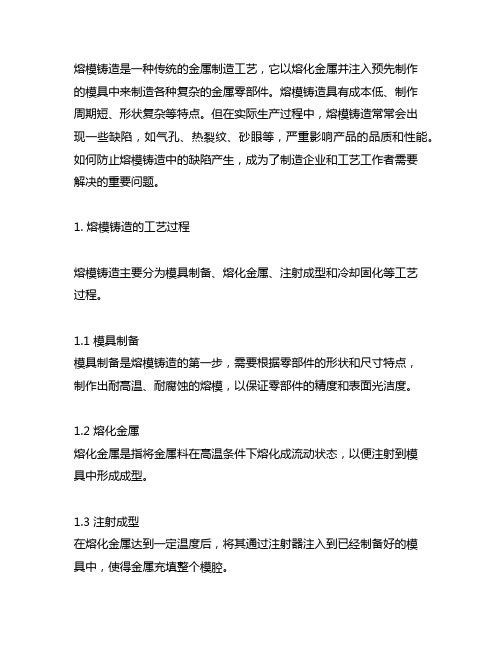
熔模铸造是一种传统的金属制造工艺,它以熔化金属并注入预先制作的模具中来制造各种复杂的金属零部件。
熔模铸造具有成本低、制作周期短、形状复杂等特点。
但在实际生产过程中,熔模铸造常常会出现一些缺陷,如气孔、热裂纹、砂眼等,严重影响产品的品质和性能。
如何防止熔模铸造中的缺陷产生,成为了制造企业和工艺工作者需要解决的重要问题。
1. 熔模铸造的工艺过程熔模铸造主要分为模具制备、熔化金属、注射成型和冷却固化等工艺过程。
1.1 模具制备模具制备是熔模铸造的第一步,需要根据零部件的形状和尺寸特点,制作出耐高温、耐腐蚀的熔模,以保证零部件的精度和表面光洁度。
1.2 熔化金属熔化金属是指将金属料在高温条件下熔化成流动状态,以便注射到模具中形成成型。
1.3 注射成型在熔化金属达到一定温度后,将其通过注射器注入到已经制备好的模具中,使得金属充填整个模腔。
1.4 冷却固化注射成型后,金属在模具中冷却并固化成型,然后可以取出零部件进行后续的处理。
2. 防止缺陷产生的方法2.1 优化模具设计模具设计是影响熔模铸造质量的重要因素之一。
合理的模具结构设计和表面涂层处理,可以有效减少金属氧化、气孔和砂眼等缺陷的产生。
2.2 控制金属熔化和浇注温度金属的熔化温度和浇注温度直接影响了熔模铸造品质。
合理控制金属熔化和浇注温度,可以降低金属的气体溶解度,减少气孔和砂眼等缺陷。
2.3 优化浇注系统浇注系统是指将熔化金属注入模具中的一系列通道和孔道。
合理设计浇注系统,可以减少金属在注射过程中的速度冲击和气体夹杂,降低缺陷的产生率。
2.4 严格控制熔模铸造工艺参数包括模具预热温度、浇注速度、压力等工艺参数的严格控制,可以有效减少热裂纹、砂眼等缺陷的产生。
3. 个人观点和理解熔模铸造作为一种常见的金属制造工艺,经过不断的发展和改进,已经成为了制造复杂金属零部件的主要方法之一。
在实际生产中,如何降低缺陷的产生,提高熔模铸造产品的质量和性能,是需要企业和工艺工作者共同努力的方向。
不锈钢熔模铸造缺陷分析及质量控制

不锈钢熔模铸造缺陷分析及质量控制熔模铸造的工艺流程通常为:压型制造→蜡模压制→蜡模组装→浸涂料→撒砂→硬化及干燥→脱蜡→焙烧→浇注→落砂及清理。
由于其工艺环节较多,过程较复杂,因而最终铸件的品质受诸多因素的影响很大,不易进行控制。
结合不锈钢熔模铸造生产过程中出现的若干缺陷类型,探讨、分析不锈钢熔模铸造过程中品质控制的关键环节。
1、典型缺陷及其成因(1)表面麻坑在生产中,有时发现成批铸件表面出现麻坑(见图1-1).呈规则的半球形小坑,凹坑直径为013~018mm,深013~015mm,麻坑在铸件局部呈密集状分布.该缺陷虽不影响铸件使用性能,但无法修整,严重影响了铸件的表面品质,导致铸件成批报废。
对该缺陷进行能谱分析(见图1-2 ),结果表明该缺陷位置存在着微量的Mg、Ca等元素。
图(1-1)铸件表面麻坑缺陷图(1-2)麻坑缺陷位置的能谱分析该表面麻坑缺陷产生的主要原因是面层型壳材料不合格。
在铸造生产中多采用锆砂作为型壳面层耐火材料,其导热性好,蓄热能力大,耐火度高,热震稳定性好。
纯ZrSiO4的耐火度在2000℃以上,但随着杂质含量增加,耐火度相应下降。
当锆砂中含有氧化物杂质时,其分解温度会下降,如含有Ca、Mg氧化物时,分解温度会降至1300℃左右,当含有K、Na氧化物时,其分解温度会降至900℃左右[1,2]。
锆砂是ZrO2・SiO2二元系中唯一的化合物,但其分解时析出的无定形SiO2具有很高的活性,能与金属中的Cr、Ni、Ti、Mn、Al 等合金元素在高温下发生化学反应,致使铸件表面产生麻坑缺陷,恶化铸件的表面品质。
(2)黑点不锈钢铸件加工或抛光后,在加工表面位置时,会出现分散的规则球状的黑点缺陷(见图1—3),其缺陷位置的能谱分析(见图1-4)。
可见该黑点缺陷存在O、Si、Mn等元素.图(1—3)铸件黑点缺陷图(1—4)黑点缺陷位置的能谱分析该黑点缺陷产生的原因可能是由于钢液中存在有非金属夹杂物(主要是金属元素的氧化物、硫化物和硅酸盐)而导致的。
熔模铸造各个工序质量管理标准要求
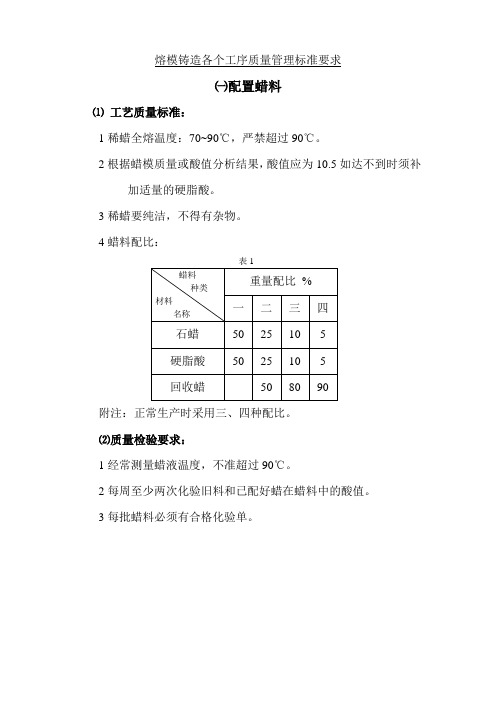
熔模铸造各个工序质量管理标准要求㈠配置蜡料⑴工艺质量标准:1稀蜡全熔温度:70~90℃,严禁超过90℃。
2根据蜡模质量或酸值分析结果,酸值应为10.5如达不到时须补加适量的硬脂酸。
3稀蜡要纯洁,不得有杂物。
4蜡料配比:附注:正常生产时采用三、四种配比。
⑵质量检验要求:1经常测量蜡液温度,不准超过90℃。
2每周至少两次化验旧料和已配好蜡在蜡料中的酸值。
3每批蜡料必须有合格化验单。
㈡压制蜡模⑴工艺质量标准:1稀蜡温度:65~80℃。
2稠蜡保温水温;48~50℃。
3压送稠蜡的压力:1.5~4公斤/厘米2 。
4不允许水分和过多的空气混入稠蜡内。
5稠蜡应呈搅拌均匀的膏状,温度应保持在45~48℃。
6蜡模冷却水温:14~24℃;冷却时间:10~60分钟。
⑵质量检验要求:1俢除分型面上的飞边和注口余头。
2用稀蜡填补注蜡口处的缺肉处并修理光滑。
3用毛刷清扫或用压缩空气吹除蜡件外表的蜡渣。
4自检蜡模质量要求到达“四不〞:即不缩、不裂、不涨、不洼陷,“两无〞即:无飞边、无蜡屑。
5容易变形的蜡模要摆放整齐,易损坏的蜡模不允许在吹洗蜡模机口吹洗。
㈢模组装配⑴工艺质量标准:1室温:18~28℃,〔最高不得超过30℃〕2蜡模之间的间距:5~15mm.3根据质量要求,选择适当的蜡棒,按照工艺参数表的规定,焊正角度和方向。
4焊缝要严密,装配要均匀,不得有蜡滴、蜡渣、灰尘。
⑵质量检验要求:1装蜡模前发现蜡模上有蜡渣或灰尘过多不许装配。
2焊缝要密实,间距应均匀并符合工艺规定。
3蜡模上不准烫伤或有蜡滴,也不准有灰尘或蜡屑。
㈣涂料模壳⑴工艺质量标准:1涂料液配制的标准参数:①原水玻璃:模数M=3.1~3.5 比重ν②工艺参数:见表22涂料配制工艺标准:①用比重计先将配好的水玻璃测量,不符合规定的水玻璃不许配料。
②按重量比将粉状料参加搅拌机与水玻璃混合直至搅拌均匀,无疙瘩前方可停顿搅拌。
③搅拌后镇静二小时,再进步均匀后测量其粘度,符合要求前方准送至制壳线用于生产。
熔模铸造工艺守则
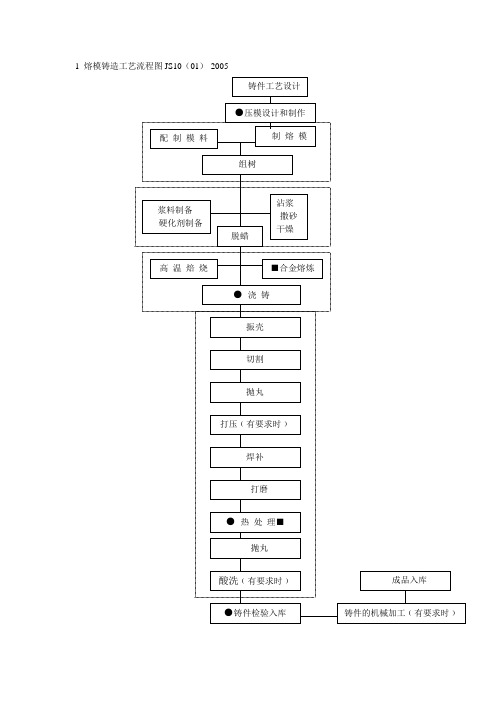
1 熔模铸造工艺流程图JS10(01)-2005注:●检验点■特殊过程2 范围本工艺守则规定了熔模铸造工艺过程中各工序的工艺要求。
适用于低温模料、手工或压蜡机压制蜡模,硅溶胶和水玻璃粘结剂制壳、酸(碱)性中频电炉熔炼,生产碳素钢、合金钢等熔模精密铸件的工艺过程。
●蜡型工艺JS02(01)-2005△1 蜡料制备工艺要求1.1稀蜡温度:65~80℃。
1.2蜡膏保温缸水温:48~50℃。
1.3蜡膏应搅拌均匀呈糊状,温度控制在45~48℃,其中不允许有颗粒状蜡料。
1.4蜡料酸值:105±5。
1.51.5.1正常生产采用3.4两种配方,配方5用于沾制浇口棒。
1.5.2蜡料配方是指酸值符合105±5范围内的基本配方,在生产过程中必须根据蜡模质量或酸值分析结果,适量增加或减少硬脂酸量,冬季的酸值取下限,夏季的酸值取上限。
△2 蜡模制造工艺要求2.1室温:10~30℃。
2.2蜡膏压注温度:45~46℃,压力:0.2~0.6Mpa,保压时间:3~10s。
2.3压型冷却水温:14~24℃,冷却时间:20~100s。
2.4制模分型剂:10#变压器油。
2.5蜡模表面应光洁,形状完整,尺寸合格,不允许有缩陷、凸包、裂纹、错位、气泡等缺陷。
△3 蜡模组装工艺要求3.1室温:10~30℃。
3.2模组间最小间隙:8mm,较大平面间隙最小20mm。
3.3模组最小压头:60mm,尾端最小余头:10mm。
3.4蜡模内浇口与蜡棒之间焊接要严密,不得有尖角和小缝。
3.5组装的蜡模应均匀,不得有蜡滴、蜡渣、灰尘及杂物。
●制壳工艺JS02(02)-2005△1 涂料配置工艺要求1.1工艺材料主要技术注:(1)涂料粘度使用4#詹氏杯测定;(2)过度层和背层涂料中不加润湿剂和消泡剂。
1.1.2室温:24℃±2℃。
1.1.3涂料搅拌时间:面层全部为新材料时搅拌时间≥24h,部分新材料时搅拌时间≥12h;过渡层涂料及背层涂料全部为新材料时搅拌时间≥10h,部分新材料搅拌时间≥5h。
铸造生产过程的质量控制
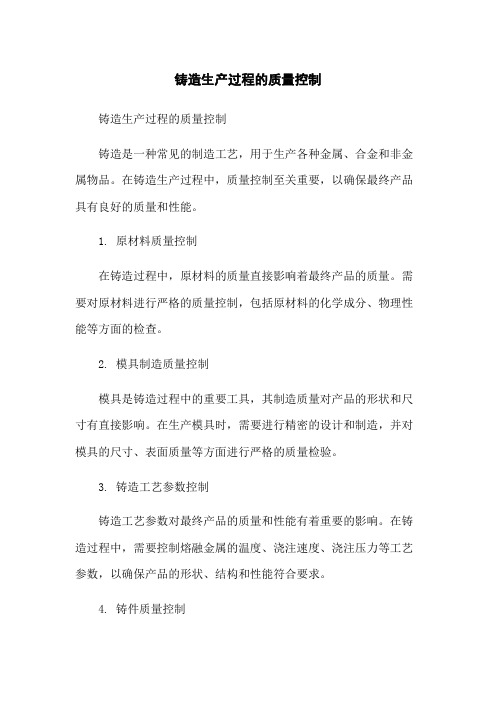
铸造生产过程的质量控制
铸造生产过程的质量控制
铸造是一种常见的制造工艺,用于生产各种金属、合金和非金属物品。
在铸造生产过程中,质量控制至关重要,以确保最终产品具有良好的质量和性能。
1. 原材料质量控制
在铸造过程中,原材料的质量直接影响着最终产品的质量。
需要对原材料进行严格的质量控制,包括原材料的化学成分、物理性能等方面的检查。
2. 模具制造质量控制
模具是铸造过程中的重要工具,其制造质量对产品的形状和尺寸有直接影响。
在生产模具时,需要进行精密的设计和制造,并对模具的尺寸、表面质量等方面进行严格的质量检验。
3. 铸造工艺参数控制
铸造工艺参数对最终产品的质量和性能有着重要的影响。
在铸造过程中,需要控制熔融金属的温度、浇注速度、浇注压力等工艺参数,以确保产品的形状、结构和性能符合要求。
4. 铸件质量控制
铸件质量是衡量铸造过程成功与否的重要指标。
在铸造过程中,需要对铸件的尺寸、表面质量、内部缺陷等进行严格的质量检验,
以确保产品的质量符合要求。
5. 产品性能检验
最终产品的性能是铸造过程成功与否的重要标志。
在铸造完成后,需要对产品的力学性能、化学性能、表面硬度等进行全面的检验,以确保产品的性能符合要求。
,铸造生产过程的质量控制是确保最终产品质量的关键环节。
通过对原材料质量、模具制造质量、铸造工艺参数、铸件质量和产
品性能的严格控制,可以提高产品的质量和性能,满足客户的需求。
熔模铸造工艺守则(新)

内部资料注意保密熔模铸造工艺守则石家庄同嘉不锈钢制品有限公司ShiJiaZhuang TongJia Stainless Steel Products Co.,Ltd.目录编号名称页号B - 01/01 总则 (1)B - 01/02 模料处理 (2)B - 01/03 压制蜡(熔)模 (3)B - 01/04 浇道(模头)制作 (5)B - 01/05 修蜡(熔)模 (6)B - 01/06 模组焊接 (7)B - 01/07 模组清洗 (8)B - 01/08 涂料配置 (9)B - 01/09 制壳 (11)B - 01/10 脱蜡 (13)B - 01/11 型壳焙烧 (14)B - 01/12 筑炉 (15)B - 01/13 炉料配制 (18)B - 01/14 熔炼 (20)B - 01/15 浇注 (22)B - 01/16 震动脱壳 (23)B - 01/17 切割浇口 (24)B - 01/18 磨內浇口 (25)B - 01/19 抛丸清理 (26)B - 01/20 喷砂清理 (27)B - 01/21 钝化 (28)B - 01/22 焊补 (29)B - 01/23 热处理 (30)B - 01/24 校正 (31)B - 01/25 砂带机修磨 (32)附加说明 (33)中国铸造协会精密铸造分会CICBA 工艺指导型文件 B –01/01共1页第1页总则一、使用范围与内容本工艺守则是针对使用中温模料、高压压蜡机压制蜡模;硅溶胶粘结剂制壳;碱性快速熔化炉熔炼;生产不锈钢等合金熔模精密铸件的工艺守则而制定的一般性工艺规则。
它规定了该工艺过程中各工序的工艺要求、操作程序和注意事项。
称为熔模铸造第Ⅰ类工艺,简称为熔模铸造工艺(Ⅰ)工艺守则。
二、熔模铸造(Ⅰ)工艺流程说明:1.图中实线框代表必要制程,虚线框代表选择性制程,即非必要制程。
2.各工厂可根据铸件特点,客户要求及本厂实际情况,对以上清理制程进行适当增减或调整次序。
特种铸造主要工序质量控制

特种铸造主要工序质量控制一、熔模铸造主要工序质量控制熔模铸造是指用易熔材料如蜡料制成模样,在模样上包覆若干层耐火涂料制成型壳,熔出模样后经高温焙烧即可浇注合金液的铸造方法。
图11-20 熔模铸造过程示意图熔模铸造过程如图11-20所示。
其过程主要工序包括:模料、涂(浆)料和硬化剂制备、制熔模、制壳和制芯、脱蜡和焙烧、合金熔炼和浇注、铸件脱壳、清理和后处理等。
熔模铸造过程工序对熔模铸造铸件的质量影响和影响程度可参见第13章的表13-8。
因此,严格控制熔模铸造过程工序的质量是十分重要的。
通常,应严格按企业制定的熔模铸造技术要求检验蜡模与型壳质量,不但应按规定检查蜡模的几何形状和指定的重要尺寸以及型壳的表面质量,而且还应注意检查:1)压型是否有合格证。
2)模料成分和配比是否正确。
3)模料熔化温度和时间。
4)模料压制温度和保持的时间、压力是否正常。
5)模料存放温度和时间是否符合要求。
6)检查蜡模表面质量。
7)检查蜡模的组合正确性和焊接质量。
8)检查组合蜡模是否有粘料、机械损伤、变形、杂物等缺陷。
9)模组的存放时间是否符合要求。
10)模组表面是否脱脂干净。
11)硬化剂的配制是否符合要求。
12)各种粉、粒材料是否符合要求。
13)粘结剂的性能是否符合要求。
14)涂料成分和配制百分比是否符合要求。
15)检查涂料的物理工艺性能。
16)检查模组表面油脂是否除净。
17)检查模组的涂料层数和涂料层是否均匀。
18)型壳在涂制涂料后到熔失蜡模的停留时间是否过长或过短。
19)检查模组涂料层是否有落脱和裂纹。
20)检查模组熔失时间及熔失后型壳的表面质量。
21)蜡模熔失后是否按规定的时间送低温烘烤。
22)型壳烘烤的时间和温度是否正确。
23)型壳的存放时间和温度是否符合要求。
24)型壳的焙烧温度和时间是否符合要求。
熔模铸造中蜡模与型壳检验项目及检验范围见表11-40。
表11-40 熔模铸造中蜡模与型壳的检验项目及检验范围(续)二、金属型铸造主要工序质量控制金属型铸造是指在重力作用下将熔融金属浇入金属型获得铸件的方法。
油漆工艺质量控制措施

油漆工艺质量控制措施一、背景介绍油漆工艺质量控制措施是在进行涂装工艺时,为了保证涂装质量,减少质量缺陷而采取的一系列措施。
本文将详细介绍油漆工艺质量控制措施的具体内容。
二、涂装前准备1. 表面处理:在进行涂装前,需要对待涂物的表面进行处理,包括去除油污、锈蚀、氧化物等,以保证涂装层与基材的良好附着力。
2. 清洁度控制:在涂装前,需要确保涂装环境的清洁度,包括清除灰尘、异物等,以避免对涂装质量产生不良影响。
3. 涂装材料准备:涂装材料的准备包括稀释剂、颜料、固化剂等的配制和调试,确保涂料的质量稳定。
三、涂装过程控制1. 涂料施工工艺:根据不同的涂装要求,选择合适的涂料施工工艺,包括刷涂、喷涂、滚涂等,以确保涂装层的均匀性和一致性。
2. 涂料用量控制:根据涂装要求和涂料的性质,控制涂料的用量,以避免涂装层过厚或者过薄导致的质量问题。
3. 涂装温度控制:在涂装过程中,需要控制涂装环境的温度,以确保涂料的干燥和固化效果。
4. 涂装时间控制:根据涂料的性质和涂装要求,控制涂装的时间,保证涂料的干燥和固化效果。
四、涂装后处理1. 涂装层检测:涂装完成后,对涂装层进行检测,包括涂层的厚度、附着力、硬度等,以确保涂装质量符合要求。
2. 缺陷修复:如果在涂装过程中发现涂装层存在缺陷,需要及时修复,包括刮除、砂磨、重新涂装等。
3. 涂装层保护:对涂装层进行保护,包括防尘、防水、防腐等,以延长涂装层的使用寿命。
五、质量控制记录1. 涂装前检查记录:记录涂装前的准备工作,包括表面处理、清洁度控制、涂装材料准备等。
2. 涂装过程记录:记录涂装过程中的关键参数,包括涂料施工工艺、涂料用量、涂装温度、涂装时间等。
3. 涂装后处理记录:记录涂装后的处理工作,包括涂装层检测结果、缺陷修复情况、涂装层保护措施等。
六、质量控制培训为了保证油漆工艺质量控制措施的有效实施,需要对涂装工艺人员进行培训,包括涂装技术、质量控制要求、安全操作等方面的培训。
铸造质量控制

铸造质量控制一、引言铸造是一种广泛应用于创造业的工艺,它涉及到将熔化的金属或者合金倒入模具中,使其冷却凝固成为所需形状的零件或者产品。
在铸造过程中,质量控制是至关重要的,它直接影响到最终产品的质量和性能。
本文将详细介绍铸造质量控制的标准格式文本,包括质量控制目标、质量控制措施和质量控制评估。
二、质量控制目标1. 产品尺寸和形状的控制:铸造产品的尺寸和形状是直接影响其装配性能和使用效果的重要因素。
质量控制目标是确保铸造产品的尺寸和形状与设计要求一致,减少尺寸偏差和形状缺陷。
2. 材料成份的控制:铸造材料的成份对产品的力学性能和化学性能有着重要影响。
质量控制目标是确保铸造材料的成份符合设计要求,减少材料成份偏差和不合格材料的使用。
3. 表面质量的控制:铸造产品的表面质量直接影响到其外观和耐久性。
质量控制目标是确保铸造产品的表面光洁度、无气孔、无裂纹和无疤痕,提高产品的美观度和使用寿命。
4. 内部质量的控制:铸造产品的内部质量对其强度和耐久性有着重要影响。
质量控制目标是确保铸造产品的内部结构均匀、无夹杂物和无缩孔,提高产品的强度和使用寿命。
三、质量控制措施1. 工艺参数控制:铸造过程中的工艺参数对产品质量有着重要影响。
质量控制措施包括控制熔炼温度、保持浇注温度、控制浇注速度和控制冷却速度等,以确保产品的尺寸和形状符合要求。
2. 模具设计和创造控制:模具的设计和创造对铸造产品的质量有着重要影响。
质量控制措施包括优化模具结构设计、控制模具创造精度和检测模具表面质量等,以确保产品的表面质量和尺寸精度。
3. 材料质量控制:铸造材料的质量对产品的质量有着重要影响。
质量控制措施包括严格控制原材料的供应商选择、进行材料成份分析和检测,以确保材料的成份符合要求。
4. 检测和检验控制:铸造产品的质量检测和检验是质量控制的重要环节。
质量控制措施包括使用非破坏性检测方法、进行尺寸测量和力学性能测试等,以确保产品的表面质量和内部质量符合要求。
熔模铸造涂料工艺性能的控制概要
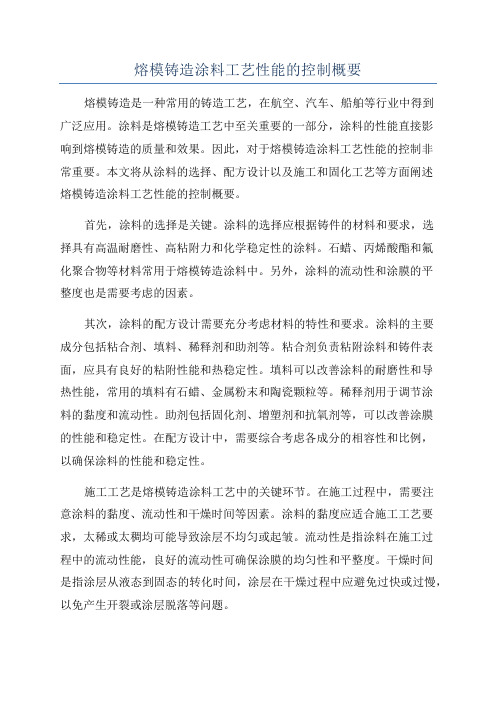
熔模铸造涂料工艺性能的控制概要熔模铸造是一种常用的铸造工艺,在航空、汽车、船舶等行业中得到广泛应用。
涂料是熔模铸造工艺中至关重要的一部分,涂料的性能直接影响到熔模铸造的质量和效果。
因此,对于熔模铸造涂料工艺性能的控制非常重要。
本文将从涂料的选择、配方设计以及施工和固化工艺等方面阐述熔模铸造涂料工艺性能的控制概要。
首先,涂料的选择是关键。
涂料的选择应根据铸件的材料和要求,选择具有高温耐磨性、高粘附力和化学稳定性的涂料。
石蜡、丙烯酸酯和氟化聚合物等材料常用于熔模铸造涂料中。
另外,涂料的流动性和涂膜的平整度也是需要考虑的因素。
其次,涂料的配方设计需要充分考虑材料的特性和要求。
涂料的主要成分包括粘合剂、填料、稀释剂和助剂等。
粘合剂负责粘附涂料和铸件表面,应具有良好的粘附性能和热稳定性。
填料可以改善涂料的耐磨性和导热性能,常用的填料有石蜡、金属粉末和陶瓷颗粒等。
稀释剂用于调节涂料的黏度和流动性。
助剂包括固化剂、增塑剂和抗氧剂等,可以改善涂膜的性能和稳定性。
在配方设计中,需要综合考虑各成分的相容性和比例,以确保涂料的性能和稳定性。
施工工艺是熔模铸造涂料工艺中的关键环节。
在施工过程中,需要注意涂料的黏度、流动性和干燥时间等因素。
涂料的黏度应适合施工工艺要求,太稀或太稠均可能导致涂层不均匀或起皱。
流动性是指涂料在施工过程中的流动性能,良好的流动性可确保涂膜的均匀性和平整度。
干燥时间是指涂层从液态到固态的转化时间,涂层在干燥过程中应避免过快或过慢,以免产生开裂或涂层脱落等问题。
最后,固化工艺对于涂料的性能和质量起着决定性的影响。
涂料在固化过程中,会经历一系列的物理和化学变化,包括挥发、热化学反应和交联等。
固化工艺的选择应根据涂料的特性和要求,包括温度、时间和压力等因素。
固化过程中的温度和时间要适中,过高或过低的温度都会对涂层的性能产生不利影响。
压力可以用于提高涂膜的结合力和抗破坏能力。
综上所述,熔模铸造涂料工艺性能的控制需要从涂料的选择、配方设计、施工工艺和固化工艺等方面综合考虑。
熔模铸造质量控制的若干工艺措施

收稿日期:2012-02-19收到初稿,2012-04-25收到修订稿。 作者简介:景宗梁 (1945-),男,高级工程师,主要从事熔模铸造的工艺和技术工作。E-mail:jzl-02@
铸造
景宗梁等:熔模铸造质量控制的若干工艺措施
·1023·
形插块,最后将蜡模放入水中冷却。 使用插块工艺操作时,安放和取出校正插块,均
!"
!!!!!"
·1022· !!!!!"
熔模铸造
!"
铸造
FOUNDRY
熔模铸造质量控制的若干工艺措施
Sep. 2012 Vol .61 No.9
景宗梁,车顺强
(郑州大禹化工产品有限公司,河南郑州 450008)
摘要:介绍了熔模铸造中校正插块的施放、二元复合芯的应用和透气砖吹氩气的工艺措施等。为了实现铸件质量过
图1 前端盖蜡模 Fig. 1 Front end housing the wax mold
图2 铝合金材质的校正插块 Fig. 2 Aluminum alloy correction insert
图3 校正插件放在蜡模之中 Fig. 3 The correction put in wax mold
表1吹氩前后钢液中有害元素的对比beforeandafterargonblowing钢号cf8ccf8c是否吹氩未吹氩吹氩o2的质?分数106542211氧化夹杂物平均m132275氧化夹杂物的弥散性集中扩散table1contrastofharmfulelementsinliquidsteel氩气保护气体本身?参与冶金反应但从钢液中上升的每个小气泡相当于一个个小真空室气泡图8氩气底吹装置结构图中h2n2co的分压接近于零具有气洗作用在精炼时发挥出搅拌钢液均匀钢液温度和化学成分fig
- 1、下载文档前请自行甄别文档内容的完整性,平台不提供额外的编辑、内容补充、找答案等附加服务。
- 2、"仅部分预览"的文档,不可在线预览部分如存在完整性等问题,可反馈申请退款(可完整预览的文档不适用该条件!)。
- 3、如文档侵犯您的权益,请联系客服反馈,我们会尽快为您处理(人工客服工作时间:9:00-18:30)。
熔模铸造涂料工艺性能的控制一、前言“制壳”是熔模铸造生产中最重要的工序之一。
精铸件的废品与返修品中有60-80%是因型壳质量不良而造成。
型壳质量除受原辅材料(粘结剂、硬化剂及耐火砂粉料)、制壳生产环境(温度、湿度等)和操作者技术水平影响外,其主要的决定性因素是“涂料工艺性能”的优劣。
上述诸多因素直接与型壳强度、高温抗变形能力、透气性、热膨胀率、热化学稳定性等有关。
实践证明,精铸件上许多表面缺陷(毛刺、麻点、结疤、披锋、流纹、气孔分层夹砂等)和型壳的质量事故(穿钢、漏壳、变形、开裂等)常因上述因素产生,其中最重要又薄弱的环节是制壳生产中对涂料工艺性能检测和控制的缺失。
目前国内无论是已有近60年生产生产历史的水玻璃型壳或从国外引进已20年的硅溶胶型壳的企业,生产中绝大多数仍只限于用一个“流杯粘度计”来控制涂料质量。
虽然早在1985年,我国精铸业已颁布了“熔模铸造涂料试验方法”(JB4007-85)行业标准,但至今未能全面贯彻和执行,无疑这正是我国精铸件质量不稳定,返修率、废品率高,一次合格率低,质量事故频繁的重要原因之一。
国外精铸十分重视“涂料质量”的管理[1][2],日本、美国等早就对硅溶胶涂料工艺性能进行有效的管理和控制。
我国精铸界同仁应认真学习,迎头赶上。
我国目前主要有两种精铸制壳工艺,即水玻璃和硅溶胶涂料。
其工艺性能指标虽然不同但控制和管理方法基本相同。
涂料工艺性能的稳定是精铸件质量稳定的必要条件。
二、涂料工艺性能的内容及定义1、流动性—涂料在蜡模(组)表面流动能力的大小及其流平性和流淌性的高低。
2、覆盖性—涂料在蜡模(组)表面覆盖能力的大小(润湿性或涂挂性能的高低)及在一定流淌时间内,涂料层平均厚度值的大小。
3、致密性—在一定覆盖性和流动性前提下,涂料内部致密程度的高低(粉料的体积浓度)。
4、稳定性—涂料中的粘结剂“胶凝”(老化)程度的高低和速度的快慢(涂料的使用寿命长短)。
5、均匀性—涂料层的均匀及洁净程度。
6、悬浮性—涂料中粉料重力沉降倾向的大小或涂料在静置一定时间后上下层致密性的差别程度。
三、涂料各工艺性能对型壳或铸件质量的影响1、流动性的影响:涂料流动性差将很难形成厚薄均匀的涂层,难以顺利流入蜡模的复杂型腔,涂料常会滞留、堆积造成干燥(或硬化)不透,使型壳在该处脱蜡或焙烧时产生裂纹,引起穿钢、披锋等缺陷,尤其对于中大件(W>10-200kg)或复杂件,流动性更是涂料最基本的性能要求。
2、覆盖性的影响:若表面层涂料对蜡模湿润能力差(涂挂性差),不能使涂层在蜡模上100%覆盖,则铸件表面会有“结疤”、“桔皮”等缺陷。
涂层(表面层或背层)均应有一定厚度要求,过厚则难干燥(硬化)透,型壳易分层、开裂,造成铸件表面“夹砂”、气孔(透气性差);涂层过薄则在撒砂较粗时会使型壳表面出现“蚁孔”,造成铸件表面“毛刺”,同时由于干燥或“硬化”过度会使型壳表面产生裂纹,导致铸件表面披锋,飞翅、流纹等缺陷出现。
第一二层型壳的厚、薄决定了铸件表面质量,背层涂层则决定了型壳整体强度。
3、致密性的影响:表面层涂料致密性高低,直接影响型壳及铸件表面质量。
高致密度涂层能获得平整、光洁无蚁孔、美观的型壳内表面,铸件相应表面粗糙度细、缺陷少,可大大降低铸件返修率(少焊补、打磨)。
背层致密度高则型壳强度高,不易开裂,当然,过高的致密性涂料会增加成本(粉料多),加速涂料“老化”(粘结剂薄膜过薄)。
粘结剂过少时型壳强度低,表面易出现微裂纹,背层型壳易开裂、漏钢。
4、稳定性的影响:涂料“老化”,即粘结剂在制壳前已有“凝胶”存在,会使型壳表面层缺陷增多:分层、结疤、开裂、落砂、夹砂、粗糙等。
而且型壳整体强度下降(背层涂料也老化时),还会影响涂料其他工艺性能:流动性下降,覆盖性增大,致密性大大降低。
5、均匀性的影响:表面层均匀性高低直接影响到铸件表面质量。
由于涂挂性差会产生“结疤”。
均匀性差会引起局部表面“毛刺”;洁净度差(涂料中有蜡屑、粉粒、粗砂)会产生麻坑、毛刺。
不均匀的的涂层型壳平面上易开裂(硬化或干燥后),铸件表面会产生披锋、“流纹”。
背层均匀性差,型壳浇注、焙烧时易开裂。
均匀性是涂料质量的基本要求之一。
6、悬浮性影响:涂料(桶)上下工艺性能不一致,直接会导致型壳涂层厚薄及致密性不同。
硅溶胶涂料悬浮性差,粉料沉降快,为保持涂料的悬浮性,必须24小时低速搅拌,水玻璃涂料也应在浸涂时充分搅拌。
对于悬浮性差的涂料,边搅拌边涂挂是最理想、合理的涂制方法。
四、涂料工艺性能的影响因素<一>涂料的流变特性:1、流体按流变特性分两种:牛顿流体和非牛顿流体。
水玻璃与硅溶胶涂料均属于非牛顿流体,主要特点是其剪切应力τ与剪切速率v不成正比,因而它没有一个固定的绝对“粘度值”η,只有一个随剪切应力τ大小变化的“表现粘度”ηa,它是涂料“稠度”的大小度量[3]。
在生产中用流杯(ηΦ6、ηΦ4或ηΦ5)按一定体积涂料流尽的时间来计算,这就是“条件粘度”如ηΦ6或ηΦ4等,它等同于“表现粘度”ηa。
条件粘度ηΦ6或ηΦ4与表现粘度ηa无理论关系,但有相关关系,即ηΦ6或ηΦ4大,则ηa也大,反之也成立。
2、水玻璃—石英粉涂料是具有较低屈服值τy的“胀塑性”流体,而水玻璃—铝硅系耐火粉料的涂料是属于有较高屈服值τy的“胀塑性”流体。
其主要特点是随剪切速率v增大其表现粘度ηa也会增大,即它具有“剪切增稠”效应,涂料在搅拌或自然流动时(等于剪切)ηa会增大,而且只有剪切应力τ大于涂料屈服值(涂料内部结构阻力)τy 时(τ>τy),涂料才会流动。
3、硅溶胶—锆英粉(或铝硅系粉料)涂料是低屈服值的“假塑性”流体。
其特点是随v增大ηa会减小,即“剪切稀释”效应,因而硅溶胶涂料在模组上流动或搅拌时其表现粘度ηa会降低,故它比水玻璃涂料流动性要高得多。
<二>涂料流动性影响因素:1、涂料流动性高低主要影响因素是涂料的屈服值τy ,其次是表现粘度ηa (即条件粘度ηΦ6、ηΦ4)及流型的类别。
单一用测定涂料的条件粘度ηΦ6不能全面真实地反映涂料的流动性高低。
涂料流动性应该用JB/T4007-1999标准中“流动长度法”来测定,既直观又合理。
涂料的流动长度L 与粘度ηΦ6及涂层厚度三者关系可通过试验予以确定。
表一是测定了不同产地的石英粉料与水玻璃配成的涂料L ,ηΦ6及δ的数据。
表一 水玻璃—石英粉涂料工艺性能注:①水玻璃ρ=1.254g/cm3 M=3.54 n=1.0 t=15℃②δ=涂p S G ×10(mm )见下节。
由表一数据分析可得出下述几点结论:1)涂料的δ和ηΦ6相同(近)时其流动性L 值也相同(近),如表一中的3#,6#(n 相同时);2)粉液比n 相同时涂料流动L 值与δ关系密切,δ越大,L 越小,反之δ小则L 值大,流动性好;(1#,5#,2#,4#,3#,6#依次δ减小,L 依次增大)3)由表一测试结果可知,代表涂料屈服值τy 大小的涂层厚度δ是影响涂料流动性的主要因素,其次才是ηΦ6。
4)当涂料n 和δ相同时涂料粘度ηΦ6越高,其流动性越差,即L 值越小;反之ηΦ6越低,其流动性越好,即L 值越大。
(如表一中的2#,4#)5)由上结论可知:①仅凭ηΦ6一个粘度参数不能正确反映涂料流动性高低。
如1#与2#,虽然n 相同,但由于δ不同,其粘度值ηΦ6高的2#涂料其流动性反比ηΦ6低的1#高一倍。
1#涂料:η16Φ=21(s),L=44mm2#涂料:η26Φ=50(s),L=84mm②当涂料粉液比n(严格说是涂料的致密性K值)与δ值相同时,则ηΦ6可以代表其流动性高低(ηΦ大流动性差,反之ηΦ小流动性好)。
生产中ηΦ6比L更容易检测、操作方便,故在n(K),δ相同时可用ηΦ值来代表L值反映出涂料的流动性高低。
当然如前分析,若δ相同,n(K)值不同的涂料,其相同流动性L对应的ηΦ6也略有不同(在一定范围内)。
<三>涂料覆盖性的影响因素:1、影响涂挂性的因素,主要有(1)涂料对模料的润湿性:水基涂料如水玻璃、硅溶胶对蜡基模料润湿性很差(润湿角θ>90°),而醇基涂料如硅酸乙脂则有良好涂挂性(θ<90°)。
生产中只要在涂料中加入0.1-0.3%的 JFC(占粘结剂重量)即可减小θ,改善润湿性。
(2)相同粘结剂,但低温蜡比中温蜡润湿性较好.这是因为低温蜡表面比中温蜡粗糙度粗,而且其中含有硬脂酸。
其他蜡基、树脂基中温蜡不含硬脂酸,其涂料性不如低温蜡。
(3)高粉液比即高致密度的涂料比粉液比n(K)低的涂料涂挂性好,覆盖性高。
2、影响涂层厚度δ的因素:只有在涂挂性(润湿性)达到100%时涂层厚度δ才有实际意义。
(1)涂料的屈服值τy是影响δ的主要因素,其次是涂料密度ρ涂。
δ=τy/ρ涂·g·sinθ……①当θ=90°时(涂层垂直于水平线)δ=τy /ρ涂·g ……②公式①中:τy —涂料屈服值;ρ涂—涂料密度; g —重力加速度;θ—涂层与水平面夹角。
由公式②可知:涂层平均厚度δ与涂料的屈服值τy 成正比,与涂料密度 ρ涂呈反比关系。
(2)涂料的屈服值τy 的大小主要由:粘结剂的密度ρ液及涂料的致密性K%(即涂料中粉料的体积浓度)和粉料中微粉(粒径0.2-10um )含量W 0%有关。
ρ液,K %,W%越大则τy 也越高,其中主要因素是W 0%。
<四>涂料致密性的影响因素:涂料的致密性可用其中耐火粉料的体积浓度K (%)来代表。
K =ρ粉ρ涂W ·×100% ……<1> W =液粉+粉W W W ×100% ……<2> n =液粉W W ……<3> W =1+n n ×100% ……<4> 公式<1>中:ρ涂—涂料密度(g/cm ³);W —涂料中粉料的含量(质或重量%);ρ粉—粉料的真密度(g/cm ³)。
公式<2>中:W 粉—粉料质(重)量(g );W 液—粘结剂质(重)量(g )。
公式<3>中:n —涂料中粉料质量与粘结剂质量的比例(粉液比)。
将公式<4>代入公式<1>则得:K =ρ粉+ρ涂)1n (·n ×100% ……<5> 公式<5>中ρ涂=ρ液ρ粉+ρ液ρ粉n n )1(+⨯……<6>(详见下节) 将<6>代入<5>则得公式<7>表明了涂料致密性K%与粉液比n 的关系;由公式<7>还可知:(1)不同密度和类别的粘结剂及粉料组成的涂料其致密性可统一用涂料中粉料的体积密度K%来计算和表达,比用n 更准确。